Бурение скважин на нефть и газ
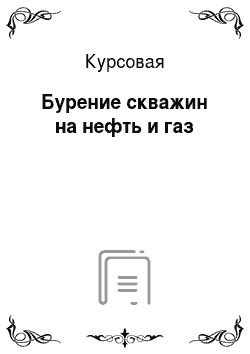
Плотность бурового раствора должна быть такой, чтобы гидростатическое давление в скважине превышало пластовое на 2−15%. Но для сохранения высокой производительности и низкой себестоимости бурения необходимо поддерживать минимально необходимое превышение давления. скважина колонна бурение цементирование Объем жидкости в запасных емкостях должен превышать объем скважины в 1,5−3 раза. Раствор… Читать ещё >
Бурение скважин на нефть и газ (реферат, курсовая, диплом, контрольная)
Содержание Введение
1. Ход решения работы
1.1 Выбор конструкции скважины
1.2 Расчет эксплуатационной и технической колонн на прочность
1.3 Расчет цементирования эксплуатационной колонны
1.4 Определение продолжительности цементирования обсадной колонны
1.5 Выбор буровой установки
1.6 Режим бурения
2. Теоретическая часть
3. Мероприятия по технике безопасности
4. Осложнения при бурении скважины на газ (газопроявление) Заключение Список используемой литературы Введение Бурение — процесс сооружения горной выработки цилиндрической формы — скважины, шпура или шахтного ствола — путём разрушения горных пород на забое, бурение осуществляется, как правило, в земной коре, реже в искусственных материалах (бетоне, асфальте и др.). В ряде случаев процесс бурения включает крепление стенок скважин (как правило, глубоких) обсадными трубами с закачкой цементного раствора в кольцевой зазор между трубами и стенками скважин.
Область применения бурения многогранна: поиски и разведка полезных ископаемых; изучение свойств горных пород; добыча жидких, газообразных и твёрдых (при выщелачивании и выплавлении) полезных ископаемых через эксплуатационные скважины; производство взрывных работ; выемка твёрдых полезных ископаемых; искусственное закрепление горных пород (замораживание, битумизация, цементация и др.); осушение обводнённых месторождений полезных ископаемых и заболоченных районов; вскрытие месторождений; прокладка подземных коммуникаций: сооружение свайных фундаментов и др.
Бурение скважин на нефть и газ. В Китае свыше 2 тыс. лет назад впервые в мировой практике вручную бурились скважины (диаметром 12—15 см и глубиной до 900 м) для добычи соляных растворов. Буровой инструмент (долото и бамбуковые штанги) опускался в скважину на канатах толщиной 1—4 см, свитых из индийского тростника. Бурение первых скважин в России относится к 9 в. и связано с добычей растворов поваренной соли (Старая Русса). Затем соляные промыслы развиваются в Балахне (12 в.), в Соликамске (16 в.). На русских соляных промыслах издавна применялось ударное штанговое бурение. Во избежание ржавления буровые штанги делали деревянными; стенки скважин закрепляли деревянными трубами. Первый буровой колодец, закрепленный трубами, был пробурен на воду в 1126 в провинции Артуа (Франция), отсюда глубокие колодцы с напорной водой получили название артезианских.
Развитие методов и техники бурения в России начинается с 19 в. в связи с необходимостью снабжения крупных городов питьевой водой. В 1831 в Одессе было образовано «Общество артезианских фонтанов» и пробурены 4 скважины глубиной от 36 до 189 м. В 1831—32 бурили скважины в Петербурге (на Выборгской стороне), в 1833 в Царском Селе, в Симферополе и Керчи, в 1834 в Тамбове, Казани и Евпатории, в 1836 в Астрахани. В 1844 была заложена первая буровая скважина для артезианской воды в Киеве. В Москве первая артезианская скважина глубиной 458 м пробурена на Яузском бульваре в 1876. Первая буровая скважина в США пробурена для добычи соляного раствора близ Чарлстона в Западной Виргинии (1806).
Поворотным моментом, с которого начинается бурный прогресс в бурения, было развитие нефтедобычи. Первая нефтяная скважина была пробурена в США случайно в 1826 близ Бернсвилла в Кентукки при поисках рассолов. Первую скважину на нефть заложил в 1859 американец Дрейк близ г. Тайтесвилла в Пенсильвании. 29 августа 1859 нефть была встречена на глубине 71 фута (около 20 м), что положило начало нефтяной промышленности США. Первая скважина на нефть в России пробурена в 1864 около Анапы (Северный Кавказ).
Технические усовершенствования бурения в 19 в. открываются предложением немецкого инженера Эйгаузена (1834) применять так называемые ножницы (сдвигавшаяся пара звеньев при штанговом бурении). Идея сбрасывать соединённое со штангами долото привела к изобретению во Франции Киндом (1844) и Фабианом (1849) свободно падающего бурового инструмента («фрейфала»). Этот способ получил название «немецкий». В 1846 французский инженер Фовель сделал сообщение о новом способе очистки буровых скважин водяной струей, подаваемой насосом с поверхности в полую штангу. Первый успешный опыт бурения с промывкой проведён Фовелем в Перпиньяне (Франция).
В 1859 Г. Д. Романовский впервые механизировал работы, применив паровой двигатель для бурения скважины вблизи Подольска. На нефтяных промыслах Баку первые паровые машины появились в 1873, а через 10 лет почти повсеместно они заменили конную тягу. При бурении скважин на нефть на первом этапе получил развитие ударный способ (бурение штанговое, канатное, быстроударное с промывкой забоя). В конце 80-х гг. в Новом Орлеане в Луизиане (США) внедряется роторное бурение на нефть с применением лопастных долот и промывкой глинистым раствором. В России вращательное роторное бурение с промывкой впервые применили в г. Грозном для бурения скважины на нефть глубиной 345 м (1902). В Сураханах (Баку) на территории завода Кокорева в 1901 заложена скважина для добычи газа. Через год с глубины 207 м был получен газ, использовавшийся для отопления завода. В 1901 на Бакинских нефтепромыслах появились первые электродвигатели, заменившие паровые машины при бурении. В 1907 пройдена скважина вращательным бурением сплошным забоем с промывкой глинистым раствором.
Впервые автомат для регулирования подачи инструмента при роторном бурении был предложен в 1924 Хилдом (США). В начале 20 в. в США разработан метод наклонного роторного бурения с долотами малого диаметра для забуривания с последующим расширением скважин.
Ещё в 70-х гг. 19 в. появились предложения по созданию забойных двигателей, то есть размещению двигателя непосредственно над буровым долотом у забоя буримой скважины. Созданием забойного двигателя занимались крупнейшие специалисты во многих странах, проектируя его на принципе получения энергии от гидравлического потока, позднее — на принципе использования электрической энергии. В 1873 американский инженер Х. Г. Кросс запатентовал инструмент с гидравлической одноступенчатой турбиной для бурения скважин. В 1883 Дж. Вестингауз (США) сконструировал турбинный забойный двигатель. Эти изобретения не были реализованы, и проблема считалась неосуществимой. В 1890 бакинский инженер К. Г. Симченко запатентовал ротационный гидравлический забойный двигатель. В начале 20 в. польский инженер Вольский сконструировал быстроударный забойный гидравлический двигатель (так называемый таран Вольского), который получил промышленное применение и явился прототипом современных забойных гидроударников.
