Разработка установки для переработки отходов слюдопластового производства на слюдяной фабрике
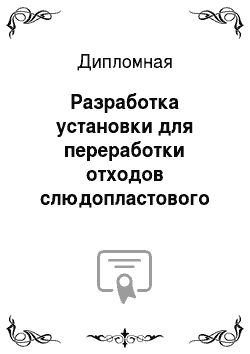
Отходы, получаемые в процессе производства слюдопластовой бумаги и слюдопласта, по своим характеристикам близки к природным компонентам, поэтому могут быть вторично вовлечены в производство. Продукт переработки отходов производства слюдопластовой бумаги — молотая слюда флогопит пользуется спросом на рынке и находит применение в различных отраслях промышленности. Отходы слюдяной пульпы образуются… Читать ещё >
Разработка установки для переработки отходов слюдопластового производства на слюдяной фабрике (реферат, курсовая, диплом, контрольная)
АННОТАЦИЯ
В настоящем дипломном проекте разработана установка для переработки отходов слюдопластового производства на «Слюдяной фабрике» в Колпино.
Актуальность темы
обусловлена необходимостью решения проблемы утилизации отходов производства, которой должно уделяться особое внимание, так как использование техногенных минеральных ресурсов является важной составной частью государственной политики ресурсосбережения и охраны окружающей среды. Настоящая разработка позволяет практически полностью использовать отходы, имеющие 3−4 класс опасности. В настоящее время отходы размещаются на территории предприятия, а затем вывозятся и захораниваются, что приносит немалые убытки предприятию. Внедрение же разработанной установки позволит не только снизить отрицательное воздействие на экологию, но и получить экономический эффект. Годовая прибыль от реализации продукта переработки — слюды флогопит мокрого помола 315 составит около 2 млн руб. в год, и это не считая экономии на вывозе и утилизации отходов другими предприятиями. Срок окупаемости установки — 2 года.
Главными техническими решениями, принятыми в данной работе являются использование для помола шаровой барабанной мельницы с разгрузкой через решетку, классификация при помощи гидроциклона, отжим слюдяной пульпы в осадительной горизонтальной шнековой центрифуге и окончательное удаление влаги в сушилке кипящего слоя.
При помощи технологических расчетов выявлены основные конструктивные размеры оборудования и его потребное количество. Конструктивные расчеты выполнены для сушилки кипящего слоя. Рассчитана толщина стенки корпуса аппарата, толщина газораспределительной решетки, произведен расчет укреплений отверстий, фланцевого соединения и др.
В качестве объекта автоматизации выбрана спроектированная сушилка кипящего слоя. Нормальная работа сушилок КС возможна только при определенной высоте кипящего слоя, с целью поддержания заданного значения этого параметра стабилизируется гидродинамическое сопротивление слоя, т. е. перепад давлений до и после решетки, воздействием на вариатор электродвигателя питателя сухого материала.
Сушилка кипящего слоя является наиболее опасным аппаратом установки для переработки отходов. Поэтому она выбрана в качестве основного объекта анализа с точки зрения безопасности. Универсальное оборудование эксплуатируется в соответствии с технической документацией завода-изготовителя и паспортом промышленной безопасности объекта.
В данной пояснительной записке содержатся 33 рисунка и 18 таблиц, общий объем — 114 страниц. К пояснительной записке прилагаются 9 чертежей.
1 ВВЕДЕНИЕ
2 ТЕХНИКО-ЭКОНОМИЧЕСКОЕ ОБОСНОВАНИЕ
2.1 Производство слюдопластовых электроизоляционных материалов
2.2 Образование отходов при производстве слюдопластовой бумаги
2.3 Продукт переработки отходов — молотая слюда флогопит
2.4 Измельчение
2.5 Классификация
2.6 Центрифугирование
2.7 Сушка
2.8 Транспортирование материала
2.9 Технические решения
3 ТЕХНОЛОГИЧЕСКИЕ РАСЧЕТЫ
3.1 Расчет барабанной мельницы
3.2 Расчет классификатора
3.3 Подбор насосов
3.4 Расчет центрифуги
3.5 Расчет сушилки с кипящим слоем
3.5.1 Материальный и тепловой баланс процесса горения
3.5.1.1 Сжигание газообразного топлива
3.5.1.2 Определение избытка воздуха и параметров смеси
3.5.2 Тепловой и материальный баланс процесса сушки
3.5.3 Тепловой конструктивный расчет
3.6 Подбор циклона
3.7 Подбор фильтра
3.8 Расчет топочного устройства
3.9 Подбор газодувки
3.10 Подбор питателей
4 КОНСТРУКТИВНЫЕ РАСЧЕТЫ
4.1 Расчет сушилки кипящего слоя
4.1.1 Выбор материала аппарата
4.1.2 Расчет толщины обечайки
4.1.3 Расчет толщины газораспределительной решетки
4.1.4 Расчет штуцеров и подбор фланцев
4.1.5 Расчет фланцевого соединения
4.1.5.1 Определение конструктивных размеров фланца
4.1.5.2 Расчет нагрузок, действующих на фланец
4.1.5.3 Проверка прочности и герметичности соединения
4.1.6 Расчет укрепления отверстий
4.1.7 Расчет тепловой изоляции
4.1.8 Расчет опор аппарата
5 СИСТЕМА АВТОМАТИЗАЦИИ
6 БЕЗОПАСНОСТЬ ОБЪЕКТОВ
7 РАСЧЕТ ЭКОНОМИЧЕСКОЙ ЭФФЕКТИВНОСТИ СПИСОК ИСПОЛЬЗОВАННОЙ ЛИТЕРАТУРЫ
1 ВВЕДЕНИЕ
Актуальность темы
дипломной работы обусловлена необходимостью решения проблемы утилизации отходов производства, которой должно уделяться особое внимание, так как использование техногенных минеральных ресурсов является важной составной частью государственной политики ресурсосбережения и охраны окружающей среды. Ежегодно на территории России накапливается 3,5 млрд. т техногенных отходов, но уровень их использования продолжает оставаться крайне низким. Необходимо постоянно улучшать качество и количество используемых минерально-сырьевых ресурсов на всех стадиях от добычи полезных ископаемых и переработки сырья до выпуска и использования конечной продукции. В силу вышесказанного, появляется объективная необходимость в разработке максимально возможной безотходной технологии, позволяющей наиболее полно использовать отходы производства.
