Организация ремонта грузовых автомобилей марки КАМАЗ 5320
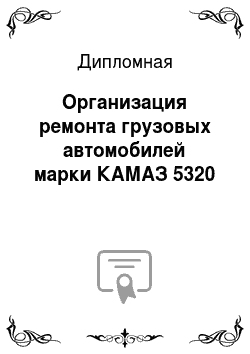
В целях проведения качественной обкатки отремонтированных двигателей разработана централизованная циркуляционная проточная система смазки дизелей. Новая система смазки включает: масляный бак вместимостью до 1 т с подогревающими элементами и трубопроводами для подвода и отвода масла; блок очистки с двумя высокооборотными (до 9000 мин-1) четырехлитровыми центрифугами, насосной станцией, состоящей… Читать ещё >
Организация ремонта грузовых автомобилей марки КАМАЗ 5320 (реферат, курсовая, диплом, контрольная)
Министерство образования и науки Республики Казахстан Костанайский социально технический университет им. акад. З. Алдамжар ДИПЛОМНАЯ РАБОТА На тему: «Организация ремонта грузовых автомобилей марки КАМАЗ 5320»
о специальности 50 713 «Транспорт, транспортная техника и технологии»
Выполнил С. В. Долматов Костанай 2011
Содержание Введение
1. Анализ деятельности предприятия
1.1 Общая характеристика предприятия
1.2 Организация технологического процесса обкатки двигателей
1.3 Анализ технико-экономических показателей работы предприятия
2. Основная часть
2.1 Анализ использования автомобильного транспорта в ТОО «Автоцентр «КамАЗ»
2.2 Размеры и структура затрат на выполнения транспортных работ
2.3 Обоснование производственной программы ремонта
2.4 Режим работы предприятия и фонды времени
2.5 Годовой календарный план работ и график загрузки
2.6 График цикла производства и обоснование метода ремонта
2.8 График грузовых потоков и выбор подъемно-транспортного оборудования сборочного цеха
3. Конструктивная разработка
3.1 Обкатка двигателей
3.2 Конструкторская разработка системы смазки
3.3 Конструкторская разработка стенда — кантователя для разборки и сборки двигателей
3.4 Прочностные расчеты
4. Охрана труда
4.1 Вопросы охраны труда при эксплуатации ремонтного оборудования
4.2 Анализ безопасности и безвредности эксплуатации ремонтного и диагностического оборудования
4.3 Требования безопасности при эксплуатации ремонтного и диагностического оборудования
5. Охрана окружающей среды
6. Экономическая эффективность работы
6.1 Расчёт экономической эффективности внедряемой конструкции
6.2 Расчет экономической эффективности технологического процесса агрегатного участка
6.3 Расчёт экономической эффективности и технико-экономическое обоснование
Заключение
Зона северного Казахстана и в частности Костанайская область относится к одному из зернопроизводящих регионов Республики Казахстан. В доперестроечный период все предприятия Советского Союза, работающие в сельскохозяйственной отрасли, были ориентированы на потребности Казахстана. Поэтому постепенное завоевание рынка грузовых сельскохозяйственных автомобилей к 90-м годам производили наиболее современные и надежные автомобили семейства КамАЗ.
С целью технического обслуживания сложных узлов и агрегатов автомобиля, а также накопления опыта работы с ним, и использования накопленного при дальнейшем усовершенствовании конструкции к 1989 году предусматривалось построить и запустить в области станцию технического обслуживания автомобилей КамАЗ.
В сложившихся условиях предприятия нашей области были вынуждены собственными силами решать, чем и как заниматься в рыночных условиях.
К таким предприятиям относятся в нашей области ОАО «Дормаш» (г. Костанай), ТОО «ЗРД» (г. Костанай), ТОО «ЗРДТ» (п. Затобольск).
Указанные предприятия специализируются на ремонте узлов и агрегатов трансмиссий тракторов, двигателей КамАЗ, А-01М, А-41, Д-240, СМД, ЯМЗ и др, а также выпускают необходимое для сельского хозяйства оборудование: насосы, вентиляторы, жатки, подборщики и т. д.
В настоящее время рынок грузового автотранспорта Республики Казахстан в большей степени насыщен автомобилями Российского производства. Самая распространенная марка автомобиля — КамАЗ.
Актуальность темы нашего исследования преследует организацию ремонта автомобилей КамАЗ на специализированном ремонтном предприятии, взамен некачественного технического обслуживания и ремонта в сельских ремонтных мастерских. Как показывает опыт работы, ремонт сложных узлов и агрегатов автомобилей в сельских хозяйствах проводится некачественно из-за низкой оснащенности ремонтной базы. В ремонтных мастерских отсутствует необходимое технологическое оборудование для проведения капитального ремонта грузовых автомобилей, а крупные предприятия предпочитают заниматься наиболее распространенным видом ремонта — ремонтом тракторов и сельскохозяйственных машин.
Самым обеспеченным предприятием для ремонта грузовых автомобилей в Костанайской области является СП ТОО «Костанайский автоцентр КамАЗ». Однако переход в последнее десятилетие экономики государства к рыночным регулированиям повлек за собой диспаритет цен на промышленную и сельскохозяйственную продукцию, основные производители которой и являлись непосредственными партнерами предприятия. В результате количество ремонтов было снижено, высококлассные специалисты были вынуждены уехать из страны, а оставшиеся не имеют соответствующей квалификации, в результате чего снижено качество выполнения ремонтных работ.
В последние годы предприятие вынуждено было заниматься распространением запасных частей и комплектующих к автомобилям, а также проведением на базе предприятия ежегодных технических осмотров грузовых автомобилей.
Практическая ценность результатов нашей работы подтверждается внедрением на предприятии.
Теоретическая ценность нашей дипломной работы состоит в расчете и его подробном описании.
Цель работы: организовать ремонт грузовых автомобилей марки КАМАЗ 5320 на предприятии ТОО «Автоцентр КамАЗ»
Стабилизация экономики страны привела к желанию руководителей предприятия расширить рынок предлагаемых авто услуг сначала за счет использования мощностей предприятия, а в дальнейшем и за счет расширения ремонтной базы.
В соответствии с целью, были поставлены следующие задачи:
— собрать и проанализировать теоретический материал;
— рассмотреть проект организации грузовых перевозок и ремонта автомобилей в ТОО «Автоцентр КамАЗ» ;
— определить необходимый объем ремонтных работ в 2011 году;
— разработать рекомендаций к наиболее ответственному — обкаточно-испытательному участку;
— добиться снижения затрат на производство работ и повысить качество выполняемых работ.
Поставленные задачи и порядок их решения, определили структуру дипломной работы.
Для решения указанных задач и в соответствии с целью работы, были использованы следующие методы:
Теоретические: анализ научной, технической, нормативной и учебной литературы по теме исследования, систематизирование собранных и проанализированных данных.
Практические: расчет, методы математической статистики, эксперимент.
1. Анализ деятельности предприятия
1.1 Общая характеристика предприятия
Зона северного Казахстана и в частности Костанайская область относиться к одному из зернопроизводящих регионов Республики Казахстан. В доперестроечный период все предприятия Советского Союза, работающие в сельскохозяйственной отрасли, были ориентированы на потребности Казахстана. В сложившихся условиях предприятия нашей области вынуждены собственными силами решать, на что ориентировать выпуск продукции и где брать комплектующие. К таким предприятиям относится в нашей области ТОО «Автоцентр КамАЗ».
Предприятие специализируется на грузовых перевозках и ремонте узлов и агрегатов трансмиссий тракторов, двигателей КамАЗ, А-01М, А-41, Д-240, СМД, ЯМЗ и др. 11 января 1985 года было принято решение о строительстве Кустанайского филиала СТО «КамАЗ». К 1989 году были построены и сданы в эксплуатацию производственные и административные корпуса предприятия. В 1996 году станция была приватизирована и реорганизована в СП ТОО «Кустанайский автоцентр КамАЗ» .
Основное направление специализации — грузовые перевозки, техническое обслуживание, диагностика, ремонт, а также поставка запасных частей для автомобилей КамАЗ. Предприятие имеет производственные и ремонтные цеха: мотороремонтный цех, цех по ремонту автомобилей, коробок перемены передач, ведущих мостов, ведущих валов, цех диагностирования и проведения технического осмотра автомобилей.
ТОО «Кустанайский автоцентр КамАЗ» расположено в северо-западной части города Костаная. Вблизи с предприятием проходит железнодорожная ветка, соединяющая промышленные предприятия города с железнодорожной станцией.
Основная часть территории имеет выезд на улицу им. Карбышева, здесь же располагаются административные здания. По этой улице разрешено движение грузового автотранспорта, выезд с нее возможен на объездную дорогу вокруг города. Следовательно, предприятие имеет в достаточном количестве подъездные пути, как железнодорожного так и автомобильного транспорта.
Территория центра составляет 24 000 кв. м., из которых производственная площадь, составляет 9950 кв. м.
Электроэнергией предприятие частично снабжается из городской распределительной энергетической сети. Во время отключений производиться перевод необходимых цехов на питание от собственной генераторной станции.
Горячая вода, отопление и пар подаются от городской теплоэнергоцентрали (ТЭЦ).
Очистные сооружения завода и канализация подключены к городской системе канализации.
Оплата за предоставляемые услуги с соответствующими службами производиться за счет бартерных сделок.
Уровень рентабельности, зависящий от объемов производства, а также ряда других причин, представлен на рисунке 1.1.
Рисунок 1.1 Уровень рентабельности предприятия
На основании представленных, на рисунке данных можно сделать заключение: работа центра является прибыльной с очень низким уровнем рентабельности. Для повышения эффективности производства необходимо разнообразить номенклатуру выпускаемой продукции, постепенно снижать себестоимость работ при одновременном повышении качества продукции. Указанные мероприятия необходимо проводить с совершенствованием технологий.
1.2 Организация технологического процесса обкатки двигателей
Для того чтобы определить номенклатуру ремонтируемых двигателей рассмотрим состав автомобильного парка (ТПК ТОО «Иволга») в крупных хозяйствах области, обслуживаемых предприятием — таблица 1.1. и табл. 1.2.
Таблица 1.1 Состав и техническое состояние автомобильного парка области
Марка машины | Годы выпуска | Средний пробег автомобилей (ориентировочно), тыс. км | |
ГАЗ | 1985;1992 | ||
УАЗ | 1981;1990 | ||
ЗИЛ | 1979;1992 | ||
КамАЗ | 1986;2005 | ||
Таблица 1.2 Состав автомобильного парка хозяйств области, обслуживаемых ТОО «Кустанайский автоцентр КамАЗ»
Название хозяйств | Наличие автомобилей | ||||
ГАЗ | УАЗ | ЗИЛ | КамАЗ | ||
ТОО Банновка | |||||
ТОО Жер | ; | ; | |||
ТОО Абайское | ; | ; | |||
ОАО Троицкий КХП | |||||
ТОО Рос-Бидай | ; | ; | |||
ТОО Алтын-Инвест | ; | ||||
ТОО Ново-Троицк | |||||
ТОО Жас-Берлик | ; | ||||
ТОО Аманжол-Агро | ; | ; | |||
ТОО Арыстан | ; | ; | |||
ТОО Крыловское | ; | ; | |||
ТОО Салиха | ; | ; | |||
ТОО Ак-Бидай | ; | ||||
ТОО Кулан | ; | ||||
ТОО Алма-Коль | ; | ||||
ТОО Жана-Жол | ; | ||||
Большечураковский ХПП | |||||
ТОО Акбай-Агро | ; | ; | |||
ТОО Буревестник-Агро | |||||
ТОО Шолаксай Агро | ; | ; | ; | ||
ТОО Бубек | ; | ; | ; | ||
ТОО Целинное | ; | ||||
ТОО Денисовское | |||||
ТОО Тобольское-1 | ; | ||||
ТОО Пешковский КХП | |||||
ТОО Большое | ; | ||||
ТОО Федоровское | |||||
ТОО Озерное | ; | ||||
ТОО Ак-Кудук | ; | ||||
ТОО Садчиковское | ; | ||||
ТОО Силантьевское | ; | ||||
ИТОГО: | |||||
Общее количество грузовых автомобилей около 1000 единиц.
Номенклатура и основная годовая программа обкаточно-испытательного участка на 2006 год, согласно с планом предприятия, представлена в таблице 1.3.
Таблица 1.3 Программа работы обкаточно-испытательного участка на период 2010 года
Наименование обкатываемого дизеля | Трудоемкость работ, чел-часов | Программа обкатки, шт. | Отпускная цена ремонта изделия, тенге | |
КамАЗ-740 | ||||
Перечень и характеристика технического состояния оборудования указаны в табл. 1.4.
Таблица 1.4 Ведомость оборудования и орг. оснастки обкаточного участка.
