Методы и средства неразрушающего контроля
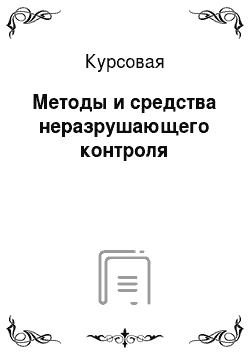
Рациональное использование комплекса неразрушающих методов контроля позволяет повысить надежность и качество продукции, предотвращает аварии сложных агрегатов и дает производству огромные экономические преимущества. Это помогает также осваивать новое более сложное производство, а также внедрять новые прогрессивные технологические процессы. Стопроцентный неразрушающий контроль позволяет определить… Читать ещё >
Методы и средства неразрушающего контроля (реферат, курсовая, диплом, контрольная)
Введение
Уровень развития промышленности передовых стран на современном этапе характеризуется не только объемом производства и ассортиментом выпускаемой продукции, но и показателями ее качества.
Контроль качества является самой массовой технологической операцией в производстве. В связи с усложнением и требованием неуклонного повышения надежности новой техники, трудоемкость контрольных операций в промышленности резко увеличивается. Срок окупаемости затрат на оборудование неразрушающего для контроля качества изделий во многих случаях в 5…10 раз меньше срока окупаемости технологического оборудования.
Качество продукции — это совокупность свойств продукции, обуславливающих ее пригодность удовлетворять определенные потребности в соответствии с ее назначением. Высококачественный объект отличается постоянством химического состава, микрои макроструктуры, электрических и магнитных характеристик материала, неизменными геометрическими размерами, повышенными механическими, антикоррозионными и другими свойствами.
Рациональное использование комплекса неразрушающих методов контроля позволяет повысить надежность и качество продукции, предотвращает аварии сложных агрегатов и дает производству огромные экономические преимущества. Это помогает также осваивать новое более сложное производство, а также внедрять новые прогрессивные технологические процессы. Стопроцентный неразрушающий контроль позволяет определить качество материалов или полуфабрикатов, проверить эффективность совершенствования производственного процесса и дает возможность отобрать часть годной продукции для дальнейшей обработки.
Систематическое проведение неразрушающих испытаний на различных стадиях технологического процесса и статистическая обработка результатов этих испытании позволяют определять, на каких стадиях процесса возникают дефекты, и, следовательно, устанавливать и устранять причины брака.
При этом меняется сама сущность операций контроля. Пассивный контроль, фиксирующий только качество готовых деталей, становится активным методом корректировки технологического процесса. Особенно возрастает активная роль контроля в условиях автоматизации производства.
Таким образом, при рациональном использовании методов неразрушающего контроля, они могут стать эффективным средством совершенствования технологического процесса.
Операции неразрушающего контроля представляют собой неотъемлемое и равноправное звено технологического процесса, которое способно:
— определить качество изделия
— определить прочность изделий;
— нацелить на лучшее конструктивное и технологическое решение;
— поддержать марку фирмы;
— предотвратить несчастные случаи и повысить безопасность;
— снизить стоимость производства.
Неразрушающий контроль — определение характеристик материалов и изделий без их разрушения. Неразрушающий контроль основан на использовании проникающих полей, излучений и веществ для получения информации о качестве материалов и объектов.
Неразрушающий контроль подразделяется на следующие виды: акустический, магнитный, электрический, вихретоковый, радиоволновой, тепловой, оптический, радиационный и проникающими веществами. Неразрушающий контроль, в отличие от разрушающего, обеспечивает проверку качества надежности и безопасности объектов без разрушения, т. е. после него продукция может использоваться по прямому назначению и, во многих случаях, без остановки работы объекта. Контролироваться могут сварные швы, материалы, из которых собираются что-либо делать или уже готовые изделия из этих материалов в процессе их изготовления, или при эксплуатации.
1. Анализ объекта контроля По заданию объектом контроля является вал редуктора ТРКП пассажирского вагона (рисунок 1.1).
Рисунок 1.1 — вал редуктора ТРКП вал редуктора ТРКП пассажирского вагона изготавливается методом поперечно-винтового проката и представляет собой ступенчатый вал.
Шероховатость контролируемой поверхности Rа = 3,6 мкм.
В процессе эксплуатации колёсная пара испытывает как статические, так и динамические нагрузки. Температурный диапазон эксплуатации составляет (-50 °С — +100 °С).
При ремонте подвижного состава главным образом контролируются эксплуатационные дефекты.
Эксплуатационные дефекты возникают при длительном нагружении конструкций подвижного состава знакопеременными динамическими усилиями. В эту группу входят следующие дефекты:
Трещины усталости, возникающие под действием переменных напряжений, в местах резких переходов сечений и других концентраторов напряжений (раковины, выщерблины, отколы).
Трещины при перегрузке — надрывы в поверхностном слое детали при нагрузках, превышающих предел прочности детали.
Механические повреждения в виде забоин, вмятин, рисок, местного наклепа, местного уширения, ползунов.
