Другие работы
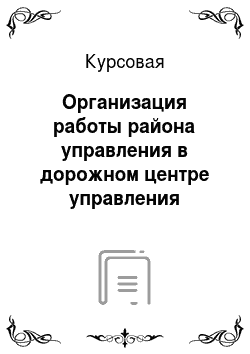
Промышленный транспорт в процессе перевозок взаимодействует с магистральным транспортом и основным производством. В этой связи перевозки, выполняемые на промышленном транспорте, подразделяются на внешние и внутренние. Внешними называются перевозки, осуществляемые с предприятий на сеть железных дорог общего пользования в обратном направлении в вагонах МПС и предприятий, которым разрешён выход…
Курсовая 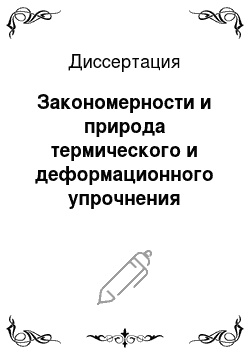
В этой же главе на монокристаллах с разными' ориентировками* осей деформации выполнен анализ влияния состава сплава на механические свойства в случае, когда деформация* осуществляется октаэдрическим скольжением (ориентация) и кубическим скольжением (ориентация). Проведено детальное сравнение кривых течения, коэффициентов деформационного упрочнения и температурных зависимостей предела текучести…
Диссертация 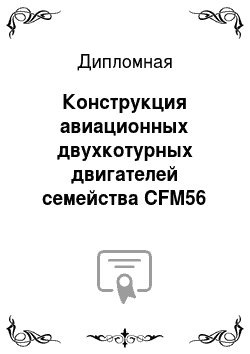
Под воздействием факторов научно-технического прогресса: морального и физического устаревания АД; потребности в более экономичных, бесшумных и надёжных двигателях с малым уровнем выбросов вредных веществ, конструкция двигателя в процессе эволюции претерпевала некоторые изменения. В первую очередь эти изменения обуславливались потребностями рынка и заключались в том, что двигатели рассчитывались…
Дипломная 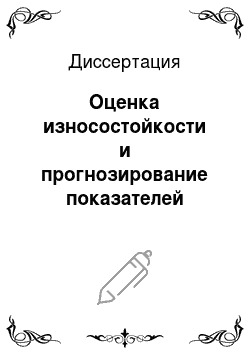
Качество текстильной продукции закладывается на стадии ее проектирования и должно обеспечиваться при ее производстве. Но прежде чем проектировать продукцию, необходимо точно знать какими свойствами она должна обладать. Умение правильно и объективно измерять, оценивать и контролировать показатели качества дает возможность совершенствовать качество текстильных материалов. Поэтому, комплексная…
Диссертация 
Далее бутылки направляются на этикетировочный автомат «KRONES STARMATIC» для наклеивания этикеток. Традиционно для пива этикетки на бутылке три — это лицевая (главная) этикетка, контрэтикетка и кольеретка. На лицевой этикетке обычно печатается оригинальный рисунок, характерный для производителя и марки пива. Основные тона зависят от того светлое пиво или тёмное (золотые, красные и более тёмные…
Реферат 
Основными направлениями экономического и социального развития СССР на I98I-I985 года и на период до 1990 года, принятыми на ХХУ1 съезде КПСС /I/, предусматривается: «…обеспечить рост выпуска машин и агрегатов большой единичной мощности…», «обеспечить в 1985 году по сравнению с 1980 годом экономию топливно-энергетических ресурсов в народном хозяйстве в количестве 160−170 млн. тонн условного…
Диссертация 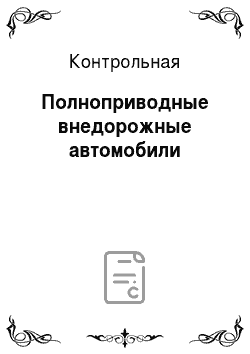
ЛуАЗ не так примитивен, как может показаться на первый взгляд. Взять хотя бы его кузов — классический кабриолет (если снять верхние надставки дверей), а не общепринятый в настоящее время ландо с тентованной лишь задней частью салона. Такие настоящие кабриолеты — удел в основном рамных джипов. Между тем кузов ЛуАЗа нельзя назвать классически рамным. Он скорее полунесущий, функцию рамы в нем…
Контрольная 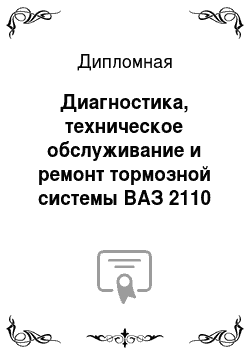
