Очистка сточных вод от взвешенных частиц фильтрованием
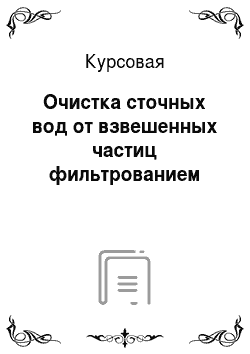
Любой существующий фильтр непрерывного действия отличается тем, что каждый элементарный участок его поверхности фильтрования непрерывно перемещается по замкнутой кривой, причем на этом участке последовательно осуществляются различные операции: разделение суспензии, промывка, обезвоживание, сушка и удаление осадка, промывка фильтровальной перегородки. Можно считать, что такой фильтр состоит… Читать ещё >
Очистка сточных вод от взвешенных частиц фильтрованием (реферат, курсовая, диплом, контрольная)
Министерство образования и науки Российской Федерации Федеральное государственное бюджетное образовательное учреждение высшего профессионального образования
«Тульский государственный университет»
Кафедра «Аэрологии, охраны труда и окружающей среды»
Курсовая работа
по дисциплине: Техника защиты окружающей среды
на тему: «Очистка сточных вод от взвешенных частиц фильтрованием»
Вариант 23
Выполнил:
Проверил
Тула 2013
- Введение
- 1. Основа процесса
- 2. Основные расчетные формулы и зависимости
- 3. Оборудование
- 4. Современные аппараты
- 5. Пример реализации метода
- Список литературы
- Введение
- Природа представляет собой целостную систему с множеством сбалансированных связей. Стабильное состояние биосферы, включая атмосферу, гидросферу и литосферу, достигается за счет непрерывного круговорота веществ и энергии. Однако рост населения, развитие промышленности и сельского хозяйства привели к резкому увеличению антропогенной нагрузки и серьезным нарушениям природного круговорота, особенно в водоемах. Проблема сохранения водоемов стала одной из важнейших задач.
- Вода — самое распространенное неорганическое соединение на нашей планете. Это ценнейший природный ресурс. Она играет исключительно важную роль в процессах обмена веществ и в жизни общества. Вода используется для питья, городского, промышленного и сельскохозяйственного водоснабжения, без нее немыслима жизнь обитающих в воде живых организмов, а также отдых людей.
- Во многих случаях возможность использования воды для тех или иных целей ограничивается её качеством. Все возрастающее загрязнение водоемов обусловлено сбросом неочищенных или недостаточно очищенных сточных вод, а также поступлением в водные объекты поверхностных стоков. настоящее время очистка сточных вод является основной мерой снижения загрязнения водных объектов и остаётся, в большинстве случаев, затратной технологией (затраты на очистку стоков достигают 20% себестоимости продукций промышленного предприятия). Эффективность большинства существующих очистных сооружений недостаточна. Процессы деградации водоемов продолжаются и могут стать практически необратимыми. Актуальность проблемы очистки воды ни у кого не вызывает сомнения.
- Методы очистки сточных вод делятся на четыре группы: механические, физико-химические, химические и биологические. Механическая очисткаэто удаление примесей из воды за счет гравитационных сил (отстаивание), центробежных сил (центрифугирование, очистка в гидроциклонах), а также путем механического задержания на решетках и ситах (процеживание), фильтрах (фильтрование). Механическая очистка позволяет удалить из воды крупные примеси и взвешенные частицы. Она часто применяется как первая ступень обработки сточных вод, для доочистки от взвешенных веществ, а также входит в состав систем физико-химической, химической и биологической очистки. Механические методы широко используются для уплотнения и обезвоживания осадков, образующихся при очистке сточных вод.
- Одним из наиболее распространённых на сегодняшний день вариантов водоочистки жидкости для промышленного и хозяйственного использования, является механическая очистка сточных вод. Она производится в целях удаления из производственных сточных вод, не растворенных примесей. Основными методами механической очистки являются: фильтрование, осаждение и флотация стоков. Тот или иной способ механической очистки применяют в зависимости от свойств примесей и необходимой полноты их выделения.
- 1. Основа процесса
- Фильтрование применяют в промышленности для тонкого разделения жидких и газовых гетерогенных систем. С его помощью можно добиться более полной, чем в процессах осаждения, очистки жидкости или газа от взвешенных частиц (обуславливают мутность воды) и более высокого выхода продукта.
- В процессе фильтрования твердые частицы задерживаются на поверхности фильтрующей перегородки, образуя осадок, либо проникают в глубину фильтрующей перегородки, задерживаясь в порах.
- Сущность метода заключается в пропуске жидкости через фильтрующий материал, проницаемый для жидкости и непроницаемый для гетерогенных примесей. Движущей силой процесса является разность давлений до и после фильтрующей перегородки. Фильтрование осуществляется либо в режиме постоянной разности давлений (например, вакуум-фильтры), либо в режиме постоянной скорости (например, рамный фильтр-пресс).
Классификация процессов фильтрования
Классификация процессов фильтрования может быть основана на различии технических задач, которые ставят при разделении суспензий, или на различии способов, которыми достигался поставленная цель.
При разделении суспензий можно поставить следующие технические задачи:
— выделение из суспензии ценной твердой фазы, когда жидкая фаза представляет отход;
— отделение ценной жидкой фазы суспензии от содержащейся в ней твердой фазы, когда последняя представляет отход;
— одновременное получение ценных твердой и жидкой фаз суспензии.
В процессе фильтрования твердые частицы либо задерживаются на поверхности фильтровальной перегородки, образуя осадок (фильтрование с образованием осадка), либо проникают в её глубину, задерживаясь в порах (фильтрование с закупориванием пор).
Разделение суспензий может производиться разными способами;
1.Фильтрование с образованием на поверхности фильтровальной перегородки осадка, представляющего собой твердую фазу суспензии.
2. Фильтрование с закупориванием пор фильтровальной перегородки твердой фазой суспензии.
3. Фильтрование с образованием на поверхности фильтровальной перегородки осадка, состоящего из вспомогательного вещества и твердой фазы суспензии.
4. Фильтрование с частичным разделением и сгущением суспензии.
Выбор способа разделения суспензии определяется различными условиями проведения процесса, в особенности концентрацией суспензии.