Впервые в мировой практике М. А. Капелюшниковым, С. М. Волохом и Н. А. Корневым запатентован (1922) турбобур, примененный двумя годами позже для бурения в Сураханах. Этот турбобур был выполнен на базе одноступенчатой турбины и многоярусного планетарного редуктора. Турбобуры такой конструкции применялись при бурении нефтяных скважин до 1934. В 1935—39 П. П. Шумилов, Р. А. Иоаннесян, Э. И. Тагиев и М. Т. Гусман разработали и запатентовали более совершенную конструкцию многоступенчатого безредукторного турбобура, благодаря которому турбинный способ бурения стал основным в СССР. Совершенствование турбинного бурения осуществляется за счёт создания секционных турбобуров с пониженной частотой вращения и увеличенным вращающим моментом.
В 1899 в России был запатентован электробур на канате. В 30-х гг. в США прошёл промышленные испытания электробур с якорем для восприятия реактивного момента, опускавшийся в скважину на кабеле-канате. В 1936 впервые в СССР Квитнером и Н. В. Александровым разработана конструкция электробура с редуктором, а в 1938 А. П. Островским и Н. В. Александровым создан электробур, долото которого приводится во вращение погружным электродвигателем. В 1940 в Баку электробуром пробурена первая скважина.
В 1951—52 в Башкирии при бурении нефтяной скважины по предложению А. А. Минина, А. А. Погарского и К. А. Чефранова впервые применили электробур знакопеременного вращения для гашения реактивного момента, опускаемый на гибком электрокабеле-канате. В конце 60-х гг. в СССР значительно усовершенствована конструкция электробура (повышена надёжность, улучшен токопровод).
Появление наклонного бурения относится к 1894, когда С. Г. Войслав провёл этим способом скважину на воду близ Брянска. Успешная проходка скважины в Бухте Ильича (Баку) по предложению Р. А. Иоаннесяна, П. П. Шумилова, Э. И. Тагиева, М. Т. Гусмана (1941) турбинным наклонно-направленным бурением положила начало внедрению наклонного турбобурения, ставшего основным методом направленного бурения в СССР и получившего применение за рубежом. Этим методом при пересечённом рельефе местности и на морских месторождениях бурят кусты до 20 скважин с одного основания. В 1938—41 в СССР разработаны основы теории непрерывного наклонного регулируемого турбинного бурения при неподвижной колонне бурильных труб. Этот метод стал основным при бурении наклонных скважин в СССР и за рубежом.
В 1941 Н. С. Тимофеев предложил в устойчивых породах применять так называемое многозабойное бурение.
В 1897 в Тихом океане, в районе о. Сомерленд (Калифорния, США), впервые было осуществлено бурение на море. В 1924—25 в СССР вблизи бухты Ильича на искусственно созданном островке вращательным способом была пробурена первая морская скважина, давшая нефть с глубины 461 м. В 1934 Н. С. Тимофеевым осуществлено на острове Артема в Каспийском море кустовое бурение, при котором несколько скважин бурятся с общей площадки, а в 1935 там же сооружено первое морское металлическое основание для бурения в море. С 50-х гг. 20 в. применяется бурение для добычи нефти и газа со дна моря. Созданы эстакады, плавающие буровые установки с затапливаемыми понтонами, специальные буровые суда, разработаны методы динамической стабилизации буровых установок при бурении на больших глубинах.
Основной метод бурения на нефть и газ в СССР (1970) — турбобурами (76% метража пробуренных скважин), электробурами пройдено 1,5% метража, остальное роторным бурением. В США преимущественно распространение получило роторное бурение; в конце 60-х гг. при проведении наклонно-направленных скважин начали применяться турбобуры. В странах Западной Европы турбобуры применяются в наклонном бурении и при бурении вертикальных скважин алмазными долотами. В 60-е гг. в СССР заметно возросли скорости и глубина бурения на нефть и газ. Так, например, в Татарии скважины, бурящиеся долотом диаметром 214 мм на глубину 1800 м, проходятся в среднем за 12—14 дней, рекордный результат в этом районе 8—9 дней. За 1963—69 в СССР средняя глубина эксплуатационных нефтяных и газовых скважин возросла с 1627 до 1710 м. Самые глубокие скважины в мире — 7—8 км — пробурены в 60-е гг. (США). В СССР в районе г. Баку пробурена скважина на глубину 6,7 км и в Прикаспийской низменности (район Аралсор) на глубину 6,8 км. Эти скважины пройдены в целях разведки на нефть и газ. Работы по сверхглубокому бурению для изучения коры и верхней мантии Земли ведутся по международной программе «Верхняя мантия Земли». В СССР по этой программе намечено пробурить в 5 районах ряд скважин глубиной до 15 км. Первая такая скважина начата бурением на Балтийском щите в 1970. Эта скважина проходится методом турбинного бурения.
Основное направление совершенствования бурения на нефть и газ в СССР — создание конструкций турбобуров, обеспечивающих увеличение проходки скважины на рейс долота (полное время работы долота в скважине до его подъёма на поверхность). В 1970 созданы безредукторные турбобуры, позволяющие осуществить оптимизацию режимов Б. шарошечными долотами в диапазоне наиболее эффективных оборотов (от 150 до 400 в мин) и использовать долота с перепадом давлений в насадках до 10 Мн/м2 (100 атм) вместо 1—1,5 Мн/м2 (10—15 атм). Создаются турбобуры с высокой частотой вращения (800—100 об/мин) для бурения алмазными долотами, обеспечивающими при глубоком бурении многократное увеличение проходки и механической скорости бурения за рейс. Разрабатываются новые конструкции низа бурильной колонны, позволяющие бурить в сложных геологических условиях с минимальным искривлением ствола скважины. Ведутся работы по химической обработке промывочных растворов для облегчения и повышения безопасности процесса бурения. Конструируются турбины с наклонной линией давления, которые позволяют получить информацию о режиме работы турбобура на забое скважины и автоматизировать процесс бурения.
Элементы конструкции скважин приведены на рис. 1. Начальный участок I скважин называют направлением. Поскольку устье скважины лежит в зоне легкоразмываемых пород его необходимо укреплять. В связи с этим направление выполняют следующим образом. Сначала бурят шурф — колодец до глубины залегания устойчивых горных пород (4−8 м). Затем в него устанавливают трубу необходимой длины и диаметра, а пространство между стенками шурфа и трубой заполняют бутовым камнем и заливают цементным раствором 2.
Рис. 1. Конструкция скважины:
1 — обсадные трубы; 2 — цементный камень; 3 — пласт; 4 — перфорация в обсадной трубе ицементном камне; I — направление; II — кондуктор; III — промежуточная колонна; IV — эксплуатационная колонна.
Нижерасположенные участки скважины — цилиндрические. Сразу за направлением бурится участок на глубину от 50 до 400 м диаметром до 900 мм. Этот участок скважины закрепляют обсадной трубой 1 (состоящей из свинченных стальных труб), которую называют кондуктором II.
Затрубное пространство кондуктора цементируют. С помощью кондуктора изолируют неустойчивые, мягкие и трещиноватые породы, осложняющие процесс бурения.
После установки кондуктора не всегда удается пробурить скважину до проектной глубины из-за прохождения новых осложняющих горизонтов или из-за необходимости перекрытия продуктивных пластов, которые не планируется эксплуатировать данной скважиной. В таких случаях устанавливают и цементируют еще одну колонну III, называемую промежуточной. Если продуктивный пласт, для разработки которого предназначена скважина, залегает очень глубоко, то количество промежуточных колонн может быть больше одной.
