Расчет и проектирование режущих инструментов
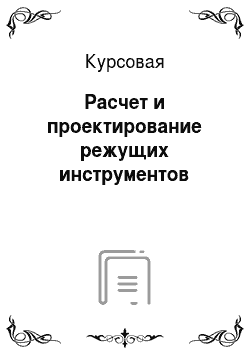
Протяжки — металлоемкий, сложный в изготовлении и поэтому дорогой инструмент. Экономическая целесообразность их применения оправдывается при обеспечении оптимальных элементов конструкций и режимов резания, качественном изготовлении протяжек и правильной эксплуатации. Определяем цилиндрические обдирочные зубья в секции. Для уменьшения длины протяжки, данные зубья располагают после фасочных, а при… Читать ещё >
Расчет и проектирование режущих инструментов (реферат, курсовая, диплом, контрольная)
Федеральное агентство по высшему образованию Государственное образовательное учреждение высшего профессионального образования Сарапульский политехнический институт (филиал) Ижевского государственного технического университета Кафедра ТММСиИ Пояснительная записка к курсовому проекту по дисциплине: «Режущий инструмент»
на тему: «Расчет и проектирование режущих инструментов»
2007 г.
1. Расчет и проектирование призматического фасонного резца
2. Расчет и проектирование шлицевой протяжки Список литературы
В данной курсовой работе спроектированы два режущих инструмента: фасонный призматический резец и шлицевая протяжка.
Фасонные резцы применяют в качестве основного вида режущего инструмента для обработки фасонных деталей в крупносерийном и массовом производстве при частичной или полной автоматизации процессов механической обработки. Фасонные резцы обеспечивают высокую производительность, точные форму и размеры однотипных деталей.
Протяжка — многолезвийный инструмент с рядом последовательно выступающих одно за другим лезвиями в направлении, перпендикулярном к направлению скорости главного движения. Предназначается для обработки при поступательном главном движении резания и отсутствия движения подачи.
Протяжки имеют значительные преимущества перед инструментами других видов. Они являются самыми высокопроизводительными инструментами, примерно в сто и более раз производительнее зенкеров и разверток. При протягивании совмещаются операции черновой, получистовой и чистовой обработки. Это повышает производительность, снижает число применяемых режущих и мерительных инструментов, уменьшает число станков и технологической оснастки.
Многошлицевые отверстия в настоящее время обрабатывают только протягиванием.
Протяжки — металлоемкий, сложный в изготовлении и поэтому дорогой инструмент. Экономическая целесообразность их применения оправдывается при обеспечении оптимальных элементов конструкций и режимов резания, качественном изготовлении протяжек и правильной эксплуатации.
1. Расчет и проектирование призматического фасонного резца
Исходные данные:
Рассчитать и сконструировать фасонный призматический резец для обработки заготовки из прутка диаметром 20 мм марки 40Х, с пределом прочности ув = 600 МПа. Заготовка обрабатывается с подготовкой под последующее отрезание.
Данные размеров приведены на рис. 1.
рис. 1 Эскиз заготовки Расчетная часть:
1. Выбор геометрических параметров резца.
Для наружной точки профиля фасонного резца задаем передний и задний углы. Передний угол г выбираем в зависимости от свойств обрабатываемого материала, г = 20є. Задний угол б принимаем из интервала 10−12є, учитывая, что при больших значениях заднего угла уменьшается износ лезвия, выбираем б = 12є.
2. Выбор конструктивных параметров резца.
а) Высота резца.
Н = 75 мм.
б) Ширина профиля.
рис. 2 Выбор конструктивных параметров резца
Lр = Lд + S1 + S2 + S3 + S4,
где Lд — ширина обрабатываемой детали;
S1 — дополнительная режущая кромка, подготавливающая отрезку детали, если заготовкой служит пруток;
S2 — дополнительная режущая кромка, обрабатывающая фаску или часть детали, срезаемую при отрезке;
S3 — перекрытие, имеющее место при обработке фасок, S3 = 1−2 мм;
S4 — упрочняющая дополнительная режущая кромка, S4 = 2−5 мм;
S5 — ширина фаски под отрезку, должна быть несколько больше ширины режущей кромки отрезного резца.
3. Коррекционный расчет конструируемого призматического резца проводим вычислением расстояния от прямолинейной образующей точки до параллельных ей прямолинейных образующих задней поверхности резца, проведенных через узловые контуры точек. Эти расстояния измеряют в плоскости, параллельной к задней фасонной поверхности призматического резца (размеры Р2, Р3, Р4, Р5, Р6).
