Проектирование машиностроительного производства
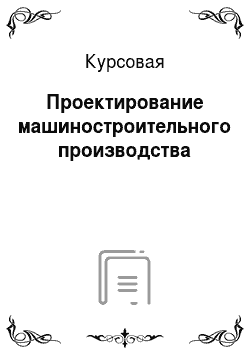
Q = 500 т — масса материала и заготовок; t = 6 дней — принятая норма запаса заготовок; q = 10 кН/м2 — средняя допускаемая нагрузка на 1 м² полезной площади пола; Ки = 0,3 — коэффициент использования площади складирования; Ф = 250 — число рабочих дней в году; Приобретение практических навыков по определению основного технологического оборудования на стадии технического проекта и подготовка… Читать ещё >
Проектирование машиностроительного производства (реферат, курсовая, диплом, контрольная)
Министерство образования российской федерации ТОЛЬЯТТИНСКИЙ ГОСУДАРСТВЕННЫЙ УНИВЕРСИТЕТ Кафедра «Технология машиностроения»
ПРАКТИЧЕСКАЯ РАБОТА по дисциплине «Проектирование машиностроительного производства»
Студент: Рожков А.В.
Группа: М-501
Преподаватель: Черемисин А.С.
ТОЛЬЯТТИ, 2005 г.
- Введение
- 1. Исходные данные для расчетов
- 2. Определение технологического маршрута обработки детали «Конус ведущий» и штучно калькуляционного времени
- 3. Расчет действительного фонда времени работы оборудования
- 4. Рассчитываем количество оборудования по операциям
- 5. Определение коэффициента загрузки оборудования
- 6. Определение количества рабочих
- 7. Определение площади цеха
- 8. Определяем площадь контрольного отделения
- Литература
На любом машиностроительном предприятии, выпускающем ту или иную продукцию, необходимо рационально использовать производственные площади, энергетические ресурсы и технологическое оборудование, тем самым снижая затраты на производство, что в свою очередь положительно скажется на себестоимости выпускаемой продукции.
Цель данной работы:
приобретение практических навыков по определению основного технологического оборудования на стадии технического проекта и подготовка исходных данных для составления планировки участков механической обработки деталей;
усвоение принципов и требований, которые предъявляются к планировкам участков механических цехов;
приобретение навыков по рациональному распределению площадей и размещению отделений, участков и служб цеха.
1. Исходные данные для расчетов
а. Производственная программа выпуска деталей — 5000 шт.;
б. Число рабочих смен в день: две смены;
в. Чертеж детали «конус ведущий» (см. приложение).
2. Определение технологического маршрута обработки детали «Конус ведущий» и штучно калькуляционного времени
2.1 Выбор и проектирование заготовки.
Для детали типа конуса ведущего в среднесерийном производстве в качестве заготовки целесообразно принять прокат.
Согласно рекомендациям выбираем штамповку на ГКМ и прокат.
Согласно рекомендациям стоимость заготовок, получаемых такими методами, как штамповка и прокат, можно с достаточной для курсового проектирования точностью определить по следующим формулам:
для штамповки
для проката
где Ci — базовая стоимость 1 т. заготовок (по определяем C1 = 373 руб., С2 = 295 руб.);
КТ, КС, КВ, КМ, КП — коэффициенты, зависящие от класса точности, группы сложности, массы, марки материала и объема производства заготовок;
Q — масса заготовки;
q — масса детали;
Sотх — цена за 1 т. отходов (по табл.2.7 определяем Sотх1 = Sотх2 = 25 руб)
КТ = 1 (по для нормальной точности);
КС = 0,77 (по табл.2.12 для стали ШХ15 и 1-ой группы сложности);
КВ = 1,3 (по табл.2.12 для стали ШХ15);
КМ = 1,77 (по для стали ШХ15); КП = 1 (по табл.2.13 [2]);
Определим массу детали, разбивая объем детали на элементарные объемы:
V1 = м3
V2 = м3 V3 = м3
V4 = м3 V5 = м3
V6 = м3
Тогда Vдет. = V5 + V6 — V1 — V2 — V3 — V4 = 0,6 849 м3
Зная плотность стали ШХ15 (= 7800 кг/м3) находим массу:
q =
Определим массу штампованной заготовки. Для этого по табл. ориентировочно назначаем припуски на обработку.
