Задачи оперативного регулирования хода производства
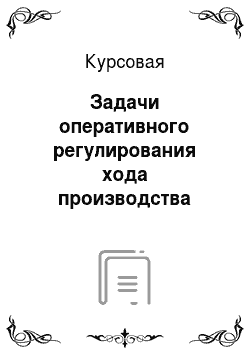
В условиях серийного производства главными объектами диспетчерского наблюдения и контроля являются установленные по плану сроки запуска-выпуска партий заготовок и деталей на всех участках производства, состояние складских заделов деталей и заготовок и степень комплектной обеспеченности сборочных единиц в соответствии с графиком. В зависимости от характера серийного производства диспетчерский… Читать ещё >
Задачи оперативного регулирования хода производства (реферат, курсовая, диплом, контрольная)
Содержание Введение
1. Теоретическая часть
1.1 Оперативное управление производством
1.2 Текущий контроль и регулирование производства
1.3 Организация оперативного регулирования единичного, серийного и массового производства
2. Практическая часть
2.1 Обоснование и расчёты организационно-производственных параметров цеха
2.2 Обоснование производственной структуры цеха
2.3 Расчёт штучного времени комплекта обработки деталей и определение основного технологического маршрута
2.4 Расчёт показателей относительной трудоёмкости деталей и относительной трудоёмкости операций
2.5 Определение профиля предметной специализации
2.6 Расчёт пооперационного показателя массовости по деталям и выбор форм поточного производства на участках цеха Заключение Список использованной литературы Введение Задача оперативного регулирования производства заключается в организации слаженной и комплектной работы всех звеньев производства по изготовлению и выпуску заданной номенклатуры изделий в установленных объёмах и сроках при наилучшем использовании всех производственных ресурсов.
Создавая условия для пропорционального развития производства, учет и регулирование должны быть, ориентированы на достижение конечных результатов — своевременного выпуска продукции высокого качества и повышение эффективности производства.
Оперативный учет и регулирование производства должны отвечать следующим требованиям и принципам: базироваться на прогрессивных календарно-плановых нормативах, которые в свою очередь являются основой календарных графиков изготовления и выпуска продукции; обеспечивать необходимую сопряжённость в работе производственных подразделений и насыщенность всех стадий производства комплектными заделами; способствовать наилучшему использованию производственных фондов; предусматривать возможность осуществления вариантных расчётов и получению оптимальных решений; обладать гибкостью и возможностью перестройки в связи с динамизмом производства; соответствовать организационному типу производства; обладать способностью быстрой реакции на все возмущающие факторы в ходе производства, сокращая до минимума время между возникновением ситуации, требующей принятия решения и осуществлением управляющего воздействия.
Основная особенность системы оперативного учета и регулирования производства заключается в увязке частичных процессов, которые выполняются отдельными производственными звеньями, благодаря чему достигается слаженный ход производства. Важнейшим фактором, определяющим построение всей системы организации, планирования и управления на предприятии, является тип производства (единичный, серийный или массовый).
Под типом производства понимается классификационная категория производства, характеризуемая по признакам широты номенклатуры, регулярности, стабильности и объема выпуска продукции.
Целью курсовой работы является раскрытие сущности, определение задач оперативного регулирования хода производства, а именно:
— в чем заключаются смысл и содержание оперативного управления производством, на уровне организации, цеха, участка, рабочего места;
— каковы задачи и содержание оперативного регулирования производства;
— каковы основные цели и задачи контроля и анализа хода производства.
1. Теоретическая часть
1.1 Оперативное управление производством Установившееся в практике управления производством понятие «оперативное управление» имеет отношение к завершающей стадии этого процесса. Оперативное управление производством характеризуется принятием управленческим персоналом решений в реально складывающейся или сложившейся производственной ситуации.
В этих условиях разработанные плановые здания или решения руководителей производственных подразделений должны обеспечить строгий и четкий во времени порядок выполнения запланированных работ. Этому соответствует разработка оперативно-календарных планов (графиков запуска-выпуска деталей) и сменно-суточных заданий на уровне цехов, участков (бригад) и рабочих мест. В составе системы ОУП выполняются следующие основные функции, присущие управлению в целом:
— оперативное планирование;
— организация работ по ОУП;
— оперативная координация;
— оперативный учет;
— оперативный анализ;
— оперативный контроль;
— оперативное регулирование (диспетчеризация).
На межцеховом уровне оперативное управление осуществляется для решения принципиальных вопросов снятия, замены запущенных в производство изделий, включения в программу выпуска новых изделий, обеспечения внешних поставок комплектующих изделий, использования внутренних материальных, трудовых и финансовых ресурсов.
Для оперативного управления производством в цехах характерна строгая регламентация выполнения работ во времени по каждой позиции производственной программы и номенклатурно-календарного плана в зависимости от фактически складывающейся производственной ситуации. Работы по оперативному управлению производством выполняются в реальном масштабе времени, не допускающем перерывов в процессе изготовления деталей и сборки изделий. Временной горизонт оперативности управления для цеха в целом может быть в пределах месяца, для участков (бригад) и рабочих мест — в интервале недели — смены. Для межцехового уровня этот интервал расширяется от месяца до года.
В настоящее время процедуры оперативного управления все больше переплетаются с технологией и регулированием (диспетчеризацией) производства. Повседневно выполняемые управленческим персоналом функции по оперативному учету, контролю и анализу хода производства являются основой для выработки вариантов регулирующих воздействий на ход производства.
Таким образом, оперативное управление производством осуществляется на основе непрерывного (повседневного) слежения за ходом производства, оказывая целенаправленное воздействие на коллективы цехов, участков (бригад), рабочих для обеспечения безусловного выполнения утвержденных производственных программ.
