Организация производственного процесса на предприятии по выпуску биотоплива
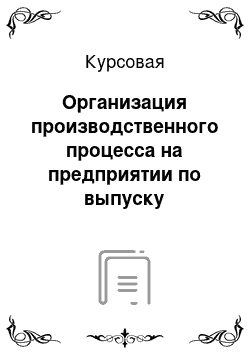
Сырьем для производства брикетов является тот же материал, что и для изготовления гранул — опилки различных пород древесины, щепа, лузга подсолнечника, гречихи, солома и многие другие растительные отходы. Технология производства брикетов схожа с технологией гранулирования, но более простая. Брикеты бывают разных форм — в виде кирпича, цилиндра или шестигранника с отверстием внутри. Стандартных… Читать ещё >
Организация производственного процесса на предприятии по выпуску биотоплива (реферат, курсовая, диплом, контрольная)
Курсовой проект
Организация производственного процесса на предприятии по выпуску биотоплива
Гранулирование отходов позволяет сократить статьи расходов предприятия, платежи за негативное воздействие на окружающую среду, за вывоз и утилизацию отходов, экономить на затратах на складские помещения. Гранулы занимают намного меньше места, чем отходы в чистом виде. Срок хранения у гранул практически неограничен. Немаловажным преимуществом гранулирования отходов является простая транспортировка. Благодаря правильной форме, небольшому размеру, однородной консистенции и высокой насыпной плотности продукта, гранулы можно пересыпать через специальные рукава, что позволяет автоматизировать процессы погрузки и разгрузки. Преимущества топливных гранул очевидны, поэтому популярность их использования увеличивается с каждым днем.
Развитие новых технологий для комплекса предприятий по сбору и утилизации отходов уже многие годы является важной задачей. Вторичная переработка отходов ЛПК является основной задачей ежедневных разработок в области производства биотоплива.
1. Технология производства топливных гранул
Древесные топливные гранулы (пеллеты, ДТГ) — это небольшие цилиндрические прессованные древесные изделия диаметром 4−12 мм, длиной 20−50 мм, переработанные из высушенных остатков деревообрабатывающего и лесопильного производства: опилки, стружка, древесная мука, щепа, древесная пыль и т. д. Гранулы используются в котлах для получения тепловой и электрической энергии путем сжигания. Преимуществом использования древесных гранул перед другими видами топлива является:
— снижение вредных выбросов в атмосферу: древесное биотопливо признано СО2 — нейтральным, т. е. при его сжигании количество выделяемого углекислого газа в атмосферу не превышает объем выбросов, который бы образовался путем естественного разложения древесины;
— бoльшая теплотворная способность: по сравнению со щепой и с кусковыми отходами древесины. Энергосодержание одного килограмма древесных гранул соответствует 0,5 литра жидкого дизельного топлива; древесные гранулы не уступают по теплотворной способности ни углю, ни мазуту;
— низкая стоимость по сравнению и дизтопливом и отоплением электричеством,
— чистота помещения, в котором установлен котел,
— возможность автоматизации котельных.
На производство одной тонны гранул уходит 3−5 кубометров древесных отходов естественной влажности.
Гранулирование состоит из нескольких этапов: измельчение сырья, подача и дозирование, прессование, охлаждение и просеивание, фасовка и складирование готовой продукции.
Измельчение сырья. Начальным этапом гранулирования является измельчение исходного сырья. Для получения качественных и прочных гранул необходимо измельчить сырье до фракции размером 1−3 мм. Солома и сено измельчаются в роторном измельчителе рулонов соломы и сена. До измельчения полученной сечки измельчение другого сырья (опилок, стружки, щепы, лузги) происходит в дробилке, оснащенной пневматической загрузкой и выгрузкой сырья.
Сушка. Древесное сырье перед прессованием должно иметь влажность 10% ± 2%. Сырье с большей или меньшей влажностью требует дополнительного увлажнения или дополнительной сушки. Сушилки делятся на два типа: барабанного и ленточного. Ленточного типа: дороже, но безопасней. По типу применяемого сушильного агента они подразделяются на сушилки на топочных газах, горячем воздухе и водяном паре. По типу применяемого вида топлива для производства ДТГ: газовые и на древесных отходах.
Доизмельчение сухого сырья. Для устойчивой работы пресса входная фракция должна быть не более 4 мм. Такую фракцию может обеспечить молотковая мельница, стружечный станок или дезинтегратор.
