Проект привода одноступенчатого червячного редуктора
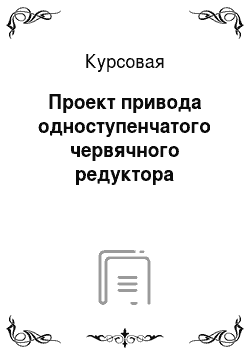
Для изучения курса «Детали машин» требуется знание следующих дисциплин: начертательной геометрии и машиностроительного черчения, на базе которых выполняются все машиностроительные чертежи; теоретической механики и теории машин и механизмов, дающих возможность определять законы движения деталей машин и силы, действующие на эти детали; сопротивления материалов — дисциплины, на основе которой… Читать ещё >
Проект привода одноступенчатого червячного редуктора (реферат, курсовая, диплом, контрольная)
Забайкальский государственный гуманитарно-педагогический университет им. Н. Г. Чернышевского КУРСОВОЙ ПРОЕКТ по дисциплине Детали машин Тема: Проект привода одноступенчатого червячного редуктора ЧИТА 2011 г.
Содержание Введение
1. Выбор мощности и кинематический расчет
2. Расчет редуктора
3. Предварительный расчет валов редуктора и конструирование червяка и червячного колеса
4. Конструктивные размеры корпуса редуктора
5. Первый этап компоновки редуктора
6. Проверка долговечности подшипников
7. Второй этап компоновки редуктора
8. Тепловой расчет редуктора
9. Проверка прочности шпоночных соединений
10. Уточненный расчет валов
11. Посадки деталей редуктора и оформление чертежа
12. Выбор сорта масла
13. Сборка редуктора Заключение Список литературы Приложения Введение Целевая установка курса «Детали машин» заключается в том, чтобы, исходя из заданных условий работы деталей машины рекомендовать методы, правила и нормы их проектирования, обеспечивающие выбор наиболее рациональных материалов, форм, размеров, степени точности и шероховатости поверхности, а также технических условий изготовления.
Для изучения курса «Детали машин» требуется знание следующих дисциплин: начертательной геометрии и машиностроительного черчения, на базе которых выполняются все машиностроительные чертежи; теоретической механики и теории машин и механизмов, дающих возможность определять законы движения деталей машин и силы, действующие на эти детали; сопротивления материалов — дисциплины, на основе которой производятся расчеты деталей машин на прочность, жесткость и устойчивость; технологии металлов и технологии машиностроения, позволяющих производить для деталей машин выбор наивыгоднейших материалов, форм, степени точности и шероховатости поверхностей, а также технических условий изготовления.
Для проектирования деталей машин требуется знание основ проектирования деталей машин, к которым относятся: основные критерии работоспособности, надежности и расчета деталей машин; выбор допускаемых напряжений и запасов прочности в машиностроении: стандартизация деталей машин; машиностроительные материалы; шероховатость поверхности деталей машин; допуски и посадки; технологичность деталей машин.
В выполняемом курсовом проекте рассматривается червячный редуктор. Наиболее распространены одноступенчатые червячные редукторы. На основе последнего рассматривается методика расчета.
1. Определение мощности и кинематический расчет привода Двигатель является одним из основных элементов машинного агрегата. От типа двигателя, его мощности, частоты вращения и прочего зависят конструктивные и эксплуатационные характеристики рабочей машины и ее привода.
1.Определим общий коэффициент полезного действия (КПД) привода:
з = ззп зоп зм зпх зпс где ззп, зоп, зм, зпк, зпс — коэффициенты полезного действия закрытой передачи (редуктора), открытой передачи, муфты, подшипников качения (по кинематической схеме в редукторе две пары подшипников) и подшипников скольжения (по схеме на приводном валу одна пара подшипников).
Значения КПД механических передач (без учета потерь в подшипниках):
Передаточное число. | КПД | |
Свыше 30 | 0,70 — 0,75 | |
14 — 30 | 0,80 — 0,85 | |
8 — 14 | 0,85 — 0,95 | |
Выбираем: з = 0,80
2.Определяем требуемую мощность двигателя:
Рдв = ,
N2 — мощность на выходном валу.
Рдв = 11/0,8 = 13,75 кВт.
Выбираем номинальную мощность из стандартного ряда: Рном = 15 кВт.
Выбираем тип двигателя: для пректируемых машинных агрегатов рекомендуются трехфазные асинхронные короткозамкнутые двигатели серии 4А. эти двигатели наиболее универсальны. Закрытое и обдуваемое исполнение позволяет применять эти двигатели для работы в загрязненных условиях, в открытых помещениях и т. п. Двигатели серии 4А применяют для приводов механизмов, имеющих постоянную или мало меняющуюся нагрузку при длительном режиме работы и большую пусковую нагрузку, вследствие повышенной силы трения и больших инерционных масс. Эти двигатели работают при любом направлении вращения, обеспечивая при необходимости реверсивность машинного агрегата.
Выбор оптимального типа двигателя зависит от типов передач, входящих в привод, кинематических характеристик рабочей машины, и производится после определения передаточного числа привода:
i = = = 12
n1 — частота вращения входного вала, об/мин;
n2 — частота вращения выходного вала, об/мин.
При этом, надо учесть, что двигатели с большой частотой вращения (3 000 об/мин) имеют низкий рабочий ресурс, а двигатели с низкими частотами (750 об/мин) весьма металлоемки, поэтому их нежелательно применять без особой необходимости в приводах общего назначения малой мощности.
