Π’Π΅Ρ Π½ΠΎΠ»ΠΎΠ³ΠΈΠΈ ΠΈ ΠΎΠ±ΠΎΡΡΠ΄ΠΎΠ²Π°Π½ΠΈΡ ΠΎΠ±ΡΠ²Π½ΠΎΠ³ΠΎ ΠΏΡΠΎΠΈΠ·Π²ΠΎΠ΄ΡΡΠ²Π°
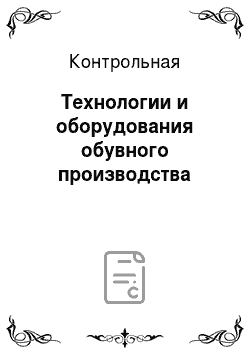
Π ΠΈΡΡΠ½ΠΎΠΊ 9. Π‘Ρ Π΅ΠΌΠ° ΡΠ΅Ρ Π½ΠΎΠ»ΠΎΠ³ΠΈΡΠ΅ΡΠΊΠΎΠ³ΠΎ ΠΏΡΠΎΡΠ΅ΡΡΠ° Π»ΠΈΡΡΡ ΠΏΠΎΠ»ΠΈΡΡΠ΅ΡΠ°Π½ΠΎΠ²ΠΎΠ³ΠΎ Π½ΠΈΠ·Π° ΠΎΠ±ΡΠ²ΠΈ Π½Π° ΡΠΎΡΠΎΡΠ½ΠΎΠΉ 24-ΡΠ΅ΠΊΡΠΈΠΎΠ½Π½ΠΎΠΉ Π»ΠΈΡΡΠ΅Π²ΠΎΠΉ ΠΌΠ°ΡΠΈΠ½Π΅ ΡΠΎ ΡΠΏΠ°ΡΠ΅Π½Π½ΡΠΌΠΈ ΠΌΠ΅ΡΠ°Π»Π»ΠΈΡΠ΅ΡΠΊΠΈΠΌΠΈ ΠΊΠΎΠ»ΠΎΠ΄ΠΊΠ°ΠΌΠΈ Π ΡΠ΅Ρ Π½ΠΎΠ»ΠΎΠ³ΠΈΠΈ ΠΏΡΠΎΠΈΠ·Π²ΠΎΠ΄ΡΡΠ²Π° ΠΎΠ±ΡΠ²ΠΈ Ρ ΠΏΡΠΈΠΌΠ΅Π½Π΅Π½ΠΈΠ΅ΠΌ ΠΌΠ΅ΡΠΎΠ΄Π° ΠΆΠΈΠ΄ΠΊΠΎΠ³ΠΎ ΡΠΎΡΠΌΠΎΠ²Π°Π½ΠΈΡ Π΄Π»Ρ ΠΎΠ±ΡΠ°Π·ΠΎΠ²Π°Π½ΠΈΡ Π½ΠΈΠ·Π° ΠΈΠ· ΠΏΠΎΠ»ΠΈΡΡΠ΅ΡΠ°Π½ΠΎΠ² ΠΈΠ·Π³ΠΎΡΠΎΠ²Π»Π΅Π½ΠΈΠ΅ Π·Π°Π³ΠΎΡΠΎΠ²ΠΎΠΊ Π²Π΅ΡΡ Π°, ΡΠΎΡΠΌΠΎΠ²Π°Π½ΠΈΠ΅ Π½Π° ΠΊΠΎΠ»ΠΎΠ΄ΠΊΠ΅, ΠΏΠΎΠ΄Π³ΠΎΡΠΎΠ²ΠΊΠ° ΡΠ»Π΅Π΄Π° Π΄Π»Ρ ΠΊΡΠ΅ΠΏΠ»Π΅Π½ΠΈΡ Π½ΠΈΠ·Π°, Π° ΡΠ°ΠΊΠΆΠ΅ Π½Π°Π΄Π΅Π²Π°Π½ΠΈΠ΅ Π·Π°Π³ΠΎΡΠΎΠ²ΠΎΠΊ Π½Π° Π»ΠΈΡΡΠ΅Π²ΡΠ΅… Π§ΠΈΡΠ°ΡΡ Π΅ΡΡ >
