Завод по производству железобетонных изделий для промышленного строительства
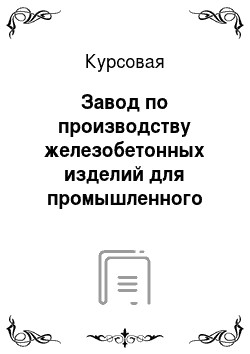
Тепловая обработка железобетонных изделий на стендах осуществляется пропариванием, контактным обогревом и электропрогревом. При пропаривании изделия накрывают колпаками, брезентом или пластмассовыми пленками, под которые пускают пар. Этот способ ускоренной тепловой обработки, как наименее экономичный по расходу тепла, применяется при изготовлении немассовой продукции. При массовом выпуске изделий… Читать ещё >
Завод по производству железобетонных изделий для промышленного строительства (реферат, курсовая, диплом, контрольная)
Министерство образования Российской Федерации.
НОВОСИБИРСКИЙ ГОСУДАРСТВЕННЫЙ АРХИТЕКТУРНО-СТРОИТЕЛЬНЫЙ УНИВЕРСИТЕТ.
(СИБСТРИН) КАФЕДРА СМиСТ КУРСОВОЙ ПРОЕКТ по курсу: «Проектирование предприятий».
НА ТЕМУ: Завод по производству железобетонных изделий для промышленного строительства.
П=80 тыс. м3 в год Студент… Марченко Ю.Н.
Специальность, группа…290 600, 561 гр.
Руководитель проекта… Пименов Оценка.
НОВОСИБИРСК 2010.
Оглавление Введение.
1. Анализ задания.
2. Номенклатура выпускаемой продукции.
3. Сырьевая база.
3.1 Вяжущие вещества.
3.2 Заполнители.
3.2.1 Песок.
3.2.2 Щебень.
3.3 Вода.
3.4 Арматурная сталь.
4. Расчет материальнопроизводственного потока.
4.1 Режим работы предприятия.
4.2 Определение расхода компонентов бетона /состав бетона/.
4.3 Определение усредненно-условного состава бетона.
4.4 Расчет материального потока.
5. Проектирование бетоносмесительного цеха.
5.1 Проектирование склада цемента.
5.2 Проектирование склада заполнителей.
5.3 Проектирование бетоносмесительного узла.
6. Проектирование формовочного цеха.
6.1 Выбор способа производства.
6.1.1 Стендовый способ.
6.1.2 Поточно-агрегатный способ.
6.1.3 Конвейерный способ.
6.2 Выбор и обоснование способа производства.
6.3 Расчет технологических линий.
6.3.1 Расчет стендовой технологической линии.
6.3.2 Расчет агрегатно-поточных линий.
6.4 Подбор формовочного оборудования.
6.5 Описание технологии изготовления изделий.
6.5.1 Технология изготовления изделий по стендовой технологии.
6.5.2 Технология изготовления изделий по агрегатно-поточной технологии.
7. Проектирование склада арматуры.
8. Расчет склада готовой продукции.
9. Контроль качества.
10. Техника безопасности и охрана окружающей среды Список литературы.
Введение
Современное строительство немыслимо без бетона. 2 млрд. м3 в год — таков сегодня мировой объем его применения. Это один из самых массовых строительных материалов, во многом определяющий уровень развития цивилизации. Бетон — самый сложный искусственный композиционный материал, который может обладать совершенно уникальными свойствами.
Бетонами называют искусственные каменные материалы, получаемые в результате затвердевания тщательно перемешанной и уплотненной смеси из вяжущего вещества с водой (реже без воды), мелкого и крупного заполнителей, взятых в определенных пропорциях. До затвердевания эту смесь называют бетонной смесью.
Бетон применяется в самых разных эксплуатационных условиях, гармонично сочетается с окружающей средой, имеет неограниченную сырьевую базу и сравнительно низкую стоимость, сравнительная простота и доступность технологии, возможность широкого использования местного сырья и утилизации техногенных отходов при его изготовлении, малая энергоемкость, экологическая безопасность.
Широкое применение сборного железобетона позволило значительно сократить в строительстве расход металла, древесины и других традиционных материалов, резко повысить производительность труда, сократить сроки возведения зданий и сооружений.
Полное удовлетворение потребностей строек страны и их экономическое и техническое соответствие научнотехническому прогрессу связано с расширением заводского производства изделий и конструкций из сборного железобетона и создание крупных предприятий с передовой технологией, механизацией и автоматизацией производства.
Важнейшим звеном технического прогресса в производстве сборного железобетона, связывающим науку с производством, является проектирование новых технологических линий, цехов, заводов, реконструкция и переоснащение действующих предприятий. В проектах непосредственно реализуются результаты научных исследований, используются достижения передовой техники. От качества проектирования в значительной степени зависят темпы технического прогресса.
1. Анализ задания Необходимо запроектировать завод по производству железобетонных конструкций для транспортного строительства. Мощность завода 60 тыс. м3 в год.
Место строительства: г. Новосибирск Сырьевая база:
— цементОАО «Искитимцемент», г. Искитим.
— щебень диабазовый — Тогучинское месторождение, г. Тогучин.
— песок — Кривощекого-Кривадановское месторождение.
НСО, Криводановка.
— вода — из городской коммуникации.
— арматура — Новокузнецкий металлургический комбинат.
— тепло и электроэнергия берется из городских сетей Вид транспорта для сырья: материалы на завод доставляются железнодорожным и автомобильным транспортом.
2. Номенклатура выпускаемой продукции Таблица 1 Номенклатура продукции.
Название изделия. | Эскиз. | Размеры, мм. | Марка бетона. | Масса, т. | Объем бетона, м3 на одно изделие. | Сталь, кг на одно изделие. | |||
l. | h. | b. | |||||||
Столбы. С35Д. | 0,12. | 0,05. | 8,40. | ||||||
Панели. Ц2. | 0,21. | 0,089. | 3,90. | ||||||
Плита Дорожная. ПД2−6. | 2,0. | 0,80. | 55,60. | ||||||
Плита Дорожная. I.П30.18−10. Сваи СЦ6−30. | 2,20. 1,38. | 0,88. 0,55. | 46,48. 13,8. | ||||||
Таблица 2 Производительность завода по номенклатуре.
ЖБИ. | %. | м3. | |
Столбы С35Д. | |||
Панели Ц2. | |||
Плита дорожная ПД2−6. | |||
Плита дорожная I. П30.18−10. | |||
Сваи СЦ6−30. | |||
Всего. | |||
Таблица 3 Производительность завода по бетону.
ЖБИ. | %. | м3. | |
1. Тяжёлый бетон марки: 200. | |||
3. Сырьевая база Сырьевыми материалами для производства железобетонных изделий являются вяжущие, заполнители различного типа, добавки, и арматурная сталь. Для проектирования предприятия ЖБИ необходим правильный выбор сырьевых материалов для каждого вида и марки бетона, обеспечивающий экономию средств и свойства.
3.1 Вяжущие вещества Портландцемент — гидравлическое вяжущее вещество, твердеющее в воде или на воздухе. Он представляет собой порошок серого цвета, получаемый тонким помолом клинкера с добавкой гипса.
Для получения цемента высокого качества необходимо, чтобы его химический состав и состав сырьевой смеси были устойчивы.
MgO в клинкере более 5% - в автоклаве. Содержание свободного СаО не более 0,05%, т.к. свободный СаО, как и MgO. В данном проекте будет использоваться цемент г. Искитим. Насыпная плотность 1100 кг/м3, истинная плотность 3000 кг/м3, Rц=400кгс/см2 (ГОСТ10 178−95).