2. Анализ исходных данных и характеристик объекта контроля На основе проведенного анализа колёсной пары можно определить характеристики необходимые для выбора метода контроля, расчета и разработки оборудования. В качестве материала изделия будем использовать сталь 20 (таблица 2.2). В таблице 2.1 приведены данные, необходимые для расчета намагничивающего устройства и проведения магнитопорошкового контроля.
магнитопорошковый ультразвуковой феррозондовый контроль Таблица 2.1 — Характеристики объекта контроля и намагничивающего устройства
Метод НК | Манитопорошковый | |
Материал: — магнитопровода — изделия | Сталь 40 Сталь 20 | |
Шероховатость поверхности обьекта контроля Rа, мкм | 3,6 | |
Толщина стенок намагничиваемой детали b, мм | ||
Толщина полюсов электромагнита d, мм | ||
Ширина полюсов электромагнита с, мм | ||
Расстояние между полюсами электромагнита L, мм | ||
Высота электромагнита h, мм | ||
Толщина неферромагнитного покрытия д, мкм | ||
Сталь 20 | Hc=320; Br=0,17, Нприл.=5600 А/м. | |
Таблица 2.3 — Данные для построения кривой намагничивания материала магнитопровода и изделия.
Напряженность магнитного поля H, А/м | Магнитная индукция Br, Тл | ||
Сталь 40 | Сталь 20 | ||
0,090 | 0,050 | ||
0,300 | 0,500 | ||
0,810 | 0,975 | ||
1,070 | 1,240 | ||
1,220 | 1,380 | ||
1,320 | 1,430 | ||
1,395 | 1,515 | ||
1,475 | 1,585 | ||
1,560 | 1,630 | ||
1,665 | 1,725 | ||
1,730 | 1,780 | ||
1,790 | 1,830 | ||
1,820 | 1,860 | ||
1,900 | 1,940 | ||
2,940 | 1,960 | ||
2,990 | 2,040 | ||
2,020 | 2,070 | ||
2,040 | 2,110 | ||
2,060 | 2,140 | ||
2,080 | 2,166 | ||
3. Выбор и обоснование метода контроля При выборе метода контроля руководствуются следующими положениями:
— выбранный метод должен обеспечить максимальную вероятность выявления поверхностных и подповерхностных дефектов.
— выбранный метод должен быть экономически эффективным.
В связи с тем, что материал, из которого изготовлена вал редуктора ТРКП является ферромагнетиком, а возможные дефекты лежат в поверхностной и подповерхностной зоне, наиболее целесообразно проводить контроль магнитопорошковым, ультразвуковым или феррозондовым методом. На основе литературных данных приведенных в источнике, я отдал предпочтение магнитопорошковому методу.
Суть магнитопорошкового метода заключается в следующем: магнитный поток в бездефектной части изделия не меняет своего направления, если же на пути его встречаются участки с пониженной магнитной проницаемостью, например дефекты в виде разрыва сплошности металла (трещины, неметаллические включения и т. д.), то часть силовых линий магнитного поля выходит из детали наружу и входит в нее обратно, при этом возникают местные магнитные полюсы и, как следствие, магнитное поле над дефектом. Так как магнитное поле над дефектом неоднородно, то на магнитные частицы, попавшие в это поле, действует сила, стремящаяся затянуть частицы в место наибольшей концентрации магнитных силовых линий, то есть к дефекту. Частицы в области поля дефекта намагничиваются и притягиваются друг к другу как магнитные диполи под действием силы так, что образуют цепочные структуры, ориентированные по магнитным силовым линиям поля.
Наиболее распространенным способом нанесения порошка на контролируемую поверхность является нанесение порошка в виде магнитной суспензии. После намагничивания или во время него, деталь или её контролируемый участок должны быть равномерно и обильно обработаны суспензией с заданной концентрацией порошка. Обработка проводится либо путём полива детали суспензией, либо путём окунания её в ванну с хорошо перемешанной суспензией. Осмотр деталей проводится, как правило, невооруженным глазом после полного стекания с контролируемого участка основной массы суспензии.
Магнитопорошковый метод позволяет обнаруживать поверхностные и подповерхностных дефекты типа нарушений сплошности материала: трещины различного происхождения, флокены, закаты, надрывы, волосовины, расслоения, дефекты сварных соединений и др. соединений.
Необходимым условием применения магнитопорошкового метода для выявления дефектов является наличие доступа к объекту контроля для намагничивания, обработки индикаторными материалами и оценки качества.
Результаты контроля объектов магнитопорошковым методом зависят от следующих условий:
— магнитные характеристики материала,
— форма и размеры ОК;
— шероховатость поверхности ОК;
— наличие и уровень поверхностного упрочнения;
— толщина немагнитных покрытий;
— местоположение и ориентация дефектов;
— напряженность магнитного поля и его распределение по поверхности объекта;
— угол между направлением намагничивающего поля и плоскости дефектов;
— свойства магнитного индикатора и способ его нанесения на объект контроля;
— способ и условия регистрации индикаторного рисунка выявляемых дефектов.
