Разработка комбинированной энергетической установки
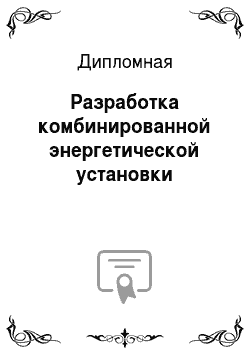
Целью дипломного проекта является разработка комбинированной энергетической установки, способной обеспечить функционирование газотурбинной и паротурбинной её частей. Главным объектом проектирования является паровая турбина мощностью 660 МВт, работающая в составе такой установки. Также значительным преимуществом такой энергоустановки является её способность работать в составе электростанции… Читать ещё >
Разработка комбинированной энергетической установки (реферат, курсовая, диплом, контрольная)
Введение
Целью дипломного проекта является разработка комбинированной энергетической установки, способной обеспечить функционирование газотурбинной и паротурбинной её частей. Главным объектом проектирования является паровая турбина мощностью 660 МВт, работающая в составе такой установки. Также значительным преимуществом такой энергоустановки является её способность работать в составе электростанции с внутрицикловой газификацией угля, с применением таких передовых технологий, как мембранные реакторы конверсии для извлечения водорода из синтез газа и системой улавливания и удержания СО2 — CCS.
Получение водорода рассматривается как попутное производство при обработке синтез газа после газификации угля и занимает второстепенную позицию. Но если в регионе, где планируется устанавливать такой энергоблок, высокий спрос на водородное топливо, то установленную мощность газовой турбины можно уменьшить или исключить её как компонент из цикла вообще, что позволит производить больше водорода без снижения мощности паровой турбины.
КОНСТРУКТОРСКАЯ ЧАСТЬ Выбор основных параметров В соответствии с поставленной задачей на дипломное проектирование и ретроспекривным анализом технической литературы задаемся следующими основными параметрами паротурбинной установки, работающей в составе комбинированной парогазовой установки:
Номинальная мощность турбогенератора:
Nэ=660 МВт;
Начальные параметры пара выбраны сверхкритические:
Р0=24,7 МПа;
t0 =535 ?C;
Давление в конденсаторе:
Рк=5 кПа.
Температура и давление промежуточного перегрева пара:
Рпп=6,5 МПа
tпп=565?С В качестве прототипа выбираем паровую турбину К-660−247 производства ЛМЗ филиала ОАО «Силовые машины». Паровая турбина К-66—247 номинальной мощностью 660 МВт с начальным абсолютным давлением 24,7 МПа предназначена для привода двухполюсного генератора переменного тока ТВВ-660−2, для работы в блоке с прямоточным котлом, использующим органическое топливо. В тепловой схеме, предложенной в данной работе, паровой котел работает на синтез газе, получаемом при газификации угля.
Предусмотрена параллельная работа ГТУ и ПТУ, причем регенерация тепла и подогрев питательной воды осуществляется в котле-утилизаторе. При этом из самой паротурбинной установки планируется производить отборы пара на деаэратор, привод турбонасоса и два ПНД, в которые производится слив дренажей. Также в связи с включением дополнительного газификатора, производящего синтез-газ для ГТУ, планируется отбирать пар из цикла ПТУ с давлением, превышающем давление в газификаторе.
Предварительный термодинамический расчет турбины При выполнении расчетов использовалась программа MathCAD 14, а также готовые библиотеки Water Steam Pro 6. Результаты расчета приведены из интерфейса программы с некоторыми пояснениями.
Исходные данные:
Начальные параметры пара перед турбиной:
Промежуточный перегрев:
Конечное давление за турбиной:
Давление питательной воды после ПН Расход пара на турбопривод питательных насосов:
— мощность турбопривода
— теплоперепад на приводных турбинах Предварительный тепловой расчет турбины Потери давления на паровпуске
Давление в промежуточном перегреве определяется из условия максимальной экономичности по рис. 1.18 в [1]
Потери давления в тракте пром. перегрева составляют Конечная температура:
Энтальпия в конце процесса адиабатного расширения:
Энтальпия на выходе из конденсатора Промежуточный перегрев пара.
Предварительно задаемся КПД:
По i-s диаграмме находим:
Энтальпия пара в конце процесса расшитения в ЦВД (перед пром. перегревом):
Энтальпия пара в конце процесса расшитения в ЦНД (перед конденсатором):
— без пром. перегрева Учет регенеративного подогрева питательной воды Температуру питательной воды определяется как где — температура насыщения при
Но т.к. в данном проекте параметры пара сверхкритические и при давлении 24 МПа вода сразу переходит в перегретый пар, минуя двухфазное состояние, то по рекомендациям выбираем:
По
И
Определяем КПД цикла с бесконечным числом отборов на регенерацию:
Определим термический КПД цикла без регенерации Прирост КПД в идеальном регенеративном цикле составит:
Для числа отборов на регенерацию, равного z по рисунку 1.25 в находим реальный выигрыш в КПД в цикле с регенерацией:
В ходе предварительного расчета были найдены значения располагаемого теплоперепада в турбине, внутренний и термический к.п.д., а также построен процесс расширения пара в турбине в I-S координатах.
Выполненный предварительный термодинамический расчет турбины позволяет произвести более детальные вычисления.
Проведем тепловой расчет турбины при её совместной работе, то есть с включенной газотурбинной частью и реактором газификации. Отдельно производим расчет реактора газификации, входе расчета должно получиться количество газа необходимое для работы газотурбинной части. Расчет газовой турбины производиться в составе ПГУ.
Расчет газовой турбины Для расчета газотурбинной части за основу возьмем новую турбину Siemens SGT5−8000H.
Основные техничесие характеристики, заявленные производителем этой ГТУ таковы:
Мощность номинальная Коэффициент полезного действия Степень сжатия в компрессоре Температура газов после ГТ Массовый расход рабочего газа Для расчета зададимся некоторыми величинами, а некоторые примем из прототипа:
КПД компрессора
КПД камеры сгорания
КПД турбины
1. Определение температуры воздуха после компрессора, К
2. Определение температуры газов после газовой турбины, К
— термический КПД цикла Брайтона
4. Удельная работа ГТУ, кДж/кг
5. Количество энергии, подводимое к ГТУ при сжигании синтез-газа в камере сгорания, кВт Расчет реактора газификации В реакторе предполагается аллотермический процесс паровой газификации угля (с подводом тепла в реакционную зону извне) согласно уравнению реакции:
C + H2O -> CO + H2
Уравнение энергобаланса на 1 кг угля:
Где
— теплоты сгорания углерода, окиси углерода и водорода соответственно, МДж/кг
— энтальпия пара, подаваемого в реактор для процесса газификации Молекулярные массы соответствующих веществ:
— изобарная теплоемкость синтез-газа
— массовая доля углерода в угле
Определяем физическое тепло синтез-газа, МДж/кг.угля:
Теплота аллометрического процесса, МДж/кг.угля:
Теплота сгорания синтез-газа при высокой золоочистке, МДж/кг:
Удельный расход синтез-газа на реактор:
Удельный расход синтез-газа на ГТУ-ступень кг/кг уг:
— удельный расход синтез-газа потребителю Количество синтез-газа на ГТУ, кг/с:
Количество угля на реактор Отпуск водорода потребителю Работа энергоустановки по парогазовому циклу Исходные данные:
Мощность энергетической установки:
— механический КПД
— КПД электрогенератора
— расход в головную часть турбины
— расход в обвод ЦВД из пароперегревателя КУ Расход пара на газогенератор По стехиометрическому соотношению количество Расход пара на трубопривод питательных насосов:
Тогда расход пара на входе в турбину будет равен:
Расход пара в конденсатор Расчет тепловой схемы Предполагается, что на регенерацию идет тот пар, который подается в головную часть турбины.
