Электрометаллургия и производство ферросплавов
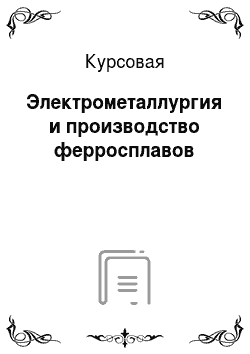
Для устранения этого явления было решено дать в завалку хромистую руду, а во время плавления присаживать небольшими порциями железную руду. Завалку в этом варианте располагали так: на подину давали 400−500 кг извести, 200−250 кг плавикового шпата и 100 кг кварцевого песка. Затем заваливали никель, а на него 400 кг хромистой руды. Далее укладывали блюмы мягкого железа и по откосам печи феррохром… Читать ещё >
Электрометаллургия и производство ферросплавов (реферат, курсовая, диплом, контрольная)
Электрометаллургия и производство ферросплавов
1. Требования к качеству заданной марки стали
Марка: | 40Х13 | |
Применение: | Пружины для работы при температурах до 400−450 град. Рессоры, шариковые подшипники, режущий и мерительный инструмент, клапанные пластины компрессоров, предметы домашнего обихода и другие детали. Сталь коррозионно-стойкая мартенситного класса. | |
Заменители: | 30Х13 | |
Таблица 1 — Химический состав в% стали 40Х13
C | Si | Mn | Cr | P | S | Cu | Ni | |
0,395 | 0,600 | 0,600 | 13,000 | 0,030 | 0,025 | 0,300 | 0.300 | |
Таблица 2 — Технологические свойства стали 40Х13
Свариваемость: | Не применяется для сварных конструкций | |
Склонность к отпускной хрупкости: | Склонна | |
Коррозионно-стойкая (нержавеющая) сталь отличается стойкостью против электрохимической коррозии (атмосферной, почвенной, щелочной, кислотной, солевой, морской).
Изделия из нержавеющей стали предназначены для работы в агрессивных средах при обычных или высоких температурах, поэтому основным требованием, предъявляемым к нержавеющей стали, является коррозионная стойкость (способность противостоять воздействию агрессивной среды при обычной температуре), а также жаростойкость (сопротивление воздействию газовой среды или пара высоких температур). Жаростойкая сталь, как правило, должна быть и жаропрочной, т. е. противостоять при высокой температуре в течении промежутка времени разрушению и ползучести.
Главное влияние, которое оказывают легирующие элементы на сталь, заключается в значительном повышении её коррозионной стойкости, механических свойств, главным образом предела прочности, предела текучести, твердости и в ряде случаев относительного сужения и ударной вязкости. Особенно благоприятные результаты получаются при легировании стали двумя, тремя, а иногда большим числом легирующих элементов.
В качестве легирующих в нержавеющих сталях применяют хром, никель, марганец, кремний.
Легирующие элементы вводят в сталь в виде сплавов с железом (например, феррохром, ферромарганец, ферросилиций) либо с железом и другим каким-либо элементом (например, ферросиликохром), либо в виде одного элемента (никель, металлический хром, металлический марганец).
Феррохром. Хром — основной легирующий элемент для получения стали с особыми химическими свойствами. Поэтому феррохром при выплавке нержавеющих сталей является одной из главных легирующих добавок. В ряде случаев применяют металлический хром. В качестве легирующей присадки и в качестве раскислителя нередко применяют ферросиликохром.
Ферроникель, как и хром, является основным легирующим элементом при производстве хромоникелевой нержавеющей стали. Никель, как правило, вводят в завалку на нижний предел заданного состава с учетом содержания его в шихте. Гранулированный и прессованный никель, ферроникель и закись никеля вводят только в завалку на плавках с полным окислением и при выплавке переплавом с кислородом. Для корректировки химического состава плавки во время кипения и рафинирования применяют только электролитический, огневой (чушковый) или карбонильный никель.
Ферромарганец, или металлический марганец, присаживают в период плавления или рафинировки. При выплавке хромоникелевой нержавеющей стали ферромарганец употребляют в небольших количествах и главным образом малоуглеродистый.
Ферросилиций. Кремний в количестве до 0,2−0,3% остается в стали после раскисления и считается постоянной примесью, свыше 0,3−0,7% он является уже легирующим элементом. Ферросилиций для легирования металла кремнием вводят за 10−20 мин до выпуска. При выплавке нержавеющей стали для легирования металла применяют только 75%-ный ферросилиций.
Алюминий для окончательного раскисления вводят в металл за 2−3 мин до выпуска. Куски алюминия на шомполе погружают как можно глубже в металл и выдерживают там в спокойном состоянии до полного растворения.
Раскисление стали алюминием можно производить и в ковше. В этом случае куски алюминия с отверстиями по центру насаживают на шомполы диаметром 25 мм; шомполы с алюминием до выпуска плавки закрепляют на борту так, чтобы нижний кусок был на расстоянии не более 0,5 м от дна ковша. Алюминий применяют для окончательного раскисления металла почти всех марок, кроме легированных титаном. Для раскисления сталей обычно применяют алюминий, содержащий до 8% примесей, а для легирования-алюминий, содержащий не менее 98% А1.
Медь повышает пластичность стали в холодном состоянии, сопротивляемость стали атмосферной коррозии. При 0,3% меди в стали образуются участки сплава с низкой температурой плавления. Этот сплав отлагается по границам зёрен и вызывают красноломкость металла при ковке и прокатке.
Сера вызывает красноломкость стали, понижает механические свойства, увеличивает склонность к ржавлению и истиранию, снижает способность стали к глубокой вытяжке (штамповке).