Магнитопорошковый метод может быть использован как для контроля деталей, изготовленных из ферромагнитных материалов, так и для контроля объектов с немагнитным покрытием (слой краски, лака, хрома, меди, кадмия, цинка и др.). Объекты с немагнитными покрытиями толщиной < 40 мкм могут быть проконтролированы без существенного уменьшения выявляемости дефектов. Колёсная пара не имеет немагнитного покрытия и поэтому целесообразно использовать для её контроля магнитопорошковый метод.
Магнитопорошковый метод не позволяет определять глубину и ширину поверхностных дефектов, размеры подповерхностных дефектов и глубину их залегания, поэтому магнитопорошковый метод совмещают с ультразвуковым.
Магнитный контроль в зависимости от физико — химических свойств ОК, его формы и размеров, типа и расположения искомых дефектов, а также мощности намагничивающих устройств проводят способом приложенного магнитного поля (СПП) или способом остаточной намагниченности (СОН).
СПП контролируют детали из магнитомягких, малоуглеродистых сталей, обладающих малыми значениями Вr и коэрцитивной силы Нc (менее 800 А/м). Например, оси колесных пар, детали автосцепки дефектоскопируют в приложенном переменном магнитном поле при продольном намагничивании магнитопорошковым методом. Явление поверхностного эффекта, проявляющееся при этом, способствует лучшему выявлению поверхностных трещин: магнитный поток концентрируется в поверхностном слое металла, увеличивая магнитное поле рассеяния над дефектом.
Контроль СОН применяют для деталей из термически обработанных конструкционных сталей. Магнитные свойства этих металлов должны характеризоваться значениями Br > (0,6…0,8) Тл и Нс > 800…1000 А/м. СОН используется для обнаружения трещин в роликах и кольцах буксовых подшипников магнитопорошковым методом.
Поскольку материал изделия сталь 20 с параметрами Вr = 0,17 Тл, Hc = 32 А/м, из графика выбора способа магнитопорошкового контроля (рисунок 3.1) выбираю СПП.
Рисунок 3.1 — Выбор способа магнитопорошкового контроля
Для проведения магнитопорошкового контроля будем использовать дефектоскоп магнитопорошковый разъемный МД-12ПЭ, так как он спроектирован специально для контроля валов.
Он предназначен для обнаружения поверхностных поперечных трещин осей вагонных колесных пар при неразрущающем контроле магнитопорошковым методом. Позволяет производить контроль валов при намагничивании их приложенным продольным магнитным полем соленоида, питаемого переменным током частотой 50Гц.
Возможность выявления дефектов основана на явлении притяжения частиц магнитного порошка в местах выхода на поверхность магнитного потока, связанного с наличием в контролируемой детали нарушений сплошности. Намагничивание контролируемой детали производится с помощью соленоида. В намагниченных деталях дефекты вызывают перераспределение магнитного потока и выход части его на поверхность. На поверхности детали создаются локальные магнитные полюсы, притягивающие частицы магнитного порошка, в результате чего дефект становится видимым.
Технические характеристики:
— Эффективное значение тока намагничивания без контролируемой
— детали при номинальном напряжении сети, А, не менее … 1320
— Потребляемая мощность, кВ· А, не более …1,85
— Напряжение/частота, В/Гц …220/50
— Габаритные размеры блока управления, мм, не более …400×270×160
— Масса блока управления, кг, не более …30
— Масса блока контроля, кг, не более …9
— Масса соединительного кабеля, кг, не более …8
— диаметр рабочего отверстия, мм… 240
— Напряженность поля, А/м…12 000
Дефектоскоп состоит из блока управления и блока контроля с разъемным соленоидом (рисунок 4.2).
Рисунок 4.2 — Основные блоки дефектоскопа МД-12ПЭ
Блок управления предназначен для подключения блока контроля к сети 220 В (50 Гц). На лицевой панели блока управления расположены стрелочные индикаторы напряжения сети и намагничивающего тока, выключатели сети и переносного светильника на 12 В. Блок контроля преобразует напряжение сети 220 В (50 Гц) в напряжение питания соленоида 3,5 В. Диаметр рабочего отверстия соленоида — 185 мм. Блок контроля и соленоид размещены на тележке, которая перемещается вдоль контролируемой средней части оси. Блок контроля имеет подъемное устройство с рычажной подачей, позволяющее устанавливать соленоид на нужной высоте.
Обеспечение взаимодействия магнитного поля с объектом контроля возможно при его намагничивании. Способы и схемы намагничивания выбирают в зависимости от формы и размеров объектов контроля, а также ориентации подлежащих выявлению дефектов.
Магнитные индикаторы — это магнитные суспензии (взвесь магнитных частиц в дисперсной среде — жидкости), магнитные порошки (взвесь
магнитных частиц в воздухе), полимеризирующиеся смеси, применяемые для визуализации дефектов. Магнитные индикаторы и способы их нанесения выбирают в зависимости от цели и условий контроля. Магнитные индикаторы наносят на контролируемую поверхность «сухим» или «мокрым» способом. Сухой способ не применяют при контроле средней части оси седлообразным намагничивающим устройством (НУ), мелких деталей круглого сечения диаметром менее 100 мм и деталей с резьбой. Магнитный порошок наносится с помощью пульверизатора, резиновой груши и сита тонким слоем зигзагообразно вдоль детали с шагом не более 30 мм. Сам распылитель располагают на расстоянии 30—50 мм от поверхности. Скопление порошка вблизи намагничивающего устройства следует сдувать с помощью резиновой груши, а на участки, оказавшиеся без порошка, следует подсыпать порошок повторно.