для пов.11 (d = 68) 2Z =1,6 мм. для пов.6 (d = 50) 2Z = 1,6 мм.
для пов.1 (d = 64) 2Z = 1,6 мм.
Определим массу заготовки, разбивая ее объем на элементарные объемы:
V1 = м3
V2 = м3
V3= м3
Тогда Vзаг. = V1 + V2 + V3= 0,1 638 м3
Находим массу заготовки:
Q =
Определим массу заготовки из проката. Для этого, используя табл.1,2,3 ориентировочно назначаем припуск на обработку.
На диаметр (d = 68) 2Z = 1,6 мм.
На длину (d = 50) 2Z = 1,6 мм.
Определим массу заготовки:
Vзаг = м3
Находим массу заготовки:
Q =
Зная массы детали и заготовок, определим коэффициент использования материала:
Для заготовки из проката
Для штампованной заготовки
Находим стоимость заготовок:
Т. к. в результате сравнительного экономического анализа получили, что, то в качестве метода получения заготовки принимаем прокат.
2.2 Выбор маршрутов обработки поверхностей.
Маршрут обработки поверхности — это перечень методов обработки, расположенных в в технологической последовательности.
Таблица 2.1
Маршрут обработки
№ опер. | Наименование операции | Оборудование (тип, модель) | Время, мин | Разряд рабочего | ||
То, мин | Тшт-к, мин | |||||
Заготовительная | Ножовочный станок 872 | |||||
Токарная (черновая) 2 установа | Универсальный токарно; револьверный станок 1Е371 | 1,254 | 1,379 | |||
Токарная (чистовая) 2 установа | Токарно-винторезный станок 1Е61 | 1,15 | 1,265 | |||
Сверлильная | Вертикально-сверлильный станок 2Р135 | 1,5 | 1,65 | |||
Внутришлифовальная (чистовая) 2 установа | Внутришлифовальный станок 3К227А | 1,13 | 0,9 | |||
Круглошлифовальная (чистовая) | Круглошлифовальный станок 3У120А | 0,75 | 1,2 | |||
Итого: 6,394 мин
3. Расчет действительного фонда времени работы оборудования
час.
где: Дк — количество календарных дней в году;
Дв — количество выходных дней в году;
Дп — количество праздничных дней в году;
tсм = 8 час. — продолжительность;
n — количество смен;
Кисп. об. = 0,95 — коэффициент использования оборудования;
час.
