Методы управления автомобильным транспортом и его подсистемами
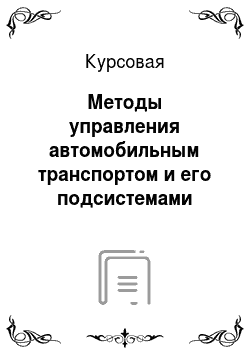
Основной задачей ГОАИ является систематизация, обработка, анализ и хранение информации о деятельности всех подразделений технической службы, а также планирование ТО и ремонтов. В состав ГОАИ входят работники, занимающиеся первичной обработкой информации, анализом информации и планированием. Обеспечение комплексов технического обслуживания и диагностики и ТР запчастями и материалами выполняется… Читать ещё >
Методы управления автомобильным транспортом и его подсистемами (реферат, курсовая, диплом, контрольная)
СОДЕРЖАНИЕ Введение
1. Теоретическая часть
1.1 Методы управления автомобильным транспортом и его подсистемами
1.2 Оборудование, используемое при ТО автомобиля
2. Определение оптимального срока службы автомобиля Заключение Список использованных информационных источников
ВВЕДЕНИЕ
автомобиль техническое обслуживание Автомобильный транспорт является наиболее массовым и удобным видом транспорта, обладающим большой маневренностью, хорошей проходимостью и приспособленностью для работы в различных климатических и географических условиях. Он является эффективным средством для перевозок грузов и пассажиров на относительно небольшие расстояния.
Автомобильная промышленность, непрерывно совершенствуя свою продукцию, обеспечивает народное хозяйство разнообразными перевозочными средствами, систематически работают над улучшением технологии производства и совершенствованием конструкции подвижного состава. Обеспечением его безотказности, долговечности и ремонтопригодности. При этом резко возрастает доля специализированного подвижного состава и автомобильных поездов повышенной грузоподъёмности.
Задачи службы технической эксплуатации АТП заключаются в постоянном поддержании высокой технической готовности подвижного состава, обеспечении его работоспособности в течение установленных сроков наработки. Сегодня для этих целей создаются крупные автотранспортные объединения, позволяющие улучшить показатели использования производственных площадей и оборудования за счет внедрения поточного метода производства всех видов технического обслуживания автомобилей, применения эффективных средств диагностики, механизации и автоматизации производственных процессов и внедрения нового высокопроизводительного оборудования.
Для выполнения поставленных задач на всех предприятиях, базах, отделениях постах необходимо широко использовать средства технической диагностики, максимально механизировать производственные участки и цеха технического обслуживания (ТО) и текущего ремонта (ТР) автомобилей, оснащать их подъёмно-транспортными механизмами и контрольно-регулировочными приборами, совершенствовать технологию ТО и ТР и управление производством, создавать требуемые производственно-бытовые и санитарно-гигиенические условия труда ремонтных рабочих. Проведение вышеперечисленных и других технических организационных мероприятий способствует повышению производительности труда при провидении ТО и выполнении ремонта подвижного состава, обеспечивает сокращение трудовых и материальных затрат.
Исходные данные, для выполнения контрольной работы:
Номер варианта № 22
1. Методы управления автомобильным транспортом и его подсистемами;
2. Оборудование, используемое при ТО автомобилей Определение оптимального срока службы автомобиля
1. ТЕОРЕТИЧЕСКАЯ ЧАСТЬ
1.1 Методы управления автомобильным транспортом и его подсистемами Руководство производством на большинстве предприятий полностью осуществляет начальник производства через подчиненных ему руководителей производственных подразделений. Непосредственное руководство производственными процессами на своих участках работы осуществляют руководители различных производственных подразделений. На АТП применяются следующие методы организации производства ТО и ТР транспортных средств: специализированных бригад, комплексных бригад, агрегатно-участковый, операционно-постовой, агрегатно-зональный. Из них первые три получили широкое распространение.
Метод специализированных бригад представляет собой такую форму организации производства, при которой работы каждого вида ТО и ТР выполняются специализированными бригадами рабочих (рисунок 1.1). Управление технической службой АТП в этом случае осуществляет главный инженер. Он руководит производством через непосредственного подчиненного ему начальника производства.