Цемент должен удовлетворять следующим требованиям:
1. Тонкость помола должна быть такой, чтобы при просеивании пробы цемента сквозь сито с сеткой № 008 проходило не менее 85% массы просеиваемой пробы.
2. Начало схватывания не ранее 45 мин., конец схватывания не позднее 10 часов от начала затворения водой.
3. Цемент должен показывать равномерность изменения объема при испытании образцов кипячением в воде, а при содержании вызывает растрескивание затвердевшего цемента. Коэффициент насыщения-0,88; модуль-1,67; глиноземистый модуль-1,26.
4. По прочности при сжатии в 28 суточном возрасте образцов из цементно-песчаного раствора, изготовленных по ГОСТ 310.4−81, портландцемент подразделяют на марки 400, 500, 550, 600.
Требования к портландцементу приведены в таблицах 4,5,6.
Таблица 4 Требования ГОСТ 10 178–85* к прочности цементов.
Гарантированная марка. | Предел прочности в возрасте 28суток, МПа (кгс/см2). | ||
при изгибе. | при сжатии. | ||
4.4(45). | 29.4(300). | ||
5.4(55). | 39.2(400). | ||
5.9(60). | 49.0(500). | ||
6.1(62). | 53.9(550). | ||
6.4(65). | 58.8(600). | ||
Таблица 5 Химический состав ПЦ клинкера.
SiO2. | CaO. | Al2O3. | Fe2O3. | MgO. | SO3. | п.п.п. | |
20.62%. | 64.27%. | 6.94%. | 5.44%. | 1.56%. | 0.97%. | 0.2%. | |
Таблица 6 Минералогический состав ПЦ клинкера.
C3S. | C2S. | C3S. | C4AF. | |
50.16%. | 20.22%. | 9.0%. | 16.53%. | |
Допускается введение в цемент специальных пластифицирующих и гидрофобизирующих добавок в количестве не более 0.3% от массы цемента в пересчете на сухое вещество добавки. Гидрофобизированный цемент не должен впитывать в себя воду в течение 5 минут от момента нанесения капли воды на поверхность цемента.
3.2 Заполнители.
Заполнители являются основными компонентами бетона, как по массе, так и по объему (70−90% объема бетона). Они оказывают влияние на технологические свойства бетонной смеси, процессы твердения и на строительно-технические и эксплуатационные свойства бетона. В качестве заполнителей принимаем: песок, щебень и керамзитовый гравий.
3.2.1Песок Песок должен удовлетворять требованиям ГОСТ 8736–93. Основными показателями качества песка является зерновой состав и содержание пылевидных и глинистых частиц, в том числе глины в комках. Рекомендуемые стандартом зерновые составы песка обеспечивают компактную упаковку его частиц и наименьшую межзерновую пустотность, что ведет за собой экономию вяжущего вещества.
В соответствии с требованиями ГОСТ 8736–93 в тяжелых бетонах должны использоваться пески с модулем крупности 1,5…3,25. В природном песке не допускается присутствие зерен размером свыше 10 мм в количестве более 0,5% по массе, свыше 5 мм — более 10% по массе, Содержание зерен проходящих через сито № 016, не должно превышать, % по массе: в природных песках повышенной крупности, крупных и средних-10, в мелком и очень мелком песке — 15.
Таблица 7.
Характеристика песка.
Месторождение. | Плотность,. т/м3. | Насыпная Плотность,. т/м3. | Модуль крупности. | Содержание Глинистых примесей,%. | |
Кривощеково; Криводановское. | 2,580. | 1,870. | 1,79. | Не более 1,5. | |
Рисунок 1 Зерновой состав песка.
3.2.2 Щебень В качестве крупного заполнителя для тяжелого бетона применяют диабазовый щебень Тогучинский район. Щебень должен удовлетворять требованиям ГОСТ 8736–93. Показателями качества щебня являются: зерновой состав, форма зерен, прочность, содержание зерен слабых пород, пылевидных и глинистых частиц, морозостойкость; петрографическая характеристика; плотность, средняя и насыпная плотность, межзерновая пустотность, водопоглощение.
Содержание фракций в заполнителе 5−10 и 10−20 соответственно 25−40% и 60−75%, при наибольшей крупности 20 мм. Содержание пластинчатых и игловатых зерен в щебне не должно превышать 35%, зерен слабых и выветренных пород не должно превышать 10%.Наличие глин в виде отдельных комьев в количестве 0,25% или пленки, обволакивающей зерна заполнителя, не допускается.
Таблица 8.
Характеристика щебня.
Наименование месторождения. | Физико-технические показатели. | |||||
Rсж. | ?,. кг/ м3. | ?н, кг/ м3. | Мрз, цикл. | Вт,. %. | ||
п.Горный. | 0,05. | |||||
Рисунок 2 Гранулометрический состав щебня.
3.3 Вода Для затворения бетонной смеси применяют грунтовые, поверхностные и пресные озерные воды (ГОСТ 23 732−79*). Содержание в воде органических ПАВ, сахаров или фенолов, каждого, не должно быть более 10 мг/л.
Вода не должна содержать пленки нефтепродуктов, жиров, масел. Вода не должна содержать сульфатов более 2700 мг/л (в пересчете на SO4) и всех солей более 5000 мг/л. В сомнительных случаях пригодность воды для приготовления бетонной смеси необходимо проверять путем сравнительных испытаний образцов, изготовленных на данной воде и на обычной водопроводной.
Для приготовления бетонной смеси можно применять морскую и другие соленые воды, удовлетворяющие приведенным выше условиям. Исключением является бетонирование внутренних конструкций жилых и общественных зданий и надводных железобетонных сооружений в жарком и сухом климате, так как морские соли могут выступать на поверхности бетона и вызывать коррозию стальной арматуры.
Для поливки бетона следует использовать воду такого же качества, как и для приготовления бетонной смеси.
Окисляемость воды не должна быть более 15 мг/л. Водородный показатель воды (рН) не должен быть менее 4 и более 12. Вода не должна содержать также примесей в количествах нарушающих сроки схватывания и твердения цементного теста и бетона, снижающих прочность и морозостойкость бетона. В данном проекте будем использовать воду от городских сетей.
3.4 Арматурная сталь.
Для армирования бетона используют в основном стальную арматуру из углеродистых и низкоуглеродистых сталей.
Арматурные канаты изготавливают из высокопрочной холоднотянутой проволоки.
Арматурную проволоку и канаты поставляют в несмазанном виде. Канаты поставляют на барабанах или в мотках, проволоку в мотках массой 500−1500 кг. Каждый моток должен состоять из одного отрезка проволоки.
В качестве ненапрягаемой арматуры следует преимущественно применять стержневую арматурную сталь классов А-III, Ат-IIIС.
Основной нормативный документ по арматурным изделиям — ГОСТ 10 922–75, который регламентирует технические требования и свойства арматуры.
4. Расчет материальнопроизводственного потока.
4.1 Режим работы предприятия При назначении режима работы цеха принимается:
— номинальное количество рабочих суток в год, Тн- 262;
— количество рабочих смен в сутки /кроме тепловой обработки/- 2 или 3;
— для тепловой обработки, n-3;
— количество рабочих смен в сутки по приему сырья, материалов и отгрузки готовой продукции железнодорожным транспортом, n-3;
— то же автотранспортом, n-2 или 3;
— номинальное количество рабочих суток в году по приему сырья и материалов с железнодорожного транспорта-365;
— продолжительность рабочей смены в час, t-8;
— длительность плановых остановок в сутках на ремонт конвейерных линий, Tр-13, поточно — агрегатных, стендовых линий и кассетных установок по приготовлению бетонных и растворных смесей, Tр-7;
— коэффициент использования технологического оборудования:
— конвейерных линий, Ки- 0,95;
— поточно — агрегатных и других- 0,92;
Определим годовой фонд рабочего времени по формуле:
Тф = (ТH — ТP)*n*t*Kи, (1).