Это достигается:
— строгим распределением работ на короткие периоды времени (декада, неделя, сутки, смена) в цехах, на производственных участках (бригадах) — в подетальном и узловом разрезах, а для рабочих мест в подетально-пооперационном виде;
— четкой организацией сбора и обработки информации о ходе производства;
— комплексным использованием средств вычислительной техники для подготовки вариантов управленческих решений;
— повседневным анализом и владением управленческим персоналом производственной ситуацией в каждом звене предприятия;
— своевременным принятием решений и организацией работы по предупреждению нарушений в ходе производства или для быстрого его восстановления в случае отклонений от запланированной траектории управления.
1.2 Текущий контроль и регулирование производства Диспетчирование (регулирование) производства является заключительным этапом оперативного планирования.
Под диспетчированием производства понимается централизованное руководство работой всех органов предприятия на основе плана — графика, а также систематического учета и контроля текущего хода производства. Для осуществления функции диспетчирования в составе производственно-диспетчерского отдела предприятия создается диспетчерская служба, основной задачей которой служит поддержание бесперебойного и ритмичного хода производства в соответствии с заданным планом запуска-выпуска продукции на всех стадиях ее изготовления.
Оперативное регулирование хода производства осуществляется диспетчированием путем систематического учета и контроля за выполнением сменно-суточных заданий и применением профилактических мероприятий, устраняющих причины, нарушающие ритм производства и срывы выполнения планов. ОПП по месту его выполнения подразделяется на межцеховое и внутрицеховое. Межцеховое осуществляется ПДО — производственно-диспетчерским отделом предприятия (рисунок 1).
серийный цех деталь трудоёмкость Рисунок 1 — Структура производственно-диспетчерского отдела предприятия.
В функции его входят разработка оперативно-календарных нормативов, взаимная увязка содержания и сроков календарных графиков работы цехов, составление и выдача цехам календарных планов по месяцам, оперативный учет и диспетчирование выполнения календарного плана.
Внутрицеховое планирование направлено на ритмичное выполнение участками и их рабочими местами заданной месячной программы и выполняется производственно-диспетчерскими бюро (ПДБ).
Основными принципами диспетчирования являются централизация, плановость, оперативность, профилактика отклонений от заданного графика работ.
Централизация диспетчерской деятельности означает осуществление её из единого центра — ПДО и обязательных распоряжений главного или сменного диспетчера для всех начальников цехов и отделов.
Плановость выражается в ведении диспетчирования на основе месячных сменно-суточных планов, в соблюдении сроков запуска-выпуска, поддержании хода производственного процесса в заданном ритме и в соответствии с заданным сменным планом. Оперативность диспетчерской службы основывается на конкретности руководства, широкой осведомленности о состоянии работы в любом звене предприятия, систематическом контроле за ходом производственного процесса по графику и принятие незамедлительных мер по устранению возникающих отклонений.
Профилактика отклонений заключается в контроле качества сменно-суточных планов, их обеспеченности, знании пропускной способности каждого участка, его слабых сторон.
Оперативный контроль охватывает ежесменный учет сдачи цехами по графику деталей, сборочных единиц и изделий, состояния межцеховых передач и заделов в производстве, равномерность хода производства, выявление отклонений и их устранение.
Контроль равномерности хода производства в течение смены осуществляется централизованно из ПДО, где дежурят диспетчера и операторы, поддерживающие постоянную связь с диспетчерами.
В журнале диспетчерской службы регистрируются все отклонения от плана за смену, новые срочные задания, сообщения поставщиков о задержке в отправке грузов и разные поручения, которые необходимо выполнить диспетчерскому аппарату.
Исходной информацией, необходимой для облегчения бесперебойности работы, является: сменно-суточный план и данные оперативного учета о выполнении плана, об обеспеченности сменных заданий всем необходимым, перечень позиций плана, идущих с опережением или отставанием, данные журнала диспетчерской службы.
В журнале дежурный диспетчер делает отметки о принятых мерах. Кроме того, диспетчерская служба ведет картотеку, в которую входят мероприятия, осуществление которых требует более длительного периода.
Оперативность контроля усиливается ежедневными диспетчированными совещаниями, которые дают отправные данные всей работы диспетчерского отдела в течение текущих суток.
Для работы диспетчерских органов используют устройства, позволяющие руководителям быстро связываться с любым подразделением, получать информацию, давать указания с помощью телефонной, телеграфной, электронной связи.
Для непрерывного диспетчерского контроля и регулирования используется диспетчерский пульт с телевизионным устройством. В центральной части пульта помещена станция диспетчерской связи, которая обеспечивает связь проведения диспетчерских совещаний. Пульт имеет световую поисковую антенну, блоки автоматического счета и учета выпуска изделий, аппаратуру аудиои видеозаписи и звукоусилительную станцию.
Профилактика отклонений заключается в контроле качества сменно-суточных планов, их обеспеченности необходимыми материальными ресурсами, технологической оснасткой и оборудованием, хорошим знанием пропускной способности каждого производственного участка и их слабых сторон, в разработке совокупности профилактических мероприятий, позволяющих знать все факторы, ведущие к отклонению производства от плана, и не допускать появления таких отклонений.
Оперативный контроль выполнения планов цехами осуществляется ведущими инженерами ПДО, закреплёнными за определёнными цехами, и сменными диспетчерами ПДО с диспетчерского пульта предприятия.
Оперативный контроль охватывает:
— ежесменный учёт сдачи цехами по графику деталей, сборочных единиц и изделий;
— состояние межцеховых передач и состояние заделов в производстве;
— равномерность хода производства;
— выявление отклонений и их своевременное устранение.
Контроль равномерности хода производства в течение смены в цехах осуществляется централизованно из ПДО, где круглосуточно дежурят диспетчеры и операторы, поддерживающие постоянную связь с планово-диспетчерскими бюро (ПДБ) цехов. Особенности диспетчерского контроля в зависимости от типа производства приведены в таблице 1. Он отличается, прежде всего, составом объектов наблюдений.
