Разработка научных основ технологии переиспытаний нефтепроводов
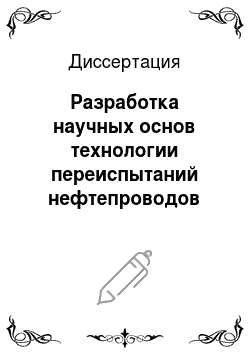
Диссертация
В настоящее время для обеспечения надежной работы трубопровода, имеющего участки с уменьшенной несущей способностью, применяют ряд методов: перекачку продукта производят при давлении ниже проектного, на отдельных участках или по всей длине трубопровода прокладывают лупинги, производят ремонт стенок трубопровода путем заплавки коррозионных язв, приваркой усилительных накладных элементов. Если… Читать ещё >
Список литературы
- Александров A.A., Пирогов А. Г., Велиев М. М., Воробьев В. А. Взаимосвязь локальных и номинальных напряжений в трубных сталях // Прикладная механика механохимического разрушения. Уфа: «БЭСТС», 2004. — № 3. -С. 23−25.
- Березин B. JL, Постников В. В., Ясин Э. М. Испытание магистральных нефтепроводов как метод повышения надежности.- М.: ВНИИОЭНГ, 1972. -47 с.
- Байкова И.В. Влияние внешней растягивающей нагрузки на сварочные напряжения и деформации // Сварочное производство. 1969. — № 6. -С. 3−5.
- Бакши O.A., Зайнуллин P.C. О снятии сварочных напряжений в соединениях с механической неоднородностью приложением внешней нагрузки // Сварочное производство. -1973.-№ 7. С.5−7.
- Бабич В.К., Гуль Ю. П., Долженков И. Е. Деформационное старение стали. М.: Металлургия, 1972. — 241 с.
- Болотин В.В. Ресурс машин и конструкций. М.: Машиностроение, 1975. — 448 с.
- Брукс Л.Э. Гидростатические методы испытаний трубопроводов // Инженер-нефтяник. 1967. — № 10. — С. 74−78.
- Волский М.И., Аистов A.C., Гусенков А. П., Гуменный JI.K. Прочность труб магистральных нефте- и продуктопроводов при статическом и малоцикловом нагружениях // Транспорт и хранение нефти и нефтепродуктов. М.: ВНИИОЭНГ, 1979. — 50 с.
- ГОСТ 25–506−85. Расчеты и испытания на прочность. Методы механических испытаний металлов. Определение характеристик трещиностойкости (вязкости разрушения) при статическом нагружении. М.: Изд-во стандартов, 1985.-61 с.
- ГОСТ 9905–82 (CT СЭВ 3283−81). Методы коррозионных испытаний.- М.: Изд-во стандартов, 1982.
- Гутман Э.М. Механохимия металлов и защита от коррозии. М.: Металлургия, 1981.-271 с.
- Гутман Э.М., Зайнуллин P.C. Определение прибавки к толщине стенок сосудов и трубопроводов на коррозионный износ // Химическое и нефтяное машиностроение. 1983. -№ 11. — С. 38−40.
- Галюк В.Х. Испытания действующих нефтепроводов // Обзорная информация. М.: ВНИИОЭНГ, 1985. — 53 с.
- Гутман Э.М., Зайнуллин P.C. Оценка скорости коррозии нагруженных элементов трубопроводов и сосудов давления // Физико-химическая механика материалов. 1984. — № 4. — С. 95−97.
- Гутман Э.М., Зайнуллин P.C., Зарипов P.A. Кинетика механохимиче-ского разрушения и долговечность растянутых конструктивных элементов при упругопластических деформациях // Физико-химическая механика материалов.- 1984.-№ 2.-С. 14−17.
- Гутман Э.М., Зайнуллин P.C. К методике длительных коррозионно-механических испытаний металла газопромысловых труб // Заводская лаборатория. 1978.-№ 4. — С. 63−65.
