Разработка технологического процесса изготовления детали «Ограничитель»
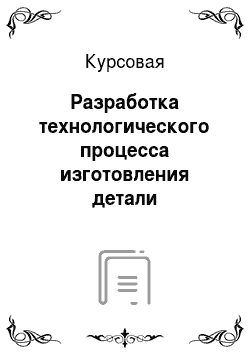
Для фрезерной обработки заготовки я использовал горизонтально-фрезерный станок. Фрезерные станки предназначены для обработки плоских и фасонных поверхностей. Главным движением у фрезерных станков является вращение фрезы, движение подачи — перемещение заготовки относительно фрезы. В зависимости от расположения узлов фрезерные станки бывают консольные и бесконсольные. Основным отличием первых… Читать ещё >
Разработка технологического процесса изготовления детали «Ограничитель» (реферат, курсовая, диплом, контрольная)
Министерство труда, занятости и социальной защиты Республики Татарстан ГАОУ СПО «Набережночелнинский политехнический колледж»
Пояснительная записка
к письменной экзаменационной работе
Тема работы: Разработка технологического процесса изготовления детали " Ограничитель"
Выпускник: Юнусов Р.Р.
Руководитель работы: Мутыгуллина М.Х.
г. Набережные Челны 2015 г.
- Введение
- 1. Построение технологического процесса
- 1.1 Характеристика детали «Ограничитель»
- 1.2 Изучение заготовки для изготовления детали «Ограничитель»
- 1.3 Разработка технологического процесса изготовления детали «Ограничитель»
- 1.4 Контроль деталей после обработки цилиндрических и торцевых поверхностей
- 1.5 Расчет режимов резания и машинного времени
- 2. Металлорежущие станки и работа, выполняемая на них
- 2.1 Выбор оборудования и его характеристика для обработки детали «Ограничитель»
- 3. Организация рабочего места
- 3.1 Рабочее место станочника широкого профиля
- 3.2 Техника безопасности
- Заключение
- Литература
Станочник широкого профиля — одна из самых распространенных профессий в металлообрабатывающей промышленности. Предприятия и объединения металлообрабатывающей промышленности входят в различные отрасли хозяйства-от металлоремонтной (авто-, судоремонтной и т. п.), лесной, деревообрабатывающей, медицинской промышленности до многообразных отраслей машиностроения.
Машиностроение как материальная основа технического перевооружения производства, в свою очередь, включает в себя такие крупные под отрасли, как энергетическое машиностроение, электротехническая, станкостроительная и инструментальная промышленности, приборостроение, тракторное и сельскохозяйственное машиностроение и т. д.
Специалисты, работающие в любой из этих отраслей производства, должны представлять себе производственный процесс, основные стадии производства: заготовительную, обрабатывающую и обслуживающую, помнить, что основными задачами, которые решает рабочий в процессе производства, являются повышение качества изготовления изделий, снижение себестоимости продукции, повышение производительности труда. Для решения этих задач нужны теоретические знания и практические навыки работы, которые будущие токари приобретают при обучении.
Современные рабочие должны уметь переналаживать оборудование, на котором производится обработка изделий, выбирать рациональные режимы резания, контролировать качество обработки с помощью контрольно-измерительных инструментов, диагностировать оборудование и устранять возникшие неполадки.
В настоящее время станочный парк оснащен станками с программным управлением, роботизированными комплексами, гибкими производственными системами, автоматическими линиями, которые не только повышают качество обработки изделий, но и позволяют стабилизировать точностные показатели.
Оборудование с программным управлением обеспечивает автоматический процесс обработки, сокращение времени наладки, возможность многостаночного обслуживания, повышение качества продукции, производительности труда и культуры производства.
Качественные теоретические знания и их постоянное совершенствование в процессе производственной деятельности позволяют повысить уровень профессионального мастерства станочника широкого профиля.
1. Построение технологического процесса
1.1 Характеристика детали «Ограничитель»
Данная мне деталь для изготовления называется «Ограничитель» .
" Ограничитель" применяется во многих сборочных соединениях, в машиностроительном производстве при сборке узлов, в сантехнике.