Рисунок 1.1 — Управление производством при организации труда методом специализированных бригад
Бригады, выполняющие ЕО, ТО-1, ТО-2 и ремонт агрегатов, комплектуются из рабочих соответствующих специальностей, имеют свой объем работ, соответствующий штат исполнителей и отдельный фонд заработной платы. При такой организации работ обеспечивается технологическая однородность каждого участка, облегчается маневрирование внутри него людей, инструмента, оборудования, упрощаются руководство и учет количества выполненных различных видов технических воздействий. Одним из недостатков данной структуры и организации работ является низкое качество работ. Этот недостаток обусловлен отсутствием необходимой ответственности исполнителей за техническое состояние и надежную работу автотранспортных средств. Сложность анализа причин отказов и выявления конкретных виновников недостаточной надежности автомобилей в эксплуатации приводит к значительному увеличению числа ТР и снижению коэффициента технической готовности парка. В результате увеличиваются трудовые ресурсы и финансовые затраты.
Рисунок 1.2 — Управление производством при организации труда методом комплексных бригад Метод комплексных бригад характеризуется тем, что каждое из подразделений крупного АТП имеет свою комплексную бригаду, выполняющую ТО-1, ТО-2 и ТР закрепленных за ней автомобилей (рисунок 1.2). Централизованно выполняются только ЕО и ремонт агрегатов. Комплексные бригады укомплектовываются исполнителями различных специальностей, необходимых для выполнения закрепленных за бригадой работ.
При такой организации недостаточная ответственность за качество ТО, а следовательно, и увеличение объема работ по ТР существует, как при методе специализированных бригад, но ограничиваются размерами комплексной бригады. Кроме того, данный метод затрудняет организацию поточного ТО автомобилей. Материально-технические средства распределяются по бригадам и, следовательно, используются неэффективно.
Агрегатно-участковый метод состоит в том, что все работы по ТО и ремонту подвижного состава распределяются между производственными участками, полностью ответственными за качество и результаты своей работы (рисунок 1.3). Эти участки являются основными звеньями производства. Каждый из основных производственных участков выполняет все работы по ТО и ТР одного или нескольких агрегатов по всем автомобилям АТП. Моральная и материальная ответственность при данной форме организации производства становятся совершенно конкретными. На крупных и средних АТП с интенсивным использованием подвижного состава число участков, между которыми распределяются работы по ТО и ТР, принимаются от четырех до восьми. Различают следующие участки:
— ТО и ремонт двигателей, сцепления, коробок передач, стояночного тормоза, карданной передачи, редуктора, самосвального механизма;
— ТО и ремонт переднего моста, рулевого управления, заднего моста, тормозной системы, подвески автомобиля;
— ТО и ремонт систем электрооборудования и питания;
Рисунок 1.3 — Управление производством при организации труда агрегатно-участковым методом
— ТО и ремонт рамы, кузова, кабины, оперения и облицовки;
— Медницкие, жестяницкие, сварочные, кузнечные, термические, и кузовные работы;
— ТО и ремонт шин;
— Слесарно-механические работы;
— Уборочно-моечные работы.
Неправильное использование материальных ресурсов происходит из-за децентрализованного распределения автомобилей по постам и исполнителям. Применительно к существующей планово-предупредительной системе обслуживания и ремонта дорожно-транспортных средств с использованием метода специализированных бригад разработана система управления производством, получившая название централизованной системы управления ЦУП (рисунок 1.4). Она предусматривает:
— четкое разделение административных и оперативных функций между руководящим персоналом;
— сбор, обработку и анализ информации о состоянии производственных ресурсов и объемах работ, подлежащих выполнению;
— организацию производства ТО и ремонта дорожно-транспортных средств, основанную на технологическом принципе формирования производственных подразделений;
— объединение производственных подразделений, выполняющих однородные работы, в производственные комплексы;
— исполнение средств связи, автоматики, телемеханики и вычислительной техники;
— подготовку производства, осуществляемую централизованно комплексом производства, т. е. комплектование оборотного фонда запасных частей и материалов, хранение и регулирование запасов, доставку агрегатов, узлов и деталей на рабочие места, мойку и комплектование ремонтного фонда, обеспечение рабочих инструментом, перегон автомобилей.
