Оборудование для бурения
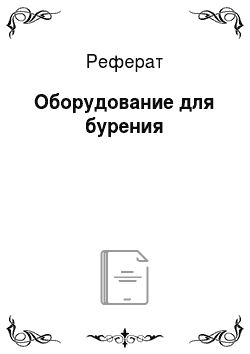
Далее начинается обратный ход поршня (рис. 2, б). Сжатый воздух поступает через канал 13 в штоковую полость 12 цилиндра, в результате чего поршень начинает перемещаться влево, вытесняя воздух из поршневой полости 10 в атмосферу через выхлопное отверстие 11. При дальнейшем перемещении влево поршень закрывает выхлопное отверстие 11, сжимает воздух в полости 10, который будет теперь оказывать… Читать ещё >
Оборудование для бурения (реферат, курсовая, диплом, контрольная)
Буровзрывной способ проведения горных выработок с погрузкой горной массы погрузочными машинами и механизмами или вручную отличается высокой трудоемкостью бурения шпуров, составляющей 20−40% общих трудовых затрат и 50−60% стоимости всех работ при этом способе проведения. горный оборудование бурение очистной струговой.
Шпуры — цилиндрические полости, выполненные в горной породе, глубиной до 5 м и диаметром до 85 мм. Шпуры большего диаметра принято называть скважинами, а длиной более 5 м — глубокими скважинами. Горные машины, предназначенные для бурения шпуров, называются бурильными машинами и установками.
По способу разрушения горной породы различают механические, физические и комбинированные способы бурения.
Наибольшее распространение получили механические способы бурения. При бурении шпуров или скважин механическим способом горная порода разрушается под действием внешних сил, передаваемых от бурильной машины буровому инструменту, а от него — непосредственно на породу в забое. При этом порода разрушается инструментом, который перемещается под действием осевой нагрузки (ударной или статической) и крутящего момента. В зависимости от точек приложения и величин этих нагрузок различают четыре способа бурения: ударно-поворотный, вращательный и занимающие между ними промежуточное положение ударно-вращательный и вращательно-ударный.
Ударно-поворотное бурение (рис. 1, а) характеризуется тем, что клиновидный инструмент внедряется в породу под действием значительной ударной нагрузки Fyд, направленной по оси инструмента. При этом осевое усилие Foc и крутящий момент Мкр очень малы. После каждого удара инструмент отскакивает от забоя шпура из-за упругости породы и инструмента, и последний поворачивается механизмом поворота на некоторый небольшой угол = 10ч20°. Вследствие этого каждый последующий удар наносится на новое место. Под действием ударной нагрузки порода под лезвием бура разрушается в виде борозд 1—1, 2—2, 3—3 и т. д. с толщиной среза h. Остающиеся между бороздами целики породы скалываются под действием горизонтальной боковой составляющей Fб,.
где — угол заострения бура, обычно = 90ч120°. Разрушенную породу удаляют из шпура или скважины промывкой, продувкой или пылеотсосом.
Основное преимущество ударно-поворотного способа бурения — возможность бурить породы любой крепости. К недостаткам следует отнести периодичность воздействия инструмента на породу, значительное пылеобразование, шум и вибрацию при работе.
Вращательное бурение (рис. 1, б) характеризуется тем, что инструмент под действием значительного осевого усилия подачи и крутящего момента Мкр, двигаясь поступательно на забой, отделяет по винтовой линии срез толщиной h. Ударные нагрузки отсутствуют. При вращательном бурении различают бурение сплошным забоем и кольцевым. В последнем случае в центре забоя скважины остается колонка (керн) неразрушенной породы.
Область рационального применения вращательного бурения — малоабразивные породы с коэффициентом крепости до f8 (по шкале проф. М. М. Протодьяконова). При более крепких породах инструмент, даже армированный твердым сплавом, быстро изнашивается. Применение инструмента с алмазами, закрепленными на режущих кромках, несколько расширяет эту область. Преимуществами вращательного бурения являются: непрерывность процесса разрушения горной породы, что обеспечивает высокую производительность; отсутствие ударных нагрузок и вибрации Мишины при работе; разрушение породы крупным срезом, что уменьшает пылеобразование и удельный расход энергии. Вращательное бурение получило широкое применение и осуществляется горными сверлами и бурильными машинами различного назначения.
