Переработка сахарной свеклы
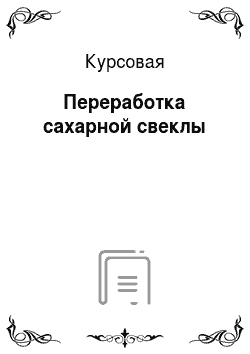
Мойка сахарной свеклы При ручной уборке свеклы количество прилипших к ней примесей составляет 1…3% к массе свеклы, а при поточной механизированной уборке — 10… 12%. В примесях содержится определенное количество микроорганизмов, которые могут загрязнять диффузионный сок при дальнейшей переработке свеклы. Вследствие этого свеклу необходимо очищать от примесей. Основные цели очистки: предупреждение… Читать ещё >
Переработка сахарной свеклы (реферат, курсовая, диплом, контрольная)
Содержание Введение
1. Характеристика сырья и виды продукции переработки сахарной свеклы
2. Транспортировка и очистка сахарной свеклы
3. Регулирование количества свеклы, поступающей на переработку
4. Удаление легких примесей
5. Подъем сахарной свеклы
6. Мойка сахарной свеклы
7. Резанье сахарной свеклы в стружку
8. Использование диффузных аппаратов при переработке сахарной свеклы
9. Физико-химическая очистка диффузионного сока и сиропа
10. Получение и фильтрация известкового молока и сатурационного газа
11. Приготовление и очистка рафинадных сиропов
12. Выпаривание сока и уваривание утфеля
13. Высушивание сахарного сиропа
14. Прессование Заключение Список использованной литературы
Введение
Сахарное производство в России возникло в XVII в. и заключалось в рафинировании тростникового сахара-сырца. В конце XVIII в. в России и за рубежом усиленно занимались поиском новых видов сырья для получения сахара. Лучшим сырьем оказалась сахарная свекла. В 1802 г. Я. С. Есипов в селе Алябьеве Чернского уезда Тульской губернии построил первый русский свеклосахарный завод. В дальнейшем одновременно с ростом числа сахарных заводов происходило совершенствование технологической схемы и оборудования заводов. К 1844 г. насчитывалось уже 206 сахарных заводов, и технология производства сахара к этому времени значительно усовершенствовалась. Вместо огневого выпаривания применяли паровое выпаривание, а для очистки диффузионного сока использовали известь. В 1844 г. на сахарных заводах начали применять многокорпусное выпаривание. В 1832—1853 гг. на сахарных заводах начали внедрять диффузионный способ извлечения сахара из свеклы, способ варки сахарных растворов с получением кристаллов и разделение утфеля в центрифугах с пробелкой сахара. С развитием капитализма в России сахарная промышленность быстро развивалась и уже к 1860 г. насчитывала 427 сахарных заводов небольшой мощности. В дальнейшем проявляется тенденция укрупнения сахарных заводов с разработкой новых видов оборудования и совершенствованием технологии сахарного производства. После революции были предприняты реконструкция существующих сахарных заводов и строительство новых. Эти направления достигли наибольшего развития в период индустриализации страны в связи с развитием отечественного машиностроения. К 1 января 1941 г. в СССР действовали 211 сахарных заводов, средняя производительность которых достигала 800 т свеклы в сутки. Великая Отечественная война 1941 — 1945 гг. нанесла большой ущерб сахарной промышленности. Было разрушено 42 завода, и 64 завода требовали восстановления. К 1949 г. сахарные заводы были почти полностью восстановлены, и в 1950 г. выработано сахара на 17,2% больше, чем в 1940 г. К 1991 г. в стране насчитывалось 330 сахарных заводов, представляющих собой высокомеханизированные и в значительной степени автоматизированные предприятия со среднесуточной производительностью 1,5…6,0 тыс. т свеклы. В результате распада СССР многие заводы отошли к различным странам СНГ. В Российской Федерации в 2004 г. действовали 93 сахарных завода. Средняя производительность их составила около 3 тыс. т свеклы в сутки. Значительное число предприятий были заняты переработкой тростникового сахара-сырца, поставляемого по импорту. В целом было выработано 5,6 млн т сахара, из которых 2,48 тыс. т — свекловичного, 3,11 млн т — тростникового.
Исходя из вышеперечисленных фактов, мы сформулировали тему нашего исследования: «Переработка сахарной свеклы» .
Объектом нашего исследования является технология переработки овощей.
Предмет исследования — технология переработки сахарной свеклы.
Цель исследования — дать характеристику переработки сахарной свеклы.
Задачи исследования:
1. Проанализировать литературу по теме исследования.
2. Дать характеристику основным понятиям работы.
3. Охарактеризовать основные этапы переработки сахарной свеклы.
1. Характеристика сырья и виды продукции переработки сахарной свеклы Исходным сырьем для получения сахара служит сахарная свекла и сахарный тростник. Благодаря более высокой урожайности сахарного тростника по сравнению с сахарной свеклой с каждого гектара его посевов получают сахара примерно в два раза больше, хотя содержание сахарозы в стеблях сахарного тростника несколько меньше, чем в сахарной свекле. Сахарная промышленность выпускает следующие виды сахара: сахар-песок — сыпучий пищевой продукт белого цвета (без комков), имеющий сладкий вкус, без посторонних привкусов и запахов (с содержанием влаги не более 0,14%, сахарозы не менее 99,75%, металл о приме се и не более 3 мг на 1 кг сахара, с размерами не более 0,3 мм);
сахар жидкий — жидкий пищевой продукт светло-желтого цвета, сладкий на вкус, без посторонних привкусов и запахов (с содержанием сахарозы не менее 99,80% для высшей категории и не менее 99,5% для первой категории, с содержанием сухих веществ не менее 64%);
сахар-рафинад — кусковой прессованный сахар, рафинадный сахар-песок и рафинадная пудра белого цвета, сладкие на вкус, без посторонних привкусов и запахов (с содержанием сахарозы не менее 99,9%, редуцирующих веществ не более 0,03%, влаги не более 0,2%).