Фильтрование с образованием на поверхности фильтровальной перегородки осадка, состоящего из твердой фазы суспензии.
Этот способ наиболее распространен в промышленности и отличается необходимостью периодически удалять с фильтровальной перегородки слой осадка. Перед удалением осадок часто промывают жидкостью (например, водой) для извлечения из пор фильтрата: промытый осадок нередко продувают газом (например, воздухом) для вытеснения из его пор промывной жидкости.
Полученный в начальный момент фильтрования тонкий слой осадка предотвращает в дальнейшем проникание в поры перегородки тонкодисперсных твердых частиц. Поэтому проницаемость фильтровальной перегородки по отношению к жидкой фазе суспензии уменьшается не очень быстро и обычно частично восстанавливается после ее промывки.
Среди многочисленных примеров фильтрования по этому способу можно указать на разделение суспензий бикарбоната натрия в производстве соды, литопона в производстве красок, в-нафтола в производстве полупродуктов для красителей, твердых парафиновых углеводородов при рафинировании нефтяных продуктов.
Фильтрование с закупориванием пор фильтровальной перегородки твердой фазой суспензии.
В данном случае процесс фильтрования протекает, как правило, довольно медленно, поскольку закупоривание пор перегородки происходит уже в начальной стадии процесса. При этом для поддержания достаточной производительности фильтра необходимо часто сменять или промывать фильтровальную перегородку. Промывка перегородки с успехом может быть выполнена лишь при условии, что твердые частицы, закупоривающие ее поры, растворяются в промывной жидкости. Для этого промывную жидкость (чаще всего воду) в зависимости от свойств твердых частиц предварительно нагревают, подкисляют или подщелачивают.
В качестве примеров процесса разделения суспензий с закупориванием нор фильтровальной перегородки следует отметить фильтрование различных соков и сиропов в пищевой промышленности, растворов целлюлозы в производстве искусственного волокна, а также минеральных масел при их очистке.
Фильтрование с образованием на поверхности фильтровальной перегородки осадка, состоящего из вспомогательного вещества и твердой фазы суспензии.
Суспензию предварительно сгущают отстаиванием или прибавляют к ней вспомогательное вещество для повышения концентрации твердых частиц. Вспомогательное веществ (например, диатомит, отбеливающая земля, асбест) прибавляете в количестве до 2% от веса суспензии и после фильтрования часто может быть регенерировано промывкой.
Для предотвращения закупоривания пор фильтровальной перегородки на нее также предварительно наносят слой вспомогательного вещества толщиной до 100 мм, через который затем фильтруют очищаемую жидкость, содержащую небольшое количество твердой фазы. При таком способе работы в первую очередь закупориваются поры в той части слоя вспомогательного вещества, которая в процессе фильтрования соприкасается с суспензией. В связи с этим указанную часть слоя периодически срезают ножевым устройством, которое при помощи специального механизма медленно перемещается к фильтровальной перегородке, уменьшая толщину слоя вспомогательного вещества.
Для предотвращения закупоривания пор фильтровальной перегородки и поддержания достаточной проницаемости осадка рекомендуют смешанный способ работы с вспомогательным веществом. Сначала приблизительно 1/5 часть общего количества вспомогательного вещества наносят на перегородку фильтрованием взвеси этого вещества в чистой жидкости, а затем оставшуюся часть вещества наносят в процессе разделения суспензии.
Фильтрование с частичным разделением и сгущением суспензии.
Суспензии сначала сгущают под действием силы тяжести в отстойниках или под действием разности давлении в сгустителях. Последние представляют собой фильтры, поверхность фильтрования которых в процессе работы постоянно погружена в сгущаемую суспензии), причем цикл их работы состоит из стадии фильтрования с образованием осадка и стадии его удаления с фильтровальной перегородки обратным потоком фильтрата. При этом объем фильтрата, полученного в стадии фильтрования, должен быть больше объема фильтрата, возвращаемого в сгущаемую суспензию в стадии удаления осадка. Это позволяет получить в нижней части сгустителя такую смесь осадка и фильтрата, в которой концентрация твердых частиц больше, чем в исходной суспензии. Использование обратного потока фильтрата дает возможность удалять с фильтровальной перегородки тонкий слой осадка и поддерживать относительно высокую среднюю скорость фильтрования, а также обеспечивает достаточно хорошую промывку фильтровальной перегородки.
Сгущение суспензии применяется, например, в производстве сахара при обработке соков после сатурации.
Фильтрование в основном используется для жидкости, загрязнённой тяжёлыми взвешенными веществами. Применение этого метода возможно в двух альтернативных формах:
1. Фильтрация под воздействием силы тяжести. В этом случае осуществляется простое отстаивание жидкости, в результате которого тяжёлые загрязняющие вещества отслаиваются и остаются на дне отстойника.
2. Фильтрация под воздействием центробежных сил. Однако сооружения для очистки сточных вод механическим способом путем осаждения могут очищать стоки лишь от более или менее крупных частиц, имеющих размеры в пределах нескольких миллиметров. В таком случае проводят многоступенчатое очищение, сущность которого заключается в том, что частично очищенная жидкость после первой обработки поступает на следующий этап восстановления своих свойств, и так раз за разом, пока вода не достигнет совершенной чистоты в соответствии с установленными нормами.
В зависимости от способа достижения разности давлений можно осуществлять различные режимы фильтрования:
— при постоянной разности давлений и уменьшающейся скорости процесса; - при постоянной скорости процесса и возрастающей разности давлений; - при переменных разности давлений и скорости процесса.
В первом случае постоянная разность давлений обеспечивается присоединением фильтра к ресиверу, в котором поддерживается постоянное разрежение или избыточное давление; во втором случае постоянная скорость процесса обеспечивается подачей суспензии на фильтр поршневым насосом; в третьем случае изменение разности давлений и скорости процесса обусловлено подачей суспензии на фильтр центробежным насосом, производительность которого изменяется с возрастанием сопротивления фильтра вследствие увеличения толщины осадка.
Фильтрование суспензий
Рис. 1. Фильтрование суспензий
В простейшем случае фильтр представляет собой сосуд, корпус которого разделен на две части фильтровальной перегородкой. Суспензию помещают в верхнюю часть сосуда. В разделенных частях сосуда создают разность давлений, под действием которой жидкость проходит через поры фильтровальной перегородки, образуя фильтрат. Твердые частицы задерживаются на поверхности перегородки, образуя осадок.
