Проектирование цеха с гипсоварочным котлом
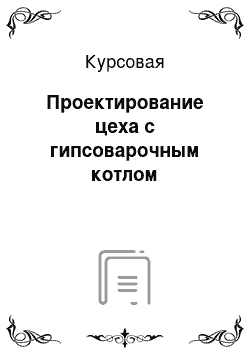
Установка усеченного конуса 5 позволяет получить скорости вращающегося основного газопылевого потока ниже уступов 4 большие, чем в зоне уступов 4, тем самым давление под уступами 4 будет меньше, чем в области уступов 4. Это обстоятельство позволяет сепарированным частицам мелкодисперсной пыли, находящимся в области концентрированного завихренного потока отрывной зоны перемещаться по спиралевидной… Читать ещё >
Проектирование цеха с гипсоварочным котлом (реферат, курсовая, диплом, контрольная)
В условиях рыночной экономики наметились определенные тенденции в производстве и применении строительных материалов. Во-первых, происходит быстрое развитие производства материалов и изделий, обеспечивающих значительное снижение массы возводимых зданий, базирующиеся на использовании местного сырья. Во-вторых, значительно возрастают масштабы производства материалов, изделий и конструкций по энергосберегающим технологиям. В-третьих, для современного строительства характерна тенденция роста доли экологически безопасных материалов и изделий, при этом расширяется сырьевая база за счет использования вторичного сырья и отходов различных производств, что обеспечивает снижение затрат при производстве материалов и изделий на 12…20%; в 2…3 раза позволяет снижать потребность в капитальных вложениях на развитие материальной базы строительства и одновременно решать задачу охраны окружающей среды. Если рассматривать гипсовые вяжущие материалы с позиции этих тенденций, то они находятся в более предпочтительном положении по сравнению с другими широко применяемыми в настоящее время аналогичными строительными материалами и изделиями. Обусловлено это повсеместным распространением гипсового сырья и гипсосодержащих отходов, простотой и экологичностью их переработки в гипсовые вяжущие, а последних — в гипсовые материалы с более низким, по сравнению с другими минеральными вяжущими изделиями, расхода топлива и энергии; низкими удельными капиталовложениями и металлоемкостью оборудования гипсовых предприятий по сравнению цементными, что особенно важно при организации производства на предприятиях средней и малой мощности. По химическому составу гипс не токсичен, при его переработке не выделяется в окружающую среду СО2. Поэтому получаемые из него вяжущие не являются аллергенами и не вызывают заболевание силикозом. Производимые на его основе строительные материалы и изделия имеют самые высокие показатели свойств (легкость, малую теплои звукопроводность, высокие огнеи пожаростойкость, а также декоративность). Нельзя не отметить и то, что гипсовые материалы и изделия создают благоприятный микроклимат в помещениях за счет способности поглощать избыточную влагу и отдавать ее, когда в помещениях «сухо». Вот почему в зарубежных странах за последние 20 лет возросло применение гипсовых материалов и изделий на единицу объема строительных работ. Основными видами гипсовых материалов за рубежом являются гипсокартонные и гипсоволокнистые листы, а также мелкои среднеразмерные плиты и блоки. Здесь получили достаточно широкое применение декоративно-отделочные и акустические изделия, а также в больших объемах гипсовые смеси различного функционального назначения. Однако, указанные гипсовые материалы и изделия используются, как правило, только внутри зданий с относительной влажностью воздуха не более 60%, что связано с присущим им отрицательным свойствам (низкой водои морозостойкостью, а также высокой ползучестью). Это, а также повышение требований к качеству и эффективности гипсовых вяжущих, материалов и изделий и привело исследователей в России и других странах к необходимости уделять большое внимание исходному сырью и его переработке в высококачественные гипсовые вяжущие, а последних — в материалы и изделия с новыми свойствами, новыми принципами их получения, а также разработке современных технологий.
Целью данной курсовой работы является разработка проекта завода по производству гипса в г. Бресте.
Поставленная цель достигается решением следующих задач:
1. технико-экономическое обоснование места строительства
2. выбор эффективных видов продукции и исходных сырьевых материалов
3. расчет режима работы предприятия
4. выбор технологической схемы и обоснование оборудования
5. скомпоновать цех основного производства
6. спроектировать генеральный план завода
7. экологически обосновать данное предприятие завод производство гипс проектирование
1. Технико-экономическое обоснование места строительства
Брест — город на юго-западе Белоруссии, административный центр Брестской области и Брестского района. Население — 315 тыс. человек (2008 год). Расположен в юго-западной части области, при впадении реки Мухавец в Западный Буг, у государственной границы с Польшей. Крупный железнодорожный узел, речной порт на Мухавце, важный узел автодорог. Это город с богатой и древней историей, не раз менявший свою государственную принадлежность, сейчас находится на самом стыке территорий Европейского союза и Содружества Независимых Государств, вблизи места, где сходятся границы трёх славянских стран — Белоруссии, Украины и Польши. Географически центр Брестской области располагается в 320 км к юго-западу от Минска, на западной окраине Полесья, представляющего собой заболоченную плоскую низину, достаточно обезлесенную вследствие воздействия человека. Рельеф территории, на которой лежит Брест, ровный (абсолютные высоты от 123 м, высоты уреза Западного Буга, до 130 м), слабо понижающийся к пойме Мухавца. На западной окраине города Мухавец впадает в Западный Буг, раздваиваясь на два рукава. На территории Бреста Мухавец притоков не принимает. По северной окраине Бреста протекает небольшая река Лесная, правый приток Западного Буга. Брест находится в часовом поясе, обозначаемом по международному стандарту как Eastern European Time (Восточноевропейское время), EET (UTC+2). Летом в Белоруссии используется Восточно-Европейское летнее время (UTC+3). Климат — умеренно континентальный (характерна мягкая зима и умеренно тёплое лето). Средняя температура января ?4,5°C, июля 18,5°C. Годовое количество осадков — около 550 мм. Вегетационный период длится 214 суток. Площадь города — 7372 га, из них 1/6 занята зелеными насаждениями (1155,9 га, в том числе общего пользования — 526,3 га). Город расположен в окружении лесопарковой зоны, занимающей площадь 2500 га. На территории Бреста имеется ряд парков (в том числе парк имени 1 мая, парк воинов-интернационалистов и др.) и скверов.
