Другие работы
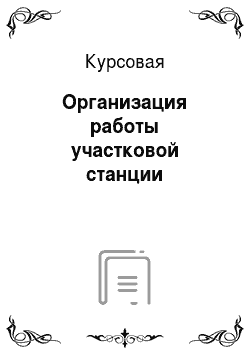
Приказы об отправлении поезда при запрещающем показании выходного светофора при АБ двухпутных участков, ПАБ одно — и двухпутных участков; о приеме поезда при запрещающем показании входного сигнала; о занятии П-О путей промежуточных станций вагонами; отправлении длинносоставных поездов; об установлении порядка отправления и следования по участкам, оборудованным АБ, маневровых локомотивов…
Курсовая 
Планирование и организация проведения ТО тракторов Число и виды ТО на год или месяц данного трактора определяют, в зависимости от их планируемой наработки за данный период, в килограммах или условных эталонных гектарах, фактической наработки к началу периода от последнего капитального или от момента в вода в эксплуатацию и от периодичности вида ТО. Используя исходные данные годового планового…
Курсовая 
В последние годы для получения различных фасонных отливок из тугоплавких и твердых сплавов широко применяют литье по выплавляемым моделям. Точность отливок по этому методу составляет 0,04—0,05 мм на 25 мм длины. Чистота поверхности отливок соответствует V4—б классам. Отлитые детали, как правило, не подвергаются механической обработке и лишь в некоторых местах шлифуются. По этому способу…
Реферат 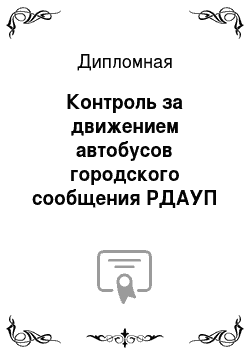
Линейная диспетчеризация автобусных маршрутов может осуществляться различными методами. Метод контроля за движением транспортных средств путем обустройства конечных остановочных пунктов маршрутов линейными диспетчерскими пунктами рассмотрен выше. Следует отметить, что рассмотренный метод обеспечивает лишь сбор данных о регулярности движения и количестве выполненных рейсов. Обработка полученных…
Дипломная 
Проведённый патентный поиск и сопоставительный анализ различных схем и конструктивных решений виброзащиты позволил определить одну из наиболее рациональных конструкций управляемого динамического виброгасителя и разработать ряд новых решений в реализации управляемых гасителей колебаний, позволяющих решить большинство проблем, связанных с использованием устройств такого рода. Проведённые…
Диссертация 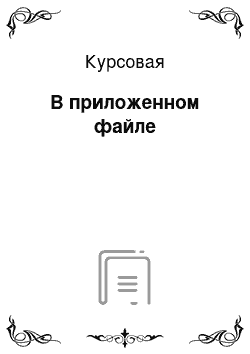
Для определения толщины плиты базы находим изгибающие моменты на участках 1, 2, 3, 4. Каждый участок рассматриваетсякак свободно опертая пластинана ребра, траверсы или стерженьколонны и загруженная равномерно распределенной нагрузкой реактивным давлением со стороны фундамента на полосе шириной 1см:; = 0,865*1 = 0,865 кН/см.Рис. К определению толщины опорной плиты. Участок 1 — будет изгибаться…
Курсовая 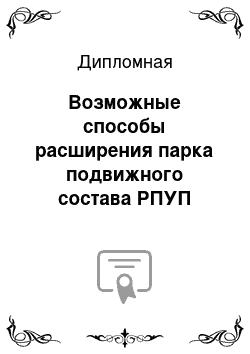
Банковский — это такой кредит, при котором владельцы свободных денежных средств предоставляют их в ссуду заемщикам через посредство банков. Его субъектами являются, с одной стороны, банк как кредитор, с другой — предприятие, организации и населения как заемщики. Банковский кредит выступает всегда в денежной форме и объектом кредитования предстает денежный капитал. В силу этого, в банковском…
Дипломная 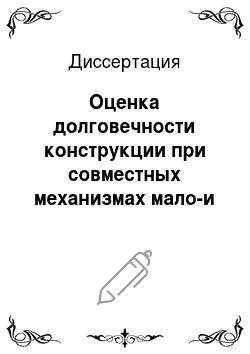
Обоснованность оценки ресурса ответственных инженерных объектов (ОИО) (ядерных энергетических установок, объектов химической, газовой, нефтяной отрасли и др.) в течение длительного срока службы (40−60 лет) требует корректного учета вкладов действующих факторов в повреждение материала критических зон элементов оборудования, которые из-за специфики своего эксплуатационного нагружения определяют…