В единичном производстве основным объектом диспетчерского контроля за ходом производства являются сроки выполнения важнейших работ по отдельным заказам. Диспетчерский контроль осуществляется в этих условиях применительно к разработанным цикловым планам-графикам выполнения заказов. Он предусматривает систематическую проверку своевременности запуска-выпуска заготовок, деталей и узлов по отдельным этапам их изготовления, а также своевременности комплектования деталей и узлов для окончательного монтажа и выпуска готовой машины в установленные планом сроки.
Таблица 1 — Особенности общепроизводственного диспетчерского контроля в зависимости от типа производства
Вид контроля | Производство (тип) | |||||
Массовое | Крупносерийное | Серийное | Мелкосерийное | Единичное | ||
Контроль выполнения номенклатурного плана предприятия и плана отгрузки продукции | Контроль выпуска изделий со сборки и после испытания, контроль выпуска узлов и ведущих деталей | Контроль выполнения заказов в соответствии с календарным позаказным графиком | ||||
Посменно и по часам суток в соответствии с установленным ритмом | В соответствии с календарным планом-графиком | |||||
В реальном масштабе времени | ||||||
Контроль межцеховых передач узлов, деталей заготовок | Контроль за соблюдением установленных стандартных сроков подач | Проверка соответствия месячному календарному плану подач | ||||
Контроль за состоянием заделов на межцеховых складах | Подетальный | В комплектах на узел, в групповых комплектах | В комплектах на заказ, на узел | |||
Контроль оперативной подготовки производства | Контроль за подготовкой по особо важным позициям (изготовление инструмента, приспособлений, аварийный ремонт оборудования и т. п.) | |||||
Наблюдение за работой отстающих цехов | Контроль за изготовлением отстающих деталей | |||||
Почасовой | Ежедневный | Поэтапный (в отдельных случаях пооперационный) | ||||
В реальном масштабе времени | ||||||
Важнейшим условием бесперебойного выполнения производственных заданий в этих условиях является своевременная и комплектная техническая подготовка, а также сопровождающая ее оперативная подготовка всего необходимого для выполнения заказа. Диспетчерское руководство производством должно осуществлять текущую увязку работы органов технической подготовки, участвующих в последовательных стадиях разработки заказов, а также руководить комплектованием технологического оснащения и необходимых материалов.
В условиях серийного производства главными объектами диспетчерского наблюдения и контроля являются установленные по плану сроки запуска-выпуска партий заготовок и деталей на всех участках производства, состояние складских заделов деталей и заготовок и степень комплектной обеспеченности сборочных единиц в соответствии с графиком. В зависимости от характера серийного производства диспетчерский контроль может осуществляться либо применительно к стандартным графикам межцеховых подач по отдельным цехам и планам-графикам работ производственных участков, либо применительно к установленным на очередной месяц срокам комплектования узлов, обработки деталей и производства заготовок. Так, при использовании системы планирования по заделам основными объектами диспетчерского контроля являются степень укомплектованности изделий, которая устанавливается на основании данных картотеки пропорциональности, и показатель отставания в сутко-позициях, определяемый из графика пропорциональности.
В условиях массового производства диспетчерское наблюдение и контроль осуществляются с помощью суточных и часовых графиков работы над соблюдением установленного такта и нормы заделов на всех стадиях производственного процесса.
Использование комплекса современных технических средств в сочетании с ЭВМ значительно повысили эффективность оперативного управления производством.
В зависимости от специализации, производственной структуры предприятий, масштабов выпуска продукции, принятых систем планирования и других причин состав работ и расчетов в АСУП на каждом предприятии может быть различным.
Независимо от этого некоторые из них по форме, содержанию и методике решения выполняются на всех машиностроительных предприятиях, то есть являются стандартными, другие — только на ряде предприятий. Имеют место и оригинальные решения задач планирования и управления. Конкретное выражение перечисленных выше признаков для одних и тех же задач, но выполняемых на разных предприятиях позволяет выявить степень типизации их решения и тем самым определить по каждой функциональной подсистеме перечень типовых задач, то есть используемых при определенных условиях организации, планирования производства и управления предприятием, и стандартных, для которых эти условия одинаковы на всех предприятиях.
Как конечные, так и промежуточные результаты выполненных работ и расчетов несут свою «функциональную нагрузку», то есть используются для принятия решений по управлению тем или иным объектом, для целей учета, контроля, анализа или служат дополнительной исходной информацией при решении других задач.
Многие из работ и расчетов АСУП, особенно из числа комплексных и сложных задач планирования и управления, включают отдельные элементы, которые многократно используются при решении других задач.
Каждый расчет, как и непосредственно блок, имеет четкое и однозначное определение (название), которое по существу выражает какую-то цель. Например, расчет нормативного размера партии запуска деталей в обработку, формирование программы запуска деталей и т. д. Однако, несмотря на однозначность в названии работ, выполняемых для аналогичных или одинаковых объектов, их методическое решение может быть осуществлено различными способами. Это объясняется многообразием типов производства, разновидностью организации производственных процессов, систем планирования, методов решения задач и т. д.
Система блоков, из которых должны компоноваться АСУП или отдельные подсистемы для различных условий применения, представляет собой по существу набор методик решения задач управления производственно-хозяйственной деятельностью предприятия с программами их реализации на ЭВМ.
В оперативно-производственном планировании особое внимание уделяется автоматизированной системе управления сборочным производством.
Основная задача управления сборкой состоит в определении оптимальной очередности запуска на сборку изделий различных модификаций в условиях различных производственных ситуаций, а также в обеспечении сборки этих модификаций в установленной очередности деталями, узлами, которые должны быть поданы в определенный момент в требуемое место.