Брест — крупный центр обрабатывающей промышленности юго-запада Белоруссии. В числе машиностроительных предприятий города нужно выделить электромеханический, электротехнический и электроламповый заводы, завод газовой аппаратуры «Брестгазоаппарат» (торговая марка «Гефест»), предприятие «Цветотрон» (производство микроэлектронных компонентов), завод «Брестсельмаш». Имеются предприятия лёгкой (чулочно-носочная фабрика, ковровый комбинат, трикотажное, швейное производство) промышленности. Развито пищевое производство (мясокомбинат, ликёроводочный, пивобезалкогольный заводы). Имеются мебельная, сувенирная фабрики, завод бытовой химии. Производство стройматериалов представлено комбинатом строительных материалов (выпускает кирпич, облицовочную плитку) и заводом железобетонных конструкций и деталей. По данным на 2006 год, наибольший вес в промышленном производстве города играли предприятия пищевой промышленности (45,92%), на втором месте — предприятия отрасли машиностроения и металлообработки (37,34%), третье место занимает вклад лёгкой промышленности (8,71%). На территории Бреста и Брестского района расположена крупнейшая свободная экономическая зона страны. На территории СЭЗ работает более 90 предприятий. Крупнейшие предприятия-экспортёры — «Санта-Бремор» и Брестский молочный комбинат (торговая марка «Савушкин Продукт»).
В 2007 году темп роста промышленного производства предприятий города составил 119,8%, розничного товарооборота — 128%. За этот год введено в эксплуатацию почти 200 тыс. мІ жилья.
Город Брест является важнейшим транспортным узлом на юго-западе Белоруссии, а также значительным транзитным пунктом на государственной границе с Польшей. В городе функционируют три таможенных терминала. Брест — важный железнодорожный узел на магистрали Москва — Берлин, имеются также линии на Ковель, Высоколитовск, Влодаву. Действуют крупные грузовые терминалы, локомотивное депо. На территории города расположены станции Брест-Центральный, Брест-Северный, Брест-Восточный, Брест-Полесский, Брест-Южный. Железнодорожная станция Брест-Центральный принимает 37 поездов дальнего и 28 ближнего следования в день. В Бресте осуществляется замена вагонных тележек составов, пересекающих границу между Белоруссией и Польшей в связи с различным размером железнодорожной колеи. Станции Бреста и прилегающие участки железных дорог обслуживаются Брестским отделением Белорусской железной дороги. Через Брест проходит международный автомобильный транспортный коридор E30 (Корк — Берлин — Варшава — Брест — Минск — Москва — Челябинск — Омск), также имеются автомобильные дороги на Каменец, Малориту и др. Вблизи Бреста расположены автомобильные пропускные пограничные переходы «Варшавский мост» и «Козловичи». В течение 2006;2007 годов построен южный автомобильный обход города с мостами через реку Мухавец.
Таким образом, проанализировав технико-экономическую характеристику города можем придти к заключению, что Брест по всем показателям пригоден для строительства завода по производству гипса, поскольку он является перспективным промышленным центром с развитыми путями сообщения. Так как Брест является развитым транспортным узлом возможен выбор любого месторождения гипсового камня в качестве источника сырья, но принимая во внимание экономические аспекты приходим к выводу, что наиболее оптимальным вариантом является Бриневское месторождение гипса (расположенное в гомельском районе).
2. Номенклатура и выбор выпускаемой продукции
Строительный гипс (жженый гипс) — 2CaSO4*H2O. Представляет собой порошок белого или серого цвета в зависимости от количества примесей в гипсовом камне и чистоты обжига.
Получают путем термической обработки природного двухводного гипса CaSO4*2H2O при температуре 150−180 градусов в аппаратах сообщающихся с атмосферой до превращения его в полуводный гипс 2CaSO4*H2O. Разновидность продукта обжига называется гипсом в-модификации. Продукт измельчения гипса в-модификации в тонкий порошок до или после обработки называется строительным гипсом, при более тонком помоле получают формовочный гипс или, при использовании сырья повышенной чистоты, медицинский гипс. Используется в строительстве как воздушное вяжущее для оштукатуривания стен и потолков в зданиях с относительной влажностью не более 60%, в производстве гипсовых перегородочных панелей, листов сухой штукатурки, гипсокартона, вентиляционных коробов, арболита, гипсоволокнистых и гипсостружечных плит. Гипсовые изделия в конструктивном аспекте выполняют функции облицовочных и перегородочных элементов, а в строительном и техническом — тепло и звукоизоляционных материалов. Выпускаемый гипс должен соответствовать ГОСТу 125−79. Номенклатура выпускаемой продукции представлена в таблице 1.
3. Исходные сырьевые материалы
Сырьем для производства гипсовых вяжущих в-модификации (строительный гипс) служит природный гипсовый камень, а также гипсосодержащие отходы, кроме сульфатов кальция. Возможно применение гипсосодержащего природного сырья в виде сажи и глиногипса. При тепловой обработке природный гипс постепенно теряет часть химически связанной воды, а при температуре от 110 до 180 °C становится полуводным гипсом. После тонкого измельчения этого продукта обжига получают гипсовое вяжущее вещество. При тепловой обработке природного гипса в герметически закрытых аппаратах и, следовательно, при повышенном давлении пара химически связанная вода выделяется в капельножидком состоянии с образованием при температуре примерно 95…100°С а-модификации полуводного гипса. Обе модификации полуводного гипса отличаются между собой: модификация полугидрата отличается крупнокристаллическим строением.
Гипсовый камень, используемый для производства вяжущих материалов в данном проекте, должен соответствовать требованиям настоящего стандарта — ГОСТ 4013–82 от 1983;07−01.
Содержание гипса в гипсовом камне определяют по кристаллизационной воде. Основные характеристики исходных сырьевых материалов представлены в таблице 2.
