Экологические особенности свинцово-кислотных аккумуляторных батарей
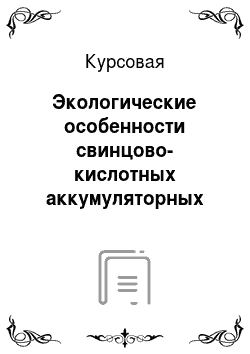
Аккумуляторные батареи с отдельными крышками (рис. 1) собирают в одном многоячеечном корпусе — моноблоке (2), выполненном из эбонита или другой кислотостойкой пластмассы, разделенном перегородками (16) на отдельные камеры-ячейки (банки), по числу аккумуляторов в батарее. В каждую из ячеек помещен блок, состоящий из чередующихся положительных (5) и отрицательных (3) электродов, разделенных… Читать ещё >
Экологические особенности свинцово-кислотных аккумуляторных батарей (реферат, курсовая, диплом, контрольная)
Свинцово-кислотные аккумуляторы и батареи, собранные из них, являются очень распространёнными вторичными источниками тока и применяются в различных областях техники. Они обладают относительно высокими электрическими характеристиками на единицу веса и объёма.
Положительными качествами свинцово-кислотных аккумуляторов по сравнению со щелочными, являются высокие допустимые разрядные токи и низкий саморазряд. Это определило их широкое применение на транспорте, в качестве стартерных, тяговых и буферных аккумуляторов, в связи и энергоснабжении, в качестве аварийного и буферного источника тока.
ГЛАВА 1. ТЕХНОЛОГИЯ ПРОИЗВОДСТВА АККУМУЛЯТОРНЫХ БАТАРЕЙ
Свинцово-кислотные аккумуляторы и батареи, собранные из них, являются очень распространёнными вторичными источниками тока и применяются в различных областях техники. Они обладают относительно высокими электрическими характеристиками на единицу веса и объёма.
Положительными качествами свинцово-кислотных аккумуляторов по сравнению со щелочными, являются высокие допустимые разрядные токи и низкий саморазряд. Это определило их широкое применение на транспорте, в качестве стартерных, тяговых и буферных аккумуляторов, в связи и энергоснабжении, в качестве аварийного и буферного источника тока.
Конструкция и работа стартерных аккумуляторных батарей
В аккумуляторной батарее электрическая энергия, поступающая в процессе её заряда от внешнего источника постоянного тока, превращается в химическую и в этом виде может быть запасена, а в процессе разряда — вновь преобразуется в электрическую энергию. Автотракторные аккумуляторные батареи называют стартерными, так как при малом внутреннем падении напряжения они обладают свойством кратковременно отдавать ток большой силы, необходимый для работы стартера при запуске двигателя.
Основными составными частями кислотных АКБ являются положительные и отрицательные пластины (электроды), соединённые перемычками в полублоки и блоки, сепараторы, моноблоки (банки), крышки и электролит.
Батареи обычно собирают в пластмассовом сосуде — моноблоке. Пластина каждой полярности состоит из активной массы и решетки, которая служит токоотводом и удерживает активную массу.
Положительные пластины имеют тёмно-коричневый цвет (двуокись свинца), а отрицательные (губчатый свинец) — светло-серый.
Сепараторы, проложенные между пластинами, служат для предотвращения замыкания разноимённых пластин и представляют собой тонкие листы из пористого кислотостойкого материала.
Блок пластин, составленный из полублоков положительных и отрицательных пластин, помещённый в ячейку моноблока, представляет собой отдельный аккумулятор батареи.
Схема производства аккумуляторных батарей и комплектующих
Производство свинцово-кислотных аккумуляторных батарей относят к области относительно сложных производств, когда качество конечной продукции в значительной мере зависит как от качества исходных материалов, так и от соблюдения технологических режимов в процессе их переработки и сборки комплектующих. Производство можно разбить на два основных передела, каждый из которых заканчивается выпуском готовой продукции — производство электродов и сборка батарей.
Аккумуляторное производство можно разворачивать поэтапно, начав с производства пластин. В этом случае реализуемой продукцией являются электроды, ремкомплекты (электрод с сепаратором) или комплекты для сборки батарей (электроды, сепараторы, корпуса и крышки). Можно также собирать аккумуляторы в эбонитовых моноблоках, учитывая малую стоимость оборудования для их сборки. Следующим этапом является сборка малоуходных АКБ с общей крышкой. Возможны также варианты формировки пластин в ваннах или в самих аккумуляторах.
Финансовые затраты на организацию сборочного или полного производства зависят от объема выпуска и степени механизации и автоматизации процессов и могут колебаться от 5 до 500 тыс. $. Для расчета предложения по началу выпуска батарей необходимы следующие данные: вид батареи — с общей или с ячеистой крышкой; номенклатура; объемы производства по номенклатуре. Перечень оборудования и исполнение по степени механизации оговаривается с заказчиком. Дополнительно для сборки также необходимы исходные данные по комплектующих и КД на батарею (может быть разработана нами).
Для производства электродов используется сурьмянистый, малосурьмянистый, кальциевый и другие сплавы свинца и чистый свинец марок от С3 до СО. Кроме этого при производстве необходимы аккумуляторная кислота, полипропиленовое волокно, органические добавки, дистилированная вода и газ для пайки. При сборке батарей, в зависимости от их типа используются эбонитовые и полиэтиленовые детали корпуса, электроды, токоведущие детали, сепараторы и мастика либо полипропиленовый моноблок с общей крышкой, электроды и сепараторы и токоведущие детали.
Для производства электродов основным оборудованием являются — литейные автоматы для токоотводов (решеток), мельницы помола свинца для получения порошка, смесители и намазочные машины. При сборке батарей с общей крышкой все операции производятся вручную и оборудование значительно дешевле, чем для сборки батарей с общей крышкой, где необходима большая степень механизации и возможна полная автоматизация процесса сборки и контроля качества. Оборудование производится с адаптацией под заказчика, под его батарею. Оборудование для сборки производится в трех исполнениях по степени механизации — пост (простое оборудование, где позиционирование батареи и подвод инструмента осуществляется вручную); установка (вручную подается батарея, подача инструмента механизирована); автомат (все операции автоматизированы). Ряд автоматов может быть смонтировано в линию, снабженную системой управления. Принципиально все операции и транспорт могут быть автоматизированы, целесообразность этого определяет заказчик.
