ΠΡΡΠ»Π΅Π΄ΠΎΠ²Π°Π½ΠΈΠ΅ Π²Π»ΠΈΡΠ½ΠΈΡ ΡΠ΅Ρ Π½ΠΎΠ»ΠΎΠ³ΠΈΡΠ΅ΡΠΊΠΈΡ ΠΏΠ°ΡΠ°ΠΌΠ΅ΡΡΠΎΠ² Π²Π½Π΅ΠΏΠ΅ΡΠ½ΠΎΠΉ ΠΎΠ±ΡΠ°Π±ΠΎΡΠΊΠΈ Π½Π° ΠΊΠ°ΡΠ΅ΡΡΠ²ΠΎ ΡΡΠ°Π»ΠΈ
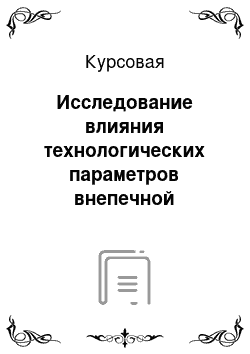
Π£ΡΡΠ°Π½ΠΎΠ²ΠΊΠ° Π΄Π»Ρ ΠΈΡΡΠ»Π΅Π΄ΠΎΠ²Π°Π½ΠΈΡ ΠΊΠΈΠ½Π΅ΠΌΠ°ΡΠΈΡΠ΅ΡΠΊΠΎΠΉ Π²ΡΠ·ΠΊΠΎΡΡΠΈ ΠΆΠΈΠ΄ΠΊΠΈΡ ΠΌΠ΅ΡΠ°Π»Π»ΠΎΠ², ΡΡΡΡΠΎΠΉΡΡΠ²ΠΎ ΠΊΠΎΡΠΎΡΠΎΠΉ ΠΏΠΎΠΊΠ°Π·Π°Π½ΠΎ Π½Π° ΡΠΈΡ. 2.2, 2.3, 2.4, Π²ΠΊΠ»ΡΡΠ°Π΅Ρ Π²ΡΡΠΎΠΊΠΎΡΠ΅ΠΌΠΏΠ΅ΡΠ°ΡΡΡΠ½ΡΠΉ Π²ΠΈΡΠΊΠΎΠ·ΠΈΠΌΠ΅ΡΡ, Π²Π°ΠΊΡΡΠΌΠ½ΡΡ ΡΠΈΡΡΠ΅ΠΌΡ, ΡΠΈΡΡΠ΅ΠΌΡ ΡΠ»Π΅ΠΊΡΡΠΎΠΏΠΈΡΠ°Π½ΠΈΡ, ΡΠΈΡΡΠ΅ΠΌΡ Π²ΠΎΠ΄ΡΠ½ΠΎΠ³ΠΎ ΠΎΡ Π»Π°ΠΆΠ΄Π΅Π½ΠΈΡ, ΡΠΈΡΡΠ΅ΠΌΡ ΠΏΠΎΠ΄Π°ΡΠΈ Π³Π°Π·ΠΎΠ², ΡΠΈΡΡΠ΅ΠΌΡ ΠΊΠΎΠ½ΡΡΠΎΠ»ΡΠ½ΠΎ-ΠΈΠ·ΠΌΠ΅ΡΠΈΡΠ΅Π»ΡΠ½ΡΡ ΠΏΡΠΈΠ±ΠΎΡΠΎΠ². ΠΠΈΡΠΊΠΎΠ·ΠΈΠΌΠ΅ΡΡ (ΡΠΈΡ. 2.3) ΠΏΡΠ΅Π΄ΡΡΠ°Π²Π»Π΅Π½ Π²ΡΡΠΎΠΊΠΎΡΠ΅ΠΌΠΏΠ΅ΡΠ°ΡΡΡΠ½ΠΎΠΉ Π²Π°ΠΊΡΡΠΌΠ½ΠΎΠΉ ΡΠ»Π΅ΠΊΡΡΠΎΠΏΠ΅ΡΡΡ ΡΠΎΠΏΡΠΎΡΠΈΠ²Π»Π΅Π½ΠΈΡ… Π§ΠΈΡΠ°ΡΡ Π΅ΡΡ >
ΠΡΡΠ»Π΅Π΄ΠΎΠ²Π°Π½ΠΈΠ΅ Π²Π»ΠΈΡΠ½ΠΈΡ ΡΠ΅Ρ Π½ΠΎΠ»ΠΎΠ³ΠΈΡΠ΅ΡΠΊΠΈΡ ΠΏΠ°ΡΠ°ΠΌΠ΅ΡΡΠΎΠ² Π²Π½Π΅ΠΏΠ΅ΡΠ½ΠΎΠΉ ΠΎΠ±ΡΠ°Π±ΠΎΡΠΊΠΈ Π½Π° ΠΊΠ°ΡΠ΅ΡΡΠ²ΠΎ ΡΡΠ°Π»ΠΈ (ΡΠ΅ΡΠ΅ΡΠ°Ρ, ΠΊΡΡΡΠΎΠ²Π°Ρ, Π΄ΠΈΠΏΠ»ΠΎΠΌ, ΠΊΠΎΠ½ΡΡΠΎΠ»ΡΠ½Π°Ρ)
ΠΠ΄Π½ΠΎΠΉ ΠΈΠ· ΠΎΡΠ½ΠΎΠ²Π½ΡΡ ΡΠ΅Π½Π΄Π΅Π½ΡΠΈΠΉ ΠΌΠΈΡΠΎΠ²ΠΎΠ³ΠΎ ΠΏΡΠΎΠΌΡΡΠ»Π΅Π½Π½ΠΎΠ³ΠΎ ΡΠ°Π·Π²ΠΈΡΠΈΡ ΡΠ²Π»ΡΠ΅ΡΡΡ ΡΠ½ΠΈΠΆΠ΅Π½ΠΈΠ΅ ΡΠ΄Π΅Π»ΡΠ½ΡΡ ΡΠ°ΡΡ ΠΎΠ΄ΠΎΠ² ΠΊΠΎΠ½ΡΡΡΡΠΊΡΠΈΠΎΠ½Π½ΡΡ ΠΌΠ°ΡΠ΅ΡΠΈΠ°Π»ΠΎΠ². Π ΡΡΠ»ΠΎΠ²ΠΈΡΡ ΠΊΠΎΠ½ΠΊΡΡΠ΅Π½ΡΠΈΠΈ Ρ Π½ΠΎΠ²ΡΠΌΠΈ ΠΌΠ°ΡΠ΅ΡΠΈΠ°Π»Π°ΠΌΠΈ Π½Π° ΠΎΡΠ½ΠΎΠ²Π΅ ΡΠ²Π΅ΡΠ½ΡΡ ΠΌΠ΅ΡΠ°Π»Π»ΠΎΠ² (Al, Ti), ΠΊΠ΅ΡΠ°ΠΌΠΈΠΊΠΈ, ΠΏΠ»Π°ΡΡΠΌΠ°ΡΡ, ΡΠ³Π»Π΅Π²ΠΎΠ»ΠΎΠΊΠ½Π° ΠΈ ΠΊΠΎΠΌΠΏΠΎΠ·ΠΈΡΠΎΠ², Π° ΡΠ°ΠΊΠΆΠ΅ ΡΠ°ΡΡΠΈΡΠ΅Π½ΠΈΡ ΡΡΠ΅ΡΡ ΡΠΊΡΠΏΠ»ΡΠ°ΡΠ°ΡΠΈΠΈ ΠΌΠ°ΡΠ΅ΡΠΈΠ°Π»ΠΎΠ² Π² ΡΠΊΡΡΡΠ΅ΠΌΠ°Π»ΡΠ½ΡΡ ΡΡΠ»ΠΎΠ²ΠΈΡΡ Π²ΡΡΠΎΠΊΠΈΡ Π΄Π°Π²Π»Π΅Π½ΠΈΠΉ, ΠΏΠΎΠ½ΠΈΠΆΠ΅Π½Π½ΡΡ ΠΈ ΠΏΠΎΠ²ΡΡΠ΅Π½Π½ΡΡ ΡΠ΅ΠΌΠΏΠ΅ΡΠ°ΡΡΡ, ΠΊΠΎΠ½ΡΠ°ΠΊΡΠ° Ρ ΡΠ°Π·Π»ΠΈΡΠ½ΡΠΌΠΈ Π²ΠΈΠ΄Π°ΠΌΠΈ ΠΊΠΎΡΡΠΎΠ·ΠΈΠΎΠ½Π½ΡΡ ΡΡΠ΅Π΄ Π΄ΠΎΡΡΠ°ΡΠΎΡΠ½ΠΎ ΠΎΡΡΡΠΎ ΡΡΠΎΠΈΡ ΠΏΡΠΎΠ±Π»Π΅ΠΌΠ° ΠΏΠΎΠ²ΡΡΠ΅Π½ΠΈΡ ΠΊΠ°ΡΠ΅ΡΡΠ²Π° ΡΡΠ°Π»ΠΈ. ΠΠ΄Π½ΠΈΠΌ ΠΈΠ· ΠΏΡΡΠ΅ΠΉ ΡΠ΅ΡΠ΅Π½ΠΈΡ ΡΡΠΎΠΉ ΠΏΡΠΎΠ±Π»Π΅ΠΌΡ, Π½Π°ΡΡΠ΄Ρ Ρ ΡΠΎΠ²Π΅ΡΡΠ΅Π½ΡΡΠ²ΠΎΠ²Π°Π½ΠΈΠ΅ΠΌ ΡΠ»Π΅ΠΌΠ΅Π½ΡΠ½ΠΎΠ³ΠΎ ΡΠΎΡΡΠ°Π²Π° ΠΈ ΡΠ΅ΡΠΌΠΎΠΌΠ΅Ρ Π°Π½ΠΈΡΠ΅ΡΠΊΠΎΠΉ ΠΎΠ±ΡΠ°Π±ΠΎΡΠΊΠΈ, ΡΠ²Π»ΡΠ΅ΡΡΡ Π½Π°ΠΈΠ±ΠΎΠ»Π΅Π΅ ΠΏΠΎΠ»Π½ΠΎΠ΅ ΠΈΡΠΏΠΎΠ»ΡΠ·ΠΎΠ²Π°Π½ΠΈΠ΅ ΡΠ΅Ρ Π½ΠΎΠ»ΠΎΠ³ΠΈΡΠ΅ΡΠΊΠΈΡ Π²ΠΎΠ·ΠΌΠΎΠΆΠ½ΠΎΡΡΠ΅ΠΉ ΠΏΡΠΎΡΠ΅ΡΡΠΎΠ² Π²ΡΠΏΠ»Π°Π²ΠΊΠΈ ΠΈ Π²Π½Π΅ΠΏΠ΅ΡΠ½ΠΎΠΉ ΠΎΠ±ΡΠ°Π±ΠΎΡΠΊΠΈ ΠΆΠΈΠ΄ΠΊΠΎΠ³ΠΎ ΠΌΠ΅ΡΠ°Π»Π»Π°. ΠΡΠ½ΠΎΠ²Π½ΠΎΠ΅ Π²Π½ΠΈΠΌΠ°Π½ΠΈΠ΅ ΡΠ΄Π΅Π»ΡΠ΅ΡΡΡ ΠΏΠ΅ΡΠ΅Π³ΡΠ΅Π²Ρ ΠΌΠ΅ΡΠ°Π»Π»Π° Π΄ΠΎ ΠΎΠΏΡΠ΅Π΄Π΅Π»Π΅Π½Π½ΡΡ (ΠΊΡΠΈΡΠΈΡΠ΅ΡΠΊΠΈΡ ) ΡΠ΅ΠΌΠΏΠ΅ΡΠ°ΡΡΡ, ΠΎΠΏΡΠ΅Π΄Π΅Π»ΡΠ΅ΠΌΡΡ ΡΡΡΠΎΠΉΡΠΈΠ²ΠΎΡΡΡΡ Π½Π΅ΡΠ°Π²Π½ΠΎΠ²Π΅ΡΠ½ΡΡ ΠΌΠΈΠΊΡΠΎΠ³ΡΡΠΏΠΏΠΈΡΠΎΠ²ΠΎΠΊ Π°ΡΠΎΠΌΠΎΠ². ΠΠ° ΠΎΡΠ½ΠΎΠ²Π°Π½ΠΈΠΈ ΡΠ΅Π·ΡΠ»ΡΡΠ°ΡΠΎΠ² Π»Π°Π±ΠΎΡΠ°ΡΠΎΡΠ½ΡΡ ΠΈ ΠΏΡΠΎΠΌΡΡΠ»Π΅Π½Π½ΡΡ ΠΈΡΡΠ»Π΅Π΄ΠΎΠ²Π°Π½ΠΈΠΉ Π°Π½Π°Π»ΠΈΠ·ΠΈΡΡΠ΅ΡΡΡ Π²ΠΎΠ·ΠΌΠΎΠΆΠ½ΠΎΡΡΡ Π΄ΠΎΡΡΠΈΠΆΠ΅Π½ΠΈΡ ΡΠ°Π²Π½ΠΎΠ²Π΅ΡΠ½ΠΎΡΡΠΈ ΡΠ°ΡΠΏΠ»Π°Π²ΠΎΠ² ΡΠΆΠ΅ Π² ΠΏΡΠΎΡΠ΅ΡΡΠ΅ ΠΈΡ ΡΠΎΡΠΌΠΈΡΠΎΠ²Π°Π½ΠΈΡ Π² ΡΠ΅Ρ Π½ΠΎΠ»ΠΎΠ³ΠΈΡΠ΅ΡΠΊΠΈΡ ΡΡΠ»ΠΎΠ²ΠΈΡΡ Π²ΡΠΏΠ»Π°Π²ΠΊΠΈ ΠΈ ΠΎΠ±ΡΠ°Π±ΠΎΡΠΊΠΈ ΠΆΠΈΠ΄ΠΊΠΎΠ³ΠΎ ΠΌΠ΅ΡΠ°Π»Π»Π°, ΠΈΡΡΠ»Π΅Π΄ΠΎΠ²Π°Π½ΠΈΠ΅ Π·Π°ΠΊΠΎΠ½ΠΎΠΌΠ΅ΡΠ½ΠΎΡΡΠΈ ΡΠΎΡΠΌΠΈΡΠΎΠ²Π°Π½ΠΈΡ ΡΠ°ΡΠΏΠ»Π°Π²ΠΎΠ² ΠΏΡΠΈ ΠΏΠ»Π°Π²Π»Π΅Π½ΠΈΠΈ ΠΌΠ΅ΡΠ°Π»Π»ΠΈΡΠ΅ΡΠΊΠΎΠΉ ΡΠΈΡ ΡΡ, Π½Π°ΡΠ³Π»Π΅ΡΠΎΠΆΠΈΠ²Π°Π½ΠΈΠΈ, Π»Π΅Π³ΠΈΡΠΎΠ²Π°Π½ΠΈΠΈ ΠΈ ΠΌΠΈΠΊΡΠΎΠ»Π΅Π³ΠΈΡΠΎΠ²Π°Π½ΠΈΠΈ ΠΆΠΈΠ΄ΠΊΠΎΠ³ΠΎ ΠΌΠ΅ΡΠ°Π»Π»Π°.
1. ΠΠΎΡΡΠ°Π½ΠΎΠ²ΠΊΠ° Π·Π°Π΄Π°ΡΠΈ ΠΈΡΡΠ»Π΅Π΄ΠΎΠ²Π°Π½ΠΈΡ
Π²Π½Π΅ΠΏΠ΅ΡΠ½ΠΎΠΉ ΡΡΠ°Π»Ρ ΠΌΠ΅ΡΠ°Π»Π»ΠΈΡΠ΅ΡΠΊΠΈΠΉ ΡΠ°ΡΠΏΠ»Π°Π²
Π ΡΠΎΠ²ΡΠ΅ΠΌΠ΅Π½Π½ΡΡ ΡΠ΅Ρ Π½ΠΎΠ»ΠΎΠ³ΠΈΡΠ΅ΡΠΊΠΈΡ ΡΡ Π΅ΠΌΠ°Ρ Π·Π½Π°ΡΠΈΠΌΠΎΡΡΡ ΡΡΠ°ΠΏΠ° Π²Π½Π΅ΠΏΠ΅ΡΠ½ΠΎΠΉ ΠΎΠ±ΡΠ°Π±ΠΎΡΠΊΠΈ ΡΡΠ΅Π·Π²ΡΡΠ°ΠΉΠ½ΠΎ Π²ΡΡΠΎΠΊΠ°. ΠΠΌΠ΅Π½Π½ΠΎ Π½Π° Π²Π½Π΅ΠΏΠ΅ΡΠ½ΡΡ ΠΎΠ±ΡΠ°Π±ΠΎΡΠΊΡ, ΠΏΡΠ΅ΠΆΠ΄Π΅ Π²ΡΠ΅Π³ΠΎ, Π²ΠΎΠ·Π»Π°Π³Π°ΡΡΡΡ Π·Π°Π΄Π°ΡΠΈ ΠΏΠΎΠ»ΡΡΠ΅Π½ΠΈΡ ΡΡΠ΅Π±ΡΠ΅ΠΌΡΡ ΠΏΠ°ΡΠ°ΠΌΠ΅ΡΡΠΎΠ² ΠΊΠ°ΡΠ΅ΡΡΠ²Π° ΠΆΠΈΠ΄ΠΊΠΎΠ³ΠΎ ΠΌΠ΅ΡΠ°Π»Π»Π° ΠΈ ΡΠ΅Π³Π»Π°ΠΌΠ΅Π½ΡΠΈΡΠΎΠ²Π°Π½Π½ΠΎΠ³ΠΎ Π½ΠΎΡΠΌΠ°ΡΠΈΠ²Π½ΠΎΠΉ Π΄ΠΎΠΊΡΠΌΠ΅Π½ΡΠ°ΡΠΈΠ΅ΠΉ Ρ ΠΈΠΌΠΈΡΠ΅ΡΠΊΠΎΠ³ΠΎ ΡΠΎΡΡΠ°Π²Π°, ΠΎΠ±Π΅ΡΠΏΠ΅ΡΠ΅Π½ΠΈΡ ΠΎΠΏΡΠΈΠΌΠ°Π»ΡΠ½ΠΎΠ³ΠΎ ΡΠ΅ΠΌΠΏΠ΅ΡΠ°ΡΡΡΠ½ΠΎΠ³ΠΎ ΡΠ΅ΠΆΠΈΠΌΠ° ΡΠ°Π·Π»ΠΈΠ²ΠΊΠΈ.
ΠΡΠΎ ΠΊΠ°ΡΠ°Π΅ΡΡΡ ΠΈ Π·Π°Π΄Π°ΡΠΈ Π³Π»ΡΠ±ΠΎΠΊΠΎΠ³ΠΎ ΡΠ°ΡΠΊΠΈΡΠ»Π΅Π½ΠΈΡ ΠΌΠ΅ΡΠ°Π»Π»Π° ΠΈ ΡΠ°ΡΠΈΠ½ΠΈΡΠΎΠ²Π°Π½ΠΈΡ ΠΌΠ΅ΡΠ°Π»Π»Π° ΠΎΡ ΠΏΡΠΎΠ΄ΡΠΊΡΠΎΠ² ΡΠ°ΡΠΊΠΈΡΠ»Π΅Π½ΠΈΡ. Π’ΡΠ°Π΄ΠΈΡΠΈΠΎΠ½Π½ΠΎ ΡΡΠΈΡΠ°Π΅ΡΡΡ, ΡΡΠΎ ΡΡΡΠ΅ΠΊΡΠΈΠ²Π½ΠΎΡΡΡ ΠΎΡΠ°ΠΆΠ΄Π°ΡΡΠ΅Π³ΠΎ ΡΠ°ΡΠΊΠΈΡΠ»Π΅Π½ΠΈΡ ΠΎΠΏΡΠ΅Π΄Π΅Π»ΡΠ΅ΡΡΡ, ΠΏΡΠ΅ΠΆΠ΄Π΅ Π²ΡΠ΅Π³ΠΎ, ΡΠΎΠ·Π΄Π°Π½ΠΈΠ΅ΠΌ ΠΎΠΏΡΠΈΠΌΠ°Π»ΡΠ½ΡΡ ΡΠ΅ΡΠΌΠΎΠ΄ΠΈΠ½Π°ΠΌΠΈΡΠ΅ΡΠΊΠΈΡ ΡΡΠ»ΠΎΠ²ΠΈΠΉ. ΠΡΠΈ ΡΡΠΎΠΌ ΡΡΠ΅Ρ ΠΈΡΡ ΠΎΠ΄Π½ΠΎΠΉ ΠΎΠΊΠΈΡΠ»Π΅Π½Π½ΠΎΡΡΠΈ ΠΌΠ΅ΡΠ°Π»Π»Π° Π½Π΅ΠΎΠ±Ρ ΠΎΠ΄ΠΈΠΌ Π»ΠΈΡΡ Ρ ΡΠΎΡΠΊΠΈ Π·ΡΠ΅Π½ΠΈΡ ΠΎΠΏΡΠ΅Π΄Π΅Π»Π΅Π½ΠΈΡ ΠΎΠΏΡΠΈΠΌΠ°Π»ΡΠ½ΠΎΠ³ΠΎ ΡΠ°ΡΡ ΠΎΠ΄Π° ΡΠ°ΡΠΊΠΈΡΠ»ΠΈΡΠ΅Π»Π΅ΠΉ. Π‘ΡΠΈΡΠ°Π΅ΡΡΡ, ΡΡΠΎ ΠΈΡΠΏΠΎΠ»ΡΠ·ΠΎΠ²Π°Π½ΠΈΠ΅ ΠΏΡΠΎΠ΄ΡΠ²ΠΊΠΈ ΠΈΠ½Π΅ΡΡΠ½ΡΠΌ Π³Π°Π·ΠΎΠΌ ΠΏΠΎΠ·Π²ΠΎΠ»ΡΠ΅Ρ Π΄ΠΎΡΡΠ°ΡΠΎΡΠ½ΠΎ Π³Π»ΡΠ±ΠΎΠΊΠΎ ΡΠ°ΡΠΈΠ½ΠΈΡΠΎΠ²Π°ΡΡ ΠΌΠ΅ΡΠ°Π»Π» ΠΎΡ ΠΏΡΠΎΠ΄ΡΠΊΡΠΎΠ² ΡΠ°ΡΠΊΠΈΡΠ»Π΅Π½ΠΈΡ. Π‘ΠΎΠΎΡΠ²Π΅ΡΡΡΠ²Π΅Π½Π½ΠΎ, ΠΏΡΠΈ ΠΎΠΏΡΠΈΠΌΠ°Π»ΡΠ½ΠΎΠΌ ΡΠ°ΡΠΊΠΈΡΠ»Π΅Π½ΠΈΠΈ ΠΎΠΊΠΈΡΠ»Π΅Π½Π½ΠΎΡΡΡ ΠΏΠΎΠ»ΡΠΏΡΠΎΠ΄ΡΠΊΡΠ° Π½Π΅ Π΄ΠΎΠ»ΠΆΠ½Π° Π²Π»ΠΈΡΡΡ Π½Π° ΠΏΡΠΈΠΌΠ΅ΡΠ½ΡΠΉ ΡΠΎΡΡΠ°Π² Π³ΠΎΡΠΎΠ²ΠΎΠ³ΠΎ ΠΌΠ΅ΡΠ°Π»Π»Π°.
ΠΠ΄Π½Π°ΠΊΠΎ ΡΡΠΎ Π½Π΅ ΡΠ°ΠΊ. ΠΠΊΠΈΡΠ»Π΅Π½Π½ΠΎΡΡΡ ΠΏΠΎΠ»ΡΠΏΡΠΎΠ΄ΡΠΊΡΠ° Π²Π»ΠΈΡΠ΅Ρ Π½Π° ΡΠΎΠ΄Π΅ΡΠΆΠ°Π½ΠΈΠ΅ Π² Π»ΠΈΡΠΎΠΌ ΠΌΠ΅ΡΠ°Π»Π»Π΅ ΠΎΠ±ΡΠ΅Π³ΠΎ ΠΊΠΈΡΠ»ΠΎΡΠΎΠ΄Π°. ΠΠ½Π΅ΠΏΠ΅ΡΠ½Π°Ρ ΠΎΠ±ΡΠ°Π±ΠΎΡΠΊΠ° Π½Π΅ ΠΏΠΎΠ·Π²ΠΎΠ»ΡΠ΅Ρ Π½Π΅ΠΉΡΡΠ°Π»ΠΈΠ·ΠΎΠ²Π°ΡΡ Π½Π΅Π³Π°ΡΠΈΠ²Π½ΠΎΠ΅ Π²Π»ΠΈΡΠ½ΠΈΠ΅ ΠΏΠΎΠ²ΡΡΠ΅Π½Π½ΠΎΠΉ ΠΎΠΊΠΈΡΠ»Π΅Π½Π½ΠΎΡΡΠΈ ΠΌΠ΅ΡΠ°Π»Π»Π° Π½Π° Π²ΡΠΏΡΡΠΊΠ΅ ΠΈΠ· ΠΏΠ΅ΡΠΈ. ΠΠΎΡΡΠΎΠΌΡ ΠΎΠΏΡΠΈΠΌΠΈΠ·Π°ΡΠΈΡ ΠΎΠΊΠΈΡΠ»Π΅Π½Π½ΠΎΡΡΠΈ ΠΏΠΎΠ»ΡΠΏΡΠΎΠ΄ΡΠΊΡΠ° — ΠΎΠ΄Π½ΠΎ ΠΈΠ· Π½Π΅ΠΎΠ±Ρ ΠΎΠ΄ΠΈΠΌΡΡ ΡΡΠ»ΠΎΠ²ΠΈΠΉ ΠΎΠ±Π΅ΡΠΏΠ΅ΡΠ΅Π½ΠΈΡ Π²ΡΡΠΎΠΊΠΎΠ³ΠΎ ΠΊΠ°ΡΠ΅ΡΡΠ²Π° ΡΡΠ°Π»ΠΈ. Π‘ Π΄ΡΡΠ³ΠΎΠΉ ΡΡΠΎΡΠΎΠ½Ρ, ΠΎΡΠ΅Π²ΠΈΠ΄Π½ΠΎ, Π½Π΅Π»ΡΠ·Ρ ΠΎΡΡΠΈΡΠ°ΡΡ Π²Π»ΠΈΡΠ½ΠΈΠ΅ ΠΈ ΡΠ΅ΠΆΠΈΠΌΠΎΠ² ΡΠ°ΡΠΊΠΈΡΠ»Π΅Π½ΠΈΡ, ΠΌΠΎΠ΄ΠΈΡΠΈΡΠΈΡΠΎΠ²Π°Π½ΠΈΡ ΠΈ ΠΏΡΠΎΠ΄ΡΠ²ΠΊΠΈ ΠΈΠ½Π΅ΡΡΠ½ΡΠΌ Π³Π°Π·ΠΎΠΌ Π½Π° ΡΡΡΠ΅ΠΊΡΠΈΠ²Π½ΠΎΡΡΡ ΡΠ΅ΡΠ΅Π½ΠΈΡ Π·Π°Π΄Π°ΡΠΈ ΡΠ°ΡΠΈΠ½ΠΈΡΠΎΠ²Π°Π½ΠΈΡ ΠΎΡ ΠΊΠΈΡΠ»ΠΎΡΠΎΠ΄Π°. Π‘ΠΎΠΎΡΠ²Π΅ΡΡΡΠ²Π΅Π½Π½ΠΎ, ΠΎΠΏΡΠΈΠΌΠΈΠ·Π°ΡΠΈΡ ΠΎΡΠΌΠ΅ΡΠ΅Π½Π½ΡΡ ΠΏΠ°ΡΠ°ΠΌΠ΅ΡΡΠΎΠ² Π²Π½Π΅ΠΏΠ΅ΡΠ½ΠΎΠΉ ΠΎΠ±ΡΠ°Π±ΠΎΡΠΊΠΈ Π΄ΠΎΠ»ΠΆΠ½ΠΎ ΠΏΠΎΠ»ΠΎΠΆΠΈΡΠ΅Π»ΡΠ½ΠΎ ΡΠΊΠ°Π·Π°ΡΡΡΡ Π½Π° ΠΊΠ°ΡΠ΅ΡΡΠ²Π΅ ΡΡΠ°Π»ΠΈ.
Π‘ ΡΠΎΡΠΊΠΈ Π·ΡΠ΅Π½ΠΈΡ ΠΏΠΎΠ»ΡΡΠ΅Π½ΠΈΡ ΡΠΎΡΠ½ΠΎΠ³ΠΎ Ρ ΠΈΠΌΠΈΡΠ΅ΡΠΊΠΎΠ³ΠΎ ΡΠΎΡΡΠ°Π²Π° Π² Π±ΠΎΠ»ΡΡΠΈΠ½ΡΡΠ²Π΅ ΡΠ»ΡΡΠ°Π΅Π² ΠΎΡΠΈΠ΅Π½ΡΠΈΡΡΡΡΡΡ Π½Π° ΡΠ΅Π·ΡΠ»ΡΡΠ°ΡΡ Π°Π½Π°Π»ΠΈΠ·Π° Ρ ΠΈΠΌΠΈΡΠ΅ΡΠΊΠΎΠΉ Π»Π°Π±ΠΎΡΠ°ΡΠΎΡΠΈΠΈ. Π‘ Π΄ΡΡΠ³ΠΎΠΉ ΡΡΠΎΡΠΎΠ½Ρ, ΡΡΠΎΠ²Π΅Π½Ρ ΡΠΊΡΠΏΠ»ΡΠ°ΡΠ°ΡΠΈΠΎΠ½Π½ΡΡ ΡΠ²ΠΎΠΉΡΡΠ² ΠΌΠ΅ΡΠ°Π»Π»Π° ΡΡΡΠ± ΠΎΠ΄Π½ΠΎΠΉ ΠΌΠ°ΡΠΊΠΈ ΠΏΡΠΈ ΡΠ΅ΡΠΈΠΉΠ½ΠΎΠΉ ΡΠ΅Ρ Π½ΠΎΠ»ΠΎΠ³ΠΈΠΈ ΠΏΡΠΎΠΈΠ·Π²ΠΎΠ΄ΡΡΠ²Π°, ΠΏΡΠΈ ΠΎΠ΄Π½ΠΎΠΌ ΡΠ΅ΠΆΠΈΠΌΠ΅ ΡΠ΅ΡΠΌΠΎΠΎΠ±ΡΠ°Π±ΠΎΡΠΊΠΈ ΠΌΠΎΠΆΠ΅Ρ ΠΊΠΎΠ»Π΅Π±Π°ΡΡΡΡ Π² Π΄ΠΎΡΡΠ°ΡΠΎΡΠ½ΠΎ ΡΠΈΡΠΎΠΊΠΈΡ ΠΏΡΠ΅Π΄Π΅Π»Π°Ρ . ΠΠ°ΠΏΡΠΈΠΌΠ΅Ρ, ΡΠ΄Π°ΡΠ½Π°Ρ Π²ΡΠ·ΠΊΠΎΡΡΡ ΠΌΠΎΠΆΠ΅Ρ ΡΠ°Π·Π»ΠΈΡΠ°ΡΡΡΡ Π² 2 ΡΠ°Π·Π°. Π ΠΊΠ°ΡΠ΅ΡΡΠ²Π΅ Π³Π»Π°Π²Π½ΠΎΠΉ ΠΏΡΠΈΡΠΈΠ½Ρ Π½Π΅ΡΡΠ°Π±ΠΈΠ»ΡΠ½ΠΎΡΡΠΈ ΠΌΠΎΠΆΠ΅Ρ ΡΠ°ΡΡΠΌΠ°ΡΡΠΈΠ²Π°ΡΡΡΡ ΡΠ°Π·Π»ΠΈΡΠ½Π°Ρ ΡΡΠ΅ΠΏΠ΅Π½Ρ ΡΠ°Π²Π½ΠΎΠ²Π΅ΡΠ½ΠΎΡΡΠΈ ΠΈ, ΡΠΎΠΎΡΠ²Π΅ΡΡΡΠ²Π΅Π½Π½ΠΎ, Π΄Π΅ΡΠ΅ΠΊΡΠ½ΠΎΡΡΠΈ ΡΡΡΡΠΊΡΡΡΠ½ΠΎΠ³ΠΎ ΡΠΎΡΡΠΎΡΠ½ΠΈΡ ΠΌΠ΅ΡΠ°Π»Π»Π°. ΠΡΠ½ΠΎΠ²Π½ΠΎΠ΅ Π½Π°ΠΏΡΠ°Π²Π»Π΅Π½ΠΈΠ΅ Π²ΠΎΠ·Π΄Π΅ΠΉΡΡΠ²ΠΈΡ Π½Π° ΡΡΡΡΠΊΡΡΡΠ½ΠΎΠ΅ ΡΠΎΡΡΠΎΡΠ½ΠΈΠ΅ ΠΌΠ΅ΡΠ°Π»Π»Π° Ρ ΡΠ΅Π»ΡΡ ΠΏΠΎΠ²ΡΡΠ΅Π½ΠΈΡ Π΅Π³ΠΎ ΡΠ°Π²Π½ΠΎΠ²Π΅ΡΠ½ΠΎΡΡΠΈ — ΡΠΎΠ·Π΄Π°Π½ΠΈΠ΅ ΠΎΠΏΡΠΈΠΌΠ°Π»ΡΠ½ΡΡ ΡΡΠ»ΠΎΠ²ΠΈΠΉ Π΄Π»Ρ ΡΠΎΡΠΌΠΈΡΠΎΠ²Π°Π½ΠΈΡ ΠΌΠΈΠΊΡΠΎΠΎΠ΄Π½ΠΎΡΠΎΠ΄Π½ΠΎΠ³ΠΎ, ΡΠ°Π²Π½ΠΎΠ²Π΅ΡΠ½ΠΎΠ³ΠΎ ΡΡΡΡΠΊΡΡΡΠ½ΠΎΠ³ΠΎ ΡΠΎΡΡΠΎΡΠ½ΠΈΡ ΡΠ°ΡΠΏΠ»Π°Π²Π°, Π΄Π»Ρ ΠΌΠ°ΠΊΡΠΈΠΌΠ°Π»ΡΠ½ΠΎΠΉ ΡΠ΅Π»Π°ΠΊΡΠ°ΡΠΈΠΈ Π²ΡΠ΅Ρ Π²Π½Π΅ΡΠ΅Π½Π½ΡΡ Π½Π΅ΡΠ°Π²Π½ΠΎΠ²Π΅ΡΠ½ΠΎΡΡΠ΅ΠΉ Π² ΡΠ΅Π·ΡΠ»ΡΡΠ°ΡΠ΅ Π΄Π΅ΡΡΠ°Π±ΠΈΠ»ΠΈΠ·ΠΈΡΡΡΡΠ΅Π³ΠΎ Π²ΠΎΠ·Π΄Π΅ΠΉΡΡΠ²ΠΈΡ ΠΏΠ»Π°Π²Π»Π΅Π½ΠΈΡ, Π»Π΅Π³ΠΈΡΠΎΠ²Π°Π½ΠΈΡ, Π½Π°ΡΠ³Π»Π΅ΡΠΎΠΆΠΈΠ²Π°Π½ΠΈΡ ΠΈ Ρ. ΠΏ.
