Высококальциевая зола-унос
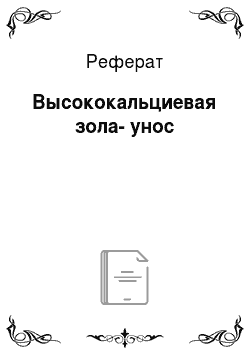
Предлагаемое разделение высококальциевых зол по основности и содержанию в них свободной закрытой извести позволяет для зол с основностью по коэффициенту основности более 0,7 и содержанием свободной закрытой извести более 1,4% осуществить глубокую переработку, включающую помол и силосование, что обеспечивает последующее бездефектное твердение силикатного кирпича, стабилизацию характеристик… Читать ещё >
Высококальциевая зола-унос (реферат, курсовая, диплом, контрольная)
Содержание Введение Высококальциевая зола-уноса
1. Вяжущие на основе высококальциевой золы для силикатного кирпича
1.1 Состав и строение зол ТЭС
1.1.1 Химический состав
1.1.2 Минералогический состав
1.1.3 Гранулометрический состав
1.2 Свойства зол ТЭС
1.2.1 Физические свойства
1.2.2 Химическая активность
1.2.3 Термические свойства
1.3 Классификация зол как сырья для изготовления строительных материалов
1.3.1 ВКЗ
1.4 Способы улучшения использования зол
1.4.1 Гашение пережога
1.4.2 Карбонизация
1.5 Известково-золопесчанные смеси для производства
1.6 Получение вяжущих на основе высококальциевых зол ТЭЦ Список литературы Введение Высококальциевая зола-уноса Зола-уноса — тонкодисперсный продукт высокотемпературной обработки минеральной части углей. Зола-уноса по своей природе может быть кислой (богатой кварцем — SiO2) либо основной (богатой оксидами кальция — СаО). Первая проявляет пуццоланические свойства, вторая дополнительно проявляет свойства самостоятельного вяжущего.
По химическому, гранулометрическому и фазово-минералогическому составам золы-уноса во многом идентичны природному минеральному сырью. Это позволяет использовать их для производства строительных материалов и изделий самой широкой номенклатуры: портландцемента, смешанных и бесцементных вяжущих, обжиговых (зольного гравия, золоаглопорита) и безобжиговых заполнителей, стеновых материалов (силикатного и глинозольного кирпича, керамических камней, плитки, пенокерамики), строительных растворов и бетонов плотной и ячеистой структур, получения камнелитных изделий, пропантов для расклинивания скважин при добыче нефти, а также для дорожного строительства и т. д. Высококальциевые золы-уноса сухого улавливания можно применять в качестве самостоятельного вяжущего, а также как активную добавку к неорганическим и органическим вяжущим веществам.
1. Вяжущие на основе высококальциевой золы для силикатного кирпича На основе топливных зол и шлаков и воздушной или гидравлической извести могут быть получены бесклинкерные известково-зольные и известково-шлаковые вяжущие. Они получаются совместным помолом извести с золой или шлаком и двуводным гипсом (в количестве до 5%). Количество извести допускается в вяжущем до 50% общей массы.
Требования к золам определены ОСТ 21 9—81. В соответствии с этими требованиями особое внимание уделяется содержанию в золах ангидрида серной кислоты (не более 5%), а также частиц не сгоревшего топлива (ППП — не более 5%). Состав известково-золошлаковых вяжущих зависит от химического состава зол или шлаков.
При использовании кислых зол и шлаков (с содержанием СаО 5… 10%) берут 20…40% извести и 60…80% золы или шлака, при использовании основных зол или шлаков (с содержанием СаО 30…50%) количество извести уменьшается до 10…30%, золы или шлака увеличивается до 70…90%.
Тонкость помола вяжущих характеризуется остатком на сите с сеткой № 008 не более 10%.
Оптимальные составы известково-золошлаковых вяжущих устанавливают опытным путем, учитывая их назначение и условия твердения. Технология вяжущих заключается в дозировании и совместном помоле указанных компонентов. При необходимости золу или шлак подсушивают до остаточной влажности 2…3%.
Такие вяжущие отличаются замедленным твердением в нормальных условиях. Повышение температуры до 85…95 °С способствует значительному ускорению твердения, а автоклавная обработка при 174…200 °С ведет к получению еще более высоких показателей. Водопотребность известково-золошлаковых вяжущих в тесте нормальной густоты 30… 35%. Насыпная плотность известково-зольных вяжущих в рыхлом состоянии 700…800, а в уплотненном — 900…1200 кг/м3.
Твердение известково-зольных и известково-шлаковых вяжущих происходит в результате взаимодействия кремнеземисто-глиноземистых соединений золы с известью и водой. Образующиеся цементирующие вещества представлены гидросиликатами и гидроалюмосиликатами кальция различной основности.
Известково-зольные вяжущие подразделяют на марки 50, 100, 150, 200. Прочность и другие свойства вяжущих определяют в соответствии с ГОСТ 310.4−81*.
Существенным недостатком указанных вяжущих является их пониженная воздухои морозостойкость. Для улучшения этих свойств, а также для повышения прочности рекомендуется вводить в состав вяжущих 15…25% портландцемента.
Себестоимость известково-зольных вяжущих меньше себестоимости портландцемента и шлакопортландцемента соответственно в 2,3 и 1,5 раза. Применение бесклинкерных вяжущих на основе топливных зол и шлаков снижает себестоимость бетона на 2…2,5 руб/м3.
