Исследование причин повышения концентрации серы в ферросиликомарганце и разработка способов ее снижения
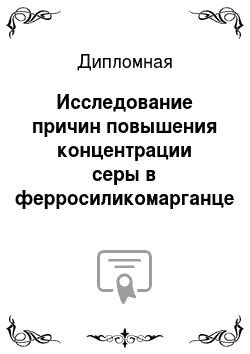
Древесный уголь, обладает высокими удельными электрическим сопротивлением и реакционной способностью, чистотой. Древесный уголь уменьшает спекание шихты, что особенно важно при выплавке высокопроцентных сплавов кремния. Древесный уголь—пористый высокоуглеродистый продукт, получаемый из древесины в результате ее нагрева без доступа или с очень ограниченным доступом воздуха в ретортах или… Читать ещё >
Исследование причин повышения концентрации серы в ферросиликомарганце и разработка способов ее снижения (реферат, курсовая, диплом, контрольная)
МІНІСТЕРСТВО ОСВІТИ І НАУКИ УКРАЇНИ
ЗАПОРІЗЬКА ДЕРЖАВНА ІНЖЕНЕРНА АКАДЕМІЯ
ФАКУЛЬТЕТ Металургійний
КАФЕДРА МЧМ
КВАЛІФІКАЦІЙНА РОБОТА МАГІСТРА
на тему: Дослідження причин підвищення концентрації сірки в феросилікомарганцю та розробка способів її зниження
Спеціальність металургія чорних металів
Виконавець Бойко М.В.
Керівник роботи доц. Сиваченко В.М.
Розглянуто на засіданні кафедри МЧМ
Рекомендовано до захисту в ДЕК
Протокол №____ від_____
Завідувач кафедрою
Воденнiков С.А.
Запоріжжя
Реферат
Магистерская работа содержит 58 стр., 17 рис., 16 табл., 36 источников.
Объект исследования — поведение серы при выплавке силикомарганца.
Цель работы заключалась в выявлении причин повышения содержания серы в силикомарганце для обоснования необходимости повышения регламентируемого предела массовой ее доли в разрабатываемых ДСТУ на марганцевые сплавы.
Методика исследований заключалась в использовании микрорентгеноструктурного и петрографического анализов опытных плавок силикомарганца, математической статистики, термодинамических методов расчета равновесий металлургических реакций.
Изучены особенности балансов серы и титана, их распределение в продукты плавки. Сера вносится преимущественно коксом 85−90% с учетом его расхода при агломерации сырья и на 95% переходит в шлак. Основная масса титана поступает с рудными материалами. Коксом вносится около 13−15%.
Выявлена структура перехода серы в силикомарганец в виде комплексного соединения сульфида марганца с карбидом титана.
На базе термодинамических расчетов и результатов исследований предложен механизм перехода серы в силикомарганец, заключающийся в одновременном восстановлении титаната марганца Mn2TiO4.
Разработаны рекомендации для понижения серы в силикомарганце.
СИЛИКОМАРГАНЕЦ, СЕРА, ТИТАН, ПЕРЕХОД В СПЛАВ, ВЗАИМОСВЯЗЬ, МЕХАНИЗМ, КАЧЕТВО, ПУТИ УЛУЧШЕНИЯ.
- Введение
- 1. Общие технологические особенности получения ферросиликомарганца в рудовосстановительных печах
- 1.1 Характеристика шихтовых материалов
- 1.1.1 Марганцевая руда и концентраты
- 1.1.2 Восстановители
- 1.1.3 Кварцит
- 1.2 Печи для производства ферросиликомарганца
- 1.3 Технология производства ферросиликомарганца
- 1.3.1 Сортамент
- 1.3.2 Технологические особенности выплавки силикомарганца
- 2. Исследование сульфидных компонентов ферросиликомарганца
- 2.1 Сера в структуре стали и ферросплавов
- 2.1.1 Влияние серы на свойства стали и методы ее снижения
- 2.1.2 Некоторые особенности сульфидов компонентов силикомарганца
- 2.2 Результаты экспериментальных исследований
- 2.3 Рентгеноструктурные исследования опытных сплавов
- 3. Разработка способа снижения концентрации серы в силикомарганце
- 3.1 Источники серы и титана при выплавке силикомарганца
- 3.2 Вероятная модель взаимодействия серы с оксидами
- Выводы
- Список использованной литературы
В многочисленных исследованиях технологии производства марганцевых ферросплавов сере не уделяется серьезного внимания. В лучшем случае можно встретить материальные балансы серы, оценки распределения ее между продуктами плавки, влияние на жидкоподвижность шлаков. Сегодня не представляется возможным на базе опубликованных результатов исследований дать однозначную характеристику соединениям серы в сплавах и механизму ее перехода в металлическую фазу при электроплавке.
Ограниченное количество текущих анализов содержания серы в марганцевых сплавах не позволяет получить состоятельных статистических оценок влияния качества используемых шихтовых материалов.
Такое отношение обусловлено тем, что концентрация серы в массовых марганцевых сплавах не превышает, как правило, 0,02 — 0,03%, независимо от ее колебаний в шихтовых материалах. Кроме того, использование указанных сплавов в качестве раскислителей в производстве стали не может существенно повлиять на содержание серы в ней. Эти изменения могут происходить в пределах десятитысячных долей процента при увеличении массовой доли серы в марганцевых сплавах от 0,01 до 0,03%, т. е. в три раза.
В производстве углетермических марганцевых ферросплавов основным источником серы является кокс из донецких углей. В общем балансе серы на долю этого материала приходится 85−90%.
Распределение серы между продуктами плавки также характеризуется преимущественным переходом в один из них, в частности по данным [20], %:
Малая доля перехода серы в сплав обусловлена следующими причинами. Марганец из всех основных компонентов сплава (железа, кремния, углерода) обладает наибольшим сродством к сере. Образующийся сульфид марганца имеет ограниченную растворимость в сплаве [2,3]. Вследствие этой особенности он ассимилируется слоем шлака (как неметаллическое включение) из капель сплава, которые при электроплавке опускаются из реакционной зоны через шлак на подину.
По петрографическим исследованиям сульфид марганца в шлаках образует самостоятельную фазу с отражательными способностями, близкими манганозиту.
По термодинамическим характеристикам марганец, входящий в оксиды, карбиды и силициды, должен взаимодействовать при технологических температурах с сульфидами других элементов, присутствующих в металле, с выделением в самостоятельную фазу сульфида марганца.
Поэтому простое увеличение массы серы в шихте не должно приводить к повышению степени перехода серы в сплав, несмотря на растворимость, хотя и ограниченную, сульфида марганца в нем. Так, при использовании углистого колчедана на выплавке углеродистого ферромарганца в промышленной печи степень перехода серы понизилась с 1,15 до 0,45% при увеличении вносимой серы шихтой с 8,8 до 47,3 кг на тонну сплава.
Повышение содержания серы в шлаке с 1,0−1,5 до 3,0−4,0% не приводит к заметному увеличению ее в ферромарганце.
На основании приведенных особенностей можно заключить, что увеличение серы в углетермических марганцевых сплавах, тем более в силикомарганце, должно быть связано с концентрацией сопутствующих элементов.
Основными сульфидообразующими примесными элементами силикомарганца являются титан 0,09−0,15%, никель 0,06−0,08%, хром 0,03−0,07%.