Магнитную суспензию наносят путем полива слабой струей, не смывающей осевшие над дефектами магнитные частицы; погружения детали в емкость с суспензией; распыления суспензии из пульверизатора. При этом необходимо обеспечить небольшой наклон контролируемой поверхности для равномерного стекания суспензии. Перед нанесением суспензии ее тщательно перемешивают лопаткой из немагнитного материала, так чтобы она равномерно распределилась по всему объему дисперсионной среды.
Для облегчения работы дефектоскопистов вместо магнитных порошков часто используют суспензии, в которых порошок разведен в дисперсионной среде (воде, минеральном масле или керосине), плюс добавки, без которых частицы порошка в суспензии имеют свойство соединяться между собой с образованием разрозненных специфических частиц-скоплений, каждая из которых состоит из большого числа обычных частиц.
Соединение частиц порошка происходит под воздействием молекулярных сил, возникающих вследствие большой свободной поверхностной энергии молекул различных слоев суспензии и воздуха.
При интенсивном слипании частиц с образованием крупных частиц-скоплений происходит снижение, а иногда и полная потеря чувствительности магнитной суспензии. Для предотвращения этого негативного явления в суспензию вводят вещества, понижающие свободную поверхностную энергию.
Молекулы поверхностно-активных веществ имеют дипольное строение, поэтому в результате адсорбции таких молекул на частицах порошка все частицы суспензии оказываются заряженными электростатическими зарядами одного знака. Возникающие при этом электростатические силы отталкивания не дают возможность частицам сблизиться на расстояния, на которых
проявляются молекулярные силы притяжения. Благодаря этому суспензия переходит в устойчивое состояние, что обеспечивает ей высокую чувствительность.
В нашем случае деталь имеет светлую поверхность. Из технической литературы выбираем магнитный индикатор КМС ДИАГМА 0473, характеристики которого приведены в таблице 4.
Таблица 3 — Тип магнитного индикатора
Наименование | Цвет | Способ нанесения | Назначение | Количество | |
1 Концентрат маг-нитной суспензии (КМС) ДИАГМА 1100 | Черный | Мокрый способ (вода) | Контроль деталей со свет-лой поверхностью любой шероховатости | 1 Концентрат маг-нитной суспензии (КМС) ДИАГМА 1100 | |
4. Разработка методики контроля Согласно имеющейся в научно-технической литературе информации, метод МПК должен включать в себя следующие операции:
— подготовку поверхностей изделий к контролю;
— намагничивание деталей;
— обработку поверхности детали суспензией (порошком) ;
— осмотр деталей;
— размагничивание;
— контроль качества процесса.
Для обеспечения надёжного магнитопорошкового контроля необходимы следующие вспомогательные устройства:
— намагничивающее устройство;
— устройство для нанесения магнитной суспензии или порошка на детали;
— осветители контролируемой поверхности видимым (белым) или ультрафиолетовым светом;
— измерители напряженности магнитного поля ;
— измерители концентрации порошка в магнитной суспензии;
— контрольные образцы с тонкими дефектами и другие средства метрологической проверки;
— размагничивающие устройства. [6]
Рассмотрим более подробно основные из них:
1. Очистить поверхность вал редуктора ТРКП до металла.
2. Осмотреть контролируемую поверхность с целью выявления видимых глазом дефектов
3. При обнаружении дефекта визуально внести запись в «Журнал учета результатов контроля».
4. Раскрыть разъемный соленоид и опустить его максимально вниз.
5. Установить вал редуктора ТРКП
6. Отрегулировать высоту соленоида так, чтобы зазор между его витками и вал сверху был не меньше, чем снизу.
7. Переместить тележку к краю вала.
8. Замкнуть витки соленоида.
9. Нанести равномерно по всей длине оси сухой магнитный порошок.
10. Включить намагничивание и перемещение соленоида.
11. Осмотреть поверхность оси с двух сторон от соленоида в пределах зоны достаточной намагниченности.
12. Остановить соленоид у другого края вала, выключить намагничивание, осмотреть поверхность вала. Включить соленоид и переместить его к середине средней части вала, выключить намагничивание.
13. Отметить мелом границы проконтролированного участка вала.
14. Проверить вала на 1/5 полного оборота (72±5)0, переместить соленоид одному из краёв вала и повторить контроль по п.п. 9−13.
15. Провести контроль всей поверхности вала по п. 14 не менее чем за пять проходов.
16. Внести запись о результатах контроля в «Журнал учета результатов контроля».
5. Методика расчета устройства для намагничивания вала редуктора ТРКП пассажирского вагона Схема намагничивающего устройства приведена на рисунках 5.1 и 5.2. Определим величину намагничивающей силы Iw устройства для создания в изделии необходимой индукции.