Фосфор вызывает хладноломкость стали, но также повышает коррозионную стойкость стали.
В настоящее время нержавеющую сталь марки 40Х13 выплавляют главным образом в электродуговых печах с основной футеровкой.
При выплавке в дуговых печах используют разные методы:
ѕ Выплавка нержавеющей стали методом полного окисления Первоначальный технологический процесс выплавки стали 40Х13 был аналогичен процессу плавок прочих легированных марок сталей. Он предусматривал проведение полного окисления примесей и рафинирования ванны под белым шлаком. Основные положения этой технологии были разработаны в довоенное время для плавки стали в небольших печах (5−6-т). Шихту составляли из чистого углеродистого лома, никеля и передельного чугуна из расчета получения в первой пробе 0,7 — 0,8% С, 0,6−0,7% Мn и 13,0−14,0% Ni. Окислительный период проводили до получения в металле не более 0,04−0,05%, после чего шлак начисто скачивали. Содержание марганца в процессе кипения ванны поддерживалось не менее 0,20% систематическими присадками ферромарганца. Общая продолжительность окислительного периода составляла около 2 ч. После скачивания шлака давали металлический марганец, сухой речной песок для образования под электродами тонкой пленки шлака для предохранения металла от науглероживания, а затем известь и плавиковый шпат. Через 8−10 мин от включения печи давали около 1 кг/т А1, после 30−40 мин жидкоподвижный шлак раскисленым 75%-ным ферросилицием до получения го металла. Кокс в период рафинирования безуглеродистым феррохром марки ФХ 005 в несколько приемов в хорошо нагретый металл. Расплавление феррохрома длилось 1,5−2 ч. После расплавления феррохрома продолжали раскисление ванны молотым ферросилицием до получения светлого рассыпающегося в порошок шлака.
Основным недостатком этого метода была необходимость сильного нагрева металла перед присадкой феррохрома, а затем продолжительное плавление его и вновь нагревание ванны до необходимой при выпуске температуры. Это приводило к сильному износу футеровки печи и особенно свода, который в то время выкладывался только из динасового кирпича и на плавке сильно оплавлялся.
Оплавление свода сказывалось на шлаках, они становились кислыми, что требовало больших присадок извести. Образовывалось большое количество шлака, что в свою очередь затягивало расплавление феррохрома и расстраивало нормальный ход рафинирования.
ѕ Выплавка нержавеющей стали методом частичного окисления Желание избежать длительного периода окисления привело к разработке метода частичного окисления. Сущность метода состоит в изготовлении низкоуглеродистого мягкого железа в самой электропечи в процессе плавки. Для этого в качестве шихты использовали низкоуглеродистое железо, содержащее 0,10−0,15% С.
Завалку начинали с загрузкой на подину извести (1,5−2% от массы шихты), поверх которой заваливали никель и шихтовое углеродистое железо.
За 15−20 мин до полного расплавления давали порцию железной руды (1,5−2% от массы шихты) и отбирали пробу металла на углерод. После полного расплавлеиия давали еще одну-две порции руды в зависимости от содержания углерода. По достижении содержания 0,03−0,04% С окислительный шлак скачивали начисто. Далее плавку вели под глиноземистым или известковым шлаком. Выбор характера шлака зависел от содержания серы в исходной шихте и от требований к содержанию серы в готовой стали. Металл раскисляли 75%-ным ферросилицием через 25−30 мин от начала рафинирования. В хорошо нагретый и раскисленный металл давали подогретый до 800−900° С феррохром марки ФХ005 в два-три приема. Через 1−1,5 ч от конца дачи феррохрома при достижении нужной температуры скачивали около 75% шлака. Средняя продолжительность плавки составляла 6 часов.
Метод частичного окисления давал возможность получать нержавеющую сталь в 95% всех плавок с содержанием углерода в готовом металле не выше 0,12%. Металл получался вполне удовлетворительного качества. Угар хрома был минимальным и составлял всего 2−4%.
В течение примерно двух лет метод частичного окисления был основным методом производства нержавеющей стали. Были выполнены сотни плавок. Вначале метод не подвергался изменениям и осваивался таким, каким он был разработан при проведении опытных плавок. Через некоторое время в изложенную выше технологию внесены были изменения: 1) большая часть мягкого железа была заменена отходами хромоникелевых сталей с низким содержанием углерода; 2) масса плавки была повышена; 3) после скачивания окислительного шлака в металл добавляли 10−12% нагретых до красна отходов стали 40Х13 для экономии легирующих материалов.
ѕ Выплавка нержавеющей стали методом сплавления Метод сплавления был разработан в 1947;1948 гг. Он был одним из вариантов, позволяющих выплавлять нержавеющую сталь в больших 30-т электропечах. Главным отличием его было то, что в качестве основного шихтового материала использовали предварительно выплавленное в электропечах и прокатанное на блюмы мягкое железо, содержащее не более 0,05% С; 0,010% Р и 0.020% S.
При организации выплавки нержавеющей стали методом сплавления были опробованы три варианта завалки и расплавления. Переход от одного варианта к другому обусловливался величиной получаемых по расплавлении содержаний углерода.
В первом варианте расположение материалов было следующее: на подину печи давали известь и плавиковый шпат, затем в центр печи заваливали мульдой никель и мягкое железо; по откосам укладывали феррохром марки ФХ006. В первой же плавке содержание углерода по расплавлении всей шихты оказалось 0,19% при расчетном 0,07%. Рост содержания углерода можно объяснить науглероживающим влиянием электродов, качество которых в то время было еще низким.