- Гутман Э.М., Зайнуллин P.C., Шаталов А. Г., Зарипов P.A. Прочность газопромысловых труб в условиях коррозионного износа. М.: Недра, 1984. -75 с.
- Гумеров А.Г., Зайнуллин P.C., Ямалеев K.M., Росляков A.B. Старение труб нефтепроводов. М.: Недра, 1995. — 222 с.
- Методика определения трещиностойкости материала труб нефтепроводов: РД 39−147 103−387−87. М., 1987. — 36 с.
- Гумеров А.Г., Зайнуллин P.C. Безопасность нефтепроводов. М.: Недра — Бизнесцентр, 2000. — 310 с.
- Гумеров А.Г., Зайнуллин P.C., Гумеров Р.С и др. Восстановление работоспособности труб нефтепроводов. Уфа: Башк. кн. изд-во, 1992. — 240 с.
- Гумеров А.Г. и др. Периодичность испытаний нефтепроводов / А. Г. Гумеров, P.C. Зайнуллин, А. Г. Пирогов. Уфа: МНТЦ «БЭСТС», 2000.97 с.
- Гумеров А.Г. и др. Периодичность испытаний нефтепроводов / А. Г. Гумеров, P.C. Зайнуллин, А. Г. Пирогов. Уфа: Транстэк, 2001. — 130 с.
- Гумеров А.Г., Худякова Л. П., Пирогов А. Г. Повышение ресурса оборудования, работающего в сероводородсодержащей нефти // Мониторинг и безопасность трубопроводных систем. Уфа: Транстэк, 2004. — № 1. — С. 3−10.
- Гумеров А.Г., Зайнуллин P.C., Пирогов А. Г. Оценка ресурса по параметрам испытаний // Мониторинг и безопасность трубопроводных систем. Уфа: Транстэк, 2004. — № 1. С. 16−21.
- Зайнуллин P.C., Тулумгузин М. С., Постников В. В. Определение параметров гидравлических испытаний//Строительство трубопроводов. 1981. -№ 9. — С. 23−25.
- Зайнуллин P.C. Влияние давления испытания на долговечность труб, работающих в коррозионных средах // Нефтяное хозяйство. 1987. -№ 1. — С. 54−56.
- Зайнуллин P.C., Халимов A.A. Ремонт сваркой элементов оборудования из стали 15Х5М без опорожнения от продукта // Обеспечение работоспособности нефтяной аппаратуры. Уфа: БашНИИстрой, 1999. — С. 43−56.
- Зайнуллин P.C., Черных Ю. А., Оськин Ю. В. Остаточные напряжения в кольцевых швах сосудов и трубопроводов после гидравлических испытаний // Обеспечение работоспособности действующих нефте- и продуктопроводов. -М.: ЦЩГИХИМНЕФТЕМАШ, 1992. С. 55−64.
- Зайнуллин P.C., Черных Ю. А. Особенности гидравлических испытаний сосудов и аппаратов повышенным давлением // Информационный сборник ЦИНТИХИМНЕФТЕМАШ. 1992. — № 2. — С. 22−23.
- Зайнуллин P.C., Черных Ю. А., Шарафиев Р. Г. и др. Роль гидравлических испытаний в формировании показателей качества нефтегазоперерабаты-вающего оборудования и нефтепроводов. Уфа: МНТЦ «БЭСТС», — 1997. — 88 с.
- Зайнуллин P.C. Влияние параметров режима гидравлических испытаний на прочность и долговечность трубопроводов // Обеспечение надежности магистральных нефтепроводов в условиях эксплуатации. Уфа: ВНИИСПТнефть, 1986. — С. 32−39.
- Зайнуллин P.C., Пирогов А. Г., Велиев М. М. Определение долговечности сосудов при малоцикловом нагружении // Перспективы развития трубопроводного транспорта России. Тез. докл. конф. 22 мая 2002 г. Уфа: Транстэк, 2002.-С. 13−16.