ΠΡΠΈ ΠΏΠ΅ΡΠ΅Ρ ΠΎΠ΄Π΅ Π½Π° Π²ΡΠΏΠ»Π°Π²ΠΊΡ ΠΏΠΎΠ»ΡΠΏΡΠΎΠ΄ΡΠΊΡΠ° Π² ΠΠ‘Π ΡΠΎΡ ΡΠ°Π½ΠΈΠ»ΠΈΡΡ Π·Π½Π°ΡΠΈΡΠ΅Π»ΡΠ½ΡΠ΅ ΠΊΠΎΠ»Π΅Π±Π°Π½ΠΈΡ Ρ ΠΈΠΌΠΈΡΠ΅ΡΠΊΠΎΠ³ΠΎ ΡΠΎΡΡΠ°Π²Π° ΠΌΠ΅ΡΠ°Π»Π»Π° ΠΏΠΎ ΠΏΡΠΈΡ ΠΎΠ΄Ρ Π½Π° ΠΠΠ. Π‘ΠΎΠΎΡΠ²Π΅ΡΡΡΠ²Π΅Π½Π½ΠΎ, ΡΠΎΡ ΡΠ°Π½ΠΈΠ»Π°ΡΡ Π½Π΅ΡΡΠ°Π±ΠΈΠ»ΡΠ½ΠΎΡΡΡ Π²Π΅Π»ΠΈΡΠΈΠ½Ρ ΠΊΠΎΡΡΠ΅ΠΊΡΠΈΡΡΡΡΠΈΡ Π΄ΠΎΠ±Π°Π²ΠΎΠΊ. Π‘ ΡΡΠ΅ΡΠΎΠΌ ΠΊΠΎΠ»Π΅Π±Π°Π½ΠΈΠΉ ΡΠ΅ΠΌΠΏΠ΅ΡΠ°ΡΡΡΠ½ΠΎΠ³ΠΎ ΡΠ΅ΠΆΠΈΠΌΠ° ΠΎΠ±ΡΠ°Π±ΠΎΡΠΊΠΈ, Π²ΡΠ΅ΠΌΠ΅Π½Π½ΠΎΠ³ΠΎ ΡΠ΅ΠΆΠΈΠΌΠ° Π²Π²ΠΎΠ΄Π° Π΄ΠΎΠ±Π°Π²ΠΎΠΊ, ΡΠ΅ΠΆΠΈΠΌΠΎΠ² ΡΠ°ΡΠΊΠΈΡΠ»Π΅Π½ΠΈΡ ΠΈ ΠΏΡΠΎΠ΄ΡΠ²ΠΊΠΈ ΠΈΠ½Π΅ΡΡΠ½ΡΠΌ Π³Π°Π·ΠΎΠΌ ΡΡΠΎ ΠΏΡΠ΅Π΄ΠΎΠΏΡΠ΅Π΄Π΅Π»ΠΈΠ»ΠΎ ΡΠΎΡ ΡΠ°Π½Π΅Π½ΠΈΠ΅ ΡΡΡΠ΅ΡΡΠ²Π΅Π½Π½ΡΡ ΡΠ°Π·Π»ΠΈΡΠΈΠΉ ΡΡΠ»ΠΎΠ²ΠΈΠΉ ΡΠΎΡΠΌΠΈΡΠΎΠ²Π°Π½ΠΈΡ ΡΠ°ΡΠΏΠ»Π°Π²ΠΎΠ². ΠΠ΅ΡΠΎΠΌΠ½Π΅Π½Π½ΠΎ, ΡΡΠΎ ΠΌΠΎΠΆΠ΅Ρ ΡΠ°ΡΡΠΌΠ°ΡΡΠΈΠ²Π°ΡΡ Π² ΠΊΠ°ΡΠ΅ΡΡΠ²Π΅ ΠΎΠ΄Π½ΠΎΠΉ ΠΈΠ· Π³Π»Π°Π²Π½ΡΡ ΠΏΡΠΈΡΠΈΠ½ ΠΊΠΎΠ»Π΅Π±Π°Π½ΠΈΠΉ ΡΠΊΡΠΏΠ»ΡΠ°ΡΠ°ΡΠΈΠΎΠ½Π½ΡΡ ΡΠ²ΠΎΠΉΡΡΠ² ΠΌΠ΅ΡΠ°Π»Π»Π° ΠΎΠ΄Π½ΠΎΠΉ ΠΌΠ°ΡΠΊΠΈ (ΡΠ°Π±Π»ΠΈΡΠ°). ΠΠΎΡΡΠΎΠΌΡ Π°Π½Π°Π»ΠΈΠ· Π½Π°ΠΏΡΠ°Π²Π»Π΅Π½ΠΈΠΉ ΠΎΠΏΡΠΈΠΌΠΈΠ·Π°ΡΠΈΠΈ ΡΠ΅Ρ Π½ΠΎΠ»ΠΎΠ³ΠΈΠΈ Π²Π½Π΅ΠΏΠ΅ΡΠ½ΠΎΠΉ ΠΎΠ±ΡΠ°Π±ΠΎΡΠΊΠΈ ΠΈ Ρ ΡΠΎΡΠΊΠΈ Π·ΡΠ΅Π½ΠΈΡ ΠΏΠΎΠ²ΡΡΠ΅Π½ΠΈΡ ΡΠ°Π²Π½ΠΎΠ²Π΅ΡΠ½ΠΎΡΡΠΈΠΈ ΡΡΡΡΠΊΡΡΡΠ½ΠΎΠ³ΠΎ ΡΠΎΡΡΠΎΡΠ½ΠΈΡ ΠΌΠ΅ΡΠ°Π»Π»Π° ΡΠ²Π»ΡΠ΅ΡΡΡ Π²Π΅ΡΡΠΌΠ° Π·Π½Π°ΡΠΈΠΌΡΠΌ.
Π’Π°ΠΊΠΈΠΌ ΠΎΠ±ΡΠ°Π·ΠΎΠΌ, ΠΎΡΠ½ΠΎΠ²Π½ΡΠΌΠΈ Π·Π°Π΄Π°ΡΠ°ΠΌΠΈ ΠΈΡΡΠ»Π΅Π΄ΠΎΠ²Π°Π½ΠΈΡ ΡΠ²Π»ΡΠ»ΠΈΡΡ:
1. ΠΡΠ΅Π½ΠΊΠ° Π²Π»ΠΈΡΠ½ΠΈΡ ΡΠ΅Ρ Π½ΠΎΠ»ΠΎΠ³ΠΈΡΠ΅ΡΠΊΠΈΡ ΠΏΠ°ΡΠ°ΠΌΠ΅ΡΡΠΎΠ² ΠΎΠ±ΡΠ°Π±ΠΎΡΠΊΠΈ Π½Π° ΠΠΠ Π½Π° ΡΠΎΠ΄Π΅ΡΠΆΠ°Π½ΠΈΠ΅ Π² ΠΌΠ΅ΡΠ°Π»Π»Π΅ ΠΎΠ±ΡΠ΅Π³ΠΎ ΠΊΠΈΡΠ»ΠΎΡΠΎΠ΄Π°.
2. ΠΡΡΠ»Π΅Π΄ΠΎΠ²Π°Π½ΠΈΠ΅ Π²Π»ΠΈΡΠ½ΠΈΡ ΡΠ΅Ρ Π½ΠΎΠ»ΠΎΠ³ΠΈΡΠ΅ΡΠΊΠΈΡ ΠΏΠ°ΡΠ°ΠΌΠ΅ΡΡΠΎΠ² ΠΎΠ±ΡΠ°Π±ΠΎΡΠΊΠΈ Π½Π° ΠΠΠ Π½Π° ΡΠ°Π²Π½ΠΎΠ²Π΅ΡΠ½ΠΎΡΡΡ ΡΡΡΡΠΊΡΡΡΠ½ΠΎΠ³ΠΎ ΡΠΎΡΡΠΎΡΠ½ΠΈΡ ΠΌΠ΅ΡΠ°Π»Π»Π°.
Π’Π°Π±Π»ΠΈΡΠ°1
Π‘ΡΠ°Π²Π½Π΅Π½ΠΈΠ΅ ΡΡΠ°Π±ΠΈΠ»ΡΠ½ΠΎΡΡΠΈ ΡΠΊΡΠΏΠ»ΡΠ°ΡΠ°ΡΠΈΠΎΠ½Π½ΡΡ ΡΠ²ΠΎΠΉΡΡΠ² ΡΡΠ°Π»ΠΈ Π ΠΏΡΠΈ ΡΠ°Π·Π»ΠΈΡΠ½ΠΎΠΉ ΡΠ΅Ρ Π½ΠΎΠ»ΠΎΠ³ΠΈΠΈ Π²ΡΠΏΠ»Π°Π²ΠΊΠΈ ΠΏΠΎΠ»ΡΠΏΡΠΎΠ΄ΡΠΊΡΠ°
Π’ΠΈΠΏΠΎΡΠ°Π·ΠΌΠ΅Ρ ΡΡΡΠ±Ρ, ΠΌΠΌΠ§ΠΌΠΌ | Π’Π΅Ρ Π½ΠΎΠ»ΠΎΠ³ΠΈΡ Π²ΡΠΏΠ»Π°Π²ΠΊΠΈ ΠΏΠΎΠ»ΡΠΏΡΠΎΠ΄ΡΠΊΡΠ° | ΠΠΎΠ»-Π²ΠΎ ΠΏΠ°ΡΡΠΈΠΉ | ΠΠ΅Ρ Π°Π½ΠΈΡΠ΅ΡΠΊΠΈΠ΅ ΡΠ²ΠΎΠΉΡΡΠ²Π° ΠΌΠ΅ΡΠ°Π»Π»Π° ΡΡΡΠ± | |||
ΡΡ, ΠΠΠ° | ΡΠ², ΠΠΠ° | Π΄, % | ||||
max min | max min | max min | ||||
245Π§7,9 | ΠΠ°ΡΡΠ΅Π½ΠΎΠ²ΡΠΊΠ°Ρ ΠΏΠ΅ΡΡ | 1.32 | 1.20 | 1.86 | ||
ΠΠ‘Π | 1.38 | 1.21 | 1.86 | |||
245Π§8,9 | ΠΠ°ΡΡΠ΅Π½ΠΎΠ²ΡΠΊΠ°Ρ ΠΏΠ΅ΡΡ | 1.29 | 1.21 | 1.79 | ||
ΠΠ‘Π | 1.28 | 1.19 | 2.03 | |||
245Π§10 | ΠΠ°ΡΡΠ΅Π½ΠΎΠ²ΡΠΊΠ°Ρ ΠΏΠ΅ΡΡ | 1.28 | 1.17 | 1.66 | ||
ΠΠ‘Π | 1.27 | 1.18 | 1.57 | |||
324Π§9,5 | ΠΠ°ΡΡΠ΅Π½ΠΎΠ²ΡΠΊΠ°Ρ ΠΏΠ΅ΡΡ | 1.40 | 1.23 | 1.73 | ||
ΠΠ‘Π | 1.37 | 1.16 | 2.36 | |||
324Π§11 | ΠΠ°ΡΡΠ΅Π½ΠΎΠ²ΡΠΊΠ°Ρ ΠΏΠ΅ΡΡ | 1.37 | 1.16 | 1.62 | ||
ΠΠ‘Π | 1.16 | 1.18 | 1.52 | |||
245Π§11,1 | ΠΠ°ΡΡΠ΅Π½ΠΎΠ²ΡΠΊΠ°Ρ ΠΏΠ΅ΡΡ | 1.28 | 1.15 | 1.57 | ||
ΠΠ‘Π | 1.35 | 1.16 | 1.35 | |||
Π‘ΡΠ΅Π΄Π½Π΅Π΅ ΠΏΠΎ ΡΠΈΠΏΠΎΡΠ°Π·ΠΌΠ΅ΡΠ°ΠΌ | ΠΠ°ΡΡΠ΅Π½ΠΎΠ²ΡΠΊΠ°Ρ ΠΏΠ΅ΡΡ | 1.32 | 1.19 | 1.71 | ||
ΠΠ‘Π | 1.30 | 1.18 | 1.78 | |||
2. ΠΠ΅ΡΠΎΠ΄ΠΈΠΊΠ° ΠΈΡΡΠ»Π΅Π΄ΠΎΠ²Π°Π½ΠΈΠΉ
Π Ρ ΠΎΠ΄Π΅ ΡΠ°Π±ΠΎΡΡ Π΄Π»Ρ ΡΡΠ΄Π° ΠΏΠ»Π°Π²ΠΎΠΊ ΡΡΠ°Π»ΠΈ Π Π±ΡΠ»ΠΎ ΠΈΡΡΠ»Π΅Π΄ΠΎΠ²Π°Π½ΠΎ ΡΠΎΠ΄Π΅ΡΠΆΠ°Π½ΠΈΠ΅ Π² ΠΌΠ΅ΡΠ°Π»Π»Π΅ ΠΎΠ±ΡΠ΅Π³ΠΎ ΠΊΠΈΡΠ»ΠΎΡΠΎΠ΄Π° ΠΈ ΠΏΡΠΎΠ²Π΅Π΄Π΅Π½Π° ΠΎΡΠ΅Π½ΠΊΠ° ΡΠ°Π²Π½ΠΎΠ²Π΅ΡΠ½ΠΎΡΡΠΈ ΡΠ°ΡΠΏΠ»Π°Π²Π°. ΠΠ΅ΡΠΎΠ΄ΠΈΠΊΠ° ΠΈΡΡΠ»Π΅Π΄ΠΎΠ²Π°Π½ΠΈΠΉ ΠΏΡΠ΅Π΄ΡΡΠ°Π²Π»Π΅Π½Π° Π½ΠΈΠΆΠ΅.
2.1 ΠΠ΅ΡΠΎΠ΄ΠΈΠΊΠ° ΠΈΡΡΠ»Π΅Π΄ΠΎΠ²Π°Π½ΠΈΡ Π³Π°Π·ΠΎΠ½Π°ΡΡΡΠ΅Π½Π½ΠΎΡΡΠΈ ΡΡΠ°Π»ΠΈ ΠΡΠ°ΡΠΊΠΎΠ΅ ΠΎΠΏΠΈΡΠ°Π½ΠΈΠ΅ Π³Π°Π·ΠΎΠ°Π½Π°Π»ΠΈΠ·Π°ΡΠΎΡΠ°.
ΠΠ°Π·ΠΎΠ°Π½Π°Π»ΠΈΠ·Π°ΡΠΎΡ ΠNΠ 2000 ΡΠ°Π·ΡΠ°Π±ΠΎΡΠ°Π½, ΠΏΡΠ΅ΠΆΠ΄Π΅ Π²ΡΠ΅Π³ΠΎ, Π΄Π»Ρ Π°Π½Π°Π»ΠΈΠ·Π° Π³Π°Π·ΠΎΠ² Π² ΠΌΠ΅ΡΠ°Π»Π»Π°Ρ . ΠΠ»Ρ ΠΎΠΏΡΠ΅Π΄Π΅Π»Π΅Π½ΠΈΡ ΡΠΎΠ΄Π΅ΡΠΆΠ°Π½ΠΈΡ ΠΊΠΈΡΠ»ΠΎΡΠΎΠ΄Π°, Π°Π·ΠΎΡΠ° ΠΈ Π²ΠΎΠ΄ΠΎΡΠΎΠ΄Π° ΠΈΡΠΏΠΎΠ»ΡΠ·ΡΠ΅ΡΡΡ ΠΌΠ΅ΡΠΎΠ΄ Π²ΠΎΡΡΡΠ°Π½ΠΎΠ²ΠΈΡΠ΅Π»ΡΠ½ΠΎΠ³ΠΎ ΠΏΠ»Π°Π²Π»Π΅Π½ΠΈΡ. ΠΠ»Ρ ΡΡΠΎΠ³ΠΎ Π³Π°Π·ΠΎΠ°Π½Π°Π»ΠΈΠ·Π°ΡΠΎΡ ΠΎΡΠ½Π°ΡΠ΅Π½ ΠΈΠΌΠΏΡΠ»ΡΡΠ½ΠΎΠΉ ΠΏΠ΅ΡΡΡ, Π² ΡΠ°Π±ΠΎΡΠ΅ΠΌ ΠΏΡΠΎΡΡΡΠ°Π½ΡΡΠ²Π΅ ΠΊΠΎΡΠΎΡΠΎΠΉ, Π³Π΅ΡΠΌΠ΅ΡΠΈΡΠ½ΠΎ ΠΈΠ·ΠΎΠ»ΠΈΡΠΎΠ²Π°Π½Π½ΠΎΠΌ ΠΎΡ ΠΎΠΊΡΡΠΆΠ°ΡΡΠ΅ΠΉ Π°ΡΠΌΠΎΡΡΠ΅ΡΡ, Π² ΡΡΠ»ΠΎΠ²ΠΈΡΡ ΠΏΠΎΡΡΠΎΡΠ½Π½ΠΎΠ³ΠΎ ΠΏΠΎΡΠΎΠΊΠ° Π³Π°Π·Π°-Π½ΠΎΡΠΈΡΠ΅Π»Ρ ΠΎΠ±ΡΠ°Π·Π΅Ρ ΠΏΠ»Π°Π²ΠΈΡΡΡ Π² Π³ΡΠ°ΡΠΈΡΠΎΠ²ΠΎΠΌ ΡΠΈΠ³Π»Π΅, Π½Π΅ΠΏΠΎΡΡΠ΅Π΄ΡΡΠ²Π΅Π½Π½ΠΎ ΡΠ΅ΡΠ΅Π· ΠΊΠΎΡΠΎΡΡΠΉ ΠΏΡΠΎΠΏΡΡΠΊΠ°Π΅ΡΡΡ ΡΠ»Π΅ΠΊΡΡΠΈΡΠ΅ΡΠΊΠΈΠΉ ΡΠΎΠΊ. ΠΠΏΠΈΡΠ°Π½ΠΈΠ΅ Π»ΠΈΡΠ΅Π²ΠΎΠΉ (ΡΠ°Π±ΠΎΡΠ΅ΠΉ) ΠΏΠ°Π½Π΅Π»ΠΈ Π³Π°Π·ΠΎΠ°Π½Π°Π»ΠΈΠ·Π°ΡΠΎΡΠ° ΠΏΡΠ΅Π΄ΡΡΠ°Π²Π»Π΅Π½ΠΎ Π½Π° ΡΠΈΡ. 1.
ΠΠ»Ρ ΠΎΠΏΡΠ΅Π΄Π΅Π»Π΅Π½ΠΈΡ ΡΠΎΠ΄Π΅ΡΠΆΠ°Π½ΠΈΡ Π³Π°Π·ΠΎΠ² Π² ΠΏΡΠΈΠ±ΠΎΡΠ΅ ΠΈΡΠΏΠΎΠ»ΡΠ·ΠΎΠ²Π°Π½Ρ Π΄Π²Π° ΠΈΠ·ΠΌΠ΅ΡΠΈΡΠ΅Π»ΡΠ½ΡΡ ΠΏΡΠΈΠ½ΡΠΈΠΏΠ° ΠΈ, ΡΠΎΠΎΡΠ²Π΅ΡΡΡΠ²Π΅Π½Π½ΠΎ, ΠΈΡΠΏΠΎΠ»ΡΠ·ΡΠ΅ΡΡΡ Π΄Π²Π° Π΄Π΅ΡΠ΅ΠΊΡΠΎΡΠ°. ΠΠ»Ρ ΠΎΠΏΡΠ΅Π΄Π΅Π»Π΅Π½ΠΈΡ ΡΠΎΠ΄Π΅ΡΠΆΠ°Π½ΠΈΡ ΠΊΠΈΡΠ»ΠΎΡΠΎΠ΄Π° ΠΏΡΠ΅Π΄Π½Π°Π·Π½Π°ΡΠ΅Π½Π° ΠΈΠ½ΡΡΠ°ΠΊΡΠ°ΡΠ½Π°Ρ ΡΡΠ΅ΠΉΠΊΠ°. ΠΠ»Ρ ΠΎΠΏΡΠ΅Π΄Π΅Π»Π΅Π½ΠΈΡ Π°Π·ΠΎΡΠ° ΠΈ Π²ΠΎΠ΄ΠΎΡΠΎΠ΄Π° ΠΈΡΠΏΠΎΠ»ΡΠ·ΡΠ΅ΡΡΡ Π΄Π΅ΡΠ΅ΠΊΡΠΎΡ ΡΠ΅ΠΏΠ»ΠΎΠΏΡΠΎΠ²ΠΎΠ΄Π½ΠΎΡΡΠΈ. Π’Π°ΠΊ ΠΊΠ°ΠΊ Π΄Π»Ρ ΠΎΠΏΡΠ΅Π΄Π΅Π»Π΅Π½ΠΈΡ ΡΠΎΠ΄Π΅ΡΠΆΠ°Π½ΠΈΡ Π°Π·ΠΎΡΠ° ΠΈ Π²ΠΎΠ΄ΠΎΡΠΎΠ΄Π° ΠΈΡΠΏΠΎΠ»ΡΠ·ΡΠ΅ΡΡΡ ΠΎΠ΄ΠΈΠ½ ΠΈΠ·ΠΌΠ΅ΡΠΈΡΠ΅Π»ΡΠ½ΡΠΉ ΠΏΡΠΈΠ½ΡΠΈΠΏ ΠΈ Π΄Π΅ΡΠ΅ΠΊΡΠΎΡ, ΡΠΎ ΠΏΡΠΈΠ±ΠΎΡ Π½Π΅ ΠΏΠΎΠ·Π²ΠΎΠ»ΡΠ΅Ρ ΠΎΠ΄Π½ΠΎΠ²ΡΠ΅ΠΌΠ΅Π½Π½ΠΎ ΠΎΠΏΡΠ΅Π΄Π΅Π»ΡΡΡ ΡΠΎΠ΄Π΅ΡΠΆΠ°Π½ΠΈΠ΅ Π°Π·ΠΎΡΠ° ΠΈ Π²ΠΎΠ΄ΠΎΡΠΎΠ΄Π° Π² ΠΌΠ΅ΡΠ°Π»Π»Π΅. ΠΠΎΡΡΠΎΠΌΡ Π³Π°Π·ΠΎΠ°Π½Π°Π»ΠΈΠ·Π°ΡΠΎΡ ΠΈΠΌΠ΅Π΅Ρ Π΄Π²Π° ΡΠ΅ΠΆΠΈΠΌΠ° ΡΠ°Π±ΠΎΡΡ: «ON» — Π΄Π»Ρ ΠΎΠ΄Π½ΠΎΠ²ΡΠ΅ΠΌΠ΅Π½Π½ΠΎΠ³ΠΎ ΠΎΠΏΡΠ΅Π΄Π΅Π»Π΅Π½ΠΈΡ ΡΠΎΠ΄Π΅ΡΠΆΠ°Π½ΠΈΡ Π² ΠΌΠ΅ΡΠ°Π»Π»Π΅ ΠΊΠΈΡΠ»ΠΎΡΠΎΠ΄Π° ΠΈ Π°Π·ΠΎΡΠ°, «OΠ» — Π΄Π»Ρ ΠΎΠ΄Π½ΠΎΠ²ΡΠ΅ΠΌΠ΅Π½Π½ΠΎΠ³ΠΎ ΠΎΠΏΡΠ΅Π΄Π΅Π»Π΅Π½ΠΈΡ ΡΠΎΠ΄Π΅ΡΠΆΠ°Π½ΠΈΡ Π² ΠΌΠ΅ΡΠ°Π»Π»Π΅ ΠΊΠΈΡΠ»ΠΎΡΠΎΠ΄Π° ΠΈ Π²ΠΎΠ΄ΠΎΡΠΎΠ΄Π°. Π‘ΠΎΠΎΡΠ²Π΅ΡΡΡΠ²Π΅Π½Π½ΠΎ, Π΄Π»Ρ ΠΏΡΠΎΠ²Π΅Π΄Π΅Π½ΠΈΡ Π°Π½Π°Π»ΠΈΠ·ΠΎΠ² ΠΈΡΠΏΠΎΠ»ΡΠ·ΡΡΡ Π΄Π²Π° ΡΠ΅Ρ Π½ΠΎΠ»ΠΎΠ³ΠΈΡΠ΅ΡΠΊΠΈΡ Π³Π°Π·Π°. ΠΡΠΈ ΡΠ°Π±ΠΎΡΠ΅ Π² ΡΠ΅ΠΆΠΈΠΌΠ΅ ΠΎΠΏΡΠ΅Π΄Π΅Π»Π΅Π½ΠΈΡ ΡΠΎΠ΄Π΅ΡΠΆΠ°Π½ΠΈΡ Π² ΠΌΠ΅ΡΠ°Π»Π»Π΅ ΠΊΠΈΡΠ»ΠΎΡΠΎΠ΄Π° ΠΈ Π°Π·ΠΎΡΠ° ΠΈΡΠΏΠΎΠ»ΡΠ·ΡΠ΅ΡΡΡ Π³Π΅Π»ΠΈΠΉ. ΠΠ»Ρ ΠΎΠΏΡΠ΅Π΄Π΅Π»Π΅Π½ΠΈΡ ΡΠΎΠ΄Π΅ΡΠΆΠ°Π½ΠΈΡ Π² ΠΌΠ΅ΡΠ°Π»Π»Π΅ ΠΊΠΈΡΠ»ΠΎΡΠΎΠ΄Π° ΠΈ Π²ΠΎΠ΄ΠΎΡΠΎΠ΄Π° ΠΈΡΠΏΠΎΠ»ΡΠ·ΡΠ΅ΡΡΡ Π°Π·ΠΎΡ.
ΠΡΠΈΠ½ΡΠΈΠΏ ΡΠ°Π±ΠΎΡΡ Π³Π°Π·ΠΎΠ°Π½Π°Π»ΠΈΠ·Π°ΡΠΎΡΠ° Π½Π°ΠΊΠ»Π°Π΄ΡΠ²Π°Π΅Ρ ΠΆΠ΅ΡΡΠΊΠΈΠ΅ ΠΎΠ³ΡΠ°Π½ΠΈΡΠ΅Π½ΠΈΡ Π½Π° ΡΠΈΡΡΠΎΡΡ ΡΠ΅Ρ Π½ΠΎΠ»ΠΎΠ³ΠΈΡΠ΅ΡΠΊΠΈΡ Π³Π°Π·ΠΎΠ²: Π΄Π»Ρ Π½Π°Π΄Π΅ΠΆΠ½ΠΎΡΡΠΈ ΡΠ΅Π·ΡΠ»ΡΡΠ°ΡΠΎΠ² Π½Π΅ΠΎΠ±Ρ ΠΎΠ΄ΠΈΠΌΠΎ ΠΈΡΠΏΠΎΠ»ΡΠ·ΠΎΠ²Π°Π½ΠΈΠ΅ Π³Π΅Π»ΠΈΡ ΠΈ Π°Π·ΠΎΡΠ° Ρ ΡΠΈΡΡΠΎΡΠΎΠΉ Π½Π΅ ΠΌΠ΅Π½Π΅Π΅ 99,995%. ΠΠ΅ΡΠΌΠΎΡΡΡ Π½Π° ΡΡΠΎ, ΠΏΡΠΎΠΈΠ·Π²ΠΎΠ΄ΠΈΡΡΡ ΠΏΡΠ΅Π΄Π²Π°ΡΠΈΡΠ΅Π»ΡΠ½Π°Ρ ΠΎΡΠΈΡΡΠΊΠ° Π³Π°Π·Π°-Π½ΠΎΡΠΈΡΠ΅Π»Ρ Ρ ΠΏΠΎΠΌΠΎΡΡΡ ΡΠΏΠ΅ΡΠΈΠ°Π»ΡΠ½ΡΡ Π°Π΄ΡΠΎΡΠ±Π΅Π½ΡΠΎΠ²: ΠΏΠ΅ΡΡ Π»ΠΎΡΠ°ΡΠ° ΠΌΠ°Π³Π½ΠΈΡ (Π°Π½Π³ΠΈΠ΄ΡΠΎΠ½Π°) ΠΊΠ°ΠΊ ΠΏΠΎΠ³Π»ΠΎΡΠΈΡΠ΅Π»Ρ Π²Π»Π°Π³ΠΈ ΠΈ Π³ΠΈΠ΄ΡΠΎΠΊΡΠΈΠ΄Π° Π½Π°ΡΡΠΈΡ (Π°ΡΠΊΠ°ΡΠΈΡΠ°) ΠΊΠ°ΠΊ ΠΏΠΎΠ³Π»ΠΎΡΠΈΡΠ΅Π»Ρ Π‘Π2.
ΠΡΠΈ ΡΠ°Π±ΠΎΡΠ΅ ΡΡΡΠ°Π½ΠΎΠ²ΠΊΠΈ ΠΏΠΎΡΠΎΠΊ ΡΠ΅Ρ Π½ΠΎΠ»ΠΎΠ³ΠΈΡΠ΅ΡΠΊΠΎΠ³ΠΎ Π³Π°Π·Π° ΡΠ΅ΡΠ΅Π· Π°Π½Π°Π»ΠΈΠ·Π°ΡΠΎΡ ΡΠ²Π»ΡΠ΅ΡΡΡ Π½Π΅ΠΏΡΠ΅ΡΡΠ²Π½ΡΠΌ. ΠΠ΄Π½Π°ΠΊΠΎ Π² Π·Π°Π²ΠΈΡΠΈΠΌΠΎΡΡΠΈ ΠΎΡ ΡΡΠ°Π΄ΠΈΠΈ ΡΠ°ΡΡ ΠΎΠ΄ Π³Π°Π·Π° ΠΈΠ·ΠΌΠ΅Π½ΡΠ΅ΡΡΡ:
Π² Ρ ΠΎΠ΄Π΅ Π°Π½Π°Π»ΠΈΠ·Π° ΡΠ°ΡΡ ΠΎΠ΄ Π³Π°Π·Π° ΡΠΎΡΡΠ°Π²Π»ΡΠ΅Ρ Π½Π΅ ΠΌΠ΅Π½Π΅Π΅ 30 Π»/ΠΌΠΈΠ½;
Π²ΠΎ Π²ΡΠ΅ΠΌΡ ΠΏΡΠΎΠ΄ΡΠ²ΠΊΠΈ, Π΄Π΅Π³Π°Π·Π°ΡΠΈΠΈ ΠΈ ΠΊΠΎΠ³Π΄Π° ΠΏΠ΅ΡΡ ΠΎΡΠΊΡΡΡΠ° ΠΏΠΎΡΠΎΠΊ Π³Π°Π·Π° ΡΠΎΡΡΠ°Π²Π»ΡΠ΅Ρ Π½Π΅ ΠΌΠ΅Π½Π΅Π΅ 50 Π»/ΠΌΠΈΠ½.
Π ΠΈΡ. 1. ΠΠΏΠΈΡΠ°Π½ΠΈΠ΅ Π»ΠΈΡΠ΅Π²ΠΎΠΉ (ΡΠ°Π±ΠΎΡΠ΅ΠΉ) ΠΏΠ°Π½Π΅Π»ΠΈ Π³Π°Π·ΠΎΠ°Π½Π°Π»ΠΈΠ·Π°ΡΠΎΡΠ°
1 — Π°ΠΌΠΏΠ΅ΡΠΌΠ΅ΡΡ; 2 — ΠΎΠ±ΡΠΈΠΉ ΡΠ°ΡΡ ΠΎΠ΄ΠΎΠΌΠ΅Ρ; 3 — ΡΠ°ΡΡ ΠΎΠ΄ΠΎΠΌΠ΅Ρ Π³Π°Π·Π°-Π½ΠΎΡΠΈΡΠ΅Π»Ρ;
4 — ΡΠ΅Π³ΡΠ»ΡΡΠΎΡ ΠΏΠΎΡΠΎΠΊΠ° ΠΏΡΠΎΠ΄ΡΠ²ΠΊΠΈ; 5 — ΡΠ΅Π³ΡΠ»ΡΡΠΎΡ Π³Π°Π·Π°-Π½ΠΎΡΠΈΡΠ΅Π»Ρ; 6 — Π·Π°Π³ΡΡΠ·ΠΎΡΠ½ΠΎΠ΅ ΡΡΡΡΠΎΠΉΡΡΠ²ΠΎ; 7 — ΠΏΠ½Π΅Π²ΠΌΠ°ΡΠΈΡΠ΅ΡΠΊΠΈΠΉ Π»ΠΈΡΡ; 8 — Π²Π΅ΡΡ Π½ΠΈΠΉ ΡΠ»Π΅ΠΊΡΡΠΎΠ΄ ΠΈ ΠΊΠ°ΠΌΠ΅ΡΠ° ΡΠ°Π±ΠΎΡΠ΅Π³ΠΎ ΠΏΡΠΎΡΡΡΠ°Π½ΡΡΠ²Π° ΠΏΠ΅ΡΠΈ; 9 — Π½ΠΈΠΆΠ½ΠΈΠΉ ΡΠ»Π΅ΠΊΡΡΠΎΠ΄ (ΠΏΠΎΠ΄Π²ΠΈΠΆΠ½Π°Ρ ΡΠ°ΡΡΡ ΠΏΠ΅ΡΠΈ); 10 — ΠΏΡΠ»Π΅ΡΠ»ΠΎΠ²ΠΈΡΠ΅Π»Ρ; 11 — Π΄Π°Π²Π»Π΅Π½ΠΈΠ΅ Π³Π°Π·Π°-Π½ΠΎΡΠΈΡΠ΅Π»Ρ; 12 — Π΄Π°Π²Π»Π΅Π½ΠΈΠ΅ ΡΠΆΠ°ΡΠΎΠ³ΠΎ Π²ΠΎΠ·Π΄ΡΡ Π°; 13 — ΡΠ΅Π°ΠΊΡΠΈΠ² Π¨ΡΡΡΠ΅; 14 — ΠΊΠ°ΡΠ°Π»ΠΈΡΠΈΡΠ΅ΡΠΊΠ°Ρ ΠΏΠ΅ΡΡ Ρ ΠΊΠ°ΡΠ°Π»ΠΈΠ·Π°ΡΠΎΡΠΎΠΌ ΠΎΠΊΡΠΈΠ΄ΠΎΠΌ ΠΌΠ΅Π΄ΠΈ; 15 — Π³Π»Π°Π²Π½ΡΠΉ ΠΏΠ΅ΡΠ΅ΠΊΠ»ΡΡΠ°ΡΠ΅Π»Ρ; 16 — ΠΏΡΠ΅Π΄Π²Π°ΡΠΈΡΠ΅Π»ΡΠ½Π°Ρ ΠΎΡΠΈΡΡΠΊΠ° Π³Π°Π·Π°; 17 — Π2Π Π»ΠΎΠ²ΡΡΠΊΠ°; 18 — ΠΎΡΠΈΡΡΠΊΠ° Π³Π°Π·Π° ΠΏΠ΅ΡΠ΅Π΄ ΠΠ ΡΡΠ΅ΠΉΠΊΠΎΠΉ; 19 — ΠΏΠ΅ΡΠ΅ΠΊΠ»ΡΡΠ°ΡΠ΅Π»Ρ ΡΠ΅ΠΆΠΈΠΌΠΎΠ² ΡΠ°Π±ΠΎΡΡ: ΠN (ΠΎΠΏΡΠ΅Π΄Π΅Π»Π΅Π½ΠΈΠ΅ ΡΠΎΠ΄Π΅ΡΠΆΠ°Π½ΠΈΠΉ ΠΊΠΈΡΠ»ΠΎΡΠΎΠ΄Π° ΠΈ Π°Π·ΠΎΡΠ°) ΠΈ ΠΠ (ΠΎΠΏΡΠ΅Π΄Π΅Π»Π΅Π½ΠΈΠ΅ ΡΠΎΠ΄Π΅ΡΠΆΠ°Π½ΠΈΠΉ ΠΊΠΈΡΠ»ΠΎΡΠΎΠ΄Π° ΠΈ Π²ΠΎΠ΄ΠΎΡΠΎΠ΄Π°) ΠΠΎΠ΄Π±ΠΎΡ ΠΎΠΏΡΠΈΠΌΠ°Π»ΡΠ½ΠΎΠ³ΠΎ ΡΠ°ΡΡ ΠΎΠ΄Π° Π³Π°Π·Π° — ΠΎΠ΄Π½ΠΎ ΠΈΠ· Π½Π΅ΠΎΠ±Ρ ΠΎΠ΄ΠΈΠΌΡΡ ΡΡΠ»ΠΎΠ²ΠΈΠΉ ΠΌΠΈΠ½ΠΈΠΌΠΈΠ·Π°ΡΠΈΠΈ ΠΈ ΡΡΠ°Π±ΠΈΠ»ΠΈΠ·Π°ΡΠΈΠΈ Π²Π»ΠΈΡΠ½ΠΈΡ Ρ ΠΎΠ»ΠΎΡΡΠΎΠ³ΠΎ ΠΎΠΏΡΡΠ° (Π±Π΅Π· ΠΌΠ΅ΡΠ°Π»Π»Π°) Π½Π° ΡΠ΅Π·ΡΠ»ΡΡΠ°ΡΡ ΡΠΊΡΠΏΠ΅ΡΠΈΠΌΠ΅Π½ΡΠ°.
ΠΠ°ΡΡΠ° ΠΎΠ±ΡΠ°Π·ΡΠ° ΠΌΠ΅ΡΠ°Π»Π»Π° Π΄Π»Ρ Π°Π½Π°Π»ΠΈΠ·Π° 1000 ΠΌΠ³. ΠΠ±ΡΠ°Π·Π΅Ρ ΡΡΠ΅Π±ΡΠ΅Ρ ΠΎΡΠ΅Π½Ρ ΡΡΠ°ΡΠ΅Π»ΡΠ½ΠΎΠΉ ΠΏΠΎΠ΄Π³ΠΎΡΠΎΠ²ΠΊΠΈ. ΠΠ΅ΠΎΠ±Ρ ΠΎΠ΄ΠΈΠΌΠΎ Π΄ΠΎΠ±ΠΈΡΡΡΡ ΠΌΠ°ΠΊΡΠΈΠΌΠ°Π»ΡΠ½ΠΎΠΉ ΡΠΈΡΡΠΎΡΡ ΠΏΠΎΠ²Π΅ΡΡ Π½ΠΎΡΡΠΈ. ΠΠ΅ΡΠ΅Π΄ Π°Π½Π°Π»ΠΈΠ·ΠΎΠΌ ΠΎΠ±ΡΠ°Π·Π΅Ρ Π²Π·Π²Π΅ΡΠΈΠ²Π°Π΅ΡΡΡ Π½Π° ΡΠ»Π΅ΠΊΡΡΠΎΠ½Π½ΡΡ Π²Π΅ΡΠ°Ρ Ρ ΡΠΎΡΠ½ΠΎΡΡΡΡ Π΄ΠΎ 0,1 ΠΌΠ³.
ΠΠ½Π°Π»ΠΈΠ·ΠΈΡΡΠ΅ΠΌΠ°Ρ ΠΏΡΠΎΠ±Π° ΠΏΠΎΠΏΠ°Π΄Π°Π΅Ρ Π² ΠΏΡΠ΅Π΄Π²Π°ΡΠΈΡΠ΅Π»ΡΠ½ΠΎ ΠΏΡΠΎΠΊΠ°Π»Π΅Π½Π½ΡΠΉ Π³ΡΠ°ΡΠΈΡΠΎΠ²ΡΠΉ ΡΠΈΠ³Π΅Π»Ρ ΡΠ΅ΡΠ΅Π· ΡΠ»ΡΠ·ΠΎΠ²ΠΎΠ΅ ΡΡΡΡΠΎΠΉΡΡΠ²ΠΎ. Π’Π°ΠΌ ΠΎΠ½Π° ΡΠ°ΡΠΏΠ»Π°Π²Π»ΡΠ΅ΡΡΡ ΠΏΡΠΈ ΠΏΠΎΠΌΠΎΡΠΈ Π±ΠΎΠ»ΡΡΠΎΠ³ΠΎ ΡΠΎΠΊΠ°. ΠΠΈΡΠ»ΠΎΡΠΎΠ΄ ΡΠ΅Π°Π³ΠΈΡΡΠ΅Ρ Ρ Π³ΠΎΡΡΡΠΈΠΌ Π³ΡΠ°ΡΠΈΡΠΎΠ²ΡΠΌ ΡΠΈΠ³Π»Π΅ΠΌ ΠΈ ΠΏΡΠ΅Π²ΡΠ°ΡΠ°Π΅ΡΡΡ Π² ΠΌΠΎΠ½ΠΎΠΊΡΠΈΠ΄ ΡΠ³Π»Π΅ΡΠΎΠ΄Π°. ΠΠ°Π·-Π½ΠΎΡΠΈΡΠ΅Π»Ρ Π²ΡΠ½ΠΎΡΠΈΡ Π²ΡΠ΄Π΅Π»ΠΈΠ²ΡΠΈΠ΅ΡΡ Π² ΡΠ΅Π·ΡΠ»ΡΡΠ°ΡΠ΅ ΠΏΠ»Π°Π²Π»Π΅Π½ΠΈΡ Π³Π°Π·Ρ ΠΈΠ· ΡΠ°Π±ΠΎΡΠ΅Π³ΠΎ ΠΏΡΠΎΡΡΡΠ°Π½ΡΡΠ²Π°. Π‘ ΠΏΠΎΠΌΠΎΡΡΡ Π½Π°ΡΠΎΡΠ° Π² ΡΠ΅ΠΆΠΈΠΌΠ΅ «ON» ΡΠΌΠ΅ΡΡ Π³Π°Π·ΠΎΠ² ΠΏΡΠΎΠΊΠ°ΡΠΈΠ²Π°Π΅ΡΡΡ ΡΠ΅ΡΠ΅Π· ΠΊΠ°ΡΠ°Π»ΠΈΡΠΈΡΠ΅ΡΠΊΡΡ ΠΏΠ΅ΡΡ, Π³Π΄Π΅ CO Π² ΠΏΡΠΈΡΡΡΡΡΠ²ΠΈΠΈ ΠΊΠ°ΡΠ°Π»ΠΈΠ·Π°ΡΠΎΡΠ° Π² Π²ΠΈΠ΄Π΅ ΠΎΠΊΡΠΈΠ΄Π° ΠΌΠ΅Π΄ΠΈ Ρ Π΄ΠΎΠ±Π°Π²ΠΊΠ°ΠΌΠΈ ΡΠ΅Π΄ΠΊΠΎΠ·Π΅ΠΌΠ΅Π»ΡΠ½ΡΡ ΠΌΠ΅ΡΠ°Π»Π»ΠΎΠ² ΠΎΠΊΠΈΡΠ»ΡΠ΅ΡΡΡ Π΄ΠΎ CO2. Π ΡΠ΅ΠΆΠΈΠΌΠ΅ «ΠΠ» ΠΏΡΠ΅ΠΎΠ±ΡΠ°Π·ΠΎΠ²Π°Π½ΠΈΠ΅ Π‘Π Π² CO2 ΠΎΡΡΡΠ΅ΡΡΠ²Π»ΡΠ΅ΡΡΡ Π² ΡΠ΅Π°Π³Π΅Π½ΡΠ½ΠΎΠΉ ΡΡΡΠ±ΠΊΠ΅, ΡΠΎΠ΄Π΅ΡΠΆΠ°ΡΠ΅ΠΉ ΡΠ΅Π°ΠΊΡΠΈΠ² Π¨ΡΡΡΠ΅. ΠΠΎΡΠ»Π΅ ΡΡΠΎΠ³ΠΎ ΡΠΎΠ΄Π΅ΡΠΆΠ°Π½ΠΈΠ΅ CO2 Π² ΡΠΎΡΡΠ°Π²Π΅ Π³Π°Π·ΠΎΠ²ΠΎΠΉ ΡΠΌΠ΅ΡΠΈ ΠΎΠΏΡΠ΅Π΄Π΅Π»ΡΠ΅ΡΡΡ Π² ΠΠ-ΡΡΠ΅ΠΉΠΊΠ΅. ΠΠ°Π»Π΅Π΅ ΠΏΠΎΡΠ»Π΅ ΠΏΠΎΠ³Π»ΠΎΡΠ΅Π½ΠΈΡ Π‘Π2 ΠΈ Π²Π»Π°Π³ΠΈ Π² ΡΠ΅Π·ΡΠ»ΡΡΠ°ΡΠ΅ ΠΏΡΠΎΡ ΠΎΠΆΠ΄Π΅Π½ΠΈΡ ΡΠ΅ΡΠ΅Π· ΡΠ΅Π°Π³Π΅Π½ΡΠ½ΡΡ ΠΊΠ²Π°ΡΡΠ΅Π²ΡΡ ΡΡΡΠ±ΠΊΡ, ΡΠΎΠ΄Π΅ΡΠΆΠ°ΡΡΡ ΠΏΠ΅ΡΡ Π»ΠΎΡΠ°Ρ ΠΌΠ°Π³Π½ΠΈΡ (Π°Π½Π³ΠΈΠ΄ΡΠΎΠ½) ΠΈ Π³ΠΈΠ΄ΡΠΎΠΊΡΠΈΠ΄ Π½Π°ΡΡΠΈΡ (Π°ΡΠΊΠ°ΡΠΈΡ) ΡΠΌΠ΅ΡΡ Π³Π°Π·ΠΎΠ² ΠΏΠΎΡΡΡΠΏΠ°Π΅Ρ Π² Π΄Π΅ΡΠ΅ΠΊΡΠΎΡ ΡΠ΅ΠΏΠ»ΠΎΠΏΡΠΎΠ²ΠΎΠ΄Π½ΠΎΡΡΠΈ, Π³Π΄Π΅ ΠΏΡΠΎΠΈΡΡ ΠΎΠ΄ΠΈΡ Π°Π½Π°Π»ΠΈΠ· Π½Π° ΡΠΎΠ΄Π΅ΡΠΆΠ°Π½ΠΈΠ΅ Π°Π·ΠΎΡΠ° (ΡΠ΅ΠΆΠΈΠΌ «ON») ΠΈΠ»ΠΈ Π²ΠΎΠ΄ΠΎΡΠΎΠ΄Π° (ΡΠ΅ΠΆΠΈΠΌ «OΠ»).
Π‘ΠΈΠ³Π½Π°Π» ΠΎΡ ΡΡΠ΅Π΅ΠΊ ΠΏΡΠ΅ΠΎΠ±ΡΠ°Π·ΡΠ΅ΡΡΡ Π±Π»ΠΎΠΊΠΎΠΌ ΡΠ»Π΅ΠΊΡΡΠΎΠ½ΠΈΠΊΠΈ, ΠΈ ΡΠ΅Π·ΡΠ»ΡΡΠ°ΡΡ ΠΏΠΎΠΊΠ°Π·ΡΠ²Π°ΡΡΡΡ Π½Π° Π΄ΠΈΡΠΏΠ»Π΅Π΅.
2.1.1 ΠΡΠΈΠ½ΡΠΈΠΏ ΡΠ°Π±ΠΎΡΡ ΠΈΠ½ΡΡΠ°ΠΊΡΠ°ΡΠ½ΠΎΠΉ ΡΡΠ΅ΠΉΠΊΠΈ
ΠΠ·ΠΌΠ΅ΡΠΈΡΠ΅Π»ΡΠ½ΡΠ΅ ΠΏΡΠΈΠ½ΡΠΈΠΏΡ ΠΎΡΠ½ΠΎΠ²Π°Π½Ρ Π½Π° ΡΠ²ΠΎΠΉΡΡΠ²Π΅ ΠΏΠΎΠ³Π»ΠΎΡΠ΅Π½ΠΈΡ ΠΈΠ½ΡΡΠ°ΠΊΡΠ°ΡΠ½ΠΎΠ³ΠΎ ΠΈΠ·Π»ΡΡΠ΅Π½ΠΈΡ ΠΌΠ½ΠΎΠ³ΠΈΠΌΠΈ Π³Π°Π·Π°ΠΌΠΈ. ΠΠ°ΠΆΠ΄ΡΠΉ ΠΈΠ· ΡΡΠΈΡ Π³Π°Π·ΠΎΠ² ΠΏΠΎΠ³Π»ΠΎΡΠ°Π΅Ρ ΠΈΠ½ΡΡΠ°ΠΊΡΠ°ΡΠ½ΠΎΠ΅ ΠΈΠ·Π»ΡΡΠ΅Π½ΠΈΠ΅ Ρ ΠΊΠΎΠ½ΠΊΡΠ΅ΡΠ½ΡΠΌΠΈ Ρ Π°ΡΠ°ΠΊΡΠ΅ΡΠΈΡΡΠΈΠΊΠ°ΠΌΠΈ ΡΠΏΠ΅ΠΊΡΡΠ°Π»ΡΠ½ΡΡ Π΄Π»ΠΈΠ½ Π²ΠΎΠ»Π½. ΠΠΎΠ³Π»ΠΎΡΠ°Π΅ΠΌΡΠΉ ΡΠΏΠ΅ΠΊΡΡ ΠΎΠΏΡΠ΅Π΄Π΅Π»ΡΠ΅ΡΡΡ Π½ΠΎΠΌΠ΅ΡΠΎΠΌ, ΠΊΠΎΠ½ΡΠΈΠ³ΡΡΠ°ΡΠΈΠ΅ΠΉ ΠΈ ΡΠΈΠΏΠΎΠΌ Π°ΡΠΎΠΌΠΎΠ² Π² Π³Π°Π·ΠΎΠ²ΠΎΠΉ ΠΌΠΎΠ»Π΅ΠΊΡΠ»Π΅. Π‘Ρ Π΅ΠΌΠ° ΡΡΡΡΠΎΠΉΡΡΠ²Π° ΠΈΠ½ΡΡΠ°ΠΊΡΠ°ΡΠ½ΠΎΠΉ ΡΡΠ΅ΠΉΠΊΠΈ ΠΏΡΠ΅Π΄ΡΡΠ°Π²Π»Π΅Π½Π° Π½Π° ΡΠΈΡ. 2.
ΠΠ½ΡΡΠ°ΠΊΡΠ°ΡΠ½ΡΠΉ ΠΈΡΡΠΎΡΠ½ΠΈΠΊ (2) ΡΠ»Π΅ΠΊΡΡΠΈΡΠ΅ΡΠΊΠΈ Π½Π°Π³ΡΠ΅Π²Π°Π΅ΡΡΡ ΠΈ ΠΈΠ·Π»ΡΡΠ°Π΅Ρ ΡΠΈΡΠΎΠΊΠΎΠΏΠΎΠ»ΠΎΡΠ½ΠΎΠ΅ ΠΈΠ½ΡΡΠ°ΠΊΡΠ°ΡΠ½ΠΎΠ΅ ΠΈΠ·Π»ΡΡΠ΅Π½ΠΈΠ΅. ΠΡΡΠΎΠΊ ΡΠ²Π΅ΡΠ° ΠΏΡΠ΅ΡΡΠ²Π°Π΅ΡΡΡ ΠΊΡΡΡΡΡΠ΅ΠΉΡΡ Π»ΠΎΠΏΠ°ΡΡΡΡ (ΠΏΡΠ΅ΡΡΠ²Π°ΡΠ΅Π»Π΅ΠΌ) (3), ΡΡΠ°Π½ΠΎΠ²ΠΈΡΡΡ ΠΏΠ΅ΡΠ΅ΠΌΠ΅Π½Π½ΡΠΌ ΡΠ²Π΅ΡΠΎΠΌ. ΠΠ»Ρ Π²ΡΡΠΎΠΊΠΎΠΉ ΡΡΠ°Π±ΠΈΠ»ΡΠ½ΠΎΡΡΠΈ ΡΠ°ΡΡΠΎΡΡ Π»ΠΎΠΏΠ°ΡΡΠΈ ΠΏΡΠ΅ΡΡΠ²Π°ΡΠ΅Π»Ρ ΠΈΡΠΏΠΎΠ»ΡΠ·ΡΠ΅ΡΡΡ ΠΌΠΎΡΠΎΡ (1) Ρ ΠΊΠ²Π°ΡΡΠ΅Π²ΡΠΌ ΠΊΠΎΠ½ΡΡΠΎΠ»Π»Π΅ΡΠΎΠΌ. ΠΠ°Π»Π΅Π΅ ΠΈΠ½ΡΡΠ°ΠΊΡΠ°ΡΠ½ΠΎΠ΅ ΠΈΠ·Π»ΡΡΠ΅Π½ΠΈΠ΅ ΠΏΡΠΎΡ ΠΎΠ΄ΠΈΡ ΡΠ΅ΡΠ΅Π· ΠΈΠ·ΠΌΠ΅ΡΠΈΡΠ΅Π»ΡΠ½ΡΠ΅ ΠΠ-ΡΡΠ°ΠΊΡΡ (10,11) ΠΏΠΎ ΠΊΠΎΡΠΎΡΡΠΌ ΠΏΡΠΎΡΠ΅ΠΊΠ°Π΅Ρ ΡΠΌΠ΅ΡΡ Π³Π°Π·Π° ΠΎΠ±ΡΠ°Π·ΡΠ° ΠΈ Π³Π°Π·Π° Π½ΠΎΡΠΈΡΠ΅Π»Ρ.
Π Π·Π°Π²ΠΈΡΠΈΠΌΠΎΡΡΠΈ ΠΎΡ ΡΠΎΡΡΠ°Π²Π° Π³Π°Π·ΠΎΠ²ΠΎΠΉ ΡΠΌΠ΅ΡΠΈ ΠΏΠΎΠ³Π»ΠΎΡΠ°Π΅ΡΡΡ ΠΎΠΏΡΠ΅Π΄Π΅Π»Π΅Π½Π½Π°Ρ ΡΠ°ΡΡΠΎΡΠ° ΠΈΠ½ΡΡΠ°ΠΊΡΠ°ΡΠ½ΠΎΠ³ΠΎ ΡΠΏΠ΅ΠΊΡΡΠ°. Π£ΡΠΎΠ²Π΅Π½Ρ ΠΏΠΎΠ³Π»ΠΎΡΠ΅Π½ΠΈΡ Π·Π°Π²ΠΈΡΠΈΡ ΠΎΡ Π³Π°Π·ΠΎΠ²ΠΎΠΉ ΠΊΠΎΠ½ΡΠ΅Π½ΡΡΠ°ΡΠΈΠΈ.
ΠΠΎΡΠ»Π΅ ΠΠ-ΡΡΠ°ΠΊΡΠ° ΠΈΠ½ΡΡΠ°ΠΊΡΠ°ΡΠ½ΡΠΉ ΠΏΡΡΠΎΠΊ ΠΏΡΠΎΡ ΠΎΠ΄ΠΈΡ ΡΠ΅ΡΠ΅Π· ΡΠΈΠ»ΡΡΡΡ (6, 9), ΠΏΡΠΎΠΏΡΡΠΊΠ°ΡΡΠΈΠ΅ ΡΠΎΠ»ΡΠΊΠΎ ΡΠ·ΠΊΡΡ ΠΏΠΎΠ»ΠΎΡΡ ΠΈΠ½ΡΡΠ°ΠΊΡΠ°ΡΠ½ΠΎΠ³ΠΎ ΡΠ²Π΅ΡΠ°. ΠΡΠ° ΡΠ·ΠΊΠ°Ρ ΠΏΠΎΠ»ΠΎΡΠ° Π΄ΠΎΠ»ΠΆΠ½Π° ΡΠΎΠΎΡΠ²Π΅ΡΡΡΠ²ΠΎΠ²Π°ΡΡ Π΄ΠΈΠ°ΠΏΠ°Π·ΠΎΠ½Ρ ΠΈΠ½ΡΡΠ°ΠΊΡΠ°ΡΠ½ΡΡ ΡΠ°ΡΡΠΎΡ, Π΄Π»Ρ ΠΊΠΎΡΠΎΡΠΎΠ³ΠΎ Π³Π°Π· ΠΎΠ±ΡΠ°Π·ΡΠ° ΠΏΡΠΎΡΠ²Π»ΡΠ΅Ρ ΠΌΠ°ΠΊΡΠΈΠΌΠ°Π»ΡΠ½ΡΡ ΡΠΏΠΎΡΠΎΠ±Π½ΠΎΡΡΡ ΠΏΠΎΠ³Π»ΠΎΡΠ΅Π½ΠΈΡ.
Π ΠΈΡ. 1.1. Π‘Ρ Π΅ΠΌΠ° ΡΡΡΡΠΎΠΉΡΡΠ²Π° ΠΈΠ½ΡΡΠ°ΠΊΡΠ°ΡΠ½ΠΎΠΉ ΡΡΠ΅ΠΉΠΊΠΈ
1 — ΠΠ-ΠΈΡΡΠΎΡΠ½ΠΈΠΊ, 2 — ΠΌΠΎΡΠΎΡ, 3 — ΠΏΡΠ΅ΡΡΠ²Π°ΡΠ΅Π»Ρ, 4 — Π²Π²ΠΎΠ΄, 5 — Π²ΡΠ²ΠΎΠ΄,
6 — Π‘O2 ΡΠΈΠ»ΡΡΡ, 7 — ΠΈΠ½ΡΡΠ°ΠΊΡΠ°ΡΠ½ΡΠΉ Π΄Π΅ΡΠ΅ΠΊΡΠΎΡ, 8 — ΠΈΠ½ΡΡΠ°ΠΊΡΠ°ΡΠ½ΡΠΉ Π΄Π΅ΡΠ΅ΠΊΡΠΎΡ,
9 — CO2 ΡΠΈΠ»ΡΡΡ, 10 — ΠΈΠ·ΠΌΠ΅ΡΠΈΡΠ΅Π»ΡΠ½ΡΠΉ ΠΠ-ΡΡΠ°ΠΊΡ, 11 — ΠΈΠ·ΠΌΠ΅ΡΠΈΡΠ΅Π»ΡΠ½ΡΠΉ ΠΠ-ΡΡΠ°ΠΊΡ, 12 — ΠΏΡΠ΅Π΄ΡΡΠΈΠ»ΠΈΡΠ΅Π»Ρ Π’Π°ΠΊΠΈΠΌ ΠΎΠ±ΡΠ°Π·ΠΎΠΌ, ΠΈΠ½ΡΠ΅Π½ΡΠΈΠ²Π½ΠΎΡΡΡ ΠΏΡΡΠΊΠ° ΠΏΠΎΠΊΠΈΠ΄Π°ΡΡΠ΅Π³ΠΎ ΡΠΈΠ»ΡΡΡ ΠΎΠ±Π΅ΡΠΏΠ΅ΡΠΈΠ²Π°Π΅Ρ ΠΈΠ½ΡΠΎΡΠΌΠ°ΡΠΈΡ ΠΎ ΠΊΠΎΠ½ΡΠ΅Π½ΡΡΠ°ΡΠΈΠΈ Π΄Π°Π½Π½ΠΎΠ³ΠΎ Π³Π°Π·Π° Π² ΡΡΠ°ΠΊΡΠ΅. Π Π·Π°ΠΊΠ»ΡΡΠ΅Π½ΠΈΠ΅ ΠΏΡΡΠΎΠΊ Π΄ΠΎΡΡΠΈΠ³Π°Π΅Ρ ΠΏΠΎΠ»ΡΠΏΡΠΎΠ²ΠΎΠ΄Π½ΠΈΠΊΠΎΠ²ΠΎΠ³ΠΎ ΠΈΠ½ΡΡΠ°ΠΊΡΠ°ΡΠ½ΠΎΠ³ΠΎ Π΄Π΅ΡΠ΅ΠΊΡΠΎΡΠ° (7, 8), ΠΈΡΠΏΡΡΠΊΠ°ΡΡΠ΅Π³ΠΎ ΡΠΈΠ³Π½Π°Π» ΠΏΡΠΎΠΏΠΎΡΡΠΈΠΎΠ½Π°Π»ΡΠ½ΡΠΉ ΠΈΠ½ΡΠ΅Π½ΡΠΈΠ²Π½ΠΎΡΡΠΈ ΠΏΡΡΠΊΠ°.
Π’Π°ΠΊ ΠΊΠ°ΠΊ ΠΏΡΡΠΎΠΊ ΠΏΡΠ΅ΡΡΠ²Π°Π΅ΡΡΡ Π²ΡΠ°ΡΠ°ΡΡΠΈΠΌΡΡ ΠΏΡΠ΅ΡΡΠ²Π°ΡΠ΅Π»Π΅ΠΌ, Π΄Π΅ΡΠ΅ΠΊΡΠΎΡ ΠΏΠΎΠ»ΡΡΠ°Π΅Ρ ΠΏΡΠ΅ΡΡΠ²ΠΈΡΡΡΠΉ ΡΠΈΠ³Π½Π°Π». Π’Π΅ΠΌ ΡΠ°ΠΌΡΠΌ Π΄ΠΎΡΡΠΈΠ³Π°Π΅ΡΡΡ ΠΏΠΎΠ΄Π°Π²Π»Π΅Π½ΠΈΠ΅ Π²Π»ΠΈΡΠ½ΠΈΡ ΡΠ΅ΠΌΠΏΠ΅ΡΠ°ΡΡΡΡ ΠΈ ΡΡΠ°ΡΠ΅Π½ΠΈΡ Π΄Π΅ΡΠ΅ΠΊΡΠΎΡΠ°, Π° ΡΠ°ΠΊ ΠΆΠ΅ ΡΡΠΌΡ.
Π‘ΠΈΠ³Π½Π°Π», ΠΏΠΎΠ»ΡΡΠ΅Π½Π½ΡΠΉ ΡΠ°ΠΊΠΈΠΌ ΠΎΠ±ΡΠ°Π·ΠΎΠΌ, ΡΡΠΈΠ»ΡΡΡΡ, ΠΈ Π²ΡΠΏΡΡΠΌΠ»ΡΠ΅ΡΡΡ ΠΈ ΠΏΠΎΠΊΠΈΠ΄Π°Π΅Ρ ΠΈΠ½ΡΡΠ°ΠΊΡΠ°ΡΠ½ΡΡ ΡΡΠ΅ΠΉΠΊΡ ΠΊΠ°ΠΊ ΠΏΠΎΡΡΠΎΡΠ½Π½ΠΎΠ΅ Π·Π½Π°ΡΠ΅Π½ΠΈΠ΅.
ΠΠ½ΡΡΠ°ΠΊΡΠ°ΡΠ½Π°Ρ ΡΡΠ΅ΠΉΠΊΠ° ΡΠ°ΠΊΠΆΠ΅ ΠΎΠ±Π΅ΡΠΏΠ΅ΡΠΈΠ²Π°Π΅Ρ ΠΏΠΎΡΡΠΎΡΠ½Π½ΡΡ Π°Π²ΡΠΎΠΌΠ°ΡΠΈΡΠ΅ΡΠΊΡΡ ΠΊΠΎΡΡΠ΅ΠΊΡΠΈΡ Π½ΡΠ»Π΅Π²ΠΎΠΉ ΡΠΎΡΠΊΠΈ ΠΈ ΡΡΠ²ΡΡΠ²ΠΈΡΠ΅Π»ΡΠ½ΠΎΡΡΠΈ Π°Π½Π°Π»ΠΈΠ·Π°ΡΠΎΡΠ°, ΡΡΠΎ ΠΏΠΎΠ»Π½ΠΎΡΡΡΡ ΠΈΡΠΊΠ»ΡΡΠ°Π΅Ρ Π½Π΅ΠΎΠ±Ρ ΠΎΠ΄ΠΈΠΌΠΎΡΡΡ Π² ΡΡΡΠ½ΠΎΠΉ ΠΏΡΠΎΠ²Π΅ΡΠΊΠ΅ ΠΈ ΠΏΠ΅ΡΠ΅Π½Π°ΡΡΡΠΎΠΉΠΊΠ΅.
ΠΠ½ΡΡΠ°ΠΊΡΠ°ΡΠ½ΡΠΉ Π°Π½Π°Π»ΠΈΠ·Π°ΡΠΎΡ ΠΊΠΎΠ½ΡΡΠΎΠ»ΠΈΡΡΠ΅ΡΡΡ ΡΠ΅ΡΠΌΠΎΡΡΠ°ΡΠΈΡΠ΅ΡΠΊΠΈ, ΠΏΠΎΠ΄Π΄Π΅ΡΠΆΠΈΠ²Π°Ρ ΠΏΠΎΡΡΠΎΡΠ½Π½ΡΡ ΡΠ΅ΠΌΠΏΠ΅ΡΠ°ΡΡΡΡ Π³Π°Π·Π° ΠΎΠ±ΡΠ°Π·ΡΠ° ΠΏΡΠΎΡ ΠΎΠ΄ΡΡΠ΅Π³ΠΎ ΡΠ΅ΡΠ΅Π· Π½Π΅Π³ΠΎ.
2.1.2 ΠΡΠΈΠ½ΡΠΈΠΏ ΡΠ°Π±ΠΎΡΡ Π΄Π΅ΡΠ΅ΠΊΡΠΎΡΠ° ΡΠ΅ΠΏΠ»ΠΎΠΏΡΠΎΠ²ΠΎΠ΄Π½ΠΎΡΡΠΈ
ΠΡΠΈΠ½ΡΠΈΠΏ ΠΈΠ·ΠΌΠ΅ΡΠ΅Π½ΠΈΡ Π΄Π΅ΡΠ΅ΠΊΡΠΎΡΠ° ΡΠ΅ΠΏΠ»ΠΎΠΏΡΠΎΠ²ΠΎΠ΄Π½ΠΎΡΡΠΈ ΠΎΡΠ½ΠΎΠ²ΡΠ²Π°Π΅ΡΡΡ Π½Π° ΡΠΎΠΌ, ΡΡΠΎ ΡΠ΅ΠΏΠ»ΠΎΠΏΡΠΎΠ²ΠΎΠ΄Π½ΠΎΡΡΡ Π³Π°Π·ΠΎΠ²ΠΎΠΉ ΡΠΌΠ΅ΡΠΈ ΠΌΠ΅Π½ΡΠ΅ΡΡΡ ΡΠΎ ΡΠ²ΠΎΠΈΠΌ ΡΠΎΡΡΠ°Π²ΠΎΠΌ. Π§ΡΠΎΠ±Ρ ΠΈΠ·ΠΌΠ΅ΡΡΡΡ Π΄Π°ΠΆΠ΅ ΠΌΠ°Π»Π΅ΠΉΡΠΈΠ΅ ΠΈΠ·ΠΌΠ΅Π½Π΅Π½ΠΈΡ, ΠΎΡΠΊΠ°Π·ΡΠ²Π°ΡΡΡΡ ΠΎΡ Π°Π±ΡΠΎΠ»ΡΡΠ½ΠΎΠ³ΠΎ ΠΈΠ·ΠΌΠ΅ΡΠ΅Π½ΠΈΡ. Π’Π°ΠΊΠΈΠΌ ΠΎΠ±ΡΠ°Π·ΠΎΠΌ, ΡΠ΅ΠΏΠ»ΠΎΠΏΡΠΎΠ²ΠΎΠ΄Π½ΠΎΡΡΡ ΠΏΠΎΡΠΎΠΊΠ° ΠΈΠ·ΠΌΠ΅ΡΡΠ΅ΠΌΠΎΠ³ΠΎ Π³Π°Π·Π° ΡΡΠ°Π²Π½ΠΈΠ²Π°Π΅ΡΡΡ ΡΠΎ ΡΡΠ°Π½Π΄Π°ΡΡΠΎΠΌ. Π ΠΊΠ°ΡΠ΅ΡΡΠ²Π΅ ΡΡΠ°Π½Π΄Π°ΡΡΠ° ΡΠ»ΡΠΆΠΈΡ ΡΠ»Π°Π±ΡΠΉ ΠΏΠΎΡΠΎΠΊ ΡΠΈΡΡΠΎΠ³ΠΎ Π³Π°Π·Π°. Π‘Ρ Π΅ΠΌΠ° ΡΡΡΡΠΎΠΉΡΡΠ²Π° Π΄Π΅ΡΠ΅ΠΊΡΠΎΡΠ° ΡΠ΅ΠΏΠ»ΠΎΠΏΡΠΎΠ²ΠΎΠ΄Π½ΠΎΡΡΠΈ ΠΏΡΠ΅Π΄ΡΡΠ°Π²Π»Π΅Π½Π° Π½Π° ΡΠΈΡ. 3.
Π ΠΈΡ. 1.2. Π‘Ρ Π΅ΠΌΠ° ΡΡΡΡΠΎΠΉΡΡΠ²Π° Π΄Π΅ΡΠ΅ΠΊΡΠΎΡΠ° ΡΠ΅ΠΏΠ»ΠΎΠΏΡΠΎΠ²ΠΎΠ΄Π½ΠΎΡΡΠΈ
1 — ΡΠ΅ΡΠΌΠΎΡΡΠ°Π±ΠΈΠ»ΠΈΠ·ΠΈΡΠΎΠ²Π°Π½Π½Π°Ρ ΡΡΠ΅ΠΉΠΊΠ°, 2 — ΠΊΠ°Π½Π°Π» ΠΈΠ·ΠΌΠ΅ΡΠ΅Π½ΠΈΡ, 3 — ΠΊΠ°Π½Π°Π» ΡΡΠ°Π²Π½Π΅Π½ΠΈΡ, 4 — ΡΠ΅ΡΠΌΠΈΡΡΠΎΡ, 5 — ΡΡΠΈΠ»ΠΈΡΠ΅Π»Ρ, 6 — Π±Π»ΠΎΠΊ ΡΠ»Π΅ΠΊΡΡΠΎΠ½ΠΈΠΊΠΈ Π ΡΡΠ΅ΠΉΠΊΠ΅ (1) Π΅ΡΡΡ Π΄Π²Π° ΠΊΠ°Π½Π°Π»Π°: ΠΊΠ°Π½Π°Π» ΠΈΠ·ΠΌΠ΅ΡΠ΅Π½ΠΈΡ (2), Π² ΠΊΠΎΡΠΎΡΠΎΠΌ ΠΏΡΠΎΡΠ΅ΠΊΠ°Π΅Ρ Π°Π½Π°Π»ΠΈΠ·ΠΈΡΡΠ΅ΠΌΡΠΉ Π³Π°Π·, ΠΈ ΠΊΠ°Π½Π°Π» ΡΡΠ°Π²Π½Π΅Π½ΠΈΡ (3) Ρ ΠΏΠΎΡΠΎΠΊΠΎΠΌ ΡΠΈΡΡΠΎΠ³ΠΎ Π³Π°Π·Π°-Π½ΠΎΡΠΈΡΠ΅Π»Ρ.
Π ΠΊΠ°ΠΆΠ΄ΠΎΠΌ ΠΊΠ°Π½Π°Π»Π΅ Π΅ΡΡΡ Π΄Π²Π° ΡΠ΅ΡΠΌΠΈΡΡΠΎΡΠ° (4), ΠΊΠΎΡΠΎΡΡΠ΅ ΠΎΠΏΡΠ΅Π΄Π΅Π»ΡΡΡ Π»ΡΠ±ΠΎΠ΅ ΠΈΠ·ΠΌΠ΅Π½Π΅Π½ΠΈΠ΅ Π² ΡΠ΅ΠΏΠ»ΠΎΠΏΡΠΎΠ²ΠΎΠ΄Π½ΠΎΡΡΠΈ ΠΏΡΠΎΡΠ΅ΠΊΠ°ΡΡΠ΅Π³ΠΎ Π³Π°Π·Π°. Π’Π΅ΡΠΌΠΈΡΡΠΎΡΡ ΡΠΎΠ΅Π΄ΠΈΠ½Π΅Π½Ρ ΠΏΠΎΠ΄ΠΎΠ±Π½ΠΎ ΠΌΠΎΡΡΡ Π£ΠΈΡΡΠΎΠ½Π°, ΡΡΠΎ ΠΏΠΎΠ·Π²ΠΎΠ»ΡΠ΅Ρ ΠΏΡΠΎΠΈΠ·Π²ΠΎΠ΄ΠΈΡΡ ΠΈΠ·ΠΌΠ΅ΡΠ΅Π½ΠΈΠ΅ ΡΠΎΠΊΠΎΠ²ΠΎΠ³ΠΎ ΡΠΈΠ³Π½Π°Π»Π°.
ΠΡΠΎΡ ΡΠΈΠ³Π½Π°Π» Π·Π°ΡΠ΅ΠΌ ΡΡΠΈΠ»ΠΈΠ²Π°Π΅ΡΡΡ ΡΡΠΈΠ»ΠΈΡΠ΅Π»Π΅ΠΌ (5) ΠΈ ΠΏΠ΅ΡΠ΅Π΄Π°Π΅ΡΡΡ Π² Π±Π»ΠΎΠΊ ΡΠ»Π΅ΠΊΡΡΠΎΠ½ΠΈΠΊΠΈ (6). ΠΠ°Π·ΠΎΠ²Π°Ρ Π»ΠΈΠ½ΠΈΡ Π°Π²ΡΠΎΠΌΠ°ΡΠΈΡΠ΅ΡΠΊΠΈ Π½Π°ΡΡΡΠ°ΠΈΠ²Π°Π΅ΡΡΡ Π½Π° Π½ΠΎΠ»Ρ ΠΈ Π½Π΅ ΡΡΠ΅Π±ΡΠ΅Ρ ΡΠ΅Π³ΡΠ»ΠΈΡΠΎΠ²ΠΊΠΈ. Π’Π΅ΡΠΌΠΎΡΡΠ°Π±ΠΈΠ»ΠΈΠ·Π°ΡΠΈΡ ΠΎΠ±Π΅ΡΠΏΠ΅ΡΠΈΠ²Π°Π΅Ρ Π·Π°ΡΠΈΡΡ ΡΡΠ΅ΠΉΠΊΠΈ ΠΎΡ Π²Π»ΠΈΡΠ½ΠΈΡ ΠΎΠΊΡΡΠΆΠ°ΡΡΠ΅ΠΉ ΡΡΠ΅Π΄Ρ.
2.1.3 ΠΠ±ΡΠ°Π±ΠΎΡΠΊΠ° ΠΏΠ΅ΡΠ²ΠΈΡΠ½ΡΡ ΡΠΈΠ³Π½Π°Π»ΠΎΠ² Π΄Π΅ΡΠ΅ΠΊΡΠΎΡΠΎΠ² Π±Π»ΠΎΠΊΠΎΠΌ ΡΠ»Π΅ΠΊΡΡΠΎΠ½ΠΈΠΊΠΈ
ΠΠ»ΠΎΠΊ ΡΠ»Π΅ΠΊΡΡΠΎΠ½ΠΈΠΊΠΈ ΡΠΎΠ΄Π΅ΡΠΆΠΈΡ Π²ΡΠ΅ ΠΊΠΎΠΌΠΏΠΎΠ½Π΅Π½ΡΡ Π΄Π»Ρ ΠΎΠ±ΡΠ°Π±ΠΎΡΠΊΠΈ ΡΠΈΠ³Π½Π°Π»ΠΎΠ² ΠΈ ΠΊΠΎΠ½ΡΡΠΎΠ»Ρ Π²ΡΡΠΈΡΠ»Π΅Π½ΠΈΠΉ.
