Проектирование привода ленточного конвейера
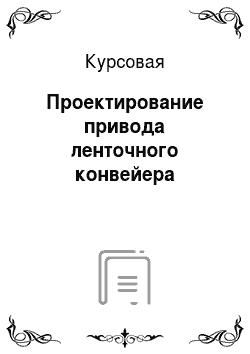
Основная цель курсового проекта по деталям машин — приобретение студентом навыков проектирования. Работая над проектом, студент выполняет расчёты, учится рациональному выбору материалов и форм деталей, стремится обеспечить их высокую экономичность, надёжность и долговечность. Приобретённый студентом опыт является основой для выполнения им курсовых проектов по специальным дисциплинам и для… Читать ещё >
Проектирование привода ленточного конвейера (реферат, курсовая, диплом, контрольная)
Курсовое проектирование по дисциплине «Детали машин»
Тема:
«Проектирование привода ленточного конвейера»
Введение
Основная цель курсового проекта по деталям машин — приобретение студентом навыков проектирования. Работая над проектом, студент выполняет расчёты, учится рациональному выбору материалов и форм деталей, стремится обеспечить их высокую экономичность, надёжность и долговечность. Приобретённый студентом опыт является основой для выполнения им курсовых проектов по специальным дисциплинам и для дипломного проектирования, а так же всей дальнейшей конструкторской работы.
Проектируемый привод ленточного конвейера состоит из электродвигателя марки 4A100L8У3 (Pд=3,0 кВт;Nд=710 мин), редуктора коническо-цилиндрического двухступенчатого, барабана. Передача крутящего момента от электродвигателя на редуктор осуществляется с помощью муфты МУВП (радиальное смещение 0,3 мм, угловое 0,8). Крутящий момент от редуктора на приводной вал передаётся с помощью жёстко-компенсирующей муфта (ГОСТ 5006−55).
1. Энергетический и кинематический расчет привода
Мощность, потребляемую конвейером, по ф. стр. 5 [1]:
Pp=FtV=3,10,8=2,48 кВт,
где Ft — тяговое усилие на барабане, кН;
V — окружная скорость
Мощность, потребляемая электродвигателем:
Pэп=Рр/=2,48/0,879=2,821 кВт,
где — общий К.П.Д. привода:
=124324=0,980,99540,920,995=0,879
где пк, м, кп, цп — КПД соответственно подшипников качения, муфты, конической и цилиндрической зубчатой передач.
Определяем частоту вращения приводного вала:
nр=60000V/(D)=600 000,8/(3,14 225)=67,9 мин-1.
Определяем желаемую частоту вращения электродвигателя по ф. стр. 6 [1]:
nэж=nрU0=67,9*10=679 мин-1,
где U0 — общее ориентировочное передаточное число привода, табл. 5.6 [4],
U0=UбпоUтпо=2,54=10,
где Uбпо, Uтпо — ориентировочные передаточные числа соответственно быстроходной и тихоходной передач из табл. 2.
Исходя из вычисленных значений Рэп и nэж по ГОСТ 28 330–89 выбираем электродвигатель 4А100L8У3 с синхронной частотой вращения nэдс=710 мин-1 и мощностью Рэд=3,0 кВт.
Определяем передаточное число привода:
U0=nэда/np=710/67,9=10,45.
Разбиваем U0 на передаточные числа:
Uтп=U0/Uбп=10,45/2,5=4
где Uбп=2.5 — передаточное число быстроходной передачи;
Определяем частоты вращения валов стр. 11 [1]:
n1=710 мин-1,
n2=n1/Uбп=710/2.5=284 мин-1,
n3=n2/Uтп=284/4=71 мин-1,
Определяем мощности, передаваемые валами по ф. стр. 11 [1]:
Р1=Рэпм =2,80.995=2.786 кВт;
Р2= Рэп к.ппкм=2.783*0.995*0,995*0,95=2.633 кВт;
Р3=Р2к.п=2.633*0.98=2.58 кВт;
Определяем угловые скорости валов привода по ф. cтр. 11[1]:
1=n1/30=3,14 710/30=74.35 с-1;
2=n2/30=3,14 284/30=29.74 с-1;
3=n3/30=3,1471/30=7.43 с-1.