Сегодня проблема утилизации отходов горнодобывающего и горноперерабатывающего производств чрезвычайно актуальна в силу различных причин. С одной стороны, происходит истощение разрабатываемых месторождений, а дальнейшая их разработка требует крупных капитальных вложений. В такой ситуации возможно вовлечение в переработку так называемых техногенных образований. С другой стороны, особый интерес представляет переработка текущих отходов производства, позволяющая наиболее рационально извлечь из них ценные компоненты, снижая количество вновь поступающих отходов. Основная масса добываемых и перерабатываемых сегодня слюд идет на производство электроизоляционных материалов, среди которых следует выделить слюдяную бумагу, слюдопластоленту, слюдопласт, микалекс, миканит. Производство любого вида продукции из слюды сопровождается наличием определенного количества технологических отходов (от 10 до 40%).
На «Слюдяной фабрике» наибольшее количество отходов образуется при производстве слюдопластовой бумаги из слюды флогопит. Среди видов отходов следует выделить нерасщепленную слюду, слюду в оборотной воде, укрупненные частицы — «хвосты» и «мику» в отходящей воде. Отходам слюды присвоен 4 класс опасности, степень вредного воздействия на окружающую природную среду — низкая. Критерием отнесения к данному классу является нарушение экологической системы с периодом самовосстановления не менее 3-х лет. Слюда флогопит мелкодисперсная имеет 3 класс опасности, для которого период восстановления — не менее 10 лет после снижения вредного воздействия от существующего источника. Вовлечение этих отходов в переработку позволит решить проблему их утилизации и снизить себестоимость основной продукции — слюдопластовой бумаги.
Существующие сейчас на «Слюдяной фабрике» способы утилизации отходов слюдяного производства имеют огромное количество недостатков. Для складирования требуются все большие и большие территории, отходы проникают в почву, нарушая обменные процессы в природной среде. Дальнейшее захоронение отходов опять же требует новых территорий. Подземные свалки не заметны на первый взгляд, но на поверхности земли над ними почва отравлена и разрыхлена, она не пригодна, ни для строительства, ни для земледелия, ни для выпаса скота. Таким образом, единственным, относительно экологически чистым, способом борьбы с промышленными отходами, на сегодняшний день, является переработка отходов.
Отходы, получаемые в процессе производства слюдопластовой бумаги и слюдопласта, по своим характеристикам близки к природным компонентам, поэтому могут быть вторично вовлечены в производство. Продукт переработки отходов производства слюдопластовой бумаги — молотая слюда флогопит пользуется спросом на рынке и находит применение в различных отраслях промышленности. Отходы слюдяной пульпы образуются в результате сброса из системы расщепления находятся в отстойниках в водной среде. Это обстоятельство определяет способ помола, которым производится порошок слюды флогопит. Слюда мокрого помола используется, в основном, в качестве наполнителя для производства «перламутровых» красок для автомобильной промышленности и в качестве добавок во всевозможные лаки и шпаклевки, что придает им влагоустойчивость, морозоустойчивость и стойкость против коррозии. Уникальные светоотражающие и светопреломляющие свойства слюды мокрого помола обусловили ее применение в производстве художественных обоев и в косметической промышленности в качестве наполнителя при производстве средств макияжа (тени, пудра, помада с эффектом блеска и т. д.). Также молотую слюду флогопит используют для производства резины и в качестве наполнителя в пластмассу.
Таким образом, разработка установки для переработки отходов слюдопластового производства актуальна не только из-за необходимости снижения отрицательного воздействия на окружающую среду, но и по экономическим соображениям.
К сожалению, на сегодняшний день нельзя говорить о достаточной степени изученности проблемы по использованию отходов слюдяного производства. Проведенный анализ литературы показал, что в настоящее время уделяется недостаточное внимание вопросам утилизации отходов слюдяного производства как в форме техногенных образований, так и текущим производственным отходам. Но все же стоит отметить, что кое-какие исследования и разработки в этой области ведутся.
В 2008 году при Иркутском государственном техническом университете Перфильевой Ю. В. была разработана технология извлечения слюды из отходов горно-обогатительных и слюдоперерабатывающих предприятий.
«Нижнеудинская слюдинитовая фабрика» являлась базой эксперимента. Производственные отходы этой фабрики были использованы в качестве исходного компонента для производства модифицированного микалекса. Отходы фабрики можно разделить на две группы — отходы слюдяного производства (включают 5 видов) и отходы слюдокерамического сырья (включают два вида). Обе группы отходов были использованы в производстве микалекса. После грохочения в процессе производства слюдопластовой бумаги на базе скрапа флогопита Ковдорского месторождения образуются отходы. Подрешетный продукт является отходом и представляет собой грубые чешуйки различной формы и разных размеров. Из этих отходов были изготовлены пластины модифицированного микалекса. Технология изготовления модифицированного микалекса из отходов осталась та же, что и при изготовлении микалекса из слюды мусковит.
Кроме того были проведены исследования процесса измельчения отходов с целью получения сырья оптимальной структуры и плотности. Была проведена проверка уравнения кинетики измельчения отходов в шаровой мельнице и молотковой дробилке экспериментальным и графическим методом, обосновано применение технологии флотации для получения дополнительного источника сырья при производстве модифицированного микалекса.
Также решением проблемы по переработке отходов слюды занимаются в Горном институте Кольского научного центра Российской академии наук. В 2000 году сотрудники института обратились к проблеме переработки мусковитовых руд отвалов рудника Риколатва. Были обследованы все отвалы, выделены промышленно значимые, подсчитаны запасы и отобраны технологические пробы. По данным опробований отвалов, проведенных технологических исследований, впервые в России были утверждены запасы забалансовых мусковитовых руд на примере рудника Риколатва с учетом всей слюды, находящейся в отвалах. Эта слюда может быть использована для производства молотых слюд, а крупный мусковит (до 20 мм) для производства слюдобумаг. Учитывая состояние мусковитовых рудников, эти отвалы могут стать основным сырьем для производства концентратов различной крупности и молотых слюд на основе мусковита.
Перечисленные выше факторы в пользу актуальности проблемы переработки отходов слюды и ее недостаточная изученность определили тему дипломной работы. Целью настоящей работы является разработка установки, позволяющей использовать отходы слюдопластового производства для производства молотой слюды флогопит.
Работа имеет практическую значимость, так как разработанная установка может быть использована для переработки отходов на «Слюдяной фабрике» в городе Колпино.