- Расчет предельного состояния газопроводных труб с дефектами / P.C. Зайнуллин, A.C. Надршин, Р. Х. Хажиев и др. М.: Недра, 2002.-90с.
- Зайнуллин P.C., Велиев М. М., Тарабарин О. И., Медведев А. П., Пирогов А. Г. Метод расчета элементов конструкций // Обеспечение работоспособности трубопроводов. Сб. научн. тр. М.: Недра, 2002. — С. 7−9.
- Зайнуллин P.C., Пирогов А. Г. Оценка остаточного ресурса трубопроводов и их конструктивных элементов по параметрам испытаний // Обеспечение работоспособности трубопроводов: Сб. научн. тр. М.: Недра, 2002. -С. 6.
- Зайнуллин P.C., Пирогов А. Г., Щепин J1.C., Велиев М. М. Метод расчета ресурса трубопроводов при малоцикловом нагружении // Обеспечениеработоспособности трубопроводов: Сб. научн. тр. М.: Недра, 2002. — С. 11.
- Зайнуллин P.C., Гильфанов Р. Г., Вахитов А. Г., Пирогов А. Г., Велиев М. М. Оценка пригодности бездействующих труб // Обеспечение работоспособности трубопроводов: Сб. научн. тр. М.: Недра, 2002. — С. 16.
- Зайцев К.И. Межотраслевой семинар «Старение трубопроводов, технология и техника их диагностики и ремонта» // Трубопроводный транспорт нефти. 1996. — № 11. — С. 15−18.
- Зайнуллин P.C., Шарафиев Р. Г., Ямуров Н. Р., Мокроусов С. Н. Оценка предельных состояний при испытаниях элементов оборудования с трещиноподобными дефектами // Заводская лаборатория (диагностика материалов). 1996. — № 11. — С. 50−51.
- Зайнуллин P.C., Пирогов А. Г. Расчетная оценка ресурса элементов оборудования на основе априорной информации // Ресурс сосудов и трубопроводов. Уфа: Транстэк, 2000. — С. 82−86.
- Зайнуллин P.C., Абдуллин P.C., Пирогов А. Г. Исследование трещи-ностойкости элементов оборудования с учетом конструкционного и эксплуатационного факторов // Ресурс сосудов и трубопроводов. Уфа: Транстэк, 2000. — С. 87−94.
- Зайнуллин P.C., Абдуллин P.C., Пирогов А. Г. Малоцикловая коррозионная трещиностойкость элементов трубопроводов // Ресурс сосудов и трубопроводов. Уфа: Транстэк, 2000. — С. 108−109.
- Зайнуллин P.C., Шарафиев Р. Г. Сертификация нефтегазохимического оборудования по параметрам испытаний. М.: Недра, 1998. — 447 с.
- Зайнуллин P.C., Шарафиев Р. Г., Ямуров Н. Р. Определение остаточного ресурса элементов конструкций. М: МИБ СТС, 1996. — 160 с.
- Зайнуллин P.C. Обеспечение работоспособности оборудования в условиях механохимической повреждаемости. Уфа: ИПК Госсобрания РБ, 1997. — 426 с.
- Зайнуллин P.C., Бакши O.A., Абдуллин P.C., Вахитов А. Г. Ресурс нефтехимического оборудования с механической неоднородностью. М.: Недра, 1998. — 268 с.
- Зайнуллин P.C., Гумеров А. Г. Повышение ресурса нефтепроводов. -М.: Недра, 2000. 494 с.
- Зайнуллин P.C., Гумеров А. Г., Морозов Е. М. и др. Гидравлические испытания действующих нефтепроводов. М.: Недра, 1990. — 224 с.
- Расчеты ресурса оборудования и трубопроводов с учетом фактора времени / P.C. Зайнуллин, А. Г. Вахитов, О. И. Тарабарин и др- под ред. P.C. Зайнуллина. М.: Недра, 2003. — 50 с.