Рисунок 1.4 — Схема организации централизованного управления производством ТО и ТР ЦУП состоит из двух подразделений:
— группы оперативного управления (ГОУ);
— группы обработки и анализа информации (ГОАИ).
ЦУП возглавляет начальник, а основную оперативную работу по управлению выполняют диспетчеры ГОУ и техники-операторы. Численность персонала ЦУП определяется общим объемом выполняемых им работ. Основное руководство всеми работами по ТО и ремонту автомобилей осуществляет ГОУ. На персонал ГОУ возлагается выполнение следующих задач:
— принятие смены;
— осуществление оперативного контроля выполнения планов проведения диагностирования, ТО-1, ТО-2;
— осуществление оперативного планирования, регулирования, учета и контроля выполнения ТО и ремонтов.
Основной задачей ГОАИ является систематизация, обработка, анализ и хранение информации о деятельности всех подразделений технической службы, а также планирование ТО и ремонтов. В состав ГОАИ входят работники, занимающиеся первичной обработкой информации, анализом информации и планированием. Обеспечение комплексов технического обслуживания и диагностики и ТР запчастями и материалами выполняется по указанию ЦУП комплексом подготовки производства, оперативное руководство которым осуществляется диспетчером ЦУП. На основании информации о наличии запасов на промежуточном и основном складах и ожидаемом пополнении запасов начальник ЦУП совместно с начальниками комплексов подготовки производства и РУ планирует задание на ремонт агрегатов, узлов, деталей различным участкам комплекса РУ. В соответствии с этим планом участок комплектации комплекса подготовки производства доставляет неисправные элементы на участки комплекса РУ, а отремонтированные агрегаты, узлы и детали — на основной или промежуточный склады. На каждом предприятии кроме центрального склада, находящегося в ведении отдела материально-технического снабжения, организуется промежуточный склад, входящий в состав комплекса подготовки производства. Основную часть номенклатуры промежуточного склада составляют агрегаты, узлы и детали, отремонтированные и изготовленные собственными силами в ремонтных отделениях, а также полученные с авторемонтных заводов.
1.2 Оборудование, используемое при ТО автомобилей В настоящее время при проведении ТО и ремонта автомобилей используются разнообразные подъемники, которые классифицируются по способу установки, типу механизма подъемника и привода, месту установки, по количеству стоек и по конструкции опорной рамы (рисунок 1.5)
Рисунок 1.5 — Классификация подъемных устройств, применяемых при ТО и ТР автомобилей Простейшими подъемными механизмами являются механические (винтовые, реечные), гидравлические и пневматические домкраты. Винтовые домкраты получили широкое распространение, так как обладают высокой надежностью и грузоподъемностью (от 1 до 20 т), имеют свойства самоторможения, которое обеспечивается выбором такого угла подъема винтовой резьбы, который был бы меньше угла в винтовой паре.
Простейший винтовой домкрат представлен на рисунке 1.6. Он состоит из корпуса 6, в который запрессована бронзовая гайка 4, с трапецеидальной резьбой, винта 5 и опоры 1. Опора выполнена самоустанавливающейся для наилучшего ее прилегания к поднимаемой поверхности и крепится к винту гайкой 2. При подъеме опора не вращается. Вращение винта осуществляется рукояткой 3.
1-опора; 2-гайка; 3-рукоятка; 4-бронзовая гайка; 5-винт; 6-корпус;
Рисунок 1.6 — Схема винтового домкрата К недостаткам относят низкий КПД (0,3…0,4) и малую скорость подъема (20…30 мм/мин).
Гидравлические домкраты (рисунок 1.7) имеют компактную конструкцию при высокой грузоподъемности (от 3 до 50 т). При перемещении плунжера 3 рукояткой 1 вправо масло засасывается из резервуара в полость 2 через шариковый клапан 4. Под действием создаваемого в полости разряжения, шариковый клапан 8 закрыт. При перемещении плунжера влево под действием возникающего в полости 2 давления шариковый клапан 4 закрывается, а клапан 8 открывается и масло поступает под плунжер 5, в результате чего он начинает перемещаться в вверх. Герметизация плунжера осуществляется уплотнением 6. Самоторможение при прекращении движения плунжера достигается закрытием шарикового клапана под действием давления в подплунжерной полости. Для опускания груза открывают кран 7, и масло из подплунжерной полости сливается в резервуар.