Для устранения этого явления было решено дать в завалку хромистую руду, а во время плавления присаживать небольшими порциями железную руду. Завалку в этом варианте располагали так: на подину давали 400−500 кг извести, 200−250 кг плавикового шпата и 100 кг кварцевого песка. Затем заваливали никель, а на него 400 кг хромистой руды. Далее укладывали блюмы мягкого железа и по откосам печи феррохром. Во время расплавления в образовавшиеся колодцы под электроды давали порциями по 7−15 кг железную руду в количестве 600−700 кг на плавку. В плавках, выплавленных по этому методу, содержание углерода по расплавлении получилось 0,11−0,12%. Это содержание углерода удавалось удержать до выпуска металла из печи. Однако в ходе плавок было установлено, что хромистая руда играет незначительную роль в окислении углерода ванны и сохранении в ней хрома.
Переход хромистой руды в шлак по расплавлении ванны приводил к высокому содержанию окислов хрома в нем, что сильно затрудняло ведение плавки. Поэтому в дальнейшем был применен третий вариант, заключавшийся в том, что и в завалку, ив период расплавления давали железную руду.
Порядок завалки шихтовых материалов был следующий: на подину давали 400 кг извести, 200 кг плавикового шпата, 100 кг кварцевого песка. Затем заваливали весь никель, поверх которого загружали 4−5 т мягкого железа. Далее присаживали железную руду в количестве 1500 кг под каждый электрод по одной мульде. Поверх руды загружали остальную часть мягкого железа, а по откосам укладывали феррохром марки ФХ005.
Этот метод обеспечил получение стали с содержанием углерода до 0,12% в 89% плавок. Ввиду того что в завалку и во время плавления давали железную руду, значительно повысился угар хрома, который колебался в пределах 15 — 20%, а на некоторых плавках доходил до 24%. Раскисление шлака молотым ферросилицием несколько уменьшало угар, но все же он оставался высоким. Это является одной из причин того, что от метода сплавления перешли к другому, более экономичному.
Таким образом, метод сплавления по третьему варианту на определенном этапе освоения выплавки нержавеющей стали позволил получить металл с необходимым содержанием углерода и удовлетворительного качества. Средняя продолжительность плавки — 6 ч 40 мин.
ѕ Выплавка нержавеющей стали методом смешения Сущность этого метода заключается в том, что водной электропечи выплавляют мягкое железо с никелем, а в другой сплавляют отходы нержавеющей стали 40Х13 или при их отсутствии мягкое железо с феррохромом. Затем обе плавки смешивают в одном ковше.
Технология этого метода была разработана и осуществлена на уральском заводе. Электропечи, выплавляющие равные части плавки, были условно названы Л и Б. В печи, А выплавляли хромистую часть плавки, а в печи Б никелевую. Расчет шихты производили таким образом, чтобы феррохром и никель, загружаемые в разные печи, обеспечили необходимый состав металла после смешения. При расчете учитывали угар хрома 5%, титана 50%; усвояемость никеля брали 97%. Завалка в печах, А ц Б составляла 14−15 т.
После доводки шлака металл раскисляли порошком 75%-пого ферросилиция до спокойной пробы в стаканчике. Далее брали пробы на химический анализ и производили тщательную соответствующую корректировку.
При совпадений фактических содержаний элементов с расчетными плавку подготавливали к выпуску. Первой выпускали в ковш плавку из печи А, а на нее плавку из печи Б. Такой порядок выпуска плавок гарантировал надлежащее смешение металла и его однородность. Следует отметить, что в период освоения этой технологии были трудности с обеспечением в готовом металле необходимого содержания углерода.
Каждый из рассмотренных способов имеет как преимущества, так и недостатки. Поэтому целесообразно проводить выплавку нержавеющей стали марки 40Х13 в электродуговой печи методом частичного окисления. Этот способ хорошо зарекомендовал себя, как простой в организации технологии производства сданной марки стали и, сравнительно, дешёвый.
2. Выбор и обоснование конструкции и мощности ДСП (удельная мощность, футеровка, выпуск и т.д.)
2.1 Расчет основных геометрических размеров рабочего пространства ДСП
Таблица 3 — Константы
dЖ | kM | kШ | kШЛ | dШЛ | dШ | h3 | h4 | k3 | |
7,1т/м3 | 0,21 | 2,0 | 3,0 | 1,2 | 0,03 | 0,03 | 1,0 | ||
Для печи заданной вместимости необходимый объём металлической ванны находим по массе жидкого металла:
м3
Для заданных значений kШ и kM определяем коэффициент, характеризующий форму металлической ванны:
Находим размеры металлической ванны в соответствии с формулами, м:
Для заданного количества шлака kшл=4% объем шлаковой ванны составит согласно
dшл — плотность жидкого шлака, примем 3,0 т/м3
Толщину слоя шлака можно определить, пренебрегая конусностью шлаковой ванны:
Уровень порога рабочего окна принимаем на 30 мм выше «зеркала» шлаковой ванны для создания дополнительного объёма ванны на случай кипения металла и шлака в окислительный период плавки: h3?0,03.
Паспортной характеристикой, т. е. параметром печи является глубина ванны от уровня порога рабочего окна:
Другой параметр печи — диаметр ванны на уровне порога рабочего окна можно определить:
Уровень откосов ванны принимаем выше уровня порога рабочего окна на 70 мм во избежание размывания шлаком основания футеровки стен и возможного аварийного выхода жидкого металла, т. е.
h4 = 0,07
Суммарная глубина ванны (от уровня откосов подины) в виде:
определяем такой параметр, как диаметр рабочего пространства на уровне откосов, являющийся также паспортной характеристикой печи:
Объём рабочего пространства Vраб состоит из объёмов ванны VВ и свободного пространства Vпр.
