
Оценим потребляемый ток на основании рассчитанной мощности потребления, где — напряжение питания;- косинус угла потерь. На основании рассчитанного тока выбираем кабель ВВГ (3*1,5 мм2) который допускает ток до 25 АЗАКЛЮЧЕНИЕВ ходе выполнения данной квалификационной работы была разработана система видеонаблюдения для заданного объекта. Также в ходе выполнения дипломного проекта была произведена…
Курсовая 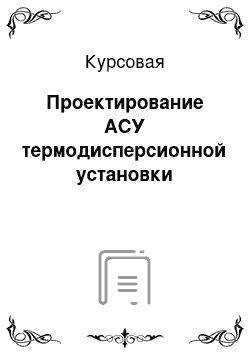
Также принято различать критерии и виды эффективности. Например, для оценки технической эффективности от внедрения АСУ сравнивают, как изменился объем выпуска продуктов за конкретный временной промежуток и вычисляют темп прироста объема выпускаемой продукции. Результаты выражают как в стоимостном, так и в натуральном значении. Также к показателям эффективности АСУ относят критерий потребительской…
Курсовая