Разработка технического процесса на сборку и сварку корпуса абсорбера
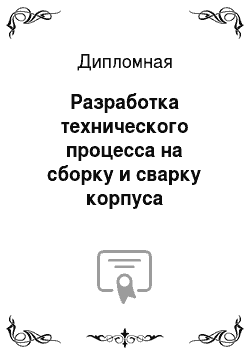
Характеристика сварочного выпрямителя ВД-306УЗ Сварочные выпрямители получили большое распространение. Основные их преимущества: высокий к.п.д. и небольшие потери холостого хода; отсутствие вращающихся частей и бесшумность в работе; равномерность нагрузки фаз; небольшая масса. Однако для выпрямителей продолжительные короткие замыкания представляют большую опасность, так как могут выйти из строя… Читать ещё >
Разработка технического процесса на сборку и сварку корпуса абсорбера (реферат, курсовая, диплом, контрольная)
Реферат Данная пояснительная записка выполнена в соответствии с требованиями ЕСКД и ЕСТД.
Записка состоит из четырех частей и двадцати четырех разделов.
Первая часть — общая, содержит назначение, условия работы и описание конструкции; технические условия на материалы, сборку сварку, ГОСТы.
Вторая часть — технологическая, содержит схему сборки сварки; выбор сварочного тока; выбор метода сварки; выбор марки электродов, сварочной проволоки, флюса, защитного газа; выбор и расчет режимов сварки; расчет норм времени; выбор сварочного оборудования; меры принимаемые по борьбе со сварочными напряжениями и деформациями; описание конструкций приспособлений, контроль сварных швов и испытание изделия.
Третья часть — организационная, содержит выбор наиболее экономического процесса; расчет потребного оборудования, необходимого для выполнения производственной программы; подсчет и планировку площадей пролета (участка); мероприятия по технике безопасности, охране труда и противопожарной безопасности на участке; расчет потребного количества участников производства.
Четвертая часть — экономическая, содержит расчет стоимости основных и вспомогательных материалов, расчет фондов заработной платы, расчет себестоимости.
Введение
Основой дипломного проекта является выбор главных параметров технологического процесса изготовления сварной конструкций, в первую очередь заготовительных и сборочно-сварочных работ. Важной задачей дипломного проекта является приобретение навыков использования в практической разработке комплекса знаний, полученных при изучении специальных дисциплин по специальности, а так же навыков приобретенных во время прохождения практики.
Сварка — технологический процесс, как и обработка металлов резанием, литье, ковка, штамповка. Большие технологические возможности сварки обеспечили её широкое применение при изготовлении и ремонте судов, автомобилей, турбин, котлов, реакторов, мостов и других металлических конструкций. Перспективы сварки как в научном, так и в техническом плане безграничны. Её применение способствует совершенствованию машиностроения и развитию ракетостроения, атомной энергетики, радиоэлектроники.
О возможности применения «электрических искр» для плавления металлов еще в 1753 году говорил академик Российской академии наук Г. Р. Рихман при исследовании атмосферного электричества. В 1802 году профессор Санкт-Петербургской военно-хирургической академии В. В. Петров открыл явление электрической дуги и указал возможные области её практического использования. Однако потребовались многие годы совместных усилий ученых и инженеров, направленных на создание источников энергии, для реализации процесса электрической сварки металлов. Важную роль в создании этих источников сыграли открытия и изобретения в области магнетизма и электричества.
В 1882 году российский ученый Н. Н. Бенардос, работая над созданием аккумуляторных батарей, открыл способ электродуговой сварки неплавящимся угольным электродом. Им был разработан способ дуговой сварки в защитном газе и дуговая резка металлов.
В 1888 году российский инженер Н. Г. Славянов предложил проводить сварки плавящимся металлическим электродом. С его именем связано развитие металлургических основ электрической дуговой сварки, разработка флюсов для воздействия на состав металла шва, создание первого электрического генератора.
В середине 1920 годов интенсивные исследования процессов сварки были начаты во Владивостоке (В.П. Вологдин, Н.Н. Рыкалин), в Москве (Г.А. Николаев, К.К. Окерблом). Особую роль в развитии и становлении сварки в нашей стране сыграл академик Е. О. Патон, организовавший в 1929 году лабораторию, а затем институт электросварки (ИЭС).
В 1924 — 1935 годах в основном применяли ручную сварку электродами с тонкими ионизирующими (меловыми) покрытиями. В эти годы под руководством академика В. П. Волошина были изготовлены первые отечественные котлы и корпуса нескольких судов. С 1935 — 1939 годов начали применять толсто-покрытые электроды, в которых стержни изготавливали из легированной стали, что обеспечивало широкое использование сварки в промышленности и строительстве. В 1940 годы была разработана сварка под флюсом, которая позволила повысить производительность процесса и качество сварных соединений, механизировать производство сварных конструкций. В начале 1950 годах в институте электросварки имени Е. О. Патона создают электрошлаковую сварку для изготовления крупногабаритных деталей из литых и кованых заготовок, что снизило затраты при изготовлении оборудования тяжелого машиностроения. С 1948 года получили промышленное применение способы дуговой сварки в защитных газах: ручная сварка неплавящимся электродом, механизированная и автоматическая сварка плавящимся и неплавящимся электродами. С 1950 — 1952 годах ЦНИИТМаше при участии МГТУ имени Н. Э. Баумана и ИЭС Е. О. Патона был разработан высокопроизводительный процесс сварки низкоуглеродистых и низколегированных сталей в среде углекислого газа, обеспечивающий высокое качество сварных соединений.
В последние десятилетия создание учеными новых источников энергии концентрированных электронного и лазерного лучей обусловило появление принципиально новых способов сварки плавлением, получивших название электронно-лучевой и лазерной сварки. Эти способы сварки успешно применяют в нашей промышленности.
Сварка потребовалась и в космосе. В 1969 году наши космонавты В. Кубасов и Г. Шонин и 1984 году С. Савицкая и В. Джанибеков провели в космосе сварку, резку и пайку различных металлов.
Одно из наиболее развивающихся направлений в сварочном производстве — широкое использование механизированной и автоматической сварки. Речь идет как о механизации и автоматизации самих сварочных процессов (переход от ручного труда сварщика к механизированному), так и о комплексной механизации и автоматизации, охватывающей все виды работ, связанных с изготовлением сварных конструкций и созданием поточных и автоматических производственных линий. С развитием техники возникает необходимость сварки деталей разных толщин из разных материалов, в связи с этим постоянно расширяется набор применяемых видов и способов сварки. В настоящее время сваривают детали толщиной от нескольких микрометров (в микроэлектронике) до десятков сантиметров и даже метров (в тяжелом машиностроении). Наряду с конструкционными углеродистыми и низколегированными сталями все чаще приходится сваривать специальные стали, легкие сплавы на основе титана, молибдена, хрома, циркония и других металлов, а также разнородные материалы.