Выбираем двигатель: 4АН160S2 — Рном = 15кВт, синхронная частота вращения n = 3 000 об/мин., частота при номинальном режиме nном = 2920 об/мин.
Ммах/Мном = 2,2
Мпуск/Мном = 1,4
По табличным данным: диаметр конца вала ротора — dдв = 42 мм.
угловые скорости валов редуктора:
щ1 = рn1/30 = 3,14*3 000/30 = 314 с-1;
щ2 = 3,14*250/30 = 26,167 с-1
2. Расчет редуктора Определим число витков червяка z2, принимая их в зависимости от передаточного числа i =12; z1 = 2 (минимально возможное число заходов червяка), тогда число зубьев червячного колеса z2 = i? z1 = 12? 2 = 24.
Выбор материала червяка и червячного колеса.
Червяки изготовляют из стали. Сталь в настоящее время — основной материал. Применим среднеуглеродистую конструкционную сталь 45 с закалкой ТВЧ до твердости не менее 45 с последующим шлифованием.
Червячные колеса изготовляют обычно составными: венец — бронзовый, центр чугунный (чугун марки СЧ15 — 32); венцы соединяют с центром либо посадкой с натягом, либо болтами, поставленными без зазора в отверстия из-под развертки.
Натяг бронзового венца на чугунном центре во время работы червячного колеса уменьшается, так как коэффициент линейного расширения бронзы больше, чем чугуна. Во избежание смещения венца относительно центра на их стыке устанавливают 4 — 6 винтов, которые проверяют на срез [ф]ср = 0,25ут. стенки отверстий проверяют на смятие: для бронзы [у]см = 0,3ут, и для чугуна [у]см = 0,4уи. соединение венца с центром осуществляют еще отливкой бронзового венца в литейную форму (кокиль), в которую заранее устанавливают чугунный центр. Во избежание проворота венца на боковых поверхностях центра делают пазы, заполняемые металлом венца при отливке.
Материалы для изготовления зубчатых венцов червячных колес условно делят на три группы: группа I — оловянные бронзы; группа II — безоловянные бронзы и латуни; группа III — серые чугуны.
Выбор марки материала червячного колеса зависит от скорости скольжения и выбирается из таблиц, причем для группы I — vs 5; для группы II vs = 2…5; для группы III — 2.
Скорость скольжения определяется по эмпирической формуле:
vs = 4,3? щ2? i? 10−3 ;
где щ2 — угловая скорость тихоходного вала;
Т2 — вращающий момент на валу червячного колеса:
Т2 = 9,55 Рдв/n2 = 9,55* 15 000/250 = 573 Нм.
vs = 0,45*0,001*3 000* = 11,213 м/с.
Таким образом, выбираем бронзу Бр. АЖ9−4Л (отливка в кокиль). Предел прочности ув = 490 Н/мм2
Определяем допускаемые контактные Н, Н/мм2 и изгибные F, Н/мм2 напряжения.
Допускаемые напряжения определяют для зубчатого венца червячного колеса в зависимости от материала зубьев, твердости витков червяка, скорости скольжения, ресурса и обычно вычисляют по эмпирическим формулам.
Контактное напряжение определим по таблицам:
Н = 152 Н/мм2.
Изгибное напряжение для непрерывной работы:
F = КFLF,
КFL — коэффициент долговечности при расчете на изгиб, при бронзовом венце червячного колеса он определяется по формуле:
КFL =
NУ — суммарное число циклов перемен напряжения Значение КFL изменяется в пределах 0,543…1,0.
Величину NУ определим по формуле: NУ = 60 n2 Lh
Lh — время работы передачи, ч
NУ = 60* 250 *10 000 = 1,5*108
КFL = = 0,573
т. е. получили значение, близкое к минимальному (КFL = 0,543), которое соответствует режиму длительной работы, когда NУ 25 107.
F определяем из таблиц, F = 108 Н/мм,
F = 0,573*108 = 61,892 Н/мм.
Элемент передачи | Марка. | Dмах | Способ изготовления | НRС | ув | ут | [у]н | [у]F | |
Червяк. | Сталь 40Х | У+ТВЧ | 45…50 | ; | ; | ||||
Колесо. (венец) | Бр.АЖ9−4Л | ; | К | ; | 61,89 | ||||
Принимаем предварительно коэффициент диаметра червяка q = 10 для слабонагруженной передачи (Т2 300 Нм).
Крутящий момент на валу червячного колеса:
Т2 = N2/щ2,
где щ2 = - угловая скорость тихоходного вала.
щ2 = 3,14*250/30 = 26,167 с-1 ;
Т2 = 11 000/26,167 = 420,382 Нм.
Принимаем предварительно коэффициент нагрузки, при vs = 11,213м/с 3 м/с: К = 1,3.
Определяем основной параметр — межосевое расстояние из условия контактной прочности:
ащ = [z2/(q + 1] ;
ащ = = 2,182 = 107,292 мм. (110 мм).
Определим модуль:
m = 2ащ/(z2 + q) = 2*107,292/(24 + 10) = 6,308.
Принимаем по ГОСТ 2144– — 76 стандартные значения m и q:
m = 6,3 q = 10.
Минимально допустимое значение q и условия жесткости червяка
qmin = 0,212z2 = 0,212 = 5,088
Межосевое расстояние при стандартных значениях m и q:
ащ = m (q + z2)/2 = 6,3(10 + 24)/2 = 107,1 мм.
