Проектирование привода к ленточному конвейеру
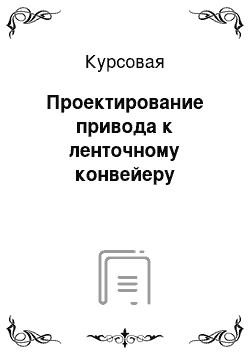
Пусть КПД каждой червячной передачи равно 0.85, потери в опорах валов 0.993, потери в муфтах — 0.992. Тогда мощность на приводном валу Вт Значит подойдет электродвигатель серии АИР исполнения IM1081 типа АИР71В4 номинальной мощностью 0.75 кВт и частотой вращения 1500 мин-1. Отношение пускового момента к номинальному у этого двигателя равно 2, а по заданию перегрузки при пуске равны только 40… Читать ещё >
Проектирование привода к ленточному конвейеру (реферат, курсовая, диплом, контрольная)
Проектирование привода к ленточному конвейеру
1. Задание Спроектировать привод к ленточному конвейеру по схеме:
Окружное усилие барабана P = 3 кН, окружная скорость барабана v = 0.14 м/с, диаметр барабана D = 450 мм.
Привод состоит из последовательно соединенных электродвигателя M, муфты A, двухступенчатого червячного редуктора и муфты B.
В своем проекте я подберу электродвигатель и рассчитаю двухступенчатый червячный редуктор. Основным критерием проектирования выберу минимальные размеры редуктора. Для этого материалы валов, червяков и червячных колес буду выбирать по их прочности, не взирая на стоимость. Класс точности выбираю из этих же соображений: 7 как наилучший из возможных в реальных условиях.
2. Подбор электродвигателя Сначала определю номинальную мощность на выходе привода.
Угловая скорость равна червячный редуктор проектирование рад/с Рабочий момент равен Нм И мощность равна Вт, А число оборотов в минуту мин-1
Пусть КПД каждой червячной передачи равно 0.85, потери в опорах валов 0.993, потери в муфтах — 0.992. Тогда мощность на приводном валу Вт Значит подойдет электродвигатель серии АИР исполнения IM1081 типа АИР71В4 номинальной мощностью 0.75 кВт и частотой вращения 1500 мин-1. Отношение пускового момента к номинальному у этого двигателя равно 2, а по заданию перегрузки при пуске равны только 40%.
3. Параметры передач В данном случае оправдано использование двухступенчатой червячной передачи, т.к. необходимо на выходе получить достаточно большой момент при небольшой частоте оборотов.
Общее передаточное число редуктора равно Обычно, судя по червячным редукторам, выпускаемым НКМЗ, в двухступенчатых червячных редукторах передаточное число быстроходной передачи в 3−4 раза превышает передаточное число тихоходной передачи. Из ряда стандартных значений выберу u1 = 31.5, u2 = 8. При этом общее передаточное число, отклонение от необходимого составит 0.5%. Остальные параметры распределятся так:
Номер передачи | Мощность, Вт | Угловая скорость червяка, рад/с | Момент червяка, Нм | Частота вращения червяка, мин-1 | |
Задаю числа зубьев червяков z1 = 2, z3 = 4, получится число зубьев червячных колес:
При этом число зубьев червячных колес не превышает 80, что положительно сказывается на прочности зубьев, и больше 28, что уменьшает подрез зуба.
4. Расчет быстроходной передачи Исходя из того, что выбор более прочных материалов должен обеспечить меньший размер редуктора, выбираю материалы: для червяка — сталь ст. 12ХН3А, термообработка — цементация и закалка, витки шлифовать и полировать, HRC 60; для венца колеса — бронза БРОФ10−1 (отливка в кокиль), с показателями: Н/мм2, Н/мм2.
Скорость скольжения в зацеплении предварительно оцениваю по приближенной зависимости м/с Суммарное эквивалентное число циклов перемен напряжений при переменном режиме нагрузки (по графику нагрузки) При показателе степени x = 9 NЭF = 6.6106 часов; при x = 4 NЭH = 9.2106 часов.
