Другие работы
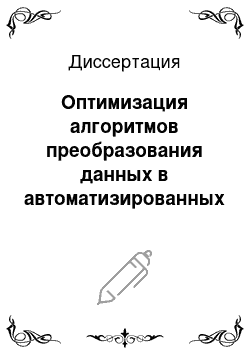
Ни одна сфера жизни современного общества не может функционировать без развитой информационной инфраструктуры. Национальный информационный ресурс является сегодня одним из главных источников экономической и военной мощи государства, основной предпосылкой его социально-экономического развития. В настоящее время информационная безопасность приобретает первостепенное значение во всех сферах…
Диссертация 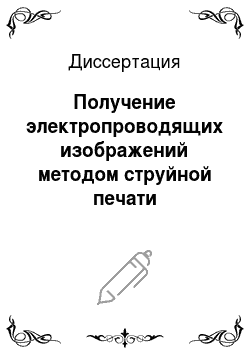
О перспективности и практической значимости таких исследований свидетельствует большое количество публикаций в этой области. Однако, накоплено еще недостаточное количество экспериментального материала для перехода исследований с этапа теоретических исследований в область реализации полноценных практических разработок. К сожалению, публикации в этой области носят, в основном, рекламный характер…
Диссертация 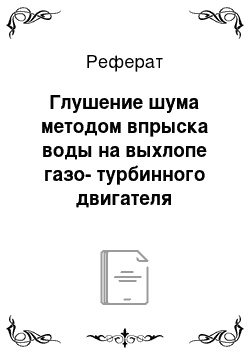
В прошлом большинство «сухих» выхлопных систем не имели водяного охлаждения выхлопных газов. Такой раскаленный газопровод был основательно изолирован, но даже в этом случае он производил достаточно шума («звучный рык», так о нем говорили!). Понижение температуры выхлопных газов до 40−50°С могло достигаться впрыском охлаждающей воды двигателя напрямую в линию газовыхлопа. Теперь появилась система…
Реферат 
Прогнозирование режимных параметров и технико-экономических показателей является одной из-важных задач, как при планировании, так и при ведении текущих режимов ЭЭС. Создание условий для свободной конкуренции на оптовом рынке электроэнергии является частью комплекса мероприятий, проводимых в рамках реформирования отрасли, и направлено на выработку нового механизма образования цен на электрическую…
Диссертация 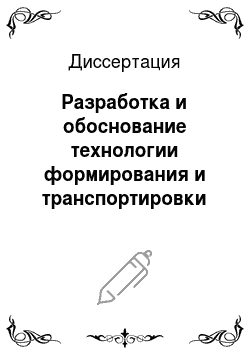
Наряду с этим современное состояние лесопромышленного комплекса характеризуется ростом дефицита сырья. В последние годы отмечается уменьшение площади лесопокрытых территорий вследствие разного рода причин (пожары, нашествия вредителей, неэффективная заготовка леса и т. д.), что приводит к уменьшению запасов лесных ресурсов Российской Федерации. В этой ситуации необходимо эффективно использовать…
Диссертация 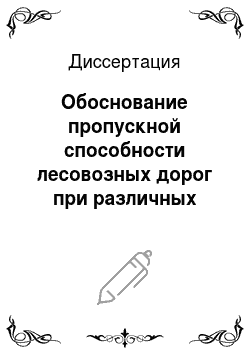
В нормативных документах категорию лесовозных дорог устанавливают по расчетному объему перевозок, обоснование которого нигде не приводится. Очевидно, эти нормы созданы на основе учета опыта эксплуатации магистральных дорог и изучения закономерностей движения потоков. В связи с этим вопросы исследования и разработки научно обоснованных технических решений по категорированию лесовозных дорог…
Диссертация 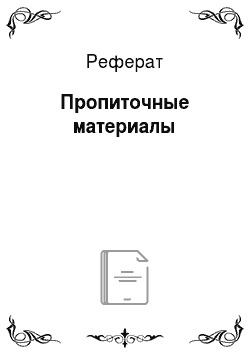
Трансформаторное масло, которым заливают силовые трансформаторы, из всех жидких электроизоляционных материалов находит наибольшее применение в электротехнике. Его назначение двояко: во-первых, масло, заполняя поры в волокнистой изоляции, а также промежутки между проводами обмоток и между обмотками и баком трансформатора, значительно повышает электрическую прочность изоляции; во-вторых, оно…
Реферат 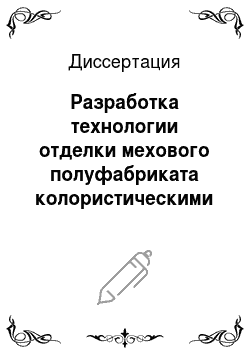
