Расчет ректификационной установки
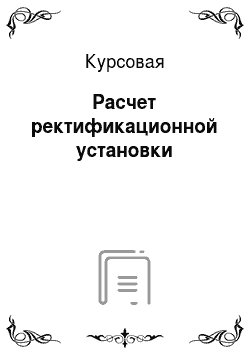
По данным таблицы 3.3 строим кинетическую кривую. Точки А1, А2, А3, …, А10 лежат на рабочих линиях, точки С1, С2, С3, …, С10 — на равновесной кривой. Вычисленные отрезки В1С1, В2С2, В3С3, …, В10С10 откладываются от соответствующих точек С вниз. Кинетическая кривая начинается в начале координат, проходит через точки В1, В2, В3,…, В10 и заканчивается в правом верхнем углу диаграммы у-х (рис. 3.3… Читать ещё >
Расчет ректификационной установки (реферат, курсовая, диплом, контрольная)
Колонные ректификационные аппараты и установки являются важнейшим массообменным оборудованием химических, нефтехимических и других смежных отраслей промышленности. Наибольшее распространение в процессах ректификации получили тарельчатые и насадочные аппараты.
Ректификацией называется процесс разделения однородных гомогенных смесей на составляющие вещества или группы составляющих веществ путем взаимодействия пара и жидкости, не находящихся в термодинамическом равновесии. При взаимодействии пара и жидкости компоненты перераспределяются между фазами: пар обогащается легколетучим компонентом или низкокипящим (НК), а жидкость — высококипящим компонентом (ВК).
В основе любого метода расчета лежит ряд исходных допущений, упрощающих расчетную процедуру. При расчете ректификационной установки принимаем следующие допущения:
1. Состав жидкости, стекающий в куб колонны, равен составу пара, поднимающегося из кипятильника в колонну (xw = yw).
2. Состав пара, поступающего из колонны в дефлегматор, равен составу жидкости, стекающей из дефлегматора в колонну (yp = xp).
3. Скрытые мольные теплоты парообразования компонентов смеси равны, а это значит, что один кмоль сконденсировавшегося пара испаряет один кмоль жидкости, вследствие чего, количество пара, поднимающегося по колонне, не меняется.
4. Исходная смесь поступает в колонну при температуре кипения.
Связь между равновесными концентрациями жидкости и пара для идеальных растворов устанавливается на основании законов Рауля и Дальтона. На основании данных по равновесию могут быть построены графики: 1) кривая равновесия у-х; 2) изобара температур кипения и конденсации t — x, y.
Задание Производительность по исходной смеси — 4 т/ч;
Концентрация ацетона:
в исходной смеси — aF = 40% (масс.),
в дистилляте — aР = 96% (масс.),
в кубовом остатке — aW = 1,8% (масс.).
Температура:
охлаждающей воды — 12 °C, дистиллята после холодильника — 24 °C, кубового остатка после холодильника — 28 °C, исходной смеси — 20 °C.
Давление насыщенного водяного пара — 6,0 кгс/см2,
Коэффициент избытка флегмы — 1,55.
Колонна работает под атмосферным давлением.
Исходная смесь и флегма вводятся в аппарат при температуре кипения.
Расчет проводится в следующей последовательности.
1. Определение производительности по дистилляту и кубовому остатку
Производительность колонны по дистилляту определяем по формуле:
кг/ч = 0,45 кг/с.
Производительность колонны по дистилляту определяем из уравнения:
GW = GF — GP = 4000 — 1622,081 = 2377,919кг/ч = 0.66 кг/с.
Проверка:
4000. 0,4 = 1622,081. 0,96 + 2377,919. 0,018
1600 = 1557,197 + 42,803
1600=1600
2. Определение минимального и действительного флегмового числа
Пересчитываем массовые концентрации в мольные по формуле:
где Х — концентрация низкокипящего компонента, А (ацетона) в бинарной смеси, мол. доли;
а — содержание низкокипящего компонента, А (ацетона) в бинарной смеси, масс. доли;
МА, МВ — молярная масса компонента, А (ацетона) и В (вода) (соответственно).
Молярные массы: ацетон — 58 кг/кмоль.
вода — 18 кг/кмоль.