Сахар-песок на свеклосахарных заводах и сахар-рафинад на рафинадных заводах производят в соответствии с типовыми технологическими схемами или по схемам, приближающимся к типовым. Типовые технологические схемы разрабатываются на основе передовых достижений науки и техники с целью получения продукта высокого качества при минимальных затратах сырья, материалов, энергии и трудовых ресурсов. Для выполнения отдельных операций в технологической схеме применяют типовое технологическое оборудование. Технологические схемы включают в себя большое число операций, которые необходимы для переработки свеклы в сахар-песок и последнего — в рафинад. Отдельным важнейшим операциям обычно предшествуют подготовительные, а в некоторых случаях предусмотрены сопутствующие операции, обеспечивающие качественное выполнение главной. Из этих операций можно выделить важнейшие, при проведении которых сырье или промежуточные продукты производства существенно изменяются. Совокупность машин и аппаратов, необходимых для проведения какойлибо главной и сопровождающих операций, называют машинно-аппаратурной системой. У свеклосахарного завода таких систем шесть, а у рафинадного — три.
Свеклосахарное производство включает в себя пять машинно-аппаратурных систем:
системы машин и аппаратов для переработки свеклы;
машинно-аппаратурная система для очистки и сгущения сиропа;
система, включающая в себя машины и аппараты для кристаллизации и получения товарного сахара;
совокупность машин и оборудования для получения извести, известкового молока и сатурационного газа;
машинно-аппаратурная система для прессования сырого жома, его сушки и брикетирования.
Сооружения и специальные машины, предназначенные для комплексной механизации работ по приемке, хранению и транспортированию свеклы, составляют шестую систему, которая рассматривается в специальной литературе. В качестве типовой схемы сахарорафинадного производства принята схема с тремя рафинадными и четырьмя продуктовыми утфелями (утфель — смесь кристаллов сахара и межкристального раствора). В зависимости от качества перерабатываемого сахара-песка на сахарорафинадном заводе должна быть обеспечена возможность работы по схеме с двумя рафинадными и тремя или четырьмя продуктовыми утфелями.
В сахарорафинадном производстве выделяют три машинно-аппаратных системы:
система машин и аппаратов для получения и очистки сиропов;
система для кристаллизации сахара, разделения рафинадных и продуктовых утфелей;
система машин и аппаратов для прессования, сушки, разделки и упаковки рафинадов.
Машины и аппараты каждой системы и системы между собой связаны в единый непрерывный производственный поток. Поскольку некоторые виды оборудования относятся к оборудованию периодического действия, для обеспечения непрерывного процесса в данной системе устанавливают несколько периодически действующих аппаратов или буферные емкости.
2. Транспортировка и очистка сахарной свеклы В настоящее время почти всю свеклу убирают механизированным способом. При ручной уборке и доочистке свеклы примеси в ней составляют 1…2% к общей массе, а при механизированном — достигают 10…20%. Перед хранением свеклы ее тщательно очищают при помощи комплекса буртоукладочных машин. Однако даже на современных буртоукладочных машинах нельзя полностью очистить свеклу от примесей, поэтому в тракте подачи свеклы из кагатов на завод устанавливают устройства для отделения легких и тяжелых примесей. К примесям относятся: солома, песок, шлак, камни и даже железные предметы. В случае попадания этих примесей в свеклорезку диффузионные ножи тупятся и повреждаются, что ведет к получению свекловичной стружки плохого качества. Для получения стружки высокого качества необходимо более полно отделять легкие и тяжелые примеси от свеклы. Для этого в тракте подачи свеклы на завод устанавливают песко-, соломои камнеловушки. Кроме того, после выхода свеклы из мойки от нее отделяют воду и ботву на специальных водоотделителях, а для улавливания металлических примесей устанавливают электромагнитные сепараторы. Для равномерной подачи свеклы на гидротранспортер устанавливают пульсирующие шиберы. Для лучшего улавливания ботвы и соломы перед соломоловушками устанавливают ботвоподъемник, в который подается вода или сжатый воздух. Свекла поднимается в моечное отделение свеклонасосами. Тяжелые примеси отделяют при помощи камнеловушек. Окончательно свекла очищается от примесей на дисковых водоотделителях. Для лучшего отделения примесей над дисковым водоотделителем перед мойкой устанавливают оросители, питаемые осветленной транспортерно-моечной водой. Их располагают в том месте над водоотделителем, где от свеклы уже отделилась транспортерно-моечная вода. Свекла отмывается в свекломойках. Отмытая свекла поступает на дисковые водоотделители, на которых она отделяется от моечной воды и через форсунки ополаскивается чистой хлорированной водой. Отмытая свекла из свекломойки элеватором, после которого установлен контрольный ленточный транспортер с подвесным электромагнитом, направляется в бункер перед свеклорезками. Транспортерно-моечные воды из первого водоотделителя и свекломойки направляются на хвостикоуловитель. Хвостики, бой свеклы и легкие примеси из хвостикоуловителей поступают на сортировочное устройство. Из него хвостики и кусочки свеклы попадают в мойку, а ботва, черешки листьев и мелкие кусочки свеклы — на транспортер и направляются в жомохранилище или используются на корм скоту[6]. Отсортированные хвостики и бой свеклы из мойки насосом подаются в открытый лоток и шнеком-водоотделителем направляются на элеватор, которым вместе со свеклой транспортируются на свеклорезки. Компоновка оборудования на тракте подачи свеклы в значительной степени зависит от местных условий. Однако при расстановке оборудования следует соблюдать определенные условия. Первый пульсирующий шибер необходимо устанавливать в начале главного транспортера или туннеля, что позволяет избежать заливания лотков главного транспортера и облегчает их обслуживание. Первую камнеловушку следует устанавливать перед свеклонасосами для защиты их от преждевременного износа. Если отсутствует станция подъема свеклы, то камнеловушку необходимо устанавливать как можно ближе к бурачной. Вторую камнеловушку устанавливают на подвесном гидротранспортере. Ботволовушки грабельного типа устанавливают перед камнеловушками. Основное условие качественной очистки свеклы от примесей и надежной работы оборудования тракта подачи свеклы — обеспечение относительно равномерного потока свекловодяной смеси в гидротранспортере с колебаниями среднечасового расхода в пределах 60… 140%. Гидротранспортеры предназначены для подачи свеклы в моечное отделение завода со складов длительного хранения — кагатных полей, бурачных или непосредственно после разгрузки из железнодорожных вагонов и автомашин. Гидравлическая подача свеклы на завод имеет свои преимущества. В процессе транспортирования свекла освобождается от основной массы тяжелых и легких примесей, а также частично отмывается от приставшей к ней земли и глины. В настоящее время гидротранспортирование свеклы является основным способом ее подачи на завод. Однако гидротранспортирование имеет и несколько существенных недостатков. Это прежде всего низкий коэффициент использования дорогостоящего оборудования. Так, вспомогательные транспортеры, расположенные под кагатами на складах хранения свеклы, используются один раз в производственный сезон. При гидротранспортиррвании свеклы наблюдаются заметные потери сахара в результате его диффузии в транспортерную воду, особенно при транспортировании подпорченной, мороженой и травмированной свеклы. Для нового сахарного завода производительностью 1500 т свеклы в сутки требуется площадь для хранения свеклы около 12…15 га с десятками гидротранспортеров длиной около 100 м каждый. При большой длине гидравлических транспортеров и значительном их заглублении необходимо устанавливать станции промежуточного подъема свеклы. Подача свеклы на завод гидротранспортерами получила распространение в сахарной промышленности в тот период, когда не было достаточного количества транспортных средств и погрузчиков разного типа. В настоящее время наличие большого количества транспортно-погрузочных средств позволяет применять сухую подачу свеклы к мойке. Необходимо отметить, что сухая подача свеклы на завод может дать ожидаемый эффект только при правильном выборе оборудования и рациональной организации работ. При выборе способа подачи свеклы необходимы тщательные технико-экономические исследования.