2 ТЕХНИКО-ЭКОНОМИЧЕСКОЕ ОБОСНОВАНИЕ
2.1 Производство слюдопластовых электроизоляционных материалов
Темой настоящей дипломной работы является переработка отходов слюды. В коммерческом отношении термином «слюда» обозначают мусковит и маложелезистый флогопит. К листовой слюде относят светлые прозрачные разновидности, которые расщепляются на пластины разной толщины, пригодные для штамповки изделий нужных форм. Благодаря высоким электроизоляционным свойствам слюды используются в радиоэлектронике, электромашиностроении, электротермии. С самого начала использования слюды специалисты стремились заменить редкую и чрезвычайно ценную крупнолистовую слюду более мелкой. Мелкочешуйчатая слюда под торговым названием «скрап» идет на изготовление теплоизоляционных материалов в теплоэнергетике и стройиндустрии и служит сорбентом в сельском хозяйстве.
Продуктами слюдопластового производства являются следующие теплоизоляционные материалы: слюдопластовая бумага, слюдопласт, слюдопластовая лента, изделия из слюдопластов (трубки и втулки). Последним направлением использования мелкой слюды как заменителя крупнолистовой слюды является изготовление различных слюдопластовых бумаг. Их производство интенсивно растет во всем мире. В слюдопластовой бумаге чешуйки скреплены между собой молекулярными силами без помощи склеивающих веществ. Он изготовляется посредством расщепления отходов или мелких (не пригодных для ручной щипки) кристаллов слюды на чешуйки и соединения их в листы без применения смолы.
В зависимости от назначения листы слюдопластовой бумаги в дальнейшем подвергают пропитке (лакировке) с термообработкой и прессованием. Склеивающие вещества служат для заполнения пор в материале и склеивания листов слюдопластовой бумаги между собой. Слюдопласты обладают достаточно высокой механической прочностью при повышенной температуре, позволяющей изготовлять из них различные фасонные изделия. Эти свойства слюдопласта являются следствием того, что в данном производстве слюда не подвергается химической деструкции и не загрязняется химикатами, как это происходит при получении слюдинитовых бумаг; элементарные частицы имеют в основном толщину от 0,5 до 2 мкм, а по площади намного превосходят свою толщину, что обеспечивает хорошее прилегание частиц друг к другу и дальнейшее их сцепление за счет сил молекулярного притяжения.
Как говорилось раньше, наиболее отходным видом слюдопластового производства является производство слюдопластовой бумаги. Поэтому целью настоящей работы является разработка установки, позволяющей перерабатывать отходы и получать при этом не менее полезный и востребованный в промышленности продукт — молотую слюду флогопит.
2.2 Образование отходов при производстве слюдопластовой бумаги
На «Слюдяной фабрике» в Колпино производят слюдяную бумагу из слюды флогопит марок ИФ-14, ИФ-12 ТУ 21−25−41−78. Сырьем для слюдобумаги является слюда-сырец флогопит Ковдорского месторождения марок СФК-25, СФК-10, СФК-4, СФК-4−10 (ТУ 21−25−223−79). Эта слюда представляет собой пластинчатые кристаллы произвольной формы, ограниченные по площади и толщине. В таблице 2.2.1 приведены технические требования к сырью для производства слюдобумаги.
Таблица 2.2.1
Технические требования к слюде флогопит для производства слюдопластовой бумаги
Продукт | Площадь кристалла, мм2•102 | Толщина кристалла, мм | |
СФК-25 | от 25 до 35 | не более 20 | |
СФК-10 | то 10 до 25 | не более 20 | |
СФК-4 | от 4 до 25 | от 0,05 до 2 | |
СФК-4−10 | от 4 до 35 | не более 20 | |
Технологический процесс производства состоит из следующих этапов:
1. участок первичной обработки слюды (термирование, расколка, очистка);
2. участок производства слюдяной массы;
3. участок отлива слюдобумаги.
1. Участок первичной обработки слюды.
Термист насыпает из ящика слюду в приемный бункер, откуда она подается транспортером (2) на грохот (3) и далее в конвейерную электропечь (4). Грохот служит для очистки слюды от песка и пыли. В процессе подачи сырья в термопечь обеспечивается очистка его от щепок и мусора вручную. Загрузка слюды регулируется скоростью движения подающего транспортера. При термировании слюды удаляется вода, что приводит к уменьшению связей между плоскостями совершенной спайности. Продолжительность термирования слюды — не менее 15 минут.
Из печи термированная слюда поступает в ударную машину (8), где происходит расщепление кристаллов на слои. Расщепленные пластинки слюды проскакивают в щель между броней и лопастями, подаются на пневмосепарацию и далее на сито-бурат (14). Толщина кристаллов регулируется величиной зазора между лопастями ротора и лопастями брони.
Вентилятор (5) подает слюду в циклон (11), где она оседает и поступает в трубопровод, в котором происходит пневмосепарация, плохо расщепленные кристаллы возвращаются в ударную машину, а кристаллы толщиной менее 2 мм поступают в следующий циклон и далее на сито бурат. Пневмосепарация регулируется шибером перед вентилятором (13). Воздух, который расходуется на пневмотранспорт и пневмосепарацию, очищается от слюдяной пыли в скруббере (7) и выбрасывается в атмосферу.
Сито-бурат (14) представляет собой вращающийся барабан, покрытый сеткой с размером ячеек 3*4 мм. Слюда поступает внутрь барабана, где проходит сортировка ее по площади. Мелкая фракция (класс «-5») проходит сквозь ячейки барабана и поступает в бумажные мешки (15). Деловая слюда (класс «+5») поступает в делитель объемов (16). Содержание мелочи в деловой слюде не превышает 1%.
2. Участок производства слюдяной массы После сито-бурат деловая фракция поступает в делитель объемов слюды, где происходит разделение общей массы на четыре примерно равных потока, каждый поток слюды по пневмотранспорту подается в осадитель (17). Из осадителя слюда подается в моечные машины непрерывного действия (19). В моечной машине происходит удаление с поверхности слюды загрязнений. Слюда непрерывно через загрузочный лоток поступает во вращающийся перфорированный барабан, погруженный в бак с водой и с помощью ребер лопастей перемещается к выходу, где посредством ковшей выгружается из барабана в лоток и по лотку подается на вибролоток (20) и далее на многовалковый прокатный станок (21).
Прокатные станки служат для расщепления кристаллов слюды по плоскостям совершенной спайности и частичного измельчения по площади за счет вдавливания последней рифлеными валиками в резиновую ленту. В процессе прокатки кристаллы слюды смачиваются водой. В конце транспортирующей ленты прокатанные кристаллы смачиваются водой в течку, соединенную с приемной воронкой дезинтегратора (22).