Поскольку выбираем профиль стен цилиндрический, то формула для объема свободного пространства следующая:
Высоту стен печи в виде расстояния от уровня откосов подины до верха стен, определяем из условий теплообмена и возможности размещения металлошихты большего в 5…7 раз объёма по сравнению с жидким металлом:
тогда: = 63,855 (м3)
Объем, занимаемый металлошихтой с насыпной плотностью dШ=1,2…1,6 т/м3 (примем dШ=1,4 т/м3) при единовременной загрузке (kз=1), равен:
kр-расходный коэффициент (примем 1,08)
Объём занимаемый металлошихтой VШ =45 м3 меньше, чем Vраб, т. е. загружаемая шихта разместится в рабочем пространстве печи ниже верхнего уровня корпуса печи.
Толщина многослойной футеровки подины:
=1 — для печей без ЭМП, тогда
Принимаем толщину элементов футеровки ДСП:
толщина подины, мм:
ѕ теплоизоляционный слой (теплоизоляционная кирпичная кладка (85), выравнивающая засыпка (30)) — 115 мм,
ѕ огнеупорный слой 525 мм,
ѕ рабочий (набивной) слой 150 мм;
ѕ общая толщина 790 мм.
толщина футеровки свода ?св=300 мм в районе отверстии для электродов.
На высоту, от уровня откосов, равную 400 мм — стена выкладывается огнеупорным кирпичом. Затем от кирпичной футеровки до уровня свода располагаем водоохлаждаемые панели. Их высота будет составлять:
— высота водоохлаждаемой панели толщина футеровки стены: (мм) Внутренний диаметр кожуха равен:
Кожух изготавливают из котельной листовой стали толщиной ДК
По форме кожух выполняем цилиндрическим, для размещения водоохлаждаемых панелей.
Размеры рабочего окна составляют: ширина, высота:
b0=0,25•4,414=1,103 м, высота h0=0,8•1,103=0,883 м.
Диаметр распада электродов равен: м Стрела подъёма кирпичной футеровки сферического свода составит:
Высоту расположения hСВ центральной точки кирпичной секции комбинированного свода с водоохлаждаемыми панелями относительно уровня откосов ванны, где горят электрические дуги, определяем с учётом стрелы подъёма hПС кирпичной секции в соответствии с:
А радиус сферы свода будет:
= 6,23 м
2.2 Проектирование строения подины, выбор конструкции и материалов стен и свода
Назначение подины — сформировать ванну соответствующей формы и размеров для жидкого металла и шлака, а также обеспечить тепловую изоляцию металла в ванне. Рабочий слой подины испытывает механические нагрузки и резкое охлаждение при загрузке холодной твердой металлошихты, активно участвуют в физико-химических процессах, происходящих в жидком металле, взаимодействует со шлаками, испытывает эрозионный и коррозионный износ в условиях высокой температуры, ферростатического давления и электромагнитного перемешивания жидкого металла. Разрушение подин происходит двумя путями — оплавлением и вымыванием участков футеровки с пониженной огнеупорностью; при охлаждении печи в период ремонтов возможно рассыпание в порошок поверхностного слоя, содержащего двукальциевый силикат.
Подина состоит из двух основных слоев: верхнего — рабочего набивного слоя, образующего прочную и плотную чашу для жидкого металла и шлака, и нижнего слоя — кирпичной кладки.
Верхняя часть кирпичной кладки должна обладать высокими огнеупорностью и механической прочностью, чтобы образовать прочное основание для набивного слоя. К нижней части кирпичной кладки, прилегающей к кожуху печи, предъявляются меньшие требования в отношении огнеупорности и механической прочности (более низкая рабочая температура), но от нее требуется более низкая теплопроводность.
Для тепловой изоляции на днище кожуха насыпаем выравнивающий слой шамотного порошка толщиной 30 мм, на который укладываем два ряда шамотного кирпича на плашку толщиной 85 мм. Т.о. общая толщина теплоизоляции составляет 115 мм.
Огнеупорный слой основной подины принимаем из двух рядов прямого периклазового кирпича размером 230Х115Х65 мм. Кирпичи каждого последующего ряда кладки смещаем на 45°, чтобы перекрыть вертикальные швы. Швы кладки заполняем просеянным периклазовым порошком марки ППЭ фракции 1… 0 мм.
Такие меры предотвращают выход жидкого металла сквозь кладку подины.
Рабочий слой подины толщиной 500 мм набираем из сухого периклазового порошка марки ППЭ без связки (так называемая сухая падина).
Рисунок 1 — Конструкция футеровки подины ДСП: 1 — рабочий слой; 2, 3 — огнеупорная и теплоизоляционная кирпичные кладки соответственно; 4 — выравнивающая засыпка; 5 — днище Назначение стен — сформировать свободное пространство как часть рабочего пространства печи для размещения загружаемой металлошихты и обеспечения соответствующей схемы направленного теплообмена. Температурные условия тепловой работы футеровки стен значительно тяжелее, чем подины, так как она в период открытого горения дуг подвергается непосредственному излучению от них. Скорость изменения температуры внутренней поверхности достигает 30…100 град/мин к концу периода расплавления и даже 150…170 град/мин при открывании рабочего пространства во время заправки или загрузки металлошихты. В нижних горизонтах стен футеровка подвергается комплексному разрушающему воздействию металла, шлака, печной атмосферы и высоких температур. Разрушение огнеупорной футеровки происходит в результате оплавления и отекания расплавленной массы с пониженной огнеупорностью, а также сколов, вызываемых термическими или структурными изменениями.
