Методы и средства защиты РЭС от ударных воздействий
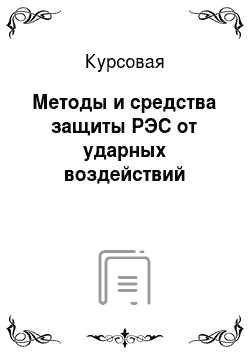
Во-вторых, движение блока на нелинейных амортизаторах более сложно — несиносуидально по времени. Такое периодическое сложное движение можно представить в виде суперпозиции нескольких гармонических составляющих. Таким образом, при замене линейного амортизатора нелинейным помимо основной низшей гармонической составляющей колебаний, частота которой равна частоте внешних воздействий, появляются более… Читать ещё >
Методы и средства защиты РЭС от ударных воздействий (реферат, курсовая, диплом, контрольная)
1. Основные понятия об ударе
2. Защита конструкций РЭС от воздействий ударов
3. Повышение жесткости конструкций
4. Защита конструкций с помощью амортизаторов и демпферов
5. Повышение прочности конструкций
6. Ударопрочные конструкции крепления радиоэлементов и узлов
6.1 Способы крепления соединительных проводов
6.2 Конструкции креплений конденсаторов
6.3 Крепление резисторов
6.4 Ударопрочные шасси и каркасы
7. Расчеты механических нагрузок
7.1 Статический расчет амортизаторов
7.2 Упаковочная тара для транспортирования
7.3 Ударная прочность элементов Список использованных источников
1. Основные понятия об ударе
В механике ударом твердых тел друг о друга называют такое движение, при котором за очень малый промежуток времени происходят конечные изменения количества движения твердых тел.
При ударе происходит конечное изменение скорости v, а следовательно, и количества движения mv за весьма малый промежуток времени, называемый длительностью импульса ф. Величина силы взаимодействия тел за время их соударения определяется импульсом силы или ударной силой
где F (t) — мгновенное значение силы, действующей при ударе.
Ударный процесс характеризуется импульсом силы, длительностью импульса, коэффициентом восстановления скорости и формой ударного импульса. Ударные импульсы различают простой (скоростной удар, вызываемый изменением ускорения, скорости, смещения) и сложной формы (импульсы, которые могут быть представлены энергетическим спектром удара).
2. Защита конструкций РЭС от воздействий ударов
Радиоэлектроника и вычислительная техника применяются практически во всех отраслях народного хозяйства для выполнения однотипных задач — сбора, обработки и выдачи информации. но условия эксплуатации в разных областях могут быть неодинаковыми. Поэтому при изготовлении аппаратуры различными предприятиями, объединениями складываются определённые приёмы конструирования и типовые конструкции. Типовые конструкции многократно испытаны, проверены многолетней практикой, и нет сомнений в их высокой надежности. Они вошли в соответствующие стандарты и отступление от них рассматривается как нарушение закона.
Постоянное расширение сферы применения аппаратуры, новые условия эксплуатации, новые требования заказчиков приводят к необходимости пересмотра сложившихся приёмов конструирования и к разработке принципиально новых конструкций.
Каждая новая идея, новое конструкторское решение должно вначале проверяться теоретически — с помощью имитационной системы, и только после этого, если проверка дала положительный результат, можно переходить к изготовлению макетов и опытных образцов и проводить натурные испытания.
Мероприятия конструктора по защите РЭС от ударных нагрузок сводится к выбору соответствующих материалов, ударопрочному конструктивному исполнению и использованию элементов защиты. При разработке ударопрочных РЭС, кроме прочностных свойств используемых материалов, большое значение имеет их пластичность, причём на основе материалов с повышенной пластичностью элементы конструкций характеризуются большей ударопрочностью. Материалы с малой степенью пластичности разрушаются при незначительных деформациях, и их применение в составе ударопрочной аппаратуры следует ограничивать. К таким материалам относят, например, литьевой алюминий, фарфор, силикатное стекло и др. Однако стремление в наибольшей степени использовать прочностные свойства материалов приводит к повышению уровней возникающих механических напряжений и увеличению деформаций из-за недостаточной жёсткости конструктивных элементов. В этом случае нарушается расчётное взаимодействие элементов конструкции — ослабляются контакты, изменяется сопротивление контактных пар соединителей, возможно соударение близко расположенных элементов конструкции и т. д. Деформацию изгиба элементов конструкций блоков при воздействии ударных нагрузок можно уменьшить выбором соответствующего сечения и его формы, применением дополнительных точек крепления, ребер жесткости для печатных плат. Эффективными мерами защиты являются также использование клеевого соединения компонентов для их присоединения к печатным платам, покрытие лаком печатных плат совместно с размещёнными на их поверхности компонентами, заливкой компаундами.