1.2 Изучение заготовки для изготовления детали «Ограничитель»
Заготовка может быть выдана в виде прутка Ш20,5 мм. Поскольку наибольший диаметр поверхности детали Ш20(-0,020)мм, то припуск на диаметр 2,5 мм. Сопоставляя заготовку с чертежом детали, устанавливаем, что поверхности обрабатываются все, длина заготовки 102 мм, достаточна для закрепления в патроне. Материал заготовки — сталь 45
Сталь — сплав железа с углеродом, содержащий до 2,14% углерода и другими элементами. Большое влияние на обрабатываемость стали оказывает ее химический состав. С увеличением содержания углерода повышается механическая прочность стали и соответственно возрастает сопротивление ее резанию, но увеличивается шероховатость поверхности. При обработке стали с малым содержанием углерода достигается лучшая шероховатость поверхности. По химическому составу стали подразделяют на углеродистые и легированные.
Качественные углеродистые стали маркируют цифрами 10, 20, 45 и т. д., которые показывают среднее содержание углерода в сотых долях процента. Стали с малым содержанием углерода 08, 10, 15,20 имеют относительно низкую прочность и высокую пластичность. Стали марок 25, 30, 40, 50 имеют более высокую прочность при пониженной пластичности.
1.3 Разработка технологического процесса изготовления детали «Ограничитель»
Технологический процесс — это часть производственного процесса, содержащая целенаправленные действия по изменению и последующему определению состояния изделия. В процессе механической обработки изменяются размеры, форма, взаимное расположение поверхностей и величина микронеровностей обрабатываемых деталей. Весь технологический процесс механической обработки заготовок расчленяется на составные части. Основной частью технологического процесса является технологическая операция.
Технологическая операция — законченная часть технологического процесса, выполняемая на одном рабочем месте и охватывающая все действия рабочего по обработке детали до перехода к следующей. В зависимости от рабочего места операции разделяют на токарную, фрезерную, шлифовальную. При изготовлении детали за одну операцию её обрабатывают сначала с одной стороны, затем переворачивают и обрабатывают другую сторону, т. е. деталь обрабатывается за два установа. Установ — часть технологической операции, выполняемая при неизменном закреплении обрабатываемых заготовок.
Выполняемые виды работ (подрезание торца, наружное точение, сверление, и т. д.) называются технологическими переходами.
Технологический переход — законченная часть технологической операции, выполняемая одними и теми же средствами технологического оснащения, при постоянных технических режимах резания и установке.
Вспомогательный переход — законченная часть технологической операции, состоящая из действий человека или оборудования, которые не сопровождаются изменением свойств предмета труда, но необходимы для выполнения технического перехода.
Рабочий ход — законченная часть технического перехода, состоящая из однократного перемещения инструмента относительно заготовки, сопровождаемого изменением формы, размеров, качества поверхности и свойств заготовки.
Вспомогательный ход — законченная часть технического перехода, состоящая из однократного перемещения инструмента относительно заготовки, необходимого для подготовки рабочего хода.
Прием — законченная совокупность действий человека, применяемых при выполнении технического перехода или его части, объединенная одним целевым назначением.
Позиция — фиксированное положение, занимаемое неизменно закрепленной обрабатываемой заготовкой совместно с приспособлением относительно инструмента или неподвижной части оборудования при выполнении определенной части операции.
Технологический процесс должен обеспечивать наиболее экономичное изготовление деталей в соответствии с указанными в чертеже техническими требованиями.
При изготовлении моей детали применяются токарная и фрезерная операции.
Я изучил чертеж детали и технические требования по её изготовлению. В чертеже я указал все сведения необходимые для её изготовления: форма и размеры поверхностей, материал заготовки, технические требования по изготовлению, точность формы, точность размеров, точность взаимного рас положения поверхностей, требования к шероховатости поверхностей.
Изучил заготовку и сравнил её с чертежом. Изучил остальные исходные данные: резцы, сверла, фрезы, которые необходимы для обработки, приспособления.
