Монтаж аппаратов и оборудования для нефтяной и газовой промышленности
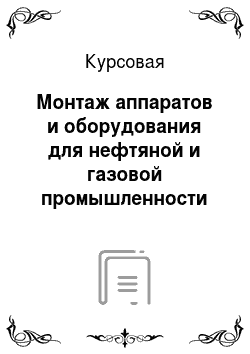
Определение положения центра тяжести поднимаемого аппарата Момент силы тяжести всего аппарата, действующий в центре его тяжести, равен сумме моментов всех частей аппарата относительно точки, А где х и xi — расстояния от центра тяжести соответственно аппарата и отдельных частей аппарата до точки А, м; Масса якоря будет равна Рисунок 4 — Общий вид якорей Список используемых источников такелажная… Читать ещё >
Монтаж аппаратов и оборудования для нефтяной и газовой промышленности (реферат, курсовая, диплом, контрольная)
Содержание Описание метода подъема аппарата Определение положения центра тяжести поднимаемого аппарата Выбор способа строповки Графический метод расчет усилий в основных элементах такелажной оснастки Выбор такелажных средств по максимальным нагрузкам Выбор мачты и ее характеристика Выбор строповых устройств Выбор блоков и каната грузовых полиспастов Выбор блоков полиспаста и каната дотягивающего устройства Выбор тормозного каната, блоков полиспаста и лебедки Выбор каната для расчалок Выбор якорей Список используемой литературы Описание метода подъема аппарата При монтаже аппарат закрепляют в поворотном шарнире, установленном рядом с фундаментом, и в процессе всего монтажа аппарат не отрывают от земли. Мачту обычно устанавливают в плоскости подъема аппарата. По такой схеме осуществляют подъем как одиночных, так и группы рядом стоящих полностью оснащенных и изолированных аппаратов. Иногда в начальный период подъема аппарата мачту устанавливают с наклоном в сторону поднимаемого аппарата на угол около 15°. Тогда конечную стадию подъема аппарата осуществляют путем поворота мачты в вертикальное положение за заднюю расчалку, выполненную в данном случае в виде полиспаста.
Для снижения нагрузки на мачту применяют также другую схему установки ее по отношению к поднимаемому аппарату. По этой схеме мачту устанавливают рядом с аппаратом между шарниром и центром тяжести аппарата и, кроме того, наклоняют так, чтобы ее вершина расположилась в плоскости подъема аппарата. При такой схеме аппарат нельзя поднять мачтой в положение неустойчивого равновесия за один прием. Поэтому мачтой аппарат поднимают на угол 50—70°, а затем дотягивающими средствами доводят до положения неустойчивого равновесия. Иногда аппарат доводят до положения неустойчивого равновесия наклоном мачты за расчалку.
Определение положения центра тяжести поднимаемого аппарата Момент силы тяжести всего аппарата, действующий в центре его тяжести, равен сумме моментов всех частей аппарата относительно точки, А где х и xi — расстояния от центра тяжести соответственно аппарата и отдельных частей аппарата до точки А, м;
mi — масса отдельной части аппарата, кг;
т — общая масса аппарата, кг.
Тогда положение центра тяжести аппарата находится по формуле Разделим аппарат на девять частей:
верхнее полусферическое днище, первая обечайка, вторая обечайка, третья обечайка, четвертая обечайка, пятая обечайка, нижнее полусферическое днище, опорная обечайка, внутренние устройства и остальные детали аппарата.
Для каждой части найдем массу и определим расстояние между точкой, А и центром тяжести.
В силу симметричности аппарата допустим, что центры тяжести и колонны, и ее составных частей расположены на оси симметрии, поэтому для определения центров тяжести достаточно определить только их координату по оси Ох.
Рисунок 1 — Размеры аппарата.
Верхнее полусферическое днище.
V1 =, где Rвн и Rн — соответственно внутренний и наружной диаметры днища, равные соответственно внутреннему и наружному диаметру обечайки, Rвн = 0,4 м, Rн = 0,5 м.
V1 = = 0,1278 м³;
m1 = с • V1 = 7850 • 0,1278 = 1002,90 кг;
xG1 = = = 0,1909 м.
x1 = xG1 + l1 = 0,1909 + 14,95 = 15,14 м.
