Анализ изотермических и термокинетических диаграмм распада переохлажденного аустенита и выбор термической обработки
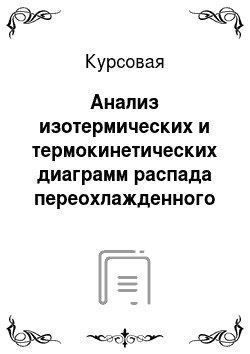
Термическая обработка штампов для горячего деформирования из стали марки 4Х5МФС Наиболее распространенный технологический процесс окончательной термической обработки инструмента для горячего деформирования состоит из закалки и отпуска. Большое разнообразие условий работы такого инструмента предопределяет не только применение различных сталей, но и необходимость получать в каждом конкретном случае… Читать ещё >
Анализ изотермических и термокинетических диаграмм распада переохлажденного аустенита и выбор термической обработки (реферат, курсовая, диплом, контрольная)
Курсовая работа на тему Анализ изотермических и термокинетических диаграмм распада переохлажденного аустенита и выбор термической обработки Выполнил: ст. гр. МВ-03−10.
Ишков С.С.
Введение
В настоящее время легированные стали и сплавы являются распространенным и универсальным классом материалов. Большинство металлических материалов характеризуются кристаллическим состоянием, их структура сформирована в результате ограниченного числа фазовых превращений. Это позволяет рассматривать закономерности формирования структуры и свойств с единых позиций в сплавах любого состава. Установление взаимосвязи состав — структура — свойства позволяет не только улучшить качество уже существующих материалов, но и создавать новые, с заранее заданными свойствами. Характеристика стали обусловлена не только химическим составом, но и данные о положении критических точек и кинетике распада переохлаждённого аустенита, о чувствительности стали к прогреву и роста зерна. Особое большое значение имеет сведения о кинетики превращения переохлаждённого аустенита, на основании которых решают вопросы прокаливаемости, режимов термической обработки и механических свойств детали.
С целью снижения металлоемкости в последнее время большое внимание уделяется вопросам создания материалов, которые можно использовать для уменьшения весовых с сохранением прочностных характеристик. Получение знаний о кинетике превращения и процессах структурообразования переохлажденного аустенита, являются основой при создании технологических процессов термической обработки для новых видов металлопродукции.
1. ФАЗОВЫЙ СОСТАВ, СТРУКТУРА, СВОЙСТВА И НАЗНАЧЕНИЕ СТАЛИ.
1.1 Общее положение Сплавы железа — сталь и чугун — основные металлические материалы, используемые в различных отраслях народного хозяйства. Наиболее широко применяют стали. Они должны иметь хорошие технологические свойства: легко обрабатываться давлением, а также хорошо обрабатываются на металлорежущих станках, свариваться. В ряде случаев от них требуется высокая коррозионная стойкость или жаропрочность и т. д. Достоинством сталей является возможность получать нужный комплекс свойств, изменяя их состав и вид обработки.
Стали подразделяют на углеродистые и легированные. Углеродистые стали — это основной конструкционный материал, который используют в различных областях промышленности. Они проще в производстве и значительно дешевле легированных. Свойства их определяются количеством углерода и содержанием присутствующих в них примесей, которые взаимодействуют и с железом, и с углеродом.
Элементы, специально вводимые в сталь в определенных концентрациях с целью изменения ее строения и свойств, называются легирующими элементами. Легирующие добавки повышают прочность, коррозийную стойкость стали, снижают опасность хрупкого разрушения. В качестве легирующих элементов выступают: Cr, Ni, Si, Mn, Mo, W, V, Ti, Mo и т. д.
Легированную сталь по степени легирования разделяют на: низколегированную (легирующих элементов до 2,5%), среднелегированную (от 2,5 до 10%), высоколегированную (от 10 до 50%).
Примесями называют химические элементы, перешедшие в состав стали в процессе ее производства как технологические добавки, или как составляющие шихтовых материалов. Содержание примесей в стали, конечно, ограничивается следующими пределами: Mn0,8%; Si0,4%; Cr0,3%; Ni0,3%; Cu0,3%; Mo0,1%; W0,2%; P0,025−0,040%; S0,015−0,050%.