В резцедержатель установил 4 резца
Выбрал способы обработки поверхностей:
— Торцовые поверхности и фаски обрабатываю проходными отогнутыми резцами;
— Цилиндрические поверхности — проходными упорными резцами
— Фаски — проходным резцом
— Подрезание канавок — канавочным резцом
— Фрезерование лыски — цилиндрической фрезой
— Шлифование — шлифовальным кругом
Режущие инструменты в основном изготовлены из твердых сплавов Т 15К 6 (титано-вольфрамовая группа). Они используются при черновом и получистовом точении при непрерывном резании, чистовое точение при нарезании резьбы токарными резцами, рассверливании, растачивании. Буква Т обозначает карбид титана, цифра за ней — процентное содержание карбида кобальта
Далее выбрал установочные базы.
За черновую базу принимаем цилиндрическую поверхность диаметром 20,5 мм. За чистовую цилиндрическую поверхность диаметром 20(-0,020)
Заготовка будет закрепляться в центрах. Обработка будет производиться за четыре установки и три операции — токарная, фрезерная и шлифовальная.
Определил припуски на обработку. Они зависят от размеров детали, её материала, точности, способа изготовления детали.
В карте технологического процесса я описал все технологические операции в последовательности их выполнения с указанием технологических переходов и режимов обработки.
1.4 Контроль деталей после обработки цилиндрических и торцевых поверхностей
Мною указан измерительный инструмент, который я применил для контроля всех нанесенных на чертеже размеров.
При контроле нанесенных по чертежу размеров я использовал:
Штангенциркуль — универсальный измерительный инструмент, предназначенный для измерения наружных и внутренних диаметров, длин, толщин, глубин т. д.
Точность измерения штангенциркулем определяется шкалой нониуса.
Использование нониуса позволяет получить отсчет дробных частей миллиметра (0,1; 0.005; и 0.02 мм.)
Основной частью штангенциркуля является штанга с миллиметровыми делениями. Шкала нониуса имеет деления, отличающиеся от целого числа делений штанги на значение отсчёта. У штангенциркуля со значением отсчета 0,1 мм деление нониуса равно 1,9 (или 4,9) мм, у штангенциркуля со значением 0,05 мм деление нониуса-1,95 мм, а у штангенциркуля со значением отсчёта 0,02 мм — 0,98 мм при длине шкалы нониуса соответственно 19 (или 49), 39 и 49 мм и числе делений нониуса 10, 20 и 50.
По ГОСТ 166–80 изготовляются штангенциркули трёх типов: ШЦ-Й, ШЦ-ЙЙ и ШЦ-ЙЙЙ
Я использовал штангенциркуль ШЦ-I и ЩЦ-II.
Штангенциркуль ШЦ-I с двухсторонним расположением губок предназначен для наружных и внутренних измерений. Он имеет линейку для измерения глубин, пределы измерений — 0−125 мм. И значение отсчета 0.1 мм.
Штангенциркуль ШЦ-II с двусторонним расположением губок предназначен для измерения и для разметки, пределы измерений 0−200 и 0−300 мм, значение отсчета 0.05 мм и 0.1 мм.
Микрометр служит для измерения наружных размеров с точностью до 0.01 мм.
Все микрометры снабжаются установочными мерами. Я применил микрометр гладкий для измерения наружных размеров.
Для измерения отверстий я применял калибр-пробку. Проходной стороне калибра-пробки соответствует наименьший размер предельный размер и рабочая часть большей длины. Непроходная сторона имеет наибольший предельный размер и рабочую часть меньшей длины.
1.5 Расчет режимов резания и машинного времени
Одним из средств достижения высокой производительности труда является выбор рациональных режимов резания. Режимы резания зависят от обрабатываемого материала и материала резца, от припуска на обработку, допускаемой шероховатости поверхности детали, жесткости заготовки и резца, способа закрепления заготовки и резца, СОЖ, и других факторов.
Расчет режимов резания при точении наружных и цилиндрических поверхностей осуществляют в определенной последовательности:
1. Определяют глубину резания t, исходя из физико-механических свойств обрабатываемого материала, припуска и характера обработки. Минимальное число рабочих ходов определяется мощностью станка и заданной точностью обработки. При черновом точении глубину резания назначаем максимально равной всему припуску. При чистовой обработке глубину резания назначаем в зависимости от требуемых точности и шероховатости обрабатываемой поверхности. Применяем таблицу по выбору глубины резания.