ГЛАВА 2. ОСНОВНЫЕ ХАРАКТЕРИСТИКИ ПРОМЫШЛЕННО ВЫПУСКАЕМЫХ ВТОРИЧНЫХ ХИТ (АККУМУЛЯТОРОВ)
Реагентами в свинцовых аккумуляторах служат диоксид свинца (РЬ02) и свинец (РЬ), электролитом — раствор серной кислоты. Они называются также свинцово-кислотными аккумуляторами. Их подразделяют на четыре основные группы: стартерные, стационарные, тяговые и портативные (герметизированные) (см. табл. 4.1.2). Наиболее распространенные из них стартерные аккумуляторы предназначены для запуска двигателей внутреннего сгорания и энергообеспечения приборов различных машин. Они характеризуются невысокой стоимостью, горизонтальной разрядной кривой, способностью разряда с высокими скоростями, при низких температурах (до -40°С), могут постоянно подзаряжаться при стабилизированном напряжении. Выпускаются АБ призматической конструкции емкостью 30—200 А * ч (при разряде нормированным током 0,05С). В последние годы в основном применяются аккумуляторы, не требующие ухода (далее используется термин «безуходные»). К недостаткам относят невысокие удельную энергию и наработку, плохую сохраняемость заряда, выделение водорода.
Стационарные аккумуляторы применяются в энергетике, на телефонных станциях, в телекоммуникационных системах, в качестве аварийного источника тока и т. п. Обычно они работают в режиме постоянного подзаряда. Относятся к дешевым аккумуляторам. Выпускаются АБ емкостью 5—400 А * ч. Недостатки стационарных АБ аналогичны недостаткам стартерных АБ.
Тяговые аккумуляторы предназначены для энергоснабжения электрокар, подъемников, шахтных электровозов, электромобилей и других машин. Работают в режимах глубокого разряда, имеют высокий ресурс и низкую стоимость. Выпускаются АБ емкостью 45—200 А * ч.
Портативные (герметизированные) свинцовые аккумуляторы применяются для питания приборов, инструмента, аварийного освещения. Выпускаются аккумуляторы и АБ призматической (1—30 А * ч) и цилиндрической (2,5—25 А * ч) конструкций. К их достоинствам относятся более низкая стоимость по сравнению со стоимостью других портативных ХИТ, широкий рабочий температурный диапазон, работа в любом положении. Недостатками ХИТ являются невозможность хранения в разряженном состоянии, трудность производства аккумуляторов малых размеров. По сравнению с НК-аккумуляторами портативные свинцовые аккумуляторы имеют несколько меньший ресурс.
Ннкель-кадмиевые (НК) аккумуляторы и АБ. Реагентами в НК-аккумуляторах служат гидроксид никеля и кадмий, электролитом — раствор КОН, поэтому они называются щелочными аккумуляторами. Имеются три основных вида НК-аккумуляторов: негерметичные с ламельными (ламельные аккумуляторы) и спеченными электродами (безламельные аккумуляторы) и герметичные (см. табл. 4.1.2). Наиболее дешевые ламельные НК-аккумуляторы характеризуются плоской разрядной кривой, высокими ресурсом и прочностью, но не высокой удельной энергией. Удельная энергия, скорость разряда аккумуляторов со спеченными электродами выше, они работоспособны при низких температурах, но дороже, характеризуются эффектом «памяти» и способностью к тепловому разгону. Негерметичные аккумуляторы и АБ выпускаются призматической формы емкостью 5—1300 А «ч (ламельные) и 10—100 А * ч (безламель-ные). Применяются для питания шахтных электровозов, подъемников, стационарного оборудования, средств связи и электронных приборов, для запуска дизелей и авиационных двигателей и др. Герметичные аккумуляторы характеризуются горизонтальной разрядной кривой, высокими скоростями разряда и способностью работать при низких температурах, но они дороже герметизированных свинцовых аккумуляторов и характеризуются эффектом «памяти». Выпускаются цилиндрической (до 10 А * ч), дисковой (до 0,5 А * ч) и призматической форм. Применяются для питания портативной аппаратуры (сотовых телефонов, магнитофонов, компьютеров и др.), бытовых приборов, игрушек и т. п. Недостатком НК-аккумуляторов является применение токсичного кадмия.
Никель-железные (НЖ) аккумуляторы и АБ. Вместо кадмия в этих аккумуляторах применяется железо. Из-за выделения водорода с самого начала заряда аккумуляторы выпускаются только в негерметичном варианте. Они дешевле НК-аккумуляторов, не содержат токсичный кадмий, имеют длительный срок службы и высокую механическую прочность. Однако они характеризуются большим саморазрядом, низкой отдачей по энергии, практически неработоспособны при температуре ниже -10°С (см. табл. 4.1.2). Выпускаются в призматическом виде и применяются в основном как тяговые источники тока в шахтных электровозах, электрокарах и промышленных подъемниках.
Никель-металлогидридные (НМ) аккумуляторы и АБ. Активным материалом отрицательного электрода является интерметаллид, обратимо сорбирующий водород, т. е. фактически отрицательный электрод является водородным электродом, у которого восстановленная форма водорода находится в абсорбированном состоянии. Разрядная кривая этого аккумулятора аналогична кривой НК-аккумулятора. Удельная емкость и энергия НМ-аккумуляторов в 1,5—2 раза выше удельной энергии НК-аккумуляторов (см. табл. 4.1.2), кроме того, они не содержат токсичный кадмий. Выпускаются в герметичном исполнении цилиндрической, призматической и дисковой форм. Применяются для питания портативных приборов и аппаратуры.
Никель-цинковые (НЦ) аккумуляторы и АБ. Это щелочные аккумуляторы, у которых отрицательный электрод — цинковый. Удельная энергия этих аккумуляторов примерно в 2 раза выше удельной энергии НК-аккумуляторов. Они характеризуются горизонтальной разрядной кривой, высокой удельной мощностью и относительно невысокой начальной стоимостью, однако ресурс их невелик (см. табл. 4.1.2), поэтому массового применения не имеют. Используются для питания портативной аппаратуры, рассматривается возможность применения в электромобилях.
Серебряно-цинковые (СЦ) и серебряно-кадмиевые (СК) аккумуляторы и АБ.
Активными материалами служат оксид серебра на положительном и цинк или кадмий — на отрицательном электродах соответственно, электролитом является раствор щелочи. Характеризуются высокими удельными энергиями и мощностью, низким саморазрядом (см. табл. 4.1.2), но очень дороги. Серебряно-цинковые аккумуляторы имеют небольшой ресурс. Выпускаются в призматической и дисковой формах, используются для питания портативных приборов и аппаратов, в космосе и в военной технике.