если бы требовалось спроектировать стандартный редуктор с параметрами по ГОСТ 2144– — 76, то то следовало бы принять, а = 100 мм и пересчитать m и q и т. д.
Основные размеры червяка:
делительный диаметр червяка: d1 = qm = 10*6,3 = 63 мм;
диаметр вершин витков червяка: dа1 = d1 + 2m = 63 + 12.6 = 75.6 мм;
диаметр впадин витков червяка: df1 = d1 — 2,4m = 63 — 15.12 =47.88 мм;
длина нарезанной части шлифованного червяка: при z1 = 2
b1 (11 + 0,06z2)m + 25 = (11 + 0,06*24)6.3 + 25 = 78.372 мм.
принимаем b1 = 80 мм.
Делительный угол подъема г находим из таблиц:
г = 11 018/36//
tg г = z1/q = 2/10 = 0,20 г = 11.30 990 110 19/.
Основные размеры венца червячного колеса:
делительный диаметр червячного колеса: d2 = z2m = 24*6.3 = 151.2мм;
диаметр вершин зубьев червячного колеса: da2 = d2 + 2m = 151.2 + 2*6.3 = 163.8 мм;
диаметр впадин червячного колеса: df2 = d2 — 2,4m = 151.2 — 2,4*6.3 = 136.08 мм;
наибольший диаметр червячного колеса: daм2 da2 + (6m/z1 + 2) = 163.8 + (6*6.3/2 + 2) = 184.7 мм; принимаем 185 мм.
ширина венца червячного колеса: b2 0,75da1 = 0,75*75.6 = 56.7 мм, принимаем 60 мм.
Окружная скорость червяка:
V1 = рd1n1/60 = 3,14*63*10−3*3000/60 = 9.89м/с;
Скорость скольжения:
Vs = V1/Соs г = 9.89/0,98 = 10.086 м/с.
По таблицам при данной скорости определяем [у]н: [у]н =135 Н/мм2
Отклонение [(135 — 152)/152]*100 = 11.18% (допускается 15%).
К тому же межосевое расстояние, полученное по расчету (107,292 мм) после выравнивания по стандарту m и q немного уменьшилось до 107,1 мм.
Произведем проверку [у]н. для этого уточняем КПД редуктора: по таблицам определяем значение коэффициента трения f/ и приведенного угла трения р/: при Vs = 10 м/с: f/ = 0,016…0,024; р/ = 0055/ - 1022/.
Выбираем меньшее значение f/ = 0.016 и р/ = 10, так как червяк шлифованный.
КПД редуктора с учетом потерь в опорах, потери на разбрызгивание и перемешивание масла:
з = (0,95…0,96)tg г/ tg (г + р/) = 0,95*0,20/0,2182 = 0,8708
выбираем 7 класс точности.
Коэффициент динамической нагрузки: КV = 1,2.
Коэффициент неравномерности распределения нагрузки:
Кв = 1 + (z2/и)3 (1 — х),
где и — коэффициент деформации, определяемый по таблицам (при q = 10 и = 86)
х — вспомогательный коэффициент, при незначительных нагрузках х = 0,6 :
Кв = 1 + (24/86)3 (1 — 0,6) = 1,0087.
Коэффициент нагрузки:
К = КVКв = 1,2*1,0087 = 1,21.
Проверяем контактное напряжение:
ун = 170/(z2/q) = ун = 170/(24/10) = 145 Н/мм2
получили: ун [у]н = 152 н/мм2, что вполне удовлетворительно.
Проверяем прочность зубьев червячного колеса на изгиб.
Эквивалентное число зубьев: zи = z2/Соs3 г = 24/0,983 = 25,5.
Коэффициент формы зуба для zи = 26: гF = 2,43.
Напряжение изгиба:
уF = 1,2Т2КгF/z2b2m2.
уF = 1,2*420 382*1,21*2,43/24*60*39,69 = 25,952 Н/мм2.
Полученный результат вполне удовлетворителен: он значительно меньше уF [у]F = 61,89 Н/мм.
Проверка на смещение:
коэффициент смещения ч = ащ/m — 0,5(q + z2)
ч = 107,1/6,3 — 0,5(10 + 24) = 17 — 17 = 0
Следовательно, расчет проведен верно!
Таким образом, произведен расчет червячной передачи. Расчет производился в два этапа: первый расчет — п р о е к т н ы й, второй — п р о в е р о ч н ы й. Проектный проводился по допускаемым контактным напряжениям с целью определения геометрических размеров редукторной пары. В процесс проектного расчета мы задавались целым рядом табличных величин коэффициентов; результаты некоторых расчетных величин округлялись до целых или стандартных значений. Поэтому после окончатального определения параметров зацепления был выполнен проверочный расчет. Он подтвердил правильность выбора табличных величин, коэффициентов и полученных результатов в проектном расчете, а также определены соотношения между расчетными и допускаемыми напряжениями изгибной и контактной выносливости.
3. Предварительный расчет валов редуктора и конструирование червяка и червячного колеса Определяем крутящие моменты в поперечных сечениях валов.
Ведомый — вал червячного колеса:
ТК2 = Т2 = 420,382 Нм = 420,382 103 Нмм.
Ведущий — червяк:
ТК1 = Т1 = Т2/uз = 420,382 103/120,8708 = 40,229 103 Нмм.
Витки червяка выполнены заодно с валом.
Ведущий вал.