Исходя из того, что выбрана мощная печь, целесообразно футеровать стены водоохлаждаемыми панелями. Такие стены имеют высокую стойкость, оцениваемую тысячами плавок, в результате чего сокращаются простои оборудования и уменьшаются затраты на ремонт. Отсутствие больших масс огнеупорных материалов исключает энергозатраты на их нагрев (аккумулируемая энергия), оплавление и соответствующее дополнительное шлакообразование.
Вместе с тем водоохлаждаемые стены неблагоприятно влияют на тепловую работу дуговых печей: возрастает мощность тепловых потерь в систему водяного охлаждения, что требует дополнительного ввода тепловой мощности в рабочее пространство; возможно увеличение удельного расхода электроэнергии на 10…20 кВт· ч/т; снижается температура теплоизлучающих поверхностей свободного пространства, нарушая условие направленного косвенного теплообмена; существует опасность соприкосновения жидкого металла с металлическими (медными) водоохлаждаемыми панелями при барботаже ванны в окислительный период и при сливе металла из печи. Поэтому панели устанавливаем на некоторой высоте над откосами ванны (не менее двух — трех рядов кладки), уступами поднимая их вблизи выпускного отверстия. Такая мера уменьшает поверхность охлаждения до 65…75% от величины площади внутренней поверхности стен и снижает эффективность применения водоохлаждаемых стен.
Так как в данном случае рассматривается печь четвертого поколения, то конструкция футеровки стены будет состоять из водоохлаждаемых панелей. Выбираем панели из толстого стального листа (каналы системы охлаждения выполняются сверлением), и небольшого слоя периклазоуглеродстых огнеупорных кирпичей.
Конструкция футеровки свода Свод имеет такое же назначение, как и стены, но работает в еще более тяжелых условиях: более высокие тепловые нагрузки от дуг и от зеркала ванны из-за больших значений локальных и средних угловых коэффициентов; более резкие колебания температуры внутренней поверхности при открывании печи путем поворота свода. Конструкция свода осложняется необходимостью иметь отверстия для электродов (с соответствующей электроизоляцией, если материал свода обладает проводимостью) газоотсоса, кислородной фурмы и т. д.
Так как выбрана печь высокой мощности целесообразно применять комбинированный водоохлаждаемый свод ((рисунок 2) состоящий из водо — охлаждаемого каркаса — опорной рамы 3, сьемных водоохлаждаемых панелей 4 и центральной секции 2). Для уменьшения тепловых потерь рабочую поверхность водоохлаждаемых панелей следует обмазывать огнеупорным бетоном толщиной 50…70 мм. Конструкция водоохлаждаемого металлического свода должна иметь минимальные электрические потери из-за перемагничивания магнитных масс и вихревых токов под влиянием мощных переменных магнитных полей, создаваемых токами в электродах. Поэтому металлоконструкцию изготавливаем из немагнитных материалов в виде электроизолированных секций. Электродные отверстия выполняем между футерованными фигурными секциями металлического свода.
Рисунок 2 — Комбинированный свод ДСП
2.3 Эскиз рабочего пространства печи с указанием размеров и вида материалов
Рис. 5 — Эскиз рабочего пространства и формы ванны ДСП-100: 1 — Уровень откосов ванны; 2 — Уровень порога рабочего окна; 3 — Рабочее окно; 4 — Шлаковая ванна; 5 — Металлическая ванна
2.4 Расчет мощности электропечного трансформатора
Номинальное значение полной мощности Sн электропечного трансформатора определяет величину активной мощности Рн, выделяемой в рабочем пространстве печи в соответствии с графиком энергетического режима плавки, согласно которому устанавливаем максимальный kи.м. и средний kи коэффициенты использования мощности трансформатора.
Для проектируемой ДСП вместимостью 100 (т) теплотехнические характеристики можно определить по формулам:
W1 т. п = k1*0,19*(m0)0,67;
W1 т. п — энергия тепловых потерь за период подготовки печи к плавке.
Р2 т. п.? k2*0,14*(m0)0,67;
Р2 т. п — мощность тепловых потерь из рабочего пространства печи.
k1 и k2 — коэффициенты, учитывающие возможное изменение тепловых потерь за подготовительный период.
Для печей четвертого поколения k1 и k2 =1,2
W1т.п. =1,2*0,19*(50)0,67 = 3,13 (МВт) Р2 т. п.? 1,2*0,14*(50)0,67? 2,31 (МВт) В соответствии с данными технологическими условиями энергетические затраты необходимые для расплавления металлошихты, составляют:
УW2 = W2у.т.*mШ + ДWак + (-Wф) + (-Wд) = kр*kл*(1 — kф)*(1 — kд)*W2у.т.*m0 + W1т.п.;
Где: kл = (1 — mл / mО) — коэффициент, учитывающий отсутствие массы легирующих материалов и остаточного жидкого металла в составе металлозавалки mШ;
kф = 0,02…0,2 — коэффициент, учитывающий возможный приход теплоты Wф;
kд = 0…0,1 — коэффициент, учитывающий дополнительный ввод теплоты Wд при работе ТКГ;
W2у.т = 0,2…0,4 МВт•ч/т — удельный полезный (теоретический) расход энергии на проведение периода расплавления, зависящий от технологии плавки.
W1т.п — энергия тепловых потерь за период подготовки печи к плавке;
УW2 =1,08*0,9*(1 — 0,1)*(1 — 0)*(0,3*50) + 3,1 = 16,2 (МВт•ч) В сумму УW2 входят затраты энергии на изменение энтальпии нагреваемой и расплавляемой металлошихты с учётом энергетических затрат на возможные эндотермические процессы (испарение влаги, разложение оксидов железа железной руды, загружаемой одновременно с металлошихтой для ранней дефосфорации и т. п.), шлакообразующих материалов с учётом экзотермических процессов шлакообра зования, жидкого металла, нагреваемого выше температуры окончания плавления (ликвидуса) до температуры начала окислительного периода с учётом тепловых эффектов экзотермических реакций окисления элементов в ванне жидкого металла (на основе материального баланса).