Строение и состав золы зависит от целого комплекса одновременно действующих факторов: вида и морфологических особенностей сжигаемого топлива, тонкости помола в процессе его подготовки, зольности топлива, химического состава минеральной части топлива, температуры в зоне горения, времени пребывания частиц в этой зоне и др. При значительном содержании карбонатов в минеральной части исходного топлива под воздействием высоких температур в процессе горения образуются силикаты, алюминаты и ферриты кальция — минералы, способные к гидратации. Такие золы при затворении водой способны к схватыванию и самостоятельному твердению. В них, как правило, содержатся окись кальция и окись магния в свободном состоянии.
1.1 Состав и строение зол ТЭС Химический и минерально-фазовый состав зол и шлаков ТЭС, их строение и свойства зависят от состава минеральной части топлива, от режима его сжигания и теплотворной способности, от способа улавливания и удаления золы и шлака, от места их отбора.
1.1.1 Химический состав Золы и шлаки от сжигания каменных углей и антрацитов по химическому составу представлены в основном Si02 и Аl203. Содержание СаО обычно не превышает в них 5%. Основную массу топливных зол составляют именно такие золы.
Соотношения главных оксидов в золах ТЭС в среднем таковы: Si02 — 40…58%, Аl203 — 21…27, СаО — 4…6, Fe203 — 4…17, Na20- 0,4…1,4, К20 — 0,4…4,7%. Помимо этого в состав зол входят S03, MgO, Ti02 и др. Нормативные требования к химическому составу зол ТЭС призваны обеспечить надлежащую прочность и долговечность бетона. Верхний предел содержания S03 (< 3%) в золах ограничен требованиями сульфатостойкости. Для обеспечения равномерности изменения объема при твердении вяжущего с золой содержание свободного СаО не должно превышать 2…5% в зависимости от вида золы, a MgO — 5%. Суммарное содержание Na20 и К20 в золах должно быть менее 1,5… 3% (в зависимости от вида исходного угля) во избежание возможных деформаций при их реакции с заполнителями.
Стандарты ограничивают также нижний предел содержания Si02 — 40% либо Si02 + Аl203 + Fe203 — 50…70% (в зависимости от вида золы), от которых в значительной степени зависит активность золы.
Высококальциевые золы и шлаки образуются при сжигании углей Канско-Ачинского бассейна (СаО — 20…40%) бурых углей месторождений Украины и Урала, каменных углей некоторых месторождений Средней Азии и Дальнего Востока (СаО > 10%), а также горючих сланцев (СаО до 45%).
В зависимости от вида углей и условий их сжигания в золах может содержаться 0,5…20% и более несгоревших органических частиц топлива. Они считаются вредными примесями, ухудшающими важнейшие технические свойства бетонов с золой. Содержание остатков топлива оценивается по потерям при прокаливании пробы золы при 1000° С. Стандарты устанавливают допустимое содержание органических остатков в золах в зависимости от вида исходного угля (антрацит, каменный или бурый уголь), вида бетона (тяжелый, легкий), вида бетонной конструкции (армированная, неармированная). По этим признакам допустимое содержание органических остатков колеблется в буроугольных золах в пределах 2…5%, в каменноугольных — 3…10, в антрацитовых — 5…20%.
1.1.2 Минералогический состав Минерально-фазовый состав. Из рассмотрения процессов, происходящих при сжигании твердого топлива, следует, что золы ТЭС состоят из неорганической и органической фаз. Неорганическая фаза включает аморфную и кристаллическую составляющие. Аморфная составляющая может быть представлена стеклом и аморфизованным глинистым веществом. Кристаллическая составляющая включает, во-первых, слабоизмененные зерна минералов исходного топлива (кварц, полевые шпаты и другие термически устойчивые минералы), а во-вторых, кристаллические новообразования, возникшие при сжигании топлива (муллит, гематит, алюминат кальция и др.).
Стекло в золах может быть силикатного, алюмосиликатного, а иногда железистоалюмосиликатного состава. В зависимости от состава стекло может быть бесцветным, желтым, бурым и даже черным.
Вид аморфной фазы (метакаолинит, слабоспекшееся аморфизованное глинистое вещество, спекшееся и частично остеклованное стекло) определяет химическую активность золы, форму и характер поверхности зольных частиц.
Большинство зол имеют сферическую форму частиц и гладкую остеклованную фактуру поверхности. Однородность шарообразных частиц может быть различной. Наиболее однородны частицы, полностью состоящие из стекла. Имеются также частицы, внутренняя часть которых не расплавилась в процессе сжигания топлива и слагается из мельчайших минеральных и коксовых зерен. Встречаются и полые шарики в результате вспучивания стекла в момент образования частицы. Размер сферических частиц колеблется от нескольких микрон до 50…60 мкм.
Встречаются в золах также стекловидные частицы неправильной формы. Некоторые частицы содержат различное количество пузырьков, так что их поверхность может быть губчатой. Они тоже могут содержать во внутренней части большое количество кристаллических веществ.
Если температура сжигания топлива недостаточно высока, а его зольная часть тугоплавка, образуются золы, состоящие в основном из аморфизованного глинистого вещества, представленного пористыми частицами неправильной формы. Пористые частицы имеют высокое водопоглощение.
В крупных фракциях золы содержатся частицы-агрегаты, образовавшиеся в результате спекания множества мелких зерен. Такие частицы неоднородны и непрочны, что отрицательно сказывается на свойствах бетона, содержащего золу. Измельчение таких частиц повышает однородность и гидравлическую активность золы, а ввиду их низкой прочности не требует больших затрат времени и энергии.