№ на плане | Наименование, тип, модель оборудования | Число, шт. | Габариты, мм | Мощность эл. дв., кВт | Износ по балансовой стоимости, % | |
Универсальный передвижной стенд для ремонта двигателей, до 1,5 т. | 98,7 | |||||
Эл. тельфер, 2 т. | 97,0 | |||||
Обкаточно-тормозной стенд КИ-5540 | 99,0 | |||||
Стенд для обкатки КПП | 95,0 | |||||
Агрегат отопительный СГД-300 | 95,0 | |||||
Стенд обкаточно-тормозной КИ-5274 | 90,0 | |||||
Монорельс с эл. тельфером, до 2 т. | 99,0 | |||||
Стенд для обкатки ведущих мостов К-700 | 80,0 | |||||
Кран-балка электрифицированная до 3 т. | 100,0 | |||||
Яма для хранения ГСМ | ; | 100,0 | ||||
Емкость | ; | ; | ||||
Насос | 1,5 | ; | ||||
Установка для смешивания присадки ЛП-2 с дизельным топливом | 1,5 | 94,0 | ||||
Маслоочистительная машина ОМ-300 | 1,5 | 99,7 | ||||
Маслоотстойник | 0,8 | 100,0 | ||||
Выпрямитель В-630 | ; | 100,0 | ||||
Трансформатор сварочный ТД-300 | ; | 100,0 | ||||
Оборудования для обкатки запланированного количества двигателей вполне достаточно, однако из таблицы 1.4 видно, что оборудование используется явно устаревшее как морально, так и физически. В рекомендации к планам развития предприятия необходимо предусмотреть постепенное обновление и своевременную поверку в органах стандартизации применяемого обкаточного оборудования.
Размещение оборудования соответствует его назначению и решаемым обкаточно-испытательным участком задачам.
Данные о наличии подъемно-транспортного оборудования представлены в таблице 1.5.
Таблица 1.5 Перечень и характеристика подъемно-транспортного оборудования.
Наименование рабочего места | Наименование оборудования | Тех. характеристика: мощность двигателя; грузоподъемность; длина пролета; угол поворота | Прим. | |
Разборка-сборка, контроль | Универсальный передвижной стенд для ремонта двигателей | 10 кВт; до 1,5 тонн | ||
Установка двигателей на стенд | Электротельфер | 5 кВт; до 2 тонн;12 м | 8 шт. | |
Разборка-сборка, контроль | Монорельс с электротельфером | 5 кВт; до 2 тонн; 5 м;60 градусов | ||
Транспортировка двигателей | Кран-балка электрифицированная | 3 кВт; до 3 тонн; 12 м | 2 шт. | |
Среднегодовая численность работающих ТОО «Кустанайский автоцентр КамАЗ», по специальностям, за последние четыре года представлена в таблице 1.6.
Таблица 1.6 Среднегодовая численность работников за 2007;2010 гг.
Показатель | |||||
Производственных рабочих | |||||
Вспомогательных рабочих | |||||
ИТР | |||||
Служащих | |||||
МОП | |||||
В связи с тем, что предприятие испытывает затруднение с приобретением запасных частей и материалов к установкам и стендам, измерительных инструментов предприятие вынуждено не соблюдать технологию ремонта, что ведет к увеличению числа рекламаций, предъявляемых владельцами ремонтируемой техники. Количество рекламаций за последние четыре года представлены в таблице 1.7.
Таблица 1.7 Поступление рекламаций по ремонту дизелей
Марка дизеля | Показатели | |||||
КамАЗ | Рассмотрено рекламаций, шт., из них: | |||||
отклонено по вине хозяйства, шт.; | ; | ; | ||||
принято по вине завода, шт. | ||||||
Сумма затрат на устранение дефектов, тыс. тнг. | 169,7 | 203,8 | 192,4 | 313,3 | ||
Рассматривая поступающие рекламации по двигателям КамАЗ-740 можно выделить основные причины возникновения неисправностей по вине завода:
износ рабочей поверхности цилиндра из-за некачественной обработки;
износ гнезд под вкладыши коренных подшипников из-за некачественного материала;
некачественный ремонт трещин или пробоин в стенках водяной рубашки из-за отсутствия ремонтных материалов;
срыв резьбы в отверстиях из-за некачественных переходных втулок, вставок или ступенчатых шпилек, не ввернутых до отказа и не выступающих на нормальную величину;
деформация посадочных мест под бурты гильз из-за неправильной технологии ремонта;
износ гильз из-за некачественного изготовления деталей;
пробой прокладки блока, в результате неравномерного затягивания головки;
скручивание распределительного вала;
падение давления масла — некачественная сборка;
течь масла из-под заглушки блока из-за некачественной сборки дизеля.
Приведенные данные свидетельствуют об недостаточно качественной сборке двигателей, поступлению бракованных деталей и запчастей, а также недостаточной работе отдела технического контроля предприятия, так как большинство неисправностей можно обнаружить на стадии контроля сборки двигателей и обкатки.
Анализ использования рабочего времени на рабочем месте оператора обкаточно-испытательного участка при установке, обкатке, приемо-сдаточных испытаниях и снятии двигателя со стенда проводиться по таблице 1.8, составленной на основании хронометража времени смены рабочего, обслуживающего обкаточный стенд.
Представленные в таблице 1.8 результаты хронометражных наблюдений свидетельствуют о нарушениях в технологии обкатки двигателей. Так, процесс обкатки и испытаний необоснованно сокращен на 20 минут. Остальные элементы затрат времени также необходимо сокращать повышая трудовую дисциплину и улучшая условия труда.
Таблица 1.8 Анализ использования рабочего времени
Усл. обозн. | Наименование затрат рабочего времени | Затраты времени | |||||
норматив | фактически | подлежит сокращению | |||||
минут | %, к итогу | минут | %, к итогу | ||||
Тпз | Подготовительно-заключительное время | ||||||
Топ | Оперативное время | ; | |||||
Тобсл | Время обслуживания рабочего места | ||||||
Тп.н.т. | Перерывы, вызванные нарушением нормального хода производственного процесса | ; | |||||
Тп.н.д. | Перерывы из-за нарушения трудовой дисциплины | ||||||
Тотдых | Перерывы на отдых и личные надобности | ||||||
Итого: | |||||||
1.3 Анализ технико-экономических показателей работы предприятия
Анализ использования рабочего времени на рабочем месте проведен в подразделе 1.2 по данным таблицы 1.8.
Сведения об отоплении производственных участков приведены в таблице 1.9
Обогрев производственных участков производиться с помощью агрегатов отопительных СГД-300, в которых нагрев воздуха производиться с помощью электрических спиралей, обдуваемых мощным вентилятором.
Основные технико-экономические показатели работы предприятия ТОО «Кустанайский автоцентр КамАЗ» за 2009 год сведены в таблицу 1.10.
Таблица 1.9 Сведения об отоплении производственных помещений
Наименование отделений | Отделения, м3 | Число нагревательных приборов, шт. | Общая поверхность нагревательных приборов, м2 | Прим. | |
Приемки | Определены по плану застройки | ||||
Наружной мойки | |||||
Разборки | |||||
Мойки | |||||
Дефектовки | |||||
Кузнечное | |||||
Сварки | |||||
Механическое | |||||
Склад запчастей | |||||
Комплектовки | |||||
Сборки | |||||
Испытательное | |||||
Таблица 1.10 Основные технико-экономические показатели работы предприятия за 2009 год
Наименование показателей | Значение | |
Абсолютные | ||
1. Площадь усадьбы предприятия, м2 | ||
2. Площадь под застройками, м2 | ||
3. Годовой выпуск реализованной продукции: | ||
а) в условных единицах, шт.; | ||
б) в оптовых ценах, тыс. тн. | ||
4. Общая площадь производственного корпуса, м2 | ||
5. Полезная площадь производственного корпуса, м2 | ||
6. Здания производственного корпуса, тыс. м3 | 947,5 | |
7. Количество работающих, человек, всего из них: | ||
а) производственных рабочих; | ||
б) вспомогательных рабочих; | ||
в) ИТР | ||
г) служащих; | ||
д) МОП | ||
8. Основные фонды, тыс. тн. | ||
9. Нормируемые оборотные средства, тыс. тн. | ||
10. Годовой фонд заработной платы производственных рабочих, тыс. тн. | ||
11. Число металлорежущих станков, шт. | ||
12. Установленная мощность электродвигателей, кВт | ||
13. Годовой расход электроэнергии, тыс. кВтч: | ||
а) силовой; | 62,0 | |
б) осветительной | 10,7 | |
Относительные | ||
1. Коэффициент застройки земельного участка | 0,56 | |
2. Коэффициент использования производственной площади | 0,60 | |
3. Коэффициент специализации | ||
4. Использование полезной площади предприятия | 0,24 | |
5. Установленная мощность электродвигателей на одного производственного рабочего, кВт | 77,70 | |
6. Полезная площадь на одну условную единицу продукции, м2 | 61,47 | |
Характеризующие работу предприятия | ||
1. Коэффициент механизации | 0,43 | |
2. Фондоотдача | 0,16 | |
3. Прибыль на 1 тн. основных фондов | 0,16 | |
4. Рентабельность предприятия, % | 5,6 | |
2. Основная часть
2.1 Анализ использования автомобильного транспорта в ТОО «Автоцентр «КамАЗ»
Во всяком производстве, автомобильный транспорт выполняет роль связующего звена. Хорошо налаженная система транспортного обслуживания является условием успешной деятельности любого предприятия.
Влияния транспорта на эффективность производства многократно и проявляется через уровень транспортных издержек с одной стороны, и через своевременное выполнение транспортных работ с другой. Очевидно, процессы должны быть организованы так, чтобы издержки на автоперевозку были минимальные. А это зависит от достаточно большого числа факторов: состава и структуры автопарка, организации его использования, качества и сроков выполнения работ и т. д.
Все это необходимо учитывать при разборке рекомендаций по повышению эффективности использования автопарка в условиях ТОО «Автоцентр «КамАЗ». Но прежде чем разработать эти рекомендации, мы должны провести анализ использования автопарка в условиях ТОО «Автоцентр «КамАЗ».
Основной задачей Костанайского ТОО «Автоцентр КамАЗ» является перевозка грузов для обеспечения готовой продукцией предприятий и населения города, а так же техобслуживание и ремонт машин.
На некоторых транспортных работах выгоднее использовать автомобили меньшей грузоподъемности, чем автомобили, например, марки КамАЗ. Автопарк предприятия необходимо обновлять, так как некоторые автомобили отработали срок службы, и по этой причине количество автомобилей снизилось. А снижения численности машин отрицательно сказывается на объеме и сроках перевозки грузов.
Эффективность использования машин при выполнении транспортных работ можно оценить, используя списочные показатели.
2.2 Размеры и структура затрат на выполнения транспортных работ 17
Как было отмечено раннее, эффективность работы автотранспорта оценивается еще и через затраты на автомобильные перевозки. С этой целью проанализируем затраты на выполнения транспортных работ за последние два года (таблица 2.1.).
Таблица 2.1 Размеры и структура затрат на выполнение транспортных работ
Статьи затрат | 2009г | % | 2010г | % | |
Заработная плата водителей с начислениями, тыс. тенге. | 17,1 | 19,1 | |||
Стоимость горюче-смазочных материалов, тыс. тенге. | 34,7 | 35,8 | |||
Амортизация основных средств, тыс. тенге. | 11,5 | ||||
Текущий ремонт и обслуживания автомобилей, тыс. тенге. | 16,7 | 18,5 | |||
Прочие затраты (общепроизводственные), тыс. тенге. | 17,7 | 18,5 | |||
Итого затрат тыс. тенге. | |||||
Объем грузоперевозок, тыс. тенге. | За первое полугодие 498 | ||||
Себестоимость 1ткм, тенге. | 14,04 | 20,96 | |||
Из таблицы следует, что самая большая доля затрат это стоимость горюче-смазочных материалов, удельный вес которых за анализируемый период составляет 34,7 и 35,8% соответственно. Примерно одинаковые затраты на зарплату, текущий ремонт и техническое обслуживание. Себестоимость 1ткм, 2010 году снизилась, что является результатам того, что показатели использования подвижного состава — улучшились. Таким образом, эффективность использования автотранспорта несколько повысились, однако имеются еще резервы улучшения таких показателей, как коэффициент использования автотранспорта в работе, использования пробега и другие. Необходимо так же обновить автопарк, так как большая часть автомобилей находится в изношенном состоянии.
В данной главе предусматривается — техническое обслуживание автомобиля является, необходимым условием эффективного выполнения планов перевозок грузов является исправное техническое состояние автомобилей. Значительный вклад в улучшение технического состояния автомобилей в процессе их эксплуатации вносят работники ТОО «Автоцентр КамАЗ». Примеры достижений новаторов производства убедительно показывают наличие на автотранспорте резервов улучшения технического состояния парка автомобилей, повышение их производительности и снижения затрат на ТО и ремонт.
