Влияние некоторых рецептурно-технологических факторов на свойства неавтоклавного газобетона
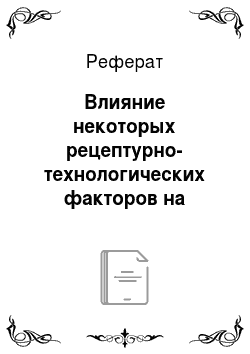
Анализ полученных данных показал, что введение «горбушки» в состав газобетонной смеси позволило изготовить газобетон повышенной прочности, но плотность при этом возросла. Для объективной оценки эффективности предложенного способа и его влияния на качество структуры газобетона определены значения коэффициентов конструктивного качества (ККК) для полученного в эксперименте газобетона. Коэффициент… Читать ещё >
Влияние некоторых рецептурно-технологических факторов на свойства неавтоклавного газобетона (реферат, курсовая, диплом, контрольная)
Аннотация:
Статья посвящена вопросу повышения качества неавтоклавного газобетона. Рассмотрены теоретические аспекты, предложены рецептурно-технологические приемы, приведены результаты экспериментальных исследований. Изучена роль последовательности введения компонентов и режима приготовления газобетонной смеси. Выявлено влияние ускорителей твердения на свойства газобетона. Проанализированы пути утилизации отходов производства и целесообразного их применения.
Ключевые слова: Газобетон, структурообразование, технология, рецептура, утилизация, сульфат натрия, частично гидратированная цементная система, алюминиевая суспензия, ускоритель твердения, коэффициент конструктивного качества.
Улучшение свойств ограждающих конструкций и снижение стоимости строительства являются приоритетными задачами современной стройиндустрии.
Одним из наиболее востребованных теплоизоляционных материалов в строительстве является газобетон. По способу твердения различают автоклавный газобетон, который твердеет при избыточном давлении и повышенной температуре в специальных устройствах — автоклавах и неавтоклавный, предусматривающий естественное твердение или тепловлажностную обработку с использованием теплового воздействия при атмосферном давлении.
Неавтоклавные газобетоны характеризуются относительной простотой технологии их изготовления, несравнимо меньшей энергоемкостью и стоимостью оборудования для производства. Однако, неавтоклавные газобетоны характеризуются повышенной усадкой и пониженными прочностными характеристиками, в сравнении с автоклавными [1−2].
На процесс структурообразования и свойства газобетона оказывают влияние множество технологических факторов. Рациональные значения этих факторов позволяет значительно повысить качество структуры газобетона неавтоклавного твердения и приблизить его показатели качества к автоклавному ячеистому бетону. Проведенные нами исследования направлены на решение этой задачи в условиях производства стеновых газобетонных блоков на технологической линии ООО «БЕТОН ДОН» в г. Новочеркасске.
Объектами исследований были такие технологические факторы, как последовательность дозирования компонентов при приготовлении газобетонной смеси, использование добавок — ускорителей твердения и водотвердое отношение. Эти факторы были выбраны на основании предварительного анализа состояния производства и качества выпускаемой продукции.
На первом этапе исследований нами оценивалось влияние последовательности дозирования компонентов при приготовлении газобетонной смеси на показатели качества неавтоклавного газобетона. В наших исследованиях за базовый был принят порядок введения компонентов, реализуемый в условиях предприятия.
При базовой технологии в емкость турбулентного газобетоносмесителя дозируется вода (при t = 45°С), затем, при включенном смесителе, вводится песок, дозируются сухие добавки соды и сульфата натрия, после чего дозируется цемент. Все компоненты перемешиваются 4 мин. с момента затворения. После этого в мешалку подается алюминиевая суспензия, смесь перемешивается 20 сек. и заливается в формы.
Из литературных данных [1−4] и проведенных нами предварительных опытов установлено, что такие компоненты газобетонной смеси, как песок и газообразователь, рациональнее вводить в приготовленную цементную суспензию. На этом основании, при проведении экспериментов принята следующая схема приготовления смеси:
- — в емкость смесителя дозируется вода (при t = 45°С) и включается привод мешалки;
- — вводятся добавки соды и сульфата натрия и компоненты перемешиваются, в течение 15 сек.;
- — дозируется цемент, и суспензия перемешивается 30 сек.;
- — дозируется песок, и раствор перемешивается 4 мин. с момента затворения цемента;
- — в приготовленный раствор дозируется алюминиевая суспензия и смесь перемешивается еще 20 сек.
Из приготовленной газобетонной смеси, по заводской (З1) и экспериментальной (Э1) технологиям, изготовлены образцы газобетона.
Результаты испытаний образцов газобетона в 7-суточном возрасте нормального твердения приведены на рис. 1.