Последний участок IV скважины закрепляют эксплуатационной колонной. Она предназначена для подъема нефти и газа от забоя к устью скважины или для нагнетания воды (газа) в продуктивный пласт с целью поддержания давления в нем. Во избежание перетоков нефти и газа в вышележащие горизонты, а воды в продуктивные пласты пространство между стенкой эксплуатационной колонны и стенкой скважины заполняют цементным раствором.
Для извлечения из пластов нефти и газа применяют различные методы вскрытия и оборудования забоя скважины. В большинстве случаев в нижней части эксплуатационной колонны, находящейся в продуктивном пласте, простреливают (перфорируют) ряд отверстий 4 в стенке обсадных труб и цементной оболочке.
В устойчивых породах призабойную зону скважины оборудуют различными фильтрами и не цементируют или обсадную колонну опускают только до кровли продуктивного пласта, а его разбуривание и эксплуатацию производят без крепления ствола скважины.
Устье скважины в зависимости от ее назначения оборудуют арматурой (колонная головка, задвижки, крестовина и др.).
При поисках, разведке и разработке нефтяных и газовых месторождений бурят опорные, параметрические, структурные, поисковые разведочные, эксплуатационные, нагнетательные, наблюдательные и другие скважины.
Опорные скважины закладываются в районах, не исследованных бурением, и служат для изучения состава и возраста слагающих их пород.
Параметрические скважины закладываются в относительно изученных районах с целью уточнения их геологического строения и перспектив нефтегазоносности.
Структурные скважины бурятся для выявления перспективных площадей и их подготовки к поисково-разведочному бурению.
Поисковые скважины бурят с целью открытия новых промышленных залежей нефти и газа.
Разведочные скважины бурятся на площадях с установленной промышленной нефтегазоносностью для изучения размеров и строения залежи, получения необходимых исходных данных для подсчета запасов нефти и газа, а также проектирования ее разработки.
Эксплуатационные скважины закладываются в соответствии со схемой разработки залежи и служат для получения нефти и газа из земных недр Нагнетательные скважины используют при воздействии на эксплуатируемый пласт различных агентов (закачки воды, газа и т. д.).
Наблюдательные скважины бурят для контроля за разработкой залежей (изменением давления, положения водонефтяного и газонефтяного контактов и т. д.).
Кроме того при поиске, разведке и разработке нефтяных и газовых месторождений бурят картировочные, сейсморазведочные, специальные и другие скважины.
1. Ход решения работы Дано:
1) Скважина на газ
2) Глубина 3000 м.
3) Пластовое давление 29 мПа = 290 атмосфер
4) Дебит 75 000 м3/сут.
5) Перетек жидкости из пласта 1900;1950 м.
6) Разрез П2−4
Разрез П2−4:
1) Лесовидные суглинки и галечник из песчаника 0−70 м.
2) Песчаники известковые, глинистые, различной цементации, глины
70−600 м.
3) Песчаники кварцевые 600−2000 м.
4) Глины известковые и чистые, неравномерно песчанистые, мергели
2000;2400 м.
5) Известняки 2400−2600 м.
6) Пески серые и темно-серые 2600−2800 м.
7) Песчаники 2800−3000 м.
Продуктивная толща 2840−2950 м.
1.1 Выбор конструкции скважины Выбор конструкции скважины определяется рядом факторов, основными из которых являются: целевое назначение скважины; конечный диаметр; глубина; наличие бурового оборудования.
Конструкция скважины должна отвечать следующим требованиям:
— качественное опробование и вскрытие продуктивных пластов с целью их эксплуатации;
— надежная изоляция пластов друг от друга;
— минимальная металлоемкость;
— простота сооружения и минимальная стоимость;
— надежность эксплуатации скважины и возможность проведения ремонтных работ.
Определение числа обсадных колон
Название колонны | Глубина | Диаметр колонны | Диаметр долота | Схема | |
Шахтное направление (Ш.н) | 40 м. | 339,7 мм. | 444,5 мм. | ||
Кондуктор (К.) | 600 м. | 242,9 мм. | 295,3 мм. | ||
Промежуточное направление (П.к) | 1960 м. | 168,3 мм. | 212,7 мм. | ||
Эксплуатационная колонна (Э.к) | 3000 м. | 114,3 мм. | 146,1 мм. | ||
Определение длины обсадных колон:
Lш.к = 40 м. (т.к. Lскв. > 2500 м.) — глубина шахтного направления
Lк. —? — глубина кондуктора:
Lmin= V1/V + 10 = (7,84/0,191)+10 = 51,047 м.
где V1 = (d2б.тр — d2вн.б.тр)*Lпр.к = (0,1682−0,1542)*1960 = 0,004*1960 = 7,84
V = П* d2вн. к / 4 = 3,14*0,2432 = 0,191
Lп.к = 1960 м. (Lп.к. = Lоп. уч + 10 м.) — глубина промежуточных колон
Lэ.к = 3000 м. (глубина всей скважины) — глубина эксплуатационных колон Определяем диаметры обсадных колон (Д) и диаметры долот (Дд.)
Диаметр эксплуатационных колон (Дэ.к) и диаметр долота (Драсчд.э.к):
Дэ.к = 114.3м. (т.к. суммарный дебит <75тыс.м3/сут — см. тыбл.1);
Драсчд.э.к = Дм.э.к + 2д = 127+15 = 142? 146,1 мм. (округл. по ГОСТ (см. табл.4))
Диаметр промежуточных колон (Дп.к.) и диаметр долота (Драсчд.п.к):
Драсчп.к. = Драсчд.э.к+6+2д = 146,1+6+2*8 = 158? 168,3 (ГОСТ (см. табл.3)); Драсчд.п.к = Дм.п.к+2д = 187,7+25 = 212,7 мм.
Диаметр кондуктора (Дк.) и диаметр долота (Драсчд.к):
Драсчк. = Драсчд.п.к+6+2д = 212,7+6+18 = 236,7? 242,9 (округл. по ГОСТ (см. табл.3));
Драсчд.к = Дм. к+2д = 249,9+25 = 294,9? 295,3 мм. (округл. по ГОСТ (см.табл4))
Диаметр шахтного направления (Дш.н) и диаметр долота (Драсчд.ш.н):
Драсчш.н = Драсчд. к+8+2*10 = 295,3+8+28 = 331,3 ?339,7 мм. (Гост (см. табл.3));
Драсчд.ш.н = Дм.ш.к+2д = 365,1+35 = 400,1? 444,5 (округл. по ГОСТ (см. табл.4))
где Дм. — диаметр муфты; 2д — разность диаметров.
1.2 Расчет эксплуатационной и технической колонн на прочность
1. Растяжение от сил собственного веса колонны — Pстр.
2. Под действием сил внешнего давления Pсм. — сминающие усилия, со стороны горной породы и плотности бурового раствора или цементного раствора.
3. Разрушение под действием внутреннего давления — в процессе вскрытия перфорации обсадных колонн — Pвн.
Материалы стали, из которых изготавливаются обсадные колонны:
С | Д | К | Е | Л | М | Р | Т | ||
Ур. | |||||||||
Толщина стенки д=(6,5−12)мм.
Кондуктор рассчитывается (при глубине спуска до 100 м.) на максимальное понижение уровня жидкости в нем, и если глубина спуска кондуктора более 400 м. на страгивание.