ΠΠ΅ΡΠ²ΠΈΡΠ½ΡΠ΅ ΡΠΈΠ³Π½Π°Π»Ρ Ρ Π΄Π΅ΡΠ΅ΠΊΡΠΎΡΠΎΠ² ΠΏΠΎΡΡΡΠΏΠ°ΡΡ Π² Π²ΠΈΠ΄Π΅ Π°Π½Π°Π»ΠΎΠ³ΠΎΠ²ΡΡ ΡΠΈΠ³Π½Π°Π»ΠΎΠ², ΠΊΠΎΡΠΎΡΡΠ΅ Ρ ΠΏΠΎΠΌΠΎΡΡΡ Π°Π½Π°Π»ΠΎΠ³ΠΎ-ΡΠΈΡΡΠΎΠ²ΠΎΠ³ΠΎ ΠΊΠΎΠ½Π²Π΅ΡΡΠ΅ΡΠ° ΠΏΡΠ΅ΠΎΠ±ΡΠ°Π·ΡΡΡΡΡ ΠΈ ΠΏΡΠ΅Π΄ΡΡΠ°Π²Π»ΡΡΡΡΡ Π² Π²ΠΈΠ΄Π΅ Π·Π°Π²ΠΈΡΠΈΠΌΠΎΡΡΠΈ ΡΠΈΠ³Π½Π°Π»Π° Π² Π²ΠΎΠ»ΡΡΠ°Ρ ΠΎΡ Π²ΡΠ΅ΠΌΠ΅Π½ΠΈ Π°Π½Π°Π»ΠΈΠ·Π°. ΠΠ΅ΡΠΎΠ΄ΠΈΠΊΠ° ΠΎΠ±ΡΠ°Π±ΠΎΡΠΊΠΈ ΠΏΠ΅ΡΠ²ΠΈΡΠ½ΡΡ Π΄Π°Π½Π½ΡΡ ΡΡΠ°Π²ΠΈΡ Π² ΡΠΎΠΎΡΠ²Π΅ΡΡΡΠ²ΠΈΠ΅ ΡΠΎΠ΄Π΅ΡΠΆΠ°Π½ΠΈΡ Π³Π°Π·ΠΎΠ² Π²Π΅Π»ΠΈΡΠΈΠ½Ρ ΠΏΠ»ΠΎΡΠ°Π΄ΠΈ ΠΏΠΎΠ΄ ΠΊΡΠΈΠ²ΠΎΠΉ, ΠΊΠΎΡΠΎΡΠ°Ρ ΡΠ°ΡΡΡΠΈΡΡΠ²Π°Π΅ΡΡΡ Π°Π²ΡΠΎΠΌΠ°ΡΠΈΡΠ΅ΡΠΊΠΈ. ΠΡΠΈ ΡΡΠΎΠΌ ΡΠ°ΡΡΠ΅Ρ ΠΊΠΎΠ½Π΅ΡΠ½ΠΎΠ³ΠΎ ΡΠ΅Π·ΡΠ»ΡΡΠ°ΡΠ° ΠΏΡΠΎΠΈΠ·Π²ΠΎΠ΄ΠΈΡΡΡ Ρ ΡΡΠ΅ΡΠΎΠΌ ΡΠ»Π΅Π΄ΡΡΡΠ΅Π³ΠΎ:
— ΠΏΡΠΈ ΠΈΠ½ΡΠ΅Π³ΡΠΈΡΠΎΠ²Π°Π½ΠΈΠ΅ Π°Π²ΡΠΎΠΌΠ°ΡΠΈΡΠ΅ΡΠΊΠΈ ΠΊΠΎΡΡΠ΅ΠΊΡΠΈΡΡΠ΅ΡΡΡ Π½ΡΠ»Π΅Π²Π°Ρ ΡΠΎΡΠΊΠ° Π½Π° Π²Π΅Π»ΠΈΡΠΈΠ½Ρ ΠΏΠΎΠΊΠ°Π·Π°Π½ΠΈΠΉ Π΄Π΅ΡΠ΅ΠΊΡΠΎΡΠ° ΠΏΠ΅ΡΠ΅Π΄ Π½Π°ΡΠ°Π»ΠΎΠΌ Π·Π°ΠΌΠ΅ΡΠ°;
— ΠΈΠ· ΡΠ΅Π·ΡΠ»ΡΡΠ°ΡΠΎΠ² ΠΈΠ½ΡΠ΅Π³ΡΠΈΡΠΎΠ²Π°Π½ΠΈΡ Π²ΡΡΠΈΡΠ°Π΅ΡΡΡ Π²Π΅Π»ΠΈΡΠΈΠ½Π° Ρ ΠΎΠ»ΠΎΡΡΠΎΠ³ΠΎ ΠΎΠΏΡΡΠ° (Π½Π° Π²Π΅Π»ΠΈΡΠΈΠ½Ρ Ρ ΠΎΠ»ΠΎΡΡΠΎΠ³ΠΎ ΠΎΠΏΡΡΠ° ΠΎΡΠ½ΠΎΠ²Π½ΠΎΠ΅ Π²Π»ΠΈΡΠ½ΠΈΠ΅ ΠΎΠΊΠ°Π·ΡΠ²Π°Π΅Ρ ΡΠΈΡΡΠΎΡΠ° Π³Π°Π·Π°-Π½ΠΎΡΠΈΡΠ΅Π»Ρ ΠΈ Π³Π°Π·ΠΎΠ½Π°ΡΡΡΠ΅Π½Π½ΠΎΡΡΡ Π³ΡΠ°ΡΠΈΡΠΎΠ²ΡΡ ΡΠΈΠ³Π»Π΅ΠΉ);
— Π΄Π°Π»Π΅Π΅ ΡΠ΅Π·ΡΠ»ΡΡΠ°Ρ ΡΠΌΠ½ΠΎΠΆΠ°Π΅ΡΡΡ Π½Π° Π²Π΅Π»ΠΈΡΠΈΠ½Ρ ΠΊΠ°Π»ΠΈΠ±ΡΠΎΠ²ΠΎΡΠ½ΠΎΠ³ΠΎ ΠΊΠΎΡΡΡΠΈΡΠΈΠ΅Π½ΡΠ°;
— Π·Π°ΡΠ΅ΠΌ ΠΏΡΠΎΠΈΠ·Π²ΠΎΠ΄ΠΈΡΡΡ ΡΠ°ΡΡΠ΅Ρ ΠΊΠΎΠ½ΡΠ΅Π½ΡΡΠ°ΡΠΈΠΈ Π³Π°Π·Π° Ρ ΡΡΠ΅ΡΠΎΠΌ ΠΌΠ°ΡΡΡ ΠΎΠ±ΡΠ°Π·ΡΠ°.
Π‘ΠΎΠΎΡΠ²Π΅ΡΡΡΠ²Π΅Π½Π½ΠΎ, Π΄Π»Ρ ΠΏΠΎΠ»ΡΡΠ΅Π½ΠΈΡ Π΄ΠΎΡΡΠΎΠ²Π΅ΡΠ½ΡΡ Π΄Π°Π½Π½ΡΡ ΠΎ ΡΠΎΠ΄Π΅ΡΠΆΠ°Π½ΠΈΠΈ Π³Π°Π·ΠΎΠ² Π² ΠΈΡΡΠ»Π΅Π΄ΡΠ΅ΠΌΠΎΠΌ ΠΌΠ΅ΡΠ°Π»Π»Π΅ Π½Π΅ΠΎΠ±Ρ ΠΎΠ΄ΠΈΠΌΠΎ ΠΏΡΠ΅Π΄Π²Π°ΡΠΈΡΠ΅Π»ΡΠ½ΠΎ:
Π°) ΠΏΠΎΠ΄ΠΎΠ±ΡΠ°ΡΡ ΠΏΠ°ΡΠ°ΠΌΠ΅ΡΡΠΎΠ² ΠΌΠ΅ΡΠΎΠ΄ΠΈΠΊΠΈ, ΠΊΠΎΡΠΎΡΡΠ΅ ΠΎΠ±Π΅ΡΠΏΠ΅ΡΠΈΠ²Π°ΡΡ:
— ΡΡΠ°Π±ΠΈΠ»ΡΠ½ΠΎΡΡΡ ΠΏΠΎΠΊΠ°Π·Π°Π½ΠΈΠΉ Π΄Π΅ΡΠ΅ΠΊΡΠΎΡΠ° ΠΏΠ΅ΡΠ΅Π΄ Π½Π°ΡΠ°Π»ΠΎΠΌ Π°Π½Π°Π»ΠΈΠ·ΠΎΠ²;
— ΡΡΠ°Π±ΠΈΠ»ΡΠ½ΠΎΡΡΡ Π·Π½Π°ΡΠ΅Π½ΠΈΠΉ Ρ ΠΎΠ»ΠΎΡΡΠΎΠ³ΠΎ ΠΎΠΏΡΡΠ° (Π±Π΅Π· ΠΌΠ΅ΡΠ°Π»Π»Π°);
— ΡΡΠ°Π±ΠΈΠ»ΡΠ½ΠΎΡΡΡ ΡΠ΅Π·ΡΠ»ΡΡΠ°ΡΠΎΠ² Π°Π½Π°Π»ΠΈΠ·Π° ΡΡΠ°Π½Π΄Π°ΡΡΠ½ΡΡ ΠΎΠ±ΡΠ°Π·ΡΠΎΠ² Ρ ΠΈΠ·Π²Π΅ΡΡΠ½ΡΠΌ ΡΠΎΠ΄Π΅ΡΠΆΠ°Π½ΠΈΠ΅ΠΌ Π³Π°Π·ΠΎΠ²;
Π±) ΠΏΡΠΈ Π½Π΅ΠΎΠ±Ρ ΠΎΠ΄ΠΈΠΌΠΎΡΡΠΈ Π·Π°Π΄Π°ΡΡ ΠΊΠΎΡΡΠ΅ΠΊΡΠΈΡΠΎΠ²ΠΊΡ Π½Π° Π²Π΅Π»ΠΈΡΠΈΠ½Ρ Ρ ΠΎΠ»ΠΎΡΡΠΎΠ³ΠΎ ΠΎΠΏΡΡΠ° Ρ ΠΈΡΠΏΠΎΠ»ΡΠ·ΠΎΠ²Π°Π½ΠΈΠ΅ΠΌ ΠΈΠ½ΡΠ΅ΡΡΠ΅ΠΉΡΠ° ΠΏΡΠΎΠ³ΡΠ°ΠΌΠΌΠ½ΠΎΠ³ΠΎ ΠΎΠ±Π΅ΡΠΏΠ΅ΡΠ΅Π½ΠΈΡ;
Π²) ΠΏΡΠΈ Π½Π΅ΠΎΠ±Ρ ΠΎΠ΄ΠΈΠΌΠΎΡΡΠΈ ΠΏΡΠΎΠ²Π΅ΡΡΠΈ ΠΊΠ°Π»ΠΈΠ±ΡΠΎΠ²ΠΊΡ ΡΠ΅Π·ΡΠ»ΡΡΠ°ΡΠΎΠ² Π½Π° ΠΎΡΠ½ΠΎΠ²Π°Π½ΠΈΠΈ Π΄Π°Π½Π½ΡΡ Π°Π½Π°Π»ΠΈΠ·Π° ΡΡΠ°Π½Π΄Π°ΡΡΠ½ΡΡ ΠΎΠ±ΡΠ°Π·ΡΠΎΠ² Ρ ΠΈΡΠΏΠΎΠ»ΡΠ·ΠΎΠ²Π°Π½ΠΈΠ΅ΠΌ ΠΈΠ½ΡΠ΅ΡΡΠ΅ΠΉΡΠ° ΠΏΡΠΎΠ³ΡΠ°ΠΌΠΌΠ½ΠΎΠ³ΠΎ ΠΎΠ±Π΅ΡΠΏΠ΅ΡΠ΅Π½ΠΈΡ.
2.1.4 Π£ΠΏΡΠ°Π²Π»Π΅Π½ΠΈΠ΅ Π°Π½Π°Π»ΠΈΠ·ΠΎΠΌ
Π£ΠΏΡΠ°Π²Π»Π΅Π½ΠΈΠ΅ ΠΏΡΠΎΠ²Π΅Π΄Π΅Π½ΠΈΠ΅ΠΌ Π°Π½Π°Π»ΠΈΠ·Π° Π³Π°Π·ΠΎΠ½Π°ΡΡΡΠ΅Π½Π½ΠΎΡΡΠΈ ΠΌΠ΅ΡΠ°Π»Π»Π° Π°Π²ΡΠΎΠΌΠ°ΡΠΈΠ·ΠΈΡΠΎΠ²Π°Π½ΠΎ ΠΈ ΠΎΡΡΡΠ΅ΡΡΠ²Π»ΡΠ΅ΡΡΡ Ρ ΠΊΠΎΠΌΠΏΡΡΡΠ΅ΡΠ° Ρ ΠΏΠΎΠΌΠΎΡΡΡ ΡΠΏΠ΅ΡΠΈΠ°Π»ΡΠ½ΠΎΠ³ΠΎ ΠΏΡΠΎΠ³ΡΠ°ΠΌΠΌΠ½ΠΎΠ³ΠΎ ΠΎΠ±Π΅ΡΠΏΠ΅ΡΠ΅Π½ΠΈΡ.
ΠΠ΅ΡΠ΅Π΄ Π½Π°ΡΠ°Π»ΠΎΠΌ Π°Π½Π°Π»ΠΈΠ·Π° Π½Π΅ΠΎΠ±Ρ ΠΎΠ΄ΠΈΠΌΠΎ Π²ΡΠ±ΡΠ°ΡΡ ΠΎΠ΄Π½Ρ ΠΈΠ· ΡΡΡΠ΅ΡΡΠ²ΡΡΡΠΈΡ ΠΌΠ΅ΡΠΎΠ΄ΠΈΠΊ ΠΈΠ»ΠΈ ΡΠΎΠ·Π΄Π°ΡΡ Π½ΠΎΠ²ΡΡ. ΠΠ΅ΡΠΎΠ΄ΠΈΠΊΠ° Π°Π½Π°Π»ΠΈΠ·Π° ΡΠΎΡΡΠΎΠΈΡ ΠΈΠ· Π½Π΅ΡΠΊΠΎΠ»ΡΠΊΠΈΡ ΡΡΠ°ΠΏΠΎΠ²:
— ΠΏΡΠ΅Π΄Π²Π°ΡΠΈΡΠ΅Π»ΡΠ½Π°Ρ Π΄Π΅Π³Π°Π·Π°ΡΠΈΡ ΡΠΈΠ³Π»Ρ;
— ΠΏΡΠΎΠ΄ΡΠ²ΠΊΠ° ΡΠΈΡΡΠ΅ΠΌΡ;
— ΡΡΠ°Π±ΠΈΠ»ΠΈΠ·Π°ΡΠΈΡ ΠΏΠΎΠΊΠ°Π·Π°Π½ΠΈΠΉ Π΄Π΅ΡΠ΅ΠΊΡΠΎΡΠΎΠ²;
— ΡΠΎΠ±ΡΡΠ²Π΅Π½Π½ΠΎ Π°Π½Π°Π»ΠΈΠ·.
ΠΡΠ½ΠΎΠ²Π½ΡΠ΅ Π·Π°Π΄Π°Π²Π°Π΅ΠΌΡΠ΅ ΠΏΠ°ΡΠ°ΠΌΠ΅ΡΡΡ ΠΌΠ΅ΡΠΎΠ΄ΠΈΠΊΠΈ:
— ΠΌΠΎΡΠ½ΠΎΡΡΡ ΠΈ Π²ΡΠ΅ΠΌΡ Π΄Π΅Π³Π°Π·Π°ΡΠΈΠΈ;
— Π²ΡΠ΅ΠΌΡ ΠΏΡΠΎΠ΄ΡΠ²ΠΊΠΈ (ΠΈΠ½ΡΠ΅Π½ΡΠΈΠ²Π½ΠΎΡΡΡ Π·Π°Π΄Π°Π΅ΡΡΡ ΡΠ°Π½Π΅Π΅ Π΄Π»Ρ Π²ΡΠ΅Ρ ΠΌΠ΅ΡΠΎΠ΄ΠΈΠΊ);
— Π²ΡΠ΅ΠΌΡ Π²ΡΠ΄Π΅ΡΠΆΠΊΠΈ Π΄Π»Ρ ΡΡΠ°Π±ΠΈΠ»ΠΈΠ·Π°ΡΠΈΠΈ ΠΏΠΎΠΊΠ°Π·Π°Π½ΠΈΠΉ Π΄Π΅ΡΠ΅ΠΊΡΠΎΡΠΎΠ²;
— ΠΌΠΈΠ½ΠΈΠΌΠ°Π»ΡΠ½ΠΎΠ΅ ΠΈ ΠΌΠ°ΠΊΡΠΈΠΌΠ°Π»ΡΠ½ΠΎΠ΅ Π²ΡΠ΅ΠΌΡ Π°Π½Π°Π»ΠΈΠ·Π°;
— ΡΠ΅ΠΆΠΈΠΌ ΠΏΠΎΠ΄Π²ΠΎΠ΄Π° ΠΌΠΎΡΠ½ΠΎΡΡΠΈ Π² ΠΏΠ΅ΡΡ Π²ΠΎ Π²ΡΠ΅ΠΌΡ Π°Π½Π°Π»ΠΈΠ·Π° (ΠΏΡΠΈ ΡΡΠΎΠΌ Π²ΠΎΠ·ΠΌΠΎΠΆΠ½ΠΎ ΠΊΠ°ΠΊ ΠΌΠΎΠ½ΠΎΡΠΎΠ½Π½ΠΎΠ΅, ΡΠ°ΠΊ ΠΈ ΡΡΡΠΏΠ΅Π½ΡΠ°ΡΠΎΠ΅ ΠΈΠ·ΠΌΠ΅Π½Π΅Π½ΠΈΠ΅ ΠΌΠΎΡΠ½ΠΎΡΡΠΈ Π² ΡΠ΅ΡΠ΅Π½ΠΈΠ΅ Π·Π°Π΄Π°Π²Π°Π΅ΠΌΠΎΠ³ΠΎ Π²ΡΠ΅ΠΌΠ΅Π½ΠΈ ΡΠ°Π±ΠΎΡΡ ΠΏΠΎΠ΄ ΡΠΎΠΊΠΎΠΌ).
ΠΠ΅ΠΎΠ±Ρ ΠΎΠ΄ΠΈΠΌΠΎ ΠΏΡΠΎΠΈΠ·Π²Π΅ΡΡΠΈ Π²Π·Π²Π΅ΡΠΈΠ²Π°Π½ΠΈΠ΅ ΠΎΠ±ΡΠ°Π·ΡΠ° (ΠΏΡΠΈ Π½Π΅ΠΎΠ±Ρ ΠΎΠ΄ΠΈΠΌΠΎΡΡΠΈ ΠΏΡΠ΅Π΄Π²Π°ΡΠΈΡΠ΅Π»ΡΠ½ΠΎ ΠΏΡΠΎΠΈΠ·Π²Π΅Π΄Ρ ΡΠ°ΡΠΈΡΠΎΠ²ΠΊΡ Π²Π΅ΡΠΎΠ²) ΠΈ Π·Π°Π³ΡΡΠ·ΠΈΡΡ Π΅Π³ΠΎ Π² ΡΠ»ΡΠ·ΡΡΡΠ΅Π΅ ΡΡΡΡΠΎΠΉΡΡΠ²ΠΎ. ΠΠ°Π΄Π°ΡΡ ΠΈΠ΄Π΅Π½ΡΠΈΡΠΈΠΊΠ°ΡΠΈΠΎΠ½Π½ΠΎΠ΅ ΠΎΠ±ΠΎΠ·Π½Π°ΡΠ΅Π½ΠΈΠ΅ ΠΎΠ±ΡΠ°Π·ΡΠ°.
ΠΠ°Π»ΡΠ½Π΅ΠΉΡΠΈΠΉ Π°Π½Π°Π»ΠΈΠ· ΠΏΡΠΎΠΈΠ·Π²ΠΎΠ΄ΠΈΡΡΡ Π°Π²ΡΠΎΠΌΠ°ΡΠΈΡΠ΅ΡΠΊΠΈ Ρ ΡΠΊΠ°Π·Π°Π½ΠΈΠ΅ΠΌ ΡΠ΅ΠΊΡΡΠ΅ΠΉ ΡΡΠ°Π΄ΠΈΠΈ Π½Π° ΡΠΊΡΠ°Π½Π΅ Π΄ΠΈΡΠΏΠ»Π΅Ρ. Π ΠΊΠΎΠ½ΡΠ΅ Π½Π° ΡΠΊΡΠ°Π½ Π²ΡΠ²ΠΎΠ΄ΡΡΡΡ ΡΠ΅Π·ΡΠ»ΡΡΠ°ΡΡ Π°Π½Π°Π»ΠΈΠ·Π° Π΄Π»Ρ ΡΠΎΠΎΡΠ²Π΅ΡΡΡΠ²ΡΡΡΠΈΡ Π³Π°Π·ΠΎΠ² Π² ppm.
2.2 ΠΠ΅ΡΠΎΠ΄ΠΈΠΊΠ° ΠΈΡΡΠ»Π΅Π΄ΠΎΠ²Π°Π½ΠΈΡ ΡΠ°Π²Π½ΠΎΠ²Π΅ΡΠ½ΠΎΡΡΠΈ ΡΠ°ΡΠΏΠ»Π°Π²Π°
Π Π°Π²Π½ΠΎΠ²Π΅ΡΠ½ΠΎΡΡΡ ΡΠ°ΡΠΏΠ»Π°Π²Π° ΠΎΡΠ΅Π½ΠΈΠ²Π°Π»ΠΈ ΠΌΠ΅ΡΠΎΠ΄ΠΎΠΌ Π²ΠΈΡΠΊΠΎΠ·ΠΈΠΌΠ΅ΡΡΠΈΠΈ. ΠΠ»Ρ ΠΈΡΡΠ»Π΅Π΄ΠΎΠ²Π°Π½ΠΈΠΉ Π±ΡΠ» ΠΈΡΠΏΠΎΠ»ΡΠ·ΠΎΠ²Π°Π½ ΠΌΠ΅ΡΠΎΠ΄ ΠΊΡΡΡΠΈΠ»ΡΠ½ΡΡ ΠΊΠΎΠ»Π΅Π±Π°Π½ΠΈΠΉ ΡΠΈΠ³Π»Ρ Ρ ΠΌΠ΅ΡΠ°Π»Π»ΠΎΠΌ. ΠΠ³ΠΎ ΠΏΡΠ΅ΠΈΠΌΡΡΠ΅ΡΡΠ²ΠΎΠΌ ΡΠ²Π»ΡΠ΅ΡΡΡ ΠΎΠΊΠ°Π·Π°Π½ΠΈΠ΅ ΠΌΠΈΠ½ΠΈΠΌΠ°Π»ΡΠ½ΠΎΠ³ΠΎ Π²ΠΎΠ·ΠΌΡΡΠ°ΡΡΠ΅Π³ΠΎ Π²ΠΎΠ·Π΄Π΅ΠΉΡΡΠ²ΠΈΡ Π½Π° ΡΡΡΡΠΊΡΡΡΡ ΠΆΠΈΠ΄ΠΊΠΎΠ³ΠΎ ΠΌΠ΅ΡΠ°Π»Π»Π°.
2.2.1 ΠΠΊΡΠΏΠ΅ΡΠΈΠΌΠ΅Π½ΡΠ°Π»ΡΠ½Π°Ρ ΡΡΡΠ°Π½ΠΎΠ²ΠΊΠ°
ΠΠΊΡΠΏΠ΅ΡΠΈΠΌΠ΅Π½ΡΡ ΠΏΡΠΎΠ²ΠΎΠ΄ΠΈΠ»ΠΈ Π² Π²Π°ΠΊΡΡΠΌΠ½ΠΎΠΌ Π²ΡΡΠΎΠΊΠΎΡΠ΅ΠΌΠΏΠ΅ΡΠ°ΡΡΡΠ½ΠΎΠΌ Π²ΠΈΡΠΊΠΎΠ·ΠΈΠΌΠ΅ΡΡΠ΅ Π² Π°ΡΠΌΠΎΡΡΠ΅ΡΠ΅ Π³Π΅Π»ΠΈΡ Ρ ΠΈΡΠΏΠΎΠ»ΡΠ·ΠΎΠ²Π°Π½ΠΈΠ΅ΠΌ ΡΠΈΠ³Π»Π΅ΠΉ ΠΈΠ· ΡΠ°Π·Π»ΠΈΡΠ½ΡΡ ΠΎΠ³Π½Π΅ΡΠΏΠΎΡΠ½ΡΡ ΠΌΠ°ΡΠ΅ΡΠΈΠ°Π»ΠΎΠ²: ΠΎΠΊΡΠΈΠ΄Π° ΡΠΈΡΠΊΠΎΠ½ΠΈΡ, ΠΎΠΊΡΠΈΠ΄Π° Π°Π»ΡΠΌΠΈΠ½ΠΈΡ ΠΈ ΠΎΠΊΡΠΈΠ΄Π° Π±Π΅ΡΠΈΠ»Π»ΠΈΡ.
Π£ΡΡΠ°Π½ΠΎΠ²ΠΊΠ° Π΄Π»Ρ ΠΈΡΡΠ»Π΅Π΄ΠΎΠ²Π°Π½ΠΈΡ ΠΊΠΈΠ½Π΅ΠΌΠ°ΡΠΈΡΠ΅ΡΠΊΠΎΠΉ Π²ΡΠ·ΠΊΠΎΡΡΠΈ ΠΆΠΈΠ΄ΠΊΠΈΡ ΠΌΠ΅ΡΠ°Π»Π»ΠΎΠ², ΡΡΡΡΠΎΠΉΡΡΠ²ΠΎ ΠΊΠΎΡΠΎΡΠΎΠΉ ΠΏΠΎΠΊΠ°Π·Π°Π½ΠΎ Π½Π° ΡΠΈΡ. 2.2, 2.3, 2.4, Π²ΠΊΠ»ΡΡΠ°Π΅Ρ Π²ΡΡΠΎΠΊΠΎΡΠ΅ΠΌΠΏΠ΅ΡΠ°ΡΡΡΠ½ΡΠΉ Π²ΠΈΡΠΊΠΎΠ·ΠΈΠΌΠ΅ΡΡ, Π²Π°ΠΊΡΡΠΌΠ½ΡΡ ΡΠΈΡΡΠ΅ΠΌΡ, ΡΠΈΡΡΠ΅ΠΌΡ ΡΠ»Π΅ΠΊΡΡΠΎΠΏΠΈΡΠ°Π½ΠΈΡ, ΡΠΈΡΡΠ΅ΠΌΡ Π²ΠΎΠ΄ΡΠ½ΠΎΠ³ΠΎ ΠΎΡ Π»Π°ΠΆΠ΄Π΅Π½ΠΈΡ, ΡΠΈΡΡΠ΅ΠΌΡ ΠΏΠΎΠ΄Π°ΡΠΈ Π³Π°Π·ΠΎΠ², ΡΠΈΡΡΠ΅ΠΌΡ ΠΊΠΎΠ½ΡΡΠΎΠ»ΡΠ½ΠΎ-ΠΈΠ·ΠΌΠ΅ΡΠΈΡΠ΅Π»ΡΠ½ΡΡ ΠΏΡΠΈΠ±ΠΎΡΠΎΠ². ΠΠΈΡΠΊΠΎΠ·ΠΈΠΌΠ΅ΡΡ (ΡΠΈΡ. 2.3) ΠΏΡΠ΅Π΄ΡΡΠ°Π²Π»Π΅Π½ Π²ΡΡΠΎΠΊΠΎΡΠ΅ΠΌΠΏΠ΅ΡΠ°ΡΡΡΠ½ΠΎΠΉ Π²Π°ΠΊΡΡΠΌΠ½ΠΎΠΉ ΡΠ»Π΅ΠΊΡΡΠΎΠΏΠ΅ΡΡΡ ΡΠΎΠΏΡΠΎΡΠΈΠ²Π»Π΅Π½ΠΈΡ, ΡΠΎΡΡΠΎΡΡΠ΅ΠΉ ΠΈΠ· ΠΊΠΎΡΠΏΡΡΠ° (1), Π½ΠΈΠΆΠ½Π΅ΠΉ ΠΊΡΡΡΠΊΠΈ (2), ΡΡΡΠ±Ρ (3) Ρ ΠΏΠ°ΡΡΡΠ±ΠΊΠΎΠΌ (4). ΠΠΎΡΠΏΡΡ ΠΏΠ΅ΡΠΈ ΠΈ Π½ΠΈΠΆΠ½ΡΡ ΠΊΡΡΡΠΊΠ° ΠΎΡ Π»Π°ΠΆΠ΄Π°Π»ΠΈΡΡ Π²ΠΎΠ΄ΠΎΠΉ. ΠΠ° ΠΊΠΎΡΠΏΡΡΠ΅ ΡΠΊΡΠ΅ΠΏΠ»Π΅Π½Ρ ΠΊΠ°ΡΡΡΠΊΠΈ ΡΡΠ°ΡΠΎΡΠ° (5), ΠΊ ΠΊΠΎΡΠΎΡΡΠΌ ΠΏΠΎΠ΄Π°Π²Π°Π»ΠΈ ΡΡΠ΅Ρ ΡΠ°Π·Π½ΠΎΠ΅ Π½Π°ΠΏΡΡΠΆΠ΅Π½ΠΈΠ΅, ΡΠΎΠ·Π΄Π°ΡΡΠ΅Π΅ Π²ΡΠ°ΡΠ°ΡΡΠ΅Π΅ΡΡ ΠΌΠ°Π³Π½ΠΈΡΠ½ΠΎΠ΅ ΠΏΠΎΠ»Π΅ Π΄Π»Ρ Π·Π°ΠΊΡΡΡΠΈΠ²Π°Π½ΠΈΡ ΡΠΈΠ³Π»Ρ Ρ ΠΌΠ΅ΡΠ°Π»Π»ΠΎΠΌ. Π§Π΅ΡΠ΅Π· Π²Π°ΠΊΡΡΠΌΠ½ΡΠ΅ ΡΠΏΠ»ΠΎΡΠ½Π΅Π½ΠΈΡ Π² Π½ΠΈΠΆΠ½Π΅ΠΉ ΠΊΡΡΡΠΊΠ΅ Π²ΠΎ Π²Π½ΡΡΡΠ΅Π½Π½Π΅Π΅ ΠΏΡΠΎΡΡΡΠ°Π½ΡΡΠ²ΠΎ ΠΏΠ΅ΡΠΈ Π²Π²Π΅Π΄Π΅Π½Ρ ΡΠ΅ΡΠΌΠΎΠΏΠ°ΡΠ° (8) ΠΈ Π²ΠΎΠ΄ΠΎΠΎΡ Π»Π°ΠΆΠ΄Π°Π΅ΠΌΡΠ΅ ΠΌΠ΅Π΄Π½ΡΠ΅ ΡΠΎΠΊΠΎΠΏΠΎΠ΄Π²ΠΎΠ΄Ρ (6), ΡΠΎΠ΅Π΄ΠΈΠ½Π΅Π½Π½ΡΠ΅ Π±ΠΈΡΠΈΠ»ΡΡΠ½ΡΠΌ ΠΌΠΎΠ»ΠΈΠ±Π΄Π΅Π½ΠΎΠ²ΡΠΌ Π½Π°Π³ΡΠ΅Π²Π°ΡΠ΅Π»Π΅ΠΌ (7), ΠΎΠΊΡΡΠΆΠ΅Π½Π½ΡΠΌ ΡΠΈΡΡΠ΅ΠΌΠΎΠΉ ΡΠΈΠ»ΠΈΠ½Π΄ΡΠΈΡΠ΅ΡΠΊΠΈΡ ΠΈ ΡΠΎΡΡΠ΅Π²ΡΡ (Π²Π΅ΡΡ Π½ΠΈΡ ΠΈ Π½ΠΈΠΆΠ½ΠΈΡ ) ΡΠΊΡΠ°Π½ΠΎΠ² (11).
ΠΠ° ΡΠ΅Ρ Π»Π΅ ΡΠ΅ΡΠΌΠΎΠΏΠ°ΡΡ ΡΡΡΠ°Π½ΠΎΠ²Π»Π΅Π½Π° Π΄ΠΎΠΏΠΎΠ»Π½ΠΈΡΠ΅Π»ΡΠ½Π°Ρ ΡΠΈΡΡΠ΅ΠΌΠ° ΡΠΊΡΠ°Π½ΠΎΠ², ΠΏΠΎΠ΄Π°Π²Π»ΡΡΡΠ°Ρ ΠΊΠΎΠ½Π²Π΅ΠΊΡΠΈΠ²Π½ΡΠ΅ ΠΏΠΎΡΠΎΠΊΠΈ Π³Π°Π·Π° Π² ΠΈΠ·ΠΎΡΠ΅ΡΠΌΠΈΡΠ΅ΡΠΊΠΎΠΉ Π·ΠΎΠ½Π΅ ΠΏΠ΅ΡΠΈ.
Π ΠΈΡ. 2.2. Π‘Ρ Π΅ΠΌΠ° ΡΡΡΠ°Π½ΠΎΠ²ΠΊΠΈ Π΄Π»Ρ ΠΈΠ·ΡΡΠ΅Π½ΠΈΡ ΠΊΠΈΠ½Π΅ΠΌΠ°ΡΠΈΡΠ΅ΡΠΊΠΎΠΉ Π²ΡΠ·ΠΊΠΎΡΡΠΈ ΠΌΠ΅ΡΠ°Π»Π»ΠΈΡΠ΅ΡΠΊΠΈΡ ΡΠ°ΡΠΏΠ»Π°Π²ΠΎΠ²
ΠΠ±ΠΎΠ·Π½Π°ΡΠ΅Π½ΠΈΡ — Π² ΡΠ΅ΠΊΡΡΠ΅.
Π ΠΈΡ. 2.3. Π‘Ρ Π΅ΠΌΠ° Π²ΡΡΠΎΠΊΠΎΡΠ΅ΠΌΠΏΠ΅ΡΠ°ΡΡΡΠ½ΠΎΠ³ΠΎ Π²ΠΈΡΠΊΠΎΠ·ΠΈΠΌΠ΅ΡΡΠ° ΠΠ±ΠΎΠ·Π½Π°ΡΠ΅Π½ΠΈΡ Π² ΡΠ΅ΠΊΡΡΠ΅.
Π ΠΈΡ. 2.4. Π‘Ρ Π΅ΠΌΠ° ΠΏΠΎΠ΄Π²Π΅ΡΠ½ΠΎΠΉ ΡΠΈΡΡΠ΅ΠΌΡ ΠΠ±ΠΎΠ·Π½Π°ΡΠ΅Π½ΠΈΡ Π² ΡΠ΅ΠΊΡΡΠ΅.
Π ΡΡΡΠ±Π΅ (3) Π½Π° ΡΡΠΎΠ²Π½Π΅ Π·Π΅ΡΠΊΠ°Π»Π° ΠΏΠΎΠ΄Π²Π΅ΡΠ½ΠΎΠΉ ΡΠΈΡΡΠ΅ΠΌΡ Π½Π°Ρ ΠΎΠ΄ΠΈΡΡΡ ΠΎΠΊΠ½ΠΎ (13) Π΄Π»Ρ ΡΠ΅Π³ΠΈΡΡΡΠ°ΡΠΈΠΈ ΠΏΠ°ΡΠ°ΠΌΠ΅ΡΡΠΎΠ² ΠΊΠΎΠ»Π΅Π±Π°Π½ΠΈΠΉ ΡΠΈΠ³Π»Ρ. ΠΠ° ΠΏΠ°ΡΡΡΠ±ΠΊΠ΅ (4) Π·Π°ΠΊΡΠ΅ΠΏΠ»Π΅Π½Ρ Π²Π°ΠΊΡΡΠΌΠ½ΡΠ΅ Π²Π²ΠΎΠ΄Ρ Π΄Π»Ρ ΡΠ΅ΡΠΌΠΎΠΏΠ°ΡΠ½ΠΎΠΉ Π»Π°ΠΌΠΏΡ ΠΈ ΠΌΠ°Π½ΠΎΠ²Π°ΠΊΡΡΠΌΠ΅ΡΡΠ° ΠΈ ΡΡΡΠ±Π°, ΡΠΎΠ΅Π΄ΠΈΠ½ΡΡΡΠ°Ρ Π²ΠΈΡΠΊΠΎΠ·ΠΈΠΌΠ΅ΡΡ Ρ ΡΠΈΡΡΠ΅ΠΌΠΎΠΉ ΠΏΠΎΠ΄Π°ΡΠΈ Π³Π°Π·Π°. ΠΠ° ΡΠ»Π°Π½ΡΠ΅ ΠΏΠ°ΡΡΡΠ±ΠΊΠ° ΡΡΡΠ°Π½ΠΎΠ²Π»Π΅Π½ Π΄ΠΈΡΡΡΠ·ΠΈΠΎΠ½Π½ΡΠΉ Π½Π°ΡΠΎΡ (12). ΠΡΠ΅ ΡΠ°Π·ΡΠ΅ΠΌΠ½ΡΠ΅ ΡΠΎΠ΅Π΄ΠΈΠ½Π΅Π½ΠΈΡ Π²ΠΈΡΠΊΠΎΠ·ΠΈΠΌΠ΅ΡΡΠ° Π³Π΅ΡΠΌΠ΅ΡΠΈΠ·ΠΈΡΠΎΠ²Π°Π½Ρ ΡΠΏΠ»ΠΎΡΠ½ΠΈΡΠ΅Π»ΡΠ½ΡΠΌΠΈ ΠΏΡΠΎΠΊΠ»Π°Π΄ΠΊΠ°ΠΌΠΈ (9) ΠΈΠ· Π²Π°ΠΊΡΡΠΌΠ½ΠΎΠΉ ΡΠ΅Π·ΠΈΠ½Ρ.