Рисунок 5.1 — Эквивалентная электрическая схема НУ Рисунок 5.2 — Расчетная схема намагничивающего устройства Величину намагничивающей силы можно определить исходя из закона Кирхгофа
(1)
где I — ток в обмотке электромагнита; w — число витков в обмотке;
Hili — падение магнитного напряжения на участке магнитной цепи li.
Строим кривую намагничивания материала магнитопровода (Сталь 40) и кривую намагничивания материала вала редуктора (Сталь 20) рисунок 5.3, используя данные таблицы 2.3.
Рисунок 5.3 — Кривая намагничивания материала магнитопровода и материала вала редуктора Сумму падений магнитных напряжений в изделии Uи, зазорах Uy, в магнитопроводе Uп находим из выражений:
(2)
Используя выражения (2) по значениям Hи и Bи, взятым с кривой намагничивания, строим зависимость Uи = f (Фи).
Падение магнитного напряжения в изделии Uи и магнитный поток Фи в изделии при Ни = 4000 А/м, Ви = 1,270 Тл будут равны:
В,
Вб.
Затем строим зависимость Uу = f (Фи) в той же системе координат (рисунок 5.4) по формуле
(3)
где H0 — напряженность поля в зазоре между полюсами магнита и замыкающим магнитопроводом; * - толщина суммарного зазора, *=2(R+); R — шероховатость; - толщина неферромагнитного покрытия.
Падение магнитного напряжения в зазорах Uу при Ни = 4000 А/м, Ви = 1,270 Тл будет равно
В.
Падения магнитного напряжения в изделии Uи и магнитного напряжения в зазорах Uу, а также магнитного потока Фи в изделии при других значениях Ни и Ви сведем в таблицу 5.1.
Таблица 5.1 — Значения магнитных напряжений Uи, Uу и магнитного потока Фи в изделии
Фи, Вб | Uи, В | Uy, В | |
0,3 125 | 147,5 | 82,5 | |
0,609 375 | 160,8 | ||
0,775 | 442,5 | 204,6 | |
0,8 625 | 227,7 | ||
0,89 375 | 737,5 | 235,9 | |
0,946 875 | 249,9 | ||
0,990 625 | 261,5 | ||
0,101 875 | 268,9 | ||
Рисунок 5.4 — Зависимости магнитных напряжений в зазоре Uy (1) и в изделии Uи (2) от магнитного потока Фи изделии Затем на отдельном графике рисунок 5.5 строим кривую падения магнитного напряжения Uп в магнитопроводе в зависимости от потока в нем Uп = f (Фп)
(4)
Значения В и Н определим по кривой намагничивания материала магнитопровода рисунок 5.3, используя данные таблицы 2.3.
В; Вб Значения магнитного напряжения Uп и магнитного потока Фп в магнитопроводе при других значениях Ни и Ви представим в виде таблицы 5.2.
Таблица 5.2 — Значения магнитного Uп и магнитного потока Фп в магнитопроводе
Uп, В | Фп, Вб | |
0,375 | ||
0,10 125 | ||
0,13 375 | ||
0,1 525 | ||
0,165 | ||
0,174 375 | ||
0,184 375 | ||
0,195 | ||
Рисунок 5.5 — Зависимости магнитного напряжения в магнитопроводе от магнитного потока в нем Чтобы пересчитать Uп в зависимости от Фи, запишем уравнение Кирхгофа для точки М в эквивалентной электрической схеме, рисунок 5.1:
(5)
где F — магнитный поток рассеяния, шунтирующий изделие и переходный участок.
Так как отношение потоков Фи и F обратно пропорционально магнитным сопротивлениям Rи+Ry и RF, то справедливо выражение
откуда следует
(6)
где RF — магнитное сопротивление потока рассеяния между полюсами электромагнита, .
(7)
где GF — проводимость участка между параллельными призмами (полюсами намагничивающего устройства).
(8)
;
.
Определим проводимость участка между параллельными призмами (полюсами намагничивающего устройства)
м;
;
;
Гн.
Рассчитаем магнитное сопротивление потока рассеяния между полюсами электромагнита Из выражений (5) и (6) следует
(9)
где RF — получаем из соотношений (7) и (9), оно постоянно;
— тоже постоянно;
где lи — длина средней линии в изделии, lи = L+d, lи =0,3 м; Ви, Ни — соответствуют оптимальному режиму намагничивания.
По значению коэрцитивной силы для стали 20 Hс=320А/м материала изделия по Приложению Д находим значение оптимальной напряженности магнитного поля Нопт.
Далее по кривой намагничивания материала изделия (рисунок 5.3) определяем оптимальное значение магнитной индукции Вопт. В результате получили: Вопт = 1,27 Тл, Нопт = 3000 А/м.
Гн-1
Гн-1
Путем пересчета с использованием формулы (9) из последнего графика, (см. рисунок 5.5), получаем зависимость Uп = f (Фи), рисунок 5.6.
Вб.
Остальные значения Фи* в пересчете представим в виде таблицы 5.3.