3. Регулирование количества свеклы, поступающей на переработку Тракт гидравлической подачи свеклы на завод включает в себя гидравлические транспортеры, расположенные под кагатами, сборные гидротранспортеры, главный гидротранспортер, станцию подъема и очистки свеклы и бункер над свеклорезками. Для нормальной работы завода необходимо, чтобы свекла поступала равномерно. Однако часто равномерная подача нарушается из-за неравномерной подачи ее в гидротранспортер с мест хранения, большой длины гидравлических транспортеров, приводящей при изменении темпа подачи свеклы на завод к пульсациям расхода свекловодяной смеси в них. Для нормальной работы соломоло-, камнеловушек, свеклонасосов и свекломоек поступление свеклы необходимо регулировать. Для этого применяют турникеты с горизонтальным и вертикальным валом, пульсирующие и отсекающие шиберы. Правильное размещение регулирующих механизмов по тракту подачи играет существенную роль в обеспечении нормальной работы моющей части свекломойки. Расстояние между первым пульсирующим шибером и моющей частью свекломойки принимают равным 30…50 м. Чем меньше это расстояние, тем более надежно осуществляется регулирование. Расстановка регулирующих устройств по длине тракта подачи зависит от местных условий. Существует несколько конструкций пульсирующих шиберов. На отечественных заводах наибольшее распространение получили шиберы конструкции РШ. Перед шибером в гидротранспортере устанавливают горизонтальную решетку на высоте от дна гидротранспортера, равной высоте затвора шибера. Наибольшее распространение для регулирования поступления свеклы получили регуляторы-турникеты с горизонтальным и вертикальным расположением валов.
4. Удаление легких примесей Для удаления легких примесей из потока свеклы во время перемещения ее по гидротранспортеру предназначены ботвосоломоловушки. При движении свеклы и примесей по гидротранспортеру последние сегрегируются по высоте потока соответственно их плотности. Тяжелые примеси, камни и песок опускаются преимущественно на дно, свекла располагается выше, а в верхних слоях потока оказываются легкие примеси, которые и удаляются при помощи ботвосоломоловушек. Ботвосоломоловушки устанавливают на желобе гидротранспортера в специальном помещении или на открытом воздухе. Основным рабочим органом для улавливания легких примесей служат грабли, опущенные в верхнюю часть водяного потока гидравлического транспортера. При взаимно противоточном перемещении свекловодяной смеси и грабель последние захватывают легкие примеси. Гребенки грабель могут быть прямыми или изогнутыми, с треугольными или квадратными вырезами. Лучшими являются изогнутые гребенки с неразведенными зубьями и треугольными вырезами. На сахарных заводах применяют ботвосоломоловушки двух типов — цепные и ротационные. Цепные в зависимости от профиля каркаса подразделяются на треугольные и четырехугольные. К треугольным ботвосоломоловушкам относятся ботвосоломоловушки типа ССТ-700 М и ССТ-900М, а к четырехугольным — ССП-700 и ССП-900. Выпускается прямоугольная двухвачьная ботвосоломо-ловушка типа СБГ-1060. Работа ботвосоломоловушки заключается в следующем. При движении со скоростью 0,1 м/с против потока свекловодяной смеси в гидротранспортере грабли погружаются в верхний слой потока, несущего легкие примеси, которые захватываются зубьями гребенок и выносятся наверх. Здесь на амортизаторах 8 закреплена вытряхивающая рама 6 с рядом поперечных уголков. Для удаления примесей из лотка установлена смывающая брызгалка. Освобожденные от примесей гребенки своими верхними концами проходят через успокоительный обрезиненныи валик и вновь опускаются в поток гидротранспортера. Обычно для всплывания легких примесей перед ботвосоломоловушкой в гидротранспортере устанавливают ботвоподъемник, в который подают воздух или воду.
5. Подъем сахарной свеклы Из гидравлического транспортера свеклу необходимо поднимать в мойку на высоту до 10… 15 м, а из мойки — на площадку автоматических весов на высоту около 20 м. Кроме того, в случае большого заглубления гидравлического транспортера приходится осуществлять промежуточный подъем свеклы. Почти единственным видом подъемников для свеклы от свекломоек на площадку автоматических весов являются элеваторы, которые работают в тяжелых условиях, что приводит к частым обрывам цепей, перекосам карманов и необходимости проведения трудоемкого ежегодного ремонта. Применение свеклонасосов с достаточной высотой подъема позволяет поднимать свекловодяную смесь на такую высоту, которая позволяет применять оригинальную компоновку моечного отделения. В такой компоновке свекломойка располагается на высоте, обеспечивающей гравитационный спуск свеклы на автоматические весы и в свеклорезки. Это исключает необходимость установки свекловичных элеваторов, облегчает сброс транспортерно-моечной воды на отстойники и улучшает условия улавливания, мойки и очистки боя свеклы и хвостиков. В настоящее время на сахарных заводах применяют свеклонасосы различных конструкций: насосы Пенского машиностроительного завода, ВСН-50, LIHC-400, 14CB-6, насосы Гипросахара, чешские насосы моделей RN-500 и РХО19, польские WB-400 и SD-20×24. Наибольшее распространение получили насосы Пенского машиностроительного завода ЦНС-400. Для заводов большой производительности (порядка 5000 т перерабатываемой свеклы в сутки) применяют насосы типа ВСН-50.
