Разработка проекта цеха рудоподготовки производительностью 27000 т/сутки
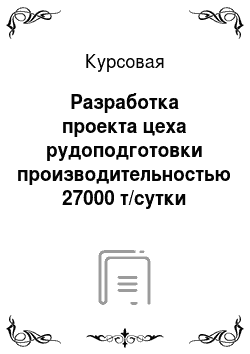
Поскольку сырье, поступающее на обогатительные фабрики, имеет куски критического размера, процесс дробления проводят в несколько стадий. Технологически грамотно процессы дробления сопровождать операциями грохочения. При этом соблюдается принцип не дробить ничего лишнего, своевременно выводить из процесса готовый по крупности класс, что исключает переизмельчение продукта, экономит электроэнергию… Читать ещё >
Разработка проекта цеха рудоподготовки производительностью 27000 т/сутки (реферат, курсовая, диплом, контрольная)
Разработка проекта цеха рудоподготовки производительностью.
27 000 т/сутки Курсовой проект по дисциплине «Обогащение полезных ископаемых».
СОДЕРЖАНИЕ Введение.
1. Исходные данные.
2. Расчет схемы дробления.
3. Выбор и расчет оборудования для I стадии дробления.
4. Выбор и расчет оборудования для II стадии дробления.
5. Выбор и расчет оборудования для II стадии дробления Заключение Список использованных источников Приложения.
1.1. Курсовой проект по дисциплине «Обогащение полезных ископаемых» является завершающим этапом в изучении данной дисциплины.
1.2. Целью курсового проекта является: Разработать проект отделений рудоподготовки с обоснованием и расчетом схемы используемого оборудования.
1.3. Задачами курсового проекта являются:
Ш углубление, закрепление и обобщение знаний, полученных при изучении дисциплины «Обогащение полезных ископаемых»;
Ш развитие навыков теоретической инженерной работы в области подготовительных процессов обогащения полезных ископаемых;
Ш приобретение навыков работы с технической литературой, справочниками, стандартами.
1.4. Назначение процессов рудоподготовки заключается в следующем:
Ш Раскрытие зерен ценного компонента, путем доведения сырья до крупности, соответствующей размеру вкрапленности, пригодного для переработки известными методами.
Ш Получение готового продукта заданной крупности для дальнейшего использования в народном хозяйстве (строительная промышленность).
1.5. Поскольку сырье, поступающее на обогатительные фабрики, имеет куски критического размера, процесс дробления проводят в несколько стадий. Технологически грамотно процессы дробления сопровождать операциями грохочения. При этом соблюдается принцип не дробить ничего лишнего, своевременно выводить из процесса готовый по крупности класс, что исключает переизмельчение продукта, экономит электроэнергию и увеличивает срок службы футеровочных плит дробилок.
1.6. Графическое отображение операций подготовки руды к обогащению называют схемой рудоподготовки. Выбор схемы зависит от следующих факторов:
Ш исходной и конечной крупности продукта;
Ш размера вкрапленности основного и сопутствующих ценных компонентов;
Ш физико-механических особенностей руды (насыпная плотность, абразивность, влажность, показатели дробимости);
Ш имеющегося технологического оборудования.
1.7. Правильный выбор схемы рудоподготовки снижает себестоимость продукта, повышает качество концентрата и показатель извлечения.
2. ИСХОДНЫЕ ДАННЫЕ.
2.1. Исходные данные для расчета представлены в таблице 1.
Таблица 1 — Исходные данные.
Производительность цеха дробления, Qc, т/сутки. | Диаметр максимального куска в исходной руде, Dmax, мм. | Крупность дробленого продукта, dmax мм. | Насыпная плотность, дп т/м3. | |
1,8. | ||||
2.2. Характеристики крупности исходной и дробленой руды представлены в таблицах 2−4.
Таблица 2 — Характеристика крупности исходной руды.
Классы крупности в долях Dmax. | Выход классов крупности,. | |
Dmax+0,75Dmax. | ||
0,75Dmax+0,5Dmax. | ||
0,5Dmax +0,25Dmax. | ||
0,25Dmax+0,125Dmax. | ||
0,12Dmax. | ||
Итого. | ||
Таблица 3 — Характеристика крупности дробленой руды после дробилок 1, 2 стадии.
Классы крупности в. долях разгрузочного отверстия дробилки. | Выход классов крупности, %. | |
+2L. | ||
2L + 1,5L. | ||
1,5L +L. | ||
L + 0,75L. | ||
0,75L + 0,5L. | ||
0,5L + 0,25L. | ||
0,25L. | ||
Итого. | ||
Таблица 4 — Характеристика крупности дробленой руды после дробилок 3 стадии.
