Другие работы

Эта проблема особенно актуальна для автоматизированного производства, где оперативное вмешательство человека в процесс обработки затруднено или невозможно, поэтому обычно на практике устойчивая работа системы обеспечивается экспериментально в период наладки оборудования и пробных обработок деталей. Следовательно, возникает необходимость создания алгоритмов автоматического управления с требуемыми…
Диссертация 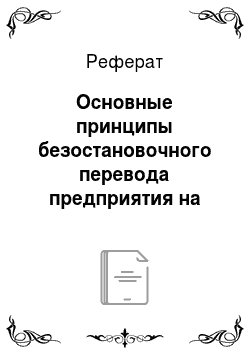
Успех безостановочного перевода производства на выпуск модели новой машины в значительной степени зависит от степени наладки и освоения новых технологических процессов к моменту переходя. Монтаж нового оборудования немедленно после его поступления и создание поточных линий для обработки деталей новой машины являются важными предпосылками, обеспечивающими наладку новых технологических процессов…
Реферат 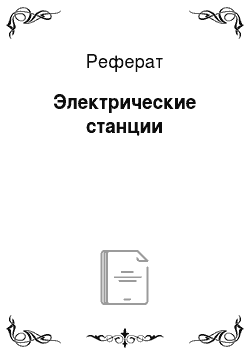
Комплектное распределительное устройство (КРУ) — это распределительное устройство, которое сформировано из полностью или частично закрытых шкафов и блоков, в которые встроены аппараты, устройства защиты и автоматики. Такие устройства обычно поставляются в полностью собранном, готовом к использованию состоянии. Комплектные распределительные устройства предназначены и для внутренней, и для наружной…
Реферат 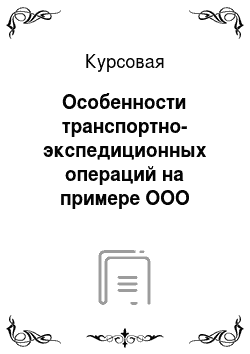
В среднесрочной перспективе можно ожидать повышения конкурентоспособности автоперевозчиков на внутреннем рынке транспортных услуг за счет повышения эффективности функционирования автотранспорта, качества транспортных услуг и лучшего использования, данных мониторинга потребительского спроса. Уровень загрузки автомобилей при междугородных перевозках грузов повысится примерно в 1,5 раза (с 48−50…
Курсовая 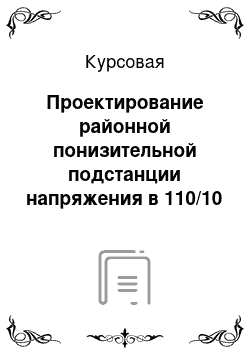
В соответствии с принятой схемой электрических соединений подстанции в курсовом проекте необходимо произвести выбор и проверку следующих аппаратов: На стороне высокого напряжения подстанции -разъединители, выключатели, ограничители перенапряжения, контрольно-измерительная аппаратура (трансформаторы тока и напряжения, измерительные приборы). На стороне низкого напряжения подстанцииопределить тип…
Курсовая 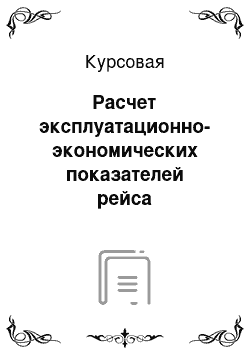
Кокосовое масло вырабатывается из копры плодов кокосовой пальмы (Cocos nucifera L.) методами прессования и экстракции. 5.3.2 Содержание пестицидов, токсичных элементов, афлатоксина В1, радионуклидов, значение показателя окислительной порчи в кокосовом масле, используемом в качестве сырья в пищевых целях, не должно превышать уровни, установленные для растительных масел в санитарных правилах…
Курсовая 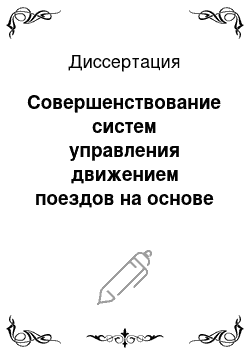
Актуальность совершенствования существующих, разработки и внедрения новых систем в указанных сферах объясняется необходимостью существенного улучшения условий сбора информации, выполнения на этой основе качественного оперативного анализа с целью принятия оптимальных решений и реализации регулировочных воздействий. Продекларированные в ранних работах /44−45, 48, 50−51/ принципы создания систем…
Диссертация 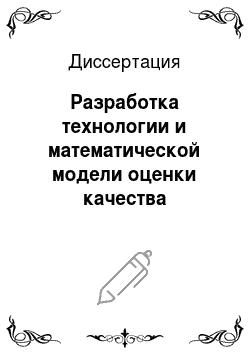
