Синтетические латексы; их переработка и применение в производстве изделий сферы быта и услуг
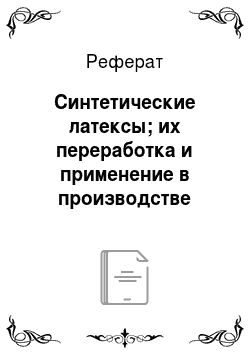
Способы переработки латекса существенно зависят от его коллоидно-химических свойств, определяемых природой и содержанием эмульгатора, степенью насыщенности поверхности глобул эмульгатором, размером глобул, вязкостью, концентрацией, стойкостью к действию высоких и низких температур и других факторов. Латексы, стабилизированные анионактивными эмульгаторами, позволяют получать ЛИ методами… Читать ещё >
Синтетические латексы; их переработка и применение в производстве изделий сферы быта и услуг (реферат, курсовая, диплом, контрольная)
Последние года характеризуются все более возрастающим потреблением резиновой в другими отраслями промышленности разнообразных синтетических латексов.
Вначале латексы применялись в резиновой промышленности в качестве заменителей резиновых клеев для пропитки и склеивания текстильных и некоторых других материалов. По мере изучения физико-химических и коллоидных свойств латексов их начали широко применять для изготовления различных резиновых изделий, которые не удается получить из каучука.
Применение синтетических латексов в промышленности позволяет:
- · упростить производство многих резиновых изделий;
- · повысить эксплуатационные свойства изделий;
- · исключить применение в производстве дорогих токсичных растворителей;
- · создать новые виды изделий и организовать непрерывный, поточный метод их производства.
Синтетические латексы — коллоидные системы, представляющие собой водные дисперсии синтетических каучуков. Макромолекулы полимера находятся в СЛ в виде глобулярных агрегатов. Коллоидная система СЛ стабилизирована поверхностно-активными веществами (эмульгаторами). Большинство СЛ — водные дисперсии эластомеров, образующиеся непосредственно в результате эмульсионной полимеризации. Некоторые СЛ изготовляют диспергированием в воде «готовых» полимеров (например, оутилкаучука, синтетического изопренового каучука). Такие дисперсии обычно называют искусственными латексами. К СЛ относят также водные дисперсии термопластов (например, поливинилацетата, поливинилхлорида), образующиеся при эмульсионной или суспензионной полимеризации.
СЛ делят в зависимости от химического состава полимера на бутадиен-стирольные, бутадиен-нитрильные, хлоропреновые, карбоксилатные, поливинилхлоридные и другие.
Свойства синтетических латексов Размер частиц каучука (глобул) в латексах составляет 0.02−2 мкм. Он оказывает существенное влияние на вязкость латекса, а также на его стабильность. Последняя тем выше, чем меньше размер глобул.
Концентрация СЛ изменяется в пределах 18−75%.
Вязкость СЛ зависит не только от размера глобул, но также и от способа получения СЛ, их концентрации, типа и количества эмульгатора. Латексы с концентрацией выше 30% ведут себя как неньютоновские жидкости.
Снижают вязкость СЛ агломерацией глобул или добавлением небольших количеств электролита; повышение вязкости достигается диализом с последующим концентрированием, введением загустителей и другими способами.
На агрегативную стабильность СЛ оказывают влияние многие факторы. Среди них, например, заряд глобул (электростатический фактор), обусловленный диссоциацией эмульгатора. Кроме того, стабильность СЛ существенно зависит то свойств полимера. При наличии в полимере значительного количества полярных групп можно получить стабильный латекс и в отсутствии эмульгатора. Так как латекс может утрачивать стабильность в результате химических реакций полимера (структурирование, деструкция и т. п.), то введение активных антиоксидантов и уменьшение концентрации латекс способствуют повышению его стабильности.
Морозостойкость СЛ ухудшается с повышением молекулярной массы эмульгатора, снижением рН и температуры замораживания. Этот показатель зависит также от типа полимера. Например, морозостойкость бутадиен-стирольных латексов тем хуже, чем выше содержание в сополимере винильного мономера. Для улучшения морозостойкости СЛ в них вводят небольшие количества низших спиртов, казеината аммония или насыщают глобулы эмульгатором. СЛ, выпускаемые в промышленности, как правило, недостаточно морозостойки, и поэтому их следует хранить при температурах выше 0 °C.