ΠΠΈΡΠΊΠΎΠ·ΠΈΠΌΠ΅ΡΡ Ρ ΠΏΠΎΠΌΠΎΡΡΡ ΡΠ΅Π³ΡΠ»ΠΈΡΠΎΠ²ΠΎΡΠ½ΡΡ Π²ΠΈΠ½ΡΠΎΠ² ΡΡΡΠ°Π½ΠΎΠ²Π»Π΅Π½ Π½Π° ΠΊΠΎΠ½ΡΠΎΠ»ΡΠ½ΠΎΠΉ ΠΎΠΏΠΎΡΠ΅, ΠΊΡΠ΅ΠΏΡΡΠ΅ΠΉΡΡ ΠΊ ΠΊΠ°ΠΏΠΈΡΠ°Π»ΡΠ½ΠΎΠΉ ΡΡΠ΅Π½Π΅, ΡΡΠΎ ΠΈΡΠΊΠ»ΡΡΠ°Π»ΠΎ Π²ΠΎΠ·Π½ΠΈΠΊΠ½ΠΎΠ²Π΅Π½ΠΈΠ΅ ΠΊΠ°ΡΠ°ΡΠ΅Π»ΡΠ½ΡΡ ΠΊΠΎΠ»Π΅Π±Π°Π½ΠΈΠΉ ΠΏΠΎΠ΄Π²Π΅ΡΠ½ΠΎΠΉ ΡΠΈΡΡΠ΅ΠΌΡ Π·Π° ΡΡΠ΅Ρ Π²Π½Π΅ΡΠ½ΠΈΡ Π²ΠΎΠ·ΠΌΡΡΠ΅Π½ΠΈΠΉ ΠΈ Π΄Π°Π²Π°Π»ΠΎ Π²ΠΎΠ·ΠΌΠΎΠΆΠ½ΠΎΡΡΡ Π½Π°ΡΡΡΠ°ΠΈΠ²Π°ΡΡ ΠΎΡΡ Π²ΠΈΡΠΊΠΎΠ·ΠΈΠΌΠ΅ΡΡΠ° ΡΡΡΠΎΠ³ΠΎ Π²Π΅ΡΡΠΈΠΊΠ°Π»ΡΠ½ΠΎ.
ΠΠ°ΠΊΡΡΠΌΠ½Π°Ρ ΡΠΈΡΡΠ΅ΠΌΠ° ΡΡΡΠ°Π½ΠΎΠ²ΠΊΠΈ (ΡΠΈΡ. 2.2) Π²ΠΊΠ»ΡΡΠ°Π΅Ρ ΡΠΎΡΠ²Π°ΠΊΡΡΠΌΠ½ΡΠΉ (2ΠΠΠ -5ΠΠ) ΠΈ Π΄ΠΈΡΡΡΠ·ΠΈΠΎΠ½Π½ΡΠΉ (Π¦ΠΠ-100) Π½Π°ΡΠΎΡΡ (8,9) ΠΈ ΠΏΠΎΠ·Π²ΠΎΠ»ΡΠ΅Ρ ΡΠΎΠ·Π΄Π°Π²Π°ΡΡΡΠ°Π·ΡΡΠΆΠ΅Π½ΠΈΠ΅ Π΄ΠΎ 0,0133 ΠΠ° (10-4 ΠΌΠΌ.ΡΡ.ΡΡ.). ΠΠ°Π²Π»Π΅Π½ΠΈΠ΅ Π² ΡΠΈΡΡΠ΅ΠΌΠ΅ ΠΈΠ·ΠΌΠ΅ΡΡΠ»ΠΈ Ρ ΠΏΠΎΠΌΠΎΡΡΡ ΠΌΠ΅ΠΌΠ±ΡΠ°Π½Π½ΠΎΠ³ΠΎ ΠΌΠ°Π½ΠΎΠ²Π°ΠΊΡΡΠΌΠ΅ΡΡΠ° (12), ΡΠ΅ΡΠΌΠΎΠΏΠ°ΡΠ½ΠΎΠΉ Π»Π°ΠΌΠΏΡ ΠΠ’-2 (11) ΠΈ Π²Π°ΠΊΡΡΠΌΠΌΠ΅ΡΡΠ° ΠΠΠ’-2 (10).
ΠΠ°ΠΏΡΡΠΆΠ΅Π½ΠΈΠ΅ Π½Π° Π½Π°Π³ΡΠ΅Π²Π°ΡΠ΅Π»Ρ ΠΏΠΎΠ΄Π°Π²Π°Π»ΠΈ ΡΠ΅ΡΠ΅Π· ΡΠΈΠ»ΠΎΠ²ΠΎΠΉ ΠΏΠΎΠ½ΠΈΠΆΠ°ΡΡΠΈΠΉ ΡΡΠ°Π½ΡΡΠΎΡΠΌΠ°ΡΠΎΡ (2) ΠΌΠΎΡΠ½ΠΎΡΡΡΡ 15 ΠΊΠΡ. ΠΠ»Π°Π²Π½ΡΡ ΡΠ΅Π³ΡΠ»ΠΈΡΠΎΠ²ΠΊΡ Π½Π°ΠΏΡΡΠΆΠ΅Π½ΠΈΡ ΠΎΠ±Π΅ΡΠΏΠ΅ΡΠΈΠ²Π°Π»ΠΈ ΡΠΈΡΠΈΡΡΠΎΡΠ½ΡΠΌ ΡΠ΅Π³ΡΠ»ΡΡΠΎΡΠΎΠΌ (3) ΠΌΠ°ΡΠΊΠΈ ΠΠ Π’-3, ΡΡΠΎ ΠΎΠ±Π΅ΡΠΏΠ΅ΡΠΈΠ²Π°Π»ΠΎ ΡΡΡΠ°Π½ΠΎΠ²Π»Π΅Π½ΠΈΠ΅ ΡΡΠ΅Π±ΡΠ΅ΠΌΠΎΠΉ ΡΠ΅ΠΌΠΏΠ΅ΡΠ°ΡΡΡΡ Π·Π° 1−2 ΠΌΠΈΠ½ΡΡΡ ΠΈ Π΅Π΅ ΠΏΠΎΠ΄Π΄Π΅ΡΠΆΠ°Π½ΠΈΠ΅ Ρ ΡΠΎΡΠ½ΠΎΡΡΡΡ ± 20Π‘. Π’Π΅ΠΌΠΏΠ΅ΡΠ°ΡΡΡΡ Π² ΠΈΠ·ΠΎΡΠ΅ΡΠΌΠΈΡΠ΅ΡΠΊΠΎΠΉ Π·ΠΎΠ½Π΅ ΠΏΠ΅ΡΠΈ ΠΈΠ·ΠΌΠ΅ΡΡΠ»ΠΈ Ρ ΠΏΠΎΠΌΠΎΡΡΡ ΡΠ΅ΡΠΌΠΎΠΏΠ°ΡΡ ΠΠ 5/20, Ρ ΠΎΠ»ΠΎΠ΄Π½ΡΠ΅ ΠΊΠΎΠ½ΡΡ ΠΊΠΎΡΠΎΡΠΎΠΉ ΡΠ΅ΡΠΌΠΎΡΡΠ°ΡΠΈΡΠΎΠ²Π°Π»ΠΈ ΠΏΡΠΈΠ±ΠΎΡΠΎΠΌ «ΠΡΠ»Ρ-Π» (4), ΠΈ ΠΏΡΠΈΠ±ΠΎΡΠ° ΠΊΠΎΠΌΠ±ΠΈΠ½ΠΈΡΠΎΠ²Π°Π½Π½ΠΎΠ³ΠΎ ΡΠΈΡΡΠΎΠ²ΠΎΠ³ΠΎ Π© 4313 (5). Π‘ ΡΠ΅Π»ΡΡ ΡΡΠ°Π²Π½ΠΈΠ²Π°Π½ΠΈΡ ΡΠΊΠΎΡΠΎΡΡΠ΅ΠΉ Π½Π°Π³ΡΠ΅Π²Π° ΠΌΠ΅ΡΠ°Π»Π»Π° Π² ΡΠΈΠ³Π»Π΅ ΠΈ Π³ΠΎΡΡΡΠ΅Π³ΠΎ ΡΠΏΠ°Ρ ΡΠ΅ΡΠΌΠΎΠΏΠ°ΡΡ ΠΏΠΎΡΠ»Π΅Π΄Π½ΠΈΠΉ ΠΏΠΎΠΌΠ΅ΡΠ°Π»ΠΈ Π² Π·Π°ΡΠΈΡΠ½ΡΠΉ ΠΊΠΎΡΡΠ½Π΄ΠΎΠ²ΡΠΉ ΡΠ΅Ρ ΠΎΠ». Π Π°ΡΡΡΠΎΡΠ½ΠΈΠ΅ ΠΎΡ Π³ΠΎΡΡΡΠ΅Π³ΠΎ ΡΠΏΠ°Ρ ΡΠ΅ΡΠΌΠΎΠΏΠ°ΡΡ Π΄ΠΎ Π΄Π½Π° ΡΠΈΠ³Π»Ρ Π½Π΅ ΠΏΡΠ΅Π²ΡΡΠ°Π»ΠΎ 5 ΠΌΠΌ. ΠΠ΅ΡΠ΅Π΄ ΠΎΠΏΡΡΠ°ΠΌΠΈ ΡΠ΅ΡΠΌΠΎΠΏΠ°ΡΡ ΠΏΠ΅ΡΠΈΠΎΠ΄ΠΈΡΠ΅ΡΠΊΠΈ Π³ΡΠ°Π΄ΡΠΈΡΠΎΠ²Π°Π»ΠΈ ΠΏΠΎ ΡΠΎΡΠΊΠ°ΠΌ ΠΏΠ»Π°Π²Π»Π΅Π½ΠΈΡ ΡΠΈΡΡΡΡ ΠΌΠ΅ΡΠ°Π»Π»ΠΎΠ² Π½ΠΈΠΊΠ΅Π»Ρ, ΠΆΠ΅Π»Π΅Π·Π°.
ΠΡΠΈ ΠΈΠ·Π³ΠΎΡΠΎΠ²Π»Π΅Π½ΠΈΠΈ ΠΏΠΎΠ΄Π²Π΅ΡΠ½ΠΎΠΉ ΡΠΈΡΡΠ΅ΠΌΡ ΠΎΡΠΎΠ±ΠΎΠ΅ Π²Π½ΠΈΠΌΠ°Π½ΠΈΠ΅ ΠΎΠ±ΡΠ°ΡΠ°Π»ΠΈ Π½Π° Π²ΡΠΏΠΎΠ»Π½Π΅Π½ΠΈΠ΅ ΡΡΠ»ΠΎΠ²ΠΈΡ, ΠΏΡΠ΅Π΄ΡΡΠ²Π»ΡΠ΅ΠΌΠΎΠ³ΠΎ ΠΊ Π±Π΅Π·ΡΠ°Π·ΠΌΠ΅ΡΠ½ΠΎΠΌΡ ΠΏΠ°ΡΠ°ΠΌΠ΅ΡΡΡ Π΄Π°Π½Π½ΠΎΠ³ΠΎ ΠΌΠ΅ΡΠΎΠ΄Π°:
(2.21)
Π³Π΄Π΅ R — ΡΠ°Π΄ΠΈΡΡ ΡΠΈΠ³Π»Ρ;
Ρ — ΠΏΠ΅ΡΠΈΠΎΠ΄ ΠΊΠΎΠ»Π΅Π±Π°Π½ΠΈΠΉ ΠΏΠΎΠ΄Π²Π΅ΡΠ½ΠΎΠΉ ΡΠΈΡΡΠ΅ΠΌΡ;
Π½ — ΠΊΠΈΠ½Π΅ΠΌΠ°ΡΠΈΡΠ΅ΡΠΊΠ°Ρ Π²ΡΠ·ΠΊΠΎΡΡΡ ΡΠ°ΡΠΏΠ»Π°Π²Π»Π΅Π½Π½ΠΎΠ³ΠΎ ΠΌΠ΅ΡΠ°Π»Π»Π°.
ΠΡΠΎ Π΄ΠΎΡΡΠΈΠ³Π°Π»ΠΈ ΠΏΠΎΠ΄Π±ΠΎΡΠΎΠΌ ΠΌΠ°ΡΠ΅ΡΠΈΠ°Π»Π° ΠΈ ΡΠΎΠ»ΡΠΈΠ½Ρ Π½ΠΈΡΠΈ, ΡΠ°Π΄ΠΈΡΡΠ° ΡΠΈΠ³Π»Ρ ΠΈ ΠΌΠ°ΡΡΡ ΠΏΠΎΠ΄Π²Π΅ΡΠ½ΠΎΠΉ ΡΠΈΡΡΠ΅ΠΌΡ.
ΠΠΎΠ΄Π²Π΅ΡΠ½Π°Ρ ΡΠΈΡΡΠ΅ΠΌΠ° (ΡΠΈΡ. 2.4) ΡΠΎΡΡΠΎΠΈΡ ΠΈΠ· ΠΎΠΏΠΎΡΠ½ΠΎΠ³ΠΎ ΠΊΠΎΠ»ΡΡΠ° (1), ΠΊ ΠΊΠΎΡΠΎΡΠΎΠΌΡ ΠΊΡΠ΅ΠΏΠΈΠ»ΠΈ ΡΠΏΡΡΠ³ΡΡ Π½ΠΈΡ ΡΠΎΠΌΠΎΠ²ΡΡ Π½ΠΈΡΡ (2) Π΄ΠΈΠ°ΠΌΠ΅ΡΡΠΎΠΌ 0,2 ΠΌΠΌ. ΠΠ»Ρ ΡΠ½ΡΡΠΈΡ Π²Π½ΡΡΡΠ΅Π½Π½ΠΈΡ Π½Π°ΠΏΡΡΠΆΠ΅Π½ΠΈΠΉ Π½ΠΈΡΡ ΠΏΡΠ΅Π΄Π²Π°ΡΠΈΡΠ΅Π»ΡΠ½ΠΎ ΠΏΠΎΠ΄Π²Π΅ΡΠ³Π°Π»ΠΈ ΠΎΡΠΆΠΈΠ³Ρ. ΠΠ° Π½ΠΈΠΆΠ½Π΅ΠΌ ΠΊΠΎΠ½ΡΠ΅ Π½ΠΈΡΠΈ Π·Π°ΠΊΡΠ΅ΠΏΠ»ΡΠ»ΠΈ Π²ΡΡΠ»ΠΊΡ (13) ΠΈΠ· ΡΠ±ΠΎΠ½ΠΈΡΠ°, ΠΏΡΠ΅ΠΏΡΡΡΡΠ²ΡΡΡΡΡ Π΅Π΅ Π½Π°Π³ΡΠ΅Π²Ρ Π·Π° ΡΡΠ΅Ρ ΡΠ΅ΠΏΠ»ΠΎΠΏΡΠΎΠ²ΠΎΠ΄Π½ΠΎΡΡΠΈ, ΡΠΎΠ΅Π΄ΠΈΠ½Π΅Π½Π½ΡΡ ΡΠ΅ΡΠ΅Π· ΠΏΠ΅ΡΠ΅Ρ ΠΎΠ΄Π½ΡΡ Π°Π»ΡΠΌΠΈΠ½ΠΈΠ΅Π²ΡΡ Π²ΡΡΠ»ΠΊΡ (3), Π½Π° ΠΊΠΎΡΠΎΡΠΎΠΉ ΠΊΡΠ΅ΠΏΠΈΠ»ΠΈ Π·Π΅ΡΠΊΠ°Π»ΠΎ (12), Ρ ΠΌΠΎΠ»ΠΈΠ±Π΄Π΅Π½ΠΎΠ²ΡΠΌ ΡΡΠΎΠΊΠΎΠΌ (4). ΠΠ° ΡΡΠΎΠΊΠ΅ Ρ ΠΏΠΎΠΌΠΎΡΡΡ ΡΠ°ΠΉΠ±Ρ (5) ΡΡΡΠ°Π½Π°Π²Π»ΠΈΠ²Π°Π»ΠΈ Π½Π°ΡΡΠΆΠ½ΡΠΉ ΠΌΠΎΠ»ΠΈΠ±Π΄Π΅Π½ΠΎΠ²ΡΠΉ ΡΠΈΠ³Π΅Π»Ρ (7), ΠΌΠ΅ΠΆΠ΄Ρ ΠΊΠΎΡΠΎΡΡΠΌ ΠΈ Π²Π½ΡΡΡΠ΅Π½Π½ΠΈΠΌ ΠΎΠ³Π½Π΅ΡΠΏΠΎΡΠ½ΡΠΌ (8) ΡΠ°ΡΠΏΠΎΠ»Π°Π³Π°Π»ΠΈ ΡΠ΅Π½ΡΡΠΈΡΡΡΡΠ΅Π΅ ΠΌΠΎΠ»ΠΈΠ±Π΄Π΅Π½ΠΎΠ²ΠΎΠ΅ ΠΊΠΎΠ»ΡΡΠΎ (9). ΠΠ»Ρ Π·Π°ΡΠΈΡΡ Π½ΠΈΡΠΈ ΠΈ Π·Π΅ΡΠΊΠ°Π»Π° ΠΎΡ Π΄Π΅ΠΉΡΡΠ²ΠΈΡ ΠΏΡΡΠΌΠΎΠ³ΠΎ ΠΈΠ·Π»ΡΡΠ΅Π½ΠΈΡ Π½Π°Π³ΡΠ΅Π²Π°ΡΠ΅Π»Ρ Π½Π° ΡΡΠΎΠΊ Π±ΡΠ»ΠΈ Π½Π°Π΄Π΅ΡΡ ΠΌΠΎΠ»ΠΈΠ±Π΄Π΅Π½ΠΎΠ²ΡΠ΅ ΡΠΊΡΠ°Π½Ρ (11). ΠΠ»Ρ ΠΏΡΠ΅Π΄ΠΎΡΠ²ΡΠ°ΡΠ΅Π½ΠΈΡ ΠΏΠΎΠΏΠ°Π΄Π°Π½ΠΈΡ Π² ΠΆΠΈΠ΄ΠΊΠΈΠΉ ΠΌΠ΅ΡΠ°Π»Π» «Π½Π°Π³Π°ΡΠ°» ΡΠΎ ΡΡΠ΅Π½ΠΎΠΊ ΡΡΡΠ±Ρ ΠΈ Π±ΡΡΠ·Π³ ΠΆΠΈΠ΄ΠΊΠΎΠ³ΠΎ ΠΌΠ΅ΡΠ°Π»Π»Π° Π½Π° Π΄Π΅ΡΠ°Π»ΠΈ ΠΏΠΎΠ΄Π²Π΅ΡΠ½ΠΎΠΉ ΡΠΈΡΡΠ΅ΠΌΡ Π½Π° Π²Π½ΡΡΡΠ΅Π½Π½ΠΈΠΉ ΡΠΈΠ³Π΅Π»Ρ ΠΏΠΎΠΌΠ΅ΡΠ°Π»ΠΈ ΠΊΡΡΡΠΊΡ (6) ΠΈΠ· ΠΌΠΎΠ»ΠΈΠ±Π΄Π΅Π½Π°. ΠΠ»Ρ ΡΠ΅Π³ΠΈΡΡΡΠ°ΡΠΈΠΈ ΠΏΠ°ΡΠ°ΠΌΠ΅ΡΡΠΎΠ² Π²ΡΠ°ΡΠ°ΡΠ΅Π»ΡΠ½ΡΡ ΠΊΠΎΠ»Π΅Π±Π°Π½ΠΈΠΉ ΠΏΠΎΠ΄Π²Π΅ΡΠ½ΠΎΠΉ ΡΠΈΡΡΠ΅ΠΌΡ (ΡΠΌ. ΡΠΈΡ. 2.2) ΡΠ»ΡΠΆΠΈΠ» ΠΎΡΠ²Π΅ΡΠΈΡΠ΅Π»Ρ (6) ΠΈ ΠΏΠΎΠ»ΡΠΏΡΠΎΠ·ΡΠ°ΡΠ½Π°Ρ ΡΠΊΠ°Π»Π° (7).
2.2.2 ΠΠ΅ΡΠΎΠ΄ΠΈΠΊΠ° ΡΠΊΡΠΏΠ΅ΡΠΈΠΌΠ΅Π½ΡΠ°
ΠΠ°ΡΡΡ ΠΈΡΡΠ»Π΅Π΄ΡΠ΅ΠΌΡΡ ΠΎΠ±ΡΠ°Π·ΡΠΎΠ² ΠΌΠ΅ΡΠ°Π»Π»Π° Π²ΡΠ±ΠΈΡΠ°Π»ΠΈ ΠΈΠ· ΡΠΎΠΎΡΠ½ΠΎΡΠ΅Π½ΠΈΡ
Π? 1,85R, (2.22)
ΡΡΠΎ ΠΎΠ±Π΅ΡΠΏΠ΅ΡΠΈΠ²Π°Π»ΠΎ ΠΏΠΎΠ»Π½ΠΎΠ΅ Π·Π°ΡΡΡ Π°Π½ΠΈΠ΅ Π²ΡΠ·ΠΊΠΈΡ Π²ΠΎΠ»Π½, ΡΠ°ΡΠΏΡΠΎΡΡΡΠ°Π½ΡΡΡΠΈΡ ΡΡ ΠΎΡ Π΄Π½Π° ΡΠΈΠ³Π»Ρ ΠΈ ΠΈΡΠΊΠ»ΡΡΠ°Π»ΠΎ ΠΈΡ Π²Π»ΠΈΡΠ½ΠΈΠ΅ Π½Π° ΡΠ°ΡΠΏΡΠ΅Π΄Π΅Π»Π΅Π½ΠΈΠ΅ ΡΠΊΠΎΡΠΎΡΡΠ΅ΠΉ Ρ ΠΏΠΎΠ²Π΅ΡΡ Π½ΠΎΡΡΠΈ ΠΆΠΈΠ΄ΠΊΠΎΡΡΠΈ. ΠΠ±ΡΠ°Π·ΡΡ ΠΏΠ΅ΡΠ΅Π΄ ΠΎΠΏΡΡΠΎΠΌ Π²Π·Π²Π΅ΡΠΈΠ²Π°Π»ΠΈ Π½Π° Π°Π½Π°Π»ΠΈΡΠΈΡΠ΅ΡΠΊΠΈΡ Π²Π΅ΡΠ°Ρ ΠΈ ΠΏΠΎΠΌΠ΅ΡΠ°Π»ΠΈ Π²ΠΎ Π²Π½ΡΡΡΠ΅Π½Π½ΠΈΠΉ ΡΠΈΠ³Π΅Π»Ρ ΠΏΠΎΠ΄Π²Π΅ΡΠ½ΠΎΠΉ ΡΠΈΡΡΠ΅ΠΌΡ. Π Π°Π΄ΠΈΡΡ ΡΠΈΠ³Π»Ρ ΠΈΠ·ΠΌΠ΅ΡΡΠ»ΠΈ Π² Π½Π΅ΡΠΊΠΎΠ»ΡΠΊΠΈΡ ΠΌΠ΅ΡΡΠ°Ρ Ρ ΡΠΎΡΠ½ΠΎΡΡΡΡ 0,05 ΠΌΠΌ ΠΈ ΡΡΡΠ΅Π΄Π½ΡΠ»ΠΈ ΠΏΠΎΠ»ΡΡΠ΅Π½Π½ΡΠ΅ Π·Π½Π°ΡΠ΅Π½ΠΈΡ. ΠΠΎΠ΄Π²Π΅ΡΠ½ΡΡ ΡΠΈΡΡΠ΅ΠΌΡ ΡΡΡΠ°Π½Π°Π²Π»ΠΈΠ²Π°Π»ΠΈ Π² Π²ΠΈΡΠΊΠΎΠ·ΠΈΠΌΠ΅ΡΡΠ΅, ΠΊΠΎΡΠΎΡΡΠΉ Π²Π°ΠΊΡΡΠΌΠΈΡΠΎΠ²Π°Π»ΠΈ Π΄ΠΎ ΡΠ°Π·ΡΡΠΆΠ΅Π½ΠΈΡ 0,0133 ΠΠ° (10-4 ΠΌΠΌ.ΡΡ.ΡΡ.). ΠΠΎΡΠ»Π΅ ΡΡΠΎΠ³ΠΎ Π² ΡΠ°Π±ΠΎΡΠ΅ΠΉ ΠΊΠ°ΠΌΠ΅ΡΠ΅ ΡΠΎΠ·Π΄Π°Π²Π°Π»ΠΈ ΠΈΠ½Π΅ΡΡΠ½ΡΡ Π°ΡΠΌΠΎΡΡΠ΅ΡΡ, ΠΏΡΡΠ΅ΠΌ Π½Π°ΠΏΡΡΠΊΠ°Π½ΠΈΡ Π³Π΅Π»ΠΈΡ Π²ΡΡΠΎΠΊΠΎΠΉ ΡΠΈΡΡΠΎΡΡ (ΠΊΠ»Π°ΡΡ Π). Π‘ ΡΠ΅Π»ΡΡ Π΄ΠΎΠΏΠΎΠ»Π½ΠΈΡΠ΅Π»ΡΠ½ΠΎΠ³ΠΎ ΠΏΠΎΠ½ΠΈΠΆΠ΅Π½ΠΈΡ ΠΏΠ°ΡΡΠΈΠ°Π»ΡΠ½ΠΎΠ³ΠΎ Π΄Π°Π²Π»Π΅Π½ΠΈΡ ΠΊΠΈΡΠ»ΠΎΡΠΎΠ΄Π° ΠΈΡΠΏΠΎΠ»ΡΠ·ΠΎΠ²Π°Π»ΠΈ ΡΠΈΡΠ°Π½ΠΎΠ²ΡΠΉ Π³Π΅ΡΡΠ΅Ρ. ΠΠ°Π»Π΅Π΅ ΠΏΡΠΎΠ²ΠΎΠ΄ΠΈΠ»ΠΈ Π½Π°Π³ΡΠ΅Π² ΠΈ ΠΎΡ Π»Π°ΠΆΠ΄Π΅Π½ΠΈΠ΅. ΠΡΠΏΠΎΠ»ΡΠ·ΠΎΠ²Π°Π»ΠΈ ΡΠ°Π·Π»ΠΈΡΠ½ΡΠΉ ΡΠ΅ΠΆΠΈΠΌ ΠΈΠ·ΠΌΠ΅Π½Π΅Π½ΠΈΡ ΡΠ΅ΠΌΠΏΠ΅ΡΠ°ΡΡΡΡ. ΠΠ°ΠΈΠ±ΠΎΠ»Π΅Π΅ ΡΠ°ΡΠΏΡΠΎΡΡΡΠ°Π½Π΅Π½Π½Π°Ρ ΠΌΠ΅ΡΠΎΠ΄ΠΈΠΊΠ° ΠΏΡΠ΅Π΄ΡΡΠ°Π²Π»Π΅Π½Π° Π½ΠΈΠΆΠ΅. Π Ρ ΠΎΠ΄Π΅ ΡΠΊΡΠΏΠ΅ΡΠΈΠΌΠ΅Π½ΡΠ° Π² ΡΠ°Π±ΠΎΡΠ΅ΠΉ ΠΊΠ°ΠΌΠ΅ΡΠ΅ ΠΏΠΎΠ΄Π΄Π΅ΡΠΆΠΈΠ²Π°Π»ΠΈ Π°ΡΠΌΠΎΡΡΠ΅ΡΠ½ΠΎΠ΅ Π΄Π°Π²Π»Π΅Π½ΠΈΠ΅ Ρ ΠΏΠΎΠΌΠΎΡΡΡ Π±ΡΡΠ΅ΡΠ½ΠΎΠΉ ΠΊΠ°ΠΌΠ΅ΡΡ.
ΠΡΠΈ ΠΏΡΠΎΠ²Π΅Π΄Π΅Π½ΠΈΠΈ ΡΠΊΡΠΏΠ΅ΡΠΈΠΌΠ΅Π½ΡΠ° ΠΎΠΏΡΠ΅Π΄Π΅Π»ΡΠ»ΠΈΡΡ Π»ΠΎΠ³Π°ΡΠΈΡΠΌΠΈΡΠ΅ΡΠΊΠΈΠΉ Π΄Π΅ΠΊΡΠ΅ΠΌΠ΅Π½Ρ Π·Π°ΡΡΡ Π°Π½ΠΈΡ ΠΈ ΠΏΠ΅ΡΠΈΠΎΠ΄ ΠΊΠΎΠ»Π΅Π±Π°Π½ΠΈΠΉ ΠΏΠΎΠ΄Π²Π΅ΡΠ½ΠΎΠΉ ΡΠΈΡΡΠ΅ΠΌΡ. ΠΠΎΡΠ»Π΅Π΄Π½ΠΈΠ΅ ΡΠ΅Π³ΠΈΡΡΡΠΈΡΠΎΠ²Π°Π»ΠΈΡΡ Ρ ΠΏΠΎΠΌΠΎΡΡΡ ΠΎΠΏΡΠΈΡΠ΅ΡΠΊΠΎΠΉ ΡΠΈΡΡΠ΅ΠΌΡ, ΡΠΎΡΡΠΎΡΡΠ΅ΠΉ ΠΈΠ· ΡΡΠ°Π½Π΄Π°ΡΡΠ½ΠΎΠ³ΠΎ ΠΎΡΠ²Π΅ΡΠΈΡΠ΅Π»Ρ ΠΈ Π°Π²ΡΠΎΠΌΠ°ΡΠΈΡΠ΅ΡΠΊΠΎΠ³ΠΎ ΡΠ΅Π³ΠΈΡΡΡΠ°ΡΠΎΡΠ° ΠΏΠΎΠ»ΠΎΠΆΠ΅Π½ΠΈΡ ΡΠ²Π΅ΡΠΎΠ²ΠΎΠΉ ΠΌΠ΅ΡΠΊΠΈ. ΠΡΡ ΡΠ²Π΅ΡΠ°, ΠΏΡΠΎΠΉΠ΄Ρ ΡΠ΅ΡΠ΅Π· ΡΠΎΠΊΡΡΠΈΡΡΡΡΡΡ Π»ΠΈΠ½Π·Ρ ΠΈ ΠΊΠ²Π°ΡΡΠ΅Π²ΠΎΠ΅ ΠΎΠΊΠΎΡΠΊΠΎ, ΠΎΡΡΠ°ΠΆΠ°Π»ΡΡ ΠΎΡ Π·Π΅ΡΠΊΠ°Π»Π° ΠΏΠΎΠ΄Π²Π΅ΡΠ½ΠΎΠΉ ΡΠΈΡΡΠ΅ΠΌΡ ΠΈ ΠΏΠ°Π΄Π°Π» Π½Π° ΡΠ΅Π³ΠΈΡΡΡΠ°ΡΠΎΡ. Π ΡΠ΅Π·ΡΠ»ΡΡΠ°ΡΠ΅ Π°ΠΏΠΏΠ°ΡΠ°ΡΠ½ΠΎΠΉ ΠΈ ΠΏΡΠΎΠ³ΡΠ°ΠΌΠΌΠ½ΠΎΠΉ ΠΎΠ±ΡΠ°Π±ΠΎΡΠΊΠΈ ΠΏΠΎΠ»ΡΡΠ°Π»ΠΈ Π·Π°Π²ΠΈΡΠΈΠΌΠΎΡΡΡ ΠΈΠ·ΠΌΠ΅Π½Π΅Π½ΠΈΡ ΠΊΠΎΠΎΡΠ΄ΠΈΠ½Π°ΡΡ ΡΠ²Π΅ΡΠΎΠ²ΠΎΠΉ ΠΌΠ΅ΡΠΊΠΈ Π²ΠΎ Π²ΡΠ΅ΠΌΠ΅Π½ΠΈ. ΠΠ°Π»Π΅Π΅ Ρ ΠΏΠΎΠΌΠΎΡΡΡ ΠΏΠ°ΠΊΠ΅ΡΠ° ΠΏΡΠΈΠΊΠ»Π°Π΄Π½ΡΡ ΠΏΡΠΎΠ³ΡΠ°ΠΌΠΌ MATLAB ΠΏΡΠΎΠΈΠ·Π²ΠΎΠ΄ΠΈΠ»ΡΡ ΡΠ°ΡΡΠ΅Ρ Π»ΠΎΠ³Π°ΡΠΈΡΠΌΠΈΡΠ΅ΡΠΊΠΎΠ³ΠΎ Π΄Π΅ΠΊΡΠ΅ΠΌΠ΅Π½ΡΠ° Π·Π°ΡΡΡ Π°Π½ΠΈΡ ΠΈ ΠΏΠ΅ΡΠΈΠΎΠ΄Π° ΠΊΡΡΡΠΈΠ»ΡΠ½ΡΡ ΠΊΠΎΠ»Π΅Π±Π°Π½ΠΈΠΉ.
ΠΡΠ°Π΄ΡΠΈΡΠΎΠ²ΠΊΡ ΠΏΠΎΠ΄Π²Π΅ΡΠ½ΠΎΠΉ ΡΠΈΡΡΠ΅ΠΌΡ ΠΏΡΠΎΠ²ΠΎΠ΄ΠΈΠ»ΠΈ Π΄Π²ΡΠΌΡ ΡΡΠ°Π»ΠΎΠ½Π½ΡΠΌΠΈ Π΄ΠΈΡΠΊΠ°ΠΌΠΈ Ρ ΡΠ°Π·Π»ΠΈΡΠ½ΡΠΌΠΈ ΠΌΠΎΠΌΠ΅Π½ΡΠ°ΠΌΠΈ ΠΈΠ½Π΅ΡΡΠΈΠΈ. ΠΠΎΠ»ΡΡΠ΅Π½Π½ΡΠ΅ Π·Π½Π°ΡΠ΅Π½ΠΈΡ ΠΌΠΎΠΌΠ΅Π½ΡΠ° ΠΈΠ½Π΅ΡΡΠΈΠΈ ΡΡΡΠ΅Π΄Π½ΡΠ»ΠΈΡΡ.
ΠΠ΅Π»ΠΈΡΠΈΠ½Ρ ΠΎΡΠ½ΠΎΡΠ΅Π½ΠΈΡ Π΄Π΅ΠΊΡΠ΅ΠΌΠ΅Π½ΡΠ° Π·Π°ΡΡΡ Π°Π½ΠΈΡ ΠΊΡΡΡΠΈΠ»ΡΠ½ΡΡ ΠΊΠΎΠ»Π΅Π±Π°Π½ΠΈΠΉ ΠΊ ΠΏΠ΅ΡΠΈΠΎΠ΄Ρ ΠΊΠΎΠ»Π΅Π±Π°Π½ΠΈΠΉ Π΄Π»Ρ ΠΏΡΡΡΠΎΠΉ ΠΏΠΎΠ΄Π²Π΅ΡΠ½ΠΎΠΉ ΡΠΈΡΡΠ΅ΠΌΡ Π΄0/Ρ0 ΠΎΠΏΡΠ΅Π΄Π΅Π»ΡΠ»ΠΈ Π½Π΅ΠΏΠΎΡΡΠ΅Π΄ΡΡΠ²Π΅Π½Π½ΠΎ Π² Π²ΠΈΡΠΊΠΎΠ·ΠΈΠΌΠ΅ΡΡΠ΅ Π² Π°ΡΠΌΠΎΡΡΠ΅ΡΠ΅ ΠΈ ΠΏΡΠΈ ΡΠ΅ΠΌΠΏΠ΅ΡΠ°ΡΡΡΠ°Ρ , ΠΏΡΠΈ ΠΊΠΎΡΠΎΡΡΡ ΠΏΡΠΎΠ²ΠΎΠ΄ΠΈΠ»ΠΈ Π² Π΄Π°Π»ΡΠ½Π΅ΠΉΡΠ΅ΠΌ ΡΠΊΡΠΏΠ΅ΡΠΈΠΌΠ΅Π½ΡΡ.