Где D — диаметр заготовки
d — диаметр детали
2. Выбираем подачу S (учитывая размеры заготовки и поперечное сечение стержня резца), глубину резания и инструментальный материал. При чистовом точении на выбор подачи влияет состояние поверхности после обработки. Для чернового, получистового и чистового точения подачу выбираем по таблице.№ 55 стр. 152 (2) S=0,5 мм/об
3. Выбираем геометрические параметры режущей части резца
4. Назначаем период стойкости резца Т по таблице.
5. Выбираем скорость резанияV. Из таб. № 59 стр. 155 (2) приведены средние значения экономичных скоростей резания по материалу заготовки, глубины резания, материала режущей части резца и вида обработки
V= 166 м/мин.
Рассчитываем скорость резания с учетом поправочных коэффициентов
V= Vтаб. *К 1*К 2*К 3*К 4*К 5= 120*1*1.65*1*1*0.92=250 ммин
7. Вычисляем расчетную частоту вращения шпинделя (с учетом диаметра обрабатываемой заготовки) по формуле:
n=1000V/рD =1000*250/3.14*20.025=1510об/мин
8. После определения расчетной частоты вращения её уточняем по паспорту станка, т. е. принимаем фактически имеющуюся частоту вращения шпинделя, близкую к расчетной n= 1600 об/мин.
9. По принятой частоте вращения шпинделя уточняем скорости резания по каждому обрабатываемому диаметру
Vфакт. = 3.14*41*1600/1000 = 200 м/мин.
и определяем эффективную мощность резания
Nрез. = P э/10= 150*200/41*120=1.8 квт
10. Проверяем возможность обработки заготовки на выбранной модели станка 16К 20
Nшп. < Nэл. Ю
Где N мощность электродвигателя, кВт.;
Ю — КПД главного привода станка. Принимаем Ю=0.85
Nшп= 11*0,85=8.8
Мощность шпинделя станка 16К 20 равняется 11 квт.
Nшп. > Nрез.
При подрезании торцов:
Глубина резания определяется по формуле
t = ?заг.-? дет.
t=102−92=10мм.
Где? заг. — длина заготовки
? дет. — длина детали
Выбор подачи при черновом подрезании S=0,5мм/об
Выбор скорости резания V=202м/мин
n= 1000 V /рD = 1000*202/3.14*20.025= 3212 об/мин
Округляем по паспорту станка n= 1600 об/мин
При фрезеровании:
1. Выбираем глубину резания t, тип и параметры фрезы по таблице в зависимости от чертежа, конфигурации обрабатываемой поверхности, ширины В, глубины фрезерования и характера обработки t=1.5 мм.
2. Выбор материала фрезы от характера обработки, обрабатываемого материала, условий обработки
3. Назначаем геометрические параметры фрезы по материалу режущей части фрезы, диаметра фрезы, материала заготовки и его твердости.
4. Назначаем подачу на зуб S по материалу заготовки и его твердости, типа фрезы и материала режущей части, вида фрезеруемой поверхности, шероховатости обрабатываемой поверхности, глубины резания, характера обработки, вылета фрезы S=0.1мм/об
5. Определяем период стойкости фрезы Т по диаметру фрезы, материала режущей части
6. Определяем скорость резания V по материалу заготовки и его твердости, подачи на зуб, периода стойкости Т фрезы, глубины резания, характера обработки V=32 м/мин
Выбираем по поправочному коэффициенту
V=Vт*К 1*К 2*К 3*К 4*К 5=41*1*0.9*1*1.1*1=35 м/мин
7. Определяем частоту вращения фрезы по скорости резания и диаметру фрезы
n= 1000 V /рD
n =1000 *35/3.14*20.025=308 об/мин
8. Определение фактической частоты вращения фрезы по паспорту станка n=350 об/мин
9. Определение фактической скорости резания
V= рdn/1000 V=3.14*20.025*350/100=39 м/мин
Расчет режимов резания при шлифовании:
При щлифовании я использовал шлифовальный круг: 1 500*50*305 24А 10П С2 7 КПГ 35 м/сек, А 1 кл.