Таблица 5.3 — Данные для построения зависимости Uп = f (Фи*)
Uп, В | Фи*, Вб | |
0,34 841 | ||
0,9 407 | ||
0,124 265 | ||
0,141 686 | ||
0,153 299 | ||
0,162 009 | ||
0,1 713 | ||
0,181 172 | ||
0,193 366 | ||
0,200 915 | ||
0,207 883 | ||
0,211 367 | ||
0,220 658 | ||
0,225 304 | ||
0,23 111 | ||
Рисунок 5.6 — Зависимость магнитного напряжения в магнітопроводе от магнитного потока в изделии Затем, суммируя Uи, Uy, Uп (таблица 7.6), получаем зависимость U = f (Фи), рисунок 7.8.
Таблица 5.4 — Данные для построения зависимости U = f (Фи)
Uи, В | Uy, В | Uп, В | UУ, В | |
147,5 | 82,5 | 440,0 | ||
160,8 | 875,8 | |||
442,5 | 204,6 | 1277,1 | ||
227,7 | 1657,7 | |||
737,5 | 235,9 | 2023,4 | ||
249,9 | 2394,9 | |||
261,5 | 3121,5 | |||
268,9 | 3843,9 | |||
2212,5 | 284,6 | 5647,1 | ||
293,6 | 7443,6 | |||
3687,5 | 301,9 | 9239,4 | ||
306,8 | 11 031,8 | |||
320,0 | 14 620,0 | |||
323,3 | 18 198,3 | |||
336,5 | 21 786,5 | |||
Рисунок 5.7 — Зависимость суммарного магнитного напряжения от магнитного потока в изделии Затем строим аналогичную зависимость U = f (Ви), (рисунок 7.9.), где
Ви = =Ф*и/Sи
Тл Таблица 5.5 — Данные для построения зависимости U = f (Ви)
Ви, Тл | UУ, В | |
0,557 | 440,0 | |
1,505 | 875,8 | |
1,988 | 1277,1 | |
2,267 | 1657,7 | |
2,453 | 2023,4 | |
2,592 | 2394,9 | |
2,741 | 3121,5 | |
2,899 | 3843,9 | |
Рисунок 5.8 — Зависимость суммарного магнитного напряжения в магнитопроводе от индукции в изделии По значению оптимальной индукции Вопт=1,27 в контролируемом сечении, найденному по кривой намагничивания материала изделия, определяем U1 = 1120 В, рисунок 5.8.
С учетом коэффициента заполнения Кз = 0,4 и площади S окна, занимаемого всеми витками катушки в сечении, перпендикулярном осям витков (S? 80% площади окна Ss, образованного П-образным сердечником и намагничиваемым изделием, Ss = L (h — d + д)=0,22• (0,1 — 0,05 + 0,207)=0,011 м2), находим число витков w1 обмоточного провода, задаваясь различными его диаметрами (d = 0,5…3,5 мм)
(10)
Число витков w1 обмоточного провода диаметром d =0,5 равно
.
По известным намагничивающей силе U1 и числу витков w1 определяем величину тока в катушке
(11)
тогда получим
A.
Расчет выполняется для случая контроля плоских изделий и не учитывает растекание магнитного потока в изделии. Должно также выполняться ограничение по плотности тока: j 12 А/мм2 (см. таблицу 7.8).
Определим электрическое сопротивление обмотки R и потребляемую мощность P
(12)
(13)
где lср — средняя длина витка провода в катушке,
lср = 2(c + d);
lср = 2•(0,025 + 0,05)=0,15 м;
— удельное электрическое сопротивление.
Ом;
Вт.
Остальные значения, ,, запишем в таблицу 7.8.
Таблица 5.6 — Значения, ,, при различных диаметрах обмоточного провода
d, м | w1 | I1, А | j, А/мм2 | R, Ом | P, Вт | |
0,001 | 5628,3231 | 0,710 691 259 | 0,625 | 18,3 | 9,234 | |
0,0015 | 2501,4769 | 1,599 055 333 | 0,625 | 3,61 | 9,234 | |
0,002 | 1407,0808 | 2,842 765 036 | 0,625 | 1,14 | 9,234 | |
0,0025 | 900,53 169 | 4,441 820 369 | 0,625 | 0,47 | 9,234 | |
0,003 | 625,36 923 | 6,396 221 332 | 0,625 | 0,23 | 9,234 | |
0,0035 | 459,45 494 | 8,705 967 923 | 0,625 | 18,3 | 9,234 | |
0,001 | 5628,3231 | 0,710 691 259 | 0,625 | 3,61 | 9,234 | |
Поскольку потребляемые мощности одинаковы P=9,234 Вт, то диаметр провода выбираем, исходя из приемлемого числа витков катушки.
Принимаем d = 2 мм с числом витков w1=1407.
Для расчета габаритных размеров катушки рассчитаем количество витков в одном слое (без учета толщины изоляции провода):
(14)
где d — диаметр провода,
L — расстояние между полюсами электромагнита.
;
Тогда количество слоев в катушке (без учета изоляции):
(15)
Высоту катушки рассчитаем как произведение количества слоев на диаметр провода:
(16)
;
Т.к. рассчетная высота катушкиd, то размер катушки удовлетворяет размерам сердечника магнитопровода.