Давление в барабане КУ Давление в ПГ Давление в деаэраторе Схема установки: ГВП КУ ВД + Д + ГВП КУ НД + 2 ПНД Коэффициент регенерации.
Предварительный расход питательной воды.
Расход пара на собственные нужды котельного
оборудования Расход питательной воды Расход химически очищенной воды (ХОВ), подаваемой в деаэратор.
— утечки из деаэратора Энтальпия химически очищенной воды, поступающей в деаэратор из подогревателя ХОВ.
Давление питательного насоса.
Количество пара, поступившего из концевых уплотнений турбины в конденсатор.
Количество пара, поступившего из передних концевых уплотнений в деаэратор.
Энтальпия питательной воды после повышения давления в ПН.
энтальпия питательной воды за деаэратором:
Расчет перегревателя КУ:
— удельная изобарная теплоемкость продуктов сгорания,
находится по таблицам теплофизических свойств газов температура газов после газовой турбины температура газов перед перегревателем Температура пароводяной смеси при давлении в барабане:
Энтальпия пара в барабане
Энтальпия воды в барабане температура газов перед испарителем Количество теплоты, переданное пару в перегревателе:
Расчет испарителя КУ:
Количество теплоты, переданное пароводяной смеси в испарителе:
Расчет ГВП ВД:
температура газов перед ГВП ВД Для добавочного расхода:
Количество теплоты, переданное воде в газо-водяном подогревателе высокого давления:
Для основного расхода:
Количество теплоты, переданное воде в газо-водяном подогревателе высокого давления:
Расчет деаэратора.
Давление в деаэраторе Давление пара в отборе В точке пересечения изобары и линии процесса находим
Энтальпия греющего пара
Энтальпия воды на выходе из деаэратора Использованный теплоперепад
— средний подогрев воды в ПНД Давление конденсатного насоса:
Энергетический баланс деаэратора:
Расход основного конденсата:
— кпд теплообменника
— расход в отборе на деаэратор Расчет ГВП НД:
температура газов на выходе из КУ Количество теплоты, переданное воде в газо-водяном подогревателе низкого давления:
ПНД 2:
Давление в подогревателе
Энтальпия воды на выходе из ПНД Энтальпия конденсата греющего пара В точке пересечения изобары и линии процесса находим
Энтальпия греющего пара
Энтальпия воды на входе в ПВД Использованный теплоперепад ПНД 1:
Давление в подогревателе Энтальпия воды на выходе из ПНД Энтальпия конденсата греющего пара В точке пересечения изобары и линии процесса находим
Энтальпия греющего пара
Энтальпия воды на входе в ПВД Энтальпия дренажа пара из подогревателя Использованный теплоперепад Расходы пара на ПНД:
ПНД4 и ПНД3 отключены Из отбора 7 на ПНД 2:
Из отбора 8 на ПНД 1:
Отборы 5 и 6 идут на газогенератор с расходом
Расход пара в конденсатор через последнюю ступень турбины.
Мощность турбины с учетом отборов пара на регенерацию:
Электрическая мощность турбины.
Небаланс мощности.
Требуемый дополнительный расход пара на турбину.
Уточненный расход пара на турбоустановку.
Уточненный коэффициент регенерации.
Расчет ПТС с уточненным коэффициентм регенерации.
Расход пара на собственные нужды котельного оборудования Расход питательной воды Расход химически очищенной воды (ХОВ), подаваемой в деаэратор.
— утечки из деаэратора Количество пара, поступившего из концевых уплотнений турбины в конденсатор.
Количество пара, поступившего из передних концевых уплотнений в деаэратор.
Расход основного конденсата:
— расход в отборе на деаэратор Расчет расходов пара на ПНД.
Из отбора 7 на ПНД 2:
Из отбора 8 на ПНД 1:
Мощность турбины с учетом отборов пара на регенерацию:
Электрическая мощность турбины.
Небаланс мощности.
— менее 2%
Коэффициенты отбираемого пара.
Регулирующая ступень:
Принимаем Для одновенечной регулирующей ступенни:
Первый отсек ЦВД:
Параметры за регулирующей ступенью и перед первым отсеком ЦВД:
Параметры за первым отсеком:
Второй отсек ЦВД:
Параметры перед вторым отсеком:
Параметры за вторым отсеком:
ЦСД Параметры пара перед ЦСД:
Параметры пара за ЦСД:
ЦНД Потери в ресивере приняты 2%
Число потоков в ЦНД Вычисляем потери с выходной скоростью, для чего принимаем для последней ступени:
Кольцевая площадь последних лопаток:
Веерность ступени:
— теплоперепад, приходящийся на область влажного пара Максимальный расход пара на ЦНД принимаем по оценке из условия 180 кг/с на один поток:
— предварительое значение общего выхода в конденсатор Вычисляем потери от влажности на последних ступенях:
— к-т, учитывающий эффективность влагоудаления Параметры пара на выходе из ЦНД:
Разбивка теплоперепадов по цилиндрам и отсекам турбины Отборы разбивают проточную часть турбины на 9 отсеков:
Используемые теплоперепады отсеков находятся через вычисленные используемые теплоперепады цилиндров:
Использованные теплоперепады:
Находим приведенный теплоперепад турбины:
Уточняем значение расхода пара:
— расход в головную часть турбины
— расход в обвод ЦВД из пароперегревателя КУ
— общий выход в конденсатор Мощност отсеков составляет:
— с учетом расхода теплоты на газификатор и расхода синтез-газа потребителю.
Уточняем количество отбираемого пара:
Распределение теплоперепадов по ступеням турбины Задаемся числом ступеней в отсеке, средним диаметром первой ступени. Теплоперепад отсека известен. Варьируя степенью реактивности добиваемся лучшего отношения скоростей U/Cф Разбивка теплоперепадов по цилиндрам и отсекам турбины Первый отсек ЦВД:
— расход в головную часть турбины на
Принимаем количество ступеней
Задаемся средним диаметром первой ступени отсека:
Задаемся постоянным корневым диаметром для отсека:
Задаемся средним диаметром регулирующей ступени:
Определяем средний располагаемый теплоперепад на ступень Расчет проточной части произведен в специальном программном приложении, модернизированной программе RTPT. Результаты расчета приведены на рисунках.