Мокрые, прокатанные кристаллы слюды через загрузочную трубу попадают в расщепляющую камеру дезинтегратора. Расщепление слюды происходит под действием струи воды, входящей в камеру через сопловое отверстие под давлением. Расщепленные чешуйки слюды поднимаются в классифицирующую часть дезинтегратора и под действием восходящего потока подпиточной воды поднимаются наверх и через переливную трубу транспортируются в сгуститель (25). Нерасщепленные чешуйки слюды снова опускаются в расщепляющую камеру.
В сгустителе происходит повышение концентрации пульпы за счет осаждения слюдяных частиц. Подача пульпы в сгуститель осуществляется через центральный приемник, оборудованный гасителем в виде сеточного рукава. Сгущенная пульпа подается в классификатор непрерывным потоком в нижней части конуса по трубопроводу, называющемуся «гусиной шейкой». Осветленная вода от сгустителей поступает в бак оборотных вод.
В гидравлическом классификаторе (26) происходит выделение из слюдяной пульпы грубых частиц — «хвостов», которые не могут подняться вверх, вследствие малой скорости восходящего потока. Частицы эти опускаются вниз классификатора, откуда через «гусиную шейку» непрерывно сливаются в канализацию. Верхний класс слюдяной пульпы поступает через слив в сгуститель-накопитель (28). Сгуститель-накопитель представляет собой емкость, оборудованную барботирующим устройством периодического действия. При достижении заданного количества пульпы автоматически включается в работу пневматический затвор, герметизирующий накопитель. Затем открывается кран и через отверстия в барботирующее устройство подается сжатый воздух, необходимый для взрыхления слюдяной массы перед ее поднятием наверх в промежуточную емкость (29). После взрыхления кран перекрывается, а барботирующее устройство продолжает работать. В результате того воздух собирается в верхней части накопителя и выдавливает пульпу в промежуточную емкость, в которой производится накапливание слюдяной массы перед загрузкой мешального бассейна. Мешальный бассейн заполняется водой, затем из промежуточной емкости выгружается пульпа, перемешивается и перекачивается в рабочий бассейн.
3. Участок отлива слюдобумаги
Отлив слюдобумаги производится на слюдопластоделательной машине К-1425. Слюдяная пульпа из рабочего бассейна (32) по лотку поступает в напускное устройство машины, где она равномерно распределяется по ширине и через переливной барьер, поступает в ригельную зону (зону осаждения). В ригельной зоне частицы слюды оседают на непрерывно движущуюся по наклонному формовочному столу сетку, образую слой слюдопластовой бумаги. Этот слой удерживается на сетке при выходе из воды благодаря вакууму в отсасывающих ящиках формовочного стола. Далее сетка со слюдобумагой перемещается по вакуум-блоку, где слюдобумага подвергается вакуумированию. В зоне вакуума воздух над блоком нагревается трубчатыми электронагревателями, что способствует лучшему испарению воды. Затем полотно слюдобумаги поступает в сушильную часть, которая разделена на 4 зоны сушки. Сушка производится горячим воздухом, нагретым электрокалориферами. Намотка слюдобумаги производится на накате осевого типа. Слюдобумага после прохождения сушильной части поступает на натяжную станцию, состоящую из параллельно укрепленных на поворотной вилке валов и неподвижно укрепленного вала. Рулоны слюдобумаги, снятые с машины, взвешиваются и проверяются контролером на соответствие требованиям ТУ.
На рисунках 2.1.1 и 2.1.2 изображены качественно-количественные схемы производства слюдопластовой бумаги марок ИФ-12 и ИФ-14 из слюды флогопит СФК-10, а в сводной таблице 2.1.1 подытожены данные об отходах производства и их использовании.
Как видно из таблицы 2.1.1, отходы, подлежащие переработке, находятся в отстойнике в водной среде. Эти отходы представляют собой пульпу — смесь воды и пластинок слюды, размером до 30−40 мм. Массовая влажность отходов, находящихся в отстойнике и поступающих на дальнейшую переработку, равна примерно 50−60%, т. е. на 2 тонны слюдяной пульпы, поступающей в отстойник в сутки от основного производства слюдопластовой бумаги, приходится примерно 1 т воды и 1 т слюды. Остальные отходы реализуются другими предприятиями, например, слюда мелкой фракции (класс «-5»). На свалку вывозится только мелкая загрязненная слюда класс «-4», дальнейшее применение которой пока что невозможно на данном предприятии. Отходы производства можно переработать в пористый наполнитель для бетона, например. Но так как в данном производстве слюдопластовой бумаги слюда не подвергается химической деструкции и не загрязняется химикатами, из отходов можно получить более качественный продукт — слюду мокрого помола по ГОСТ 19 571–74, 19 572−74, 19 573−74, ТУ 5725−011−13 187 253−97, применяемую в качестве добавок в лаки, краски, шпаклевки, жидкие обои, в качестве наполнителя в пластмассу, для производства резины и др.