Выполнение дипломного проекта учит самостоятельно решать несложные технологические задачи при проектировании сварной конструкции, пользоваться сварочно-технической литературой по сварке, увязывать теоретические знания с практикой.
1. ОБЩАЯ ЧАСТЬ
1.1 Назначение, условия работы и описания конструкции изделия Абсорбер — это вертикальный колонный аппарат, который сверху орошает абсорбентом, снизу в него подаётся газовая смесь. В химической промышленности применяют абсорберы поверхностные, плёночные, насадочные, барботажные и механические.
Поверхностные абсорберы представляют собой вертикальные или горизонтальные ёмкостные аппараты, заполненные до середины крошечным абсорбентом. Через вводной или выводной штуцера на поверхности абсорбента получают газовую смесь, из которой абсорбент поглощает рабочий компонент.
Плёночные абсорберы — чаще всего трубчатые аппараты аналогичные по конструкции вертикальным полутрубчатым теплообменником. Газовая смесь движется по этим же трубкам сверху вниз и из него поглощается рабочей компонент.
Насадочные абсорберы — находят наибольшее распространение. Конструктивно они представляют собой цилиндрические аппараты, которые имеют внутри несколько слоёв насадки, насыпанной на решётки. Для ввода и вывода газа служат штуцера для ввода и вывода абсорбента. Для осмотра и обслуживания внутренних устройств предусмотрены люки лазы.
Тарельчатые и барабанные абсорберы — колонные аппараты, имеющие барботажные тарелки рассмотренных типов и конструкций. Для отвода тепла часто на тарелках устанавливают теплообменные устройства в виде спиральных змеевиков, в которые подаётся хладоген.
Механические абсорберы — колонные аппараты в которых поверхности соприкосновения фаз создаются распылением жидкости в газе на мелкие капли с помощью дисков вращающего устройства (ротора, конуса и т. д.).
1.2 Технические условия на материалы, сборку и сварку, ГОСТы Выбор материала для сварной конструкции является одним из факторов рационального проектирования. Прежде всего, сталь должна быть свариваемой. Свариваемость можно рассматривать как с физической, так и с технологической точки зрения. Под физической свариваемостью понимается возможность достижения надежной связи между атомами свариваемого металла. Под технологической свариваемостью понимается отношение металлов к конкретному виду и режимам сварки. Свариваемость данного металла считается тем выше, чем больше число применяемы к нему видов сварки, проще их технология и шире пределы допускаемых режимов сварки, позволяющие получить качественные швы без трещин, пор и других дефектов.
Сталь ВСт3сп5 низкоуглеродистая, конструкционная, обыкновенного качества, поставляется по механическим свойствам и химическому составу. Сталь относится к разряду хорошо сваривающихся металлов, она поставляется по ГОСТ 380–94. Сварка стали ведётся без предварительного подогрева, а после сварки не требуется последующая термообработка. Сталь не склонна к образованию горячих и холодных трещин. Сварные соединения обладают высоким качеством. Сталь изготавливается горячекатаной, сортовой, фасонной, толстолистовой, тонколистовой, широкополосной, универсальной. Из стали изготавливаются поковки, штамповки, сварочная лента, проволока. В стандарте учтены международные требования и рекомендации по стандартизации. В конструкции применяется сталь ВСт3сп5, эта сталь относится к группе В. Стали этой марки поставляются заказчику по механическим и химическим составам.
Сборка сварных конструкций заключается в размещении элементов конструкции (узла) в порядке, указанном в технологической карте, и предварительном скреплении их между собой с помощью приспособлений и наложении прихваток. Сборка одна из наиболее ответственных операций. От качества сборки в значительной степени зависит качество сварной конструкции. Технология сборки определяется следующими факторами: типом производства, особенностями конструкции и оснащенностью сборочного цеха. При сборке конструкций широко используют разнообразные сборочные и сборочно-сварочные приспособления. Тип приспособления определяется серийностью производства и степенью сложности конструкции. Применение приспособлений снижает трудоемкость сборочных операций, уменьшает остаточные деформации, повышает качество конструкции и упрощает контроль и приемку собранных конструкций. Прихватка должна производиться квалифицированным сварщиком. Все сварочные работы при изготовлении сосудов, аппаратов и их элементов должны производится, при положительных температурах, в закрытых, отапливаемых помещениях.
Сварка сосудов и аппаратов, а также приварка деталей к корпусам должны производится сварщиками, сдавшими экзамены в соответствии с Правилами Аттестации сварщиков, утвержденные Госгортехнадзором РФ, не дипломированные сварщики могут производить сварку деталей и узлов, внутренних устройств сосудов, аппаратов, за исключением приварки этих деталей к корпусам. Сварка должна производится в соответствии с технологической документацией, разработанной с учетом требований и ОСТ 26−294−98, спецификаций и свариваемых изделий и свариваемых материалов, ГОСТов.
Таблица 1.2. — Химический состав стали ВСт3сп5, в % по ГОСТ 380–94
марка материала | содержание элементов, % | никель | медь | сера | фосфор | |||
углерод | марганец | кремний | ||||||
не более | ||||||||
ВСт 3 сп5 | 0,14−0,22 | 0,40−0,65 | 0,12−0,80 | ?0,30 | ?0,30 | 0,05. | 0,04 | |
Таблица 1.3 — Механические свойства стали ВСт3сп5, в % по ГОСТ 380–94
Толщина Проката S, мм | Предел текучести, н/ | Временное сопротивление разрыву, н/ | Относительное удлинение у, % | Ударная вязкость Дж/ | |
На предприятии — изготовителе сосудов и аппаратов материалы до запуска в производство должны приниматься отделом технического контроля. При этом проверяется соответствие материалов, требованием чертежа, настоящего стандарта, стандартов и технических условий. Данные сертификатов или результаты испытаний, материалов, нагруженных давлением деталей сосудов и аппаратов, подведомственных ГОСГОРТЕХНАДЗОРУ должны заноситься в паспорт изделия или приложение к нему.
На поверхности деталей не допускаются брызги металла в результате огневой резке и сварки. Заусенцы должны быть удалены, острые кромки деталей и узлов притуплены. Сварщик может приступить к сварке после установления контроля ОТК правильности сборки и зачистки всех поверхностей металла, подлежащих сварке. На листах, принятых для изготовления обечаек, должна быть сохранена маркировка предприятия-поставщика материала. В случаях, когда лист разрезается на части, до разметки, на каждом из них должна быть нанесена маркировка, заверенная клеймом ОТК.
Обечайки диаметром свыше 1000 мм допускается изготовлять из нескольких листов, максимально возможной длины. Не допускается вставка шириной менее 400 мм. Допускается изготовление обечаек путем вальцовки карт, сваренных в плоском состоянии из нескольких листов. В обечайках свальцованных из карт, сваренные швы должны быть параллельны образующим, ширина листов между швами должна быть не менее 800 мм, а ширина замыкающей вставки не менее 400 мм.