Структура затрат на выполнения транспортных работ на 2010 г. составляет, тыс. тенге:
— заработная плата водителей с начислениями — 19,1%;
— стоимость ГСМ — 35,8%;
— амортизация основных средств — 11%;
— затраты на ТО и ТР — 18,5%;
— прочие затраты (общепроизводственные) — 18,5%;
2.3 Обоснование производственной программы ремонта
Проведем обоснование производственной программы и оценку пункта расположения предприятия. Расчеты производятся по методике ГОСНИТИ:
Так как, предприятие «Автоцентр КамАЗ» занимается капитальным ремонтом двигателей, коробок перемены передач, ведущих мостов, то количество капитальных ремонтов Кк расчитывается по следующей формуле:
Кк = К (2.1)
где К — число ремонтов запланированных на период работ К =120 шт.
Кк = 120
Рассчитываем количество приведенных ремонтов для предприятий выполняющих капитальный ремонт агрегатов машин одной марки, по формуле:
NМ = Ка (2.3)
где Ка — количество ремонтов для агрегатов определяется из выражения:
Ка=а1 Кк (2.4)
где а1=1 — коэффициент охвата капитальными ремонтами агрегатов.
NМ =Ка=1201=120
Далее необходимо определить плотность объектов ремонта Nк или их количество, приходящееся на площадь со средним расстоянием перевозок, равным 1 км, по формуле
Nк=7 Nк /F (2.5)
где F=9,95 км2— площадь обслуживаемой территории
Nк=7120/9,950=84,42 (1/ км2)
Полученные данные заносятся в таблицу 2.2.
Таблица 2.2 Количество объектов, подлежащих капитальному ремонту на 2010 год в ТОО «Автоцентр КамАЗ»
Марка машины, тип, наименование агрегата | Число машин на 2010 г К | Кол-во ремонтов | Коэффициент охвата ремонтами агрегатов | Количество капитальных ремонтов агрегатов Ка | |||
капитальных Кк | текущих КТ | от капитального ремонта машин а1 | от текущего ремонта машин а2 | ||||
КамАЗ | ; | ; | 84,42 | ||||
Рассчитываем средний рациональный радиус перевозок Rср (км) объектов ремонта по выражению
Rср= (2.6)
где А1 — коэффициент, характеризующий долю затрат на оплату труда производственных рабочих, изменяющихся с изменением программы ремонтного предприятия равный 73,4;
D1 — затраты на оплату труда производственных рабочих равный 39,5 тенге/т, а — коэффициент, учитывающий затраты на перевозку ремонтируемого объекта на ремонтное предприятие и обратно равный 0,11 тенге/ткм;
з — коэффициент, учитывающий встречные перевозки запасных частей равный 0,15;
м — коэффициент, учитывающий перевозку материалов, необходимых для ремонта объектов равный 0,125;
н — коэффициент, учитывающий накладные расходы определяющийся по формуле н=1+Rоп/100;
Rоп — процент общепроизводственных накладных расходов исходного предприятия равный 40%;
н=1+Rоп/100=1+40/100=1,4 (2.7)
Rср==
==10,64
Определим оптимальную программу ремонтного предприятия по формуле:
Wo=R2ср Nк=10,642· 84,42=9557,15 (2.8)
Подсчитываем ориентировочную себестоимость ремонта объекта с учетом транспортных затрат:
Срmin=[(A/Wo+B)D+a (1-з —м) Rср]Q (2.9)
где, А — коэффициент, характеризующий долю себестоимости собственно ремонта, изменяющуюся с изменением программы производственного предприятия равный А=88%;
В — доля затрат, не изменяющаяся с изменением программы В=0,266;
D — себестоимость ремонта, приходящаяся на 1 т ремонтируемого объекта в исходном предприятии, D=163 680/0,760=215 368,42 тенге/т
Q — масса перевозимого объекта Q =0,760 т Срmin=[(88/9557,15+0,266)215368,42+0,11(1−0,15−0,125*10,64]0,76=135 138,66
Полученные данные заносятся в таблицу 2.3
Таблица 2.3 Основные результаты расчетов вариантов специализации ТОО «Автоцентр КамАЗ»
Наименование и марка машин | Среднегодовое кол-во капитальных ремонтов Кк | Масса перевоз. объекта Q, т | Плотность объектов ремонта, Nк | Себестоимость ремонта, на 1 т ремонт. объекта D, тнг | Средний рациональный радиус перевозок Rср, км | Годовая оптимал. программа предприятия, Wo | Ориентирную себестоимость ремонта объекта Срmin,, тнг | |
КамАЗ | 0,760 | 84,42 | 215 368,42 | 10,64 | 9557,15 | 135 138,66 | ||
Для экономически выгодного варианта определяют количество ремонтных предприятий на рассматриваемой территории из выражения:
пр= Nм/ Wo=120/9557,15=0,013 (2.10)
Т. к. пр<1, то необходимо расширять возможность обслуживания соседних районов или областей.
2.4 Режим работы предприятия и фонды времени
Режим работы предприятия «Автоцентр КамАЗ», то есть характер рабочей недели, количество рабочих дней, смен и их продолжительность, зависит от характера производства.
В данном ремонтном предприятии «Автоцентр КамАЗ» как правило, режим работы планируется по шестидневной рабочей неделе в одну смену. Продолжительность смены в данном случае длится семь часов, а предпраздничные дни — шесть часов.
Исходя из режима работы, необходимо определить годовой или месячные фонды времени предприятия в целом.
Номинальный фонд времени при работе в одну смену при шестидневной рабочей недели определяется по следующей формуле:
Фн.р.=(dк— dв— dп) tр— dпп (2.11)
где dк, dв, dп, dпп — число дней — календарных, выходных, праздничных и предпраздничных;
tp — продолжительность смены, ч.
На данном предприятии продолжительность смены в предпраздничные дни сокращается на 1 ч.
Фн.р.=(365- 48- 9) 8- 5=2459 ч Номинальный фонд времени оборудования предприятия «Автоцентр КамАЗ» при шестидневной рабочих неделях определяют по формуле
Фн. о=[(dк— dв— dп) tр -(dпв + dпп)] z (2.12)
где z — количество смен.
Фн. о=24 591=2459 ч.
Действительный фонд времени рабочего при шестидневной рабочей недели будет:
Фд.р.=(dк— dв— dп -do) tр) tpбdпп) (2.13)
где do — число отпускных дней в планируемом периоде составляет 22 календарных дня ;
бкоэффициент, учитывающий невыход на работу по уважительным причинам (болезнь, выполнение государственных обязанностей); для расчетов берут равным 0,96.
Фд.р.=(365- 48- 9−24) 80,96- 5=2176,12 ч Действительный фонд времени оборудования определяется из следующего выражения:
Фд.о = Фн.о бо (2.14)
где бо — коэффициент, учитывающий простои оборудования на ремонте, равный 0,95.
Фд.о = 24 590,95=2336,05 ч
2.5 Годовой календарный план работ и график загрузки
Годовой календарный план работ ремонтного предприятия «Автоцентр КамАЗ» составляется на основании годовой производственной программы, то есть количества ремонтируемых объектов по видам выполняемых работ, а также их трудоемкости представлен в таблице 2.4.
Таблица 2.4 Годовой календарный план работ ремонтного предприятия «Автоцентр КамАЗ»
Наименование машин и выполняемых работ | Вид ремонта, ТО | Количество ремонтов, ТО | Трудоемкость ремонта одного агрегата Тм, чел.-ч | Суммарная трудоемкость ремонта Т, чел. — ч | Количество машин и узлов подлежащих ремонту, и трудоемкость работ в чел.- ч по месяцам | ||||||||||||||||||||||||
январь | февраль | март | апрель | май | июнь | июль | август | сентябрь | октябрь | ноябрь | декабрь | ||||||||||||||||||
N | T | N | T | N | T | N | T | N | T | N | T | N | T | N | T | N | T | N | T | N | T | N | T | ||||||
КамАЗ — 740 | Разборка на агрегаты | ||||||||||||||||||||||||||||
КамАЗ — 740 | Ремонт двигателя | ||||||||||||||||||||||||||||
КамАЗ — 740 | Обкатка двигателя | ||||||||||||||||||||||||||||
КамАЗ — 740 | Ремонт электро оборудования | ||||||||||||||||||||||||||||
КамАЗ — 740 | Ремонт каробки передач | ||||||||||||||||||||||||||||
КамАЗ — 740 | Ремонт ведущих мостов | ||||||||||||||||||||||||||||
КамАЗ — 740 | Сборка автомашины | ||||||||||||||||||||||||||||
График загрузки.
По данным годового календарного плана приведенного в таблице 2.3 строят график загрузки ремонтного предприятия. На рисунке 2.1 в масштабе по оси абсцисс откладывают рабочие дни (часы) каждого месяца (номинальные фонды времени рабочего), а по оси ординат — расчетное количество рабочих, необходимое для выполнения соответствующего вида работы по месяцам.
Рисунок 2.1 График загрузки ремонтного предприятия «Автоцентр КамАЗ» 1 — разборка автомобиля; 2 — ремонт двигателя; 3 — обкатка двигателя; 4 — ремонт электрооборудования; 5 — ремонт коробки передач; 6 — ремонта ведущих мостов; 7 — сборка автомашины.
Количество рабочих на отдельных операциях в каждом месяце определяются по формуле:
Р=Т/Фн.р. (2.15)
где Т — месячная трудоемкость работ, чел.- ч;
Фн.р. — месячный номинальный фонд времени рабочего, ч.
Рассчитаем необходимое количество людей на различных операциях в январе месяце:
для разборки автомобиля на агрегаты необходимое количество рабочих определяется как Р=180/204,91=0,9
для ремонт двигателя необходимое количество рабочих определяется как Р=324/204,91=1,6
для обкатка двигателя необходимое количество рабочих определяется как Р=90/204,91=0,4
для ремонта электрооборудования необходимое количество рабочих определяется как Р=8/204,91=0,1
для ремонт коробки передач необходимое количество рабочих определяется как
Р=36/204,91=0,2
для ремонт ведущих мостов необходимое количество рабочих определяется как Р=60/204,91=0,3
для сборки автомашины необходимое количество рабочих определяется как Р=110/204,91=0,5
Аналогично рассчитывается необходимое количество людей на различных операциях в оставшиеся месяцы.
Месячные трудоемкости работ изображаются на графике Определим среднегодовое число рабочих Рср. г=Тг/Фн.р. (2.16)
где Тг — годовая трудоемкость работ, чел. — ч;
Фн.р. — годовой номинальный фонд времени рабочего, ч.
Рср. г=10 350/2459=4,2 ч
2.6 График цикла производства и обоснование метода ремонта
Из представленного в разделе 2.5 годового графика загрузки ремонтного предприятия выбирают расчетный период — месяц, на который запланирован ремонт максимального количества дизельных двигателей. В данном случае наиболее загруженными месяцами являются сентябрь.
Определим такт производства в специализированном предприятии «Автоцентр КамАЗ» занимающимся ремонтом машин одной марки, а также и ремонтом их агрегатов, такт производства
= Ф/N (2.17)
где Ф — фонд времени предприятия за расчетный месяц, ч;
N — количество объектов ремонтируемых в расчетном месяце.
=204,91/56=3,65
Рассчитаем необходимое количество рабочих по каждому рабочему месту по следующей формуле
Рр=Т/ (2.18)
где Т — трудоемкость работ на определенном рабочем месте, чел. — ч.
Для разборки машины на агрегаты и ходовой части на детали необходимо Рр =18/3,65=4,91 ч Ремонт двигателя трудоемкостью — 36 чел. — ч. включает в себя следующие основные операции: разборка двигателя трудоемкостью — 4 чел. — ч.
Рр =4/3,65=1,1 ч Мойка деталей и узлов трудоемкостью — 3 чел. — ч.
Рр =3/3,65=0,8 ч Дефектовка и гидравлическое испытание блока трудоемкостью — 5 чел. — ч.
Рр =5/3,65=1,4 ч Комплектовка деталей к сборке трудоемкостью — 4 чел. — ч.
Рр =4/3,65=1,1 ч Ремонт шатунно-поршневой группы трудоемкостью — 2 чел. — ч.
Рр =2/3,65=0,5 ч Ремонт головки цилиндров и г. р.м. трудоемкостью — 3 чел. — ч.
Рр =3/3,65=0,8 ч Ремонт блока, маховика и шкивов трудоемкостью — 2 чел. — ч.
Рр =2/3,65=0,5 ч Сборка двигателя трудоемкостью — 13 чел. — ч.
Рр =13/3,65=3,6 ч После сборки двигателя необходимо провести его обкатку трудоемкостью — 10 чел. -ч.
Рр =10/3,65=2,7 ч Ремонт электрооборудования трудоемкостью — 4 чел. — ч.
Рр =4/3,65=1,1 ч Ремонт коробки передач трудоемкостью — 6 чел. — ч. включает в себя следующие основные операции: ремонт муфты сцепления трудоемкостью — 3 чел. — ч.
