Технологии бурения сверхглубоких скважин
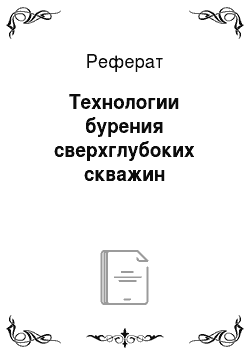
При бурении глубоких скважин нередко возникают аварии, вызванные мертвым прихватом бурового снаряда и другими причинами. На устранение аварий требуется много времени, зачастую их вообще невозможно устранить, приходится начинать бурение нового ствола. Поэтому многокилометровый столбик керна диаметром от 5 до 20 см, который является одним из основных, но не единственным результатом научного… Читать ещё >
Технологии бурения сверхглубоких скважин (реферат, курсовая, диплом, контрольная)
Существуют разные способы бурения. Если глубина скважин невелика (сотни метров), то двигатель, находящийся на поверхности, вращает колонну стальных бурильных труб; на нижнем конце трубы крепится буровая коронка, армированная твердыми сплавами или алмазами. Вращаясь коронка вырезает цилиндрический столбик породы, который постепенно заполняет специальную внутреннюю (колонковую) трубу. При бурении без отбора керна часто используют буровые головки, которые представляют собой систему нескольких вращающихся конусов, армированных твердыми сплавами. Если стенки скважины неустойчивы, в нее опускают стальную обсадную трубу. В процессе бурения насос постоянно закачивает в скважину специальный глинистый раствор, необходимый для придания устойчивости стенкам, охлаждения инструмента, выноса мелких частиц породы (шлама) и для других целей. Время от времени колонну буровых труб поднимают на поверхность с помощью лебедки, установленной на буровой вышке, выгружают керн, если необходимо, заменяют изношенную коронку на новую и опять опускают буровой снаряд на забой.
Бурение сопровождается измерениями физических свойств пород вдоль ствола скважины. Для этого на специальном кабеле в скважину опускают приборы, которые фиксируют температуру, электропроводность, магнитную восприимчивость, радиоактивность и другие свойства пород. Этот процесс называют каротажем скважин.
Как показывает опыт бурения в США и других странах, увеличивая мощность двигателей и давление насосов, нагнетающих буровой раствор, повышая грузоподъемность лебедок и прочность стальных буровых труб, таким способом можно бурить скважины глубиной до 9−10 км. Для более глубоких скважин нужны нетрадиционные инженерные решения. Многие из них были предложены и реализованы в ходе выполнения программ сверхглубокого научного бурения.
Так, если забой скважины находится на многокилометровой глубине, целесообразно использовать забойные двигатели, установленные не на поверхности, а в нижней части буровой колонны, которая при этом сама не вращается. Забойные двигатели представляют собой миниатюрные турбины или винтовые механизмы, которые приводятся во вращение буровым раствором, нагнетаемым под давлением в скважину.
Для того чтобы уменьшить вес колонны буровых труб длиной в несколько километров, их изготавливают из специальных легких, но достаточно прочных и термостойких сплавов. Например, при бурении Кольской скважины использовали алюминиевые сплавы, которые в 2,4 раза легче стали. Для этих же целей предлагается применять трубы из титановых сплавов.
Когда скважина достигает большой глубины, возникает значительная разница между гидростатическим давлением столба бурового раствора и литостатическим (горным) давлением, обусловленным весом горных пород. В результате стенки скважины могут быть разрушены, что приводит к серьезным осложнениям при бурении. Для того чтобы уравновесить горное давление, увеличивают плотность бурового раствора примерно до, добавляя в него специальные наполнители.
Одна из наиболее сложных технических задач заключается в том, чтобы обеспечить надежную работу бурового оборудования при высоких температурах, существующих в сверхглубоких скважинах. Это касается металлических деталей, их соединений, смазок, бурового раствора и измерительной аппаратуры. Хотя на забое, то есть в самой нижней точке скважины Солтон-Си в США на глубине 3220 м. была зафиксирована температура 355 °C, а в другой скважине, пробуренной до 1440 м. в одной из молодых вулканических структур на западе США, измеренная температура достигала 465 °C, современные технические средства не позволяют бурить сверхглубокие скважины при столь высоких температурах в течение длительного времени, поскольку термостойкость существующего бурового оборудования не превышает 200−300°С. Самые большие проблемы возникают с измерительной аппаратурой, особенно с электроникой, которая отказывает уже при 150 °C. Водные буровые растворы сохраняют технологические свойства до 230−250°С. При более высокой температуре приходится переходить на нефтяную основу растворов и применять более сложные смеси. Высокая температура земных недр остается одним из главных факторов, ограничивающих глубину научного бурения.