После сборки и сварки, корпуса сосудов и аппаратов должны удовлетворять следующим требованиям:
а) отклонение по длине не должно превышать 3%, от минимальной длины (без днища), но не более 75 мм;
б) отклонение от прямолинейности, за исключением колонных аппаратов, не должно превышать 2 мм на длине 1 м, но не более 20 мм при длине изделия более 10 м, без учета допускаемой местной не прямолинейности в местах сварных швов.
Отклонение от наружного диаметра корпуса цилиндрических сосудов и аппаратов, за исключением колонной и теплообменной аппаратуры, не должно превышать 1%, от минимального диаметра. На поверхности днища не допускаются забоины, вмятины, уменьшающие расчетную толщину днища, а также раковины, надрывы, расслоения и другие дефекты. Исправление дефектов производится с разрешением ОТК.
При установке штуцеров и люков:
а) отклонение осей штуцеров и люков от номинальных размеров не должны превышать 10 мм;
б) отклонения диаметров отверстий под штуцера и люки должны быть в пределах зазоров, допускаемых для сварки соединений по ГОСТам;
в) отклонение по высоте (вылету) штуцеров 5 мм.
При подготовке кромок свариваемых изделий необходимо исключить их механические повреждения, снижающих регламентированные свойства сварных соединений. Разделка кромок должна соответствовать требованиям действующих стандартов, нормативно-технической документации и чертежа. Кромки, подготовленные под сварку, должны быть зачищены до чистого металла и обезжирены на ширину 20 мм и не должны иметь следов ржавчины, масла и прочих загрязнений. Подготовленные кромки подвергаются визуальному контролю для выявления пороков металла, расслоения, трещин, а двухслойной стали отслоения коррозионного слоя.
Все сварные швы подлежат клеймению, позволяющему установить сварщика, выполняющего эти швы. Клеймо наносится на расстоянии 20−50 мм от кромки сварного шва. У продольных швов клеймо должно находиться в начале и в конце шва на расстоянии 100 мм от кольцевого шва. Для кольцевого шва клеймо выбирается на месте пересечения кольцевого шва с продольным и далее через каждые 2 мм, но при этом должно быть не менее трёх клейм на каждом шве. Клеймо ставится с внутренней стороны. Продольные швы смежных обечаек и швы днищ в сосудах и аппаратах, должны быть смещены относительно друг от друга на величину трёхкратной толщины наиболее толстого элемента, но не менее чем на 100 мм между осями швов.
При сварке стыковых соединений элементов разной толщины, необходимо предусмотреть плавный переход от одного элемента к другому, последовательным уточнением более толстого элемента в соответствии с требованием ГОСТ 8713–79 и ГОСТ 5264–80, а в случаях, не предусмотренных стандартными, угол скоса элементов разной толщины должен быть не менее 20 0. Допускается применить стыковые швы без предварительного уточнения более толстой стенки, если разность в толщинах соединяемых элементов не превышает 30% от толщины более тонкого элемента, но не более 5 мм. Форма шва должна обеспечивать плавный переход от толстого элемента к тонкому. В случае приварки стандартных фланцев к патрубкам или обечайкам допускается обеспечивать плавный переход наплавкой от более толстого элемента (патрубка или обечайки). Форма и размеры швов должны соответствовать стандартам и требованиям чертежа. Резкие переходы в сварных швах не допускаются. Сварной шов должен иметь плавный переход к основному металлу в соответствии со стандартами.
При разработке технологического процесса использовались следующие стандарты:
ОСТ 26 291−94 Отраслевой стандарт. Общие требования к изготовлению сепаратора, сварки сварных соединений, качеству сварных соединений.
ГОСТ 8713–79 Автоматическая сварка под флюсом. Соединения сварные, основные типы, конструктивные элементы и размеры.
ГОСТ 14 771–76 Дуговая сварка в защитном газе. Соединения сварные, основные типы, конструктивные элементы и размеры.
ГОСТ 5264–80 Ручная дуговая сварка. Соединения сварные, основные типы, конструктивные элементы и размеры.
ГОСТ 2246–70 Проволока стальная сварочная.
ГОСТ 9087–81 Флюсы сварочные плавленые.
ГОСТ 8050–85 Двуокись углерода газообразная и жидкая. Технические условия.
ГОСТ 13 821–77 Выпрямители с крутопадающими характеристиками для дуговой сварки. Основные параметры и технические требования.
ГОСТ 8213–75 Автоматы для дуговой сварки плавящимся электродом, самоходные.
ГОСТ 18 130–79 Полуавтоматы шланговые для электродуговой сварки плавящимся электродом.
ОСТ 288−91 Отраслевой стандарт. Контроль качества сварных соединений.
2. ТЕХНОЛОГИЧЕСКАЯ ЧАСТЬ
2.1 Определение типа производства и его характеристика Характеристика предприятия в зависимости от степени его специализации, широты номенклатуры изготавливаемых изделий, регулярности, стабильности и объема выпуска изделий называется типом производства. Крупносерийный тип характеризуется ограниченной номенклатурой изготавливаемых или ремонтируемых изделий и большим объемом выпуска, повторяющегося через определенный промежуток времени партии. Технологический процесс в крупносерийном производстве дифференцирован, т. е. разделён на отдельные операции, которые закреплены за отдельными рабочими местами. Сравнительно устойчивая номенклатура в крупносерийном сварочном производстве позволяет шире применять специальные сборочно-сварочные приспособления и механизмы, внедрять автоматизированные способы сварки, а на отдельных участках организовать поточные линии. При этом используется как общецеховой, так и напольный транспорт. Специализация отдельных видов работ не требует столь высокой квалификации рабочих, как в единичном производстве.
Главными отличительными особенностями крупносерийного производства является постоянство, сравнительно большой номенклатурой выпускаемых изделий; специализация рабочих мест выполнение нескольких постоянно закрепленных за ними операций; выпуска изделий сериями в определенном, заранее установленном чередовании; применение наряду с универсальным специального оборудования, сборочно-сварочное приспособление и другие специальные оснастки; сокращение удельного веса ручных работ; использование труда специализированных рабочих средней квалификации; относительное сокращение длительности производственного цикла по сравнению с единичным производством.
2.2 Схема сборки и сварки Разработка технологического процесса сборки и сварки и его обоснование.
2.3.1 Особенности сборки и сварки После заготовки детали сварных конструкций поступают на сборку. Сборкой называется процесс последовательного соединения деталей между собой в порядке, предусмотренном технологическим процессом и чертежом, для последующей сварки. В зависимости от типа производства, особенностей конструкции и технологических условий на сборку можно выполнять различными способами: по разметке, по шаблонам или по первому изделию, по сборочным отверстиям, в приспособлениях (универсальных, специализированных и специальных), сборку по разметке ведут без приспособлений. Наибольшую точность сборки при минимальной трудоёмкости можно обеспечить при использовании сборочно-сварочного оборудования.