- Зайнуллин P.C., Тарабарин О. И., Пирогов А. Г. и др. Новый метод расчета малоцикловой долговечности оборудования и трубопроводов с учетом старения металла // Безопасность сосудов и трубопроводов: Сб. научн. тр. М.: Недра, 2003. — С. 14−17.
- Иванова B.C., Гордиенко JI.K., Геминов В. Н. и др. Роль дислокаций в упрочнении и разрушении металлов. М.: Наука, 1965. — 180 с.
- Ирмяков Р.З. и др. Вопросы испытаний на надежность объектов магистральных нефтепроводов. М.: ВНИИОЭНГ, 1982. — 36 с.
- Иванцов О.М., Харитонов В. И. Надежность магистральных трубопроводов. М.: Недра, 1987. — 165 с.
- Справочник по коэффициентам интенсивности напряжений / Ю. Ито, Ю. Муракми, Хасебэ и др. М.: Мир, 1990. — Т. 1 — 2. — 1016 с.
- Иванова B.C., Гордиенко JI.K., Геминов В. Н. и др. Роль дислокаций в упрочнении и разрушении металлов. М.: Наука, 1965. — 180 с.
- Климовский Е.М. Гидравлические испытания магистральных трубопроводов: Научно-технический обзор. М.: Информнефтегазстрой, 1980. -41 с.
- Карзов Г. П., Леонов В. П., Тимофеев Б. Г. Сварные сосуды высокого давления. Л.: Машиностроение, 1982. — 287 с.
- Когут Н.С., Шахматов М. В., Ерофеев В. В. Несущая способность сварных соединений. Львов: Свит, 1991. — 184 с.
- Касаткин О.Г. Расчетная оценка сопротивляемости металла шва развитию усталостных трещин // Автоматическая сварка. 1985. — № 12. -С. 1−4.
- Коцаньда С. Усталостное разрушение металлов. М.: Металлургия, 1976.-456 с.
- Когаев В.П., Махутов H.A., Гусенков А. П. Расчеты деталей машин и конструкций на прочность и долговечность: Справочник. М.: Машиностроение, 1985.-224 с.
- Куркин С.А. Прочность сварных тонкостенных сосудов, работающих под давлением. М.: Машиностроение, 1976. — 184 с.
- Лютцау В.Г. Современные представления о структурном механизме деформационного старения и его роли в развитии разрушения при малоцикловой усталости // Структурные факторы малоциклового разрушения. М.: Наука, 1977. С. 5−19.
- Лобанов Л.М., Махненко В. И., Труфяков В. И. Основы проектирования конструкций. Киев: Наукова думка, 1993. — Том 1. — 416 с.
- Мэнсон С. Температурные напряжения и малоцикловая усталость. -М.: Машиностроение, 1974. 344 с.
- Махутов H.A. Сопротивление элементов конструкций хрупкому разрушению. М.: Машиностроение, 1973. — 200 с.
- Морозов Е.М., Зайнуллин P.C., Пашков Ю. И., Гумеров P.C. и др. Оценка трещиностойкости газонефтепроводных труб. М.: МИБ СТС, 1997. -75 с.
- Морозов Е.М., Зайнуллин Р.С, Шарафиев Р. Г. Механика развития трещин в деталях конструкций при испытаниях и эксплуатации. Уфа: УГНТУ, 1996. — 88 с.
- Морозов Е.М., Фридман Я. Б. Анализ трещин как метод оценки характеристик разрушения // Заводская лаборатория. 1996.-№ 8.-С. 977−984.
- Махутов H.A. Деформационные критерии разрушения и расчет элементов конструкций на прочность. М.: Машиностроение, 1981. — 237 с.
- Механические свойства конструкционных материалов при низких температурах: Сб. научн. тр.: Пер. с англ. / Под ред. М. Н. Фридляндера. М.: Металлургия, 1983. — 432 с.
- Морозов Е.М. Расчет на прочность при наличии трещин // Прочность материалов и конструкций. Киев: Наукова думка, 1975. — С. 375−382.