6. Мойка сахарной свеклы При ручной уборке свеклы количество прилипших к ней примесей составляет 1…3% к массе свеклы, а при поточной механизированной уборке — 10… 12%. В примесях содержится определенное количество микроорганизмов, которые могут загрязнять диффузионный сок при дальнейшей переработке свеклы. Вследствие этого свеклу необходимо очищать от примесей. Основные цели очистки: предупреждение затупления ножей в свеклорезках; освобождение свеклы от микроорганизмов. Частично свекла отмывается от приставших к ней примесей в гидравлических транспортерах и свеклоподъемных устройствах. Для окончательного отделения прилипших к свекле примесей и частичного отделения тяжелых примесей применяют свекломойки. Прилипшие к свекле примеси (земля и глина) лучше всего отмываются при трении корней друг о друга, поэтому в начальной стадии мойки свекла должна находиться в скученном состоянии. Для этого в начале корпуса свекломойки отделение примесей должно происходить при пониженном уровне воды. При дальнейшем перемещении свеклы вдоль корпуса свекломойки, когда основная масса загрязнений удалена, лучше мыть свеклу в менее скученном состоянии и в более чистой воде. Кроме того, необходимо над свеклой иметь спокойное зеркало воды для отделения легких всплывающих примесей. Для этой цели в свекломойке должно быть отделение с высоким уровнем воды. В нем зеркало воды должно быть выше уровня свеклы на 300…400 мм. Отмытая от свеклы земля не должна взмучиваться в корпусе свекломойки транспортирующими устройствами — кулаками. Для этого в нижней части свекломойки по всей ее длине над нижним днищем устанавливают ложное перфорированное днище. Зазор между нижним и перфорированным днищами составляет 100…150 мм. В пространстве между днищами осаждаются земля, песок и мелкие камни. Через песколовушки и камнеловушки они удаляются из свекломойки. Потери сахара в транспортерно-моечной воде зависят от качества свеклы и времени года. До наступления морозов потери сахара не должны превышать 0,07% к массе свеклы. После наступления морозов потери зависят от качества свеклы и находятся в пределах 0,17…0,35% к ее массе. Температура воды, поступающей в свекломойку, не должна превышать 15…18 °С. При переработке мороженой свеклы температура воды должна быть такой, чтобы не допускать смерзания свеклы в свекломойке. Машины для отмывания свеклы можно классифицировать в зависимости от их принципа действия, числа корпусов и уровня воды в них, а также выделить в классификации специальные свекломойки. Наибольшее распространение в сахарной промышленности получила свекломойка системы Добровольского. В связи с тем что чистку камнеловушек в этой мойке производят вручную, затраты физического труда на чистку оказываются большими.
7. Резанье сахарной свеклы в стружку Для извлечения сахара из свеклы диффузионным способом ее необходимо превратить в стружку. Стружку из свекловичных корней получают на свеклорезках при помощи ножей, установленных в специальные рамы. Поскольку изрезанная свекла поступает далее в экстрактор, где из нее извлекается сахар с использованием процесса диффузии, ножи свеклорезок также называют диффузионными. Производительность диффузионной установки и содержание сахара в обессахаренной свекловичной стружке в очень большой степени зависят от ее качества. Форма свекловичной стружки, получаемой на свеклорезках, может быть желобчатой или пластинчатой. Толщина нормальной стружки 0,5…1,0 мм. Ее поверхность должна быть гладкой, без трещин. Слишком тонкая стружка нежелательна, так как она деформируется, сбивается в комки и ухудшает циркуляцию диффузионного сока в диффузионных аппаратах.
Качество свекловичной стружки принято определять ее длиной в метрах в навеске массой 100 г. Для этого стружку раскладывают на специальной доске с канавками. Короткие части стружки (меньше 1 см), пластинки гребешков и тонкую просвечивающуюся стружку независимо от ее длины на доске не раскладывают и считают браком. Количество брака должно быть по возможности меньшим. Масса брака в хорошей свекловичной стружке не должна превышать 3% массы свеклы. Такое определение качества не полностью характеризует качество свекловичной стружки и качество установки ножей в рамах. Качество стружки следует характеризовать не только длиной и количеством брака, но и степенью ее однородности по толщине. Хорошим показателем может быть проницаемость слоя стружки при определенной температуре и давлении на ее слой. В Швеции для оценки качества стружки применяют так называемый шведский фактор, который представляет собой отношение массы стружки длиной более 5 см к массе стружки длиной менее 1 см в навеске массой 100 г. Хорошей считается стружка, для которой шведский фактор превышает 10. Для получения качественной свекловичной стружки на центробежных или дисковых свеклорезках необходимо, чтобы свекла в процессе резания с достаточным усилием прижималась к поверхности ножей и внутренней поверхности барабана или к диску свеклорезки. Для центробежных свеклорезок диаметром 1200 мм при скорости резания 8,2 м/с давление на внутренней поверхности барабана составляет около 4,10 кПа, а для дисковых свеклорезок при высоте слоя свеклы в бункере 3,0 м — 30 кПа. Действительно, давление корня свеклы при резании не может быть постоянным, так как в процессе работы центробежной свеклорезки изменяются центробежная сила и опорная поверхность корня свеклы. А при работе дисковой свеклорезки изменяются высота столба свеклы над диском свеклорезки и опорная поверхность свеклы. Чтобы свекла при резании с достаточным усилием прижималась к поверхности ножей, в центробежных свеклорезках применяют трехлопастной ротор (улитку), а в дисковых свеклорезках — специальные прижимные устройства.