Рр =3/3,65=0,8 ч Ремонт коробки передач трудоемкостью — 3 чел. — ч Рр =3/3,65=0,8 ч Также производят ремонт ведущего моста трудоемкостью — 15 чел. — ч Рр =15/3,65=4,1 ч Последней операцией является сборка машины трудоемкостью — 11 чел. — ч Рр =11/3,65=3 ч На основании комплектования рабочих мест впосты или отделения по призаку сходности выполняемых операций, близких по разряду, до наиболее полной загрузки рабочего устанавливают принятое число рабочих. При этом недогрузка рабочих допускается порядка 5%, перегрузка — от 10 до 15%. Далее необходимо подсчитать загрузку рабочих по каждому посту:
З= (Рр/Рпр)100% (2.19)
где Рр, Рпр — соответственно расчетное и принятое количество рабочих на посту или в отделении.
На разборочно-моечном отделении группируем три рабочих места: разборка машины на агрегаты, разборка двигателя и мойка деталей и узлов при этом загрузку рабочих на этом посту составит
З= (6,8/7)100=98%
Обьеденив участки дефектовки, комплектования и одну операцию (ремонт шатунно-поршневой группы) с мотороремонтного участка загрузка рабочих составит З= (3/3)100=100%
Загрузка рабочих на моторо-ремонтном участке составит З= (4,9/5)100=98%
Обьеденив обкаточный участок и участок ремонта электрооборудования загрузка рабочих составит З= (3,8/4)100=95%
На ремонтно-монтажном участке загрузка рабочих составит З= (8,7/9)100=95%
Полученные данные заносятся в таблицу 2.5 и строят график цикла производства капитального ремонта автомобиля КамАЗ
Таблица 2.5 Цикл производства капитального ремонта автомобиля КамАЗ
Наименование отделений | № постов | № рабочих мест | Наименование операций | Разряд работы | трудоемкость | Количество рабочих | % загрузки | ||
расчетное | принятое | ||||||||
Разборочно-моечное | I | Разборка машины на агрегаты | I-III | 4,9 | |||||
Разборка двигателя | II-III | 1,1 | |||||||
Мойка деталей и узлов | II | 0,8 | |||||||
Дефектовки | II | Дефектовка и гидравлическое испытание блока | IV | 1,4 | |||||
Комплек товки | III | Комплектовка деталей к сборке | IV | 1,1 | |||||
Моторо-ремонтное | IV | Ремонт шатунно-поршневой группы | IV-V | 0,5 | |||||
Ремонт головки цилиндров и г. р.м. | IIIIV | 0,8 | |||||||
Ремонт блока, маховика и шкивов | IIIIV | 0,5 | |||||||
Сборка двигателя | IIIIV | 3,6 | |||||||
Обкаточный | V | Обкатка двигателя | IIIV | 2,7 | |||||
Ремонта электрооборуд. | VI | Ремонт электрооборудования | IIIV | 1,1 | |||||
Ремонтно-монтажное | VII | Ремонт муфты сцепления | II-III | 0,8 | |||||
Ремонт коробки передач | II-III | 0,8 | |||||||
Ремонт ведущего моста | II-III | 4,1 | |||||||
Сборка машины | II-III | ||||||||
Определяем цикл производства t как время от начала первой до конца последней операции. В нашем случае цикл производства равен 37,5 часа.
Зная цикл производства определим фронт работ, т. е.число машин, одновременно находящихся в ремонте по формуле:
f= t/=37,5/3,65=10,3 (2.20)
2.7 Общая компоновка производственного корпуса Учитывая прямоугольную форму производственного цеха «Автоцентра КамАЗ», а также учитывая целесообразность плана самого здания и расположение производственных участков принимаем П-образную форму потока которая обуславливает взаимное территориальное размещение участков.
Отделения и участки на плане производственного корпуса размещаем так, чтобы ремонтируемые агрегаты и отдельные громоздкие детали перемещались по наикротчайшему пути, а взаимосвязь разборо-сборочного участка и участка по восстановлению деталей соответствовала ходу технологического процесса и направлению основного грузопотока.
Обкаточный участок планируем рядом с мотороремонтным участком, а инструментально-раздаточную кладовую располагаем рядом со слесарно-механическим участком.
Оборудование на производственных участках расстанавливаем с учетом необходимых проездов и проходов учитывая габаритные размеры оборудования и ремонтируемых машин.
На разборо-сборочном участке согласно требований ширину основного проезда принимаем равной три метра, а проходы между верстаками и другим оборудованием — около 1,5 м, капитальные стены выложены в два кирпича (толщиной 52 см), а простенки в один — (толщиной 26 см).
Ширина окон соответствует ГОСТу и ровна 1,92 м; ширина дверей в зависимости от назначения помещения — 0,8; 1,5; 2,0 м; ширина ворот — 5,0 м, что также соответствует ГОСТу.
Расстановку производственного оборудования производим с учетом нормативных требований.
Верстаки и стеллажи устанавливаем в плотную к внутренним перегородкам.
План производственного цеха" Автоцентра КамАЗ" представлен на листе в графической части.
2.8 График грузовых потоков и выбор подъемно-транспортного оборудования сборочного цеха
Для выбора кратчайшего пути движения объектов ремонта, материалов и запасных частей, что позволит повысить эффективность и безопасность работы ремонтного предприятия, а также для проверки правильности компоновки цехов, на план производственного корпуса наносят график грузовых потоков в соответствии с последовательностью хода производственного (технологического) процесса. При построении этого графика выявляются встречные и пересекающиеся грузопотоки.
На графике грузовых потоков рисунок 2.2 линией вида показан путь движения деталей или агрегатов на сборку и обкатку, линией вида показан путь движения деталей или агрегатов поступающих на восстановление, линией вида показан путь движения восстановленных и новых деталей или агрегатов.
Описание графиков грузовых потоков: машина поступающая на ремонт ТОО «Автоцентр КамАЗ» заезжает в разборо-моечный участок I, где происходит разборка и мойка узлов подлежащих ремонту. Из разборо-моечного участка детали поступают в дефектовачный участок II. Изношенные детали, подлежащие ремонту поступают в слесарно-механический VII. Восстановленные детали поступают на участок комплектовки III куда также поступают и новые недостающие для сборки детали синструментально-раздаточной кладовой. С комплектовачного участка детали поступают в моторо-ремонтный участок IV. Собранные двигатели из моторо-ремонтного участка поступают в обкаточный участок V. Пройдя холодную обкатку двигатель поступает в ремонтно-монтажный участок VI.
Так как дипломная работа рассчитывается для действующего ТОО «Кустанайский автоцентр КамАЗ» в наличии которого уже имеется следующее подъемно-транспортное оборудование сборочного цеха приведенные в таблице 2.6
Рисунок 2.2 График грузовых потоков ремонтного предприятия ТОО «Автоцентр КамАЗ» I — разборо-моечный участок; II — дефектовачный участок; III — участок комплектовки; IV — моторо-ремонтный участок; V — обкаточный участок; VI — ремонтно-монтажный участок; VII — слесарно-механический участок; IIX — участок технического обслуживания автомобилей; IX — участок ремонта электрооборудования; X — комната мастера; XI — компрессорная; XII — тепловой узел; XIII — инструментально-раздаточная кладовая.
Таблица 2.6 Имеющееся подъемно-транспортное оборудование сборочного цеха ТОО «Автоцентр КамАЗ»
№ п/п | Наименование, тип, модель оборудования | Число, шт. | Габариты, мм | Мощность эл. дв., кВт | |
Универсальный передвижной стенд для ремонта двигателей, до 1,5 т. | |||||
Эл. тельфер, 2 т. | |||||
Определим соответствие имеющегося оборудования условиям работы по следующей формуле:
Р=10(Gм+Gт)[(2+fd)/D] (2.20)
где Gм+Gт — сумарная масса машин, перемещаемых лебедкой, кг;
— коэффициент трения колес тележки, равный 0,1;
f — коэффициент трения колес тележки, для подшипников качения 0,02;
d — диаметр подшипника, равный 5,6 см;
D — диаметр колеса тележки, равный 20 см;
— коэффициент учитывающий дополнительное сопративление, вуозникающее от трения колес о рельс, от перекосов колеи равный 2,4;
Для электротельфера грузоподьемностью 2 т., установленного в отделениях мойки и дефектовки, определим усилие Р=10(760+23)[(20,1+0,02 5,6)/20]2,4= 923,16 кг.
Из приведенного расчета видно, что используемая электротельферная балка соответствует безопасным условиям работы.
Для универсального передвижного стенда для ремонта двигателей грузоподъемностью до 1,5 т. используемого для сборки двигателей, устанавливаемых в мотороремонтном и обкаточном отделениях определим усилие
Р=10(760+23)[(20,1+0,02 5,6)/20] = 384,6 кг.
Из приведенного расчета видно, что использование универсального передвижного стенда для ремонта двигателей грузоподъемностью до 1,5 т соответствует безопасным условиям работы. Рассчитанные данные заносятся в таблицу 2.7
Таблица 2.7 Основные данные подъемно-транспортного оборудования
Наименование цеха, отделения | Наименование подъемно-транспортного оборудования, марка | Основные параметры оборудования | Прим. | |
Мотороремонтном и обкаточном | универсального передвижного стенда для ремонта двигателей грузоподъемностью до 1,5 т | Габариты 80 010 001 200 мм | ||
Мойки, дефектовки, мотороремонтном, обкаточном и слесаро-механическом | электротельфера грузоподьемностью 2 т | Габариты 3 001 000 400 мм | Допустимый радиус закругления — не менее 2,5 м | |
обкатка двигатель ремонт кантователь
3. Конструктивная разработка
3.1 Обкатка двигателей
Автомобильный транспорт имеет широкий спектр применения в различных средах и различных климатических условиях и в связи с этим подвергаются нагрузкам. Поэтому техническое состояние автомобиля, как и всякой другой машины в процессе длительной эксплуатации не остается неизменным. Оно ухудшается вследствие изнашивания деталей и механизмов, поломок и других неисправностей, что приводит к понижению эксплуатационных качеств автомобиля.
Качество сборки проверяют наружным осмотром с помощью измерительных приборов и приспособлений, испытанием наиболее ответственных отдельных агрегатов или машины в целом. После устранения неисправностей, замеченных при наружном осмотре, и проведения необходимых регулировочных работ машина подвергается испытаниям. Перед испытаниями машину заправляют маслом, водой, топливом и рабочими жидкостями.
Испытания узлов и агрегатов машин подразделяют на производственные и контрольные.
Производственными испытаниями предусматривается обкатка ответственных элементов на специальных стендах, в результате чего выявляются дефекты сборки (ненормальные зазоры, ненадежные крепления, перекосы), легко обнаруживаемые по повышенному нагреву отдельных сопряжений, стуку, течи масла и пр.; кроме того, при обкатке достигается правильная начальная приработка трущихся поверхностей.
Контрольные испытания проводят для проверки качества выпускаемой продукции. На стендах и специальных приспособлениях проверяют герметичность, сбалансированность, соосность, а также рабочие параметры отдельных агрегатов (например, расход топлива у двигателей).
Топливные и масляные насосы, магнето, генераторы, форсунки и другие подобные элементы после сборки испытывают на подачу, момент впуска и качество распыла топлива, интенсивность искры и на другие показатели.
Испытаниям подвергаются редукторы, коробки перемены передач, двигатели внутреннего сгорания, гидравлическая аппаратура, насосы, приводные лебедки. Peдукторы и коробки передач трансмиссий испытывают на отсутствие течи масла через сальниковые уплотнения и прокладки, плавность зацепления зубчатых передач, отсутствие шума. Испытания проводят на стендах, позволяющих создать условия, близкие к эксплуатационным. Режимы испытаний по каждому агрегату или машине указаны в технических условиях на испытания.
Особое внимание уделяют испытанию двигателя. Для обкатки двигателей применяют стенды с электрическим и гидравлическим нагружением. Обкатка производится в три этапа: холодная, горячая без нагрузки, горячая с нагрузкой.
Двигатели обкатывают на электротормозных стендах с помощью установленных на них асинхронных электродвигателей с фазными роторами.
Электрический обкаточно-тормозной стенд (рис. 3.1) состоит из следующих сборочных единиц: плиты с четырьмя стойками, имеющими регулируемые опоры, на которых крепят обкатываемый двигатель; электродвигателя-тормоза, статор которого балансирно закреплен в подшипниках на стойках 1,5; редуктора для изменения частоты вращения; весового механизма в качестве генератора; пульта управления; регулировочного реостата и оборудования для замера расхода топлива весовым способом.
В корпусе пульта управления расположен весовой механизм, который передает поворот корпуса электродвигателя-тормоза на стрелку большого циферблата, показывающего усилие от действия крутящего момента. На пульте управления смонтированы тахометр, показывающий частоту вращения электродвигателя с учетом передаточных чисел и частоты вращения коленчатого вала двигателя; манометр, показывающий давление масла в системе смазки двигателя; два дистанционных термометра на 125 °C, контролирующих температуру картерного масла и воды; сигнальная лампочка, указывающая на необходимость выключения стенда, если электроды реостата выведутся из раствора.