Тогда концентрация исходной смеси:
;
дистиллята:
;
кубового остатка:
.
Минимальное флегмовое число определяем графо-аналитическим способом. Для этого на основании опытных данных [7, 8], в координатах у-х строим кривую равновесия для смеси ацетон-вода при атмосферном давлении и кривую температур кипения и конденсации.
На диаграмме у-х из точки 1 (хр = ур) через точку 2? (хF, уF*) проводим прямую линию до пересечения с осью у. Отрезок, отсекаемый на оси у, обозначим через Вmax = 0,78. По величине этого отрезка находим минимальное флегмовое число
.
Равновесные данные для смеси ацетон-вода
Содержание компонента А, мол. % | Температура кипения, t, °С | ||
в жидкости (х) | в паре (у) | ||
0,0 | |||
60,3 | 77,9 | ||
69,6 | |||
80,3 | 64,5 | ||
82,7 | 62,6 | ||
84,2 | 61,6 | ||
85,5 | 60,7 | ||
86,9 | 59,8 | ||
88,2 | |||
90,4 | 58,2 | ||
94,3 | 57,5 | ||
100,0 | 56,9 | ||
Действительное флегмовое число определяем, используя уравнение:
R = KR. Rmin = 1,55. 0.1516= 0.2349
На диаграмме у-х наносим линии рабочих концентраций (рабочие линии) для оптимального флегмового числа R = 0,2349: для этого на оси у откладываем отрезок, конец которого соединяем прямой с точкой 1 (хр = ур); точку пересечения этой прямой с вертикальной линией, проведенной с абсциссы хF, обозначим точкой 2 (хF, уF) и, наконец, точку 2 соединяем с точкой 3 (хW = уW). Линии 1−2 и 2−3 являются рабочими линиями для верхней и нижней частей колонны, соответственно.
3. Определение средних значений параметров по колонне, физико-химических и термодинамических констант фаз
Жидкая фаза.
Средняя мольная концентрация в нижней части колонны:
.
Средняя мольная концентрация в верхней части колонны:
.
Средняя мольная концентрация по колонне:
.
Средняя массовая концентрация по колонне:
.
Средняя температура в нижней части колонны:
°С.
Средняя температура в верхней части колонны:
°С.
Средняя температура по колонне:
°С.
Значения tXW, tXF, tXР взяты из диаграммы t — x, y .
Средняя мольная масса Мх ср = МА. Хср + МВ. (1 — Хср),
Мх ср = 58. 0,3075 + 18. (1 — 0,3075) = 30,301 кг/кмоль.
Средняя плотность определяется по формуле:
кг/м3.
где сА и сВ — плотность компонентов, А (ацетона) и В (воды) при температуре tx cp.
сА = 734,066 кг/м3 при tx cp = 71,16 °С [1, с. 512]; Приложение Б.
сВ = 978,14 кг/м3.
Среднюю вязкость рассчитываем по уравнению:
lg мх ср = Хср. lg мА + (1 — Хср). lg мB,
где мА и мВ — динамические коэффициенты вязкости компонентов, А (ацетона) и В (воды), Па.с.
мА = 0,217 МПа. с при tcp = 71,16 °С [1, с. 516]; Приложение Б.
мВ = 0,419 МПа. с.
lg мх ср = 0,3075. lg 0,217 + (1 — 0,3075). lg 0,419 = -0,46 547
мх ср = 0,342 МПа. с = 0,342. 10−3 Па. с.
Среднее поверхностное натяжение определяем по уравнению ух ср = уА. Хср + уB. (1 — Хср),
где уА и уB — поверхностные натяжения компонентов, А (ацетон) и В (вода), н/м.
уА = 17,54. 10−3 н/м при tх cp = 71,16 °С [1, с. 526]:
уВ = 64,61. 10−3 н/м.
ух ср = 17,54. 10−3. 0,3075 + 64,61. 10−3 (1 — 0,3075) = 50,13. 10−3 н/м.
Коэффициент диффузии при средней температуре определяем [1]:
Dx (t) = Dx (20) [1 + b. (t — 20)],
где Dx (20) — коэффициент диффузии при t = 20 °C, м2/с;
здесь м [мПа. с] и с [кг/м3] - вязкость и плотность растворителя (воды) при t = 20 °C; t = tх cp.