1.1.3 Гранулометрический состав Гранулометрический состав зол определяет многие строительно-технические свойства. Зола, улавливаемая в электрофильтрах, обычно имеет удельную поверхность более 200 м2/кг, и основная ее часть (80−90%) проходит через сито № 008 с диаметром отверстий 80 мкм.
Применение ситового и седиментационного методов оценки дисперсности зол показывает, что около половины массы частиц имеют размеры от 10 до 30 мкм и еще 10−20% частиц имеют размер от 30 до 50 мкм. Фракции золы размером 0−10 мкм составляют от 3 до20% ее массы, фракции размером 50−100 мкм составляют обычно не более 15% массы золы. Средний размер зольных частиц равен 30−40 мкм.
1.2 Свойства зол ТЭС
1.2.1 Физические свойства Физические свойства. Важнейшими физическими свойствами зол и шлаков ТЭС являются их насыпная и истинная плотность, а также гранулометрический состав.
Гранулометрический (зерновой) состав пылевидных зол зависит от вида топлива, условий его подготовки, режима сжигания, способа улавливания золы и места ее отбора. Наиболее крупные частицы золы улавливаются циклонами, мелкие и мельчайшие — электрофильтрами, причем на каждом поле электрофильтра собирается определенная фракция золы. Максимальное содержание сферических стекловидных частиц имеют мельчайшие фракции золы. Чем крупнее фракция, тем выше в ней содержание агрегированных, шероховатых, пористых частиц.
Системы совместного гидроудаления золы и шлака направляют в отвалы полидисперсные шлакозольные смеси. Вблизи места выпуска пульпы образуется шлаковая зона отвала с преобладанием частиц крупнее 0,25 мм, в отдалении — зольная зона с частицами менее 0,25 мм. В стандартах разных стран используется характеристика дисперсности золы, оцениваемая по удельной поверхности, которая должна быть не менее 2700…4000 см2/г. Этим подчеркивается желательность использования мелких фракций золы.
От гранулометрического, химического и фазового состава золы зависит ее насыпная плотность, которая для различных зол находится в пределах 600… 1300 кг/м3. Истинная плотность золы различных углей может колебаться от 1,75 до 3,5 г/см3 и в среднем составляет 2,1… 2,4 г/см3[1].
1.2.2 Химическая активность Химическая активность является наиболее важным свойством зол и шлаков ТЭС, обусловливающим возможность их применения в составе вяжущих веществ и бетонов. Способностью к непосредственному взаимодействию с водой топливные золы, как правило, не обладают. Это характерно лишь для высококальциевых зол, содержащих свободные оксиды кальция и магния. В то же время аморфные компоненты зол обладают так называемой пуццолановой активностью, т. е. способностью при обычных температурах связывать гидроксид кальция с образованием нерастворимых соединений. Накопление нерастворимых новообразований дает возможность гидравлического (сначала на воздухе, а затем и в воде) твердения вяжущих из смесей извести с золой.
Пуццолановой активностью в составе зол обладают продукты обжига глин: аморфизованное глинистое вещество типа метакаолинита, аморфные Si02 и Аl203 и алюмосиликатное стекло. Реакционная способность по отношению к гидроксиду кальция у них различна и связана с температурными превращениями каолиновых глин при сжигании топлива. Обладающий большой удельной поверхностью метакаолинит Аl2 03 * 2 Si02 активно реагирует с Са (ОН) 2 при обычных температурах с образованием гидросиликатов кальция и гидрогеленита по следующей реакции:
Аl203 * 2Si02 + 3 Са (ОН)2 + (n+ 5) Н20 = 2СаО * Аl203 * Si02 *8Н20 + + СаО * Si02 * Н20
Активность образующихся при более высоких температурах аморфных Si02 и Аl2 03 заметно меньше, что объясняется резким снижением удельной поверхности вследствие спекания и кристаллизации новообразований (муллита, кристобалита).
Высокотемпературное спекание и плавление глинистых минералов резко снижает их удельную поверхность и соответственно активность, поэтому стеклофаза зол малоактивна при обычных температурах. Установлено, что повышение температуры сжигания топлива сверх допустимого предела приводит к падению активности большинства топливных зол.
Водотепловая обработка (пропаривание при нормальном давлении, автоклавирование) резко увеличивает активность всех аморфных фаз зол, в особенности спекшихся и остеклованных. Продуктами взаимодействия пуццоланового компонента с Са (ОН)2 при повышенных температурах являются гидросиликаты кальция состава СаО * Si02 * Н2 О и гидроалюмосиликаты кальция (гидрогранаты).
При повышенных давлении и температуре проявляют активность и некоторые кристаллические компоненты зол (кварц, полевые шпаты, алюмосиликаты кальция).
1.2.3 Термические свойства Термические свойства. Без исследования термических свойств зол ТЭС нельзя установить их Пригодность для производства искусственных пористых заполнителей, минеральной ваты, жароупорного бетона и других материалов, изготовление которых связано с нагреванием до высоких температур.
При нагревании до 100…300 °С пылевидные золы теряют адсорбированную воду. Причем, чем больше в золе аморфизованного глинистого вещества и органических остатков, тем больше она адсорбирует воды. При температуре 400…700 °С из золы выгорают органические остатки топлива. При 700…850 °С происходит разложение имеющихся в золе карбонатов, а при 920…980 °С происходит кристаллизация аморфизованного глинистого вещества и стеклофазы.
Высокотемпературные процессы включают размягчение частиц золы, их контактное спекание, вспучивание и кристаллизацию при охлаждении. Плавкость золы оценивают по трем показателям: началу деформации, началу размягчения и началу жидкоплавкого состояния. Различные по составу золы размягчаются при 1050…1470 °С, а плавятся при 1250… 1710 °C.
