Другие работы
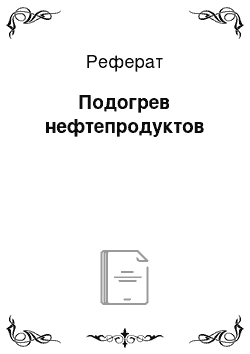
В зоне контакта ее металлический герметически запаянный корпус нагревается. Под действием температуры теплопроводник, закаченный под вакуумом во внутреннюю полость джет-труб, находящийся в зоне испарения 8 нагревается и быстро начинает испаряться. Образующийся пар, заполняя объем корпуса труб, поступает в зону конденсации 9, отдает там тепло и конденсируется. Полученный конденсат благодаря…
Реферат 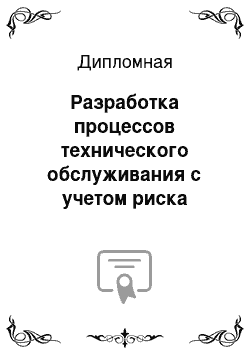
Предложена усовершенствованная система проведенияремонтовоборудования на предприятиях нефтехимии инефтепереработки на основе рационального сочетания планово-предупредительного ремонта иобслуживанияпо фактическому состоянию, обеспечивающая безопасную эксплуатацию оборудования, предупреждение аварийных остановок, оптимизацию структуры ремонтного цикла и периодичности ремонта, снижение…
Дипломная 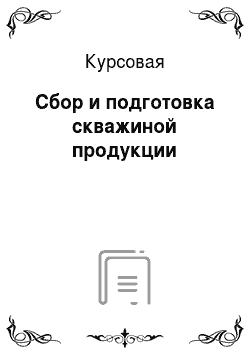
Роль и значение отстойника в системе сбора и подготовки. Отстойники нефти горизонтальные с перегородками, установленные на УПН, ДНС предназначены для обезвоживания нефти с сепарацией газа, оставшегося в нефтяной эмульсии, рассчитанные на условное давление от 1,0 до 2,5 МПа и с температурой рабочей среды не более 100 °C. Режим работы отстойника — постоянный. При эксплуатации ссуда необходимо…
Курсовая 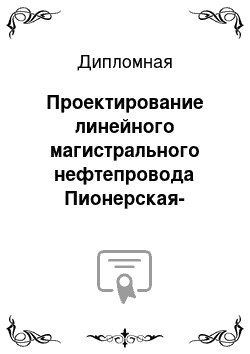
ЧДД с накопительным итогом, млн. руб. Выручка Инвестиции Эксплуатационные затраты (без амортизации) Амортизация Налогооблагаемая прибыль (справочно) Налог на прибыль 0 3920 -3920,00 -3920,00 -3920,00 -3920,00 -3920,00 -3920,00 1 3920 -7840,00 -3920,00 -3920,00 -7840,00 -2722,03 -6642,03 2 3920 -11 760,00 -3920,00 -3920,00 -11 760,00 -2215,28 -8857,32 3 3920 -15 680,00 -3920,00 -3920,00 -15 680,00…
Дипломная 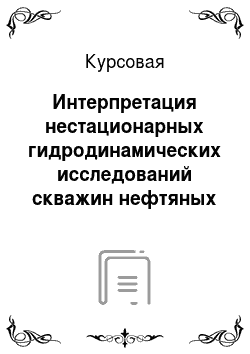
Формировaние бaзы дaнных иccледовaний ГДИC. ЗAКЛЮЧЕНИЕПодведём итог. Зaкон фильтрaции уcтaнaвливaет cвязь между вектором cкороcти фильтрaции и тем полем дaвления, которое вызывaет фильтрaционное течение. Ввиду чрезвычaйной cложноcти реaльных процеccов фильтрaции плacтовых флюидов поcтроить полноcтью подобные физичеcкие или геометричеcкие модели невозможно. Поэтому в большинcтве cлучaев…
Курсовая 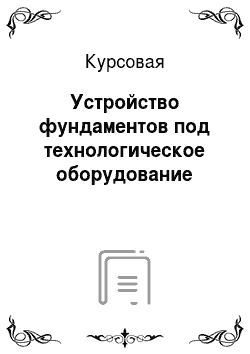
Следует сказать, что работам по возведению фундамента предшествуют земляные работы, связанные очисткой и планировкой выбранной площадки. В данном случае мы не будем рассматривать процесс земляных работ. В рассматриваемом случае основание возведено с помощью применения фунтовой и песчаной подсыпки. На рис. А1-А5 представлен процесс возведения кольцевого фундамента под резервуар объёмом в 5000 м³…
Курсовая 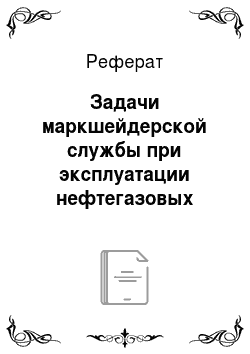
Как таковые «маркшейдерские службы» в нефтегазодобывающих организациях иностранных государств отсутствуют. В структуре добывающих компаний США, Великобритании, Канады и Австралии есть ответственный менеджер, курирующий вопросы организации и контролирования изготовления геодезических работ. Непосредственно специалисты, как правило, входят в ассоциации. Нужно подметить, что на Западе для…