Коэффициент диффузии при 20 °C рассчитываем по эмпирическому уравнению [1]:
где VA и VB — мольные объемы компонентов, А (ацетона) и В (воды), см3/моль;
А, В — коэффициенты, зависящие от свойств компонентов, А= 1,0; В = 4,7 [1, с. 269]:
.
Мольные объемы компонентов [1, с. 288]:
VA = 14,8•3+6•3,7+7,4 = 74 см3/моль;
VB = 18,9 см3/моль.
м2/с.
Dx (t) = 1. 10−9 [1 + 0,02 (71,16 — 20)] = 2. 10−9 м2/с.
Паровая фаза.
Средняя мольная концентрация в нижней части колонны:
.
Средняя мольная концентрация в верхней части колонны:
.
Средняя мольная концентрация по колонне:
.
Средняя температура в нижней части колонны: °С.
Средняя температура в верхней части колонны: °С.
Температуры, найдены из диаграммы t — x, y .
Средняя температура по колонне:
°С.
Средняя мольная масса Му ср = МА. уср + МВ. (1 — уср) = 58. 0,6447 + 18. (1 — 0,6447) =
= 43,786 кг/кмоль.
Средняя плотность:
кг/м3.
здесь Т = 273 + tу ср, °С; Р = 1 кгс/см2 (давление в колонне атмосферное).
Средняя вязкость [1]:
где муА и муВ — динамический коэффициент вязкости паров компонента, А (ацетон) и В (вода).
муА = 0,95. 10−5 Па. с при tу cp = 73,91 °С [9, с. 8, 9]:
муВ = 1,23. 10−5 Па.с.
му ср = 0,982. 10−5 Па. с.
Коэффициент диффузии для паровой фазы определяем по уравнению [1]:
где Р — давление кгс/см2 (давление в колонне атмосферное);
Т = 273 + tу ср, °С. м2/с.
4. Определение диаметра колонны
Диаметр колонны определяем по уравнению [1]:
Расход, проходящего по колонне пара, может быть определен:
м3/с.
Скорость пара в колонне определяем по уравнению (2.9). Предварительно принимаем расстояние между тарелками h = 300 мм. Используем ранее найденные сх cp = 818,0299 кг/м3 и су cp = 1,4891 кг/м3. Для колпачковых тарелок С = 0,032. Тогда скорость пара в колонне:
м/с.
Тогда диаметр колонны
м.
Принимаем стандартное значение диаметра колонны D = 0,8 м (см. Приложение В) и уточняем скорость пара в колонне:
м/с.
5. Определение высоты колонны По уравнению находим коэффициент массоотдачи в жидкой фазе:
.
где сх ср — средняя плотность жидкой фазы, кг/м3;
Dх (t) — коэффициент диффузии при средней температуре жидкости, м2/с;
Мх ср — средняя молекулярная масса жидкости, кг/кмоль;
h — линейный размер, h = 1 м;
— диффузионный критерий Прандтля, равный
;
Коэффициент массоотдачи в паровой фазе находим по уравнению (2.19):
.
Общий коэффициент массопередачи Kyf находим из уравнения (2.17):
где — тангенс угла наклона линии равновесия;
у*, х* - равновесные концентрации.
Так как величина m является переменной по высоте колонны, находим ее значение для различных концентраций, используя диаграмму (рис. 1)
В пределах от Хw до Хр выбираем ряд значений Х, для каждого значения Х определяем по диаграмме (рис. 1) величины у* - у, х — х* как разность между равновесной и рабочей линией, а затем по этим значением определяем величину m. Результаты сводим в таблицу 3.2.
Определение коэффициента массопередачи
х | 0,0057 | 0,1 | 0,2 | 0,3 | 0,4 | 0,5 | 0,6 | 0,7 | 0,8 | 0,8816 | |
у*- у | 0,0631 | 0,2942 | 0,0509 | 0,0561 | 0,052 | 0,046 | 0,041 | 0,035 | 0,0379 | 0,0527 | |
хх* | 0,0141 | 0,0659 | 0,2676 | 0,2972 | 0,2736 | 0,2419 | 0,2156 | 0,1825 | 0,1068 | 0,0527 | |
m | 4,4752 | 4,4634 | 0,1902 | 0,1888 | 0,1901 | 0,1902 | 0,1902 | 0,1919 | 0,3549 | 1,000 | |
2,99 | 3,00 | 36,14 | 36,27 | 36,15 | 36,14 | 36,14 | 35,99 | 25,36 | 11,69 | ||
Для построения кинетической кривой воспользуемся формулой:
.