Классы крупности в. долях разгрузочного отверстия дробилки. | Выход классов крупности, %. | |
+2L. | ||
2L + 1,5L. | ||
1,5L +L. | ||
L + 0,75L. | ||
0,75L + 0,5L. | ||
0,5L + 0,25L. | ||
0,25L. | ||
Итого. | ||
2.3. Тип руды — твердая (коэффициент крепости по М. Протодъяконову 16−17).
2.4. Схема дробления (рисунок 1).
На измельчение Рисунок 1.
3. РАСЧЕТ СХЕМЫ ДРОБЛЕНИЯ.
3.1. Число стадий дробления;
Число стадий дробления определяется размером максимального куска (Dmax, мм) в поступающей руде, номинальной крупностью дроблёного продукта (dн, мм) и заданной суточной производительностью фабрики (Qс, т/сут).
3.1.1. Часовая производительность цеха дробления;
Qч = (Qс· Kн·Kи)/t = (27 000· 1,0·1,1)/24 = 1237,5 т/ч; Kн=1,0 Kи=1,1.
где: Qч — часовая производительность цеха, т/ч; Qс — Производительность цеха дробления т/сут t — время работы цеха дробления, ч; Kи — коэффициент использования оборудования; Kн — коэффициент учитывающий не равномерность подачи сырья; tс — сутки Цех дробления работает в 3 стадии, 3 смены в сутки и 6 дней в неделю по 8 часов. Чистое время работы 24 часа в сутки.
3.2. Степень дробления.
Степень дробления (измельчения) называется отношение размеров зёрен исходного материала к размерам зёрен дроблёного (измельчённого) продукта.
Степень дробления (измельчения) i вычисляют по формуле:
i = Dcp/dcp,.
где Dcp и dcp — средневзвешенный диаметр зёрен исходного материала и дробленого продукта.
При ориентировочных определениях степени дробления в промышленности широко пользуются формулой:
i = Dmax/dmax = 750/15 = 50.
где Dmax и dmax — размер максимального куска материала соответственно до и после дробления.
3.3. Выбираем степень дробления по отдельным стадиям дробления.
iобщ= i1· i2·i3.
iср== icp =.
Где icр — средняя степень дробления для одной стадии. Учитывая большие размеры максимальных кусков исходной руды (Dmax = 750) предполагаем установку в I стадии крупноразмерных дробилок с большой шириной приемных отверстий. В этом случае можно ожидать запас по производительности, в связи с чем степень дробления в I и II стадии принимаем несколько меньшей, чем в стадии III.
3.3.1. Принимаем степени дробления:
i1 = 3,5 i2 = 3,5 i3 = 4.
iобщ= 3,5· 3,5·4=50.
3.4. Номинальная крупность дробленых продуктов по стадиям дробления:
мм мм мм.
3.5. Определяем ширину загрузочных щелей дробилок — В.
Ширина приемного отверстия (щели) должна быть на 1520% больше диаметра наибольшего куска материала, поступающего в дробилку, т. е.
В = (1,15? 1,20)· Dн;
Для I стадии В1 = 1,15 Dн = 1,15· 750 = 862,5 мм; Для II стадии В2 = 1,15· d5 = 1,15· 214,3 = 246,4 мм; Для III стадии В3 = 1,15· d9 = 1,15· 61,2 = 70,38 мм;
где В — ширина приемного отверстия дробилки, мм; DН — номинальная крупность руды в питании дробилки, мм;
3.6. Определяем ширину разгрузочных щелей дробилок — l.
l = d/Zщ, к ZIщ = 1,7 ZIk = 1,6 ZII = 2,4.
Для I стадии мм; Для I стадии мм; Для II стадии мм;
При работе дробилки в замкнутом цикле с грохотом ширина ее разгрузочной щели должна быть на 20 — 25% меньше размера отверстия сита грохота. В этом случае выход подрешетного продукта будет максимальным, а количество циркулирующего продукта минимальным.
3.6.1. Принимаем в III стадии:
l3 = d11•0,2 = 15−15•0,2 = 12 мм;
где l — ширина разгрузочной щели дробилки, мм (для щековых и конусных дробилок крупного дробления это размер в фазе раскрытия профилей, для конусных дробилок среднего и мелкого дробления — в фазе смыкания профилей) Zщ — коэффициент закрупнения щёковых дробилок; Zк — коэффициент закрупнения конусных дробилок Значения Z по стадиям дробления равны [3, стр. 41, табл. 2.12]:
3.7. По исходным данным, представленным в таблице 5, строим характеристику крупности исходной руды (рисунок 2).