- Мороз J1.C., Чечулин Б. Б. Водородная хрупкость металлов. М.: Металлургия, 1967. — 255 с.
- Механические напряжения котлов, работающих под давлением, из стали 18G2A. Катовице, 1984. — 76 с.
- Методика оценки работоспособности труб линейной части нефтепроводов на основе диагностической информации: РД 39−147 105−001−91. -Уфа: ВНИИСПТнефть, 1992. С. 120−125.
- Методика по выбору параметров труб и поверочного расчета линейной части магистральных нефтепроводов: РД 39−147 103−361−86. Уфа: ВНИИСПТнефть, 1987. — 38 с.
- Морозов Е.М. Техническая механика разрушения. Уфа: МНТЦ «БЭСТС», 1997.-429 с.
- Методика оценки ресурса остаточной работоспособности технологического оборудования нефтеперерабатывающих, нефтехимических и химических производств. Волгоград: ВНИКТИнефтехимоборудования, 1991. — 44 с.
- Методика контроля и оценки пригодности труб, бывших в эксплуатации. М.: Металлургия, 1996. — 12 с.
- Механика разрушения и прочность материалов: Справочное пособие. Киев: Наукова думка, 1988. — Т. 2. — 619 с.
- Методика оценки ресурса оборудования по параметрам испытаний и эксплуатации / Под ред. P.C. Зайнуллина. М.: Металлургия, 1996. — 10 с.
- Морозов Е.М., Зайнуллин P.C., Пашков Ю. И., Гумеров P.C., Мокро-усов С.Н., Ямуров Н. Р. Оценка трещиностойкости газонефтепроводных труб. -М.: МИБ СТС, 1997. 75 с.
- Николаев Г. А., Куркин С. А., Винокуров В. А. Сварные конструкции. Прочность сварных соединений и деформации конструкций. М.: Высшая школа, 1982. — 272 с.
- Мокроусов С.Н., Пирогов А. Г., Макаров Ю. В. Оценка периодичности испытаний нефтепроводов // Прикладная механика механохимического разрушения. Уфа: МНТЦ «БЭСТС», 2003. — № 3. — С. 22−29.
- Нейбер Г. Концентрация напряжений. М.: ГИТЛ, 1974. — 204 с.
- Навроцкий Д.И. Расчет сварных соединений с учетом концентрации напряжений. Л.: Машиностроение, 1968. — 170 с.
- Новые методы оценки сопротивления металлов хрупкому разрушению. М.: Мир, 1972. — 439 с.
- Надршин A.C. Разработка методов оценки ресурса демонтированного оборудования нефтехимических производств: Автореф. канд. техн. наук. Уфа, 1996. — 23 с.
- Нормы расчета на прочность оборудования и трубопроводов атомных энергетических установок. М.: Энергоатомнадзор, 1989. — 525 с.
- Зайнуллин P.C. и др. Оценка ресурса сосудов и трубопроводов по критериям статической прочности / P.C. Зайнуллин, A.C. Надршин, М. Н. Кожикин. Уфа: МНТЦ «БЭСТС», 1995. — 47 с.
- РИО РУМНЦ МО РБ, 2004. С. 91−102.
- Обеспечение работоспособности нефтепроводов и сосудов работающих под давлением / Под ред. проф. P.C. Зайнуллина. Уфа: Изд-во ИПТЭР, 1999.-112 с.
- Обеспечение работоспособности сосудов и трубопроводов / Под ред. проф. P.C. Зайнуллина. М.: ЦИНТИХИМНЕФТЕМАШ, 1991. — 44 с.
- Окерблом Н.О. и др. Проектирование технологии изготовления сварных конструкций / Н. О. Окерблом, В. П. Демянцевич, И. П. Бажова. JL: Суд-промгиз, 1963.- 602 с.
- Пирогов А.Г. Определение запаса по коррозионной долговечности нефтепроводов, обеспечиваемого гидравлическими испытаниями // Ресурс сосудов и трубопроводов. Уфа: Транстэк, 2000. — С. 4−10.