1-рукоятка; 2-полость всасывания; 3-плунжер; 4-шариковый клапан; 5-плунжер; 6-уплотнение; 7-кран; 8-шариковый клапан;
Рисунок 1.7 — Схема гидравлического домкрата У пневматических домкратов основным исполнительным механизмом является пневматический цилиндр с двухходовым поршнем. С помощью золотникового устройства сжатый воздух поочередно подается в полости пневмоцилиндра, обеспечивая подъем или опускание груза. Подача сжатого воздуха к золотниковому устройству осуществляется под давлением от 3 до 6 МПа.
Электрогидравлические подъемники (рисунок 1.8) обладают более высокой скоростью подъема (до 2 м/мин) и имеют высоту подъема 1,5…2,0 метров. Подъемник имеет грузоподъемности (2, 4, 6, 8, 12, 16, 20 т) и работает следующим образом. При включении электродвигателя привода подъемника масло из бака 1 подается насосом 2 через обратный клапан 3 к распределителю 4. При подъеме автомобиля рукоятку распределителя переводят и удерживают в положении «подъем», после чего масло начинает поступать через гидрозамок 5 в рабочую полость, А гидроцилиндра 6. Из полости Б масло через распределитель сливается сквозь фильтр 7 в расходный бак. При засорении фильтра масло сливается в бак через предохранительный клапан 8. При опускании рукоятки золотник распределителя занимает нейтральное положение. При нажатии на рукоятку распределителя в положение «опускание» рабочая жидкость подается насосом в полость Б гидроцилиндра, а полость, А соединяется распределителем со сливной магистралью, так как управляющее давление открывает клапан 5. Если давление в напорной магистрали превышает 0,9 МПа, открывается предохранительный клапан 9 и рабочая жидкость от насоса сливается в бак 1.
1-бак; 2-насос; 3-обратный клапан; 4-распределитель; 5-гидрозамок; 6-гидроцилиндр; 7-фильтр; 8-предохранительный клапан; 9-предохранительный клапан;
Рисунок 1.8 — Схема электрогидравлического одноплунжерного подъемника Электромеханические подъемники (рисунок 1.9) выпускаются одно-, двух-, четырехи шестистоечными грузоподъемностью от 1,5…14 тонн.
1-опорный подшипник; 2-цепная передача; 3-грузоподъемная гайка; 4-грузоподъемный винт; 5-коническая передача; 6-мотор-редуктор; 7-радиальный подшипник; 8- грузоподъемный винт;9- грузоподъемная гайка; 10, 11-цепная передача;
Рисунок 1.9 — Схема электромеханического подъемника Такой подъемник состоит из двух стоек 3 коробчатой конструкции, приваренных к фундаментальной плите, опорной рамы 6 и подхватов 5. В каждой стойке размещается ходовой винт 4, по которому перемещается грузоподъемная гайка 3, шарнирно соединенная с кареткой, несущей на себе подхваты. Крутящий момент от мотор-редуктора 6 передается через коническую передачу 5 на первый грузоподъемный винт 4. При вращении гайка 3 поднимается вверх или опускается вниз в зависимости от направления вращения ротора электродвигателя. Крутящий момент на второй винт 8 передается с помощью цепной передачи 2, 10, 11. Для обеспечения синхронного движения грузоподъемных гаек 3,9 в одну сторону винт 4 имеет правую, а винт 8 — левую нарезку. Сами винты вращаются на радиальных 7 и опорных 1 подшипниках. Высота подъема, как правило, не превышает 1,8 м за время 0,7…1 мин. Подъемник устанавливают без фундаментов на бетонный пол и крепят анкерными болтами.
Для вывешивания отдельной оси или колес грузового автомобиля или автобуса на осмотровой канаве используются двухстоечные канавные электромеханические подъемники (рисунок 1.10).