где ТH — номинальное количество рабочих суток в году;
ТP — продолжительность плановых остановок технологических линий на ремонт в сутках;
n — количество смен в сутки;
t — продолжительность рабочей смены в часах;
Kи — коэффициент использования оборудования.
Тф = (260 — 7)280,92=3724,16 часов (233 дня);
Тф = (260 — 7)380,92=5586,24 часов — для тепловлажностной обработки;
Тф= (365 — 7)380,92=7904,64 часов — складское хозяйство.
4.2 Определение расхода компонентов бетона /состав бетона/.
Расчет состава тяжелого бетона на плотных заполнителях Для получения наиболее экономичного бетона по расходу цемента рекомендуется принимать марку цемента в зависимости от требуемой марки бетона по таблице 9.
Таблица 9 Зависимость марки бетона от марки цемента.
Марка бетона. | 600 и более. | ||||||||
Марка цемента по ГОСТ 10 178–85. | 300−400. | 400−500. | 550−600. | ||||||
· Цементно-водное отношение определяется по формуле:
(2).
где Rб — требуемая прочность бетона, кгс/см2; Rц — марка цемента, кгс/см2;
А — коэффициент качества заполнителей, А=0,6.
Ц/В = 200/(4000,6) + 0,5 = 1,33.
· Количество цемента определяется по формуле:
(3).
где В-расход воды.
Расход воды определяется, исходя из заданной удобоукладываемости бетонной смеси, вида и крупности заполнителя.
Для О.К. = 3 — 4 см и Дмакс = 20 мм расход воды равен В = 195л/м3.
Ц = 1901,33 = 253 кг.
· Количество крупного заполнителя определяется:
(4).
где Кр — коэффициент раздвижки зерен (принимаем Кр =1,38);
Vп — определяется по формуле (5).
(5).
Vп = (2,89 — 1,75)/2,89 = 0,39.
Щ = 1000/(0,391,38/1,75 + ½, 89) = 1520,8 кг.
· Количество мелкого заполнителя определяется по формуле:
(6).
П = [1000 — (253/3,1+ 190 + 1520,8/2,89)] 2,51 = 507,52 кг.
Таблица 10 Результаты расчетов составов тяжелого бетона.
Марка бетона. | Предельная крупность заполнителя, мм. | ОК, см. | Расходы материалов, кг/л на м3 бетона. | ||||
Вода. | Цемент. | Щебень. | Песок. | ||||
3−4. 3−4. 3−4. | 279,3. 367,5. | 1520,8. 1520,8. 1509,4. | 507,52. 438,5. 387,76. | ||||
4.3 Определение усредненно-условного состава бетона.
1. Расход воды Ву=?1В1+?2В2+?3В3. (7).
Ву=0,1*190+0,4*210+0,5*210= 208 л.
2. Расход песка Пу=?1П1+?2П2+?3П3. (8).
Пу= 0,1*507,52+0,4*438,5+0,5*387,76=420 кг/м3;
3. Расход цемента Цу=?1Ц1+?2Ц2+?3Ц3. (9).
Цу=0,1*253+0,4*279,3+0,5*367,5=320,77 кг/м3;
4. Расход щебня Щу=?1Щ1+?2Щ2+?3Щ3. (10).
Щу=0,1*1520,8+0,4*1520,8+0,5*1509,4=1515,1 кг/м3.
Таблица 11 Результаты расчета усреднёно-условного состава тяжелого бетона.
Вид бетона. | Марка бетона. | Предельная крупность заполнителя, мм. | ОК, см. | Расходы материалов, кг/л на м3 бетона. | Доля. | ||||
Вода. | Цемент. | Щебень. | Песок. | ||||||
1Тяжелый. 2 Тяжелый. 3 Тяжелый. | 3−4. 3−4. 3−4. | 279,3. 367,5. | 1520,8. 1520,8. 1509,4. | 507,52. 438,5. 387,76. | 0,1. 0,4. 0,5. | ||||
Усредненный. | 320,77. | 1515,1. | |||||||
4.4 Расчет материального потока Для расчета материального производственного потока уточняется деление производственного процесса на технологические зоны и нормы неизбежных потерь материалов по зонам.
Зона 1: транспортно-сырьевой участок. Потери цемента 1%, щебня 1%, песка 2%.
Зона 2: склады сырья. Потери цемента 1%, щебня 1,5%, песка 2%.
Зона 3: бетоносмесительный узел. Потери бетонной смеси 1%.
Зона 4: формовочные линии. Потери бетонной смеси 0,5%.
Зона 5: участок термообработки и доводки изделий. Потери 0,5%.
Зона 6: склад готовой продукции. Потери 0,5%.
Затем подсчитываются необходимые производительности технологических переделов и потребности в материалах, начиная с зоны /склад готовой продукции/ по формуле.1.10.:
Пn = П (n+1)/(1-Qn/100), м3/год (11).
где Пn — производительность в зоне n (n — номер зоны);
П (n+1) — производительность в зоне, следующей за рассчитываемой зоной /зона номер n+1/;
Qn — производственные потери в зоне, %.
Расчет потребности завода в цементе и песке ведется по формуле (12) и формуле (20).:
Ц = П (БСУ) · Цу/(1-Q (склад сырья)/100), т, (12).
Щ = П (БСУ) · Щу/((1-Q (склад сырья)/100) · н (щ)), м3, (13).
где П (БСУ) — производительность в зоне БСУ;
Цу, Щу — расход цемента и щебня на 1 м³ условного бетона;
Q (склад сырья) — потери цемента и щебня на складе, %;
н (щ) — насыпная плотность щебня, т/м3.
Таблица 13 Материальный поток тяжелого бетона проектируемого предприятия.
№ п/п. | № зоны. | Передел. | Потери,%. | Ед. изм. | Формула. | Производительность. | |||
В год. | В сутки. | В час. | |||||||
Реализация ЖБИ. | 0,0. | м3. | 14,3. | ||||||
Склад готовой продукции. | 0,5. | м3. | 60 000/1−0,005/100. | 60 301,5. | 230,15. | 14,38. | |||
Термообработка. | 0,5. | м3. | 60 301,5/1−0,005/100. | 60 604,5. | 6,9. | ||||
Формовочные линии цеха. | 0,5. | м3. | 60 604,5/1−0,005/100. | 244,6. | 15,3. | ||||
Бетоносмесительный узел. | 1,0. | м3. | 60 909/1−0,01/100. | 61 524,24. | 241,27. | 15,07. | |||
Склад сырья. — цемента. — щебня. — песка. | 1,0. 1,5. 2,0. | т м3. м3. | 61 524,240,27 815/1−0,01/100. 61 524,24*1,58 936/[(1−0.015/100)*1.75]. 61 524,24*0,41 034/[(1−0,02/100)*1,59]. | 17 285,8. 56 158.2. 16 224.48. | 47,35. 153,8. 44,48. | 1,97. 6,4. 1,85. | |||
Транспортносырьевой участок. — цемента. — щебня. — песка. | 1,0. 1,5. 2,0. | т м3. м3. | 17 285,8/(1−0,01/100). 56 158,2/(1−0,01/100). 16 224,48/(1−0,02/100). | 17 460,4. 56 725,4516555,6. | 47,8. 155,4. 45,36. | 2,0. 6,47. 1,9. | |||
5. Проектирование бетоносмесительного цеха В состав бетоносмесительного цеха входят: склад цемента, склады заполнителей, бетоносмесительные узлы БСУ и внутрицеховые транспортные связи между складами сырья и БСУ.