Легирующие элементы в сплавах Fe-C классифицируют по степени сродства к углероду, по сравнению со сродством к нему железа. По этому признаку различают карбидообразующую и некарбидообразующие легирующие элементы.
Карбидообразующие элементы — Ti, Zr, V, Nb, Ta, Cr, Mo, W, Mn, Fe.
Некарбидообразующие элементы — Cu, Ni, Co, Si, Al.
Склонность к карбидообразования легирующих элементов тем сильнее, чем менее пристроенной является d-оболочка у металического атома.
1.2 Фазовый состав, структура, свойства и назначение стали марки 35ХГ2 и 4Х5МФС Марка стали 35ХГ2.
Марки стали 35ХГ2 — это конструкционная легированная сталь. Применяться для цементуемых деталей небольших сечений, работающих на трение.
Заменители марки стали 35ХГ2 являются 35ХГФ, 40ХГТР Таблица 1.1 — Химический состав в % марки стали — 35ХГ2.
C. | Si. | Mn. | Ni. | S. | P. | Cr. | Cu. | |
0.32−0.4. | 0.17−0.37. | 1.6−1.9. | до 0.3. | до 0.035. | до 0.035. | 0.4- 0.7. | до 0.3. | |
Марганец (Mn) — как и кремний, содержится в обыкновенной углеродистой стали в небольшом количестве и особого влияния на ее свойства также не оказывает. Однако марганец образует с железом твердый раствор и несколько повышает твердость и прочность стали, незначительно уменьшая ее пластичность. Марганец связывает серу в соединение MnS, препятствуя образованию вредного соединения FeS. Кроме того, марганец раскисляет сталь. При высоком содержании марганца сталь приобретает исключительно большую твердость и сопротивление износу.
Хром (Cr) — наиболее дешевый и распространенный элемент. Хром повышает твердость и прочность, незначительно уменьшая пластичность, увеличивает коррозионную стойкость; содержание большого количества хрома делает сталь нержавеющей и обеспечивает устойчивость магнитных сил.
Таблица 1.2- Технологические свойства.
Температура ковки, °С. | Обрабатывае-мость резаньем. | Склон-ность к отпускной хрупкости. | Флокеночувствительность. | Коррозионная стойкость. | ||
Начало 1150. | Конца 800. | Твердый сплав Kн=0,75 Быстрорежущая сталь Kн=0,55. | Склонна. | Не чувствительна. | Низкая. | |
Свариваемость марки стали 35ХГ2. Для получения качественных сварных соединений требуются дополнительные операции: подогрев до 200 — 300 °C при сварке, термообработка после сварки — отжиг.
Таблица 1.3 — Механические свойства при Т=20oС материала 35ХГ2.
Сортамент. | Размер | sb. | st. | d5. | y. | KCU. | |
; | мм. | Мпа. | Мпа. | %. | %. | кДж / м2. | |
Пруток, ГОСТ 4543–71. | O 25. | ||||||
Обозначения:
Механические свойства :
sв — Предел кратковременной прочности, [МПа].
sT — Предел пропорциональности (предел текучести для остаточной деформации), [МПа].
d5 — Относительное удлинение при разрыве, [ % ].
y — Относительное сужение, [%].
KCU — Ударная вязкость, [кДж / м2].
Марка стали 4Х5МФС Марка стали 4Х5МФС — это инструментальная штампованная сталь. Достаточно устойчивой маркой инструментальной стали к коррозийному растрескиванию при воздействии высокого напряжения. Также данная марка стали устойчива к коррозии. Основными изделиями, производимыми из такой стали, являются инструменты, эксплуатируемые при различных температурных режимах. Следует отметить, что поковка из марки стали 4Х5МФС отличается вязкостью и повышенной стойкостью к термическому удару. Сплав 4Х5МФС применяется для производства поковок различных деталей общего машиностроения, пресс-форм для литья под лавлением алюминиевых, а также цинковых и магниевых сплавов, мелких молотовых штампов, крупных (толщиной или диаметром более 200 мм) молотовых и прессовых вставок при горячем деформировании конструкционных сталей и цветных сплавов в условиях крупносерийного массового производства.