Реакция конструктивных элементов блоков на ударные нагрузки оценивается с помощью методов сопротивления материалов и теории упругости после представления элементов конструкций моделями в виде балок и пластин с определёнными способами закрепления сторон в соответствии с реальной конструкцией.
Для защиты блоков аппаратуры от ударных нагрузок используют стандартные виброизоляторы. Низкочастотные виброизоляторы, обладающие меньшей жесткостью, могут быть доведены ударной нагрузкой до упора, и защита окажется неэффективной. В системах противоударной виброизоляции используются виброизоляторы с нелинейными силовыми характеристиками.
3. Повышение жесткости конструкций
радиоэлемент надежность ударопрочный демпфер Предположим, что с помощью численных экспериментов проверяется действие на конструкцию низкочастотной вибрации. Диапазон частот источника вибрации fн…fв охватывает частоты до 200…300 Гц, и более высокочастотных воздействий на конструкцию нет. Предположим далее, что нижняя резонансная частота конструкции f1 попадает в интервал fн< f1<fв. Следовательно, неизбежно возникновение резонанса на частоте f1, что и вызывает отказы или сбои. В этом случае можно попытаться повысить нижнюю резонансную частоту конструкции так, чтобы выполнялось условие f1>fв. Тогда резонансов в диапазоне fн…fв не будет. Повысить резонансные частоты конструкции можно двумя путями: или уменьшить массы деталей, или увеличить жесткость упругих звеньев несущих конструкций.
Формула для резонансной частоты блока на амортизаторах
(1)
показывает, что для повышения резонансной частоты вдвое необходимо уменьшить массу или увеличить жесткость в 4 раза. Эта зависимость справедлива только для пружинного маятника. Но её можно использовать для качественных оценок и более сложных конструкций.
Уменьшение массы деталей всегда целесообразно, и всякую такую возможность необходимо использовать. Но вряд ли удаётся уменьшить массу всех деталей в такой степени.
Другое дело — жесткость конструкции. Здесь возможности более широкие. Рассмотрим формулу
(2),
где hz — толщина пластины.
Следует обратить внимание на то, что в формуле (2) отражена зависимость (1). Действительно, если считать, что жесткость пластины пропорциональна модулю Юнга Е, а масса пропорциональна плотности материала с, то зависимость (1) выполняется с точностью до некоторого постоянного множителя. То же самое можно сказать про любую конструкцию; например, увеличение модуля Юнга всех деталей конструкции в 4 раза приводит к увеличению любой резонансной частоты в 2 раза. Но жесткость конструкции зависит не только от модуля Юнга материалов, но и от размеров и конфигурации деталей.
Таким образом, можно повысить нижнюю резонансную частоту за счёт увеличения толщины пластины. Отрицательный эффект от такого увеличения толщины пластины — увеличение расхода материалов и массы изделия.
Ещё больший эффект даёт уменьшение размеров платы и увеличение жесткости крепления. Однако и здесь имеется отрицательный эффект — уменьшение полезной площади для размещения навесных элементов. Поэтому у конструктора чаще всего имеется один путь повышения нижней резонансной частоты — применение более жесткого крепления.
Случаи шарнирного закрепления по контуру и жесткого закрепления по контуру можно считать предельными случаями: шарнирное — самым мягким, а жесткое — самым жестким креплением. Между ними лежат крепления с помощью различного числа винтов или болтов, расположенных по контуру (рис. 1).
Если увеличение жесткости крепления по контуру даёт недостаточный эффект, то используют различные виды дополнительного крепления по площади пластины. И здесь возможности достаточно широкие. В зависимости от формы несущих конструкций применяют дополнительное крепление винтами в различных точках вблизи центра (рис.2).
Для увеличения жесткости используют также дополнительную арматуру (рис. 3). В пределе если считать арматуру по сравнению с пластиной абсолютно жёсткой, то фактически вместо одной пластины нужно рассматривать четыре пластины меньших размеров. Эта мера повышает резонансные частоты в 4 раза. Фактически ребра жесткости и арматура имеют конечную жесткость, и эффект от их применения снижается. Дальнейшее повышение жесткости пластинчатых конструкций за счёт дополнительных ребер, арматуры и других дополнительных деталей не всегда даёт положительный результат.
Считается, что если нижняя резонансная частота конструкции вдвое превышает верхнюю частоту внешних воздействий, f1>2fв, то это является достаточной гарантией от возникновения в конструкции резонансных явлений.