Определяем крутящие моменты на валах привода по:
Т1=Р1/1=2786/74.35=37.47 Нм;
Т2=Р2/2=2633/29.74=88.53 Нм;
Т3=Р3/3=2580/7.43=347.24 Нм;
Т1 | Т2 | Т3 | ||||
74.35 с-1 | 29.74 с-1 | 7.43 с-1 | 37.47 Нм | 88.53 Нм | 347.24 Нм | |
2. Выбор материала и определение допускаемых напряжений для зубчатых передач
Желая получить сравнительно небольшие габариты и невысокую стоимость редуктора, выбираем для изготовления шестерен и колёс сравнительно недорогую легированную сталь 40Х. По таблице 8.8 назначаем термообработку: для шестерен — азотирование поверхности 50…59 HRC при твёрдости сердцевины 26…30 HRC, ,;для колеса — улучшение 230…260 HB,.
Определяем допускаемые контактные напряжения
Для колёс обеих ступеней по табл. 8.9 (с. 168, [2]):
мПа
для шестерни обеих ступеней
Коэффициент безопасности
Число циклов напряжений для колеса второй ступени, по формуле (8.65,[2]), при с=1:
=60*1*71*10 416=4,4*
Здесь n-частота вращения выходного вала,
=5*365*0,29*24*0,82=10 416 ч-срок службы передачи.
По графику (рис. 8.40[2]), для 245HB =1.5*, для 50…59 HRC =.
По таблице (8.10[2]), =0,25. По формуле (8.64[2]), для колеса второй ступени:
=*=0,25*4,4*=1,7*.
Сравнивая и, отмечаем, что для колёс второй ступени >. Так как все другие колёса вращаются быстрей, то аналогичным расчётом получим и для них >. При этом для всех колёс передачи =1.
Допускаемые контактные напряжения определяем по формуле (8.55[2]),
Для колёс обеих ступеней =550/1.1=509 МПа
Для шестерней =1050/1.2=875 МПа.
Допускаемое контактное напряжение для обеих ступеней у которых H1>350 HB, а H2<350 HB, по формуле (8.56[2]),
=(875+509)/2=692 МПа,
но не более чем 1.25=1.25*509=636МПа. Принимаем =636 МПа.
Допускаемые напряжения изгиба
По таблице 8.9[2] для колёс обеих ступеней
=1.8HB=1.8*240=432МПа;
для шестерней
=12*HRC + 300=12*28+300=636 МПа.
Определяем по формуле (8.67[2]),
где — предел выносливости зубьев
SF — коэффициент безопасности
KFL — коэффициент долговечности
KFC — коэффициент учитывающий влияние двустороннего приложения нагрузки.
KFС=1 т.к. нагрузка односторонняя.
число циклов (рекомендуется для всех сталей)
=0,14*1,77*=2.4*
=0.14
т.к., то KFL=1
По таблице 8.9[2] SF =1.75.
Допускаемые напряжения изгиба:
для шестерни =636/1.75=363 МПа;
для колеса =247 МПа.
3. Расчет тихоходной зубчатой передачи
3.1 Проектный расчет передачи
Межосевое расстояние передачи, ф. (8.13 [2])
=0.85(4+1) =125
ba =0.4- коэффициент ширины относительно межосевого расстояния, табл. 8.4.
bd=0.5*ba (U+1)=0.5*0.4(4+1)=1- коэффициент ширины шестерни
KH=1.08 — коэффициент концентрации нагрузки в зависимости от bd (рис. 8.15, с. 130 [2])
Определяем ширину колеса:
мм
Определяем модуль:
где m=30 — коэффициент модуля, в зависимости от жёсткости (табл. 8.4, с136, [2])
По таблице 8.1 назначаем =1.5мм
Выбираем число зубьев в рекомендуемых пределах:
=9o
Определяем суммарное число зубьев:
Находим число зубьев:
Уточняем значения делительных диаметров:
=мм
=мм
Определяем диаметры вершин:
мм
мм
Определяем ширину шестерни:
мм
3.2 Проверочный расчёт тихоходной ступени на усталость по контактным напряжениям (8.29,с.149,[2]):
где KH=KHVKH — коэффициент нагрузки
KH=1.03
KHV — коэффициент динамической нагрузки
м/c
Назначаем девятую степень точности. Принимаем KHV=1,06 (табл.8.3,с.131, [2]).