Таблица 2 — Основные сырьевые материалы
Сорт | Содержание в гипсовом камне | ||
гипса (CaSO4Ч2H2O) | кристаллизационной воды | ||
19,88 | |||
18,83 | |||
16,74 | |||
14,64 | |||
Гипсовый камень применяют в зависимости от размера фракции: 60 — 300 мм — гипсовый камень для производства гипсовых вяжущих.
Перед непосредственной поставкой на производство сырьевые материалы проходят исследования.
Определение фракционного состава.
Фракционный состав пробы определяют контрольными ситами посредством калибра (для камня размером, большим или равным 300 мм).
Из общей пробы, подготовленной к испытаниям, берут 5 кг камня максимальным размером 300 мм. Пробу фракции размером 60 — 300 мм просеивают через сито с размером ячеек 60 мм, а более 300 мм определяют при помощи калибра диаметром 300 мм.
Камень, прошедший через сито размером 60 мм, а также выделенный на калибре размером более 300 мм взвешивают.
Определение содержания гипса (CaSО4Ч2H2О).
Камень после определения фракционного состава дробят до размеров около 10 мм и отбирают среднюю пробу массой около 1 кг. Затем последовательным квартованием отбирают пробу массой около 100 г. м Пробу камня измельчают в фарфоровой ступке до полного прохождения через сито с сеткой № 02. Допускается пробу камня массой около 100 г. отбирать после помольного оборудования. Навеску массой около 2 г, высушенную до постоянной массы при температуре (50±5) °С, помещают в предварительно прокаленный взвешенный фарфоровый тигель и нагревают в муфельной печи при температуре (400±15) °С в течение 1 ч. После прокаливания тигель с навеской охлаждают в эксикаторе и взвешивают. Прокаливание повторяют при той же температуре до получения постоянной массы. Взвешивание проводят с погрешностью до 0,0002 г.
Затем по формулам вычисляют содержание кристаллизационной воды и гипса.
4. Режим работы предприятия
Мощность предприятий по производству гипсовых вяжущих определяется на основе расчета потребности в гипсовой продукции с учетом запаса сырья, наличия топливно-энергетических ресурсов, а также фоновых выбросов и сбросов веществ загрязняющих атмосферный воздух, водоемы и почвы в соответствии с Общесоюзными нормативами технологического проектирования предприятий по производству гипсовых вяжущих изделий (ОНТП 15−86). Расчетный годовой фонд времени работы технологического оборудования в часах (Вр) определяем по формуле:
Вр= Ср*Сч*Ки
Сч = Сс*n
Ср — расчетное количество дней в году;
Сч — расчетное количество часов в сутки, ч;
Ки — среднегодовой коэффициент использования технологического оборудования:
Ки=0,9−0,92 — при трехсменной работе и Ки=0,94 — при двухсменной работе Сс — длительность рабочей смены в часах; n-количество смен в сутки, шт.
Таблица 3 — Режим работы завода
Наименование отделения | Количество рабочих дней в году, Ср | Количество смен в сутки, n | Длительность смены Сс, час | Коэффициент использования, Ки | Расчетный фонд времени, Вр | |
подача и складирование сырьевых материалов | 0,94 | 1955,2 | ||||
гипсоварочный цех | 0,92 | 8059,2 | ||||
силосный склад гипсового вяжущего | 0,94 | 3910,4 | ||||
дробильное отделение | 0,92 | 8059,2 | ||||
склад готовой продукции | 0,94 | 3910,4 | ||||
5. Краткое описание технологической схемы производства и основное оборудование
Технологический процесс производства неводостойких гипсовых вяжущих из природного сырья состоит из следующих основных переделов:
1. предварительная подготовка сырья (дробление, сушка и тонкое измельчение)
2. тепловая обработка подготовленного сырья (дегидратация)
3. дополнительный помол при необходимости основной помол, предусмотренный на этой стадии технологической схемой производства.
В зависимости от порядка выполнения этих операций имеются три технологические схемы производства строительного гипса:
1. предварительная сушка и измельчение гипсового камня в порошок необходимой дисперсности с последующей дегидратацией гипса в различных обжиговых аппаратах;
2. обжиг гипса в виде кусков различных размеров в разных печах с измельчением полугидрата в порошок после обжига;
3. совмещение операций сушки, помола и обезвоживания двугидрата в мельницах.
Последний способ получил название обжига гипса во взвешенном состоянии. Тепловую обработку гипсового камня производят в варочных котлах, сушильных барабанах, шахтных или других мельницах.