Машины для резания свеклы можно классифицировать исходя из взаимного относительного движения свеклы и режущих устройств. К свеклорезкам с неподвижными режущими устройствами относятся: центробежные типа СЦБ-12, СЦБ-16, А2-ПБР-24 и барабанные. К свеклорезкам с подвижными режущими устройствами относятся дисковые с верхним и нижним приводами. В центробежных свеклорезках рамы с ножами закреплены в вырезах корпуса с вертикальной осью. Свекла, поступающая в свеклорезку, перемещается относительно ножей при помощи ротора-улитки и прижимается к ножам под действием центробежной силы и лопастей ротора. В дисковых свеклорезках рамы с ножами устанавливают в вырезах диска, вращающегося вокруг вертикальной оси, свекла остается неподвижной и прижимается к ножам под действием силы тяжести и специальными прижимными устройствами. В барабанных свеклорезках ножи с рамами закреплены в вырезах стенки барабана, вращающегося вокруг вертикальной оси; свекла находится внутри барабана, удерживается от вращения вместе с ним и прижимается к ножам специальными прижимами.
На центробежных свеклорезках при нормальных условиях эксплуатации получают стружку наилучшего качества, в них расходуется наименьшее число ножей на 100 т свеклы по сравнению со свеклорезками других конструкций. Ножи можно менять на ходу. Производительность свеклорезок регулируют изменением частоты вращения ротора или числа установленных ножей. Дисковые свеклорезки потребляют меньше энергии по сравнению с центробежными и барабанными, на них можно получать стружку хорошего качества, но расход ножей на 100 т свеклы больше по сравнению со свеклорезками других конструкций. Для замены ножей свеклорезку останавливают. Барабанные свеклорезки просты по устройству, но в процессе эксплуатации требуется большое количество ножей и энергии, стружка получается низкого качества, ножи можно заменять только при остановке. Ко всем типам свеклорезок предъявляют одинаковые требования: высокая производительность; хорошее качество свекловичной стружки; простота и удобство обслуживания и ремонта; надежность и экономичность.
8. Использование диффузных аппаратов при переработке сахарной свеклы Аппараты, в которых производится экстрагирование из твердого вещества, нашли широкое распространение в сахарной промышленности и называются диффузионными. В диффузионных аппаратах сахар извлекается из свекловичной стружки при помощи экстрагирующей жидкости. От этого процесса в значительной мере зависят и производительность завода, и потери сахара не только в процессе экстрагирования, но и на других стадиях свеклосахарного производства. В производственных условиях диффузионные аппараты должны обеспечивать:
обессахаривание наиболее толстой свекловичной стружки при равномерном ее обтекании диффузионным соком;
строго противоточное перемещение свекловичной стружки и диффузионного сока;
минимальные потери сахара в отходах (жоме) при максимальной концентрации диффузионного сока;
высокое качество диффузионного сока при минимальном содержании в нем мезги.
Кроме того, аппараты должны быть несложными в изготовлении и ремонте и удобными для обслуживания в производственных условиях. Отмытая в свекломойках и взвешенная на весах свекла поступает в бункер, а затем — на свеклорезки. Свекловичная стружка, полученная на свеклорезках, ленточным транспортером, на котором установлены конвейерные весы, взвешивается и направляется в шахту ошпаривателя. В ней стружка предварительно подогревается диффузионным соком температурой 72 °C. Сок, нагревая стружку, охлаждается до 47 °C и направляется насосом в песколовушку. Далее песок поступает в мезголовушку, из которой направляется на очистку. Мезга, отделившаяся в ловушке, направляется в ошпариватель. В ошпаривателе свекловичная стружка окончательно подогревается циркуляционным соком. Его расход составляет 290% к массе стружки. Сок подогревается паром в подогревателе 2 от 72 до 85 °C. Нагретая сокостружечная смесь из ошпаривателя насосом 18 подается в диффузионный аппарат. Ее расход составляет 405% к массе свеклы, температура — 78 °C. Свекловичная стружка в диффузионном аппарате перемещается вверх при помощи транспортирующих устройств и за счет подпора насоса. В верхнюю часть диффузионного аппарата подается жомопрессовая вода с расходом 40% к массе свекловичной стружки при температуре 74 °C и сульфитированная барометрическая вода (расход 60% к массе стружки) с температурой 65 °C.
9. Физико-химическая очистка диффузионного сока и сиропа Диффузионный сок необходимо очищать по следующим причинам.
Сок содержит взвешенные тонкие частицы, а при нагревании к нему присоединяются хлопья коагулированных белков. Все эти частицы необходимо удалить, чтобы они не присоединялись к кристаллам сахара.
Отфильтровать сырой диффузионный сок на фильтрах невозможно, так как они рассчитаны на использование процесса шламового фильтрования, а взвешенные частицы закупоривают отверстия фильтрующего осадка.
Кислая реакция диффузионного сока привела бы на выпарной станции к инверсии сахарозы; кроме того, неочищенный диффузионный сок при выпаривании сильно пенится.
Для диффузионного сока характерна слабая окраска, которая передается кристаллам сахара.
Большое количество несахаров, содержащихся в диффузионном соке, увеличивает выход мелассы и содержание в ней сахара.