- Пирогов А.Г. Выбор параметров режима испытаний элементов оборудования // Ресурс сосудов и трубопроводов. Уфа: Транстэк, 2000. — С. 79−81.
- Пирогов А.Г. Расчеты ресурса элементов оборудования по критериям малоцикловой трещиностойкости // Ресурс сосудов и трубопроводов. Уфа: Транстэк, 2000. — С. 106−107.
- Пирогов А.Г. Обеспечение работоспособности действующих нефтепроводов регламентацией сроков переиспытаний: Автореф. канд. техн. наук. -Уфа: ИПТЭР,-2001.-23 с.
- Пирогов А.Г., Кузнецов Д. Б., Хажиев Р. Х., Хажиев P.P. Натурные испытания муфт нефтепроводов // Обеспечение работоспособности трубопроводов. Сб. научн. тр. М.: Недра, 2002. — С. 18−22.
- Пирогов А.Г. Оценка предельных параметров коррозионных повреждений трубопроводов // Безопасность сосудов и трубопроводов: Сб. научн. тр. -М.: Недра, 2003. С. 53−54.
- Пирогов А.Г., Велиев М. М., Хажиев P.P. Повышение надежности и металлоемкости ремонтных муфт и нефтепроводов // Безопасность сосудов и трубопроводов: Сб. научн. тр. М.: Недра, 2003. — С. 55−58.
- Пирогов А.Г., Кузнецов Д. Б., Щепин JI.C. Проблемы прогнозирования ресурса трубопроводов при циклических нагрузках // Прикладная механика механохимического разрушения. Уфа: МНТЦ «БЭСТС», 2003. — № 4. — С. 4−8.
- Пирогов А.Г., Кузнецов Д. Б., Хажиев Р. Х., Хажиев P.P. Несущая способность труб с отверстиями // Прикладная механика механохимического разрушения. Уфа: МНТЦ «БЭСТС», 2003. — № 4. — с. 27−30.
- Пирогов А.Г., Кузнецов Д. Б. Определение напряжений при приварке накладных элементов на трубы под коррозией // Мониторинг и безопасность трубопроводных систем. Уфа: Транстэк, 2004. — № 1 — С. 13−14.
- Пирогов А.Г. Правила по расчету тарифов на транспорт нефти по магистральным трубопроводам // Нефтяное хозяйство. 2003. — № 7. — С. 110−111.
- Пирогов А.Г. Перспективы развития и совершенствование технологических процессов в трубопроводном транспорте Республики Казахстан // Нефтяное хозяйство. 2003. — № 7. — С. 108−109.
- Пирогов А.Г., Кузнецов Д. Б., Велиев М. М. Эффективность испытаний накладных элементов // Мониторинг и безопасность трубопроводных систем. Уфа: Транстэк, 2004. — № 1. — С. 15.
- Пирогов А.Г. и др. Оценка качества труб по данным диагностики испытаний / А. Г. Пирогов, A.A. Александров, В. А. Воробьев, В. В. Семено. — Уфа: МНТЦ «БЭСТС», 2004. 52 с.
- Пирогов А.Г. и др. Обеспечение безопасности оборудования переиспытаниями / А. Г. Пирогов, A.A. Александров, В.А. Воробьев- Под ред. проф. P.C. Зайнуллина. Уфа: РИО РУНМЦ Министерства образования Республики Башкортостан, 2004. — 32 с.
- Оценка технического состояния и ресурса нефтегазохимического оборудования / P.C. Зайнуллин, А. Г. Гумеров, А. Г. Халимов и др. М.: Недра, 2004.-286 с.
- Методики определения максимального разрешенного давления трубопроводов с учетом дефектности металла / P.C. Зайнуллин, С. Н. Мокроусов, А. Г. Вахитов и др. М.: Недра, 2003. — 54 с.
- Оценка остаточного ресурса трубопроводов и их конструктивных элементов по параметрам испытаний: Методические рекомендации / P.C. Зайнуллин, С. Н. Мокроусов, А. Г. Пирогов и др. М.: Недра, 2003. — 15 с.