Т.е. D=500мм. Высотой Т=50мм, диаметром посадочного отверстия Н = 305 мм. Из белого электрокорунда 24А, зернистостью 10П, степени твердости С2, с номером структуры 7, на керамической связке КПГ, с рабочей скоростью 35 м/сек, класса точности А, 1-го класса неуравновешенности.
Режимы резания выбираем из. Табл. 2.21стр. 93(7)
Vкр.=35 м/сек
nкр. = 1000*20.025=557 об/сек
nдет.=450
Количество проходов — 2
t = 0.5
Sпрод. = 2500 мм/мин.
Расчет основного времени:
Основное машинное время рассчитывается на каждый проход в отдельности по формуле:
То=L+L1+L2+L3 *I / n S
где L — длина обрабатываемой поверхности по чертежу, мм
L1 — величина врезания режущего инструмента, мм.
L2 — величина перебега режущего инструмента, мм.
L3 — дополнительная длина на изгиб при взятии пробных стружек, мм.
n — число оборотов шпинделя в мин.
S — подача резца на один оборот шпинделя
I — число проходов
При токарной обработке
То=92*2/0.5*1600=0.05 минподрезать торец 92
То=20.025*2/1600*0.5=0.09 минобточить диаметр 20.025
То= 1.5*2/0.1*350=0.09 мм при фрезеровании
То= 20.025*2/420*2500= 0.07 при шлифовании
2. Металлорежущие станки и работа, выполняемая на них
2.1 Выбор оборудования и его характеристика для обработки детали «Ограничитель»
Металлорежущие станки классифицируются по многим признакам:
По назначению — токарные, сверлильные, фрезерные.
По степени универсальности — универсальные, специальные.
По степени автоматизации — неавтоматизированные, полуавтоматы, автоматы.
По степени точности — нормальной точности (класс Н), повышенной (П), высокой (В), особо высокой точности (А).
По массе — легкие (до 1 кг), средние (до 10 кг) тяжелые (более 10кг)
По расположению шпинделей — с горизонтальным, с вертикальным, наклонным и комбинированным расположением шпинделей. Токарную обработку своей детали я проводил на токарном станке 16К 20.
1 — эта первая цифра обозначает группу станков. В моем случае — токарную.
6 — Обозначает тип станка, в данном случае токарно-винторезный.
20 — для токарных станков наиболее важной характеристикой является высота центров над станиной 200 мм.
К — модификация станка.
Следовательно, мой станок 16К 20 — токарно-винторезный с высотой центров 200 мм. Это также универсальный станок, на котором можно выполнять все виды токарных работ, в том числе и нарезание резьбы. Все сборочные узлы и механизмы токарно-винторезных станков имеют одинаковое название, назначение и расположение. Основание — узел, используемый для установки станины, одновременно является стружкосборником и резервуаром для охлаждающей жидкости.
Станина — базовый уровень станка, на котором монтируется все взаимное расположение. деталь сталь резание станочник
По передним призматическим и задним плоским направляющим перемещается каретка суппорта, а по передним плоским и задним призматическим направляющим перемещается задняя бабка.
Коробка скоростей — механизм, находящийся в передней бабке, используется для передачи движения шпинделю и для изменения скоростей его движения.
Шпиндель — представляет собой массивный пустотелый вал. На его переднем конце выполнен посадочный конус, по которому базируются патроны, используемые для закрепления заготовок.