Естественно ожидать, что наиболее сильное влияние на содержание серы в силикомарганце будет оказывать титан. В случае образования моносульфида с 0,02−0,03% серы в силикомарганце будет связана третья часть содержащегося в сплаве титана. Остальная доля может быть представлена карбидом, поскольку титан обладает наибольшим сродством к углероду из всех перечисленных элементов силикомарганца. При полном переходе титана в сульфид содержание серы должно достигать 0,06−0,10%.
Проведенными микрорентгеноструктурными исследованиями промышленного и опытного (с повышенной серой) силикомарганца установлено, что сера в сплаве представлена комплексными соединениями с карбидом титана. Через серу на карбиде формируются сульфиды марганца.
На базе полученных результатов, термодинамического анализа взаимодействий в оксикарбидных системах и литературным данным предложен механизм перехода серы в силикомарганец.
Изучением динамики изменения качества марганцевых руд и концентратов на Марганецком и Орджоникидзевском ГОКах показана тенденция ее понижения с естественным увеличением оксидов пустой породы, в том числе и титана на единицу марганца.
На основе проведенных исследований в проектах ДСТУ на ферромарганец и ферросиликомарганец увеличен регламентируемый предел массовой доли серы до 0,03%.
1 Общие технологические особенности получения ферросиликомарганца в рудовосстановительных печах
1.1 Характеристика шихтовых материалов
1.1.1 Марганцевая руда и концентраты
Как и большинство металлов, марганец распределен по земному шару неравномерно. Некоторое количество марганцевых месторождений расположено на суше, но значительно больше марганца содержится в конкрециях Тихого океана. Мировые континентальные разведанные запасы марганцевых руд оцениваются на сегодняшний день в 17,6−18,0 млрд. тонн при их распределении по регионам планеты следующим образом, %: Африка (ЮАР, Габон, Гана) — 80,6, в т. ч. ЮАР — 77,3; Австралия — 2,4; Америка (Бразилия, Мексика) — 2,9; Украина — 12,6; прочие регионы — 1,5.
Отличительной особенностью марганцевых руд отечественных месторождений является относительно невысокое содержание марганца и повышенная концентрация фосфора и кремнезема (табл.1.1), что не позволяет, в отличие от некоторых зарубежных месторождений, использовать сырье без предварительной подготовки, называемой обогащением. Основная задача процесса обогащения заключается в максимальном отделении от основных рудных минералов так называемых хвостов или пустой породы. Все методы обогащения основаны на различных механических, физических, физико-механических и т. д. свойствах минералов руды, а выбор их для каждого конкретного случая определяется эффективностью и экономической целесообразностью.
Марганцевые руды на отечественных обогатительных фабриках перерабатываются по единой схеме (рис. 1.1), позволяющей получать готовый продукт в виде концентратов различного качества (табл.1.2).
Таблица 1.1 Усредненные химические составы марганцевых руд основных месторождений Украины и импортные руды
Руда, ГОК, карьер | Массовое содержание, % | ||||||||||||
Mn | Fe | MnO2 | MnO | SiO2 | Al2O3 | CaO | MgO | P | S | R2O | п.п.п. | ||
ОГОК, Александровский карьер | 16,9 | 2,54 | 2,88 | 19,5 | 35,4 | 4,96 | 6,86 | 2,30 | 0,147 | 0,052 | 1,61 | 19,8 | |
ОГОК, Шевченковский карьер | 25,0 | 2,74 | 33,0 | 5,29 | 36,4 | 4,86 | 2,70 | 1,92 | 0,170 | 0,044 | 2,39 | 11,3 | |
ОГОК, Северный карьер | 25,8 | 2,56 | 33,8 | 5,61 | 32,8 | 4,37 | 4,6 | 1,81 | 0,160 | 0,056 | 2,22 | 13,2 | |
ОГОК, Запорожский карьер | 24,7 | 2,95 | 33,1 | 4,90 | 35,3 | 4,78 | 2,74 | 2,26 | 0,166 | 0,055 | 2,49 | 12,0 | |
МГОК, Басановский карьер | 26,8 | 2,55 | 34,4 | 6,54 | 35,5 | 3,09 | 1,24 | 1,54 | 0,144 | 0,022 | 2,19 | 9,4 | |
МГОК, Грушевский карьер | 20,3 | 2,72 | 8,27 | 19,6 | 38,6 | 4,10 | 6,26 | 2,14 | 0,153 | 0,059 | 1,75 | 19,6 | |
Габон | 52,0 | 3,0 | н.св | н.св | 4,0 | 6,0 | 0,3 | 0,2 | 0,13 | н.св | н.св | н.св | |
Австралия | 48,0 | 5,0 | н.св | н.св | 13,3 | 1,0 | 0,7 | 0,5 | 0,05 | 0,02 | н.св | 7,2 | |
Таблица 1.2 Полный химический состав марганцевых концентратов из руд основных месторождений Украины
Наименование и сорт концентрата | ||||||||||||||
Мn | МnО2 | МnО | SiO2 | СаО | MgO | Al2O3 | Fe2O3 | Р | Na2O | К2О | BaO | П.П.П. | ||
Никопольские: | ||||||||||||||
Оксидный I сорта | 44,0 | 48,3 | 17,4 | 13,7 | 3,2 | 1,3 | 1,5 | 1,9 | 0,19 | 0,4 | 1,0 | 0,4 | 14,2 | |
Оксидный 1Б сорта | 42,0 | 46,0 | 16,7 | 15,4 | 3,3 | 1,4 | 1,7 | 2,2 | 0,19 | 0,4 | 1,2 | 0,1 | 14,5 | |
Оксидный IIсорта | 36,8 | 38,5 | 16,2 | 20,7 | 3,9 | 1,8 | 1,7 | 2,6 | 0,19 | 0,4 | 1,5 | 0,3 | 15,2 | |
Карбонатный Iсорта | 31,0 | 19,3 | 24,3 | 19,2 | 7,3 | 1,5 | 2,5 | 2,5 | 0,18 | 0,9 | 0,9 | 0,4 | 22,5 | |
Рис. 1.1 Принципиальная технологическая схема обогащения марганцевых руд: а — окисных; б — карбонатных
Способы обогащения
Существует несколько способов обогащения. Наиболее распространенными являются промывка, магнитная сепарация и флотация.
Промывка является наиболее простым и дешевым способом обогащения. Промывке подвергают главным образом такие руды, которые содержат твердый неразмываемый полезный минерал, а пустая порода состоит из песка или глины. Способ основан на принципе, когда водой уносится часть пустой породы, которая легче по весу, чем железорудный (марганцевый) минерал.
Магнитная сепарация заключается в том, что руду, обладающую магнитными свойствами, пропускают через магнитное поле, в результате чего магнитные окислы железа отделяются от немагнитной пустой породы. Для эффективного обогащения магнитным способом требуется тонкое измельчение руд.
Флотация является сравнительно новым методом обогащения. Методом флотации обычно обогащают кварциты, которые содержат железо в виде Fe2O3. Этот способ основан на принципе различной смачиваемости окислов железа и пустой породы.
Способы окускования
Известны три метода окускования металлургического сырья: брикетирование, агломерация и окатывание.
Первый из них не получил распространения из-за низкой производительности и недостаточной прочности брикетов.
Агломерация и окатывание широко применяются в нашей стране и за рубежом.