Никель-водородные (НВ) аккумуляторы и АБ. Отрицательным электродом является пористый газодиффузионный электрод с платиновым катализатором, на котором обратимо реагирует газообразный водород. Характеризуются высокой удельной энергией и очень высоким ресурсом (см. табл. 4.1.2), но значительным саморазрядом и очень дороги. Применяются в космической технике.
Литий-ионные аккумуляторы и АБ. В качестве отрицательного электрода используется углеродистый материал, в который обратимо внедряются ионы лития. Активным материалом положительного электрода обычно служит оксид кобальта, в который обратимо внедряются ионы лития. Электролитом является раствор соли лития в неводном апротонном растворителе. Аккумуляторы имеют большую удельную энергию, высокий ресурс и способны работать при низких температурах (см. табл. 4.1.2). К недостаткам можно отнести высокую стоимость, наклонную разрядную кривую и относительно большой саморазряд. Благодаря высокой удельной энергии их производство в последние годы резко возросло. Выпускаются в виде цилиндрической и призматической форм. Они применяются в сотовых телефонах, ноутбуках и других портативных устройствах.
Литий-полимерные аккумуляторы. Анодом служит либо углеродистый материал, в который обратимо внедряются ионы лития, либо металлический литий. Активными материалами положительных электродов являются оксиды ванадия, кобальта или марганца. Электролитом служит либо раствор соли лития в неводных апротонных растворителях, заключенный в микропористую полимерную матрицу, либо полимер (полиакрилонитрил, полиметилметакрилат, поливинилхлорид или другие), пластифицированный раствором соли лития в апротонном растворителе (гель-полимерный электролит). По сравнению с литий-ионными аккумуляторами литий-полимерные аккумуляторы имеют более высокие удельную энергию и ресурс и лучшую безопасность. Применяются для питания портативных электронных устройств.
Перезаряжаемые марганцсво-цииковые (МЦ) ХИТ. Первичные цилиндрические МЦ-ХИТ с щелочным электролитом определенного состава, изготовленные по специальной технологии, могут электрически перезаряжаться. Они характеризуются высокой удельной энергией, малым саморазрядом (см. табл. 4.1.2) и невысокой стоимостью, выпускаются в герметичном исполнении, однако имеют очень малый ресурс (до 25—50 циклов), небольшую скорость разряда и наклонную разрядную кривую. Выпускаются ХИТ типоразмеров R03, R6, R14 и R20. Применяются для питания фонарей, электрических приборов, игрушек и других устройств.
Назначение и устройство автомобильных аккумуляторов и аккумуляторных батарей
o Что такое АКБ?
o Виды АКБ, продаваемые в России
Что такое АКБ?
Что там внутри? Да все то же самое, что и раньше, поскольку принципиально конструкция аккумуляторов остается неизменной с незапамятных времен: свинцовые пластины и кислота.
Стандартный автомобильный аккумулятор состоит из шести 2-вольтовых элементов, что дает на выходе 12 вольт. Каждый элемент состоит из свинцовых решетчатых пластин, покрытых активным веществом и погруженных в кислотный электролит.
Отрицательные пластины покрыты мелкопористым свинцом, а положительные двуокисью свинца. Когда к аккумулятору подключают нагрузку, активное вещество вступает в химическую реакцию с сернокислотным электролитом, вырабатывая электрический ток. На пластинах при этом осаждается сульфат свинца, и электролит, соответственно, истощается. При зарядке эта реакция проходит в обратном направлении, и способность аккумулятора давать ток восстанавливается.
Автомобильный аккумулятор выполняет три функции: во-первых, он запускает двигатель, во-вторых, питает некоторые электрические устройства, например, сигнализацию и телефон, когда двигатель не работает. И, наконец, он «помогает» генератору, когда тот не справляется с нагрузкой.
Аккумулятор обычно соседствует с двигателем. А как раз высокой температуры этот агрегат не переносит. Законы, ограничивающие уровень шума, заставляют производителей все тщательнее затыкать любые отверстия в отсеке двигателя, что приводит к повышению температуры в моторном отсеке. На сегодняшний день это, пожалуй, самая большая проблема для производителей аккумуляторов.
Ведь верхний предел рабочей температуры этих устройств — 100 градусов С, дальше электролит просто закипает. Но даже если температура и не достигает рокового предела, а только к нему приближается, срок службы батарей все равно снижается в три-четыре раза.
Свинцовая стартерная аккумуляторная батарея (АКБ) — вторичный источник электрической энергии. Это значит, что после глубокого разряда ее работоспособность можно полностью восстановить при помощи заряда — пропускания электрического тока в направлении, обратному тому, в котором протекал ток при разряде.
Работает АКБ по принципу превращения электрической энергии в химическую (при заряде) и обратном превращении — химической энергии в электрическую (при разряде). Активные вещества заряженного свинцового аккумулятора, принимающие участие в токообразующем процессе:
· на положительном электроде — двуокись свинца темно-коричневого цвета;
· на отрицательном электроде — губчатый свинец серого цвета.
Электролит — водный раствор серной кислоты плотностью 1,28 г/смі, который, как и активная масса электродов, принимает участие в токообразующем процессе.
В процессе разряда активная масса как положительного, так и отрицательного электродов превращается в сульфат свинца (белого цвета). Поэтому теория, описывающая химические процессы, протекающие при заряде и разряде свинцового аккумулятора, называется теорией двойной сульфатации. При этом плотность электролита снижется к концу разряда до 1,08−1,10 г/смі.
Сегодня наиболее распространены автомобильные АКБ номинальным напряжением 12 В. Их емкость составляет от 36 до 190 А· ч.
Основы традиционного исполнения батарей сформировались уже в начале 20-го века и постепенно трансформировались до современного состояния по мере появления новых конструкционных материалов, но их эксплуатационные недостатки при этом сохранились.
В России батареи традиционного исполнения выпускают как в моноблоках с отдельными крышками, герметизируемыми битумной смазкой, так и в моноблоках с общей крышкой, герметизируемой контактно-тепловой сваркой.