Качество бетонной смеси и бетона зависит от качества сырьевых материалов. Поэтому одно из основных назначений складов — сохранение, а часто и улучшение качества сырья.
Внутрицеховые транспортные связи должны исключать засорение, ухудшение качества материалов и снижать потери.
5.1 Проектирование склада цемента.
Цемент на заводе хранится в силосных складах.
Требуемая вместимость склада цемента, т:
Vс.ц=Цсут*n/Кз, (14).
где Цсутсуточная потребность завода в цементе, т;
nнормативный запас цемента, сут., n=7 сут.;
Кзкоэффициент заполнения емкости склада, равный 0,9.
Vс.ц=47,35*7/0,9=368,3 т Принимаем прирельсовый склад цемента 409−29−64.
Таблица 15 Техническая характеристика склада цемента.
Показатели. | Склад 409−29−64. | |
Вместимость, т. | ||
Количество силосов, шт. | ||
Мощность электродвигателей, кВт. | 50,8. | |
Себестоимость складирования, р./т. | 2,18. | |
Грузооборот, тыс, т/год. | ||
Число работающих, чел. | ||
5.2 Проектирование склада заполнителей Расчет склада производится, исходя из потребности в сырьевых материалах, нормативных запасов и конкретной характеристики принятого типа склада.
Емкость в складе для хранения каждого вида заполнителя рассчитывается по формуле, м3:
Vс=Зсут*n*Кф*Кз, (15).
где Зсутсуточная потребность предприятия в данном виде заполнителя, т;
nнормативный запас заполнителя, сут., n=7 сут.;
Кфкоэффициент, учитывающий необходимое увеличение емкости склада при хранении нескольких фракций заполнителей, 2 фракции Кф=1,05, 3 фракции Кф=1,10, 4 фракции Кф=1,15;
Кзкоэффициент загрузки (Кз = 1,2 для полубункерных складов).
Для щебня:
Vс.щ=153,8*7*1,05*1,2=1356,5 м³;
Для песка:
Vс.п= 44,45*7*1,05*1,2=392,05 м³;
Общая вместимость склада заполнителей рассчитывается как сумма емкостей для хранения каждого вида заполнителя:
VОбщ = (Vсщ + Vсп)* 1,2 = (1356,5+392,05)*1,2 = 2098,26 м³.
По величине суммарной вместимости склада заполнителей подбираем типовой склад прирельсового типа, характеристики которого представлены в таблице 15. Принимаем склад заполнителя 708−18−85.
Таблица 16 Техническая характеристика типового склада заполнителей.
Шифр | Вместимость склада, м3. | Годовой грузооборот, тыс. м3/год. | Размеры склада, м. | |
708−13−84. | 92×37. | |||
5.3 Проектирование бетоносмесительного узла Требуемая часовая производительность БСУ, м3/час:
Пб.ч= Пз*К1* К2, (16).
где Пзчасовая производительность БСЦ К1- коэффициент резерва производства, К1=1,2;
К2- коэффициент неравномерности выдачи и потребления бетонной смеси, К2=1,25.
Пб.ч=15,07*1,2*1,25= 22,6м3/ч.
Определение часовой производительности бетоносмесителя, м3/час:
Qч=60*Vз/tц*Ки, (17).
гдеVзобъем одного готового замеса, м3;
Кикоэффициент использования оборудования, Ки=0,97;
tцвремя цикла приготовления одного замеса, мин.
Необходимое количество смесителей, шт.:
Z=Пб.ч/Qч (18).
tц.тяж.бет.=2 мин;
Qч.тяж.бет.=60*0,8/2*0,97=23,28 м3/ч;
Zтяж.бет.=22,6/23,28 =0,97 шт;
Принимаем 1 бетоносмесителя принудительного действия СБ-93.
Таблица17 Техническая характеристика бетоносмесителя СБ-93.
Параметр | Величина. | |
Объем готового замеса, л: Vз бетонной смеси раствора. | ||
2. Вместимость по загрузке, л. | ||
Число циклов в 1 час при: приготовлении бетонной смеси раствора. | ||
4. Наибольшая крупность заполнителя, мм. | ||
5. Частота вращения рабочего органа, об/мин. | ||
Мощность двигателя, кВт вращения рабочего органа подъема скипового ковша. | ||
7. Давление в пневмосистеме, МПа. | 0,4.0,6. | |
8. Габаритные размеры, м. | 3,34×2,69×2,85. | |
9. Масса, кг. | ||
Подбор дозаторов Выбор дозаторных устройств осуществляется по максимальному расходу того или иного компонента. Технические характеристики дозаторов представлены в таблице 18.
Таблица 18 Техническая характеристика весовых дозаторов цикличного действия.
Материал. | Вода. | Цемент. | Песок. | Щебень. | Керамзит. | |
Обозначение. | АВДЖ-2400М. | АВДЦ-1200М. | АВДИ-1200М. | АВДИ-2400М. | АД-800−2БК. | |
Предел. дозирования, кг. | 50−500. | 100−300. | 200−1200. | 250−1300. | 200−800. | |
Цикл. дозирования, с. | ||||||
Габариты, м. | 1,861,12,75. | 1,810,962,15. | 2,061,172,66. | 2,061,172,6. | 2,151,552,68. | |
Объем расходного бункера определяется по формуле:
м3 (19).
где П — расход материала, м3ч;
n — время, на которое делается запас, ч, n=3 ч ;
m — количество бункеров.
Для цемента: *н (ц),.
где н (ц) — насыпная плотность цемента, т/ м3.
Бункер цемента: Vбц = 1,973/0,81 =7,39 м³;
Бункер песка: Vбп =1,853/0,82 =13,87 м³;
Бункер щебня: Vбщ =6,43/0,82 =48 м3.
6. Проектирование формовочного цеха Операции формования и твердения изделий выполняются на технологических линиях с помощью специальных механизмов, приспособлений и установок. Технологические линии формируются из оборудования, выбираемого в зависимости от вида, габаритов, назначения, требуемого объема производства железобетонных изделий, вида отделки и степени заводской готовности.
Ряд технологических линий, размещенных в одном или нескольких пролетах или в отдельном здании, и объединенных комплектностью производимых изделий или сходством их основных характеристик, могут составить организационно-формовочный цех. От того, каким методом и оборудованием осуществляются операции формования и ускорения твердения бетона в изделиях, технологические линии можно отнести к различным способам изготовления железобетона.
6.1 Выбор способа производства Классификацию способов производства сборного железобетона представлены в таблице 19.
Таблица 19 Способы производства сборного железобетона.
1 группа. | 2 группа. | |
по методу без перемещения форм в процессе изготовления изделий. | по методу с перемещением форм в процессе изготовления изделий. | |
1. Стендовый. | 1. Поточно-агрегатный. | |
а) линейные стенды б) короткие стенды. | 2. Полуконвейерный (прерывистый конвейер). | |
в) стационарные силовые. | 3. Конвейерный. | |
формы г) линии индивидуальных или. | а) конвейерные линии б) вибропрокатные станы. | |
спаренных термоформ. | в) комбинированный конвейер 4. Кассетно-конвейерный. | |
5. Карусельно-конвейерный. | ||
Технологическая организация производства железобетонных изделий может осуществляться несколькими способами: стендовым, агрегатно-поточным, конвейерным или кассетным. Выбор способа зависит от производительности предприятия, номенклатуры изделий и технико-экономических показателей.
бетон склад цемент формовочный.
6.1.1Стендовый способ производства.