Значения разности (у* - ун) это значения АС = (у* - у) для каждого выбранного значения х в пределах от хw до хр.
Рабочая площадь тарелки может быть найдена из Приложения В, таблица В.1: Fp = 0,395 м².
Мольный расход пара по колонне:
кмоль/с.
По данным таблицы 3.3 строим кинетическую кривую. Точки А1, А2, А3, …, А10 лежат на рабочих линиях, точки С1, С2, С3, …, С10 — на равновесной кривой. Вычисленные отрезки В1С1, В2С2, В3С3, …, В10С10 откладываются от соответствующих точек С вниз. Кинетическая кривая начинается в начале координат, проходит через точки В1, В2, В3,…, В10 и заканчивается в правом верхнем углу диаграммы у-х (рис. 3.3).
Число действительных тарелок, которое обеспечивает заданную четкость разделения, определяется путем построения «ступенек» между рабочими и кинетической линиями. Число ступеней в пределах концентраций XWXP равно числу действительных тарелок.
К построению кинетической кривой
х | 0,0057 | 0,1 | 0,2 | 0,3 | 0,4 | 0,5 | 0,6 | 0,7 | 0,8 | 0,8816 | |
0,09 | 0,09 | 1,12 | 1,13 | 1,12 | 1,12 | 1,12 | 1,12 | 0,79 | 0,36 | ||
мм | 6,31 | 29,42 | 5,09 | 5,61 | 5,20 | 4,60 | 4,10 | 3,50 | 3,79 | 5,27 | |
мм | 5,74 | 26,78 | 1,66 | 1,82 | 1,69 | 1,50 | 1,33 | 1,14 | 1,72 | 3,66 | |
В результате построения (рис. 3.3) получаем число действительных тарелок n= 50, тарелка питания 46-я снизу.
Высоту колонны определяем по уравнению (2.10)
H = (n — 1). h + Hсеп + Hкуб = (50 — 1). 0,3 + 0,8 + 2,0 = 17,5 м.
6. Определение гидравлического сопротивлении колонны с колпачковыми тарелками
Полное гидравлическое сопротивление колонны определяем по уравнению (2.20), а гидравлическое сопротивление тарелки — по уравнению (2.22).
По таблице В.2 Приложения выбираем тарелку типа ТСК-1 для колонны диаметром D = 800 мм. Эта тарелка имеет следующие параметры:
рабочая площадь тарелки Fp = 0,395 м²;
площадь прохода паров Fо = 0,049 м²;
площадь слива Fсл = 0,021 м²;
периметр слива П = 0,57 м;
длина пути слива lx = 0,52 м;
количество колпачков на тарелке m = 24;
диаметр колпачка 80 мм.
Сопротивление сухой тарелки:
Па;
м/с,
где Fo — площадь прохода паров, м2.
Глубина барботажа, согласно уравнению (2.29):
м.
Высота подпора жидкости над сливным порогом по уравнению (2.33):
м,
м3/с;
П = 0,578 м (из характеристики тарелки).
Для дальнейших расчетов примем колпачок капсульный с прямоугольными прорезями шириной b = 4 мм; количество прорезей в одном колпачке z = 20 (см. Приложение, таблицы В.4, В.5). Высоту открытия прорези рассчитываем по уравнению (2.30):
принимаем по таблице В.4 высоту прорези hпр = 20 мм.
Высоту установки колпачка примем hу = 10 мм.
Высоту сливного порога найдем по уравнению (2.31)
hпор = hг. б — hсл + hпр + hу = 0,047 — 0,0127 + 0,020 + 0,01 = 0,064 м.