Марку стали 4Х5МФС заменяют такие марки как 4Х5МФ1С и 4Х4ВМФС.
Таблица 1.4 — Химический состав в % марки стали 4Х5МФС.
C. | Si. | Mn. | Ni. | S. | P. | Cr. | Mo. | V. | Cu. | |
0.32 — 0.4. | 0.9 — 1.2. | 0.2 — 0.5. | до 0.35. | до 0.03. | до 0.03. | 4.5 — 5.5. | 1.2 — 1.5. | 0.3 — 0.5. | до 0.3. | |
Хром (Cr) — наиболее дешевый и распространенный элемент. Хром повышает твердость и прочность, незначительно уменьшая пластичность, увеличивает коррозионную стойкость; содержание большого количества хрома делает сталь нержавеющей и обеспечивает устойчивость магнитных сил.
Ванадий (V) — повышает прочность, эластичность, твердость и ударную вязкость в соединении с другими элементами, повышает сопротивление стали на ползучесть и измельчает зерно. Увеличивает плотность стали, так как является хорошим раскислителем, он дорог и дефицитен.
Кремний (Si) — в количестве свыше 1% оказывает особое влияние на свойства стали: содержание 1−1,5% увеличивает прочность, при этом вязкость сохраняется. При большем содержании кремния увеличивается электросопротивление и магнитопроницаемость. Кремний увеличивает также упругость, кислостойкость, окалиностойкость.
Таблица 1.5 — Механические свойства при Т=20oС марки стали 4Х5МФС.
Сортамент. | Размер | sв. | st. | d5. | y. | KCU. | |
; | мм. | Мпа. | Мпа. | %. | %. | кДж / м2. | |
Сортовая. | |||||||
Свариваемость марки стали 4Х5МФС. Без ограничений — сварка производится без подогрева и без последующей термообработки. Ограниченно свариваемая — сварка возможна при подогреве до 100−120 0С и последующей термообработке. Трудносвариваемая — для получения качественных сварных соединений требуются дополнительные операции: подогрев до 200−300 0С при сварке, термообработка после сварки.
Обозначения:
Механические свойства :
sв — Предел кратковременной прочности, [МПа].
sT — Предел пропорциональности (предел текучести для остаточной деформации), [МПа].
d5 — Относительное удлинение при разрыве, [ % ].
y — Относительное сужение, [ % ].
KCU — Ударная вязкость, [ кДж / м2].
2. РЕЖИМ ТЕРМООБРАБОТКИ СТАЛИ МАРОК.
2.1 Виды термообработки для марки стали 35ХГ2 и 4Х5МФС Основные виды термообработки для марки стали 35ХГС это закалка и отпуск. Такой же вид термообработки применяется и для марки стали 4Х5МФС.
Закалка — вид термической обработки материалов заключающийся в их нагреве выше критической температуры (температуры изменения типа кристаллической решетки, т. е. полиморфного превращения, либо температуры, при которой в матрице растворяются фазы, существующие при низкой температуре), с последующим быстрым охлаждением. Чаще всего охлаждение осуществляется в воде или масле, но существуют и другие способы охлаждения: в псевдокипящем слое твёрдого теплоносителя, струёй сжатого воздуха, водяным туманом, в жидкую полимерную закалочную среду. Различают закалку с полиморфным превращением, для сталей, и закалку без полиморфного превращения, для большинства цветных металлов.
Материал подвергшийся закалке приобретает большую твердость, но становится хрупким, менее пластичным и менее вязким, если сделать большее количество повторов нагревание-охлаждение. Для снижения хрупкости и увеличения пластичности и вязкости, после закалки с полиморфным превращением применяют отпуск.
Отпуском называется операция термической обработки, состоящая в нагреве закаленной стали до температуры ниже критической АC1, выдержке при этой температуре и последующем медленном или быстром охлаждении. Цель отпуска — устранить или уменьшить напряжения в стали, повысить вязкость и понизить твердость. Отпуск является заключительной операцией термической обработки, и правильное выполнение его в значительной степени определяет качество готовой закаленной детали.
В зависимости от температуры нагрева различают низкий, средний и высокий отпуск.