6. Описание мероприятий по охране труда и противопожарной безопасности Требования к персоналу. Руководитель подразделения НК должен быть сертифицирован на уровень квалификации не ниже второго по СТБ ЕН 473−2005 хотя бы по одному из применяемых методов НК и должен повышать свою квалификацию не реже одного раза в 5 лет.
1 Дефектоскописты должны пройти профессиональную подготовку и сдать квалификационный экзамен на присвоение профессии и квалификационного разряда в соответствии с установленными требованиями.
2 Квалификационный экзамен на присвоение профессии и квалификационного разряда проводится в соответствии с положением о непрерывном профессиональном обучении рабочих (служащих), утвержденным постановлением Совета Министров РБ от 15 мая 2007 г. № 599, и положением о непрерывном профессиональном обучении кадров железнодорожного транспорта, утвержденным и введенном в действие на БелЖД приказом от 10 декабря 2003 г. № 277Н.
3 Дефектоскописты должны повышать свою квалификацию не реже одного раза в 2 года, а также после перерыва в практической работе более 6 месяцев.
Требования к рабочему месту
1 Рабочее место (участок) для проведения НК должно быть организовано непосредственно на участке предприятия, на котором в соответствии с установ-ленным технологическим процессом проводятся ремонтные работы.
2 Расположение рабочего места должно быть согласовано с имеющимися в цехе элементами управления подъемно-транспортными механизмами или транспортирующим конвейером.
3 Рабочее место должно быть обеспечено средствами НК в соответствии с требованиями технологических документов.
4 Для обеспечения электрического питания дефектоскопов, вспомогатель-ных приборов и оборудования к рабочим местам должна быть подведена трехфазная сеть переменного тока напряжением 380/220 В (50 Гц) и сеть переменного тока напряжением 42 или 12 В, а также заземляющая шина.
5 На рабочем месте должны быть предусмотрены:
— подъемно-транспортные механизмы, обеспечивающие перемещение и установку на позицию контроля крупногабаритных деталей;
— стенды для размещения деталей, дефектоскопов и вспомогательных при-боров;
— стенды-кантователи для закрепления и поворота крупногабаритных деталей (боковых рам, надрессорных и соединительных балок, рам тележек грузо-вых вагонов и др.);
— площадки, стеллажи и контейнеры для размещения подготовленных к про-ведению контроля и проконтролированных деталей (годных, подлежащих ремонту или забракованных), снабженные соответствующими надписями;
— металлические шкафы для хранения переносных дефектоскопов, вспомо-гательных приборов, инструмента и оборудования;
— емкости для дефектоскопических материалов;
— металлические ящики для хранения обтирочного материала;
— столы для ведения записей в журналах учета результатов контроля.
6 На рабочем месте должны находиться:
— операционные или технологические карты НК;
— журналы учета результатов контроля;
— средства для очистки деталей (щетка металлическая, щетка волосяная, об-тирочный материал);
— шкурка шлифовальная водостойкая;
— измерительные инструменты (линейка длиной не менее 250 мм по ГОСТ 427 и т. п.);
— лупа по ГОСТ 25 706 с кратностью увеличения не менее четырех;
— переносный светильник;
— средства маркировки (мелки или краска);
— молоток слесарный по ГОСТ 2310 массой 200 г;
— ручная пневматическая шлифовальная машина по ГОСТ 12 633 или элек-трическая шлифовальная машина по ГОСТ 10 084.
7 Температура окружающего воздуха на рабочем месте НК должна обеспечиваться в пределах от плюс 5 до плюс 40 °C.
8 На рабочем месте НК следует применять комбинированное освещение (общее и местное). Освещенность рабочего места должна быть не менее 500 лк. При магнитопорошковом контроле освещенность контролируемой поверхности при осмотре деталей должна быть не менее 1000 лк.
Применяемые для местного освещения переносные светильники должны иметь непрозрачный отражатель, обеспечивающий рассеяние света, и экран, защищающий глаза дефектоскописта от слепящего воздействия света.
Экраны, цифровые индикаторы, дисплеи средств НК должны быть защищены от прямого попадания света.
Требования безопасности
1 Все виды работ по НК должны проводиться с соблюдением действующих на предприятии правил по охране труда и пожарной безопасности.
2 К проведению НК допускаются дефектоскописты, прошедшие обучение и инструктаж по безопасности труда в соответствии с требованиями ГОСТ 12.0.004.
3 Конструкция дефектоскопов и технологического оборудования должна соответствовать общим требованиям безопасности по ГОСТ 12.2.003 и общим эргономическим требованиям по ГОСТ 12.2.049.
4 Оборудование рабочих мест дефектоскопами, вспомогательными уст-ройствами и механизмами и их обслуживание должны осуществляться в соот-ветствии с требованиями ГОСТ 12.2.007.0, ГОСТ 12.1.019, «Правилами устройства электроустановок потребителей», утвержденными Госэнергонадзором 01.06.85 и межотраслевыми правилами по охране труда при работе в электроустановках, утвержденными постановлением Министерства труда и Социальной защиты РБ и Минэнерго РБ 30 декабря 2008 г. № 205/59.