Тогда величина перепада уровня жидкости на тарелке (по уравнению 2.28)
Сопротивление слоя жидкости на тарелке, согласно уравнению (2.27):
Тогда гидравлическое сопротивление тарелки (пренебрегая ДРу) ДРт = ДРсух + ДРст = 195,05 + 462,23 = 657,28 Па, а гидравлическое сопротивление колонны ДРк = n • ДРт = 50 • 657,28 = 32 864 Па.
Проверим ранее принятое расстояние между тарелками h = 0,3 м. Для этого необходимо рассчитать величину относительного уноса жидкости.
Высота пены, образующейся на тарелке, согласно уравнению (2.35):
Тогда величина относительного уноса жидкости (уравнение 2.34)
0,0245 < 0,1, следовательно, расстояние между тарелками выбрано верно.
Значение коэффициентов К1, К2, К3, К4 и показателя степени n взяты из таблицы В.6 Приложения.
7. Определение диаметра штуцеров
Диаметр штуцера определяем по уравнению:
Штуцер подачи флегмы:
м3/с.
Так как скорости потока принимаем ориентировочно, то можно принять плотность флегмы, как плотность ацетона: сА = 745,55 кг/м3 при t = 60,33 °С.
Принимаем Wф = 0,5 м/с, тогда
м.
Стандартный размер трубы для изготовления штуцера Ш20×4 мм, [6, с. 16].
Штуцер подачи исходной смеси:
; ,
при tXF = 65,41 °С кг/м3,
м3/с.
Принимаем WF = 0,8 м/с, тогда ректификационный колонна термодинамический
м.
Стандартный размер трубы для изготовления штуцера Ш48×4 мм, [6, с. 17].
Штуцер выхода кубового остатка:
м3/с.
сВ = 963,24 кг/м3 — плотность воды при 87,49°С.
Принимаем WW = 0,3 м/с, тогда
м.
Стандартный размер трубы для изготовления штуцера Ш56×3,5 мм, [6, с. 16].
Штуцер выхода кубовой жидкости (подается на кипятильник):
м3/с.
Принимаем Wк. ж = 0,3 м/с, тогда
м.
Стандартный размер трубы для изготовления штуцера Ш56×3,5 мм, [6, с. 17].
Штуцер выхода паров из колонны:
м3/с.
Принимаем Wу = 15 м/с, тогда
м.
Стандартный размер трубы для изготовления штуцера Ш194×6 мм, [6, с. 17].
8. Тепловые расчеты
Подогреватель исходной смеси
Уравнение теплового баланса для подогревателя:
Q = 1,05. GF.. (tXF — tнач) = Gг.п. r,
здесь тепловые потери приняты в размере 5% от полезно затрачиваемой теплоты;
tXF — температура кипения исходной смеси;
tнач — начальная температура (задана).
Удельная теплоемкость исходной смеси
= аF. СА + (1 — аF). СВ, где СА, СВ — удельные теплоемкости ацетона и воды при средней температуре
°С;
СА = 0,5369; СВ = 0,9983, [1, с. 562]; таблица Б.7 Приложения.
= 0,40. 0,5369 + (1 — 0,40). 0,9983 = 0,809 = 3390,238 .
Q = 1,05. GF. (tXF — tнач) = 1,05.. 3390,238 (71,16 — 20) =
=202 352 Вт.
Расход греющего пара:
кг/с,
r = 2095 при Р = 6,0 кгс/см2 [1, c. 550]:
Температура насыщенного водяного пара при Р = 5,8 кгс/см2 составляет 156,7°С [1, c. 550]:
Большая разность температур:
Дtб = 158,1 — 20 = 138,1 °С;
меньшая разность температур:
Дtм = 158,1 — 65,41 = 92,69°С.
Так как, тогда среднюю разность температур определяем по уравнению:
°С.
Коэффициент теплопередачи принимаем ориентировочно равным 300Вт/м2.К [6, с. 47].
Поверхность теплообмена подогревателя исходной смеси
м2.
Принимаем одноходовой кожухотрубчатый теплообменник со следующими характеристиками [6, с. 51]:
— диаметр кожуха 325 мм;
— труба 20×2 мм;
— количество труб в теплообменнике 100 шт;
— длина труб 1,5 м;
— поверхность теплообмена 9,5 м².