где l1 — расстояние от точки, А до верхнего полусферического днища,.
l1 = 14,95 м Первая обечайка.
V2 =, где h2 — высота обечайки, h2 = 2,7 м.
V2 = = 0,763 м³;
m2 = с • V2 = 7850 • 0,848 = 5989,6 кг;
xG2 = = = 1,35 м;
x2 = xG2 + l2 = 1,35+1,4 = 2,75 м.
где l2 — расстояние от точки, А до обечайки,.
l2 = 1,4 м Вторая обечайка.
V3 =, где h3 — высота обечайки, h3 = 2,7 м.
V3 = = 0,763 м³;
M3 = с • V3 = 7850 • 0,848 = 5989,6 кг;
xG3 = = = 1,35 м;
x3 = xG3 + l3 = 1,35+4,1 = 5,45 м.
где l3 — расстояние от точки, А до обечайки,.
l3 = 4,1 м.
Третья обечайка.
V4 =, где h4 — высота обечайки, h4 = 2,7 м.
V4 = = 0,763 м³;
m4 = с • V4 = 7850 • 0,848 = 5989,6 кг;
xG4 = = = 1,35 м;
x4 = xG4 + l4 = 1,35+6,8 = 8,05 м.
где l4 — расстояние от точки, А до обечайки,.
l4 = 6,8 м.
Четвертая обечайка.
V5 =, где h5 — высота обечайки, h5 = 2,7 м.
V5 = = 0,763 м³;
m5 = с • V5 = 7850 • 0,848 = 5989,6 кг;
xG5 = = = 1,35 м;
x5 = xG5 + l5 = 1,35+9,5 = 10,85 м.
где l5 — расстояние от точки, А до обечайки,.
l5 = 9,5 м.
Пятая обечайка.
V6 =, где h6 — высота обечайки, h6 = 2,7 м.
V6 = = 0,763 м³;
m6 = с • V6 = 7850 • 0,848 = 5989,6 кг;
xG6 = = = 1,35 м;
x6 = xG6 + l6 = 1,35+12,2 = 13,55 м.
где l6 — расстояние от точки, А до обечайки,.
l6 = 12,2 м.
Нижнее полусферическое днище.
V7 = 0,1278 м³.
m7 = 1002,90 кг;
xG7 = xG1 = 0,1909 м;
x7 = l2 — xG7 = 1,4 — 0,1909 = 1,21 м.
Опорная обечайка.
V8 =, где Rвн8 и Rн8 — соответственно внутренний и наружной диаметры опоры, Rвн8 = 0,5 м, Rн8 = 0,4 м.
h8 — высота опорной обечайки, h8 = 1,4 м.
V8 = = 0,396 м³;
m8 = с • V8 = 7850 • 0,396 = 3107,35 кг;
xG8 = x8= = = 0,7 м;
Внутренние устройства и остальные детали аппарата.
m9 = = (6658,6*5)/2 = 16 646,5 кг;
Допустим, что внутренние устройство и остальные детали аппарата распределены по длине корпуса равномерно. Тогда центр тяжести совокупности внутренних устройств и остальных деталей аппарата совпадает с центром тяжести всего корпуса, т. е.
x9 ==8,15 м;
m=29 947,5+1002,9+1002,9+3107,35+16 646,5=51 706,15.
x =.
= 7,564 м Выбор способа строповки Центр тяжести находится выше середины на 136 мм. L — расстояние от основания аппарата до места строповки. H — высота мачты. Lя — расстояние от основания до якоря рабочей расчалки. x — расстояние от основания до центра тяжести колонны. L/x = 1,3…2. Выберем место строповки сверху аппарата. L = 15,4 м, учитывая высоту колонны (высота 15,4 м) и фундамента (высота 1 м), выберем мачты высотой H = 24 м, с грузоподъемностью 50 т. При подъеме аппарата наклоним мачту на 150, что допускается без учета снижения грузоподъемности мачты. Примем Lя = 50 м, чтобы угол между вантой и мачтой был равен примерно 600.
Графический метод расчета усилий в основных элементах такелажных оснастки Основные усилия в элементах такелажной оснастки.