Осадки, образующиеся в процессе фильтрования, подразделяются на сжимаемые несжимаемые, в зависимости от того, уменьшается ли пористость осадка при увеличении разности давлений или остается практически постоянной. Уменьшение пористости сжимаемых осадков приводит к увеличению сопротивления потоку жидкой фазы. Поэтому фильтрование в данном случае обычно проводят под вакуумом или небольшом избыточном давлении.
Обычно процесс фильтрования не завершается разделением суспензии на фильтрат и осадок. Перед удалением осадка с фильтровальной перегородки его, как правило, подвергают промывке другими жидкостями для удаления остатков фильтрата и продувки холодным или нагретым газом для уменьшения влажности.
В зависимости от размера дисперсных частиц, химической агрессивности и вязкости жидкой суспензии на практике применяют фильтровальные перегородки из стеклянных, хлопчатобумажных, шерстяных тканей, металлических сеток и так далее.
Фильтровальные перегородки
Фильтровальные перегородки представляют собой самую существенную часть фильтра и от правильного выбора их во многом зависят производительность фильтровального оборудования и чистота получаемого фильтрата.
При выборе фильтровальных перегородок надлежит руководствоваться следующим основным правилом: фильтровальная перегородка должна обладать максимальным размером пор и одновременно обеспечивать получение достаточно чистого фильтрата.
В общем случае фильтровальная перегородка должна обладать следующими свойствами:
· хорошо задерживать твердые частицы суспензии; иметь небольшое гидравлическое сопротивление потоку фильтрата;
· легко отделяться от осадка; обладать устойчивостью к химическому воздействию разделяемых веществ; не набухать при соприкосновении с жидкой фазой суспензии и промывной жидкостью;
· иметь достаточную, механическую прочность;
· обладать теплостойкостью при температуре фильтрования.
Известно большое число разнообразных по свойствам фильтровальных перегородок, изготавливаемых из неорганических и органических материалов. Все фильтровальные перегородки могут быть разделены на различные группы по нескольким признакам.
По принципу действия фильтровальные перегородки подразделяют на поверхностные и глубинные.
Поверхностные фильтровальные перегородки отличаются тем, что твердые частицы суспензии при ее разделении в основном задерживаются на их поверхности, не проникая в поры. К таким перегородкам относятся, в частности, фильтровальная бумага, ткани, металлические сетки.
Глубинные фильтровальные перегородки, которые используются преимущественно для осветления жидкостей, характеризуются тем, что твердые частицы суспензии в процессе ее разделения в основном проникают в поры и задерживаются там. Это происходит вследствие того что поры таких перегородок значительно больше частиц суспензии, а концентрация последних недостаточна для образования сводиков над входами в поры. При этом частицы суспензии задерживаются в порах в результате адсорбции, осаждения и застревания. Как правило, глубинные фильтровальные перегородки не могут задерживать все частицы суспензии; задерживающая способность их составляет 90—99%. К числу рассматриваемых перегородок относятся, например, слои вспомогательного вещества и песка.
Некоторые фильтровальные перегородки могут действовать как поверхностные так и глубинные в зависимости от размера пор и свойств суспензии (размер частиц, концентрация их, вязкость жидкой фазы).
Фильтровальные перегородки могут быть классифицированы по материалам, из которых они изготовлены, например, на перегородки из хлопчатобумажных, шерстяных, синтетических, стеклянных, керамических, металлических материалов. Такаяклассификация удобна при выборе фильтровальной перегородки с определенной способностью противостоять действию химически агрессивных веществ.
По структуре фильтровальные перегородки подразделяют на гибкие и негибкие. При этом гибкие перегородки могут быть металлическими и неметаллическими, а также состоять из смешанных материалов. Негибкие перегородки могут быть жесткими (состоящими из связанных твердых частиц) или нежесткими (состоящими из несвязанных твердых частиц).
Гибкие фильтровальные перегородки — тканые, трикотажные, сетчатые, нетканые и др. Тканые перегородки изготавливают из натуральных (хлопок, шерсть, шелк), искусственных (ацетаты целлюлозы, вискоза), синтетических (полиакрилонитрил, полиамиды, поливинил-хлорид, полиэфиры и др.), силикатных (асбест, стекло) и металлических (W, Mo, сплавы и т. д.) волокон и нитей.
Негибкие фильтровальные перегородки могут быть жесткими и нежесткими.
Жесткие (керамика и металлокерамика, пористые пластмассы и металлы и др.) выпускаются в виде цилиндров (патронов), плит, листов толщиной 0,2−50 мм и тончайших нитей (металлический войлок) и отличаются постоянством структуры при изменении давления, хорошей задерживающей способностью, грязеемкостью (от незначительной — керамика, до повышенной — пластмассовые патроны), эффективностью регенерации 70−100% (за исключением трудно регенерируемой керамики и нерегенерируемых патронов одноразового пользования).
Нежесткие фильтровальные перегородки бывают намывными (наиболее распространены) и насыпными (слои из песка, гравия, кокса, каменного угля и т. п., с толщиной загрузки до 1 м; регенерируются обратным током фильтрата).
Намывные перегородки — инертные тонкозернистые или волокнистые слои фильтровальных вспомогательных веществ. Намывные слои бывают одноразовыми и обновляемыми. В последнем случае, если при фильтровании происходят интенсивное закупоривание пор намывного слоя и образование на нем слоя осадка, фильтровальные вспомогательные вещества добавляют в суспензию. В результате увеличиваются пористость и проницаемость осадка. При этом дисперсность и количество вспомогательного вещества выбирают близкими соответствующим параметрам механических примесей.
Ввиду очень большого разнообразия типов фильтровальных перегородок, конструкций фильтров, свойств суспензий и условий их разделения выбор наиболее подходящей фильтровальной перегородки весьма сложен, в связи с рядом требований, одновременное выполнение которых нельзя достигнуть выбором одной из имеющихся фильтровальных перегородок. Поэтому выбор нередко сводится к нахождению наиболее разумного компромисса между различными, взаимно противоречивыми требованиями, предъявляемыми к фильтровальной перегородке в данных условиях разделения суспензии.