Определяем диаметр выходного конца вала по расчету на кручение:
d в1
где [ф]к — допускаемое напряжение на кручение. Для валов из сталей 40, 45, ст. 6 обычно принимают пониженное значение [ф]к = 20…25 Н/мм2. Если значение d в1 находится в одном диаметральном диапазоне со значением диаметра вала двигателя dдв, то их приравнивают, исходя из конструктивных особенностей.
d в1 20 = 21.585 мм.
Но для соединения его с валом ранее выбранного электродвигателя принимаем размер диаметра d в1 = dдв = 42 мм.
Диаметр вала под подшипники (диаметры подшипниковых шеек): d n1 = d в1 + 2t, где t — параметр, определяемый по таблицам. В нашем случае t = 4,0, тогда d n1 = 42 + 8 = 50 мм.
Полученный результат округляем до ближайшего значения из стандартного ряда R40 по ГОСТ 6636– — 69: d n1 = 50 мм.
Параметры нарезной части (находим исходя из найденных ранее размеров червяка):
делительный диаметр червяка: d1 = 63 мм.
диаметр вершин витков червяка: d а1 = 75.6 мм (76мм) .
диаметр впадин витков червяка: d f1 = 47.88 мм (50 мм).
Для выхода режущего инструмента при нарезании витков рекомендуется участки вала, прилегающие к нарезке, протачивать до диаметра меньше d f1.
длина нарезной части: b1 = 80 мм.
расстояние между опорами червяка принимаем равным наибольшему диаметру червячного колеса L1 d am2 = 185 мм. По конструктивным соображениям выбираем d am2 = 200 мм.
расстояние от середины выходного конца до ближайшей опоры f1 принимаем исходя из конструктивных соображений: 110 мм.
Ведомый вал.
Диаметр выходного конца вала
d в2
d в2 20 = 47,19 мм.
Полученное значение округляем до ближайшего значения стандартного ряда R40: d в2 = 50 мм.
Диаметр под подшипники:
d n2 = d в2 + 2t,
d n2 = 50 + 8 = 58 мм.
Полученное значение округляем до ближайшего значения стандартного ряда R40: d n2 = 60 мм.
Диаметр вала под червячным колесом:
d k2 = d n2 + 3r,
значение r берем из таблиц: r = 3
d k2 = 60 + 9 = 69 мм.
Округляем до стандартного значения d к2 = 70 мм.
Диаметр ступицы червячного колеса: d сm2 = (1,6…1,8)d к2 = 112… 126 мм, выбираем 120 мм .
Длина ступицы червячного колеса: L сm2 = (1,2…1,8)d к2 = 84…126 мм, выбираем 100 мм.
Условный угол 2н охвата червяка венцом колеса:
Sinн = = = 0.82 816; н = 55,90.
4. Конструктивные размеры корпуса редуктора В корпусе редуктора размещаются детали зубчатых и червячных передач. При его конструировании должны быть обеспечены прочность и жесткость, исключающие перекосы валов.
Для повышения жесткости служат ребра, располагаемые у приливов под подшипники. Корпус обычно выполняют разъемным, состоящим из основания (его иногда называют картером) и крышки. Плоскость разъема проходит через оси валов. В вертикальных цилиндрических редукторах разъемы делают по двум и даже по трем плоскостям. При конструировании червячных редукторов иногда применяют неразъемные корпуса со съемными крышками.
Материал корпуса обычно чугун СЧ 12 — 28 или СЧ 15 — 32. сварные конструкции из листовой стали Ст2 и Ст3 применяют редко, главным образом для крупногабаритных редукторов индивидуального изготовления. Толщина стенок сварных корпусов на 20 — 30% меньше, чем чугунных.
При конструировании таких корпусов следует придерживаться установленных литейных уклонов, радиусов галтелей и переходов.
Основание корпуса и крышку фиксируют относительно друг друга двумя коническими штифтами, устанавливаемыми без зазора до расточки гнезд под подшипники. Основание и крышку корпуса соединяют болтами (dб) для обеспечения герметичности. Ориентировочно принимают расстояние между осями болтов (10…15) dб.
Для предотвращения протекания масла плоскости разъема смазывают спиртовым лаком или жидким стеклом. Ставить прокладку между основанием и крышкой нельзя, так как при затяжке болтов она деформируется и посадка подшипников нарушается.
Для захватывания редуктора при подъеме делают под фланцем основания приливы в виде крюков. Для снятия крышки делают крюки или петли на ней.
Для заливки масла и осмотра в крышке корпуса имеется окно, закрываемое крышкой. В редукторах с большим выделением тепла предусматривают отдушину, соединяющую внутреннюю полость редуктора с окружающим воздухом. Установка отдушины повышает надежность уплотнителей. Простой отдушиной может быть ручка крышки смотрового отверстия или пробка с отверстиями.
Для удаления загрязненного масла и для промывки редуктора в нижней части корпуса делают отверстие под пробку с цилиндрической или конической резьбой. Под цилиндрическую пробку ставят уплотняющуюся прокладку из кожи, маслостойкой резины, алюминия или меди. Надежнее уплотняет коническая резьба.
Маслоспускное отверстие выполняют на уровне днища или несколько ниже его. Желательно, чтобы днище имело наклон 1 — 20 в сторону маслоспускного отверстия.
Для облегчения отделения крышки от основания корпуса при разборке на поясе крышки устанавливают два отжимных болта.
Подшипники закрывают чугунными крышками (литье СЧ 12 — 28 и СЧ 15 — 32).