Таблица 5 — Характеристика крупности продукта 1.
Классы крупности, мм. | Выход классов крупности. | |||
Частный, %. | Суммарный по «- «,%. | Суммарный по «+ «,%. | ||
750 +562,5. | ||||
562,5 +375. | ||||
375 +187,5. | ||||
187,5 +90. | ||||
Рисунок 2- Характеристика крупности продукта.
3.8. Определяем массу и выход продуктов 2, 3, 4 и 5.
Для расчета схемы дробления необходимо знать содержание класса минус d1, мм, т. е,, которое определяют по графику характеристики крупности исходной руды, (рисунок 2) построенному по данным таблицы 5. После этого приступаем к определению масс и выходов продуктов 2, 3, 4 и 5.
Qч = Q1 = 1237,5 Q2 = Q1· B1-a·E1 = 1237,5· 0,64·0,65 = 538,9 т/ч; Q3 = Q1-Q2 = 1237,5−539 = 698,5 т/ч; Q4 = Q3= 698,5 т/ч; Q5 = Q1= 1237,5 т/ч; 1 = 100%; 2 = Q2· 100/Q1= 538,9•100/1237,5 = 44%; 3 = 100-2 = 100−44 = 56%; 4 = 3 = 56%; 5 = 1 = 100%; Е1 = 0,65.
4. ВЫБОР И РАСЧЁТ ОБОРУДОВАНИЯ ДЛЯ I СТАДИИ ДРОБЛЕНИЯ.
4.1. Дробилки, которые подходят для установки в 1 стадии дробления (табл.6) подбираем по расчетным данным, представленным в таблице 7.
Таблица 6 — Варианты дробилок для 1 стадии дробления.
Марка дробилки. | Dmax. | Номинальная ширина разгрузочного отверстия, мм. | Пределы регулирования разгрузочного отверстия, мм. | Изменение производительности, м3/ч. | Мощность двигателя, кВт. | Масса дробилки, т. | |
ЩДП-1500×2100. | 135−225. | 450−750. | 250.2. | ||||
ККД-1200/150. | 130−180. | 560−800. | |||||
Таблица 7 — Расчетные данные для дробилок I стадии.
Показатели. | I стадия. | |
Размер загрузочного отверстия, В, мм. | 862,5. | |
Размер разгрузочной щели, l1щ, l1к мм. | 126, 134. | |
Наибольший размер куска в питании dmax, мм. | ||
4.2. Определяем производительность дробилок ЩДП-1500×2100 и.
ККД-1200/150.
м3/ч м3/ч где: Q0щ — производительность щёковой дробилки; Q0к — производительность щёковой дробилки; Dmax — размер максимального куска материала; Qmax - Qmin — lmax - lmin — паспортные данные дробилки;
4.2.1. Домножаем на насыпную плотность дн = 1,8 для перевода в т/ч получим:
746,7· 1,8 = 1344 т/ч 745,2· 1,8 = 1341 т/ч.
4.3. Далее определяем количество конусных и щековых дробилок.
(nщ, nк), необходимое для обеспечения заданной производительности.
nщ = Q3 / Q0щ = 710/1344 = 0,52 — 1 дробилка nк = Q3 / Q0к = 710/1341 = 0,53 — 1 дробилка.
4.4. Определяем коэффициенты загрузки дробилок коэффициент загрузки Кзщ = Q3/ Q0щ· nщ = 710/1344· 1=0,52 Кзк = Q3/ Q0к· nк = 710/1341· 1=0,53.
где: КЗ — коэффициент загрузки Q3 — количество подачи уды в дробилку (первая стадия) n1 — количество дробилок для первой стадии Q0щ — производительность щёковой дробилки Q0к — производительность щёковой дробилки Принимаем к установке в первой стадии дробления конусную дробилку ЩДП-1500×2100, т.к. у неё более низкое потребление энергии и более высокая производительность.
4.5. Перед первой стадией крупного дробления обычно устанавливают колосниковые грохоты. Количество грохотов должно быть равным числу дробилок, так как верхний класс колосникового грохота в дробилку поступает самотеком. Размеры колосникового грохота должны удовлетворять двум условиям: обеспечение требуемой производительности; обеспечение продвижения руды по грохоту самотеком.