Водоподготовка. Сырье с влажностью менее 8% плохо поддается прессованию, поэтому требуется, устройство дополнительного увлажнения сырья. Лучший вариант — это шнековые смесители, имеющие возможность подачи воды или пара. Пар применяют для снижения прочности и увеличения пластичности древесного сырья твердых пород. Прессы некоторых производителей из-за конструктивных особенностей не требуют добавления пара. Некоторые применяют пар для старого, слежавшегося сырья, но таким сырьем сложно получить гранулы хорошего качества.
Подача и дозирование. Измельченный продукт под действием воздушного потока, создаваемого дробилкой, подается в накопительный бункер-ворошитель, который не допускает слеживание и зависания сырья на стенках, что обеспечивает поточность работы линии. После этого продукт поступает в дозатор гранулятора, который дозировано подает сырье в смеситель гранулятора.
Прессование. Из смесителя увлажненный продукт выводится в прессующую камеру гранулятора. В прессующей камере продукт затягивается между вращающейся матрицей и прессующими вальцами и продавливается в радиальные отверстия матрицы, где под действием большого давления происходит формирование гранул. Благодаря двухступенчатому редуктору, скорость вращения матрицы составляет всего 150 об/мин и мощностью привода 90/110 кВт, что позволяет получать прочные и качественные гранулы из таких продуктов как опил, лузга, торф.
Сегодня существует несколько десятков производителей прессов из разных стран мира (CPM, Andritz, Salmatec, Amandus Kahl, Buhler, Munch и многие другие). Многие прессы конструктивно различаются по видам матриц:
— пресс с круглой матрицей
— пресс с плоской матрицей.
Пресс с круглой матрицей разрабатывался для комбикормовой, пищевой и химической промышленности. А пресс с плоской матрицей изначально для утилизации промышленных и бытовых твердых отходов. На сегодняшний день прессы обеих модификаций, используемые в гранулировании, работают по одинаковому принципу. Бегущие катки создают контактное напряжение смятия сырья на матрице, и через отверстия в матрице продавливают сырье, которое обрезается ножами. Прессы выполнены из особо прочных материалов с жесткими мощными корпусами. Матрица и катки изготовлены из специальных закаленных износостойких сплавов. Гранулирование древесины, как материала имеющего высокую плотность, требует повышенного усилия для прессования. При прессовании происходит уплотнение древесного сырья до 3 раз. Из-за сил трения и адиабатических процессов, происходящих при резком сжатии сырья, температура в рабочей зоне пресса достигает 100 °C.
Охлаждение и просеивание. На выходе из камеры прессования гранулы мягкие и имеют повышенную температуру и влажность, поэтому их нужно охладить до температуры окружающей среды и удалить лишнюю влагу, чтобы продукт стал боле прочным. Ленточно-скребковый транспортер предотвращая повреждения доставляет гранулы в охладитель гранул, основанный на принципе противотока. Подача охлаждающего воздуха осуществляется во встречном направлении к подаче гранул. Охлаждение гранул происходит постепенно, в результате чего исключается растрескивание поверхности гранул за счет резкого испарения влаги и падения температуры гранул. После охлаждения температура гранул будет выше температуры окружающей среды не более чем на пять градусов, влажность уменьшится более чем на 5%.
После охлаждения гранулы попадают на стол рассева где происходит отделение крошки и фракций от готового продукта. Несгранулированная часть подается обратно в бункер-ворошитель для повторного гранулирования. Готовый продукт содержит не более 1% несгранулированной части.
Фасовка и складирование готовой продукции. Готовые гранулы могут поступать в бункер готовой продукции на склад либо могут быть сразу расфасованы в удобную для транспортировки и хранения тару.
Способы расфасофки топливных гранул
* В свободном виде — насыпью Подразделяется на две группы:
— Первая идет на крупные ТЭЦ, требования по качеству невысокие, цена также небольшая: промышленные пеллеты.
— Вторая — высокого качества для котлов небольшой мощности и дальнейшей фасовки в мелкую упаковку, требования высокие, цена также достаточно высокая.
* Фасовка в биг-бэги Фасовка в биг-бэги применяется для индустриальной транспортировки сыпучих продуктов. Биг-бэги изготавливаются из прочного полимера, имеют петли для механизации погрузо-разгрузочных работ, а также позволяют сохранять постоянную требуемую влажность ДТГ при открытом складировании. Цена ДТГ в биг-бэгах выше, чем при доставке насыпью.