5 Стационарные и передвижные дефектоскопы и установки должны быть заземлены или занулены в соответствии с требованиями ГОСТ 12.1.030. У ста-ционарных дефектоскопов и установок для магнитопорошкового контроля должны быть предусмотрены резиновые коврики или деревянные напольные решетки.
6 Переносные электрические светильники должны иметь напряжение питания не более 42 В.
7 Размещение, хранение, транспортирование и использование вспомога-тельных материалов и отходов производства должны проводиться с соблюдением требований защиты от пожаров по ГОСТ 12.1.004.
8 На каждом рабочем месте должны находиться инструкции по охране труда и пожарной безопасности, утвержденные в установленном порядке.
9 Рабочие места, на которых контролируются детали, перемещение которых вручную не допускается по санитарным нормам, должны быть оборудованы подъемно-транспортными механизмами и (или) стендами-кантователями по ГОСТ 12.3.020. Стенды-кантователи перед началом работы необходимо осматривать. При этом необходимо проверять надежность зажимов и предохранительных устройств.
10 Подъемно-транспортные механизмы должны удовлетворять требованиям «Правил устройства и безопасной эксплуатации грузоподъемных кранов» МЧС РБ от 3 декабря 2004 г. № 45.
11 Уровень шума на рабочих местах не должен превышать нормы, уста-новленные ГОСТ 12.1.003 для производственных помещений и СанПиН 2.2.4/2.1.8.10−32.2002 г. «Шум на рабочих местах, в помещениях жилых, общественных зданий и на территории жилой застройки», утвержденным постановлением Главного государственного санитарного врача РБ от 31 декабря 2008 г. № 158.
12 Требования к допустимому содержанию вредных веществ в воздухе рабочей зоны, к температуре, относительной влажности и скорости движения воздуха в рабочей зоне участков НК — по ГОСТ 12.1.005.
13 Требования к защите от воздействия постоянных магнитных полей должны соответствовать предельно допустимым уровням воздействия посто-янных магнитных полей при работе с магнитными устройствами и магнитными материалами по СанПиН 9−85 РБ 98 «Постоянное магнитное поле. Предельно допустимые уровни на рабочих местах».
14 Требования к защите от воздействия магнитных полей промышленной частоты должны соответствовать санитарным нормам и правилам «Переменные магнитные поля промышленной частоты (50 Гц) в производственных условиях» СанПиН 2.2.4.11−25−2003 «Переменные магнитные поля промышленной частоты 50 Гц в производственных условиях».
15 Требования к защите от ультрафиолетового излучения должны соот-ветствовать гигиеническим требованиям к конструированию и эксплуатации установок с искусственными источниками УФ-излучения для люминесцентного контроля качества промышленных изделий по СанПиН 2.2.4.13−45−2005 «Санитарные нормы ультрафиолетового излучения производственных источников».
16 Для защиты кожи рук от дефектоскопических и вспомогательных материалов должны применяться перчатки резиновые технические по ГОСТ 50 435–92 или дерматологические средства индивидуальной защиты (защитные мази и пасты) в соответствии с ГОСТ 12.4.068−79.
17 Отходы производства в виде отработанных дефектоскопических мате-риалов подлежат утилизации, регенерации, удалению в установленном порядке.
18 Ветошь должна храниться в специальных металлических ящиках с плотно закрывающимися крышками. Использованную ветошь необходимо собирать в металлический ящик с крышкой и отправлять на утилизацию.
Выводы В результате выполнения данного курсового проекта был изучен магнитопорошковый метод неразрушающего контроля, изучены особенности его проведения, способы намагничивания и др. Также были изучены требования охраны труда и пожарной безопасности. Научились составлять технологическую карту для проведения неразрушающего контроля.
Также при выполнении курсового проекта получено наглядное представление о разработке методик НК, приобретены знания необходимые в дальнейшем изучении смежных дисциплин.
Список использованных источников
1 Клюев, В. В. Неразрушающий контроль и диагностика: cправочник / В. В. Клюев, Ф. Р. Соснин, А. В. Ковалев. -Машиностроение, 1995. -64с
2 Криворудченко, В. Ф. Современные методы технической диагностики и неразрушающего контроля деталей и узлов подвижного состава железнодорожного транспорта / В. Ф. Криворудченко, Р. А. Ахмеджанов. — М.: Маршрут, 2005. — 436 с.
3 Ергучев, Л. А. Магнитные методы неразрушающего контроля деталей железнодорожного подвижного состава: пособие / Л. А. Ергучев. — Гомель: БелГУТ, 2005. — 90 с
4 Холодилов, О. В. Методы и средства неразрушающего контроля (электроискровой, магнитопорошковый, феррозондовый, вихретоковый): лабораторный практикум / О. В. Холодилов. — Гомель: БелГУТ, 2008. — 70 с.
5 Неразрушающий контроль деталей вагонов. Общие положения. РД 32.174−2001 / МПС. — М.: Транспорт, 2001. — 56 с.
6 Холодилов, О. В. Методы и средства неразрушающего контроля (магнитные методы): учебно-методическое пособие / О. В. Холодилов. — Гомель: БелГУТ, 2008. — 44 с.