Колонны любого диаметра, спускающиесяся на глубину до 400 м., подбираются без рассчета из труб стали Д с минимальной толщиной стенки, находящейся в стандарте для данного диаметра труб. Промежуточная колонна рассчитывается на Pстр. и Pвн. Эксплуатационная колонна рассчитывается на Pстр., Pвн. и Pсм.
Lк = (V1/V) + 10 м.
где V1=(П/4)*(Д2б.т — d2вн.б.т)*Lпр.к — максимальный объем бурильной трубы для бурения под следующую колонну
V=(П/4)*d2вн.к (м3) — объем 1-го метра кондуктора Расчет промежуточной колонны:
Дано: Дп. к = 168,3 мм.;
Lп.к = 1960 м.;
с = 1,2 г/см3.
Найти: Рстр, Рвн. Решение:
1) Кстр < Рстр/уп.к — коэффициент запаса прочности на стягивание (при Д < 219 мм., Кстр=1,1; при Д > 219 мм., Кстр=1,15).
2) Lп. к = Рстр/Кстр*qп.к = 73 000/1.1*26,8 = 73 000/29,48 = 2476 м. (Рстр, qп. к взяли из таблицы прочностных характеристик обсадных труб)
— Выбираем трубы с минимальной толщиной стенки, материал труб Д
— Рассчитываем возможную глубину спуска выбранной колонны
3) Условие прочности колонны:
Рвн > Квн*Рвн.ф где Квн = 1,5 (для промеж. колонны),
Рвн.ф = ((hц — hо)/10)*(сц.р — сг. р) + (L п. к/100) + 20 = ((1960 — 20)*(1,85 — 1,2)/10) + (1960/100) +20 = ((1940*0,65)/10) + 39,60 = 165,7
где hц — высота цементирования колонны; hо — пенек (20м.); сц. р = 1,85 г/см3; сг. р = 1,2 г/см3.
Расчет эксплуатационной колонны на прочность:
Дано: Дэ. к = 114,3 мм., Lэ. к = 3000 м., сн = 1,2 г/см3, сб. р = 0,85 г/см3, ИПП = 2840−2950 м. Найти: Рстр, Рвн, Рсм Решение:
1) Найдем Рсм
Толщина стенки бмм. | |||||
Рсм, материал: Д | |||||
Рсм, материал К | |||||
Из таблицы принимаем самый дешевый материал: «Д» и рассчитываем для него
Lmax = 10*Рсм/Ксм* сб. р: Lmax1 = 10*240/1,15*1.2 = 1739 м. — сталь Д Lmax2 = 10*315/1,15*1.2 = 2283 м. — сталь Д Lmax3 = 10*385/1,15*1.2 = 2790 м. — сталь Д Lmax4 = 10*455/1,3*1.2 = 2917 м. — сталь Д Lmax5 = 10*485/1,3*1.2 = 3108 м. — сталь К
№ | Марка стали | Толщина б, мм | Глубина, м | Длина секции l, м. | q1, кг/м | Вес секции q*l, кгс. | Вес колонны от забоя | ||
от | до | ||||||||
Д | 16,4 | ||||||||
Д | 18,9 | ||||||||
Д | 21,4 | ||||||||
Д | 24,0 | ||||||||
К | 21,4 | ||||||||
2) Найдем Рстр.
д, мм. | ||||||
Материал | Д | Д | Д | Д | К | |
Рстр.ст | ||||||
Gфак. = Gэк. + Gдоп. тс где Gдоп. = (Ргидр. + Рстоп.)*П*d2вн/4
Ргидр. = 0,02*Lэк. + 16 = 0,02*3000+16 = 76 атм.
Рстоп. = (15−20) атм.
Ш Gдоп. = (76+20)*0,785*96,04 = 7237 кгс = 7,3 т.
Ш Gфакт. = 54 475 + 7237 = 61 712,7 кгс.
Кстр.? Рстр./Gфакт. где Кстр. = 1,15
Ш 45/61,7 = 0,729? Кстр.
Ш 45/(61,7−28,52) = 1,356? Кстр.
Т.к первое значение не сходится, то следует материал 1-ой трубы и толщину стенки заменить: материал К; толщина стенки = 7 мм.
Квн.? Рвн./Рфакт. где Квн. = 1,5; Рвн. = 465; Рфакт. = 290
Рвн./Рфакт. = 465/290 = 1,6 Кстр.
1.3 Расчет цементирования эксплуатационной колонны Основная цель цементирования — получение прочного водогазонефтенепроницаемого, концентрично расположенного в затрубном пространстве кольца цементного камня, который по всей высоте обеспечивал бы разобщение и надежную изоляцию вскрытых скважиной продуктивных горизонтов и зон осложнений.
Способ цементирования выбирается в зависимости от температуры в ее стволе, опасности поглощения при заданной высоте подъема цементного раствора и возникновения затрубных проявлений в период ОЗЦ для каждой конкретной скважины.
Расчет цементирования сводится к определению:
— потребного количества сухого цемента, воды, промывочной жидкости;
— конечного давления при цементировании и выбора типа и потребного количества цементировачных агрегатов и цементно-смесительных машин;
— продолжительности цементирования.
Дано: Дд. эк = 146,1 мм., Дэк. = 114,3 мм., dвн.эк. = 98,3 мм., hц.эк. = 3000 м., Lэк. = 3000 м., h0 = 20 м., гпр.ж. = 1,0, m = В/ц = 0,5
Решение:
Определение потребляемого количества сухого цемента, воды, продавочной жидкости при цементировании обсадной колонны:
Определение потребного количества цементного раствора:
г ц.р. = (р/4)*[(kІ*DІ-dІ)*hц + h0*dІв ] = = 0,785*((1,22 *0,1462 — 0,1142)*3000 + 20*0,0982 = = 0,785*((1,44*0,0213 — 0,013)*3000 + 0,192) = = 0,785*((0,031 — 0,013)*3000 + 0,192) = 0,785*54,192 = 42,541 м3
где k — коэффициент увеличения ствола скважины (k = 1.1−1.25)
Определение удельного веса цементного раствора:
г ц.р. = (гц*гв*(1+m))/(m*гц +гв) = 3,15*1,0*(1 + 0,5) / (0,5*3,15 + 1) = = 4,725 / 2,575 = 1,835 г/см3
где гц, гв — соответственно удельный вес сухого цемента и воды m — водоцементное отношение.
Определение потребного количества сухого цемента:
Qц = e*(1/1+m)* гц.р.* Vц.р. = (1,04 / (1+0,5))*1,83*42,541 = 54 Т.
где e — коэффициент, учитывающий потери сухого цемента при транспортировке и затворении (e = 1.03−1.05)
Определение потребного раствора количества воды для затворения цемента:
Vв = m*Qц = 0,5*54 = 27 м3
Определение объема продавочной жидкости:
Vпр. = ?*(р/4)*dІвн.ср. *(L-h0) = 1,04*0,785*0,0982 *(3000−20) = = 0,0096*2432,9 = 23,4 м3
где? — коэффициент, учитывающий сжатие жидкости (? = 1.03−1.05)
Определение конечного давления при цементировании:
Определение давления в цементировочной головке в конце цементирования:
Pmax = Pгидр.+0.1*[(L-hц)* г г. р.+(hц-h0)* г ц.р.-(L-h0)*г пр. ж.]+(15−20) = = 76 + 0,1 ((0 + (3000 — 20)*1,835 — (3000 — 20)*1) + 17 = 341,83 атм.