Модификация синтетических латексов Для придания изделиям некоторых химических свойств латексы подвергают модификации.
Один из способов — получение привитых сополимеров радикальной сополимеризацией винильного мономера (например, винилацетата, стирола) с полимером латекса. Вулканизованные пленки из таких сополимеров характеризуются повышенным модулем при растяжении и твердостью. Модификация СЛ галогенсодержащими веществами, например, трихлорбромметаном, придает изделиям из СЛ огнестойкость. Для повышения мягкости, пластичности и клейкости пленок из СЛ полимер окисляют, например, путем нагревания латекса острым паром в течение 3−4 ч в присутствии перекиси водорода. Латексы, содержащие окисленный полимер, применяют для получения клеев.
Значительная часть СЛ расходуется в производстве латексных изделий и губчатой резины.
Широкий ассортимент латексных изделий (метеорологические радиозондовые оболочки, перчатки различных типов, резиновые нити, изделия из губчатых резин и др.) обусловлен простотой технологии их производства и возможностью легкой механизации и автоматизации всех стадий процесса. Применение латексов позволяет получать резиновые изделия, которые не могут быть изготовлены из твердых каучуков, например, тонкостенные бесшовные. Кроме того, замена растворов каучука (резиновых клеев) латексом при изготовлении некоторых изделий исключает необходимость применения токсичных и пожароопасных органических растворителей.
Технология производства латексных изделий (ЛИ) Технологическая схема производства большинства ЛИ включает следующие основные стадии:
- 1. приготовление латексной смеси,
- 2. получение полуфабриката (геля),
- 3. уплотнение геля,
- 4. сушку изделия,
- 5. его вулканизацию.
Приготовление латексной смеси. Основная задача при составлении латексных смесей — правильный выбор типа латекса. Так, ЛИ с высокой прочностью при растяжении получают при использовании натурального или синтетического карбоксилатного латекса. При изготовлении ЛИ, стойких к действию масел и растворителей, применяют бутадиен-нитрильные или хлоропреновые латексы. Низкая газопроницаемость и высокая озоностойкость могут быть достигнуты при использовании хлоропренового латекса или искусственного латекса бутилкаучука.
Способы переработки латекса существенно зависят от его коллоидно-химических свойств, определяемых природой и содержанием эмульгатора, степенью насыщенности поверхности глобул эмульгатором, размером глобул, вязкостью, концентрацией, стойкостью к действию высоких и низких температур и других факторов. Латексы, стабилизированные анионактивными эмульгаторами, позволяют получать ЛИ методами желатинирования, коагулянтного макания и ионного отложения (см. ниже). Эти методы неприменимы для латексов с неионогенными эмульгаторами, обладающих высокой агрегативной стабильностью. Высокое содержание эмульгатора, обеспечивающее полное насыщение поверхности глобул латекса, позволяет вводить в смесь значительное количество наполнителей, но обусловливает низкие механические свойства и невысокую водостойкость ЛИ. Кроме того, высокая (более 60%) степень насыщенности поверхности глобул эмульгатором может отрицательно сказываться на получении ЛИ указанными выше методами.
В состав латексных смесей, кроме каучука и воды, входят различные ингредиенты, которые по назначению делятся на две группы.
К первой относятся ингредиенты, придающие требуемые свойства готовым изделиям. Это обычные ингредиенты резиновых смесей:
- · вулканизующие агенты,
- · ускорители и активаторы вулканизации,
- · антиоксиданты, противостарители,
- · наполнители,
- · пластификаторы.
Ко второй группе относят ингредиенты, придающие латексной смеси определенные технологические свойства. Это поверхностно-активные вещества, так называемые стабилизирующие добавки, способствующие снижению устойчивости коллоидной системы, загустители, пеногасители, антисептики, желатинирующие вещества и др.
Для вулканизации смесей используют те же системы, что и для изделий м твердых каучуков. Карбоксилатные латексы вулканизуют с использованием солей Zn, Ca и Mg, являющихся одновременно стабилизирующими агентами при ионном отложении.
