Другие работы

Апробация работы. Основные положения и результаты диссертационных исследований доложены и обсуждены на всероссийских, международных конференциях и форумах: «Продукты питания и рациональное использование сырьевых ресурсов», «Пищевые продукты и здоровье человека» (Кемерово, 2004), «Пища. Экология. Качество» (Новосибирск, 2004, 2010), «Актуальные проблемы коммерции и маркетинга в потребительской…
Диссертация 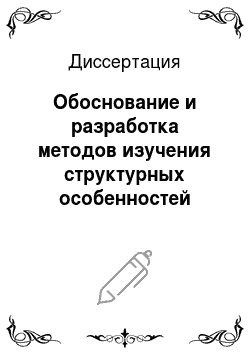
Все вышесказанное показывает, что на сегодняшний день существует два основных подхода к изучению структуры, физико-механических и физико-химических свойств углей. Первый — петролого-технологический — основан на установлении взаимосвязей между петрографическим и химическим составом вещества углей в целом и их свойствами. Этот метод не учитывает особенностей текстуры органического вещества углей…
Диссертация 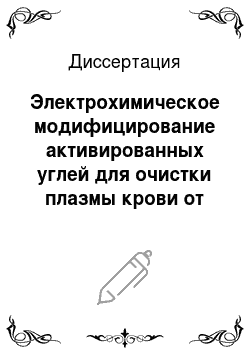
При травмах различной этиологии острая кровопотеря — один из основных факторов, определяющих тяжесть состояния пострадавшего. Если пациент потерял более одного литра крови, быстрое восстановление объема циркулирующей крови является первоочередной задачей в комплексе лечебных мероприятий. С этой целью обычно используют кровь доноров. Но переливание донорской крови, по сути, является…
Диссертация 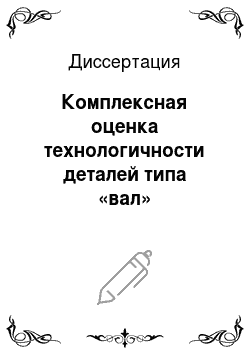
Процесс обеспечения технологичности изделия является противоречивым и трудноформализуемым, в ходе его выполнения неизбежны конфликты профессиональных интересов между разработчиками проектного решения и его внешними и внутренними потребителями. Для объективного разрешения таких конфликтов необходимо введение квалиметрической оценки качества проектного решения по критерию технологичности…
Диссертация 
Между тем, как показали проведенные нами эксперименты, перспективным способом МХА катализаторных масс (композиций), в частности, ни-кельмедьалюминиевой каталитической системы, является их обработка в гидромеханической мельнице струями воды высокого давления и мелющими телами. Данная система проявляет высокие каталитические свойства в процессах очистки технологических газов от кислорода, а также…
Диссертация 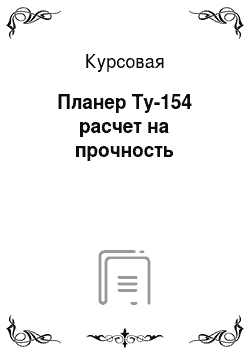
Осмотр остекления фюзеляжа производится изнутри кабин при хорошей освещенности. Особое внимание обращается на отсутствие трещин, царапин, забоин и других механических повреждений. Органические стекла проверяются также на отсутствие «серебра» (мелких поверхностных трещин), триплексные стекла на отсутствие отлипов. Проверяется крепление стекол фонаря и прилегание их к каркасу. На остеклении…
Курсовая 
При автоблокировке перегон делят на блок-участки, что позволяет отправлять поезда с интервалом 6—8 мин, а на пригородных линиях, где блок-участки меньшей длины, — с интервалом 3−4 мин. Благодаря этому обеспечивается высокая пропускная способность железных дорог (на двухпутных магистральных линиях до 200 пар поездов в сутки, а на пригородных линиях до 300 пар). Каждый блок-участок оборудуют…
Курсовая 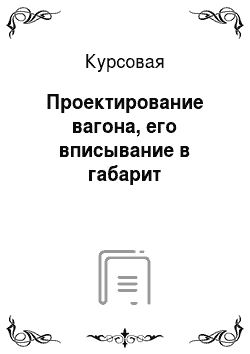