Второй отсек ЦВД:
Принимаем количество ступеней
Задаемся средним диаметром первой ступени отсека:
Задаемся постоянным корневым диаметром для отсека:
Определяем средний располагаемый теплоперепад на ступень Отсек ЦСД:
Принимаем количество ступеней
Задаемся средним диаметром первой ступени отсека:
Задаемся постоянным корневым диаметром для отсека:
Определяем средний располагаемый теплоперепад на ступень Отсек ЦНД:
Принимаем количество ступеней
Задаемся средним диаметром первой ступени отсека:
Задаемся постоянным корневым диаметром для отсека:
Определяем средний располагаемый теплоперепад на ступень Задаемся повышенным теплоперепадом на последнюю ступень — 200 кДж/кг Профилирование первой ступени ЦСД
Значения параметров на среднем диаметре:
Располагаемый теплоперепад на ступень:
Расход пара:
Параметры ступени:
Реактивность рабочей решетки в среднем сечении:
в корневом сечении:
Критический перепад давлений для перегретого пара:
К-ты скорости для сопловой и рабочей решеток соответственно:
К-т расхода для сопловой решетки:
для рабочей решетки:
Расчет ступени по среднему диаметру.
Теплопрепад от параметров торможения:
сопловая решетка Скорость на выходе из сопловой решетки:
Параметры пара за сопловой решоткой:
Выходная площадь сопловой решетки:
Эффективный угол выхода из сопловой решетки:
— перепад докритический рабочая решетка Скорости за рабочей решеткой:
Параметры пара за рабочей решеткой:
Выходная площадь рабочей решетки:
Эффективный угол выхода из рабочей решетки:
Расчет ступени с учетом изменения параметров по радиусу.
Разобьем высоту лопатки на элементарные участки:
Задаемся шагом в корневом сечении:
Закон закрутки косвенно выражается уравнением Подберем такое значение m, которое будет удовлетворять вычисленным в корне и на среднем диаметре
сопловая решетка считаем что удельный расход пара остается постояным по высоте лопатки
— совпадает с расчетным значением
Выбираем профиля:
рабочая решетка Скорости за рабочей решеткой:
Параметры пара за рабочей решоткой:
Эффективный угол выхода из рабочей решетки:
Выбираем профиля:
Оценка экономичности ступени.
Расчет на прочность рабочей лопатки первой ступени ЦСД.
1). Расчет пера лопатки на растяжение центробежными силами.
Рабочие лопатки всех ступеней выполняются из стали 15Х12ВМФ Плотность стали
— угловая скорость Окружная скорость посередине длины лопатки Отношение среднего диаметра к длине лопатки Разбиваем лопатку по высоте на элементарные участки:
Площадь стандартного профиля (из атласа турбинных решеток) находим для каждого сечения
Центробежные силы растяжения:
Напряжение растяжения в пере лопатки:
Коэффициент запаса
2). Расчет пера лопатки на изгиб силами пара.
— число лопаток на рабочем колесе Угол установки, находим по атласу профилей:
— плотность пара за рабочей решеткой Коэффициент запаса
3). Расчет на прочность хвостовика лопатки.
— высота рабочей части хвостовика
— ширина хвостовика
— площадь хвостовика
— радиус среднего сечения хвостовика
— сила, действующая на каждую площадку хвостовика Коэффициент запаса
Расчет разъема внешнего корпуса ЦВД на нераскрытие
— расчетное давление, действующее на стык Расчет производится по условию герметичности соединения. Полная сила, растягивающая шпильки при действии расчетного давления, складывается из силы действия среды на крышку и остаточной силы, потребной для сжатия прокладки:
— внутренний диаметр корпуса
— длина корпуса Вертикальную силу, действующую на крышку можно с малой погрешностью определить по формуле Принимаем число шпилек равным:
(H)-осевая сила, действующая на один болт.
Сила затяжки шпилек
(по рекомендациям Л. 2])
Расчетная сила, действующая на шпильку Определим расчетный диаметр шпильки:
(Па) — допускаемое напряжение при растяжении.
Для стали 35ХМ:
(Па)-предел прочности.
(Па)-предел текучести.
— запас по пределу прочности.
— запас по пределу текучести.
(Па) — допускаемое напряжение по пределу прочности.
(Па) — допускаемое напряжение по пределу текучести.
Дальнейший расчет ведем по меньшему значению :
(м) Принимаем диаметр шпильки Описание спроектированной паротурбинной установки Таким образом, в результате выполненных конструкторских, тепловых и прочностных расчетов была спроектирована паровая турбина, удовлетворяющая предъявленным требованиям.
Турбина имеет 7 нерегулируемых отборов пара, предназначенных для подогрева питательной воды в ПВД, основного конденсата — в ПНД, деаэраторе до температуры 280 °C при номинальной нагрузке турбины. Кроме регенеративных отборов, допускаются отборы пара без снижения номинальной мощности на подогрев сетевой воды и на собственные нужды станции. В составе парогазового блока планируются производить отбор после ЦВД на нужды газификатора, для получения синтез-газа, и дальнейшего получения из него водорода методом конверсии.
Турбина представляет собой одновальный четырехцилиндровый агрегат, выполненный по схеме 1ЦВД+1ЦСД+1ЦНДх2.
ЦВД с облопачиванием реактивного типа, с сопловым парораспределением. В конструкции применены высокоэффективные профиля направляющих и рабочих лопаток, развитые надбандажные, диафрагменные и концевые уплотнения, втулочная конструкция обойм концевых уплотнений. ЦВД имеет внутренний корпус, в патрубки которого вварены сопловые коробки. Паропроводящие штуцера имеют сварные соединения с наружным корпусом цилиндра и подвижные — с горловинами сопловых коробок.
После промежуточного перегрева пар по двум паропроводам подводится к двум стопорным клапанам ЦСД, установленным по обе стороны цилиндра, и от них — к четырем регулирующим клапанам, расположенным непосредственно на корпусе ЦСД. ЦСД — двухпоточный, с облопачиванием активного типа. Также применены высокоэффективные профили и уплотнения. Из выхлопных патрубков ЦСД пар по двум трубам подводится к ЦНД.
ЦНД — двухпоточный, по пять ступеней в каждом потоке. Из двух выхлопов после ЦНД отработавший пар поступает в общий конденсатор. Расход охлаждающей воды через конденсатор 64 000 м3/ч. Номинальная температура охлаждающей воды 33 °C.
Ротор ЦНД выполнен сварным. Длина рабочей лопатки последней ступени ЦНД — 1200 мм, средний диаметр этой ступени — 3000 мм. Все роторы имеют жесткие соединительные муфты и по две опоры. Фикспункт валопровода (упорный подшипник) расположен между ЦВД и ЦСД. Для турбины К-660−247 разработаны новые корпуса ЦВД и ЦСД. Новая цельнолитая конструкция устойчива к перекосам и короблению цилиндров. Подвод/отвод пара осуществлен только в нижней половине цилиндров, что обеспечивает большую ремонтопригодность конструкции.