* Мелкая расфасовка Самая дорогая группа. Цены на гранулы в мелкой расфасовке наиболее высокие, и превышают 200 Евро за тонну. К данной группе ДТГ предъявляются повышенные требования по качеству. Очень удобна для тех заказчиков, кто не может иметь склада для хранения в насыпном виде. Перевозится на паллетах (поддонах), массой до одной тонны.
2. Технология производства топливных брикетов
В основе технологии производства топливных брикетов лежит процесс прессования шнеком агро-отходов (шелухи подсолнечника, гречихи и др.) и мелко измельченных отходов древесины (опилок) под высоким давлением при нагревании от 250 до 350 С°. Получаемые топливные брикеты не включают в себя никаких связующих веществ, кроме одного натурального — лигнина, содержащегося в клетках растительных отходов. При использовании агросырья возможно добавление связующих элементов. Температура, присутствующая при прессовании, способствует оплавлению поверхности брикетов, которая благодаря этому становится более прочной, что немаловажно для транспортировки брикет.
Сырьем для производства брикетов является тот же материал, что и для изготовления гранул — опилки различных пород древесины, щепа, лузга подсолнечника, гречихи, солома и многие другие растительные отходы. Технология производства брикетов схожа с технологией гранулирования, но более простая. Брикеты бывают разных форм — в виде кирпича, цилиндра или шестигранника с отверстием внутри. Стандартных размеров у данной продукции нет. Основным фактором, определяющим механическую прочность, водостойкость и калорийность брикета, являются его плотность. Чем плотнее брикет, тем выше показатели его качества. Чем ниже плотность брикетов, тем меньше их калорийность. Например, при плотности брикета 650−750 кг/м3 калорийность брикетов равна 12−14 МДж/кг; при плотности 1200−1300 кг/м3 — 25−31 МДж/кг. Качество брикетов в значительной мере зависит от влажности исходной смеси. Различают оптимальную и критическую влажности. Оптимальная влажность составляет 4−10%, при ней достигаются наилучшие механические характеристики брикетов (следует учитывать, что для некоторых видов сырья верхним пределом влажности является 6−8%). Критической называется влажность, при которой возможно образование брикетов, но в нем появляются трещины — таким образом, брикет товарного вида не имеет. Критическая влажность находится в пределах 10−15%. При более высокой влажности полученный брикет будет «разорван» внутренним давлением влаги, возникающем при сжатии измельченной массы.
Существует 3 основных типа топливных брикетов. Они отличаются по форме, которая зависит от метода производства. «В народе» прижилось три названия, которые произошли из имен компаний, выпускающих оборудование для производства того или иного брикета. Таким образом, выделяют брикеты RUF, брикеты NESTRO и брикеты Pini-Kay. Однако, кроме упомянутых производителей брикетирующего оборудования, существуют и другие фирмы — например C.F. Nielsen (Дания), UPM (Литва), Bogma (Швеция), Pawert-SPM AG (Швейцария), DI-PIU (Италия).
Брикеты подразделяются по двум принципам:
Первое — по сырью, из которого они изготовлены. Здесь выделяют: брикеты из древесных отходов (стружка и опил без коры, отходы с корой, кора, отходы производства МДФ, шлифпыль, отходы фанерных производств, лигнин, брикеты из сельскохозяйственных отходов); брикеты из агробиомассы (солома, шелуха подсолнечника, шелуха злаковых, отходы хлопка, сено, камыш); брикеты из прочих материалов (бумага, картон, целлюлоза, полимеры, торф).
Второе — по способу прессования и форме. Брикеты бывают трех видов: цилиндрические, экструдерные и в виде кирпичика.
Цилиндрические брикеты.
Этот вид брикетов получается путём прессования на оборудовании ударно-механического типа. Они имеют бесконечную длину, и могут быть разделены как на шайбы, так и на поленья. Имеют очень высокую плотность, пользуются большой популярностью в Европе. Такие брикеты могут иметь не только круглую, но и квадратную или восьмиугольную форму, иметь или не иметь отверстие. Вид брикета заказывает покупатель, он зависит от того, какие формы больше популярны в каждой отдельно взятой стране. Данные брикеты охотно покупают такие страны, как Германия, Дания, Великобритания, Норвегия, Швеция, Италия. На внутреннем рынке, чаще всего используют кусковые брикеты, изготовленные по данной технологии, в качестве топлива для твёрдотопливных котлов.