Коэффициенты долговечности Значит допускаемое контактное напряжение для выбранного материала венца составит Н/мм2
А допускаемое напряжение изгиба Н/мм2
Так как должно выполняться соотношение q 0.25z2, выбираю q = 16.
Определяю коэффициент нагрузки. Для этого по коэффициентам графика нагрузки определяю коэффициент x по формуле По таблице 4.6 коэффициент деформации = 163.
И коэффициент характера изменения нагрузки
Предварительно предполагаю, что коэффициент динамичности нагрузки Kv = 1.2.
И тогда коэффициент нагрузки Межосевое расстояние, как расчет на контактную выносливость, выполняю по формуле (где M2 — в Hмм, []H — в H/мм2, aw — в мм):
При этом модуль будет равен мм Это стандартное значение модуля. Все равно исходя из модуля пересчитаю межосевое расстояние:
мм Основные размеры червяка Делительный диаметрмм Диаметр вершин витковмм Диаметр впадин витковмм Длина нарезанной частимм С учетом рекомендаций в пусть b1 = 55 мм Делительный угол подъема Основные размеры венца червячного колеса Делительный диаметр мм Диаметр вершин витков мм Диаметр впадин витков мм Наибольший диаметр колеса мм Ширина венца мм
При всем при этом окружная скорость червяка равна м/с Теперь можно точно посчитать скорость скольжения м/с При этой скорости коэффициент трения (по таблице 4.4 [1]) равен f' = 0.032, а приведенный угол трения равен ' = 150'.
КПД передачи с учетом потерь в опорах, потерь на разбрызгивание и перемешивание масла По таблице 4.7 при данной скорости скольжения выясняю, что при 7 степени точности коэффициент неравномерности нагрузки Kv = 1.0.
Уточненный коэффициент нагрузки Проверяю контактное напряжение Н/мм2
200 < 223.2 — ниже допустимого на 10%
Проверю прочность зубьев червячного колеса на изгиб. Эквивалентное число зубьев шт.
Коэффициент формы зуба по таблице 4.5 YF = 2.12.
Напряжение изгиба Н/мм2
32.9 < 57.5 — условие прочности выполняется.
5. Расчет тихоходной передачи Пусть материалы и термическая обработка будут те же, что и для тихоходной передачи.
Скорость скольжения должна быть в u1 раз меньше, чем в быстроходной передаче, т. е.
м/с Суммарное эквивалентное число циклов напряжений тоже в u1 раз меньше, т. е.
часов часов При этом коэффициенты долговечности будут иметь граничные значения: KFL = 1, KHL = 1.15.
Допускаемое контактное напряжение Н/мм2
А допускаемое напряжение изгиба Н/мм2
Из соотношения q2 0.25z4, выбираю q2 = 8.
Коэффициент деформации будет равен = 47.
Коэффициент характера изменения нагрузки Коэффициент динамичности нагрузки по таблице 4.7 равен 1. Значит коэффициент нагрузки K = 1.085.
И тогда межосевое расстояние равно мм Модуль мм По ГОСТ 2144–76 выбираю модуль 8 мм Пересчитаю межосевое расстояние мм Основные размеры червяка Делительный диаметрмм Диаметр вершин витковмм Диаметр впадин витковмм Длина нарезанной частимм С учетом рекомендаций в пусть b3 = 148 мм Делительный угол подъема Основные размеры венца червячного колеса Делительный диаметрмм Диаметр вершин витковмм Диаметр впадин витковмм Наибольший диаметр колесамм Ширина венцамм Окружная скорость червяка м/с Скорость скольжения м/с При этой скорости коэффициент трения f' = 0.085, приведенный угол трения ' = 452'.
КПД передачи Проверяю контактное напряжение Н/мм2
201 < 254 — условие прочности соблюдается Проверю прочность зубьев червячного колеса на изгиб. Эквивалентное число зубьев шт.
Коэффициент формы зуба при этом YF = 2.22.
Напряжение изгиба Н/мм2
70 < 71 — условие прочности соблюдается Так как уточнился КПД редуктора, проверю мощность на приводном валу Вт Все равно мощности двигателя хватает.