Рисунок 3.1. Электрический обкаточно-тормозной стенд для обкатки двигателей: 1, 5 —стойки; 2 — электродвигатель-тормоз; 3 — пульт управления; 4 — редуктор
Регулировочный реостат жидкостного типа предназначен для пуска электродвигателя, регулирования скорости вращения, а при работе в режиме генератора — для нагрузки. Бак реостата наполняется 1… 1,5%-м раствором кальцинированной соды в воде. Регулируют работу электродвигателя в моторном и генераторном режиме, погружая электроды в раствор или выводя из него.
Во время холодной обкатки в картер двигателя заливают нормальное количество масла или смеси масел с присадками. Рубашка охлаждения двигателя должна быть заполнена водой. В случае испытания без масляного радиатора вместо подводящих трубок к маслофильтру надо установить трубчатую перемычку, чтобы фильтр грубой очистки масла мог работать.
Перед началом обкатки все механизмы двигателя должны быть смазаны и двигатель опробован на легкость вращения вручную, форсунки или свечи вывернуты. Коленчатый вал должен быть хорошо сцентрирован с приводным валом обкаточного стенда. При существующем стандартном режиме длительность холодной обкатки для тракторных двигателей устанавливают 50…70 мин, а для автомобильных—20…30 мин на двух-трех режимах по частоте вращения с постепенным ее увеличением от 500…600 до 1000 об/мин вначале без компрессии, а затем с компрессией.
Во время холодной обкатки на ощупь проверяют нагрев трущихся поверхностей. С помощью стетоскопа прослушивают стуки и шумы внутри двигателя. Осмотром убеждаются, нет ли просачивания масла, воды и топлива.
По окончании холодной обкатки сливают смазочно-охлаждающую жидкость из картера двигателя, корпусов маслофильтров и масляного радиатора и дают жидкости стечь из всех полостей маслосистемы.
Если в процессе холодной обкатки никаких дефектов в работе механизмов двигателя не обнаружено, следует промыть масляный фильтр грубой очистки, реактивные масляные центрифуги и картер. Затем вновь собрать двигатель, залить масло соответствующей марки и присоединить к проточно-циркуляционной системе смазки.
Перед горячей обкаткой двигателя его кратковременно прокручивают при малой частоте вращения, чтобы заполнить свежим маслом систему смазки двигателя. Горячая обкатка двигателя без нагрузки продолжается для тракторных двигателей 30 мин, для автомобильных до 20 мин на одном-двух режимах при частоте вращения ниже нормальной в зависимости от модели двигателя. При нормальной частоте вращения во время этой обкатки проводят те же проверки, что и при холодной обкатке и, кроме того, проверяют действие всех механизмов двигателя, регулируют зазоры в клапанах, следят за показаниями приборов и проверяют угол опережения впрыска топлива (для дизельных) и установку зажигания (для карбюраторных) двигателей.
Двигатель во время обкатки должен работать бесперебойно и на всех диапазонах частоты вращения иметь хорошую приемистость.
По окончании этого этапа устраняют неисправности и проверяют затяжку гаек крепления головки болта. Горячая обкатка двигателя под нагрузкой продолжается в течение 60…80 мин.
На всех этапах обкатки двигатель не должен перегреваться и иметь стук коренных и шатунных подшипников, поршней, поршневых колец. В конце обкатки двигатель не останавливают, а плавно нагружают, пока частота вращения не снизится до номинальной.
В связи с тем, что за время обкатки поверхности трения еще не успевают подготовиться к восприятию нормальных нагрузок, на период приработки (30…40 ч работы) на карбюраторные двигатели устанавливают дроссельную ограничительную шайбу, а на дизельные — болт, ограничивающий ход рейки топливного насоса. Этим предупреждают перегрузку двигателя и обеспечивают окончательную приработку деталей.
Обкатку собранных машин проводят в основном для выявления возможных дефектов сборки и проверки правильности регулировок.
Обкатка состоит из следующих операций: подготовки к обкатке; запуска и проверки на холостом ходу двигателя; обкатки машины и устранения обнаруженных неисправностей.
Подготовка к обкатке заключается в проверке комплектности машины. Наружным осмотром проверяют внешнее состояние машины, стопорение и шплинтовку крепежных деталей, а обстукиванием — надежность их затяжки. Кабина, крылья, капот и щитки должны быть надежно закреплены. Двери кабины должны легко открываться и плотно закрываться, не иметь перекосов и заметного качания на осях. Стекла дверей кабины должны плавно опускаться и подниматься. Капот двигателя должен легко подниматься, прочно удерживаться в поднятом состоянии и плотно прикрываться.
Проверяют соответствие техническим условиям регулировок Тормозов и рулевого управления, муфты сцепления, механизма управления двигателем, натяжение гусениц, давление воздуха в шинах, натяжение ремней вентилятора. Проверяют легкость проворачивания коленчатого вала основного и пускового двигателей и т. д.
Заправляют машину топливом, маслом и водой. Проверяют наличие смазки во всех узлах машины и отсутствие подтекания топлива, масла и воды через соединения рукавов, топливные и масляные трубки, прокладки и другие уплотнения. Контролируют плотность завертывания спускных пробок.
Если обкатку проводят в холодное время (ниже 5°С), то в картер двигателя заливают нагретое до 70…80°С масло, а в радиатор — горячую воду.
Запускают пусковой двигатель, прогревают его в течение 2…3 мин и проверяют его работу. Пусковой двигатель должен устойчиво работать на минимальных, средних, максимальных оборотах и при полной нагрузке. Запускают основной двигатель, который должен заводиться в течение 5 мин. Двигатели тракторов и автомобилей с электрозапуском должны легко запускаться от стартера, При наличии в системе запуска спирали или свечи накала следует пользоваться ими. Продолжительность непрерывной работы стартера не должна превышать 5 с за одну попытку запуска. Таких попыток разрешается проводить до 3…4 с перерывом между ними не менее 1 мин.
После запуска прогревают двигатель при закрытой шторке радиатора. Прогретый двигатель должен легко запускаться от стартера (с одной попытки) или с 2…3 оборотов заводной рукоятки (у автомобиля) и работать на всех оборотах устойчиво с бездымным выхлопом. Рычаг газа у тракторных двигателей должен надежно удерживаться на секторе в любом положении. При крайних положениях рычага должна обеспечиваться в одном из положений полная подача топлива, а во втором — полное выключение подачи топлива.
Во время работы прогретого двигателя на холостом ходу проверяют соответствие давления масла техническим условиям, отсутствие подтекания топлива, масла и воды, отсутствие пробивания выхлопных газов соединения.
Двигатель должен работать без стуков. Допускается слабый равномерный шум распределительных шестерен, незначительные стуки клапанов и привода прерывателя-распределителя (у карбюраторных двигателей). При работе двигателя на холостом ходу проверяют непрерывную работу контрольно-измерительных приборов, освещения, сигнала и других приборов — потребителей электроэнергии.
Обкатка машин может проводиться пробегом или на обкаточных стендах. Все большее распространение, особенно на специализированных ремонтных предприятиях, получает проведение обкатки на стендах.
Колесные машины при обкатке на стенде устанавливаются ведущими колесами на опорные барабаны, обтянутые резиной или другими материалами для лучшего сцепления с ведущими колесами машины. Если соединить один из опорных барабанов с тормозным устройств вом, то обкатка будет проходить под нагрузкой.
Автомобили проходят испытания пробегом на расстояние 30 км с нагрузкой, равной 75% номинальной грузоподъемности, на дорогах с твердым покрытием со скоростью не более 30 км/ч.
Во время обкатки необходимо слушать машину и проверять нагрев узлов. Не допускаются шумы и стуки в Коробке передач, заднем мосту, стук кардана у автомобиля, стуки и сильные шумы в конечных передачах тракторов, в механизмах вала отбора мощности и др. Нагрев коробки передач, заднего моста, тормозных барабанов, муфт сцепления и ступиц колес не допускается. Подтекания масла, топлива и воды через уплотнения двигателя не допускается. Температура воды в радиаторе при обкатке машины не должна превышать 90…95°С.
Если в процессе обкатки обнаруживаются неисправности, угрожающие безопасности движения или сохранности узлов и агрегатов машины, обкатку прекращают до их устранения. По окончании обкатки вновь проводят контрольный осмотр машины и устраняют замеченные неисправности. В зависимости от характера обнаруженных неисправностей машину снова обкатывают и испытывают по сокращенному или полному режиму. Повторную обкатку назначают в том случае, если устранение неисправности требует замены или вскрытия агрегатов и при необходимости проведения перерегулировок.
3.2 Конструкторская разработка системы смазки
В целях проведения качественной обкатки отремонтированных двигателей разработана централизованная циркуляционная проточная система смазки дизелей. Новая система смазки включает: масляный бак вместимостью до 1 т с подогревающими элементами и трубопроводами для подвода и отвода масла; блок очистки с двумя высокооборотными (до 9000 мин-1) четырехлитровыми центрифугами, насосной станцией, состоящей из электродвигателя мощностью 3 кВт и частотой вращения 1500 мин-1, гидравлического насоса НШ-71, перепускного клапана, манометра и маслоподводящих и отводящих шлангов; электрощит, обеспечивающий работу установки в автоматическом режиме. Для постоянной подпитки обкаточным маслом системы смазки имеется дополнительный подвесной бак, объемом 1 м3. Общая технологическая схема движения масла в режиме обкатки показана на листе 5. В сравнении с замкнутой кольцевой системой смазки, предусматривающей на протяжении всего процесса обкатки использование масла, заключенного только в объеме картера, применение циркулярно-проточной системы смазки в технологической линии обкатки позволяет в 10 раз повысить срок службы обкаточного масла. При проточно-циркуляционной системе смазки масло, забираемое насосной станцией из рабочего бака, поступает под давлением 106 Па в центрифугу, где очищается от частиц размером до 5 мкм. Затем очищенное подается под давлением до 5*105 Па в систему смазки двигателя, из которого вытекает через открытый «сухой» картер в сливную магистраль. Этот поток масла дополнительно выполняет промывочную функцию.
Рисунок 3.2 Централизованная циркуляционная проточная система смазки дизелей Современный двигатель внутреннего сгорания представляет собой сложный механизм, работоспособность которого зависит от четкого функционирования его различных систем и, в первую очередь, системы смазки.
ГИДРОЦИКЛОН включает корпус 1 с криволинейной (вогнуто-выпуклой) поверхностью, тангенциальный входной патрубок 2, крышку 3, сливной патрубок 4, песковый патрубок 5. Форма внутренней поверхности гидроциклона определена математическими зависимостями. Исходная суспензия подается через тангенциальный патрубок в корпус и закручивается. Под действием центробежной силы инерции осуществляется разделение суспензии. Тяжелая фаза перемещается в направлении к песковому патрубку 5, легкая фаза образует восходящий поток и выводится из аппарата через сливной патрубок 4.
Устройство и принцип действия установки для очистки масла.
Устройство имеет: гидронасос с электроприводом, гидроциклон, общую рамку для их крепления, а также гидропроводы.
Принцип работы гидроциклона аналогичен вышеприведенными описаниями изобретений. Отличительной особенностью является наличие завихрительного участка выполненого в виде резьбовой проточки с переменной шириной канавки, а также наличие отстойной камеры на выходе тяжелой фракции.
Процентное соотношение тяжелой и легкой фракции можно регулировать разместив дроссель на нижнем гидропроводе.
Пропускная производительность установки — 2880 л/час Масса гидроциклона не более 5−7 кг.
Таким образом, используемые гидроциклоны имеют ряд преимуществ в сравнение с центрифугами:
1 — отсутствие вращающихся конструктивных элементов фильтра и его привода;
2 — меньшая металлоемкость и высокая производительность;
3 — простота изготовления и эксплуатации.
3.3 Конструкторская разработка стенда — кантователя для разборки и сборки двигателей
Основным средством уменьшения изнашивания деталей и механизмов и предотвращения неисправностей автомобиля, т. е. поддержание его в должном техническом состоянии, является своевременное и высококачественное выполнение технического обслуживания и ремонта, как капитального, так и текущего.
Знание всех факторов и закономерностей изменений технического состояния автомобилей позволяет правильно организовать работы по повышению его мощности и долговечности, путем своевременного и высококачественного технического обслуживания и ремонта.
В качестве конструкторской разработки нами представлен стенд для закрепления двигателей, а при наличии дополнительных кронштейнов и других агрегатов в подвешенном состоянии и фиксации их в положении удобном для проведения сборочно-разборочных и работ ремонтных работ.
Проанализировав известные приспособления и стенды, мы пришли к выводу, что все аналоги имеют определенные недостатки. Представленный в качестве конструкторской разработки стенд имеет кронштейны, установленные соосно. Тем самым возможность стенд имеет возможность поворачиваться вокруг горизонтальной оси. Один кронштейн установлен на валу червячного редуктора и поворачивается с помощью рукоятки, что дает возможность установить агрегат в положение, удобное для проведения ремонтных работ. Стенд можно изготовить своими силами в условиях мастерской предприятия.