где Pгидр. — гидравлическое сопротивление, атм.:
Pгидр. = 0.02*L + 16 = 0,02*3000 + 16 = 76 атм.
Определение производительности цементировочного агрегата в конце цементирования:
?q =(р/4)*(kІ*DІ-dІ)*Vвосх = 0,785*(1,12 *0,1462 — 0,1142)*2 = = 0,785*(1,21*0,0213 — 0,013)*2 = 0,785*(0,026 — 0,013)*2 = 2 м3/с = 20 л/с Определение необходимого количества цементировочных агрегатов по скорости:
n = ?q/qIV + 1 = (20 / 19,7) + 1 = 1,015 + 1 = 2,015? 3 шт.
где
?q — необходимый расход для обеспечения заданной скорости поднятия цементного раствора за эксплуатационную колонну, л/с;
qIV — производительность выбранного агрегата на высшей скорости, л/с.
Скорость | Число двойных ходов поршня насоса в 1 мин. | d = 100 мм. | ||
Подача, л/c | Давление, атм. | |||
I | 53.4 | 6.5 | ||
II | 76.2 | 9.6 | ||
III | 112.5 | 14.2 | ||
IV | 156.0 | 19.7 | ||
Определение количества цементных машин:
i = Q/20 = 54/20 = 3шт.
1.4 Определение продолжительности цементирования обсадной колонны Возможность начала закачки определяется следующим условием:
PIV> Pг? 131>78 — условие выполняется!
где Pг — максимальное давление, развиваемое ЦА на наивысшей скорости, атм;
Pг — давление на преодоление в скважине гидравлических сопротивлений, атм.
Весь объем цементного раствора будет закачан на IV скорости.
Определение высоты столба продавочной жидкости в колонне при работе агрегата на IV скорости:
lIV1 =(L*(dІвн.+kІ*DІсdІэ.к.)+(kІ*DІс-dІэ.к.)*(10*(PIVH — Pг))/(г ц.р.-г г. р.)-(4*Vц.р./р))/((kІ*DІс-dІэ.к.)* (г ц.р.-г пр. ж.)/(г ц.р.-г г. р.)+dІвн.) = ((81,816+0,018*10*(131−78)/(1,835−1,2)) — 52,2) / (0,018*1,312+0,0096) = = ((81,816+0,018*10*(131−78)/0,635) — 54,2) / (0,018*1,312+0,0096) = 1292 м.
Определяем постоянные элементы для данной формулы:
a = L*(dІвн.+kІ*DІсdІэ.к. = 3000*(0,0982 + 1,22 * 0,1462 — 0,1142) = 3000*(0,0096+1,44*0,0213−0,013) = 3000*0,0273 = 81,816
b = (kІ*DІс-dІэ.к.) = 1,22 *0,1462 — 0,1142 = 0,018
c = (г ц.р.*г пр. ж.)/(г ц.р.-г г. р.) = (1,835−1,0) / (1,835−1,2) = 0,835/0,635 = 1,312
Z = 4*Vц.р./р = 4*42,541 / 3,14 = 54,2
Определение высоты подъема цементного раствора за колонной на IV скорости агрегата:
lIV2 = ((4*Vц.р./р)-dІ*(L-lIV1))/(kІ*DІс-dІэ.к.), м.
т.е. lIV2 = (Z-dІ*(L-lIV1))/b = 54,2−0,1142 * (3000−1292) / 0,018 = =(54,2−22,204) / 0,018 = 1777,5 м.
Определение высоты столба продавочной жидкости в колонне при работе агрегата на III скорости:
lIII1 =(a+b*(10*(PIII — PIV)/(г ц.р.-г г. р.)-Z)/(b*c+dІвн.) = = ((81,816+0,018*10*(182−131)/0,635) — 54,2) / 0,033 = 1115 м.
Определение высоты подъема цементного раствора за колонной на III скорости агрегата:
lIII2 = (Z-dІ*(L-lIII1))/b = (54,2−0,1142 *(3000−2917,35)) / 0,018 = (54,2−0,013*82,65) / 0,018 = 2951,4 м.
Определение высоты столба продавочной жидкости в колонне при работе агрегата на II скорости:
lII1 =(a+b*(10*(PII — PIII)/(г ц.р.-г г. р.)-Z)/(b*c+dІвн.) = (81,816+0.018*(10*(270 — 182)/(1.835−1.25)-54.2) / 0,033 = 1592,75 м.
Определение высоты подъема цементного раствора за колонной на II скорости агрегата:
lII2 = (Z-dІ*(L-lII1))/b = =(54.2−0.114І*(3000−1592,75))/0.018 = 1994.4 м.
Определение количества продавочной жидкости, закачиваемой на различных скоростях агрегата:
VIVпр.= e*(р*dІвн./4)*lIV1 = 1,04*3,14*0,0982 *1292 / 4 = 10,13 м³
VIIIпр.= e*(р*dІвн./4)*(lIII1 — lIV1) = 1,04*3,14*0,0982 *1115/4 = 8,74 м3
VII пр.= Vпр.-VIVпр.-VIпр — VIIIпр = 23,4 — 8,74 — 2 — 10,13 = 2,53 м3
VIпр. = 2 мі
Определяем время работы одним агрегатом на разных скоростях:
tIV = ((VIVц.р.+ VIVпр.)*1000)/(qIV*60) = ((42,541+ 10,13)*1000)/(19.7*60) = 45.1 мин.
tIII = (VIIIпр.*1000)/(qIII*60) = (8,74*1000)/(14.2*60) = 10,26 мин.
tII = (VIIпр.*1000)/(qII*60) = (2,53*1000)/(9,6*60) = 4,39 мин.
tI = 2*1000)/(qI*60) = 2*1000)/(6.5*60) = 5,13 мин.
Общее время цементирования:
T/ = tI + tII + tIII + tIV = 5,13+4,39+10,26+45,1 = 64,9 мин.
С учетом подготовительно-заключительных работ:
Tц = T/ + 15 = 64,9+15 = 79,9 мин.
Определяем температуру на забое скважины:
tзаб. = tср. + 0.025L = 0+0,025*3000 = 75єC
где tср. — среднегодовая температура воздуха, єC L — глубина скважины, м.
Определяем количество агрегатов: по времени схватывания:
nца = (Tц./0.75*Tскв.)+1 = (79,9/0,75*1,05)+1 = 2,015? 3 шт.
по скорости:
n = ?q/qIV+1 = (20/19,7)+1 = 2,015? 3 шт.
Фактическое время цементирования:
Tфакт. = T//nца +15 = (64,9/3)+15 = 36,6 мин.
1.5 Выбор буровой установки Выбор буровой установки производится по 3-м ниже перечисленным показателям.
1) глубина бурения Lскв = 3000 м.
2) грузоподъемность на крюке:
Gэ.к = 54 475,2 кг =0,55мН
Gп.к =qп.к*Lскв = 26,8*1960 = 52 528 кг. = 0,53 м.
Gб.к = (Lскв.+0,1*Lскв)*300 = (3000+0,1*3000)*300 = 1 000 000 Н. = 1,00 мН
3) Вид привода: электрический По представленным данным выбираем буровую установку Уралмаш 3000БЭ.
Основные технические характеристики буровой установки:
1) Максимальная грузоподъемность: 1,7 МН
2) Рекомендуемая глубина бурения: 3000 м.