2. Основные расчетные формулы и зависимости
1) При р=const объем фильтрата V, прошедшего через 1 м² фильтрующей поверхности за время t, и продолжительность фильтрования т связаны уравнением:
(1)
Где Сконстанта фильтрования, характеризующая гидравлическое сопротивление фильтрующей перегородки (ткани), м3/м2; К — константа фильтрования, учитывающая режим процесса фильтрования и физико-химические свойства осадка и жидкости м2/с; ф — продолжительность фильтрования, с. Константы К. и С определяются опытным путем.
2) Скорость фильтрования [в м3/(м2-с)] определяется по уравнению:
(2)
3) Константа фильтрования К (в м2/с), отнесенная к 1 м² фильтрующей поверхности, при Дp = const
(3)
где Дp — перепад давлений на фильтре, Па; µ - динамический коэффициент вязкости фильтрата, Па-с; r — удельное сопротивление осадка (в расчете на 1 кг содержащегося в нем твердого сухого вещества), м/кг; с — масса сухого твердого вещества, отлагающегося па фильтре при прохождении через фильтрующую поверхность 1 м³ фильтрата, кг/м3.
4) Величина C (в кг/м3) может быть выражена через концентрацию фильтруемой суспензии x следующим образом:
(4)
где р — плотность фильтрата, кг/м3; х — массовая концентрация твердой фазы в суспензии, кг/кг; m — масса влажного осадка в расчете на 1 кг содержащегося в нем сухого вещества, кг/кг. При подстановке значения с в уравнение (3) получаем следующую формулу для константы К (в м2/с):
(5)
Если известна константа фильтрования K, то удельное сопротивление осадка r может быть найдено из уравнения (3), решенного относительно r (м/кг сухого осадка):
(6)
5) Константа фильтрования С (в м3/м2), характеризующая сопротивление фильтрующей перегородки (ткани) и отнесена к 1 м² поверхности фильтра, при р = const определяется следующим выражением
(7)
или в соответствии с уравнением (4):
(8)
где rтк — удельное сопротивление фильтрующей ткани (на 1 м² поверхности), м/м2; r — удельное сопротивление осадка, м/кг. Следовательно, если значение константы фильтрования С (в м3/м2) известно, то удельное сопротивление ткани может быть вычислено по формуле:
(9)
6) Количество сухого вещества G (в кг) в осадке, получаемом на фильтре, зависит от количества собранного фильтрата V, плотности фильтрата р, массовой доли твердой фазы в суспензии x влажности осадка (выражаемой массовым отношением т) и может быть вычислено по формуле:
(10)
7) Концентрация твердой фазы в суспензии х в зависимости от плотности суспензии рс выражается формулой:
(11)
Плотность суспензии:
(12)
В этих формулах х — массовая концентрация твердой фазы в суспензии, кг/кг; рс — плотность суспензии, кг/м3; р — плотность жидкой фазы, кг/м3; ртвплотность твердой фазы, кг/м3; n — масса жидкой фазы в суспензии на единицу массы твердой фазы (Т:Ж= 1: n).
По формуле (12) можно вычислить и плотность влажного осадка, рассматривая его как концентрированную суспензию.
3. Оборудование
Собственно фильтром является тонкая сетка с микроскопическими отверстиями. В качестве фильтрующего материала могут быть использованы кварцевый песок, дробленый гравий, коксовая мелочь, а также все виды газифицируемого твердого топлива (бурый уголь, торф, древесина). Выбор материала производится в зависимости от вида сточных вод и наличия фильтрующего материала.
Классификация фильтров
Одной из основных характеристик, используемых для классификации фильтров, является периодичность или непрерывность их действия, в связи с чем они подразделяются на фильтры периодического и непрерывного действия. Оба типа широко применяют в промышленности для процессов фильтрования с образованием осадка.
Непрерывный процесс соответствует установившемуся процессу, когда параметры вещества (температура, давление, состав) в каждой точке аппарата не изменяются с течением времени.
Любой существующий фильтр непрерывного действия отличается тем, что каждый элементарный участок его поверхности фильтрования непрерывно перемещается по замкнутой кривой, причем на этом участке последовательно осуществляются различные операции: разделение суспензии, промывка, обезвоживание, сушка и удаление осадка, промывка фильтровальной перегородки. Можно считать, что такой фильтр состоит из двух систем: одна из них включает неподвижные части (опорные приспособления, резервуар для суспензии, устройства для удаления осадка), а другая — движущиеся части (фильтровальная перегородка). При этом параметры вещества в каждой точке активного пространства фильтра постоянны только относительно первой системы, но переменны относительно второй. Так в любой момент времени в произвольной точке, выбранной вблизи поверхности фильтрования и неподвижной относительно первой системы; будут постоянны, например, давление и состав осадка; однако в аналогичной точке, неподвижной относительно второй системы, указанные величины будут изменяться по мере протекания отдельных стадии процесса.
Поэтому по отношению к фильтровальной перегородке процесс, осуществляемый на так называемых фильтрах непрерывного действия, является неустановившимся и по существу — периодическим.
В связи с приведенной выше классификацией процессов фильтрования отметим следующее:
— для проведения процессов разделения суспензий с образованием осадка, включая процессы с использованием вспомогательного вещества, применяют как фильтры периодического, так и фильтры непрерывного действия;
— для проведения процессов разделения суспензий с закупориванием пор фильтровальной перегородки используют, как правило, фильтры периодического действия;
— на фильтрах периодического действия осуществляют любой режим фильтрования;
— на фильтрах непрерывного действия практически осуществляют лишь режим фильтрования при постоянной разности давлений.
Фильтры можно классифицировать также следующим образом.
1. По способу создания разности давлений различают вакуум-фильтры (?р = 0,06−0,08 МПа) и фильтры, работающие под давлением (?р = 0,3−0,5 МПа). Последние наиболее целесообразно использовать, когда осадок малосжимаем, но обладает высоким гидравлическим сопротивлением. В других случаях вакуум-фильтры предпочтительнее, поскольку проще по конструкции.
2. По взаимному направлению силы тяжести и движения фильтрата различают фильтры с совпадающими (рис.2а), противоположными (б) и перпендикулярными (в) направлениями.