Дана комплексная товароведная оценка нового быстрорастворимого гранулированного напитка. На основании результатов анализа физико-химических, органолептических и микробиологических показателей обоснован и установлен срок хранения напитка, который составил 6 месяцев при температуре 20±-2°С и относительной влажности воздуха 75±5%. Установлены регламентируемые показатели качества и пищевой…
Диссертация 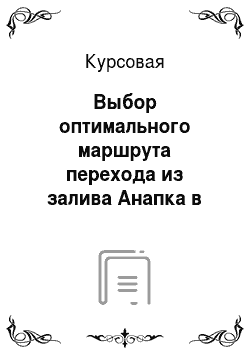
Порт Петропавловск-Камчатский географические координаты 53 град. 2 минуты север. широты; 158 град. 39 минут восточ. долготы. Петропавловск-Камчатский — один из крупных тихоокеанских портов России — расположен на восточном побережье полуострова Камчатка в Авачинской губе. Порт открыт для навигации в течение круглого года. В суровые зимы, когда лед достигает большой толщины, проводка судов…
Курсовая 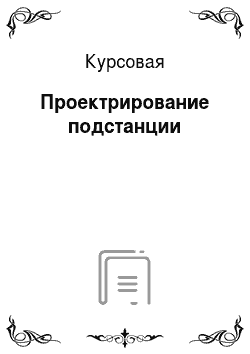
Таблица 8.1 — Выбранные контрольно-измерительные приборы Приборы Тип Число приборов Ввод от трансформаторов к сборным шинам 110 кВ Амперметр Э 335 2 Ваттметр Д-335 2 Счётчик ватт-часов СА3-И681 2 Счётчик вольт-амперчасов реактивный СР4-И689 2 На отходящих линиях 110 кВ Амперметр Э 335 5 Счётчик ватт-часов СА3−681 0,5 Счётчик вольт-амперчасов реактивный СР4-И689 0,5 Подключено секционному ТТ (110…
Курсовая 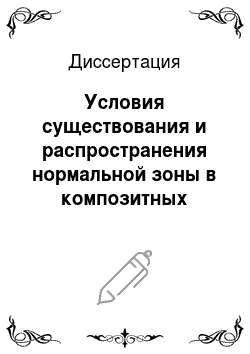
Тот факт, что при сверхпроводники обладают запасом устойчивости по отношению к конечным возмущениям, был отмечен в. В этом интервале токов стабильность композита от соотношения между энергией необходимой для создания распространяющейся нормальной зоны (критическая энергия) и тепловыделениями, возникающими при изменении режима работы сверхпроводящей магнитной системы. Причиной таких тепловыделений…
Диссертация 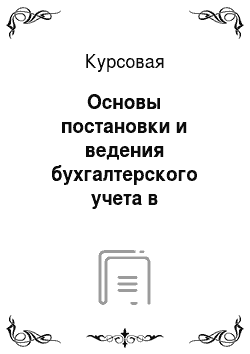
Особую актуальность тема расчетов с персоналом по оплате труда приобретает на современном этапе. Поиск резервов ее повышения, тем самым повышения мотивации персонала к труду помогает многим предприятиям повысить свою конкурентоспособность, избежать банкротства и выжить в условиях рыночной экономики. В условиях рыночных отношений система управления затратами на заработную плату является одним…
Курсовая 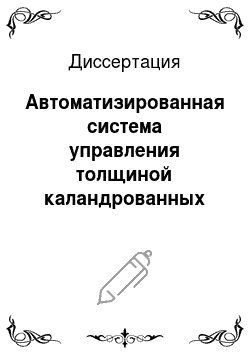
В этих условиях для повышения эффективности управления качеством каландрованных полимерных материалов актуальна разработка математических моделей, позволяющих исследовать влияние различных типов управляющих воздействий на толщину и равнотолщинность и выбирать наиболее рациональные способы управления и значения управляющих воздействий, как в номинальном режиме, так и при переходе производств…
Диссертация 
Первичную защиту гидросистемы (от активных и реактивных перегрузок для РО1 и от реактивных и инерционных при пуске для РО2) обеспечивают предохранительные клапаны КП 1, КП 2 непрямого действия. В приводе РО 1 с электрическим управлением, нормально открытый, в приводе РО2 неуправляемый. Первичная защита РО1 настроена на давление 35 МПа, первичная защита РО2 — 35 МПа. Вторичную защиту…
Курсовая 
Туризм сегодня — это глобальный компьютеризированный бизнес, в котором участвуют крупнейшие авиакомпании, гостиничные цепочки и туристические корпорации всего мира. Современный турпродукт становится более гибким и индивидуальным, более привлекательным и доступным для потребителя. Персональный компьютер и Интернет, их доступность и надежность, способствуют проникновению во все сферы общества…
Курсовая