Π‘ΡΡΡ ΡΠΊΡΠΏΠ΅ΡΠΈΠΌΠ΅Π½ΡΠ°Π»ΡΠ½ΠΎΠΉ ΠΌΠ΅ΡΠΎΠ΄ΠΈΠΊΠΈ ΡΠΎΡΡΠΎΡΠ»Π° Π² ΠΈΠ·ΡΡΠ΅Π½ΠΈΠΈ Π΄ΠΈΠ½Π°ΠΌΠΈΠΊΠΈ ΡΠΎΡΠΌΠΈΡΠΎΠ²Π°Π½ΠΈΡ ΡΠ°ΡΠΏΠ»Π°Π²Π° Π² Ρ ΠΎΠ΄Π΅ ΠΈΠ·ΠΎΡΠ΅ΡΠΌΠΈΡΠ΅ΡΠΊΠΎΠΉ Π²ΡΠ΄Π΅ΡΠΆΠΊΠΈ ΠΏΡΠΈ 1600 ΠΎΠ‘ Ρ ΡΠΈΠΊΡΠ°ΡΠΈΠ΅ΠΉ Ρ Π°ΡΠ°ΠΊΡΠ΅ΡΠ° ΠΈΠ·ΠΌΠ΅Π½Π΅Π½ΠΈΠΉ ΠΊΠΈΠ½Π΅ΠΌΠ°ΡΠΈΡΠ΅ΡΠΊΠΎΠΉ Π²ΡΠ·ΠΊΠΎΡΡΠΈ ΠΆΠΈΠ΄ΠΊΠΎΠ³ΠΎ ΠΌΠ΅ΡΠ°Π»Π»Π°. Π ΠΊΠ°ΡΠ΅ΡΡΠ²Π΅ ΠΏΡΠΈΠΌΠ΅ΡΠ° Π½Π° ΡΠΈΡ. ΠΏΡΠ΅Π΄ΡΡΠ°Π²Π»Π΅Π½Ρ ΡΠ΅Π·ΡΠ»ΡΡΠ°ΡΡ ΡΠΊΡΠΏΠ΅ΡΠΈΠΌΠ΅Π½ΡΠ° Π΄Π»Ρ ΡΡΠ°Π»ΠΈ Π (ΠΏΠ»Π°Π²ΠΊΠ° № 1928).
ΠΡΠ΅ΠΌΡ ΡΡΠ°Π±ΠΈΠ»ΠΈΠ·Π°ΡΠΈΠΈ Π·Π½Π°ΡΠ΅Π½ΠΈΠΉ ΠΊΠΈΠ½Π΅ΠΌΠ°ΡΠΈΡΠ΅ΡΠΊΠΎΠΉ (Π²ΡΠ΅ΠΌΡ ΡΠ΅Π»Π°ΠΊΡΠ°ΡΠΈΠΈ) ΡΡΠ°Π²ΠΈΠ»ΠΈ Π² ΡΠΎΠΎΡΠ²Π΅ΡΡΡΠ²ΠΈΠ΅ Π·Π°Π²Π΅ΡΡΠ΅Π½ΠΈΡ ΡΠΎΡΠΌΠΈΡΠΎΠ²Π°Π½ΠΈΡ ΠΌΠΈΠΊΡΠΎΠΎΠ΄Π½ΠΎΡΠΎΠ΄Π½ΠΎΠ³ΠΎ, ΡΠ°Π²Π½ΠΎΠ²Π΅ΡΠ½ΠΎΠ³ΠΎ ΡΠ°ΡΠΏΠ»Π°Π²Π°. ΠΠΎΠ»ΡΡΠ΅Π΅ Π²ΡΠ΅ΠΌΡ ΡΠ΅Π»Π°ΠΊΡΠ°ΡΠΈΠΈ ΡΠ²ΠΈΠ΄Π΅ΡΠ΅Π»ΡΡΡΠ²ΠΎΠ²Π°Π»ΠΎ ΠΎ Π±ΠΎΠ»ΡΡΠ΅ΠΉ Π½Π΅ΡΠ°Π²Π½ΠΎΠ²Π΅ΡΠ½ΠΎΡΡΠΈ ΠΈΡΡ ΠΎΠ΄Π½ΠΎΠ³ΠΎ ΠΌΠ΅ΡΠ°Π»Π»Π°.
Π ΠΈΡ. 2.5. ΠΠΈΠ½Π°ΠΌΠΈΠΊΠ° ΠΈΠ·ΠΌΠ΅Π½Π΅Π½ΠΈΡ ΠΊΠΈΠ½Π΅ΠΌΠ°ΡΠΈΡΠ΅ΡΠΊΠΎΠΉ Π²ΡΠ·ΠΊΠΎΡΡΠΈ ΠΏΡΠΈ ΡΠΎΡΠΌΠΈΡΠΎΠ²Π°Π½ΠΈΠΈ ΡΠ°ΡΠΏΠ»Π°Π²Π° ΡΡΠ°Π»ΠΈ Π
2.2.3 Π Π°ΡΡΠ΅Ρ Π°Π±ΡΠΎΠ»ΡΡΠ½ΡΡ Π·Π½Π°ΡΠ΅Π½ΠΈΠΉ ΠΊΠΈΠ½Π΅ΠΌΠ°ΡΠΈΡΠ΅ΡΠΊΠΎΠΉ Π²ΡΠ·ΠΊΠΎΡΡΠΈ
ΠΠ΅ΡΠ°Π»Π»ΠΈΡΠ΅ΡΠΊΠΈΠ΅ ΠΆΠΈΠ΄ΠΊΠΎΡΡΠΈ ΠΏΡΠΈΠ½ΡΡΠΎ ΠΎΡΠ½ΠΎΡΠΈΡΡ ΠΊ ΡΠ»Π°Π±ΠΎΠ²ΡΠ·ΠΊΠΈΠΌ ΠΆΠΈΠ΄ΠΊΠΎΡΡΡΠΌ. Π Π°ΡΡΠ΅Ρ ΠΊΠΈΠ½Π΅ΠΌΠ°ΡΠΈΡΠ΅ΡΠΊΠΎΠΉ Π²ΡΠ·ΠΊΠΎΡΡΠΈ ΡΠ»Π°Π±ΠΎΠ²ΡΠ·ΠΊΠΈΡ ΠΆΠΈΠ΄ΠΊΠΎΡΡΠ΅ΠΉ ΠΏΡΠΎΠΈΠ·Π²ΠΎΠ΄ΡΡ Ρ ΠΏΠΎΠΌΠΎΡΡΡ ΠΌΠ°ΡΠ΅ΠΌΠ°ΡΠΈΡΠ΅ΡΠΊΠΎΠ³ΠΎ Π°ΠΏΠΏΠ°ΡΠ°ΡΠ°, ΡΠ°Π·ΡΠ°Π±ΠΎΡΠ°Π½Π½ΠΎΠ³ΠΎ Π. Π. Π¨Π²ΠΈΠ΄ΠΊΠΎΠ²ΡΠΊΠΈΠΌ [83], ΠΏΠΎ ΡΠ»Π΅Π΄ΡΡΡΠΈΠΌ ΡΠ°ΡΡΠ΅ΡΠ½ΡΠΌ ΡΠΎΡΠΌΡΠ»Π°ΠΌ:
(2.23)
Π³Π΄Π΅, (2.24)
(2.25)
m — ΠΌΠ°ΡΡΠ° ΠΆΠΈΠ΄ΠΊΠΎΠ³ΠΎ ΠΌΠ΅ΡΠ°Π»Π»Π° Π² ΡΠΈΠ³Π»Π΅;
R — Π²Π½ΡΡΡΠ΅Π½Π½ΠΈΠΉ ΡΠ°Π΄ΠΈΡΡ ΡΠΈΠ³Π»Ρ;
H — Π²ΡΡΠΎΡΠ° ΠΆΠΈΠ΄ΠΊΠΎΠ³ΠΎ ΠΌΠ΅ΡΠ°Π»Π»Π° Π² ΡΠΈΠ³Π»Π΅;
(2.26)
Π΄ ΠΈ Π΄0 — Π»ΠΎΠ³Π°ΡΠΈΡΠΌΠΈΡΠ΅ΡΠΊΠΈΠ΅ Π΄Π΅ΠΊΡΠ΅ΠΌΠ΅Π½ΡΡ Π·Π°ΡΡΡ Π°Π½ΠΈΡ ΠΊΡΡΡΠΈΠ»ΡΠ½ΡΡ ΠΊΠΎΠ»Π΅Π±Π°Π½ΠΈΠΉ ΠΏΠΎΠ΄Π²Π΅ΡΠ½ΠΎΠΉ ΡΠΈΡΡΠ΅ΠΌΡ Ρ ΠΆΠΈΠ΄ΠΊΠΎΡΡΡΡ ΠΈ Π±Π΅Π· Π½Π΅Π΅,
(2.27)
Π³Π΄Π΅ n — ΡΠΈΡΠ»ΠΎ ΠΏΠ΅ΡΠΈΠΎΠ΄ΠΎΠ² ΠΊΠΎΠ»Π΅Π±Π°Π½ΠΈΠΉ ΠΏΠΎΠ΄Π²Π΅ΡΠ½ΠΎΠΉ ΡΠΈΡΡΠ΅ΠΌΡ;
A0 ΠΈ A — Π½Π°ΡΠ°Π»ΡΠ½Π°Ρ ΠΈ ΠΊΠΎΠ½Π΅ΡΠ½Π°Ρ Π°ΠΌΠΏΠ»ΠΈΡΡΠ΄Ρ ΠΊΠΎΠ»Π΅Π±Π°Π½ΠΈΠΉ;
Ρ ΠΈ Ρ0 — ΡΠΎΠΎΡΠ²Π΅ΡΡΡΠ²ΡΡΡΠΈΠ΅ ΠΏΠ΅ΡΠΈΠΎΠ΄Ρ ΠΊΠΎΠ»Π΅Π±Π°Π½ΠΈΡ ΠΏΠΎΠ΄Π²Π΅ΡΠ½ΠΎΠΉ ΡΠΈΡΡΠ΅ΠΌΡ;
a, b, c — ΠΊΠΎΡΡΡΠΈΡΠΈΠ΅Π½ΡΡ, ΠΎΠΏΡΠ΅Π΄Π΅Π»ΡΠ΅ΠΌΡΠ΅ ΠΏΠΎ ΡΠ°Π±Π»ΠΈΡΠ°ΠΌ Π² Π·Π°Π²ΠΈΡΠΈΠΌΠΎΡΡΠΈ ΠΎΡ Π·Π½Π°ΡΠ΅Π½ΠΈΠΉ ΠΏΠ°ΡΠ°ΠΌΠ΅ΡΡΠ° ΠΌΠ΅ΡΠΎΠ΄Π° y,
; (2.28)
Π — ΠΎΡΠ΅Π²ΠΎΠΉ ΠΌΠΎΠΌΠ΅Π½Ρ ΠΈΠ½Π΅ΡΡΠΈΠΈ ΠΏΠΎΠ΄Π²Π΅ΡΠ½ΠΎΠΉ ΡΠΈΡΡΠ΅ΠΌΡ,
(2.29)
Π³Π΄Π΅ ΠΡΡ ΠΈ ΡΡΡ — ΡΠΎΠΎΡΠ²Π΅ΡΡΡΠ²Π΅Π½Π½ΠΎ ΠΌΠΎΠΌΠ΅Π½Ρ ΠΈΠ½Π΅ΡΡΠΈΠΈ ΡΡΠ°Π»ΠΎΠ½Π½ΠΎΠ³ΠΎ Π΄ΠΈΡΠΊΠ° ΠΈ ΠΏΠ΅ΡΠΈΠΎΠ΄ ΠΊΠΎΠ»Π΅Π±Π°Π½ΠΈΠΉ ΡΠΈΡΡΠ΅ΠΌΡ, Π½Π°Π³ΡΡΠΆΠ΅Π½Π½ΠΎΠΉ ΡΡΠ°Π»ΠΎΠ½Π½ΡΠΌ Π΄ΠΈΡΠΊΠΎΠΌ, Ρ0 — ΠΏΠ΅ΡΠΈΠΎΠ΄ ΠΊΠΎΠ»Π΅Π±Π°Π½ΠΈΠΉ ΠΏΠΎΠ΄Π²Π΅ΡΠ½ΠΎΠΉ ΡΠΈΡΡΠ΅ΠΌΡ, Π½Π΅ Π½Π°Π³ΡΡΠΆΠ΅Π½Π½ΠΎΠΉ ΡΡΠ°Π»ΠΎΠ½ΠΎΠΌ.
ΠΡΠ΅Π½ΠΊΠ° ΠΏΠΎΠ³ΡΠ΅ΡΠ½ΠΎΡΡΠΈ ΠΎΠΏΡΠ΅Π΄Π΅Π»Π΅Π½ΠΈΡ Π²ΡΠ·ΠΊΠΎΡΡΠΈ ΠΏΡΠΎΠΈΠ·Π²ΠΎΠ΄ΠΈΠ»Π°ΡΡ Ρ ΠΈΡΠΏΠΎΠ»ΡΠ·ΠΎΠ²Π°Π½ΠΈΠ΅ΠΌ ΡΠΎΠΎΡΠ½ΠΎΡΠ΅Π½ΠΈΡ Π΄Π»Ρ ΠΎΠΏΡΠ΅Π΄Π΅Π»Π΅Π½ΠΈΡ ΠΎΡΠ½ΠΎΡΠΈΡΠ΅Π»ΡΠ½ΠΎΠΉ ΠΏΠΎΠ³ΡΠ΅ΡΠ½ΠΎΡΡΠΈ ΠΊΠΎΡΠ²Π΅Π½Π½ΠΎΠ³ΠΎ ΠΈΠ·ΠΌΠ΅ΡΠ΅Π½ΠΈΡ [84]
(2.30)
Π³Π΄Π΅ y = f (x1, x2, … xi, … xk) — ΡΡΠ½ΠΊΡΠΈΡ ΠΎΡ Π°ΡΠ³ΡΠΌΠ΅Π½ΡΠΎΠ², ΠΎΠΏΡΠ΅Π΄Π΅Π»Π΅Π½Π½ΡΡ Π½Π΅Π·Π°Π²ΠΈΡΠΈΠΌΠΎ Π΄ΡΡΠ³ ΠΎΡ Π΄ΡΡΠ³Π°.
Π ΠΏΠ΅ΡΠ²ΠΎΠΌ ΠΏΡΠΈΠ±Π»ΠΈΠΆΠ΅Π½ΠΈΠΈ ΡΠ°ΡΡΠ΅Ρ ΠΎΡΠ½ΠΎΡΠΈΡΠ΅Π»ΡΠ½ΠΎΠΉ ΠΏΠΎΠ³ΡΠ΅ΡΠ½ΠΎΡΡΠΈ ΠΎΠΏΡΠ΅Π΄Π΅Π»Π΅Π½ΠΈΡ ΠΊΠΈΠ½Π΅ΠΌΠ°ΡΠΈΡΠ΅ΡΠΊΠΎΠΉ Π²ΡΠ·ΠΊΠΎΡΡΠΈ ΠΌΠΎΠΆΠ΅Ρ Π±ΡΡΡ ΠΏΡΠΎΠΈΠ·Π²Π΅Π΄Π΅Π½ ΠΏΠΎ ΡΠΎΡΠΌΡΠ»Π΅:
(2.31)
ΠΠ»Ρ ΠΎΡΠ΅Π½ΠΊΠΈ ΠΏΠΎΠ³ΡΠ΅ΡΠ½ΠΎΡΡΠΈ ΠΏΡΡΠΌΡΡ ΠΈΠ·ΠΌΠ΅ΡΠ΅Π½ΠΈΠΉ ΡΠΎΡΡΠ°Π²Π»ΡΡΡΠΈΡ ΡΠ°ΡΡΠ΅ΡΠ½ΠΎΠΉ ΡΠΎΡΠΌΡΠ»Ρ Π²ΡΠ·ΠΊΠΎΡΡΠΈ Π±ΡΠ»ΠΈ ΠΏΡΠΎΠ²Π΅Π΄Π΅Π½Ρ ΠΏΠΎ 10 ΠΈΠ·ΠΌΠ΅ΡΠ΅Π½ΠΈΠΉ Π»ΠΎΠ³Π°ΡΠΈΡΠΌΠΈΡΠ΅ΡΠΊΠΎΠ³ΠΎ Π΄Π΅ΠΊΡΠ΅ΠΌΠ΅Π½ΡΠ° ΠΈ ΠΏΠ΅ΡΠΈΠΎΠ΄Π° ΠΊΡΡΡΠΈΠ»ΡΠ½ΡΡ ΠΊΠΎΠ»Π΅Π±Π°Π½ΠΈΠΉ, ΠΌΠΎΠΌΠ΅Π½ΡΠ° ΠΈΠ½Π΅ΡΡΠΈΠΈ ΠΏΠΎΠ΄Π²Π΅ΡΠ½ΠΎΠΉ ΡΠΈΡΡΠ΅ΠΌΡ, ΡΠ°Π΄ΠΈΡΡΠ° ΡΠΈΠ³Π»Ρ, ΠΌΠ°ΡΡΡ ΠΈ Π²ΡΡΠΎΡΡ ΠΌΠ΅ΡΠ°Π»Π»Π° Π² ΡΠΈΠ³Π»Π΅. Π Π°ΡΡΠ΅Ρ Π΄ΠΎΠ²Π΅ΡΠΈΡΠ΅Π»ΡΠ½ΡΡ Π³ΡΠ°Π½ΠΈΡ Π΄Π»Ρ ΡΠ»ΡΡΠ°ΠΉΠ½ΠΎΠΉ ΠΏΠΎΠ³ΡΠ΅ΡΠ½ΠΎΡΡΠΈ ΠΏΡΡΠΌΡΡ ΠΈΠ·ΠΌΠ΅ΡΠ΅Π½ΠΈΠΉ ΠΏΡΠΎΠ²ΠΎΠ΄ΠΈΠ»ΡΡ ΠΏΠΎ ΡΠΎΡΠΌΡΠ»Π΅:
(2.32)
Π³Π΄Π΅ n — ΡΠΈΡΠ»ΠΎ ΠΈΠ·ΠΌΠ΅ΡΠ΅Π½ΠΈΠΉ;
t (P, n-1) — Π΄Π²ΡΡΡΠΎΡΠΎΠ½Π½ΠΈΠ΅ ΠΏΡΠ΅Π΄Π΅Π»Ρ ΡΠ°ΡΠΏΡΠ΅Π΄Π΅Π»Π΅Π½ΠΈΡ Π‘ΡΡΡΠ΄Π΅Π½ΡΠ° (t — ΡΠ°ΡΠΏΡΠ΅Π΄Π΅Π»Π΅Π½ΠΈΡ) Ρ Π΄ΠΎΠ²Π΅ΡΠΈΡΠ΅Π»ΡΠ½ΠΎΠΉ Π²Π΅ΡΠΎΡΡΠ½ΠΎΡΡΡ Π (0,95) ΠΈ Ρ n-1 (9) ΡΠ²ΠΎΠ±ΠΎΠ΄Ρ;
S — Π²ΡΠ±ΠΎΡΠΎΡΠ½ΠΎΠ΅ ΡΡΠ΅Π΄Π½Π΅ΠΊΠ²Π°Π΄ΡΠ°ΡΠΈΡΠ½ΠΎΠ΅ ΠΎΡΠΊΠ»ΠΎΠ½Π΅Π½ΠΈΠ΅, ΠΊΠΎΡΠΎΡΠΎΠ΅ ΠΎΠΏΡΠ΅Π΄Π΅Π»ΡΠ»ΠΎΡΡ Ρ ΠΈΡΠΏΠΎΠ»ΡΠ·ΠΎΠ²Π°Π½ΠΈΠ΅ΠΌ Π²ΡΡΠ°ΠΆΠ΅Π½ΠΈΡ:
(2.33)
Π³Π΄Π΅ — ΡΡΠ΅Π΄Π½Π΅Π΅ Π°ΡΠΈΡΠΌΠ΅ΡΠΈΡΠ΅ΡΠΊΠΎΠ΅,
— ΠΈΠ·ΠΌΠ΅ΡΠ΅Π½Π½ΠΎΠ΅ Π·Π½Π°ΡΠ΅Π½ΠΈΠ΅ Π²Π΅Π»ΠΈΡΠΈΠ½Ρ.
Π Π΅Π·ΡΠ»ΡΡΠ°ΡΡ ΠΏΡΠ΅Π΄ΡΡΠ°Π²Π»Π΅Π½Ρ Π² ΡΠ°Π±Π»ΠΈΡΠ΅ 2.1.
Π’Π°Π±Π»ΠΈΡΠ° 2.1
ΠΠΎΠ²Π΅ΡΠΈΡΠ΅Π»ΡΠ½ΡΠ΅ ΠΈΠ½ΡΠ΅ΡΠ²Π°Π»Ρ ΡΠΎΡΡΠ°Π²Π»ΡΡΡΠΈΡ ΡΠ°ΡΡΠ΅ΡΠ½ΠΎΠΉ ΡΠΎΡΠΌΡΠ»Ρ Π²ΡΠ·ΠΊΠΎΡΡΠΈ
ΠΠ·ΠΌΠ΅ΡΠ΅Π½Π½ΡΠ΅ Π²Π΅Π»ΠΈΡΠΈΠ½Ρ | Π, Π³ Β· ΡΠΌ2 | m, Π³ | R, ΡΠΌ | Π΄ | Ρ, Ρ | Π, ΡΠΌ | |
Π ± ?Π (Π = 0,95) | 50,386 ± 0,004 | 21,380 ± 0,001 | 0,725 ± 0,005 | 0,0775 ± 0,0004 | 3,53 ± 0,01 | 1,775 ± 0,005 | |
Π‘ ΠΈΡΠΏΠΎΠ»ΡΠ·ΠΎΠ²Π°Π½ΠΈΠ΅ΠΌ ΠΏΠΎΠ»ΡΡΠ΅Π½Π½ΡΡ Π·Π½Π°ΡΠ΅Π½ΠΈΠΉ ΠΏΠΎ ΡΠΎΠΎΡΠ½ΠΎΡΠ΅Π½ΠΈΡ (2.31) Π±ΡΠ» ΠΏΡΠΎΠ²Π΅Π΄Π΅Π½ ΡΠ°ΡΡΠ΅Ρ ΠΎΡΠ½ΠΎΡΠΈΡΠ΅Π»ΡΠ½ΠΎΠΉ ΠΏΠΎΠ³ΡΠ΅ΡΠ½ΠΎΡΡΠΈ ΠΎΠΏΡΠ΅Π΄Π΅Π»Π΅Π½ΠΈΡ ΠΊΠΈΠ½Π΅ΠΌΠ°ΡΠΈΡΠ΅ΡΠΊΠΎΠΉ Π²ΡΠ·ΠΊΠΎΡΡΠΈ, ΠΊΠΎΡΠΎΡΠ°Ρ ΡΠΎΡΡΠ°Π²ΠΈΠ»Π° 0,018 (ΠΈΠ»ΠΈ 1,8%).
Π Π°ΡΡΠ΅Ρ ΠΊΠΈΠ½Π΅ΠΌΠ°ΡΠΈΡΠ΅ΡΠΊΠΎΠΉ Π²ΡΠ·ΠΊΠΎΡΡΠΈ ΠΏΡΠΎΠΈΠ·Π²ΠΎΠ΄ΠΈΠ»ΠΈ Ρ ΠΏΠΎΠΌΠΎΡΡΡ ΡΠΏΠ΅ΡΠΈΠ°Π»ΡΠ½ΠΎΠΉ ΠΏΡΠΎΠ³ΡΠ°ΠΌΠΌΡ, ΡΠ°Π·ΡΠ°Π±ΠΎΡΠ°Π½Π½ΠΎΠΉ ΡΠ°Π½Π΅Π΅ Π² ΠΈΡΡΠ»Π΅Π΄ΠΎΠ²Π°ΡΠ΅Π»ΡΡΠΊΠΎΠΉ Π»Π°Π±ΠΎΡΠ°ΡΠΎΡΠΈΠΈ ΠΊΠ°ΡΠ΅Π΄ΡΡ «ΠΠ΅ΡΠ°Π»Π»ΡΡΠ³ΠΈΡ ΠΆΠ΅Π»Π΅Π·Π° ΠΈ ΡΠΏΠ»Π°Π²ΠΎΠ²».
3. Π Π΅Π·ΡΠ»ΡΡΠ°ΡΡ ΠΈΡΡΠ»Π΅Π΄ΠΎΠ²Π°Π½ΠΈΠΉ
3.1 ΠΠ»ΠΈΡΠ½ΠΈΠ΅ ΡΠ΅Ρ Π½ΠΎΠ»ΠΎΠ³ΠΈΡΠ΅ΡΠΊΠΈΡ ΠΏΠ°ΡΠ°ΠΌΠ΅ΡΡΠΎΠ² Π²Π½Π΅ΠΏΠ΅ΡΠ½ΠΎΠΉ ΠΎΠ±ΡΠ°Π±ΠΎΡΠΊΠΈ Π½Π° ΡΠΎΠ΄Π΅ΡΠΆΠ°Π½ΠΈΠ΅ Π² ΠΌΠ΅ΡΠ°Π»Π»Π΅ ΠΎΠ±ΡΠ΅Π³ΠΎ ΠΊΠΈΡΠ»ΠΎΡΠΎΠ΄Π°
ΠΠ΅ΡΠΌΠΎΡΡΡ Π½Π° Π½Π°Π»ΠΈΡΠΈΠ΅ Π² ΡΠ΅Ρ Π½ΠΎΠ»ΠΎΠ³ΠΈΡΠ΅ΡΠΊΠΎΠΉ ΡΡ Π΅ΠΌΠ΅ Π²Π½Π΅ΠΏΠ΅ΡΠ½ΠΎΠΉ ΠΎΠ±ΡΠ°Π±ΠΎΡΠΊΠΈ, Π±ΡΠ»ΠΎ ΡΡΡΠ°Π½ΠΎΠ²Π»Π΅Π½ΠΎ Π·Π½Π°ΡΠΈΡΠ΅Π»ΡΠ½ΠΎΠ΅ Π½Π°ΡΠ»Π΅Π΄ΡΡΠ²Π΅Π½Π½ΠΎΠ΅ Π²Π»ΠΈΡΠ½ΠΈΠ΅ ΠΎΠΊΠΈΡΠ»Π΅Π½Π½ΠΎΡΡΠΈ ΠΏΠΎΠ»ΡΠΏΡΠΎΠ΄ΡΠΊΡΠ° Π½Π° Π²ΡΠΏΡΡΠΊΠ΅ ΠΈΠ· ΠΠ‘Π Π½Π° ΡΠΎΠ΄Π΅ΡΠΆΠ°Π½ΠΈΠ΅ Π² Π»ΠΈΡΠΎΠΌ ΠΌΠ΅ΡΠ°Π»Π»Π΅ ΠΎΠ±ΡΠ΅Π³ΠΎ ΠΊΠΈΡΠ»ΠΎΡΠΎΠ΄Π°. ΠΠ° ΡΠΎΠ²ΡΠ΅ΠΌΠ΅Π½Π½ΠΎΠΌ ΡΡΠ°ΠΏΠ΅ ΡΠ°Π·Π²ΠΈΡΠΈΡ ΡΠ΅Ρ Π½ΠΎΠ»ΠΎΠ³ΠΈΡΠ΅ΡΠΊΠΎΠΉ ΡΡ Π΅ΠΌΡ ΠΏΡΠΎΠΈΠ·Π²ΠΎΠ΄ΡΡΠ²Π° ΡΡΠ°Π»ΠΈ ΠΏΠΎΠ²ΡΡΠ΅Π½ΠΈΠ΅ ΠΊΠ°ΡΠ΅ΡΡΠ²Π° ΠΌΠ΅ΡΠ°Π»Π»Π°, Π² ΡΠΎΠΌ ΡΠΈΡΠ»Π΅ Π³Π»ΡΠ±ΠΎΠΊΠΎΠ΅ ΡΠ°ΡΠΈΠ½ΠΈΡΠΎΠ²Π°Π½ΠΈΠ΅ ΠΌΠ΅ΡΠ°Π»Π»Π° ΠΎΡ ΠΊΠΈΡΠ»ΠΎΡΠΎΠ΄Π°, ΡΠ²Π»ΡΠ΅ΡΡΡ Π·Π°Π΄Π°ΡΠ΅ΠΉ Π²Π½Π΅ΠΏΠ΅ΡΠ½ΠΎΠΉ ΠΎΠ±ΡΠ°Π±ΠΎΡΠΊΠΈ. ΠΠ»Ρ Π²ΡΡΠ²Π»Π΅Π½ΠΈΡ Π½Π°ΠΏΡΠ°Π²Π»Π΅Π½ΠΈΠΉ ΡΠΎΠ²Π΅ΡΡΠ΅Π½ΡΡΠ²ΠΎΠ²Π°Π½ΠΈΡ ΡΠ΅Ρ Π½ΠΎΠ»ΠΎΠ³ΠΈΡΠ΅ΡΠΊΠΈΡ ΠΏΠ°ΡΠ°ΠΌΠ΅ΡΡΠΎΠ² Π²Π½Π΅ΠΏΠ΅ΡΠ½ΠΎΠΉ ΠΎΠ±ΡΠ°Π±ΠΎΡΠΊΠΈ Ρ ΡΠ΅Π»ΡΡ ΠΌΠΈΠ½ΠΈΠΌΠΈΠ·Π°ΡΠΈΠΈ ΡΠΎΠ΄Π΅ΡΠΆΠ°Π½ΠΈΡ Π² ΠΌΠ΅ΡΠ°Π»Π»Π΅ ΠΎΠ±ΡΠ΅Π³ΠΎ ΠΊΠΈΡΠ»ΠΎΡΠΎΠ΄Π° Π½Π°ΠΌΠΈ Π±ΡΠ»ΠΈ ΡΠΎΠΏΠΎΡΡΠ°Π²Π»Π΅Π½Ρ ΡΠ΅Π·ΡΠ»ΡΡΠ°ΡΡ Π»Π°Π±ΠΎΡΠ°ΡΠΎΡΠ½ΡΡ ΠΈΡΡΠ»Π΅Π΄ΠΎΠ²Π°Π½ΠΈΠΉ Π³Π°Π·ΠΎΠ½Π°ΡΡΡΠ΅Π½Π½ΠΎΡΡΠΈ ΡΡΠ°Π»ΠΈ ΠΈ Π΄Π°Π½Π½ΡΠ΅ ΠΏΠ°ΡΠΏΠΎΡΡΠΎΠ² ΡΠΎΠΎΡΠ²Π΅ΡΡΡΠ²ΡΡΡΠΈΡ ΠΏΠ»Π°Π²ΠΎΠΊ. ΠΡΠΎ ΠΏΠΎΠ·Π²ΠΎΠ»ΠΈΠ»ΠΎ ΡΠ΄Π΅Π»Π°ΡΡ ΡΠ»Π΅Π΄ΡΡΡΠΈΠ΅ Π·Π°ΠΊΠ»ΡΡΠ΅Π½ΠΈΡ:
1) ΠΠ»Ρ ΡΠΌΠ΅Π½ΡΡΠ΅Π½ΠΈΡ ΡΠΎΠ΄Π΅ΡΠΆΠ°Π½ΠΈΡ Π² ΠΌΠ΅ΡΠ°Π»Π»Π΅ ΠΎΠ±ΡΠ΅Π³ΠΎ ΠΊΠΈΡΠ»ΠΎΡΠΎΠ΄Π° ΡΠ΅Π»Π΅ΡΠΎΠΎΠ±ΡΠ°Π·Π½ΠΎ ΡΠ²Π΅ΡΡΠΈ ΠΊ ΠΌΠΈΠ½ΠΈΠΌΡΠΌΡ ΡΠ΅ΡΠ΅Π½ΠΈΠ΅ ΡΠ΅Ρ Π½ΠΎΠ»ΠΎΠ³ΠΈΡΠ΅ΡΠΊΠΎΠΉ Π·Π°Π΄Π°ΡΠΈ ΡΠ°ΡΠΊΠΈΡΠ»Π΅Π½ΠΈΡ Π½Π° ΠΠΠ. ΠΠΊΡΠΏΠ΅ΡΠΈΠΌΠ΅Π½ΡΠ°Π»ΡΠ½ΡΠ΅ Π΄Π°Π½Π½ΡΠ΅, ΠΏΡΠ΅Π΄ΡΡΠ°Π²Π»Π΅Π½Π½ΡΠ΅ Π½Π° ΡΠΈΡΡΠ½ΠΊΠ΅ 3.4, ΡΠΊΠ°Π·ΡΠ²Π°ΡΡ, ΡΡΠΎ Π΄Π»Ρ ΠΏΠΎΠ»ΡΡΠ΅Π½ΠΈΡ ΡΡΠ΅Π±ΡΠ΅ΠΌΠΎΠ³ΠΎ ΠΊΠ°ΡΠ΅ΡΡΠ²Π° ΠΌΠ΅ΡΠ°Π»Π»Π° ΠΊΠΎΠ»ΠΈΡΠ΅ΡΡΠ²ΠΎ Π°Π»ΡΠΌΠΈΠ½ΠΈΠ΅Π²ΠΎΠΉ ΠΊΠ°ΡΠ°Π½ΠΊΠΈ, ΠΎΡΠ΄Π°Π½Π½ΠΎΠΉ Π½Π° ΠΏΠ΅ΡΠΈ-ΠΊΠΎΠ²ΡΠ΅, Π½Π΅ Π΄ΠΎΠ»ΠΆΠ½ΠΎ ΠΏΡΠ΅Π²ΡΡΠ°ΡΡ 30 ΠΊΠ³. Π¦Π΅Π»Π΅ΡΠΎΠΎΠ±ΡΠ°Π·Π½ΠΎ ΠΌΠ°ΠΊΡΠΈΠΌΠ°Π»ΡΠ½ΠΎ ΠΏΠΎΠ»Π½ΠΎ ΡΠ°ΡΠΊΠΈΡΠ»ΠΈΡΡ ΠΌΠ΅ΡΠ°Π»Π» Π½Π° Π²ΡΠΏΡΡΠΊΠ΅ ΠΈΠ· ΠΠ‘Π ΠΈ ΠΈΠΌΠ΅ΡΡ Π² ΠΏΠ΅ΡΠ²ΠΎΠΉ ΠΏΡΠΎΠ±Π΅ Π½Π° ΠΠΠ ΡΠΎΠ΄Π΅ΡΠΆΠ°Π½ΠΈΠ΅ Π°Π»ΡΠΌΠΈΠ½ΠΈΡ Π½Π΅ ΠΌΠ΅Π½Π΅Π΅ 0,015Ρ0,020%.