Агломерацией называется процесс окускования мелкозернистых руд и концентратов путем спекания их при сжигании топлива в слое рудного материала при помощи просасываемого воздуха.
Агломерацию применяют также для удаления серы из руды. В этом случае даже кусковую руду подвергают вначале мелкому дроблению, а затем агломерации.
Окускование при агломерации происходит и результате спекания мелких рудных частиц и извести под действием тепла, которое образуется при горении топлива. При спекании сернистых руд значительная часть тепла получается от горения серы.
Горение топлива и серы происходит благодаря воздуху, просасываемому через слой шихтовых материалов сверху вниз.
Готовый агломерат дробится посредством одновалковой дробилки и поступает на стационарные или вибрационные грохоты, на которых отсеивается мелочь, непригодная для доменной плавки, так называемый возврат.
По химическому, гранулометрическому составам и физическим свойствам продукция должна соответствовать нормам, указанным в таблице 1.3 [9,10].
Таблица 1.3 Технические требования к марганцевым концентратам
Вид и тип продукции | Под; вид (сорт) | Гранулометрический состав | Химический состав, физические свойства | |||||
наименование типа продукции | класс крупности, мм | контрольный класс крупности, мм | массовая доля контрольного класса крупности,%, не более | массовая доля марганца, %, не менее | массовая доля влаги, %, не более | |||
Концентрат марганцевый оксидный (О) | I | неклассифи-цированный | 0−60 | +60 | 42,0 | 16,0 | ||
IБ | неклассифицированный | 0−60 | +60 | 41,0 | 16,0 | |||
II | неклассифицированный | 0−60 | +60 | 34,0 | 22,0 | |||
III | неклассифицированный | 0−60 | +60 | 25,0 | 23,0 | |||
Концентрат марганцевый оксидно-карбонатный (ОК) | I | поклассифи-цированный | 0−100 | + 100 | 26,0 | 18,0 | ||
0−50 | + 50 | |||||||
II | неклассифи-цированный | 0−100 | + 100 | 23,0 | 20,0 | |||
0−50 | + 50 | |||||||
I | крупно-кусковый | 10−150 | — 10 | 26,0 | 12,0 | |||
I | мелко-кусковый | 0−10 | + 10 | 26,0 | 18,0 | |||
Концентрат марганцевый высоко-интенсивной магнитной сепарации (ВМС) | ; | крупнозернистый | 0 — 1 | + 1 | ; | 26,0 | 23,0 | |
1.1.2 Восстановители
Правильный выбор восстановителя и соответствующая его подготовка в значительной степени определяют технико-экономические показатели производства. По химическим свойствам в качестве восстановителей оксидов руды при выплавке ферросплавов можно применять многие элементы. Однако экономически выгодно применять углерод, кремний и алюминий. Наиболее широко используют углерод, а если необходимо предотвратить науглероживание выплавляемого сплава, то применяют более дорогие кремний и алюминий.
В качестве углеродсодержащего восстановителя могут быть использованы различные материалы: древесный, бурый и каменный уголь, нефтяной, пековый или каменноугольный кокс, различные полукоксы, древесные отходы и др.
Углеродистые восстановители, применяемые при выплавке ферросплавов, должны обладать хорошей, реакционной способностью, высоким удельным электрическим сопротивлением, соответствующим для каждого сплава химическим составом золы, достаточной прочностью, оптимальным размером куска, хорошей газопроницаемостью и термоустойчивостью, невысокой стоимостью.
Почти все углеродистые материалы при нагревании до высоких температур (1800—2300 К) выравнивают свою химическую активность, приближаясь к так называемому графитовому пределу, однако в процессе плавки различные углеродистые материалы проявляют свои специфические свойства и присущую им реакционную способность, так как скорости графитизации для различных материалов различны и проходят в печи эти процессы до разной степени полноты.
На реакционную способность кокса определенное влияние оказывают минеральные включения, содержащиеся в золе угля, а также искусственно внесенные. Так, отмечено повышение реакционной способности при внесении в угольную шихту для изготовления кокса или в готовый кокс солей щелочных металлов, железной руды и др.
В реальных условиях ферросплавного процесса (высокие температуры, низкий столб шихты в ферросплавной печи, неизбежный процесс образования карбидов металлов и газообразных низших оксидов металлов и т. д.) наиболее правильной характеристикой является восстановительная способность углеродистого материала с учетом его электрического сопротивления и других параметров.
С этой точки зрения наиболее оптимальным углеродистым восстановителем является древесный уголь (табл.1.4). В последние годы, в связи с постоянно растущим дефицитом, все большее распространение получают такие углеродистые восстановители как газовый уголь, нефтяной кокс и полукокс [12,13].
Таблица 1.4 Характеристика углеродистых восстановителей
Показатель | Металлургический кокс | Кокcик | Полукокс | Нефтяной кокс | Древесный уголь | |
Содержание по техническому анализу, %: | ||||||
Зола Аd | 10,65 | 10,80 | 27,00 | 0,71 | 1,45 | |
Летучие Vdaf | 1,44 | 1,20 | 5,60 | 8,08 | 14,54 | |
Влага Wp | 0,44 | 1,30 | 1,90 | 0,80 | 2,10 | |
Сера SdI | 0,89 | 1,34 | 0,91 | 0,58 | 0,04 | |
Твердый углерод CT | 87,02 | 86,66 | 71,49 | 86,98 | 83,97 | |
Реакционная способность при 1323 К, мл/(г•с) | 0,69 | 0,92 | 8,00 | 0,42 | 11,1 | |
уд, Ом•м (фракция 3−6 мм) | 1,21 | 1,48 | 3•I06 | 2•106 | ||
Структурная прочность,% | 83,0 | 85,0 | 63,7 | 64,3 | 39,0 | |
Плотность, г/см3: | ||||||
истинная | 1,82 | 1,95 | 1,58 | 1,41 | 1,40 | |
кажущаяся | 0,91 | 0,93 | 0,93 | 1,12 | 0,40 | |
Пористость, % (см3/г) | 53,1 (0,49) | 49,7 (0,51) | 55,0 (0,67) | 20,1 (0,18) | 63,8 (1,1) | |
Состав золы, %: | ||||||
SiO2 | 35,4 | 36,5 | 75,7 | 46,3 | 1,90 | |
Al2O3 | 23,3 | 22,2 | 11,2 | 24,3 | 3,40 | |
CaO+MgO | 3,8 | 3,9 | 3,0 | 10,5 | 41,1 | |
Fe2O3, | 33,8 | 33,7 | 7,6 | 14,2 | 0,85 | |
Р2О5 | 0,24 | 0,24 | 0,03 | 0,75 | 5,12 | |
К2О + Na2O | 2,13 | 2,64 | 1,18 | 0,13 | 0,29 | |
Древесный уголь, обладает высокими удельными электрическим сопротивлением и реакционной способностью, чистотой. Древесный уголь уменьшает спекание шихты, что особенно важно при выплавке высокопроцентных сплавов кремния. Древесный уголь—пористый высокоуглеродистый продукт, получаемый из древесины в результате ее нагрева без доступа или с очень ограниченным доступом воздуха в ретортах или углевыжигательных печах различных систем. Состав древесного угля зависит от конечной температуры переугливания и от вида использованной древесины. Древесный уголь имеет достаточную прочность и малую истираемость, лучшим является уголь из твердых пород дерева. Высокая пористость древесного угля обеспечивает его высокую реакционную способность.