6. Предварительный расчет валов редуктора и конструирование червяков и червячных колес Крутящие моменты в поперечных сечениях валов Нм Нм Нм Ведущий вал Витки червяка выполнены заодно с валом. Минимальный диаметр вала по расчету на кручение при []K = 25Н/мм2
мм Для соединения его с валом электродвигателя целесообразно выбрать диаметр выходного конца как у электродвигателя — 19 мм и соединить их стандартной муфтой. Диаметры подшипниковых шеек — 20 мм.
Ориентировочные размеры показаны на эскизе.
Промежуточный вал Минимальный диаметр вала мм На валу выполнены витки червяка тихоходной передачи и на шпонку будет посажено червячное колесо быстроходной передачи. Выберу диаметры с небольшим запасом. Ориентировочные размеры — на эскизе.
Ведомый вал Минимальный диаметр вала мм Пусть dв3 = 55 мм. И такие же будут диаметры подшипниковых шеек. Диаметр вала в месте посадки червячного колеса — 60 мм. А длина вала пусть будет как у ведущего.
Параметры червячных колес Диаметр ступицы червячного колеса определяется по формуле:
Пусть dст2 = 60 мм, dст4 = 100 мм.
Длина ступицы червячного колеса определяется по формуле:
Принимаю lст2 = 42 мм, lст4 = 80 мм.
7. Параметры корпуса редуктора Корпус будет литой, чугунный, состоящий из корпусной детали и крышки.
Толщины стенок, исходя из межосевого расстояния тихоходной передачи:
корпусамм, пусть = 8 мм;
крышкимм, пусть 1 = 8 мм.
Толщина фланцев корпуса и крышки мм, пусть это будет 10 мм Толщина нижнего пояса корпуса мм Диаметры болтов:
фундаментныхмм, придется брать М20
винты крышек подшипников — М8
соединение корпуса с крышкой — М10
8. Первый этап компоновки редуктора В двух проекциях в масштабе набросаю компоновочный чертеж для определения внутренних габаритов и размещения валов, колес и подшипников. Главный вопрос — насколько близко разместятся первый червяк и последнее червячное колесо.
Оставляю принятые ранее размеры валов.
Так как в червячном зацеплении возникают значительные осевые усилия, подшипники выбираю радиально-упорные: для ведущего вала — шариковые, для двух других — роликовые конические.
9. Проверка долговечности подшипников Для начала определю усилия в подшипниках. Для этого в изометрии изображу валы, колеса с указанием действующих сил.
Окружное усилие на червячном колесе, равное осевому усилию на червяке Н
Н Окружное усилие на червяке, равное осевому усилию на колесе
Н Н
Радиальные усилия Н
Н Расстояния между опорами, колесами и червяками определены при расчете валов.
Реакции опор Н
Н Для определения прочих реакций буду составлять уравнения моментов:
Н Н
Проверка:
Н Н
Проверка:
Н Н
Проверка:
Н Н
Проверка:
Суммарные реакции:
Н Н
Н Н
Н Н
Подшипники ведущего вала Предварительно выберу радиально-упорные подшипники средней серии. По диаметру выбираю подшипники 46 304 с параметрами: C = 13.7 кН, С0 = 8.99 кН, = 26.
По таблице 7.3 коэффициент осевого нагружения e = 0.68.
Осевые составляющие радиальных реакций:
Н Н
Более нагружен подшипник 2, долговечность буду определять по нему.
;
Н; Н Отношение, значит осевую нагрузку учитываю при определении эквивалентной (из табл. 7.1−7.3 [1]: X = 0.41; Y = 0.87; V = 1; K = 1; KT = 1):
Н Расчетная долговечность млн. об.
тыс. часов, А время работы редуктора (по графику нагрузки) часов Выбранные подшипники подходят.
Подшипники промежуточного вала Здесь пусть будут роликовые конические подшипники 7206 с параметрами: C = 29.2 кН, С0 = 21.9 кН, e = 0.365, X = 0.4, Y = 1.645.
Осевые составляющие Н
Н Расчет буду вести по подшипнику 4, как более нагруженному.
