Твердые сплавы и режущая керамика
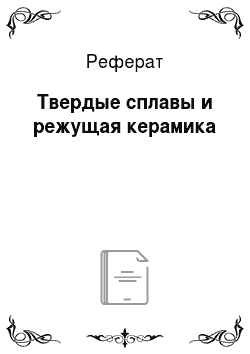
Основные технологические процессы порошковой металлургии: получение порошков, приготовление смесей, формование смесей, спекание — заключительная технологическая операция порошковой металлургии. В процессе спекания происходит превращение пористого вещества (уплотненного порошка) в компактный малопористый или (в идеале) беспористый материал; за счет снижения пористости увеличивается плотность, т… Читать ещё >
Твердые сплавы и режущая керамика (реферат, курсовая, диплом, контрольная)
Твердые сплавы — это материалы, состоящие из зерен карбидов или карбонитридов тугоплавких металлов, соединенных металлической связкой. Режущая керамика состоит только из твердых химических соединений — оксидов, карбидов, нитридов.
Карбиды и нитриды этих инструментальных материалов имеют ковалентный или ионный тип связи. Именно сильные межатомные связи обусловливают их свойства: высокие твердость, модуль упругости, теплостойкость.
Основной метод изготовления изделий из таких материалов — порошковая металлургия. Отличие этой технологии от литья в том, что по крайней мере один из компонентов в процессе спекания — окончательной операции получения материала — находится в твердом состоянии. Технология порошковой металлургии для получения некоторых материалов является единственно возможной. Это связано с высокими температурами плавления, а также с разложением при нагреве некоторых компонентов (например, карбида вольфрама) еще до их расплавления.
Основные технологические процессы порошковой металлургии: получение порошков, приготовление смесей, формование смесей, спекание — заключительная технологическая операция порошковой металлургии. В процессе спекания происходит превращение пористого вещества (уплотненного порошка) в компактный малопористый или (в идеале) беспористый материал; за счет снижения пористости увеличивается плотность, т. е. происходит уменьшение объема исходной смеси, ее усадка. Спекание может выполняться без приложения нагрузки после холодного прессования («ХП + С» — холодное прессование + спекание), при совмещении процессов прессования и спекания — горячее прессование («ГП»), а также в условиях всестороннего давления в изостатах — горячее изостатическое прессование («ГИП»), «ГИП» может быть использовано в качестве основного метода или быть дополнительной операцией после «ХП + С» или «ГП». Его осуществляют в печах высокого давления (до 300 МПа), достигаемого за счет подачи нейтрального газа.
Наиболее дешевым является метод «ХП + С». Методы «ГП» и «ГИП» более энергоемки, требуют применения дорогостоящей прессовой оснастки из высокопрочного графита, поэтому для массовой продукции основным является метод «ХП + С» .
Режущие пластины из твердого сплава изготавливают, как правило, методом «XII + С». Технология «ГП» применяется главным образом при изготовлении изделий больших габаритов — волок, размольных шаров; технология «ГИП» — для изготовления тяжелонагруженного штампового инструмента.
Твердые сплавы
Основной фазой твердых сплавов являются карбиды или карбонитриды (80% и более), связанные для получения компактного материала металлической связкой. Твердые сплавы имеют высокие твердость — 87…92 HRA (HRC = 2/7/64 — 102) и теплостойкость (800… 1100 °С), поэтому допустимые скорости резания при использовании твердосплавного инструмента также высокие — 100…300 м/мин в зависимости от типа твердой фазы (карбиды, карбонитриды) и металла-связки. Наиболее широко как металл-связку используют кобальт. Это объясняется тем, что он нейтрален по отношение к углероду (не разрушает и не образует собственные карбиды (см. 6.4.2), т. е. не вступает в химическое взаимодействие с карбидами твердых сплавов).
Твердые сплавы подразделяются на следующие группы: WC-Co — вольфрамокобальтовые типа ВК (связка — Со);
- — WC-TiC-Co — титановольфрамокобальтовые типа ТК (связка — Со);
- — WC-TiC-TaC-Co — титанотанталовольфрамокобальтовые типа ТТК (связка — Со);
- — TiC и TiCN — Ni+Mo — сплавы на основе карбида и карбонитрида титана — безвольфрамовые (БВТС) типа ТН и КНТ (связка — Ni + Мо).
Сплавы ВК
Сплавы маркируются буквами «ВК» и цифрой, указывающей на содержание кобальта (например, состав сплава ВК6 — 94% WC и 6% Со). Свойства сплавов определяются главным образом содержанием кобальта. Его увеличение приводит к повышению прочности, но твердость и износостойкость при этом снижаются (табл. 9.2).