1-электродвигатель; 2-червячный редуктор; 3-карданная передача; 4- червячный редуктор; 5-стойка; 6-верхняя траверса; 7-опора ходового винта; 8-ходовой винт; 9-муфта; 10-концевой выключатель; 11-контрольный выключатель; 12-штанги; 13-нижняя траверса с грузоподъемной гайкой; 14-страхующая гайка; 15- концевой выключатель; 16- контрольный выключатель;
Рисунок 1.10- Схема двухстоечного канавного подъемника Подъем автомобиля осуществляется верхними траверсами, упираемыми в мост или раму автомобиля. При подъеме крутящий момент от электродвигателя передается на ходовые винты 8 через два червячных редуктора 2 и 4, связанных между собой карданной передачей 3. Вращение винтов приводит к линейному перемещению нижней траверсы 13 с запрессованной грузоподъемной гайкой. Верхняя траверса 6 связана с нижней через две штанги 12, и все элементы перемещаются как одно целое. В конструкции стенда используются червячные редукторы и упорная трапецеидальная резьба ходовых винтов.
Для выполнения монтажно-демонтажных работ и транспортировки агрегатов используется подъемно-транспортное оборудование, которое подразделяется на монорельсы с тельферами, кран-балки, передвижные краны, грузовые тележки, электротельферы. На небольших АТП применяют монорельсы с электротельферами грузоподъемностью до 1 т и подвесные кран балки грузоподъемностью до 3 тонн. Для транспортировки агрегатов могут также использоваться грузовые тележки.
Для перемещения автомобилей на поточных линиях ТО могут использоваться конвейеры непрерывного или прерывного действия. По способу передачи движения конвейеры подразделяются на несущие, толкающие или тянущие.
1-приводная станция; 2-каретки; 3-тяговая цепь; 4-натяжная станция; 5-направляющий путь; 6-ведущая звездочка;
Рисунок 1.11- Схема толкающего конвейера Толкающие конвейеры (рисунок 1.1.11) могут перемещать автомобиль за заднее колесо, задний или передний мост. Они состоят из приводной 1 и натяжной 4 станции, тяговой цепи 3 и направляющего пути 5. Привод конвейера осуществляется натяжной станцией, в состав которой входят тяговый электродвигатель, редуктор, клиноременная передача и ведущая звездочка 6. Натяжная станция 4 используется для натяжения цепи. Цепь несет толкающие каретки 2, которые движутся по направляющим путям и, воздействуя на мосты или колеса автомобиля, заставляют его перемещаться с поста на пост. Их скорость перемещения — до 10 м/мин.
Для снижения простоя автомобилей в ТО, обеспечения возможности выполнения смазочных работ, уменьшения расхода масел и смазок необходимо использовать специализированное смазочно-заправочное оборудование (рисунок 1.12).
Рисунок 1.12- Схема классификации смазочно-заправочного оборудования Для заправки автомобилей моторными маслами применяются маслораздаточные колонки с насосной установкой (рисунок 1.13). Масло из резервуара 1 масляным насосом 3 подается в напорную магистраль. При превышении давления масла в напорной магистрали нормативного значения открывается предохранительный клапан 4. Чтобы система была заполнена маслом, установлен обратный клапан 5. При заправке маслом двигателя необходимо открыть кран 10. Насосная установка погружного типа монтируется на горловине резервуара с маслом. Фланцевый электродвигатель соединяется с насосом валом, проходящим в подвесной трубе. Пуск и остановка электродвигателя осуществляется с помощью реле давления, настроенного на предельные значения давления в системе.
1-резервуар; 2-фильтр грубой очистки; 3-насос; 4-предохранительный клапан; 5-обратный клапан; 6-воздушно-гидравлический аккумулятор; 7-манометр; 8-фильтр тонкой очистки топлива; 9-расходомер; 10-кран; 11-раздаточный пистолет;
Рисунок 1.13 — Гидравлическая схема маслораздаточной колонки
1-электродвигатель; 2-муфта; 3-приводной вал; 4-муфта; 5-насос; 6-фильтр; 7-блок клапанов; 8-воздушно-гидравлический аккумулятор; 9-реле давления; 10-манометр; 11-раздаточный ствол; 12-отсечный клапан; 13-запорный клапан; 14-раздаточный рукав; 15-маслопровод;
Рисунок 1.14 — Установка для заправки трансмиссионным маслом Аналогичные гидравлическую и электрическую схемы имеют установки для раздачи трансмиссионных масел (рисунок 1.14). Они монтируются на стационарной емкости 150…200литров и включают в себя электропривод погружного шестеренчатого насоса 5, который подает масло к двум раздаточным рукавам 14.