Серьезные технические трудности связаны с самопроизвольным искривлением глубоких скважин в процессе бурения из-за неравномерного разрушения пород на забое, геологических неоднородностей разреза и других причин. Например, забой Кольской скважины на глубине около 12 км отклонился от вертикали на 840 м. Существуют технические приемы удержания скважины в вертикальном положении. Так, благодаря удачной конструкции специального приспособления скважина КТБ-Оберпфальц в Германии оставалась до глубины 7500 м. самой вертикальной скважиной в мире. Однако глубже это приспособление вышло из строя из-за высокой температуры и давления, и скважина пошла своим путем; в результате на глубине 9101 м. она отклонилась от вертикали на 300 м.
Сверхглубокое бурение требует создания специальной измерительной аппаратуры, контролирующей условия вдоль ствола и на забое. Обычная технология каротажа с датчиками, которые опускают в скважину на термостойком кабеле, мало пригодна для этих целей. Разработана телеметрическая и другая электронная аппаратура, которая крепится на буровом снаряде, а также автономные измерительные приборы, которые опускаются вниз и выносятся наверх потоком бурового раствора. Сигналы датчиков могут передаваться не по проводам, а гидравлическим способом путем создания импульсов давления в буровом растворе.
Глубокие и сверхглубокие скважины имеют телескопическую конструкцию. Бурение начинают с самого большого диаметра (92 см в Кольской скважине, 71 см в скважине КТБ-Оберпфальц), а затем переходят на меньшие. Нижняя часть Кольской скважины пробурена диаметром 21,5 см, а диаметр скважины КТБ-Оберпфальц на забое был 16,5 см.
Механическая скорость бурения (углубления) сверхглубоких научных скважин составляет 1−3 м/ч. За один рейс между спуско-подъемными операциями углубляются на 6−10 м. Средняя скорость подъема колонны буровых труб равна 0,3−0,5 м/с. Не менее 10% времени тратится на измерения в скважине. В целом бурение одной сверхглубокой скважины занимает годы (см. табл. 1) и стоит очень дорого. Например, бурение сверхглубокой скважины в Германии обошлось в 583 млн. немецких марок. Затраты на сверхглубокое бурение в нашей стране были не меньше.
При бурении глубоких скважин нередко возникают аварии, вызванные мертвым прихватом бурового снаряда и другими причинами. На устранение аварий требуется много времени, зачастую их вообще невозможно устранить, приходится начинать бурение нового ствола. Поэтому многокилометровый столбик керна диаметром от 5 до 20 см, который является одним из основных, но не единственным результатом научного бурения, становится поистине драгоценным. Керн тщательно документируют и хранят в специальных помещениях. Его изучением занимаются большие коллективы специалистов, которые проводят разнообразные исследования. Например, материал, полученный при бурении немецкой сверхглубокой скважины, изучали около 400 ученых, результаты этих исследований изложены в 2000 научных публикаций!
После того как бурение сверхглубокой скважины закончено, она превращается в постоянно действующую лабораторию. Специалисты следят за изменением режима земных недр вдоль ствола скважины и в околоскважинном пространстве, проводят различные эксперименты. Такие лаборатории созданы на базе Кольской и Воротиловской скважин в России и скважины КТБ-Оберпфальц в Германии [5].
Бурение сверхглубоких скважин (более 7000 м.) имеет ряд особенностей по сравнению с бурением скважин на освоенные глубины. В частности, исходные геологические данные для проектирования сверхглубоких скважин, как правило, прогнозные и не имеют достаточной степени достоверности; проектные решения по способам бурения, конструкции скважины, выбору технических средств бурения (бурильных труб, долот), а также материалов для буровых и тампонажных растворов содержат несколько возможных вариантов, которые корректируются или даже меняются по мере углубления скважин; большой объем научно-исследовательских и опытно-конструкторских работ — необходимое условие обеспечения оптимальных технико-технологических решений в условиях многовариантности геологического строения и др.