Экструдерные брикеты.
Эти брикеты обязательно имеют отверстие внутри и обожженную верхнюю поверхность. В основе экструзивной технологии производства брикетов лежит процесс прессования шнеком под высоким давлением при нагревании от 250 до 350 С°. Температура, присутствующая при прессовании, способствует оплавлению поверхности брикетов, которая благодаря этому становится прочной, что немаловажно для транспортировки брикета.
Такие брикеты закладываются вручную в топку котла или в печку, они пользуются спросом в Прибалтике и на внутреннем рынке России.
Брикеты в виде кирпичика Эта продукция имеет вид прямоугольного параллелепипеда со скошенными углами. Такой брикет получается путём гидравлического прессования, и его размеры зависят от рыхлости сырья, из которого он произведён и давления, которое на него оказано. Они хорошо используются на внутреннем рынке, и также отлично покупаются во все европейские страны.
Технология Процесс брикетирования — это процесс сжатия материала под высоким давлением, с выделением температуры от силы трения. За счет данного воздействия в древесине происходит выделение лигнина, который является связующим веществом для формирования брикета. Для брикетов не из древесного сырья, могут применяться экологически чистые добавки (не более 2%). При производстве данной продукции следует обратить особое внимание на влагу — очень важный параметр, влияющий на плотность брикета. В случае превышения 14% влажности сырья брикет разваливается на произвольные куски из-за избытка влаги. Объем брикета составляет 1/10 от объёма затраченного на его производство сырья, что дает значительную экономию при транспортировке и хранении биотоплива.
Для производства древесных брикетов применяют поршневые и шнековые прессы, сырье — опилки и стружки. Перед прессованием материал дополнительно измельчают и подсушивают (влажность не должна превышать 12 — 14%)
Поршневой пресс работает циклически — при каждом ходе поршня продавливают определенное количество материала через коническое сопло, на брикетах четко различимы соответствующие цик-лам слои. В приводе всегда применяется маховик, позволяющий выровнять нагрузку двигателя. Износ поршня невелик, поскольку относительное перемещение между прессуемым материалом и поршнем мало, быстро изнашивается сопло. Поршневые прессы относительно дешевы и поэтому широко распространены.
Шнековый пресс легче поршневого, поскольку отсутствуют массивные поршни и маховики. Продукция выходит непрерывно, поэтому ее можно разрезать на нужные куски. Плотность выше, чем у поршневых прессов. Шнековые прессы менее шумные, благодаря отсутствию ударных нагрузок. К недостаткам можно отнести больший расход энергии и быстрый износ шнека.
Топливные брикеты имеют широкое применение и могут использоваться для всех видов топок, котлов центрального отопления и пр. Большим достоинством брикетов является постоянство температуры при горении на протяжении 4 и более часов.
3. Технология производства древесного угля
В специальную печь загружаются и поджигаются березовые поленья. После первичного прогорания древесины, в печи останавливают подачу кислорода. Начинается процесс обугливания (пиролиз). После охлаждения березовый уголь вынимают, просеивают и упаковывают.
Сейчас также производят древесный уголь из прессованных опилок (брикетов). При этом уголь может быть не только из березовых опилок, но и из любых других.
В России углежжение было давно известно. Старинными способами получения древесного угля считаются технологии «стог» и «кабан». Эти технологии были примитивными, процесс продолжался до месяца и требовал периодического контроля и обслуживания. Все газообразные и жидкие (в парах) продукты распада (а это около двух третей от исходной массы абсолютно сухой древесины) выбрасывались в атмосферу. Массовое производство угля по таким технологиям было возможно только в 17−18 веке, когда плотность населения была низкой и многие территории не освоены. Уже с 19 века в России предпочитали простейшие кирпичные печи для изготовления угля.
В СССР вначале использовали старинные ручные методы получения угля, а затем начали строить крупные углевыжигательные заводы, которые обеспечивали относительно чистое углежжение.
В России действует ГОСТ на древесный уголь (ГОСТ 7657−84).
Щепа.