Для выравнивания давления масла в системе имеется воздушно-гидравлический аккумулятор 8. Реле давления настроено на минимальное и максимальное давление. При выходе за его пределы происходит соответственно включение или отключение электропривода насоса. В период между включениями электродвигателя масло подается из аккумулятора за счет давления воздушной подушки на масло, поступившее в него при включенном приводе насоса. Для очистки масла установка имеет фильтр 6.
В небольших и средних АТП для раздачи пластичных смазок используют передвижные солидолонагнетатели (рисунок 1.15).
1-плита; 2-бункер; 3-шнек; 4-фильтр; 5-плунжерный насос; 6-реле давления; 7-электродвигатель; 8-напорный трубопровод; 9-редуктор; 10-поддон редуктора;
Рисунок 1.15 — Схема передвижного солидолонагнетателя В их привод входят электродвигатель 7 и двухступенчатый редуктор 9, смонтированный в поддоне 10. При включении электродвигателя вторая ступень редуктора приводит во вращение шнек 3, который обеспечивает подачу пластичной смазки под небольшим давлением из бункера 2 к плунжерному насосу 5, приводимому в работу первой ступенью редуктора. Плунжерный насос увеличивает давление смазки, подаваемой к раздаточному пистолету, до 15…20 МПа. Реле давления 6 отключает электропривод установки при величине давления, превышающей 40 МПа.
При проведении технических обслуживаний автомобилей большое внимание уделяется проверке затяжки резьбовых соединений. Для повышения производительности труда при выполнении крепежных и разборочно-сборочных работ используют гайковерты (пневматические и электромеханические).
Гайковерт (рисунок 1.16) имеет реверсивный пневматический двигатель роторного типа. Изменение вращения ротора 6 достигается пуском воздуха в соответствующий канал статора 5. Для повышения развиваемого момента гайковерт снабжен планетарным редуктором и ударным механизмом. Ударный механизм состоит из массивного корпуса 9, пружины 10 и шпинделя 12 с двумя сателлитными шестернями 8, образующими с центральным колесом 7 планетарный редуктор. Шпиндель и корпус связаны между собой двумя шариками 11, катающимися по спиральным канавкам, нарезанным в шпинделе и корпусе. Крутящий момент на ведущую вилку 13 передается через эту винтовую пару. После прекращения свободного вращения, вила 13 и входящий с ней в зацепление корпус ударного механизма 9 останавливаются. Шпиндель же продолжает вращаться, заставляя корпус 9 по винтовой нарезке подниматься вверх. Происходит разобщение кулачков корпуса 9 и вилки 13. После этого корпус разгоняется шпинделем и под воздействием пружины 10 перемещается в направлении обратно, ударяя по кулачкам вилки. Требуемое усилие затяжки достигается за несколько таких последовательных ударов.
1-штуцер; 2-рукоятка; 3-кнопка управления двигателем; 4-корпус; 5-статор; 6- ротор; 7-центральное колесо редуктора; 8-сателлит; 9-корпус ударного механизма; 10-пружина; 11-шарик; 12-шпиндель; 13-вилка; 14-торцовая головка;
Рисунок 1.16 — Схема пневматического гайковерта Электромеханический передвижной реверсивный инерционно-ударный гайковерт для гаек колес грузовых автомобилей и автобусов (рисунок 1.17)
Рисунок 1.17 — Электромеханический инерционно-ударный гайковерт Смонтирован на трехколесной тележке с коробчатой стойкой, по которой перемещается каретка с вертикальной плитой 12 (рисунок 1.1.18), к которой крепятся: электродвигатель мощностью 0,55 кВт, приводимый им во вращение посредством клиноременной передачи маховик 6, передняя опора шпинделя 3 и электромагнит 11, используемый для включения в работу ударного механизма. При вхождении наковальни 8 в зацепление с ударником 7 крутящий момент от маховика 6 ударным импульсом передается на шпиндель 2 и ключ торцового типа. Крутящий момент затяжки на ключе за один удар составляет 400 Н.м. Максимально допустимый момент 1500 Н. м достигается за четыре-пять включений.