Основная цель технологического процесса сборки заключается в определении наиболее выгодной последовательности сборки отдельных деталей, обеспечивающих выполнение технических требований на изготовление данного изделия при минимальных затратах рабочей силы, времени и вспомогательных материалов. Перед сборкой сборщик визуально проверяет соответствие деталей требованием чертежа и технологического процесса. Сопрягаемые поверхности и прилегающие к ним зоны собираемых деталей шириной не менее 20 мм должны быть тщательно очищены от ржавчины, масла, грязи, окалины, и влаги во избежание появления пор и других дефектов в металле шва. При сборке сварных конструкций обеспечивается такое взаимное расположение деталей собираемого узла, в котором они должны находится в готовом узле. Зазоры при сборке должны строго соответствовать чертежу. Превышение кромки одного из элементов стыкового соединения над другим, если оно не предусмотрено и не оговорено специально в чертеже, допускается по всей длине шва не более 0.2 толщины элемента до 4 мм и 0.15 толщины элемента свыше 4 мм, но не менее 1.5 мм. Местные превышения кромок контролируются до сварки.
При сборке сварных конструкций детали между собой соединяют посредствам прихваток, которые размещают в местах расположения будущих сварных швов. Прихватки выполняются покрытыми электродами, в защитных газах или под флюсом. Площадь сечения прихваток не должна превышать 2/3 площади сечения будущего шва и составлять не более 25−30 мм2. Длина каждой прихватки должна быть равна 4−5 толщинам соединяемых деталей, но не менее 30 мм и не более 100 мм. Чем меньше толщина свариваемых деталей, чем меньше расстояние между прихватками.
Разрешается наложение прихваток вне мест расположения швов для временного скрепления детали. Эти прихватки после выполнения своего назначения удаляют, а места их размещения зачищают. Рациональна замена прихваток сплошным швом небольшого сечения (технологический шов). Сборочные прихватки выполняют сварочными материалами тех же марок, что и при сварке данной конструкции. Требования к качеству прихваток устанавливаются те же, что и при сварки основного шва. При сварке продольных швов для ввода электрода в шов и вывода его из шва за пределы изделия, по окончании сварки, к кромкам необходимо приварить вводные и выводные планки. Форма разделки планок должна соответствовать разделке кромок основного шва.
2.3.2 Выбор рода тока и полярности Однако полярность постоянного тока оказывает различное влияние на глубину провара, что объясняется разным количеством тепла выделяемого на катоде (минус) и аноде (плюс). Тепло на аноде выделяется в результате бомбардировки его потоком электронов, а на катоде в результате бомбардировки положительно заряженными ионами. При сварке на воздухе ручной дуговой сваркой больше тепла выделяется на аноде, так как анод бомбардируется электронами.
При сварке почти всеми флюсами в результате возрастания кинетической энергии положительно заряженных ионов, бомбардирующих катод, больше тепла будет выделяться на катоде (минус). Исходя из этого при автоматической и полуавтоматической дуговой сварке под флюсом постоянным током, применяется обратная полярность, при которой больше расплавляется основной металл. Сварку в среде CO2 плавящимся электродом производят на постоянном токе обратной полярности. Это объясняется тем, что при прямой полярности процесс сварки характеризуется большим разбрызгиванием даже при сварке значительно меньшими токами. Это приводит к уменьшению глубины провара, ширины и к увеличению высоты шва. Кроме того, сварка на прямой полярности характеризуется увеличением окисления элементов и повышением склонности шва к образованию пор.
2.3.3 Выбор метода сварки В разрабатываемом проекте применяются три вида сварки:
— автоматическая сварка под флюсом для кольцевых и продольных швов обечаек;
— полуавтоматическая сварка в среде защитного газа для приварки люков к корпусу аппарата
— ручная дуговая сварка применяется для прихваток при сборке узлов сепаратора и для приварки конического днища к корпусу сепаратора.
Наиболее эффективными и производительными методами сварки является автоматическая сварка под флюсом и полуавтоматическая сварка в среде защитных газов. Менее производительным методом сварки является ручная дуговая сварка, но она проста в практическом применении. Автоматическая сварка под флюсом выполняется с помощью сварочной головки или с помощью сварочного трактора. При этом узлы, входящие в сварочные головку, позволяют использовать её как подвесную неподвижную (А или АБ) и как самоходную (АБС).
При автоматической сварке под флюсом подача и перемещение электродной проволоки механизированы, а плавильное пространство защищено шлаком. Изделие сваривается электродной проволокой, подаваемой в плавильное пространство. Перед дугой из бункера насыпается флюс. Он в процессе сварки плавится, а образующийся в процессе шлак защищает плавильное пространство и шов. Остатки не использованного флюса собираются с поверхности шва обратно в бункер. Таким образом, дуга и всё плавильное пространство находятся в условиях полной изоляции от атмосферы.
Автоматическая сварка под флюсом имеет следующие основные преимущества перед ручной сваркой:
— высокая производительность, превышающая производительность ручной сварки в 5−10 раз;
— высокое качество сварного шва, в следствии хорошей защиты металла сварочной ванны расплавленным шлаком от кислорода и азота воздуха, легирования металла шва;
— экономия электродного металла при значительном снижении потерь на угар, разбрызгивание металла и огарки (потери превышают 2−5%);
— экономия электроэнергии за счёт более полного использования теплоты дуги (затраты электроэнергии уменьшаются на 30−40%).
Кроме этих преимуществ, при автоматической сварке условия труда значительно лучше, чем при ручной сварке; дуга закрыта слоем шлака и флюса, выделения вредных газов и пыли значительно снижены, нет необходимости в защите глаз и кожи лица сварщика от излучения дуги, а для вытяжки достаточно естественной вытяжной вентиляции. К квалификации оператора автоматической сварочной установки предъявляются менее высокие требования.
При полуавтоматической сварке в среде защитных газов подача сварочной проволоки механизирована, а перемещение вдоль шва осуществляется сварщиком вручную. В место флюса используется защитный газ, который, как и флюс предохраняет расплавленный металл от воздействия воздуха, окисления и азотирования.
Преимущества сварки в защитном газе:
— хорошая защита зоны сварки от воздействия кислорода и азота воздуха;
— хорошие механические качества сварного шва;
— высокая производительность;
— отсутствие необходимости применения флюса и последующей отчистки шва от шлаков;
— возможность наблюдения за процессом формирования шва;
— малая зона термического влияния;
— возможность полной автоматизации сварки.