В качестве восстановителя также используются торфяные брикеты и торфяной кокс, характеризующиеся высокой реакционной способностьюпористостью, чистотой и низкой электрической проводимостью.
Наиболее широко используют при выплавке ферросплавов наиболее дешевый сорт восстановителя — " орешек" металлургического кокса («коксик»), получающийся как отсев при сортировке доменного кокса. В зависимости от качества использованного для производства угля и условий получения кокса на коксохимическом заводе свойства коксика различны, но общим его недостатком являются невысокие электрическое сопротивление и реакционная способность, относительно большое содержание золы, серы и фосфора и высокое, нестабильное содержание влаги. Коксик имеет губчатую структуру с большим количеством трещин, пористость его колеблется в пределах 35—55%. Кажущаяся плотность кокса составляет 800—1000 кг/м3. Теплоемкость кокса возрастает с повышением конечной температуры коксования и уменьшается с увеличением зольности кокса, колеблясь в интервале 1,38—1,53 кДж/(кг•К).
В зависимости от сырьевой базы, кокс условно разделен на марки: К1 — кокс из углей Донбасса или в смеси с углями других бассейнов, отсеянных от доменного кокса; К2 — кокс из углей Донбасса или в смеси с углями других бассейнов, отсеянный от литейного кокса; К3 — кокс из смеси углей Кавказа и Донбасса, отсеянный от доменного кокса.
Качественные показатели орешка коксового, используемого для производства сплавов, должны отвечать требованиям ТУУ 322−190 443−120−97 для марок K01, K02, К03 (табл.1.5).
Таблица 1.5 Качественные показатели орешка коксового, % (ТУУ 322−190 443−120−97)
Наименование показателей | Норма для класса и марки | ||||
10−25 мм | 8−25 мм | ||||
К01 | К02 | К03 | К04 | ||
Зольность А, не более | 11,0 | 13,0 | 15,0 | 16,0 | |
Массовая доля общей влаги, не более | 20,0 | 20,0 | 20,0 | 22,0 | |
Массовая доля кусков размером, не более | |||||
более 25 мм | 10,0 | 10,0 | 10,0 | 10,0 | |
менее 10 мм | 9,0 | 12,0 | 15,0 | ; | |
менее 8 мм | ; | ; | ; | 13,0 | |
Качественные показатели кокса доменного фракции 25−40 мм должны соответствовать требованиям ТУУ 322−190 443−085−96 «Кокс каменноугольный класса крупности 25 мм и более» (табл.1.6).
Таблица 1.6 Качественные показатели каменноугольного доменного кокса класса крупности 25 мм и более, % (ТУУ 322−190 443−085−96)
Наименование показателя | Норма для марки | ||
КК1 | КК2 | ||
Зольность А, не более | 13,0 | 15,0 | |
Массовая доля общей серы, не более | 2,0 | 2,2 | |
Массовая доля общей влаги | 8,0 | 8,0 | |
Показатель прочности | |||
М25, не более | 80,0 | 76,0 | |
М10, не более | 9,0 | 10,0 | |
Массовая доля кусков размером менее 25 мм, не более | 7,0 | 9,0 | |
В ферросплавном производстве могут быть также использованы отсевы металлургического кокса фракции более 10 мм (табл.1.7) и коксовая мелочь (табл.1.8) [15,16].
Таблица 1.7 Отсевы металлургического кокса фракции более 10 мм (ТУУ 322−190 443−048−97)
Показатели | Норма | |||
Размер кусков, мм | 10−35 | |||
Массовая доля кусков размером менее 10 мм, %, не более | ||||
Массовая доля кусков размером более 25 мм, %, не более | ||||
Зольность А, %, не более | ||||
Массовая доля общей влаги, %, средняя | ||||
Наименование показателя | Норма для марки | |||
МК1 | МК2 | МК3 | ||
Зольность, Ас, % не более | 13,0 | 16,0 | 18,0 | |
Массовая доля общей влаги, % не более | 22,0 | 22,0 | 24,0 | |
Массовая доля кусков размером, % не более | 9,0 | 8,0 | 6,0 | |
Размер кусков, мм | 0−10, 0−8 | 0−10, 0−8 | 0−8 | |
1.1.3 Кварцит
Известно более двухсот разновидностей природного кремнезема: песок, кварц, кварцит, горный хрусталь, опал и многие другие. Для выплавки кремния и его сплавов используют наиболее дешевые и в то же время богатые кремнеземом материалы: кварцит, кварц и кварцевый песчаник. Главным минералом кварцитов и большей части песчаников является кварц — широко распространенный минерал, представляющий собой более или менее чистый кремнезем SiO2.
Кварцитами называют кремнистые песчаники, в которых цементируемое вещество и цемент представлены минералами кремнезема. Кварциты обычно характеризуются высокой плотностью и значительным сопротивлением сжатию (100—140 МПа), имеют светлую окраску с различными оттенками серого, желтого, розового и других тонов. С увеличением содержания SiO2 в кварците увеличивается извлечение кремния и производительность печи и снижается удельный расход электроэнергии.
Коренные заложи кварцита встречаются в виде пластов, гнезд или линз, состоящих из несцементированных кристаллов различной крупности.
Перед выплавкой кремния кварциты дробят, и часть примесей удаляется с мелочью. Дробление необходимо совмещать с промывкой для удаления глинистых примазок, пылевидных наносов и хрупких включений. Кварциты должны обладать высокой термостойкостью, при нагревании мало растрескиваться, иметь небольшую кажущуюся пористость (<2%), низкое водопоглощение (0,1—0,5%). Температура начала интенсивного разрушения должна быть как можно выше.
Кварциты должны соответствовать требованиям ТУУ 1 911 879−011−97.
Стандарт предусматривает две марки кварцита — КФ и КШ. Кварцит КФ используется в основном для производства ферросплавов (ферросилиция, силикокальция, кристаллического кремния, силикомарганца, ферросиликохрома и др.). Кварцит КШ предназначен в первую очередь для получения шлака определенного состава.
В некоторых случаях требования потребителей и заводов-изготовителей могут изменяться. Ниже приведен химический состав кварцита по отраслевому стандарту (ОСТ 14−49—80), действующему с 01.01.81, а в табл. 1.9 — химический состав кварцита различных месторождений.
Таблица 1.9 Химический состав кварцита различных месторождений
Месторождение | Массовое содержание, % | |||||
SiO2 | Fe2O3 | А12О3 | СаО | MgO | ||
Васильковское | 97—98 | 0,2—0,4 | 0,9—1,3 | 0,2—0,4 | 0,1—0,3 | |
Толкачевское | 96—98 | 0,4—0,9 | 0,2—1,0 | 0,7—0,3 | 0,1—0,3 | |
Овручское | 97—98 | 0,5—1,0 | 0,4—1,2 | 0,2—1,0 | 0,2—0,4 | |
1.2 Печи для производства ферросиликомарганца
Силикомарганец представляет собой комплексный раскислитель, широко используемый при выплавке стали в кислородных конвертерах, электрических
и мартеновских печах. Повышение качества стали, достигаемое при использовании силикомарганца взамен ферросилиция и ферромарганца, обусловливает и высокие темпы наращивания объема производства силикомарганца [18, 6].