Аккумуляторные батареи с отдельными крышками (рис. 1) собирают в одном многоячеечном корпусе — моноблоке (2), выполненном из эбонита или другой кислотостойкой пластмассы, разделенном перегородками (16) на отдельные камеры-ячейки (банки), по числу аккумуляторов в батарее. В каждую из ячеек помещен блок, состоящий из чередующихся положительных (5) и отрицательных (3) электродов, разделенных сепараторами (4). Он представляет собой отдельный аккумулятор напряжением 2 В. Пространство между дном моноблока и верхними кромками фиксирующих электроды опорных призм (1) служит для накаливания шлама — осадка, образующегося в процессе эксплуатации вследствие оплывания частиц активной массы положительных электродов. Когда объем шламового пространства заполняется, происходит замыкание нижних кромок разноименных электродов и аккумулятор теряет работоспособность.
Рис. 1 Аккумуляторная батарея с отдельными крышками Электроды состоят из активной массы, нанесенной на токоотвод решетчатой конструкции — решетку. Сепараторы разделяют участвующие в электрохимических превращениях реагенты, а также обеспечивают возможность диффузии электролита от одного электрода к другому. Сторона сепаратора, обращенная к положительному электроду для облегчения доступа электролита к поверхности активной массы, выполнена ребристой.
Борн (8), который служит наружным токоотводом аккумулятора, последовательно соединяет соседние аккумуляторы между собой в батарею. К выводным борнам крайних аккумуляторов батареи привариваются полюсные выводы (9) и (14), служащие для соединения батареи с внешней электрической цепью. Положительный (9) и отрицательный (14) выводы имеют разный диаметр, что позволяет исключить возможность переполюсовки при подключении АКБ к бортовой цепи автомобиля.
В верхней части электродного блока устанавливают щиток (7), предохраняющий верхние кромки сепараторов (4) от повреждения при замерах уровня и плотности электролита.
Каждый аккумулятор после установки электродного блока в камеру-ячейку моноблока закрывают сверху отдельной пластмассовой или эбонитовой крышкой (15). В ней выполняют по два отверстия с втулками для выводных борнов электродного блока. Между ними расположено резьбовое отверстие для заливки электролита и периодического обслуживания аккумулятора в процессе эксплуатации. После заливки электролита резьбовое отверстие закрывают пробкой из полиэтилена (11), имеющей небольшое вентиляционное отверстие (13), предназначенное для выхода газов при эксплуатации.
Для герметичной укупорки новых сухозаряженных батарей в верхней части пробки над вентиляционным отверстием выполнен глухой прилив. Для обеспечения нормальной эксплуатации этот прилив, после заливки электролита в батарею, необходимо срезать.
Благодаря специфическим свойствам термопластичной пластмассы появились аккумуляторные батареи с общей крышкой в моноблоке из сополимера пропилена с этиленом, устройство которых показано на рис. 2.
В моноблоке (1) установлены электродные блоки, состоящие из разноименных электродов (2) и (3), разделенных сепараторами (4). Эти блоки соединены между собой при помощи укороченных межэлементных соединений (6) через отверстия в перегородках (5) моноблока. Крышка (7) сделана единой на все шесть аккумуляторов батареи. Свойства термопластичной пластмассы позволили применить для герметизации АКБ с общей крышкой метод контактно-тепловой сварки, обеспечивающий сохранение герметичности как по периметру, так и между отдельными аккумуляторами в широком диапазоне температур (от ?50°C до 70°C).
Рис. 2 Аккумуляторная батарея с общей крышкой Необслуживаемое исполнение.
Недостатки традиционных свинцовых батарей обусловлены тем, что содержащаяся в сплаве положительных токоотводов сурьма постепенно, по мере их коррозии, через раствор переходит на поверхность отрицательного электрода. Осаждение большого количества сурьмы на поверхности отрицательной активной массы снижает напряжение на электродах батареи, при котором начинается разложение воды на водород и кислород. Поэтому, в конце зарядного процесса и при небольшом перезаряде, происходит бурное газовыделение, сопровождающееся «кипением» электролита вследствие электролитического разложения входящей в него воды.
За последние 20−25 лет, по мере развития технологии и совершенствования оборудования, появилось несколько разновидностей батарей так называемого «необслуживаемого» исполнения. Их основная отличительная особенность — использование сплавов с пониженным содержанием сурьмы или вовсе без нее для производства токоотводов.
Усовершенствование конструкции при создании необслуживаемых АКБ заключается еще и в том, что для увеличения запаса электролита без изменения высоты батареи, один из аккумуляторных электродов помещают в сепаратор-конверт, который изготовлен из микропористого полиэтиленового материала с низким электросопротивлением. В этом случае замыкание электродов различной полярности, при отсутствии сбоев в работе сборочного оборудования, практически исключено. Поэтому опорные призмы становятся ненужными, и блок электродов можно установить прямо на дно ячейки моноблока. В результате та часть электролита, которая раньше находилась в шламовом пространстве между призмами и не принимала участия в работе аккумулятора, теперь находится над электродами и пополняет его запас, расходуемый при эксплуатации батареи.
Первоначально такие батареи начали выпускать в США на базе свинцово-кальциевого сплава (0,07−0,1% Ca; 0,1−0,12% Sn; остальное — Pb) для токоотводов, положительного и отрицательного электродов. Это снизило газовыделение, что обеспечило эксплуатацию АКБ без доливки воды в течение как минимум двух лет. Расход воды у этих батарей так мал, что конструкторы убрали из крышек отверстия для доливки воды и сделали батареи полностью необслуживаемыми. При этом самозаряд батарей замедлился более чем в 6 раз. Однако, при нескольких глубоких разрядах такие АКБ быстро теряют емкость и их стартерные характеристики резко снижаются, из-за чего они не нашли широкого распространения в Европе и России.
В это же время в США появились батареи системы «кальций плюс» (гибридные) с содержанием до 1,5−1,8% сурьмы и 1,4−1,6% кадмия в положительном токоотводе и свинцово-кальциевым отрицательным токоотводом. Характеристики этих батарей по расходу воды и саморазряду вдвое лучше, чем у малосурьмяных, но все еще не такие хорошие, как у свинцово-кальциевых.
К началу 80-х годов производство необслуживаемых батарей стало быстро развиваться в странах Европы. Но там пошли по пути применения сплавов с пониженным до 2,5−3,0% содержанием сурьмы. Однако, у таких АКБ расход воды и саморазряд в 2−3 раза выше, чем у батарей с кальциевыми токоотводами. Позже и в Европе появились так называемые гибридные батареи.
Наконец, в конце 90-х годов и в США, и в Западной Европе началось производство батарей с токоотводами из свинцово-кальциевого сплава с добавкой новых легирующих компонентов, в том числе серебра, которые не боятся глубоких разрядов.