Рис. 1 — Результаты испытаний образцов (З1) и (Э1)
Анализ результатов испытаний образцов (З1) и (Э1) позволил сделать вывод, что при незначительном повышении плотности, прочность при сжатии образцов возрастает с Rсж = 0,62 МПа (у З1) до Rсж = 0,96 МПа (у Э1), а коэффициент конструктивного качества газобетона (универсальная характеристика качества структуры ячеистого бетона ККК = Rсж/с2) увеличивается на 15%.
С помощью микроскопа с 500-кратным увеличением нами был выполнен сравнительный анализ фотографий микроструктуры газобетонных образцов, изготовленных из контрольных составов (рис. 2а), и образцов, изготовленных по предложенной технологии (рис. 2б). Вторые характеризуются монодисперсной структурой пор, равномерно распределенных по всему объему.


а) б) Рис. 2 — Фотографии структуры газобетонных образцов, изготовленных по заводской технологии (а), и образцов, изготовленных по технологии с измененным порядком введения компонентов (б)
Полученные результаты позволили принять в дальнейших исследованиях предложенную нами последовательность введения компонентов и режим приготовления газобетонной смеси.
На втором этапе исследований исследовалось влияние ускорителей твердения на свойства газобетона.
В заводской технологии в качестве ускорителя твердения используется добавка сульфата натрия. При этом на предприятии скапливается значительное количество отходов производства в виде так называемой «горбушки», являющейся излишком срезаемой массы поризованной смеси, после прекращения вспучивания и набора требуемой пластической прочности структуры.
«Горбушка» представляет собой частично гидратированную цементную систему, содержащую кристаллы гидратных новообразований, в основном гидроалюминатов кальция. Установлено, что образование гидроалюминатов кальция в цементном растворе протекает очень интенсивно. В течение первых десяти минут после затворения цемента водой идет накопление в системе новообразований типа С3АН6 коллоидной степени дисперсности, которые образуют пространственную коагуляционную структуру. В дальнейшем, в течение примерно 30 минут наблюдается быстрый рост прочности этой структуры. Этот рост обусловлен как взаимодействием между частицами новообразований, так и образованием сростков кристаллов гидроалюминатов. Теоретически, если отход «горбушки» ввести в приготавливаемую газобетонную смесь, то гидратированные зерна цемента должны стать центрами кристаллизации гидратных новообразований, тем самым ускорить процессы структурообразования и твердения газобетона [5].
Для проверки выдвинутой гипотезы проведен эксперимент, в котором ускоритель твердения — сульфат натрия, применяемый в заводской технологии, заменен вводимой в состав приготавливаемой газобетонной смеси «горбушкой».
При проведении эксперимента готовилась контрольная газобетонная смесь З1, а срезанная с вспученных образцов «горбушка» вводилась в аналогично приготовленную смесь Э2 вместо сульфата натрия. Расход горбушки был принят в количестве 30% от массы цемента.
Сравнение производилось по следующим показателям: средняя плотность, прочность при сжатии, коэффициент конструктивного качества.
Результаты эксперимента представлены на рис. 3.

Рис. 3 — Результаты испытаний образцов (З1) и (Э2)
Анализ полученных данных показал, что введение «горбушки» в состав газобетонной смеси позволило изготовить газобетон повышенной прочности, но плотность при этом возросла. Для объективной оценки эффективности предложенного способа и его влияния на качество структуры газобетона определены значения коэффициентов конструктивного качества (ККК) для полученного в эксперименте газобетона. Коэффициент конструктивного качества газобетона заводского состава З1 на 9% ниже чем экспериментального состава Э2.
Проведенный эксперимент подтвердил эффективность введения на стадии приготовления газобетона добавки частично гидратированной газобетонной смеси. Это позволит не только утилизировать отходы газобетонной смеси, но и снизить издержки производства, за счет исключения из состава смеси добавки сульфата натрия.
Для оценки степени влияния количества «горбушки», вводимой в состав газобетонной смеси, на показатели качества газобетона, проведен эксперимент, с варьированием количества «горбушки» от 10 до 30% от массы цемента. Была произведена формовка контрольного (заводского) состава З1 с которого взята «горбушка» для введения в составы Э2, Э3, Э4 и Э5.
Таблица 1.
Количество вводимой «горбушки».
№. | Буквенное обозначение состава. | Количество вводимой «горбушки» от массы вяжущего, %. | |
Э2. | |||
Э3. | |||
Э4. | |||
Э5. | |||
Результаты эксперимента приведены на рис. 4.

