Каталитическая очистка газов от оксида углерода
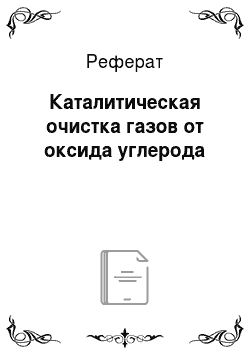
Рис. 1−55. Схемы установок каталитического обезвреживания отходящих газов: а — производства нитрила акриловой кислоты: 1 — воздуходувка, 2 — топка-подогреватель, 3 — реактор, 4 — котел-утилизатор, 5 — дымосос, 6 — дымовая труба; б — линий лакирования: 1 — вентилятор, 2 — теплообменник, 3 — реактор, 4 — калорифер, 5 — емкость, 6 — насос; в — агломерационных агрегатов: 1 — агломерационная машина… Читать ещё >
Каталитическая очистка газов от оксида углерода (реферат, курсовая, диплом, контрольная)
Каталитическое окисление является наиболее рациональным методом обезвреживания отходящих газов промышленности от оксида углерода. Однако наряду с оксидом углерода в зависимости от условий конкретного производства в газах могут содержаться и другие токсичные компоненты: диоксид серы, оксиды азота, пары различных углеводородов. Кроме того, в них обычно присутствуют диоксид углерода, кислород, азот, пары воды и часто механические примеси в виде различных пылей. Некоторые из этих примесей могут быть ядами для катализаторов.
Для окисления оксида углерода используют марганцевые, медно-хромовые и содержащие металлы платиновой группы катализаторы. В зависимости от состава отходящих газов в промышленности применяют различные технологические схемы очистки.
На рис. 1−55,а представлена схема установки каталитического обезвреживания отходящих газов в производстве нитрила акриловой кислоты. При синтезе этого продукта на основе аммиака и пропилена технологические газы отмывают от нитрила акриловой кислоты водой. Поступающие со стадии абсорбции отходящие газы содержат, в % (об): оксида углерода — 2,3, пропилена — 0,5, пропана — 0,04, кислорода — до 3,0, инертные газы — остальное.
Для очистки их подают в топку-подогреватель, где нагревают до 220- 250 °C (в зависимости от типа используемого катализатора) путем сжигания вводимого в топку топливного газа в воздухе, нагнетаемом воздуходувкой. Расход воздуха рассчитан не только на сжигание топливного газа, но и на последующее каталитическое окисление находящихся в газах оксида углерода и углеводородов. Смесь топочных и отходящих газов с воздухом направляют в работающий в адиабатических условиях реактор. Используется шариковый катализатор ШПК-2, содержащий 0,2% платины, нанесенной на оксид алюминия. Степень очистки достигает 98−99%. Происходящие на катализаторе окислительные реакции экзотермичны, что приводит к сильному разогреву продуктов катализа. Конвертированные газы при температуре до 700 °C передают в котел-утилизатор, обеспечивающий производство перегретого до 380 °C водяного пара под давлением 4 МПа. Выходящие из котла-утилизатора обезвреженные газы при температуре около 200 °C дымососом через дымовую трубу эвакуируют в атмосферу.
При обработке 60 тыс м3/ч отходящих газов расход электроэнергии составляет 500 кВт, производится пара 26,5 т/ч.
Для санитарной очистки промышленных выбросов от оксида углерода и паров органических загрязнений разработана другая установка, схематично представленная на рис. 1−55 Д.
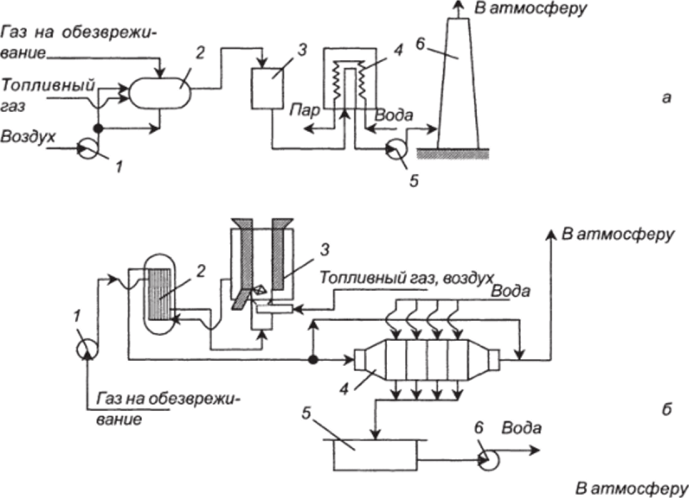
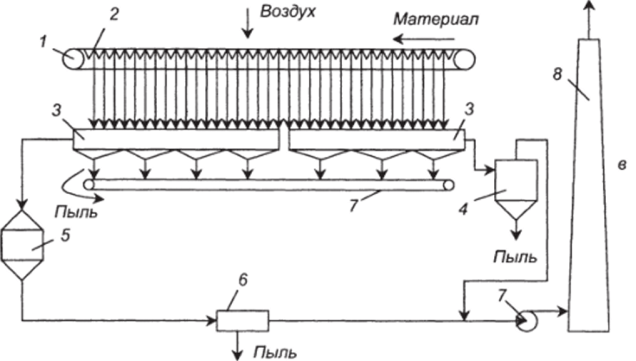
Рис. 1−55. Схемы установок каталитического обезвреживания отходящих газов: а — производства нитрила акриловой кислоты: 1 — воздуходувка, 2 — топка-подогреватель, 3 — реактор, 4 — котел-утилизатор, 5 — дымосос, 6 — дымовая труба; б — линий лакирования: 1 — вентилятор, 2 — теплообменник, 3 — реактор, 4 — калорифер, 5 — емкость, 6 — насос; в — агломерационных агрегатов: 1 — агломерационная машина, 2 — вакуумная камера, 3 — коллекторы, 4, 6 — пылеочистные аппараты, 5 — реактор, 7 — вентилятор, 8 — дымовая труба Отходящие газы сушильных печей линий лакирования кроме СО содержат этилцеллозольв, этанол, ксилол и другие компоненты. Центробежным вентилятором их направляют в теплообменник, где подогревают теплом конвертированных газов, а затем в реактор, в котором происходит дополнительный нагрев газов при помощи горелки. Процесс конверсии проводят в реакторе на катализаторе НТК-4 при температуре 320−450°С и объемной скорости газа 16 700 «Г1. Конвертированные газы из реактора через теплообменник выводят в калорифер, где их избыточное тепло утилизируют для подогрева воды на бытовые нужды предприятия, после чего обезвреженный воздух через 20-метровую трубу выбрасывают в атмосферу.