Rв — максимальное усилие, возникающие в вантах, поддерживающих мачту. Rм — усилие в мачте, Rп — усилие в грузовом полиспасте, Rш — реакция в шарнире, Rт — усилие оттяжки, при выведении колонны в вертикальное положение, Rд — усилие в дотягивающем канате.
Для определения основных усилий составим рабочие схемы подъема колонны в восьми различных положениях в масштабе 1:0,5 и расставим все вектора сил, действующих на данной схеме.
Начальное положение. Мачты наклонены на 15°.
Аппарат поднят на 18°.
Аппарат поднят на 36°.
Аппарат поднят на 54°.
Аппарат поднят на 72°.
Продолжение подъема мачтами приведет к выравниванию аппарата из шарнира. Дальнейший подъем аппарата будем осуществлять посредством дотяжки лебедкой. Это также обусловлено габаритными размерами полиспастов в стянутом состоянии и балансирной траверсы. Застропим дотягивающий канат за балансирную траверсу. Расположим лебедку дотягивающего устройства за якоря расчалок мачт.
Рассчитаем угол, при котором аппарат займет положение неустойчивого равновесия а.
х — расстояние от основания до центра тяжести колонны,.
x = 7,564 м;
r — срединный радиус колонны,.
r = 1,0 м;
tg (900 — б) = r/ x = 1,0/7,564 = 0,1322.
arctg (900 — б) = 7,530.
б = 82,470.
Rш=G=427,4 кН Усилие в тормозном канате рассчитаем из уравнения крутящих моментов относительно шарнира кН.
Занесем полученные выше силовые факторы в таблицу.
Таблица 1.
№ положения. | RП. | RШ. | RВ. | RМ. | RД. | RТ. | |
232,18. | 242,82. | 195,66. | 294,78. | ; | ; | ||
199,28. | 274,10. | 179,76. | 251,50. | ; | ; | ||
163,70. | 289,12. | 148,40. | 206,46. | ; | ; | ||
135,64. | 307,92. | 118,98. | 176,96. | ; | ; | ||
142,98. | 286,06. | 24,92. | 157,02. | ; | |||
; | 446,38. | ; | ; | 60,46. | ; | ||
; | 427,40. | ; | ; | 0,00. | 0,00. | ||
; | ; | ; | ; | 32,63. | |||
Выбор такелажных средств по максимальным нагрузкам Выбор мачты и ее характеристики Выберем мачту по максимальным усилиям, действующем в грузовых полиспастах.
Rn = 232,18 кН, учитывая коэффициент динамичности.
kп = 1,1; где kп — коэффициент перегрузки.
kд1 = 1,1; где kд1 — динамический коэффициент, учитывающий использование грузовых полиспастов.
Rn =232,18•1,1= 255,39 кН. Выбираем решетчатые мачты постоянного сечения.
Таблица 2 — Характеристики мачты.
Грузоподъемность, т. | ||
Высота, м. | ||
Высота до места крепления полиспаста, м. | 23,1. | |
Число секций. | ||
Масса мачты, т. | ||
Выбор строповых устройств Строповку аппарата осуществляем путем протягивания монтажного стропа через два технологических штуцера, расположенных на верхнем полусферическом днище. Во избежание излома стропа об острые края горловин штуцеров, предварительно пропускаем его через патрубок, которому предадим необходимую форму. Концы патрубка разрежем на лепестки и отогнем их, чтобы сгладить острые грани.
Выбираем штуцер 18 по ГОСТ 141 185.
диаметр аппарата — 1,0 м;
толщина стенки аппарата — 10 мм;
наружный диаметр штуцера — 273 мм;
длина штуцера — 115 мм;
толщина стенки штуцера — 11 мм;
масса штуцера — 33,9 кг.
Так как толщина стенки аппарата меньше наименьшей толщины, не требующей усиления в месте приварки монтажного штуцера, то требуется применение монтажных листов.
Выбираем подкладной лист 800 по ГОСТ 14 114–85.
диаметр аппарата — 1,0 м;
диаметр листа — d+500 = 273+500 = 773 мм;
толщина листа — 11 мм;
Найдем разрывное усилие действующее на стропы:
R = k3 • Rп = 5 • 255,39 = 1276,99 кН;
где k3 = 5,0 — коэфициент запаса.