Цель очистки диффузионного сока — освободить его от взвешенных частиц, придать ему нейтральную реакцию и удалить наибольшее количество несахаров. В настоящее время наиболее рациональным методом очистки сока признана обработка его известью с последующим удалением ее избытка диоксидом углерода. Сок обрабатывают известью в процессе дефекации в два приема — на преддефекации и на основной дефекации. Обработку сока диоксидом углерода также осуществляют в два приема — в процессах I и II сатурации. При дефекации осаждаются щавелевая, оксилимонная, лимонная и винная кислоты. Безазотистые органические кислоты, аминокислоты и бетаин осаждаются известью и остаются в растворе. Кроме обычных реакций осаждения в процессе дефекации протекают еще и коллоидные реакции. Коагулируют главным образом белки из диффузионного сока, сапонины и красящие вещества. Очищенный сок приобретает желтую окраску, пенистость его уменьшается. Уже при добавлении к диффузионному соку 0,06% оксида кальция (извести) начинается заметная коагуляция веществ. При увеличении количества извести осадок становится более плотным, а раствор более светлым и прозрачным. Оптимум плотности осадка и прозрачности раствора достигается при расходе извести 0,2…0,3% и рН среды II. Когда плотный осадок уже образовался при добавлении остальной извести вплоть до ее концентрации, равной 2…3%, осадок остается плотным. Без предварительной дефекации при добавлении сразу полной порции известкового молока осадок становится рыхлым, желеобразным и плохо фильтруется. Таким образом, для дефекации вовсе не требуется 2…3% извести, как это принято на сахарных заводах, а достаточно всего около 0,3%. Но уменьшение количества извести приводит к нежелательным явлениям: ухудшается фильтрование сока вследствие того, что осадок становится слизистым, повышается цветность сатурационного сока и понижается его качество вследствие уменьшения эффекта адсорбции на сатурации. Цель дефекации — очистка диффузионного сока путем коагуляции известью белков и красящих веществ, а также осаждение некоторых анионов, образующих нерастворимые соли с ионом кальция извести. При дефекации для очистки диффузионного сока к нему прибавляют 2,0…2,5% обожженной (жженой), но негашеной извести. Образующийся в результате этой реакции гидроксид кальция Са (ОН)2, или гашеная известь, присутствует в избытке воды в виде суспензии известкового молока или известковой воды. В таком виде ее и добавляют к диффузионному соку. Указанная дозировка значительно превышает количество извести, которое необходимо для протекания химических реакций в соке. Дефекованный сок вместе со всеми осадками направляется на I сатурацию. При сатурации через сок пропускают диоксид углерода СО2
Данную реакцию интерпретируют как выпадение извести в осадок в виде карбоната кальция СаСО3 под воздействием диоксида углерода. При образовании частиц карбоната кальция на их поверхности адсорбируется определенное количество несахаров, находящихся в растворе. Особенно интенсивно адсорбируются окрашенные коллоидные продукты разложения инвертного сахара. Главная цель I сатурации — дополнительная очистка путем адсорбции. Щелочность сока I сатурации должна соответствовать 0,08… 1,0% негашеной извести (СаО) в 100 мл сока, при этом кислотность рН 11. Отфильтрованный сок I сатурации поступает на II сатурацию. Цель И сатурации — уменьшение содержания извести и солей кальция в соке до минимума и повышение его доброкачественности. Присутствие извести и солей кальция в диффузионном соке приводит к быстрому загоранию поверхности нагрева выпарной станции и увеличенному выходу мелассы. На II сатурации сок обрабатывают диоксидом углерода до достижения оптимальной кислотности, которая зависит от качества перерабатываемой свеклы. Кислотность рН сока II сатурации обычно составляет 9,0…9,5. Иногда процессе второй сатурации в продукт добавляют около 0,25% негашеной извести (СаО) к массе свеклы для дополнительной очистки сока путем адсорбции. После предварительной очистки диффузионного сока в нем всегда содержатся окрашенные вещества. Применяя дополнительную очистку сока сернистым газом, его обесцвечивают путем восстановления красящих веществ в бесцветные соединения; при этом часть сернистой кислоты в растворе сока превращается в серную. Оптимизация условий проведения процесса сульфитации диффузионного сока и сиропа позволяет снизить общую цветность раствора почти на 35%. Наилучшее обесцвечивание соков и сиропов достигается применением в качестве сорбентов активных углей. Их использование уже в количестве 0,3…0,5% в пересчете на сухое вещество позволяет достичь значительного обесцвечивания. Однако применение активных углей ограничивается их высокой стоимостью и усложнением технологической схемы производства. В сахарной промышленности применяют также ионообменную очистку сока.
В соответствии с типовой схемой очистки диффузионного сока очищенный в пульполовушках диффузионный сок поступает в подогреватель и затем направляется в котел прогрессивной преддефекации. Перед преддефекацией к диффузионному соку добавляют недогазированный сок I сатурации с содержанием 0,3…0,5% извести (СаО) или 60… 100% массы свеклы. Возможно добавление нормально отгазированного сока со щелочностью 0,08…0,1% по содержанию СаО (около 150% массы свеклы). В последнем случае к нему в контрольный ящик сатуратора добавляют также известковое молоко в количестве 0,25…0,3% или 10% дефекованного сока.
Преддефекованный сок поступает самотеком в котел основной дефекации, куда при помощи струйного дозатора добавляют известковое молоко из расчета 2,0…2,5% массы свеклы. Из котла основной дефекации сок самотеком поступает в котел сатурации, где обрабатывается сатурационным газом, содержащим 28…32% диоксида углерода (СО2), до щелочности 0,08…0,10% по содержанию СаО. Часть нефильтрованного сока I сатурации из особого отделения контрольного ящика сатуратора или недогазированного сока из ящика направляют на преддефекацию, а остальную часть сока I сатурации из основного отделения контрольного ящика насосом перекачивают через подогреватель, в котором он нагревается до 90…95 °С, на станцию фильтрования. После станции фильтрования сок поступает в сборник и контрольные салфеточные фильтры.
Отфильтрованный сок I сатурации, подогретый в подогревателе до 100… 102 °C, насосом направляют в котел II сатурации, где его обрабатывают диоксидом углерода до щелочности 0,01…0,25% по содержанию СаО. При этом на преддефекацию возвращается нефильтрованный нормально отгазированный сок. Из котла II сатурации сок непрерывно поступает в фильтры и затем в сборник и контрольные салфеточные фильтры. Отфильтрованный сок II сатурации самотеком или насосом подают в сульфитатор, где его обрабатывают сульфитационным газом, содержащим 10… 12% диоксида серы (SO2) до щелочности 0,05…0,10% по содержанию СаО. Сульфитированный газ получается сжиганием серы в печи. Охлажденный в сублиматоре газ вентилятором подается в нижнюю часть сульфитатора. Сульфитированный сок вначале насосом нагнетается в напорный ящик, затем фильтруется. Фильтрованный сок направляется на выпарную станцию. Значительное влияние на полноту осаждения несахаров и структуру осадка оказывает способ добавления извести к диффузионному соку. При прогрессивном постепенном добавлении извести к диффузионному соку образовавшийся осадок меньше растворяется, чем при одноразовом введении извести. Прогрессивная обработка диффузионного сока известью имеет большое значение для эффективной его очистки, так как структура коагулятора органических веществ не только делает его устойчивым на основной дефекации, но и способствует улучшению седиментационно-фильтрационных свойств осадка сока I сатурации. Технологические свойства свеклы, убранной механизированным способом и выращенной с применением аммиачных удобрений, в некоторой степени изменяются. Переработка такой, а также подпорченной свеклы по обычной технологической схеме не обеспечивает выполнения установленных требований к качеству сахара, по содержанию его в мелассе и других показателей работы сахарного завода.