4. Размеры Р2, Р3, Р4, Р5, Р6 определяем исходя из следующих условий:
(1)
(2)
(3)
(4)
(5)
(6)
(7)
(8)
(9)
Полученные данные представляем в виде таблицы:
Р2 | 0,449 | С2 | 0,530 | |
Р3 | 2,220 | С3 | 2,618 | |
Р4 | 2,220 | С4 | 2,618 | |
Р5 | 6,126 | С5 | 7,224 | |
Р6 | 9,759 | С6 | 11,508 | |
2. Расчет и проектирование шлицевой протяжки
Исходные данные Рассчитать и сконструировать шлицевую протяжку для обработки шлицевой втулки из стали 40ХН с твердостью НВ 269. Наружный диаметр шлицевого отверстия D, внутренний диаметр шлицевого отверстия d, число шлицев z, ширина шлица b, длина протягивания L. Центрирование по наружному диаметру D (ГОСТ 11 399 — 80). Диаметр отверстия для протягивания d0. Станок горизонтально — протяжной 7Б520. Технические требования на протяжку по ГОСТ 6767– — 79.
D (H7) = 40 мм;
d (H11) = 35 мм;
b (H12) = 10 мм;
n = 6;
d0 = 34 мм;
L = 75 мм;
f = 2 мм;
Станок горизонтально — протяжной 7Б520:
Максимальная длина хода штока hштока=1600 мм;
Номинальное тяговое усилие Q=20 000 кг.
рис. 3
Расчет шлицевой протяжки
1 Группу обрабатываемости устанавливаем по таблице П1 ([2], стр. 200). Сталь 40ХН относится ко 2-ой группе обрабатываемости.
2 Группу качества назначаем 2-ую таблице П2 ([2], стр. 203).
3. За материал рабочей части протяжки принимаем быстрорежущую сталь Р6АМ5 ([2], табл. П3, стр. 203).
4. Конструкцию протяжки принимаем с приваренным хвостовиком, материал хвостовика — сталь 40Х. Конструкцию хвостовика и размеры принимаем с учетом размеров патрона по учебному пособию ([2], табл. П4, стр. 205). Диаметр переднего хвостовика Dхв=28мм, диаметр заднего хвостовика Dз хв=22мм. Площадь опасного сечения Fоп=380,1 мм2.
Усилие, допустимое прочностью этого хвостовика:
Рхв=[у]р· Fоп (1)
где[у]р — допустимое напряжении при растяжении, МПа
[у]р = 300 МПа ([2], стр. 51)
Рхв=300МПа · 380,1 мм2=114 030 Н (2)
5 Передний угол черновых и переходных зубьев г=15°, чистовых и калибрующих г=18°
Задний угол б0=3°; бч=2°; бк=1°.
Допуски на передние и задние углы по ГОСТ 9126– — 76.
6 Скорость резания определяем из таблицы П6 ([2], стр. 208).
хрез=6 м/мин. Поправочный коэффициент на скорость резания в зависимости от марки инструментальной стали равен 1. Поэтому хрез=6 м/мин.
7 Наибольшая толщина срезаемого слоя цилиндрических зубьев Sz=0,06 мм, наибольшая толщина срезаемого слоя для шлицевых зубьев Sz=0,25 мм. Из двух значений окончательно принимаем для черновых зубьев всех частей протяжки минимальную величину, т. е. Sz=0,06 мм
8 Максимальная глубина стружечной канавки:
(3)
Где Рдоп — наибольшее допускаемое усилие станка:
Рдоп=0,9· Q (4)
Рдоп=0,9· 20 000=18000кг
мм (5)
9 Шаг зубьев:
(7)
=12.
10 Количество зубьев работающих одновременно:
; (8)
зуба.
Принимаем zi=5.
11 Проводим корректировку шага:
(9)
мм
12 Размеры и форму стружечной канавки для t=10 выбираем по учебному пособию ([2], табл. П19, стр. 217).
h=4; r=2; b=3,5; R=6; Fакт.=12,6 мм2; Nпрофиля=7.
13 Определяем величину номинального припуска — А, обработанных перед протягиванием сверлом или зенкером.
14 Определяем число режущих зубьев — Zp.
(10)
15 Определяем максимально допустимую силу резания Рмах. Принимаем Рмах наименьший из трех сил: Рст, Рхв, Ро.п.:
Рст=0,8· Q (11)
Рст=0,8· 20 000·9,81=156 960Н Рхв=114 030 (см. п. 4)
Ро.п =Fo.п.· [у]р (12)
[у]р = 400 МПа ([2], стр. 51).