Если опасность возникновения резонансных явлений остаётся, то повышение жесткости конструкции может привести к отрицательным результатам и нужно позаботиться не о повышении жесткости, а о повышении прочности конструкции.
4. Защита конструкций с помощью амортизаторов и демпферов
Если рассматривать блок как жесткое недеформируемое тело, то при установке его на амортизаторы получается колебательная система, в общем случае имеющая шесть степеней свободы. Обычно рассматривается только одна степень свободы — в направлении, наиболее опасном с точки зрения внешних воздействий. Тогда резонансная частота щ0 определяется формулой (1). Эта частота обычно является довольно низкой и не превышает 100 Гц. В этом случае весь диапазон частот внешних возмущений оказывается выше щ0. И только при условии
сказывается защитное действие амортизатора. Амплитуда колебаний блока уменьшается по сравнению с амплитудой колебаний точек крепления амортизаторов к источнику вибрации в k раз
k=f/f0.
То, что блок аппаратуры не является абсолютно жестким и сам деформируется при колебаниях на амортизаторах, практически мало влияет на защитные свойства амортизаторов и, кроме того, это влияние положительно, поскольку установка более мягкого блока на амортизаторы уменьшает резонансную частоту f0. С другой стороны, установка конструкции на амортизаторы изменяет резонансные частоты самой конструкции. Все резонансные частоты становятся несколько ниже. Стремление повысить эффективность применения амортизаторов привело к изобретению множества различных конструкций амортизаторов:
1. Амортизаторы с дополнительными пружинами (рис. 4). Дополнительные пружины имеют длину, меньшую чем у основной пружины, и вступают в действие при увеличении амплитуды колебаний. В результате получается нелинейная ступенчатая характеристика жесткости. Дополнительные пружины могут устанавливаться как рядом с основной, так и внутри её.
2. Амортизаторы с коническими пружинами, позволяющими плавно изменять жесткость с ростом растяжения и сжатия (рис. 5). У таких пружин наружные витки, которые имеют больший диаметр, имеют меньшую жёсткость. Поэтому при небольшом сжатии работают только эти большие витки. При увеличении сжатия большие витки касаются нижней жесткой поверхности и начинают сжиматься верхние витки меньшего диаметра и большей жесткости. Поскольку амортизатор имеет начальное сжатие под действие массы блока, то аналогичный процесс получается и при растяжении амортизатора, когда начинают растягиваться сначала витки меньшего диаметра, а затем большего. В результате при растяжении жесткость плавно уменьшается.
3. Проволочно-пружинные (сетчатые) амортизаторы (рис. 6), получающиеся прессованием упругого элемента из тонкой спирали. В качестве материала спирали используется тонкая проволока из легированной стали или бериллиевой бронзы. Трение проволоки при деформации упругого элемента создаёт большие потери энергии в упругом элементе. При больших деформациях, например при растяжении, отдельные спирали вытягиваются в одном направлении. При этом получается картина такая же, как и при деформации материалов с длинными волокнами, например резины. Поэтому материал упругого элемента сеточного амортизатора стали называть металлической резиной.
Основной недостаток металлической резины — непостоянство во времени её упругих свойств. Поэтому промышленностью выпускаются пружинно-сеточные амортизаторы (рис. 7), в которых роль упругого элемента выполняет пружина 1, а роль демпфера — металлическая резина 2.
4. Тросовые амортизаторы. Металлический трос, или канат, свитый из множества тонких жил, при растяжении и особенно при изгибе обладает свойствами упругого тела с большими потерями энергии на трение между отдельными жилами. Эти свойства изменяются в широких пределах в зависимости от материала жил, их диаметра, способа изготовления троса и способа использования его в качестве амортизатора. Поэтому возможно большое разнообразие конструкций и характеристик тросовых амортизаторов (рис. 8).
Заметим, что все амортизаторы, в которых используется трение металлических частей, обладают тем недостатком, что металлы истираются, образуя металлическую пыль. Поэтому приходится принимать меры предосторожности, чтобы эта пыль не попадала на электрические цепи.
5. При малой массе блоков стали применять амортизаторы с распределёнными параметрами. Такими амортизаторами и демпферами можно считать амортизационные прокладки, а также заливки и засыпки аппаратуры различными синтетическими материалами. Амортизационные прокладки применяют для защиты от ударов и вибраций как целых блоков (рис. 9), так и отдельных частей внутри блока (рис. 10).