Н; Н
— осевую нагрузку надо учитывать.
Н Расчетная долговечность млн. об.
тыс. часов Выбранные подшипники подходят.
Подшипники ведомого вала Выбираю роликовые конические подшипники 7211 с параметрами: C = 56.8 кН, С0 = 45.2 кН, e = 0.411, X = 0.4, Y = 1.459.
Осевые составляющие Н
Н Расчет буду вести по подшипнику 5, как более нагруженному.
Н; Н
— все равно осевую нагрузку надо учитывать.
Н Расчетная долговечность млн. об.
млн. часов Выбранные подшипники подходят — с большим запасом.
10. Второй этап компоновки редуктора Взяв за основу результаты первой компоновки, на листе А1 в масштабе 1:1 выполняю чертеж редуктора в двух проекциях.
Смазка зацепления и подшипников — разбрызгиванием жидкого масла, залитого в корпус на уровень погружения витков червячного колеса быстроходной передачи. Так как червяк этой передачи имеет большую скорость вращения и близко расположен от червячного колеса тихоходной передачи, он будет забрызгивать масло на это колесо и таким образом смазывать вторую передачу. В качестве смазки выбираю масло индустриальное И-100А.
Уплотнение валов обеспечивается щелевыми уплотнениями с кольцевыми проточками, заполняемыми пластичной смазкой. В крышке люка — отдушина, совмещенная с ручкой. В корпусе есть пробка для спуска масла и жезловый маслоуказатель. Червячные колеса выполнены насаживанием бронзового венца на чугунный центр с натягом. Венец закрепляется винтами, выступающую часть которых после завинчивания спиливают и раскерняют.
Для соединения с мотором использую муфту МУВП по ГОСТ 21 424–75 для диаметра вала 20 мм. На выходе будет кулачково-дисковая муфта по ГОСТ 20 720–81 на диаметр вала 56 мм, тип 1, исполнение 2.
11. Тепловой расчет Площадь теплоотводящей поверхности очень приблизительно составляет F 0.55 м2.
Условие работы редуктора без перегрева Допускаемый перепад температур [t] = 40C.
Мощность на входном валу N0 = 86.6 Вт.
Считаю, что циркуляция воздуха достаточно хорошая и коэффициент теплопередачи kt = 17 Вт/(м2С).
Отсюда
12. Уточненный расчет валов Проверю стрелу прогиба червяков.
Приведенный момент инерции поперечного сечения червяков вычисляется по формуле мм2
мм2
Стрела прогиба вычисляется по формуле Так как к сожалению я не нашел модуля упругости для используемой мной стали ст. 12ХН3А, для расчета использую модуль упругости стали ст. 3: E = 2.1105 МПа.
мм мм Допускаемый прогиб мм мм Жесткость достаточная Червячный вал на прочность проверять не имеет смысла, так как размеры его поперечных сечений были взяты с двукратным запасом, для согласования с электромотором.
Промежуточный вал Промежуточный вал совершенно очевидно имеет смысл проверить только в месте насаживания червячного колеса. Здесь концентрацию напряжений вызывает наличие шпоночной канавки. Для расчета буду пользоваться схемой сил реакций в разделе 9.
Материал вала — сталь ст. 12ХН3А, среднее значение в = 900 Н/мм2. Предел выносливости при симметричном цикле изгиба Н/мм2, предел выносливости при симметричном цикле касательных напряженийН/мм2.
По таблице 6.5 [1]: k = k = 1.9.
По таблице 6.8 [1]: = 0.86, = 0.75.
Коэффициенты = 0.27, = 0.1.
Крутящий момент MK = 103 Нм.
Изгибающий момент в горизонтальной плоскости Нмм Изгибающий момент в вертикальной плоскости Нмм Суммарный изгибающий момент Нмм Момент сопротивления кручению (d = 35 мм, b = 10 мм, c = 5 мм) мм3
Момент сопротивления изгибу мм3
Амплитуда и среднее напряжение цикла касательных напряжений изгиба Н/мм2
Амплитуда нормальных напряжений изгиба Н/мм2
Среднее напряжение Н/мм2
Коэффициент запаса прочности по нормальным напряжениям Коэффициент запаса прочности по касательным напряжениям Результирующий коэффициент запаса прочности Такой большой запас прочности говорит о том, что задачу уменьшения габаритов редуктора я выполнил не очень хорошо. Видимо сказалось отсутствие опыта.