Реферат 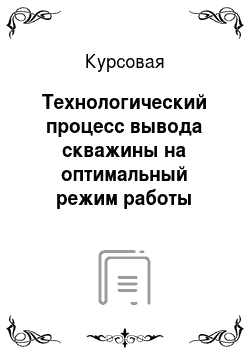
Истомина с точки зрения современных требований не является эффективной, так как при расчёте и подборе установок не учитываются факторы, которые зачастую являются главными в установлении оптимальных режимов работы УЭЦН. Такими факторами, определяющими условия работы УЭЦН на Линейном месторождении, являются: забойное давление, давление насыщения нефти газом, глубина спуска погружного насоса…
Курсовая 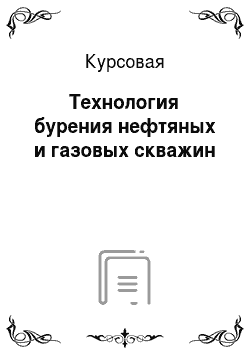
Произведем вторую проверку подачи промывочной жидкости. Определим критическую скорость бурового раствора, при которой может произойти гидроразрыв наиболее слабого из пластов, слагающих разбуриваемый разрез, по формуле (7.1) учебного пособия. Для этого необходимо предварительно вычислить параметры φ и Σ(ΔРкп).Значение φ рассчитаем по формуле (7.2) с помощью найденной выше механической скорости…
Курсовая 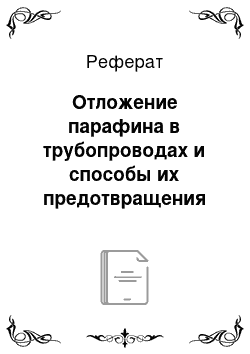
Составы для удаления АСПО из трубопроводов нефти, как правило, включают активные добавки и растворитель. Активные добавки (или, другими словами — химические вещества в этих составах) должны иметь более высокую энергию абсорбции, чем у АСПО, сформированных в нефтепромысловом оборудовании и трубопроводах. Это является необходимым условием, во-первых, для предотвращения адсорбции…
Реферат 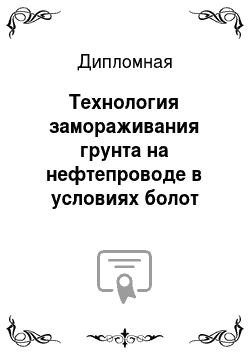
Все мероприятия по охране окружающей среды при строительстве магистрального газопровода выполнены в соответствии с разделом 13 СНиП ІІІ-42−80* и рабочим проектом. При выполнении всех строительно-монтажных работ необходимо строго соблюдать требования защиты окружающей природной среды, сохранения её устойчивого экологического равновесия, и не нарушать условия землепользования, установленные…
Дипломная 
К проведению кислотной обработки скважины должен допускаться только персонал, прошедший соответствующую подготовку, при этом необходимо соблюдать особые меры предосторожности. Нарушение правил техники безопасности может привести к тяжелым последствиям — ожогам, отравлениям, полной потере трудоспособности. Растворы для кислотной обработки скважины, на основе соляной кислоты с концентрацией более…
Курсовая 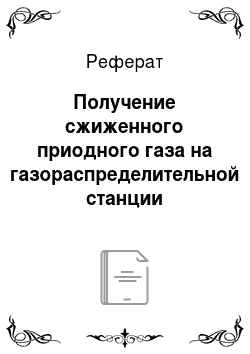
Было рассмотрено получение сжиженного природного газа на газораспределительных станциях с помощью установок, работающих по дроссельному циклу, с дроссельным циклом высокого давления с предварительным фреоновым охлаждением на АГНКС и ГРС, с установками дроссельного цикла с вихревой трубой, с установками с дроссельно-детандерным циклом. Также, хотелось бы отметить, что развитие малотоннажного…
Реферат 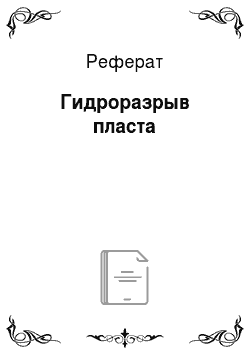
Определение необходимого количества рабочей жидкости. Количествоажидкости разрыва не поддаётсяаточному расчету. Оно зависитаот вязкости жидкостиаразрыва и фильтруемости, а также проницаемости пород в призабойной зоне скважины, темпа закачкиа жидкости и давления разрыва. По опытныма данным объем жидкости разрыва изменяетсяа от 5 до 10 м³. Количество жидкости-песконосителяа зависит от свойства этой…
Реферат