К материалу амортизационных прокладок предъявляются высокие требования. Во-первых, материал должен обладать хорошими упругими свойствами, т. е. должен после снятия нагрузок полностью восстанавливать свою форму, и должен быть достаточно мягким и эластичным. Во-вторых, он должен обладать высокими потерями энергии на внутреннее трение. Эти потери зависят от внутреннего строения вещества чем сложнее макроскопическая структура, тем больше потери. В-третьих, материал должен обладать высокой износостойкостью. Особенно он должен хорошо противостоять истиранию.
В различных конструкциях применяются сотни различных материалов, но по-видимому, самыми надежными материалами являются поролоны, пенопласты и резина.
При создании различных амортизаторов конструкторы стремились обеспечить, во-первых, нелинейную характеристику упругости и, во-вторых, большие потери энергии на трение.
Нелинейность характеристики «сила — деформация» амортизатора оказывается полезной по трём причинам.
Во-первых, она позволяет уменьшать габариты амортизатора. Дело в том, что большой эффект защиты конструкции дают «мягкие» амортизаторы. Но чем меньше жесткость, тем больше ход амортизатора при действии тех же сил. Приходится в конструкции выделять значительное место для устройств защиты. Для избежания ударов приходится увеличивать габариты амортизатора. Установка дополнительных коротких пружин (см. рис. 4) или конической пружины (см. рис. 5) позволяет с ростом амплитуды колебаний включать дополнительные жесткости и тем ограничивать амплитуды колебаний, не допуская ударов об ограничители движения.
Во-вторых, движение блока на нелинейных амортизаторах более сложно — несиносуидально по времени. Такое периодическое сложное движение можно представить в виде суперпозиции нескольких гармонических составляющих. Таким образом, при замене линейного амортизатора нелинейным помимо основной низшей гармонической составляющей колебаний, частота которой равна частоте внешних воздействий, появляются более высокие гармоники. На возбуждение этих гармоник расходуется часть энергии, передаваемой через амортизаторы от источника вибрации. Значит, меньшая часть энергии остаётся на возбуждение колебаний низшей гармоники. Резонансные явления развиваются не так интенсивно, как при линейных амортизаторах. Возникающие при этом высокочастотные гармоники быстро затухают вследствие потерь энергии на трение в амортизаторах. Эта энергия потерь тем больше, чем выше частота.
В-третьих, если в этом диапазоне имеются резонансные частоты конструкции, то начинают развиваться резонансные колебания. В этом случае иногда говорят о переходе через резонанс. В действительности, резонанс просто не успевает полностью развиться, поскольку для этого теоретически требуется бесконечное время. Но и такой развивающийся резонанс может привести к отказам и сбоям аппаратуры.
5. Повышение прочности конструкций
Если принятые меры защиты аппаратуры от механических воздействий не дают результата и численные или натурные эксперименты показывают, что отдельные детали не выдерживают нагрузок и появляются отказы, например в результате поломок, то приходится принимать меры по повышению прочности конструкций. Эти меры могут быть настолько разнообразны и неожиданны, что указать какие-то определённые пути повышения прочности конструкций аппаратуры не удаётся. Всё зависит от конкретных условий. Часто работа конструктора выливается в изобретение новой, неизвестной ранее конструкции.
Однако, анализ ошибок многих поколений конструкторов — и не только в области радиоэлектроники — даёт возможность выработать рекомендации, позволяющие избегать грубых ошибок. Приведём некоторые из них:
1. Нужно стремиться к равнопрочным конструкциям. Конструкция, которая должна выдерживать механические нагрузки, должна быть равнопрочной. Это значит, что все детали конструкции должны обладать одинаковым запасом прочности, т. е. отношение предельно допустимых для материалов деталей напряжений к реально возникающим во всех точках деталей должно быть одинаковым.
2. Нужно избегать концентраторов напряжения. Аналитические и численные решения задач о сложном напряженном состоянии различных деталей показали, что далеко не всегда напряжения в материалах распределяются равномерно по сечению детали. Чаще всего происходит концентрация напряжений в определённых местах. Эти места и называют концентраторами напряжения.
3. Следует избегать обработки поверхности деталей со снятием стружки. Заготовки деталей, полученные литьём или прессованием, имеют определённую внутреннюю макроскопическую структуру. Это может быть монокристаллическая или поликристаллическая структура у металлов или структура больших молекул у некоторых пластмасс. У поверхностей деталей эта структура повторяет форму поверхности и образует прочный защитный слой.
Механическая обработка поверхности, например точение или фрезерование, разрушает этот слой и, кроме того, оставляет на поверхности канавки риски, царапины, что также снижает прочность. Поэтому можно рекомендовать такие прогрессивные методы формообразования деталей несущих конструкций, как литьё, прессование, штамповка без дальнейшей механической обработки поверхности.