3) Максимальная оснастка талевой системы: 5х6
4) Длина свечи: 27 м.
5) Максимальное натяжение ходовой ветви талевого каната: 210 кН.
6) Диаметр талевого каната: 28 мм.
7) Вид привода: электрический переменного тока
8) Тип привода: разделительный
9) Мощность на барабане лебедки: 661 кВт.
10) Лебедка: У2−2-11
1.6 Режим бурения
— это совокупность параметров обеспечивающих проходку скважины:
7.1 Осевая нагрузка:
Рос.= Руд.*Дд., кН.
где Руд. — удельная нагрузка (кгс/см) — табличное значение Дд. — диаметр долота (см.)
Р1 = 400*44,45 = 177,84 кН.
Р2 = 600*29,53 = 177,18 кН.
Р3 = 600*21,27 = 127,62 кН.
Р4 = 1000*14,61 = 141,60 кН.
Частота вращение долота:
n = 60V/ П*Дд., об/мин.
где Vокружная скорость, м/с. — табличное значение Дд. — диаметр долота, м.
n1 = 60*3,1 / 3,14*0,4445 = 186/1,396 = 133,24 об/мин
n2 = 60*2,3 / 3,14*0,2953 = 138/0,927 = 148,87 об/мин
n3 = 60*2,3 / 3,14*0,2127 = 138/0,668 = 206,59 об/мин
n4 = 60*1,2 / 3,14*0,1461 = 72/0,445 = 161,8 об/мин Количество бурового раствора:
Q = 0,07*Fзаб., л/с.
где Fзаб. = (Д2д. — d2б. тр)*П / 4 — площадь забоя, см2.
Q1 = 0,07*(44,452 — 33,972)*3,14 / 4 = 44,17 л/с
Q2 = 0,07*(29,532 — 24,292)*3,14 / 4 = 15,5 л/с
Q3 = 0,07*(21,272 — 16,832)*3,14 / 4 = 9,3 л/с
Q4 = 0,07*(14,612 — 11,432)*3,14 / 4 = 4,55 л/с
Параметры | Дд.ш.н = 444,5 мм. | Дд.к = 295,3 мм. | Дд.п.к = 212,7 мм. | Дд.э.к = 146,1 мм. | |
Рос., кН. | 177,84 | 177,18 | 127,62 | 141,60 | |
n, об/мин. | 133,24 | 148,87 | 206,59 | 161,8 | |
Q, л/с. | 44,17 | 15,5 | 9,3 | 4,55 | |
2. Теоретическая часть Вскрытие пласта и освоение скважины.
Вскрытие продуктивных горизонтов должно быть проведено качественно. Причин снижения продуктивности горизонта много, но одной из основных причин считается проникновение в пласт инородных жидкостей и частиц породы. При бурении скважины выбирается такой буровой раствор, чтобы гидростатическое давление его столба было больше пластового давления.
При разбуривании продуктивного горизонта следует снижать противодавление на горизонт до безопасного, т. е. до того значения, при котором не может быть открытого фонтанирования. При вскрытии продуктивного горизонта следует применять высококачественный буровой раствор, имеющий минимальную водоотдачу, или буровые растворы на углеводородной основе.
При вскрытии продуктивных горизонтов с низким пластовым давлением, особенно тщательно следует выбирать буровой раствор, поскольку может происходить интенсивное поглощение бурового раствора горизонтом, сопровождающиеся оттеснением нефти от забоя скважины и значительным ухудшением фильтрационных свойств пород призабойной зоны. Для вскрытия продуктивных горизонтов с низким пластовым давлением применяют специальные буровые растворы на нефтяной основе, эмульсионные буровые растворы, глинистые растворы с добавление поверхностно активных веществ, аэрированные жидкости.
Промывка скважины.
Промывка скважины является важнейшим элементом процесса вращательного бурения.
В настоящее время разработано и применяется в практике бурения большое количество промывочных жидкостей, обладающих различными структурно-механическими и физико-химическими свойствами, отвечающими требованиями бурения в различных горно-геологических условиях.
В практике бурения находят применение разнообразные промывочные жидкости, однако наиболее распространенными остаются — техническая вода и в осложненных условиях — глинистые растворы, как наиболее простой и дешевый тип буровых растворов, с помощью которых возможно решение многих технологических задач.
Выбор типа промывочной жидкости определяется геолого-техническими условиями бурения, составом и свойствами проходимых пород, способом бурения; опытом буровых работ и экономической эффективностью.
Для данного проекта скважины проектируется использование глинистого раствора в качестве промывочной жидкости.
Глинистое сырье имеет широкое распространение. Для приготовления промывочных жидкостей используются порошкообразные глины, в том числе бентонитовые, а также различные местные комовые глины. Производство глинопорошков организовано на ряде заводов из высококачественных глин и бентонита. Качество глинопорошков регламентируется ТУ 39−043—74.
Испытание колонны на герметичность.
При истечении срока схватывания и твердения цементного раствора скважину нужно испытать на герметичность. В скважину закачивают воду под давлением. Давление опрессовки должно на 20% превышать максимальное устьевое давление, которое может возникнуть при эксплуатации данной скважины.
Колонна считается герметичной, если не наблюдается перелива воды или выделения газа, а также, если за 30 мин. Испытания давление снижается не более чем на 5 кгс/см*см при опрессовке давлением более 70 кгс/см*см. Отчет времени начинается спустя 5 мин. После создания давления.
Для испытания обсадных колонн опрессовкой обычно пользуются цементировочным агрегатом. Для испытания обсадных колонн на герметичность путем понижения уровня пользуются компрессором или желонкой, опускаемой в скважину на канате.
При испытании труб на герметичность может оказаться, что колонна негерметична. Одним из первоначальных мероприятий по устранению негерметичности является определение места утечки в колонне. Для этого проводят исследования резистивиметром, который служит для измерения удельного сопротивления жидкости. После замера электросопротивляемости однородной жидкости внутри колонны получают диаграмму равного сопротивления, выраженную прямой линией по оси ординат. Вызвав снижением уровня в колонне приток воды и вновь замерив сопротивления, получают другую диаграмму, точки отклонения которой от первой диаграммы связаны с местом течи в колонне.
После установления места течи в колонне производят дополнительное цементирование по способу Н. К. Байбакова, опуская трубы, через которые будет прокачиваться цементный раствор на 2 м. ниже места течи.
3. Мероприятия по технике безопасности Буровые работы Работы по бурению скважин могут быть начаты только на законченной монтажом буровой установке при наличии геолого-технического снаряда и после оформления акта о приемке буровой установки в эксплуатацию.
До пуска буровой установки должна быть тщательно проверена работа всех механизмов, состояние смазки, крепления ограждений, исправность механизма управления, совпадение оси вышки с центром скважины и т. д. Выявленные недостатки подлежат устранению до ввода буровой установки в эксплуатацию.
Оборудование, инструменты, полы, перила, лестницы буровых установок следует содержать в исправности и чистоте.
При неисправности Буровое оборудование (станки, двигатели, насосы и т. д.) необходимо устанавливать в соответствии с требованиями их эксплуатации и типовым схемам монтажа.
Буровая установка должна быть обеспечена средствами малой механизации (элеваторы, механизмы для свинчивания и развинчивания труб и пр.), а также приспособлениями и устройствами по технике безопасности (ограждения шпинделя, ограждения муфты и др.).