Ручная дуговая сварка производится двумя способами: неплавящимся и плавящимся электродом. Второй способ сварки выполняемой плавящимся электродом, является основным при ручной сварке. Сущность сварки состоит в следующем: электрическая дуга возбуждается между металлическим (плавящимся) электродом и свариваемыми кромками изделия. Теплота дуги расплавляет электрод и свариваемые кромки изделия. Получается общая ванна расплавленного металла, которая, охлаждаясь, образует сварной шов. К преимуществам сварки можно отнести маневренность и возможность сварки в любых пространственных положениях. К недостаткам — малая производительность и неоднородность шва, зависящих от квалификации сварщика. Производительность сварки ограничивается максимально допустимым значением сварочного тока для применяемых при ручной дуговой сварке диаметров электродов.
2.3.4 Выбор электродов, сварочной проволоки, флюса, защитного газа Для выполнения прихваток при сборке конструкции предлагается применять электроды марки УОНИ — 13/55 типа Э50А ГОСТ 9467–75. Электроды с фтористо-кальциевым покрытием марки УОНИ — 13/55 предназначены для сварки особо ответственных конструкций из малоуглеродистой и низколегированной стали. Электроды УОНИ — 13/55 применяются для сварки ответственных швов. Эти электроды имеют основное покрытие, состоящее из карбонатов кальция, магния и плавикового шпата, а также из ферросплавов. Расплавленный металл защищается углекислым газом и окисью углерода, которые образуются вследствие диссоциации карбонатов. Электроды с основным покрытием применяются преимущественно при сварке постоянным током обратной полярности во всех пространственных положениях. Электроды обеспечивают высокую стойкость металла шва против образования кристаллизационных трещин и характеризуются низким содержанием водорода, вредных примесей в наплавленном металле. Электроды с основным покрытием весьма чувствительны к образованию пор во время сварки, если кромки свариваемых изделий покрыты окалиной, ржавчиной, маслом, а также если электродное покрытие увлажнено и поддерживается большая длина дуги. Сварку рекомендуется производить короткой дугой методом опирания. После зажигания дуги нужно подвинуть её назад на 5 — 8 мм от места возбуждения дуги, получить спокойную сварочную ванну и только после этого продолжать сварку. Так же следует поступать при смене электрода или случайном обрыве дуги.
Таблица 2.1. Химический состав наплавленного металла УОНИ 13/55, в % по ГОСТ 9467–75 [7, стр22]
С | Cr | Mg | S | Р. | |
0,08−0,12 | 0,18- 0.50 | 0,65 — 1.20 | ?0,03 | ?0,03 | |
Таблица 2.2 Механические свойства металла шва и сварочного соединения [7, стр. 2]
Gr МПа (кгс/мм) | Gb МПа (кгс/мм2) | д% | ш% | бк кгс/мм 2 при 20 0 С | б град | |
420 (42) | 520 (52) | 13,0 | ||||
Таблица 2.3 сварочно-технологические свойства электродов УОНИ 13/45 по ГОСТ 9467–75 [6, стр.20]
Для автоматической сварки под флюсом основного металла в соответствии с ОСТ 26 291−94 выбирается сварочная проволока марки Св-08А и флюс марки АН-348А, которые обеспечивают, получение сварного соединения, с требуемыми механическими свойствами. Правильный выбор марки электродной проволоки для сварки — один из главных элементов разработки технологии механизированной сварки под флюсом. Химический состав электродной проволоки определяет состав металла шва и, следовательно, его механические свойства. Сварочная проволока выпускается по ГОСТ 2246–70. Проволока поставляется в бухтах массой до 80 кг с обязательной металлической биркой с указанием завода изготовителя, условного изготовления проволоки, номера партии, клейма технического контроля. Транспортировать и хранить проволоку следует в условиях исключающих коррозию проволоки, загрязнения и механических повреждений. Если же поверхность проволоки загрязнена или покрыта ржавчиной, то перед использованием её необходимо отчистить. Регламентированная ГОСТом стальная сварочная проволока применяется для изготовления покрытых электродов разного назначения, для сварки под флюсом и в среде защитных газов.
Таблица 2.4 Химический состав проволоки Св08А, в %, по ГОСТ 2246–70 [8, стр. 275]
Проволока | Марганец | Сера | Фосфор | |
Св-08А | 0,80 — 1,10 | ? 0,025 | 0,03 | |
Сварочный флюс один из важнейших элементов, определяющий качество металла шва и условий протекания процесса сварки. От состава флюса зависит состав жидкого шлака и газовой атмосферы. Взаимодействие шлака с металлом обуславливает определенный химический состав металла шва. От состава металла шва зависят его структура, стойкость против образования трещин. Состав газовой атмосферы обуславливает устойчивость горения дуги, стойкость появления пор и количество выделяемых при сварке вредных газов. Флюс выполняет следующие функции: физическую изоляцию сварочной ванны от атмосферы; стабилизацию дугового разряда; химического взаимодействия с жидким металлом; легирование металла шва; формирование поверхности шва.
Таблица 2.5 Химический состав флюса АН-348А ГОСТ 9087–81, % [10, стр. 140, табл.6]
Марка флюса | SiO2 | MnO | CaF2 | MgO | CaO | Al2O3 | Fe2O3 | S | P | |
АН-348 А | 41,0−34,0 | 34,0−38,0 | 4 — 5,5 | 5 — 7,5 | 6,5 | 4,5 | 0,15 | 0,12 | ||
Таблица 2.6 Состав углекислого газа по ГОСТ 8050–85, в % [11, стр. 38]
Показатель | Сорт Первый Высший | |
1 Чистота не менее, % 2 Массовая концентрация минеральных масел и примесей (не более) 3 Массовая концентрация водяных паров, при t=20 С и P=0,1 МПа | 99,5 99,8 0,1 0,1 0,1240,1 | |
2.3.5 Выбор и расчет режимов сварки Расчет режимов автоматической сварки под флюсом.
Основными параметрами режима автоматической сварки стали под флюсом являются: сила сварочного тока, напряжение на дуге, скорость перемещения дуги, диаметр и скорость подачи сварочной проволоки. Основным условием выбора режима автоматической сварки стыковых швов является получение провара всего сечения при хорошем формировании шва.
Глубина провара при стыковой сварке находится в прямой зависимости от сварочного тока и это может быть выражено уравнением
h = R· есв.
Рисунок 2.1. Эскиз стыкового соединения С29 по ГОСТ 9713–79.
Исходные данные для расчета:
Материал: ВСт3сп5 по ГОСТ 380–94;
в = 2 ± 1 мм;
е = 19 не более мм;
g = 2 ±11,5 мм;
S = 8 мм.
Сварочная проволока Св-08А по ГОСТ 2246–70;
Флюс АН-348А по ГОСТ 9087–81;
Определяем силу сварочного тока.
Iсв = h/k * 100 (2.1)
Iсв = 6/1.1*100 = 545 А К принимаем 1,1, [1, стр. 245, табл. 34]
Определяем глубину проплавления
h = S/2+ (2~3) = 4+2 = 6 мм. (2.2)
Зная что напряжение на дуге меняется в пределах (32−40), принимаем напряжение на дуге Uд = 36 В.