Наиболее распространена схема производства гипсового вяжущего с применением варочных котлов. Гипсовый камень, поступающий на завод в крупных кусках, сначала дробят, затем измельчают в мельнице, одновременно подсушивая его. В порошкообразном виде камень направляют в варочный котел периодического или в установку непрерывного действия. Последняя имеет в 2…3 раза выше производительность, но еще находится в стадии практического освоения. Варочный котел периодического действия представляет собой обмурованный кирпичом стальной котел со сферическим днищем, обращенным выпуклой стороной внутрь цилиндра. Разборное днище лучше выдерживает напряжения, возникающие при местном перегреве, а при износе отдельные его части легко заменяются новыми элементами. Для перемешивания гипса в процессе варки котел снабжен мешалкой, состоящей из вертикального вала, лопастей и привода. Котел закрывают крышкой с патрубком и пароотводной трубой, через которую удаляются пары воды, образующиеся при варке гипса. Устанавливают котел вертикально и обмуровывают кирпичной кладкой. Чтобы обеспечить равномерный прогрев гипса и увеличить поверхность нагрева, в варочных котлах большой емкости устанавливают жаровые трубы. В этом случае топочные газы обогревают сначала днище, затем боковые поверхности котла в кольцевых каналах, далее проходят через котел по жаровым трубам и, наконец, уходят в дымовую трубу. Часто газы из топок варочных котлов направляют в установки для совместной сушки и помола двуводного гипса, что способствует значительной экономии топлива. Загружают котел порошком двуводного гипса при помощи винтового конвейера, привод которого установлен на каркасе котла. Пары воды удаляются через трубу. Обжигают гипс в котле следующим образом. После прогрева котла включают мешалку и начинают постепенно загружать его гипсовым порошком. Продолжительность процесса варки зависит от размеров котла, температуры и степени влажности и частичной дегидратации поступающего в него гипса. Обычно продолжительность варки колеблется от 1 до 3 ч, при этом, а первые 20−30 мин гипс нагревается от температуры 60−70°С, которую он имел при загрузке в варочный котел, до начала интенсивной его дегидратации, т. е. до 130−150°С. Далее температура материала почти не меняется вследствие интенсивного выделения и испарения кристаллизационной (гидратной) воды. В это время наблюдается как бы «кипение» гипсового порошка. После окончания дегидратации гипса начинается ступающего в установку гипсового порошка до температуры дегидратации (115−125°С); в следующих секциях температура греющей поверхности 220 °C, материала — около 150 °C, что почти исключает образование обезвоженных модификаций сернокислого кальция. Пар, образующийся при дегидратации гипса, отводят из установки через трубки с вентилями, что позволяет регулировать количество отводимого пара на каждом участке и создавать условия для преимущественного образования а-модификации полугидрата и сушки готового продукта. Применение установок непрерывного действия, как и котлов больших размеров периодического действия, позволяет значительно сократить количество обслуживающего персонала, уменьшить объем здания на единицу продукции. И повысить качество гипса. Поэтому при строительстве новых заводов предусматривается установка только этих котлов. Для улучшения качества готовой продукции на отдельных заводах после обжига в варочных котлах гипс подвергают вторичному помолу в шаровых мельницах. При этом обнажающиеся при помоле необезвоженные ядра частиц гипса под влиянием тепла, выделяющегося от трения и ударов шаров, дегидратируются, а обезвоженный полугидрат и растворимый ангидрит гидратируются выделяющимися водяными парами и переходят в полуводный гипс. Кроме того, полагают, что частицы при вторичном помоле приобретают таблитчатую форму, обеспечивающую повышение пластичности теста и раствора из такого материала. Гипс в варочных котлах непосредственно не соприкасается с топочными газами. Кроме того, в процессе варки он интенсивно перемешивается и равномерно нагревается, что обеспечивает получение однородного продукта высокого качества. Расход условного топлива при изготовлении строительного гипса в варочных котлах составляет 40−45 кг, электроэнергии — 20−25 кВт-ч на 1 т. Данный способ получил наибольшее распространение в промышленности. Капиталовложения в этом случае составляют 20−25 руб. на 1 т вяжущего.
Гипсовое вяжущее в сушильных барабанах получают путем обжига гипсового камня в виде щебня размером до 20 мм. Сушильный барабан представляет собой сварной стальной цилиндр, вращающийся на опорных роликах со скоростью 2−3 оборота в 1 мин. Барабан устанавливают с наклоном к горизонту 3−5° и приводят во вращение электродвигателем. Гипс для обжига в виде щебня размером до 35 мм с помощью питателя подают в приподнятый конец барабана через загрузочную воронку; благодаря наклону 1 барабана он перемещается в нем в осевом направлении к разгрузочной воронке. В зависимости от выбранного направления потока горячих газов в барабане к загрузочному или разгрузочному концу его пристраивают топку. В первом случае направление движения горячих газов! и материала в печи совпадает, и барабан работает по принципу прямотока; во втором случае — газы и материал движутся навстречу друг другу (противоток). Эта схема отличается пониженным расходом топлива. Сушильные барабаны могут работать на твердом (кусковом и пылевидном), жидком и газообразном топливе. Удельный расход топлива в них составляет около 5% массы готового продукта. Для обжига гипса применяют сушильные барабаны производительностью 5−15 т/ч. Технологические процессы производства гипса с обжигом его во вращающихся печах непрерывные, и поэтому легко осуществить их автоматическое управление. Получать гипс по этому способу экономично.
При обжиге гипса во взвешенном состоянии совмещают две операции: измельчение и обжиг. В мельницу (шахтную, шаровую или роликовую) подают гипсовый щебень и одновременно нагнетают горячие дымовые газы. Образующиеся при размоле мельчайшие зерна гипса товарной фракции увлекаются из мельницы потоком дымовых газов и в процессе транспортирования в раскаленном газовом потоке обжигаются. Пылевоздушная смесь поступает в циклоны и фильтры для осаждения гипса. Наибольшую производительность из рассмотренных схем имеет последняя, затем схема обжига в сушильных барабанах и, наконец, в варочных котлах. Однако первые две схемы существенно уступают по качеству продукции (как уже было описано выше) схеме с варкой гипса. При затворении порошка гипса водой полуводный сернокислый кальций CaSO4−5H2O, содержащийся в нем, начинает растворяться до образования насыщенного раствора и одновременно гидратироваться. В результате образовавшийся насыщенный раствор полугидрата оказывается пересыщенным по отношению к двугидрату. Пересыщенный раствор в обычных условиях не может существовать — из него выделяются мельчайшие частицы твердого вещества — двуводного сернокислого кальция. По мере накопления этих частиц они склеиваются между собой, вызывая загустевание (схватывание) теста. Затем мельчайшие частицы гидрата начинают кристаллизоваться, определяя этим образование прочного гипсового камня. Дальнейшее увеличение прочности гипса происходит вследствие высыхания твердеющей массы и более полной кристаллизации при этом. Твердение гипса можно ускорить сушкой, но при температуре не выше 65 °C во избежание обратной дегидратации двуводного гипса.
На основании вышеизложенного можем придти к выводу, что наиболее рациональным вариантом с точки зрения качества готовой продукции будет использование технологической схемы с применением варочных котлов периодического действия.