СЛЮДА-ФЛОГОПИТ СФК-10
100%
ГРОХОЧЕНИЕ
потери 3% 97%
ТЕРМИРОВАНИЕ
97%
УДАРНАЯ ОБРАБОТКА
97%
ПНЕВМОСЕПАРАЦИЯ
потери 2% 95%
СИТОВАНИЕ
потери 12% 83%
ПРОМЫВКА 2%
потери 8% 77%
ДИСПЕРГИРОВАНИЕ 7%
потери 4% 80%
СГУЩЕНИЕ
74% 6%
СГУЩЕНИЕ-НАКОПЛЕНИЕ
71% 3%
ОТЛИВ СЛЮДОБУМАГИ
потери 18,4% 52,6%
СЛЮДОБУМАГА МАРКИ ИФ-12
КОЭФФИЦИЕНТ РАСХОДА СЛЮДЫ-ФЛОГОПИТ СФК-10 НА 1 ТН СЛЮДОБУМАГИ МАРКИ ИФ-12 — 1,9
Рисунок 2.1.1. Качественно-количественная схема производства слюдопластовой бумаги марки ИФ-12
СЛЮДА-ФЛОГОПИТ СФК-10
100%
ГРОХОЧЕНИЕ
потери 3% 97%
ТЕРМИРОВАНИЕ
97%
УДАРНАЯ ОБРАБОТКА
97%
ПНЕВМОСЕПАРАЦИЯ
потери 1,5% 95,5%
СИТОВАНИЕ
потери 13% 82,5%
ПРОМЫВКА 3%
потери 8% 77,5%
ДИСПЕРГИРОВАНИЕ 8%
потери 4% 81,5%
СГУЩЕНИЕ
74,5% 7%
КЛАССИФИКАЦИЯ
потери 8% 66,5%
СГУЩЕНИЕ-НАКОПЛЕНИЕ
62,5% 4%
ОТЛИВ СЛЮДОБУМАГИ
потери 19% 43,5%
СЛЮДОБУМАГА МАРКИ ИФ-14
КОЭФФИЦИЕНТ РАСХОДА СЛЮДЫ-ФЛОГОПИТ СФК-10 НА 1 ТН СЛЮДОБУМАГИ МАРКИ ИФ-14 — 2,3
Рисунок 2.1.2. Качественно-количественная схема производства слюдопластовой бумаги марки ИФ-14
Таблица 2.1.1
Отходы производства, их использование
Наименование отходов | % отходов | Местообразование отходов | Использование отходов | |
Мелкая загрязненная слюда (класс «-4») | Грохот | Вывоз на свалку | ||
Слюда крупная толщиной более 2 мм | Пневмосепарация | Подача в термопечь | ||
Слюда мелкой фракции (класс «-5») | Сито-бурат | Реализация другими предприятиями | ||
Слюда (класс «-5») в оборотной воде | Моечная машина | В отстойник | ||
Нерасщепленная слюда | Дезинтегратор | В отстойник | ||
Слюда в оборотной воде | 9−11 | Сгуститель-осадитель, сгуститель-накопитель | Подается с оборотной водой в дезинтеграторы, моечные машины | |
Укрупненные частицы слюды (хвосты) | Классификатор | В отстойник | ||
«Мика» в отходящей воде | 13−14 | Слюдопласто-делательная машина | В отстойник | |
Кромка, обрывы слюдобумаги | 5−6 | Накат | Барботер отходов, затем промежуточная емкость | |
2.3 Продукт переработки отходов — молотая слюда флогопит
Как говорилось раньше, слюдопластовая бумага производится из флогопита, поэтому продуктом переработки отходов является молотая слюда флогопит по ГОСТ 19 571–74, 19 572−74, 19 573−74 — порошок с размером частиц до 315 мкм. Слюда флогопит является представителем группы слюд алюмосиликатов щелочных и щелочноземельных металлов. Для слюды характерна высокая электрическая и механическая прочность, термическая и химическая стойкость, гибкость, упругость, прозрачность. В таблице 2.2.1 представлен химический состав слюды флогопит.
Таблица 2.2.1
Химический состав флогопита (%):
SiO2 | 37−41 | |
Al2O3 | 12−14 | |
Fe2O | 6,5−7 | |
MgO | 24−26 | |
K2O | 9−11 | |
TiO2 | 0,8−2 | |
Na2O | 0,4−0,7 | |
Физические свойства слюды флогопит:
· удельная теплоемкость: 0,87•10-3 Дж/кг•К;
· твердость: 23 (по шкале Мооса);
· плотность: 26 702 730 кг/м3;
· удельное объемное сопротивление: (1,76,8)•1012 Ом•мм;
· пробивное напряжение: 4,24,6 кВ при частоте 50 ГЦ;
· термостойкость: линейное увеличение толщины 29 169% при нагревании до 750 градусов Цельсия;
· тангенс угла диэлектрических потерь: 0,340,0147 при частоте 50 кГц.
Технические требования к порошку слюды флогопит 315:
· массовая доля остатка на сетке № 2 — отсутствует;
· массовая доля остатка на сетке № 0315 — не более 6,0%;
· массовая доля остатка на сетке № 0125 — не более 50,0%;
· массовая доля частиц, проходящих через сетку № 0063 ;
не более 55,0%;
· массовая доля пустой породы — не более 5%;
· массовая доля влаги — не более 3,0%;
· массовая доля Si2Oне более 40,0%;
· массовая доля FeO3— не более 7,5%;
· массовая доля Al2O3— не более 15,0%;
· массовая доля MgO — не менее 20,0%;
· массовая доля (K2O и Na2O) — не менее 8,0%;
· массовая доля SO3 — не более 0,1%;
· массовая доля P2O5 — не более 0,1%;
· насыпная масса — не более 0,5 г/см3.
Данные качественные показатели вырабатываемой продукции определяют технологию производства, а с учетом заданной производительности, равной 1 тонне порошка в сутки, и основные конструктивные параметры оборудования. Из слюдяной пульпы со средним размером частиц, равным 20 мм и влажностью 50 процентов необходимо получить продукт — порошок с размером частиц до 315 мкм и влажностью не более 3%. На рисунке 2.3.1 изображена схема материального баланса производства молотой слюды флогопит с размером частиц до 315 мкм. Отходы от производства слюдопластовой бумаги подлежат измельчению и сушке с предварительным отжимом в центрифуге. Таким образом, целью настоящей дипломной работы является разработка установки, позволяющей осуществить технологический процесс по переработке отходов, образующихся при производстве слюдопластовой бумаги, в материал с заданными качествами.
влажная слюда — 2 т/сут
влажность — 50%
размер частиц — 20 мм
влажная слюда — 2 т/сут
влажность — 50%
размер частиц — 315 мкм
влажная слюда - 1,43 т/сут
влажность — 30%
размер частиц — 315 мм
слюда - 1 т/сут
влажность — 1 %
размер частиц — 315 мм
Рисунок 2.3.1. Материальный баланс производства молотой слюды
2.4 Измельчение
Измельчением называют процесс разрушения кусков твердого материала при критических внутренних напряжениях, создаваемых в результате какого-либо нагружения и превышающих соответствующий предел прочности. Напряжения в материале могут создаваться механическим нагружением, температурными воздействиями, ультразвуковыми колебаниями и др. Наибольшее применение в современном производстве имеют механические способы измельчения. Измельчение делят на дробление и помол, а машины, применяемые для этих целей, называются дробилками и мельницами. В зависимости от размеров частиц продукта (конечного размера частиц dк) различают следующие виды измельчения: дробление крупное (dк = 100 350 мм), среднее (dк = 40 100 мм), мелкое (dк = 540 мм), помол грубый (dк = =0,15 мм), средий (dк = 0,050,1 мм), тонкий (dк = 0,0010,05 мм), сверхтонкий (dк < 0,001 мм).
Основной характеристикой процесса измельчения является степень измельчения, которая определяется соотношением средневзвешенных размеров частиц материала до (dн) и после (dк) измельчения:
i = dн/dк,
i = 20/0,315 65.