Низкий отпуск достигается нагревом до температуры 150—250° С, выдержкой при этой температуре и последующим охлаждением на воздухе. При выдержке во время отпуска в указанном интервале температур мартенсит закалки превращается в мартенсит отпуска, при этом внутренние напряжения частично снимаются и остаточный аустенит превращается в мартенсит отпуска.
В результате низкого отпуска сталь сохраняет высокую твердость, а иногда твердость повышается за счет распада остаточного аустенита; устраняется закалочная хрупкость. Такой отпуск применяют для режущего инструмента и изделий, которым необходима высокая твердость. Превращение мартенсита закалки в мартенсит отпуска способствует стабилизации размеров детали, что необходимо для измерительного инструмента, изготовляемого из инструментальной стали. Этому инструменту также дают низкий отпуск.
Средний отпуск производят при 300—500° С. Твердость стали заметно понижается, вязкость увеличивается. Средний отпуск применяют для пружин, рессор, а также инструмента, который должен иметь значительную прочность и упругость при средней твердости.
Высокий отпуск происходит при 500—600° С, его основное назначение — получить наибольшую вязкость при достаточных пределах прочности и упругости стали. Применяют этот вид отпуска для деталей из конструкционных сталей, подвергающихся действию высоких напряжений, особенно при ударной нагрузке.
3. ОПИСАНИЕ И АНАЛИЗ ДИАГРАММ ИЗОТЕРМИЧЕСКОГО РАССПАДА АУСТЕНИТА.
3.1 Общее описание и характеристика диаграмм изотермического распада аустенита Превращение аустенита в субкритическом интервале температур может развиваться несколькими путями с образованием различных структурных образований. Обычно различают диффузионный, бездиффузионный и промежуточный механизм превращения. При диффузионном превращении аустенита происходит образование избыточных фаз — феррита или карбида и образование ферритокарбидной смеси различной степени дисперсности.
Сталь со структурой аустенита, быстро охлажденная до температуры ниже Аr1 (т.е. переохлажденная), оказывается в метастабильном состоянии и претерпевает превращение. Для его описания строят так называемые диаграммы изотермического превращения аустенита, отражающие степень распада аустенита во времени при разных температурах. Образцы стали, быстро охлажденные до определенной температуры, выдерживают при этой температуре, контролируя количество распавшегося аустенита.
На рис. 3.1 приведена диаграмма изотермического распада аустенита эвтектоидной стали, где П, Б, М — области перлитного, бейнитного и мартенситного превращений; Мн — температура начала превращения аустенита в мартенсит; Мк — температура конца превращения. Левая С-образная кривая характеризует начало распада, правая кривая показывает время, когда процесс распада полностью заканчивается (или приостанавливается). Область, расположенная левее кривой начала распада, определяет продолжительность инкубационного периода, в течение которого распад аустенита экспериментально не фиксируется.
Рис 3.1 — Схема диаграммы изотермического распада переохлаждённого аустенита эвтектоидной стали Из рис. 3.1 видно, что устойчивость аустенита с увеличением степени переохлаждения сначала быстро уменьшается, что связано с возрастанием разности свободных энергий аустенита и образующихся фаз. При дальнейшем увеличении степени переохлаждения устойчивость аустенита вновь повышается, что вызывается снижением скорости образования новых фаз и их роста в результате замедления диффузионных процессов.
При температурах, соответствующих точке МН и более низких, процессы диффузии полностью подавляются. Происходит сдвиговое бездиффузионное фазовое превращение аустенита в структуру закалённой стали, называемую мартенситом. Мартенситное превращение обусловливается упорядоченным перемещением атомов, причем такие перемещения малы по сравнению с междуатомным расстоянием.
В зависимости от степени переохлаждения различают три области превращения: перлитную, мартенситную и бейнитную (промежуточную) между ними, в которых соответственно протекают перлитное, мартенситное и бейнитное превращения.
Перлитное превращение аустенита по своему механизму является диффузионным. Ведущей, в первую очередь возникающей фазой является цементит. Его зародыши образуются на границах зерен аустенита. Образовавшаяся пластинка цементита растет за счет диффузии углерода из прилегающих объемов аустенита, в которых его содержание понижается. Когда содержание углерода в аустените снизится до 0,2%, происходит полиморфное превращение гамма-железа в альфа-железо и рядом с пластинкой цементита (вдоль нее) образуется пластинка феррита.