В соответствии с выбранной технологической схемой используется гипсовый камень размером 300…500 мм, который подвергается первичному дроблению в щековых дробилках до размера кусков 30.50 мм. Рабочим раздавливающим органом щековой дробилки служат две дробящие поверхности — щеки, неподвижная и подвижная. Материал, поступая сверху через загрузочное отверстие, заклинивается между щеками и при надавливании на него подвижной щеки раздавливается. Образовавшиеся при этом мелкие куски ссыпаются в нижнюю часть дробящей полости и снова раздавливаются нажатием подвижной щеки. Так происходит до тех пор, пока размер зерен материала не окажется меньше размера нижней разгрузочной щели дробилки. Изменяя размер этой щели, можно регулировать наибольшую крупность дробленого продукта. Основной помольной установкой для измельчения гипса является шахтная мельница, представляющая собой молотковую мельницу с гравитационным сепаратором. Эта мельница служит не только для помола, но и для сушки гипса. Температура газов при выходе из мельницы находится в пределах 300…5000. Тонкость помола материала и производительность мельниц зависят от скорости газового потока. Газопылевая смесь после выхода из мельниц проходит через систему пылеулавливающих устройств — циклонов. Они имеют верхнюю цилиндрическую и нижнюю коническую части. Запыленные газы подводятся по касательной в верхней части циклона через входной патрубок. В циклоне газовый поток приобретает вращательное движение. При этом взвешенные частицы пыли под действием центробежной силы отбрасываются на внутреннюю поверхность цилиндра и по ней соскальзывают в коническую часть — пылесборник. В данном случаях нам необходимо очищать большие объемы газа, содержащего тонкую пыль, вместе с уже имеющимися циклонами установлены группы параллельно соединенных циклонов малого диаметра. Так как значение центробежной силы, создаваемой в циклоне, обратно пропорционально его радиусу, объединение циклонов меньшего диаметра в секции дает возможность, не уменьшая их производительности, довести степень очистки газов в батарейных циклонах до 80−98%.Движение газов в системе принудительное и осуществляется за счет работы центробежных вентиляторов. Осажденный в процессе пылеочистки гипсовый порошок поступает в расходные бункеры над варочными котлами. В зависимости от температуры газов при выходе из мельниц температура порошка может колебаться от 70 до 950С. По мере прекращения парообразования и увеличения плотности полученных продуктов дегидратации гипса масса уплотняется и снижается ее уровень в котле (первая «осадка» порошка). Вторая «осадка» наблюдается в последний период варки и соответствует обезвоживанию полугидрата сульфата кальция до растворимого безводного сульфата кальция (ангидрита). Готовый продукт выгружается из котла в приемный бункер, откуда механическим и пневматическим транспортом передается в силосные склады для хранения и отгрузки потребителю. Выбранная технологическая схема изображена на рисунке 1. Оборудование, участвующее в производственном процессе представлено таблице 4.
Таблица 4 — Сводная ведомость основного технологического оборудования и транспорта
Наименование оборудования | Краткая характеристика оборудования, транспорта | Количество машин, шт. | |
бункер гипсового камня | мощность 0,7 кВт, объём бункера не менее, -3,0 м3, диаметр бункера-18 000 высота с опорами не более-3300 мм | ||
ленточный конвейер ЛК-500 | производительность до 60 м3/ч; ширина ленты 500 мм; длина конвейера между осями барабанов до 30 м; скорость движения ленты 1.3, м/с*; нагрузка на погонный метр ленты 200 кг; мощность установленного электродвигателя 4−5.5 кВт; максимальный крутящий момент 273 Н*м | ||
щековая дробилка | размер загружаемого материала 200−600 мм; ширина загрузочной щели 13 мм; мощность двигателя 55 кВТ | ||
рукавные фильтры | скорость фильтрации от 0,7 до 1,5 м/мин | ||
циклоны ЦН-11 | допустимая запылённость газа, для слабо слипающихся пылей не более 1000 г./м3, температура очищаемого газа не более 250 0С; максимальное давление (разряжение) не более 3000 Па; эффективность очистки от пыли 10 мкм, плотностью 2,72 г./см3-50−99%; условная скорость в корпусе циклона — 2,2−2,8 м/сек | ||
Качество строительной продукции зависит от ряда факторов, и прежде всего от организации на производстве работы системы качества в соответствии с требованиями государственных стандартов. На производстве осуществляют следующие основные виды контроля качества:
· входной (контроль сырьевых материалов, вспомогательных материалов) осуществляется лабораторией предприятия.
· операционные — проверка соблюдения нормативных требований в процессе выполнения технологических операций в соответствии с технологическими регламентами, осуществляется техническим персоналом цехов.
· приемочный, осуществляется службой отдела технического контроля.
6. Компоновка цеха основного производства
Компоновка цехов по производству строительного гипса преследует цель наиболее рационально разместить производственное оборудование, чтобы обеспечить удобство и безопасность его монтажа, ремонта и обслуживания, непрерывность технологического потока, наименьшее расстояние транспортировки материалов от одного участка к другому при наименьшем числе транспортных устройств. Технологическое проектирование цехов по производству гипсовых вяжущих должно осуществляться на основе «Общесоюзных норм технологического проектирования предприятий по производству гипсовых вяжущих и изделий». При одновременном проектировании дробильно-сортировочных фабрик и установок входящих в состав цехов по производству гипсовых вяжущих необходимо руководствоваться «Общесоюзными нормами технологического проектирования предприятий нерудных строительных материалов». Гипсоварочные цехи в большинстве случаев не блокируются с другими цехами предприятия, за исключением силосных складов гипсового вяжущего и трансформаторных подстанций. При подборе и компоновке оборудования гипсоварочных цехов целесообразнее объединить основные агрегаты в один блок: котел, мельница и пылеосадительные аппараты. Необходимая мощность цеха (33 тыс. тон) достигается установкой одного такого блока. Дробильно-помольное отделение примыкает непосредственно к цеху варки гипса. Для приема, доставляемого со склада гипсового камня устраивается углубленный в землю бункерный приямок, под которым проходит ленточный транспортер. Перед приямком предусматривается бетонированная площадка для подачи и разгрузки опрокидных вагонеток. Приямок граничит со стеной дробильного отделения, а в стене оставляется проем для питающего дробилки транспортера. Дробленая щебенка элеватором подается в расходный бункер, питающий помольные установки. Поскольку в технологической схеме используется шахтная мельница, проектируется высотная часть здания для размещения самой мельницы, бункеров щебня и системы пылеосадительных устройств. Высотная часть распределена на площадки на отдельные этажи. В нижнем устанавливается рабочая камера мельницы с мотором, приводящим в движение ротор с билами, здесь же предусмотрен подвод теплоносителя в мельницу. Шахта мельницы примыкает непосредственно к помольной камере и проходит через все этажи. На второй снизу площадке расположен тарельчатый питатель для загрузки мельницы щебенкой. К балкам перекрытия второго этажа (третья площадка) подвешивают бункеры для щебня и готового измельченного гипсового порошка. На четвертой площадке установлены пылеосадительные аппараты. Разгрузочные секции пылеосадительных аппаратов опущены через проемы в площадке и выходят на третий этаж. Герметичными патрубками, снабженными шлюзовыми затворами, все пылеосадители присоединяются к одному общему закрытому винтовому транспортеру, распределяющему гипсовый порошок по питательным бункерам над варочными котлами. Отделение обжига изолировано от помольного отделения капитальными стенами. Для создания лучших санитарно-гигиенических условий топки гипсоварочных котлов вынесены в специальные отделения. Расположение бункеров питающих варочные котлы сырым гипсовым порошком смещено относительно оси варочных котлов, для того чтобы соединяющие их патрубки имели наклон к линии горизонта не менее 400С. Такое расположение течек предохраняет от резкого завала котла порошком из бункера. Бункер томления для готового гипса располагается непосредственно перед фронтом варочных котлов, расстояние крышки камеры до выгрузочного отверстия обеспечивает удобный доступ для наблюдения, регулирования и ремонта разгрузочного затвора. Бункер снабжен вытяжной трубой для быстрого удаления воздуха при его заполнении готовым гипсом. Так как вместе с воздухом удаляется некоторое количество тонкого гипса, эта вытяжная труба включена в общую пылеосадительную систему цеха.