Вакуумный усилитель. Резиновая диафрагма вместе с корпусом клапана делят полость вакуумного усилителя на две камеры: вакуумную, А и атмосферную В. Камера, А соединяется с впускной трубой двигателя через обратный клапан наконечника и шланг. Корпус клапана пластмассовый. На выходе из крышки он уплотняется гофрированным защитным чехлом. В корпусе клапана размещен шток привода главного цилиндра…
Дипломная 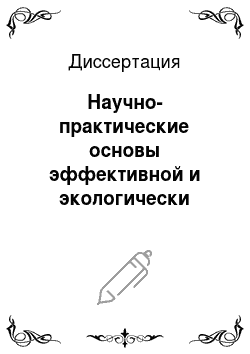
Исследования проводились на кафедре технологии и техники бурения скважин СПГГИ на основе ряда госбюджетных и хоздоговорных тем и грантов государственных и общественных организаций, в частности, Гранта Государственного комитета РФ по делам науки и высшей школы «Оптимизация процесса бурения скважин во льду колонковыми электромеханическими снарядами на грузонесущем кабеле» (код темы по ГАСНТИ…
Диссертация 
Теоретически установлено, что комбинированный рабочий орган для выполнения энергосберегающего технологического процесса, должен состоять из части корпуса плуга, у которого заменена полевая доска на левый лемех стрельчатой лапы. Удельное тяговое сопротивление комбинированного рабочего органа по сравнению с корпусом плуга снижается на 24,5−29,2%, при этом ширина захвата лемеха стрельчатой лапы…
Диссертация 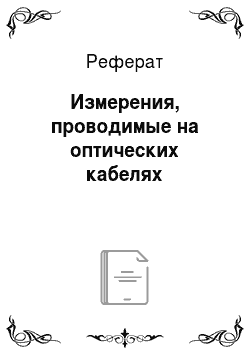
Некоторые изготовители контрольного оборудования для кабельных систем выпускают приставки к своим кабельным сканерам, позволяющие тестировать волоконно-оптические кабели. При подключении приставки контроллер сканера автоматически опознает ее присутствие и запускает соответствующую программу. Результаты измерения уровня оптического сигнала выводятся на штатный индикатор основного прибора сканера…
Реферат 
Я принимал участие в ремонте помещений гончарного цеха. Под руководством опытного штукатура, мной проводились работы по оштукатуриванию помещений, а также малярные работы. Отделочные работы один из важнейших процессов в строительстве здания. Они являются одними из самых трудоемких и материалоемких процессов. Сначала мы занимались тем, что отдирали от стен с помощью шпателей и мастерков старую…
Реферат 
Для подвески проводов ЭУФ рекомендуется принимать типовой кронштейн КФД или КФДС. Провод ДПР, как наиболее легкий, расположен с краю. УП и ЭП имеют одинаковое натяжение, так как выполняются из проводов одной марки, и смещены по горизонтали и вертикали таким образом чтобы выдержать между ними расстояние 600 — 800 мм. При таком расположение проводов УП и ЭП удобно присоединять электрические…
Дипломная 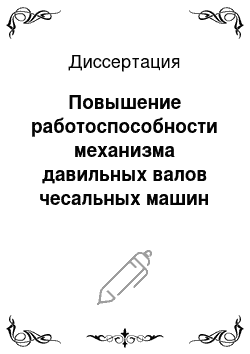
РЕАЛИЗАЦИЯ РЕЗУЛЬТАТОВ РАБОТЫ. С целью определения эффективности использования чесальных машин, оснащенных механизмами давильных валов повыпенной работоспособности были проведены технологические испытания 8 машин ЧВД-4 в условиях Ореховского хлопчатобумажного комбината и Костромской хлопкопрядильной фабрики «Знамя труда». В результате было установлено, что использование механизма давильных валов…
Диссертация 
В научной литературе, посвященной проблемам обеспечения безопасности дорожного движения, признан целесообразным и апробированным подход, при котором весь комплекс мероприятий по предупреждению ДТП разбивается на три подкомплекса. Первый из них охватывает деятельность, связанную с подготовкой людей к участию в дорожном движении и повышением их роли в обеспечении его безопасности. Второй…
Курсовая