Первое условие требует, чтобы площадь каждого колосникового грохота должна быть не меньше, определяемой по формуле:
Q1 = 1237,5 т/ч;
а = 214 мм;
n = 1;
м2;
где a ширина щели между колосниками грохота, мм; n количество дробилок, а следовательно и грохотов, шт.; Q1 производительность цеха дробления, т/ч; F площадь просеивающей поверхности грохота, м2.
4.6. Обычно площадь по расчету получается весьма малой, и размеры грохота назначаются конструктивно.
Второе условие требует, чтобы ширина грохота превышала диаметр максимального куска в материале в 23 раза. При такой ширине грохота исключается заклинивание руды и задержка продвижения материала по просеивающей поверхности грохота.
B = (2 3) Dmax = 3•750 = 2250 мм = 2,25 м2.
4.7. Длину грохота необходимо принимать в два раза больше ширины, L2B. В этом случае площадь грохота определится из выражения.
L = 2•2250 = 4500 мм = 4,5 м2;
4.8.Далее определяем вторую возможную площадь просевающей поверхности.
F = B•L = 2,25•4,5 = = 10 м2;
4.9. Из двух полученных значений площади грохота F к установке принимаем бoльшую величину. Т. к в первой стадии одна дробилка — принимаем к установке один колосниковой грохот: F = 10 м2.
5. ВЫБОР И РАСЧЕТ ОБОРУДОВАНИЯ ДЛЯ II СТАДИИ ДРОБЛЕНИЯ.
5.1. Для расчета второй стадии дробления необходимо знать характеристику крупности продукта, поступающего в неё. Гранулометрическая характеристика определяется аналитическим путем исходя из характеристик продуктов 2 и 3. Характеристика продукта 4 задана в таблице 8 и представлена на рисунке 3.
Таблица 8 — Характеристика крупности продукта 4.
Классы крупности в долях разгрузочного отверстия дробилки. l1 = 126 мм. | Выход классов крупности. | |||
Частный, %. | Суммарный по минусу «-»,%. | Суммарный по плюсу «+», %. | ||
+252. | ||||
— 252 +189. | ||||
— 189 +126. | ||||
— 126 +94,5. | ||||
— 94,5 +63. | ||||
— 63 +31,5. | ||||
— 31,5 +0. | ||||
Рисунок 3 -Характеристика крупности продукта 4.
5.2. В продукте 5 максимальным куском будет кусок размером 200 мм. Следовательно, в этом продукте присутствуют куски всех размеров от 200 до 0. Поэтому для определения характеристики крупности продукта 5 весь диапазон размеров от 300 до 0 разбиваем на классы крупности с учетом шкалы классификации. По данным графиков характеристик крупности продуктов 1 и 4 определяем кумулятивные содержания классов и, и эти значения записываем в графы 2 и 4 таблицы 9.
Таблица 9 — Расчет характеристики крупности продукта 5.
Классы крупности, мм. | Кумулятивные выходы или содержания классов по «минусу» в долях единицы. | Суммарные выходы по «плюсу» продукта 5, %. | |||||
Продукт 1. | Продукт 2. | Продукт 4. | Продукт 5. | ||||
доли. | %. | ||||||
0−200. | 0,67. | 1,0. | 0,97. | 1,0. | |||
0−155. | 0,60. | 0,9. | 0,92. | 0,91. | |||
0−110. | 0,50. | 0,75. | 0,7. | 0,72. | |||
0−65. | 0,3. | 0,45. | 0,4. | 0,42. | |||
0−20. | 0,1. | 0,14. | 0,2. | 0,17. | |||
d5 a1 < l1щ.
a1 = 200 мм Значения определяют по формуле.
0.
где E1 эффективность грохочения колосникового грохота в долях единицы; Q2 масса продукта 2, т/ч.
5.2.1 Определяем содержание искомых классов в продукте 5 по формуле:
Q3 = Q4 = Q1-Q2 = 1237,5−538,9= 710,6.
Q5 = Q1 = 1237,5.
В графу 6 таблицы 10 занесены выходы продукта 5 в процентах. Графа 7 дает кумулятивную характеристику по «плюсу» этого же продукта. После построения характеристики крупности продукта 5.
5.2.2. Строим характеристику крупности продукта 5 (рисунок 4).
Рисунок 4 — Характеристика крупности продукта 5.
5.3. Определяем массу и выход продуктов 6, 7, 8.