Диссертация 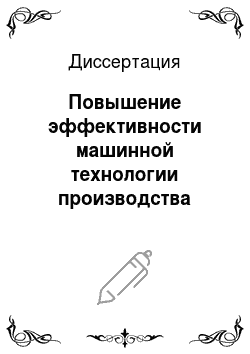
Традиционные методы принятия решений при построении технологий в сельском хозяйстве, в том числе и при построении технологии производства картофеля, на основе практического опыта, интуиции и несложных расчётов, мало учитывающих взаимодействие факторов сельскохозяйственного производства, более или менее приемлемы при управлении небольшими и несложными объектами. В современных же условиях при…
Диссертация 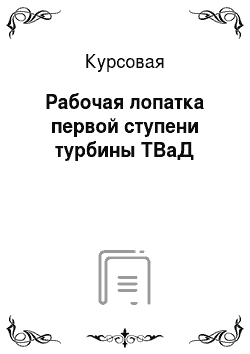
Создание сетки производим на ЭВМ с помощью подмодуля САПР «Расчетная сетка». Этот подмодуль является частью САПР охлаждаемых лопаток турбин и предназначен для автоматизированного построения сетки триангуляционных (треугольных) элементов внутри плоской многосвязанной области для решения уравнений теплопроводности и термонапряженного состояния. Для визуального просмотра температурного поля…
Курсовая 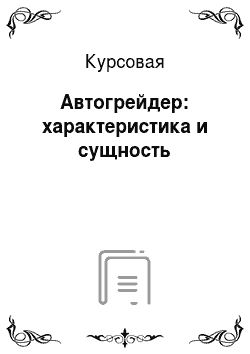
Автогрейдер — универсальная землеройно-транспортная машина, предназначенная для выполнения профилировочных работ и отделки земляного дорожного полотна и обеспечивающая полный цикл земляных работ при строительстве дорог. Кроме того, автогрейдер применяют для возведения невысоких насыпей из боковых резервов, устройства террас на косогорах, корыта в дорожном полотне, срезки и планировки откосов…
Курсовая 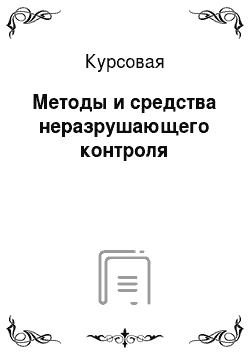
Суть магнитопорошкового метода заключается в следующем: магнитный поток в бездефектной части изделия не меняет своего направления, если же на пути его встречаются участки с пониженной магнитной проницаемостью, например дефекты в виде разрыва сплошности металла (трещины, неметаллические включения и т. д.), то часть силовых линий магнитного поля выходит из детали наружу и входит в нее обратно, при…
Курсовая 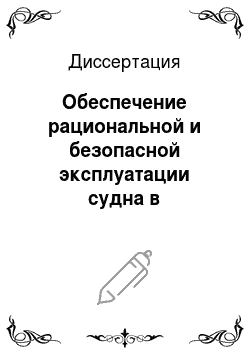
Дальнейшее развитие гидроакустических рыбопоисковых средств, превращение этих средств в информационно-вычислительные системы за счет использования в практике промышленного морского рыболовства вычислительной техники позволяет расширить селективные способности активных орудий лова, таких, например, как тралы. Для увеличения селективной способности тралов и обеспечения изъятия объекта лова при…
Диссертация 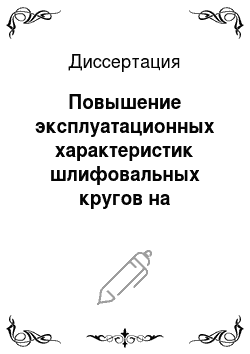
Масловым Е. Н. отмечено, что сцепление органической связки с металлическим покрытием из-за повышенной адгезии может превышать усилие сцепления между поверхностью зерна и связки. По данным некоторых авторов, усилие разрушения металлизированных зерен увеличивается в 1,2 — 2,5 раза. В качестве неметаллического покрытия зерен электрокорунда используют диметилдихлорсилан, трифенилборат, азодикарбонамид…
Диссертация 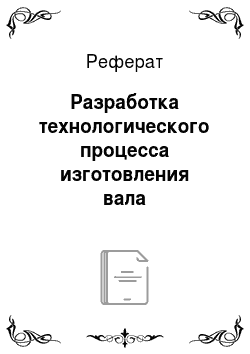
Анализ исходных данных… 2 1.1. Анализ Материала… 2 2. Количественная оценка выпуска деталей… 3 2.1. Количество изготавливаемых деталей в год… 3 2.2. Размер партии деталей … 3 3. Выбор исходной заготовки и методов ее изготовления … 3 3.1 Расчет варианта получения заготовки — штамповки… 4 3.2 Расчет варианта получения заготовки — из проката… 5 4. Выбор технологических баз. … 6 5. Составление…
Реферат