Силикомарганец выплавляют в ферросплавных печах следующих типов: рудовосстановительных круглых закрытых [РКЗ], открытых [РКО] и прямоугольных закрытых [РПЗ]. Установленная мощность круглых открытых и закрытых печей достигает 16,5 Мва, а прямоугольных — 48—63 Мва. Печи оборудованы непрерывными самообжигающимися электродами. В круглых трехфазных печах три электрода диаметром 1000— 1200 мм расположены по вершинам равностороннего треугольника. В прямоугольных печах шесть плоских электродов размером 2800×650 мм каждый расположены в линию. Каждые два электрода питаются от однофазного трансформатора, образуя в целом трехфазный электрометаллургический печной агрегат. Закрытые печи снабжены газоочистной системой, что позволяет получать высококалорийный колошниковый газ высокой чистоты.
Печь типа РКО. Ванна имеет следующие размеры: диаметр кожуха — 6400 мм, высота кожуха — 3650 мм, диаметр ванны зафутерованной печи [рабочего пространства]— 4900 мм, глубина ванны — 1950 мм. Ванна печи футерована угольными блоками 400×400×1200 мм. Диаметр электродов — 940 мм, диаметр распада электродов — 2450 мм. Подача шихты в печь механизирована. Печи оборудованы трансформаторами типа ЭТЦП-17 000/35 с 8 ступенями напряжения [139—176 В]. Рабочее напряжение 148 В. Короткая сеть включает токоведущие шины [280×15 мм], гибкую часть и токопроводящие трубы [8 труб ш 60×30 мм], соединенные с контактными щеками [980×350×65 мм]. Короткая сеть выполнена на электродах по схеме «треугольник» .
Печь типа РКЗ-16,5. Вращающаяся ванна имеет следующие размеры: диаметр на уровне подины — 6650 мм; глубина — 2300 мм, глубина ванны с учетом опорного кольца свода — 3050 мм, диаметр распада электродов — 3100 мм, диаметр электрода — 1200 мм. Электрическое питание осуществляется от трех однофазных трасформаторов типа ЭПЦН-8200/10, установленных в специальной камере на уровне рабочей площадки. Короткая сеть собрана на электродах по схеме «треугольник». Максимально допустимый ток в электроде— 60 кА.
Печь типа РПЗ-48. Печь оборудована тремя однофазными трансформаторами мощностью 21 МВА. Общая мощность ее составляет 63 МВА. Благодаря установке на печи РПЗ-48 мощных трансформаторов есть возможность повысить их мощность за счет увеличения рабочего тока при относительно медленном увеличении рабочего напряжения. Однако при этом снижается коэффициент мощности [cos ф] электропечного агрегата.
Отличие открытой и закрытой печей состоит в отсутствии на открытой печи водоохлаждаемого металлического свода. Это определило место подачи шихты по труботечкам в печь: на закрытой печи шихта подавалась в загрузочные воронки электродов, а на открытой — шихта поступала непосредственно на колошник. Представление о геометрических размерах зон превращения шихты в открытой и закрытой печах можно получить из рассмотрения рис. 1.2.
В закрытой печи перед выпуском плавки шлаковый расплав достигает более высоких горизонтов, чем в открытой печи. Освобождающиеся объемы ванн в процессе выпуска заполняются холодной сыпучей шихтой и температурное поле имеет несколько отличный характер. На открытой печи по мере погружения зондов плотность тока увеличивается.
Рис. 1.2 Вертикальные разрезы открытой (а) и закрытой (б) ванн печей РКЗ-16,5, выплавляющих силикомарганец:
1— холодная шихта; 2 — разогретая шихта; 3 — оплавленная шихта; 4 — расплав.
Вокруг электрода ток распределяется крайне неравномерно, что обусловлено системой загрузки шихты и размещением выходных отверстий труботечек на колошнике. На закрытой печи наибольшее значение плотности тока достигает 1,28 А/см2 на участке электрод—футеровка; в сторону от каждого электрода величина плотности тока была в 2—3 раза ниже.
В шихту для выплавки силикомарганца иногда используют необожженный доломит фракции 25—80 мм, имеющий следующий химический состав, %: 33,6— 35,7 СаО; 16,0—18,2 MgO; 1,1—1,3 SiO2; 0,6— 0,8 А12О3; 0,1—0,3 Fe2O3; 0,005—0,0008 Р; 0,03 S; 45—46 п.п.п. В некоторых случаях используют известняк состава, %: 54,6 СаО; 0,49 MgO; 1,67 SiO2; 0,2 Fe2O3; 1,5 А12О3; 0,005 Р; 0,04 S; 41,3 п.п.п.
1.3 Технология производства ферросиликомарганца
1.3.1 Сортамент
По химическому составу силикомарганец должен удовлетворять требованиям ДСТУ 3548 — 97, что приведено в таблице 1.10.
Таблица 1.10 Требования к химическому составу силикомарганца по ДСТУ 3548 — 97, %
Марка | Si | Мn, Не менее | С | Р | S | ||
Группа силикомарганца | |||||||
А | Б | ||||||
не более | |||||||
МнС25 | 25,0—35,0 | 60,0 | 0,5 | 0,05 | 0,25 | 0,03 | |
МнС22 | 20,0—25,0 | 65,0 | 1,0 | 0,10 | 0,35 | ||
МнС17 | 15,0—20,0 | 2,5 | 0,10 | 0,60 | |||
МнС12 | 10,0—15,0 | 3,5 | 0,20 | 0,60 | |||
Таблица 1.11 Требования к фракционному составу ферросиликомарганца
Класс крупности | Размер кусков ферросиликома-ргаица, мм | Массовая доля кусков по размерам в партии | Максимальный размер надрешетных кусков по усредненным измерениям в трех направлениях, мм | ||
в процентах не более | |||||
надрешетного | подрешетного | ||||
20 — 200 | |||||
20 — 100 | |||||
5 — 100 | |||||
5 — 50 | |||||
5 — 25 | |||||
0 — 300 | ; | ||||
1.3.2 Технологические особенности выплавки силикомарганца
Выплавка силикомарганца ведется непрерывно. Шихта загружается в печь непрерывно самотеком по труботечкам из бункеров. Рабочие концы электродов, погруженные в шихту, необходимо держать от подины на расстоянии 900—1200 мм. Давление газа под сводом должно быть 2,8—4,9 Па при температуре 750 °C, а в газоходе — не выше 300 °C. Допустимое содержание водорода в газе не выше 8%, окиси углерода — 70—80% и кислорода — не более 1%.
При пониженном содержании кремния в сплаве шихта корректируется добавкой 400 — 600 кг кварцита с коксом, а в случае повышенной концентрации кремния — 500 — 700 кг марганцевого концентрата с коксом.
Выпускают сплав и шлак через 2 ч работы печи. Летки открывают машиной. Шлак выпускают в стальные ковши вместимостью 11 м3. Продолжительность выпуска — 20 — 40 мин. Летки закрывают огнеупорной глиной в смеси с коксовой мелочью. Ковши с металлом и шлаком выкатывают в разливочный пролет. Перед разливкой сплава сливают шлак из ковша с металлом так, чтобы исключить потери силикомарганца. Оставшийся в ковше над металлом шлак загущают песком с целью
предотвращения попадания плохо отделяющегося кислого шлака в слитки сплава при разливке. Силикомарганец разливают на разливочной машине, характеристика которой приведена ниже:
Такие машины используются также для разливки ферромарганца и малофосфористого шлака. Производительность машины зависит от вида разливаемого продукта.