Стенды представляют собой горизонтальную железобетонную площадку, разделенную по ширине на отдельные самостоятельные технологические линии. Наличие на стенде нескольких технологических линий обеспечивает поточность организации изготовления изделий: на одной линии производят армирование, на другой изделия формуют, а на следующей происходит твердение. Такая организация позволяет более полно использовать рабочее время и повышает в целом съем продукции со стендовых линий.
Тепловая обработка железобетонных изделий на стендах осуществляется пропариванием, контактным обогревом и электропрогревом. При пропаривании изделия накрывают колпаками, брезентом или пластмассовыми пленками, под которые пускают пар. Этот способ ускоренной тепловой обработки, как наименее экономичный по расходу тепла, применяется при изготовлении немассовой продукции. При массовом выпуске изделий применяют формы с паровыми рубашками и изделия в этом случае подвергают контактному обогреву. Последний достигается оснащением основания стенда тепловыми приборами (теплый стенд).
В современной технологии сборного железобетона получили распространение протяжные, пакетные стенды и индивидуальные стенды.
Наиболее целесообразным, а в ряде случаев и единственно осуществимым оказывается стендовый способ при изготовлении сложных предварительно напряженных изделий значительного веса, перемещение которых по технологическим постам явилось бы сложной и дорогой технической задачей. В таком направлении и ориентировано в настоящее время стендовое производство.
6.1.2 Поточно — агрегатный способ.
Поточно-агрегатный способ находит самое широкое применение в промышленности сборного железобетона; примерно 70%, всей продукции изготавливается этим способом. Причинами такого предпочтения оказываются следующие достоинства поточно-агрегатного способа: высокий съем продукции с производственных площадей, наименьшая металлоемкость производства, имея в виду потребность металла форм на единицу годовой производительности предприятия, технологическая и организационная несложность перехода на выпуск изделий другого вида.
Основным технологическим оборудованием формовочных линий предприятий с поточно-агрегатным способом производства являются:
виброплощадки, бетоноукладчики или бетонораздатчики, вибропригрузочный щит, применяемый при формовании изделий из жестких смесей, поставляется в комплекте с виброплощадкой, при поточно-агрегатном способе в основном применяют ямные камеры, транспортное оборудование. Все основные технологические транспортные операции при поточно-агрегатном способе выполняются преимущественно мостовыми кранами, либо кранами в сочетании с рольгангами, специальными тележками и т. д. Готовая продукция вывозится на склад на вагонетках. Склады оборудуются мостовыми, козловыми либо башенными кранами.
Технологические операции в последовательности их выполнения при поточно-агрегатном способе производства железобетонных изделий представлены следующим комплексом:
1) очистка формы и оснастки от цементной пленки и раствора;
2) сборка разъемной формы;
3) смазка рабочей емкости формы;
4) укладка в форму арматурных каркасов, нижних арматурных сеток и закладных деталей.
5) подача формы на формовочный пост;
6) укладка в форму бетонной смеси и ее уплотнение.
7) заглаживание верхней поверхности изделия или декоративная отделка ее по сырому бетону, если она предусмотрена проектом;
8) снятие оснастки формы, если формование производится с немедленной распалубкой;
9) подача изделия в форме или на поддоне (при немедленной распалубке) в камеру тепловой обработки;
10) тепловая обработка бетона до приобретения им необходимой прочности, предусмотренной данной технологией;
11) извлечение формы с изделием из камеры и передача ее на пост распалубки;
12) распалубка и остывание изделия;
13) декоративная отделка поверхности изделия по отвердевшему бетону (если она предусмотрена проектом) или доведение поверхности изделий до полной заводской готовности;
14) приемка изделий отделом технического контроля — осмотр их и маркировка;
15) транспортирование на склад готовой продукции.
Приведенный комплекс технологических операций обычно совмещается и посты для их выполнения компануютея в виде отдельных технологических линий, на которых предусматриваются также площадки для хранения запасных форм, расходного запаса арматуры, закладных деталей и других элементов железобетонных изделий, например утеплителя. Количество технологических линий в одном строительном пролете здания 1—2.
6.1.3 Конвейерный способ По принципу действия конвейеры различают непрерывно действующие (вибропрокатный стан) и пульсирующие (формы-вагонетки, перемещающиеся последовательно через отдельные технологические посты формования). Пропарочные камеры преимущественно непрерывного действия являются одним из звеньев технологического кольца.
По компоновке конвейерного кольца различают конвейеры одноярусные и двухъярусные. В первых пути перемещения вагонеток и пропарочные камеры расположены в одном уровне, на отметке пола формовочного цеха. Такой конвейер может быть назван горизонтально замкнутым. В двухъярусных вертикально замкнутых конвейерах формовочные посты располагаются на уровне пола цеха или несколько приподняты, а пропарочные камеры — под ними. Такая компоновка конвейерного кольца существенно уменьшает потребность в производственных площадях, однако при этом нельзя не учитывать более сложного конструктивного решения установки.
Принудительный ритм перемещения форм-вагонеток и постоянные размеры последних обусловливают необходимость узкой специализации конвейерных линий. По технико-экономическим причинам конвейеры проектируются на массовый выпуск однотипных изделий. Наиболее характерными среди них являются пустотелые предварительно напряженные панели и настилы перекрытий, колонны (стойки) и ригели жилых зданий, панели наружных стен.
Основное технологическое оборудование этих конвейерных линий представлено:
1) навивочными машинами для предварительно напряженного армирования изделий холоднотянутой проволокой.
2) формовочными машинами;
3) транспортирующие устройства конвейерной линии представлены тросовым приводом для перемещения форм-вагонеток по формовочным постам; передаточным рольгангом или передаточной платформой для перемещения форм-вагонеток с формовочной линии к камерам твердения и от них; подъемниками-снижателями с толкателями, служащими для загрузки многоярусной тоннельной камеры и проталкивания форм-вагонеток по тоннелю;
4) камеры пропаривания непрерывного действия горизонтального типа, вертикальные камеры проходят стадию производственного освоения.
Выбор технологических линий и оборудования произведен после анализа степени совместимости конструктивных и технологических параметров изделий в процессе их формования и твердения.
Для данной номенклатуры изделий рассмотрим такие способы производства изделий как:
1.агрегатно-поточный для производства столбов, свай.
2. конвейерный — для дорожных плит и панелей.
6.2 Расчет технологических линий.
6.2.1 Конвейерный способ производства Годовая производительность конвейерных линий вычисляется по формуле:
Рг.к.=60*Ки*С*В*Vф/Тц, м3 (6.2.1.1).
где С — число рабочих дней в году, С=262 дней; В — число часов формовочной линии в сутки, В=16 ч; Ки — коэффициент использования оборудования, Ки=0,95; Vф — объем одной формовки, м3; Тц — продолжительность цикла формования, мин.
Требуемое количество конвейерных линий определяется по формуле:
Nк.л.=Пг/(Рк.г.*Ки), шт (6.2.1.2).
где Пг — требуемая годовая программа цеха, шт. или м3; Рк.г. — годовая производительность конвейерной линии, шт. или м3; Ки — коэффициент использования оборудования, Ки=0,95.
Требуемая длина линии формования при размещении на каждом посту по одной форме — вагонетке определяется по формуле:
Lф.л.=lф*(Nn+2)+ln*(Nn-1)+2*lр+2*lм, м (6.2.1.3).
где lф — длина формы-вагонетки, м; Nn — количество постов, шт; ln — величина промежутков между формами, м, ln=1,2−3,4 м; lр — расстояние от крайних форм до участка размещения подъемника или снижателя, м, lр=0,4−0,5 м; lм — величина участка, где размещается механизм подъема и опускания форм — вагонеток, равна габариту (длине) механизма, но не меньше длины формы.
