Экструзионные агрегаты для производства труб из термопластов
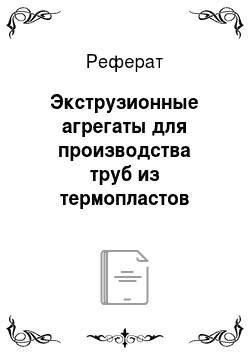
При производстве труб большого диаметра применение ванн наливного типа затруднено из-за весьма значительных усилий всплытия, воздействующих на трубную заготовку. Этого недостатка лишены охлаждающие ванны оросительного типа. Охлаждающая жидкость подается в этом случае либо путем полива, либо разбрызгиванием с помощью форсунок, установленных вокруг заготовок с шагом, обеспечивающим создание… Читать ещё >
Экструзионные агрегаты для производства труб из термопластов (реферат, курсовая, диплом, контрольная)
Описание технологического процесса
.Изготовление труб на экструзионных агрегатах включает следующие технологические операции:
- — плавление исходного сырья и гомогенизация расплава в экструдере;
- — выдавливание трубчатой заготовки в вязкотекучем состоянии из кольцевого зазора экструзионной головки;
- — придание заготовке необходимой формы и размеров и их фиксирование за счет частичного охлаждения в калибрующем устройстве;
- — завершение процесса охлаждения трубы в охлаждающем устройстве;
- — отвод непрерывно экструдируемой изготовленной трубы, разрезка ее на мерные отрезки или намотка на барабан;
- — контроль качества готовой продукции.
Технологическая схема агрегата для производства труб приведена на рис. 2.91. Компоновка машин и устройств, показанная на рисунке, является наиболее распространенной.
Производительность линии зависит от типоразмера трубы и с увеличением последнего увеличивается. Линейная скорость отвода трубы не превышает 4 м/мин (исключение составляют только очень маленького диаметра трубы). Таким образом, увеличение производительности линии в первую очередь связано с проблемой повышения линейной скорости отвода трубы.
Выходящая из формующего зазора головки 2 расплавленная заготовка проходит через калибрующее устройство 3; частично охлаждаясь в нем, труба приобретает форму и размеры, соответствующие форме и размерам готовой трубы 8. Окончательное охлаждение происходит в ванне 4.
В зависимости от того, какая из поверхностей трубы подвергается калибрующему воздействию, различают наружное, внутреннее и двухстороннее калибрование. Прижатие заготовки к калибрующей поверхности осуществляется путем раздува ее сжатым воздухом, подаваемым в полость трубы (пневмокалибрование), присоса (вакуумкалибрование), а также протяжки.

Рис. 2.91. Технологическая схема экструзионного агрегата для производства труб:
/ — экструдер; 2—головка; 3—калибрующее устройство; 4 — охлаждающая ванна; 5 —заглушка; 6 — тянущее устройство; 7— отрезное устройство; 8— готовая труба. Стрелками показаны вход и выход охлаждающего агента В калибрующем устройстве 3 (см. рис. 2.91) отводится лишь незначительная часть тепла, содержащегося в материале трубы. Большая его часть отбирается в охлаждающем устройстве 4. При современном уровне производительности экструзионных машин длина охлаждающих ванн составляет до 70% длины трубной линии. В связи с тем что процессу охлаждения трубной заготовки первоначально не придавали существенного значения, а также по причине значительных габаритов охлаждающих ванн в течение длительного времени стремились к максимально упрощенным конструктивным решениям. Трубную заготовку охлаждали погружением в неподвижную или слабо перемешиваемую жидкость. Так как максимальный тепловой поток при охлаждении заготовки наблюдается на стадии калибрования и в начальной стадии охлаждения, влияние на время охлаждения повышения температуры охлаждаемой поверхности заготовки вследствие недостаточности теплоотвода не представлялось очевидным. Кроме того, существовало ошибочное мнение, что вследствие низкой теплопроводности полимеров внешние условия теплообмена не являются фактором, лимитирующим интенсивность отвода тепла от заготовки. Однако, как показала практика, интенсификация теплообмена в охлаждающем устройстве может существенно повысить его производительность (до 30%).
Основным путем интенсификации теплообмена является принудительная циркуляция охлаждающей жидкости у поверхности заготовки. Это достигается путем отвода жидкости из калибрующей насадки через кольцевой зазор, направляющей струю жидкости вдоль поверхности заготовки. Струя разрушает пограничный тепловой слой, препятствующий интенсивному теплообмену. Однако ее действие распространяется лишь на весьма незначительную часть длины заготовки и не может существенно сказаться на уровне коэффициента теплоотвода в целом.
При производстве труб большого диаметра применение ванн наливного типа затруднено из-за весьма значительных усилий всплытия, воздействующих на трубную заготовку. Этого недостатка лишены охлаждающие ванны оросительного типа. Охлаждающая жидкость подается в этом случае либо путем полива, либо разбрызгиванием с помощью форсунок, установленных вокруг заготовок с шагом, обеспечивающим создание на ее поверхности непрерывной пленки жидкости, стекающей под действием собственного веса. Как показал опыт, такая организация охлаждения имеет ряд преимуществ по сравнению с ранее рассмотренными. Основным из них является то, что слой жидкости на поверхности трубы, достаточный для максимальной интенсификации теплоотвода от заготовки, оказывается весьма тонким, а энергетические расходы, связанные с циркуляцией жидкости, минимальны; повышается стабильность и равномерность охлаждения по периметру трубы. Кроме того, существенно снижаются металлоемкость конструкции и требования к уплотнению отсеков ванн при входе и выходе заготовки. В наиболее прогрессивных технологических процессах производства труб малого диаметра также используется такой способ охлаждения (в частности, вакуумные ванны с калибрующими шайбами и распылением жидкости).
Одним из решающих качественных показателей напорных труб как конструкционных изделий является их несущая способность. В связи с этим наиболее важными характеристиками труб являются их прочностные свойства и способность противостоять определенному давлению в течение заданного промежутка времени.
Применяемый метод контроля долговременной прочности трубы состоит в следующем. Образец изготовленной тр>%ы при испытании нагружают внутренним гидростатическим давлением, уровень которого зависит от типа трубы, и при определенной температуре выдерживают контрольное время.