Кроме того, при классификации фильтров иногда следует учитывать их конструктивные особенности; форму и расположение, фильтровальной перегородки, а также зон для размещения суспензии, осадка и фильтрата; способ удаления осадка; наличие или отсутствие устройств для промывки, обезвоживания и сушки осадка.
Рассмотрим некоторые конструкции фильтров.
Барабанный вакуум-фильтр с устройством для снятия осадка шнурами (рис. 3). Бесконечные шнуры 1, имеющие сопротивление разрыву 300—400 нм, расположены параллельно один другому на расстоянии 6—25 мм. Они перемещаются по замкнутому пути вследствие трения о поверхность ткани на барабане, огибая натяжной ролик 2 и направляющий ролик, 3. При этом шнуры отделяются от ткани вместе с осадком, который затем снимается с них при огибании натяжного ролика. Между роликами 2 и 3 установлена направляющая гребенка 4, зубья которой обеспечивают сохранение нужного расстояния между соседними шнурами.
Рис. 3. Барабанный вакуум-фильтр с устройством для снятия осадка шнурами:
1 — бесконечные шнуры; 2 — натяжной ролик; 3 — направляющий ролик; 4 — направляющая гребенка; 5 — бесконечная промывная лента.
Фильтр снабжен бесконечной лентой 5, предназначенной для улучшения условий промывки и обезвоживания. При помощи шнуров удается снимать довольно липкие осадки толщиной 2—4 мм.
Рассмотренный фильтр по принципу действия является обычным ячейковым барабанным вакуум-фильтром и находит применение, в частности, в производстве литопона.
При работе с тяжелыми осадками небольшой прочности вместо шнуров используют плоские цепочки, расположенные близко одна от другой. Возможно также применение сеток, изготовленных из связанных между собою цепочек.
Опытами установлено, что толщина слоя осадка при снятии его шнурами, цепочками или сетками должна быть не менее толщины этих съемных приспособлений.
Барабанный вакуум-фильтр со сходящей фильтровальной тканью.
В этом фильтре по замкнутому пути перемещается бесконечная фильтровальная ткань, причем ее путь аналогичен замкнутому пути бесконечных шнуров в предыдущем фильтре.
На рис. 4 показан принцип действия фильтра, применяемого, в частности, в процессе обогащения минералов. Фильтровальная ткань или сетка 1 при движении по замкнутому пути последовательно встречает разгрузочный ролик 2, нож 3, промывной ролик 4; под которым размещается лоток 5 для удаления промывной жидкости, и направляющий ролик 6.
Рис. 4 Барабанный вакуум фильтр со сходящей фильтровальной тканью
1 — фильтровальная ткань или сетка; 2 — разгрузочный ролик; 3 -нож для съема осадка; 4 — промывной ролик; 5-лоток для удаления промывной жидкости; 6 — направляющий ролик; 7 — сопла для разбрызгивания промывочной жидкости
Вблизи промывного ролика на ткань или сетку направляются струи промывной жидкости, поступающей из сопел 7. При огибании тканью или сеткой разгрузочного ролика небольшого диаметра создаются благоприятные условия для отделения осадка от поверхности фильтровальной перегородки. Таким образом, особенностью рассмотренного фильтра является возможность не только осуществлять хорошую регенерацию фильтровальной перегородки, но и отделять от нее достаточно тонкие слои осадка (1—3 мм).
Для устранения смещения ткани в сторону или образования на ней складок при движении по замкнутому пути этот фильтр снабжают направляющими роликовыми устройствами.
Описанный фильтр получил распространение в промышленности и по имеющимся сведениям он изготавливается с поверхностью фильтрования до 140 мг (диаметр 6 м, длина 7,5 м).
Дисковые вакуум-фильтры
Эти фильтры имеют следующее устройство (рис. 5). Резервуар для суспензии состоит из секций 1; на вращающемся горизонтальном вале (на рисунке не виден) укреплены вертикальные фильтровальные диски 2, причем каждый диск находится в отдельной секции резервуара; распределительное устройство 3 снабжено трубопроводом 4 для соединения с источником вакуума и удаления фильтрата, а также трубопроводами 5 для подачи сжатого воздуха. В небольших дисковых фильтрах устанавливают одно распределительное устройство на одном из концов вала, а на более крупных — два на обоих концах вала. Отделение осадка от поверхности дисков облегчается благодаря наличию валиков или ножей 6, расположенных по обеим сторонам дисков. При помощи переливных трубок суспензия в секциях резервуара поддерживается на постоянном уровне так, что в нее погружена приблизительно половина каждого диска. Для предотвращения осаждения твердых частиц суспензия в секциях постоянно взмучивается мешалками маятникового типа.
Число дисков в фильтре достигает 14, а общая поверхность фильтрования изменяется от 1 до 300 м².
К достоинствам дисковых фильтров следует отнести значительную поверхность фильтрования, приходящуюся на единицу объема, который занимает аппарат. Недостатком дисковых фильтров является трудность промывки осадка.
Рис. 5 Дисковый вакуум-фильтр
1 — секции; 2 — фильтровальные диски; 3 — распределительное устройство; 4 — трубопровод для соединения с источником вакуума и удаления фильтрата; 5- трубопроводы для подачи сжатого воздуха; 6 — ножи для съема осадка
Дисковые фильтры в особенности пригодны для разделения суспензий, содержащих достаточно однородные и медленно осаждающиеся твердые частицы, которые образуют не растрескивающийся и не требующий промывки осадок.
Нутч-фильтры
Ниже рассматриваются фильтры с плоской фильтровальной перегородкой, которые по существу являются более или менее сложными модификациями простейшего фильтра, называемого нутчем.
Нутч представляет собой прямоугольный или круглый резервуар с плоским дном, над которым на некотором расстоянии имеется ложное дно, поддерживающее горизонтальную фильтровальную перегородку. Разделение суспензии, находящейся над фильтровальной перегородкой, происходит при разрежении, создаваемом в пространстве под ложным дном, или под давлением гидростатического столба суспензии, а разгрузка осадка из нутча производится вручную. Нутч в виде круглого резервуара с выпуклым дном и крышкой используется для разделения суспензии под действием избыточного давления, создаваемого в пространстве над суспензией.