При неисправности электрооборудования (чрезмерный нагрев, замыкание, искрение, дым и т. д.) необходимо отключить общий рубильник и вызвать дежурного электромонтера.
В процессе ремонтных работ на полатях и кронблочной площадке рабочий инструмент должен привязываться к ноге или поясу вышки. По окончании работы весь инструмент должен быть перенесен в отведенное для него место.
Бурение скважины Буровой агрегат должен проверяться в начале смены машинистом буровой установки и периодически, но не реже одного раза в декаду, буровым мастером.
Результаты проверки следует заносить в буровой журнал, а обнаруженные неисправности устранять до начала работ.
Во время работы буровых станков запрещается:
а) переключать скорости лебедки и вращателя, а также переключать вращение с лебедки на вращатель и обратно до их полной остановки;
б) заклинивать рукоятки управления машин и механизмов;
в) пользоваться патронами шпинделя с выступающими головками зажимных болтов.
Во время спускоподъемных операций запрещается:
а) работать на лебедке с неисправными тормозами;
б) стоять в непосредственной близости от спускаемых (поднимаемых) труб и элеватора;
в) спускать трубы с не полностью завинченными резьбовыми соединениями;
г) производить быстрый спуск на всех уступах и переходах в скважине;
д) держать на весу талевую систему под нагрузкой или без нее при помощи груза, наложенного на рукоятку тормоза или путем ее заклинивания;
е) проверять или чистить резьбовые соединения голыми руками.
Запрещается охлаждать трущиеся поверхности тормозных шкивов водой, глинистым раствором.
Все операции по свинчиванию и развинчиванию сальника, бурильных труб и другие работы на высоте более 1,5 м, требуется производить со специальных полатей и площадок или переносных лестниц, огражденных перилами.
При кратковременных остановках бурения необходимо приподнять бурильные трубы на высоту, исключающую возможность их прихвата.
Подтягивание бурильных труб диаметром 63,5 м и выше от устья скважины к подсвечнику и обратно, а также к полатям верхового рабочего на расстояние не более 0,7 м должно осуществляться с помощью специальных приспособлений (крючка, захвата и др.).
Находящиеся на полатях крючки для подтягивания, установки свечей за палец должны быть привязаны.
Соединять и отвинчивать вертлюг-сальник от рабочей трубы следует только штанговыми ключами.
После окончания разведочных буровых работ на скважине необходимо выполнить следующее:
а) засыпать все ямы и шурфы, оставшиеся после демонтажа буровой;
б) герметизировать устье скважины;
в) выровнять площадку.
Запрещается:
а) во время подъема бурильных труб очищать их непосредственно руками от глинистого раствора; очистка должна производиться механическим способом;
б) оставлять свечи, не заведенными за палец полатей;
в) составлять свечи бурового инструмента такой длины, что при выполнении спускоподъемных операций верховой рабочий вынужден становиться на перила полатей или работать с лестниц;
г) перемещать в шпинделе бурильные трубы, а также свинчивать и развинчивать их во время вращения шпинделя;
д) поднимать бурильные, колонковые и обсадные трубы из горизонтального положения в вертикальное со скоростью лебедки на прямом канате.
Для ограничения предельной высоты подъема элеватора (фарштуля, талевого блока) и предупреждения затягивания его в кронблок или подвесной блок в вышке или мачте требуется установить противозатаскиватель или на подъемном канате в надлежащем месте должна быть нанесена ясно видимая метка.
Подкладная вилка должна иметь скобу для держания и загнутый кверху конец рукоятки.
При работе лебедкой с помощью рукоятки ручного подъема следует:
а) правильно сочетать действия рукояток ручного подъема и тормоза;
б) по прекращении работы немедленно снять со станка рукоятку подъема.
Перекрепление патронов шпинделя необходимо производить при выключенном вращателе и полной остановке шпинделя.
Разрешается свинчивание и развинчивание рабочего наконечника и извлечение керна из подвешенной колонковой трубы при соблюдении следующих условий:
а) труба удерживается на весу тормозом, управляемым буровым мастером, причем для подвески трубы запрещается применять полуавтоматические элеваторы и фарштули;
б) если расстояние от нижнего конца трубы до пола не более 0,2 м.
При извлечении керна из колонковой трубы запрещается:
а) поддерживать руками снизу колонковую трубу, находящуюся в подвешенном состоянии;
б) проверять рукой положение керна в подвешенной колонковой трубе.
При использовании полуавтоматических элеваторов необходимо:
а) проверять перед началом работы исправность их запоров, упорного подшипника подвесной головки, вращение подвесной головки;
б) содержать элеваторы и наголовники в чистоте;
в) производить операции, связанные с расхаживанием, перемещением и заменой бурового снаряда, только на фарштуле;
г) навинчивать свечу при ослабленном канате;
д) поднимать элеватор по свече, без рывков, со скоростью, не превышающей второй скорости лебедки на прямом канате;
е) довинчивать наголовники ключом или вилкой;
ж) обеспечить буровую бригаду шахтерскими касками. Запрещается применять полуавтоматические элеваторы при работе со свечами «на вынос» .
Механизмы для свинчивания и развинчивания бурильных труб должны быть установлены на прочном основании, закреплены и отцентрированы по оси скважины и кронблока.
При свинчивании и развинчивании бурильных труб с помощью механизмов запрещается:
а) держать руками вращающуюся свечу;
б) вставлять или снимать вилки в прорези замка свечи при включенном двигателе механизма;
в) пользоваться ведущими вилками с удлиненными рукоятками без защелок и с разработанными зевами, превышающими размеры прорезей в замках и ниппелях более чем на 2,5 мм;
г) откреплять сильно затянутые резьбовые соединения одновременно с помощью трубных ключей;
д) стоять в направлении усилия водила в начальный момент открытия резьбового соединения.
Ликвидация аварий Работы по ликвидации аварий должны проводиться под руководством лица, имеющего право ответственного ведения буровых работ (буровой мастер, инженер по бурению, технический руководитель). Сложные аварии в скважинах необходимо ликвидировать по плану, утвержденному главным инженером.
До начала работ по ликвидации аварий буровой мастер и бурильщик обязаны проверить исправность вышки (мачты), оборудования, талевой системы, спускоподъемного инструмента и контрольно измерительных приборов.
При ликвидации аварий, связанных с прихватом труб в скважине, запрещается создавать нагрузки одновременно лебедкой станка и домкратом (гидравлическими цилиндрами подачи станка).
При работе с домкратами должна быть обеспечена их правильная установка. Во избежание разлета клиньев домкрата при обрыве труб клинья должны быть соединены между собой и прикреплены к домкрату или к станку стальным канатом.
При извлечении с помощью домкрата трубы должны быть застрахованы выше домкрата шарнирными хомутами. При натяжке труб лебедкой или домкратом, а также при их расхаживании все рабочие кроме непосредственно занятых на этих работах должны быть удалены на безопасное расстояние.
При использовании домкратов запрещается:
— удерживать натянутые трубы талевым канатом при перестановке и выравнивании домкратом; исправлять перекосы домкратов, находящихся под нагрузкой;
— применять прокладки между головками домкрата и лафетом или хомутами; класть на домкрат какие-либо предметы;
— работать с неисправным манометром и при наличии утечки масла из гидросистемы;
— допускать выход штока поршня домкрата более чем на ¾ его длины; резко снижать давление путем быстрого отвинчивания выпускной пробки;
— освобождать верхний зажимной хомут (лафет), сбивая его ударами падающего сверху груза.