Ударно-вращательное бурение (рис. 1, в) можно рассматривать как ударное бурение с непрерывным вращением инструмента.
Вращение инструмента и удар осуществляются независимо друг от друга. Порода разрушается под действием большой ударной нагрузки Fуд, осевого усилия Foc и крутящегося момента Мкр. Для ударно-вращательного бурения используются буровые агрегаты, применяемые для бурения скважин диаметром 80−150 мм и глубиной до 70 м в горных породах крепостью f = 8ч20. В агрегате имеется пневмоударник, расположенный на конце бурового става, который подается в скважину и приводится во вращение при помощи станка, расположенного в горной выработке.
Вращательно-ударное бурение (рис. 1, г) характеризуется тем, что порода разрушается под действием значительных по величине осевого усилия Foc, крутящего момента Мкр и дополнительной ударной нагрузки Fуд, наносимой в процессе бурения механизмом-ударником по хвостовику бурового инструмента. Ударная нагрузка увеличивает глубину внедрения инструмента в породу, что расширяет область применения вращателыю-ударного бурения при работе на неабразивных породах с коэффициентом крепости f = 6ч14.
На открытых горных работах для бурения скважин в породах с крепостью f = 6−18 используется шарошечное бурение. Разрушение породы при этом происходит под действием ударов зубьев шарошек при вращении прижатого к забою инструмента.
При физических способах разрушения на породу воздействуют газами, жидкостью, электрическим током, теплом и другими видами энергоносителя. К этим способам относят взрывное, термическое, ультразвуковое, гидравлическое и электрогидравлическое бурение.
При комбинированном способе горную породу разрушают одновременно механическим и физическим способами.
Одной из самых простых машин вращательного бурения является ручное сверло.
Ручные сверла предназначены для бурения шпуров по углю и породе с коэффициентом крепости f до 4. Сверла подразделяют: по способу подачи бурового инструмента на забой — с ручной и механической подачей; по роду потребляемой энергии — на электрические, пневматические и гидравлические; по типу управления — с непосредственным и дистанционным управлением.
В угольной промышленности применяют ручные электрические сверла, выпускаемые Томским электромеханическим заводом им. В. В. Вахрушева (электросверла ЭР14Д-2М, ЭР18Д-2М, ЭРП18Д-2М) и Конотопским электромеханическим заводом «Красный металлист» (СЭР19М).
Ручное электросверло СЭР19М состоит из асинхронного короткозамкнутого электродвигателя, литого алюминиевого корпуса, промежуточного щитка, обеспечивающего взрывобезопасность корпуса, передней крышки с двухступенчатым цилиндрическим редуктором, шпинделя, камеры с выключателем и крышкой, вентилятора и крышки с окнами для всасывания воздуха.
Дистанционное управление осуществляется с помощью пускового аппарата АП-4, в этом случае однофазный выключатель цепи управления на напряжение 24 В устанавливается в корпусе электросверла, а силовой трехфазный выключатель — в корпусе понижающего трансформатора.
Электросверло ЭРП18Д-2М отличается от электросверл СЭР19М, ЭР14Д-2М и ЭР18Д-2М наличием принудительной подачи — небольшой лебедки с канатным барабаном, смонтированной на корпусе сверла.
Ленинградским заводом «Пневматика» выпускаются пневматические ручные сверла СР3 и СР3М, предназначенные для бурения шпуров по углю и мягким породам с коэффициентом крепости f до 4, и сверла СПР13−750М для бурения шпуров по породам с / до 6 с применением пневмоподдержки. Сверла СР3 и СР3М могут быть использованы для бурения дегазационных скважин в угольных пластах.