В соответствии с заданными внешними условиями расчётное значение полной мощности электропечного трансформатора, составит:
(Sн) р = (УW2 / фэ + Р2 т. п.) / (kИ.•л?зэ);
где: фэ — длительность периода расплавления
kи — коэффициент использования номинальной мощности трансформатора.
kи = 1 — для печей с водоохлаждаемыми панелями л = 0,7 — коэффициент мощности для ДСП высокой и сверхвысокой мощности зэ = 0,95 — электрический к.п.д.
(Sн) р = (16,2/ 0,5 +2,31) / (1*0,7*0,95) = 52,19 (МВА)
2.5 Расчет параметров электрического режима — U, I и др
Высшая ступень вторичного линейного напряжения, равна Номинальную силу тока, протекающего через дугу, определяем по уравнению:
Низшую ступень вторичного линейного напряжения можно определить, зная минимально необходимую мощность для работы ДСП в конце технологического периода, когда происходит выдержка жидкого металла в условиях компенсации тепловых потерь Рт.п.в., (Рт.п.в =7 МВт) т. е.:
Smin = Рт.п.в / (л*зэ);
Smin = 7 / (0,7*0,95) = 10,53 (МВА) Определим глубину регулирования мощности:
Гs = Sн / Smin;
Гs = 52,19 / 10,53 = 4,9
Учитывая, что для современных ДСП глубина регулирования мощности составляет от 2,5 до 9, то полученное значение соответствует норме.
Определим глубину регулирования напряжения:
Гu = Гs½ = 4,9½ = 2,2
Учитывая, что для современных ДСП глубина регулирования напряжения составляет от 1,5 до 3, то полученное значение соответствует норме.
Проделанные расчёты позволяют оценить низшую ступень вторичного линейного напряжения согласно формуле:
U2 л.н. = U2 л.в. / Гu;
U2 л.н. = 672,69 / 2,2 = 305,77 (В)
2.6 Оценка диаметра графитизированных электродов
Электроды, предназначены для подвода электроэнергии в рабочее пространство дуговой печи. Для обеспечения нормальной работы дуговой печи электроды должны обладать достаточной механической прочностью и электропроводностью, иметь высокую термическую стойкость и хорошо противостоять окислению воздухом при высоких температурах. Этим требованиям отвечают электроды, изготовленные из углеродистых материалов. В дуговых сталеплавильных печах применяют электроды графитизированные, угольные, и комбинированные.
Таблица 4 — Основные физико-химические свойства графитизированных и угольных (в скобках) электродов
Плотность, г/см3: действительная кажущаяся | 2,2…2,23 1,55…1,7 | (1,9…2,05) (1,5…1,6) | |
Общая пористость, % | 23…30 | (18…25) | |
Кажущаяся пористость, кг/м3 | 1500…1700 | (1480…1650) | |
Механическая прочность, 10-5 Па: сжатие растяжение изгиб | 200…400 70…200 60…200 | (150…300) (30…70) (30…50) | |
Теплопроводность при 20 °C, кДж/(м*ч*град) | 420…100 | (84…20) | |
Удельное электросопротивление, 106 Ом*мм2/м | 8…12,5 | (20…30) | |
Допустимая плотность тока, А/см2 | 15…30 | (5,0…11,0) | |
Температура окисления, °С | 600…700 | (460…500) | |
Из приведённых данных видно, что графитизированные электроды обладают более высокими свойствами по сравнению с угольными. Как правило, графитизированные электроды используются в дуговых печах, предназначенных для выплавки сталей и сплавов различных марок. Диаметр электродов составляет от 75 до 555 мм по ГОСТ 4426–71. Для обеспечения требуемой плотности тока особенно при эксплуатации дуговых печей средней мощности используют графитизированные электроды диаметром 500 мм. Качество электродов и условия подвода к ним электрического тока существенно влияют на потери подводимой электроэнергии.
Для рассчитываемой печи, вместимостью 50 т, возьмём рекомендованные для отечественных ДСП конструкции ВНИИЭТО графитизированные электроды диаметром 500 мм.
2.7 Расчет технико-экономических показателей плавки в ДСП: производительность, расход электрической энергии
Зная длительность цикла плавки фпл., состоящего в общем случае из периода подготовки печи к плавке фП, периода расплавления металлошихты фЭ, окислительного ф0 и восстановительного фв периодов, для выбранного номинального значения полной мощности трансформатора Sн уточняем длительность периода расплавления:
фэ = УW2 / (kИ.•л?зэ • Sн — Р2т. п);
фэ = 16,2 / (1*0,7*0,95*52,19 — 2,31) = 0,50 (ч) Длительность плавки включает в себя:
фпл = фп + фэ + фО + фв;
фпл = 0,05 + 0,5 + 0,25 +0 = 0,8 (ч) Зная фактический фонд рабочего времени, определим производительность печи.
Суточная производительность:
Мс = 24*m0 / фпл;
Мс = 24*50 / 0,8 = 1500 (т/сут),
т.е. за одни сутки выплавляют 30 плавок.
Годовая производительность (при условии, что простои составляют 7% календарного времени), рассчитывается по формуле:
Мг = 8760*(1 — 0,01*Пр)*m0 / фпл;
Мг = 8760*(1 — 0,01*7)*50 / 0,8? 509 175 (т/год) где: Пр — величина простоев печи по техническим и организационным причинам.