Средний расход изложниц составляет 5,14 кг/т сплава. С целью уменьшения расхода изложниц разработаны и внедрены новые составы чугунов и конструкции изложниц. Слитки силикомарганца вследствие малой механической прочности сплавов системы Мn—Si также имеют низкие характеристики прочности, что приводит к образованию некондиционной мелочи. Применение в шихту малофосфористого шлака обеспечивает получение силикомарганца с относительно низким содержанием фосфора (табл. 1.12).
Таблица 1.12 Химический состав силикомарганца, %
Р | Si | Mn | Fe | Al | С | S | Ti | Ni | Cu | Cr | |
0,4 | 17,8 | 74,2 | 5,8 | 0,019 | 1,34 | 0,008 | 0,13 | 0,04 | 0,020 | 0,018 | |
0,35 | 18,0 | 74,2 | 5,9 | 0,017 | 1,21 | 0,011 | 0,14 | 0,04 | 0,011 | 0,014 | |
0,25 | 18,3 | 73,6 | 6,0 | 0,020 | 1,20 | 0,015 | 0,15 | 0,03 | 0,014 | 0,020 | |
Отвальный шлак силикомарганца имеет следующий химический состав, %: 49,0−49,8 SiO2; 12,2−14,0 СаО; 2,9−3,1 MgO; 13,4−15,3 Мn; 0,002−0,003 Р; 0,5−0,6 S; 7,2−8,0 А12О3.
С целью повышения использования марганца отвальный шлак частично можно использовать в качестве компонента шихты при выплавке литейного и бессемеровского чугуна в количестве 22—25 кг/т чугуна.
Таким образом, как видно из выше перечисленных сведений особое место занимает сера, которая является одной из вредных примесей. Но полностью удалить ее невозможно, удается лишь снизить процентное содержание.
2. Исследование сульфидных компонентов ферросиликомарганца
2.1 Сера в структуре стали и ферросплавов
2.1.1 Влияние серы на свойства стали и методы ее снижения
Сернистые включения сильно снижают механические свойства, особенно ударную вязкость и пластичность в поперечном направлении вытяжки при прокатке и ковке, а также предел выносливости. Работа зарождения трещины не зависит от содержания серы, а работа развития трещины с увеличением содержания серы резко падает. Свариваемость и коррозионную стойкость сернистые включения ухудшают.
Источниками серы в стали служат руда, восстановители, а также ферросплавы, которые применяют для раскисления и легирования. Химический состав некоторых ферросплавов приведен в таблице 2.1.
Таблица 2.1 Химический состав ферросплавов
Марка сплава | Химический состав, % | ||||||||||
Si | V | C | Cr | S | W | P | Мо | Mn | Тi | ||
Ферросилиций ФС90 | >89 | ; | ; | ; | <0,02 | ; | <0,03 | ; | <0,2 | ; | |
Феррохром ФХ001 | <0,8 | ; | <0,01 | >68 | <0,02 | ; | 0,02 | ; | ; | ; | |
Ферромарганец ФМн75 | <2,0 | ; | <7,0 | ; | <0,03 | ; | <0,45 | ; | >75 | ; | |
Феррованадий Вд1 | <2,0 | >35 | <0,75 | ; | <2,0 | ; | <0,10 | ; | ; | ; | |
Ферровольфрам В3 | <1,2 | ; | <0,7 | ; | <0,15 | <0,10 | ; | <0,6 | ; | ||
Ферротитан Ти0 | ; | <0,2 | <0,10 | ; | <0,03 | ; | <0,04 | ; | ; | ||
Ферромолибден ФМ2 | <1,5 | ; | <0,10 | ; | <0,15 | <1,0 | <0,10 | >55 | ; | ; | |
В исходных углях сера находится в виде сульфидов (FeS2, FeS), сульфатов (CaSO4, FeSO4), а также в виде органических соединений. Содержание сульфатной серы невелико (0,1−0,2%).
Содержание серы в коксе является важнейшим показателем его качества (например, при работе на коксе 70— 95% всей вносимой в доменную печь серы составляет сера кокса). Практикой установлено, что повышение содержания серы в коксе на 0,1% вызывает увеличение удельного расхода кокса на 0,8—1,2% и снижает производительность печи на 1—1,4%. Этим объясняется непрерывная борьба за снижение содержания серы — от добычи угля до загрузки кокса в печь.
При обогащении углей 15—20% серы отделяется с породой, что соответствует снижению содержания ее на 0,4—0,8%. В процессе коксования 5—20% серы шихты удаляется с летучими веществами, а остальная остается в коксе. Сера в коксе находится в органической массе (67—76%) в виде органических горючих соединений и в минеральной части— золе (20—25% в сульфидах, 6—8% в сульфатах).
Одной из вредных примесей железных руд является сера. По действующим стандартам, содержание ее в передельном чугуне не должно превышать 0,015—0,06%. Наиболее часто сера встречается в магнетитах, где содержание ее не должно превышать 0,2%. Если же руда подвергается агломерации, то этот предел может быть значительно повышен (до 2%). Такое резкое изменение объясняется тем, что при агломерации уходит с газами до 95% всей серы.
В доменную печь сера вносится рудой, коксом и флюсами в виде соединений FeS2, FeS, CaSO4, BaSO4. Больше всего серу вносит кокс. Самым активным десульфуратором является известь:
Из константы равновесия следует: чтобы перевести максимальное количество серы в шлак, необходимо увеличить основность шлака и снизить в нем содержание продуктов реакции FeO и CaS.
Степень десульфурации определяется отношением содержаний серы в шлаке и металле (коэффициентом распределения серы): Ls =
Содержание серы в чугуне зависит от количества остающейся в печи серы, коэффициента распределения серы и относительного количества шлака.
При других неизменных условиях содержание серы в чугуне будет тем ниже, чем меньше серы на единицу чугуна будет вноситься в печь шихтой, так как при обычных условиях плавки на передельный чугун в печи остается и распределяется между чугуном и шлаком 95—98% серы шихты. Поэтому уменьшение расхода кокса на единицу чугуна, понижение содержания серы во всех шихтовых материалах позволяют уменьшить содержание серы в чугуне.
Сера является вредной примесью в стали. Содержание серы в стали допускается до 0,05−0,06%.
Сера имеет неограниченную растворимость в жидком железе и ограниченную — в твердом. При кристаллизации стали с повышенным содержанием серы, сульфиды железа выделяются по границам зерен, через что при нагревании стали для прокатки или ковки, металл становится красноломким.
Десульфураторами могут быть следующие элементы: Мn, Мg, Na, Са, а также редкоземельные элементы.
Введение
марганца в сталь приводит к получению в твердом металле сульфидов марганца МnS, что имеют температуру плавления 1620 °C, что предотвращает красноломкость стали при горячей обработке.
Поскольку сера поверхностно-активный элемент, то процесс десульфурации происходит в основном на поверхности раздела металл-шлак по реакции:
Feж + [S] + (СаО) = (СаS) + (FеО) (2.2)
Чем выше значение коэффициента распределения серы LS, тем лучше проходит десульфурация металла.
Удалению серы из металла способствуют:
— наличие основных шлаков с высокой активностью СаО;
— низкая окисленность металла (минимальное содержание кислорода) и низкая окисленность шлака (минимальное содержание закиси железа);
— низкая концентрация серы в шлаке (достигается скатыванием шлака и наведением нового);
— перемешивание металла со шлаком и увеличение поверхности контакта;
— повышение температуры ванны.