Для решения этих задач автоматизированная система управления сборочным производством обеспечивает:
— составление графиков сборки изделия и подборки главных узлов;
— непрерывный учет хода производства по всем этапам главной сборки;
— управление системой подвесных толкающих конвейеров;
— контроль за наличием деталей и узлов на складах;
— своевременную регистрацию отклонений от запланированного ходa производства;
— запрос и выдачу справок о текущем состоянии производства;
— обработку данных и выдачу сопроводительной документации на изделие.
Автоматизированная система управления сборочным производством как самостоятельная система взаимодействует с АСУП. Ежедневно она выдает в АСУП сменно-суточные графики подачи главных узлов, информацию о дефиците узлов и деталей, подаваемых на главный конвейер, и о фактическом выпуске изделий.
Непрерывный учет в процессе сборки изделий ведется по отдельным технологическим переходам, таким, как запуск на сборку, выход со сборочной линии и т. п. Данные по учету вводятся с терминальных устройств. Оперативный учет ведется в разрезе зон, на которые разделены производственные подразделения, в реальном масштабе времени. Управление системой позволяет осуществлять синхронизированную подачу главных узлов в определенные зоны сборочных линий в соответствии с очередностью сборки изделий конкретных наименований.
Система автоматически осуществляет транспортировку, хранение и сортировку всех главных узлов.
Контроль за наличием деталей и узлов на складах и регулирование и подачи в цех ведутся по дефициту. Система составляет и обновляет учетные списки состояния складов, контролирует заделы по минимальному и максимальному уровням.
Контроль за отклонениями, такими, как сборка незапланированных изделий, отклонение от минимального уровня заделов и др., в ходе производства осуществляется системой в реальном масштабе времени. В случае возникновения сбоев информация автоматически выводится оператору системы на телетайп отклонений для принятия экстренных мер по их ликвидации.
Запрос и выдача справок о ходе производства осуществляется в процессе сборки. Выдачу справок о ходе производства система осуществляет в реальном масштабе времени автоматически. Системой предусмотрены локальная обработка данных по управлению главной сборкой и выдача отчетных документов о состоянии:
— производства по технологическим переходам по окончании смены, суток, месяца;
— запасов мелких узлов, деталей и главных узлов.
Значительно упростить работу с информационными ресурсами позволяют возникшие и развивающиеся в результате эволюции гиперсети Интернет-технологии. Для оперативно-производственного планирования и регулирования хода производства особо важное значение имеет осуществляющийся перенос этих технологий на корпоративные сети и сети предприятий и учреждений. Так возникли интрасети и сети по технологии Интернет. В отличие от Интернет, по самой своей природе являющегося средой передачи данных для массового использования, интрасети — системы с ограниченным кругом пользователей (как правило, их пользователи — работники одного предприятия или организации). Позаимствованные у Интернет технологии, их простой и удобный интерфейс делают интрасети весьма перспективными для предприятий, в том числе для целей оперативно-производственного планирования и регулирования производством. Открывающиеся возможности структуризации корпоративных информационных ресурсов и предоставление доступа к ним нужным сотрудникам может привести к существенному росту эффективности работы с информацией. Это в свою очередь повысит эффективность принимаемых решений и эффективность предприятия в целом. Важно, что в пределах предприятия, корпорации, учреждения возникает возможность унификации программного инструментария, что в масштабах глобальной информационной системы практически невозможно.
1.3 Организация оперативного регулирования единичного, серийного и массового производства Единичное производство характеризуется широкой номенклатурой изготавливаемых изделий при единичных и малых разовых объемах выпуска.
Отличительными признаками единичного производства являются:
— практически полная неповторяемость выпуска изделий при их изготовлении отдельными экземплярами или некоторым количеством изделий оригинальной конструкции — например, опытно-экспериментальные производства различных отраслей машиностроения;
— широкая номенклатура деталей и операций, выполняемых на рабочих местах;
— полная нестабильность производственных условий на рабочих местах вследствие воздействия первых двух признаков;
— ограниченный состав нормативной базы, имеющей укрупненный характер;
— значительная сложность организации и планирования производства вследствие большой, постоянно меняющейся номенклатуры деталей, сборочных единиц и изделий;
— более низкие по сравнению с серийным производством технико-экономические показатели.
Эти особенности в определенной степени затрудняют организацию нормальных условий производства и ослабляют технико-организационную базу планирования единичного типа производства. Это проявляется в следующем:
— применение более простой и менее производительной технологической оснастки. Объясняется это тем, что незначительность серии предметов (2−5 штук) заказа или неповторяемость продукции не вызывает необходимости проектирования и изготовления сложной, дорогостоящей, со значительным циклом изготовления оснастки разового пользования;
— укрупнение нормативов времени, используемых для планирования производства. Это объясняется частой сменностью операций, незначительным количеством объектов, нецелесообразностью проведения точных расчетов времени. Обычно применяются опытно-статические нормы;
— ухудшение показателей использования основных фондов;
— многообразие неповторяющейся продукции увеличивает простои оборудования из-за частых его переналадок и времени освоения новых технологических операций.
— частых отклонений от установленных технических условий производства. Это проявляется в несоответствии применяемых материалов, отклонении их от нормальных размеров в связи несовременностью материально-технического снабжения и сложностью обеспечения наиболее дефицитных позиций.
Изготовление продукции в единичном производстве осуществляется по заказам, это и предопределяет методику планирования — так называемый позаказный метод. В объем работ заказа входит не только изготовление самого изделия, но и вся техническая подготовка производства. Основной задачей оперативно-календарного планирования в единичном производстве является одновременное выполнение множества заказов в сроки, предусмотренные договорами. При этом должна быть обеспечена равномерная загрузка всех звеньев производства и, как следствие, рациональное использование оборудования и рабочей силы.