Решение крепления кронштейнов для установки агрегатов делает их легкосменными и позволяет быстро переналаживать стенд на работу с различными двигателями или агрегатами. Комплектуя стенд новыми кронштейнами можно и далее расширять его функциональные возможности, что отличает его от аналогов.
Описание, назначение, принцип работы.
Стенд предназначен для закрепления двигателей, а при наличии дополнительных кронштейнов и других агрегатов в подвешенном состоянии и фиксации их в положении удобном для проведения сборочно-разборочных и работ ремонтных работ.
Конструкция стенда для разборки-сборки двигателя представлена на рисунке 3.3
Рисунок 3.3 Стенд — кантователь для разборки и сборки двигателей: 1- рама, 2- поворотные кронштейны, 3- червячный редуктор, 4- рукоятка поворота, 5- ванна для сбора технических жидкостей.
Стенд состоит из сварного основания-1, на котором крепятся кронштейны-2, для установки двигателя или иного агрегата на стенд. Кронштейны установлены соосно и имеют возможность поворачиваться вокруг горизонтальной оси. Один из них установлен на валу червячного редуктора -3 и поворачивается с помощью рукоятки -4, что дает возможность установить агрегат в положение, удобное для проведения ремонтных работ. Дополнительной фиксации кронштейн не требует, т.к. редуктор является самотормозящимся. Под кронштейнами установлена ванна -5, препятствующая попаданию на пол остатков масел, охлаждающей или моющей жидкостей, которые могут остаться после слива или мойки.
3.4 Прочностные расчеты
Прочностной расчет элементов кронштейна для установки двигателей
Наиболее нагруженным и ответственным узлом конструкции являются кронштейны. Произведем проверочный расчет кронштейна для установки двигателей марок ЗИЛ, КАМАЗ. Проверим условия выполнения прочности па изгиб в месте имеющем максимальное значение изгибающего момента — в защемлении. Этот момент будет создаваться силой тяжести двигателя. Расстояние от заделки рычага до края кронштейна Н=0,44 м. Вес двигателя создает силу тяжести равную F=784,0 Н. Кронштейны установлены симметрично и относительно центра тяжести и на каждый из них будет действовать сила равная половине этой величины. Отсюда максимальный изгибающий момент на рычаге кронштейна:
Ми max=7840Н•0,44м•=3450Н•м (3.1)
Применяя расчетное уравнение при изгибе, найдем необходимое сопротивление изгибу,
Принимая [у]=120 МПа уmax= Mи max/ Wx[у] (3.2)
Wx 3450/120•106 =28•10-6м3=28см3
Рисунок 3.4 Кинематическая схема кронштейна
Для круглого сечения
Wx= Wy= = ?0.1d3 (3.3)
Отсюда определим минимальный диаметр вала
d===4,3 см (3.4)
Выберем по ряду нормальных линейных размеров ближайшее большее значение. Принимаем диаметр вала D=45мм.
Произведем прочностной расчет сварного соединения крепления рычага к валу.
Расчет произведем на совместное действие среза и изгиба.
у = ?[фСР] (3.5)
где фСР = F/S? [фСР] - уравнение прочности на срез.
S-площадь среза шва, для бокового шва
S =2· 0.7д·b (3.6)
b-длина бокового шва у нас конструктивно b=120мм.
д-ширина свариваемого металла д=10мм.
[фСР]-допускаемое напряжение на срез материала шва:
[фСР]=б1· [ур] ,
б1-коэффициент, учитывающий тип сварки, для ручной сварки б1= 0,6
[фСР]=0,6· 160=96МПа
уИ -напряжение изгиба, возникающее в материале шва:
уИ = 3 F· Н/1,4 д· b2 (3.7)
Н-Расстояние от основания шва до направления действия силы. Конструктивно у нас получилось Н=440мм Подставим значения в (3.5) и вычислим у у==79МПа
39МПа<[фСР]
Из расчета следует, что прочность сварочного шва обеспечена.
Запас прочности соединения
n ==1,2.
На самом деле запас прочности гораздо больше т.к. при расчете мы не учитывали заделку второго конца кронштейна. Следовательно, при выбранных размерах кронштейна его прочность обеспечена.
4. Охрана труда
4.1 Вопросы охраны труда при эксплуатации ремонтного оборудования
На базе предприятия авто центра КамАЗ производится ремонт двигателей, коробок передач, а также других узлов и деталей автомобилей семейства КамАЗ. Помимо ремонта на предприятии осуществляется диагностирование механизмов, проведение плановых технических обслуживаний грузовых автомобилей.
Для проведения ремонтов, диагностирования, технического обслуживания на предприятии имеется соответствующее оборудование: контрольно-измерительный инструмент, средства диагностирования машин типа КИ-9918 ГОСНИТИ, КИ-4801 ГОСНИТИ, КИ-4998 ГОСНИТИ, моечное ОМ-5360, подъемно-транспортное, сварочное, металлорежущее, шиноремонтное оборудование.
Вопросы безопасности при эксплуатации этого оборудования рассматриваются в разделе охрана труда. Основной задачей охраны труда является создание безопасных и безвредных условий труда для работающих на предприятии людей.
При проведении работ могут возникать производственные опасности — опасность получить травму, профессиональное отравление или заболевание в результате воздействия профессиональных вредностей. Профессиональные вредности — неблагоприятные факторы, сопровождающие трудовой процесс и отрицательно действующие на здоровье работников. В связи с этим возникает необходимость в разработке вопросов безопасности при эксплуатации имеющегося на предприятии оборудования.
Существуют общие требования безопасности, предъявляемые к производственному оборудованию в соответствии с ГОСТ 12.2.003−76 и ГОСТ 12.2.061−81. За выполнением данных требований осуществляет надзор инженерная служба предприятия во главе с инженером по технике безопасности входит ежеквартальный инструктаж работников, обеспечение их инструкциями по технике безопасности при проведении различных ремонтных работ, вести учет травматизма на предприятии. Кроме требований безопасности к производственному оборудованию существуют требования к производственным помещениям и территории предприятия, которые должны соответствовать ГОСТ 12.3.006−75, СНиП II -4−79, и т. д. Организация рабочих мест должна соответствовать требованиям ГОСТ 12.2.032−78.
Выполнение требований безопасности позволяет значительно сократить количество случаев травматизма на предприятии.
4.2 Анализ безопасности и безвредности эксплуатации ремонтного и диагностического оборудования
Операции разработки, диагностирования, ремонта, сборки двигателей, коробок передач и других механизмов и агрегатов автомобилей КамАЗ проводятся с помощью различных средств механизации. Поэтому при проведении ремонтных и диагностических работ, с помощью соответствующего оборудования, на работника могут воздействовать опасные и вредные производственные факторы (ОВПФ). При контакте с оборудованием, механизмами, воздухом рабочей зоны возникает опасность травматизма, отравление и т. д. В связи с этим была проведена декомпозиция и идентификация опасностей и вредностей, возникающих при эксплуатации различных видов ремонтного и диагностического оборудования на предприятии ТОО «Автоцентр КамАЗ», которая представлена в таблице 4.1. В качестве конструктивной разработки в дипломной работе предложена централизованная система смазки двигателей, находящихся на обкаточно-тормозном стенде.
4.3 Требования безопасности при эксплуатации ремонтного и диагностического оборудования
Требования технической безопасности:
— требование технической безопасности предъявляются в соответствии с ГОСТ 12.2.003−76, ГОСТ 12.2.061−81;
— размеры помещения и размещение в нем производственного оборудования должно удовлетворять требованиям безопасного обслуживания и ремонта машин;
— при выполнении операций по техническому обслуживанию и диагностированию, требующих работы двигателя машины, выхлопная труба должна быть присоединена к вытяжным устройствам;
— испытательные и диагностические стенды должны быть установлены на прочных основаниях;
— испытываемые агрегаты, узлы и машины должны прочно укрепляться на стендах;
— при испытании и диагностировании гидросистем и топливной аппаратуры не допускается течь жидкостей;
— вращающиеся части испытательных стендов ограждаются защитными кожухами, а корпуса стендов необходимо заземлять;
— запрещается оставлять без присмотра работающие стенды;
— запрещается работать на обкаточно-испытательном оборудовании без средств индивидуальной защиты;
— используемые при подъемно-транспортных работах электротельферы, лебедки и др. механизмы подлежат обязательному техническому освидетельствованию;
— с помощью грузоподъемной машины можно перемещать лишь те грузы, масса которых не превышает грузоподъемности машин;
— тележки и тачки для погрузочно-разгрузочных работ должны иметь трафареты, указывающие предельную рабочую нагрузку, а обода колес должны быть обрезинены;
— организация и оборудование рабочих мест при работе на металлорежущем оборудовании должны соответствовать требованиям ГОСТ 12.2.009−80;
— органы управления станочным оборудованием должно быть снабжены надежными фиксациями, исключающими самопроизвольное или случайное их перемещение;
— приспособления для закрепления рабочего инструмента на станках должны обеспечивать надежный зажим, точное центрирование инструмента и не должно иметь выступающих частей;
— при эксплуатации сварочного оборудования запрещается работать без защитных очков и щитков со специальными стеклами;
— запрещается вести электросварку при плохой изоляции проводов идущих от сварочных трансформаторов к щитам;
— запрещается использоваться самодельными ацетиленовыми аппаратами и выполнять работы от одного генератора несколькими горелками или резаками;
— при эксплуатации шиноремонтного оборудования запрещается работать на неисправном парогенераторе и вулканизационной установке;
— запрещается повышать давление воздуха в шинах выше установленной нормы;
— при работе на вулканизаторах необходимо пользоваться рукавицами;
— организация рабочих мест при выполнении шиноремонтных работ должна соответствовать требованиям ГОСТ 12.3.028−82.
Требования производственной санитарии:
— требование производственной санитарии должны соответствовать ГОСТ 12.1.005−83, ОСТ 46.0.175−84;
— вентиляция в помещениях должна обеспечивать воздухообмен не менее 30 м3/ч;
— температура воздуха рабочей зоны должна составлять 17−200С, относительная влажность 40−60%;
— освещенность рабочей зоны должна соответствовать требованиям ГОСТ 12.2.019−86;
— загазованность воздуха рабочей зоны не должна превышать допустимого по ГОСТ 12.1.005−83;
— предельные величины вибрации на рабочем месте определяются по ГОСТ 12.1.102−78;
— уровень шума на рабочем месте не должен превышать допустимого по ГОСТ
Требования электробезопасности:
— при эксплуатации ремонтного и диагностического оборудования должны выполнять требования электробезопасности в соответствии с ГОСТ 12.2.002−81;
— к работе с электроустановками допускаются лица прошедшие первичный инструктаж по электробезопасности, который должен повторяться каждые 6 месяцев;
— электродвигатели станков, стендов, ручного электрифицированного инструмента должны иметь соответствующую защиту от коротких замыканий и перегрузки;
— металлические части станков и стендов, которые могут оказаться под напряжением должны иметь надежное заземление;
— заземленный нулевой провод внутренней электропроводки должен иметь отличительные знаки или иметь четкую отличительную окраску;
— при нарушении или неисправности заземляющего устройства, а также механическом повреждении изоляции кабелей, надо немедленно отключить установку и ликвидировать неисправность;
— при ремонте и техобслуживании электрической части оборудования следует пользоваться диэлектрическим инструментом;
— для защиты здания от атмосферного электричества необходимо установить стержневые молниеотводы;
— пусковая (рубильники, выключатели и т. д.) и защитная (предохранители, автоматы и т. д.) аппаратура должна быть закрытого типа, для исключения возможности прикосновения к токоведущим частям.
Требования пожарной безопасности:
— требования пожарной безопасности предъявляются в соответствии с ГОСТ 12.1.032−81, СНиП 2.01.02−85;
— при работе на стендах с топливной аппаратурой не допускать подтеканий топлива из трубопроводов;
— запрещается пользоваться в помещениях открытым огнем;
— запрещается эксплуатации сварочного оборудования ближе 10 м от легко воспламеняемых материалов;
— нельзя допускать в процессе работы оборудования задевание вращающихся деталей за кожухи или корпуса узлов во избежании искрения и загорания;
— запрещается пользоваться неисправными выключателями и рубильниками;
— производственное помещение должно быть обеспечено необходимыми средствами пожаротушения в соответствии с требованиями ГОСТ 12.04.009−83 (ручные огнетушители типа ОХП-10, ОП-М, воздушно — пенные ОВП-5,10, песок, лопаты и т. д.)
— запрещается загромождать проходы, лестницы различными предметами, препятствующими движению людей.