4. Рассчитываем количество оборудования по операциям
где: tшт — норма времени на единицу продукции;
Nг — годовой объем выпуска продукции;
Кв. н. = 1,2 — коэффициент выполнения нормы;
Таблица 4.1
Sp05 = 1,379.5000/ (3800.1, 2.60) =0,025 | Sпр = 1 | |
Sp10 = 1,265.5000/ (3800.1, 2.60) =0,023 | Sпр = 1 | |
Sp15 = 1,65.5000/ (3800.1, 2.60) =0,03 | Sпр = 1 | |
Sp20 = 0,9.5000/ (3800.1, 2.60) =0,016 | Sпр = 1 | |
Sp25 = 1,2.5000/ (3800.1, 2.60) =0,022 | Sпр = 1 | |
Всего оборудования | ||
Расчет годовой нормы догрузки оборудования где Ку = 1.05 — коэффициент ужесточения норм
Nд05 = (1.0, 95 — 0,025).3800.60/1,379.1, 05 =145 654 шт;
Nд10 = (1.0, 95 — 0,023).3800.60/1,265.1, 05 =159 124 шт;
Nд15 = (1.0, 95 — 0,03).3800.60/1,65.1, 05 =121 074 шт;
Nд20 = (1.0, 95 — 0,016).3800.60/0,9.1, 05 =225 346 шт;
Nд25 = (1.0, 95 — 0,022).3800.60/1,2.1,05 =167 924 шт;
Пересчет количества оборудования по догруженным операциям
Таблица 4.2
Sp05 = 1,379. (5000+145 654) / (3800.1, 2.60) =0,759 | Sпр = 1 | |
Sp10 = 1,265. (5000+159 124) / (3800.1, 2.60) =0,7588 | Sпр = 1 | |
Sp15 = 1,65. (5000+121 074) / (3800.1, 2.60) =0,76 | Sпр = 1 | |
Sp20 = 0,9. (5000+225 346) / (3800.1, 2.60) =0,7577 | Sпр = 1 | |
Sp25 = 1,2. (5000+167 924) / (3800.1, 2.60) =0,758 | Sпр = 1 | |
Всего оборудования | ||
5. Определение коэффициента загрузки оборудования
Кз. об.05 = 0,759.100 = 75,9% Кз. об.10 = 0,7588.100 = 75,88%
Кз. об.15 = 0,76.100 = 76% Кз. об20 = 0,7577.100 = 75,77%
Кз. об.25 = 0,758.100 = 75,8%
5.1. Определяем средний коэффициент загрузки оборудования
Полученные данные заносим в таблицу
Таблица 5.1
Номер операции | Наименование операции | Норма догрузки Nд | Количество оборудования | Кз. об.% | ||
Sp | Snp | |||||
Токарная | 0,759 | 75,9 | ||||
Токарная | 0,7588 | 75,88 | ||||
Сверлильная | 0,76 | |||||
Внутришлифовальная | 0,7577 | 75,77 | ||||
Круглошлифовальная | 0,758 | 75,8 | ||||
6. Определение количества рабочих
Расчет действительного фонда времени одного рабочего
где: Кпнр. = 0,9 — коэффициент плановых невыходов на работу.
6.2. Расчет численности основных рабочих
Таблица 6.1
Росн. p05 = 1,379. (5000+145 654) / (1800.1, 2.60) =1,603 | Sпр = 2 | |
Росн. p10=1,265. (5000+159 124) / (1800.1, 2.60) =1,602 | Sпр = 2 | |
Росн. p15 = 1,65. (5000+121 074) / (1800.1, 2.60) =1,605 | Sпр = 2 | |
Росн. p20 = 0,9. (5000+225 346) / (1800.1, 2.60) =1,6 | Sпр = 2 | |
Росн. p25 = 1,2. (5000+167 924) / (1800.1, 2.60) =1,601 | Sпр = 2 | |
Всего основных рабочих | ||
6.3. Определение количества вспомогательных рабочих Рвсп = 0,15. Росн. = 0,15.10 = 1,5? 2.
6.4. Определение числа контролеров Ркон = 0,25. Росн. = 0,25.10 = 2,5? 3.
6.5. Определение численности ИТР ИТР = 0,13. (Росн + Рвсп) = 0,13. (10+2) = 1,56? 2.
6.6. Определение численности младшего обслуживающего персонала МОП = 0,025. (Росн + Рвсп) =0,025. (10+3) = 0,325? 1.
7. Определение площади цеха
Определение метода удаления стружки с участка.
Принимаем для данного участка «Систему М» удаления стружки, которая подразумевает механизированную уборку с использованием ручного труда, малой механизации и колесного транспорта, доставляющего стружку в контейнерах в отделение переработки. Оборудование расставлено по группам и в соответствии с нормами расположения станков в зданиях.