Выполнение заказа можно разделить на ряд этапов: оформление заказа, подготовка производства и собственно изготовление изделия. Примерная технология выполнения этих работ следующая: получив предложение на выполнение заказа, бюро заказов выясняет возможность его исполнения, При наличии такой возможности ставит об этом в известность заказчика и приступает к его оформлению. Процесс оформления заключается в установлении сроков выполнения, определении стоимости заказа и некоторых технических условий. Эти данные затем включаются в проект договора, представляемый на подпись заказчику. Определение указанных выше параметров проекта договора осуществляется на основании запросного листа. Этот лист составляет бюро заказов после решения вопроса о возможности выполнения заказа и направляет в конструкторский отдел. Здесь определяются объемы работ, сроки их выполнения, перечень и нормы расхода материалов и покупных полуфабрикатов. Далее запросный лист проходит технологический, инструментальный отдел и другие службы, каждая из которых устанавливает параметры заказа применительно к своим выполняемым функциям. При разработке этих предварительных данных используются укрупненные нормативы. Основные данные заказа заносятся в специальный журнал, так называемый портфель заказов. Данные являются исходными параметрами для производственного планирования.
Системы оперативно-календарного планирования (ОКП) в единичном производстве в наименьшей степени типизированы и ориентированы на сложившиеся на предприятиях методы организации производства, труда и управления. Тем не менее при всем разнообразии применяемых в оперативно-календарном планировании средств и методов они должны решать три важные задачи:
— разработка календарно-плановых нормативов, регламентирующих ход выполнения заказа;
— планирование технической, организационной, экономической и материальной подготовки производства;
— применение серийных методов организации производства и оперативно-календарного планирования на отдельных участках производства, специализированных деталей и узлов.
Внутрицеховое ОКП характеризуется тем, что задания для производственных участков и рабочих мест по каждому заказу формируются путем выборки из оперативного цехового плана соответствующей номенклатуры с учетом технологических маршрутов изготовления. Кроме того, задания на месяц регламентируют, сроки изготовления ведущих и оригинальных деталей и узлов. Сроки изготовления остальной номенклатуры цеха устанавливаются в порядке текущего распределения в зависимости от загрузки рабочих мест.
Оперативно-календарное планирование в единичном производстве включает следующие плановые расчеты: расчет производственного цикла выполнения заказа и построение объемно-календарного графика выполнения отдельных заказов и сводного по всем заказам; расчет календарных сроков опережений в работе цехов; расчет загрузки оборудования и производственных площадей в планируемом периоде; ежесменный учет выполнения заказов. Данные расчеты представлены на рисунке 2.
Рисунок 2 — Алгоритм оперативно-календарного планирования единичного производства.
Расчет производственного цикла по каждому заказу () начинается с распределения трудоемкости заказа по видам работ и расчета потребного числа рабочих мест () (оборудования):
;
где — трудоемкость данного вида работ по заказу;
— действительный фонд времени работы оборудования.
На основе таких расчетов и с учетом возможного межоперационного пролеживания деталей по каждому заказу формируется объемно-календарный график выполнения заказа.
График строится в порядке, обратном ходу технологического процесса, начиная с испытательного или сборочного цеха. По графику определяют общий цикл изготовления заказа, который сопоставляют с заданным сроком. Для заказов с коротким производственным циклом (менее месяца) и незначительным числом цехов-исполнителей (один-два) объемно-календарный график не составляют.
Расчет календарных сроков опережения в работе цехов необходим для их согласованной бесперебойной работы и для того, чтобы все детали, входящие в данное изделие, поступали на сборку к заданному сроку. Поэтому детали, имеющие более длительный цикл изготовления, запускают в производство раньше, чем другие детали.
Сводный объемно-календарный график выполнения всех заказов, представлен на рисунке 3, необходим для взаимной увязки работ по заказам во времени и для более полного использования оборудования и площадей. При построении сводного объемно-календарного графика может случиться, что сроки выполнения одинаковых работ по разным заказам на одном и том же оборудовании совпадут, и оно оказывается перегруженным, или сроки окончания работ по одному заказу и начала работ по другому на одном и том же оборудовании не совпадут, и это оборудование оказывается недогруженным. В обоих случаях необходимо откорректировать сроки выполнения работ, предусмотренные графиками выполнения отдельных заказов. При этом нужно определить мероприятия по ликвидации узких мест и догрузить недогруженное оборудование. Чтобы сводный объемно-календарный график отвечал перечисленным требованиям, ПДО и ПДБ (планово-диспетчерский отдел и планово-диспетчерский бюро соответственно) основных цехов рассчитывают загрузку оборудования и использования производственных площадей, находя оптимальный вариант использования имеющихся мощностей.
Рисунок 3 — Сводный объемно-календарный график выполнения заказов.
Сводный объемно-календарный график ежемесячно корректируют с учетом данных о выполнении месячной программы основными цехами, состоянии незавершенного производства по заказам, новых заказах, принятых предприятием. Одновременно уточняются номенклатура и объем работ по включенным ранее заказам. Месячная цеховая программа содержит следующие реквизиты:
— наименование и код заказа;
— наименование и код детали (сборочной единицы);
— количество планируемых к выпуску деталей (сборочных единиц);
— сроки запуска-выпуска;
— трудоемкость изготовления единицы продукции и планируемого объема работ.
Цеховая производственная программа служит исходным документом для составления программ производственных участков. Для этого предусмотренные программой цеха работы распределяются по производственным участкам, производятся объемные расчеты для правильного использования мощностей и устранения диспропорций в загрузке оборудования участков.
Основой планово-распределительной работы на смену является сменно-суточный план, в котором задания конкретизируются на каждые сутки и смену для каждого рабочего. Реальность сменных заданий должна обеспечиваться заблаговременной и тщательной оперативной подготовкой производства. В сменные задания включаются только такие работы, для которых подготовлены технологическая документация, оснастка, материалы и заготовки.