Редуктор и электродвигатель обычно устанавливают на сварной раме. Диаметр фундаментных болтов и их число выбраны ниже.
При конструировании корпусов редукторов стремятся к устранению выступающих элементов с наружных поверхностей. Бобышки подшипниковых гнезд убирают внутрь корпуса; крепежные болты размещают в нишах, располагая их вдоль длинных сторон (там, где есть бобышки). Крышки подшипниковых гнезд врезные.
Основные размеры корпуса и крышки:
толщина стенок корпуса: д = 0,04ащ + 2 = 0,04*107.1 + 2 = 6.284 мм (принимаем д = 7 мм);
крышки: д1 = 0,032ащ + 2 = 0,032*107.1 + 2 = 5.427 мм (принимаем д1 = 6 мм);
толщина фланцев (поясов) корпуса и крышки: b = b1 = 1,5д = 1,5*7 = 10.5 мм, выбираем 11 мм;
толщина нижнего пояса корпуса при наличии бобышек:
р1 = 1,5д = 1,5*7 = 10,5 мм (11 мм);
р2 = (2,25…2,75)д = 15,75…19,25 мм (выбираем р2 = 18 мм);
диаметры фундаментных болтов:
dф = (0,03…0,036)а + 12 = 15,213…15,856 мм;
выбираем стандартный болт: d = 16 мм. с резьбой М20.
5. Первый этап компоновки редуктора Компоновочный чертеж выполняем в двух проекциях — разрез по оси колеса и разрез по оси червяка. Масштаб выбирается в зависимости от габаритных размеров редуктора (1: 1; 1:2; 1:2,5; 1:4). Чертить тонкими линиями!
Примерно посередине листа параллельно его длинной стороне проводим осевую линию; вторую осевую, параллельную первой, проводим на расстоянии ащ = 95 мм. затем проводим две вертикальные осевые линии, одну для главного вида, вторую — для вида сбоку.
Вычерчиваем на двух проекциях червяк и червячное колесо.
Очерчиваем внутреннюю стенку корпуса, принимая зазор между стенкой и червячным колесом и между стенкой и ступицей червячного колеса 15 мм.
Вычерчиваем подшипники червяка на расстоянии l1 = d ам2 = 185 мм один от другого, располагая их симметрично относительно среднего сечения червяка.
Так же симметрично располагаем подшипники вала червячного колеса. Расстояние между ними замеряем по чертежу l2 = 150 мм.
В связи с тем, что в червячном зацеплении возникают значительные осевые усилия, принимаем радиально-упорные подшипники: шариковые средней серии для червяка и роликовые конические легкой серии для вала червячного колеса.
Условное обозначение подшипников | d | D | В | Т | С | е | |
Размеры, мм | кН | ||||||
23,5…24,0 | 58,1 70,8 | 0,62 0,351 | |||||
6. Проверка долговечности подшипников Изобразим усилия в зацеплении:
Рис. 1. Усилия в червячном зацеплении и опорные реакции.
Окружное усилие на червячном колесе, равное осевому усилию на червяке:
Р2 = Ра1 = 2Т2/d2,
Р2 = 2420,382 103/151,2 = 5560,608 Н.
Окружное усилие на червяке, равное осевому усилию на колесе:
Р1 = Ра2 = 2Т1/d1;
Р1 = 240,229 103/63 = 1277,111 Н.
Радиальные усилия на колесе и червяке:
Рr2 = Рr1 = Р2 tgб = 5560,608tg200 = 2023,896 Н.
При отсутствии специальных требований червяк должен иметь правое направление витков.
Вал червяка.
Расстояние между опорами l1 = 185 мм.
Диаметр d1 = 50 мм.
Определяем реакции опор (правую опору, воспринимающую внешнюю осевую силу Ра1, обозначаем цифрой «2»):
в плоскости ху
Rх1 = Rх2 = Р½ = 1277,111/2 = 638,556 Н;
в плоскости уz
— Rу1l1 + Рr1l½ — Ра1d½ = 0
Rу1 = (2023,896 185/2 — 5560,60 850/2)/185 = 65,142 Н.
Rу2l1 — Рr1l½ — Ра1d½ = 0
Rу2 = (2023,896 185/2 + 5560,60 850/2)/185 = 1958,754 Н.
Контроль: 65,142 + 1958,754 — 2023,896 = 0.
Суммарные реакции:
Fr1 = R1 = = = 641,87 Н.
Fr2 = R2 = = = 2060,021 Н.
Осевые составляющие радиальных реакций шариковых радиально-упорных подшипников:
S1 = еFr1 = 0,62 641,87 = 397,96 Н.
S2 = еFr2 = 0,622 060,021 = 1277,213 Н, где для подшипников шариковых радиально-упорных с углом б = 260 коэффициент осевого нагружения е = 0,62 (табличные данные).
Осевые нагрузки подшипников.
В нашем случае S1 S2;
Fа = Ра1 S2 — S1 = 1277,213 — 397,96 = 879,253 Н, тогда
Fа1 = S1 = 397,96 Н;
Fа2 = S1 + Fа = 397,96 + 5560,608 = 5958,568 Н.
Рассмотрим левый («первый») подшипник.
Отношение Fа1/Fr1 = 397,96/641,87 = 0,62 = е;
Осевую нагрузку не учитываем.
Эквивалентная нагрузка:
Рэ1 = Fr1 V Кб Кт = 641,871,3 = 834,431 Н.