Рис. 4. — Результаты испытаний образцов (З1), (Э2), (Э3), (Э4) и (Э5)
Анализ полученных данных показал, что введение «горбушки» в состав газобетонной смеси количестве 20% от массы цемента позволило получить газобетон повышенной прочности. При этом значение коэффициента конструктивного качества у состава Э4 на 20,4% выше чем у Э2 и на 31% выше чем у газобетона заводского состава, что позволило принять его за основу в дальнейших исследованиях. Структуры сравниваемых материалов представлены на рис. 5.


а) б) Рис. 5. — Фотографий структуры газобетонных образцов, изготовленных по заводской технологии (а), и образцов, изготовленных по технологии с использованием оптимального количеством «горбушки» (б)
рецептурный технологический неавтоклавный газобетон Анализ структуры газобетона позволил сделать вывод о том, что введение предварительно гидратированной газобетонной смеси обеспечивает формирование равномерно распределенной поровой структуры газобетона и более плотных межпоровых перегородок.
Проведенные нами исследования степени влияния частично гидратированной газобетонной смеси («горбушки», срезанной с вспученного газобетонного массива) на свойства газобетона позволили выявить оптимальную дозировку этой добавки. На следующем этапе исследований ставилась задача определить эффективность введения в состав газобетонной смеси комплексной добавки сульфата натрия и «горбушки».
Механизм действия добавки сульфата натрия в газобетонной смеси заключается в том, что, реагируя с гидратом окиси кальция, выделяющимся из цемента, он образует гипс по формуле (1):
Ca (OH)2 + Na2SO4 + nH2O = CaSO4x2H2O + 2NaOH + H2O (1).
Образующийся мелкодисперсный гипс реагирует с цементным клинкером и способствует более быстрой выкристаллизации новообразований из цементного геля [6].
Авторами проведены эксперименты по выявлению оптимального количества вводимой добавки — сульфата натрия в состав смеси в сочетании с ранее выявленным оптимальным содержанием добавки частично гидратированной газобетонной смеси. Исследовались составы, приведенные в таблице 2.
Таблица 2.
Количество вводимого сульфата натрия.
№. | Буквенное обозначение состава. | Количество вводимой сульфата натрия от массы вяжущего, %. | |
З1. | 1,54. | ||
Э4. | вместо сульфата натрия 20% горбушки от массы вяжущего. | ||
С1. | добавка «горбушки» 20% и сульфата натрия 1,23%. | ||
С2. | добавка «горбушки» 20% и сульфата натрия 2,4%. | ||
С3. | добавка «горбушки» 20% и сульфата натрия 3,7%. | ||
Результаты экспериментов приведены на рис. 6.

Рис. 6. — Результаты испытаний образцов (З1), (Э4), (С1), (С2) и (С3)
Анализ полученных данных показал, что введение в состав газобетонной смеси сульфата натрия в количестве 1,23% от массы цемента с оптимальной дозировкой «горбушки» (20%) позволило получить газобетон повышенной прочности (С1). Коэффициент конструктивного качества у состава С1 на 17% выше чем у Э4. Структуры сравниваемых материалов представлены на рис. 7.