7. Проектирование основного плана завода. Основные ТЭП
Генеральный план — это графическое изображение всех объектов в плане, а также инженерных сетей и транспортных связей с элементами благоустройства, обеспечивающими бесперебойную работу предприятия.
Проектирование завода по производству гипса проводим в соответствии с требованиями СниП II-89 «Генеральные планы промышленных предприятий». Взаимное расположение зданий и сооружения осуществляется с учетом выделяемых вредных веществ и розы ветров. Промышленные предприятия, выделяющие в результате своей работы газ, дым, пыль, шум по отношению к ближайшему жилому району должны располагаться с подветренной стороны для господствующих ветров, определяемых по розе ветров. Также их необходимо отделить от границ жилых районов санитарно-защитными зонами. В данном районе преобладающим является западное направление ветра, основные характеристики которого представлены в таблице 6.
Таблица 6 — Основные характеристики ветров г. Брест
январь | июль | |||||||||||||||
с | св | в | юв | ю | юз | з | сз | с | св | в | юв | ю | юз | з | сз | |
Основное направление ветров определяется по средней розе ветров теплого периода в результате многолетних наблюдений. Роза ветров представлена на рисунке 3.
Размещение зданий и сооружений при проектировании генпланов обеспечивает наилучшую схему технологического процесса, кратчайшие транспортные связи, экономное использование территорий, максимальную блокировку зданий и сооружений, зонирование территорий, санитарные и противопожарные разрывы между зданиями и сооружениями, а также возможность одновременной отгрузки готовой продукции на автомобильный и железнодорожный транспорт, возможность дальнейшего расширения предприятий без сноса построенных зданий и сооружений, целесообразную прокладку инженерных коммуникаций и удобный и безопасный подход работающих на предприятии к бытовым помещениям.
Рисунок 3 — Роза ветров г. Брест Пути следования к производственным зданиям не должны пересекаться с внутренними площадочными, автомобильными и железными дорогами, подъезд пожарных должен быть обеспечен с 3 сторон. Должно быть обеспечено архитектурное единство планирования застройки и благоустройства предприятия, с учетом транспортных связей для внутризаводского транспорта.
На предприятии по производству гипса действует как автомобильный, так и железнодорожный транспорт. Путем первого происходит вывоз готовой продукции, вторым поставляется сырьевые материалы для производства. Ширина автомобильных ворот въезда на территорию составляет 4,5 м. Тротуары на площадке предприятия размещаются не ближе 1,5 м от зданий и сооружений. Ширина проезжей части на территории предприятия 4,5 — 6 м.
Главным принципом проектирования генерального плана является группирование производственных зданий, сооружений и коммуникаций по функциональному назначению, что позволяет делить территорию завода на 4 зоны: предзаводскую, производственную, подсобную и складскую.
Предзаводская зона предназначена для осуществления кратчайшей путей, людских потоков и транспортных средств на территории предприятия и включает административно-бытовой корпус, стоянку для автотранспорта, контрольно пропускной пункт, лабораторию и гараж.
Производственная зона является основной. В ее состав входят гипсоварочные цеха. В подсобной зоне расположена компрессорная станция. Складская зона предназначена для размещения складов сырья, горюче смазочных веществ, готовой продукции и должна иметь удобные транспортные связи. Складская зона располагается на крайних участках заводской территории с целью пожарной безопасности, а также исключения пересечения грузовых потоков и засорения территории пылью при погрузочно-разгрузочных работах. На генеральном плане она представлена двумя складами готовой продукцией, двумя складами силосного вяжущего, складом горюче смазочных материалов. На территории предприятия предусмотрена зона отдыха с зелеными насаждениями.
Для обеспечения компактности и благоустроенности с сохранением близлежащих территорий определяют технико-экономические показатели генерального плана.
Компактность территории предприятия (генплан) оценивают показателем плотности застройки (К), который определяют в процентах, как отношение площади застройки (Sз) к площади предприятия в ограде (Sобщ). Площадь застройки (Sз) определяют как сумму площадей, занятых зданиями, сооружениями, включая открытые склады, галереи и подземные сооружения. Площадь покрытия дорог (Sд) рассчитывают, как сумму территории, занятой автои железными дорогами, включая тротуары. Площадь озеленения определяется по формуле:
Sоз = Sобщ — (Sз + Sд)=133 623.9 — (61 971.79+9239.5)= 62 412,6 м2
где SЗ — площадь всех зданий и сооружений;
Sобщ — общая площадь предприятия в ограде.