Стружка удаляется скребковым конвейером под полом. Для инструмента предусмотрены инструментальные ящики. Для улучшения условий труда на участке предусмотрено место для отдыха, место для питьевого аппарата. Для доставки контейнеров с заготовками и деталями по периметру участка расположена дорога для автопогрузчиков с односторонним движением. В соответствии с нормами, ширина проездов составляет 2500 мм. Подвод сжатого воздуха от общезаводской централизованной системы. В качестве средств пожарной безопасности предусмотрен пожарный щит, ящик с песком.
Определяем предварительную площадь участка из расчета м = 25 м2 на один станок Fпр. = 5.25 = 125 м2.
Параметры станков на операциях
Таблица 7.1
Название операции, станок | Габариты станка, мм | Площадь по габаритам станка, м2 | Удельная площадь, м2 | |
Токарная 1Е371 | 3320×1530 | 5,1 | ||
Токарная 1Е61 | 3320×1565 | 5,2 | ||
Сверлильная 6Р135 | 1240×810 | |||
Внутришлифовальная 3К227А | 2815×1775 | |||
Круглошлифовальная 3У120А | 1600×1670 | 2,7 | ||
Итого | ||||
Определение площади цехового склада материалов и заготовок где:
Q = 500 т — масса материала и заготовок; t = 6 дней — принятая норма запаса заготовок; q = 10 кН/м2 — средняя допускаемая нагрузка на 1 м2 полезной площади пола; Ки = 0,3 — коэффициент использования площади складирования; Ф = 250 — число рабочих дней в году;
Определение площади заточного отделения: Sз = 0,03. Sпр = 0,03.5 = 0,15? 1. Площадь заточного отделения
Fз = Sз. м = 1.25 = 25 м2
8. Определяем площадь контрольного отделения
Площадь контрольных помещений составляет 3…5% от площади, занятой производственным оборудованием
Fк. о. = 0,04. Fпр = 0,04.125 = 5 м2
Определение площади цеховой ремонтной базы
Fм = 1,3. м. Sм = 1,3.25.2 = 65 м2,
где Sм = 2 — количество основных станков ремонтной базы по отношению к количеству обслуживаемого оборудования.
Отделение для переработки стружки
Площадь для переработки стружки составляет 2…4% от площади занятой производственным оборудованием цеха.
Fпстр = 0,02. Fпр = 0,02.125 = 2,5 м2
Определение площади термического отделения
Fтер. = 0,2. Q/g = 0,2.500/2,3 = 43,5, м2
где g =2,3 т/м2 — норма съема продукции с 1 м2 термического отделения.
7.8. Определение площади занимаемой магистральными поездами
Fм = 0,06. Fпр = 0,06.125 = 7,5 м2
Площадь под проходы
Принимаем 30% от площади станков
Sпрох = 125.0, 3 = 37,5 м2
Площадь для места мастера
Принимаем 9 м2
Площадь места отдыха
Принимаем 9 м2
Определение общей площади для размещения участка
Fобщ. = 125+40+25+5+65+2,5+43,5+7,5+37,5+9+9= 369 м2
Для данного участка используем сетку колон 18Ч12 м.
Оборудование расставлено по группам, в соответствии с нормативами расположения станков в зданиях.
Стружка удаляется механизировано с использованием ручного труда. Поэтому между оборудованием предусматривают проходы, достаточные для удаления стружки.
Для перемещения контейнеров используются вильчатые погрузчики, поэтому ширину магистральных проездов принимаем 4 м.
1. " Основы проектирования машиностроительных заводов" Егоров М. Е. Изд.6-е, переработанное, «Высшая школа», 1969 г.
2. «Основы проектирования машиностроительных заводов» Мамаев В. С., Осипов Е. Г., «Машиностроение», 1974 г.
3. Методические указания к организационно-экономическому обоснованию дипломных проектов с развитой технологической частью (проект цеха, участка), сост. Мурахтанова Н. М., Тольятти 1982 г.
4. Методические указания по курсу «Проектирование механосборочных цехов», сост. Черемисин А. С., Тольятти, 1990 г.