Степень измельчения отражает технологию и определяет параметры измельчителей. Таким образом, необходимо подобрать аппарат, способный обеспечить степень измельчения, равную 65. Степень измельчения, достигаемая на одной машине, для большинства видов дробильного оборудования не превышает 550. Поэтому для обеспечения больших степеней измельчения необходимо применить несколько стадий дробления. В то же время следует отметить, что увеличение стадий измельчения приводит к переизмельчению материала и увеличению эксплуатационных затрат. Поэтому процесс измельчения следует осуществлять, исходя из условия обеспечения минимального числа стадий дробления. Кроме того, необходимо учесть, что измельчаемый материал представляет собой пульпу, т. е. аппарат должен обеспечивать мокрое измельчение.
Рассмотрим возможность применения различных видов используемого в промышленности оборудования для проведения мокрого измельчения с i = 65.
Щековые и конусные дробилки применяют для крупного и среднего дробления различных материалов во многих отраслях народного хозяйства. По технологическому назначению их делят на дробилки: крупного дробления, обеспечивающие степень измельчения i = 58; среднего и мелкого дробления (степень измельчения i = 2050). Вышеперечисленные аппараты не могут обеспечить требуемую степень измельчения в одну стадию.
Валковые дробилки применяют для среднего и мелкого дробления материалов высокой и средней прочности, а также для измельчения пластичных и хрупких материалов. Процесс измельчения осуществляется непрерывно при затягивании кусков материала в суживающееся пространство между параллельно расположенными и вращающимися навстречу друг другу валками. Валковые дробилки также не способны обеспечить требуемую степень измельчения.
Выше были рассмотрены дробилки, разрушающие материал сжатием, рассмотрим дробилки ударного действия. В измельчителях ударного действия измельчение материала осуществляется под действием ударных нагрузок, которые могут возникать при взаимном столкновении частиц измельчаемого материала, столкновении частиц материала с неподвижной поверхностью, столкновении материала и движущихся рабочих органов машин. К дробилкам ударного действия относятся роторные и молотковые дробилки, а также пальцевые измельчители. Дробилки ударного действия применяют для измельчения малоабразивных материалов средней и низкой прочности (известняков, мела, гипса, калийных руд и др.). Они обеспечивают степень измельчения i = 1520, и лишь в отдельных случаях до i = 50.
Таким образом, осуществить необходимый технологический процесс способны лишь аппараты для помола. Среди них можно выделить барабанные, вибрационные и струйные мельницы. При проектировании схем измельчения любых материалов необходимо соблюдать принцип «не измельчать ничего лишнего», поскольку переизмельчение приводит к излишнему расходу энергии, снижению производительности и росту износа дробилок и мельниц. Поэтому нецелесообразно применять в данном производстве молотой слюды вибрационную и бисерную мельницы, которые способны произвести помол слюды до 5 мкм.
Наиболее оптимальным является использование барабанной мельницы. Она способна обеспечить степень измельчения до 100. Достоинствами барабанных мельниц являются простота конструкции и удобство в эксплуатации. Кроме того, существуют конструкции барабанных мельниц мокрого помола.
Схема процесса измельчения материала в барабанной мельнице показана на рисунке 2.4.1. При вращении полого барабана смесь измельчаемого материала и мелющих тел (шаров или стержней) сначала движется по круговой траектории вместе с барабаном, а затем, отрываясь от стенок, падает по параболической траектории. Часть смеси, расположенная ближе к оси вращения, скатывается вниз по слоям смеси. Измельчение материала происходит в результате истирания при относительном движении мелющих тел и частиц материала, а также вследствие удара.
Рисунок 2.4.1. Схема рабочего процесса в барабанной шаровой мельнице Режим движения мелющих тел в барабане, от которого зависит эффективность помола, определяется его угловой скоростью щ. При небольшой угловой скорости загрузка (мелющие тела и измельчаемый материал) циркулирует в нижней части барабана (рисунок 2.4.2), поднимаясь по концентрическим круговым траекториям на некоторую высоту и затем скатываясь параллельными слоями вниз. Такой режим работы называют каскадным.
Рисунок 2.4.2. Схема для расчета параметров шаровой барабанной мельницы
При большей скорости центробежная сила инерции Ри превысит составляющую G•cosб силы тяжести G шара, и последний не будет отрываться от стенки барабана даже в верхней точке C, т. е.
m?щ2•R > m•g, (2.4.1)
где m — масса шара, кг.
Откуда критическая угловая скорость вращения барабана будет равна:
щк =, (2.4.2)
где R — радиус внутренней поверхности барабана, м.
Большей эффективностью помола характеризуется водопадный режим движения шаров. Он реализуется при частоте вращения барабана меньше критической. При этом шары поднимаются, например, в точку, А (рисунок 2.4.2), а затем, отрываясь от стенок, свободно падают по параболическим траекториям. Измельчение материала происходит под воздействием удара, а также, частично, раздавливания и истирания.
Для определения условия отрыва и свободного полета шара массой m рассматриваем его как материальную точку, на которую действуют лишь массовые силы. Отрыв шара в точке, А от стенки барабана происходит при условии m•g•cosб? Pи. Следовательно, условие отрыва и свободного падения, которое можно получить из соотношения m•g•cosб? m? щ2R, имеет вид: щ?. (2.4.3)
Опыт эксплуатации барабанных мельниц показал, что наиболее рациональным является избирательное измельчение материала, когда крупные частицы измельчаются ударом, а мелкие — истиранием. Следовательно, режим работы мельниц должен обеспечивать чередование ударного режима с истиранием. На практике это реализуется за счет использования для футеровки элементов, обеспечивающих переменный коэффициент сцепления мелющих тел со стенками барабана. [4]
Основными критериями при выборе той или иной конструкции барабанной мельницы являются производительность, природа измельчаемого материала и вид помола — сухой или мокрый. В меньшей степени влияние на выбор оказывает тонина помола.
Шаровые мельницы по виду разгрузки измельчаемого материала делятся на два вида: мельницы с принудительной разгрузкой через решетку и мельницы с центральной разгрузкой через цапфу. Мельницы с разгрузкой через решетку предназначены для получения сравнительно крупного продукта, а мельницы с центральной разгрузкой — более мелкого продукта.
Так как помол, производимый при переработке отходов является грубым (dк= = 0,15 мм), то наиболее рационально использовать мельницу с разгрузкой через решетку. Решетку перед разгрузочной цапфой ставят для увеличения производительности шаровой мельницы за счет понижения уровня разгрузки и регулирования степени измельчения при значительных коэффициентах заполнения барабана. Так же решетка служит для удержания в рабочем пространстве барабана шаров и недостаточно размолотого материала. Достаточно измельченный продукт проходит через отверстия решетки, поднимается ее ребрами (лифтерами) и выгружается через разгрузочную цапфу. Разгрузочная решетка мельницы, конструкция которой приведена на рисунке 2.4.3, обычно характеризуется «живым сечением», т. е. суммарной площадью всех отверстий.