Е2 = 0,8?0,85 1237,5· 0,4·0,8 = 396 т/ч; Q7 = Q5-Q6 = 1237,5−396 = 841,5 т/ч; Q8 = Q7 = 841,5 т/ч; 6 = Q6100/Q5 = (396· 100)/1237,5 = 32%; 7 = 100-6 = 100−32 = 68%; 8 = 7 = 68%; 9 = 5 = 100%:
Где содержание класса d2 в продукте 5 в долях единицы; Е2 эффективность грохочения грохота перед второй стадией дробления в долях единицы, для вибрационных грохотов Е2 = 0,8?0,85; Q6, Q7, Q8, Q9 — массовые выхода продуктов 6, 7, 8, 9, т/ч; 5, 6, 7, 8, 9 — выходы продуктов 5, 6, 7, 8, 9, %. Значение в5-d2 определяется из характеристики продукта 5.
5.4 Варианты дробилок во 2 стадии приведены в таблице 10, а параметры дробилок, удовлетворяющие выбранным вариантам в таблице 11;
Типы дробилок. | Ширина приёмной щели (B). | Наибольший размер куска в питании, мм. | Диаметр основания дробящего конуса, мм. | Размер разгрузочной щели, мм. | Производительность, м3/час. | Мощность двигателя, кВт. | Масса дробилки, т. | |
Таблица 10 — Варианты дробилок для 2 стадии.
КСД-1750-Гр | 25−60. | 170−320. | 50.1. | |||||
КСД-2200-Гр | 30−60. | 360−610. | 89.6. | |||||
Таблица 11 — Требования к дробилкам II стадии.
Показатели. | II стадия. | |
Размер загрузочного отверстия, В, мм. | ||
Размер разгрузочной щели,, мм. | ||
Наибольший размер куска в питании, мм. | ||
5.4.1. Расчет производительности дробилок КСД-1750-Гр и.
КСД-2200-Гр:
Расчет дробилки КСД-2200-Гр:
м3/ч Расчет дробилки КСД-1750Гр:
м3/ч где Qmax — максимальная производительность при максимальной паспортной ширине разгрузочной щели, м3/ч; Qmin — минимальная производительность при минимальной паспортной ширине разгрузочной щели, м3/ч; - максимальная паспортная ширина разгрузочной щели, мм; - минимальная паспортная ширина разгрузочной щели, мм; 2 — расчетная ширина разгрузочной щели, мм.
5.4.2. Домножаем на насыпную плотность дн = 1,8 для перевода в т/ч получим:
КСД-2200-Гр
610· 1,8 = 1098 т/ч КСД-1750-Гр
320· 1,8 = 576 т/ч.
5.4.3. Определяем необходимое количество дробилок, для обеспечения заданной производительности:
Расчет дробилки КСД-2200-Гр:
= 1 дробилки.
Расчет дробилки КСД-1750-Гр:
= 2 дробилки где Q2к производительность конусной дробилки, т/ч;
5.4.3. Определяем коэффициент загрузки Расчет дробилки КСД-1750-Гр:
— так как коэффициент загрузки больше 0,85 то берём ещё одну дробилку получим:
Расчет дробилки КСД-2200Гр:
5.4.4. Принимаем к установке во второй стадии 1 дробилку КСД-2200-Гр, так как у неё большая производительность следовательно меньшее число дробило к установке.
5.5. В соответствии со схемой, на грохочение поступает продукт после I стадии дробления в количестве 100%. Размер отверстий сита грохота принимается равным номинальному размеру дробленого продукта II стадии дробления, т. е. 60 мм.
5.6.В стадиях среднего и мелкого дробления к установке принимаются вибрационные грохоты тяжелого типа. Необходимая площадь грохочения, которых рассчитывается по формуле:
d9 a2 < l2 = 60 мм м2;
где: q удельная производительность грохота, м3/(чм2) [2, с. 94; 3, с. 62; 4, с. 68]; дн, K, L, M, N, O, P поправочные коэффициенты, определяемые из данных, приведенных в литературе [2 с. 95; 3, с. 63; 4, с. 69]. Значение коэффициента М для эффективности грохочения 85% составит.
M = 1.35. Значения коэффициентов N, O, P принимаются равными 1,0.
q0 =42 м3/м2· ч К= 0,6.
L =1,55.
5.6.1. По таблицам, приведенным в литературе 2, прил. 47; 3, прил. 24; 4, прил. 13 подбирают подходящий условиям грохот и рабочую площадь просеивающей поверхности. Для второй стадии грохочения предпочтительно ставить грохоты тяжелого типа, которые принимают крупные куски.