1.3 Классификация зол как сырья для изготовления строительных материалов С целью выбора рационального направления использования золошлаковых материалов их классифицируют по различным признакам. Поскольку состав и свойства их отличаются непостоянством, единой классификации золошлаковых материалов, которая охватывала бы все признаки, еще не создано. Поэтому мы рассмотрим несколько классификаций, применяемых в строительстве.
В соответствии с ГОСТ 25 818–91 все золы по виду сжигаемого угля подразделяют на:
антрацитовые, образующиеся при сжигании антрацита, полуантрацита и тощего каменного угля (А);
каменноугольные, образующиеся при сжигании каменного, кроме тощего, угля (КУ);
буроугольные, образующиеся при сжигании бурого угля (Б).
В зависимости от химического состава золы подразделяют на типы:
кислые (К) — антрацитовые, каменноугольные и буроугольные, содержащие оксид кальция до 10%;
основные (О) — буроугольные, содержащие оксид кальция более 10% по массе.
Золы в зависимости от качественных показателей подразделяют на 4 вида:
I — для железобетонных конструкций и изделий из тяжелого и легкого бетонов;
II — для бетонных конструкций и изделий из тяжелого и легкого бетонов, строительных растворов;
III — для изделий и конструкций из ячеистого бетона;
IV — для бетонных и железобетонных изделий и конструкций, работающих в особо тяжелых условиях (гидротехнические сооружения, дороги, аэродромы и др.).
В соответствии с ОСТ 34 70−542−81 «Зола-унос тепловых электростанций. Общие технические требования» золы классифицируют исходя из районирования многочисленных месторождений угля и подчинения их крупным регионам. Этот стандарт устанавливает требования к пылевидным золам, полученным при сжигании донецких, подмосковных, львовско-волынских, кузнецких, экибастузских, ирша-бородинских, назаровских углей и прибалтийских сланцев. Помимо показателей химического состава и дисперсности нормируется характеристика плавкости зол, что необходимо в случае их применения для производства обжиговых материалов.
Помимо приведенных в стандартах существует ряд классификаций, разработанных различными исследователями, например, в зависимости от места осаждения и отбора зол. По-разному осажденные золы отличаются существенными особенностями. Зола-провал, выпадающая из турбулентных потоков газов в бункер подтопочного пространства, имеет крупные частицы с наибольшей истинной плотностью. Зола-унос, выносимая из зоны сгорания топлива дымовыми газами и улавливаемая в аппаратах очистки, высокодисперсна. Чем больше ступеней очистки проходят отходящие газы, тем мельче выпадающие из них частицы золы. Мелкие и мельчайшие фракции золы содержат наибольшее количество шарообразных частиц и меньше несгоревших органических остатков. При добавке в бетон они наиболее активно проявляют пуццолановые свойства и повышают удобоукладываемость бетонной смеси.
Существует ряд классификаций зол ТЭС по химическому составу. В основу их положено содержание различных оксидов: Si02, Аl2 03, Fe2 03, CaO, MgO. В зависимости от их соотношения золы делят на два класса: I — золы, при смешении с водой затвердевающие в камневидное тело; II — затвердевающие лишь при смешении с известью и водой, т. е. обладающие пуццолановыми свойствами. Этот признак наиболее важен, потому что золы, имеющие высокую гидравлическую активность и способность к самостоятельному твердению, обычно непригодны для получения многих обжиговых материалов. Класс золы определяется значением модуля основности, выраженного отношением (СаО + Mg0)/(Si02 + Аl203).
По содержанию СаОобщ. Все золы классифицируются на высококальцевые — СаОобщ. Более 10% и низкокальцевые — СаОобщ. Менее 10%. Золы с высоким содержанием СаО + MgO целесообразно использовать в первую очередь в качестве сырья для производства вяжущих веществ, а низкокальциевые — в качестве активных заполнителей в ячеистых бетонах, активных минеральных добавок к цементам и бетонам, в производстве кирпича, искусственных пористых заполнителей и т. д.
Классификация зол ТЭС по фазовому составу учитывает три возможные фазовые составляющие: стекло, возникающее при быстром охлаждении расплавленных минеральных компонентов топлива; частично закристаллизованная фаза, образующаяся при медленном охлаждении шлакового расплава; аморфизованное вещество неорганической части топлива. Наиболее активная составляющая зол и шлаков — стекло. Аморфизованное глинистое вещество также является активной составляющей. Частично закристаллизованная фаза обладает пониженной активностью. От соотношения трех указанных фазовых составляющих и их индивидуальных особенностей зависит гидравлическая активность зол и шлаков, а следовательно, и возможные направления их использования.
По активности золы классифицируются на активные, скрытоактивные, инертные.
1.Активные Мо=0,5−2 СаОобщ.-20−60% СаОсвоб. До 30% Кк=1−3,6
2.Скрытоактивные Мо=0,1−0,5 СаОобщ.-5−20% СаОсвоб. До 0−2% Кк=0,5−1,5
3.Инертные Мо менее 0,1 СаОобщ.-0,5−5% СаОсвоб. До 0−1% Кк=0,4−0,9
К первой группе относятся золы, обладающие самостоятельными вяжущими свойствами, вторая и третья группы, главным образом, кислые золы, не обладающие самостоятельными вяжущими свойствами и требующие активаторов твердения.
1.3.1 ВКЗ По словам Главного технолога ООО «Строительные Технологии Сибири», к.т.н. Д. А. Киселева зола-уноса (далее — зола) представляет собой тонкодисперсный материал, состоящий, как правило, из частичек размером от долей микрона до 0,14 мм. Зола образуются в результате сжигания твердого топлива на ТЭС, и улавливается электрофильтрами, после чего в сухом состоянии отбирается с помощью золоотборника на производственные нужды, либо вместе с водой и шлаком отправляется на золоотвал.