Степень очистки газов равна 98%, а ее себестоимость в ценах 1980 г. составляла 0,28 руб. на 1000 м3 отходящих газов.
Монооксид углерода является основным токсичным компонентом отходящих газов агломерационных фабрик на предприятиях черной металлургии. Одна аглофабрика выбрасывает в атмосферу в среднем примерно 1 млн. м3/ч газов из вакуум-камер агломерационных машин.
Используемые для обезвреживания таких газов катализаторы должны обеспечивать при 220−240°С степень конверсии оксида углерода не менее 70% в условиях больших объемных скоростей запыленных потоков и обладать устойчивостью к присутствующим в составе газов каталитическим ядам.
Проведенные на реальных агломерационных газах испытания показали, что из-за присутствия в их составе диоксида серы марганцевый катализатор теряет свою активность в течение 3−4 ч. Предварительное удаление диоксида серы из газов обеспечивает стабильную работу этого катализатора уже при 150−180°С, а при 220−240°С достигается степень обезвреживания оксида углерода 90−96% при объемных скоростях газа 2000 ч'1. Медно-хромовый катализатор (50% оксида меди и 10% оксида хрома) позволяет достичь при 240 °C необходимых степеней конверсии оксида углерода при более высоких объемных скоростях газа (до 20 тыс. ч_|) и большей длительности работы (до 120 ч). Однако при использовании катализаторов этих двух типов степень обезвреживания оксида углерода падает с увеличением объемной скорости обрабатываемых газов, уменьшением температуры процесса и возрастанием содержания оксида углерода в конвертируемых газах, что ограничивает целесообразность применения этих катализаторов.
Повышенной устойчивостью к катализаторным ядам характеризуются катализаторы, содержащие палладий и платину. Их применение позволяет осуществлять процессы эффективного обезвреживания аглогазов при значительно более высоких объемных скоростях обрабатываемых газовых потоков без изменения активности катализаторов в течение длительного времени (6−12 мес.). Более высокую степень конверсии содержащегося в аглогазах оксида углерода обеспечивает катализатор, содержащий 0,3% платины, нанесенной на гранулированный оксид алюминия. Такой катализатор сохраняет первоначальную активность в течение 8000 ч при степени конверсии оксида углерода выше 70% в условиях обезвреживания аглогазов при температуре 225 °C и объемной скорости потока 100 тыс. ч-1.
Принципиальная схема установки каталитической очистки агломерационных газов от оксида углерода представлена на рис. I- 55, в. Аглогазы, образующиеся при работе агломерационной машины, через вакуум-камеры попадают в коллектор, где их разделяют на два потока. Первый из них, отводимый с головных вакуум-камер агломашины, является менее нагретым (минимальная температура 80°С) и характеризуется большим содержанием пыли. Этот поток передают на очистку от пыли. Второй поток, отбираемый с последующих вакуум-камер, характеризуется более высокой температурой (максимально 300°С) и меньшим содержанием пыли. Его направляют в каталитический реактор для обезвреживания оксида углерода. Конвертированный газовый поток освобождают затем от пыли. Оба обеспыленных потока объединяют в борове и эксгаустером выводят в атмосферу через трубу.
При использовании контактного аппарата с вращающимся плотно упакованным слоем катализатора, содержащего 0,3% платины, приведенная схема обеспечивает возможность каталитического обезвреживания оксида углерода запыленных аглогазов при затратах на очистку 1000 м' около 0,03 руб. в ценах 1980 г., что в 5−7 раз меньше затрат на очистку этих же газов от пыли.