Основное количество серы удаляется со шлаком [21,22].
2.1.2 Некоторые особенности сульфидов компонентов силикомарганца
Процессы получения сульфидов заключаются во взаимодействии оксидов, солей или чистых элементов с газообразными серосодержащими реагентами или с серой в парообразном и твердом состоянии. В качестве газообразных реагентов используют сероводород (H2S) и сероуглерод (CS2). В ряде процессов сульфидирования применяют восстановители преимущественно углерод, реже — алюминий.
По энтальпии прочность сульфидов элементов, входящих в состав силикомарганца, характеризуются следующими величинами, — ккал/моль [23]:
Сульфиды с положительным значением энтальпии (SiS, CS, CS2) в стандартных термодинамических условиях находятся в газообразном состоянии.
По склонности к образованию сульфидов в стали с содержанием серы 0,5% легирующие элементы в убывающий ряд:
Zr, Ti, Mn, Nb, V, Cr, Al, Mo, W, Fe, Ni, Co, Si.
Последние три элемента самостоятельных сульфидов не образуют и встречаются в ограниченных количествах в сульфидах железа.
Двойные диаграммы состояния элементов, содержащихся в силикомарганце, и серы имеют существенные отличия.
С марганцем в жидком состоянии образуются две несмешивающиеся жидкости (рис. 2.1). В силу различия плотностей марганца (7,4г/см3) и его сульфида (4,0г/см3). Эта особенность обеспечивает переход практически всей поступающей серы в шлак при выплавке марганцевых сплавов.
Почти аналогична диаграмма состояния системы хрома с серой (рис 2.2). В ней также образуются несмешивающиеся жидкости, что снижает вероятность участия хрома в повышении содержания серы в марганцевых сплавах. Определенным подтверждением этому может служить известное в практике производства углеродистого феррохрома использование марганца для десульфурации этих сплавов.
В отличие от марганца и хрома в системах титан-сера, железо-сера, никель-сера обеспечивается неограниченная смешиваемость в жидком состоянии (рис. 2.3 — 2.5). По этой причине не исключена вероятность участия этих элементов, преимущественно титана, в повышении содержания серы в силикомарганце [25,26].
Диаграммы состояния двухкомпонентных систем
Рис. 2.1 Диаграмма состояния системы Mn — S
Рис. 2.2 Участок диаграммы состояния системы Cr — S
Диаграмма состояния двухкомпонентной системы
Рис. 2.3 Предварительный вариант диаграммы фазовых равновесий системы титан-сера: 1- данные термического анализа; 2- дилатометрически определенные эффекты; 3- результаты измерения температуры жидкой фазы оптическим способом; 4- однофазные сплавы; 5- двухфазные сплавы.
Диаграммы состояния двухкомпонентных систем
Рис. 2.4 Диаграмма состояния системы Fe — S
Рис. 2.5 Диаграмма состояния системы Ni — S: — предполагается широкая область растворимости S в твердом NiS2
2.2 Результаты экспериментальных исследований
С целью определения влияния элементов силикомарганца на массовую долю серы в нем были проведены опытные плавки в печи Таммана. Заключались они в переплаве силикомарганца с добавлением сернокислого марганца, железа (углеродистой стали) и бесфосфористого шлака (46,7% Mn, 28,8% SiO2) для защиты сплава от окисления.
В экспериментах были использованы смеси с постоянными навесками силикомарганца (150г), шлака (50г) сернокислого марганца (10г) и переменной навеской железа от 0 (опыт № 1), 10 г (опыт № 2) и до 25 г (опыт № 5) через каждые 5 г.
Методика опытов заключалась в следующем. В графитовый тигель послойно помещались компоненты смесей. Вначале сернокислый марганец, затем силикомарганец, железо и сверху шлак. Смеси в печи Таммана нагревались до 1500_С и выдерживались при этой температуре в течение 15 минут.
Такая методика должна была обеспечивать восстановление сернокислого марганца по реакциям:
MnSO4 + 2[Si] = [MnS] + 2(SiO2); (2.3)
MnSO4 + 4C = [MnS] + 4CO; (2.4)
Попадание сульфида марганца в расплав силикомарганца и его сегрегацию в жидкой фазе.
Введение
железа в сплав обеспечивало понижение концентрации ведущих и сопутствующих элементов силикомарганца.
Химический состав сплавов, полученных в опытах, по анализам лаборатории НЗФ, ЗФЗ и УкрНИИспецстали, приведен в табл.2.2.
Таблица 2.2 Химический состав силикомарганца
Предприятие | № проб | Компоненты, % | ||||||
Mn | Si расчет) | Fe | S | P | C | |||
НЗФ | 74,6 | (15,9) | 6,6 | 0,030 | 0,47 | 2,4 | ||
71,0 | (14,7) | 11,8 | 0,033 | 0,46 | 2,4 | |||
68,4 | (13,9) | 14,2 | 0,030 | 0,46 | 2,3 | |||
66,7 | (13,4) | 17,1 | 0,024 | 0,45 | 2,2 | |||
64,5 | (12,7) | 18,9 | 0,030 | 0,44 | 2,2 | |||
ЗФЗ | 75,3 | 15,4 | 6,2 | 0,11 | 0,48 | 2,3 | ||
72,6 | 13,8 | 10,4 | 0,09 | 0,46 | 2,5 | |||
71,1 | 13,2 | 12,7 | 0,08 | 0,45 | 2,3 | |||
69,3 | 13,1 | 14,7 | 0,07 | 0,44 | 2,2 | |||
68,6 | 12,4 | 15,7 | 0,06 | 0,44 | 2,5 | |||
УкрНИИспецсталь | 74,5 | 16,30 | 5,94 | 0,063 | 0,46 | 2,5 | ||
70,0 | 15,12 | 11,31 | 0,058 | 0,46 | 2,3 | |||
68,3 | 14,32 | 14,08 | 0,042 | 0,45 | 2,3 | |||
66,7 | 14,07 | 17,13 | 0,035 | 0,44 | 2,2 | |||
64,8 | 13,63 | 19,20 | 0,024 | 0,44 | 2,3 | |||
Исходный силикомарганец | ||||||||
72,8 | 18,4 | 6,72 | 0,021 | Ti0,09 | Ni0,04 | |||
Несмотря на некоторое расхождение анализов, полученные результаты позволяют заключить, что разбавление силикомарганца железом не приводит повышению массовой доли серы в сплаве. Напротив, наблюдается ее понижение с увеличением добавок железа. По усредненным значениям — от 0,068 (опыт № 1) до 0,038% (опыт № 5).
Из внимания можно исключить также никель, как элемент не образующий в сложных системах самостоятельных сульфидов.
Поэтому из трех элементов, обеспечивающих в двойных системах неограниченную смешиваемость в жидком состоянии с сульфидами (см. рис.2.3−2.5), особое внимание заслуживает титан.
В сталях, содержащих титан, сера представлена преимущественно сульфидами марганца и титана. При содержании 0,05% титана в начале выделяется сульфид (Mn, Ti) S. Его взаимодействие с компонентами стали приводит к появлению фаз Ti (N, C) TiS4 и Ti4C2S2 или (Ti, Mn, Fe)4C2S2, которые выделяются в виде оболочек вокруг сульфидов марганца.
