Другие работы
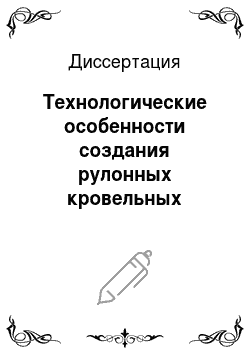
К настоящему времени исследовано значительное количество месторождений базальтов. По данным института «Теплопроект» (г. Москва) Россия и СНГ обладают практически неограниченными запасами базальтов, диабазов, габбро и их аналогов, суммарный запас которых 197 млн.м. Так, месторождения базальтов широко распространены на Камчатке, Курильских островах, в Хабаровском и Приморском краях…
Диссертация 
Для производительного использования горного и транспортного оборудования (экскаваторов и подвижного состава) необходимо взаимное согласование их параметров. Основными требованиями, предъявляемыми к карьерному транспорту, являются: обеспечение заданного грузооборота; бесперебойность работы (точное соблюдение графика движения—для средств цикличного действия и непрерывность потока— для транспортных…
Курсовая 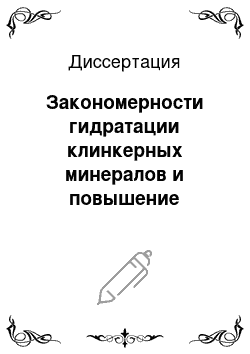
Результаты исследований доложены и обсуждены на: Всесоюзной конференции «Автоколебания в конденсированной фазе» (г.Уфа, 1989), ежегодных научно-технических конференциях Новосибирского инженерно-строительного института — Новосибирского архитектурно-строительного университета — (г.Новосибирск, 1990;1998 г. г.), региональной конференции ученых Сибири и Дальнего Востока «Наука-строительному…
Диссертация 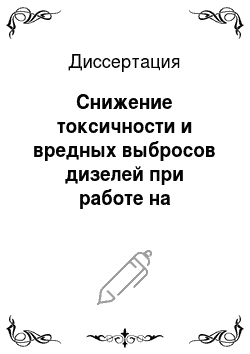
Отметим так же, что до настоящего времени при работе двигателя в нестационарных условиях не сложилось единой терминологии в отношении определения явления перехода двигателя от одного (начального) установившегося режима к другому (конечному), вследствие изменения нагрузки или смены режима обслуживающим персоналом. Попытки ввести единую терминологию /9/ пока не достигли желаемого результата. Так…
Диссертация 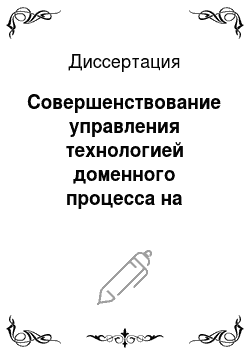
Алгоритм определения рабочего профиля и состояния кладки лещади заключается в решении нескольких уравнений: по данным дефектоскопии рассчитывается распределение температур (Чр) по вектору прозвучивания, определяется скорость ультразвуковых колебаний в каждой точке его отражения, затем по скорости и времени определяется расстояние до точки отражения ультразвука. Определение состояния кладки…
Диссертация 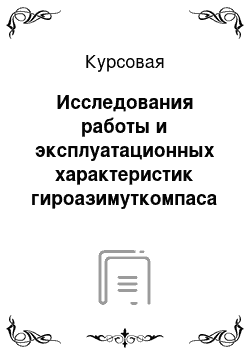
Отметить момент времени, когда погаснет табло «Пуск» (примерно через 3−5 мин. после срабатывания термореле 1ВК3). В этот момент автоматически подается питание на стабилизирующие двигатели, что сопровождается характерным «рывком» шкалы прибора ВГ-1А. Если этот рывок не наблюдается или шкала не начнет вращаться с большей частотой, гироазимуткомпас следует выключить. Если через 40 мин. после…
Курсовая 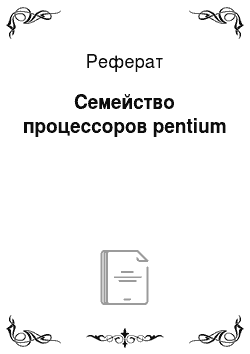
Поколение компьютеров, которое последовало за 80 486, получило назва-ние Pentium (от греческого — пять). В отличие от процессора 80 486, который имел один внутренний конвейер, у Pentium стало два, что дало ему возможность функ-ционировать практически в два раза быстрее. В дальнейшем в линейку Pentium были внедрены дополнительные команды, которые более известны под общим названием ММХ (MultiMedia…
Реферат 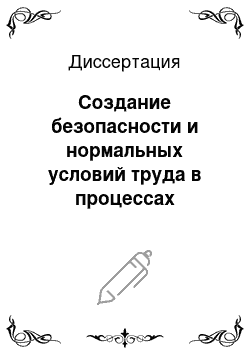