К высококальцевым золам относятся золы Прибалтийских сланцев, золы Приволжских сланцев и золы Канско-Ачинских бурых углей (КАТЭК). Наибольшее распространение в России, особенно в Сибири, получили золы КАТЭК, поскольку запасы этих углей составляют 40% от общероссийских. На этих углях работают ТЭЦ-3 г. Новосибирска, все три ТЭЦ г. Красноярска, а также ТЭЦ г. Барнаула, Ачинска, Омска и др., всего в отвалах накоплено 24 млн. т. Этих зол, а ежедневно только ТЭЦ-3 г. Новосибирска выбрасывает в отвалы 200 т. Этой золы. К достоинствам этих зол относится то, что они обладают самостоятельными вяжущими свойствами в силу присутствия в них клинкерных минералов СаОсвоб., гипса, следовательно, эти золы могут использоваться как замена части цемента в пенобетоне.
Высококальцевые золы твердых топлив являются многофазными материалами с вяжущими свойствами. Количественное содержание отдельных минералов в них различно. Вяжущие свойства зависят от состава и соотношения фаз, слагающих золы. Оптимальное соотношение этих фаз позволяет получать максимальную гидравлическую активность и улучшить физико-химические свойства материала. Определение оптимальных составов вяжущих материалов возможно лишь в том случае, если хорошо изучены гидравлическая активность фаз и механизм взаимодействия между ними. Фазы, слагающие Высококальцевые золы, могут быть объединены по типу твердения или по свойствам в следующие группы:
— клинкерные материалы (силикаты, алюминаты, алюмоферриты, и ферриты кальция).
— воздушные вяжущие вещества (свободная окись кальция, свободная окись магния, полуводный и безводный сульфат кальция).
— стекловидная фаза (кислое, основное стекло, малилиты)
— нерастворимый остаток.
Благодаря неоднородному составу зерен топливной смеси и возможности контактирования пылинок, сгорающих во взвешенном состоянии в потоке, все химические процессы проходят в объемах отдельных частиц. Это приводит к тому, что клинкерные и железосодержащие минералы и основное количество СаО (своб.) сосредоточены в тяжелой фракции золы (удельный вес >2,88), в средней фракции (1,83−2,88) в основном содержатся кварц, алюмосиликатное стекло и СаО (своб.), в легкой фракции (<1,83) сосредоточены полые шарики силикатного стекла.
Существует взаимосвязь между химическими свойствами фаз и гидравлической активностью высококальцевых зол. Все фазы, слагающие золы, в зависимости от способности к гидратации и твердению можно отнести к двум видам:
Фазы, способные гидратироваться: это клинкерные минералы и воздушные вяжущие вещества.
Фазы, способные гидратироваться и образовывать искусственный камень только в присутствии активаторов твердения: это стекловидная фаза и нерастворимый остаток.
Стекловидная фаза гидратируется и твердеет лишь при наличии свободной окиси кальция и сульфата кальция, нерастворимый остаток — в результате взаимодействия со свободной окисью кальция.
1.4 Способы улучшения использования зол
1.4.1 Гашение пережога Наиболее радикальным способом устранения деструктивных явлений при твердении зол является их предварительная автоклавная обработка. Проведенные исследования в Красноярском филиале ВНИСТРОМа, Алтайском политехническом институте (АлтПИ), ЛТИ показали, что золы всех составов С1-С3 после запаривания в сухом состоянии в дальнейшем обладают равномерностью изменения объема в автоклавных плотных изделиях. Параметры автоклавной обработки могут иметь низкие величины для зол составов С1-С3 (давление пара 0,4−0,6 МПа, пиковый режим запаривания 0+2+0+2 ч) или обычные величины для технологии обработки сильных изделий.
Следует отметить, что некоторые золы составаС1, полученные из ирша-бородинского угля, могут содержать повышенное количество периклаза, который трудно гасится при низких параметрах тепловлажнастной обработки. Запаривание снижает самостоятельную гидравлическую активность зол 30−70%. Однако при активизации их цементом достигается прочность смешанных вяжущих по типу С1.
Как показали исследования, и последующая дегидротация предварительно загашеной золы (в автоклаве или золоотвале) при 750−800оС и атмосферном давлении или вакууме (приблизительно 1кПа) позволяет получить быстротвердеющее вяжущее активностью 10−20МПа.
1.4.2 Карбонизация Углекислый газ во влажных условиях переводит СаО и Са (ОН)2 в СаСО3, устраняя дестртуктивные явлении при последующем твердении зол. Для зол составом С1-С2 в плотном материале (прессование под давлением 20 Мпа) скорость карбонизации изменяется от 5−7 мм/мин в начале процесса до 0,3−0,4 мм/мин на глубине 25−30 мм при давлении углекислого газа 0,9 МПа.
вяжущий зола шлак гашение
1.5 Известково-золопесчанные смеси для производства Силикатными называют искусственные каменные материалы и изделия, получаемые в результате формования и последующей тепловлажностной обработки в автоклавах смесей, состоящих из извести или других вяжущих на ее основе (известково-кремнеземистых вяжущих), заполнителей (кварцевого песка, шлака и др.) и воды. Твердение таких композиций осуществляется при температуре насыщенного пара 174 °C и более и давлении — 0,8 МПа и выше. В этих условиях Si02 песка приобретает химическую активность и между ним и известью происходит взаимодействие с образованием гидросиликатов; кальция, цементирующих зерна песка в прочный монолит.