Плотность застройки (Кпл), рассчитывается по следующей формуле:
Кпл = Sзд/ Sобщ * 100%= 61 971.79/133 623.9*100%=46.4%
где Sзд — площадь всех зданий и сооружений;
Sобщ — общая площадь предприятия в ограде.
Коэффициент покрытия дорог Кд рассчитывается по следующей формуле:
Кд = Sд/ Sобщ=9239.5/133 623.9=0.069
где Sд — площадь дорог, м2.
Коэффициент озеленения Коз рассчитывается по следующей формуле:
Коз = Sобщ — (Sзд+ Sд) / Sобщ =0.46
где Sоз — площадь озеленения, м2.
Полученные данные представлены в таблице графической части проекта.
Расположение зданий должно обеспечивать санитарно-технические и противопожарные требования:
1. здания, где выделяются газ и дым располагать по отношению к другим зданиям и населенным пунктам с подветренной стороны
2. здания с шумным производством отделяют защитной зоной от общих и жилых зданий
3. нельзя возводить на территории предприятия жилые здания и сооружения при расстоянии до открытых складов с пылью не менее 20 м, до административно-конторских зданий не менее 50 м;
4. пожароопасные сооружения необходимо располагать с подветренной стороны, предусматривать ко всем зданиям удобные подъезды, при необходимости располагать пожарные депо с шириной защитной площадки не менее 10 м, устраивать пожарные гидранты и водоемы с запасом воды. Санитарные разрывы между зданиями должны быть не менее наибольшей высоты одного из них;
5. должны быть обеспечены общие архитектурно-строительные требования благоустройства и озеленения территории, которые по возможности увязывают с соседними районами и предприятиями. Озеленение — это одно из средств уменьшения вредностей, связанных с производственной деятельностью предприятия. Территория предприятия должна быть озеленена кустарниками, многолетними травами, газонами.
8. Экологическое обоснование предприятия
Производство строительных материалов и изделий, в том числе гипса, связано с использование и высокотемпературной переработкой больших количеств весьма разнообразных по физико-химическим свойствам сырьевых материалов и топлива, и сопровождается образованием пылегазовых выбросов, загрязняющих атмосферный воздух. Жесткие современные требования по защите атмосферного воздуха обуславливают необходимость разработки и освоения, новых более эффективных средств и методов защиты атмосферы на гипсовых предприятиях. При проектировании, строительстве и эксплуатации и реконструкции действующих предприятий по производству вяжущих материалов необходимо руководствоваться «Общими правилами по технике безопасности и промышленной санитарии для предприятий промышленности строительных материалов». Процесс производства гипса отличается коротким технологическим циклом: дробление и помол, сушка и варка. При производстве гипса выделяются тонкодисперсная пыль гипсового щебня и готовая продукция — порошкообразный гипс. Все промышленные выбросы можно подразделить на организованные и неорганизованные. Организованный промышленный выброс поступает в атмосферу через специально сооруженные газоходы, воздуховоды и трубы, что позволяет применять для очистки от загрязняющих веществ соответствующие установки. Неорганизованный промышленный выброс поступает в атмосферу в виде ненаправленных потоков газа в результате нарушений герметичности оборудования, отсутствия или неудовлетворительной работы оборудования по отсосу газа в местах загрузки, выгрузки или хранения продукта. Для снижения негативного воздействия производства вокруг производственной зоны предусматривают санитарно-защитную зону, представленную лесополосой радиусом 500 м.
Основной задачей экологического контроля предприятий является снижение вредного воздействия на окружающую среду и на здоровье рабочих. Неблагоприятные условия труда могут быть обусловлены повышенной концентрацией пыли и влаги в помещении; недостаточной изоляцией обжиговых аппаратов; ненадежным ограждением вращающихся частей механизмов т.п., поэтому необходимо проконтролировать данные параметры. Для этого был проведен экологический мониторинг и составлена карта экологического контроля, представленная в таблице 6.
Для борьбы с пылью необходимо все технологическое и транспортное оборудование, в котором образуется пыль, заключать в герметические сплошные металлические и другие кожухи с плотно закрываемыми смотровыми и ремонтными люками, дверцами и другими отверстиями. В местах образования пыли и газов следует устраивать помимо общей вентиляции местную аспирацию для удаления пыли и газов непосредственно из точек их образования. Паропроводящие трубы из варочных котлов, сушильных барабанов и др. надо присоединять к пылеосадительной системе для улавливания пыли. Очищать дымовые газы, воздух следует в наиболее эффективных пылеосадительных устройствах, в частности в электрофильтрах, гарантирующих очистку газов от пыли не менее чем на 98%. Это не только обеспечивает охрану окружающей среды, улучшает санитарно-гигиенические условия труда, но позволяет предотвратить потери сырья. Общая и местная вентиляционные системы должны обеспечивать надлежащее санитарно-гигиеническое состояние производственных помещений. Чаще всего для обеспыливания применяют пылеосадительные камеры (грубая очистка), сухие и мокрые циклонные аппараты (первая ступень), тканевые рукавные фильтры и электрофильтры (окончательная очистка). Выбор пылеуловителя определяется свойствами обеспыливаемой пылегазовой смеси. В технологической схеме уже предусмотрены пылеосадительная камера и батарея циклонов. Но для достижения более высоких показателей по очистке воздуха, необходимо внедрить вихревой пылеуловитель непосредственно для очистки от пыли при загрузке гипсовой щебенки и пылеуловитель для очистки от мелкодисперсной пыли при загрузке гипсовой муки.