По содержанию кобальта сплавы можно разделить на три группы: низко- (3…8% Со), средне- (10…15% Со) и высококобальтовые (20…30% Со). Для режущего инструмента используются сплавы с содержанием кобальта до 10%, т. е. в основном низкокобальтовые. Сплавы с содержанием кобальта 10…15% применяют для изготовления бурового инструмента, а высококобальтовые — для штампового инструмента (см. 9.3.2).
Теплостойкость сплавов ВК — около 900 °C. Сплавы этой группы обладают наибольшей прочностью по сравнению с прочими твердыми сплавами.
Таблица 9.2
Механические свойства сплавов ВК
Сплав. | ?изг, МПа. | Твердость, HRA |
ВКЗ. | 89,5. | |
ВК4. | 89,5. | |
ВК6. | 88,5. | |
ВК8. | 87,5. | |
ВК10. | 87,0. |
Значительное влияние на свойства твердых сплавов оказывает размер карбидных частиц. Уменьшение их размера приводит к увеличению твердости, но прочность при этом снижается (сравните свойства сплавов ВК6, ВК6-М и ВКб-ОМ, табл. 9.3). В зависимости от размера карбидов сплавы подразделяются на особо мелкозернистые (ОМ), мелкозернистые (М), среднезернистые (в обозначении нет дополнительных букв) и крупнозернистые (В).
Таблица 93
Влияние размеров карбидов на механические свойства
Сплав. | Размер карбидов, (средний), мкм. | ?изг, МПа. | Твердость, HRA | Е, ГПа. |
ВК6-ОМ. | 1,3. | 90,5. | ; | |
ВК6-М. | 1,6. | |||
В6. | 2,0. | 88,5. | ||
ВК6-в. | 3,4. | 87,5. |
Для получения особо мелкозернистой структуры в состав сплавов вводится карбид тантала (ТаС), препятствующий росту карбидов WC при спекании (сплавы ВК6-ОМ и ВК10-ОМ содержат 2% ТаС). Однако из-за дороговизны вместо карбида тантала используют карбид хрома, оказывающий аналогичное влияние. В обозначение сплава в этом случае вводится буква «X» — ВК10-ХОМ, ВК15-ХОМ.
Сплавы группы ВК применяются главным образом для обработки материалов, при резании которых образуется стружка надлома (сыпучая), — в первую очередь чугунов, а также цветных металлов, стеклопластиков и др. При обработке таких материалов возникают динамические нагрузки, что и предопределяет использование твердых сплавов с повышенной прочностью. Мелкозернистые сплавы обладают высокой термоциклической стойкостью, поэтому их используют для обработки труднообрабатываемых материалов (высокие температуры в зоне резания). Следует также отметить, что из-за малого размера карбидов инструмент из мелкозернистых сплавов при заточке приобретает более острую режущую кромку. Это позволяет получать меньшую шероховатость обработанной поверхности.
Сплавы ТК
Сплавы обозначаются комбинацией букв и цифр. Цифра после «Т» указывает на содержание в сплаве карбида титана; после «К» — кобальта (например, состав сплава Т15К6 — 15% TiC; 6% Со; остальное 79% - WC).
Структура этих сплавов состоит из карбида титана, в котором растворяется некоторое количество вольфрама, — (Ti, W) C, карбида WC и кобальтовой связки.
Твердость сплавов ТК выше, чем у ВК (твердость карбидов TiC сплавов ТК — 3220 HV выше, чем твердость WС сплавов ВК — 2080 HV), они также имеют преимущество по теплостойкости (1000 °С), однако их прочность ниже (при равном содержании кобальта). Увеличение содержания кобальта приводит к повышению прочности с одновременным снижением твердости и теплостойкости. При увеличении количества TiC твердость сплава возрастает, а прочность уменьшается (табл. 9.4).
Таблица 9.4
Свойства сплавов группы ТК
Сплав. | ?изг, МПа. | Твердость,. HRA | Е, ГПа. |
Т30К4. | 92,0. | ||
Т15К6. | 90,0. | ||
Т14К8. | 89,5. | ||
Т5К10. | 88,5. | ||
Т5К12. | 87,0. |
Сплавы группы ТК используются для обработки материалов со сливной стружкой, т. е. сталей. При обработке стали (в отличие от чугуна со стружкой надлома) инструмент находится в постоянном контакте с обрабатываемым материалом. Это определяет его больший нагрев, поэтому от инструментального материала требуется повышенная теплостойкость.