Турбина снабжена паровыми лабиринтными уплотнениями. Новые усовершенствованные уплотнения имеют меньший зазор и работают на витых отжимных пружинах. Также предусмотрены специальные отверстия в обоймах уплотнений для циркуляции пара и их охлаждения. Из концевых каминных камер уплотнений всех цилиндров паровоздушная смесь отсасывается водоструйным эжектором через вакуумный охладитель.
Максимальный расход пара, при указанных начальных параметрах спроектированной турбины, составляет 611 кг/с.
В системе автоматического регулирования и защиты использованы основные конструктивные решения, отработанные на большой части и турбин данной серии.
Назначение и функции системы:
обеспечивает автоматическое регулирование частоты вращения и мощности турбины в соответствии со статической характеристикой и заданием, получаемым из системы автоматического управления энергоблока или от оператора, как при работе в сети, так и на изолированную нагрузку;
поддерживает заданное давление пара перед регулирующими клапанами высокого давления;
обеспечивает противоразгонную защиту турбоагрегата;
на основе контроля термонапряженного состояния элементов турбины вырабатывает команды на ограничение скорости изменения нагрузки и информацию о допустимом изменении нагрузки;
обеспечивает возможность взаимодействия с системой автоматического пуска блока для автоматизации разворота и нагружения турбины;
обеспечивает останов турбины при возникновении аварийных нарушений ее работы.
Система регулирования состоит из органов парораспределения, гидравлической и электронной частей, работа которых взаимосвязана.
Система регулирования обеспечивает возможность изменения нагрузки и синхронизации генератора при любой аварийной частоте в энергосистеме.
С учетом реализации в ЭЧСР ряда алгоритмов, улучшающих динамические характеристики системы регулирования турбины, максимальная частота вращения ротора при сбросе номинальной нагрузки с отключением генератора от сети не превышает 107…108% номинального значения.
Стопорные и регулирующие клапаны разгруженного типа. В корпусе каждого стопорного клапана устанавливается паровое сито.
Для ограничения поступления в ЦВД пара из «холодной» линии промперегрева при работе турбины на клапанах ЦСД (пусковые режимы) на выхлопах из ЦВД установлены два обратных клапана с байпасами. Обратные клапаны управляются индивидуальными сервомоторами.
В режиме пуска турбины разворот и начальное нагружение осуществляется путем подачи пара в цилиндр среднего давления. При этом регулирующие клапаны высокого давления и обратные клапаны на линиях холодного промперегрева остаются закрытыми, параметры пара поддерживаются регуляторами байпасных станций высокого и низкого давления. После достижения нагрузки 15…20% номинального значения, пар подается в ЦВД.
Тепловая схема турбоустановки состоит из 4 подогревателей низкого давления (ПНД), деаэратора скользящего давления и трех подогревателей высокого давления (ПВД). Все регенеративные подогреватели — горизонтального типа (поверхностные). В качестве привода питательного насоса используется турбопривод.
Конденсатор -660КП-35 500−1- поверхностный, двухпоточный, одноходовой со встроенным ПНД-1. Трубная система выполнена из нержавеющей стали ASTM TP304L. Поверхность теплообмена равна 35 500 м²
Повышена надежность соединения «трубка-трубная доска» за счет применения вальцовки трубок с последующей обваркой. Конденсатор имеет 32 000 трубок диаметром 22, 225×0,711 мм длиной 16 м. Масса сухого конденсатора 900 т.
Цилиндр Высокого Давления Для турбин с котлами, работающими на постоянном давлении, в ЦВД применяется сопловое парораспределение с регулирующей ступенью. Проточная часть с 16-ю ступенями реактивного типа имеет постоянный корневой диаметр с направляющими и рабочими лопатками переменной высоты.
Применен цельнокованый ротор. Проточная часть имеет петлевую схему течения пара, обеспечивающую компенсацию осевого усилия. Температурное состояние наружного корпуса ЦВД сохраняется за счет расположения направляющих лопаток во внутреннем цилиндре и 2-х обоймах.
Регулирующая ступень расположена на пониженном диаметре. Тепловой адиабатический перепад на регулирующую ступень на соответствующих режимах значительно уменьшен, чем на турбинах прежних конструкций. Такое перераспределение теплового перепада на ЦВД достигается увеличением числа ступеней, повышения давления в камере регулирующей ступени, и увеличения ее пропускной способности, что способствует повышению экономичности.
Все направляющие и рабочие лопатки выполнены с цельнофрезерованными бандажами (см. рис.), а в рабочих лопатках в бандаж установлены демпфирующие вставки. На периферии рабочих лопаток и в корневой зоне направляющих лопаток применено гарантированно-бесконтактное с чередующими гребнями ротора и статора развитое уплотнение, с большим числом усиков. На бандаже выполнены точеные усики, на роторе — завальцованные. Такая конструкция радиальных уплотнений обеспечивает минимальные протечки и позволяет поддерживать их в условиях длительной эксплуатации практически неизменными.
В статорной части применены надбандажные «сотовые» уплотнения.
Рис. Реактивное облопачивание ЦВД По сравнению со старой конструкцией ЦВД ожидается прирост эффективности проточной части на 4−6%.
Цилиндр Среднего Давления.
Применен цельнокованый двухпоточный ротор СД. Все диафрагмы имеют сварную конструкцию с минимальными перекрышами на корневом и периферийном обводах проточной части.
Обоймы втулочного типа предназначены для применения в цилиндрах ВД и СД турбин средней и большой мощности. Обладающие большей жесткостью со специально спрофилированными камерами отсоса пара новые обоймы не подвержены короблению и обеспечивают плотность системы концевых уплотнений турбины.
Традиционной конструкцией облопачивания турбин является пакетирование рабочих лопаток с клепаным бандажом. В необходимых случаях с целью вибрационной отстройки в рабочих лопатках устанавливаются проволочные связи, как правило, демпферные с круговым замыканием. Длительный опыт эксплуатации облопачивания такой конструкции в турбинах мощностью до 800 МВт свидетельствует о высокой ее эксплуатационной надежности при обеспечении соответствующего уровня экономичности.
Лопатки с цельнофрезерованными бандажами применялись до недавнего времени только на регулирующих ступенях ЦВД.
Кроме того, опыт эксплуатации показал, что применение лопаток с цельнофрезерованным бандажом обеспечивает более высокую надежность турбин при эксплуатации их в экстремальных условиях.
Для обеспечения динамической и статической прочности лопаточного аппарата, особенно при проходных оборотах и переменных режимах, выполнены вибрационные испытания на экспериментальных турбинах и натурные испытания на электростанциях. Небольшой уровень динамических напряжений свидетельствует о высокой вибрационной надежности, но основное подтверждение надежности, как и экономичности проточной части, заключается в многолетнем опыте эксплуатации использованного в турбине облопачивания.