В основе технологии получения щепы лежит измельчение древесины на специальной технике. Различают топливную и технологическую щепу. Технологическая щепа используется на ЦБК. Она вырабатывается из окорённой стволовой древесины хвойных и лиственных пород, а также из окорённых горбылей, реек, кусковых отходов древесины на ножевых рубильных машинах дискового типа. Топливная щепа может вырабатываться из неокоренных стволов, из низкокачественной тонкомерной древесины от рубок ухода за лесом, вершин и сучьев различных древесных пород на рубильных машинах дискового и барабанного типов. Насчитывается несколько десятков производителей оборудования для производства щепы, наиболее известные Morbark, Brucks, Peterson, Farmi и другие.
Дрова.
Технология производства дров связана с лесозаготовкой. Низкокачественную древесину, которая не может быть использована в качестве деловой (фанкряж, пиловочник, балансы) превращают в дрова путем распиловки и расколки.
4. Биогаз. Биоэтанол. Биодизель
Биогаз образуется с помощью бактерий в процессе разложения органического материала при анаэробных (без доступа воздуха) условиях и представляет собой смесь метана и других газов в следующих пропорциях:
Газ | Химическая формула | Объемная доля | |
Метан | CH4 | 40 — 70% | |
Углекислый газ | CO2 | 30 — 60% | |
Другие газы | 1 — 5% | ||
Водород | H2 | 0 — 1% | |
Сероводород | Н2S | 0 — 3% | |
Состав биогаза Теплотворная способность одного кубометра биогаза составляет в зависимости от содержания метана 20−25 МДЖ/ м3, что эквивалентно сгоранию 0,6 — 0,8 литра бензина, 1.3 — 1.7 кг дров или использованию 5 — 7 кВт электроэнергии.
Технология производства биогаза заключается в следующем. Биомасса (отходы или зеленая масса) периодически подаются с помощью насосной станции или загрузчика в реактор. Реактор представляет собой подогреваемый и утепленный резервуар, оборудованный миксерами. Стройматериалом для промышленного резервуара чаще всего служит железобетон или сталь с покрытием. В малых установках иногда используются композиционные материалы. В реакторе живут полезные бактерии, питающиеся биомассой. Продуктом жизнедеятельности бактерий является биогаз. Для поддержания жизни бактерий требуется подача корма, подогрев до 35−38°С и периодическое перемешивание. Образующийся биогаз скапливается в хранилище (газгольдере), затем проходит систему очистки и подается к потребителям (котел или электрогенератор). Реактор работает без доступа воздуха, герметичен и неопасен.
Для сбраживания некоторых видов сырья в чистом виде требуется особая двухстадийная технология. Например, птичий помет, спиртовая барда не перерабатываются в биогаз в обычном реакторе. Для переработки такого сырья необходим дополнительно реактор гидролиза. Такой реактор позволяет контролировать уровень кислотности, таким образом бактерии не погибают из-за повышения содержания кислот или щелочей. Возможна переработка этих же субстратов по одностадийной технологии, но при коферментации (смешивании) с другими видами сырья, например, с навозом или силосом.
Существуют промышленные и кустарные установки. Промышленные установки отличаются от кустарных наличием механизации, систем подогрева, гомогенизации, автоматики. Наиболее распространённый промышленный метод — анаэробное сбраживание в метантенках.
Биоэтанол — это обычный этанол, получаемый в процессе переработки растительного сырья для использования в качестве биотоплива. Его производство схоже с производством пищевого спирта.
Современная промышленная технология получения спирта этилового из пищевого сырья включает следующие стадии:
— подготовка и измельчение крахмалистого сырья — зерна (ржи, пшеницы и т. п.)
— ферментация. На подавляющем большинстве спиртовых производств мира ферментативное расщепление крахмала до спирта при помощи дрожжей оставлено. Для этих целей применяются рекомбинантные препараты альфа-амилазы, полученные биоинженерным путем — глюкамилаза, амилосубтилин.
— брагоректификация. Осуществляется на разгонных колоннах (например, «Комсомолец»). Отходами бродильного производства являются барда и сивушные масла. Барда используется для производства кормов.
Реальной альтернативой этанолу в наши дни становится биобутанол, так как он обладает более высоким энергетическим потенциалом, менее летуч и может использоваться в автомобилях без каких-либо изменений в конструкции их двигателей. Так, гибридное топливо БИО100 представляет собой смесь 65% биоэтанола с добавлением третбутилового эфира. Такое моторное топливо снижает на 1/3 тепловую нагрузку на двигатель, повышая тем самым сроки его эксплуатации.