Для создания безопасности и нормальных условий труда в процессах деревообработки по пылевому фактору необходимо решение комплекса задач: а) создание на предприятии системы управления безопасностью процессов по пылевому факторуб) разработка нормативно-законодательной базы о вредности древесной пыли и условий труда деревообработчиков с соответствующим контролем по созданию безопасных условий труда…
Диссертация 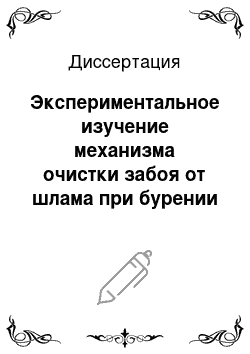
Нефть и газ сегодня, а также в ближайшей перспективе являются основой экономики России. Даже для поддержания достигнутого уровня их добычи, не говоря уже о наращивании, необходимо бурение значительного количества глубоких скважин, особенно разведочных. Чтобы выполнить эту задачу при весьма ограниченных финансовых ресурсах, нужно прежде всего снизить затраты на строительство скважины. Последние…
Диссертация 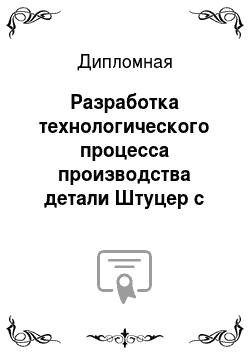
Наименование профессии Категория тяжести работ Параметры микроклимата, факт/норм Освещён-ность, факт/норм, лк Наименование вредного вещества на рабочем месте Концентрация вредного вещества, факт/норм, мг/м³ Наименование энергетического воздействия на среду Уровень энергетического воздействия Площадь, приходящаяся на 1 работающего, факт/норм, м² Объём помещения, приходящегося на 1 работающего…
Дипломная 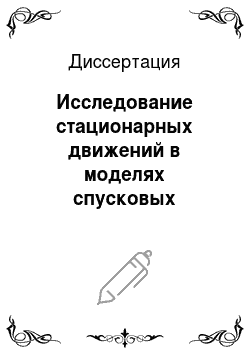
Для ряда моделей в пространстве параметров были получены области как тривиальных, так и нетривиальных интервалов вращения точечных отображений, которые дают информацию о странном аттракторе, причем для некоторых моделей область параметров разбита на подобласти, отвечающие различным значениям нижней и верхней границы интервала вращения. Дана механическая интерпретация полученных результатов…
Диссертация 
В рыночных условиях предприятия, независимо от их формы собственности, за счет собственных средств амортизации, прибыли, кредитов приобретают оборудование, строят цехи. И чтобы производство было эффективным, а огромные средства, затраченные на создание и приобретение основных производственных фондов (ОПФ), не были напрасно потерянными, основные фонды должны наиболее полно и рационально…
Отчёт 
В начале 90- х годов появились первые рекламные объявления по предоставлению услуг сети сотовой радиотелефонной связи, в которых за 2000 долларов предлагалось приобрести небольшой чемоданчик, называемый абонентским радиотелефоном, весом в пять килограммов и такую же сумму уплатить за подключение к сети. В настоящее время представляется невозможным спрос на такое предложение, ведь сейчас сотовые…
Дипломная 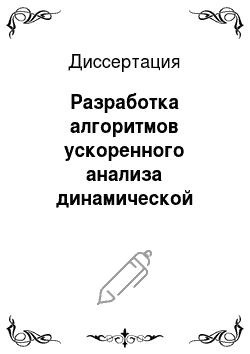
При решении проектных и эксплуатационных задач по определению структур и параметров систем противоаварийного управления необходимо проводить многократные расчеты электромеханических переходных процессов при учете вариаций схемно-режимных параметров энергосистем и различной интенсивности возмущений. Сложность и многовариантность решений затрудняют расчеты и требуют для их выполнения значительных…
Диссертация 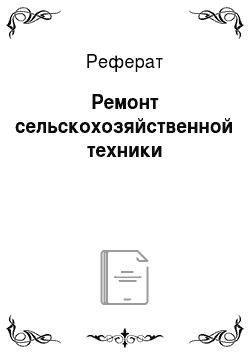
Во всех производственных помещениях применяются естественная, а в ряде отделений и цехов также искусственная вентиляция. Расчет естественной вентиляции сводится к определению площадей фрамуг или форточек. Расчет искусственной вентиляции — к выбору её вида, определению воздухообмена, подбору вентилятора и электродвигателя. По нормам промышленного строительства все помещения должны иметь сквозное…
Реферат