Определяем геометрические размеры формы шва.
Определяем коэффициент формы провара, находим шпр = 3,0 мм. [1, стр. 245 рис. 113].
Зная глубину провара и коэффициент формы провара, определяем ширину шва.
е = шпр · h, (2.3)
е = 3,0 * 6 = 18 мм.
Задавшим оптимальным значениям формы выпуклости находим высоту выпуклости.
шв = е/g, (2.4)
g = е/ шв. (2.5)
Принимаем шв = 6
g = 18/6 = 3 мм.
Определяем площадь поперечного сечения шва
F = b · s + 2 · 0,75 · е · g = 2 · 8 + 2· 0,75 · 19 · 2 = 46 мм², (2.6)
F? = 0
Fш = 18 · 2 = 36, мм2 .
При сварке постоянным током обратной полярности коэффициент наплавки приняли б = 12.
Значения бн не учитывают увеличение скорости плавления электродной проволоки за счет предварительного подогрева вылета электрода сварочным током. Действительный коэффициент наплавки при данном вылете определяется:
бн.д.= бн + бн = 12 + 3.4 = 15.4 гр/А· ч. (2.7)
бн — увеличение коэффициента наплавки за счет предварительного нагрева вылета электрода. бн = 2,7 гр/А· ч
6. Определяем скорость сварки (скорость перемещения дуги)
Vп.д = бн Iсв/(Fн · г · 100), м/ч, (2.8)
Vп.д = 15.4 · 545/(0,23 · 7,85 · 100) = 22 м/ч.
7. Определяем скорость подачи сварочной проволоки.
Vп.д=UбнIсв/(h · d2 · г), м/ч, (2.9)
Vп.д=4· 15.4·545/3.14·32·7.85=151.9 м/ч.
Прихватку под автоматическую сварку проведём электродами УОНИ 13/55, диаметром 3 мм.
Расчеты режимов ручной дуговой сварки Режим — это совокупность характеристик сварочного процесса обеспечивающих получение сварных соединений заданных размеров формы и качества. При ручной сварке такими характеристиками являются: диаметр электрода, сила сварочного тока, скорость перемещения электрода вдоль сварного шва, род тока и полярность и т. д.
Рисунок 2.2 Эскиз соединения под углом, отличным от прямого, ГОСТ 11 534– —75 У4
Исходные данные для расчета:
Материал: ВСт3сп5 (ГОСТ 380−94)
Род тока: постоянный, обратной полярности
S = 8, мм;
e = 19 не более, мм;
g = 0,5 ± 1, мм.
b = 2± 1, мм.
c = 2± 1, мм.
б = 50± 5
= 1350
1 Площадь поперечного сечения шва F = 65 мм²
2 Определяем количество проходов
F1 = (30? 35) = 30 мм2 — сечение первого прохода.
n = ((60 — 35) | 35) + 1 = 2 — количество проходов.
3 Определяем силу сварочного тока
Iсв = Fэл i = р d2 i / 4 = 3,14 · 42 · 12 / 4 = 150 А. (2.10)
4 Определяем напряжение на дуге.
Так как напряжение на дуге изменяется в пределах (20−36 В) то принимаем Ug = 26 В.
5 Определяем скорость перемещения дуги:
Vп.д = бн Iсв / (г· Fш · 100), (2.11)
Где бн — коэффициент наплавки, г/А· ч
Fш — площадь сечения сварного шва, мм2.
бн — 9,5 г/А· ч.
Производительность наплавки — 1,3 кг/ч.
Расход электродов на 1 кг — 1,6 кг.
г — 7,85 г/см3.
Vп.д = 9 · 90 / 0.24 · 7,85 · 100 = 4 м/ч.
6 Определяем скорость перемещения дуги при заварке корня шва.
Vп.д = 9 · 140 / 0.54 · 7,85 · 100 = 3 м/ч.
Расчеты режимов полуавтоматической сварки в среде углекислого газа.
Основными параметрами полуавтоматической сварки в среде углекислого газа являются: сила сварочного тока, напряжение на дуге, скорость перемещения дуги, диаметр и скорость подачи сварочной проволоки, а также расход газа и полярность. Исходные данные для расчета:
Материал: ВСт3сп5 (ГОСТ 380−94)
Толщина S = 8 мм.
Сварочная проволока Св — 08А (ГОСТ 2246−70)
Сварка проводится на постоянном токе обратной полярности.
Рисунок 2.3 Эскиз таврового соединения по ГОСТ 14 771–76 Т7.
В связи с отсутствием расчетной методики определения режима сварки в среде углекислого газа режимы подбираются на основании обобщенных опытных данных, приведенных в таблице.
Таблица 2.7 Режимы сварки в среде углекислого газа таврового соединения [1, стр.36]
Тол-щина метал-ла, мм | Режим сварки | |||||||||
Диа-метр элек-трода, мм | Число про-ходов | Сила свароч-ного тока, А | Пло-щадь попе-речного сечения | Напря-жение на дуге, В | Коэф-фициент наплавки | Ши-рина шва, мм | Скорость подачи проволо-ки, м/ч | Объём-ный расход CO2 литр | ||
1,6 | 240−260 | 1,6 | 1,5 | |||||||
2.4 Расчет норм времени Техническое нормирование предусматривает установления технически обоснованных норм времени на выполнение различных сварочных и сборочных работ. Технически обоснованные нормы времени позволяют сварщику производительно использовать рабочее место, полностью загружать сварочное оборудование, а при рациональных приемах сварки перевыполнять установленные нормы.
Нормирование сборки под сварку.
Сборка деталей и узлов может осуществляться по разметке, в простейших универсальных приспособлениях и в специальных стендах и кондукторах. Собираемые под сварку детали крепятся с помощью различного рода винтовых, рычажных, пневматических и других зажимов, а также электродуговой сваркой, прихватками.
Норма времени на сборку металлоконструкций под сварку состоит из подготовительно-заключительного, основного и вспомогательного времени и времени на организационно-техническое обслуживание рабочего места, отдых и естественные надобности.
Подготовительно-заключительное время включает в себя время, затрачиваемое рабочим на получение производственного задания, указаний и инструктажа мастера, ознакомление с работой, получение и сдача инструмента и приспособлений, сдача работы.
Основное время это время сборки металлоконструкции, под сварку, в течении которого происходит координация, соединения и крепления входящих в изделие деталей и узлов.
Вспомогательное время затрачивается на доставку деталей и узлов к месту сборки, проверку их качества, измерение, разметку места установки детали или узла, зачистку собираемых кромок деталей, незначительную правку деталей в процессе сборки, кантовку узлов и деталей, зачистку шлака, окалины после прихватки, газорезки или подогрева.
Норма штучного времени на сборку конструкции в целом, определяется как сумма затрат времени, на установку и крепления всех деталей и узлов.