В настоящее время требованиям сверхглубокого бурения удовлетворяют только два основных способа — турбинный и роторный.
Конструкция скважины, включая число обсадных колонн, их диаметр и глубину спуска, определяется с учетом многих факторов. Решающее значение в кристаллических породах играют их физико-химические свойства. Для осадочных пород важно избегать несовместимости условий бурения в разных интервалах разреза, а также обеспечивать герметичность затрубного пространства и возможность установки соответствующего по давлению противовыбросового оборудования. При выборе конструкции оцениваются стойкость труб от механического износа и их прочностные свойства, а также допустимая масса секций труб. Во многом сочетание диаметров обсадных колонн в скважине зависит от диаметра конечной колонны, которая должна соответствовать условиям проводимых в ней исследований.
Был разработан и внедрен принципиально новый метод бурения открытым стволом оптимального диаметра, позволивший в 5−6 раз сократить металлоемкость конструкции скважины (по сравнению со скважинами на нефть и газ), исключить износ зацементированных обсадных колонн, предотвратить непреодолимые осложнения и тем самым обеспечить возможность бурения на большие глубины.
Для бурения Кольской сверхглубокой скважины была создана отечественная буровая установка БУ-15 000 грузоподъемностью 400 т. при давлении нагнетания 400 кг/ с максимальной автоматизацией процессов бурения (спуск и подъем бурового инструмента, подача долота) и бесступенчатым регулированием основных технических процессов за счет применения привода на постоянном токе. Установка рассчитана для проходки скважин до глубины 15 км. Автоматизация позволила в несколько раз увеличить скорость бурения.
Сверхглубокое бурение обусловило совершенствование конструкции и повышение термостойкости объемных двигателей и маслонаполненных редукторов, которые могли работать при температурах до 160−180°С. Они стали основными низкооборотными машинами для работы с шарошечными долотами с герметизированными опорами, алмазными долотами и долотами типа «Стратопакс» .
Специально для бурения сверхглубоких скважин были сконструированы породоразрушающие инструменты и забойные двигатели с соответствующей глубинным условиям характеристикой, в том числе с маслонаполненной герметизированной опорой, обеспечившие показатели отработки, на 15−20% превышающие средние проектные параметры, а на больших глубинах — на 70−100%. Были созданы термостойкие редукторные турбобуры, устойчиво работающие со скоростью вращения 80−200 об/мин (забойный двигатель работает от энергии потока жидкости без вращения колонны или с ее вращением на минимальной — 2−4 об/мин — скорости). Сконструированы и внедрены в практику эффективные средства контроля работы турбобура на забое, без которых невозможно бурение забойным двигателем на глубинах более 8−9 км с контролем процесса по наземным датчикам. Внедрены в производство новые типы керноотборных снарядов с гидротранспортом керна в камеру складирования, которые обеспечили приемлемые показатели отбора пород практически по всей глубине скважины. Новый колонковый снаряд позволяет сохранять от истирания значительную часть выбуренного керна и поднимать его на поверхность: процент выноса керна с больших глубин повышается в 2−3 раза против обычного. Разработана принципиально новая технология ликвидации тяжелых призабойных осложнений методом безориентированного забуривания нового ствола без установки цементного моста, которая была трижды успешно применена при бурении Кольской сверхглубокой скважины на глубинах более 7 км.
Учеными и конструкторами был создан ряд уникальных приборов и аппаратуры, что обеспечило проведение наиболее полного в мировой практике комплекса исследований. Среди них аппаратура акустического каротажа, позволившая изучать закономерности акустических полей и определять интервальные и пластовые скорости распространения упругих колебаний поперечных и продольных волн, и семейство аппаратуры спектрометрического гамма-каротажа, которая обеспечила точные спектрометрические исследования при температуре до 250 °C и давлении до 210 МПа.
На Кольской сверхглубокой скважине была внедрена информационно-измерительная система, включавшая три основные программно-аппаратные подсистемы для подготовки к рейсу, контроля бурения, определения итогов рейса.
На Тюменской сверхглубокой скважине использовалась станция автоматической оптимизации бурения, разработанная ВПО «Союзгеотехника». Система обеспечивала оптимизацию по рейсовой скорости или проходки на долото, корректировку выбранного режима бурения при изменении условий бурения в процессе рейса, распознавание на ранней стадии возникновения предаварийных и аварийных ситуаций и их вероятную оценку [3].