Боковая стена безраскосной конструкции. Стена имеет каркас и обшивку: металлическую наружную и деревянную внутреннюю. Для загрузки и выгрузки вагона в средней части стены расположены самоуплотняющиеся двери и два люка, снабженные вентиляционными решетками. Каркас стены включает обвязку, две шкворневые, шесть промежуточных и две дверные стойки. Верхняя обвязка выполнена из уголка 90×56×8 мм…
Курсовая 
На отделение, как и на дорогу, возлагаются: обеспечение выполнения плана и договорных обязательств по перевозкам, оперативное руководство движением поездов, выполнение технических норм эксплуатационной работы, организация грузовой и коммерческой работы, обеспечение безопасности движения поездов, сохранности грузов при их транспортировке; руководство эксплуатацией и обеспечение содержания…
Курс лекций 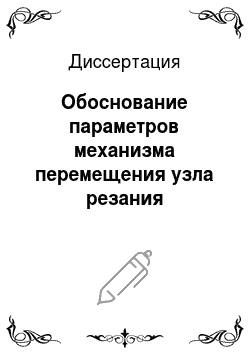
Решение задачи раскроя круглых лесоматериалов ведется в различных направлениях. Во-первых, ввиду естественного регионального расположения древостоев в зоне переработки, которые характеризуются широкой изменчивостью качественного состава. Так, например, значительные исследования в области раскроя посвящены переработке фаутных крупномерных сортиментов в регионах Сибири. Другое направление связано…
Диссертация 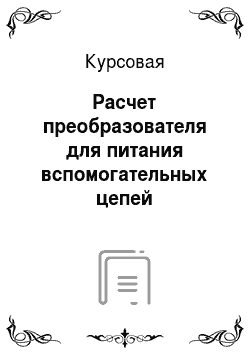
Многообмоточный специальный трансформатор; работает на повышенной частоте и прямоугольном напряжении. На высокой частоте трансформаторы имеют повышенные потери в меди и стали. Из-за эффекта вытеснения тока и периферии проводника его эффективное сопротивление возрастает. Чтобы уменьшить эти потери, используют полые проводники или делают обмотку из фольги. Потери в стали на вихревые токи…
Курсовая 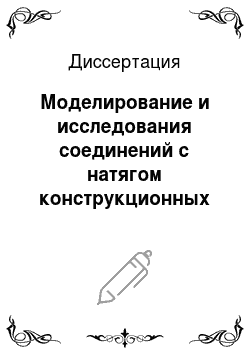
Исследованию двухпосадочных бандажных узлов посвящены работы, которые были инициированы, в первую очередь, проблемами, возникавшими в процессе эксплуатации генераторов в соединениях бандаж-ротор, бандаж-центрирующее кольцо, центрирующее кольцо-ротор. Дело в том, что при двухпосадочных бандажах с жестким ЦК возможно нарушение посадки кольца на бочку ротора из-за неизбежного в эксплуатации…
Диссертация 
В ремонтном участке составляется карта эскизов с учетом типовых норм времени. До составления карты эскизов заполняется дефектовочная ведомость, в которой указываются все возможные дефекты восстанавливаемой детали; номинальные размеры, размеры допустимые для эксплуатации детали без ремонта и предельные размеры, после достижения которых деталь необходимо ремонтировать. В операционной карте…
Курсовая 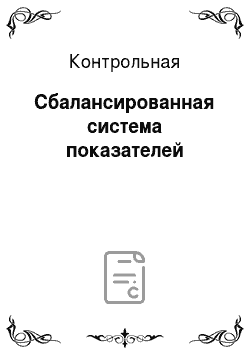
Тема данной контрольной работы является актуальной, поскольку в настоящее время примеров успешного применения сбалансированной системы показателей в мировой практике достаточно, хотя процесс внедрения BSC не прост и трудоемок. Наиболее серьезные проблемы чаще всего касаются неправильной трактовки методологии или организационных моментов. Трудоемкость разработки сбалансированной системы…
Контрольная 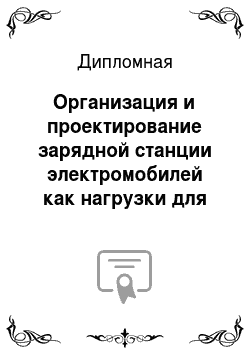
В нулевом проводнике при питании нелинейной симметричной нагрузкой протекают токи высщих гармоник, кратных трём, вызывающие дополнительные потери мощности:(3.10)В предложен метод, учитывающий фактические уровни гармонических составляющих напряжения и чувствительность узлов электрической сети на основании коллективных экспертных оценок. Выработка рекомендаций по принятию решения связана…
Дипломная