— коэффициент повышения прочности косозубых передач по контактным напряжениям (8.28,с.149,[2]):
где KH=1.03 — в зависимости от v и 9-ой степени точности (табл.8.7, с. 149, [2])
По формуле (8.25[2]):
=
— коэффициент торцового перекрытия.
МПа
мПа
Определяем недогрузку:
3.3 Проверочный расчёт тихоходной ступени по напряжениям изгиба
где YFS — коэффициент формы зуба
ZF — коэффициент повышения прочности зуба
KF — коэффициент неравномерности нагрузки
Для определения YFS определим и :
По графику (рис. 8.20, с. 140, [2]) в зависимости от и находим и: =3.8, =3.75
МПа
МПа
Так как 65.8<95.5, то принимаем YF=3.75
Определяем YF (8.34,с.150,[1]):
где по таблице 8.7[2] KF=1.35
Найдём KF:
где KF=1.3 (рис. 8.15, с. 130, [2])
KFV=1.04 (табл.8.3, с. 131, [2])
Находим окружное усилие:
Н
Определяем напряжение:
мПа
мПа
Условие прочности выполняется.
3.4 Расчет геометрических параметров тихоходной передачи
Ранее были определены мм, мм, b=50 мм.
Определяем диаметры вершин:
мм
мм
Диаметр впадин зубьев:
мм
мм
4. Расчет быстроходной передачи
Внешний делительный диаметр большего конического колеса определяем по формуле (9.40[3]):
Примем число зубьев шестерни =24
Число зубьев колеса:
*U=24*2,5=60
Внешний окружной модуль:
мм
По таблице 9.1[3] принимаем =2,25 мм
Уточняем значения и :
мм
По таблице 9.4[3] принимаем =140 мм
Конусное расстояние:
мм
Ширина зубчатого венца:
мм
По таблице 9.5[3] принимаем b=21 мм
Внешний делительный диаметр шестерни:
мм
Углы при вершине начальных конусов:
ctg;ctg2,5=; =68,198`; =90-=90−68,198=21,802`
Средний делительный диаметр шестерни:
=2(72,7−0,5*21)*0,371=46,2 мм
Средний окружной модуль:
4.1 Расчет геометрических параметров быстроходной передачи
Ранее были определены мм, мм, b=21 мм.
Диаметры вершин зубьев:
мм
мм
Диаметр впадин зубьев:
мм
мм
5. Расчет валов
5.1 Проектный расчет валов
Произведём расчёт быстроходного вала:
Определим выходной конец вала:
где T1=34.47Нм
мм
Согласуем вычисленное значение с величиной диаметра вала электродвигателя: мм
Принимаем: d=25 мм, диаметр вала под подшипники мм.
Рассчитаем промежуточный вал:
Диаметр ступени для установки на неё колеса:
где Tпр=88.53 Нм
мм
Принимаем dк=34 мм. Диаметр буртика для упора колеса dбк=40 мм. Диаметр участков для установки подшипников dп=30 мм.
Расчёт тихоходного вала.
Назначаем материал: Сталь 45.
Термообработка: улучшение.
Из таблицы 8.8 стр. 162 находим:
МПа
МПа
Определяем диаметр выходного конца вала:
мм, где МПа
Выбираем диаметры вала:
d=40 мм — диаметр в месте посадки муфты
dп=50 мм — диаметр в месте посадки подшипников
dк=55 мм — диаметр в месте посадки колеса
5.2 Проверочный расчет тихоходного вала редуктора
Определяем длины вала:
c=80 мм
где lст=74 — ширина ступицы (округлена)
x=10 мм
w=60 мм — толщина крышки
Получаем:
l=74+2*10+60=154 мм
Составляем расчётную схему.