2) Π‘ ΡΠΎΡΠΊΠΈ Π·ΡΠ΅Π½ΠΈΡ ΠΊΠ°ΡΠ΅ΡΡΠ²Π° ΠΌΠ΅ΡΠ°Π»Π»Π° ΡΠ΅Π»Π΅ΡΠΎΠΎΠ±ΡΠ°Π·Π½ΠΎ ΠΎΠ³ΡΠ°Π½ΠΈΡΠ΅Π½ΠΈΠ΅ ΠΊΠΎΠ½ΡΠ΅Π½ΡΡΠ°ΡΠΈΠΈ Π°Π»ΡΠΌΠΈΠ½ΠΈΡ ΠΈ, ΡΠΎΠΎΡΠ²Π΅ΡΡΡΠ²Π΅Π½Π½ΠΎ, ΠΊΠ°Π»ΡΡΠΈΡ Π² Π³ΠΎΡΠΎΠ²ΠΎΠΌ ΠΌΠ΅ΡΠ°Π»Π»Π΅ ΠΌΠΈΠ½ΠΈΠΌΠ°Π»ΡΠ½ΠΎ Π½Π΅ΠΎΠ±Ρ ΠΎΠ΄ΠΈΠΌΡΠΌΠΈ ΠΏΡΠ΅Π΄Π΅Π»Π°ΠΌΠΈ. ΠΠ°Π½Π½ΡΠ΅, ΠΏΡΠ΅Π΄ΡΡΠ°Π²Π»Π΅Π½Π½ΡΠ΅ Π½Π° ΡΠΈΡΡΠ½ΠΊΠ°Ρ 3.1−3.4, ΡΠ²ΠΈΠ΄Π΅ΡΠ΅Π»ΡΡΡΠ²ΡΡΡ ΠΎ ΡΡΡΠ΅ΡΡΠ²Π΅Π½Π½ΠΎΠΌ Π²Π»ΠΈΡΠ½ΠΈΠΈ Π½Π° ΡΠΎΠ΄Π΅ΡΠΆΠ°Π½ΠΈΠ΅ Π² Π»ΠΈΡΠΎΠΌ ΠΌΠ΅ΡΠ°Π»Π»Π΅ ΠΎΠ±ΡΠ΅Π³ΠΎ ΠΊΠΈΡΠ»ΠΎΡΠΎΠ΄Π° ΠΈ ΡΡΠΎΠ²Π΅Π½Ρ ΡΠΊΡΠΏΠ»ΡΠ°ΡΠ°ΡΠΈΠΎΠ½Π½ΡΡ ΡΠ²ΠΎΠΉΡΡΠ² ΠΌΠ΅ΡΠ°Π»Π»Π° ΡΡΡΠ± ΠΊΠΎΠ½ΡΠ΅Π½ΡΡΠ°ΡΠΈΠΉ Π² ΠΌΠ΅ΡΠ°Π»Π»Π΅ Π°Π»ΡΠΌΠΈΠ½ΠΈΡ ΠΈ ΠΊΠ°Π»ΡΡΠΈΡ. Π ΡΠ°ΡΡΠ½ΠΎΡΡΠΈ, ΡΠ²Π΅Π»ΠΈΡΠ΅Π½ΠΈΠ΅ ΡΠΎΠ΄Π΅ΡΠΆΠ°Π½ΠΈΡ Π°Π»ΡΠΌΠΈΠ½ΠΈΡ Π² ΠΏΡΠΎΠ±Π΅ ΠΏΠΎΡΠ»Π΅ Π²Π²ΠΎΠ΄Π° ΡΠΈΠ»ΠΈΠΊΠΎΠΊΠ°Π»ΡΡΠΈΡ ΡΠΏΠΎΡΠΎΠ±ΡΡΠ²ΡΠ΅Ρ ΡΠ²Π΅Π»ΠΈΡΠ΅Π½ΠΈΡ ΠΊΠΎΠ½ΡΠ΅Π½ΡΡΠ°ΡΠΈΠΈ ΠΎΠ±ΡΠ΅Π³ΠΎ ΠΊΠΈΡΠ»ΠΎΡΠΎΠ΄Π° Π² Π»ΠΈΡΠΎΠΌ ΠΌΠ΅ΡΠ°Π»Π»Π΅ ΠΈ ΡΠ½ΠΈΠΆΠ΅Π½ΠΈΡ ΠΏΠ»Π°ΡΡΠΈΡΠ½ΠΎΡΡΠΈ ΡΡΠ°Π»ΠΈ Π. ΠΠΎΠ·ΠΌΠΎΠΆΠ½ΠΎ, ΡΡΠΎ ΡΠ²ΡΠ·Π°Π½ΠΎ Ρ ΠΊΠΎΠ»ΠΈΡΠ΅ΡΡΠ²ΠΎΠΌ ΠΎΠΊΡΠΈΠ΄Π½ΡΡ Π½Π΅ΠΌΠ΅ΡΠ°Π»Π»ΠΈΡΠ΅ΡΠΊΠΈΡ Π²ΠΊΠ»ΡΡΠ΅Π½ΠΈΠΉ, ΠΈΡ ΠΌΠΎΡΡΠΎΠ»ΠΎΠ³ΠΈΠ΅ΠΉ, Π΄ΠΈΡΠΏΠ΅ΡΡΠ½ΠΎΡΡΡΡ ΠΈ ΡΠ°ΡΠΏΠΎΠ»ΠΎΠΆΠ΅Π½ΠΈΠ΅ΠΌ.
Π ΠΈΡΡΠ½ΠΎΠΊ 3.1. ΠΠ»ΠΈΡΠ½ΠΈΠ΅ ΠΏΠ°ΡΠ°ΠΌΠ΅ΡΡΠΎΠ² ΡΠ΅ΠΆΠΈΠΌΠ° ΡΠ°ΡΠΊΠΈΡΠ»Π΅Π½ΠΈΡ Π½Π° ΡΠΎΠ΄Π΅ΡΠΆΠ°Π½ΠΈΠ΅ Π² Π»ΠΈΡΠΎΠΌ ΠΌΠ΅ΡΠ°Π»Π»Π΅ ΠΎΠ±ΡΠ΅Π³ΠΎ ΠΊΠΈΡΠ»ΠΎΡΠΎΠ΄Π° Π ΠΈΡΡΠ½ΠΎΠΊ 3.2 — ΠΠ»ΠΈΡΠ½ΠΈΠ΅ ΠΊΠΎΠ½ΡΠ΅Π½ΡΡΠ°ΡΠΈΠΉ Π² ΠΌΠ΅ΡΠ°Π»Π»Π΅ Π°Π»ΡΠΌΠΈΠ½ΠΈΡ ΠΈ ΠΊΠ°Π»ΡΡΠΈΡ Π½Π° ΡΠΎΠ΄Π΅ΡΠΆΠ°Π½ΠΈΠ΅ Π² Π»ΠΈΡΠΎΠΌ ΠΌΠ΅ΡΠ°Π»Π»Π΅ ΠΎΠ±ΡΠ΅Π³ΠΎ ΠΊΠΈΡΠ»ΠΎΡΠΎΠ΄Π° Π΄Π»Ρ ΡΡΠ°Π»ΠΈ Π Π ΠΈΡΡΠ½ΠΎΠΊ 3.3. ΠΠ»ΠΈΡΠ½ΠΈΠ΅ ΠΊΠΎΠ½ΡΠ΅Π½ΡΡΠ°ΡΠΈΠΈ Π² ΠΌΠ΅ΡΠ°Π»Π»Π΅ Π°Π»ΡΠΌΠΈΠ½ΠΈΡ Π½Π° ΡΡΠΎΠ²Π΅Π½Ρ ΡΠΊΡΠΏΠ»ΡΠ°ΡΠ°ΡΠΈΠΎΠ½Π½ΡΡ ΡΠ²ΠΎΠΉΡΡΠ² ΠΌΠ΅ΡΠ°Π»Π»Π° ΡΡΡΠ± Π΄Π»Ρ ΡΡΠ°Π»ΠΈ Π Π ΠΈΡΡΠ½ΠΎΠΊ 3.4. ΠΠ»ΠΈΡΠ½ΠΈΠ΅ ΠΊΠΎΠ½ΡΠ΅Π½ΡΡΠ°ΡΠΈΠΈ Π² ΠΌΠ΅ΡΠ°Π»Π»Π΅ ΠΊΠ°Π»ΡΡΠΈΡ Π½Π° ΡΡΠΎΠ²Π΅Π½Ρ ΡΠΊΡΠΏΠ»ΡΠ°ΡΠ°ΡΠΈΠΎΠ½Π½ΡΡ ΡΠ²ΠΎΠΉΡΡΠ² ΠΌΠ΅ΡΠ°Π»Π»Π° ΡΡΡΠ± Π΄Π»Ρ ΡΡΠ°Π»ΠΈ Π
3) ΠΠ°Π²ΠΈΡΠΈΠΌΠΎΡΡΡ, ΠΏΡΠ΅Π΄ΡΡΠ°Π²Π»Π΅Π½Π½Π°Ρ Π½Π° ΡΠΈΡΡΠ½ΠΊΠ΅ 3.5, ΡΠΊΠ°Π·ΡΠ²Π°Π΅Ρ Π½Π° Π½Π°Π»ΠΈΡΠΈΠ΅ ΠΎΠΏΡΠ΅Π΄Π΅Π»Π΅Π½Π½ΡΡ ΡΠ΅Π·Π΅ΡΠ²ΠΎΠ² ΠΎΠΏΡΠΈΠΌΠΈΠ·Π°ΡΠΈΠΈ ΡΠ΅ΠΆΠΈΠΌΠ° ΠΏΡΠΎΠ΄ΡΠ²ΠΊΠΈ ΠΈΠ½Π΅ΡΡΠ½ΡΡ Π³Π°Π·ΠΎΠΌ Π΄Π»Ρ ΠΏΠΎΠ²ΡΡΠ΅Π½ΠΈΡ ΠΊΠ°ΡΠ΅ΡΡΠ²Π° ΡΡΠ°Π»ΠΈ. Π ΡΠ΅Π»ΡΡ ΠΏΠΎΠ»ΡΡΠ΅Π½ΠΈΡ Π·Π°Π΄Π°Π½Π½ΡΡ ΠΏΠ°ΡΠ°ΠΌΠ΅ΡΡΠΎΠ² ΠΊΠ°ΡΠ΅ΡΡΠ²Π° ΡΠ΅Π»Π΅ΡΠΎΠΎΠ±ΡΠ°Π·Π½ΠΎ ΠΏΠΎΠ΄Π΄Π΅ΡΠΆΠΈΠ²Π°ΡΡ ΠΈΠ½ΡΠ΅Π½ΡΠΈΠ²Π½ΠΎΡΡΡ ΠΏΡΠΎΠ΄ΡΠ²ΠΊΠΈ Π½Π΅ Π½ΠΈΠΆΠ΅ 400 Π»/ΠΌΠΈΠ½. Π‘Π½ΠΈΠΆΠ΅Π½ΠΈΠ΅ ΡΠΎΠ΄Π΅ΡΠΆΠ°Π½ΠΈΡ ΠΎΠ±ΡΠ΅Π³ΠΎ ΠΊΠΈΡΠ»ΠΎΡΠΎΠ΄Π° Π² ΠΌΠ΅ΡΠ°Π»Π»Π΅ ΠΏΡΠΈ ΡΠ²Π΅Π»ΠΈΡΠ΅Π½ΠΈΠΈ ΠΈΠ½ΡΠ΅Π½ΡΠΈΠ²Π½ΠΎΡΡΠΈ ΠΏΡΠΎΠ΄ΡΠ²ΠΊΠΈ ΠΌΠΎΠΆΠ΅Ρ Π±ΡΡΡ ΡΠ²ΡΠ·Π°Π½ΠΎ Ρ ΠΏΠΎΠ²ΡΡΠ΅Π½ΠΈΠ΅ΠΌ Π³Π»ΡΠ±ΠΈΠ½Ρ ΡΠ°ΡΠΈΠ½ΠΈΡΠΎΠ²Π°Π½ΠΈΡ ΠΌΠ΅ΡΠ°Π»Π»Π° ΠΎΡ ΠΏΡΠΎΠ΄ΡΠΊΡΠΎΠ² ΡΠ°ΡΠΊΠΈΡΠ»Π΅Π½ΠΈΡ.
Π ΠΈΡΡΠ½ΠΎΠΊ 3.5. ΠΠ»ΠΈΡΠ½ΠΈΠ΅ ΠΈΠ½ΡΠ΅Π½ΡΠΈΠ²Π½ΠΎΡΡΠΈ ΠΏΡΠΎΠ΄ΡΠ²ΠΊΠΈ ΠΈΠ½Π΅ΡΡΠ½ΡΠΌ Π³Π°Π·ΠΎΠΌ ΠΏΡΠΈ ΠΎΠ±ΡΠ°Π±ΠΎΡΠΊΠ΅ Π½Π° ΠΠΠ Π½Π° ΡΠΎΠ΄Π΅ΡΠΆΠ°Π½ΠΈΠ΅ Π² Π»ΠΈΡΠΎΠΌ ΠΌΠ΅ΡΠ°Π»Π»Π΅ ΠΎΠ±ΡΠ΅Π³ΠΎ ΠΊΠΈΡΠ»ΠΎΡΠΎΠ΄Π° Π² ΡΠ»ΡΡΠ°Π΅ ΡΠ°ΡΠΊΠΈΡΠ»Π΅Π½ΠΈΡ Π½Π° Π²ΡΠΏΡΡΠΊΠ΅ ΠΈΠ· ΠΠ‘Π ΡΠ΅ΡΡΠΎΠ°Π»ΡΠΌΠΈΠ½ΠΈΠ΅ΠΌ
4) Π’Π΅ΠΌΠΏΠ΅ΡΠ°ΡΡΡΠ½ΡΠΉ ΡΠ΅ΠΆΠΈΠΌ ΠΎΠ±ΡΠ°Π±ΠΎΡΠΊΠΈ Π½Π° ΠΠΠ ΡΠ°ΠΊΠΆΠ΅ Π²Π»ΠΈΡΠ΅Ρ Π½Π° ΡΠΎΠ΄Π΅ΡΠΆΠ°Π½ΠΈΠ΅ Π² Π»ΠΈΡΠΎΠΌ ΠΌΠ΅ΡΠ°Π»Π»Π΅ ΠΎΠ±ΡΠ΅Π³ΠΎ ΠΊΠΈΡΠ»ΠΎΡΠΎΠ΄Π°. ΠΠ° ΡΡΠΎ ΡΠΊΠ°Π·ΡΠ²Π°ΡΡ ΡΠ΅Π·ΡΠ»ΡΡΠ°ΡΡ ΡΠΎΠΏΠΎΡΡΠ°Π²Π»Π΅Π½ΠΈΡ Π»Π°Π±ΠΎΡΠ°ΡΠΎΡΠ½ΡΡ ΡΠ΅Π·ΡΠ»ΡΡΠ°ΡΠΎΠ² ΠΎΡΠ΅Π½ΠΊΠΈ ΠΊΠΎΠ½ΡΠ΅Π½ΡΡΠ°ΡΠΈΠΈ ΠΎΠ±ΡΠ΅Π³ΠΎ ΠΊΠΈΡΠ»ΠΎΡΠΎΠ΄Π° ΠΈ ΠΏΠ°ΡΠΏΠΎΡΡΠΎΠ² ΡΠΎΠΎΡΠ²Π΅ΡΡΡΠ²ΡΡΡΠΈΡ ΠΏΠ»Π°Π²ΠΎΠΊ, ΠΏΡΠ΅Π΄ΡΡΠ°Π²Π»Π΅Π½Π½ΠΎΠ΅ Π½Π° ΡΠΈΡΡΠ½ΠΊΠ΅ 3.6. ΠΡΠ΅Π²ΠΈΠ΄Π½ΠΎ, ΡΡΠΎ ΡΠ²ΡΠ·Π°Π½ΠΎ ΡΠΎ Π·Π½Π°ΡΠΈΡΠ΅Π»ΡΠ½ΠΎΠΉ Π·Π°Π²ΠΈΡΠΈΠΌΠΎΡΡΡΡ ΠΊΠΎΠ½ΡΡΠ°Π½ΡΡ ΡΠ°Π²Π½ΠΎΠ²Π΅ΡΠΈΡ ΡΠ΅Π°ΠΊΡΠΈΠΈ ΡΠ°ΡΠΊΠΈΡΠ»Π΅Π½ΠΈΡ ΠΎΡ ΡΠ΅ΠΌΠΏΠ΅ΡΠ°ΡΡΡΡ. Π‘ΠΎ ΡΠ½ΠΈΠΆΠ΅Π½ΠΈΠ΅ΠΌ ΡΠ΅ΠΌΠΏΠ΅ΡΠ°ΡΡΡΡ ΠΏΠΎΠ»Π½ΠΎΡΠ° ΠΏΡΠΎΡΠ΅ΠΊΠ°Π½ΠΈΡ ΡΠ΅Π°ΠΊΡΠΈΠΈ Π²ΠΎΠ·ΡΠ°ΡΡΠ°Π΅Ρ, ΡΡΠΎ ΠΏΡΠ΅Π΄ΠΎΠΏΡΠ΅Π΄Π΅Π»ΡΠ΅Ρ Π²ΠΎΠ·ΡΠ°ΡΡΠ°Π½ΠΈΠ΅ ΡΠΎΠ΄Π΅ΡΠΆΠ°Π½ΠΈΡ Π² ΠΌΠ΅ΡΠ°Π»Π»Π΅ ΠΏΡΠΎΠ΄ΡΠΊΡΠΎΠ² ΡΠ°ΡΠΊΠΈΡΠ»Π΅Π½ΠΈΡ (ΡΠ²ΡΠ·Π°Π½Π½ΡΡ Π°Π»ΡΠΌΠΈΠ½ΠΈΡ ΠΈ ΠΊΠΈΡΠ»ΠΎΡΠΎΠ΄Π°).
Π ΠΈΡΡΠ½ΠΎΠΊ 3.6. ΠΠ»ΠΈΡΠ½ΠΈΠ΅ ΠΏΠ°ΡΠ°ΠΌΠ΅ΡΡΠΎΠ² ΡΠ΅ΠΌΠΏΠ΅ΡΠ°ΡΡΡΠ½ΠΎΠ³ΠΎ ΡΠ΅ΠΆΠΈΠΌΠ° ΠΎΠ±ΡΠ°Π±ΠΎΡΠΊΠΈ Π½Π° ΠΠΠ Π½Π° ΡΠΎΠ΄Π΅ΡΠΆΠ°Π½ΠΈΠ΅ ΠΎΠ±ΡΠ΅Π³ΠΎ ΠΊΠΈΡΠ»ΠΎΡΠΎΠ΄Π° Π² Π»ΠΈΡΠΎΠΌ ΠΌΠ΅ΡΠ°Π»Π»Π΅ Π ΠΈΡΡΠ½ΠΎΠΊ 3.7. — ΠΠ»ΠΈΡΠ½ΠΈΠ΅ Π²Π΅Π»ΠΈΡΠΈΠ½Ρ ΠΏΠ΅ΡΠ΅Π³ΡΠ΅Π²Π° Π½Π° ΠΠΠ Π½Π° ΡΠ΄Π°ΡΠ½ΡΡ Π²ΡΠ·ΠΊΠΎΡΡΡ ΡΡΠ°Π»ΠΈ 20ΠΠ’ ΠΡΠΎΠ³ΠΎ Π½Π΅Π³Π°ΡΠΈΠ²Π½ΠΎ ΡΠΊΠ°Π·ΡΠ²Π°Π΅ΡΡΡ Π½Π° ΠΎΠΏΡΠ΅Π΄Π΅Π»Π΅Π½Π½ΡΡ ΡΠΊΡΠΏΠ»ΡΠ°ΡΠ°ΡΠΈΠΎΠ½Π½ΡΡ ΡΠ²ΠΎΠΉΡΡΠ²Π°Ρ ΠΌΠ΅ΡΠ°Π»Π»Π° (ΡΠΈΡ. 3.7). ΠΠ°ΡΡΠΈΡΠΎΠ²Π°Π½ΠΈΠ΅ ΡΠ΅ΠΌΠΏΠ΅ΡΠ°ΡΡΡΠΎΠΉ ΠΌΠ΅ΡΠ°Π»Π»Π° ΡΡΡΠ΅ΡΡΠ²Π΅Π½Π½ΠΎ ΠΎΠ³ΡΠ°Π½ΠΈΡΠ΅Π½ΠΎ ΡΠ΅Ρ Π½ΠΎΠ»ΠΎΠ³ΠΈΡΠ΅ΡΠΊΠΎΠΉ ΠΈΠ½ΡΡΡΡΠΊΡΠΈΠ΅ΠΉ ΠΈ ΠΏΡΠΎΠΈΠ·Π²ΠΎΠ΄ΡΡΠ²Π΅Π½Π½ΠΎΠΉ Π½Π΅ΠΎΠ±Ρ ΠΎΠ΄ΠΈΠΌΠΎΡΡΡΡ. Π ΡΠ°ΡΡΠ½ΠΎΡΡΠΈ, ΠΏΠΎΡΠ²Π»Π΅Π½ΠΈΠ΅ Π² ΡΠ΅Ρ Π½ΠΎΠ»ΠΎΠ³ΠΈΡΠ΅ΡΠΊΠΎΠΉ ΡΡ Π΅ΠΌΠ΅ Π²Π°ΠΊΡΡΠΌΠΈΡΠΎΠ²Π°Π½ΠΈΡ ΠΏΠΎΡΡΠ΅Π±ΠΎΠ²Π°Π»ΠΎ Π½Π΅ΠΈΠ·Π±Π΅ΠΆΠ½ΠΎΠ³ΠΎ ΡΠ²Π΅Π»ΠΈΡΠ΅Π½ΠΈΡ ΡΡΠ΅ΠΏΠ΅Π½ΠΈ Π½Π°Π³ΡΠ΅Π²Π° Π½Π° ΠΠΠ Π² ΡΠ΅Π»ΡΡ ΠΊΠΎΠΌΠΏΠ΅Π½ΡΠ°ΡΠΈΠΈ ΡΠ΅ΠΏΠ»ΠΎΠΏΠΎΡΠ΅ΡΡ ΠΏΡΠΈ ΠΏΠΎΡΠ»Π΅Π΄ΡΡΡΠ΅ΠΉ ΠΎΠ±ΡΠ°Π±ΠΎΡΠΊΠΈ. Π‘ Π΄ΡΡΠ³ΠΎΠΉ ΡΡΠΎΡΠΎΠ½Ρ, ΠΎΠ΄Π½ΠΈΠΌ ΠΈΠ· Π½Π°ΠΏΡΠ°Π²Π»Π΅Π½ΠΈΠΉ ΡΠ½ΠΈΠΆΠ΅Π½ΠΈΡ ΡΠΎΠ΄Π΅ΡΠΆΠ°Π½ΠΈΡ Π² Π»ΠΈΡΠΎΠΌ ΠΌΠ΅ΡΠ°Π»Π»Π΅ ΠΊΠΈΡΠ»ΠΎΡΠΎΠ΄Π°, Π²Π΅ΡΠΎΡΡΠ½ΠΎ, ΠΌΠΎΠΆΠ΅Ρ ΡΠ°ΡΡΠΌΠ°ΡΡΠΈΠ²Π°ΡΡΡΡ ΡΡΠ΅Ρ ΡΠ΅ΠΌΠΏΠ΅ΡΠ°ΡΡΡΠ½ΠΎΠ³ΠΎ ΡΠ°ΠΊΡΠΎΡΠ° ΠΏΡΠΈ ΠΎΠΏΡΠΈΠΌΠΈΠ·Π°ΡΠΈΠΈ ΡΠ΅ΠΆΠΈΠΌΠ° ΡΠ°ΡΠΊΠΈΡΠ»Π΅Π½ΠΈΡ. ΠΠΎΠ»ΡΡΠ΅Π½ΠΈΠ΅ ΠΎΠΏΡΠΈΠΌΠ°Π»ΡΠ½ΠΎΠΉ ΠΊΠΎΠ½ΡΠ΅Π½ΡΡΠ°ΡΠΈΠΈ Π°Π»ΡΠΌΠΈΠ½ΠΈΡ ΠΏΠΎ ΠΏΡΠΈΡ ΠΎΠ΄Ρ ΠΠΠ ΡΠ²Π»ΡΠ΅ΡΡΡ ΠΎΠΏΡΠΈΠΌΠ°Π»ΡΠ½ΡΠΌ ΠΈ Ρ ΡΡΠΈΡ ΠΏΠΎΠ·ΠΈΡΠΈΠΉ.
Π’Π°ΠΊΠΈΠΌ ΠΎΠ±ΡΠ°Π·ΠΎΠΌ, Π½Π°Π»ΠΈΡΠΈΠ΅ Π² ΡΠ΅Ρ Π½ΠΎΠ»ΠΎΠ³ΠΈΡΠ΅ΡΠΊΠΎΠΉ ΡΡ Π΅ΠΌΠ΅ Π²Π½Π΅ΠΏΠ΅ΡΠ½ΠΎΠΉ ΠΎΠ±ΡΠ°Π±ΠΎΡΠΊΠΈ Π½Π΅ ΠΏΠΎΠ·Π²ΠΎΠ»ΡΠ΅Ρ Π½Π΅ΠΉΡΡΠ°Π»ΠΈΠ·ΠΎΠ²Π°ΡΡ ΠΏΠΎΠ»Π½ΠΎΡΡΡΡ Π½Π΅Π³Π°ΡΠΈΠ²Π½ΠΎΠ΅ Π²Π»ΠΈΡΠ½ΠΈΠ΅ ΠΏΠΎΠ²ΡΡΠ΅Π½Π½ΠΎΠΉ ΠΎΠΊΠΈΡΠ»Π΅Π½Π½ΠΎΡΡΠΈ ΠΏΠΎΠ»ΡΠΏΡΠΎΠ΄ΡΠΊΡΠ°. ΠΠ΄Π½Π°ΠΊΠΎ ΠΎΠΏΡΠΈΠΌΠΈΠ·Π°ΡΠΈΡ ΡΠ΅Ρ Π½ΠΎΠ»ΠΎΠ³ΠΈΡΠ΅ΡΠΊΠΈΡ ΠΏΠ°ΡΠ°ΠΌΠ΅ΡΡΠΎΠ² Π²Π½Π΅ΠΏΠ΅ΡΠ½ΠΎΠΉ ΠΎΠ±ΡΠ°Π±ΠΎΡΠΊΠΈ (Π² ΡΠ°ΡΡΠ½ΠΎΡΡΠΈ, ΡΠ΅ΠΆΠΈΠΌΠ° ΡΠ°ΡΠΊΠΈΡΠ»Π΅Π½ΠΈΡ ΠΈ ΡΠ΅ΠΆΠΈΠΌΠ° ΠΏΡΠΎΠ΄ΡΠ²ΠΊΠΈ ΠΈΠ½Π΅ΡΡΠ½ΡΠΌ Π³Π°Π·ΠΎΠΌ) ΠΌΠΎΠΆΠ΅Ρ ΡΠΏΠΎΡΠΎΠ±ΡΡΠ²ΠΎΠ²Π°ΡΡ ΡΠ½ΠΈΠΆΠ΅Π½ΠΈΡ ΡΠΎΠ΄Π΅ΡΠΆΠ°Π½ΠΈΡ Π² ΠΌΠ΅ΡΠ°Π»Π»Π΅ ΠΎΠ±ΡΠ΅Π³ΠΎ ΠΊΠΈΡΠ»ΠΎΡΠΎΠ΄Π° ΠΈ ΠΏΠΎΠ²ΡΡΠ΅Π½ΠΈΡ ΠΊΠ°ΡΠ΅ΡΡΠ²Π° ΡΡΠ°Π»ΠΈ.
3.2 ΠΠ»ΠΈΡΠ½ΠΈΠ΅ ΡΠ΅Ρ Π½ΠΎΠ»ΠΎΠ³ΠΈΡΠ΅ΡΠΊΠΈΡ ΠΏΠ°ΡΠ°ΠΌΠ΅ΡΡΠΎΠ² ΠΎΠ±ΡΠ°Π±ΠΎΡΠΊΠΈ Π½Π° ΠΠΠ Π½Π° ΡΠ°Π²Π½ΠΎΠ²Π΅ΡΠ½ΠΎΡΡΡ ΠΌΠ΅ΡΠ°Π»Π»Π°
ΠΠΎ ΠΏΡΠΈΡ ΠΎΠ΄Ρ Π½Π° ΠΠΠ ΠΏΠΎΠ»ΡΠΏΡΠΎΠ΄ΡΠΊΡ ΠΈΠΌΠ΅Π΅Ρ ΠΎΡΠ½ΠΎΡΠΈΡΠ΅Π»ΡΠ½ΠΎ ΡΠ°Π²Π½ΠΎΠ²Π΅ΡΠ½ΠΎΠ΅, ΡΡΠ°Π±ΠΈΠ»ΡΠ½ΠΎΠ΅ ΡΡΡΡΠΊΡΡΡΠ½ΠΎΠ΅ ΡΠΎΡΡΠΎΡΠ½ΠΈΠ΅. ΠΠΎΡΡΠΎΠΌΡ Π΄Π°Π»ΡΠ½Π΅ΠΉΡΠΈΠ΅ ΠΊΠΎΡΡΠ΅ΠΊΡΠΈΡΠΎΠ²ΠΊΠΈ Ρ ΠΈΠΌΠΈΡΠ΅ΡΠΊΠΎΠ³ΠΎ ΡΠΎΡΡΠ°Π²Π° ΠΏΠΎΡΡΠ΅Π±ΡΡΡ Π΄ΠΎΡΡΠ°ΡΠΎΡΠ½ΠΎ Π±ΠΎΠ»ΡΡΠΎΠ³ΠΎ Π²ΡΠ΅ΠΌΠ΅Π½ΠΈ ΡΠ΅Π»Π°ΠΊΡΠ°ΡΠΈΠΈ. Π‘ΠΎΠΎΡΠ²Π΅ΡΡΡΠ²Π΅Π½Π½ΠΎ, Π²ΡΡΠ²Π»Π΅Π½Π½ΡΠ΅ ΡΠ°Π½Π΅Π΅ Π·Π°ΠΊΠΎΠ½ΠΎΠΌΠ΅ΡΠ½ΠΎΡΡΠΈ Π²Π»ΠΈΡΠ½ΠΈΡ ΠΏΠ°ΡΠ°ΠΌΠ΅ΡΡΠΎΠ² ΠΎΠ±ΡΠ°Π±ΠΎΡΠΊΠΈ ΠΌΠ°ΡΡΠ΅Π½ΠΎΠ²ΡΠΊΠΎΠ³ΠΎ ΠΏΠΎΠ»ΡΠΏΡΠΎΠ΄ΡΠΊΡΠ° Π½Π° ΠΠΠ Π½Π° ΡΠ°Π²Π½ΠΎΠ²Π΅ΡΠ½ΠΎΡΡΡ ΡΠ°ΡΠΏΠ»Π°Π²ΠΎΠ² ΠΈ ΡΡΠΎΠ²Π΅Π½Ρ ΡΠΊΡΠΏΠ»ΡΠ°ΡΠ°ΡΠΈΠΎΠ½Π½ΡΡ ΡΠ²ΠΎΠΉΡΡΠ² ΡΠΎΡ ΡΠ°Π½ΡΡΡ ΡΠ²ΠΎΡ Π°ΠΊΡΡΠ°Π»ΡΠ½ΠΎΡΡΡ ΠΈ ΠΏΡΠΈ Π²Π½Π΅ΠΏΠ΅ΡΠ½ΠΎΠΉ ΠΎΠ±ΡΠ°Π±ΠΎΡΠΊΠ΅ ΠΏΠΎΠ»ΡΠΏΡΠΎΠ΄ΡΠΊΡΠ°, Π²ΡΠΏΠ»Π°Π²Π»Π΅Π½Π½ΠΎΠ³ΠΎ Π² ΠΠ‘Π. ΠΡΠΎ ΠΏΠΎΠ΄ΡΠ²Π΅ΡΠΆΠ΄Π°ΡΡ ΡΠ΅Π·ΡΠ»ΡΡΠ°ΡΡ ΡΠΊΡΠΏΠ΅ΡΠΈΠΌΠ΅Π½ΡΠ°Π»ΡΠ½ΡΡ ΠΈΡΡΠ»Π΅Π΄ΠΎΠ²Π°Π½ΠΈΠΉ, ΠΏΡΠ΅Π΄ΡΡΠ°Π²Π»Π΅Π½Π½ΡΠ΅ Π½ΠΈΠΆΠ΅:
— Π² ΡΠΎΠ³Π»Π°ΡΠΈΠΈ Ρ ΠΏΠΎΠΊΠ°Π·Π°Π½Π½ΡΠΌ Π²ΡΡΠ΅ Π½Π΅Π³Π°ΡΠΈΠ²Π½ΡΠΌ Π²Π»ΠΈΡΠ½ΠΈΠ΅ΠΌ ΠΏΡΠΈΠΌΠ΅ΡΠΈ ΠΊΠΈΡΠ»ΠΎΡΠΎΠ΄Π° ΠΎΠΏΡΠΈΠΌΠΈΠ·Π°ΡΠΈΡ ΡΠ΅Ρ Π½ΠΎΠ»ΠΎΠ³ΠΈΠΈ ΡΠ°ΡΠΊΠΈΡΠ»Π΅Π½ΠΈΡ ΠΌΠ΅ΡΠ°Π»Π»Π° Π½Π° Π²ΡΠΏΡΡΠΊΠ΅ ΠΈΠ· ΠΠ‘Π ΠΈ ΠΏΠΎΠ»ΡΡΠ΅Π½ΠΈΠ΅ Π·Π°Π΄Π°Π½Π½ΠΎΠ³ΠΎ Π°Π»ΡΠΌΠΈΠ½ΠΈΡ ΠΏΠΎ ΠΏΡΠΈΡ ΠΎΠ΄Ρ Π½Π° ΠΠΠ ΠΏΠΎΠ»ΠΎΠΆΠΈΡΠ΅Π»ΡΠ½ΠΎ ΡΠΊΠ°Π·ΡΠ²Π°Π΅ΡΡΡ Π½Π° ΡΠ°Π²Π½ΠΎΠ²Π΅ΡΠ½ΠΎΡΡΠΈ ΡΠ°ΡΠΏΠ»Π°Π²Π° (ΡΠΈΡΡΠ½ΠΎΠΊ 3.8);
Π ΠΈΡΡΠ½ΠΎΠΊ 3.8. ΠΠ»ΠΈΡΠ½ΠΈΠ΅ ΠΊΠΎΠ½ΡΠ΅Π½ΡΡΠ°ΡΠΈΠΈ Π°Π»ΡΠΌΠΈΠ½ΠΈΡ Π² ΠΏΠΎΠ»ΡΠΏΡΠΎΠ΄ΡΠΊΡΠ΅ ΠΏΠΎ ΠΏΡΠΈΡ ΠΎΠ΄Ρ Π½Π° ΠΠΠ Π½Π° ΡΠ°Π²Π½ΠΎΠ²Π΅ΡΠ½ΠΎΡΡΡ ΡΡΠ°Π»ΠΈ 20ΠΠ’
— ΡΠ²Π΅Π»ΠΈΡΠ΅Π½ΠΈΠ΅ ΠΌΠ°ΡΡΡ ΠΏΡΠΈΡΠ°Π΄ΠΎΠΊ ΡΠ΅ΡΡΠΎΡΠΏΠ»Π°Π²ΠΎΠ² Π²ΠΎ Π²ΡΠ΅ΠΌΡ ΠΎΠ±ΡΠ°Π±ΠΎΡΠΊΠΈ Π½Π° ΠΠΠ ΠΏΠΎΠ²ΡΡΠ°Π΅Ρ Π½Π΅ΡΠ°Π²Π½ΠΎΠ²Π΅ΡΠ½ΠΎΡΡΡ Π³ΠΎΡΠΎΠ²ΠΎΠ³ΠΎ ΠΌΠ΅ΡΠ°Π»Π»Π° (ΡΠΈΡΡΠ½ΠΎΠΊ 3.9);
— ΡΠ½ΠΈΠΆΠ΅Π½ΠΈΠ΅ ΠΊΠΎΠ½ΡΠ΅Π½ΡΡΠ°ΡΠΈΠΈ ΡΠ³Π»Π΅ΡΠΎΠ΄Π° Π² ΠΏΠΎΠ»ΡΠΏΡΠΎΠ΄ΡΠΊΡΠ΅ ΠΏΠΎ ΠΏΡΠΈΡ ΠΎΠ΄Ρ Π½Π° ΠΠΠ ΠΈ, ΡΠΎΠΎΡΠ²Π΅ΡΡΡΠ²Π΅Π½Π½ΠΎ, Π²ΠΎΠ·ΡΠ°ΡΡΠ°Π½ΠΈΠ΅ Π²Π΅Π»ΠΈΡΠΈΠ½Ρ ΠΏΡΠΈΡΠ°Π΄ΠΎΠΊ ΡΠ³Π»Π΅ΡΠΎΠ΄ΡΠΎΠ΄Π΅ΡΠΆΠ°ΡΠΈΡ ΠΌΠ°ΡΠ΅ΡΠΈΠ°Π»ΠΎΠ² ΡΠ°ΠΊΠΆΠ΅ ΡΠΏΠΎΡΠΎΠ±ΡΡΠ²ΡΡΡ Π²ΠΎΠ·ΡΠ°ΡΡΠ°Π½ΠΈΡ Π½Π΅ΡΠ°Π²Π½ΠΎΠ²Π΅ΡΠ½ΠΎΡΡΠΈ ΡΠ°ΡΠΏΠ»Π°Π²Π° (ΡΠΈΡΡΠ½ΠΎΠΊ 3.9). ΠΡΠΎ, Π² ΡΠ²ΠΎΡ ΠΎΡΠ΅ΡΠ΅Π΄Ρ, ΠΏΡΠ΅Π΄ΠΎΠΏΡΠ΅Π΄Π΅Π»ΡΠ΅Ρ ΡΠ½ΠΈΠΆΠ΅Π½ΠΈΠ΅ ΠΏΠ»Π°ΡΡΠΈΡΠ½ΠΎΡΡΠΈ ΠΌΠ΅ΡΠ°Π»Π»Π° ΡΡΡΠ± (ΠΌΠ΅Π½ΡΡΠ΅Π΅ ΡΠΈΡΠ»ΠΎ ΡΠΎΡΠ΅ΠΊ ΡΠ²ΡΠ·Π°Π½ΠΎ Ρ ΡΠ΅ΠΌ, ΡΡΠΎ ΡΠ°ΡΡΡ ΠΈΡΡΠ»Π΅Π΄ΠΎΠ²Π°Π½Π½ΡΡ ΠΏΠ»Π°Π²ΠΎΠΊ ΡΠ°Π·Π»ΠΈΠ²Π°Π»Π°ΡΡ Π² Π·Π°Π³ΠΎΡΠΎΠ²ΠΊΠΈ ΡΠ΅ΡΠ΅Π½ΠΈΠ΅ΠΌ Π¨ 156 ΠΌΠΌ);
— Ρ ΡΠΎΡΠΊΠΈ Π·ΡΠ΅Π½ΠΈΡ Π²Π»ΠΈΡΠ½ΠΈΡ Π½Π° ΡΠ°Π²Π½ΠΎΠ²Π΅ΡΠ½ΠΎΡΡΡ ΡΠ°ΡΠΏΠ»Π°Π²Π° Π±ΠΎΠ»ΡΡΠΎΠ΅ Π·Π½Π°ΡΠ΅Π½ΠΈΠ΅ ΠΈΠΌΠ΅Π΅Ρ Π½Π΅ ΡΠΎΠ»ΡΠΊΠΎ Π²Π΅Π»ΠΈΡΠΈΠ½Π° ΠΊΠΎΡΡΠ΅ΠΊΡΠΈΡΠΎΠ²ΠΎΠΊ Ρ ΠΈΠΌΠΈΡΠ΅ΡΠΊΠΎΠ³ΠΎ ΡΠΎΡΡΠ°Π²Π°, Π½ΠΎ ΠΈ Π²ΡΠ΅ΠΌΡ Π²Π²ΠΎΠ΄Π° Π΄ΠΎΠ±Π°Π²ΠΎΠΊ ΠΏΠΎ Ρ ΠΎΠ΄Ρ ΠΎΠ±ΡΠ°Π±ΠΎΡΠΊΠΈ Π½Π° ΠΠΠ. Π‘ΠΌΠ΅ΡΠ΅Π½ΠΈΠ΅ ΠΊΠΎΡΡΠ΅ΠΊΡΠΈΡΠΎΠ²ΠΎΠΊ Ρ ΠΈΠΌΠΈΡΠ΅ΡΠΊΠΎΠ³ΠΎ ΡΠΎΡΡΠ°Π²Π° Π½Π° Π±ΠΎΠ»Π΅Π΅ ΡΠ°Π½Π½ΠΈΠ΅ ΡΡΠ°ΠΏΡ ΠΎΠ±ΡΠ°Π±ΠΎΡΠΊΠΈ ΠΏΠΎΠ²ΡΡΠ°Π΅Ρ ΡΠ°Π²Π½ΠΎΠ²Π΅ΡΠ½ΠΎΡΡΡ ΠΌΠ΅ΡΠ°Π»Π»Π°. ΠΡΠ΅Π΄ΡΡΠ°Π²Π»Π΅Π½Π½ΡΠ΅ Π΄Π°Π½Π½ΡΠ΅ ΡΠ²ΠΈΠ΄Π΅ΡΠ΅Π»ΡΡΡΠ²ΡΡΡ ΠΎ Π±ΠΎΠ»Π΅Π΅ ΡΠ΅ΡΠ½ΠΎΠΉ Π²Π·Π°ΠΈΠΌΠΎΡΠ²ΡΠ·ΠΈ ΡΠ°ΡΡΠΌΠ°ΡΡΠΈΠ²Π°Π΅ΠΌΠΎΠ³ΠΎ ΡΠ΅Ρ Π½ΠΎΠ»ΠΎΠ³ΠΈΡΠ΅ΡΠΊΠΎΠ³ΠΎ ΠΏΠ°ΡΠ°ΠΌΠ΅ΡΡΠ° ΠΈ ΡΠ°Π²Π½ΠΎΠ²Π΅ΡΠ½ΠΎΡΡΠΈ Π΄Π»Ρ ΡΡΠ°Π»ΠΈ Π (ΡΠΈΡΡΠ½ΠΎΠΊ 3.10). ΠΠ»Ρ ΡΡΠ°Π»ΠΈ 20ΠΠ’ Π²Π΅Π»ΠΈΡΠΈΠ½Π° ΠΊΠΎΡΡΠ΅Π»ΡΡΠΈΠΈ Π΄Π»Ρ Π²Π°ΠΊΡΡΠΌΠΈΡΠΎΠ²Π°Π½Π½ΡΡ ΠΏΠ»Π°Π²ΠΎΠΊ Π²ΡΡΠ΅, ΡΠ΅ΠΌ Π΄Π»Ρ Π½Π΅Π²Π°ΠΊΡΡΠΌΠΈΡΠΎΠ²Π°Π½Π½ΡΡ (ΡΠΈΡΡΠ½ΠΎΠΊ 3.11). Π ΡΠΎ ΠΆΠ΅ Π²ΡΠ΅ΠΌΡ Ρ ΡΠΎΡΠΊΠΈ Π·ΡΠ΅Π½ΠΈΡ Π²Π»ΠΈΡΠ½ΠΈΡ Π½Π° ΡΠ΄Π°ΡΠ½ΡΡ Π²ΡΠ·ΠΊΠΎΡΡΡ Π³ΠΎΡΠΎΠ²ΠΎΠ³ΠΎ ΠΌΠ΅ΡΠ°Π»Π»Π° Π½Π΅Π³Π°ΡΠΈΠ²Π½ΠΎΠ΅ Π²Π»ΠΈΡΠ½ΠΈΠ΅ ΡΠΌΠ΅ΡΠ΅Π½ΠΈΡ ΠΊΠΎΡΡΠ΅ΠΊΡΠΈΡΠΎΠ²ΠΎΠΊ Ρ ΠΈΠΌΠΈΡΠ΅ΡΠΊΠΎΠ³ΠΎ ΡΠΎΡΡΠ°Π²Π° Π½Π° Π±ΠΎΠ»Π΅Π΅ ΠΏΠΎΠ·Π΄Π½ΠΈΠ΅ ΡΡΠ°ΠΏΡ ΠΎΠ±ΡΠ°Π±ΠΎΡΠΊΠΈ ΠΎΡΠ΅Π²ΠΈΠ΄Π½ΠΎ:
— ΡΠ°Π·Π±ΡΠΎΡ ΡΠΎΡΠ΅ΠΊ ΠΌΠΎΠΆΠ΅Ρ Π±ΡΡΡ ΡΠ²ΡΠ·Π°Π½ Ρ ΠΌΠ½ΠΎΠ³ΠΎΡΠ°ΠΊΡΠΎΡΠ½ΠΎΠΉ Π·Π°Π²ΠΈΡΠΈΠΌΠΎΡΡΡΡ Π²ΡΠ΅ΠΌΠ΅Π½ΠΈ ΡΠ΅Π»Π°ΠΊΡΠ°ΡΠΈΠΈ ΠΎΡ ΡΠ΅Ρ Π½ΠΎΠ»ΠΎΠ³ΠΈΡΠ΅ΡΠΊΠΈΡ ΠΏΠ°ΡΠ°ΠΌΠ΅ΡΡΠΎΠ². Π ΡΠ°ΡΡΠ½ΠΎΡΡΠΈ, ΠΏΡΠΈ ΠΎΠ±ΡΠ΅ΠΌ ΠΏΠΎΠ»ΠΎΠΆΠΈΡΠ΅Π»ΡΠ½ΠΎΠΌ Π²Π»ΠΈΡΠ½ΠΈΠΈ Π½Π° ΠΏΡΠΎΠ΄ΠΎΠ»ΠΆΠΈΡΠ΅Π»ΡΠ½ΠΎΡΡΡ ΡΠ΅Π»Π°ΠΊΡΠ°ΡΠΈΠΈ Π½Π΅ΡΠ°Π²Π½ΠΎΠ²Π΅ΡΠ½ΠΎΡΡΠΈ ΡΠ²Π΅Π»ΠΈΡΠ΅Π½ΠΈΡ ΠΈΠ½ΡΠ΅Π½ΡΠΈΠ²Π½ΠΎΡΡΠΈ ΠΏΡΠΎΠ΄ΡΠ²ΠΊΠΈ ΠΈΠ½Π΅ΡΡΠ½ΡΠΌ Π³Π°Π·ΠΎΠΌ Π²Π·Π°ΠΈΠΌΠΎΡΠ²ΡΠ·Ρ Π±ΠΎΠ»Π΅Π΅ ΠΎΡΠ΅Π²ΠΈΠ΄Π½Π° Π΄Π»Ρ Π½Π΅Π²Π°ΠΊΡΡΠΌΠΈΡΠΎΠ²Π°Π½Π½ΡΡ ΠΏΠ»Π°Π²ΠΎΠΊ 20ΠΠ’ (ΡΠΈΡΡΠ½ΠΎΠΊ 3.12);
— Ρ ΡΠΎΡΠΊΠΈ Π·ΡΠ΅Π½ΠΈΡ ΡΠ΅ΠΆΠΈΠΌΠ° ΠΏΡΠΎΠ΄ΡΠ²ΠΊΠΈ ΠΏΠΎΠ»ΠΎΠΆΠΈΡΠ΅Π»ΡΠ½ΠΎ ΡΠΊΠ°Π·ΡΠ²Π°Π΅ΡΡΡ ΠΈ ΡΠ²Π΅Π»ΠΈΡΠ΅Π½ΠΈΠ΅ ΡΠ°ΡΡ ΠΎΠ΄Π° ΠΈΠ½Π΅ΡΡΠ½ΠΎΠ³ΠΎ Π³Π°Π·Π° (ΡΠΈΡΡΠ½ΠΎΠΊ 3.13). ΠΡΠΎ ΠΌΠΎΠΆΠ΅Ρ Π±ΡΡΡ ΡΠ²ΡΠ·Π°Π½ΠΎ Ρ Π²ΠΎΠ·ΡΠ°ΡΡΠ°Π½ΠΈΠ΅ΠΌ ΡΠ°Π²Π½ΠΎΠ²Π΅ΡΠ½ΠΎΡΡΠΈ ΡΠ°ΡΠΏΠ»Π°Π²Π° ΠΏΡΠΈ ΡΠ²Π΅Π»ΠΈΡΠ΅Π½ΠΈΠΈ ΠΏΡΠΎΠ΄ΠΎΠ»ΠΆΠΈΡΠ΅Π»ΡΠ½ΠΎΡΡΠΈ ΠΎΠ±ΡΠ°Π±ΠΎΡΠΊΠΈ Π½Π° ΠΠΠ (ΡΠΈΡΡΠ½ΠΎΠΊ 3.14).