Дефлегматор (конденсатор)
Расход теплоты, отдаваемый охлаждающей воде при конденсации паров в дефлегматоре, определяется из уравнения теплового баланса дефлегматора:
QД = GР. (R + 1). rР = GВ. CВ. (tк — tн),
rР = аР. rА + (1 — аР). rВ.
Удельные теплоты парообразования ацетона rА и воды rВ при tХр=57,62 °С:
rА = 521,275; rВ = 2363,395 :
rР = 0,96. 521,275 + (1 — 0,96). 2363,395 = 594,95 .
QД =. (0,2349+ 1). 594,95 .103 = 331 041,39 Вт.
Принимаем температуру охлаждающей воды на выходе из дефлегматора 25 °C, тогда расход охлаждающей воды
кг/с.
Большая разность температур:
Дtб = 57,62 — 25 = 32,62°С;
меньшая разность температур:
Дtм = 23 — 12 = 11 °C.
то
°С.
Принимаем ориентировочно коэффициент теплопередачи К = 500 Вт/м2. К [6, с. 47].
Поверхность теплообмена дефлегматора:
м2.
Принимаем четырехходовой кожухотрубчатый теплообменник со следующими характеристиками [6, с. 51]:
— диаметр кожуха 400 мм;
— труба 20×2 мм;
— количество труб в теплообменнике 181 шт;
— длина труб 3 м;
— поверхность теплообмена 34 м².
Холодильники дистиллята и кубового остатка
Расход теплоты, отдаваемый охлаждающей воде в водяном холодильнике дистиллята, определяется из уравнения теплового баланса:
Q = GР.. (tХр — tр кон) = GВ. CВ. (tк — tн),
где — теплоемкость дистиллята при его средней температуре (tХр + tр кон)/2;
tр кон — конечная температура дистиллята после холодильника, °С (по условию задания).
= аР. СА + (1 — аР). СВ, СА = 0,5388; СВ = 0,9985, при средней температуре °С; [1, с. 562]:
= 0,96. 0,5388 + (1 — 0,96). 0,9985 = 0,56 638 = 2373,141.
Q = GР.. (tXр — tр кон) =. 2373,141 (57,62 — 23) = 37 018,66 Вт.
Расход охлаждающей воды при нагревании ее на 15 °C в холодильнике товарного дистиллята:
кг/с.
Большая разность температур:
Дtб = 57,32 — 27 = 30,32 °С;
меньшая разность температур:
Дtм = 23 — 12 = 11 °C.
Так как, то среднюю разность температур определяем
°С.
При ориентировочном значении К = 400 Вт/м2. К поверхность теплообмена холодильника товарного дистиллята составит
м2.
Принимаем одноходовой кожухотрубчатый теплообменник со следующими характеристиками [6, с. 51]:
— диаметр кожуха 273 мм;
— труба 25×2 мм;
— количество труб в теплообменнике 37 шт;
— длина труб 2 м;
— поверхность теплообмена 6 м².
Расход теплоты, отдаваемый охлаждающей воде в водяном холодильнике кубового остатка, определяется из уравнения теплового баланса:
Q = Gw.. (tХw — tw кон) = GВ. CВ. (tк — tн),
где СW — теплоемкость кубового остатка при его средней температуре (tХw + tW кон)/2;
tW кон — конечная температура кубового остатка после холодильника, °С (по условию задания).
= аw. СА + (1 — аw). СВ, СА = 0,5532; СВ = 1,0, при средней температуре °С; [1, с. 562]:
= 0,01. 0,5532 + (1 — 0,01). 1,0 = 0,996 = 4171,279 .
Q = Gw.. (tXw — tW кон) =. 4171,279 (96,2- 28) =
=187 909,25 Вт.
Расход охлаждающей воды при нагревании ее на 15 °C в холодильнике кубового остатка:
кг/с.
Большая разность температур:
Дtб = 96,2 — 27 = 69,2 °С;
меньшая разность температур:
Дtм = 28 — 12 = 16 °C.
Так как, то среднюю разность температур определяем
°С.
При ориентировочном значении К = 400 Вт/м2. К [6, с. 47], поверхность теплообмена холодильника кубового остатка составит
м2.