- Никитин Ю.Г., Макаров Ю. В., Пирогов А. Г. Анализ разрушений трубопровода с коррозионной язвой // Прикладная механика механохимического разрушения. Уфа: МНТЦ «БЭСТС», 2003. — № 3. — С. 17−19.
- Пимштейн П.Г. и др. Расчет предварительной перегрузки сварных сосудов давления. Конструирование, исследование и расчеты аппаратов и трубопроводов высокого давления // Труды НИИХИММАШ. 1997. — № 76. -С. 45 — 49.
- Поведение стали при циклических нагрузках / Под ред. проф. В. Даля. М.: Металлургия, 1983. — 568 с.
- Порядок разработки декларации безопасности промышленного объекта Российской Федерации. М.: Госгортехнадзор РФ, 1996. — 22 с.
- РД 50−345−82. Определение характеристик трещиностойкости (вязкости разрушения) при циклическом нагружении. М.: Изд-во стандартов, 1983. -94 с.
- Романов О.Н., Никифорчин Н. И. Методика коррозионного разрушения конструкционных сплавов. М.: Металлургия, 1986. — 294 с.
- РД 03−85−95. Правила сертификации поднадзорной продукции для потенциально опасных промышленных производств, объектов и работ. — М.: Госгортехнадзор России, 1995. 8 с.
- РД 50−345−82. Определение характеристик трещиностойкости (вязкости разрушения) при циклическом нагружении. М.: Изд-во стандартов, 1986.-95 с.
- РД 39−147 103−361−86. Методика по выбору параметров труб и поверочный расчет линейной части магистральных нефтепроводов на малоцикловую прочность. Уфа: ВНИИСПТнефть, 1987. — 56 с.
- Рождественский В.В. и др. Испытания трубопроводов повышенным давлением // Научно-технич. обзор. М.: НИПИ ЭСУ нефтегазстрой, 1977. — 64 с.
- СНиП Ш-42−80. Строительные нормы и правила. Часть III. — М.: Стройиздат, 1981. 80 с.
- Стеклов О.И. Стойкость материалов и конструкций к коррозии под напряжением. М.: Машиностроение, 1990.-384 с.
- Сигорский В.П. Математический аппарат инженера. Киев: Техника, 1978.-768 с.
- Структура и коррозия металлов и сплавов / Под ред. Е. А. Ульянина. -M.: Металлургия, 1989. 400 с.
- Сущев С.П., Пирогов А. Г. Оценка долговечности труб по критериям механики разрушения // Мониторинг и безопасность трубопроводных систем. -Уфа: Транстэк, 2004. № 1. — С. 27−30.
- Прочность при малоцикловом нагружении / C.B. Серенсен, P.M. Шнейдерович, А. П. Гусенков и др. М.: Недра, 1975. — 392 с.
- Суханов В.Д. Определение свойств металла по измерениям твердости // Проблемы механики сплошных сред в системах добычи и транспорта нефти и газа. Тез. докл. Конгресса нефтегазопромышленников России. Уфа, 1998. — С. 83−84.
- Сергеева Т.К. Стресс-коррозионное разрушение магистральных газопроводов России // Безопасность трубопроводов. Тез. докл Междунар. научно — практич. конф. М., 1995. — С. 139−164.
- Сущев С.П., Кузнецов Д. Б., Пирогов А. Г. Повышение прочности накладных элементов труб // Мониторинг и безопасность трубопроводных систем. Уфа: Транстэк, 2004. — № 1. — С. 11−13.
- Тимошенко С.П., Войновский-Кригер С. Пластинки и оболочки. М.: Физматгиз, 1963. — 526 с.
- Тарабарин О.И., Пыльнов C.B., Пирогов А. Г. Способ снижения усилий правки обечаек и труб // Безопасность сосудов и трубопроводов: Сб. научн. тр. М.: Недра, 2003. — С. 29.