В результате образования и роста частиц цементита вновь создаются условия возникновения и роста пластинок феррита. Такой совместный рост двухфазной «колонии» в результате диффузионного перераспределения углерода — характерная особенность перлитного превращения.
Мартенсит — основная структура закаленной стали, его твердость — 62 — 64 HRC (600 — 660 НВ). Минимальная скорость охлаждения, при которой образуется структура мартенсита, называется критической скоростью закалки.
В отличие от диффузионного перлитного превращения аустенито-мартенситное имеет бездиффузионный характер.
При резком переохлаждении аустенита до температуры начала мартенситного превращения Мн = 250 — 200 °C происходит перестройка решетки гамма-железа в альфа-железо. Весь углерод, растворенный в аустените, остается в альфа-железе. Максимальная растворимость углерода в альфа-железе обычно не превышает 0,02%. В образовавшемся мартенсите его будет столько, сколько содержалось в аустените стали до начала превращения. Следовательно, мартенсит — пересыщенный твердый раствор углерода в альфа-железе.
Промежуточное (бейнитное) превращение происходит между перлитным и мартенситным превращениями в области температуры 550 °C — Мн при изотермической выдержке переохлажденного аустенита.
Бейнит (игольчатый троостит) — смесь высоуглеродистого феррита и цементита. Его твердость — 40 — 55 HRC.
Твердость бейнита возрастает с понижением температуры превращения. Бейнит, образующийся при более низкой температуре (близкой к точке Мн), по сравнению с сорбитом и трооститом имеет более высокую твердость и прочность при сохранении пластичности.
В результате на практике мы наблюдаем весьма сложную зависимость кинетики превращения аустенита от температуры переохлаждения или интенсивности охлаждения и, следовательно, разнообразный вид диаграмм.
3.2 Описание изотермической диаграммы распада переохлаждённого аустенита для марки стали 35ХГ2.
Конструкционная легированная сталь 35ХГ2 содержит небольшое количество легирующих элементов. Так как их малое количество, то диаграмма (Рис 3.2) не существенно изменила свій вид. Наличие карбидообразующий элементов (Cr, Mn) и некарбидообразующих (Si, Ni) не приводит к чёткому разделению перлитного и бейнитного превращений. Область устойчивого аустенита отсутствует. Низкая область аустенита под влиянием легирующих элементов сдунута в область меньших времён выдержки (вправо).
Рис. 3.2 — Изометрическая диаграмма распада переохлаждённого аустенита.
Температурные условия превращений по типу первой и второй ступени совпадают. Первая ступень перлитная, а вторая бейнитная. Промежуточное превращение сдвинуто в область сниженных температур, в область меньших времён выдержки. Температура нагрева образца марки стали 35ХГ2 — 875ОС, температура линии А1 = 730 ОС, мартенситное превращение начинается с линии МН, которая равняется 300 ОС. В интервале температур перлитная твёрдость колеблется от 7 до 30 HRC. Твёрдость бенитной области зависит от времён выдержки, а твёрдость равняется 40−42 HRC.
3.3 Описание термокинетической диаграммы распада переохлажденного аустенита для марки стали 4Х5МФС Инструментальная штампованная сталь марки 4Х5МФС содержит большое количество карбидообразующих элементов (Cr, Mn, V, Mo), что оказывает влияние на вид диаграммы (Рис 3.3). Наличие карбидообразующий элементов (Cr, Mn) приводит к чёткому разделению перлитного и бейнитного превращений с появлением области устойчивого аустенита. Выделяются в аустените спец карбиды.
Рис. 3.3Термокинетическая диаграмма распада переохлаждённого аустенита.
Температурные условия превращений по типу первой и второй ступени не совпадают. Температура нагрева образца 4Х5МФС — 1100ОС, температурный интервал линии А1 = 840−920 ОС, мартенситное превращение начинается с линии МН, которая равняется 260 ОС. При достаточно медленных скоростях охлаждения происходит перлитное превращение твёрдостью HV 245. Мартенситное превращение происходит при быстрых и средних скоростях охлаждения, его твёрдость валирует от 779 до 724 HV. Охлаждение прошедшее через промежуточные превращения значительно снижает твёрдость мартенсита из-за образования других фаз.