В турбине К-660−247 все рабочие лопатки ЦСД имеют цельнофрезерованные бандажи. Демпферные связи исключены из потока пара, применены специальные развитые надбандажные уплотнения, что, таким образом, повышает экономичность турбины.
Рабочие лопатки первых двух и последней ступени имеют «ёлочные» хвосты с торцевой заводкой, обеспечивающие надежную работу при минимальных габаритах. Остальные ступени имеют Т-образные хвостовики.
Все ступени спроектированы с использованием разработок новых более эффективных профилей направляющих и рабочих лопаток, геометрия которых согласована с газодинамическими расчетами потока на основе многорежимной оптимизации, в т. ч. и при больших D/L.
Цилиндр Низкого Давления Новая конструкция ротора НД предусматривает наличие специальных глухих отверстий в средней части ротора для размещения подбалансировочных грузов. Такая конструкция получила распространение на все выпускаемые ротора НД. Указанное техническое решение позволяет существенно сократить время балансировочных работ в связи с отсутствием необходимости вскрытия цилиндра. Доступ для закрепления грузов обеспечивают специальные люки на цилиндре.
Выхлопная часть ЦНД состоит из двух паровыпускных трактов с осерадиальными диффузорами в сборной камере, имеющей развитую систему внутренних ребер.
Проточная часть ЦНД основывается на отработанной в турбинах 300−500−800 МВт проточной части со стальной лопаткой последней ступени 1200 мм.
Конструкция проточной части НД также основана на аэродинамических и вибрационных исследованиях:
улучшение плавности верхних обводов проточной части низкого давления;
применение рабочих лопаток с цельнофрезерованными бандажами, в том числе и в последних ступенях;
вынесение во всех ступенях, кроме последних, демпферных проволок из проточной части в тело бандажей;
применение улучшенных профилей для направляющих лопаток сварных диафрагм и внутриканального влагоудаления с поверхности лопаток диафрагм последних ступеней.
ТЕХНОЛОГИЧЕСКАЯ ЧАСТЬ В технологической части рассматривалась технология изготовления диафрагмы 18-ой ступени, рассчитаны режимы резания на токарно-карусельную и фрезерную операции.
Диафрагма
Диафрагмы разделяют внутреннюю полость корпуса турбины на отдельные камеры — ступени, в которых располагается по одному диску ротора с рабочими лопатками.
Пар из одной камеры в другую попадает только через сопловые аппараты диафрагм. Сопловые аппараты диафрагм образованы каналами между приваренными лопатками специального профиля. Форма и расположение каналов таковы, что пар, проходя через них, расширяясь, приобретает дополнительную кинетическую энергию и направляется на рабочие лопатки соответствующего диска ротора.
Лопатки всех диафрагм изготовлены из коррозионностойкой стали 18X11МНФВ.
Условия, в которых работают диафрагмы различных ступеней давления турбины, не одинаковы. Это нашло отражение в конструктивном исполнении диафрагм. Сопловые аппараты диафрагм набраны из цельных лопаток. Диафрагмы имеют приваренные к ободу паровые щиты.
Диафрагмы состоят из двух частей. Нижняя часть своими подвесками опирается на нижний корпус турбины и центрируется шпонкой, установленной в пазу корпуса. Верхняя часть диафрагмы размещается в верхней части корпуса турбины и закреплена в ней от выпадания шпонками. Центровка верхней части диафрагмы осуществляется винтами.
В собранном состоянии взаимное положение частей диафрагмы определяется шпонками. Кроме этого, шпонки уплотняют горизонтальный стык частей диафрагмы. Основными частями диафрагмы являются полотно и обод, соединенные между собой диафрагменными лопатками. Равномерность шага лопаток выдерживается при помощи наружного и внутреннего бандажей.
К ободу приварен кольцевой паровой щит с уплотнительными усиками. Паровой щит с усиками обеспечивает максимальную подачу пара с соплового аппарата на рабочие лопатки ротора.
Во внутренней расточке полотна диафрагмы выполнен Т-образный кольцевой паз, в него заводится кольцо уплотнительное, которое состоит из шести сегментов в каждой половине уплотнительного кольца.
Для подъема частей диафрагмы при сборке и демонтаже служат резьбовые отверстия под рым-болты и глухие отверстия на полотне половин диафрагм под специальное приспособление, поставляемое с турбиной.
Определение типа производства Тип производства во многом определяет разработку техпроцесса.
Но т.к. диафрагмы для других турбин, изготовляемых на предприятии, имеют похожую конфигурацию и приблизительно одинаковые типоразмеры, то для разработки технологической части дипломного проекта принимаем мелкосерийное производство.
Анализ технологического процесса на технологичность Технологичность конструкции — это степень соответствия оптимальным производственно-технологическим условиям изготовления при заданном масштабе выпуска.
Технологичность конструкции всегда следует рассматривать как комплексное понятие, учитывающее требования всех фаз и стадий технологического процесса.
В диафрагме расположен сопловой аппарат, который имеет сложную технологическую конфигурацию, и которую выполнить за одно механической или электроэрозионной обработкой трудно. В связи с этим, для улучшения технологичности принята сварная заготовка диафрагмы.
Предварительно, полотно и обод диафрагмы механически обрабатываются из поковки, а лопатки соплового аппарата полностью обработаны и собраны с бандажами сваркой. Сварка производится электронно-лучевая. При этом виде сварки нагрев материала практически отсутствует, что приводит к отсутствию деформации при сваривании детали.
Наличие горизонтального разъёма диафрагмы приводит к сложности изготовления детали.
Первой базой для механической обработки соплового аппарата необходимо использовать элементы проточной части диафрагмы, что усложняет механическую обработку и требует специальных приспособлений или выверки на станке.
Так как диафрагма является телом вращения и в достаточной мере технологичной и малосерийной, то выбираем технологический процесс с максимальной концентрацией деталей.
Технологический процесс механической обработки включает 24 операции. Из них основными являются фрезерная, токарно-карусельная и расточная операции.
Приспособления, используемые для фрезерных, токарных и расточных операций, являются универсальными. Станки, в основном, все с ЧПУ: карусельный, продольно-фрезерный, горизонтально-расточной и базируются с максимальной выверкой. Это всё говорит о возможности быстрой переналадки линии.
Расчёт припусков Диафрагма — сварная конструкция, полученная электронно-лучевой сваркой.
Она поступает на мехобработку сваренная согласно чертежу, термообработанная с заполненной картой контроля до этапа мехобработки с клеймами БТК, маркированная согласно чертежу.
При сборке диафрагмы весь крепёж ставится на графитомеднистой смазке.
Перед установкой детали на станок и при снятии со станка предохранить выступающую лопатку и предъявить БТК сохранность лопатки.