Рисунок 2.4.3. Разгрузочная решетка шаровой мельницы:
1 — центральная футеровка; 2 — клинья крепления решетки В отношении выбора «живого сечения» решеток в литературе не имеется твердых указаний. Так, например, многие специалисты рекомендуют общее «живое сечение» решеток выбирать в 10 раз большим поперечного сечения разгрузочной цапфы. Диаметр цапф мельниц обычно не является параметром ГОСТа, поэтому определение «живого сечения» решеток, как функции нерегламентируемого параметра, следует считать неудачным. Канд. техн. наук Е. Н. Болталов «живое сечение» решетки рекомендует выражать как функцию от диаметра мельницы или от площади поперечного сечения барабана. «Живое сечение» решеток современных мельниц, выпускаемых отечественными и зарубежными заводами, составляет 2030% площади поперечного сечения барабана. Профиль сечения щелей решеток в большинстве случаев выполняется сопловидной формы с углом расширения в сторону разгрузочной цапфы. Расположение щелей в плоскости решетки определенным образом влияет на производительность мельницы. Экспериментально доказано, что мельницы, оборудованные решетками с щелями, расположенными по хордам, имеют большую производительность по мелким классам и вновь образованной поверхности измельчаемого продукта.
С учетом установки решетки задаемся отношением диаметра к длине барабана мельницы. Правильный выбор длины барабана по отношению к ее диаметру оказывает большое влияние на получение максимальной производительности и на оптимальный расход энергии, т. е. на решающие технико-экономические показатели измельчительного агрегата в целом. Для современных мельниц с разгрузкой через решетку это отношение равно 0,751,6. Принимаем это отношение, равным 1.
Применение шаров в качестве мелющих тел обусловлено тем, что стержни способны обеспечить тонину помола лишь до 0,5 мм, что неприемлемо для настоящих требований к степени измельчения слюды.
Загрузочные устройства шаровых мельниц в принципе состоят из двух элементов — питателя той или иной конструкции и загрузочного патрубка цапфы, служащего одновременно ее футеровкой. Оба эти элемента предназначены для транспортирования продукта с уровня загрузки в полость барабана мельницы. Конструкцию и размеры загрузочных устройств выбирают такими, чтобы обеспечить поступление необходимого количества продукта в барабан мельницы и тем самым обеспечивать необходимую скорость загрузки. Скорость загрузки определяется количеством материала, пропускаемого через мельницу в единицу времени. При работе мельницы в открытом цикле она равна производительности по исходному материалу. При работе в открытом цикле количество материала увеличенной крупности, выдаваемого мельницей, возрастает с увеличением скорости загрузки. Низкая скорость загрузки приводит к переизмельчению материала и, следовательно, к понижению производительности и эффективности измельчения по определенному классу. Таким образом, при неудачном выборе параметров питателя или загрузочного патрубка цапфы, может быть снижена производительнсть мельницы. Одним из основных требований, которому должны удовлетворять питатели любой конструкции, является его высокая транспортирующая сила, способная преодолеть все сопротивления движению загружаемого материала. Эти сопротивления движению материала слагаются из сопротивлений движению в спиральном проходе и загрузочном патрубке цапфы, обусловленных трением и зависанием материала, а также из сопротивлений, обусловленных давлением пульпы из внутренней полости барабана мельницы.
Барабанный питатель, конструкция которого приведена на рисунке 2.4.4, представляет собой литую из чугуна или сварную из стали цилиндро-коническую камеру, открытую с обоих концов. Отверстие 2 служит для загрузки и отверстие 3 — для разгрузки материала. Питатель крепится болтами к загрузочной цапфе мельницы. Большее распространение барабанные питатели получили для загрузки на уровне оси мельниц при питании последних крупным сухим исходным материалом. При применении этих питателей отпадает необходимость в устройстве специальной загрузочной коробки, необходимой, например, при применении улиткового питателя.
Рисунок 2.4.4. Барабанный питатель:
1 — крышка питателя; 2 — загрузочное отверстие;
3 — разгрузочное отверстие; 4 — полость Данный тип питателей трудноприменим в условиях мокрого помола, поэтому рассмотрим другие конструкции. Улитковый питатель, конструкция которого представлена на рисунке 2.4.5, представляет собой конструкцию из одного, двух или трех спиральных черпаков.
Рисунок 2.4.5. Улитковый питатель:
1 — корпус питателя; 2 — сменный козырек Обычно питатель делается сварным из листовой стали. Питатель имеет отверстие для выпуска зачерпнутого материала. На конце каждого черпака крепится сменный козырек из марганцовистой стали или легированного чугуна. Максимальный радиус улиткового питателя выбирается в зависимости от скорости вращения мельницы. Для предотвращения разбрасывания материала в загрузочной коробке скорость черпания не должна превышать 85% критической скорости, вычисленной по отношению к козырьку улитки. Предпочтительнее делать питатели симметричными, так как при одночерпаковых питателях, из-за неуравновешенности вращающихся частей мельницы иногда появляется неравномерный износ зубьев венцовой шестерни привода мельницы. Мельницы с улитковыми питателями применяют в тех случаях, когда необходимо производить загрузку материала с более низкого уровня, например, при работе с классификатором. Улитковый питатель снабжен загрузочной коробкой. Между стенками и днищем загрузочной коробки и улиткой должны быть предусмотрены зазоры, по размеру несколько большие, чем максимальный размер куска руды или догружаемого шара. Комбинированный питатель, конструкция которого приведена на рисунке 2.4.6, представляет собой конструкцию, объединяющую достоинства барабанных и улитковых питателей.