Ускорителями вулканизации служат главным образом ультраускорители (дитиокарбаматы, тиурамы). Широко используют также тиазолы и гуанидины. Ускорители вулканизации, помимо своего основного назначения, могут оказывать существенное влияние на коллоидно-химические и технологические свойства смесей. Например, в присутствии цинковой соли меркаптобензотиазояа повышается вязкость смесей из натурального латекса.
Введение
активатора вулканизации ZnO в латексы, содержащие аммиак, приводит к их медленной астабилизации. В этом случае устойчивость смеси повышают, удаляя предварительно аммиак из латексов или вводя в смесь пополнительный стабилизатор коллоидной системы.
В латексные смеси вводят те же пластификаторы, антиоксиданты и антиозонанты, что и в смеси на основе твердых каучуков.
Порошкообразные наполнители (каолин, мел, литопон, высокодисперсная SiO2, сажа) обычно не способствуют эффективному повышению механических свойств изделия.
Введение
этих ингредиентов позволяет снизить стоимость ЛИ, повысить их жесткость, изменить окраску. Для улучшения механических свойств ЛИ применяют резорцино-формальдегидные, феноло-формальдегидные, мочевино-формальдегидные смолы, латексы поливинилхлорида и полистирола, щелочной сульфатный лигнин. Действие смол наиболее аффективно в том случае, когда их синтез происходит непосредственно в латексе (в процессе гелеобразования или вулканизации) или при введении смолы в стадии резола в процессе получения латекса. В последнем случае дальнейшая поликонденсация протекает одновременно с полимеризацией мономера.
Важное значение в рецептуре латексных смесей имеют поверхностно-активные вещества:
- 1. анионные (мыла олеиновой кислоты, синтетических жирных кислот и кислот канифоли, натриевая соль продукта конденсации нафталинсульфокислоты с формальдегидом — диспергатор НФ, казеин, карбоксиметилцеллюлоза и др.),
- 2. неионогенные (продукты конденсации моноалкилфенолов с окисью этилена — продукт ОП-7 пли олеиновой кислоты с окисью этилена — эмульфор, А и др.) и
- 3. катионные (амины, соли четвертичного аммония и др.).
Эти добавки служат смачивающими и диспергирующими агентами, стабилизаторами латексных смесей, латексной пены, суспензий и эмульсий ингредиентов и т. д.
В случае необходимости повышения вязкости латексов применяют так называемые загустители, которые образуют вязкие водные растворы или способствуют созданию тиксотропных структур. Загустителями служат синтетические полимеры (соли полиакриловой кислоты и щелочных металлов, полиакриламид, поливиниловый спирт и др.), природные высокомолекулярные вещества и их производные (карбоксиметилцеллюлоза, крахмал, казеин и др.).
Для предотвращения образования пены при перемешивании латекса и латексных смесей применяют пеногасители — эмульсии кремнийорганических жидкостей, высшие спирты C8-C12, минеральные масла и др. При наличии в смесях ингредиентов, которые могут разрушаться под влиянием бактерии (казеин, костный клей, крахмал и др.), применяютантисептики — соединения фенилртути, бутилолова, фторсиликат натрия, хлорированные фенолы.
Все ингредиенты вводят в латекс в виде водных растворов, суспензий или эмульсий. При этом размер частиц суспензий или эмульсий должен быть близок к размеру глобул латекса, а применяемый для их стабилизации диспергатор должен мало отличаться по своей поверхностной активности от поверхностно-активного вещества в самом латексе; рН эмульсий или дисперсий, вводимых в латекс, должен быть равен рН латекса.
При изготовлении латексных смесей целесообразно использовать свежеприготовленные дисперсии и эмульсии ингредиентов. В случае хранения их следует непрерывно перемешивать, не допуская вспенивания. Важное значение при изготовлении латексной смеси имеет порядок введения ингредиентов. Обычно в латекс сначала вводят растворы стабилизаторов коллоидной системы, а затем дисперсии вулканизующих агентов, ускорителей вулканизации, антиоксидантов, наполнителей, эмульсии пластификаторов и, наконец, дисперсию ZnO.