В России выпускаются необслуживаемые батареи емкостью от 44 до 90 А· ч с токоотводами из малосурьмяного сплава с содержанием сурьмы 1,7−3,0%.
Следует отметить, что эксплуатация батарей без отверстий для доливки воды требует более точной работы системы энергосбережения автомобиля, а также более внимательного отношения автовладельцев к состоянию и исправной работе электрооборудования. В первую очередь это касается натяжения ремня привода генератора и исправности самого генератора, а также регулятора напряжения. Отрицательно сказывается на состоянии батарей последнего поколения и наличие утечек тока в системе электрооборудования или сигнализацию.
Подавляющее большинство АКБ, поступающих в Россию из стран Европы, выпускают, как правило, в гибридном исполнении, либо с токоотводами обеих полярностей из свинцово-кальциевых сплавов. При изготовлении сухозаряженных батарей многие производители применяют для электродов обеих полярностей малосурьмяные сплавы с содержание сурьмы 1,6−1,8%.
Перспективы развития свинцовой промышленности России Основной сферой применения свинца является производство транспортных средств (более 75% всего потребляемого в мире металла), где он используется для выпуска гальванических элементов, топливных баков, припоев, изоляции и подшипников. Еще около 20% этого металла находит применение в электротехнической и электронной промышленности, производстве телекоммуникационного оборудования, военного снаряжения, защитных покрытий и в строительстве. Таким образом, современная металлургия свинца в значительной степени зависит от состояния автомобильной отрасли и строительной индустрии, наиболее пострадавших от глобального финансово-экономического кризиса.
Доля России в мировых природных запасах свинца оценивается в 7−8%. По этому показателю РФ уступает лишь Австралии и КНР. Среди прочих стран выделяются Казахстан, Канада, США, Перу и Индия. Почти 90% запасов металла РФ сконцентрировано в Сибири, еще 7% - на Дальнем Востоке. Около 70% российских запасов свинца сосредоточено в двух регионах на трех крупнейших месторождениях: Горевском в Красноярском крае (почти 44% разведанных запасов), Озерном и Холоднинском в Республике Бурятия.
На протяжении длительного времени подавляющий объем добычи свинца в РФ обеспечивали два предприятия: ОАО «Горевский ГОК» и ОАО «ГМК Дальполиметалл». В последние годы в добыче свинца и производстве свинцовых концентратов появились новые участники — ОАО «Сибирь-Полиметалл» («УГМК»), ООО «Корпорация «Металлы Восточной Сибири» (ИФК «Метрополь»), ОАО «Новоширокинский рудник» (СП ООО «Руссдраг-мет» и «Kazzinc»), а также ряд других компаний, способных резко наращивать экспортный потенциал отрасли.
ОАО «Горевский ГОК» (п. Новоангарск, Красноярский край) осуществляет добычу свинца открытым способом и первичное обогащение-свинцово-цинковых руд Горевского месторождения, характеризующихся высоким содержанием свинца (более 7%) и низким — цинка (около 1,3%), а также содержащих драгоценные металлы В 2007 г. добыча ОАО «Горевский ГОК» составила 735,7 тыс. т свинцово-цинковой руды, в 2008 г. — 826 тыс., в 2009 г. -1,204 млн. Среднегодовой выпуск свинцового концентрата комбинатом в докризисные годы составлял около 80 — 85 тыс. т, в 2008 г. — 75 тыс., в 2009 г.- 116 тыс.
ОАО «ГМК Дальполиметалл» (подконтрольное предприятие ООО «УК «Русская горнорудная компания») ведет разведку, добычу и переработку полиметаллических руд в Дальнегорском районе Приморского края. Это один из значимых российских продуцентов свинцовых концентратов (до 12 тыс. т свинца в концентратах в год) и рафинированного свинца (в основном извлекаемого из вторичного сырья).
В докризисный период свинец был весьма востребованным металлом на мировом рынке. Так, среднегодовая цена на него на ЛБМ в 2007 г. выросла в 2,9 раза относительно 2004 г., в то время как на цинк повысилась в 3,1 раза, на алюминий — в 1,5 раза, на медь — в 2,5 раза, на никельв 2,7 раза.
Продуценты по всему миру в этот период планировали расширение мощностей, а сам металл пользовался устойчивым спросом у инвестиционных структур и хеджевых фондов. В это время российские предприниматели обратили внимание на цинк и свинец, тогда как на выпуске и экспорте рафинированных алюминия, меди и никеля РФ специализируется уже многие годы.
Докризисный «бум» в свинцово-цинковой отрасли привел к появлению нового, потенциально крупного его участника российского рынкакомпании ООО «Корпорация «Металлы Восточной Сибири» («МВС»), входящей в структуру ИФК «Метрополь», которая, разрабатывая крупные свинцово-цинковые месторождения — Озерное, Холоднинское и Назаровское в Бурятии, намерена стать одним из крупнейших в РФ вертикально-интегрированных горнодобывающих холдингов. В настоящее время корпорация «МВС» осваивает месторождение Озерное, выход на проектную мощность рудника на котором запланирован на 2013 г.
Еще не так давно рафинированный свинец из добываемых концентратов в России выплавлялся ОАО «Электроцинк» и ОАО «ГМК «Дальполиметалл» путем восстановительной плавки агломерированных концентратов в шахтных печах с получением черного свинца и последующим его рафинированием. Но с 1997 г. ОАО «Электроцинк» на фоне снижения производства свинца в концентратах на Кавказе и подорожания внутренних железнодорожных перевозок полностью перешло на переработку вторичного сырья. ОАО «ГМК «Дальполиметалл» еще до 2005 г. перерабатывало часть производимого свинцового концентрата на собственном плавильном заводе (ЗАО «Свинцовый завод — Дальполиметалл»), но впоследствии выпуск первичного свинца был почти полностью прекращен, а предприятие перешло на переработку более доступного и дешевого вторичного сырья.
В настоящее время в России, несмотря на значительные масштабы добычи свинцовых руд, практически отсутствуют действующие металлургические мощности по переработке свинцовых концентратов, содержащих драгоценные металлы, а также по выпуску первичного рафинированного свинца. Поэтому почти весь объем произведенных свинцовых концентратов экспортируется, в основном в КНР, Японию, Южную Корею и Казахстан. Поэтому основным сырьем для производства рафинированного свинца и его сплавов в России стали свинецсодержащие отходы и лом. Отработанные аккумуляторные батареи представляют собой основной источник сырья для производства вторичного свинца в РФ, другие виды вторичного сырья представлены освинцованным кабелем, листовым прокатом, отходами припоев.