Расчет требуемого количества форм определяется по формуле:
Nф.к.=Кр.ф.*(Nа+Nв+Nс), шт. (6.2.1.4).
где Кр.ф. — коэффициент запаса форм на ремонт, Кр.ф.=1,05; Nа — число форм на постах конвейера. Если на каждом посту находится по одной форме — вагонетке, то Nа=Nn; Nв — число форм, находящихся в камере тепловой обработки:
Nв=То*60/Rи, шт. (6.2.1.5).
То — продолжительность тепловой обработки, ч; Rи — ритм работы конвейера, мин; Nс — число форм, находящихся на передаточных устройствах (чаще всего 1 форма).
Определяем требуемую длину щелевой камеры по формуле:
Lк=lф*Nв+ln*(Nв-1), м (6.2.1.6).
где lф — длина формы-вагонетки, м; ln — расстояние между формами в камере, зависит от типа применяемого привода конвейерной линии и формы. Так, при применении цепного привода ln=0,3−0,5 м, а при применении толкателей формы — вагонетки располагаются вплотную, т. е. ln=0.
Необходимое количество щелевых камер определяется по формуле:
Z=Lк/(Lф.л.-l), шт. (6.2.1.7).
где l — расстояние от передаточной тележки (механизма) до входа (выхода) камеры, м. При отсутствии снижателей и подъемников перед камерами l=2 м; при наличии снижателей и подъемников l=(lсниж+1)*2, м; (Lф.л.-l) — длина одной камеры.
1. Плита дорожная:
Определяем размеры форм:
lф=6,0+2*0,3=6,6 м;
bф=1,5+2*0,3=2,1 м;
hф=0,18+0,3=0,48 м.
определяем годовую производительность линии:
Рг.к.=60*0,95*262*16*1,6/20=19 115,5 м³.
Определяем количество конвейерных линий:
Nк.л.=36 000/(19 115,5*0,95)=1,98 шт.
Принимаем 2 технологических линии.
Процесс изготовления многопустотных плит перекрытий состоит из следующих операций:
1. Передача напряжения на бетон;
2. Распалубка;
3. Чистка;
4. Смазка;
5. Укладка напрягаемых стержней;
6. Остывание;
7 и 8. Формование;
9. Установка вкладышей;
10. Выдержка.
Требуемая длина линии формования при размещении на каждом посту по одной форме — вагонетке определяется по формуле.
Lф.л.=6,6*(10+2)+2,3*(10−1)+2*0,5=100,9 м.
Расчет требуемого количества форм о:
Nф.к.=1,05*(10+24+1)=37 шт Принимаем 37 форм.
определяем требуемую длину щелевой камеры:
Lк=6,0*24+0,4*(24−1)=153,2 м.
определяем количество щелевых камер:
Z=153,2/(100,9−1)=1,53 шт.
Принимаем 2 щелевых камер.
Расчет и выбор бетоноукладчика Вместимость бункера бетоноукладчика:
Vб=1,15*1,3*1,6=2,392 м³.
Принимаем бетоноукладчик СМЖ-3507А, техническая характеристика которого приведена в таблице 6.2.1.
Таблица 6.2.1.
Техническая характеристика бетоноукладчика СМЖ-3507А.
Характеристика. | Показатель. | |
Вместимость бункера, м3. | 2,5. | |
Число бункеров. | ||
Наибольшая ширина укладки, мм. | ||
Скорость передвижения ленты питателей бункера, м/мин. | 6,0. | |
Скорость передвижения бетоноукладчика, м/мин. | 1,8;3,8;5,9;11,6. | |
Установленная мощность, кВт. | 18,4. | |
Габаритные размеры, м. | 3,4?6,5. | |
Масса, т. | 10,5. | |
Выбор типа виброплощадки Определяем требуемую грузоподъемность виброплощадки:
Qф=1,6*1,7=2,72 т.
Qв=2,72+2,67+2=7,39 т.
Согласовав габариты, способ крепления форм к виброплощадке, принимаем виброплощадку СМЖ-227Б.
Таблица 6.2.2.
Техническая характеристика виброплощадки СМЖ-227Б.
Характеристика. | Показатель. | |
Размеры изделий, мм. | 5980?1490?220. | |
Статический момент дебалансов вибровкладышей, Н? м. | ||
Скорость извлечения вибровкладышей, м/с. | 0,15. | |
Установленная мощность, кВт. | ||
Габариты, м. | 11,44?2,51?0,88. | |
Масса, т. | 6,24. | |
Для вывоза готовой продукции применяем самоходную тележку СМЖ-151.
Таблица 6.2.3.
Техническая характеристика тележки СМЖ-151.
Характеристика. | Показатель. | |
Грузоподъемность, т. | ||
Предельная дальность хода, м. | ||
Скорость передвижения, м/мин. | 31,6. | |
Установленная мощность, кВт. | 7,5. | |
Габаритные размеры, м. | 7,49?2,58?1,45. | |
Масса, кг. | ||
6.2.2 Расчет агрегатно-поточных линий.
Годовая производительность агрегатно-поточной технологической линии определяется номенклатурой выпускаемой продукции, режимом формования изделий и продолжительностью работы формовочного поста в течение суток.
Производительность линий для каждой группы изделий рассчитывается по формуле, м3/час:
Р=55,2*С*В*Vф/Тц, (6.2.2.1).
где Счисло рабочих дней в году;
Вчисло часов работы формовочного поста в сутки;
Vфобъем одной формовки, равен объему изделия-представителя или сумме объемов изделий одновременно формуемых в одной форме, м3;
Тцпродолжительность цикла формования, мин.(табл.30.3 [2]).
Р=55,2*233*16*1,1/15=15 090,94 м³;
Требуемое количество технологических линий определяют по формуле, шт:
Nт.л=Пг/Р*Ки, (6.2.2.2).
где Пггодовая производительность предприятия в м3 по данной группе изделий;
Кикоэффициент использования оборудования, Ки=0,92.
N =18 000/ (15 090,94*0,92) =1,29шт;
Принимаем две технологических линии.
Габариты форм принимают по габаритам наибольшего изделия данной группы. Если изделия малогабаритные, то принимают решение о том, что в одной форме формуем два и более изделий.
При условии формования одного изделия в форме размеры форм определяют, м:
lф=lи+2*? lф; bф=bи+2*? bф; hф=hи+2*? hф, (6.2.2.3).
где lф, bф, hфсоответственно длина, ширина, высота изделия, м;
? lфширина торцевого борта, а также участка для размещения упоров в силовых формах, м;
? bфширина бокового борта, м;
? hфвысота поддона, м.
lф=6,0+2*0,2=6,4 м;
bф=0,3*2+2*0,2=1 м;
hф=0,25+0,3=0,55 м.
Длина секции камеры, м:
Lк=n*lф+(n+1)*l, (6.2.2.4).
где nколичество форм с изделиями по длине, шт;
lфдлина формы, м;
lвеличина промежутков между стенкой и формой, а также между формами; ln=0,3…0,5 м.
L = 1*6,4 + 2*0, 3 = 7,0 м;
Ширина секции камеры, м:
Вк= n*bф+(n+1)*b, (6.2.2.5).
где nколичество форм с изделиями по ширине, шт;
bфширина формы, м;
bnвеличина промежутков, м, b=0,3 м.
В =3*1 + 4*0, 3 = 4,2 м.
Высота секции камеры, м:
Нк= n*hф+(n-1)*a+ h1+ h2, (6.2.2.6).
где nколичество форм по высоте секции /принимают 5.7 форм/;
hфвысота формы с изделием, м;
авеличина промежутков между формами, а=0,03…0,05 м;
h2- величина зазора между крышкой и верхом формы с изделием, м, h2=0,05…0,1 м;
h1- величина зазора между дном секции камеры и дном формы, h1=0,15 м.