Габаритные размеры: o 1078−0,5 — наружный диаметр, мм
o 482Н7(+0,06) — внутренний диаметр, мм
70 — толщина, мм Минимальный припуск при последовательной обработке противолежащих поверхностей:
2*Zmin=2*[(Rz+h)i-1+ДУi-1+Еi]
Минимальный припуск при обработке наружных поверхностей вращения:
2*Zi min=2*[(Rz+h)i-1+(Д2Уi-1+Е2i)½]
где Rz i-1 — высота микронеровностей на предыдущем переходе.
hi-1 — глубина дефектного слоя на предыдущем переходе.
ДУi-1 — суммарное значение пространственных отклонений до элементарной поверхности.
Еi — погрешность установки заготовки на выполняемом переходе.
ДУ=(Д21+Д22)½,
где Д1 и Д2 — пространственные отклонения.
Для o 482(+0,06):
Отклонение плоскостей торцевой поверхности: Д1=40 мкм
Отклонение постоянства размера в поперечном сечении: Д2=30 мкм
Днар=(Д21+Д22)½=(402+302)½=50 мкм
Погрешность установки ;
Е: Е=(Е2б+Е2з)½
Где Еб — погрешность базирования.
Ез — погрешность закрепления.
Значения Е для данных условий базирования и закрепления вписаны в таблицу 1.
Максимальный припуск на обработку:
Zi max=Zi min + Tdi-1 — Tdi ;
2*Zi max=2*Zi min + TDi-1 — TDi ,
где и — допуск по размеру на предшествующем переходе.
и — допуск по размеру на выполняемом переходе.
Наименьший предельный размер:
dmin i-1=dmin i + Zmin i
Dmin i-1=Dmin i + 2*Zmin i
Наибольший предельный размер:
dmax i-1=dmin i-1 + Tdi-1
Dmax i-1=Dmin i-1 + TDi-1
Результаты расчёта сведены в таблицу 1:
Таблица заполняется с использованием.
Таблица 1
Поверхность для расчёта припуска — 482А (+0,06) | ||||||||||||
Технологический маршрут обработки | Элементы припуска, мкм | Расчётный припуск, 2*Zmin, мкм | Расчётный мин. Размер, dmin, мм | Допуск на изготовление, Td, мкм | Принятые размеры по переходам, мм | Полученные предельные принятые размеры, мкм | ||||||
Rz | h | Д | Е | dmax | dmin | 2Zmax | 2Zmin | |||||
Сварная | ; | ; | ||||||||||
Черновое точение | ; | ; | 482,03 | 500,3 | ||||||||
Чистовое точение | ; | ; | 482,06 | 482,72 | 482,4 | |||||||
Проверка:
Td2 — Tdg=2*Z0 max — 2*Z0 min=2000;60=6940−5000=
1940=1940
2*Z0 max=У2*Zmax= 6940 мкм
2*Z0 min=У2*Zmin= 5000 мкм Выбор заготовки Предварительно, полотно и обод диафрагмы механически обрабатываются из поковки, а лопатки соплового аппарата полностью обработаны и собраны с бандажами сваркой. Сварка производится электронно-лучевая. При этом виде сварки нагрев материала практически отсутствует, что приводит к отсутствию деформации при сваривании детали.
Наладка — Продольно-фрезерная. Операция 426 300.
Установить 2 половины на столе станка разъёмом к шпинделю на подкладки, выставить по подрезной риске и плоскости разъёма, закрепить.
Расчёт режимов резания Фрезеровать выступающие части бандажей над торцем обода и полотна до плоскости разъёма.
Диаметр фрезы:
Dфр=(1,25?1,5)*B,
где В — ширина фрезерования, В=100 мм.
Dфр=1,25*100=125 мм Минутная подача:
Sм=S*n=Sz*z*n, мм/мин Где n — частота вращения фрезы, об/мин;
z — число зубьев фрезы; =12
Sz — подача на 1 зуб;
S — подача на 1 оборот, мм/об;
Sz=S/z=0,15/12=0,0125 мм.
Скорость резания:
мм Где V — окружная скорость фрезы;
Cv=64,7, y=0,2
q=0,25, u=0,15
x=0,1, m=0,2, p=0,
Из табл.40 (2 стр.290) T=180 мин. — период стойкости.
kv=kмv*kпv*kuv
Где kмv — коэффициент, учитывающий качество обрабатываемого материала.
kпv — коэффициент, учитывающий состояние поверхности заготовки.
kuv — коэффициент, учитывающий материал инструмента.
Из табл.3 (2 стр.262): kмv=1,0
Из табл.6 (2 стр.263): kпv=1,0
Из табл.5 (2 стр.263): kuv=1,0
kv=1,0*1,0*1,0=1,0
м/мин Частота вращения: об/мин Принимаем: n=200 об/мин Минутная подача: Sм=S*n=0,15*200=30 мм/мин Сила резания:
— окружная сила из табл.9 (2 стр.264):
из табл.41 (2 стр.291): Cp=825, y=0,75, q=1,3, x=1, u=1,1, w=0,2
Н
Составляющая, по которой рассчитываем оправку на изгиб:
Pyz=(P2y+P2z)½, Н Где Py — радиальная сила подачи, Н Из табл.42 (2 стр.292): Py/Pz=0,35, Py =Pz*0,35=534,88 Н
Pyz=(534,882+1528,232)½=1619,13 Н Крутящий момент на шпинделе:
Н*м Мощность резания (эффективная):
кВт Фрезеровать плоскость разъёма, не касаясь торцев выступающей лопатки.
Т.к. размеры близкие и обработка схожая, то задаёмся таким же режимом резания. Результаты расчёта приведены в таблице на чертеже наладки.
Нормирование операции Штучное время обработки детали:
Тшт=tо+tв+tабс+tп,
операция 426 300. Продольно-фрезерная. Станок 6Н610Ф1.
Основное время на выполнение операции:
где L — длина обрабатываемой поверхности.
l — Длина врезания и перебега инструмента.
i — Число рабочих ходов.
So — Подача на 1 оборот, мм/об.
n — Частота вращения заготовки или инструмента, об/мин.
L+l=2507,18 мм
i=1,
So=0,15 мм/об,
n=200 об/мин. (см. режимы резания)
мин Машинно-вспомогательное время tмв (мин), затрачиваемое:
на одновременное перемещение рабочих органов станка по осям Z и X:
ускоренное (на длине 2507,18 мм) — 1,866 мин установочное — 3,75 мин установочное (холостое) в зоне резания — 2,15 мин ускоренное поперечное (на длине) — 7,8 мин на поворот револьверной головки на 1 позицию — 1,9 мин установка детали — 6 мин.
tабс п на обслуживание рабочего места, личные потребности в % от оперативного времени — 15%:
tмв= 1,866+3,75+2,15+7,8+1,9+6=23,466 мин.
tабс п=tо*0,15=12,53 мин
tшт=83,57+23,466+12,53=119,56 мин = 2 ч.
Наладка — Токарно-карусельная. Операция 411 300.