Строповку аппарата осуществляем путем протягивания монтажного стропа через два технологических штуцера, расположенных на верхнем полусферическом днище. Во избежание излома стропа об острые края горловин штуцеров, предварительно пропускаем его через патрубок, которому предадим необходимую форму. Концы патрубка разрежем на лепестки и отогнем их, чтобы сгладить острые грани.
С учетом максимальной и разрывного усилия действующего на стропы и выбираем схему строповки и стропы.
В виду больших значений нагрузки и разрывного усилия при строповке сделаем четыре петли, две их них на конце строповочного троса.
По разрывному усилию, действующему на один трос, подбираем канат.
кН Выбираем канат типа ЛК-Р0 конструкции 6×19(1+9+9)+1 о.с. ГОСТ 7668–80:
маркировочная группа — 1470 МПа, диаметр каната d— 22 мм, ориентировочная масса 1000 м смазанного каната — 1830 кг, разрывное усилие — 222,5 кН.
Рисунок 2 — Строповые устройства (вид строповки и канат).
Посчитаем число ветвей каната в стропе:
n = = 5,73.
Принимаем число ветвей каната в стропе п ~ 6.
Строп зацепим за балансирную траверсу, которую необходимо предварительно рассчитать.
Зададимся длиной траверсы l = 1,6 м. С одной стороны на траверсу действует нагрузка от строп, с другой — от двух грузовых полиспастов.
Максимальный изгибающий момент от силовых факторов находится в центре траверсы:
Mmax = 92,87 кН•м Допускаемое напряжение для прокатной стали при коэффициенте запаса прочности Определим осевой момент сопротивления сечения:
Wx = = = 580,44•10−6 м3.
По значению Wx из сортамента равнополочных двутавров по ГОСТ 8239–89 выберем двутавр № 33, имеющий следующие геометрические параметры:
Wx = 597 м³.
F = 53,8 см².
h = 33 см Выбор блоков и каната грузовых полиспастов Блок выбираем в соответствии с максимальным расчетным усилием действующим на полиспаст Rn = 232,18 кН. Ввиду деформаций каната в процессе нагружения, выберем блок грузового полиспаста без учета коэффициента динамичности.
Выберем монтажный полиспастный блок БМ-50 со следующими характеристиками:
грузоподъемность — 50 т;
число роликов — 5;
диаметр роликов — 350 мм;
диаметр каната — 22 мм;
масса —336 кг.
Рисунок 3 — Полиспастный блок.
Найдем усилие в сбегающей ветви полиспаста где — КПД подшипника скольжения;
a — количество рабочих ветвей полсипаста; при сбегании ходового конца троса с неподвижного блока полиспаста.
— число роликов в неподвижном блоке полиспаста, кН Рассчитаем тяговое усилие на лебедке Определим длину каната, определяющую канатоемкость лебедки при сокращении полиспаста в процессе подняти аппарата где a — количество рабочих ветвей полиспаста,.
l — разность расстояний между блоками полиспаста в начальный и конечный момент времени подъема аппарата,.
n — число роликов в полиспасте,.
d — диаметр ролика полиспаста, м.
По величине тягового усилия и канатоемкости, выберем лебедку ЛМ-3,2/250, имеющую следующие характеристики:
тяговое усилие — 32 кН, канатоемкость — 250 м, скорость навивки — 0,28 м/с, диаметр каната — 18 мм, масса — 1,2 т.
Рассчитаем разрывное усилие в грузовом канате при коэффициенте запаса прочности k3 = 5.
R = k3 • T = 5 • 33,67 = 168,35 кН Выбираем канат типа ЛК-3 конструкции 6×25 (1+6; 6+12)+7><7 (1+6) по ГОСТ 7667–80:
маркировочная группа — 1570 МПа, диаметр каната — 20 мм, ориентировочная масса 1000 м смазанного каната — 1520 кг, разрывное усилие — 197,5 кН.
Выбор блоков полиспаста и каната дотягивающего устройства.
Блок выбираем в соответствии с максимальным расчетным усилием, действующим на полиспаст.