8760 — годовой фонд времени, ч/год Рассчитываем расход электроэнергии за плавку согласно формуле:
Wс = [(УW2 + P2т. п*фэ) + (УW3 + Pт.п.о*ф0)] / зэ;
где: УW3 — полезные затраты энергии на проведение технологического периода;
Рт.п.о — мощность тепловых потерь в окислительный период;
Рт.п.в-мощность тепловых потерь в восстановительный период;
Принимаем Рт.п.о =8 МВт;
Wс = [(16,2+ 2,31*0,5) + (0 + 8*0,25)] / 0,95 = 20,37 (МВт•ч) Удельный расход электрической энергии на 1 т. жидкой стали:
Wу.ж. = Wс / m0;
Wу.ж. = 20,37/ 50 = 407,4 (кВт•ч/т)
3. Разработка технологии электроплавки, внепечной обработки и разливки заданной марки стали
3.1 Описание этапов выбранной технологии (плавка в ДСП, внепечная обработка, разливка)
Данную сталь можно выплавить в ДСП из лома и кокса. После металл отправляют на печь-ковш, где происходит легирование, доводка по химическому составу и температуре. После происходит разливка на МНЛЗ.
Ниже представлена схема выплавки стали марки 40Х13.
Действующие в электросталеплавильных цехах технологические инструкции (частные) содержат перечень практических приёмов выполнения отдельных производственных операций при выплавке стали в дуговых печах и определяющие показатели плавки (температуру металла, расход кислорода, состав и количество шлаковой смеси и раскислителей и т. д.), характеризующие особенность технологического процесса. Разнообразие конструкций дуговых печей и отличие условий их эксплуатации ограничивают унификацию технологических процессов и позволяют сформулировать только их отдельные общие положения и правила в применении к отдельным группам марок стали.
Выплавку стали конструкционных марок осуществляют только на печи с хорошим состоянием футеровки, используя шихтовые материалы нормального и повышенного качества, отвечающие требованиям установленной технологии. Сталь выплавляют преимущественно в крупных печах с использованием в завалке никеля. Шихту составляют из 20…30% мелкого, 40…60% среднего, 20…30% крупного лома (в том числе чугуна), таким образом, чтобы загрузить все материалы в один — два приёма. На дно загрузочной корзины помещаем мелкий лом, затем тяжёлый (крупный с массой кусков более 3000 кг) и средним, а наверху мелкий лом и чугун. Кокс или электродный бой загружаем в корзину на легковесный лом. Ферросплавы для легирования прокаливаем при температуре не ниже 600 °C.
Известь применяем свежеобожжённую с содержанием недопала не более 10% без признаков гашения с размером кусков 20…80 мм. Содержание влаги в шлакообразующих материалах и руде (агломерате), а также в кислороде не должно превышать, соответственно, 1,5% и 0,8 г/см3. Содержание влаги в порошках кокса, ферросилиция и алюминия (размер частиц менее 1 мм) не должно быть более 1%. Чтобы ускорить выплавку полупродукта, применяем одношлаковый процесс, так же для этого период расплавления совмещаем с периодом окисления. Ускорения плавления шихты в 100-тонной дуговой печи достигают использованием топливно-кислородных горелок и кислорода (продувка через трубки с интенсивностью 6…10 м3/мин). После образования колодца и оседания шихты в зоне электродов в печь подаём кислород через сводовую фурму с расходом 1000…1500 м3/ч. При проплавлении завалки расход кислорода увеличиваем до 1500…2000 м3/ч и поддерживаем этот уровень до отбора первой пробы металла на химический анализ. При этом должно быть израсходовано 85…90% электроэнергии от установленного электрическим режимом количества на период расплавления садки. В печи в это время наблюдаем «осевшую» ванну с жидким активным шлаком без видимых остатков нерасплавленной шихты в середине ванны и наличии 10…15% на откосах. Содержание углерода в первой пробе должно быть не менее чем на 0,1% выше верхнего марочного предела. После полного расплавления шихты отбирают вторую пробу металла на полный химический анализ.
На печи — ковше проводим науглероживание металла и осадочное раскисление ванны присадками алюминия и ферросплавов.
Шлак периода доводки образуют присадкой в печь, 10 кг/т извести. При достаточно нагретом металле трансформатор переключают на более низкое напряжение. После получения жидкоподвижного шлака измеряем температуру металла (должна составлять 1560…1580 °С), отбираем две пробы и присаживаем требуемые ферросплавы для легирования.
Сливаем металл и шлак из печи интенсивно, обеспечивая их активное перемешивание. Температура металла перед и после выпуска плавки равна соответственно 1580…1610 и 1560…1590 °С. Содержание (FeO) в шлаке после выпуска из печи не должно быть более 2%. продолжительность доводки 20…60 мин.
Данную сталь можно разлить на МНЛЗ в блюмовые заготовки.
3.2 Расчет состава и массы металлозавалки для ДСП
Таблица 5 — Химический состав стали 40Х13, %
Сталь | C | Mn | Si | Cr | S н. б | P н. б | Cu | Fe, % | |
40Х13 | 0,39 | 0,6 | 0,6 | 0,025 | 0,03 | 0.3 | 84,75 | ||
Таблица 6 — Состав компанентов металлошихты
Материал | C, % | Mn, % | Si, % | Cr, % | S, % | P, % | Fe, % | |
Угл. лом | 0,2 | 0,4 | 0,3 | 0,1 | 0,03 | 0,04 | 98,94 | |
Таблица 6 — Состав компонентов кокса
Материал | C, % | зола (10%) | ||
Al2O3, % | SiO2, % | |||
кокс | ||||
Определим расход лома. В данном случае железо перейдет только из лома. Определим сколько необходимо лома
mлома=50 000*(96,1−0)/(98,94*0,92) = 52 787,81 кг.