Требования эргономики:
— требование эргономики должны соответствовать ГОСТ 12.2.033−78;
— все органы управления стендов и станков должны иметь четкие и ясные надписи, поясняющие их назначение;
— конструкция органов управления должна обеспечивать удобство и скорость движений, а также соответствовать допустимым нагрузкам;
— условия перемещения органов управления должны соответствовать требованиям ГОСТ 12.2.019−86;
— необходимо обеспечивать исправность системы СОИ (лампочки накаливания, подсветка и т. д.);
— необходимо использовать цветовое оформление и конструкцию оборудования, отвечающую принципам технической эстетики;
— рациональное чередование режима труда и отдыха;
— опасные узлы и агрегаты оборудования выделяют спец. предупредительными цветами в соответствии с требованием ГОСТ 12.4.026−76.
5. Охрана окружающей среды
Развитие промышленности, транспорта, энергетики, индустриализация сельского хозяйства привели к тому, что антропогенные воздействия на окружающую среду постоянно увеличивается. В процессе производственной деятельности человека загрязнению подвергаются воздушная и водная среда, что отрицательно сказывается на развитии животного и растительного мира. Также интенсивное воздействие оказывается на почвенный покров и недра земной коры, что объясняется развитием сельскохозяйственного производства и добычей, из недр, полезных ископаемых. В связи с этим остро встает вопрос рационального природопользования и охраны природных ресурсов. Наиболее уязвимыми составляющими, без которых невозможно существование человека и которым наносится наибольший ущерб человеческой деятельностью, является воздушная среда и гидросфера.
При эксплуатации ремонтного и диагностического оборудования ТОО «Автоцентр КамАЗ», происходит влияние производственных процессов на экологические параметры окружающей среды. Товарищество специализируется на проведении ремонтов, технических обслуживаний грузовых автомобилей, а также их узлов и деталей. При работе на предприятии применяют следующие виды оборудования: передвижная моечная установка ОМ-2871А ГОСНИТИ, подъемно-транспортное оборудование (электрическая толь ТЭЗ-511, электромеханический подъемник ОПР-7535 и др.), кузнечно-сварочное оборудование (гидравлический пресс ОКС-8815, сварочный агрегат АД-302 и т. д.), металлорежущее оборудование (токарный станок 16к20м, вертикально-сверлильный 2А135), средства диагностирования машин (комплекты КИ-13 919 ГОСНИТИ, стенды регулировочные, обкатки двигателей). Рассмотрим влияние эксплуатации этого оборудования на параметры окружающей среды.
Воздушная среда может быть наружной и внутренней производственной. В производственной среде человек проводит до 25−30% своего времени. Наибольшим загрязнением воздушная среда подвергается при эксплуатации кузнечно-сварочного оборудования, стенда обкатки двигателей. Загрязнение воздушной наружной среды происходит при эксплуатации котельной в зимнее время года. При работе на кузнечно-сварочном оборудовании происходит выделение вредных газов, наиболее распространенные из которых окись углерода, сернистый ангидрид (двуокись серы), окислы азота.
Кроме того, образуется пыль, которая находится в виде аэрозоли и в последствии осаждается на горизонтальных поверхностях. Содержание вредных веществ в воздухе определяется концентрацией вредных веществ. Концентрация, не оказывающая вредного влияния на здоровье человека, называется предельно-допустимой концентрацией (ПДК) /10/. ПДК для воздуха рабочей зоны регламентируется по ГОСТ 12.1.005.76. Так, предельно-допустимая концентрация вредных веществ в воздухе, для рабочей зоны производственного помещения составляет: двуокись серы — 10мг/м3, сажа (копоть) — 10 мг/м3, двуокись азота — 5 мг/м3, свинец и его соединения — 0,01 мг/м3, окись железа с примесью окислов марганца — 6 мг/м3 и т. д.
При проведении обкатки двигателей происходит выделение окиси углерода, ПДК которой составляет 20 мг/м3. Цеха, где проводятся кузнечно-сварочные и обкаточные работы, в обязательном порядке оборудуются приточно-вытяжной вентиляцией. Используемое на предприятии подъемно-транспортное, моечное, металлорежущее оборудование, а также регулировочные стенды безопасны для воздушной среды, так как имеют электрический привод и не образуют в процессе работы вредных примесей.
При работе моечного оборудования используются специальные моющие растворы, в состав которых входят различные щелочи и соли, способные вызвать загрязнение окружающей среды. Поэтому после мойки машин, узлов, деталей эти растворы вместе со сточными водами отводятся в специальные отстойники. Выпускаемые сточные воды не должны: оказывать разрушающего действия на материал труб, содержать более 500 мг/л взвешенных и всплывающих веществ, содержать горючие примеси и растворенные газообразные вещества, способные образовать взрывоопасные смеси. В отстойниках должна проводиться очистка сточных вод путем нейтрализации, флотации биофильтров в зависимости от вида загрязняющих веществ.
При работе металлорежущего оборудования образуются твердые отходы в виде металлической стружки, обрезков, брака и т. д. Н, а предприятии эти отходы собирают в контейнеры и впоследствии вывозят вместе с металлоломом на переработку. При эксплуатации диагностического оборудования (стендов для проверки прецизионных пар топливных насосов, форсунок, приборов для испытания и регулировки форсунок, а также гидрооборудования) возможны загрязнения окружающей среды дизельным топливом и маслом. Такие загрязнения могут происходить из-за неисправности используемого оборудования, неаккуратности рабочего персонала, нарушения требований безопасности при эксплуатации оборудования.
Загрязнением окружающей среды могут сопровождаться работы по проведению технического обслуживания грузовых автомобилей. Такие операции как, доливка или смена масла в двигателе и механизмах, смазка шприцом узлов и деталей, требует наличия специального оборудования (емкостей, подставок и т. д.) во избежание попадания нефтепродуктов в окружающую среду. В дальнейшем, отработанное масло сливается в специальные емкости и сдается на переработку.
В холодной время года производственные помещения центра отапливаются, расположенной на его территории, котельной. В котельной при сжигании органического топлива с уходящими газами выделяются в атмосферу вредные вещества. При использовании в качестве топлива угля Экибастузского содержание вредных примесей в продуктах горения составляет: летучей золы — 63,9 г/м3, окислов серы — 2,24 г/м3окислов азота 0,79 г/м3. При сгорании мазута: летучей золы — 0,1 г/м3, окислов серы — 3,98 г/м3, окислов азота — 0,8 г/м3.
В конструктивной разработке дипломной работы предложена централизованная система смазки обкатываемых двигателей.
Разрабатываемая установка позволяет сократить количество расходуемого при обкаточных работах масла путем высокоэффективной очистки вне конструкции двигателя. Централизованная система смазки состоит из системы баков для масла: товарного, очищенного и питающего, связанных между собой арматурой, а также маслоочистительной установкой с гидроциклонной очисткой масла, предварительным подогревом, насосом и переливным клапаном.
Разрабатываемая установка позволит не только снизить затраты предприятия на расходные материалы, но и значительно сократить возможные проливы нефтепродуктов в почву, вызванные сменой масла в двигателе после проведения обкатки.
Угрозу загрязнения окружающей среды, при эксплуатации стенда, может представлять гидроцилиндр, и питающие его гидрошланги. Неисправность, порыв гидрошлангов, подтекания соединений могут стать причиной загрязнения производственного помещения нефтепродуктами. В связи с этим перед началом эксплуатации стенда необходимо проводить осмотр оборудования на наличие неисправностей, подтеков, порезов гидрошлангов. В случае обнаружения этих неисправностей работу следует прекратить. Эксплуатация стенда возможна лишь после устранения всех неполадок.
На основе проведенного анализа возможных причин загрязнения окружающей среды, предъявляются следующие экологические требования к эксплуатации производственного оборудования и обустройству территории предприятия ТОО «Автоцентр КамАЗ» :
— если содержание, выделяемых в атмосферу, вредных веществ превышает установленные ПДК вытяжные вентиляции цехов и выводные трубы котельной должны оборудоваться очищающими фильтрами и уловителями;
— не допускать при работе на диагностических стендах подтекания топлива из топливопроводов и соединений;
— запрещается эксплуатация неисправного оборудования, инструмента и технологических емкостей;
— при проведении технического обслуживания автомобилей и их узлов не допускать попадание в окружающую среду нефтепродуктов (смазочных жидкостей, твердой смазки).
— для закрытой тары с технологическими отходами, периодически вывозимыми с территории, необходимо отвести отдельный участок;
— территорию предприятия, а также производственные помещения необходимо озеленять с целью улучшения экологического состояния окружающей среды;
— уровень звукового давления, создаваемый источниками шума не должен превышать допустимого — 50−60 дБ.
6. Экономическая эффективность работы
6.1 Расчёт экономической эффективности внедряемой конструкции
Расчёт стоимости конструкции стенда для разборки-сборки двигателей Стоимость конструкции определяется по следующей формуле:
СК = СИЗГ + ССБ + СН + СПОК, тенге (6.1)
где СИЗГ - затраты на изготовление деталей, тенге;
ССБ — затраты на сборку конструкций, тенге;
СН — накладные расходы, тенге;
СПОК — стоимость покупных деталей, тенге.
Стоимость изготовления деталей рассчитывается по следующей формуле:
Сизг.= Спр + См, тенге (6.2)
где СПР — заработная плата производственных рабочих, занятых на изготовлении деталей, тенге;
СМ — стоимость материала заготовок, тенге.
СПР = t · ССРЧАС · К, тенге (6.3)
где t — средняя трудоёмкость (на изготовление конструкции по данным отдела нормирования составит 24 чел-час);
ССРЧАС — средняя часовая ставка рабочих (140 тенгепо данным бухгалтерии предприятия);
К — коэффициент, учитывающий доплаты к основной заработной платы (0,30- входит процент отчислений на дополнительную заработную плату, отчисления в пенсионный фонд, соц. страх., подоходный налог (0,21)).
Спр=24· 140·1,51=5073,6 тенге СМ = Ц · Q3, тенге (6.4)
где Ц — цена одного кг материала (цена 1 тонны стали на сегодняшний день варьируется от 260 до 280 тыс. тенге — по данным компании «Форт -2000»);
Q3 — масса заготовок (масса конструкции составляет 15 кг).
См=15 · 260 000/1000=3900 тенге Затраты на сборку конструкции:
ССБ = ТСБ · ССРЧАС · К, тенге (6.5)
где ТСБ — время на сборку, час (время на сборку конструкции — 2 часа-данные хронометража).
Ссб= 2· 140· 1,51=422,8 тенге Накладные расходы:
СН = Спр. р. · R / 1000, тенге (6.6)
где СПР.Р — заработная плата производственных рабочих, тенге;
R — общепроизводственные накладные расходы, % (100−150% от заработной платы), тенге.
СПР.Р = СПРОСН + СД +ОСОЦ, тенге (6.7)
где СПРОСН — основная заработная плата производственных рабочих, тенге;
СД — дополнительная зарплата, тенге;
ОСОЦ — отчисления на социальные нужды, тенге.
СПРОСН = Спр. + Ссб. (6.8)
СД = СПРОСН · 9,5% / 100 (6.9)
ОСОЦ = СПРОСН * 21% / 100 (6.10)
СПРОСН=5073,6+422,8=5496,4 тенге СД =5496,4· 9,5/100=522,2 тенге ОСОЦ=5496,4· 21/100=1154,2 тенге Спр.р=5496,4+522,2+1154,2=7172,8 тенге Сн=7272,8· 100/100=7172,8 тенге Стоимость покупных деталей (Спок) составит (винты, гайки, шайбы, шплинты) =100 тенге Ск =7172,8+100+7172,8+3900=18 345,6 тенге Экономия предприятия достигается за счет снижения трудоемкости на участке агрегатного ремонта, повышения уровня механизации. По данным хронометража трудоемкость снизится на 18%. Годовая экономия от снижения трудоемкости рассчитывается по следующей формуле:
ЭГ = (Т1 — Т2) · (Сч.н.), тенге (6.11)
где Т2, Т1 — трудоемкость ремонта двигателей соответственно до внедрения приспособления и после, чел-час;
Сч.н— часовая тарифная ставка рабочего с начислениями, тенге;
Эг=(39 835−32 664,7) · 150,2= 1076,9 тыс. тенге Расчет срока окупаемости производиться по формуле:
Ток. = Ск / ЭГ (6.12)
Ток=18,3/1076,9= 2 месяца.
Срок окупаемости приспособления намного ниже нормативного (Тн=7 лет), что говорит о целесообразности внедрения данного приспособления в производство.
6.2 Расчет экономической эффективности технологического процесса агрегатного участка
Расчёт фонда заработной платы рабочих участка агрегатного ремонта
Расчёт заработной платы начинается с определения разряда, по которому выполняются работы. Каждому разряду соответствует средняя, часовая тарифная ставка Cч.
а) Определяем тарифную заработную плату:
ЗПтар. = Сч · Т, тенге, (6.13)
где Т — трудоёмкость цеха, чел.час.