Производство силикатного кирпича является материалоемким: для выпуска 1 тыс. шт. расходуется 2,3…2,5 м³ песка и 350…400 кг извести.
Введение
в состав массы для производства кирпича активных высокодисперсных добавок, какими являются золы ТЭС, позволяет существенно снизить расход извести и песка. В производстве силикатного кирпича применяют как кислые, так и основные золы ТЭС. Причем они могут использоваться при приготовлении известково-зольного вяжущего и в качестве кремнеземистого компонента вместо песка.
Известково-зольное вяжущее готовят совместным помолом извести и золы в соотношении 75:25.
Введение
20…30% золы в силикатные смеси взамен кварцевого песка повышает прочность кирпича-сырца на 30…40%, а запаренных образцов на 60…80%.
Оптимальное количество вводимой золы взамен кварцевого песка -;
40…50%. При этом улучшаются формовочные свойства массы, увеличивается прочность сырца, а также улучшаются условия работы прессов. Расход воды в зависимости от количества золы меняется от 9 до 16% от массы смеси. Обычно смесь перед формованием выдерживается в течение 3…4 ч, затем подвергается прессованию под давлением 15…20 МПа. Тепловлажностная обработка производится в автоклавах по режиму (2…4) + (6…8) + 2 ч (подъем температуры + изотермическая выдержка + остывание).
Оптимальная добавка золы зависит от крупности и зернового состава песка, расхода и дисперсности известкового вяжущего, дисперсности самой золы.
Золосиликатный кирпич по сравнению с обычным силикатным кирпичом характеризуется повышенной прочностью на сжатие и изгиб, более высоким модулем упругости, меньшим коэффициентом размягчения (табл. 8). Морозостойкость его достигает 35…45 циклов и выше, тогда как у силикатного кирпича — 15…25 циклов, деформации усадки и набухания золосиликатного кирпича несколько выше, чем у обычного.
Таблица 8
Содержание золы взамен песка, % | Прочность, МПа | Водопоглощение, % по массе | Влажность после запаривания, % | Коэффициент размягчения | Средняя плотность, кг/м3 | |
0,57 | ||||||
0,6 | ||||||
0,67 | ||||||
0,7 | ||||||
0,72 | ||||||
0,75 | ||||||
0,78 | ||||||
Увеличение доли золы в золосиликатном кирпиче (см. табл. 8) сопровождается значительным уменьшением средней плотности на 15… 20%).
Отрицательными особенностями золосиликатного кирпича являются повышенная влажность и водопоглощение, что свойственно всем бетонам на основе зол.
Использование некоторых технологических приемов позволяет улучшить эти свойства. Так, например, влажность кирпича после автоклавной обработки может быть уменьшена при продувке автоклава и создании режима сушки по окончании тепловлажностной обработки.
Существенное влияние на прочность золосиликатного кирпича оказывает введение в сырьевую смесь двуводного гипса в количестве 0,5…1% от ее массы. При этом возможно сокращение продолжительности тепловлажностной обработки. Технико-экономические расчеты показывают, что при использовании золы расход извести может быть сокращен в среднем на 30…35%.
1.6 Получение вяжущих на основе высококальциевых зол ТЭЦ Рассмотрим исследования проведенные студентами АлтГТУ. На ТЭЦ-3 г. Барнаула были отобраны три пробы высококальциевой электрофильровой золы от сжигания бурого угля КАТЭКа с различной основностью и содержанием свободной извести от 2,4 до 5,4% (таблицы 1и 2). Не смотря на значительное отличие в содержании свободной извести в ВКЗ, по основности их можно отнести к высокои среднеосновным.
Золы и золошлаковые отходы в естественном состоянии или после дополнительного помола при 50, 100 или 150% затрат энергии на стандартный помол клинкера на цемент, смешивались с предварительно молотыми известью и гипсом в количестве соответственно 5−15 и 2,5−7,5%. В качестве гранулометрической добавки к массе добавлялся обской или шлаковый пески в количестве 20%. Сырьевая смесь увлажнялась, гермети-зировалась в полиэтиленовых пакетах и силосовалась при 60 °C в течение 2−4 часов.
Таблица 1 — Характеристики высококальциевых зол ТЭЦ-3 г. Барнаула Таблица 2 — Химический состав зол и золошлаков ТЭЦ-2 и ТЭЦ-3 г. Барнаула Примечание: коэффициент качества Кк определен по ГОСТ 3476–74 «Шлаки доменные и электротермофосфорные для производства цемента». Косн. — по П. И. Боженову.
После этого из массы формовались образцы-цилиндры диаметром и высотой 50 мм при удельном давлении прессования 20 МПа с равномерной подачей нагрузки, которые запаривались в автоклаве при давлении 1,0 МПа и изотерме в 6 часов. Контрольные образцы изготавливались из молотой извести и кварцевого песка по той же методике и запаривались при каждой автоклавной обработке для получения сравнительных характеристик.
Для золы с Косн=0,8 еще может добавляться до 5% извести с незначительным повышением прочности. Более высокая добавка извести (10% и более) приводит к значительному снижению прочности кирпича. Для зол высокой основности с коэффициентом основности Косн=1,40−1,45 с их помолом или без помола добавка извести и/или гипса приводит только к снижению прочностных показателей автоклавированного материала.
Максимальную прочность показывают составы на золе без этих добавок. С повышением основности золы и увеличением в ней содержания свободной извести от 2,4 до 5,4% наблюдается снижение прочности и особенно заметно с добавлением к золам извести.