Запрещается применение винтовых домкратов для ликвидации аварий, связанных с прихватом бурового снаряда в скважине.
При постановке ловильных труб для соединения с аварийными трубами, а также во время их развинчивания должны быть приняты меры против падения ловильных труб.
Меры пожарной безопасности При установке буровой, в радиусе 50 м, рабочая площадка должна быть очищена от валежника, листьев и травы.
Трубы от двигателей и печей должны быть выведены не менее чем на 1,5 м выше откоса буровой и снабжены искрогасителями. При прохождении выхлопной трубы через деревянные конструкции или около них зазор между трубой и конструкцией должен составлять не менее 15 см, а трубу необходимо обернуть асбестом.
Пол под печкой и возле нее на расстоянии 0,5 м, а со стороны топки — 0,7 м должен быть покрыт листовой сталью. У печки стенка буровой должна быть изолирована песком между листом и стенкой буровой слоем не менее 10 см. Расстояние от стенки до печки должно быть не менее 0,7 м.
Для выключения электроэнергии, питающей буровую, требуется предусмотреть отключающее устройство, расположенное снаружи на расстоянии не менее 5 м от буровой.
Запрещается:
а) в буровой разводить открытый огонь и применять факелы и другие источники открытого пламени для освещения;
б) утеплять буровую обшивкой легковоспламеняющимися материалами;
в) располагать электропроводку в буровой в местах возможного ее повреждения буровым снарядом или инструментом при ремонте;
г) хранить ГСМ в металлических бачках ближе 15 м от буровой, при обшитой вышке высотой более 15 м не ближе 50 м от вышки.
При установке в буровой двигателей внутреннего сгорания под них должен устанавливаться металлический противень для сбора стекающего горючего и масла, которые необходимо систематически убирать.
Пол помещения, в котором устанавливаются двигатели внутреннего сгорания, должен быть защищен от возгорания обивкой листовой сталью по асбесту на расстоянии 0,5 м вокруг двигателя.
Глушитель следует систематически очищать от нагара.
Бак двигателя должен иметь объем, который рассчитан не более чем на 8 ч работы, но не более 50 л.
Запрещается:
а) работающий двигатель заправлять ГСМ, а также пользоваться открытым огнем при заправке баков с горючим и для определения уровня горючего в баке;
б) разогревать маслои топливопроводную систему двигателя открытым огнем (факелами, паяльной лампой) и допускать работу двигателя с неисправной подводкой горючего (подтекание).
Все буровые установки должны быть обеспечены противопожарным инвентарем в следующих количествах:
— огнетушители на буровые вышки с приводом от электродвигателя — один пенный, один углекислотный, на буровые с приводом от двигателя внутреннего сгорания — 2 пенных огнетушителя;
— ящики объемом 0,5 м³ с песком и лопатой — 2 компл. (один в буровой и один у входа в буровую);
— бочки с водой емкостью 250 литров — 1 шт.
— ведра пожарные — 2 шт.
— комплект шанцевого инструмента (топор, багор, лом) -2 компл.
Кошма размером 1,5×1,5 м на буровые установки с двигателем внутреннего сгорания — 1 шт.
4. Осложнения при бурении скважины на газ (газопроявление) К проявлениям относят самопроизвольный излив бурового раствора, пластового флюида различной интенсивности (перелив, выброс, фонтан) через устье скважины по межтрубному пространству, бурильным трубам, межколонному либо заколонному пространству за пределами устья скважины (грифоны).
Переливы — излив жидкости через устье при отсутствии подачи бурового раствора в скважину.
Выбросы — апериодическое выбрасывание жидкости или газожидкостной смеси через устье на значительную высоту.
Фонтаны — непрерывное интенсивное выбрасывание больших количеств пластового флюида через устье скважины. Возможно открытое — неуправляемое фонтанирование и закрытое — управляемое.
Газ в порах пород находится под большим или меньшим давлением. Это давление принято называть поровым. Давление газа в коллекторах, т. е. в породах, поры которых сообщаются друг с другом, обычно называют пластовым.
В условиях больших поровых давлений глины отличаются высокой пористостью и снижением плотности. Эти отклонения влекут за собой изменение физических свойств глинистых пород, которые фиксируются геофизическими методами.
При вероятности проявлений принимают следующие меры: усиливают контроль за состоянием скважины — чаще замеряют значения основных параметров бурового раствора и уровень в приемных емкостях: изучают изменение состава шлама, раствора и его фильтрата; проверяют готовность резервного бурового и поднапорных шламовых насосов, противовыбросовое и другое оборудование, оценивают состояние обваловки буровой и целесообразность ее расширения и укрепления; проводят инструктаж буровой бригады, механиков, слесарей, электриков.
Плотность бурового раствора должна быть такой, чтобы гидростатическое давление в скважине превышало пластовое на 2−15%. Но для сохранения высокой производительности и низкой себестоимости бурения необходимо поддерживать минимально необходимое превышение давления. скважина колонна бурение цементирование Объем жидкости в запасных емкостях должен превышать объем скважины в 1,5−3 раза. Раствор утяжеляют. Но на утяжеление требуется много времени, поэтому применяют противовыбросовую аппаратуру — превенторы (например, плашечный, универсальный), которые позволяют герметизировать кольцевое пространство между бурильными трубами (невращающейся ведущей трубой) и спущенной ранее обсадной колонной, между вращающейся ведущей трубой и обсадной колонной (вращающийся превентор) или полностью закрыть устье при отсутствии бурильных труб в скважине (глухой превентор). При наличии превенторов со штуцерами, регулируемыми вентилями на отводах, и обратного клапана, установленного в спущенных бурильных трубах, удается регулировать гидравлическое давление на забое. Но это долго продолжаться не может, так как ведет к гидроразрыву пласта, разрушению устьевого оборудования, появлению грифонов. Наиболее надежен универсальный превентор ПУГ-230×320. В случае открытого фонтана с пожаром тушение его производится отрывом пламени от вновь поступающего газа или нефти с помощью мощных струй отходящих газов реактивных двигателей, воды или взрыва. При особенно мощных фонтанах приходится прибегать к бурению наклонных скважин к стволу проявляющей скважины.
Заключение
В заключение данной работы можно сделать вывод, что перед началом проведения работ направленных на бурение нефтяных и газовых скважин необходимо учесть множество различных параметров, влияющих на ход работы, да и на результат в целом.
В работе мы определяли конструкцию скважины, т. е. число обсадных колон, их длину, диаметры, диаметры долот и в зависимости от категории пород производили подбор необходимых нам долот; рассчитывали колонны на прочность; определяли расход цемента и время цементирования, а также количество цементного раствора в целом, по расчетом которого подбирали количество агрегатов.
Т.е можно сказать, что все выше перечисленные параметры должны и просто необходимы, быть учтены и вычислены правильно для безаварийного бурения, а в дальнейшем и эксплуатации нашей скважины, что существенно сказывается на экономических показателях!
Список используемой литературы
1. Элияшевский И. В. и др. Типовые задачи и расчеты в бурении. М.: Недра, 2012.
2. Булатов А. И., Аветисов А. Г. Справочник инженера по бурению. В 2-х томах. — М.: Недра, 2010.
3. Вадецкий Ю. В. Бурение нефтяных и газовых скважин. М.: Недра, 2008.
4. Калинин А. Г., Ошкордин О. В. и др. Разведочное бурение
5. Инночкин Справочник инженера по бурению.