Переработка лома аккумуляторных батарей и свинцовых промышленных продуктов в крупных масштабах ведется на предприятиях ОАО «Электроцинк» (г. Владикавказ) и ОАО «Верх-Нейвинский завод цветных металлов» (Свердловская обл.), принадлежащих «УГМК», и ОАО «Рязцветмет» (г. Рязань). В меньших объемах вторичное производство осуществляют ОАО «ГМК «Дальполиметалл» (п. Рудная Пристань), ЗАО Комбинат по переработке вторичных ресурсов «Сплав» (г. Рязань), ЗАО «ПО «Цветметсервис» (г. Озерск, Челябинская область), ЗАО «Метком Групп» и ЗАО «Маглюк» (оба — в Московской области). Выпуск свинца из вторичного сырья в небольших количествах ведут собственными силами сами производители свинцовых аккумуляторных батарей, например ЗАО «АКОМ» (Самарская обл.), ООО «Ак-Тех» (Иркутская обл.), ООО «Курский завод «Аккумулятор» и ОАО «Тюменский аккумуляторный завод», а также ряд небольших предприятий.
Производство свинца ОАО «Электроцинк», контролируемого «УГМК», растет и составляет в последние годы в среднем немногим более 30 тыс. т в год. В 2003 г. он равнялся 20,5 тыс. т, в 2006 г. — 36,8 тыс., в 2008 г — 33,6 тыс.
Приоритетными направлениями деятельности компании ОАО «Рязцветмет», входящей в состав ГК «Русские аккумуляторы», являются утилизация и переработка вторичного аккумуляторного лома, выпуск товарного свинца и сплавов на его основе, а также производство припоев и сурьмы. Завод компании может перерабатывать до 70 тыс. т аккумуляторных батарей в год, а используемая технология позволяет получать свинец чистотой 99,985%. Основным фактором, негативно влияющим на сбыт продукции на европейском и внутреннем российском рынке, является сезонность. В связи с этим в будущем планируется заключение новых контрактов на поставку металла азиатским потребителями.
ЗАО «Метком Групп» обладает экологически безопасной технологией и способно перерабатывать до 40 тыс. т отработанных аккумуляторов в год, выпуская металлический свинец и сплавы, легированные медью, мышьяком, оловом и селеном.
В 90-е годы в России не хватало собственного рафинированного свинца, поскольку на фоне кризисных явлений и трансформаций, наблюдавшихся в экономике страны, резко уменьшились сбор и переработка вторичного свинецсодержащего сырья, а уровень первичного производства рафинированного металла оставался традиционно низким. В тот период основным поставщиком рафинированного свинца в Россию стал Казахстан. В результате Россия в 90-е годы, являлась нетто-экспортером таких основных металлов как алюминий, никель, медь и цинк, была нетто-импортером рафинированного свинца.
В последние годы повышательная тенденция в динамике добычи свинца в России была обусловлена началом постепенной реализации сибирских горнодобывающих проектов. Доля страны в мировой добыче свинца в 1995 г. составляла 0,9%, в 2000 г. — 0,4%, а в 2008 г. — достигла почти 1,4%. Доля России в мировом производстве рафинированного свинца в 1995 г. равнялась 0,55%, в 2000 г. — 0,7%, а в 2008 г. — поднялась до 1,15%. Таким образом, за счет наращивания выпуска вторичного металла роль страны в мировом выпуске рафинированного свинца растет, при этом добываемая свинцовая руда не является востребованной плавильными предприятиями Кавказа, Урала, Восточной Сибири и Приморского края.
Потребление рафинированного свинца в России находилось на достаточно высоком уровне вплоть до 2002 г., когда оно достигло 111 тыс. т, что соответствовало почти 1,7% мирового потребления (в 1995 г. аналогичный показатель равнялся 1,9%). Таким образом, на рубеже 2000;х годов потребление свинца в РФ практически в 2 раза превосходило объемы национального производства. С середины 2000;х годов сократился спрос на отечественные аккумуляторные батареи, общее потребление свинца в стране стало снижаться, что способствовало увеличению экспорта металла. С 2006 г РФ стала нетто-экспортером рафинированного свинца, при этом в последние годы свинцовые руды и концентраты в Россию практически не ввозились.
С начала 2000;х годов ситуация со вторичным производством металла в России стала постепенно улучшаться, подавляющая часть выпускаемого в стране свинца стала извлекаться из лома и отходов. Наблюдавшееся в последние годы появление новых предприятий по переработке вторичного сырья привело к заметному росту выпуска свинца в России. Однако по степени развитости вторичного производства Россия все еще значительно отстает от многих стран.
Глава 3. СПОСОБ ОТЛИВКИ СВИНЦОВЫХ РЕШЕТОК ДЛЯ ЭЛЕКТРОДОВ ИЗ ВТОРИЧНО ОТРАБОТАННОГО СВИНЦА КИСЛОТНЫХ АККУМУЛЯТОРОВ
Изобретение относится к электротехнической промышленности и используется в производстве решеток с высокими техническими характеристиками. Техническим результатом изобретения является использование свинца вторичной переработки с сохранением компонентов, добавляемых в котел в процессе литья решеток, улучшающих технические характеристики. Согласно изобретению во вторично обработанный свинец кислотных аккумуляторов, полученный в виде черного или рафинированного свинца, добавляют необходимые компоненты, которые при низкой температуре котла 320−350oС не выгорают, с последующим поднятием температуры до 450−520oС, что улучшает литейные качества решеток при их охлаждении в литьевой форме с температурой 120−180oС. Для создания равномерной структуры свинца и исключения трещин на решетках свинец перемешивается с добавкой серы 0,01−0,02%.
Изобретение относится к электротехнической промышленности и может быть использовано при производстве решеток для электродов из лома отработанных свинцово-кислотных аккумуляторных батарей.
Известны способы изготовления решеток для электродов свинцово-кислотных аккумуляторных батарей из промышленного свинца, поставляемого на аккумуляторные заводы, в которых содержатся все компоненты, необходимые для литья решеток и их технических характеристик.
Известно также, что в промышленном производстве для производства решеток аккумуляторных батарей используется вторично отработанный свинец кислотных аккумуляторов, получаемый в виде черного или рафинированного свинца, в которых основная часть компонентов, необходимых для технических характеристик решеток, выгорает в котлах. Естественно, что такой свинец для литья решеток применять нельзя. Чтобы улучшить качество отливаемых решеток, черновой свинец рафинируют, вводят необходимые добавки.