Π ΠΈΡΡΠ½ΠΎΠΊ 3.9. ΠΠ»ΠΈΡΠ½ΠΈΠ΅ Π²Π΅Π»ΠΈΡΠΈΠ½Ρ ΠΏΡΠΈΡΠ°Π΄ΠΎΠΊ ΡΠ΅ΡΡΠΎΡΠΏΠ»Π°Π²ΠΎΠ² ΠΈ Π½Π°ΡΠ³Π»Π΅ΡΠΎΠΆΠΈΠ²Π°ΡΠ΅Π»Π΅ΠΉ ΠΏΠΎ Ρ ΠΎΠ΄Ρ ΠΎΠ±ΡΠ°Π±ΠΎΡΠΊΠΈ Π½Π° ΠΠΠ Π½Π° ΡΠ°Π²Π½ΠΎΠ²Π΅ΡΠ½ΠΎΡΡΡ ΠΈ ΡΠ²ΠΎΠΉΡΡΠ²Π° ΡΡΠ°Π»ΠΈ Π.
Π ΠΈΡΡΠ½ΠΎΠΊ 3.10. ΠΠ»ΠΈΡΠ½ΠΈΠ΅ Π²ΡΠ΅ΠΌΠ΅Π½ΠΈ Π²Π²ΠΎΠ΄Π° Π΄ΠΎΠ±Π°Π²ΠΎΠΊ ΠΏΠΎ Ρ ΠΎΠ΄Ρ ΠΎΠ±ΡΠ°Π±ΠΎΡΠΊΠΈ Π½Π° ΠΠΠ Π½Π° ΡΠ°Π²Π½ΠΎΠ²Π΅ΡΠ½ΠΎΡΡΡ ΡΡΠ°Π»ΠΈ Π Π ΠΈΡΡΠ½ΠΎΠΊ 3.11. ΠΠ»ΠΈΡΠ½ΠΈΠ΅ Π²ΡΠ΅ΠΌΠ΅Π½ΠΈ Π²Π²ΠΎΠ΄Π° Π΄ΠΎΠ±Π°Π²ΠΎΠΊ ΠΏΠΎ Ρ ΠΎΠ΄Ρ ΠΎΠ±ΡΠ°Π±ΠΎΡΠΊΠΈ Π½Π° ΠΠΠ Π½Π° ΡΠ°Π²Π½ΠΎΠ²Π΅ΡΠ½ΠΎΡΡΡ ΡΡΠ°Π»ΠΈ 20ΠΠ’ Π ΠΈΡΡΠ½ΠΎΠΊ 3.12. — ΠΠ»ΠΈΡΠ½ΠΈΠ΅ ΠΈΠ½ΡΠ΅Π½ΡΠΈΠ²Π½ΠΎΡΡΠΈ ΠΏΡΠΎΠ΄ΡΠ²ΠΊΠΈ ΠΈΠ½Π΅ΡΡΠ½ΡΠΌ Π³Π°Π·ΠΎΠΌ Π²ΠΎ Π²ΡΠ΅ΠΌΡ ΠΎΠ±ΡΠ°Π±ΠΎΡΠΊΠΈ Π½Π° ΠΠΠ Π½Π° ΡΠ°Π²Π½ΠΎΠ²Π΅ΡΠ½ΠΎΡΡΡ ΡΡΠ°Π»ΠΈ 20ΠΠ’ Π ΠΈΡΡΠ½ΠΎΠΊ 3.13. ΠΠ»ΠΈΡΠ½ΠΈΠ΅ ΡΠ°ΡΡ ΠΎΠ΄Π° ΠΈΠ½Π΅ΡΡΠ½ΠΎΠ³ΠΎ Π³Π°Π·Π° Π²ΠΎ Π²ΡΠ΅ΠΌΡ ΠΎΠ±ΡΠ°Π±ΠΎΡΠΊΠΈ Π½Π° ΠΠΠ Π½Π° ΡΠ°Π²Π½ΠΎΠ²Π΅ΡΠ½ΠΎΡΡΡ ΡΡΠ°Π»ΠΈ Π (Π°) ΠΈ 20ΠΠ’ (Π±) Π ΠΈΡΡΠ½ΠΎΠΊ 3.14. ΠΠ»ΠΈΡΠ½ΠΈΠ΅ ΠΏΡΠΎΠ΄ΠΎΠ»ΠΆΠΈΡΠ΅Π»ΡΠ½ΠΎΡΡΠΈ ΠΎΠ±ΡΠ°Π±ΠΎΡΠΊΠΈ Π½Π° ΠΠΠ Π½Π° ΡΠ°Π²Π½ΠΎΠ²Π΅ΡΠ½ΠΎΡΡΡ ΡΡΠ°Π»ΠΈ Π
Π’Π΅Ρ Π½ΠΎΠ»ΠΎΠ³ΠΈΡΠ΅ΡΠΊΠΈΠ΅ Π²ΠΎΠ·ΠΌΠΎΠΆΠ½ΠΎΡΡΠΈ ΠΏΠΎ ΡΠ²Π΅Π»ΠΈΡΠ΅Π½ΠΈΡ ΠΈΠ½ΡΠ΅Π½ΡΠΈΠ²Π½ΠΎΡΡΠΈ ΠΏΡΠΎΠ΄ΡΠ²ΠΊΠΈ ΠΈ ΠΏΡΠΎΠ΄ΠΎΠ»ΠΆΠΈΡΠ΅Π»ΡΠ½ΠΎΡΡΠΈ ΠΎΠ±ΡΠ°Π±ΠΎΡΠΊΠΈ ΠΎΠ³ΡΠ°Π½ΠΈΡΠ΅Π½Ρ. Π ΡΠ²ΡΠ·ΠΈ Ρ ΡΡΠΈΠΌ Π΄Π»Ρ ΠΈΠ½ΡΠ΅Π½ΡΠΈΡΠΈΠΊΠ°ΡΠΈΠΈ ΠΏΡΠΎΡΠ΅ΡΡΠΎΠ² ΡΠ΅Π»Π°ΠΊΡΠ°ΡΠΈΠΈ Π½Π΅ΡΠ°Π²Π½ΠΎΠ²Π΅ΡΠ½ΠΎΡΡΠΈ Π½Π΅ΠΎΠ±Ρ ΠΎΠ΄ΠΈΠΌΠΎ ΡΠΎΠ²Π΅ΡΡΠ΅Π½ΡΡΠ²ΠΎΠ²Π°Π½ΠΈΡ ΡΠΏΠΎΡΠΎΠ±ΠΎΠ² ΠΈ ΡΠ΅ΠΆΠΈΠΌΠΎΠ² ΠΏΡΠΎΠ΄ΡΠ²ΠΊΠΈ ΠΈΠ½Π΅ΡΡΠ½ΡΠΌ Π³Π°Π·ΠΎΠΌ Ρ ΡΠ΅Π»ΡΡ Π²ΠΎΠ·Π±ΡΠΆΠ΄Π΅Π½ΠΈΡ ΠΊΠ°Π²ΠΈΡΠ°ΡΠΈΠΎΠ½Π½ΡΡ ΠΏΡΠΎΡΠ΅ΡΡΠΎΠ² Π² ΠΌΠ΅ΡΠ°Π»Π»ΠΈΡΠ΅ΡΠΊΠΎΠΌ ΡΠ°ΡΠΏΠ»Π°Π²Π΅.
ΠΠ°ΠΊΠ»ΡΡΠ΅Π½ΠΈΠ΅
1) ΠΠ°Π»ΠΈΡΠΈΠ΅ Π² ΡΠ΅Ρ Π½ΠΎΠ»ΠΎΠ³ΠΈΡΠ΅ΡΠΊΠΎΠΉ ΡΡ Π΅ΠΌΠ΅ Π²Π½Π΅ΠΏΠ΅ΡΠ½ΠΎΠΉ ΠΎΠ±ΡΠ°Π±ΠΎΡΠΊΠΈ Π½Π΅ ΠΏΠΎΠ·Π²ΠΎΠ»ΡΠ΅Ρ Π½Π΅ΠΉΡΡΠ°Π»ΠΈΠ·ΠΎΠ²Π°ΡΡ ΠΏΠΎΠ»Π½ΠΎΡΡΡΡ Π½Π΅Π³Π°ΡΠΈΠ²Π½ΠΎΠ΅ Π²Π»ΠΈΡΠ½ΠΈΠ΅ ΠΏΠΎΠ²ΡΡΠ΅Π½Π½ΠΎΠΉ ΠΎΠΊΠΈΡΠ»Π΅Π½Π½ΠΎΡΡΠΈ ΠΏΠΎΠ»ΡΠΏΡΠΎΠ΄ΡΠΊΡΠ°. ΠΠ΄Π½Π°ΠΊΠΎ ΠΎΠΏΡΠΈΠΌΠΈΠ·Π°ΡΠΈΡ ΡΠ΅Ρ Π½ΠΎΠ»ΠΎΠ³ΠΈΡΠ΅ΡΠΊΠΈΡ ΠΏΠ°ΡΠ°ΠΌΠ΅ΡΡΠΎΠ² Π²Π½Π΅ΠΏΠ΅ΡΠ½ΠΎΠΉ ΠΎΠ±ΡΠ°Π±ΠΎΡΠΊΠΈ ΠΌΠΎΠΆΠ΅Ρ ΡΠΏΠΎΡΠΎΠ±ΡΡΠ²ΠΎΠ²Π°ΡΡ ΡΠ½ΠΈΠΆΠ΅Π½ΠΈΡ ΡΠΎΠ΄Π΅ΡΠΆΠ°Π½ΠΈΡ Π² ΠΌΠ΅ΡΠ°Π»Π»Π΅ ΠΎΠ±ΡΠ΅Π³ΠΎ ΠΊΠΈΡΠ»ΠΎΡΠΎΠ΄Π° ΠΈ ΠΏΠΎΠ²ΡΡΠ΅Π½ΠΈΡ ΠΊΠ°ΡΠ΅ΡΡΠ²Π° ΡΡΠ°Π»ΠΈ.
2) Π‘Π½ΠΈΠΆΠ΅Π½ΠΈΡ ΡΠΎΠ΄Π΅ΡΠΆΠ°Π½ΠΈΡ Π² ΠΌΠ΅ΡΠ°Π»Π»Π΅ ΠΎΠ±ΡΠ΅Π³ΠΎ ΠΊΠΈΡΠ»ΠΎΡΠΎΠ΄Π° ΡΠΏΠΎΡΠΎΠ±ΡΡΠ²ΡΡΡ:
Π°) ΠΎΠΏΡΠΈΠΌΠΈΠ·Π°ΡΠΈΡ ΡΠ΅ΠΆΠΈΠΌΠ° ΡΠ°ΡΠΊΠΈΡΠ»Π΅Π½ΠΈΡ ΠΏΡΡΠ΅ΠΌ
— ΠΎΠ³ΡΠ°Π½ΠΈΡΠ΅Π½ΠΈΠ΅ ΠΊΠΎΠ»ΠΈΡΠ΅ΡΡΠ²Π° Π°Π»ΡΠΌΠΈΠ½ΠΈΠ΅Π²ΠΎΠΉ ΠΊΠ°ΡΠ°Π½ΠΊΠΈ, ΠΎΡΠ΄Π°Π½Π½ΠΎΠΉ Π½Π° ΠΏΠ΅ΡΠΈ-ΠΊΠΎΠ²ΡΠ΅, Π²Π΅Π»ΠΈΡΠΈΠ½ΠΎΠΉ 30 ΠΊΠ³ (Π·Π° ΡΡΠ΅Ρ ΡΡΡΠ΅ΠΊΡΠΈΠ²Π½ΠΎΠ³ΠΎ ΡΠ°ΡΠΊΠΈΡΠ»Π΅Π½ΠΈΡ Π½Π° Π²ΡΠΏΡΡΠΊΠ΅ ΠΈΠ· ΠΠ‘Π ΠΈ ΠΏΠΎΠ»ΡΡΠ΅Π½ΠΈΡ Π² ΠΏΠ΅ΡΠ²ΠΎΠΉ ΠΏΡΠΎΠ±Π΅ Π½Π° ΠΠΠ ΡΠΎΠ΄Π΅ΡΠΆΠ°Π½ΠΈΡ Π°Π»ΡΠΌΠΈΠ½ΠΈΡ Π½Π΅ ΠΌΠ΅Π½Π΅Π΅ 0,015Ρ0,020%);
— ΠΎΠ³ΡΠ°Π½ΠΈΡΠ΅Π½ΠΈΠ΅ ΠΊΠΎΠ½ΡΠ΅Π½ΡΡΠ°ΡΠΈΠΈ Π°Π»ΡΠΌΠΈΠ½ΠΈΡ ΠΈ, ΡΠΎΠΎΡΠ²Π΅ΡΡΡΠ²Π΅Π½Π½ΠΎ, ΠΊΠ°Π»ΡΡΠΈΡ Π² Π³ΠΎΡΠΎΠ²ΠΎΠΌ ΠΌΠ΅ΡΠ°Π»Π»Π΅ ΠΌΠΈΠ½ΠΈΠΌΠ°Π»ΡΠ½ΠΎ Π½Π΅ΠΎΠ±Ρ ΠΎΠ΄ΠΈΠΌΡΠΌΠΈ ΠΏΡΠ΅Π΄Π΅Π»Π°ΠΌΠΈ.
Π±) ΡΠΎΠ²Π΅ΡΡΠ΅Π½ΡΡΠ²ΠΎΠ²Π°Π½ΠΈΠ΅ ΡΠΏΠΎΡΠΎΠ±ΠΎΠ² ΠΈ ΡΠ΅ΠΆΠΈΠΌΠΎΠ² ΠΏΡΠΎΠ΄ΡΠ²ΠΊΠΈ ΠΈΠ½Π΅ΡΡΠ½ΡΠΌ Π³Π°Π·ΠΎΠΌ Ρ ΡΠ΅Π»ΡΡ ΠΏΠΎΠ²ΡΡΠ΅Π½ΠΈΡ ΡΡΡΠ΅ΠΊΡΠΈΠ²Π½ΠΎΡΡΠΈ ΠΏΠ΅ΡΠ΅ΠΌΠ΅ΡΠΈΠ²Π°Π½ΠΈΡ ΠΌΠ΅ΡΠ°Π»Π»Π° Π² ΠΊΠΎΠ²ΡΠ΅.
3) ΠΠΎΠ²ΡΡΠ΅Π½ΠΈΠ΅ ΡΡΠ΅ΠΏΠ΅Π½ΠΈ Π½Π°Π³ΡΠ΅Π²Π° ΡΡΠ°Π»ΠΈ Π½Π° ΠΠΠ ΡΠ²Π΅Π»ΠΈΡΠΈΠ²Π°Π΅Ρ ΠΊΠΎΠ½ΡΠ΅Π½ΡΡΠ°ΡΠΈΡ Π² ΠΌΠ΅ΡΠ°Π»Π»Π΅ ΠΎΠ±ΡΠ΅Π³ΠΎ ΠΊΠΈΡΠ»ΠΎΡΠΎΠ΄Π°. Π¦Π΅Π»Π΅ΡΠΎΠΎΠ±ΡΠ°Π·Π½ΠΎ ΡΡΠΈΡΡΠ²Π°ΡΡ ΡΠ΅ΠΌΠΏΠ΅ΡΠ°ΡΡΡΠ½ΡΠΉ ΡΠ°ΠΊΡΠΎΡ ΠΏΡΠΈ ΠΎΠΏΡΠΈΠΌΠΈΠ·Π°ΡΠΈΠΈ ΡΠ΅ΠΆΠΈΠΌΠ° ΡΠ°ΡΠΊΠΈΡΠ»Π΅Π½ΠΈΡ.
4) Π₯Π°ΡΠ°ΠΊΡΠ΅Ρ Π²Π»ΠΈΡΠ½ΠΈΡ ΡΠ΅Ρ Π½ΠΎΠ»ΠΎΠ³ΠΈΡΠ΅ΡΠΊΠΈΡ ΠΏΠ°ΡΠ°ΠΌΠ΅ΡΡΠΎΠ² Π²Π½Π΅ΠΏΠ΅ΡΠ½ΠΎΠΉ ΠΎΠ±ΡΠ°Π±ΠΎΡΠΊΠΈ Π½Π° ΡΠ°Π²Π½ΠΎΠ²Π΅ΡΠ½ΠΎΡΡΡ ΠΌΠ΅ΡΠ°Π»Π»Π° ΠΈ ΡΠΊΡΠΏΠ»ΡΠ°ΡΠ°ΡΠΈΠΎΠ½Π½ΡΠ΅ ΡΠ²ΠΎΠΉΡΡΠ²Π° ΡΡΡΠ± Π² ΡΠ»ΡΡΠ°Π΅ ΠΎΠ±ΡΠ°Π±ΠΎΡΠΊΠΈ ΠΏΠΎΠ»ΡΠΏΡΠΎΠ΄ΡΠΊΡΠ°, ΠΏΠΎΠ»ΡΡΠ΅Π½Π½ΠΎΠ³ΠΎ Π² ΠΠ‘Π, Π² ΡΠ΅Π»ΠΎΠΌ ΡΠΎΠ²ΠΏΠ°Π΄Π°Π΅Ρ Ρ Π·Π°Π²ΠΈΡΠΈΠΌΠΎΡΡΡΠΌΠΈ, ΡΡΡΠ°Π½ΠΎΠ²Π»Π΅Π½Π½ΡΠΌΠΈ ΡΠ°Π½Π΅Π΅ ΠΏΡΠΈ ΠΎΠ±ΡΠ°Π±ΠΎΡΠΊΠ΅ ΠΌΠ°ΡΡΠ΅Π½ΠΎΠ²ΡΠΊΠΎΠ³ΠΎ ΠΏΠΎΠ»ΡΠΏΡΠΎΠ΄ΡΠΊΡΠ°.
5) ΠΠΎΠ·ΡΠ°ΡΡΠ°Π½ΠΈΡ ΡΠ°Π²Π½ΠΎΠ²Π΅ΡΠ½ΠΎΡΡΠΈ ΡΡΡΡΠΊΡΡΡΠ½ΠΎΠ³ΠΎ ΡΠΎΡΡΠΎΡΠ½ΠΈΡ ΠΌΠ΅ΡΠ°Π»Π»Π° ΠΈ, ΡΠΎΠΎΡΠ²Π΅ΡΡΡΠ²Π΅Π½Π½ΠΎ, ΠΏΠΎΠ²ΡΡΠ΅Π½ΠΈΡ ΡΡΠΎΠ²Π½Ρ ΠΈ ΡΡΠ°Π±ΠΈΠ»ΡΠ½ΠΎΡΡΠΈ ΡΠΊΡΠΏΠ»ΡΠ°ΡΠ°ΡΠΈΠΎΠ½Π½ΡΡ ΡΠ²ΠΎΠΉΡΡΠ² ΡΡΡΠ± ΡΠΏΠΎΡΠΎΠ±ΡΡΠ²ΡΡΡ:
— ΠΎΠΏΡΠΈΠΌΠΈΠ·Π°ΡΠΈΡ ΡΠ΅ΠΆΠΈΠΌΠ° ΡΠ°ΡΠΊΠΈΡΠ»Π΅Π½ΠΈΡ ΠΏΡΡΠ΅ΠΌ ΡΠ΅ΡΠ΅Π½ΠΈΡ Π·Π°Π΄Π°ΡΠΈ ΠΏΠΎ ΡΠ°ΡΠΈΠ½ΠΈΡΠΎΠ²Π°Π½ΠΈΡ ΠΎΡ ΠΊΠΈΡΠ»ΠΎΡΠΎΠ΄Π° Π½Π° Π²ΡΠΏΡΡΠΊΠ΅ ΠΈΠ· ΠΠ‘Π;
— ΡΠ½ΠΈΠΆΠ΅Π½ΠΈΠ΅ Π²Π΅Π»ΠΈΡΠΈΠ½Ρ ΠΊΠΎΡΡΠ΅ΠΊΡΠΈΡΠΎΠ²ΠΎΠΊ Ρ ΠΈΠΌΠΈΡΠ΅ΡΠΊΠΎΠ³ΠΎ ΡΠΎΡΡΠ°Π²Π° ΠΏΠΎ Ρ ΠΎΠ΄Ρ ΠΎΠ±ΡΠ°Π±ΠΎΡΠΊΠΈ Π½Π° ΠΠΠ;
— ΡΠΌΠ΅ΡΠ΅Π½ΠΈΠ΅ Π²ΡΠ΅ΠΌΠ΅Π½ΠΈ ΠΊΠΎΡΡΠ΅ΠΊΡΠΈΡΡΡΡΠΈΡ Π΄ΠΎΠ±Π°Π²ΠΎΠΊ Π½Π° Π½Π°ΡΠ°Π»ΡΠ½ΡΠ΅ ΠΏΠ΅ΡΠΈΠΎΠ΄Ρ ΠΎΠ±ΡΠ°Π±ΠΎΡΠΊΠΈ;
— ΡΠΎΠ²Π΅ΡΡΠ΅Π½ΡΡΠ²ΠΎΠ²Π°Π½ΠΈΠ΅ ΡΠΏΠΎΡΠΎΠ±ΠΎΠ² ΠΈ ΡΠ΅ΠΆΠΈΠΌΠΎΠ² ΠΏΡΠΎΠ΄ΡΠ²ΠΊΠΈ ΠΈΠ½Π΅ΡΡΠ½ΡΠΌ Π³Π°Π·ΠΎΠΌ Ρ ΡΠ΅Π»ΡΡ ΡΡΠΈΠΌΡΠ»ΠΈΡΠΎΠ²Π°Π½ΠΈΡ ΡΠ°Π·Π²ΠΈΡΠΈΡ ΠΏΡΠΎΡΠ΅ΡΡΠΎΠ² ΠΊΠ°Π²ΠΈΡΠ°ΡΠΈΠΈ Π² ΠΌΠ΅ΡΠ°Π»Π»ΠΈΡΠ΅ΡΠΊΠΎΠΌ ΡΠ°ΡΠΏΠ»Π°Π²Π΅.
ΠΠΈΠ±Π»ΠΈΠΎΠ³ΡΠ°ΡΠΈΡΠ΅ΡΠΊΠΈΠΉ ΡΠΏΠΈΡΠΎΠΊ
1.ΠΠ°ΠΊΠΎΠ½ΠΎΠΌΠ΅ΡΠ½ΠΎΡΡΠΈ ΡΠΎΡΠΌΠΈΡΠΎΠ²Π°Π½ΠΈΡ ΡΠ°ΡΠΏΠ»Π°Π²ΠΎΠ² Π½Π° ΠΎΡΠ½ΠΎΠ²Π΅ ΠΆΠ΅Π»Π΅Π·Π° ΠΈ ΠΌΠ΅ΡΠ°Π»Π»ΡΡΠ³ΠΈΡΠ΅ΡΠΊΠΈΠ΅ ΡΠ΅Π·Π΅ΡΠ²Ρ ΡΠ»ΡΡΡΠ΅Π½ΠΈΡ ΡΠΊΡΠΏΠ»ΡΠ°ΡΠ°ΡΠΈΠΎΠ½Π½ΡΡ ΡΠ²ΠΎΠΉΡΡΠ² ΡΡΠ°Π»Π΅ΠΉ / ΠΡΡΠΌΠ°ΡΠΎΠ² Π‘. Π., ΠΡΠ΄ΠΎΠ² Π. Π., ΠΠ΅Π³Π°ΠΉ Π. Π‘. Π‘ΡΠ΅ΠΏΠ°Π½ΠΎΠ² Π.Π., Π‘ΠΌΠΈΡΠ½ΠΎΠ² Π. Π. //Π‘ΡΠ°Π»Ρ, 2010. № 8. Π‘. 42−46.
2.ΠΠ΅ΡΠ°Π²Π½ΠΎΠ²Π΅Π½ΠΎΡΡΡ ΠΆΠΈΠ΄ΠΊΠΎΠ³ΠΎ ΠΌΠ΅ΡΠ°Π»Π»Π° ΠΈ ΠΊΠ°ΡΠ΅ΡΡΠ²ΠΎ ΡΡΠ°Π»ΠΈ / ΠΡΡΠΌΠ°ΡΠΎΠ² Π‘. Π., ΠΡΠ΄ΠΎΠ² Π. Π., Π‘ΡΠ΅ΠΏΠ°Π³ΠΎΠ² Π. Π., ΠΡΡΠ·ΠΈΠ½ Π. Π., ΠΠ°ΡΠΏΠΎΠ² Π. Π., ΠΡΠ΅Π² Π. Π., Π‘ΠΌΠΈΡΠ½ΠΎΠ² Π. Π. // ΠΠΎΠ²ΡΠ΅ ΡΠ΅Ρ Π½ΠΎΠ»ΠΎΠ³ΠΈΠΈ ΠΈ ΠΌΠ°ΡΠ΅ΡΠΈΠ°Π»Ρ Π² ΠΌΠ΅ΡΠ°Π»Π»ΡΡΠ³ΠΈΠΈ: Π‘Π±. Π½Π°ΡΡΠ½. Π’Ρ. ΠΠΊΠ°ΡΠ΅ΡΠΈΠ½Π±ΡΡΠ³: Π£ΡΠ Π ΠΠ, 2010. Π‘. 242−260.
3.ΠΡΡΠ»Π΅Π΄ΠΎΠ²Π°Π½ΠΈΠ΅ ΠΎΠΊΠΈΡΠ»Π΅Π½Π½ΠΎΡΡΠΈ ΠΏΠΎΠ»ΡΠΏΡΠΎΠ΄ΡΠΊΡΠ° ΠΈ ΠΊΠ°ΡΠ΅ΡΡΠ²Π° ΠΌΠ΅ΡΠ°Π»Π»Π° ΠΏΡΠΈ ΠΏΡΠΎΠΈΠ·Π²ΠΎΠ΄ΡΡΠ²Π΅ ΡΡΡΠ±Π½ΡΡ ΡΡΠ°Π»Π΅ΠΉ ΡΠΎΠ²ΡΠ΅ΠΌΠ΅Π½Π½ΡΠΌ Π΄ΡΠ³ΠΎΠ²ΡΠΌ ΠΏΡΠΎΡΠ΅ΡΡΠΎΠΌ / Π. Π. ΠΡΠ΅Π², Π‘. Π. ΠΡΡΠΌΠ°ΡΠΎΠ², Π. Π. ΠΡΡΠ·ΠΈΠ½, Π. Π. Π‘ΡΠ΅ΠΏΠ°Π½ΠΎΠ², Π. Π. ΠΡΠ΄ΠΎΠ², Π. Π. ΠΠΈΡΠ»ΡΡ ΠΈΠ½, Π. Π. Π£ΡΠ°ΠΊΠΎΠ², Π. Π. ΠΡΠ·Π°ΠΊΠΎΠ²Π° //Π’Ρ. ΠΠ΄ΠΈΠ½Π½Π°Π΄ΡΠ°ΡΠΎΠ³ΠΎ ΠΊΠΎΠ½Π³ΡΠ΅ΡΡΠ° ΡΡΠ°Π»Π΅ΠΏΠ»Π°Π²ΠΈΠ»ΡΡΠΈΠΊΠΎΠ². Π., 2010.