В основе технологии получения биодизельного топлива лежит реакция переэтерификации любого растительного масла, или животного жира, в присутвии катализатора в биодизель (метиловые эфиры жирных кислот). Биодизель получают из рапса и ряда других культур.
Liquid-to-biofuel (биотопливо второго поколения).
Различные виды топлива, получаемые различными методами пиролиза биомассы. Быстрый пиролиз позволяет превратить биомассу в жидкость, которую легче и дешевле транспортировать, хранить и использовать. Из жидкости можно произвести автомобильное топливо, или топливо для электростанций. Из биотоплив второго поколения, продающихся на рынке, наиболее известны BioOil производства канадской компании Dynamotive и SunDiesel германской компании CHOREN Industries GmbH.
5. Перспективы использования биотоплива в республике Коми
биодизель древесный топливный Представители республики посетили два лесных предприятия — ООО ЛПК «Полеко» и котельную № 3 в п. Демьяново ЗАО «Лесэнерго». Первое является одним из самых крупных в Подосиновском районе Кировской области предприятий, которое производит ДВП для строительной и мебельной промышленности и где работает четыре котла на древесных отходах, производя горячую воду, тепловую энергию. В результате перехода на биотопливо производство ДВП вышло на устойчивую рентабельную работу.
Котельная в п. Демьяново также работает сегодня на древесных отходах. Таким образом решилась проблема по бесперебойному обеспечению поселка теплом и горячей водой.
По экспертным оценкам ежегодно в республике образуется около 1,5 млн. тонн древесных отходов. При этом, вопрос с их эффективной утилизацией в настоящее время решен только на некоторых крупных и наиболее экономически эффективных предприятиях. Так, с переводом, выведенных из эксплуатации трех старых содорегенерационных котлов, на сжигание кородревесных отходов, крупнейшее предприятие отрасли в Республике Коми — ОАО «Монди СЛПК» будет использовать весь объем древесины, поступающей на предприятие для переработки. Полностью решена данная проблема на Сыктывкарском фанерном заводе. К сожалению, остальные крупные предприятия лесопереработки, такие как, Сыктывкарский ЛДК, Севлеспил, Жешартский фанерный комбинат, Лузалес до конца еще не решили вопрос комплексного и эффективного использования древесных отходов. Особую озабоченность вызывает ситуация с утилизацией древесных отходов на средних и малых предприятиях лесопереработки в муниципальных районах.
Сегодня в республике работает программа «Обращение с отходами производства и потребления в РК (2012;2016 годы)», в рамках которой будут созданы 10 площадок для временного хранения древесных отходов с целью их дальнейшей переработки или использования для выработки тепловой энергии.
Наиболее активный район по внедрению биоэнергетики — Корткеросский. В поселке Аджером начато строительство площадки по хранению древесных отходов, также планируется строительство площадки в п. Мордино.
Разработана также программа «Использование низкосортной древесины и отходов лесопереработки для производства горячей воды, тепловой и электрической энергии (2013;2014 годы)», нацеленная на увеличение использования древесных отходов лесоперерабатывающего и лесозаготовительного производства. Программа позволит в будущем гарантировать лесному комплексу региона не только рациональное использование лесных ресурсов, но и снизить вредные выбросы в атмосферу и уменьшить бюджетные расходы по теплоснабжению социальных объектов.
Практическая часть
Производственный процесс и его организация Длительность производственного процесса, то есть календарный период времени, в течение которого выполняется производственный процесс, называется производственным циклом. Основу производственного цикла составляет технологический цикл, который в свою очередь состоит из операционных циклов.
Операционный цикл, т. е. продолжительность обработки партии деталей (мин) на одной (данной) операции процесса равен где n — размер партии деталей, шт.;
tшт — штучно-калькуляционная норма времени на операцию, мин;
c — число рабочих мест на операции.
Сочетание во времени выполнения операционных циклов существенно влияет на производственный цикл и определяет порядок передачи деталей (партий) в процессе. Возможны 3 вида сочетания операционных циклов (видов движения предметов труда по операциям процесса): последовательный, параллельный и параллельно-последовательный.
Последовательный вид движения (рис. 1), когда вся обрабатываемая партия деталей полностью передается на последующую операцию после полного окончания всех работ на предыдущей. При этом длительность технологического процесса (мин) определяется суммой операционных циклов где m — число операций в процессе.