Rд = 60,46 кН Выберем трехрольный блок БМ-10 со следующими характеристиками:
грузоподъемность — 100 кН, число роликов — 2,.
диаметр роликов — 300 мм, диаметр каната— 17,5 мм, масса— 91 кг.
Найдем усилие в сбегающей ветви полиспаста.
S0 =.
пп = 2, а = 2•2 = 4,.
S0 = = 15,89 кН Рассчитаем тяговое усилие на лебедке Т = 1,3 • S0 = 1,3 • 15,89 = 20,66 кН, Определим длину каната, определяющую канатоемкость лебедки при сокращении полиспаста в процессе дотяжки.
N = a•l+n = 6•4,2+6• = 28 м По величине тягового усилия и канатоемкости, выберем лебедку ЛМЦ-3, имеющую следующие характеристики:
тяговое усилие — 30 кН;
канатоемкость — 250 м;
скорость навивки — 0,18 м/с;
диаметр каната — 17,5 мм;
масса — 960 кг.
Рассчитаем разрывное усилие в дотягивающем канате при k3 = 5.
R = k3 • T = 5 • 20,66 = 103,3 кН Выбираем канат типа ЛК-РО конструкции 6×36 (1+1+7/7+14)+1 о.с. ГОСТ 7668–80:
маркировочная группа — 1570 МПа, диаметр каната d — 15,5 мм, ориентировочная масса 1000 м смазанного каната — 812 кг, разрывное усилие — 104,5 кН.
Выбор тормозного каната, блоков полиспаста и лебедки Блок выбираем в соответствии с максимальным расчетным усилием, действующем в тормозном полиспасте кН.
Ввиду того, что максимальное усилие в тормозной оттяжке не велико, использование тормозного полиспаста не целесообразно.
Подбираем лебедку по тяговому усилию и канатоемкости кН.
Т.к. не используется полиспаст, то длина каната зависит от расстояния, на котором находится лебедка от аппарата. Из этого следует, что значением канатоемкости лебедки можно пренебречь.
Выберем лебедку ЛМ-5, имеющую следующие характеристики:
тяговое усилие — 50 кН;
канатоемкость — 250 м;
скорость навивки — 0,29 м/с;
диаметр каната — 22,5 мм;
масса — 1500 кг.
Рассчитаем разрывное усилие в дотягивающем канате при.
кН.
Возьмем канат типа ЛК-Р0 конструкции 6×36 (1+1+7/7+14)+1 о.с. ГОСТ 7668–80:
маркировочная группа — 1770 МПа,.
диаметр каната d — 20 мм, ориентировочная масса 1000 м смазанного каната — 1520 кг, разрывное усилие -215 кН.
Выбор каната для расчалок Рассчитаем разрывное усилие в дотягивающем канате при k3 = 3,5.
R = k3 • Rв = 3,5 • 195,66 = 684,81 кН Выбираем канат типа ЛК-РО конструкции 6*36(1+7+7/7+14)+1 о.с. ГОСТ 7668–80:
маркировочная группа— I960 МПа,.
диаметр каната d— 34,5 мм, ориентировочная масса 1000 м смазанного каната — 4550 кг,.
разрывное усилие — 700 кН.
Выбор якорей Максимальная нагрузка на расчалку RB = 195,66 кН. Расчетная нагрузка на якорь с учетом коэффициента динамичности kд = 1,3.
R = k3 • Rв = 1,3 • 195,66 = 254,36 кН Выбираем полузаглубленный якорь. Для него принимаем 8 бетонных блоков, размерами 0,9Ч0,9 Ч4 м, и массой 7,5 т каждый.
Масса якоря будет равна Рисунок 4 — Общий вид якорей Список используемых источников такелажная оснастка полиспаст канат Молоканов Ю. К., Харас З. Б. Монтаж аппаратов и оборудования для нефтяной и газовой промышленности. Учебник для ВУЗов. — Изд. 2-е, перераб. и доп. М., Недра, 1982, 391 с.
Косьмин В. Д. Учебное пособие для ВУЗов. Монтажные средства и приспособления. Под редакцией профессора А. И. Владимирова — М.: отдел оперативной полиграфии РГУ нефти и газа им. И. М. Губкина, 2005. —119 с.