На проектируемом участке сборка корпуса сепаратора из готовых обечаек по кольцевым стыкам, на конструкции кольцевых стыков 2.
Штучное время на сборку двух обечаек под сварку кольцевого шва:
— подать обечайки на рабочее место сборки и установить их на роликоопоры.
— выправить обечайки, состыковать обечайки, выдержав зазоры и уступность кромок, согласно чертежу.
— прихватить ручной дуговой сваркой.
— кантовать обечайку при сборке.
K1 — коэффициент, учитывающий затраты времени на обслуживание рабочего места, отдых и естественные надобности.
Определяем основное время горения дуги.
То = 60 °F г/нд · Iсв То = 60 · 23 · 7,85/15,4 · 545 = 1,3 мин.
Определяем вспомогательное время связанное со свариваемым швом (табл. 85, стр. 130)
tв.ш = t1 + t2 + t3 + t4 + t5, (2.13)
где t1 — время на зачистку кромок, 0,5 мин,
t2 — корректирование электрода относительно оси шва с передвижением автомата вручную, 0,15 мин,
t3 — отчистка шва от шлака осмотр и промер шва, 0,4 мин.
t4 — сборка флюса со шва и ссыпка его в бункер, 0,4 мин.
tв.ш = 0,3 + 0,15 + 0,4 + 0,1 + 0,4 = 1,55 мин.
Определяем вспомогательное время связанное с изделием (табл. 87, стр. 132)
tв.и = t1 + t2 + t3 + t4 + t5, (2.14)
где
t1 — время на переходы сварщика, 1,5 мин,
t2 — подготовка флюсовой подушки для прямолинейных швов при длине подушки, 1,0 мин,
t3 — установка головки трактора, 1,6 мин.
t4 — отключение автомата после сварки, 0,5 мин.
t5 — клеймение шва, 0,1 мин. и
tв.и = 1,5 + 1,0 + 1,6 + 0,5 + 0,1 = 4,7 мин.
Определяем штучное время.
Тшт = [(То + tв. ш)· l + tв. и]· К1, мин, (2.15)
где-То — основное время на 1 погонный метр шва в минуту,
tв.ш — вспомогательное время связанное со свариваемым швом на 1 погонный метр шва в минуту,
l — длина шва, м,
tв.и — вспомогательное время связанное со свариваемым изделием в минуту, К1 — коэффициент учитывающий затраты времени на обслуживание рабочего места, отдых и естественные надобности, 1,1.
Тшт1 = [(То + tв. ш)· l + tв. и]· К1 = [(1,3 + 1,55) · 7,5 + 4,7] · 1,1 = 21 мин.
Так как сварной шов сваривается с двух сторон, то общее штучное время составляет:
Tшт общ = 2 · 21 = 42 мин.
Так как сварная конструкция состоит из трёх обечаек (два шва):
Tшт = 42 · 2 = 84 мин.
3. Нормирование полуавтоматической сварки в среде СО2
Fшв1 = 40 мм2Fшв2 = 23 мм²
lшв = 5 м.
Норма времени для полуавтоматической сварки складывается из основного и вспомогательного времени.
Основное время определяется
То = 60 °F г/нд · Iсв (2.16)
То = 60 · 40 · 7,85/1,6 · 240 = 5 мин.
Определяем вспомогательное время связанное со швом
tвш = 0,5 + 0,4 + 0,15 = 1,05 мин.
t1 — зачистка кромок вручную, 0,5 мин,
t2 — промер и осмотр последнего слоя шва, 0,4 мин,
t3 — время на один проход, 0,15 мин.
Определяем вспомогательное время связанное со свариваемым изделием.
tви = 5 + 0,31 + 0,1 = 5,32 мин.
Определяем штучное время Тшт1 = [(То + tв. ш)· l + tв. и]· К2 = [(5 + 1,05) · 3,2 + 5,32] · 1,1 = 248 мин. (2.17)
Fшв2 = 23 мм2
Нормирование ручной дуговой сварки (варка штуцера).
Подварка корня шва проводится на режимах d = 3, Iсв = 120А постоянный обратной полярности F1 = 30 мм2
б = 9 гр.
Определяем основное время.
То = 60 °F г/нд · Iсв (2.18)
То = 60 · 24 · 7,85/9 · 90 = 13 мин.
Определяем вспомогательное время связанное со швом
tвш = 12,6 + 0,18 = 12,78 мин.
Определяем вспомогательное время связанное с изделием
tви = 3,7 + 0,18 + 0,1 · 2 = 4,08 мин.
Определяем штучное время
Тшт1 = [(То + tв. ш)· l + tв. и]· К2 = [(13 + 2,25) · 1,9 + 12,78] · 1,1 = 45,9 мин. (2.19)
б = 9 гр. Fшв = 65 мм²
Определяем основное время.
То2 = 60 °F г/нд · Iсв То2 = 60 · 54 · 7,85/9 · 90 = 31,4 мин.
Определяем вспомогательное время связанное со швом
tвш = 0,6 + 1,3 + 0,3 + 0,3 + 0,5 = 2,25 мин.
t1 — зачистка швов под сварку, 0,3 мин,
t2 — зачистка швов от шлака, 0,6 мин,
t3 — зачистка сварного соединения от брызг, 1,3 мин.
t4 — время на осмотр и промер шва, 0,3 мин,
t5 — время на смену электродов, 0,05 мин, Определяем штучное время
Тшт2 = [(То + tв. ш)· l + tв. и]· К2 = [(31,4 + 2,61) · 1,9 + 12,78] · 1,1 = 85 мин.
Определяем основное время.
То3 = 60 °F г/нд · Iсв То3 = 60 · 22 · 7,85/9 · 90 = 12,7 мин.
Определяем штучное время
Тшт1 = [(То + tв. ш)· l + tв. и]· К2 = [(12,7 + 2,25) · 1,9 + 12,78] · 1,1 = 45,8 мин.
Тобщ = 13 + 31,4 + 12,7 = 57 мин.
Т.к. на корпусе абсорбера 4 аналогичных штуцера, то
Тшт = 4 · 57 = 228 мин.