Принимаем одноходовой кожухотрубчатый теплообменник со следующими характеристиками [6, с. 51]:
— диаметр кожуха 325 мм;
— труба 20×2 мм;
— количество труб в теплообменнике 100 шт;
— длина труб 4 м;
— поверхность теплообмена 25 м².
Кипятильник (испаритель)
Количество теплоты QК, которое надо подать в куб колонны, определяется из уравнения теплового баланса колонны:
QК = QД + GР. СР. tХр + GW. СW. tХw — GF. СF. tХF + Qпот.
Тепловые потери принимаем 3% от полезно затрачиваемой теплоты; удельные теплоемкости взяты соответственно при tXp = 57,62 °С, tXF = 65,41 °С, tXw = 96,2°С.
СР = аР. СА + (1 — аР). СВ = 0,96. 0,5485 + (1 — 0,96). 0,9998 =
= 0,5756 = 2276,990 .
СF = аF. СА + (1 — аF). СВ = 0,40. 0,554 + (1 — 0,40). 1,0 =
= 0,8171 = 3423,817 .
СW = аW. СА + (1 — аW). СВ = 0,018. 0,581 + (1 — 0,018). 1,009 =
= 0,8341 = 3494,87 .
Расход греющего пара при Р = 6,0 кгс/см2:
кг/с.
Средняя разность температур равна разности между температурой насыщенного пара при Р = 6,0 кгс/см2 и температурой кипения кубового остатка:
Дtср = 158,1 — 96,2 = 61,9°С.
При ориентировочно принятом коэффициенте теплопередачи К = 2000 Вт/м2.К, [6, с. 47] поверхность кипятильника составит:
м2.
Принимаем одноходовой кожухотрубчатый теплообменник со следующими характеристиками [6, с. 51]:
— диаметр кожуха 273 мм;
— труба 20×2 мм;
— количество труб в теплообменнике 61 шт;
— длина труб 1,5 м;
— поверхность теплообмена 6,0 м².
Примечание:
При расчете поверхности кипятильника температура кипения кубовой жидкости tXw = 96,2 °С взята при атмосферном давлении. Не учтено увеличение температуры кипения кубовой жидкости в связи с увеличением давления в кубе колонны на величину ДРк = 0,1−0,15 кгс/см2.
СПИСОК ЛИТЕРАТУРЫ
1. Павлов К. Ф., Романков П. Г., Носков А. А. Примеры и задачи по курсу процессов и аппаратов химической технологии. — Л.: Химия, 1987. — 576с.
2. Справочник химика, т. 5. — М.: Химия, 1968. — 975 с.
3. Отраслевой стандарт (Ост 26−01−1488−83).
4. Доманский И. В., Исаков В. П. и др. Под общей редакцией Соколова В. Н. Машины и аппараты химических производств: Примеры и задачи. — Л.: Машиностроение, 1982. — 384 с.
5. Расчеты основных процессов и аппаратов нефтепереработки. Справочник/Под редакцией Судакова Е. Н., 3-е изд., перераб. и доп. — М.: Химия, 1979. — 568 с.
6. Борисов Г. С., Брыков В. П., Дытнерский Ю. И. и др. Под ред. Дытнерского Ю. И. Основные процессы и аппараты химической технологии, 2-е изд., перераб. и дополн. — М.: Химия, 1991. — 496 с.
7. Коган В. Б., Фридман В. М, Кафаров В. В. Равновесие между жидкостью и паром. Справочное пособие, книга 1-я и 2-я. — М.-Л.: Наука, 1966. — 640 с. + 786 с.
8. Плановский А. Н., Рамм В. М., Каган С. З. Процессы и аппараты химической технологии, 4-е изд. — М.: Химия, 1967. — 848 с.
9. Романков П. Г., Курочкина М. И. Расчетные диаграммы и номограммы по курсу «Процессы и аппараты химической промышленности». — Л.: Химия, 1985. — 54 с.
10. Чернышев А. К., Коптелов В. Г., Листов В. В., Заичко Н. Д. Основные теплофизические свойства газов и жидкостей. Номографический справочник. — Кемеровское изд-во, 1971. — 225 с.
11. Плановский А. Н., Николаев П. И. Процессы и аппараты химической и нефтехимической технологии, 3-е изд. — М.: Химия, 1987. — 496 с.