Длительность производственного цикла (календарные дни) включает дополнительно межоперационные перерывы (tмо) и время естественных процессов (Тест) где S — число смен;
q — продолжительность смены, мин;
f — коэффициент для перевода рабочих дней в календарные (при 260 рабочих днях в году f = 260/365 = 0,71).
Рис. 1. График технологического цикла при последовательном виде движения партии деталей в производстве Параллельный вид движения (рис. 2), когда небольшие транспортные партии р или отдельные штуки (р=1) деталей запускаются на последующую операцию сразу после обработки их на предыдущей операции, независимо от всей партии. Полностью загружена в этом случае наиболее трудоемкая операция с самым длительным операционным циклом, менее трудоемкие имеют перерывы.
Рис. 2. График технологического цикла при параллельном виде движения партии деталей в производстве Длительность технологического цикла (мин) при параллельном виде движения определяется Длительность производственного цикла (календарные дни) примет вид Параллельно-последовательный вид движения (рис. 3), при котором следующая операция начинается до полного окончания работы на предыдущей операции и осуществляется без перерывов в изготовлении партии деталей. При этом имеет место частичное совмещение времени выполнения смежных операционных циклов. Передача изготовляемых деталей с предыдущей на последующую операцию производится не целыми партиями, а частями, транспортными партиями р (пачками) или поштучно (р=1).
Рис. 3. График технологического цикла при параллельно-последовательном виде движения партии деталей в производстве: ф1, ф2, — время перекрытия смежных операционных циклов Длительность технологического цикла (мин) будет соответственно меньше, чем при последовательном виде движения на величину совмещения операционных циклов Длительность производственного цикла (календарные дни) при параллельно — последовательном виде движения примет вид:
Задача
Определить длительность технологического и производственного циклов при всех трех видах движения предметов труда; как изменится длительность технологического цикла, если партию обработки удвоить; какой вид движения партий и ее размер оказывает наиболее существенное влияние на сокращение цикла. Построить графики технологических циклов при параллельном и параллельно-последовательном движении предметов труда.
Для всех вариантов на первой операции работа выполняется на трех станках, на четвертой — на двух, на всех остальных — на одном станке.
Работа производится в две смены по 8 ч. Естественные процессы при обработке партии деталей отсутствуют.
Решение
1. Выполним предварительные расчеты и занесем данные в табл. 3:
Таблица 1
№ операции | tштi | Сi | |||
; | |||||
ИТОГО | ; | ; | |||
2. Рассчитаем технологические и производственные циклы для трех видов движения деталей при одинарном размере партии:
Длительность технологического и производственного циклов при одинарном размере партии:
для последовательного движения деталей:
(мин)
(дней) для параллельного движения деталей:
(мин)
(дней) для параллельно-последовательного движения деталей:
(мин)
(дней) Длительность технологического и производственного циклов при удвоенном размере партии:
для последовательного движения деталей:
(мин)
(дней) для параллельного движения деталей:
(мин)
(дней) для параллельно-последовательного движения деталей:
(мин)
(дней)
3. Графики технологических циклов представлены в графической части. Для построения графиков технологических циклов для параллельно-последовательного движения деталей рассчитаем величину совмещения смежных операционных циклов:
(мин)
(мин)
(мин) Расчет производственного цикла сложного процесса В условиях машиностроительного производства наиболее характерным примером сложного производственного процесса может служить процесс создания машины. Он включает производственные циклы изготовления всех деталей, сборки всех сборочных единиц (узлы, механизмы), сборку, отладку и контроль готового изделия.
Построение сложного производственного процесса во времени проводится, чтобы определить производственный цикл, координировать отдельные простые процессы, получить исходную информацию для планирования производства.
Структура производственного цикла сложного процесса определяется составом операций и связями между ними. Состав операций зависит от номенклатуры деталей, сборочных единиц и технологических процессов изготовления и сборки. Часто для определения цикла сложного производственного процесса пользуются графическим методом. С этой целью применительно к схеме сборки изделия (рис. 4) строят цикловой график (рис. 5) в масштабе времени, с помощью которого и определяется общая продолжительность цикла.
Рис. 4. Схема сборки изделия Производственный цикл сложного процесса изготовления изделия определяется наибольшей суммой циклов последовательно связанных между собой простых процессов и межцикловых перерывов (Тмц) Коэффициент параллельности простых циклов в сложном представляет собой отношение суммы циклов простых процессов к длительности цикла сложного процесса:
Рис. 5. Цикловой график сборки изделия