Количество грохотов n для второй стадии дробления определяют из отношения площадей шт где f площадь просеивающей поверхности выбранного грохота, м2. Во второй стадии дробления желательно иметь по одному грохоту на дробилку, это облегчает конструктивное решение узла «грохот-дробилка».
5.6.2. Принимаем к установке грохот ГИТ-61А = 8 м2 в количестве 3 штук.
5.7. К установке во II стадии принимаем:
1 дробилку КСД-2200-Гр; 2 тяжёлых инерционных грохота ГИТ-61А м2.
6. ВЫБОР И РАСЧЕТ ОБОРУДОВАНИЯ ДЛЯ III СТАДИИ ДРОБЛЕНИЯ.
6.1. Диаметр отверстия грохотов перед дробилками мелкого дробления и ширину разгрузочной щели дробилки принимают равными диаметру максимального куска в питании мельницы: а3=15 мм.
6.2. Все избыточные куски руды будут отсеяны на грохоте поверочного грохочения и возвращены в дробилку. Для мелкого дробления твердых и средней твердости руд применяют конусные дробилки мелкого дробления 2, прил. 12; 3, прил. 10; 4, прил. 9. Дробилки выбирают по ширине загрузочного отверстия и по производительности при заданной ширине выходной щели.
В третьей стадии дробилка работает в замкнутом цикле с поверочным грохочением, поэтому ее выбор осуществляется по тоннажу вновь поступающего в нее продукта величиной Q12, т. е. по верхнему классу, отсеивающемуся на грохоте от продукта 9. Продукт 13 (Q13)? циркулирующая нагрузка дробилки? поступает в ту же дробилку, что и продукт величиной Q12. В сумме Q12 и Q13 составляют продукт 12, фактически поступающий в дробилку третьей стадии дробления. Но при выборе дробилки в расчет не принимается, так как производительность для конусных дробилок мелкого дробления дана в каталогах с учетом циркулирующей нагрузки.
6.3. Величину продукта Q12 определяем по формуле где? содержание класса? d3 (подрешетный продукт) в продукте 9, в долях единицы; E3? эффективность грохочения в третьей стадии дробления, в долях единицы, для вибрационных грохотов Е3 = 0,85.
6.3. Для определения содержания необходимо знать характеристику крупности продукта 9. Для получения этой характеристики необходимо сложить характеристики продуктов 6 и 8.
Характеристику продукта 8 строим по данным табл. 12.
Характеристику крупности продукта 6 определяют как характеристику крупности подрешетного продукта, отсеянного от продукта 5 на грохоте с диаметром отверстий 60 мм (аналогично расчетам при определении продукта 2, табл. 8.).
Таблица 12 — Характеристика крупности продукта 8.
Классы крупности в долях разгрузочного отверстия дробилки. l 2 =31 мм. | Выход классов крупности. | |||
Частный, %. | Суммарный по минусу «-»,%. | Суммарный по плюсу «+»,%. | ||
+62,5. | ||||
— 62,5+47. | ||||
— 47+31,25. | ||||
— 31,5+23. | ||||
— 23+16. | ||||
— 16+8. | ||||
— 8. | ||||
Рисунок 5 — Характеристика крупности продукта.
6.4. Расчет характеристики крупности продукта 9 производим так же, как для продукта 5. Данные заносим в таблицу 13.
Таблица 13 — Расчет характеристики продукта 9.
Классы крупности, мм. | Содержания классов по «минусу» в долях единицы. | ||||||
Продукт. | Продукт. | Продукт. | Продукт 9. | ||||
доли. | %. | ||||||
— 60. | 0,4. | 1,0. | 0,99. | 1,0. | |||
0−44. | 0,3. | 0,75. | 0,96. | 0,89. | |||
0−30. | 0,22. | 0,55. | 0,92. | 0,80. | |||
0−16. | 0,15. | 0,37. | 0,85. | 0,69. | |||
0−2. | 0,03. | 0,07. | 0,55. | 0,39. | |||
d9 a2 < l2.
a2 = 60.
Для заполнения графы 3 таблицы 11 определяем содержание искомых классов в продукте 9 по формуле:
6.5. Определяем содержание искомых классов в продукте 9 по формуле:
Рисунок 6 -Характеристика крупности продукта 9.
6.6. Определяем массу и выход продуктов 9, 10, 13.