Пневматические сверла отличаются друг от друга конструкцией редуктора. Сверло состоит из корпуса, пневматического ротационного мотора (двигателя), редуктора, пускового устройства и глушителя шума. Сверла СР3М и СПР13−750 оснащены муфтой боковой промывки. К пневмоподдержке сверло СПР13−750 крепится с помощью специальной вилки. Для бурения дегазационных скважин диаметром до 250 мм применяют винтовые штанги диаметром 120 мм с шагом 120 мм.
К более тяжелым буровым машинам относятся колонковые сверла. Их отличительной особенностью, в сравнении с ручными сверлами, является большая мощность привода, а соответственно и больший вес. В связи с этим для удержания сверла в процессе работы используются специальные поддерживающие устройства («колонки»).
В качестве сравнительно легких машин ударно-поворотного бурения используются перфораторы, работающие на сжатом воздухе. Основными механизмами перфораторов являются ударно-поворотный механизм, предназначенный для нанесения ударов по хвостовику бура и его поворота при обратном движении, и воздухораспределительный механизм, обеспечивающий попеременную подачу сжатого воздуха в переднюю или заднюю полость цилиндра перфоратора. Остановимся на этих механизмах более подробно.
Воздухораспределение в пневматических перфораторах осуществляется посредством клапанов, золотников или непосредственно поршнем.
Клапанное воздухораспределительное устройство (рис. 2) состоит из клапана 3, выполненного в виде кольца, втулки клапана 4 с отверстиями 6, клапанной коробки 2 с отверстиями 7 и крышки 1. Для установки поршня и клапана в исходное положение в крышке клапанной коробки предусмотрено небольшое отверстие 9.
В начале рабочего хода (рис. 2, а) клапан и поршень-ударник 14 находятся в левом положении. При включении пускового крана сжатый воздух поступает через отверстия б и 7 в кольцевое пространство 8 и далее между клапаном и его крышкой в левую полость 10 цилиндра. Под действием сжатого воздуха поршень перемещается вправо. При этом воздух из штоковой полости 12 вытесняется в атмосферу через выхлопное отверстие 11. При дальнейшем перемещении поршень перекрывает выхлопное отверстие, в результате чего воздух, находящийся в штоковой полости, а также в канале 13 и кольцевой полости 5, начинает сжиматься, оказывая давление на клапан слева. При дальнейшем движении вправо поршень открывает выхлопное отверстие и наносит удар по хвостовику бурового инструмента. Так как давление воздуха в поршневой полости 10 при этом резко снижается, то клапан перемещается вправо, соединяя кольцевые пространства 5 и 8,.
Далее начинается обратный ход поршня (рис. 2, б). Сжатый воздух поступает через канал 13 в штоковую полость 12 цилиндра, в результате чего поршень начинает перемещаться влево, вытесняя воздух из поршневой полости 10 в атмосферу через выхлопное отверстие 11. При дальнейшем перемещении влево поршень закрывает выхлопное отверстие 11, сжимает воздух в полости 10, который будет теперь оказывать давление на клапан справа. Когда поршень откроет выхлопное отверстие 11, давление воздуха в штоковой полости 12, канале 13 и кольцевом пространстве 5 резко снизится; вследствие этого клапан переместится влево. Далее цикл повторится. Особенностью клапанного воздухораспределения является то, что клапан, перекрывающий рабочие каналы, перемещается под действием разности давлений в передней и задней полостях цилиндра.
Клапанное воздухораспределение отличается простотой конструкции, небольшими движущейся массой и поверхностями трения, малым ходом клапана, что обеспечивает высокую скорость его переброски и дает возможность конструировать перфораторы с большим числом ударов поршня. По конструкции клапаны подразделяются на шариковые, мотыльковые (с откидным клапаном), кольцевые и фланцевые.
Золотниковое воздухораспределительное устройство обеспечивает меньший расход воздуха, чем клапанное, имеет больший к. п. д., позволяет получить высокие энергию удара и крутящий момент, но не обеспечивает такой большой частоты ударов, как клапанное. Различают воздухораспределительные устройства со сплошным золотником и цилиндрическим полым, который получил большее распространение.