Ро.п =380,1 · 400=152 040Н Следовательно, принимаем Рмах= Рст =114 030Н
16 Определяем размеры фасочных зубьев:
с =f· ctgв (14)
с =2· ctg36°=2,75 мм
b1=b+2· f (15)
b1=6+2· 2=10мм Диаметр первого фасочного зуба равен диаметру:
d1=d0 — 0,05 (16)
d1=32,2 — 0,05=32.15мм Диаметр последнего фасочного зуба :
d2 =d0 + 2· f·tgв + (0,3…0,4) (17)
d2 =32.2+2· 2·tg36° + (0,3…0,4)=35.46мм
17 Величину Х (рис. 2 [4], стр.4), необходимую для настроя, определяем по формуле:
(18)
где б2 =(90 — в) — б1 (19)
sinб1=b1/d0 (20)
sinб1=10/32.2мм=0,31
отсюда определяем б1=17°15'
б2=54°-17°15'=36°44'
мм
Диаметр последнего цилиндрического зуба:
d3=dмах — m (21)
Диаметр последнего шлицевого зуба:
d5=d'мах — m (22)
где dмах — внутренний диаметр шлицев + допуск=33,16 мм
d'мах — наружный диаметр шлицев + допуск=38,025 мм
m берется из таблицы 3 ([4], стр. 8) m=0,02 мм.
d3=33,16мм — 0,02=33,14 мм
d5=38,025мм — 0,02=38,00 мм
Диаметр первого цилиндрического зуба будет равен d0 и диаметр первого шлицевого зуба d4 равен диаметру последнего цилиндрического зуба d3.
d4= d3 — 0,05=33,14 — 0,05=33,09 мм
18 Общий перепад зубьев каждой группы:
Фасочных :Аф=d2 — d1 (23)
Аф=35.46мм — 32.15мм=3,31 мм
Цилиндрических: Ац=d3 — d1 (24)
Ац=33,14мм — 32,15мм=0,99 мм Шлицевых: Аш=d5 — d4 (25)
Аш=38,00мм — 33,09мм=4,91 мм
19 Перепады обдирочных зубьев:
Цилиндрических:А3= Ац — А4 (26)
Шлицевых:А5= Аш — А4 (27)
где А4 — припуск на чистовые зубья для шлицевых протяжек, назначаются в зависимости от шероховатости обработанной поверхности и от Sz ([4], табл.4 стр. 9). А4=0,10
А3= 0,99мм — 0,10мм=0,89 мм
А5= 4,91мм — 0,10мм=7,81 мм Фасонная часть протяжки имеет только обдирочные зубья.
20 Определяем цилиндрические обдирочные зубья в секции. Для уменьшения длины протяжки, данные зубья располагают после фасочных, а при малой длине отверстия — после шлицевых. Необходимо, чтобы длина цилиндрической части не превышала длины отверстий изделия.
Подъем на зуб на цилиндрической части целесообразно делать на каждый зуб, так как фасочные зубья являются прорезными. Исключением является случай, когда длина режущих кромок между соседними шлицами:
(28)
Тогда цилиндрические обдирочные зубья собирают секциями по два зуба.
(29)
Так как 44,6>7,48, то обдирочные цилиндрические зубья выполняем секцией из двух зубьев.
21 Периметры режущих кромок обдирочных зубьев:
для цилиндрических при Zc=2:
(30)
мм для шлицевых Zc=2:
(31)
мм
22 Для цилиндрической и шлицевой частей протяжки рассчитываем усилие протягивания:
(32)
где Рsz — усилие резания на 1 мм длины режущей кромки ([4], табл.5 стр. 11).
zi — наибольшее число зубьев в зацеплении Р=21,8кгс/мм· 10·5=1090кгс/мм
23 Обдирочные шлицевые зубы выполняют секцией из двух зубьев. Определим число обдирочных зубьев:
Фасочных :
(33)
Цилиндрических: (34)
Шлицевых: (35)
24 Общее число обдирочных зубьев:
(36)
25 Общая длина обдирочных частей протяжки:
(37)
мм
26 Определяем число чистовых и калибрующих зубьев Цилиндрических: (38)
Шлицевых: (39)
где zчц zч.шл zк.ц zк.шл назначаем в зависимости от класса точности ([4], табл.4 стр. 9).
27 Шаг калибрующих зубьев:
tк=0,7t (40)
tк=0,7· 10мм=7мм
28 Длина цилиндрической чистовой и калибрующей частей:
(41)
мм
29 Длина шлицевой части:
(42)
мм
30 Общая длина рабочей части протяжки:
lраб= l0 + l4 + l6 (43)
lраб= 770 + 42+49 =861мм
34 Общая длина всей протяжки:
L=l1+lраб+lз.н. (44)
где l1 — длина хвостовика до первого зуба, l1=175мм
lз.н. — длина задней направляющей.
lз.н. примем равным 40 мм ([5], табл. 5.17 стр. 158).