Q9 = Q5 = Q1 = 1237,5 т/ч; Q10 = Q9+Q13 = 1237,5+882 = 2119,5 т/ч; 9 = 100%;
г 10 = г9+г13 = 171%; ;
6.7. Далее определяем величину продукта Q12:
= 1237,5 (1−0,85· 0,68)= 522 т/ч.
6.8. Определяем количество руды, Q10, поступающей на грохочение.
Для этого построим характеристику крупности дробленой руды в третьей стадии дробления, продукт 13. Для определения характеристики крупности продукта 10 суммируют характеристики продуктов 9 и 13. Все данные заносим в таблицу 14.
Таблица 14 — Характеристика крупности продукта 13.
Классы крупности в. долях разгрузочного отверстия дробилки. l3 = 15 мм. | Выход классов крупности. | |||
Частный, %. | Суммарный по минусу «-»,%. | Суммарный по плюсу «+»,%. | ||
+30. | ||||
— 30 +22,5. | ||||
— 22,5 +15. | ||||
— 15+11,25. | ||||
— 11,25+7,5. | ||||
— 7,5+3,75. | ||||
— 3,75. | ||||
Рисунок 7 -Характеристика крупности продукта 13.
где содержание класса меньше 10 мм (кумулятивные выходы по «минусу») в продуктах 9, 10, 13 соответственно, в долях единицы.
=0,31 a3 = d11 = 15.
Характеристика крупности продукта 10 приведена в таблице 15.
Таблица 15 — Характеристика крупности продукта 10.
Классы крупности, мм. | Кумулятивные выходы или содержания классов по «минусу» в долях единицы. | |||||
Продукт. | Продукт. | Продукт 10 ,. доли. | Продукт 10,. %. | Суммарные выходы по «плюсу» продукта 10, %. | ||
0−15. | 0,68. | 0,80. | 0,58. | |||
0−12,5. | 0,61. | 0,69. | 0,46. | |||
0−10. | 0,59. | 0,60. | 0,38. | |||
0−7,5. | 0,54. | 0,52. | 0,27. | |||
0−5. | 0,48. | 0,40. | 0,16. | |||
Рисунок 8 -Характеристика крупности продукта 10.
6.9. По каталогу выбираем технологически возможные к установке в третьей стадии дробилки (таблица 16), требования к дробилкам приведены в таблице 17. Далее определяем производительность выбранной дробилки, обеспечивающие прием кусков руды.
Таблица 16 — Характеристика дробилок 3 стадии.
Типоразмер дробилок. | Ширина приемной щели (В), мм. | Наибольший размер куска в питании, мм. | Размер разгрузочной щели, мм. | Производительность, м3/час. | Мощность двигателя, кВт. | Масса дробилки, т. | |
КМД-1750-Т. | 5−15. | 85−110. | 47.8. | ||||
КМД-2200-Т. | 10−20. | 220−260. | 87.7. | ||||
Таблица 17 — Требования к дробилкам III стадии.
Показатели. | III стадия. | |
Размер загрузочного отверстия, В, мм. | ||
Размер разгрузочной щели, l3, мм. | ||
Наибольший размер куска в питании, мм. | ||
6.10. Определяем производительность дробилки КМД-2200-Т.
м3/ч.
6.11. Определяем производительность дробилки КМД-1750-Т.
м3/ч.
6.11.1. Домножаем на насыпную плотность дн = 1,8 для перевода в т/ч получим:
КМД-2200-Т.
220· 1,8 = 396 т/ч КМД-1750-Т.
110· 1,8 = 198 т/ч.
6.12. Определяем необходимое количество дробилок, для обеспечения заданной производительности: n = Q12/Qр.
Q12 = Q13 = 1237,5 т/ч.
n1 = 1237,5/396 = 3,1 = 4 дробилки.
n2 = 1237,5/110 = 6,25 = 7 дробилок.
6.13. Определяем коэффициент загрузки.
Кз,= Q12/Qр,· n = 1237,5/396· 4 = 0,78.
Кз,= Q12/Qр,· n = 1237,5/198· 7 = 0,87.
— так как коэффициент загрузки больше 0,85 то берём ещё одну дробилку получим: Кз,= Q12/Qр,· n = 1237,5/198· 8 = 0,78 Принимаем к установке в третьей стадии 8 дробилок.
6.14. Выбираем КМД-2200-Т так как она с большей производительностью, следовательно с меньшем количеством дробилок.