Π’Π΅Ρ Π½ΠΎΠ»ΠΎΠ³ΠΈΠΈ ΠΈ ΠΎΠ±ΠΎΡΡΠ΄ΠΎΠ²Π°Π½ΠΈΡ ΠΎΠ±ΡΠ²Π½ΠΎΠ³ΠΎ ΠΏΡΠΎΠΈΠ·Π²ΠΎΠ΄ΡΡΠ²Π° (ΡΠ΅ΡΠ΅ΡΠ°Ρ, ΠΊΡΡΡΠΎΠ²Π°Ρ, Π΄ΠΈΠΏΠ»ΠΎΠΌ, ΠΊΠΎΠ½ΡΡΠΎΠ»ΡΠ½Π°Ρ)
ΠΠΎΠ½ΡΡΠΎΠ»ΡΠ½Π°Ρ ΡΠ°Π±ΠΎΡΠ° № 1
ΠΏΠΎ ΡΠ΅Ρ Π½ΠΎΠ»ΠΎΠ³ΠΈΠΈ ΠΈ ΠΎΠ±ΠΎΡΡΠ΄ΠΎΠ²Π°Π½ΠΈΡ ΠΎΠ±ΡΠ²Π½ΠΎΠ³ΠΎ ΠΏΡΠΎΠΈΠ·Π²ΠΎΠ΄ΡΡΠ²Π° Π‘ΠΎΠ΄Π΅ΡΠΆΠ°Π½ΠΈΠ΅
1. Π Π°Π±ΠΎΡΠ° Π½Π°ΡΡΠΆΠ½ΡΡ Π΄Π΅ΡΠ°Π»Π΅ΠΉ Π½ΠΈΠ·Π° ΠΎΠ±ΡΠ²ΠΈ. Π’ΡΠ΅Π±ΠΎΠ²Π°Π½ΠΈΡ ΠΊ ΠΌΠ°ΡΠ΅ΡΠΈΠ°Π»Π°ΠΌ Π½Π° Π΄Π΅ΡΠ°Π»ΡΡ Π½ΠΈΠ·Π°, ΠΈΡΡ ΠΎΠ΄Ρ ΠΈΠ· ΠΈΡ ΡΠ°Π±ΠΎΡΡ Π² ΠΎΠ±ΡΠ²ΠΈ
2. Π Π°Π½ΡΠΎΠ²ΡΠΉ ΠΌΠ΅ΡΠΎΠ΄ ΠΊΡΠ΅ΠΏΠ»Π΅Π½ΠΈΡ ΠΏΠΎΠ΄ΠΎΡΠ² ΠΈ ΠΏΡΠΈΠΌΠ΅Π½ΡΠ΅ΠΌΠΎΠ΅ Π΄Π»Ρ ΡΡΠΎΠ³ΠΎ ΠΎΠ±ΠΎΡΡΠ΄ΠΎΠ²Π°Π½ΠΈΠ΅. ΠΠΎΡΡΠΎΠΈΠ½ΡΡΠ²Π° ΠΈ Π½Π΅Π΄ΠΎΡΡΠ°ΡΠΊΠΈ
3. ΠΠΈΡΡΠ΅ ΠΏΠΎΠ»ΠΈΡΡΠ΅ΡΠ°Π½ΠΎΠ². Π Π΅ΠΆΠΈΠΌΡ, ΠΎΠ±ΠΎΡΡΠ΄ΠΎΠ²Π°Π½ΠΈΠ΅, ΠΎΡΠΎΠ±Π΅Π½Π½ΠΎΡΡΠΈ Π»ΠΈΡΡΡ ΠΏΠΎΠ»ΠΈΡΡΠ΅ΡΠ°Π½ΠΎΠ² ΠΠ²Π΅Π΄Π΅Π½ΠΈΠ΅ ΠΠΎΠ»ΡΡΠΎΠΉ ΠΈ Π²Π°ΠΆΠ½ΠΎΠΉ Π³ΡΡΠΏΠΏΠΎΠΉ ΡΠΎΠ²Π°ΡΠΎΠ² Π½Π°ΡΠΎΠ΄Π½ΠΎΠ³ΠΎ ΠΏΠΎΡΡΠ΅Π±Π»Π΅Π½ΠΈΡ ΡΠ²Π»ΡΡΡΡΡ ΠΈΠ·Π΄Π΅Π»ΠΈΡ ΠΈΠ· ΠΊΠΎΠΆΠΈ. ΠΠΎΠ΄ ΡΠ΅ΡΠΌΠΈΠ½ΠΎΠΌ «ΠΈΠ·Π΄Π΅Π»ΠΈΡ ΠΈΠ· ΠΊΠΎΠΆΠΈ» ΠΏΠΎΠ½ΠΈΠΌΠ°ΡΡ ΠΈΠ·Π΄Π΅Π»ΠΈΡ, ΠΈΡΠΏΠΎΠ»ΡΠ·ΡΠ΅ΠΌΡΠ΅ ΡΠ΅Π»ΠΎΠ²Π΅ΠΊΠΎΠΌ Π² Π±ΡΡΡ ΠΈ ΠΈΠ·Π³ΠΎΡΠΎΠ²Π»ΡΠ΅ΠΌΡΠ΅ ΠΈΠ· ΠΊΠΎΠΆΠΈ. Π Π½ΠΈΠΌ ΠΎΡΠ½ΠΎΡΡΡΡΡ ΠΎΠ±ΡΠ²Ρ ΠΈ ΠΊΠΎΠΆΠ³Π°Π»Π°Π½ΡΠ΅ΡΠ΅ΠΉΠ½ΡΠ΅ ΠΈΠ·Π΄Π΅Π»ΠΈΡ. Π ΠΏΡΠΎΠΈΠ·Π²ΠΎΠ΄ΡΡΠ²Π΅ ΡΡΠΈΡ ΠΈΠ·Π΄Π΅Π»ΠΈΠΉ, ΡΠ°Π½Π΅Π΅ ΡΠ΅Π»ΠΈΠΊΠΎΠΌ ΠΈΠ·Π³ΠΎΡΠΎΠ²Π»ΡΠ²ΡΠΈΡ ΡΡ ΠΈΠ· ΠΊΠΎΠΆΠΈ, ΡΠ΅ΠΏΠ΅ΡΡ ΠΈΡΠΏΠΎΠ»ΡΠ·ΡΡΡ ΠΈΡΠΊΡΡΡΡΠ²Π΅Π½Π½ΡΠ΅ ΠΌΠ°ΡΠ΅ΡΠΈΠ°Π»Ρ, ΡΠΊΠ°Π½ΠΈ, ΠΌΠ΅ΡΠ°Π»Π»Ρ ΠΈ Π΄ΡΡΠ³ΠΈΠ΅ ΠΌΠ°ΡΠ΅ΡΠΈΠ°Π»Ρ, ΠΎΠ΄Π½Π°ΠΊΠΎ Π½Π°Π·Π²Π°Π½ΠΈΠ΅ «ΠΈΠ·Π΄Π΅Π»ΠΈΡ ΠΈΠ· ΠΊΠΎΠΆΠΈ» ΡΠΎΡ ΡΠ°Π½ΡΠ΅ΡΡΡ.
ΠΡΡΠΎΡΡΠΈΠΌΠ΅Π½Ρ ΠΈ ΠΊΠ°ΡΠ΅ΡΡΠ²ΠΎ ΠΈΠ·Π΄Π΅Π»ΠΈΠΉ ΠΈΠ· ΠΊΠΎΠΆΠΈ Π² Π·Π½Π°ΡΠΈΡΠ΅Π»ΡΠ½ΠΎΠΉ ΡΡΠ΅ΠΏΠ΅Π½ΠΈ Π·Π°Π²ΠΈΡΡΡ ΠΎΡ ΠΊΠ°ΡΠ΅ΡΡΠ²Π° ΠΏΡΠΈΠΌΠ΅Π½ΡΠ΅ΠΌΡΡ ΠΌΠ°ΡΠ΅ΡΠΈΠ°Π»ΠΎΠ², ΠΈΡ Π²Π½Π΅ΡΠ½Π΅Π³ΠΎ Π²ΠΈΠ΄Π° ΠΈ ΡΠ²ΠΎΠΉΡΡΠ².