В условиях непрерывного контакта инструментального и обрабатываемого материала возникают адгезионные связи («схватывание») между инструментальным и обрабатываемым материалом. (Адгезия — образование межатомных связей между разнородными материалами; когезия — между материалами одинаковыми по составу.) На поверхности инструмента образуется нарост, что ухудшает качество обработанной поверхности. «Схватывание» стали со сплавами ТК происходит при более высоких температурах (появление нароста в паре со сталью на сплавах ВК отмечено при 625 °C, а на сплавах ТК — при 770 °С). Это позволяет выполнять обработку с более высокими скоростями. Кроме того, сила адгезии в паре «сталь — ТК» значительно (примерно в 10 раз) ниже, чем в паре «сталь — ВК». Поэтому под воздействием сил резания для сплава ТК наиболее вероятно удаление только нароста, слабо связанного с материалом инструмента, тогда как у инструмента из сплава В К может происходить скалывание режущей кромки.
Сплавы ТТК
Обозначение сплавов ТТК и ТК аналогично. Цифра после второй буквы «Т» указывает на суммарное содержание карбидов TiC и ТаС. Структура промышленных четырехкомпонентных сплавов ТТК состоит из трех фаз. Это сложный карбид на основе TiC, в котором часть атомов титана замещена атомами вольфрама и тантала, — (Ti, Ta, W) C, WC и связка.
При равной теплостойкости (1000 °С) сплавы ТТК превосходят сплавы ТК по сочетанию свойств «твердость — прочность» (табл. 9.5). Так, при одинаковом содержании кобальта сплав ТТ8К6 превосходит сплав Т15К6 и, но твердости, и по прочности. Значительное преимущество сплавов ТТК проявляется при циклических нагрузках — ударная усталостная долговечность повышается в 6…25 раз по сравнению со сплавами ТК. Поэтому танталсодержащие сплавы используются в основном для тяжелых условий резания с большими силовыми и температурными нагрузками — при больших сечениях среза, при прерывистом резании, при обработке труднообрабатываемых (жаропрочных) материалов.
Таблица 9.5
Состав и свойства сплавов ТТК
Сплав. | Химический состав, % масс. | Свойства. | |||||
WC. | TiC. | ТаС. | Со. | ?изг, МПа. | Твердость,. HRA | Е, ГПа. | |
ТТ7К12. | 87,0. | ; | |||||
ТТ8К6. | 90,5. | -. | |||||
ТТ10К8. | 89,0. | ||||||
ТТ20К9. | 9,4. | 14,1. | 9,5. | 91,0. |
Безвольфрамовые твердые сплавы (БВТС)
Принципиальные отличия БВТС от вольфрамсодержащих твердых сплавов: отсутствие в их составе карбида вольфрама; металлическая связка никель-молибденовая, а не кобальтовая (табл. 9.6). Высокая твердость обеспечивается карбидами или карбонитридами титана.
Таблица 9.6
Состав и свойства БВТС
Сплав. | Химический состав, % масс. | Свойства. | |||||
TiC. | TiCN. | Ni. | Mo. | Твердость,. HRA | ?изг, МПа. | E, ГПа. | |
КНТ16. | ; | 19,5. | 6,5. | ||||
ТН20. | ; | e. | |||||
ТН50. | ; | 86,5. | ; |
По теплостойкости БВТС уступают вольфрамсодержащим сплавам — 800 °C. Их прочность и модуль упругости также ниже.
Теплоемкость и теплопроводность БВТС ниже, чем у традиционных сплавов. Это означает, что при одинаковом количестве теплоты, выделяемой при резании, режущая кромка инструмента из БВТС нагревается сильнее. Наряду с меньшей теплостойкостью это определяет более низкую стойкость такого инструмента при высоких скоростях резания. Вследствие более низкой прочности и трещиностойкости (значения Ки. вольфрамсодержащих сплавов составляет 10…17, а БВТС — 7…11 МПа•м½) БВТС заметно уступают традиционным сплавам при силовом резании с большими подачами и глубинами резания. Сплавы рекомендуется использовать при чистовой или в крайнем случае получистовой обработке сталей. Наиболее целесообразно применение этих сплавов для изготовления измерительного (калибры) и волочильного инструмента.
Более высокими механическими свойствами обладают БВТС следующего поколения. Прочность сплавов повышена (~ 1300 МПа — уровень сплавов ВК и ТК) за счет усовершенствования состава. Так, сплав ЛЦК20 легирован карбидом циркония; сплавы ТВ4, ЦТУ, НТНЗО — соответственно карбидами вольфрама, титана и ниобия в небольших количествах. В состав связки сплава ЦТУ введен вольфрам. Такие БВТС могут быть использованы для черновой обработки при точении и фрезеровании.