4. ТЕРМИЧЕСКАЯ ОБРАБОТКА ИЗДЕЛИЙ, ИЗГОТОВЛЕННЫХ ИЗ СТАЛИ МАРОК 35ХГ2, 4Х5МФС.
4.1 Термическая обработка поршневого пальца, изготовленного из стали 35ХГ2.
Марка стали 35ХГ2 применяться для цементуемых деталей небольших сечений, работающих на трение (поршневого пальца, зубчатое колесо полуоси втулки, валики, оси, шпильки, шлицевые валы, шестерни, шнеки, червячные передачи и многое другое). Для получения после цементации и последующей термической обработки высокой твердости поверхности и пластичной сердцевины детали получающаяся после цементации и последующей термической обработки твердая и прочная сердцевина у сталей с повышенным содержанием углерода предохраняет цементованный слой от продавливания при больших предельных нагрузках. Это позволяет снизить глубину цементованного слоя, т. е. сократить длительность цементации.
Цементация — процесс насыщения поверхностного слоя стали углеродом с целью повышения прочности, твёрдости и износостойкости поверхностного слоя. За глубину цементованного слоя принимают расстояние от поверхности до переходной зоны.
Различают следующие виды цементации: цементация с применением твёрдого карбюризатора; газовая цементация с применением жидкого или газового карбюризатора. Наиболее перспективным является газовая цементация. По сравнению с цементацией в твёрдом карбюризаторе она имеет следующие преимущества: значительно сокращается длительность процесса благодаря быстрому нагреву детали; возрастает пропускная способность оборудования, что ведёт к повышению производительности труда; улучшаются условия труда; появляется возможность автоматизации процесса.
Для обработки поршневого пальца изготовленного из стали 35ХГ2 применяют такую последовательность: отливка — цементация — механическая обработка — закалка — высокий отпуск — механическая обработка.
Доэвтектоидные стали при закалке нагревают до температуры на 30 -50°С выше верхней критической точки Ас3. При таком нагревании исходная феррито-перлитная структура превращается в аустенит, а после охлаждения со скоростью больше критической образуется структура мартенсита. Скорость охлаждения оказывает решающее влияние на результат закалки. Преимуществом масла является то, что закаливающаяся способность не изменяется с повышением температуры масла. Масло недостаточно быстро охлаждает при 550 — 650 °C, что ограничивает его применение только тех сталей, которые обладают небольшой критической скоростью закалки.
В результате длительной выдержки при высокой температуре цементации происходит перегрев, сопровождающийся ростом зерна. Для получения высокой твердости цементованного слоя и достаточно высоких механических свойств сердцевины, а также для получения в поверхностном слое мелкоигольчатого мартенсита, деталь после цементации подвергнем последующей термической обработке.
В результате цементации поверхностный слой деталей науглероживается (0,8 — 1% С), а в сердцевине остается (0.32−0.4%) С, т. е. получается как бы двухслойный металл. Поэтому для получения нужной структуры и свойств в поверхностном слое и в сердцевине необходима двойная термическая обработка.
Первая — закалка от 850 — 900 °C; Вторая от 750 — 800 °C и отпуск при 150 — 170 °C. В результате первой закалке улучшается структура низкоуглеродистой сердцевины (перекристаллизация). При этой закалке структура поверхностного слоя тоже улучшается, так как быстрым охлаждением устраняется цементитная сетка. Но для науглероживания поверхностного слоя температура 850 — 900 °C является слишком высокой и поэтому не устраняет перегрева. После цементации деталь поступает на механическую обработку. Основная цель закалки стали это получение высокой твердости, и прочности что является результатом образования в ней неравновесных структур — мартенсита, троостита, сорбита. Заэвтектоидную сталь нагревают выше точки Ас1 на 30 — 90 0С. Нагрев заэвтектоидной стали выше точки Ас1 производится для того, чтобы сохранить в структуре закаленной стали цементит, является еще более твердой составляющей, чем мартенсит (температура заэвтектоидных сталей постоянна и равна 760 — 780 0С). Вторая закалка от 750 — 800 °C является нормальной закалкой для науглероженного слоя — устраняется перегрев и достигается высокая твердость слоя. Отпуск при 150 — 170 °C проводится для снятия внутренних напряжений. После такого режима термической обработки структура поверхностного слоя — мелкоигольчатый мартенсит с вкраплениями избыточного цементита, а сердцевины — мелкозернистый феррит+перлит.