Долговечность определяем по более нагруженному подшипнику.
Рассмотрим правый («второй») подшипник.
Отношение Fа2/Fr2 = 5958,568/2060,021 = 2,892 е, поэтому эквивалентную нагрузку определяем с учетом осевой:
Рэ2 = (ХFr2V + УFа2) Кб Кт =
=(0,42 060,0211 + 0,875 958,568) 1,3 = 7810,351 Н 7,8 кН.
Расчетная долговечность в миллионах оборотов:
L = = (= 413,280 млн.об.
Расчетная долговечность в часах:
Lh = L106/60 n = 413,280 106/602920 = 2358,905 часа.
здесь n = 2920 об/мин — частота вращения червяка (электродвигателя).
Ведомый вал.
Расстояние между опорами (точнее, между точками приложения радиальных реакций R3 и R4 — рисунок) l2 = 150 мм.
Диаметр d2 = 60 мм.
Реакции опор (левую опору, воспринимающую внешнюю осевую силу Ра2, обозначим цифрой «4» и при определении осевого нагружения будем считать ее «второй»).
в плоскости ху
Rz3 = Rz4 = Р2/2 = 5560,608/2 = 2780,304 Н.
в плоскости уz
— Rу3l2 + Рr2l2/2 — Ра2d2/2 = 0
Rу3 = (2023,896 150/2 — 1277,11 160/2)/150 = 756,526 Н.
Rу4l2 — Рr2l2/2 — Ра2d2/2 = 0
Rу4 = (2023,896 150/2 + 1277,11 160/2)/150 = 1267,37 Н.
Проверка:
Rу3 — Rу4 + Рr2 = 756,526 + 1267,37 — 2023,896 = 0.
Суммарные реакции:
Fr3 = R3 = = = 2881,392 Н.
Fr4 = R4 = = = 3055,539 Н.
Осевые составляющие радиальных реакций конических подшипников:
S3 = 0,83еFr3 = 0,83* 0,351* 2881,392 = 839,436 Н.
S4 = 0,83еFr4 = 0,83*0,351*3055,539 = 890,17 = Н.
где для подшипников 7212 коэффициент влияния осевого нагружения е = 0,351.
Осевые нагрузки подшипников в нашем случае
S3 S4;
Fа = Ра2 S4 — S3 = 890,17 — 839,436 = 50,734 Н, тогда
Fа3 = S3 = 839,436 Н;
Fа4 = S3 + Fа = 839,436 + 1277,111 = 2116,547 Н.
Рассмотрим правы («третий») подшипник.
Отношение Fа3/Fr3 = 839,436/2881,392 = 0,2113 е = 0,351;
Осевую нагрузку не учитываем.
Эквивалентная нагрузка:
Рэ3 = Fr3 V Кб Кт = 2881,3921,3 = 3745,81 Н.
В качестве опор ведомого вала применены одинаковые подшипники 7212. Долговечность определим для левого подшипника («четвертого»), для которого эквивалентная нагрузка значительно больше.
Для левого («четвертого») подшипника:
Отношение Fа4/Fr4 = 2116,547/3055,539 = 0,693 е, поэтому эквивалентную нагрузку определяем с учетом осевой: учитываем, что V = 1; Кб = 1,3 Кт = 1; Х = 0,4; У = 1,71
Рэ4 = (ХFr4V + УFа4) Кб Кт =
= (0,4*3055,539*1 + 1,71*2116,547)*1,3 = 6293,964. 6,3 кН.
Расчетная долговечность в млн. оборотах:
L = = (= 3179,135 млн.об.
Расчетная долговечность в часах:
Lh = L106/60 n2 = 3179,135 106/60250 = 211 942,361 часа.
здесь n2 = 250 об/мин — частота вращения вала червячного колеса.
Столь большая расчетная долговечность объясняется тем, что по условию монтажа диаметр шейки должен быть больше диаметра dв2 = 50 мм. поэтому был выбран подшипник 7212 (легкая серия).
7. Второй этап компоновки редуктора Используем чертежи первого этапа компоновки. Второй этап имеет целью конструктивно оформить основные детали — червячный вал, вал червячного колеса, червячное колесо, корпус, подшипниковые узлы и др.
Выбираем способ смазки зацепления и подшипников: Смазка зацепления и подшипников — разбрызгиванием жидкого масла, залитого в корпус ниже уровня витков так, чтобы избежать чрезмерного заполнения подшипников маслом, нагнетаемым червяком. На валу червяка устанавливаем крыльчатки; при работе редуктора они будут разбрызгивать масло и забрасывать его на колесо и в подшипники.
Вычерчиваем уплотнения, пробку для слива масла, маслоуказатель. В крышке люка размещаем отдушину. Конструируем стенку корпуса и крышки. В нижней части корпуса вычерчиваем пробку для спуска масла. Вычерчиваем фланцы и нижний пояс, конструируем крюки для подъема. Вычерчиваем крышки подшипников. Под крышки устанавливаем металлические прокладки.
Вычерчиваем шпонки: на выходном конце вала червячного колеса и под червячным колесом. Размеры сечений шпонок, пазов и длины шпонок определяем по таблице П3. Длину шпонки выбираем из стандартного ряда, так, чтобы она была несколько меньше длины ступицы (на 5 — 10 мм.).
8. Тепловой расчет редуктора Цель теплового расчета — проверка температуры масла tм в редукторе, которая не должна превышать допускаемой [t]м = 80…950. температура воздуха вне корпуса редуктора обычно tв = 20.