Технические характеристики станка модели 16К 20
№ | Наименование параметра, размерность | Величина параметра | |
Наибольший диаметр устанавливаемого изделия над станиной, мм | |||
Наибольшая длина устанавливаемого изделия в центрах, мм | 900 (1000 при переходе задней бабки на 70 мм за торец станины) | ||
Наибольший диаметр обрабатываемого изделия над станиной, мм, не менее | |||
Наибольший диаметр обрабатываемого изделия над суппортом, мм, не менее | |||
Наибольшая длина обрабатываемого изделия в зависимости от установки инструментальной головки, мм, с числом позиций: | 850 (на длине зажима в патроне изделие не обрабатывается) | ||
Число позиций инструментальной головки | 8 (6, 12 по заказу) | ||
Наибольшая высота резца, устанавливаемого в резцедержателе, мм | |||
Центр в шпинделе с конусом Морзе по ГОСТ 13 214–79 | |||
Конец шпинделя фланцевого по ГОСТ 12 593–72 | 6К | ||
Диаметр цилиндрического отверстия в шпинделе, мм | |||
Центр в пиноли с конусом Морзе по ГОСТ 13 214–79 | |||
Наибольший ход суппортов не менее, мм: по оси X по оси Z | |||
Максимальная скорость быстрых перемещений, мм/мин: продольных поперечных | 1500±6% 7500±6% (устанавливается настройкой привода и вводом параметров в УЧПУ) | ||
Пределы частот вращения шпинделя, об/мин | 20−2500 | ||
Пределы частот вращения шпинделя в трех переключаемых вручную диапазонах, об/мин: I II III | 20−285 60−830 175−2500 | ||
Наибольший крутящий момент на шпинделе не менее, Нм (кгм) | 800 (80); 1200 (120) на станках с приводами постоянного тока при 30-минутой перегрузке | ||
Минимальная скорость рабочей подачи, мм/мин: продольной поперечной | |||
Максимальная рекомендуемая скорость рабочей подачи, мм/мин (мм/об): продольной поперечной | 2000 (2.8) 1000 (1.4) | ||
Наибольшее усилие продольной подачи, Н (кг) | 10 000 (1000) | ||
Рекомендуемые предельные диаметры сверления, мм: по чугуну по стали | 25 (исходя из наибольшего усилия продольной подачи и стандартной оснастки) | ||
Для фрезерной обработки заготовки я использовал горизонтально-фрезерный станок. Фрезерные станки предназначены для обработки плоских и фасонных поверхностей. Главным движением у фрезерных станков является вращение фрезы, движение подачи — перемещение заготовки относительно фрезы. В зависимости от расположения узлов фрезерные станки бывают консольные и бесконсольные. Основным отличием первых является наличие консоли, перемещающейся по вертикальным направляющим станины. У бесконсольных фрезерных станков салазки, несущие стол, перемещаются по горизонтальным направляющим, а шпиндельная бабка с фрезой перемещается в вертикальном направлении по направляющим стойки. Наличие в станке возможности поворота стола вокруг вертикальной оси обеспечивает фрезерование винтовых канавок сверл и других изделий.
Технические характеристики горизонтально-фрезерного станка:
Наименование характеристики Значение характеристики
Размеры рабочей поверхности стола, мм 1600×400
Наибольшее перемещение стола, мм:
— продольное (вручную/механическое) 900/880
— поперечное (вручную/механическое) 315/300
— вертикальное (вручную/механическое) 380/360
Количество скоростей шпинделя 18
Расстояние между шпинделем и столом, мм 30−410
Быстрые перемещения по осям:
— Х, мм/мин 19−950
— Y, мм/мин 19−950
— Z, мм/мин 6,3−317
Ускоренные перемещения рабочего стола по осям:
— X, мм/мин 2300
— Y, мм/мин 2300
— Z, мм/мин 770
Мощность двигателя, кВт: 11
Габариты, мм: ДхШхВ 2556×2159×2177
Масса станка, кг 3850
Шлифование я производил на круглошлифовальном станке 3У 12АФ 1.
Шлифовальная бабка с кругом совершают возвратно-поступательное движение. Ведущий круг и шлифовальный круг вращаются в одном направлении, но с разной скоростью. Скорость шлифовального круга превышает скорость ведущего круга.
Автоматическое управление режимами резания обеспечивает хорошее качество шлифуемой поверхности.
Шлифование я осуществлял сочетанием вращения шлифовального круга и вращением шлифуемой детали.
Технические характеристики станка, модель 3У 12АФ 1:
Наименование характеристики Значение характеристики
Класс точности станка по ГОСТ 8–82, (Н, П, В, А, С) А
Диаметр обрабатываемой детали, мм 200.00
Длина детали, мм 630.00
Мощность двигателя главного движения, кВт 4.00
Габариты станка Длина_Ширина_Высота, мм 3400×2260×2040
Масса станка, кг 4400
Модель УЧПУ, установленного на станке УЦИ
3. Организация рабочего места
3.1 Рабочее место станочника широкого профиля
Рабочим местом станочника называется участок производственной площади цеха, на котором расположен станок с комплектом приспособлений, вспомогательного и режущего инструмента, технической документации и других предметов и материалов, находящихся непосредственно в распоряжении рабочего.