1. Π Π½Π°ΡΡΠΆΠ½ΡΠΌ Π΄Π΅ΡΠ°Π»ΡΠΌ Π½ΠΈΠ·Π° ΠΎΠ±ΡΠ²ΠΈ ΠΎΡΠ½ΠΎΡΡΡ ΠΏΠΎΠ΄ΠΎΡΠ²Ρ, ΠΏΠΎΠ΄ΠΌΠ΅ΡΠΊΠΈ, ΠΎΠ±Π²ΠΎΠ΄ΠΊΠΈ, Π½Π΅ΡΡΡΠΈΠ΅ ΠΈ Π½Π°ΠΊΠ»Π°Π΄Π½ΡΠ΅ ΡΠ°Π½ΡΡ, ΠΊΠ°Π±Π»ΡΠΊΠΈ, Π½Π°Π±ΠΎΠΉΠΊΠΈ ΠΠΎΠ΄ΠΎΡΠ²Π° — Π΄Π΅ΡΠ°Π»Ρ, ΡΠ°ΡΠΏΠΎΠ»Π°Π³Π°Π΅ΠΌΠ°Ρ ΠΏΠΎΠ΄ Π²ΡΠ΅ΠΉ Ρ ΠΎΠ΄ΠΎΠ²ΠΎΠΉ ΠΏΠΎΠ²Π΅ΡΡ Π½ΠΎΡΡΡΡ ΡΡΠΎΠΏΡ.
ΠΠΎΠ΄ΠΌΠ΅ΡΠΊΠ° ΠΏΠΎ ΡΠΎΡΠΌΠ΅ Π°Π½Π°Π»ΠΎΠ³ΠΈΡΠ½Π° Π½ΠΎΡΠΎΡΠ½ΠΎ-ΠΏΡΡΠΊΠΎΠ²ΠΎΠΉ ΡΠ°ΡΡΠΈ ΠΏΠΎΠ΄ΠΎΡΠ²Ρ ΠΈ ΡΠ»ΡΠΆΠΈΡ Π΄Π»Ρ ΡΠ²Π΅Π»ΠΈΡΠ΅Π½ΠΈΡ ΡΡΠΎΠΊΠ° ΡΠ»ΡΠΆΠ±Ρ ΠΏΠΎΠ΄ΠΎΡΠ²Ρ.
ΠΠ±Π²ΠΎΠ΄ΠΊΡ Π² Π²ΠΈΠ΄Π΅ ΠΏΠΎΠ»ΠΎΡΠΊΠΈ ΠΏΡΠΈΠΊΡΠ΅ΠΏΠ»ΡΡΡ ΠΊ ΠΊΡΠ°Ρ Π½Π΅Ρ ΠΎΠ΄ΠΎΠ²ΠΎΠΉ ΠΏΠΎΠ²Π΅ΡΡ Π½ΠΎΡΡΠΈ ΠΏΠΎΠ΄ΠΎΡΠ²Ρ ΠΈ ΠΊΠ°Π±Π»ΡΠΊΠ° Π΄Π»Ρ ΠΎΠ±Π΅ΡΠΏΠ΅ΡΠ΅Π½ΠΈΡ ΠΏΠ»ΠΎΡΠ½ΠΎΠ³ΠΎ ΠΏΡΠΈΠ»Π΅Π³Π°Π½ΠΈΡ ΠΈΡ ΠΊ ΡΠ»Π΅Π΄Ρ ΠΎΠ±ΡΠ²ΠΈ.