Так, например, в сплав УС1 вводят олово и мышьяк, которые являются легирующими примесями и составляют олова 0,11−0,15%, мышьяка 0,14−0,20% соответственно при низком содержании меди 0,05−0,07%.
Также следует отметить, что существует технология производства решеток из отработанного свинца методом проката.
Отработанный черновой свинец очищается от шлака и прокатывается до нужной толщины в полосы. Делают сквозные просечки, растягивают и вырубают решетки по заданным размерам. После механических операций решетку покрывают электрохимическим слоем олова, серебра, кальция или чистым свинцом.
Наиболее близким по технической сущности и достигаемому результату является переработка вторично отработанного свинца, получаемого на заводах в виде черного и рафинированного свинца, загружаемого в котел с добавками необходимой лигатуры.
Недостатками таких технологических процессов переработки отходов отработанного свинца в решетки являются использование дорогостоящих материалов, сложная технология производства решеток и его оборудование, а также трудное соблюдение технологических процессов, связанное с перерасходом нужных компонентов с низким производством выпускаемых решеток.
Задачей настоящего изобретения является использование свинца вторичной переработки для литья решеток с низким содержанием мышьяково-сурьмянистой лигатуры сурьмы, олова, кальция и других компонентов с добавками их в процессе литья решеток в котел с температурой 320−350oС, что предотвращает выгорание компонентов, с последующим повышением температуры до 450−520oС в промежуточной стадии, между котлом и литейной формой, в процессе которого компоненты в виде сурьмы, олова, кальция не успевают выгорать, придавая отливкам решетки литейное качество, коррозийную стойкость, исключая трещины на решетках с добавкой серы 0,01−0,02%.
Это достигается тем, что способ отливки свинцовых решеток для электродов из вторично отработанного свинца кислотных аккумуляторов, включающий плавление чернового или рафинированного свинца, добавку лигатуры, разливку в форму, охлаждение и выталкивание решеток, отличается тем, что плавление ведут при температуре 320−350oС, после добавления лигатуры проводят перемешивание в течение 10−15 мин, контроль содержания лигатуры и добавляют серу в количестве 0,01−0,02% от массы, перед разливкой в форму температуру свинца повышают до 450−520oС, после чего свинец разливают в литейную форму, имеющую температуру 120−180oС.
Котел с черновым или рафинированным свинцом с низким содержанием компонентов разогревают до температуры 320−350oС и перемешивают, снимая шумовкой шлак, образованный на поверхности зеркала котла. Берут анализ и проверяют содержимое компонентов, находящихся в котле. С учетом проведенного анализа в котел добавляют присадки в виде сурьмы, мышьяка, олова, кальция в том количестве, в зависимости от того, какую лигатуру хотят получить, малосурьмянистую или сурьмянистую. Полученная шихта перемешивается при температуре 320−350oС, и берется анализ. После проведения анализа в шихту добавляют 0,01−0,02% серы, исключающей трещины на решетках. Вся шихта перемешивается один раз в 1 час в течение 10−15 мин.
Приготовленная лигатура позволяет сократить при температуре 320−350oС выгорание компонентов и исключить растворимость меди, влияющей на работу аккумулятора. Но такая шихта свинца, полученная в котле при низких температурах, не пригодна для литья решеток из-за вязкости и проливаемости свинца в литейную форму. Поэтому в промежуточной стадии, между котлом и литейной формой, свинец насосом перекачивается из котла в изложницу, подогретую ТЭНами до температуры 450−520oС, и заливается в литейную форму, охлажденную до температуры 120−180oС. При автоматической скорости литья решеток в литейную форму от 8−12 шт. в 1 мин лигатура свинца в изложнице за счет замкнутого пространства изложницы и скорости литья решеток сохраняет все компоненты и литейные качества для производства электродов свинцово-кислотных аккумуляторов.
Полученный необходимый сплав свинца из отработанных кислотных аккумуляторов в виде черного и рафинированного свинца с непосредственными добавками компонентов в котел при низких температурах с последующим поднятием температуры в промежуточной стадии в отливаемую литейную форму с низким температурным режимом позволяет сохранить необходимые компоненты в виде сурьмы, олова, кальция и получить высокие технологические характеристики решеток, необходимых для производства электродов свинцово-кислотных аккумуляторных батарей.
Глава 4. ВТОРИЧНОЕ ИСПОЛЬЗОВАНИЕ СТОЧНЫХ ВОД ПРОИЗВОДСТВА АККУМУЛЯТОРНЫХ БАТАРЕЙ Процесс 3. Л. Бурке (патент США 3 882 019, 6 мая 1974; фирма «Хилл Бразерс Кэмикал Ко., Инка.) заключается в обработке промывных вод, загрязненных свинцом и серной кислотой, с получением воды, пригодной для повторного использования в процессе производства аккумуляторных батарей. Процесс обработки включает на первой стадии добавку в сточные воды карбоната свинца при перемешивании с образованием воды, углекислого газа и нерастворимого сульфата свинца и последующую фильтрацию для отделения воды от сульфата свинца с возвратом воды в производство. Отфильтрованный сульфат свинца добавляется в раствор аммиака, сульфата аммония, углекислого газа и воды во втором реакторе для образования сульфата аммония и карбоната свинца.
свинцовый кислотный аккумулятор батарея Раствор сульфата аммония отфильтровывается от карбоната свинца и подается в резервуар для последующего использования во втором реакторе. Отфильтрованный карбонат свинца высушивается для удаления остаточного аммиака, после чего в порошкообразном виде подается в первый реактор. Углекислый газ и аммиак из сушилки могут возвращаться в резервуар для раствора сульфата аммония. Избыточное количество раствора сульфата аммония может подаваться в кристаллизатор для получения кристаллического сульфата аммония. Схема этого процесса представлена на рис. 17.
Производство аккумуляторов требует большого количества воды, загрязняющейся в процессе производства свинцом и серной кислотой. Загрязненная вода, содержащая свинец в различных формах и серную кислоту, по трубопроводу 1 подается на фильтр грубой очистки 2. Фильтр предназначен для удаления крупных твердых частиц, например металлического свинца и других соединений. После фильтрации вода содержит серную кислоту и растворенные соединения свинца и по трубопроводу 3 подается в резервуар 4. Поскольку последующий процесс происходит с периодической загрузкой, резервуар позволяет накапливать воду в период питания реактора из другой аналогичной емкости. В соответствующий момент времени выходной трубопровод резервуара 4 подключается к реакционному сосуду 6. Реактор 6 может представлять собой большой резервуар с мешалкой 7, связанной через вал 8 с мотором 9. После заполнения реактора 6 водой из емкости 4, порошкообразный карбонат свинца подается в 6 из бункера 29 и масса интенсивно перемешивается.