а) б) Рис. 7. — Фотографий структуры газобетонных образцов, изготовленных по заводской технологии (а), и образцов, изготовленных по технологии с использованием оптимального сочетания добавок «горбушки» и сульфата натрия (б)
Подводя итог проведенным исследованиям, можно сделать следующие общие выводы:
- 1) На процесс структурообразования и свойства газобетона оказывает влияние порядок введения компонентов в газобетонную смесь. Коэффициент конструктивного качества газобетона при этом увеличивается почти на 15%.
- 2) Подтверждена эффективность введения на стадии приготовления газобетона добавки частично гидратированной газобетонной смеси, что позволяет не только утилизировать отходы газобетонной смеси, но и снизить издержки производства, за счет исключения из состава смеси добавки сульфата натрия.
- 3) Введение в состав газобетонной смеси сульфата натрия в количестве 1,23% от массы цемента с оптимальной дозировкой «горбушки» (20%) позволило получить газобетон повышенной прочности.
- 4) Комплекс проведенных исследований позволил повысить качество производимого газобетона, коэффициент конструктивного качества повысился почти в 2 раза в сравнении с исходным.
Вышеизложенные технологические решения позволяют повысить качество продукции и сократить издержки производства неавтоклавного газобетона, тем самым увеличивая его конкурентоспособность на рынке теплоизоляционных строительных материалов.
- 1. Ахманицкий Г. Я. Технология и оборудование для производства изделий из неавтоклавного ячеистого бетона. // Строительные материалы, 1993. № 8. С.14−16.
- 2. Волженский A.B., Чистов Ю. Д. Изготовление изделий из неавтоклавного газобетона. // Строительные материалы, 1993. № 8. С.12−14.
- 3. Лотов В. А., Митина H.A. Влияние компонентов смеси на свойства газобетона неавтоклавного твердения. // Сб. докл. междунар. научно-техн. семинара «Нетрадиционные технологии в строительстве», 25−28 мая 1999 г. Томск: ТГАСУ, 1999. С.94−98.
- 4. Горлов Ю. П. Технология теплоизоляционных и акустических материалов и изделий. М.: Высшая школа, 1989. 384 с., ил.
- 5. Шуйский А. И. Оптимизация процессов структурообразования и повышение качества газобетонных изделий: дисс. … канд. техн. наук. Ростов-на-Дону, 1983. С. 98−100.
- 6. Ружинский С. И. и др. Все о пенобетоне. 2-е изд., улучшенное и дополн. Спб, ООО «Строй Бетон», 2006, 630 с.: ил.
- 7. Мальцев В. Т., Ткаченко Г. А., Мальцев Н. В. О некоторых физикохимических методах воздействия на формирование структуры пенобетонов и их свойства // «Инженерный вестник Дона», 2012, № 1
- 8. Р. А. Торлин, А. И. Шуйский, А. А. Новожилов, Е. А. Торлина, С. Б. Языева. Активизация частично гидратированного цемента в электромагнитных активаторах // «Инженерный вестник Дона», 2011, № 2
- 9. Narayanan N, Ramamurthy K. Structure and properties of aerated concrete: a
review. Cem Concr Compos 2000; 22:321−9.
10. Sengupta J. Development and application of light weight aerated concrete blocks from yash. Indian Concr J 1992; 66:383±7.
References
- 1. Ahmanickij G.JA. Stroitelnye materialy. 1993. № 8. pp.14−16.
- 2. Volzhenskij A.B., CHistov JU.D. Stroitelnye materialy. 1993. № 8. pp.12−14.
- 3. Lotov V.A., Mitina H.A. Sb. dokl. mezhdunar. nauchno-tehn. seminara «Netradicionnye tehnologii v stroitelstve», 25−28 maja 1999g. Tomsk: TGASU, 1999. pp. 94−98.
- 4. Gorlov JU.P. Tehnologija teploizoljacionnyh i akusticheskih materialov i izdelij [The technology of thermal insulation and acoustic materials and products]. M.: Vysshaja shkola, 1989. 384 p., il.
- 5. Shujskij A.I. Optimizacija processov strukturoobrazovanija i povyshenie kachestva gazobetonnyh izdelij [Process optimization of structure and improving the quality of aerated concrete products]: diss. … kand. tehn. nauk. Rostov-na-Donu, 1983. pp.98−100.
- 6. Ruzhinskij S.I. i dr. Vse o penobetone [All of aerated concrete]. 2-e izd., uluchshennoe i dopoln. Spb, OOO «Stroj Beton», 2006, 630 p.: il.
- 7. Malcev V.T., Tkachenko G.A., Malcev N.V. Inzenernyj Vestnik Dona (Rus), 2012, № 1
- 8. R.A. Torlin, A.I.Shujskij, A.A.Novozhilov, E.A. Torlina, S.B. Yazyeva. Inzenernyj Vestnik Dona (Rus), 2011, № 2
- 9. Narayanan N, Ramamurthy K. Structure and properties of aerated concrete: a
review. Cem Concr Compos 2000; 22:321−9.
10. Sengupta J. Development and application of light weight aerated concrete blocks from Їy ash. Indian Concr J 1992; 66:383±7.