Рисунок 4 — Вихревой пылеуловитель
Вихревой пылеуловитель работает следующим образом. Пылегазовый поток входит через ввод 7 под углом к оси корпуса 1 и, закручиваясь под действием тангенциально направленных центробежных сил, двигается вниз в корпусе 1. Навстречу ему снизу через осевой ввод 5 подается первичный запыленный газ, который закручивается также под действием тангенциально направленных центробежных сил в ту же сторону, что и нисходящий вторичный поток. Частицы пыли при этом под действием центробежных сил отбрасываются к стенкам корпуса 1. Закрученный вторичный поток: наталкиваясь на отбойную шайбу 6, частично разворачивается, взаимодействуя с первичным потоком, исходящим из осевого ввода 5. Частицы пыли, обладающие большей инерцией, отделяются от потока при его повороте у отбойной шайбы 6 и через зазор между ней и стенками корпуса 1 на линии разграничения цилиндрических частей 1 и 2 вылетают в бункер 8. Это способствует оптимальному взаимодействию закрученной струи первичного потока с нисходящим потоком закрученного вторичного потока и повышению эффективности пылеулавливания за счет возврата в бункер частиц пыли с малым удельным весом. Выполнение корпуса аппарата обработанным вибродемпфирующим материалом с соотношением толщины обрабатываемых деталей к толщине слоя вибродемпфирующего материала, находящимся в соотношении 1: (2,5…4), о позволяет снизить виброакустическую обстановку при пылеулавливании.
Предлагаемое устройство надежно в работе и эксплуатации за счет упрощения конструкции, а также малошумно. Преимущества: содержащит корпус, выполненный из двух цилиндрических частей разного диаметра и конической части, осевой ввод запыленного газа с завихрителем и отбойной шайбой, а также размещенные в верхней части корпуса осевой патрубок для вывода очищенного газа и периферийный ввод вторичного потока с завихрителем, отличающийся тем, что осевой ввод запыленного газа выполнен с периферийным завихрителем с углом наклона подводящего патрубка, равным углу наклона периферийного ввода вторичного потока, а профиль сечения отбойной шайбы выполнен таким образом, что максимальный диаметр ее лежит в плоскости соединения цилиндрических частей корпуса.
Устройство работает следующим образом. Запыленный газовый поток вводят тангенциально в верхнюю цилиндрическую часть корпуса 1 пылеуловителя мелкодисперсной пыли через плоский канал тангенциального входа 2. Сформировавшийся здесь вращающийся поток опускается по кольцевому пространству, образуемому внутренней поверхностью цилиндрической части корпуса 1 пылеуловителя мелкодисперсной пыли с выполненными уступами 4 и выходным патрубком 3, в конусную часть корпуса 1, а затем, продолжая вращаться, выходит из пылеуловителя мелкодисперсной пыли через выходной патрубок 3. Аэродинамические силы искривляют траектории частиц. Те из частиц, масса которых достаточно велика, успевают достигнуть стенок пылеуловителя, т. е. отделяются от потока.
Рисунок 5 — Пылеуловитель для мелкодисперсной пыли
Под влиянием силы тяжести (касается крупных частиц) и увлекающего действия осевого течения, отделившиеся частицы через тарелку 7 опускаются в бункер пыли 6, где оседают. Для мелкодисперсной фракции пыли, которая находится в потоке газа, по пути движения потока выполнены уступы 4. Из-за действия центробежных сил струя газодисперсного потока искривляется и присоединяется к стенке. Как следствие, происходит разделение частиц пыли и газа. Мелкодисперсная пыль сепарируется в зону пониженного давления, где образуется вихрь. Пыль, сконцентрированная в зоне разрежения, движется по направлению к бункеру 6 под действием перепада давления, которое создается усеченным конусом 5. установленным в области соединения цилиндрической и конусной части корпуса 1.
Установка усеченного конуса 5 позволяет получить скорости вращающегося основного газопылевого потока ниже уступов 4 большие, чем в зоне уступов 4, тем самым давление под уступами 4 будет меньше, чем в области уступов 4. Это обстоятельство позволяет сепарированным частицам мелкодисперсной пыли, находящимся в области концентрированного завихренного потока отрывной зоны перемещаться по спиралевидной вихревой нити из области большего давления по всей длине уступов в зону меньшего давления ниже уступов и далее в бункер. Второе положительное действие установленного усеченного конуса 5 в области соединения цилиндрической части корпуса 1 и его конусной части проявляется в том, что вторичный ток запыленного потока газа, вращающийся во внутренней области этого усеченного конуса 5 с мелкодисперсной пылью, сносится вниз (в направлении бункера 6) по расширяющейся поверхности конуса 5. захватывается основным запыленным потоком газа и движется по конусной части пылеуловителя в бункер пыли 6. Таким образом, мелкодисперсная пыль не выносится восходящим потоком в выходной патрубок, а улавливается и ссыпается в бункер пыли 6 через тарелку. Преимущество данного пылеочистительного устройства: содержит цилиндрический корпус, нижняя часть которого выполнена конусной, тангенциальный вход в виде плоского щелевого канала, уступы, выполнены по образующей внутренней поверхности корпуса, обечайку, выходной патрубок, отличающийся тем, что обечайка расположена в области соединения цилиндрической и конической частей корпуса и выполнена в виде усеченного конуса с центральным углом 6−10°, диаметр верхнего основания которого на 10% превышает диаметр выходного патрубка, а уступы выполнены в виде пластин, длинная сторона которых прикреплена к образующей внутренней поверхности цилиндрической части корпуса, а другая сторона является срезом уступов; высота уступа Н равна от ¼ до 1/3 расстояния h, образованного наружной стенкой выходного патрубка и срезом уступа; отношение большей стороны плоского канала к меньшей равно 10:1.
Таким образом, внедрив в технологическую схему дополнительные средства очистки от пылегазовых выбросов мы предотвратим потери сырья, а также снизим негативные воздействия на окружающую среду и здоровье рабочих.
Помимо усовершенствования пылеулавливающей системы, необходимо предусмотреть повторное использование отходов. Основными отличительными особенностями гипсосодержащих отходов является их повышенная влажность и дисперсность. Не смотря на дисперсность отходы до и после обжига необходимо измельчать.
Технологические процессы включают два основных передела: подготовка гипсосодержащего отхода (снижение содержание примесей путем промывки или нейтрализации); сушка отхода и тепловая обработка. перед загрузкой в котел материал подвергается совместной сушке и помолу в шахтной мельнице до стандартной тонкости помола. В качестве сушильного агрегата могут применятся отработанные под гипсоварочным котлом дымовые газы с температурой 3500-4500С.