Определим количество кокса. Для этого нужно определить сколько нужно сжечь углерода. Содержание углерода в шихте должно быть на 0,5…0,6% выше нижнего предела в стали заданной марки.
mкокса=50 000*(0,7−0,2)/(90*0,5)=555,55 кг Таблица 7 — Элементный состав шихты
Количество элемента, вносимого каждой составляющей металлошихты, кг | ||||||||||
М-л | кг | C | Mn | Si | Cr | S | P | Fe | ||
Кокс | 555,55 | |||||||||
Угл. лом | 52 787,81 | 105,57 | 211,15 | 158,36 | 52,79 | 15,84 | 21,11 | 52 228,26 | 52 787,81 | |
53 343,36 | 355,57 | 211,15 | 158,36 | 52.79 | 15.84 | 21.11 | 52 228.26 | 53 343.36 | ||
% | 0,48 | 0,30 | 0,30 | 0,03 | 0,03 | 98,47 | ||||
3.3 Выбор легирующих материалов и раскислителей
Часть легирующих вводится в ковш, а оставшаяся часть в УКП.
Практикой выработался определенный режим введения раскислителей в ковш, обеспечивающий наиболее полное их усвоение. Требования к введению раскислителей в ковш сводятся к следующим основным положениям.
Во-первых, наиболее полное растворение раскисляющих добавок в металл происходит в том случае, если они вводятся в металл равномерно или небольшими порциями в период, когда количество металла в ковше возрастает от 20 до 50%.
Во-вторых, сначала в металл вводится марганец, имеющий относительно невысокое сродство к кислороду, затем кремний и в последнюю очередь алюминий, являющийся наиболее сильным раскислителем. Такая последовательность введения обеспечивает наиболее полное использование раскисляющей способности добавок.
В-третьих, при расчете расхода ферросплавов для раскисления и легирования необходимо учитывать остаточное содержание в металле после продувки тех элементов, которые вносятся ферросплавами, а также учитывать их угар.
Расход ферросплава определяем по формуле где GФ — расход ферросплава, кг;
[E]С — среднее содержание элемента (марганца или кремния) в заданной марке стали, %;
[E]М — остаточное содержание элемента в металле, %;
[E]Ф — содержание элемента в ферросплаве, %;
зС — коэффициент усвоения раскисляющих и легирующих элементов из ферросплавов для выплавки стали в дуговых электропечах, в долях.
Тогда При раскислении ферромарганцем масса жидкой стали увеличивается. Это увеличение необходимо учитывать при расчете расхода ферросилиция. Увеличение массы металла почти в точности равно массе ферромарганца.
Следовательно, масса металла после раскисления ферромарганцем составит:
49 484.69 + 266,6 = 49 751,29 кг.
Тогда
Аналогично рассчитываем расход феррохрома:
Расход алюминия на раскисление выбираем с учетом кислорода растворённого в металле и перешедшего в виде оксидов из печного шлака в УПК. Алюминий вводим перед выпуском стали из УКП.
сталь свод печь ферросплав
3.4 Выбор шлакообразующих материалов, науглероживателей, окислителей и их количество
Науглероживание будем осуществлять коксом: С= 90%, зола= 10%. Масса кокса была определена выше.
Основным шлакообразующим материалом, способствующим удалению из стали вредных примесей (серы и фосфора), является обожжённая известь СаО, вводимая в завалку из расчёта 30 кг на тонну металла. Плавиковый шпат в окислительном шлаке не нужен.
Будем считать, что известь состоит СаО=91% SiO2 = 5, MgO=2; Al2O3= 2%
Кроме того в шлакообразовании участвует футеровка печи. Примем расход заправочного материала (MgO — магнезита) 2 кг/т на плавку. Для интенсификации окислительных процессов в металл необходимо вводить кислород. Источниками кислорода служат железная руда, окалина и агломерат. При получения данной марки стали в качестве окислителя будем использовать только газообразный кислород. Железная руда замедляет процесс плавления, так как присаживаемая руда постоянно охлаждает металл.
1 Конструкции и проектирование агрегатов сталеплавильного производства. Григорьев В. П., Нечкин Ю. М., Егоров А. В., Никольский Л. Е.: Учебник для вузов. — М.: МИСиС, 1995. — с. 512.
2 Оборудование и проектирование электросталеплавильных цехов. Никольский Л. Е. Зинуров И.Ю.: Учебное пособие для вузов. — М.: Металлургия, 1993. — с. 272.
3 Основы проектирования и оборудование сталеплавильных и доменных цехов. Якушев А. М. — М.: Металлургия, 1992. — с. 422.
4 Белянчиков Л. Н., Григорян В. А., Котельников Г. И., Островский О. И., Пономаренко А. Г., Стомахин А. Я., Уточкин Ю. И. Физико-химические расчеты электросталеплавильных процессов. — М.: Металлургия. 1989.
5 Внепечная обработка стали: Учебник для вузов. Поволоцкий Д. Я., Кудрин В. А., Вишкарев А. Ф. — М.: МИСиС. 1995.
6 Технологические инструкции «Днепроспецсталь'
7 Электрометаллургия стали и ферросплавов. Поволоцкий Д. Я., Рощин В. Е., Рысс М. А., Строганов А. И., Ярцев М. А. — Учебник для вузов. — М.: Металлургия. 1984.