В последнем случае воздухораспределительное устройство (рис. 3) состоит из втулки 1, золотника 2, коробки 3 и крышки 4. В начале рабочего хода (рис. 3, а) золотник и поршень-ударник 6 находятся в крайнем левом положении. Сжатый воздух поступает по каналам в золотник и через отверстия в крышке — в полость 5 цилиндра. Под действием сжатого воздуха поршень начинает перемещаться вправо. При дальнейшем движении поршень открывает канал 10, по которому сжатый воздух начинает поступать в левую кольцевую полость золотниковой коробки и передвинет золотник вправо. При дальнейшем движении поршня открывается выхлопное отверстие 9 и поршень наносит удар по хвостовику бурового инструмента. Сжатый воздух из поршневой полости 5 будет выходить при этом в атмосферу через выхлопное отверстие 9.
Далее начнется обратный ход поршня (рис. 3, б). Сжатый воздух будет поступать теперь по каналу 7 в правую полость цилиндра и переместит поршень влево. Когда поршень откроет входное отверстие канала 11, сжатый воздух по нему поступит в правую часть золотниковой коробки и под действием давления на фланец золотника передвинет его влево. Поршень откроет выхлопное отверстие 12, и воздух из правой полости цилиндра 8 поступит в атмосферу. Далее цикл повторится.
Отличительной особенностью золотникового воздухораспределения является перемещение золотника под действием давления сжатого воздуха, специально подводимого по дополнительным каналам из основного воздухопровода.
Помимо клапанного и золотникового воздухораспределения применяется еще бесклапанное, которое осуществляется самим поршнем-ударником. Несмотря на простоту конструкции, оно не нашло широкого распространения из-за увеличенного расхода сжатого воздуха и низкого к. п.д.
Ударно-поворотные механизмы зависимого действия осуществляют поворот бурового инструмента при обратном ходе поршня и могут быть конструктивно выполнены с геликоидальной (винтовой) нарезкой на штоке поршня-ударника или с отдельным геликоидальным стержнем, имеющим на конце храповое устройство (рис. 4).
В механизме первого типа (рис. 4, а) при рабочем ходе поршень-ударник 1 движется вправо, не вращаясь. Однако при этом он поворачивает двумя своими геликоидальными вырезами храповую буксу 2. Храповые собачки 3 с пружинами 4 и стержнями 5, закрепленными в корпусе 6 перфоратора, не препятствуют этому. Две прямые выточки 6, имеющиеся на штоке поршня-ударника, заходят в поворотную буксу 7, соединенную торцовыми кулаками с буксой 8, в гнездо которой вставлен хвостовик бура 9. Поворотная букса и бур при этом не вращаются. При обратном ходе храповые собачки 3 запирают храповую буксу 2. В результате этого поршень-ударник поворачивается вместе с поворотной буксой и буром на некоторый угол.
Механизм второго типа (рис. 4, б) состоит их храповой буксы 1, закрепленной в верхней части перфоратора, и стержня 2 с геликоидальной нарезкой на конце. Головка стержня имеет две или четыре собачки 3 со стержнями 4 и пружинами 5. Стержень 2 входит в геликоидальную гайку 6, расположенную внутри поршня 7. На штоке поршня имеются шлицы, на которые насажены поворотная букса 8 и соединенная с ней букса 9 с буром 10.
Принцип действия этого устройства такой же, как и у описанного выше. При рабочем ходе поршня-ударника храповые собачки не препятствуют повороту геликоидального стержня 2, вследствие этого поршень-ударник движется вправо, не вращаясь. При холостом ходе храповые собачки запирают стержень 2, в результате чего поршень-ударник вместе с поворотной буксой и буром поворачивается.