Определяем силу в месте посадки муфты:
Н
Определяем силы в зацеплении:
Н
Н
Н
Строим эпюру изгибающих моментов в вертикальной плоскости. Сначала определим реакции опор (составим сумму моментов относительно опоры А):
Н Для определения реакции в опоре A составим сумму сил на вертикальную ось:
Н Строим эпюру изгибающих моментов в вертикальной плоскости.
Рассмотрим горизонтальную плоскость.
Запишем сумму моментов относительно опоры А:
Н Запишем сумму сил на вертикальную ось:
Н Строим эпюру изгибающих моментов в горизонтальной плоскости.
Строим эпюру суммарных изгибающих моментов.
Строим эпюру крутящих моментов.
Опасным сечением будет, сечение I-I под шестерней. Проверим статическую прочность вала в этом сечении.
Мпа Крутящий момент: T=347.2МПа Напряжение изгиба:
МПа Напряжение кручения:
МПа Определяем эквивалентное напряжение:
МПа Условия прочности выполняются.
Определим пределы выносливости:
МПа
МПа Определим запасы на сопротивление усталости по формулам (15.3, с. 299, [2]):
где и — амплитуды переменных составляющих
и — амплитуда постоянных составляющих
и — масштабные коэффициенты
и — эффектные коэффициенты концентрации напряжений По графику 15.5, с. 301, [2], кривая 2 находим =0.72
По графику 15.6, с. 301, [2], кривая 1 находим =1 МПа По таблице 15.1, с. 300, получаем =1,7 МПа и =1.4 МПа Принимаем
; МПа МПа МПа МПа
По формуле 15.3, с. 299, определим суммарный коэффициент запаса:
Проверяем жёсткость вала. Для определение прогиба используем таблицу 15.2, с. 303,. Средний диаметр принимаем равным dк=55 мм.
мм4
Прогиб в вертикальной плоскости от силы Fr:
мм Прогиб в горизонтальной плоскости от сил Ft и FM:
мм Определяем суммарный прогиб:
мм Определяем допускаемый прогиб (с. 302, [1]):
мм Вал отвечает необходимым условиям жёсткости.
6. Выбор подшипников качения
6.1 Проверочный расчет подшипников качения тихоходного вала
Необходимо подобрать подшипники для вала тихоходного редуктора используя следующие данные: диаметр в месте посадки подшипника d=50 мм, L=10 416 ч.
Определяем реакции опор:
; H
; H
Учитывая сравнительно небольшую осевую силу Fa=494,2Н, назначаем конические подшипники лёгкой серии, условное обозначение 7210, для которых по таблице 16.9 из С=56 000 Н, Cо=40 000 Н, e=0,37.
Спаспортная динамическая грузоподъемность, Сопаспортная статическая грузоподъемность.
Выполняем проверочный расчет. Определяем осевую составляющую нагрузки по формуле 16.38 из [2]:
S1=0.83*0.37*4269.24=1309.85 Н
S2=0,83*0,37*5351,41=1643,42 Н
Принимаем =1643,42 Н и по формуле (16.36[2]) находим осевую нагрузку :
Н
Условие не раздвижения коле соблюдается Н
Определяем эквивалентную нагрузку по формуле 16.29 из [2]:
где по рекомендации имеем V=1; по таблице 16.5[2] при находим X1=1, Y1=0 и при, X1=1, Y1=0, по рекомендации к формуле (16.29[2]) находим Kт=1, K=1,3.
Kэффективный коэффициент концентрации напряжений при изгибе, Kт — эффективный коэффициент концентрации напряжений при кручении.
Н
Н
Так как, рассчитываем только второй подшипник.
3.68
C=6956.83*3.68=25 601.1 Н
Условие С (потребная)<=C (паспортная) выполняется.