В результате камень из наиболее основных зол, даже дважды автоклавированных, показывает низкую морозостойкость. Это должно быть обусловлено неоптимальным по основности составом вяжущего, а не влиянием свободных СаО и МgO.
Поэтому далее в работе осуществляли оптимизацию основности многокомпонентного вяжущего добавлением к ВКЗ кислой золы (КУЗ) ТЭЦ-2 от сжигания каменного угля (табл. 2), а также смеси из кислой каменно-угольной золы и извести для исследования влияния основности связки при разном содержании ВКЗ в сырьевой смеси. Добавление ВКЗ только КУЗ (без извести) показывает оптимальную основность связки при Косн. около 0,8−1,0. При добавке 10−15% извести и КУЗ к уменьшенному количеству ВКЗ оптимальная основность вяжущего остается на том же уровне. Однако прочность таких известьсодержащих композиций заметно уменьшается. Это говорит о том, что известь, находящаяся в фазах ВКЗ обеспечивает большую прочность автоклавного камня, чем известь, добавляемая в свободном виде совместно с кислой золой. Напомним, что основность и в том и другом случае — одинаковая, но природа извести — разная.
Применение в качестве кислого компонента молотого кварцевого песка также показывает оптимум основности при Косн. = 0,8−1,0. Прочность материала при этом значительно выше предыдущих вариантов.
Предварительно автоклавированные высококальциевые золы ТЭЦ без добавок и без помола обеспечивают получение силикатного кирпича достаточно высокой прочности.
Однако они значительно варьируют по химическому составу, поэтому для оптимизации основности автоклавного вяжущего необходимо обеспечивать требуемые значения Косн. за счет добавок кислого или основного характера или их смесями. В качестве таких добавок могут выступать молотые кварцевые или полевошпатовые пески, кислые золы ТЭЦ от сжигания каменного угля, товарная известь и другие.
Известны способы получения силикатного кирпича с использованием золы тепловых электростанций — Московской ТЭЦ-22 и Казанской ТЭЦ-2, включающие введение и смешивание таких компонентов, как известь и зола, помол вяжущего, приготовление силикатной массы из вяжущего и песка, введение в силикатную массу золы и прессование силикатной массы с золой (см. Хавкин Л. М. Технология силикатного кирпича, — М.: Стройиздат, 1982. — С. 108−114, табл. IV. 3).
Известен способ получения силикатного кирпича с использованием золы тепловой электростанции — Черпетской ТЭС, включающий введение и смешивание извести и золы, помол вяжущего, приготовление силикатной массы из вяжущего и песка, прессование полученной силикатной массы (см. Хавкин Л. М. Технология силикатного кирпича. — М.: Стройиздат, 1982. — С. 108−114, табл. IV.3).
Наиболее близким к предлагаемому изобретению по технологической сущности и достигаемому результату (прототипом) является способ получения силикатного кирпича с использованием высококальциевой золы тепловой электростанции — Черкасской ТЭС, включающий введение и смешивание компонентов, в качестве которых используют известь, золу и песок, помол вяжущего с введением при помоле указанной золы, приготовление силикатной массы из известково-кремнеземистого вяжущего и песка, прессование силикатной массы или включающий введение и смешивание компонентов, в качестве которых используют известь и песок, помол и получение известково-кремнеземистого вяжущего, приготовление силикатной массы из известково-кремнеземистого вяжущего и песка, введение в силикатную массу золы и прессование силикатной массы с золой (см. Хавкин Л. М. Технология силикатного кирпича. — М.: Стройиздат, 1982. — С. 108−114, табл. IV.3).
Общими недостатками описанных способов получения силикатного кирпича являются низкая эффективность, нестабильность характеристик прочности, морозостойкости и линейных размеров силикатного кирпича, полученного в соответствии с каждым из этих способов, что обусловлено отсутствием разделения зол по основности и содержанию в них свободной закрытой извести. Так, при введении в силикатную массу без помола высококальциевых зол с большим содержанием в них свободной закрытой извести происходит поздняя гидратация свободной извести в сформированном кирпиче с его растрескиванием, спадом прочности и морозостойкости.
Для повышение эффективности, обеспечение стабилизации характеристик прочности, морозостойкости и линейных размеров силикатного кирпича, полученного на основании заявляемого способа, было разработана методика.
Сущность изобретения заключается в том, что в способе получения силикатного кирпича с использованием высококальциевой золы тепловых электростанций, включающем введение и смешивание компонентов, помол вяжущего с введением при помоле указанной золы, приготовление и прессование силикатной массы, при помоле вводят указанную золу с коэффициентом основности более 0,7 и содержанием закрытой свободной извести более 1,4%, а указанную золу с коэффициентом менее 0,7 и содержанием закрытой свободной извести менее 1,4% вводят в силикатную массу перед прессованием.
Предлагаемое разделение высококальциевых зол по основности и содержанию в них свободной закрытой извести позволяет для зол с основностью по коэффициенту основности более 0,7 и содержанием свободной закрытой извести более 1,4% осуществить глубокую переработку, включающую помол и силосование, что обеспечивает последующее бездефектное твердение силикатного кирпича, стабилизацию характеристик прочности, морозостойкости и линейных размеров кирпича, а также — повышение эффективности способа путем снижения расхода исходного сырья: извести и песка на 30−40%. В то же время разделение высококальциевых зол по основности и содержанию в них свободной закрытой извести для зол с основностью по коэффициенту основности менее 0,7 и содержанием свободной закрытой извести менее 1,4% позволяет исключить операции помола и силосования зольной составляющей силикатной массы и вводить такую золу в силикатную массу непосредственно перед прессованием, получая силикатный кирпич со стабильными характеристиками прочности, морозостойкости и линейными размерами (см. таблицу), а также позволяет повысить эффективность способа вследствие помола только части исходного сырья — извести и песка (60−70%) или использования части готового вяжущего и соответствующего снижения затрат электроэнергии.