Рисунок 2.4.6. Комбинированный питатель:
1 — корпус питателя; 2 — спиральный черпак; 3 — козырек; 4 — крышка При использовании барабанного питателя крупнокусковой материал попадает в мельницу, минуя загрузочную коробку. Черпаки при этом служат как элеваторы. Конструкция комбинированного питателя наиболее предпочтительна для производства молотой слюды из отходов, так как с одной стороны улитковый питатель позволяет осуществить мокрый помол, а с другой — может служить для загрузки в мельницу крупных кусков материала. [1]
Барабан мельницы изготовлен из углеродистой стали, и если его не защитить изнутри прочной облицовкой, то при измельчении абразивных материалов он быстро износится, и мельница выйдет из строя. Кроме того футеровка обеспечивает лучший подъем мелющих тел при вращении барабана. По назначению футеровки обычно делят на две основные группы — футеровки для мельниц, работающих на крупном загружаемом материале и футеровки для мельниц тонкого измельчения. Конечно, такое деление сугубо условное. Футеровки барабанов в цилиндрической части шаровых мельниц, работающих на крупном исходном материале, имеют ребра или волны. Футеровки мельниц тонкого измельчения имеют мелкие ребра или выполняются гладкими. Совсем гладкая футеровка применяется при дроблении сравнительно мягких пород или мелкого питания, когда не требуется создавать высокое давление дробящей среды, но зато требуется получить максимальное истирающее действие. В данном технологическом процессе наиболее целесообразно использовать футеровку с небольшой высотой волн, так как помол слюды — грубый, но ближе к среднему помолу, чем к мелкому дроблению. Футеровка, конструкция которой приведена на рисунке 2.4.3, пригодна больше для очень грубого помола, чем для описанного выше. На рисунке 2.4.7 изображена волнистая футеровка с распорными клиньями. Кроме того, данная футеровка барабанных мельниц является самой распространенной и выпускается отечественными заводами.
Рисунок 2.4.7. Волнистая футеровка с распорными клиньями
Крепление к барабану ступенчатых и волнистых футеровочных плит шаровых мельниц осуществляется чаще при помощи болтов с фасонными головкам. Для посадки фасонных головок болтов в тело плиты последние имеют отверстия овальной формы, идущие на конус в направлении к барабану. На рисунке 2.4.8 изображен болт для крепления футеровочных плит к барабану.
Рисунок 2.4.8. Болт для крепления футеровочных плит к барабану:
1 — упругая шайба; 2 — уплотняющая шайба; 3- корпус барабана Также футеровочные плиты устанавливают и на торцевых частях барабана. У мельниц с решеткой роль футеровки торцевой части барабана на разгрузочном конце выполняет сама решетка, снабженная центральной футеровкой. Футеровку загрузочной и разгрузочной крышек чаще выполняют гладкой, состоящей из отдельных секторов. Футеровки загрузочной и разгрузочной цапф делают в виде вставных втулок разной конструкции. Загрузочный патрубок выполняют из чугуна в виде конуса, расширяющегося в сторону барабана. Футеровку разгрузочной цапфы выполняют в виде чугунной воронки с гладкой внутренней поверхностью.
На рисунке 2.4.9 приведена примерная конструкция барабанной мельницы мокрого помола, которую предполагается использовать при производстве молотой слюды. Для поддержания в барабане определенного уровня пульпы и вывода измельченного материала из зоны измельчения перед торцовой крышкой 15 устанавливают диафрагму. Она состоит из круглой решетки 9 с ребрами 10. Форма ребер соответствует наклону торцовой крышки. Пространство между решеткой и крышкой делится ребрами на секторы. Со стороны барабана против отверстий на решетку укладывают колосники 8 и закрепляют их с помощью кольца 11 и болтов 12. Этими же болтами притягивают к торцовой крышке и диафрагму.
Пульпа через колосники и отверстия в решетке попадает в нижние секторы между диафрагмой и крышкой. При вращении барабана секторы поднимаются вверх, а находящаяся в них пульпа стекает в выводную цапфу и удаляется из измельчителя.
Рисунок 2.4.9. Разрез барабанной мельницы мокрого помола:
1 — улитковый питатель; 2 — загрузочный вкладыш; 3 — подшипник; 4 -передняя крышка с цапфой; 5 — барабан; 6 — броневые плиты; 7 — люк; 8 — колосники; 9 — решетка диафрагмы; 10 — ребра решетки; 11- кольцо; 12 — болты; 13 — выводной вкладыш; 14 — центральная труба; 15 — задняя крышка; 16 — венцовая шестерня
Уровень пульпы в барабане, из которого она начинает переливаться в секторы, регулируется закрытием или открытием отверстий в решетке. Если в решетке открыты все отверстия, то в секторы попадает пульпа из самых нижних слоев материала в барабане. Если же в решетке все отверстия закрыты, то пульпа может выходить только через центральное отверстие в диафрагме и трубу 14. Следовательно, в этом случае уровень пульпы должен подниматься выше нижней точки центрального отверстия. Открытие и закрытие отверстий в решетке, а также очистку этих отверстий и колосников производят через люки, предусмотренные в крышке. Колосники устанавливают на решетке так, что во время вращения барабана они могут перемещаться в радикальном направлении и таким образом самоочищаться. Загрузку шаров в мельницу и их выгрузку производят через люки 7.
Исходный материал вместе с определенным объемом жидкости поступает в специальный приемный короб, устанавливаемый под улитковым питателем. Днище короба имеет цилиндрическую форму с радиусом цилиндра, несколько большим радиуса вращения крайней точки черпака питателя. При вращении барабана вместе с ним вращается и питатель, захватывая черпаком пульпу из короба. Зачерпнутая питателем пульпа по улитке проходит через загрузочный вкладыш 2 в зону измельчения, а измельченный материал также в виде пульпы, пройдя разгрузочную диафрагму и выводной вкладыш 13, выходит из мельницы. Мельницы этого типа работают в замкнутом цикле с гидравлическими классификаторами. [2]
2.5 Классификация
Измельчение слюды осуществляется в замкнутом цикле, т. е. материал неоднократно проходит через барабанную мельницу. Измельченный материал из мельницы поступает в классификатор, где из продукта выделяются частицы материала размерами больше допустимого предела, которые возвращаются в ту же мельницу. На рисунке 2.5.1 представлена схема цикла измельчения слюды. Частицы размером 315 мкм и меньше удаляются в слив и далее поступают в центрифугу, а частицы с размером больше 315 мкм возвращаются обратно на доизмельчение в мельницу.
ИСХОДНЫЙ МАТЕРИАЛ
20 мм
0,315 мм КЛАССИФИКАЦИЯ ПОВЕРОЧНАЯ
0,315 мм Рисунок 2.5.1. Замкнутый цикл измельчения Аппаратами для гидравлической классификации являются спиральные классификаторы и гидроциклоны. Первые применяются преимущественно в первой из двух или трех стадий измельчения при небольшой и средней производительности измельчительных переделов. Гидроциклоны могут устанавливаться как в первой, так и во второй стадиях измельчения, а также при доизмельчении продуктов. Гидроциклоны, используемые в качестве классификаторов, обеспечивают то же качество разделения, что и механические классификаторы, но имеют большую производительность. Достоинства гидроциклонов: высокая производительность, отсутствие движущихся частей, компактность, простота и легкость обслуживания, относительно небольшая стоимость. Выбираем в качестве классификатора гидроциклон.