Н= 7*0,55 + 6 *0,05 + 0,1+ 0,15= 4,4 м.
Принимаем ямную пропарочную камеру с размерами:
Lк=7 м; Вк=4,2 м; Нк=4,4 м.
Количество пропарочных камер, шт:
Z=П/m*q*Kоб* Kв, (6.2.2.7).
где Пгодовая производительность технологической линии, м3;
qобъем загружаемых изделий в камеру без форм, м3;
mколичество рабочих дней в году;
Kвкоэффициент использования по времени, равный 0,91;
Kобкоэффициент оборачиваемости камеры /одной секции/.
Zкп=18 000/233*11,55*0,91*1=7,3 шт.
Принимаем 8 ямных камер.
Расчет виброплощадки начинается с определения требуемой грузоподъёмности Qтр, т:
Qв= Qф+ Qб, (6.2.2.8).
где Qфмасса формы, т, определяемая по формуле Qф=Vи*Муд;
Qбусловная масса бетонной смеси, т;
Vиобъем формуемого изделия, м3;
Мудудельная металлоемкость формы, Муд=1,8 т/м3.
Qф=1,1*1,8=1,98 т;
Qб=Vи * ?m ,.
где ?m-расчетная средняя плотность бетонной смеси, т/м3;
Vиобъем формуемого изделия, м3;
Qб=1,1*2,2=2,42 т;
Принимаем виброплощадку СМЖ-187Г.
Таблица 21 Основная характеристика виброплощадки СМЖ — 187 Г.
Показатель. | Величина. | |
Максимальный размер формуемых изделий в плане, м. | 3 х 6. | |
Грузоподъемность, т. | ||
Максимальный статический момент вибровозбудителей, см. | ||
Амплитуда смещений или высоты падений, мм. | 0,2−0,5. | |
Установленная мощность, кВт. | ||
Крепление формы. | Электромагнитное. | |
Габаритные размеры, м. | 8,5 * 2,99*0,69. | |
Масса, т. | 5,6. | |
Тип и марку бетоноукладчика принимаем в зависимости от вида укладываемой бетонной смеси, конфигурации формуемого изделия, требуемой вместимости бункера.
Принимаем бетоноукладчик СМЖ-166Б. Его техническая характеристика представлена в таблице 22.
Таблица 22 Техническая характеристика бетоноукладчика СМЖ-306.
Наименование параметра. | Значение. | |
Ширина колеи, мм. | ||
Число бункеров, шт. | ||
Скорость передвижения, м/мин. | ||
Установленная мощность, кВт. | 4,5. | |
Габаритные размеры, м. | 9,5*5,74*2,39. | |
Масса, т. | 5,2. | |
7. Проектирование склада арматуры Арматурная сталь размещается на складе по маркам, профилям, диаметрам и партиям на стеллажах или подкладках в сухих закрытых помещениях с бетонным полом.
Суточная потребность завода в арматурной стали:
Qсут = Qг/ [(Тн — Тр) Ки], (39).
где Qг — годовая потребность в арматурной стали, т;
Тн — номинальное количество рабочих суток в год, Тн = 260 сут.;
Тр — длительность плановых остановок на ремонт, Тр = 7 сут.;
Ки — коэффициент использования рабочего времени, Ки = 0,92.
Qг = АусрПг, (40).
где Пг — годовая производительность завода, м3 /год;
Ауср — усредненный расход стали, т/м3 .
Усредненный расход стали определяется по формуле:
Ауср. = 0,01[А1?1+А2?2+А3?3+…+Аn?n], (41).
где А1… Аn — среднее значение расхода стали на 1 м³ бетона для каждого вида изделий;
?1???n — доля в объеме проектируемого цеха каждого вида изделий.
Ауср=8,40*0,1+3,9*0,1+55,6*0,3+46,48*0,3+13,8*0,2]=34,6кг/м3;
Qг = 34,660 000/1000 =2076 т/год;
Qсут = 2076/[(260−7)0,92] = 8,9т/сут.
Площадь для складирования арматуры и металла подсчитывается по формуле:
А = (QсутТхрК)/m, (42).
где Qсут — суточная потребность завода в арматуре одного вида с учетом потерь, т;
Тхр — запас арматурной стали на складе, сут., Тхр = 25 сут.;
К — коэффициент, учитывающий неполноту использования площади склада, К = 3; m — масса металла, размещенного на 1 м² площади склада, для стали в мотках m = 1,2 т/м2, для стали в прутках и сортового проката m = 3,2 т/м2.
А = [(8,9253)/1,2] + [(8,9253)/3,2] = 764,8 м².
Принимаем крытый склад арматурной стали, который находится вместе со складом готовой продукции.
8. Расчет склада готовой продукции Площадь склада готовой продукции подсчитывается по формуле:
А = QсутТхрК1К2/ Qн, м2, (43).
где.
А — площадь склада, м2 ;
Qсут — объем изделий, поступающих на склад в сутки, м3 ;
Тхр — запас готовых изделий на складе, Тхр =10 сут.;
Qн — объем изделий, хранящихся в горизонтальном положении на 1 м² площади склада, Qн = 1;
К1- коэффициент, учитывающий проходы между штабелями изделий,.
К1 = 1,5;
К2- коэффициент, учитывающий проезды и площадь под путями кранов, тележек, К2 = 1,3.
Площадь склада для хранения железобетонных изделий:
А = 230,15*10*1,5*1,3/1 = 4487,92 м².
В связи с тем, что склад арматуры будет располагаться на складе готовой продукции, тогда общая площадь составит:
Аобщ.=Аа+Асгп, м2, (54).
где Аа — площадь склада арматуры, м2 ;
Асгп — площадь склада готовой продукции, м2 .
Аобщ.=764,8+4487,92=5252,72 м².
Принимаем склад со следующими размерами: шириной B=36 м и длиной L =36 м (принимаем кратно 12м). Площадь склада готовой продукции будет представлять собой площадку размером 36*36м.
9. Описание климата пункта проектирования Климат описывается по СНиП 2.01.01−82.
Пункт проектированиягород Новосибирск.
1. Подрайон 1 В.
2. Среднемесячная температура воздуха в январе, в самом холодном месяце от -14 до 28? С, а в июле +12 до 21? С.
3. Температура наружного воздуха, средняя по месяцам:
Таблица 13.
Tсредняя за год, ?С. | Tсредняя наиболее холодного периода, ?С. | Tсредняя наружного воздуха по месяцам, ?С. | ||||||||||||
— 0,1. | — 24. | январь. | февраль. | март. | апрель. | май. | июнь. | июль. | август. | сентябрь. | октябрь. | ноябрь. | декабрь. | |
— 19. | — 17,2. | — 10,7. | — 0,1. | +10. | +16,3. | +18,7. | +16. | +9,9. | +1,5. | — 9,7. | — 16,9. | |||
Продолжение таблицы 13.
Табсолютная минимальная, ?С. | Табсолютная максимальная, ?С. | Тсредняя максимальная, ?С. | Тсредняя наиболее холодной пятидневки, ?С. | Тсредняя наиболее холодных суток, ?С. | Тсредняя наиболее холодного периода, ?С. | |
— 50. | 24,6. | — 39. | — 42. | — 24. | ||
Продолжение таблицы 13.
Период со среднесуточной температурой ниже +8?С. | Продолжительность периода со среднесуточной температурой ниже 0? С, сут. | Вечномерзлый грунт. | ||
Продолжительность, сут. | Средняя температура, ?С. | нет. | ||
22,7. | — 9,1. | |||
4. Таблица 14 Амплитуда колебаний температуры по месяцам, средние/максимальные в? С.