Проверяем подшипник по статической грузоподъемности. По формуле 16.33 из вычисляем, при Х=0.6, Y=1.04:
где Yoкоэффициент осевой статической нагрузки, Хокоэффициент радиальной статической нагрузки, Роэквивалентная статическая нагрузка.
H
Условие соблюдается: паспортное значение статической грузоподъемности больше расчетного.
7. Расчет шпоночных соединений
Для закрепления деталей на валах редуктора используем призматические шпонки. Размеры поперечного сечения шпонок выбираем по ГОСТ 23 360–78 в соответствии с диаметром вала в месте установки шпонок.
диаметр | сечение шпонки | рабочая длина | крутящий момент | ||
вала, мм | b | h | шпонки lр, мм | на валах Т, H*м | |
37.47 | |||||
88.53 | |||||
347.24 | |||||
347.24 | |||||
Расчет шпонок по допускаемым напряжениям на смятие:
. Условие прочности:
а)
б)
в)
г)
Все выбранные шпонки удовлетворяют напряжениям смятия.
8. Выбор муфт
Для соединения вала редуктора и вала электродвигателя применяем упругую втулочно-пальцевую муфту по ГОСТ 21 424–93.
T, H*м | d, мм | D, мм | L, мм | |
Проверим муфту по напряжениям смятия (17.34[2]):
Мпа
где мм — диаметр окружности, на которой расположены пальцы
z=6 — число пальцев
— диаметр пальца
— длина резиновой втулки
Мпа
Мпа
Для соединения тихоходного вала редуктора с валом барабана используем зубчатую жестко-компенсирующую муфту (ГОСТ 5006−55):
T, кH*м | d, мм | D0, мм | b, мм | |
Условие прочности:
Мпа
где b-длина зуба
Муфты отвечают условиям прочности.
9. Смазка редуктора
Для уменьшения износа зубьев, для уменьшения потерь на трение, а также для отвода тепла выделяющегося в зацеплении применяют смазку передач в редукторе.
Так как скорости колёс V<12…15м/с их смазывание производится погружением в масляную ванну. По рекомендации глубина погружение тихоходного колеса обычно не превышает 0,25 его радиуса.
Принимаем для смазки редуктора масло трансмиссионное ТМ-3−9 ГОСТ 17 472–85, имеющее кинетическую вязкость .
Объём заливаемого масла определяем по формуле:
где — внутренняя длина редуктора
— внутренняя ширина редуктора
— высота масла в редукторе
л.
Для смазки подшипников применяем наиболее распространённую для подшипников смазку: Жировая 1−13 ГОСТ 1631–61.
Заключение
Для изготовления шестерен и колёс, желая получить сравнительно небольшие габариты и невысокую стоимость редуктора, была выбрана легированная сталь 40Х и назначена термообработка: для шестерен — азотирование поверхности 50…59 HRC при твёрдости сердцевины 26…30 HRC, ,; для колес — улучшение 230…260 HB. Для тихоходной ступени были произведены проверочные расчёты на усталость по контактным напряжениям и напряжениям изгиба. Все условия прочности соблюдаются: мПа — по контактным напряжениям, мПа — по напряжениям изгиба.
При расчёте тихоходного вала было установлено, что все условия прочности и жёсткости выполняются: запас сопротивления усталости, суммарный максимально возможный прогиб мм.
Выбранные шпонки были проверены по напряжениям смятия, все они удовлетворяют допустимым значениям.
Список используемых источников
1. Курмаз Л. В., Скойбеда А. Т. Детали машин. Проектирование.- «Технопринт», Минск, 2000.
2. Иванов М. Н. Детали машин. — «Высшая школа», М., 1984.
Кузьмин А.В., Чернин И. М., Козинцов Б. С. Расчеты деталей машин. «Высшая школа», Мн., 1986.
Шейнблинт A.E. Курсовое проектирование деталей машин. — «Высшая школа», М., 1991.
Анурьев B.И. Справочник конструкторамашиностроителя. — «Машиностроение», М., 1978.