ΠΠ΅ΡΡΡΠΈΠΉ ΡΠ°Π½Ρ ΠΏΡΠΈΠΌΠ΅Π½ΡΡΡ Π΄Π»Ρ ΡΠΊΡΠ΅ΠΏΠ»Π΅Π½ΠΈΡ ΠΏΠΎΠ΄ΠΎΡΠ²Ρ ΡΠΎ ΡΡΠ΅Π»ΡΠΊΠΎΠΉ, Π° Π½Π°ΠΊΠ»Π°Π΄Π½ΠΎΠΉ ΡΠ°Π½Ρ — Π΄Π»Ρ Π·Π°ΡΠΈΡΡ ΡΠ²Π°, ΡΠΎΠ΅Π΄ΠΈΠ½ΡΡΡΠ΅Π³ΠΎ ΠΏΠΎΠ΄ΠΎΡΠ²Ρ ΡΠΎ ΡΡΠ΅Π»ΡΠΊΠΎΠΉ Π² ΠΎΠ±ΡΠ²ΠΈ Π΄ΠΎΠΏΠΏΠ΅Π»ΡΠ½ΠΎΠ³ΠΎ ΠΈ ΡΠ°Π½Π΄Π°Π»ΡΠ½ΠΎΠ³ΠΎ ΠΌΠ΅ΡΠΎΠ΄ΠΎΠ² ΠΊΡΠ΅ΠΏΠ»Π΅Π½ΠΈΡ.
ΠΠ°Π±Π»ΡΠΊ, ΠΏΡΠΈΠΊΡΠ΅ΠΏΠ»ΡΠ΅ΠΌΡΠΉ ΠΊ ΠΏΡΡΠΎΡΠ½ΠΎΠΉ ΡΠ°ΡΡΠΈ ΠΎΠ±ΡΠ²ΠΈ, ΡΠ»ΡΠΆΠΈΡ Π΄Π»Ρ ΠΏΠΎΠ΄ΡΠ΅ΠΌΠ° ΠΏΡΡΠΎΡΠ½ΠΎΠΉ ΡΠ°ΡΡΠΈ ΠΎΠ±ΡΠ²ΠΈ Π½Π° ΠΎΠΏΡΠ΅Π΄Π΅Π»Π΅Π½Π½ΡΡ Π²ΡΡΠΎΡΡ.
ΠΠ°Π±ΠΎΠΉΠΊΡ ΠΏΡΠΈΠΊΡΠ΅ΠΏΠ»ΡΡΡ ΠΊ Π½ΠΈΠΆΠ½Π΅ΠΉ (Ρ ΠΎΠ΄ΠΎΠ²ΠΎΠΉ) ΠΏΠΎΠ²Π΅ΡΡ Π½ΠΎΡΡΠΈ ΠΊΠ°Π±Π»ΡΠΊΠ°.