Разгрузка осадка из опрокидывающегося прямоугольного нутча, предназначенного для работы под вакуумом, производится поворотом его при помощи штурвала вокруг горизонтальной оси на такой угол, чтобы осадок отделялся от поверхности фильтровальной перегородки и удалялся через край нутча под действием силы тяжести.
Разгрузка осадка из круглого нутча с откидным дном, предназначенного для работы под избыточным давлением, осуществляется откидыванием дна (шарнирно укрепленного в одном месте на корпусе) совместно с фильтровальной перегородкой; осадок удаляется под действием силы тяжести.
Разгрузка осадка из круглого нутча с поднимающейся мешалкой, предназначенного для работы под вакуумом, производится путем приливания к осадку воды, взмучивания в ней осадка при помощи медленно опускающейся вращающейся мешалки с гребками и удаления полученной суспензии через штуцер в боковой стенке нутча.
Описанные изменения в конструкции нутч-фильтра не разрешили проблему рационального удаления осадка; ручной труд полностью не исключен; увеличилась высота помещения в связи с устройством бункеров и поднимающихся мешалок; возможность удаления осадка в виде суспензии ограничена.
В настоящее время сохранили значение лишь небольшие нутчи, которые используются главным образом для лабораторных и полузаводских работ, а также для разделения суспензий в производствах малой мощности.
Нутч цилиндрической формы для работы под избыточным давлением до 3 атм показан на рис. 6. Он состоит из корпуса 1 с рубашкой 2, съемной крышки 3 и перемещающегося дна 6; фильтровальная перегородка 7, расположенная на опорной перегородке 4, представляет собой ткань или слой волокон; в последнем случае над фильтровальной перегородкой 7 помещают защитную сетку 8.
Над фильтровальной перегородкой находится кольцевая перегородка 12 высотой 150 мм, поддерживающая осадок во время его выгрузки. Обе перегородки укреплены в дне нутча, которое для разгрузки осадка опускается на 200 мм и поворачивается на такой угол, чтобы осадок можно было снять с фильтровальной перегородки вручную. Для подачи суспензии и сжатого воздуха служат штуцеры 9 и 10, для удаления фильтрата — штуцер 5, фильтр снабжен также предохранительным клапаном 11.
Рис. 6 Нутч, работающий под избыточным давлением до 3 атм
1 — корпус; 2 — рубашка; 3 -съемная крышка; 4 -опорная перегородка; 5 -штуцер для удаления фильтрата; 6 — перемещающееся дно; 7-фильтровальная перегородка; 8 — защитная сетка; 9 — штуцер для подачb суспензии; 10 — штуцер для подачи сжатого воздуха; 11-предохранительный клапан; 12 — кольцевая перегородка.
В простейшем случае цикл работы на таком нутче состоит из следующих операций: наполнение нутча суспензией, разделение суспензии под давлением сжатого газа, удаление осадка с фильтровальной — перегородки и ее регенерация.
Такие нутчи выпускают диаметром 22—100 см и емкостью 10—500 л. Они могут быть использованы, например, для разделения суспензий в химико-фармацевтической промышленности, а также для разделения шламов, полученных после экстракции растительных материалов и трудно разделяемых под вакуумом; передвижные нутчи, установленные на тележках, применяют для фильтрования фотографической эмульсии в производстве кинопленки.
Стремление использовать достоинства обычного нутча, в частности возможность осуществления на нем равномерной и многократной промывки, привело к созданию непрерывно действующих фильтров, состоящих из ряда нутчей, которые перемещаются по кругу в горизонтальной плоскости.
Основными достоинствами нутч-фильтров работающих под давлением являются простота и надежность в работе, возможность тщательной промывки осадка. К недостаткам относятся громоздкость, ручная выгрузка осадка, не герметичность.
Тарельчатые фильтры
Тарельчатые фильтры применяются для разделения хорошо фильтрующихся суспензий. Непрерывное кольцо из фильтровальных ячеек (рис.8) вращается вокруг вертикальной оси, причем его периферийная часть опирается на ролики, укрепленные на стойках, а внутренняя — на кольцевую тарелку, расположенную на шариковом подшипнике, также укрепленном на стойках.
Каждая фильтровальная ячейка 1 соединена трубками 2 с центральным распределительным устройством. Дно ячейки имеет наклон в сторону распределительного устройств, сверху она покрыта опорными и фильтровальной перегородками. Фильтр снабжен устройствами для подачи суспензии (на рисунке не показаны), устранения трещин в осадке, распределения промывной жидкости и удаления осадка.
При вращении против часовой стрелки на каждой ячейке последовательно осуществляются операции подачи суспензии и фильтрования, первой промывки, второй промывки, удаления осадка и очистки фильтровальной перегородки; при этом операции фильтрования и промывки обычно заканчиваются стадиями обезвоживания осадка. Во время фильтрования и промывки ячейки соединены с источником вакуума таким образом, что фильтрат, первая промывная жидкость и вторая промывная жидкость могут быть собраны в отдельные резервуары. При перемещении ячейки на участке между зонами разгрузки осадка и подачи суспензии внутрь ячейки подается сжатый воздух или пар, очищающий фильтровальную перегородку.
Тарельчатые фильтры применяются для разделения обычных суспензий, когда осадок требует многоступенчатой противоточной промывки, и для разделения суспензий, содержащих быстро осаждающиеся крупнодисперсные твердые частицы. В первом случае борт 6 фильтра делают небольшим, а для удаления осадка используют шнек или валец, к которому осадок прилипает; во втором случае высота борта достигает 0,5 м, а осадок удаляется скребком.
Рис. 8 Тарельчатый фильтр:
1 — фильтровальная ячейка; 2 — соединительная трубка; 3 — устройство для устранения трещин; 4 — устройство для распределения промывной жидкости; 5 — устройство для удаления осадка; 6 — борт.
Тарельчатые фильтры имеют диаметр 1,3—4,2 м при поверхности фильтрования 1—12 мг.
Основным недостатком тарельчатых фильтров является потребность в большой площади для их установки. Для устранения этого недостатка изготовляют двухтарельчатые и многотарельчатые фильтры.