Сч— тарифная ставка рабочего=140 тенге (по данным бухгалтерии предприятия) ЗПтар.=140 · 39 835=5576,9 тыс. тенге б) Определяем премию за качественную работу в размере 20% от тарифной заработной платы Спр = ЗПтар.· 20 /100, тенге. (6.14)
Спр=5576,9· 20/100=1115,4 тыс. тенге в) Доплату за вредные условия труда:
Дву= Сч · %ву Nву/100 (6.15)
где %вупроцент доплаты за вредные условия, принимаем 15% (приказ № 111n Министерства труда и соц. защиты РКот 12.05 2000г).
Дву=140· 0,15·5576,9/100=1171 тыс. тенге г) Определяем основную заработную плату ОЗП = ЗПтар +Спр+ Дву, тенге. (6.16)
ОЗП=5576,9+1115,4+1171=7863,4 тыс. тенге д) Определяем дополнительную заработную плату, которая берётся в % от ОЗП
ДЗП = ОЗП· 9,5 /100, тенге. (6.17)
ДЗП=7863,4 · 9,5/100= 747 тыс. тенге е) Определяем общий фонд заработной платы
ФЗП = ОЗП + ДЗП, тенге (6.18)
ФЗП=7863,4+747=8610,4 тыс. тенге ж) Определяем отчисления на социальные нужды:
1) Отчисления в пенсионный фонд Опф = ФЗП · 10 /100, тенге. (6.19)
Опф=8610,4 · 10/100=861 тыс. тенге
2) на социальный налог
Осоц=8610,4 · 0,21=1808,2 тыс. тенге Расчет производится на основании таблицы ставок для исчисления социального налога [24]:
з) Определяем среднемесячную заработную плату рабочих
ЗПср.мес. = ФЗП / Nр · 12, тенге, (6.20)
где Nр — число работников, чел.
ЗПср.мес.=8610,4/ 22· 12 = 32 615 тенге
Расчёт затрат на ремонтные материалы
Норма затрат на ремонтные материалы установлены на 1000 км пробега и корректируются через коэффициенты К1, К2, К3 .
а) Определяем затраты на ремонтные материалы Зм = (Нм · Lобщ. / 1000) · К1· К2 · К3, тенге, (6.21)
где Нм — удельная норма затрат на ремонтные материалы, тенге
Зм = (186,4 · 35 084 427/1000) · 1,2 · 1,03 · 1,05=8486 тыс. тенге
б) Определяем затраты на запасные части Зз.ч.= (Нз.ч. · Lобщ / 1000) · К1 · К2· К3, тенге. (6.22)
Зз.ч.= (204· 35 084 427/1000) · 1,2 · 1,03 · 1,05=9288 тыс. тенге Таблица 6.1 Виды затрат
Вид затрат | Сумма, тыс. тенге | |
Материалы | ||
Зап. части | ||
Расчет стоимости оборотных средств участка
Расчет стоимости оборотных средств ведется раздельно по зданиям и оборудованию.
Стоимость здания определяется в следующем порядке:
а) определяем стоимость зданий производственного назначения (агрегатного участка), исходя из цены 1 м2 здания и площади
Суч=Fуч · Ц, тенге, (6.23)
где Суч — стоимость участка ТР;
Ц — цена 1 м2 здания (принимаем по укрупненным нормам стоимость 1 м2 здания — 52,0 тыс. тенге) Суч=52 · 95=4940 тыс. тенге б) Определяем стоимость оборудования и инвентаря, которые составляют для участка 70% их стоимости;
Собор.уч=Суч· 70% /100 (6.24)
Собор.уч=4940· 0,7=3458 тыс. тенге в) определяем стоимость основных производственных фондов (ОПФ)
ОПФ=Суч+Собор., тенге. (6.25)
ОПФ=4940+3458= 8398 тыс. тенге
Расчет сметы накладных расходов.
Смета расходов включает в себя все затраты, связанные с управлением и обслуживанием производства, а также с содержанием и ремонтом зданий и оборудования.
а) Амортизация зданий и оборудования принимается 6% в год от их стоимости:
Аоф=ОПФ· 6%/100, тенге. (6.26)
Аоф= 4940 · 0,06=296,4 тыс. тенге б) Содержание зданий и оборудования составляет 2,5% от их стоимости:
Сзд=ОПФ· 2,5% /100, тенге. (6.27)
Сзд= 3458· 0,025=86,5 тыс. тенге в) Затраты на ТР зданий и оборудования принимается в размере 40% от стоимости зданий и оборудования:
Зт.р=ОПФ· 40% /100, тенге. (6.28)
Зт.р=4940 · 0,4=1976 тыс. тенге г) Расходы на охрану труда и ТБ составляют 2% от ФЗП производственных рабочих:
Зо.т и т. б=ФЗПрр· 2% /100,тенге. (6.29)
Зо.т и т. б=3458 · 0,02=69,7 тыс. тенге д) Прочие расходы составляют 3% от суммы затрат по перечисленным статьям.
Спр= 20 060· 0,03=600,5 тыс. тенге Таблица 6.2 Статьи расходов
Статьи расходов | Сумма (тыс.тенге) | |
Заработная плата рабочих с отчислениями | 11 279,6 | |
Амортизация зданий и оборудования | 296,4 | |
Стоимость основных производственных фондов | 8398,0 | |
Содержание зданий и оборудования | 86,5 | |
Текущий ремонт зданий и оборудования | 1976,0 | |
Расходы на охрану труда и ТБ | 69,7 | |
Прочие расходы | 600,5 | |
Всего накладных расходов | 22 706,7 | |
Смета затрат и калькуляция себестоимости.
Смета затрат включает в себя все затраты, связанные с выполнением работ по участку в течение года.
Таблица 6.3 Смета затрат по агрегатному участку
№ | Статьи затрат | Сумма, тенге | |
Фонд заработной платы вспомогательных ремонтных рабочих с отчислениями от заработной платы, тыс. тенге | |||
Затраты на материалы, тыс. тенге | |||
Затраты на запасные части, тыс. тенге | |||
Сумма прочих накладных расходов, тыс. тенге | 22 706,7 | ||
Итого затрат, тыс. тенге | 44 270,7 | ||
Общий пробег (в среднем), тыс. км | 35 084,4 | ||
Себестоимость 1 км, тенге | 1,26 | ||
Рассчитываем себестоимость единицы технического воздействия по формуле:
С/С = затрат / Lобщ · 1000, тенге, (6.30)
где Lобщ— общий пробег автомобиля с прицепом.
С/С =44 270,4/35 084,4 · 1000=1266 тенге
6.3 Расчёт экономической эффективности и технико-экономическое обоснование
В результате внедрения различных организационнотехнических мероприятий, направленных на снижение материальных и трудовых затрат происходит снижение себестоимости работ.
Определяем % снижения себестоимости по формуле:
% сниж. с/с = (Сх— Спр) /Сх) · 100%, (6.31)
где Спр — проектная себестоимость, тенге;
Сх — себестоимость в автохозяйстве, тенге.
% сниж. с/с =(1456−1266)/1456· 100% = 13%
Определяем годовой экономический эффект по формуле:
Эг = (Сх — Спр) · Lобщ /1000, тенге. (6.32)
Эг = (1456−1266)· 35 084 400/1000=6666,0 тыс. тенге В результате данной работы были рассчитаны технико-экономические показатели работы предприятия, проанализировав которые мы можем найти пути улучшения результатов деятельности предприятия.
Из расчетов видно, что большую часть себестоимости составили затраты по заработной плате (42,1%). Гораздо меньше составили накладные расходы (33,7%), но тоже весомую долю. Расходы на материалы заняли не значительную долю (12,4%)
Т.к. большую часть себестоимости составили затраты по оплате труда, то для возможного снижения себестоимости необходимо снижение затрат на оплату труда за счет установки нового оборудования и сокращения числа рабочих, но это повлечет за собой дополнительные капитальные затраты. А также необходимо проанализировать экономическую целесообразность всех материальных затрат: оптимальность и эффективность их использования.
Также в себестоимости продукции велика доля накладных расходов. Можно проверить возможность снижения затрат, связанных с затратами на охрану труда и ТБ, содержание зданий и оборудования, можно проверить возможность сокращения штата управленческого персонала, специалистов и служащих.
Заключение
В настоящее время рынок грузового автотранспорта Республики Казахстан в большей степени насыщен автомобилями Российского производства. Самая распространенная марка автомобиля — КамАЗ.
В процессе работы проанализированы результаты хозяйственно-производственной деятельности товарищества с ограниченной ответственностью «Костанайский автоцентр КамАЗ». Результаты обследования обкаточного участка свидетельствуют о нарушениях технологического процесса и низком выходном контроле ремонтируемых двигателей.
В процессе работы выполнены следующие задачи:
— рассмотрен проект организации грузовых перевозок и ремонта автомобилей в ТОО «Автоцентр КамАЗ» ;
— обоснована производственная программа предприятия, проведена оценка его места расположения;
— определен режим работы и фонды времени по участкам, разработан годовой план работ в 2011 году;
— разработаны рекомендации к наиболее ответственному — обкаточно-испытательному участку;
— в результате внедрения конструкторской разработки было достигнуто снижение затрат на производство работ и повысили качество выполняемых работ.
Предложенные мероприятия по модернизации обкаточно-испытательного участка позволили значительно сократить расход дизельного масла, применяемого при обкатке двигателей.
Внедрение разработанных рекомендаций по организации ремонта автомобилей в ТОО «Костанайский автоцентр КамАЗ» позволит получать экономическую эффективность в сумме 1076,9 тысячи тенге в год.
Срок окупаемости приспособления составил 2 месяца, что намного ниже нормативного (Тн=7 лет), что говорит о целесообразности внедрения данного приспособления в производство.
1. Афанасьев Л. Л., Островский Н. Б., Цукерберг С. М. «Единая транспортная система и автомобильные перевозки». М., Транспорт 1984 г.
2. Фастовцев В. Г. «Единая транспортная система и автомобильные перевозки». Методические указания М., Транспорт 1986 г.
3. «Положение о ТО и ТР подвижного состава автомобильного транспорта» М., Транспорт 1988 г.
4. Крамаренко Г. В. и др. «Техническая эксплуатация автомобилей». М., Транспорт 1988 г.
5. МИИАТ Краткий автомобильный (транспортный) справочник. М., Транспорт 1987 г.
6. «Прейскурант № 07 — 02 от 24.12.01. Оптовые цены на нефтепродукты», ТНК, 2 стр.
7. Иворев С. А. «Экономические вопросы при организации работы АТП», М., Высшая школа, 1991 г., 132 стр.
8. Долик П. А. «Справочник по технике безопасности», М., Энергосетьиздат, 1984 г.
9. ГОСТ 12.0.003 — 80 ССБТ. «Опасные и вредные производственные факторы».
10. ГОСТ 12.4.011 — 75 «Средства защиты рабочих».
11. Серов И. П. «Методики определения оптовых цен на продукцию машиностроительного комплекса», М., Экономиздат, 1993 г.
12. «Экономические вопросы в дипломном проекте». Методические указания, Рязанская ГСХА, Рязань 1999 г.
13. Решетов Д. Н. «Детали машин». Издание 4-ое. М., Машиностроение, 1989 г.
14. «Нормы амортизационных отчислений и методы определения оптовых цен на продукцию машиностроения», под редакцией Симонева А. А. М., Экономика, 1992 г.
15. ГОСТ 12.0.003 — 86 ССБТ «Опасные и вредные производственные факторы».
16. Демин П. А. «Справочник по технике безопасности». М., 1988 г.
17. Напольский Г. М. «Технологическое проектирование автотранспортных предприятий и станций ТО». Учебник для ВУЗов, М., Транспорт 1985 г.
18. «Краткий справочник НИИАТ». М., Транспорт 1982 г.
19. ГОСТ 12.1.004 — 76 ССБТ «Пожарная безопасность. Общие требования».
20. «Охрана труда». Методические указания по дипломному проектированию, Рязанская ГСХА, Рязань 1998 г.
21. ГОСТ 12.1.005 — 76 ССБТ «Воздух в рабочей зоне. Общие санитарно-технические требования».
22. ГОСТ 12.1.003 — 80 ССБТ «Шум. Общие требования безопосности».
23. ГОСТ 12.01.02 — 88 ССБТ «Вибрация. Общие требования безопасности».
24. СНиП II — 4 — 79 «Естественное и искусственное освещение».
25. Новак В. М. и др. «Справочник технолога машиностроителя». М., Машиностроение 1983 г.
26. Великанов К. М. и др. «Производительность, экономика и организация труда токаря». М., Машиностроение 1984 г.
27. Александров Л. А. «Техническое нормирование на автомобильном транспорте». М., Транспорт 1978 г.
28. Аршинов В. А., Алексеев Т. Р. «Резание металлов и режущие инструменты». М., Машиностроение 1983 г.
29. Черпаков С. С. «Техническое обслуживание и ремонт автобусов». М., Колос 1978 г.
30. Боков В. Н. «Детали машин». М., Высшая школа 1960 г.
31. Кузнецов Е. С. «Техническая эксплуатация автомобилей». Учебник для ВУЗов 3-е издание. М., Транспорт 1991 г., 413 стр.