Установить диафрагму стороной паровпуска вверх, выверить по подрезной и окружной рискам и линии разъёма с точностью до 0,2 мм, под полотно установить домкраты, проверить установку диафрагмы по наружному диаметру внутреннего бандажа согласно чертежу, установить индикатор в резцедержатель, закрепить, настроить с натягом в точках у разъёма, закрепить деталь не пережимая, допустимая деформация не более 0,05 мм.
Расчёт режимов резания Подрезать торец диафрагмы.
Глубина резания: t=1,5 мм Подача мм/об: S=1,5 мм/об Скорость резания:
Из табл.17 (2 стр.269): Cv =340, x=0,15, y=0,45, m=0,2 T=50 мин, kv=1
м/мин Сила резания:
Из табл.22 (2 стр.273)
Pz | Py | Px | ||
Cp | ||||
X | 0,9 | |||
Y | 0,75 | 0,6 | 0,5 | |
n | — 0,15 | — 0,3 | — 0,4 | |
kp | ||||
Н
Н
Н Частота вращения: об/мин Принимаем n=50 об/мин.
м/мин
Н
Н
Н Мощность резания: кВт Точить наружный диаметр o 1078−0,5
Т.к. размеры близкие и обработка схожая, то задаёмся таким же режимом резания. Результаты расчёта приведены в таблице на чертеже наладки.
Точить диаметр o 1042−0,5
Т.к. размеры близкие и обработка схожая, то задаёмся таким же режимом резания. Результаты расчёта приведены в таблице на чертеже наладки.
Подрезать торец 60
Т.к. размеры близкие и обработка схожая, то задаёмся таким же режимом резания. Результаты расчёта приведены в таблице на чертеже наладки.
Подрезать торец 13−0,12−0,17
Т.к. размеры близкие и обработка схожая, то задаёмся таким же режимом резания. Результаты расчёта приведены в таблице на чертеже наладки.
Переустановить прихваты и точить o290А+0,052
Т.к. размеры близкие и обработка схожая, то задаёмся таким же режимом резания. Результаты расчёта приведены в таблице на чертеже наладки.
Фасонное точение R3
Глубина резания: t=1 мм Подача мм/об: S=0,03 мм/об Скорость резания:
Из табл.17 (2 стр.269): Cv =22,7, y=0,50, m=0,3 T=55 мин, kv=1
м/мин Сила резания:
Из табл.22 (2 стр.273)
Pz | Py | Px | ||
Cp | ; | ; | ||
X | ; | ; | ||
Y | 0,75 | ; | ; | |
n | ; | ; | ||
kp | ; | ; | ||
Н Частота вращения: об/мин
Принимаем n=18 об/мин
м/мин Мощность резания: кВт Нормирование операции Штучное время обработки детали:
Тшт=tо+tв+tабс+tп,
операция 4 113 000. Токарно-карусельная. Станок 1516Ф1.
L=806+44+60+13+17+290=1230 мм
i=1, So=0,4 мм/об, n=51 об/мин.
tо=1230*1/50*0,4=61,5 мин фасонное точение: i=1, So=0,015 мм/об, n=18 об/мин, L=3 мм
tо=3*1/18*0,015=69,8 мин
tмв= 5,88+10,4+6,1+2,3=24,68 мин.
tабс п =tо*0,15=(60,4+69,8)*0,15=19,5 мин.
tшт=130,2+24,68+19,5=174,4 мин.= 2ч. 54 мин.
Описание карусельного станка 1516Ф1
Его параметры и характеристики: станок одностоечный, с одним вертикальным суппортом с 5-ти позиционной револьверной головкой и боковым суппортом с 4-х резцовым поворотным резцедержателем. Этот станок с устройством цифровой индикации (исполнение Ф1). Позволяет выполнить обтачивание и растачивание цилиндрических, конических и фасонных поверхностей тел вращения; обтачивание торцовых поверхностей; подрезание уступов; прорезание кольцевых канавок и отрезание; сверление и рассверливание, зенкерование и развёртывание отверстий.
Наибольшие параметры обрабатываемой заготовки:
диаметр — 1600 мм высота — 1000 мм масса — 6300 кг Наибольшее перемещение вертикального суппорта:
горизонтальное — 950 мм вертикальное — 700 мм Диаметр планшайбы — 1400 мм Частота вращения планшайбы — 40 — 200 об/мин Подача суппорта вертикальная и горизонтальная — 0,1 — 1000 мм/мин Мощность главного электродвигателя привода — 30 кВт Габаритные размеры:
длина — 3170 мм ширина — 3025 мм высота — 4100 мм Масса: 19 200 кг.
Описание продольно-фрезерного станка 6Н610Ф1
Размер рабочей поверхности стола — 200×500
Наибольшие перемещения:
вертикального стола:
продольное — 320
вертикальное — 320
шпиндельной бабки — 200
гильзы вертикальной головки — 60
Частота вращения шпинделей, об/мин:
горизонтального — 40−2240
вертикального — 40−2240
Продольная, поперечная и вертикальная подачи с бесступенчатым регулированием, мм/мин — 10−600
Частота вращения быстроходной головки, об/мин — 104−5000
Мощность электродвигателя привода главного движения, кВт — 1,5
Габаритные размеры:
длина — 3700
ширина — 1975
высота — 1695
Масса, кг — 1452
Описание приспособления Приспособление для шабровки горизонтальной плоскости диафрагмы состоит из горизонтальной плиты поз.2, к которой крепятся угольники поз.4 (2 шт.) и поз.5 (2 шт.). С помощью угольников поз.4 и поз.5, шнопорта поз.7 и болта поз.1 (2 шт.) диафрагма фиксируется и предотвращается от сдвигов. Шнопорт имеет рукоятку поз.8, с помощью которой он закручивается. Два угольника друг относительно друга фиксируются штырями поз.6 (2 шт.)
Положение горизонтальной плиты на столе станка фиксируется с помощью 4 болтов поз.3.
Таким образом, затяжка болтов поз.1,6 и штопорта поз.7 фиксирует диафрагму и предотвращает её от перекосов.
Приспособление для закатки усиков в диафрагме состоит из оправки с роликами, к державке поз.1 крепятся с помощью шайбы поз 2. и гайки поз.3 ролик закатной правы или левый поз.5 между ними ставиться упорная шайба поз.4, ролик крепится с помощью втулки поз.7, кручивается винт поз.9, прижимная шайба поз.8 держит иглы поз.10 для предотвращения трения и лучшего вращения оправки и затки усиков.
Приспособления сделаны из конструкционной стали.
Расчёт прижимных усилий Сдвигу детали под действием силы резания R препятствуют силы трения, возникающие в местах контактов детали с зажимными механизмами.
Сила зажима определяется по формуле (2 стр.85):
где к=к0*к1*к2*к3*к4*к5*к6=1,5*1*1*1,2*1,3*1*1=2,34
к — коэффициент запаса.
к — коэффициент гарантированного запаса.