Ведомый вал Ведомый вал точно также совершенно очевидно имеет смысл проверить только в месте присоединения муфты — там наименьший диаметр вала при наличии шпоночной канавки. В этом расчете все коэффициенты такие же, как в предыдущем, кроме = 0.68.
Крутящий момент MK = 675 Нм Момент сопротивления кручению (d = 55 мм, b = 16 мм, c = 6 мм) мм3
Амплитуда и среднее напряжение цикла касательных напряжений изгиба Н/мм2
Коэффициент запаса прочности
— весьма большой запас Т. е. можно было диаметры данных валов брать как минимум в 2.3 раза меньше. Видимо, формулы предварительной оценки диаметра вала выведены уже с достаточным запасом прочности, и учитывают рядовую сталь в качестве материала.
13. Проверка прочности шпоночного соединения Шпонки призматические со скругленными торцами. Материал шпонок — сталь 45 нормализованная.
Условие прочности на смятие Допускаемые напряжения смятия при стальной ступице []см = 100 200 Н/мм2, при чугунной ступице []см = 5070 Н/мм2.
Ведущий вал
d = 19 мм, b = 6 мм, h = 6 мм, t1 = 3.5 мм, l = 42 мм, M = 3.25 Нм Промежуточный вал
d = 35 мм, b = 10 мм, h = 8 мм, t1 = 5 мм, l = 38 мм, M = 86.2 Нм Ведомый вал
d = 55 мм, b = 16 мм, h = 10 мм, t1 = 6 мм, l = 48 мм, M = 675 Нм
14. Сборка редуктора Перед сборкой внутреннюю полость корпуса тщательно покрывают маслостойкой краской. Сборку редуктора производят в соответствии с чертежом общего вида.
Начинают сборку с того, что в промежуточный вал закладывают шпонку и напрессовывают колесо до упора в бурт вала; затем надевают подшипники, предварительно нагрев их в масле до необходимой температуры. Собранный вал вставляют в корпус и устанавливают крышки подшипников, смазав пластичной смазкой кольцевые проточки сквозной крышки.
Затем на червячный вал надевают предварительно нагретые в масле подшипники и тоже вставляют в корпус. Устанавливают крышки подшипников.
В ведомый вал тоже закладывают шпонку, напрессовывают колесо до упора и надевают разогретые подшипники. Собранный вал укладывают в основание корпуса.
Надевают крышку корпуса, предварительно покрыв поверхности стыка фланцев спиртовым лаком. Затягивают болты крепления крышки к корпусу. Устанавливают крышки подшипников последнего вала, не забыв смазать пластичной смазкой кольцевые проточки сквозной крышки.
Ввертывают пробку маслоспускного отверстия с прокладкой и маслоуказатель. Через смотровое отверстие заливают в редуктор масло так, чтобы в него было погружено червячное колесо быстроходной передачи на глубину зуба. Закрывают смотровое отверстие крышкой.
Собранный редуктор обкатывают и испытывают на стенде в соответствии с техническими условиями.
Привод монтируется на сваренной из швеллера № 8 раме. Электродвигатель устанавливают соосно на необходимом расстоянии от редуктора, соединив их через муфту.
15. Список литературы
1. С. А. Чернавский Курсовое проектирование деталей машин, М.: Машиностроение, 1979. — 351 с.
2. М. Н. Иванов Детали машин, М.: Высшая школа, 1984. — 336 с.
3. В. И. Ануфриев Справочник конструктора-машиностроителя в трех томах, М.: Машиностроение, 2001.
4. Э. М. Чаусовский СПРАВОЧНОЕ ПОСОБИЕ КОНСТРУКТОРА, http://manual.h1.ru/const/table_of_contents.html