4. Следует учитывать направление вибрации при установке аппаратуры на транспортных средствах. Обычно нестационарная аппаратура проектируется для установки на определённых транспортных средствах. Причём заранее известно, где и в каком месте она будет установлена и какие механические воздействия будет испытывать. В частности, конструктора должно интересовать направление ударов и вибраций. При ударах и вибрациях точки конструкции перемещаются. Зная направление вектора перемещения на транспортном средстве, можно ориентировать аппаратуру при её установке так, чтобы она менее деформировалась при ударах и вибрациях.
6. Ударопрочные конструкции крепления радиоэлементов и узлов
Крепление деталей и узлов на шасси производят при помощи разъёмных и неразъёмных соединений. К конструкции любого крепления предъявляются следующие два требования:
а) вибропрочность при действии заданных ускорений в определённом диапазоне частот и ударопрочность при действии заданных ударных нагрузок,
б) отсутствие местных резонансных вибраций, т. е. крепление не должно усиливать вибрации, передаваемые от шасси к элементу или узлу.
Вибропрочность крепления зависит от конструкции, материала, технологии изготовления, от величины действующих ускорений и массы закрепляемой детали или узла. При конструировании РЭА конструкцию крепления радиодеталей не рассчитывают на вибропрочность, а используют стандартные крепёжные элементы или нормализованные крепления. Объясняется это тем, что поломки правильно применённых креплений при механических воздействиях на РЭА бывают сравнительно редко, а расчёт на прочность большего числа креплений является нецелесообразным.
Следует обращать внимание на монтаж резьбовых соединений. Для предупреждения саморазвинчивания гаек и винтов в аппаратуре, подвергающейся при эксплуатации вибрации и ударам, под гайки и винты подкладывают пружинные шайбы и закрашивают резьбовые соединения нитроэмалью.
Навесные элементы: резисторы, конденсаторы, полупроводниковые приборы, масса которых не превышает 8 г, — можно укреплять на собственных выводах путем механического крепления выводов к монтажным стойкам и лепесткам. При этом выводы не следует сильно натягивать, длина их не должна превышать 12 мм. Если масса элемента превышает 8 г, то применяют дополнительные крепления элемента и его выводов, используют заливку компаундом, приклеивание клеем или мастикой. Удобство применения мастики состоит в том, что приклеенные детали могут быть легко демонтированы.
При дополнительном креплении элементов их собственные частоты колебаний будут выше расчетных, т. е. дополнительное крепление уменьшает опасность резонанса на собственной частоте вибрации элементов.
6.1 Способы крепления соединительных проводов
Провода, кабели и кабельные соединения сами по себе нечувствительны к действию ударов и вибраций. Однако, если их монтаж недостаточно продуман, могут возникнуть определённые трудности. Провода и кабели обладают большой гибкостью, вследствие этого собственная частота секции провода или кабеля мала и может оказаться в диапазоне частот возбуждающих сил. Развивающиеся при этом в проводах переменные напряжения могут вызвать усталость металла. Обрывы происходят чаще всего на концах секции провода или кабеля, т. е. вблизи разъёмов. Обрывы могут возникнуть также вследствие трения проводов о детали аппаратуры или друг о друга. Кабель, пропускаемый через отверстие, должен быть защищён резиновой втулкой.
Несколько проводов, проходящих в одном направлении, можно связать монтажной ниткой, чтобы увеличивать прочность монтажа. При этом увеличивается и затухание вибраций, так как вибрирующие провода соприкасаются друг с другом. Связку проводов необходимо соответствующим образом закрепить, чтобы они своим весом не нагружали провода в точках соединений. Большое затухание связки проводов или кабелей полезно в том случае, когда они подвержены колебаниям изгиба.
Изгиб проволоки или кабеля в месте их соединения можно уменьшить, сократив расстояние между креплениями. Это справедливо только в том случает, если элементы крепления неподвижны. Уменьшать длину секций целесообразно в тех случаях, когда это приводит к повышению частоты собственных колебаний секции, снижению её веса и инерциальной нагрузки на детали крепления. Если элементы крепления подвижны, то для предотвращения разрыва проводов целесообразно их длину выбирать с запасом. Удлинение провода примерно на 20% от длины натяжения значительно уменьшает опасность обрыва.
При использовании витого изолированного провода увеличивается затухание и уменьшается амплитуда резонансных вибраций.
Провода и кабели, подверженные действию вибрации или ударов, разрываются главным образом в местах промежуточных закреплений или в зажимах (клеммах). Именно в этих точках развиваются максимальные напряжения изгиба. Когда провод припаен к штырю разъёма или зажима, участок провода, подверженный излому, находится между окончанием изоляции и жестко спаянной частью провода. На этом участке провода может проявиться усталость материала, приводящая к разрушению. Ограничить изгиб контактных соединений можно дополнительным креплением его к корпусу.