В ряде случаев после введения всех необходимых ингредиентов смесь «вызревает» 6−24 ч при 20−60°С и медленном перемешивании. При этом изменяются коллоидно-химические характеристики смеси (падает рН, возрастает вязкость и др.), повышается ее однородность и улучшаются технологические свойства. В ходе вызревания (особенно при повышенной температуре) полимер в латексе частично вулканизуется.
Получение полуфабрикатов. Большинство способов получения ЛИ.
- · ионное отложение,
- · коагулянтное макание,
- · термосенсибилизация,
- · электроотложение,
- · желатинирование,
- · многократное макание
основано на выделении (коагуляции) полимера в результате астабилизации коллоидной системы (например, под действием электролитов) или удаления влаги из латексной смеси (высушивания). ЛИ, которые получают погружением формы в латексную смесь, называют макаными. При ионном отложении форму, моделирующую изделие, погружают сначала в так называемый фиксатор, представляющий собой водный раствор электролита (СаСl2, Са (NО3)2), загущенный каолином или «белой сажей», а затем сразу же в латексную смесь. После образования слоя геля необходимой толщины форму с гелем извлекают из смеси. Способ отличается высокой производительностью (при одноили двукратном погружении формы в латексную смесь можно получать ЛИ толщиной до 2 мм) и широко используется в промышленности.
Разновидность ионного отложения — коагулянтное макание; в этом случае фиксатором служит незагущенный раствор электролита в летучем растворителе (спирте, ацетоне). Форму после подсушивания на ней фиксатора (обычно 1−3 мин. при комнатной температуре) погружают в латексную смесь и наращивают гель определенной толщины.
В способе, основанном на термосенсибилизации, используют латексные смеси, которые содержат агенты (поливинилметиловый эфир (лутанол М-40, игевин М-50), меркаптобензимидазолят натрия и др.), вызывающие астабилизацию латекса при погружении в него формы, нагретой до 60−100°С. Содержание термосенсибилизирующего агента в смеси составляет обычно 1−3 массовых части (здесь и далее — в расчете на 100 массовых частей каучука в латексе). Для обеспечения стабильности латексных смесей при комнатной температуре в них вводят казеин или другие стабилизаторы. Скорость отложения геля при термосенсибилизации выше, чем при ионном отложении. Например, в случае получения ЛИ с толщиной стенки 0,8 мм из вулканизованного натурального латекса «ревультекс» продолжительность образования геля при ионном отложении составляет 9 мин, при термосенсибилизации — 40 сек. Способ термосенсибилизации применяют главным образом для изготовления различных изделий медицинского назначения.
При желатинировании смесь заливают в форму, конфигурация которой определяет форму готового изделия. Смесь содержит желатинирующие агенты (чаще всего 2−10 массовых частей ZnO в смеси с 1−5 массовыми частями NH4CI и 1−4 массовыми частями NH4ОН или 1−3 массовыми частями Na2SiF6), под действием которых гель образуется при комнатной температуре за 1−5 мин. Этим способом можно изготовлять ЛИ, в том числе пустотелые, любых размеров и с различной толщиной стенки, а также изделия сложной конфигурации (например, рабочие органы («пальцы») чаесборочных машин, технические толстостенные перчатки с рифами на ладонной части, некоторые виды резиновой обуви). Способ лежит в основе получения губчатых резин из латекса.
При электроотложении глобулы латекса, имеющие отрицательный заряд, оседают в электрическом поле на аноде, образуя слой геля. Достоинство способа — возможность быстрого получения прочного геля сравнительно большой толщины при небольшом расходе энергии. Так, при плотности электрического тока, равной 400 А/м2, можно за 1 мин получить слой толщиной 1,4 мм. Недостатки способа — необходимость предотвращать газовыделение на аноде, обусловленное электролизом солей, так как в противном случае могут быть получены пористые пленки, а также трудность получения разнотолщинных пленок. Способ электроотложения не нашел широкого применения. Наиболее целесообразная область его использования — нанесение покрытий на металлические детали.
При многократном макании форму, моделирующую изделие, многократно (3−5 раз в зависимости от толщины стенки изделия) погружают в латексную смесь. Слой смеси, остающийся на форме после каждого ее погружения, сушат 5−10 мин при комнатной температуре. Способ малопроизводителен и находит применение только при получении ЛИ с толщиной стенки до 0,2 мм.