Оперативный учет выполнения программы основными цехами в единичном производстве осуществляется по данным выполнения сменно-суточного задания каждым участком. Объектами оперативного учета служат выработка рабочих, движение деталей по операциям, поступление заготовок, простои рабочих, брак, сдача готовой продукции. Учет осуществляется на основе первичной документации, обрабатываемой на ЭВМ с помощью машиночитаемых документов.
Массовое производство характеризуется высоким уровнем концентрации и узкой специализацией предприятия на выпуске небольшой, но относительно устойчивой номенклатуры изделий в больших количествах и в течение длительного времени. Это позволяет специализировать цеха, участки и рабочие места. За каждым рабочим местом закрепляется одна операция, которая выполняется непрерывно без переналадки оборудования. ОУП здесь должно быть нацелено на непрерывный ход технологического процесса в соответствии с заданным на данное время ритмом выпуска готовой продукции. Основной планово-учетной единицей для заготовительных и обрабатывающих цехов является деталь, сборочная единица (ДСЕ), комплект, а для сборочных — готовое изделие в натуральном выражении (штуках). Оперативное управление в массовом производстве основывается на следующих КПН: параметрах поточных линий и сборочного конвейера, размерах внутрилинейных, межлинейных и межцеховых заделов.
В серийном производстве выпускается более широкая номенклатура изделий, в которых имеется постоянная, но не массовая потребность. При этом в течение планового периода изделия выпускаются относительно равномерными сериями. Серия — это количество конструктивно одинаковых изделий, запускаемых в производство одновременно или последовательно, но без перерыва. Запуск изделий сериями через определенные, ритмически повторяющиеся промежутки времени ведет к необходимости согласования во времени последовательности передачи изделий с одного рабочего места на другое. В зависимости от масштабов, номенклатуры продукции, величины серий и частоты их повторяемости, уровня специализации рабочих мест серийное производство подразделяется на крупносерийное, среднесерийное и мелкосерийное.
Крупносерийное производство по своим технико-экономическим параметрам близко к массовому: сравнительно узкая номенклатура изделий, выпускаемых большими, повторяющимися сериями.
Мелкосерийное производство специализируется на выпуске продукции в небольших количествах, но относительно обширной и довольно различной номенклатуры.
Среднесерийное производство сочетает в себе особенности крупносерийного и мелкосерийного типов производства.
Оперативное планирование в серийном производстве играет роль стабилизатора ритмичности выпуска продукции в соответствии с оптимальными партиями запуска деталей в обработку в течение календарного периода при оптимальных величинах незавершенного производства по отдельным видам продукции. Составление оперативно-календарного плана запуска-выпуска деталей для цехов серийного производства — сложная, трудоемкая работа, требующая предварительного глубокого анализа реальных условий производства в каждом цехе, и является одним из наиболее ответственных и основных этапов работы по составлению ОКП. В серийном производстве контролируется номенклатура, количество и сроки выпуска сборочных единиц, ведущих деталей, состояние складских заделов заготовок, деталей, степень комплектной обеспеченности сборочных работ.
Единичный тип производства рассчитан на специализацию выпуска обширной и непостоянной номенклатуры изделий, потребность в которых исчисляется единицами. Это, в основном, предприятия, изготавливающие турбогенераторы, экскаваторы большой мощности, прокатные станы и др.
2. Практическая часть
2.1 Обоснование и расчёты организационно-производственных параметров цеха Исходные данные:
Производственная программа на год — 144 тыс. шт, цех работает в 2 смены. Продолжительность рабочего дня — 8 часов, число рабочих дней в году — 252. Нормы штучного времени на изготовление деталей Коэффициент выполнения норм Кв=1,2.
Средний коэффициент, учитывающий затраты времени на подготовительно-заключительную работу Кпз=1,04.
2.2 Обоснование производственной структуры цеха Под производственной структурой понимается состав цехов и служб предприятия с указанием связей между ними. В данной работе обоснование проводится на примере механического цеха, которое должно включать: определение количества основных участков; выбор формы специализации участков; выбор профиля предметной специализации участков; определение состава вспомогательных участков.
Количество производственных участков определяется исходя из числа рабочих мест в цехе и норм обслуживания рабочих мест одним мастером. Определяется, исходя из формул (2.1)-(2.3).
L=Qp/Qm(2.1)
где L — количество участков; Qp — расчётное число рабочих мест в цехе;
Qm — число рабочих мест, обслуживаемых одним мастером в смену
Qp= ??tшт комп*Кпз*Nгод / (60*Кв*Fрасп)(2.2)
где ?tшт комп — суммарное штучное время на комплект деталей, определённого наименования, применяемых в изделии, мин.;
Кпз — средний коэффициент, учитывающий затраты времени на подготовительно-заключительную работу, принимается для серийного производства от 1,02 до 1,05;
Nгод — годовая программа выпуска изделий;
Кв — средний плановый коэффициент выполнения норм;
Fрасп— располагаемый фонд времени одного рабочего места в плановом периоде, ч.
Fрасп=D*d*c*(1-b/100)(2.3)
где D — число рабочих дней в году;
d — продолжительность смены;
c — сменность работы;
b — средний процент потерь времени на плановые ремонты (принимается от 3% до 8%).
Fрасп= 252*8*2*(1−0,038) = 3878,79 ч.
Qp= 280,94*144 000*1,04/(60*1,2*3878,79) = 150
L = 150/65 = 2,51. Принимаем L=3 участка.
2.3 Расчёт штучного времени комплекта обработки деталей и определение основного технологического маршрута Показатель относительной трудоёмкости детали (Kg) характеризует приближённое число рабочих мест для изготовления детали определённого наименования в планируемом периоде.