Когда провод закрепляется на контактном лепестке с проушиной, проушина должна захватить провод вместе с изоляцией. Если кабель оканчивается соединительным разъёмом, то разъём должен захватывать наружную изоляцию кабеля, чтобы ограничивать изгиб отдельных проводов кабеля.
Соединительный рукав предохраняет кабель от изгибов вблизи разъёма. Соединение производится обычным способом, затем разъём заполняется эпоксидной смолой и конец кабеля оказывается закреплённым. Однако залитые разъёмы трудно демонтировать.
При креплении проводов, жгутов и кабелей к корпусу с помощью клея, компаунда или мастики длина прямолинейных участков в зависимости от диаметра провода жгута или кабеля выбирается в пределах 50 мм — 200 мм. Не допускается приклейка жгута или отдельного проводника к сильно нагревающимся в процессе работы радиоэлементам.
6.2 Конструкции креплений конденсаторов
Стандартные конденсаторы обладают достаточной прочностью, чтобы противостоять ударам и вибрациям, но они могут вызвать отказы, если конструкция крепления будет неудовлетворительной.
Конденсатор с корпусом прямоугольной формы крепится в аппаратуре пластинами с двух сторон, каждая из пластин одним концом захватывает корпус, а другим, снабженным анкерными стержнями, прикрепляется к шасси. Достоинством такого типа крепления является малая вероятность повреждения корпуса и минимальная концентрация напряжений.
Цилиндрический конденсатор может иметь монтажный стержень, расположенный по оси симметрии, за который он крепится скобами к шасси. При этом необходимо проверить, обладает ли шасси достаточной жесткостью, так как изгиб шасси вызывает деформации конденсатора.
Крепёжные отверстия делают открытыми, благодаря этому корпус конденсатора при деформации крепления остаётся недеформированным. Конденсаторы с монтажными отверстиями у основания, как правило, подвержены деформации.
Конденсаторы небольших размеров часто укрепляют только на собственных выводах, что приводит к обрыву выводов. Лучше всего прикреплять конденсатор к шасси пояском, хотя бы частично охватывающим его корпус; соединительные провода при этом освобождаются от нагрузки. Небольшие конденсаторы можно крепить на их выводах только в тех случаях, когда выводы короткие и прочные, т. е. имеют высокую частоту собственных колебаний, а контактные лепестки, к которым припаиваются выводы, установлены на плате жесткой конструкции, так что выводы не будут подвергаться изгибу.
Цилиндрические конденсаторы можно укреплять на шасси блока с помощью металлической ленты. Оригинальным является крепление конденсатора в зажиме предохранителя, это можно делать, если конструкция зажима рассчитана на большие ударные и вибрационные нагрузки.
6.3 Крепление резисторов
Способ крепления резисторов зависит от их типа и конструкции. Малогабаритные резисторы укрепляют пайкой на лепестках деталей или на монтажных платах так же, как малогабаритные конденсаторы. Применяют также дополнительные крепления в виде скоб. Для повышения механической прочности крепления используют также мастику типа ЛН.
Для повышения вибропрочности в отдельных случаях резисторы и прокладочные шайбы дополнительно крепят при помощи клея ПУ-2 или мастики ЛН. Все резьбовые соединения закрашивают нитроэмалью.
6.4 Ударопрочные шасси и каркасы
Шасси блоков РЭА изготовляют из листового и профильного материала, для повышения жесткости шасси иногда делают литыми. Шасси блоков в корпусе (каркасе) крепят на петлях, осях или других подобных элементах. Требования, предъявляемые к конструкции крепления, следующие:
а) блок должен свободно и быстро переводиться в положение, позволяющее получить доступ в деталям; при этом оператор должен быть защищён от поражения электрическим током;
б) когда блок аппаратуры занимает рабочее положение, шасси его должно прочно соединяться с каркасом и увеличивать жесткость самого каркаса (стойки).
7. Расчеты механических нагрузок
7.1 Статический расчет амортизаторов
Целью расчета является определение статических нагрузок на амортизаторы и выбор их типоразмеров.
1. Расчет начинают с нахождения положения центра масс блока. Для каждого функционального узла и крупных деталей, входящих в блок, находят положение центра масс. Обычно считают, что для таких изделий положение центра масс функционального узла или детали совпадает с центром симметрии (рис. 16).