Интерес представляют белковые препараты, широко применяемые в различных отраслях науки и практики. Благодаря структуре возможно их использование в совокупности с другими активными компонентами (стабилизаторы, ПАВ, наполнители, светофильтры, лекарственные и другие вещества). Биополимерные вещества улучшают качество обрабатываемого материала, кроме того, они имеют высокое сродство к волосу и…
Диссертация 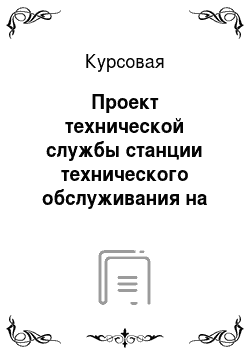
При проектировании предприятия выявим технологически необходимое (Ртi) и штатное количество (Ршi) рабочих. Технологически необходимое количество рабочих имеет решающее значение при проектировании, так как оно позволяет установить количество рабочих мест, которое необходимо организовать в АТО. Технологически необходимое количество рабочих определяется годовыми трудовыми затратами (Тi…
Курсовая 
На основе анализа влияния химической природы поверхности натуральных жиров на процессы адсорбции и смачивания НПАВ, в зависимости от гидрофобной цепи и числа оксиэтильных звеньев, установлена зависимость между химическим составом триглицеридов и способностью НПАВ к адсорбции и смачиванию. Исходя из результатов исследования процессов, происходящих на межфазных границах жирНПАВ, дано обоснование…
Диссертация 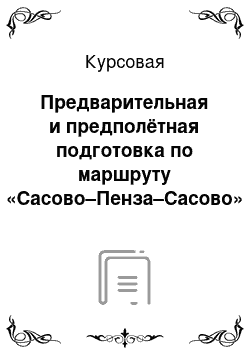
Особенности годового хода облачности ниже 200 м такие: наибольшая повторяемость приходится на холодную половину года и составляет в ноябре — декабре 20 — 25%. Перед заходом и сразу после захода Солнца повторяемость низкой облачности увеличивается по сравнению с дневной повторяемостью на 2 -3%. Максимум повторяемости приходится на период восхода Солнца и составляет 8 — 12%. В летний период…
Курсовая 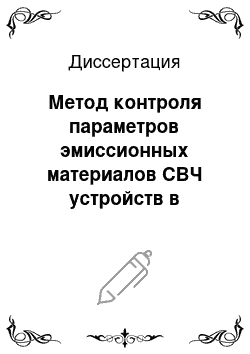
Предложены два метода определения статистической функции распределения работы выхода (ФРРВ) эмиттера из результатов эмиссионных испытаний с учетом некорректности задачи. Первый метод связан с регуляризацией и минимизацией функционала Тихонова. Второй метод основывается на применении быстрого преобразования Фурье для минимизации функционала Тихонова. Методом Монте-Карло доказана сходимость решения…
Диссертация 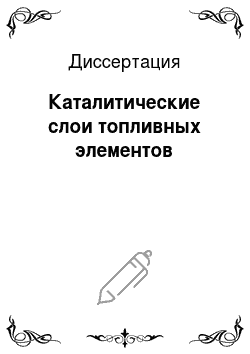
Одни из важных критериев высокой эффективности устройства — его слаженная работа. Исходя из этого, было необходимо не только усовершенствовать микрогенератор водорода, батарею топливных элементов и интерметаллидный накопитель в отдельности, но и подобрать оптимальные режимы работы для всей системы целиком. В ходе проведенных экспериментов по совмещенной системе компактного источника питания…
Диссертация 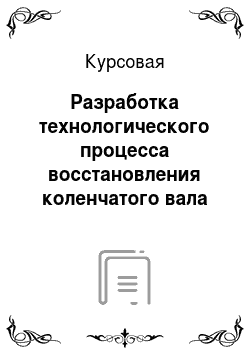
ГОСТ 16 429−70 установлены три группы изнашивания в машинах: механическое, малекулярно-механическое и каррзионно-механическое. Рассмотрим механическое изнашивание и его подвиды, потому, что анализируемая нами деталь больше всего подвергается факторам присущих для механического износа. Из приведенных видов изнашивания коленчатым валам характерно абразивное изнашивание схватывание…
Курсовая 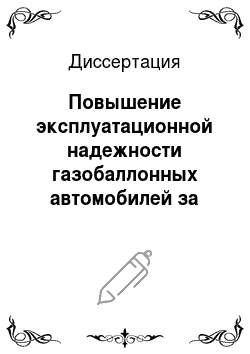
Кроме того, при работе двигателя на сжиженном нефтяном газе на режимах высоких нагрузок и больших оборотов происходит догорание топлива в начале такта выпуска. Это связано с низкой скоростью горения газовоздушной смеси по сравнению с бензовоздушной. Особенно в двигателях с устройствами для принудительного вращения выпускных клапанов происходит их ускоренный износ. Это объясняется тем, что…
Диссертация