Уплотнение геля. При получении многих ЛИ гель подвергают уплотнению, при котором происходит медленное самопроизвольное сближение глобул. Процесс обычно проводят, выдерживая форму с гелем в воде в течение 1−4 ч при 25−30°С. Его скорость возрастает при повышении температуры, уменьшении содержания в латексе поверхностно-активных веществ, улучшении аутогезионных свойств полимера. В результате уплотнения геля повышаются его механические свойства (модуль и прочность при растяжении, относительное удлинение), что необходимо для проведения дальнейших операций при изготовлении ЛИ, кроме того, ускоряется сушка изделий.
Сушка. Обычно ЛИ сушат 2−15 ч в сушильных камерах в токе горячего воздуха при постепенном повышении температуры от 40 до 70−80°С. Один из путей сокращения продолжительности сушки — применение комбинированного нагрева токами промышленной частоты и ИК-лучами. Необходимость резкого увеличения продолжительности сушки при увеличении толщины слоя геля препятствует получению ЛИ с толщиной стенки более 2−3 мм. Быстрая сушка приводит к удалению влаги только с поверхности геля, что может вызывать его растрескивание и преждевременную вулканизацию поверхностной пленки, препятствующую дальнейшей диффузии влаги из геля к его поверхности.
Вулканизацию проводят, как правило, в камерах в среде горячего воздуха при 100−140°С. ЛИ вулканизуют на формах или в свободном состоянии; в последнем случае их помещают в камеры на противнях, заполненных тальком.
Как уже упоминалось, ассортимент ЛИ чрезвычайно разнообразен (см. выше).
Кроме них, одной из основных областей применения синтетических латексов является получение губчатой резины. При ее производстве латекс подвергают механическому вспениванию до определенного объема. В конце процесса вспенивания добавляют желатинирующие агенты и смесь подвергается нагреву. При нагревании происходит желатинирование и вулканизация латексной пены.
Области применения СЛ разнообразны и непрерывно расширяются. Помимо уже упомянутых латексных изделий, пористых и губчатых резин, на основе СЛ изготовляют клеи (см. ниже), краски. Важная область применения СЛ — производство бумаги. При этом латекс вводят в бумажную массу, пропитывают им бумажное полотно или наносят на поверхность бумаги (этот способ используют наиболее широко). Применение СЛ позволяет повысить прочность, гибкость, влагои маслостойкость бумаги, а также улучшить ее внешний вид и уменьшить растекание на ней чернил.
Использование композиций на основе СЛ для обработки текстильных материалов способствует улучшению их эксплуатационных свойств (прочности, эластичности, износостойкости, водои газонепроницаемости, стойкости к действию агрессивных сред) и повышению адгезии к другим материалам. Обработки текстильных нитей пли пряжи уменьшает их истирание при ткачестве и позволяет в некоторых случаях использовать некрученые нити.
При пропитке адгезивами на основе латекса шинного корда повышается прочность его связи с резиной. Пропитка шнуров и канатов повышает их водостойкость, износостойкость и предотвращает разлохмачивание. Для пропитки наиболее пригодны латексы на основе полимеров с функциональными группами (например, карбоксилатные,.
винилпиридиновые), способные к химическому взаимодействию с волокном.
Композиции на основе СЛ применяют при изготовлении прошивных ковров, ворсовых тканей, искусственного меха с целью закрепления ворса и лучшего сохранения формы изделий из этих материалов, а также при изготовлении дублированного (кашированного) текстильного полотна. При этом используют композиции на основе СЛ обладающие высокой вязкостью, механической стабильностью и не склонные к пенообразованию. Адгезию СЛ к ткани повышают введением в композицию поливинилового спирта, водостойкостьвведением меламино-формальдегидных смол.
СЛ применяют также в качестве связующего при изготовлении:
- · резиноасбестовых изделий (асбестовый картон, фрикционные изделия), в которых используют асбестовое волокно, предварительно обработанное латексными композициями;
- · так называемого «прорезиненного волоса» — материала из растительных волокон, животного волоса или их смесей, скрепленных композициями на основе СЛ (из этого материала изготавливают
- · сиденья для автомобилей и мебели);
- · пресс-материалов из пробковой муки, древесных опилок, соломы, льняных очесов и др.