Поворотные механизмы независимого действия осуществляют поворот бурового инструмента от отдельного пневмомотора, который передает крутящий момент через редуктор. Это позволяет в 7−10 раз увеличить крутящий момент, исключить поворотное устройство на поршне и штоке и расходовать всю энергию поршня только на удар, что повышает производительность бурения на 30−35%. Кроме того, имеется возможность более простым способом изменять частоту вращения бурового инструмента и увеличивать глубину скважины до 50 м. К недостаткам независимого вращения бурового инструмента следует отнести увеличение массы перфоратора и усложнение конструкции. Независимое вращение бурового инструмента применено на колонковых перфораторах ПК60 и ПК75.
Для бурения шпуров применяется буровой инструмент (рис. 5) в виде цельного бура или состоящий из буровой штанги и резца или буровой коронки, армированных твердым сплавом. Различают буровой инструмент для вращательного, ударно-поворотного и вращательно-ударного бурения.
Буровой инструмент для вращательного бурения состоит из витых или сплошных буровых штанг и резцов. Буровая штанга состоит из хвостовика, тела буровой штанги, головки с отверстиями для закрепления резца и крепежного штифта.
Штанги изготовляют из стали круглого, ромбического и прямоугольного сечений, с навивкой на них спирального выступа или свивкой буровой стали в виде спирали для выноса буровой мелочи. Размер профиля буровой штанги 3618, 3820, 4018, 4320 мм. Для ручных сверл применяются штанги длиной 1,2 и 3 м, для колонковых — 0,7−5 м с интервалом 0,7 м.
Буровой резец состоит из корпуса, хвостовика для крепления штанги и перьев, заканчивающихся режущими лезвиями. Между перьями имеется разрыв, называемый раствором. Резцы изготовляют двухи трехперыми диаметром 41, 44 и 60 мм для бурения по углю и породе. Двухперые резцы применяют при бурении по углю и слабым породам, трехперые — по более крепким породам.
Корпуса изготовляют из стали, к ним припаивают пластины твердого сплава ВК-6 В, ВК-8 В или ВУ-15.
Соединение резца со штангой бывает конусное, резьбовое, кулачковое с цилиндрическим хвостовиком и шплинтовое. Резцы подразделяют на углепородные типа РУ, например РУ13М (рис. 5, а) и породные типа РП, например РП42 (рис. 5, б).
Углепородный резец РУ13М предназначен для вращательного бурения по углю сопротивляемостью резанию свыше 150 Н/мм и породам с коэффициентом крепости /<6. Он состоит из стального корпуса, режущая головка которого армирована двумя пластинами твердого сплава. Отверстие диаметром 4 мм на хвостовике резца предназначено дли его закрепления в буровой штанге отрезком проволоки.
Породный резец РП42 предназначен для буровых штанг колонковых сверл и бурильных машин при вращательном бурении шпуров с промывкой в породах с f = 5—12. Он состоит из стального корпуса, режущая головка которого армирована двумя пластинками твердого сплава. Конусное отверстие в хвостовике резца предназначено для соединения резца со штангой. Цилиндрическое отверстие, расположенное по оси резца, служит для подвода промывочной жидкости в зону резания.
Для ударно-поворотного бурения используют буровые коронки, выпускаемые Кузнецким машиностроительным заводом. Буровые коронки делятся по числу породоразрушающих лезвий на долотчатые, трехперые и крестовые. Форма твердосплавного вооружения бывает пластинчатой и штыревой.
Буровая коронка состоит из корпуса, изготовляемого из углеродистой инструментальной стали, армируемого твердым сплавом. Для промывки шпура в коронке предусматривается канал (отверстие).
В зависимости от армирования коронок пластинами твердого сплава (П) и штырями (Ш) различают коронки: долотчатые— (КДП (рис. 5, в) и КДШ); трехперые — КТП и КТШ; четырехперые крестовые— (ККП (рис. 5, г) и ККШ); Х-образные — КХП и КХШ. Обычно для пород с коэффициентов крепости f=12 рекомендуется пластина из твердого сплава ВК-15; при f= 10−12 — ВК-8 и ВК-8 В и при f=10 —ВК-6 и ВК-6 В.