Kgi = ?tшт i комп/(Kв*tgi)(2.4)
где tgi — такт выпуска изделий, мин.
tgi = Fрасп/Ng,(2.5)
где Fрасп— располагаемый фонд времени одного рабочего места в плановом периоде, ч;
Ng — годовая программа выпуска изделий, шт.
tgi = 3878,79/144 000 = 1,616 мин.
Правильность расчёта показателей Kgi по всем деталям следует проверить путём сравнения с Ор:
? Kgi = Ор / Кпз = 150/1,04 = 144,859
2.4 Расчёт показателей относительной трудоёмкости деталей и относительной трудоёмкости операций При выборе варианта закрепления деталей за участками суммирование показателей? Kgi происходит по двум признакам: по технологическим маршрутам и по каждому конструктивному типу деталей. Если ни один из признаков суммирования не позволяет сформировать равновеликие участки, то прибегают к одновременному использованию обоих признаков группировки деталей.
Выбор форм организации поточного производства осуществляется в зависимости от показателя массовости (y'mi), который характеризует обезличенное число рабочих мест в среднем для выполнения технологической операции по детали конкретного наименования в планируемом периоде:
y'mi = Kgi / Ко(2.6)
где Kо — количество технологических операций, выполняемых над i-й деталью в данном цехе.
Полученные результаты по каждой детали заносим в таблицу 2.
Также рассчитываем показатели относительной трудоёмкости операций по формуле (2.7):
Ymi = N* tштi /(Kв* tg)(2.7)
где tштi — продолжительность технологической операции по обработке одной детали, мин;
N — число деталей на комплект.
Анализ показателей массовости по группам деталей и операциям позволяет принять решение по организации форм поточного производства. Определение состава вспомогательных и обслуживающих подразделений устанавливается на основе рекомендаций в литературе и опыта передовых отечественных и зарубежных предприятий.
Таблица 2 — Показатель массовости и относительная трудоёмкость обработки деталей
Деталь | Кол-во деталей на изделие | Тшт сумм | Tg | Кв | Kgi | Ko | y'mi | |
32−01 | 15,899 | 1,61 616 | 1,2 | 8,1 979 301 | 0,5 465 287 | |||
32−02 | 11,5 | 1,61 616 | 1,2 | 5,9 296 934 | 0,8 470 991 | |||
32−03 | 6,23 | 1,61 616 | 1,2 | 3,212 347 | 0,6 424 694 | |||
32−04 | 5,606 | 1,61 616 | 1,2 | 2,8 905 966 | 0,4 817 661 | |||
32−06 | 9,298 | 1,61 616 | 1,2 | 4,794 286 | 1,1 985 715 | |||
32−08 | 1,76 | 1,61 616 | 1,2 | 0,9 075 009 | 0,4 537 505 | |||
32−09 | 3,494 | 1,61 616 | 1,2 | 1,8 015 956 | 0,6 005 319 | |||
32−11 | 12,884 | 1,61 616 | 1,2 | 6,6 433 191 | 0,5 536 099 | |||
32−13 | 18,379 | 1,61 616 | 1,2 | 9,4 766 814 | 0,6 317 788 | |||
32−15 | 0,365 | 1,61 616 | 1,2 | 0,1 882 033 | 0,627 344 | |||
32−16 | 3,85 | 1,61 616 | 1,2 | 1,9 851 582 | 0,4 962 896 | |||
32−17 | 34,16 | 1,61 616 | 1,2 | 17,613 768 | 0,9 270 404 | |||
32−19 | 15,42 | 1,61 616 | 1,2 | 7,9 509 455 | 1,3 251 576 | |||
32−20 | 18,522 | 1,61 616 | 1,2 | 9,5 504 158 | 0,6 821 726 | |||
32−21 | 16,415 | 1,61 616 | 1,2 | 8,4 639 928 | 0,7 694 539 | |||
32−22 | 7,62 | 1,61 616 | 1,2 | 3,9 290 664 | 0,4 911 333 | |||
32−26 | 5,081 | 1,61 616 | 1,2 | 2,6 198 932 | 0,5 239 786 | |||
32−23 | 5,946 | 1,61 616 | 1,2 | 3,659 093 | 0,3 065 909 | |||
32−27 | 4,4 | 1,61 616 | 1,2 | 2,2 687 523 | 1,1 343 761 | |||
32−28 | 4,727 | 1,61 616 | 1,2 | 2,4 373 618 | 0,3 481 945 | |||
32−30 | 0,95 | 1,61 616 | 1,2 | 0,4 898 442 | 0,2 449 221 | |||
32−31 | 1,98 | 1,61 616 | 1,2 | 1,209 385 | 0,2 552 346 | |||
32−38 | 6,81 | 1,61 616 | 1,2 | 3,5 114 098 | 0,8 778 524 | |||
32−47 | 5,29 | 1,61 616 | 1,2 | 2,727 659 | 0,5 455 318 | |||
32−48 | 5,58 | 1,61 616 | 1,2 | 2,8 771 904 | 0,4 795 317 | |||
32−49 | 19,549 | 1,61 616 | 1,2 | 10,79 963 | 0,6 299 977 | |||
32−52 | 15,397 | 1,61 616 | 1,2 | 7,9 390 861 | 0,7 939 086 | |||
32−55 | 1,48 | 1,61 616 | 1,2 | 0,7 631 258 | 0,2 543 753 | |||
32−56 | 18,948 | 1,61 616 | 1,2 | 9,7 700 723 | 0,6 978 623 | |||
32−75 | 3,4 | 1,61 616 | 1,2 | 1,7 531 268 | 0,4 382 817 | |||
Всего | 280,94 | 144,85 983 | 18,240 726 | |||||
2.5 Определение профиля предметной специализации производственных участков и количества деталей, закреплённых за участками Предметноподетальная форма специализации основных участков принимается как наиболее прогрессивная и приемлемая для условий проектируемого цеха. Профиль предметной специализации основных участков определяется путём классификации деталей. Основные технологические маршруты приняты из таблицы 2, при этом в каждый из таких маршрутов включены детали, имеющие общие операции. Детали, имеющие общий технологический маршрут, вносятся в таблицы, против соответствующего конструктивного типа с указанием номера детали и показателя Kgi. Суммирование показателей Kgi выполняется по конструктивным типам деталей и по основным технологическим маршрутам. Закрепление деталей за участками осуществляем по конструктивному типу с учётом общности технологических маршрутов.