ΠΎΠ±ΡΠ²Ρ ΡΠ°Π½ΡΠΎΠ²ΡΠΉ ΠΏΠΎΠ΄ΠΎΡΠ²Π° ΠΏΠΎΠ»ΠΈΡΡΠ΅ΡΠ°Π½
Π ΠΈΡΡΠ½ΠΎΠΊ 1. ΠΠ΅ΡΠ°Π»ΠΈ Π±ΠΎΡΠΈΠ½ΠΊΠ°: 1 — ΠΏΠΎΠ΄Π½ΠΎΡΠΎΠΊ; 2 — ΠΏΠΎΠ΄ΠΊΠ»Π°Π΄ΠΊΠ°; 3—Π·Π°ΠΊΡΠ΅ΠΏΠΊΠ°; 4 — ΡΠ·ΡΡΠΎΠΊ; 5 — ΠΏΠΎΠ΄Π±Π»ΠΎΡΠ½ΠΈΠΊ; 6 — ΡΡΠ°ΡΠ΅ΡΠΊΠ°; 7 — Π·Π°Π΄Π½ΠΈΠΉ Π½Π°ΡΡΠΆΠ½ΡΠΉ ΡΠ΅ΠΌΠ΅Π½Ρ; 8 — Π±Π΅ΡΠ΅Ρ; 9 — Π·Π°Π΄ΠΈΠ½ΠΊΠ°; 10 — Π·Π°Π΄Π½ΠΈΠΊ; // — ΠΊΠ°Π±Π»ΡΠΊ; 12 — ΡΠΎΡΠ·ΠΊΠ°; 13— ΠΏΠΎΠ΄ΠΎΡΠ²Π°; 14 — ΠΏΡΠΎΡΡΠΈΠ»ΠΊΠ°; 15 — ΠΎΡΠ½ΠΎΠ²Π½Π°Ρ ΡΡΠ΅Π»ΡΠΊΠ°; 16 — Π²ΠΊΠ»Π°Π΄Π½Π°Ρ ΡΡΠ΅Π»ΡΠΊΠ° Π ΠΏΡΠΎΡΠ΅ΡΡΠ΅ ΡΠΊΡΠΏΠ»ΡΠ°ΡΠ°ΡΠΈΠΈ Π½Π° Π΄Π΅ΡΠ°Π»ΠΈ ΠΎΠ±ΡΠ²ΠΈ Π²ΠΎΠ·Π΄Π΅ΠΉΡΡΠ²ΡΠ΅Ρ ΠΊΠ°ΠΊ ΡΡΠΎΠΏΠ° Π½ΠΎΡΡΠΈΠΊΠ°, ΡΠ°ΠΊ ΠΈ Π°ΡΠΌΠΎΡΡΠ΅ΡΠ½ΡΠ΅, ΠΌΠ΅Ρ Π°Π½ΠΈΡΠ΅ΡΠΊΠΈΠ΅ ΠΈ ΠΏΡΠΎΡΠΈΠ΅ ΡΠ°ΠΊΡΠΎΡΡ.
Π ΠΏΡΠΎΡΠ΅ΡΡΠ΅ Π½ΠΎΡΠΊΠΈ Π΄Π΅ΡΠ°Π»ΠΈ ΠΎΠ±ΡΠ²ΠΈ ΠΈ ΡΠΎΠ΅Π΄ΠΈΠ½ΠΈΡΠ΅Π»ΡΠ½ΡΠ΅ ΡΠ²Ρ ΠΈΡΠΏΡΡΡΠ²Π°ΡΡ ΡΠ°Π·Π»ΠΈΡΠ½ΡΠ΅ Π½Π°Π³ΡΡΠ·ΠΊΠΈ.
ΠΠ°ΡΡΠΆΠ½ΡΠ΅ Π΄Π΅ΡΠ°Π»ΠΈ Π½ΠΈΠ·Π° ΠΎΠ±ΡΠ²ΠΈ ΡΠΊΡΠΏΠ»ΡΠ°ΡΠΈΡΡΡΡΡΡ Π² Π½Π΅ΡΠΊΠΎΠ»ΡΠΊΠΎ ΠΈΠ½ΡΡ ΡΡΠ»ΠΎΠ²ΠΈΡΡ , ΡΠ΅ΠΌ Π΄Π΅ΡΠ°Π»ΠΈ Π²Π΅ΡΡ Π°. ΠΠ° Π½ΠΈΡ ΡΠ΅ΡΠ°ΡΡΠ΅Π΅ Π²ΠΎΠ·Π΄Π΅ΠΉΡΡΠ²ΠΈΠ΅ ΠΎΠΊΠ°Π·ΡΠ²Π°Π΅Ρ ΠΊΠΎΠ½ΡΠ°ΠΊΡ Ρ Π³ΡΡΠ½ΡΠΎΠΌ, Π°ΡΠΌΠΎΡΡΠ΅ΡΠ½ΡΠ΅ ΠΈ Π΄ΡΡΠ³ΠΈΠ΅ ΡΡΠ»ΠΎΠ²ΠΈΡ.