Карбонат свинца растворим в водном растворе серной кислоты и превращается в сульфат свинца, который выпадает из раствора вследствие его низкой растворимости (на этой стадии происходит отделение сульфат-ионов от молекул воды). Другим продуктом реакции является углекислый газ. Реакция описывается уравнением РЬС03 + H2S04->- PbS04 + Н20 + С02
Количество карбоната свинца, необходимого для добавления в реактор 6, эквивалентно суммарному количеству растворенных веществ (СРВ) в подаваемой воде.
Например, если в воде после фильтра грубой очистки СРВ составляет 15 000 ррт или 15 г/л, то для проведения реакции требуется также 15 г/л карбоната свинца. Хотя достаточно отношения реагентов 1:1, любое увеличение количеств РЬС03 выше этой величины пропорционально увеличивает скорость реакции.
В характерном примере, когда в подаваемой воде содержится 15 ООО ррт СРВ, 25 ррт свинца и рН ~ 2,3, уже после 10 мин рН возрастает до 6 и суммарное количество растворенных веществ составляет 1200 ррт, а количество свинца уменьшается до 3 ррт. В течение последующих 30 мин рН достигает значения равного 7 и концентрация растворенных веществ составляет 1000 ррт или менее. Из полученных данных видно, что уже после десятиминутной обработки в реакторе 6 качество воды позволяет возвращать ее в цикл производства. При открывании выходного вентиля 10 раствор подается на фильтр 11.
Фильтр может быть вращающимся барабанным фильтром, центрифугой или любым другим аналогичным устройством для отделения твердого осадка от раствора, в данном случае воды от сульфата свинца. Отфильтрованная вода содержит 1000 (или менее) СРВ и 3 ррт (или менее) свинца и проходит по трубопроводу 12 к фильтру 13 для последующего отделения твердых частиц. После выхода из 13 вода подается назад в цикл основного производства.
Хотя требуется около 40 мин для достижения рН = 7 в реакторе 6, реакция протекает и после остановки мешалки до тех пор, пока в смеси остается карбонат свинца и серная кислота. Поэтому раствор перемешивается в реакторе только 10 минут, что вместе с реакциями на последующих стадиях обеспечивает достаточную глубину реакции и достижение удовлетворительного качества оборотной воды.
Газообразный диоксид углерода из реактора 6 подается по трубопроводу 17 в сборник 18. Влажный сульфат свинца с фильтра // добавляется к раствору аммиака, сульфата аммония и С02, находящемуся во втором реакторе 19. Реактор 19 идентичен по своему устройству реактору 6 и также имеет лопастную мешалку 20, связанную посредством вала 21 с мотором 22. Реактор 19 заполняется сначала раствором сульфата аммония, аммиаком и углекислым газом из резервуара 26. Сульфат свинца легко растворим в растворе сульфата аммония, но в присутствии С02 свинец моментально реагирует с образованием нерастворимого карбоната свинца. Реакция описывается уравнением
PbS04 + С02 + 2NH3->- РЬС03 + (NH4)2S04.
Реакция наиболее легко протекает в избытке сульфата аммония.
Взвесь, содержащая около 15 г PbS04 в литре раствора сульфата аммония, аммиак и С02, подвергается реакции в течение 10—15 минут. Раствор должен содержать 15—100 г/л сульфата аммония, минимум 2 г/л С02 и достаточное количество аммиака для поддержания щелочной среды. Реактор 19 может заполняться по линии ведущей с фильтра //, в то время как по другой линии раствор с фильтра поступает в реактор 6. Примерно через 10 мин открывается выходной вентиль 23 реактора 19 и реакционная масса направляется на фильтр 24, идентичный фильтру // для отделения твердых частиц от раствора. На фильтре 24 происходит отделение раствора сульфата аммония от выпавшего карбоната свинца. Раствор сульфата аммония по линии 25 подается в резервуар 26.
Влажный карбонат свинца, выделенный на фильтре 24, подается в сушилку 27. Необходимость проведения этой операции обусловлена тем, что при фильтрации захватывается аммиак, загрязняющий карбонат свинца. В сушилки 27 осадок нагревается до температуры около 100 °C, при этом аммиак отгоняется по трубопроводу 32 в сборник 18. Сухой порошкообразный карбонат свинца из сушилки 27 по трубопроводу 28 отправляется назад в бункер 29 для повторного использования в реакторе 6.
Если количество карбоната свинца, выделенного в сушилке 27, соответствует количеству этого соединения необходимому для реакции в реакторе 6, то в этом случае карбонат свинца просто рециркулирует образуя замкнутый цикл в рамках полной системы очистки. Однако может возникнуть ситуация, при которой количество карбоната свинца из сушилки недостаточно или избыточно относительно требуемого количества для реакции в б. В случае недостатка некоторое количество его дополнительно вводится в бункер 29 из внешнего источника по линии 30. Избыток РЬС03 удаляется по линии 31 в качестве товарного продукта.
Сульфат-анионы, отделяемые от водного раствора в б и соединяющиеся со свинцом с образованием PbSO^, затем снова отделяются в реакторе 19 и накапливаются в резервуаре 26 в виде водного раствора сульфата аммония. Щелочная реакция раствора в 26 поддерживается за счет подачн дополнительных количеств углекислого газа и аммиака из емкостей 34 и 35 соответственно. Аммиак по линии 32 из сушилки 27 и С02 по линии 17 из реактора 6 также подаются в сборник 18 и по трубопроводу 33 возвращаются в 26 для регулирования рН содержащегося там раствора.
При стабильном проведении процесса раствор в емкости 26 становится настолько концентрированным, что начинают выпадать кристаллы сульфата аммония, забивающие трубопроводы. Избыточный сульфат аммония из 26 частично отбирается по линии 37 в кристаллизатор 38, где непрерывно протекает процесс кристаллизации. Кристаллический сульфат аммония постепенно удаляется через выпускное отверстие 40 в виде товарного продукта. Остающийся маточный раствор по трубопроводу 39 подается в сборник 18 для последующего возврата по трубопроводу 33 в резервуар 26.