При установившемся режиме работы редуктора все выделяющееся тепло отдается через его стенку окружающему воздуху; этому соответствует определенный перепад температур между маслом и окружающим воздухом.
Условие работы редуктора без перегрева:
Дt = tм — tв = [Дt]
где Nт — подводимая мощность или мощность на валу червяка, Вт з — КПД редуктора;
Rt — коэффициент теплопередачи (Rt = 11.17 Вт/м2);
F — площадь теплоодающей поверхности корпуса редуктора, м2, при подсчете площади площадь днища не учитываем;
[Дt] = 40…60 — допускаемый перепад температур между маслом и окружающим воздухом.
Дt = = 56,2 .
Температура масла: tм = Дt + 20 = 56,2 + 20 = 76,2.
Таким образом, при максимальном значении коэффициента теплопередачи перепад температур в норме, в норме же и температура масла. В нашем случае следует увеличивать теплоотдающую поверхность за счет введения ребер. Редуктор может работать в повышенном тепловом режиме.
9. Проверка прочности шпоночных соединений Шпонки призматические со скругленными торцами. Размеры сечений шпонок, пазов и длины шпонок по ГОСТ 23 360– — 78.
Материал шпонок — сталь 45 нормализованная.
Напряжения смятия и условие прочности:
= [у]см Допускаемые напряжения смятия при стальной ступице [у]см = 100…120 Н/мм2
При чугунной ступице: [у]см = 50…70 Н/мм2.
Ведущий вал.
dв1 = 42 мм; сечение шпонки b h = 12 8 мм; глубина паза t1 = 5 мм; длина шпонки l1 = 80 мм. (при длине части вала под двигатель 90 мм.).
усм = = 8,178 Н/мм2 [у]см Ведомый вал.
Шпонка в ступице: d к2 = 70 мм; сечение шпонки b h = 18 12 мм; глубина паза t2 = 6 мм; длина шпонки l2 = 85 мм. (при длине ступицы 100 мм).
усм = = 74,84 Н/мм2 [у]см.
шпонка на конце вала: d = 50 мм; сечение шпонки b h = 14 8 мм; глубина паза t2 = 5,5 мм; длина шпонки l2 = 55 мм. (при длине участка под крыльчатку 55 мм).
усм = = 32,81 Н/мм2 [у]см.
Таким образом, шпонки выбраны верно.
10. Уточненный расчет валов Червячный вал проверять на прочность не следует, так как размеры его поперечных сечений, принятые при конструировании после расчета геометрических характеристик (d1 = 63 мм; dа1 = 75,6 мм (80 мм); df1 = 47,88 мм (50 мм)), значительно превосходят те, которые могли быть получены расчетом на кручение. Диаметр выходного конца получился ранее при расчетах на кручение 21,585 мм, а мы по соображениям конструирования приняли его dв1 = 48 мм.
Проверим стрелу прогиба червяка (расчет на жесткость).
Приведенный момент инерции поперечного сечения червяка:
Jпр = (0,375 + 0,625) =
= (0,375 + 0,625) = 351 328,372 мм4 = 3,513*105 мм4.
Стрела прогиба:
f = = = 0,0043 мм.
Допускаемый прогиб:
[f] = (0,005…0,01) m = (0,005…0,01)*6,3 = 0,0315…0,063 мм.
Таким образом жесткость обеспечена, так как f = 0.0241 мм [f].
Определяем коэффициенты запаса прочности в опасных сечениях вала червячного колеса.
Материал вала — сталь 45, термообработка — улучшение.
По справочным данным при диаметре 100 — 500 мм (в нашем случае dа2 = 163,8 мм (165 мм)) среднее значение предела прочности ув = 570 Н/мм2.
Предел выносливости при симметричном цикле изгиба у-1 0,43ув = 0,43* 570 = 245,1 Н/мм2.
Предел выносливости при симметричном цикле касательных напряжений:
ф-1 = 0,58у-1 = 0,58*245,1 = 142,158 Н/мм2.
Сечение, А — А:
В этом сечении при передаче вращающего момента от электродвигателя возникают только касательные напряжения. Концентрацию напряжений вызывает наличие шпоночной канавки.
Коэффициент запаса прочности:
n = nф = .
где амплитуда и среднее напряжение от нулевого цикла фv = фm = фmax/2 = T½*Wнетто.
При d = 50 мм; b = 16 мм; t2 = 6 мм.
Момент сопротивления изгибу:
Wнетто = = =
= 24 543,693 — 1858,56 = 22 685,133 мм²;
фv = фm = 40,229*103/2*22 685,133 = 0,867 Н/мм2
Принимаем по табличным данным для валов со шпоночными канавками с выточками
(ув = 600) kф = 1,5; еф 0,70 и шф 0,1.
После подстановки:
n = nф = = 73 очень большой запас!!!
Получили довольно большой коэффициент запаса прочности. По этой причине проверять прочность в сечениях Б — Б и В — В нет необходимости.
Вывод: в нашем случае запасы прочности больше [n], так как диаметры участков выбранные по условиям монтажа, превышают расчетные.
Рис. 2. Расчетная схема вала червячного колеса.
11. Посадки деталей редуктора и оформление чертежа Посадки назначаем в соответствии с СТ СЭВ 144 — 75 и по ОСТ.