9,3/30,3. | 10/23,9. | 10,5/22,8. | 9,9/21,3. | 12,8/24,4. | 12,6/21,6. | 11,4/22,5. | 11/22,3. | 11/22. | 8,5/20,8. | 7,7/28,4. | 8,8/25,9. | |
5. Таблица 3 Средняя абсолютная влажность воздуха в Мб по месяцам.
1,4. | 1,6. | 2,5. | 7,5. | 12,4. | 15,7. | 13,6. | 9,3. | 5,6. | 2,8. | 1,7. | ||
Таблица 4 Средняя относительная влажность воздуха в % по месяцам.
Средняя амплитуда суточных колебаний относительной влажности наиболее жаркого месяца в %: 31%.
6. Количество осадков в мм:
· За год 514.
· Жидких осадков.
· За год 370.
· Суточный максимум 95.
Снежный покров:
· Средняя дата образования и разрушения устойчивого снежного покрова:1/11−10/04.
· Средняя из наибольших высот за зиму в см: 37.
7. Роза ветров:
Январь.
с. | св. | в. | юв. | ю. | юз. | з. | сз. | |
Июль.
с. | св. | в. | юв. | ю. | юз. | з. | сз. | |
Рисунок 1 Роза ветров для города Новосибирска Анализ розы ветров показал, что господствующим ветром в зимний период является ЮЗ-ный ветер, а в летнийСВ-ный. Следовательно продольные оси здания необходимо располагать с З на В.
10. Контроль качества производства и готовой продукции Таблица 26 Входной контроль.
Контролируемые показатели материалов, процессов, продукции. | Кто осуществляет контроль. | |
Цемент: — вид, марка, наличие паспорта; — физикомеханические свойства; Заполнители: — вид, наличие паспорта; — физикомеханические свойства, влажность; Сталь: — вид, класс, марка стали, наличие сертификатов; — физикомеханические свойства. | Отдел снабжения Лаборатория Отдел снабжения Лаборатория. Отдел снабжения Лаборатория. | |
Таблица 27 Пооперационный контроль качества основных технологических процессов.
Основные операции, подлежащие контролю. | Состав контроля. | Место контроля. | Метод и средства контроля. | Периодичность и объем контроля. | |
1 Состояние формовочного оборудования: виброплощадка, бетоноукладчик. | 1 Колебания виброплощадки. 2 Техническое состояние оборудования. | Посты формования. Лаборатория. | Виброграф. Паспорт. | Ежемесячно. | |
2 Арматурные работы. | 1 Марка стали. 2 Соответствие размеров арматуры рабочим чертежам. 3 Сварка сеток. 4Антикоррозионная защита. | Арматурный цех. | 1 Сравнение с эталоном. 2 Обмер рулеткой. 3 Визуальный отбор проб и испытание. | 2 раза в смену. | |
3 Установка и закрепление каркасов, сеток, закладных деталей. | 1 Соответствие рабочим чертежам. 2 Защитный слой. 3 Положение арматурного каркаса. | Пост армирования. | Обмер стальной рулеткой, мерной линейкой. Визуальный. | Раз в смену. | |
4 Приготовление бетонной смеси. | 1 Точность дозирования. 2 Время перемешивания. 3 Консистенция. | Бетоносмесительный цех. | 1 Наблюдение за приборами. 2 Проверка тарирования прибора. 3 Отбор проб испытание. | п.1- раз в смену п.2- каждый замес п.3- 2 раза в смену и при новом составе смеси. | |
5 Подготовка и смазка форм. | 1 Качество очистки и смазки форм. 2 Качество эмульсии. | Пост чистки и смазки. | 1 Осмотр 2 Отбор проб и испытание. | п.1- раз в смену п.2- раз в месяц. | |
6 Укладка бетонной смеси. | 1 Время вибрироуплотнения. 2 Плотность укладки. 3 Прочность бетона. 4 Толщина слоя. | п. 1, 2, 4- пост формования п. 3- лаборатория. | п. 1- секундомер п. 2- плотномер п. 3- отбор проб и последующее их испытание. п. 4- замер линейкой. | п.1- поштучно п. 2- раз в смену п. 3- серия контрольных кубов п. 4- поштучно. | |
Основные операции, подлежащие контролю. | Состав контроля. | Место контроля. | Метод и средства контроля. | Периодичность и объем контроля. | |
7 ТВО. | Соблюдение заданного режима ТВО. | Камер ТВО. | Приборы автоматики и регулирования. | В процессе обработки через 2 ч. партия в камере. | |
8Распалубливание Подготовка к сдаче продукции, складирование. | 1 Внешний вид. 2 Наличие дефектов. 3 Соответствие расположения изделий схеме складирования. | Пост распалубливания, склад готовой продукции. | п. 1, 2- визуально п.3- стальная рулетка, схема. | п. 1,2- поштучно п. 3- 2 раза в смену. | |
Таблица 28 Выходной контроль.
Внешний вид. | Не допускаются наличие раковин, сколов, трещин шириной > 2 мм. Не допускаются наплывы и выемки. | |
Отклонения в размерах. | 1 Отклонение от линейного размера: — по длине ±10 мм; — по ширине ±10 мм; — по высоте ±5 мм; 2 Размер выступов ±6 мм; 3 Обнажение арматуры не допускается кроме концов арматуры, которые не должны выступать за торцевые поверхности панелей более чем на 10 мм и должны быть защищены слоем цементнопесчаного раствора. | |
Отпускная прочность. | При приемке ОТК устанавливается отпускная прочность в теплый период- 70%, в холодный период- 85%. | |
11. Техника безопасности и охрана окружающей среды Заводы сборного железобетона относятся к числу предприятий, на которых санитарногигиенические условия труда и техника безопасности являются не только важнейшими критериями для повышения производительности труда, они обеспечивают сохранение здоровья каждого работающего на предприятии.
В целях предотвращения загрязнения воздуха помещений с вредными выделениями: оборудование, приборы, трубопроводы и другие источники, выделяющие теплоту, должны быть теплоизолированы; агрегаты и оборудование, при эксплуатации которых происходит влаговыделение, должны быть укрыты и изолированы; технологические процессы, связанные с выделением пыли, следует изолировать так, чтобы их работа осуществлялась без участия людей, а выделяющиеся технологические выбросы в виде пыли, паров и вредных газов перед выпуском в атмосферу должны быть подвергнуты очистке.
В цехах, где используются вибрационные механизмы, должны быть приняты меры по устранению воздействия вибрации и снижению уровня шума.
При приготовлении бетонной смеси необходимо следить за исправной работой вентиляции, герметизацией кабин пультов управления дозаторами и смесителями, системой сигнализации и автоматизации.
Формование изделий осуществлять при включенной звуковой сигнализации, управление формовочными машинами должно быть дистанционным. При тепловой обработке изделий следует не допускать утечки пара из камер, загружать и выгружать камеры с помощью автоматических траверс.
1 Баженов Ю. М. Технология бетона. / Ю. М. Баженов .- М.: АСВ. — 2009. — 500 с.
2 Михайлов К. В. Производство сборных железобетонных изделий. / К. В. Михайлов, К.М. Королев/Справочник. — М.: Стройиздат.- 2008.-447 с.
3 Тимофеев А. И. Проектирование предприятий сборного железобетона для районов Сибири и Крайнего Севера / А. И. Тимофеев, В. А. Безбородов /Учебное пособие. — Новосибирск, НГАСУ. — 2009. — 80с.
4 Белан В. И. Легкие бетоны / В. И. Белан, В.А. Безбородов/Методические указания. — Новосибирск, НГАСУ.- 1993.-34 с.