Механические свойства стали после термической обработки:
— Твердость в сердцевине повысилась до HRC 56−62 (пов.), НВ 363−415 (серд.).
— Предельная прочность (ув) равна 620 Н/мм2;
Таблица 4.1 — Физические свойства.
Температура испытания, °С. | ||
Модуль нормальной упругости, Е, ГПа. | ||
Модуль упругости при сдвиге кручением G, ГПа. | ||
Плотность, pn, кг/см3. | ||
Коэффициент теплопроводности Вт/(м · °С). | ||
Температура испытания, °С. | 20- 900. | |
4.1 Термическая обработка штампов для горячего деформирования из стали марки 4Х5МФС Наиболее распространенный технологический процесс окончательной термической обработки инструмента для горячего деформирования состоит из закалки и отпуска. Большое разнообразие условий работы такого инструмента предопределяет не только применение различных сталей, но и необходимость получать в каждом конкретном случае оптимальное для данных условий сочетание свойств за счет правильного выбора режимов термической обработки. При этом в зависимости от назначения инструмента возможен выбор разных температур нагрева под закалку, закалочных сред и способов охлаждения, температур отпуска. Режимы закалки и отпуска не универсальны, а их следует назначать дифференцированно в соответствии с условиями работы инструмента.
Обобщенная технологическая схема обработки инструмента для горячего деформирования из полутеплостойкой стали повышенной вязкости:
1) горячая пластическая деформация (ковка);
2) отжиг;
3) механическая обработка;
4) закалка и отпуск;
5) механическая обработка.
Для деформирования алюминиевых сплавов применяются стали с5% Cr: 4Х5В2ФС и типа 4Х5МС (или 4Х5МФС). При изготовлении матриц крупных размеров применяют стали с 3% Cr (типа 4Х3МС), так как они лучше сохраняют пластичность в больших сечениях.
Пониженная деформируемость штамповых сталей по сравнению с конструкционными обусловлена их меньшей пластичностью вследствие более высокой легированности твердого раствора, больших количеств карбидных фаз и степени ликвации при кристаллизации.
Температуры нагрева под ковку (прокатку) выбирают из условий достижения наиболее высокой пластичности в достаточно широком интервале температур, что определяется химическим составом стали и массой слитка. Температуры окончания пластической деформации устанавливают с учетом того, чтобы избежать образования трещин и рванин и подготовки необходимой структуры (размера зерна аустенита, распределения и дисперсности избыточных фаз и др.), обеспечивающей высокие механические свойства после окончательной термической обработки. Для полутеплостойких сталей повышенной вязкости температуры начала ковки 1150−1180оС, окончания 850−880оС. Для теплостойких штамповых сталей начало ковки при 1160−1180оС; конец ковки при 850−925оС.
Отжиг выполняют лишь при необходимости измельчения структуры слитков или крупных заготовок, мало обжатых при пластической деформации. В остальных случаях можно ограничиться высоким отпуском, после которого сталь приобретает примерно такую же структуру, как и после отжига.
Назначение отжига (отпуска) — перекристаллизация стали для измельчения зерна и получения низкой твердости, а также структуры зернистого перлита, как наиболее удовлетворяющей последующей закалке. Наиболее целесообразно применять изотермический отжиг, включающий нагрев до температур, близких или немного выше Ас1, выдержку после прогрева металла (определяется массой садки) не менее 2−3 часов, медленное охлаждение с печью до температур несколько ниже Аr1, выдержку продолжительностью 3−4 часа, медленное охлаждение до 600−650оС, затем на воздухе. Преимуществом изотермического отжига является получение более однородной структуры после последующей закалки, особенно для сталей с небольшим содержанием карбидной фазы.