СЛ используют для отделки натуральной кожи с поврежденной лицевой поверхностью, и также в качестве кожевенных лаков. При изготовлении искусственной кожи СЛ служат грунтами (их наносят на тканевую или нетканевую основу кожи с целью повышения прочности ее связи с материалом покрытия), лаками, а также компонентами водных дисперсий измельченного кожевенного волокна, из которых формуют листы.
СЛ применяют в строительной технике:
- · при изготовлении полимерцемента, используемого, в частности, при устройстве покрытий для полов,
- · для нанесения водонепроницаемого покрытия на свежий бетон, что способствует ускорению его твердения;
- · в качестве компонентов битумных композиций, используемых в материалах для дорожных покрытий и для герметизации стыков строительных конструкций.
СЛ вводят в состав композиций, используемых для защиты почвы от ветровой эрозии. Мри небольшом удельном, расходе таких композиций через 2−3 ч после их распыления на поверхности почвы образуется защитная пленка, не препятствующая прорастанию семян. На основе СЛ получают антикоррозионные полимерные покрытия для металлов, пасты для герметизации швов консервных банок и др.
В настоящий момент потребление СЛ благодаря их широкому ассортименту и разнообразию свойств превышает потребление натурального латекса.
Латексные клеи Латексные клеи (ЛК) — это клеи на основе натурального или синтетических латексов. Кроме обычных ингредиентов латексных смесейстабилизаторов коллоидной системы, вулканизующих агентов, ускорителей, а активаторов вулканизации, антиоксидантов и др. в состав ЛК вводят добавки, способствующие повышению их клеящей способности: растительные и минеральные масла, дибутилфталат, канифоль, животные клеи, казеин, альбумин крови, силикат натрия, крахмал и др. Для наиболее полного взаимодействия полимера с этими добавками в латексную смесь добавляют вещества (например, этиловый спирт), вызывающие частичную астабилизацию (разрушение защитной оболочки) глобул полимера. Иногда клеящую способность ЛК повышают предварительным окислением полимера, например, перекисью водорода. Для повышения вязкости ЛК применяют загустители (например, мездровый клей, казеинат аммония, полиакрилаты), для повышения водостойкости — меламино-формальдегидную смолу.
ЛК изготовляют таким же образом, как и смеси для латексных изделий.
ЛК применяют главным образом вместо резиновых клеев (растворов каучуков или резиновых смесей в органических растворителях). Основные преимущества ЛК перед резиновыми клеями:
- · низкая вязкость при высоком (до 60% по массе) содержании сухого вещества (вследствие высокой вязкости резиновых клеев их концентрация может быть не более 12%);
- · отсутствие в составе ЛК токсичных и огнеопасных растворителей;
- · отсутствие у большинства ЛК неприятного запаха.
В отличие от клеев животного происхождения ЛК не подвергаются плесневению. Недостаток ЛК — большая продолжительность сушки, чем для резиновых клеев.
Прочность клеевых соединений, получаемых с применением ЛК и резиновых клеев, практически одинакова. Присутствие в ЛК гидрофильных поверхностно-активных веществ обусловливает склонность клеевых соединений к набуханию в воде, приводящему к снижению их прочности; после высыхания прочностные свойства таких соединений восстанавливаются.
ЛК могут быть нанесены на склеиваемые поверхности пульверизатором, кистью, а также способами облива, макания или шпредингования. Поверхность некоторых материалов (например, кожу, резину, металлы) перед склеиванием предварительно очищают и обрабатывают различными способами с целью повышения адгезии. В случае необходимости (например, при эксплуатации изделия в условиях повышенных температур) ЛК могут быть свулканизованы.
Высокие адгезионные и когезионные свойства ЛК позволяют применять их в самых различных отраслях промышленности.