Используя моменты первого рода, находят координаты центра масс блока:
где xi, yi, zi — координаты центров масс функциональных узлов и деталей, входящих в блок; mi — массы этих изделий.
2. Наиболее часто используют вариант симметричного расположения амортизаторов на блоке РЭС (рис. 17). Амортизаторы располагают на блоке таким образом, чтобы проекции амортизаторов на плоскость XY не выходили за контур проекции блока.
Определяют координаты центра жесткости амортизаторов, используя моменты первого рода.
где xi, yi, zi — координаты размещения амортизаторов;
— суммарная статическая жесткость амортизаторов в направлении соответствующих координат;
— статические моменты жесткости амортизаторов относительно координатных плоскостей.
3. Условия статического равновесия системы амортизации
;; ;; ;
; ;
где pi — весовая нагрузка, приходящаяся на i-й амортизатор, G — вес блока.
Блок устанавливается на носителе без перекосов (поэтому Z = 0), тогда получаем:
.
4. Задаваясь координатами размещения амортизаторов, получают систему из 4 линейных уравнений
5. Решая эту систему (например, с помощью программ MathCAD) относительно нагрузок на амортизаторы, находят статические нагрузки на амортизаторы: p1; p2; p3; p4.
6. По полученным статическим нагрузкам и условиям эксплуатации выбирают типоразмер амортизатора. При несовпадении центра масс блока с центром симметрии, статическая нагрузка на амортизаторы будет разная и, следовательно, осадка однотипных амортизаторов будет различна. Для устранения перекоса блока вводят выравнивающие прокладки между амортизатором и корпусом блока.
7. Осадка амортизаторов Из полученных значений выбирают наименьшее и относительно определяют толщину выравнивающих прокладок под остальные 3 амортизатора:
где ?пр — толщина выравнивающей прокладки под соответствующий амортизатор.
Таким образом, в результате расчета получают координаты размещения амортизаторов, их типоразмеры и толщину выравнивающих прокладок.
7.2 Упаковочная тара для транспортирования
Упаковочная тара должна гарантировать сохранность РЭС при ее перевозке любыми транспортными средствами. Контейнер для транспортировки изготовляют из недорогих материалов (металл, слоистое стекловолокно и дерево). Между жесткой оболочкой тары и поверхностью РЭС прокладывают упругие амортизационные прокладки, гасящие вибрационные и ударные нагрузки при транспортировке (рис. 18).
Механические свойства упаковочных материалов характеризуются соотношением приложенной к поверхности материала нагрузкой и деформацией материала, вызываемой этой нагрузкой, т. е. статической жесткостью
P = f (z).
Амортизирующие прокладки могут быть упругие (табл. 1.1) и неупругие. Первые полностью восстанавливают свою толщину после снятия приложенной нагрузки. В неупругих прокладках наблюдается остаточная деформация, поэтому они являются прокладками разового использования.
Таблица 1.1
Материал | Плотность r, г/смі | Предельное допустимое давление sд, Н/смІ | Коэффициент демпфирования gm | |
Пенопласт полиуретановый (поролон) | 0,03−0,07 | 0,8−1,0 | 0,10 | |
Пенопласт полиуретановый с замкнутой структурой | 0,35 | 0,08 | ||
Резина губчатая | 0.127 | 0,12 | ||
Войлок мягкий | 0,3 | 2−3 | 0,18−0,2 | |
Сетка цельнометаллическая из проволоки ЭИ 708 диаметром 0,09 | 1,87 2,68 | 0,3−0,4 0,3−0,4 0,3−0,4 | ||
Исходные данные:
m — масса блока;
S — опорная поверхность блока;
К — наибольшая перегрузка, допустимая на РЭС.
Последовательность расчета:
1. Восстанавливающая сила после удара, которая вызовет в прокладке механическое напряжение (Н/смІ)
(1)
где К — наибольшая перегрузка, допустимая на РЭС.
2. Потенциальная энергия поднятого на высоту Н блока РЭС, которая приводит к максимально допустимой деформации прокладки
U = m · g · (H+z).
3. Потенциальная энергия, полностью переходящая в энергию деформации прокладки:
U=V· Tv=S·h·Tv,
где V — объем прокладки; Tv — энергия, накопленная в единице объема прокладки при минимальной упругой деформации.
4. Расчетная толщина прокладки
.
Обозначая у/Tv = И и с учетом (1), получаем толщину прокладки
5. Для приближенных расчетов удобно пользоваться выражением
видно, что чем меньше величина И, тем тоньше может быть упругая прокладка тары.
При выборе материала и размеров упругой прокладки исходят из допустимых напряжений, которые может выдержать материал, и минимальной величины безразмерной величины И (рис. 19).