Буровые коронки соединяются со штангой с помощью конусного соединения; конусность принимается 1:8. Применяется также соединение штанг с коронками с помощью веревочной резьбы, облегчающей съем коронок со штанги (коронки ККП60−32 В и КТШ52−32В).
Более производительными и мощными машинами являются буровые станки. Рассмотрим, к примеру, станок БГА-4.
Станок БГА-4 предназначен, для бурения скважин по углю диаметром 390 и 500 мм с последующим разбуриванием обратным ходом до 850 мм, длиной при наклоне скважины 0—45° до 80 м (при применении шнековых бурильных штанг) и при наклоне 45—90° до 150 м.
Гидрокинематическая схема бурового станка БГА-4 приведена на рис. 6. Она предусматривает передачу вращения от электродвигателя M1 буровому инструменту через двухскоростной редуктор посредством цилиндрических зубчатых пар 1—2, 3—4, 5—6 или 7—8 и зубчатой муфты 9. От муфты вращение передается шлицевой втулке, которая через шлицевой вал (шпиндель) соединяется с корпусом бурового замка 10. Замок служит для присоединения бурового става. Таким образом достигаются две частоты вращения бурового става — 75 и 123 об/мин.
Замок связан траверсой 11 со штоками двух гидродомкратов подачи 15 и 17 так, что может совершать одновременно вращательное и поступательное (вдоль оси) движения. Масло под давлением от маслостанции поступает в полости этих гидродомкратов через систему маслоприводов 12, 13 или 14, 16. Электродвигатель 18 мощностью 3 кВт через редуктор 19 приводит в действие два шестеренных насоса 20 и 21 общей подачей 35 л/мин. Из маслобака 22 масло подается насосами в гидросистему.
При бурении скважины став перемещается вверх с рабочей скоростью от 0 до 1,3 м/мин. При этом масло от основного насоса 20 через обратный клапан 23 и золотник управления 28 поступает в поршневые полости обоих гидродомкратов подачи 15 и 17. Рабочее давление при этом (около 10 МПа) регулируется предохранительным клапаном 24. Масло из штоковых полостей гидроцилиндров сливается через дроссель 25, которым регулируется скорость подачи бурового става. Управление дросселем осуществляется приводом дросселя, который связан со станцией управления САУБ-У5. При бурении второй насос 21 через открытый золотник 27 сливает рабочую жидкость в маслобак.
Обратный клапан 26 при этом закрывает слив масла от насоса 20.
При разбуривании скважины (рабочая подача вниз со скоростью от 0 до 1,1 м/мин) золотником управления 28 изменяется направление потока масла в гидросистеме. Масло подается в штоковые (верхние) полости гидродомкратов, а сливается из поршневых (нижних).
При маневровой скорости перемещения бурового става вверх (от 0 до 2,8 м/мин) или вниз (от 0 до 4,1 м/мин) оба насоса подают масло в гидросистему через золотник 28 в верхние или нижние полости гидродомкратов. Масло при этом сливается в маслобак через золотник 28, минуя дроссель.
Основным рабочим инструментов буровых станков является буровой став. Рассмотрим более подробно его устройство на примере бурового става станка шарошечного бурения. Буровой став образуют шарошечное долото и буровые штанги, соединенные вместе.
В комплект буровых штанг входят одна концевая штанга и несколько рабочих. Концевая штанга (забурник) устанавливается между долотом и рабочей штангой (рис. 7). Выполняется она из толстостенной трубы 1, в которую с обоих концов вварены вставки 2 и 3, снабженные внутренней конической резьбой и каналами для прохода сжатого воздуха. В гнезде верхней вставки 3 имеется еще коническая резьба 4 меньшего диаметра, служащая для присоединения к штанге шпинделя вертлюга.
Рабочая штанга 5 имеет большую длину и отличается от концевой конструкцией нижнего хвостовика, который выполнен с наружной конической резьбой.
Диаметр штанг принимается на 20—50 мм меньше диаметра долота для удаления буровой мелочи из скважины.
Изготовляются штанги из стальных бесшовных холодноили горячекатаных труб.