Фильтры периодического действия
Патронные фильтры Служат для фильтрации и сгущения малоконцентрированных суспензий, в т. ч. из токсичных, пожарои взрывоопасных, а также агрессивных сред. Из-за неравномерности распределения осадка по высоте фильтровальных элементов скорость осаждения твердой фазы не должна превышать 2−5 мм/с. Степень обезвоживания осадка ограничена; промывка его невозможна. В герметичном горизонтальном цилиндрическом корпусе на приводном валу с несколько каналами закреплен несущий диск, на котором по окружности крепятся патроны либо перфорированные трубы с набором фильтрующих дисков (шайб). Патроны: 1) дренажные основания — пружины или перфорированной трубы круглого либо звездчатого сечения, снаружи с фильтровальной рукавной тканью, плотно навитой проволокой, нитью (бобина) или набором шайб; 2) пористые трубы из керамики, металлокерамики, пластмасс, прессованных волокнистых отходов с полимеризующейся пропиткой; 3) складчатые элементы из картона, полимерных мембран. В центре вдоль оси в корыте расположено разгрузочное устройство (ленточный транспортер, шнек). Суспензия через штуцер в нижней части крышки насосом подается под давлением 0,6−1,0 МПа в корпус фильтра и поддерживается на уровне оси или ниже. Фильтрующие элементы при вращении поочередно проходят зоны фильтрования, просушки воздухом и сброса осадка. Удаление осадка производится отдувкой сжатым воздухом, пневмогидравлическим ударом или с помощью вибрационных устройств.
Рис. Схема патронного фильтра
1 — корпус; 2 — фильтровальная перегородка; 3 — крышка; 4 — решётка; 5 — откидное днище.
Фильтр-прессы. Они относятся к фильтрам периодического действия, работающим под давлением. Направления сил тяжести и движения фильтрата в них перпендикулярны. Фильтр представляет собой сборку из чередующихся плит и рам, что существенно увеличивает рабочую поверхность фильтрующей перегородки. Плиты имеют вертикальные рифления, предотвращающие прилипание фильтровальной ткани к плитам и обеспечивающие дренаж фильтрата. Полая рама фильтр-пресса помещается между двумя плитами, образуя камеру для осадка. Отверстия в плитах и рамах совпадают, образуя каналы для прохода соответственно суспензии и промывной воды. Между плитами и рамами помешают фильтровальные перегородки («салфетки»). Отверстия в салфетках также совпадают с отверстиями в плитах. Сжатие плит и рам производится посредством винтового или гидравлического зажимов. На стадии фильтрования суспензия по каналу и отводам поступает в полое пространство (камеру) внутри рам. Жидкость проходит через фильтровальные перегородки, по желобкам рифлений движется к каналам и далее в каналы. Отсюда фильтрат выводится через краны, открытые на стадии фильтрования. После заполнения пространства (камеры) осадком подачу суспензии прекращают. Затем начинается стадия промывки осадка. Промывная жидкость проходит по каналам, омывает осадок и фильтровальные перегородки и выводится через краны. По окончании промывки осадок обычно продувают сжатым воздухом для удаления остатков промывной жидкости. После этого плиты и рамы раздвигают, и осадок частично падает под действием силы тяжести в сборник, установленный под фильтром. Оставшуюся часть осадка выгружают вручную.
Рис. 13. Фильтр-пресс аплита; б рама; в — сборка, 1-отверстия в плитах и рамах, образующие при сборке канал для подачи суспензии, 2 отверстия в плитах и рамах, образующие канал для подачи промывной жидкости, 3- отводы для прохода суспензии внутрь рам; 4-внутренние пространства рам; 5-фильтровальные перегородки; брифления плит, 7- каналы в плитах для выхода фильтрата на стадии фильтрования или промывной жидкости — на стадии промывки осадка, 8 -центральные каналы в плитах для сбора фильтрата или промывной жидкости; 9 -краны на линиях вывода фильтрата или промывной жидкости
К достоинствам фильтр-прессов относятся большая удельная поверхность фильтрования, возможность проведения процесса при высоких давлениях (до 1,5 М Па), простота конструкции, отсутствие частей, движущихся в процессе эксплуатации, возможность отключения отдельных неисправных плит закрытием выходного крана.
Недостатками являются ручное обслуживание, невозможность полной промывки осадка, быстрый износ фильтровальных салфеток из-за частой разборки фильтра и работы его при повышенных давлениях.
Ленточные фильтр-прессы Предназначены для обработки предварительно флокуллированных суспензий под действием гидростатического столба жидкости в питающей камере небольшого вакуума и в камере сбора получаемого фильтрата. Обработанный раствором флокулянта для улучшения водоотдающих свойств, осадок поступает в зону предварительного сгущения на верхней ленте фильтр-пресса. Здесь происходит гравитационное сгущение. Затем осадок зажимается между двумя перфорированными лентами и проходит через 12 или 14 валов уменьшающегося диаметра, что обеспечивает постепенное повышения давления на осадок.
Рис. 14.Ленточный фильтр-пресс
1,4 — камеры фильтрата; 2,3 — приводной и натяжной барабаны; 5 — нож; 6,7,9 — натяжные, направляющие и отжимные ролики; 8 — фильтровальные ленты.
Обезвоженный осадок с помощью скребка снимается с ленты и сбрасывается в устройство выгрузки. Фильтрат собирается в нижней части пресса в специальный лоток. Для промывки лент предусмотрены две линии промывки, которые с помощью форсунок непрерывно очищают ленты перед поступлением новой порции осадка. Цех обработки осадка стандартно комплектуется насосом подачи осадка, станцией приготовления раствора флокулянта с узлом дозирования, фильтр прессом (и, при необходимости, сгустителем), насосом промывной воды.
Достоинствами ленточного фильтр-пресса является высокая эффективность очистки сточных вод, низкая стоимость эксплуатационных расходов, безопасность и надежность автоматического управления.
4. Современные аппараты
Гейзер ТВТ
Система очистки воды любой степени загрязнения. Мобильный вариант установки «Гейзер-ТВТ» позволяет очищать воду из большинства поверхностных источников или артезианских скважин (умягчение и обезжелезивание воды).