7.3 Ударная прочность элементов
Большинство элементов конструкций РЭС могут быть представлены пластинами или балками. К пластинам можно отнести стенки кожухов или корпусов блоков, шасси, печатные платы, т. е. такие элементы, у которых размеры длины и ширины одного порядка, а толщины значительно меньше. К балкам можно отнести элементы каркаса стоек, блоков, рамки кассет и др., т. е. такие элементы конструкций у которых 2 размера поперечного сечения много меньше протяженности этого элемента.
Исходные данные:
a, b, h — геометрические размеры платы; a — большая сторона, м;
mп — масса платы, кг;
E — модуль упругости материала платы, Н/мІ;
r — плотность материала платы, кг/мі;
nуд — перегрузка при ударе;
t — длительность ударного импульса, с.
Последовательность расчета
1. Амплитуда ускорения при ударе
amax = nуд · g,
где g — ускорение силы тяжести.
2. Величина скорости в начальный момент удара
v0 = amax · t
или эквивалентная высота падения
.
3. Частота свободных колебаний f01 (первой гармоники), Гц,
где
Eп, Ec — модули упругости материала платы и стали,
mэ, mп — массы элементов и масса платы.
При свободном опирании по контуру и отношении, (а/b" 1) частотная постоянная
где Dцилиндрическая жесткость;
e — коэффициент Пуассона (для большинства материалов e = 0,3);
a1 — коэффициент, зависящий от краевых условий закрепления пластины.
Некоторые схемы закрепления плат и формулы для расчета a 1 приведены в табл. 1.2.
Таблица 1.2.
№ | Схема закрепления | Формула для расчета a 1 | |
a 1 = 9,87(1+b 2), где b =a/b | |||
4. Жесткость платы
K = (2p · f01)2 · mп.
5. Статический прогиб платы
Zст=(mп+mэ) · g/K.
6. Максимальный прогиб платы при ударе
.
7. Полная динамическая деформация платы
Zд = Zст + Zmax.
8. Эквивалентная сила удара
Pуд = K · Zд.
9. Расчетный коэффициент запаса
n = n1 · n2 · n3,
где n1 — запас прочности; n2 — степень ответственности детали; n3 — однородность механических свойств материала.
Рекомендуется коэффициенты выбирать в пределах: n1=1,25 ч 1,5; n2=1,0 ч 1,5; n3=1,2 ч 3,0. (при большем коэффициенте запаса выбирают большие значения коэффициентов).
10. Допустимое напряжение в материале платы
sдоп= sп/n,
где sп — предельное допустимое напряжение в материале.
11. Изгибающий момент, действующий на плату Ми=Руд · а/4.
12. Момент инерции сечения платы
J = b · h3/12.
13. Момент сопротивления изгибу пластины
W = J/(0,5h).
14. Напряжение, возникающее в материале платы
sи = Ми/W.
15. Сравнивают расчетное значение sи в материале платы с допустимым значением sдоп для данного материала (с учетом коэффициента запаса). Если выполняется условие sи? sдоп, конструкция способна выдержать действующую ударную нагрузку. В случае sи > sдоп необходимо принять меры по увеличению жесткости платы (увеличить толщину, ввести ребра жесткости, изменить материал платы и пр.).
Расчет балочных конструкций проводится по той же схеме, только при определении частоты собственных колебаний балки следует воспользоваться выражением
где li — корень частотного уравнения, характеризующий форму колебаний и способ крепления концов балки:
li = ip (для балки с шарнирным закреплением концов),
li =(2i -1) · p/2 (консольное крепление балки),
li=(2i +1) · p/2 (жесткое крепление концов балки), i — номер тона колебаний.
Если на балке имеются сосредоточенные массы mi то расчетная масса m
где l — длина балки, xi — расстояние от начала координаты (точка крепления балки) до соответствующей массы mi.
Список использованных источников
1. Токарев М. Д., Талицкий Е. Н., Фролов В. А. Механические воздействия и защита радиоэлектронной аппаратуры. -М.: Радио и связь, 1984.
2. Карпушин В. Б. Вибрация и удары в радиоаппаратуре. -М.: Советское радио, 1972.
3. Каленкович Н. И., Ростовец Е. П., Шамгин Ю. В. Механические воздействия и защита РЭС. -М.: Высш. школа, 1989.
4. Маквецов Е. Н., Тартаковский А. М. Механические воздействия и защита радиоэлектронной аппаратуры. — М.: Радио и связь, 1993.
5. http://dvo.sut.ru/libr/pes/i286gell/1.htm — Расчеты механических нагрузок.