Рабочее место является основным звеном любой производственной Структуры, где производят механическую обработку на станках, поэтому очень важно, чтобы оно было рационально организовано. Под организацией рабочего места понимают упорядоченное расположение станка (станков при многостаночном обслуживании), организационной оснастки (инструментальные шкафы, подносы и лотки для инструментов, стеллажи для станочных приспособлений, планшеты и рамки для технической документации и др.) и других устройств, которые обеспечивают станочнику необходимые условия для высокопроизводительной и безопасной работы.
Рациональная организация рабочего места включает в себя его планировку, оснащение и обслуживание.
Под планировкой понимают наиболее целесообразное размещение на производственной площади рабочего и станочного оборудования, материалов, подъемно-транспортных средств и организационной оснастки. При планировании рабочего места в первую очередь необходимо учитывать рабочее положение станочника, а также величину и характер рабочих усилий, объем и темп выполняемых движений, степень точности операций и т. п. При производстве подавляющего большинства станочников, рабочей позой является поза стоя, так как она обеспечивает наилучшие условия для обзора, возможность развития больших усилий и движений с большим размахом. Рациональная рабочая поза стоя обеспечивает при сохранении вертикального положения туловища или наклона его на 10- 15°.
Оснащение рабочего места включает технические средства, необходимые производства определенных видов работ и их контроля (станки, подъемно-транспортные устройства, технологическую и организационную оснасток, измерительные приспособления), а также средства для обеспечения комфорта на рабочем месте (соответствующее освещение, средства связи, ограничение уровня шума и вибраций, эстетические мероприятия и другие средства обеспечения безопасности труда).
Оснащение любого рабочего места включает технологическую и организационную оснастку. Под технологической оснасткой понимают средства, обеспечивающие выполнение технологического процесса в заданных параметрах. Это — станочные приспособления, режущий, вспомогательный и измерительный инструмент. Организационная оснастка — средства, обеспечивающие размещение и хранение технологической оснастки, а также облегчающие труд и обеспечивающие его безопасность. Обычно в нее входят: средства для хранения станочных приспособлений, режущего, вспомогательного и измерительного инструмента (шкафы, тумбочки, этажерки и т. п.); средства для хранения материалов, заготовок и обработанных деталей (различные виды тары, стойки, стеллажи и пр.); средства для размещения технической и технологической документации (планшеты, полки, ящики и др.); средства, обеспечивающие нормальные условия протекания технологического процесса (производственная мебель, местное освещение, средства связи и т. п.).
Все рабочие места станочников в обязательном порядке оснащают решетками под ноги либо ступеньками со сплошным настилом. Их следует изготовлять из электроизоляционных материалов (сухой древесины, пластмассы). Решетки применяют в тех случаях, когда при обработке образуется большое количество стружки, при работе же на шлифовальных станках, куда детали поступают с малыми припусками, удобнее иметь ступеньку со сплошным настилом. Высоту расположения решеток и ступенек от пола выбирают в зависимости от роста рабочего, а их площадь — исходя из того, чтобы не перенапрягался его мышечно-связочный аппарат (подсознательная боязнь оступиться заставляет рабочего постоянно держать мышцы ног в напряженном состоянии, что вызывает их хроническое утомление, сопровождаемое дрожанием или сведением мышц судорогой).
3.2 Техника безопасности
При изготовлении своей детали я соблюдал правила ТБ:
Перед началом работы:
1. Проверить, хорошо ли убрано рабочее место
2. Привел в порядок рабочую одежду. Застегнул обшлаги рукавов, надел головной убор.
3. Проверил состояние решетки под ногой, её устойчивость на полу.
4. Проверил состояние ручного инструмента
5. Привел в порядок рабочее место, убрал все лишнее, подготовил и разложил необходимые инструменты и приспособления в удобном и безопасном порядке.
6. Проверил состояние станка, убедился в надежности крепления ограждений, в исправности электропроводки, заземляющих проводов, рукояток, маховичков управления станком.