к — коэффициент, учитывающий увеличение сил резания из-за случайных неровностей.
к — коэффициент, характеризующий увеличение сил резания из-за затупления инструмента.
к — коэффициент, характеризующий увеличение сил резания при прерывистом резании.
к — коэффициент, характеризующий увеличение сил резания из-за постоянства силы закрепления в зажимном механизме.
к — коэффициент, характеризующий эргономику ручных зажимных механизмов.
к — коэффициент, который учитывают при наличии моментов, стремящих повернуть деталь.
R — сила резания. R=2967 Н
f1, f2 — коэффициент трения: f1=f2=0,2
Н
Расчёт винтового элементарного зажима:
мм где d — диаметр винта, мм уp — напряжение растяжения (сжатия) винта, МПа
ИССЛЕДОВАТЕЛЬСКАЯ ЧАСТЬ Производство водорода методом газификации угля Быстрое развитие производственных сил, связана с большим расходом топлива и углеводородного сырья, неравномерность и сложность добычи горючих ископаемых сопровождается ростом цен и увеличение транспортных расходов и материальных затрат.
В химической индустрии наиболее неотложной задачей является перевод угольной базы производства связанного азота, синтетического метанола. Этот перевод сулит уменьшать крупнотонажность химических предприятий от сезонных колебаний в снабжении природным газом, освободить от применения значительных количеств жароупорных легированных сталей.
Переход на твердое топливо несёт и ряд негативных явлений для промышленного производства. Анализ, подготовка производства и преодоление трудностей является задачей науки.
Работа с твердым топливом в аппаратурно-техническом плане сложнее, чем с жидкими и газообразными углеводородами. Добыча и транспортировка твердого топлива, его сушке, измельчение, подача в газогенератор, удаление золы, очистка технологического газа все это требует помощи механических и технологических приспособлений. Кроме того, все технологические операции требуют энергетических затрат.
Таким образом, переход на новую сырьевую базу связан: с ростом удельных капитальных затрат, уменьшение КПД процесса, увеличение расхода рабочей силы на тонну конечного продукта. Но с какими бы затратами не был связан этот переход, его нельзя рассматривать как альтернатива, это неизбежная необходимость. И чем раньше будет развита подготовка к этому переходу, тем он пройдет более безболезненно. Наиболее важным звеном при решении задачи — это проблема газификации твердого топливаполучение генераторного газа.
Газификация угля — производство горючего (технологического) газа при неполном окислении органической массы угля, имеет давнюю историю с периодами бурного развития и спадами. Впервые горючий газ из угля получил англичанин Мэрдок в 1792 г. как попутный продукт при производстве «светильного масла». К 50-м годам XIX в. практически во всех крупных и средних городах Европы и Северной Америки действовали газовые заводы для производства отопительного, бытового и светильного газа. Это был «золотой век» газификации угля. Начиная с 60-х годов XIX в., все более серьезную конкуренцию углю начинает оказывать нефть. В начале 1960;х годов разработка месторождений дешевой нефти на Ближнем Востоке и в Западной Сибири привела практически к полной ликвидации этой отрасли промышленности. Сохранились лишь небольшие островки в уникальных регионах. Например, в ЮАР углепереработка (главным образом на основе газификации угля) стала крупной промышленным сектором из-за эмбарго на поставку нефти. Началось триумфальное шествие нефти. Однако уже в 1972 г. оно омрачилось первым «энергетическим кризисом», который по существу был спровоцирован на политической основе странами-участниками ОПЕК. Мировые цены на нефть подскочили с 5−7 до 24 долл. США за баррель (1 т сырой нефти сорта Brent? 8,06 баррелей), и стало ясно, что углепереработку списывать в архив рано, так как в большинстве развитых стран много угля и мало или совсем нет нефти. Интересно заметить, что если бы не этот первый «энергетический кризис», то крах социалистической системы мог наступить еще в 1970;е гг. Активный приток «нефтедолларов» продлил агонию СССР. Этот кризис преподнес цивилизованному миру очень важный урок. Во-первых, все осознали, что запасы углеводородного сырья распределены крайне неравномерно и неудобно, и, во-вторых, эти запасы — исчерпаемы. Запасы же угля и других твердых горючих ископаемых — нефтяных сланцев, битумных песков, торфа и т. п. распределены более равномерно, и сроки их исчерпания оценивается многими сотнями лет. Но самый главный результат этот кризиса заключается в активизации работ по энергосбережению.
В середине 1980;х годов интерес к углепереработке пошел на убыль. причин несколько. Во-первых, политикой «кнута и пряника» США установили контроль над странами — производителями нефти. Наиболее амбициозных (Ирак, Иран) наказали в назидание другим. В результате рост цен на нефть замедлился. В течение 1980;х годов цены на нефть снизились с 40 долл. США за баррель (что соответствует примерно 65 долл. США за баррель в современных ценах с поправкой на инфляцию) до минимального уровня 9,13 долл. США за баррель в декабре 1998 г. и в настоящее время колеблются в «коридоре» 17−27 долл. США за баррель.
Во-вторых, эффективно сработали государственные программы энергосбережения, что в конечном итоге привело к снижению темпа роста потребления нефти и природного газа. С середины 1970;х годов энергоемкость единицы ВВП в развитых странах снизилась на 22%, а нефтеемкость на 38%.
В-третьих, динамичное развитие нефтегазовой отрасли и масштабные работы по разведке новых месторождений нефти и газа показали, что запасы углеводородного сырья на самом деле значительно больше, чем предполагалось. Последние 20 лет ежегодный прирост разведанных запасов нефти и газа опережает их потребление, и прогнозные сроки исчерпания регулярно отодвигаются. По достаточно авторитетным данным глобальную замену нефти углем следует ожидать после середины XXI в., а замену природного газа углем — к концу века. Если, конечно, не произойдет прорыва в развитии технологии ядерного синтеза.
В-четвертых, ни одна из разрабатываемых технологий не позволила повысить рентабельность процесса получения жидкого топлива из угля в такой степени, чтобы «синтетическая нефть» могла конкурировать с природной нефтью.
В итоге «эпоха угля» не наступила и интерес к переработке угля уменьшился. Большинство программ было свернуто, а оставшиеся — радикально урезаны.
Более десятка проектов были завершены на стадии 5-летней готовности, т. е. при изменении конъюнктуры рынка углеводородного сырья можно в течение 5 лет на основе демонстрационных установок производительностью 10−60 т/ч по углю развернуть промышленное производство. Если от коммерческого использования технологий прямого и непрямого ожижения угля в конце 1980;х гг. пока отказались, то интерес к газификации угля хотя и уменьшился, но не прекратился.
Например, в ряде регионов, где природного газа нет или мало (Северная Америка, Китай и др.), использование газа из угля для синтеза метанола и аммиака экономически оправдано и построен ряд промышленных предприятий. На рис. 1 приведены данные по мировому производству газа из твердых топлив с 1970 г., а в табл. 1.2 — структура его потребления.