В производстве обуви с помощью ЛК склеивают кожаный верх с подошвой из каучука или резины, вклеивают внутренние детали, собирают заготовки. На предварительно очищенную и отшерохованную поверхность кожи или резины наносят один слой ЛК, а через 20−30 мин — другой. Когда слои Л К становятся совершенно прозрачными, склеиваемые детали соединяют друг с другом, прикатывая или обжимая места склейки. Состав некоторых обувных ЛК приведен ниже (в массовых частях):
- · каучук в натуральном латексе — 100; сера — 1,75; ZnO — 5; каптакс — 1,25; неозон Д — 0,5; натриевая соль кислот канифоли (смачиватель) — 0,5;
- · каучук в хлоропреновом латексе — 100; ZnO — 5; неозон Д — 0,5; натриевая соль кислот канифоли — 2;
- · каучук в натуральном латексе — 100; костный клей — 200; формалин — 60; альфа-нафтол — 10.
ЛК применяют для наклеивания корешков переплетов, брошюрования миг, заклеивания коробок, пакетов, наклеивания этикеток. Для ускорения «схватывания» в ЛК иногда вводят органические растворители. Корешки переплетов, предварительно отшерохованные для лучшего поглощения клея, пропускают под промазывающим валком.
В деревообрабатывающей промышленности ЛК применяют для склеивания деревянных поверхностей (шлифованных, струганных, отпиленных), например, при изготовлении фанеры.
В строительной технике с помощью ЛК приклеивают линолеум и плитки из полимерных материалов, а также паркет к различным основаниям пола.
В производстве текстильных материалов и ковров ЛК применяют для соединения хлопчатобумажных, шерстяных и льняных нитей без образования узлов. Состав такого клея (в массовых частях): каучук в натуральном латексе -100; этиловый спирт — 5; ZnO — 10.
В производстве абразивных материалов ЛК, содержащие меламино-формальдегидную смолу, наносят на тканевую или бумажную основу, а затем распыляют абразив.
ЛК широко применяют для склеивания пенополистирола, пенорезины, поливинилхлорида, а также для приклеивания керамических материалов стекла, металлов к бумаге, полистиролу, тканям, коже и др. Ниже приведен состав клея для приклеивания алюминиевой фольги к бумаге (в массовых частях): каучук в хлоропреновом латексе — 100; ZnO — 15; неозон Д — 2; казеинат алюминия — 20; силикат натрия — 0,25.
При изготовлении клейких лент на бумагу наносят клеи на основе акрилатного латекса, содержащие добавки бутилацетата и монохлорбензола.
В заключение приведем состав некоторых синтетических латексов и области их применения.
Латекс СКС-50ГП представляет собой водную дисперсию дивинила и стирола в соотношении 50:50. Латекс применяется в промышленности в качестве связующего при изготовлении нетканых материалов, для изготовления клеенки, плащевых изделий. Производство плащевых изделий с применением латексов имеет преимущество перед производством с использованием растворов каучука, которые являются токсичными и огнеопасными.
Латекс СКД-1 — водная дисперсия сополимера дивинила и метакриловой кислоты (в соотношении 100:2). Применяется для пропитки синтетических кордов. Пропитка латексом кордов существенно повышает срок службы покрышек.
Латекс СКН-40 — водная дисперсия сополимера дивинила с акрилонитрилом и метакриловой кислотой (в соотношении 60:40:3). Применяется дня изготовления нетканых материалов.
Латекс ДММА-65ГП — водная дисперсия сополимера метилметакрилата и дивинила. Применяется при изготовлении нетканых материалов, в производстве клеенки, некоторых видов искусственной кожи, а также отделки кожи.
Латекс ДВХБ-70 — водная дисперсия сополимера винилиденхлорида и бутадиена (в соотношении 50:50). Широко применяется в изготовлении искусственной кожи и для проклейки, пропитки и покрытия разнообразных материалов.
Для изготовления прокладочной кожи (футор кирзы), обувной кирзы используется ДВХБ-70 в смеси с латексом СКС-30.
Искусственная кожа типа картон производится методом проклейки кожевенных и других волокон латексами ДВХБ-70 и СКС-30.
Для изготовления искусственной кожи широко используются латексы на основе полиуретановых каучуков, а также на основе термопласта пол и вини л хлорида.
В данном пособии приводятся лишь некоторые направления применения синтетических латексов. Следует учитывать, что области использования латексов в целом гораздо разнообразнее и непрерывно расширяются.