7. Подключил станок к электросети, включил местное освещение
8. На холостом ходу проверил исправность кнопок «Пуск» и «Стоп», систему охлаждения.
9. Подготовил средства индивидуальной защиты и проверил их исправность.
Во время работы;
1. Постоянно следил за надежностью крепления станочных приспособлений, а также режущих инструментов.
2. Не производил переключения режимов резания при работе, не производил замеры при включенном станке, не регулировал и не чистил станок при работе.
3. Не отвлекался и не отвлекал других
4. Следил за своевременным удалением стружки со станка
5. Не удалял стружку руками и сжатым воздухом.
6. Следил, чтобы на пол не капало СОЖ и масла.
Также при работе нельзя:
1. Отключать станок при уходе на короткое время
2. Не класть детали на направляющую станины
3. Не останавливать патрон руками
4. Не ловить детали при отрезании
5. Во время работы не облокачиваться на станок.
6. При появлении запаха горящей изоляции, немедленно остановить станок и сообщить мастеру.
7. Не открывать дверцы электрошкафов и не производить регулировку электроаппаратуры
8. Подводить резец, сверло, фрезу только при вращающемся патроне
9. Выключать станок после отвода стружки
После работы:
1. Выключить электродвигатель станка
2. Убрать рабочее место
3. Смазать направляющие машины
4. Разложить инструмент по местам его хранения
5. Стружку смести в поддон или на совок щеткой.
6. Выключить местное освещение
7. Запрещается мыть руки СОЖ. И маслом
8. О всех неисправностях сообщить мастеру.
Заключение
В данной работе я составил технологический процесс детали «Ограничитель». Для обработки наружной цилиндрической поверхности выбрал резцы токарные c пластинками из твердого сплава Т 15К 6, они позволяют вести обработку на повышенных скоростях. Для обработки детали использовал токарный станок на базе 16К 20.
При фрезеровании лыски на горизонтальном консольно-фрезерном станке я использовал специальные тиски и цилиндрическую фрезу. Материал режущей части фрезы выбрал по таблице в зависимости от материала заготовки, и характера обработки Т 15К 6 (титановольфрамовая группа).
При шлифовании я использовал шлифовальный круг: 1 500*50*305 24А 10П С 2 7 КПГ 35 м/сек, А 1 кл на круглошлифовальном станке 3У 12АФ 1. Для снижения опасности появления прижогов и трещин я использовал обильно СОЖ, и снизил глубину резания. Приспособления для закрепления за наружную поверхность — трехкулачковый самоцентрирующий патрон.
Для контроля использовались измерительные инструменты такие как штангенциркуль ШЦ-1−150−0,05. Я применил микрометр гладкий для измерения наружных размеров с точностью до 0,01 мм, резьбовой калибр для измерения наружной резьбы М 12, скобу для измерения канавки диаметром Ш 9,5 мм.
Выполнил расчет режимов резания и машиного времени. Организовал рабочее место станочника широкого профиля.
1. Адаскин А. М., Зуев В. М. Материаловедение: Учебник. — М.: Изд. центр
" Академия", 2003. — 238с.
2. Багдасарова Т. А. Токарь — универсал: Учебник. — М.: Изд. центр «Академия», 2004. — 285с.
3. Вереина Л. И. Справочник станочника: Учебное пособие. — М.: Изд. центр «Академия» 2006. — 560с.
4. Денежный П. М., Стискин Г. М. Токарное дело: Учеб. пособие. — М.: Высш. шк., 1983. — 285с.
5. Зайцев Б. Г., Рыцев С. Б. Справочник молодого токаря. — М.: Высш. шк., 1988. — 303с.
6. Схиртладзе А. Г. Новиков В.Ю. Станочник широкого профиля: Учебник. — М.: «Высшая школа» 1989. — 464с.
7. Фещенко В. Н. Махмутов Р.Х. Токарная обработка: Учебное пособие. — М.: «Высшая школа» 1984. — 288с.
8. Фещенко В. Н. Токарная обработка: Учебник. — М.: «Высшая школа» 2002. — 303с.
9. Черпаков Б. И. Технологическое оборудование машиностроительного производства: Учебник. — М.: Изд. центр «Академия» 2005. — 456с.