10. Получение и фильтрация известкового молока и сатурационного газа Для удаления из диффузионного сока содержащихся в нем не-сахаров применяют известковое молоко и сатурационный газ. Известковое молоко [водная суспензия гидроксида кальция Са (ОН)2 или гашеной извести] получают путем гашения обожженного в известковых печах известкового камня. При обжиге одновременно получается и сатурационный газ. содержащий около 30% диоксида углерода (СО2). Для обжига известкового камня в сахарной промышленности используют кусковой антрацит. В последние годы на некоторых сахарных заводах камень обжигают на газе и мазуте, для чего печи дооборудуют специальными приспособлениями.
Большинство сахарных заводов получает известковый камень в кусках массой 15…20 кг, на месте его дробят на куски по 1…2 кг, при этом образуется большое количество отходов. Известковый камень обладает значительной механической прочностью. Его сопротивление раздавливанию составляет 2…9 кН/см. Плотность (объемная масса известкового камня колеблется в пределах от 2400 до 2800 кг/м. Вследствие большой плотности он впитывает и удерживает на своей поверхности мало влаги (до 5%).
В сахарной промышленности широко применяют фильтрование или осветление сатурационных соков и сиропов, но свойства фильтруемых суспензий различны, и это определяет разнообразие конструкций используемого оборудования. Для фильтрования соков I и II сатурации раньше применяли фильтр-прессы, но они требуют большой затраты ручного труда при обслуживании. Поэтому фильтр-прессы были заменены дисковыми фильтрами (ДФ), которые обладают некоторыми преимуществами по сравнению с фильтр-прессами. Дисковые фильтры более компактны, герметичны и осадок из них выгружается гидравлическими приспособлениями. Однако они малопроизводительны и требуют большого количества воды для промывки осадка и удаления его из фильтра. На сахарных заводах большой производительности для отделения сока I сатурации применяют отстойники и вакуум-фильтры. Эти установки обеспечивают непрерывность процесса и значительно снижают затраты рабочей силы и расход фильтровальных тканей, но они энергоемки, при длительном пребывании сока в них значительно повышается его цветность. Сиропы сахарного производства представляют собой суспензии и содержат небольшое количество взвесей. Раньше их фильтровали на тканевых фильтрах, но они требуют больших затрат труда на регенерацию фильтровальной ткани и не обеспечивают достаточной прозрачности сиропа, поэтому для фильтрования сиропов применяют дисковые фильтры с центробежным удалением осадка. Типовая схема фильтрования предусматривает применение для сока I сатурации листовых саморазгружающихся фильтров типа ФиЛС; для фильтрования и промывки сгущенной суспензии — вакуум-фильтров; для контрольного фильтрования сока I сатурации, фильтрования сока II сатурации и фильтрования сиропа с клеровкой — применения патронных фильтров и дисковых фильтров с центробежным удалением осадка. Разделение сока I сатурации на две фракции — сгущенный осадок и осветленный сок — производится в сгустителях. В качестве сгустителей на сахарных заводах применяют фильтры-сгустители, саморазгружающиеся листовые фильтры Ф и ЛС и многоярусные отстойники. В отстойнике получается 75…80% осветленного сока и 20…25% сгущенного осадка к массе нефильтрованного сока I сатурапии. Осветленный сок поступает на контрольное фильтрование, а сгущенная суспензия — на вакуум-фильтры. Производительность отстойников по свекле 1000…2500 т/сут, диаметр 4000…5500 мм, высота 4000…6500 мм; общая вместимость 95… 150 м. Независимо от того, какое оборудование используют для сгущения осадка сока I сатурации, для удаления из него жидкой фазы применяют вакуум-фильтры. Поскольку температура суспензии, поступающей из сгустителей на вакуум-фильтры, составляет около 85 °C, то остаточное давление на вакуум-фильтрах не должно превышать 0,045…0,048 МПа. Таким образом, перепад давления, при помощи которого осуществляется фильтрование на вакуум-фильтрах, в 4…5 раз меньше, чем на фильтрах циклического действия, поэтому толщина слоя осадка на барабанных фильтрах допускается не более 10…12 мм. Для быстрого роста толщины осадка на фильтрующей поверхности барабана 2 фильтра содержание сухих веществ в суспензии, поступающей на фильтрование, должно быть не менее 20%. В отечественной сахарной промышленности нашли широкое распространение фильтры Б-40, БШУ-40−3-10М. На некоторых заводах работают фильтры зарубежных фирм типа «Эймко» (Франция), БМА (ФРГ) и «Виккерс—Букерс» (Великобритания). В последнее время применяют фильтры БсХШУ-40−3 и БсХШУ-8−3,75. Кроме камерных фильтров используют также бескамерные вакуум-фильтры.
свекла сироп утфель сахарный
11. Приготовление и очистка рафинадных сиропов Качество сахара-рафинада и сахара-песка в значительной степени зависит от тщательности проведения подготовительных операций: очистки диффузного сока и сахара-песка от посторонних примесей, их обесцвечивания. В сахаре-песке, поступающем на переработку на рафинадные заводы, содержатся комки сахара и примеси, которые могут попадать в него при расшивке мешков и транспортировке со складов бестарного хранения. Для очистки сахара-песка применяют просеиватели и шпагатоуловители различных типов. Просеянный сахар накапливают в бункерах и затем направляют в клеровочные аппараты с мешалками периодического и непрерывного действия, где он растворяется в воде и получается рафинадный сироп.
В рафинадном сиропе, приготовленном на белой клеровке, содержится сравнительно много посторонних механических примесей, для отделения которых применяют фильтр-прессы и патронные фильтры ПФ-20. После механического фильтрования в рафинадных и продуктовых сиропах содержатся красящие вещества и растворенные соли. Утфели, сваренные из таких сиропов, характеризуются повышенной цветностью, что затрудняет получение кристаллов сахара рафинадного достоинства, поэтому в рафинадном производстве применяют вещества, способные в той или иной степени обесцвечивать растворы и поглощать растворенные в них соли. К таким веществам относятся сорбенты, основные из которых — костяной активированный и гранулированный угли. Применение костяного и гранулированного углей для обесцвечивания сиропов связано с использованием громоздкого оборудования и сложного процесса восстановления их адсорбционной способности. Кроме того, эффект обесцвечивания сиропов костяным углем не превышает 30…45%. Для эффективного обесцвечивания сиропов применяют иониты. Эффект обесцвечивания ионитами достигает 85…90%. Процесс регенерации ионитов прост, и эксплутационные расходы при работе с ними меньше, чем при работе с костяным и гранулированным углями. В настоящее время ионообменные установки широко распространены на рафинадных заводах.