1-ключ; 2-шпиндель; 3-передняя опора; 4-возвратная пружина; 5-ступица; 6-маховик; 7-ударник; 8-наковальня; 9-рычаг; 10-корпус; 11-электромагнит; 12-плита;
Рисунок 1.18 — Схема ударного механизма гайковерта
2. ОПРЕДЕЛЕНИЕ ОПТИМАЛЬНОГО СРОКА СЛУЖБЫ АВТОМОБИЛЯ Затраты, связанные с поддержанием автомобиля в работоспособном состоянии в течении года определяем по формуле:
(2.1)
где: — затраты на ТО, млн. руб.;
— затраты на ремонт, млн. руб.;
— затраты, связанные с потерей дохода от простоев автомобиля, обусловленных его технической готовностью, млн. руб.
Оптимальный срок службы автомобиля, соответствующий минимуму затрат определяем по формуле:
(2.2)
где: — стоимость автомобиля при его покупке, млн. руб.;
— срок службы автомобиля, лет.
Определяем удельную годовую стоимость автомобиля по формуле:
(2.3)
Полученные данные подставляем в формулу (2.1) получаем затраты, связанные с поддержанием автомобиля в работоспособном состоянии в течении срока службы:
Полученные данные подставляем в формулу (2.2) получаем оптимальный срок службы автомобиля, соответствующий минимуму затрат:
Все рассчитанные данные заносим в таблицу 2.1.
Таблица 2.1 — Исходные данные
72,50 | 96,5 | ||||||
45,33 | 75,33 | ||||||
36,25 | 72,25 | ||||||
24,17 | 72,17 | ||||||
20,71 | 74,71 | ||||||
18,13 | 81,13 | ||||||
Подставив полученные числовые значения в MS Office Excel получаем график зависимости затрат на автомобиль от срока службы:
График 2.1 — Зависимость затрат на автомобиль в зависимости от срока службы
ЗАКЛЮЧЕНИЕ
В данной контрольной работе я раскрыл тему «Методы управления автомобильным транспортом и его подсистемами», и «Оборудование, используемое при ТО автомобиля». Расчитал затраты, связанные с поддержанием автомобиля в работоспособном состоянии в течении года; определил оптимальный срок службы, соответствующий минимуму затрат; рассчитал удельную годовую стоимость автомобиля. По этим данным построили график «Зависимость затрат на автомобиль в зависимости от срока службы». Построение выполнялось в MS Office Excel для более точного расположения кривых на графике.
СПИСОК ИСПОЛЬЗОВАННЫХ ИНФОРМАЦИОННЫХ ИСТОЧНИКОВ
1. Техническая эксплуатация автомобилей: учеб. Пособие /Н. А. Коваленко, В. П. Лобах, Н. В. Вепринцев. — Минск: Новое знание, 2008. — 352 с.:ил. — (Профессиональное образование).
2. Болбас М. М., Капустин Н. М., Савич А. С. Проектирование предприятий автомобильного транспорта: учебник/ М. М. Болбас, Н. М. Капустин, А. С. Савич и др; под ред. М. М. Болбаса — Мн.: Адукацыя i выхаванне, 2004. — 528 с.
3. Кучур С. С., Болбас М. М., Ярошевич В. К. Научные исследования и решение инженерных задач: учебн. Пособие/С. С. Кучур, М. М. Болбас, В. К. Ярошевич. — Мн.: Адукацыя i выхаванне, 2003. — 251 с.
4. Ящерицин П. И., Махаринский Е. И. Планирование эксперимента в машиностроении: [Справ. пособие]/ П. И. Ящерицин, Е. И. Махаринский — Мн.: Высш. шк., 1985 — 286 с.