В процессе переработки промышленных сточных вод уменьшается количество промывочных вод и отходов за счет того, что регенерация модуля проточного фильтрования происходит продувкой сжатым воздухом В процессе умягчения питьевой воды происходит отказ от регенерации солью и утилизации промывочных растворов (как в случае ионообменных смол) или уменьшение объема дренажных вод (как в случае обратного осмоса) При обработке природных вод с повышенной жесткостью изменение структуры солей жесткости, при котором на нагреваемых поверхностях не образуется накипь. Значительное снижение затраты промышленных предприятий на электроэнергию и расходные материалы Установка проточного фильтрования собирается по модульному принципу, причем количество модулей определяется требуемой производительностью.
Рис. 15 Модуль проточного фильтра
Модуль проточного фильтрования «Гейзер-ТВТ» представляет собой цилиндрический корпус определенных геометрических размеров с установленным в нем коаксиально фильтрующим патроном из уникального материала производства компании Гейзер — Арагон.
Работа модуля производится в автоматическом режиме. Воду подают в зазор между стенкой корпуса и патроном с определенной скоростью, часть потока, перемещаясь вдоль наружной стенки элемента, подвергается очистке за счет ионного обмена, происходящего в поверхностном слое фильтрующего элемента, подвергается дополнительной очистке в толще материала, просачивается через поры элемента и отводится в накопительную емкость. Другая часть потока устремляется вдоль фильтрующего элемента, смывая задержанные примеси и удаляя их из зоны фильтрации, возвращаясь в емкость с исходной водой, и снова подается на фильтрацию. Таким образом, часть воды постоянно расходуется на очистку фильтрующих элементов, т. е. происходит их постоянное самоочищение. Для снятия осадка, образовавшегося на наружной поверхности стенки фильтрующего патрона, модуль продувают воздухом под давлением 6 атм в течение — 5−10 сек с одновременным прекращением подачи воды. Осадок отстаивается в отдельной емкости, концентрируется и в дальнейшем может быть легко отделен с помощью нутч-фильтра. Таким образом, на выходе системы получается не промывочная вода в большом объеме (как при традиционных системах очистки), а влажный осадок гидроокиси железа, составляющий около 0,1% от массы обработанной воды.
Устройство фильтров с зернистыми загрузками
Рис. 16 Фильтр с зернистой загрузкой
http://geizer.com/userfiles/enlarge/xl_s-golovamy.jpgФильтры с зернистыми загрузками состоят из следующих основных элементов: корпус фильтра, блок управления, дренажно-распределительная система, гравийная подложка, фильтрующая загрузка. Корпус фильтра изготавливается, как правило, из стекловолокна и представляет собой полый цилиндр с сферическими верхом и дном. Для устойчивости корпуса на полу его нижняя часть помещается в специальное кольцевое основание. В верхней части корпуса имеется горловина, через которую осуществляется сборка и засыпка фильтра. В корпусах большого размера подобная горловина делается и снизу, чтобы облегчить выгрузку загрузки и обслуживание фильтра.
Блок управления представляет собой многоходовой клапан с электромеханическим приводом и необходимой автоматикой (возможен вариант с ручным переключением клапана). Назначение блока управления — переключение потока воды, идущей через фильтрующую загрузку для обеспечения её своевременной промывки (регенерации). Выпускаются блоки управления, позволяющие осуществлять промывку загрузки как в заданное пользователем время и день недели, так и по результатам измерения объёма воды, прошедший через фильтр. В зависимости от типа применяемой загрузки используются блоки управления, позволяющие промывать её только обратным током воды, или, дополнительно, химическими реактивами (NaCl, KMnO4), хранящимися в специальном баке рядом с фильтром.
В состав дренажно-распределительной системы фильтра входят водоподъемная труба, нижний распределитель (собирает поток воды, идущей через загрузку в рабочем режиме, или равномерно распределяет поток в корпусе при промывке), верхний щелевой фильтр (предотвращает вынос загрузки). Нижний распределитель, как правило, закрывают гравийной подложкой, чтобы он не забился загрузкой, и распределение потока воды осуществлялось бы по всей площади поперечного сечения фильтра.
Фильтрующая загрузка — основная часть фильтра. От неё зависит, какие задачи фильтр сможет решать. Кроме того, огромное значение имеет объем используемой загрузки, который рассчитывается для каждого типоразмера фильтра, при этом учитывается требуемая производительность, скорости прохождения воды через фильтр в разных режимах, минимальная высота слоя загрузки, необходимый свободный объем на её расширение при промывке и т. п.
5. Пример реализации метода
Широкое применение для очистки шахтных вод находят напорные скорые фильтры диаметром от 1 до 3,4 метров, они применяются в подземных водоочистных установках типа «Дон» и хорошо себя зарекомендовали. На шахте № 12−13 ПО «Макеевуголь» сооружена фильтровальная установка производительностью 50 м /ч, состоящая из двух напорных фильтров с двухслойной загрузкой из пенополистирола, разделенной металлическими стенками.
Рис. 17 Схема скоросного открытого пресса
1-воздухоотводная труба; 2-сборный желоб; 3-сборный коллектор распределительной системы; 4-лоток для отвода промывной воды; 5-труба для опорожнения фильтра; 6-ответвления распределительной системы.
На шахте «Торезская» ПО «Дзержинскуголь» установлена фильтровальная станция с двумя напорными фильтрами типа ФОВ-2,0−0,6 (фильтр осветительный однокамерный) для очистки стоков от взвешенных веществ производительностью 90 м3/ч. Фильтр грубой очистки снижает содержание взвешенных веществ с 300 до 20 мг/л, а после фильтра тонкой очистки в очищенной воде остается не более 2мг/л взвешенных частиц, что соответствует высокому уровню очистки. Первый фильтр двухслойный (песок кварцевый и дробленый антрацит на поддерживающем слое из гравия), фильтр второй (тонкой очистки) — однослойный (кварцевый песок). Фильтрование через тонкие перегородки осуществляется по двум направлениям: фильтрование с закупориванием пор и фильтрование с образованием осадка.
сточный вода фильтрование
1. Лекции по ТЗОС
2. В. А. Жужиков Фильтрование. Теория и практика разделения суспензий. Издательство «Химия». Москва 1971
3. http://www.saveplanet.su
4.http://www.xumuk.ru
5. Долина Л. Ф. Сточные воды предприятий горной промышленности и методы их очистки. Днепропетровск 2000