Таблица 2.8. Сводная таблица норм времени
№ п.п. | Наименование операции | Применяемое оборудование | |||||||
I | II | I | II | I | II | ||||
Сборка обечаек по кольцевому стыку | Гидроскоба и роликовый стенд ВДУ-508 | ; | ; | 0,68 | 0,68 | 0,13 | 0,13 | ||
Сварка обечаек по кольцевому стыку | Роликовый стенд, сварочный автомат АДФ-1003 — 1 шт ВДУ-1003 — 2 шт ТС-17 | 0,65 | 0,65 | 2,7 | 2,7 | 0,54 | 0,54 | ||
Вырез отверстия Д = 500 4 отверстия | Роликовый стенд и резак | ; | ; | 0,38 | 0,38 | 0,76 | 0,76 | ||
Сварка корпуса с фланцами | Роликовый стенд, сварочный выпрямитель ВДУ-508 | ; | ; | 0,65 | 0,65 | 0,13 | 0,13 | ||
Сварка корпуса с фланцами (п/а) | Сварочный полуавтомат в сборе с источником питания «КетроMig 4000» | 2,6 | ; | 4,1 | ; | 0,82 | ; | ||
5а | Сварка корпуса с фланцами (РДС) | Роликовый стенд, сварочный выпрямитель ВДУ-508 | ; | 6,9 | ; | 8,8 | ; | 0,17 | |
Сборка штуцеров с корпусом | Роликовый стенд, сварочный выпрямитель ВДУ-508 | ; | ; | 0,38 | 0,38 | 0,76 | 0,76 | ||
Сварка штуцеров с корпусом | Сварочный выпрямитель ВДУ-508 | 0,57 | 0,57 | 3,8 | 3,8 | 0,76 | 0,76 | ||
Итого | 3,82 | 8,12 | 12,69 | 17,39 | 3,9 | 3,25 | |||
2.5 Выбор сварочного оборудования Важным условием получения сварного шва высокого качества является устойчивость процесса сварки. Это зависит от сварочного оборудования, а в первую очередь от источника питания дуги. Для этого они должны обеспечивать возбуждение с стабильное горение дуги.
Для выполнения сварочных работ предлагается следующее оборудование:
— для выполнения прихваток и ручной дуговой сварки сварочный выпрямитель ВД-306УЗ;
— для автоматической сварки под флюсом — сварочный трактор АДФ-1201УЗ и сварочный выпрямитель ВДУ-1201УЗ;
— для полуавтоматической сварки в среде углекислого газа — сварочный полуавтомат KempoMig 4000 со встроенным в него источником питания.
Характеристика сварочного выпрямителя ВД-306УЗ Сварочные выпрямители получили большое распространение. Основные их преимущества: высокий к.п.д. и небольшие потери холостого хода; отсутствие вращающихся частей и бесшумность в работе; равномерность нагрузки фаз; небольшая масса. Однако для выпрямителей продолжительные короткие замыкания представляют большую опасность, так как могут выйти из строя диоды, кроме того, они чувствительны к колебаниям напряжения в сети. Но всё же сварочные выпрямители являются более прогрессивным оборудованием. Сварочный выпрямитель ВД-306УЗ предназначен для ручной дуговой сварки, резки и наплавки, а так же для механизированной сварки под флюсом. Выпрямитель ВД-306УЗ выполнен передвижным, предназначен для ручной дуговой сварки штучными электродами. Выпрямитель обеспечивает плавное регулирование выходных тока и напряжения сети. Выпрямитель работает при воздушном принудительном охлаждении. Он может работать как с падающими, так и с жесткими внешними характеристиками. Конструктивные особенности: выпрямительный блок на тиристорах, собранных по шестифазной схеме.
Таблица 2.9 Техническая характеристика выпрямителя ВДУ-508 по ГОСТ 13 821–77 [10, стр. 48, табл. 6.]
Номинальный сварочный ток, А | Пределы регулирования сварочного тока, А | Напряжение, В. | Минимальная мощность, Кв*А. | Габаритные размеры, мм. | Масса, кг. | ||
Номинальное рабочее | Холостого хода | ||||||
45−315 | 61−70 | 785−780−830 | |||||
Характеристика сварочного полуавтомата KempoMig 4000. Для осуществления полуавтоматической сварки необходимо использовать полуавтомат KempoMig 4000 со встроенным источником питания. Источник постоянного тока KempoMig 4000 создан для профессионального применения для полуавтоматической сварки плавящимся электродом (МИГ/МАГ), а так же штучными электродами они представляют собой инверторные источники питания, подключаемые к трёх фазной сети 400 В, установка KempoMig 4000 снабжена встроенным охладителем для сварки горелки МИГ, требующими водяное охлаждение. Сварочные параметры для способов МИГ/МАГ и штучных электродов регулируются с панели проволокопадающего устройства FEED 400, подключенного к источнику тока KempoMig 4000. При поставке источники KempoMig 4000 снабжены колесами и поддоном для газового баллона.
Таблица 2.10 Техническая характеристика полуавтомата KempoMig 4000 [5, стр. 13.]
Характеристика сварочного трактора АДФ-1003
Сварочный автомат АДФ-1003 предназначен для сварки под флюсом изделий из низкоуглеродистой и низколегированной стали, соединений встык с разделкой кромок и без разделки кромок. Сварные швы могут быть прямолинейными и кольцевыми.
Таблица 2.11 Техническая характеристика АДФ-1003 по ГОСТ 8213–75 [6, стр. 8]
Номина-льный свароч-ный ток | Диаметр электрод-ной прово-локи | Скорость подачи электродной проволоки | Скорость сварки | Габаритные размеры | Масса | Пределы регулирования | |||
Сварочного тока, А | Рабочего напряжения | Напряжение холостого хода | |||||||
1000 А | 3−5 | 60−360 м/ч | 12−120 м/ч | 1050×365×655 | 60кг | 300−1200 | 30−56 | ||
2.6 Меры принимаемые по борьбе со сварочными напряжениями Если меры предотвращения образования сварочных напряжений и деформаций оказываются недостаточными, появляется необходимость в устранении (снятии) возникших напряжений и деформаций.
Отпуск.
Для снятия напряжений сварные соединения подвергают термообработке. С этой целью при сварке углеродистых конструкционных сталей проводят общий высокий отпуск конструкции (нагрев до 630…6500С с выдержкой при этой температуре в течении 2−3 минут на 1 мм. толщины металла). Охлаждение должно быть медленным для того, чтобы при этом снова не возникали напряжения. Режим охлаждения, в основном, зависит от химического состава стали. Чем больше содержание элементов, способствующих закалке, тем меньше должна быть скорость охлаждения. Во многих случаях деталь охлаждают до температуры 3500C с печью, а затем на спокойном воздухе. При высоком отпуске сварочные напряжения снимаются в следствии того, что при температуре 6000С предел текучести металла близок к нулю и материал практически не оказывает сопротивления пластической деформации, в процессе которой происходит снижение (релаксация) сварочных напряжений. В ряде случаев можно ограничиваться высоким отпуском отдельных элементов конструкции. Так, при изготовлении сферических резервуаров для хранения различных продуктов ограничиваются приваркой люков, при изготовлении сварных рам, тележек, вагонов и локомотивов. Такие операции значительно проще, чем отпуск всей конструкции, и его следует применять в действительно необходимых случаях. Если механическая обработка производится на детали, не прошедшей отпуска, то в связи с перераспределением напряжений может произойти изменение её размеров. В большинстве случаев при сварке изделий из стали с повышенным содержанием углерода и легирующих элементов можно ограничиваться только предварительным местным или общим подогревом и не проводить последующей термообработки.