- Тарабарин О.И., Пыльнов C.B., Пирогов А. Г. Определение предельных деформаций при правке обечаек и труб // Безопасность сосудов и трубопроводов: Сб. научн. тр. М.: Недра, 2003. — С. 30−31.
- Тарабарин О.И., Вячин П. Ю., Пирогов А. Г. Влияние температуры эксплуатации на степень деформационного старения трубных сталей // Прикладная механика механохимического разрушения. Уфа: МНТЦ «БЭСТС», 2004. — № 1.. с. 28.
- Худякова Л.П., Пирогов А. Г. Влияние сероводорода на механическиесвойства трубных и резервуарных сталей // Прикладная механика механохими-ческого разрушения. Уфа: МНТЦ «БЭСТС», 2004. — № 1. — С.15−19.
- Худякова Л.П., Пирогов А. Г. Методика коррозионно-химических испытаний трубных и резервуарных сталей // Прикладная механика механохи-мического разрушения. Уфа: МНТЦ «БЭСТС», 2004. -№ 1.-С. 19−22.
- Худякова Л.П., Пирогов А. Г., Гумеров P.P. Оценка скорости сероводородного растрескивания // Прикладная механика механохимического разрушения. Уфа: МНТЦ «БЭСТС», 2004. — № 1. — С. 23−24.
- Хрупкие разрушения сварных конструкций / К. Дж. Холл, X. Кихара, В. Зут и др. М.: Машиностроение, 1974. — 320 с.
- Шахматов М.В., Ерофеев В. В., Гумеров K.M. и др. Оценка допустимой дефектности нефтепроводов с учетом их реальной нагруженности // Строительство трубопроводов. 1991. — № 12. — С. 37−41.
- Фокин М.Ф. и др. Оценка эксплуатационной долговечности магистральных нефтепроводов в зоне дефектов / М. Ф Фокин, В. А. Трубицин, Е. А. Никитина Е.А. М.: ВНИИОЭНГ, 1986. — 43 с.
- Ямуров Н.Р. Оценка остаточного ресурса элементов нефтехимического оборудования по параметрам испытаний и эксплуатации // Техническая диагностика, промышленная и экологическая безопасность предприятий. Уфа: Изд-во УГНТУ, 1996. — С. 9−11.
- Ямалеев K.M., Гумеров P.C. Термический способ восстановления ресурсов пластичности металла труб нефтепроводов // Диагностика, надежность, техническое обслуживание и ремонт нефтепроводов: Сб. научн. тр. ВНИИСПТнефть. Уфа, 1990. — С. 27−33.
- Ямалеев K.M., Гумеров P.C. О классификации дефектов труб с позиции диагностики магистральных нефтепроводов // Проблемы сбора, подготовки и транспорта нефти и нефтепродуктов: Сб. научн. тр. ИПТЭР. — Уфа, 1995.-С. 55−59.
- Ямалеев K.M., Гумеров P.C. Особенности разрушения металла труб магистральных нефтепроводов // Проблемы сбора, подготовки и транспортанефти и нефтепродуктов: Сб. научн. тр./ИПТЭР—Уфа, 1995. -С.60−65.
- Ямалеев K.M. Старение металла труб в процессе эксплуатации нефтепроводов. М.: ВНИИОЭНГ, 1990. — 64 с.
- Ямалеев K.M. Влияние изменения физико-механических свойств металла труб на долговечность нефтепроводов // Нефтяное хозяйство. -1985. — № 9.-С. 50−53.
- Ямалеев K.M., Молодцов Г. И. Старение металла труб нефтепроводов, обработанного энергией взрыва / Обеспечение надежности магистральных нефтепроводов в условиях эксплуатации: Сб. научн. тр. / ВНИИСПТнефть. — Уфа, 1986.-С. 56−61.
- Pipeline testing prequalification challenges controll skills // Pipeline and Gas J. 1983. — VI, 210. -№ 6.-P. 22 — 23.