Посадка червячного колеса на вал Н7/р6 по СТ СЭВ 144 — 75 соответствует легкопрессованной посадке 2-го класса точности А/Пл по ОСТ.
Шейки валов под подшипники выполняем с отклонением вала k6, чему соответствует Нп по ОСТ. Отклонения отверстий в корпусе по Н7, чему соответствует Сп по ОСТ.
Остальные посадки назначаем, пользуясь табличными данными.
Редуктор вычерчиваем в двух проекциях на листе формата А1 (594 841) в масштабе 1: 1 со штампом и спецификацией. Сборочный чертеж вычерчивается в соответствии с требованиями ЕСКД.
12. Выбор сорта масла Смазка червячных зацеплений и подшипников уменьшает потери на трение, предотвращает повышенный износ и нагрев деталей.
По способу подвода будем применять картерную смазку. Картерная смазка осуществляется окунанием червячных колес (или червяков) в масло, заливаемое внутрь корпуса. Эту смазку применяют при окружных скоростях в зацеплении червячных передач до v 10 м/с.
Червячные колеса погружают в масло на высоту зуба, а червяк (расположенный внизу) — на высоту витка, но не выше центра нижнего тела качения подшипника. Если условия нормальной работы подшипника не позволяют погружать червяк в масло, то применяют брызговки, забрасывающие масло на червячное колесо.
Выбор сорта масла начинают с определения необходимой кинематической вязкости масла: для червячных передач — в зависимости от от скорости скольжения. Затем по найденному значению вязкости выбираем соответствующее масло по таблицам.
Смазка зацепления и подшипников производится разбрызгиванием жидкого масла. По таблицам устанавливаем вязкость масла. При скорости скольжения vск = 10 м/с рекомендуемая вязкость н50 = 118 сСт. По таблицам принимаем масло индустриальное И-100А по ГОСТ 20 799– — 75.
Контроль уровня масла, находящегося в корпусе редуктора, производят с помощью маслоуказателей.
13. Сборка редуктора Перед сборкой внутреннюю полость корпуса тщательно очищаем и покрываем маслостойкой краской. Сборку редуктора производим в соответствии с чертежом общего вида. Начинаем сборку с того, что на червячный вал надеваем крыльчатки и шариковые радиально-упорные подшипники, предварительно нагрев их в масле до температуры 80 — 100. Собранный червячный вал вставляем в корпус.
Вначале сборки вала червячного колеса закладываем шпонку и напрессовываем колесо до упора в бурт вала; затем надеваем распорную втулку и устанавливаем роликовые конические подшипники, также нагретые в масле. Собранный вал укладываем в основание корпуса и надеваем крышку корпуса, покрывая предварительно поверхности стыка фланцев спиртовым лаком. Для центровки крышку устанавливаем на корпус с помощью двух конических штифтов и затягиваем болты.
Закладываем в подшипниковые сквозные крышки резиновые манжеты и устанавливаем крышку с прокладками.
Ввертываем пробку маслоспускного отверстия с прокладкой и маслоуказатель. Заливаем в редуктор масло и закрываем смотровое отверстие крышкой с отдушиной.
Собранный редуктор обкатываем и испытываем на стенде в соответствии с техническими условиями.
редуктор червячный подшипник вал Заключение В процессе выполнения курсового проекта по дисциплине «Детали машин», была усвоена методика расчета и конструирования механизмов и деталей, научились пользоваться технической литературой, справочниками, каталогами и ГОСТами.
Были развиты способности выполнения сборочных чертежей деталей с правильной простановкой размеров, предельных отклонений и шероховатости поверхности в соответствие с требованиями ЕСКД.
Научились разрабатывать конструкцию одноступенчатого червячного редуктора, выбирать требуемый электродвигатель, подбирать соответствующие подшипники, сорт масла, соответствующие стандартные изделия.
Усвоено правило сборки и разборки редуктора.
1. Анурьев В. Н. Справочник конструктора-машиностроителя. Изд. 7-е в 3-х тт. — М.: Машиностроение, 1992.
2. Гузенков П. Г. Детали машин. Учабник для вузов. Изд. 3-е перераб. и доп. — М.: Высшая школа, 1992.
3. Дунаев П. Ф. Леликов О. П. Детали машин: Курсовое проектирование. — М.: Высшая школа, 1984.
4. Иванов М Н. Детали машин. — М.: Машиностроение, 1994.
5. Курсовое проектирование деталей машин / Под ред. В. Н. Кудрявцева. — С-Пб.: 2004.
6. Курсовое проектирование деталей машин: Учеб. пособие для техникумов./ С. А. Чернавский, Г. А. Снесарев, И. М. Чернин, Г. И. Ицкович, В. П. Козинцев. — М.: Машиностроение, 1988.
7. Мягков В. Д. Краткий справочник конструктора. — М.: Машиностроение, 1985.
8. Снесарев Г. А. Конструирование редукторов // Методические рекомендации по технической механике. Вып.6. — М.: Машиностроение, 1992.
9. Штейнблит А. Е. Курсовое проектирование деталей машин.- М.: Высшая школа, 1991.
Приложения
1. Примерный сборочный чертёж червячного одноступенчатого редуктора (вид спереди).
2. Примерный сборочный чертёж червячного одноступенчатого редуктора (вид сбоку).
3. Пример рабочего чертежа вала-червяка.
4. Пример сборочного чертежа червячного колеса.
5. Пример рабочего чертежа тихоходного вала.
Спецификация сборочного чертежа червячного одноступенчатого редуктора.