2.6 Расчёт пооперационного показателя массовости по деталям и выбор форм поточного производства на участках цеха Пооперационный показатель массовости рассчитываем, используя формулу (2.7).
Для выявления возможных форм организации производств поточных линий отбираем наиболее сложные в изготовлении детали с Kgi > 5, с высоким показателем y'mi, и имеющие общий технологический маршрут обработки. Сопоставляем показатели y'mi с условиями организации поточного производства.
По участку № 1 выбираем детали типа крышек 32−11, 32−13, 32−20 и 32−21. Для этих деталей? y'mi= 2,63, можно рекомендовать организацию групповой поточной линии. Эти детали незначительно отличаются по числу операций и изготовляются на однотипных рабочих местах, но отличаются порядком чередования технологических операций. Последнее обстоятельство не позволяет организовать обработку этих деталей на переменно-поточной линии.
Деталь 32−19 также обрабатывается на участке № 1, но она резко отличается от остальных деталей по числу и составу технологических операций. Организация однопредметной линии для обработки этой детали также не рекомендуется, т.к. не выполнено условие целесообразности поточного производства — не по всем операциям ymi>0,75.
На участке № 2 обрабатываются детали 32−01, 32−02, 32−52. Относительная трудоёмкость их обработки? y'mi= 2,19. На этом участке не рекомендуется организация поточного производства, т.к. их технологические процессы разнообразны.
На участке № 3 обрабатываются детали 32−17, 32−49, 32−56. Относительная трудоёмкость их обработки? y'mi= 2,26. Деталь 32−17 может быть рекомендована изготовлении на однопредметной прерывно-поточной линии пои условии укрупнения технологических операций 1 и 2; 3 и 4; 6 и 7; 10 и 13; 8, 11, 12, 15 и 19; 17 и 18 или возможности выполнения этих групп операций на общих рабочих местах с минимальными затратами времени на переналадку оборудования.
Для деталей 32−49 и 32−56 можно предложить организацию группового потока, т.к. по основным технологическим операциям? ymi>0,75. Обработку деталей осуществлять по типовому технологическому процессу.
Заключение
Под регулированием производства понимается централизованное руководство работой всех органов предприятия на основе плана — графика, а также систематического учета и контроля текущего хода производства.
Для наиболее эффективной работы предприятия были выдвинуты принципы рациональной организации производственного процесса: обеспечение ритмичной, согласованной работы всех звеньев производства по единому графику, обеспечение максимальной непрерывности процессов производства, обеспечение максимальной надежности плановых расчетов и минимальной трудоемкости плановых работ, обеспечение достаточной гибкости и маневренности в реализации цели при возникновении различных отклонений от плана, обеспечение непрерывности планового руководства, обеспечение соответствия системы оперативного управления производством типу и характеру конкретного производства, использование прямоточности и пропорциональности, параллельности и гибкости.
В данной работе были рассмотрены некоторые виды оперативного регулирования, а именно: обоснование и расчёты организационно-технических параметров цеха; расчёт и построение оперативно-календарного плана участка серийного производства; расчёт и построение стандарт-плана работы прерывно-поточной линии. А также представлены, рассчитаны графики работы прерывно-поточной линии, число необходимых единиц оборудования, а также величины оборотных, транспортных, технологических и страховых заделов.
1. Ильин А. И. Планирование на предприятии: учебное пособие. — Минск: Новое издание, 2010.
2. Лавров Г. И. Организация и оперативное планирование производства: Учебное пособие. — Тюмень: ТюмГНГУ, 2009.
3. Афитов Э. А. Планирование на предприятии: учеб. пособие / Э. А. Афитов. — 2-е изд., перераб. и доп. — Мн.: Выш. Шк., 2009. — 302 с.
4. Актонец А. В., Белов Н. А., Бухало С. Н. Организация планирования и управление длительностью промышленного предприятия. К.2008г.
5. Золотогоров В. Г. Организация производства и управление предприятием. Учеб. пособие / В. Г. Золотогоров. — Мн.: Книжный Дом, 2009 — 448с.
6. Курочкин А. С. Организация производства., К. э 2008.
7. Кобец Е. А. Планирование на предприятии: учебное пособие. — Таганрог: Изд-во ТРТУ, 2009.
8. Организация производства на предприятии; Учеб.-метод. Комплекс. Н. В. Шинукевич, Е. А. Зубелик, Ю. В. Карпилович. Мн.; Издательство МИУ, 2009. — 151 с.
9. Синица Л. М. Организация производства: Учеб. пособие для студентов вузов. — 2- изд., перераб и доп. — Мн.: УП «ИВЦ Минфина», 2004. — 521 с.
10. Организация производства. Учебно-практическое пособие/ М. Ю. Пасюк, Т. Н. Долинина, А. А. Шабуня. — Мн.: ООО ФУАинформ, 2002. — 76 с.
11. Оперативное управление производством [Электронный ресурс], 2014. Доступ: http://www.center-yf.ru/data/ip/Operativnoe-upravlenie-proizvodstvom.php свободный.
12. Оперативно — производственное планирование на предприятии [Электронный ресурс], 2014. Доступ: http://cased.ru/doc_r-ek1439_cased.html свободный.