Для протяжки:
L=175+861+40=1076мм.
35 Определяем окончательные диаметры и число зубьев протяжки z', для чего составляем таблицу распределительных параметров.
Диаметр зубьев | Вид зубьев | ||||
№ зуба | Допуск | б | |||
33,95 | — 0,016 | 3°±30' | Фасочные | ||
34,07 | |||||
34,19 | |||||
34,31 | |||||
34,43 | |||||
34,55 | |||||
34,67 | |||||
34,79 | |||||
34,91 | |||||
35,03 | |||||
35,15 | |||||
35,27 | |||||
35,39 | |||||
35,51 | |||||
35,63 | |||||
35,75 | |||||
35,87 | |||||
35,99 | |||||
36,11 | |||||
36,23 | |||||
36,35 | |||||
36,47 | |||||
36,59 | |||||
36,71 | |||||
36,83 | |||||
36,95 | |||||
37,26 | |||||
34,2 | — 0,007 | 1°±15' | Цилиндрические | ||
34,32 | |||||
34,44 | |||||
34,56 | |||||
34,68 | |||||
34,8 | |||||
34,92 | |||||
35,14 | |||||
35,09 | — 0,016 | 3°±30' | Шлице вые | ||
35,21 | |||||
35,33 | |||||
Диаметр зубьев | Вид зубьев | ||||
№ зуба | Допуск | б | |||
35,45 | — 0,016 | 3°±30' | Шлицевые | ||
35,57 | |||||
35,69 | |||||
35,81 | |||||
35,93 | |||||
36,05 | |||||
36,17 | |||||
36,29 | |||||
36,41 | |||||
36,53 | |||||
36,65 | |||||
36,77 | |||||
36,89 | |||||
37,01 | |||||
37,13 | |||||
37,25 | |||||
37,37 | |||||
37,49 | |||||
37,61 | |||||
37,73 | |||||
37,85 | |||||
37,97 | |||||
38,09 | |||||
38,21 | |||||
38,33 | |||||
38,45 | |||||
38,57 | |||||
38,69 | |||||
38,81 | |||||
38,93 | |||||
39,05 | |||||
39,88 | — 0,007 | 2°±30' | Чистовые | ||
39,88 | |||||
1°±15' | Калибрующие | ||||
36 Устанавливаем элементы профиля зубьев.
37 Окончательно определяем длину рабочей части протяжки:
фасочная часть (45)
27· 10мм=270мм цилиндрическая: (46)
8· 10мм=80мм шлицевая обдирочная часть (48)
мм шлицевая чистовая и калибрующая (49)
мм
38 Окончательно определяем общую длину:
(50)
L=250мм+270мм+80+420мм+42мм+40мм=1102мм
39 Находим число и размеры выкружек
1) для фасочных зубьев число выкружек равно числу шлицев отверстия то есть равно 10, а размеры берем из таблицы 6 ([4], стр. 14).
2) на цилиндрических обдирочных зубьях радиус выкружек нарезаем таким же, как и для шлицевых зубьев, а ширину режущего лезвия Бк — равной величине Б.
40 Определяем машинное время за один проход при протягивании:
мин (52)
гдеL — длина рабочего хода протяжки;
К — коэффициент, учитывающий соотношение между скоростями рабочего и обратного хода; обычно К=1,4…1,5;
q — количество одновременно обрабатываемых деталей, q =1.
мин.
режущий фасонный резец протяжка
1 Аршинов Р. А., Алексеев Г. А. «Резание металлов и режущий инструмент». Москва: Издательство «Машиностроение», 1968. — 480с., ил.
2 Маргулис Д. К., Тверский М. М., Ашихмин В. Н. и др. — М.: Машиностроение, 1986. — 232 с., ил. — (Б — ка инструментальщика).
3 Методическое руководство для курсового проектирования режущего инструмента «Фасонные резцы» для специальности 0501. / Составитель Шитова Т. В. — Ижевск: Издательство ИМИ, 1984. — 40 с, ил.
4 Методическое указания к расчету шлицевых протяжек (специальность 0501). / Составитель Л. А. Хохряков. — Ижевск: Издательство ИМИ, 1983. — 16 с, ил.
5 Режущий инструмент «Курсовое и дипломное проектирование»
6. Семенченко И. И., Матюшин В. М., Сажаров Г. Н. Проектирование металлорежущих инструментов. — М.: МАШГИЗ, 1963. — 952 с., ил.
7. Схиртладзе А. Г., Новиков В. Ю. Станочные приспособления: Учеб. пособие для вузов. — М.: Высш. шк., 2001. — 110 с., ил.
8 Барановский Ю. В. «Режимы резания металлов». Справочник изд-во «Машиностроение» 1972 г.).