Для полутеплостойких сталей повышенной вязкости температуры отжига и высокого отпуска составляют соответственно 760−800оС и 650−690оС. Данные стали чаще подвергают отпуску, чем отжигу, так как переохлажденный аустенит этих сталей имеет особо высокую устойчивость, а температура его минимальной устойчивости весьма низкая. Эти факторы значительно увеличивают продолжительность отжига, снижают скорость коагуляции карбидов и поэтому затрудняют получение низкой твердости.
Структура их после отжига — пластинчатый перлит с участками феррита, который имеет твёрдость 197−241НВ.
Для полутеплостойких сталей повышенной вязкости температура нагрева под закалку составляет 830−870оС в зависимости от марки стали с предварительным подогревом при 600−620оС.
Высокий отпуск проводится для получения сорбитной структуры (температура отпуска 500−600оС, скорость нагрева 40−50 град/час). Охлаждение после отпуска на воздухе. Инструмент обрабатывается, как правило, на твердость 35−40 HRC или 40−46 HRC.
Для марки стали 4Х5МФС закалка осуществляется при температуре 1010−1040 оС, а отпуск при 580−590 оС.
При температуре закалки 1 100°C обеспечивается достаточно мелкое зерно, соответствующее 8 баллу, что допустимо. Однако более предпочтительной для закалки является температура 1 070оС, так как в этом случае исключается возможность перегрева стали (балл аустенитного зерна 9).
При закалке важной задачей является защита от обезуглероживания; поскольку температуры закалки — высокие. Обязательно применение мер защиты; наиболее целесообразен нагрев в контролируемых атмосферах или в вакууме.
После закалки данные стали рекомендуется подстуживать на воздухе до 950−900оС, а затем охлаждать в масле.
Операцию отпуска выполняют немедленно после закалки с целью предупреждения трещин. Как правило, отпуск производят на твердость 45 HRC в штамповых сталях, предназначенных для высадки и выдавливания; 48−53 HRC для ножей и пил горячей резки.
Поскольку при нагреве для отпуска в структуре сохраняется много аустенита, целесообразно проведение двукратного отпуска. Температура второго отпуска может быть на 10−20оС ниже, а его продолжительность на 20−25% меньше, чем первого отпуска. Охлаждение после отпуска проводится на воздухе.
Выводы При выполнении курсовой работы был изучен фазовый состав, структура, свойства и назначения марок стали 35ХГ2 и 4Х5МФС. Основные виды термообработок таких как закалка и отпуск. Проведён анализ изотермического и термокинетического распада переохлаждённого аустенита на основании которых решают вопросы прокаливаемости, режимов термической обработки и механических свойств детали. Изучены режимы термообработки поршневого пальца изготовленного из стали 35ХГ2 и штамповых сталей для горячего деформирования из стали марки 4Х5МФС.
Список літератури термообработка сталь штамп поршневой.
1. Гуляев, А. П. Металловедение: учебник для вузов / А. П. Гуляев. — М.: Металлургия, 1986.
2. Металловедение и термическая обработка стали: справочник. Т. 1. Методы испытаний и исследования / под ред. М. Л. Бернштейна, А. Г. Рахштадта. — М.: Металлургия, 1983.
3. Седов Ю. Е., Адаскин А. М. Справочник молодого термиста. — М.: Высшая школа, 1986.
4. Лахтин Ю. М., Леонтьева В. П. Материаловедение. — М.: Машиностроение, 1990.
5. Марочник сталей и сплавов. 2-е изд., доп. и испр. / А. С. Зубченко, М. М. Колосков, Ю. В. Каширский и др. Под общей ред. А. С. Зубченко — М.: Машиностроение, 2003.
6. Самохоцкий А. И. Технология термической обработки металлов, М., Машгиз, 1962.
7. Куцова В. З., Ковзель М. А., Носко О. А Легированные стали и сплавы с особенными свойствами. — Днепропетровск: НМетАУ, 2008.
8. Попов А. А., Попова А. Е Изотермические и термокинетические диаграммы распада переохлаждённого аустенита. — М: Машиностроение, 1961.