Способ получения силикатного кирпича с использованием высококальциевой золы осуществляется следующим образом.
Предварительно на тепловой электростанции отбирают 9 проб высококальциевых зол разной основности и с разным содержанием свободной закрытой извести.
После проведения химического анализа проб по ГОСТ 5382–73 определяют коэффициент основности зол по следующей известной формуле:
Определяют количество свободной открытой извести спиртово-сахаратным методом без помола золы и количество суммарной свободной извести золы после помола золы до полного прохождения через сито N 006. Количество свободной закрытой извести золы определяют по разности между количеством суммарной свободной извести и открытой свободной извести.
Исходное сырье — известь и песок в соотношении 1:1 по массе смешивают и размалывают в шаровой мельнице до остатка на сите N 008 с диаметром отверстий 80 мкм 16% При помоле известково-кремнеземистого вяжущего вводят золу с основностью по коэффициенту основности более 0,7 и содержанием свободной закрытой извести более 1,4%. Если золу вводят в вяжущее, то убирают 30−40% извести и песка, а вместо них добавляют золу или используют меньше на 40% количество исходного сырья. К полученному вяжущему добавляют песок-заполнитель до получения активности (содержание активных СаО и MgO) силикатной массы 8%. В эту массу добавляют воду в количестве, необходимом для полной гидратации извести и формовочной влажности 8%. Силикатную массу силосуют при температуре 60oС в течение 4 ч и прессуют из нее образцы.
Золу с активностью по коэффициенту основности менее 0,7 и содержанием свободной закрытой извести менее 1,4% вводят перед прессованием образцов в силикатную массу. При этом получение и силосование силикатной массы осуществляют без ее зольной составляющей. Если золу вводят в силикатную массу без помола непосредственно перед прессованием образцов, то убирают 30−40% готового известково-кремнеземистого вяжущего или подвергают помолу 60−70% исходного сырья. Затем силикатную массу подвергают прессованию для получения образцов.
Силикатные образцы изготавливают с диаметром и высотой 50 мм при удельном давлении 15 МПа. Замеряют диаметры образцов. Сформованные образцы автоклавируют при удельном давлении 0,8 МПа по режиму 2+6+2 ч. После автоклава образцы высушивают при 100oС до постоянной массы, снова замеряют диаметр образцов и испытывают на прессе на прочность при сжатии.
Определяют увеличение диаметра запаренных образцов. Коэффициент морозостойкости определяют как частное от деления предела прочности образцов с золой к пределу прочности беззольных контрольных образцов после 15 циклов замораживания и оттаивания.
Вывод по главе В результате исследования влияния золы-уноса на конструкционные бетоны выявлено, что она может заменить до 40−50% цемента. Если прочность бетона в раннем возрасте не является определяющим фактором, можно заменить 60% цемента.
Замещение части цемента золой-уноса приводит к уменьшению усадочных деформаций бетона, увеличению длительности прочности бетона, также такие бетоны отличаются высокой трещиностойкостью, что особенно ценно для массивных бетонных и гидротехнических сооружений. Испытания бетонов длительными нагрузками показали, что введение золы-уноса также снижает ползучесть бетона. Зола-уноса, как и другие активные минеральные добавки, способствует повышению коррозионной стойкости, в т. ч. сульфатостойкости цементных бетонов, повышает их водонепроницаемость и удобоукладываемость.
Зола-уноса в сочетании с быстротвердеющим портландцементом может применяться для изготовления конструкционных элементов из сборного предварительно напряженного железобетона, подвергающихся тепловой обработке. Потенциальные возможности использования этого бетона разнообразны, включая массивные конструкционные элементы, устройство фундаментов, стен подземных частей зданий и т. п.
Зарубежный опыт применения золы-уноса и золошлаковых смесей демонстрирует самые разнообразные сферы эффективного применения данных материалов в промышленном, гражданском, дорожном, гидротехническом строительстве и в иных областях.
Достаточно известен и российский опыт применения золы-уноса в строительстве: добавки в бетоны при строительстве Братской и Бурейской ГЭС, производство стеновых блоков и железобетонных изделий в Ростовской, Московской, Свердловской, Иркутской, Новосибирской областях, в Краснодарском, Алтайском и Красноярском краях, в г. Москва, а также производство цемента на Воскресенском и Ангарском цементных заводах.
Список литературы
Данилович, Ирина Юрьевна. Использование топливных шлаков и зол для производства строительных материалов: Учеб. пособие для сред. ПТУ /И.Ю. Данилович, Н. А. Сканави.-М.: Высш. шк., 1988.-72 с.: ил.
Овчаренко Г. И. Золы углей КАТЭКа в строительных материалах. Изд-во Красноярского ун-та, 1991. — 180 с.
http://www.sts54.ru/new_tech/
http://www.remontnik.ru/publication2253/
Ползуновский вестник № 1 2011
Пат. 2 182 891 Российскоя Федерация, МПК C04B28/18, C04B111/20. Способ получения силикатного кирпича с использованием высококальциевой золы тепловых электростанций [текст] / Овчаренко Г. И, Францен В. Б.; заявитель и патентообладатель Алтайский государственный технический университет им. И. И. Ползунова. — заявл. 25.04.2000; опубл. 27.05.2002.
Костин В. В. Опыт использования отходов ТЭС в производстве строительных материалов. — Новосибирск, 2001.