Вполне вероятно, что аналогичные комплексные образования карбосульфидов формируются в силикомарганце. При этом марганцевая основа сплава может вносить существенные изменения в эти комплексные соединения.
2.3 Рентгеноструктурные исследования опытных сплавов
Исследование образцов сплавов проводили методом рентгеноструктурного микроанализа на приборе МS-46. Распределения элементов определялось по записи концентрационных кривых интенсивности характеристического излучения Fe, Mn, Si, Ti, Ca, Al и S при линейном сканировании зонда через включения размером более 10 мкм или в точке при размерах включений менее 10мкм.
Были исследованы исходный силикомарганец и 5 опытных сплавов. Микроструктура образцов приведена на рис. 2.6−2.11. Сера в сплавах представлена включениями. Основной тип включений — сульфиды марганца и карбиды титана, находящиеся в непосредственной близости. Причем карбиды титана служат своеобразной подложкой для формирования сульфидов марганца.
Кроме этих включений, встречаются кальцевые силикаты типа хCaO•ySiO2 с оболочкой из MnS, в состав которой в виде рассыпей входят карбиды титана.
Отличие микроструктуры сплавов друг от друга заключается в основном в размерах включений. В исходном силикомарганце они не превышают 2−5 мкм, в первом опытном сплаве увеличиваются до 10 мкм, в пятом — достигают 20 мкм. Обусловлено такое поведение включений понижением температуры плавления сплава при разбавлении его железом и, следовательно, повышенной степенью его перегрева при температуре выдержки. Это обеспечивало лучшие условия для коалесценции вкючений.
Общей закономерностью микроструктуры всех исследованных сплавов является то, что в структуре сульфида марганца не обнаружено присутствие других элементов.
Для пояснения полученных результатов можно предположить следующую схему взаимодействий. В жидком силикомарганце формируется сложный карбосульфид марганца и титана (Ti, Mn)4C2S2, при кристаллизации которого происходит переориентация углерода к титану, а марганца к сере. Причины, препятствующие разделению этого сложного соединения и выделению серы из сплава заключается, по-видимому, в интерметалидных связях типа TiMn2 или TiMn.
Микроструктура промышленного силикомарганца
Рис. 2.6 Исходный образец: -MnS; 2- TiC; свет отраженный, увелич. 800х
Микроструктура опытного образца
Рис. 2.7 Опытный сплав № 1; 1- MnS; 2- TiC; свет отраженный, увелич. 630х
Микроструктура опытного образца
Рис. 2.8 Опытный сплав № 2: 1- MnS; 2- TiC; свет отраженный, увелич. 800х
Микроструктура опытного образца
Рис. 2.9 Опытный сплав № 3: 1- MnS; 2- TiC; свет отраженный, увелич. 800х
Микроструктура опытного образца
Рис. 2.10 Опытный сплав № 4:
1- MnS; 2- TiC; 3-хСаО•уSiО2; свет отраженный, 800х
Микроструктура опытного образца
Рис. 2.11 Опытный сплав № 5: MnS; 2- TiC; свет отраженный, 800х
Поведение серы в опытных плавках обусловлено уменьшением массовой доли титана в сплавах, в первом опыте произошло насыщение связей серой. При этом доля серы из сернокислого марганца, перешедшая в сплав (по усредненному значению трех анализов), не превышает 3,5%.
Для оценки влияния массовой доли титана на концентрацию серы в сплаве в табл.2.3 приведен расчетный состав силикомарганца при условии его разбавления только железом.
Таблица 2.3 Состав силикомарганца при разбавлении его только железом
Опыты № | Добавка стали, г | Компоненты сплава, % | |||||
Mn | Si | Fe | Ti | C | |||
исходный | ; | 72,8 | 18,4 | 6,72 | 0,091 | 1,24 | |
68,3 | 17,28 | 12,40 | 0,084 | 1,55 | |||
66,2 | 16,76 | 14,98 | 0,082 | 1,69 | |||
64,3 | 16,28 | 17,41 | 0,079 | 1,82 | |||
62,5 | 15,82 | 19,70 | 0,077 | 1,95 | |||
Из данных таблиц 2.2 и 2.3 следует, что в процессе опытов происходит окисление 1,860,37 г кремния и восстанавливается 5,191,05 г марганца на 100 г исходного сплава.
При этом происходит следующее понижение содержания титана в силикомарганце, %:
С этим изменением связано понижение массовой доли серы в силикомарганце (рис. 2.12).
Рис. 2.12 Влияние содержания титана на концентрацию серы в опытном силикомарганце: по анализам: 1- ЗФЗ; 2- УкрНИИСС; 3- НЗФ.
Неточность анализов лишает целесообразности количественных оценок приведенного влияния. Однако очевидным представляется то, что с ростом концентрации титана в силикомарганце должна повышаться массовая доля серы.
3. Разработка способа снижения концентрации серы в силикомарганце
3.1 Источники серы и титана при выплавке силикомарганца
Основным источником серы при выплавке силикомарганца является кокс из донецких углей. Массовая доля серы в них составляет 1,5−1,8%. В концентратах II сорта, используемых в производстве силикомарганца массовая доля серы по анализам Марганцевого и Ордженикидзевского ГОКов находится в пределах 0,046−0,053%. При агломерации концентратов содержание серы в готовом продукте достигает 0,17−0,20%. Доля концентратов в этой общей сумме составляет около 25%, оставшиеся 75% приходятся на коксовую мелочь.
При использовании одного агломерата в качестве марганцевого сырья количество серы, вносимое шихтой на тонну силикомарганца, составляет около 12,5−13,0 кг.
На Запорожском заводе вследствие использования смеси агломерата и концентрата в соотношении 1:1 эта масса вносимой серы уменьшается до 10,0−10,5 кг. По содержанию двуокиси титана в шихтовых материалах и продуктах их плавки информация весьма ограничена. Ее содержание в лучшем случае определяется в среднегодовых пробах материалов.
Рис. 3.1 Динамика изменения содержания двуокиси титана в концентратах II сорта двух рудников марганцевого ГОКа
По марганцевым ГОКам массовая доля TiO2 в концентратах определялась до 1982 г. Динамика ее изменения по двум рудникам марганецкого ГОКа приведена на рис. 3.1. по Орджоникидзевскому ГОКу результаты предыдущих анализов не сохранились.
На основании приведенных данных можно заключить, что существует значительное расхождение до 20−22% массовой доли двуокиси титана в концентратах различных рудников. При этом по годам не наблюдалось тенденции ее повышения в концентратах.
Негативной стороной качества марганцевых концентратов является понижение в них концентрации марганца и особенно в последние годы с 1991 по 1995 г.
По среднегодовым усредненным по двум ГОКам анализам понижение содержания марганца в прокаленных концентратах II сорта за эти годы вполне удовлетворительно описывается зависимостью:
(3.1)
с коэффициентом корреляции близким единице.
Вследствие этого изменения происходит увеличение количества двуокиси титана на единицу марганца, вносимого в шихту силикомарганца, и, следовательно, на тонну получаемого сплава.
Кроме марганцевого сырья, титан в шихты вносится коксом и кварцитом. По данным УХИНа массовая доля TiO2 в золе кокса составляет 0,6−0,8%, в кварцитах — 0,08−0,10%.
С учетом расхода марганцевых концентратов и коксовой мелочи на тонну агломерата II сорта массовая доля TiO2 должна составлять 0,12−0,14%.