На некоторых свеклосахарных заводах с рафинадным отделением применяют глубокую очистку диффузионного сока при помощи искусственно приготовленных ионитов. Этот способ позволяет получить совершенно бесцветный диффузионный сок чистотой 99 единиц. При этом из сока удаляется до 88% несахаров. Ионитную очистку сока и клеровки используют главным образом в тех случаях, когда необходимо получить сразу сахар рафинадного достоинства.
Полную деионизацию сока редко применяют в сахарном производстве в связи с ее повышенной стоимостью. Чаше выбирают более простой способ применения ионитов для умягчения сока. При этом работают только с катионнтом в натриевом цикле. Очищенный сок перед выпариванием пропускают через слой катионита, который удаляет из него соли кальция. Сок становится менее жестким, и поверхность нагрева выпарного аппарата мало загорает. Считают, что стоимость установки для умягчения сока окупается в результате улучшения работы выпарной установки и связанной с этим экономией топлива.
В рафинадных и продуктовых сиропах после механического фильтрования содержатся красящие вещества и растворенные соли, снижающие качество готового продукта. Для обесцвечивания сиропов и удаления из них растворенных солей применяют обесцвечивающие адсорбенты, к которым относятся костяной и гранулированный активированные угли. Костяной уголь получают из костей крупных домашних животных путем их дробления, вываривания в воде или экстрагирования и прокаливания без доступа воздуха при температуре 700 °C в течение 8… 12 ч. После прокаливания кости охлаждают и измельчают до получения частиц размером 5…15 мм. В последние годы в качестве адсорбента для очистки сиропов все чаще применяют гранулированные активные угли марок АГС-3, АГС-4М и АГС-5. Их изготовляют из каменного угля и смолы методом парогазовой активации. Размеры частиц такого адсорбента 1…3 мм, насыпная плотность — 0,43…0,45 г/л. Применение гранулированных активных углей обеспечивает высокую эффективность осветления сиропов. Для рафинадных сиропов она составляет 30…60%, для продуктовых — 50…65%. Адсорбирующая способность костяного и гранулированного углей одна из самых больших, что объясняется развитой поверхностью адсорбции. Активная поверхность 1 г костяного угля составляет 100…125 м:, гранулированного — около 1000 м2.
Использование гранулированного угля вместо костяного на существующем оборудовании сахарных заводов снизило расход сорбента в 3…4 раза, улучшило обесцвечивание сиропов и, следовательно, привело к экономии средств на адсорбционной очистке сиропов. Применение аппаратуры периодического действия при осветлении сиропов и регенерировании костяного угля имеет существенные недостатки, к которым относятся: большие трудовые затраты при обслуживании оборудования, его громоздкость, большая производственная площадь отделения для осветления сиропа и регенерирования угля. Кроме того, периодические процессы всегда менее производительны по сравнению с непрерывными. В последние годы в производство внедряются непрерывные схемы осветления сиропов и регенерирования угля. Необходимую скорость фильтрования сиропа через слой угля устанавливают в зависимости от его вязкости при заданной температуре. Более вязкие сиропы должны иметь меньшую скорость фильтрования.
Применение костеугольной крупки и гранулированных углей связано с громоздким оборудованием и сложным процессом восстановления их адсорбционной способности. Эффект обесцвечивания сиропов костеугольной крупкой достигает 30…45%. Также для обесцвечивания сиропов применяют иониты. Они позволяют повысить эффект обесцвечивания до 85…90%, Процесс регенерации ионитов прост, и эксплуатационные расходы при работе с ними меньше, чем при работе с крупкой и гранулированными углями. При ионитной очистке сиропов резко сокращается производственная площадь для этого оборудования; достигается полная механизация и автоматизация процесса очистки, чем облегчаются условия труда. Иониты — это полярные адсорбенты, которые обладают способностью к обменной адсорбции катионов и анионов в растворе. Иониты разделяются на две группы:
катиониты, способные заменять любой катион на ион водорода;
аниониты, способные удалять из раствора кислоты, т. е. анионы и ионы водорода. В качестве катионов применяют синтетические смолы типа бакелита, получаемые из фенолов и формальдегида. Аниониты получают конденсацией анилина с альдегидами. Иониты — твердые зернистые материалы белого, черного, коричневого или желтого цвета, слабо набухающие в воде и сахарных растворах и практически в них нерастворимые. Размер частиц ионитов составляет 0,75.0,5 мм. Применение более мелких частиц ионитов затрудняет фильтрование сиропа через их слой. Плотность частиц ионитов около 1300 кг/м3, насыпная плотность — 500…700 кг/м3. Плотность анионитовых смол обычно на 15% меньше, чем катионитовых. Отработанные иониты легко регенерируются: катиониты — растворами кислот и солей, аниониты — растворами едких щелочей и аммиака. Иониты, применяемые для очистки сахарных растворов, должны иметь следующие свойства: слабо набухать в растворах, быть устойчивыми в кислых и щелочных средах, не растворяться в воде и сахарных растворах, хорошо адсорбировать красящие вещества, иметь высокую емкость поглощения несахаристых веществ, обладать достаточной механической прочностью, иметь форму и размеры частиц, обеспечивающих хорошее фильтрование сиропа через слой ионита высотой не менее 2,5 м. Емкость поглощения ионитов (активность) — наиболее важный показатель, определяющий эффективность применения ионитов в сахарной промышленности. Чем выше емкость поглощения, тем больше сиропа можно очистить в течение одного цикла и тем меньше получается промоя и меньше расходуется реактивов на регенерацию ионитов. Полной емкостью поглощения ионита называется количество катионов и анионов, поглощенных 1 г ионита. Емкость поглощения выражается в миллиграмм-эквивалентах на 1 г абсолютно сухого ионита.