6.15. Расчет грохотов в третьей стадии дробления осуществляется аналогично расчету второй стадии дробления. При расчете необходимой площади грохочения в третьей стадии необходимо значения удельной производительности грохота и коэффициентов (, K, L, M, N, O, P), входящих в формулу, выбирать в зависимости от характеристики крупности продукта 10 согласно данным, приведенным в литературе [2, с. 9495; 3, с. 6263; 4, с. 6869].
6.16. Число грохотов в третьей стадии дробления может достигать 34 на дробилку, но при этом приходится перед грохотами проектировать распределительные бункеры.
6.17. Необходимая площадь грохочения рассчитывается по формуле:
м2.
Значение коэффициента М для эффективности грохочения 85% составит M = 1.2.
Значения коэффициентов N, O, P принимаются равными — 1,0.
q0 =24 м3/м2· ч К=0,6.
L =1,55.
6.18. Количество грохотов n для второй стадии дробления определяют из отношения площадей:
шт;
где f площадь просеивающей поверхности выбранного грохота, м2.
6.19. Принимаем к установке 8 грохотов типа ГИТ-32Н с площадью сита 3,12 м2.
6.20. К установке в III стадии принимаем:
4 дробилок КМД-2200-Т; 8 инерционных грохотов ГИТ-32Н = 3,2 м2.
руда подготовка дробление.
ЗАКЛЮЧЕНИЕ
.
7.1. При выполнении курсового проекта углубил, закрепил и обобщил знания, полученные на уроках дисциплины «Обогащение полезных ископаемых».
7.2. Приобрел навыки работы с технической литературой, справочниками и государственными стандартами.
7.3. Разработав проект цеха рудоподготовки производительности цеха 27 000 т/сутки, и заданных условий принял:
Ш — на первой стадии установку одного неподвижного колосникового грохота: 2250×4500 и одной дробилки типа: ЩДП-1500×2100;
Ш — во второй стадии грохочения выбрала инерционный грохот ГИТ-61А 2000×4000 в количестве 2 штук и 1 дробилки КСД-2200-Гр;
Ш — в третьей стадии грохочения приняла 8 инерционных грохотов ГИТ-32Н 1250×2500 и 4 дробилок КМД-2200-Т.
СПИСОК ИСПОЛЬЗОВАННЫХ ИСТОЧНИКОВ
.
1. Андреев, С. Е. Дробление, измельчение и грохочение полезных ископаемых: учеб. для вузов / С. Е. Андреев, В. М. Зверевич, В. А. Перов. 3-е изд., перераб. и доп. М.: Недра, 1980. 415 с.
2 Евменова, Г. Л. Дробление, измельчение и подготовка сырья к обогащению: пособие по курсовому проектированию: учеб. пособие / Г. Л. Евменова, Г. В. Иванов, А. А. Байченко; ГУ КузГТУ. — Кемерово, 2005. 96 с.
3. Перов, В. А. Дробление, измельчение и грохочение полезных ископаемых: учеб. пособие для вузов / В. А. Перов, С. Е. Андреев, Л. Ф. Биленко. 4-е изд., перераб. и доп. М.: Недра, 1990. 301 с.
4. Разумов, К. А. Проектирование обогатительных фабрик: учеб. для вузов / К. А. Разумов, В. А. Перов.? 4-е изд., перераб. и доп.? М.: Недра, 1982. — 518 с.
5. Справочник по обогащению руд. Подготовительные процессы / под ред. О. С. Богданова, В. А. Олевского. 3-е изд., перераб. и доп. М.: Недра, 1982. 366 с.
6. Шилаев, В. П. Основы обогащения полезных ископаемых: учеб. пособие для вузов / В. П. Шилаев.? М.: Недра, 1986.? 296 с.
ПРИЛОЖЕНИЕ 1.
Спецификация основного оборудования цеха рудоподготовки.
Наименование оборудования. | Тип. | Количество, шт. | Масса. единицы, т. | Установочная. мощность, кВт. | ||
единицы. | Всего. | |||||
Грохот колосниковый. | 2250×4500. | ; | ; | ; | ||
Щековая дробилка. | ЩДП-1500×2100. | |||||
Инерционный грохот. | ГИТ-61А 2000×4000. | 8.16. | ||||
Конусная дробилка среднего дробления. | КСД-2200-Гр | 89,6. | ||||
Инерционный грохот. | ГИТ-61 2000×4000. | 8.16. | ||||
Конусная дробилка мелкого дробления. | КМД-2200-Т. | 87,9. | ||||
Инерционный грохот. | ГИТ-32Н 1250×2500. | 5.25. | ||||
ПРИЛОЖЕНИЕ 2.