Π ΠΏΡΠΎΡΠ΅ΡΡΠ΅ Ρ ΠΎΠ΄ΡΠ±Ρ ΠΏΠΎΠ΄ΠΎΡΠ²Π° ΠΈΠ·Π³ΠΈΠ±Π°Π΅ΡΡΡ Π² ΠΏΡΡΠΊΠΎΠ²ΠΎΠΉ ΡΠ°ΡΡΠΈ (ΡΠ°Π΄ΠΈΡΡ ΠΊΡΠΈΠ²ΠΈΠ·Π½Ρ Π΄ΠΎ 8 ΡΠΌ) ΠΈ ΡΠ΄Π»ΠΈΠ½ΡΠ΅ΡΡΡ Π΄ΠΎ 25%. ΠΠ° ΠΏΠΎΠ΄ΠΎΡΠ²Ρ ΠΎΠΊΠ°Π·ΡΠ²Π°Π΅Ρ Π΄Π°Π²Π»Π΅Π½ΠΈΠ΅ ΠΌΠ°ΡΡΠ° Π½ΠΎΡΡΠΈΠΊΠ°. ΠΡΠΎ Π΄Π°Π²Π»Π΅Π½ΠΈΠ΅ ΡΠ°ΡΠΏΡΠ΅Π΄Π΅Π»Π΅Π½ΠΎ ΠΏΠΎ ΠΏΠΎΠ²Π΅ΡΡ Π½ΠΎΡΡΠΈ ΠΏΠΎΠ΄ΠΎΡΠ²Ρ Π½Π΅ΡΠ°Π²Π½ΠΎΠΌΠ΅ΡΠ½ΠΎ, ΡΡΠΎ Π·Π°Π²ΠΈΡΠΈΡ ΠΎΡ ΡΡΡΠΎΠ΅Π½ΠΈΡ ΡΡΠ°ΡΡΠΊΠΎΠ² ΡΡΠΎΠΏΡ, ΠΏΠΎΡ ΠΎΠ΄ΠΊΠΈ Π½ΠΎΡΡΠΈΠΊΠ° ΠΈ ΠΊΠΎΠ½ΡΡΡΡΠΊΡΠΈΠΈ ΠΎΠ±ΡΠ²ΠΈ. ΠΠ°Π²Π»Π΅Π½ΠΈΠ΅ Π½Π° ΠΎΡΠ΄Π΅Π»ΡΠ½ΡΠ΅ ΡΡΠ°ΡΡΠΊΠΈ ΠΏΠΎΠ΄ΠΎΡΠ²Ρ ΠΏΡΠΈ Π±Π΅Π³Π΅ ΠΌΠΎΠΆΠ΅Ρ Π΄ΠΎΡΡΠΈΠ³Π°ΡΡ 20 ΠΠΠ°.
ΠΠΎΠ΄ΠΎΡΠ²Π°, Π½Π°Ρ ΠΎΠ΄ΡΡΠ°ΡΡΡ ΠΏΠΎΠ΄ Π΄Π°Π²Π»Π΅Π½ΠΈΠ΅ΠΌ ΠΌΠ°ΡΡΡ Π½ΠΎΡΡΠΈΠΊΠ°, ΠΏΡΠΈ ΠΏΠ΅ΡΠ΅ΠΌΠ΅ΡΠ΅Π½ΠΈΠΈ ΠΏΠΎ Π³ΡΡΠ½ΡΡ ΠΏΠΎΠ΄Π²Π΅ΡΠ³Π°Π΅ΡΡΡ ΡΡΠ΅Π½ΠΈΡ ΠΊΠ°ΡΠ΅Π½ΠΈΡ ΠΈ ΡΡΠ΅Π½ΠΈΡ ΡΠΊΠΎΠ»ΡΠΆΠ΅Π½ΠΈΡ. Π ΠΏΡΠΎΡΠ΅ΡΡΠ΅ Ρ ΠΎΠ΄ΡΠ±Ρ ΠΈ Π±Π΅Π³Π° Ρ ΠΌΠΎΠΌΠ΅Π½ΡΠ° ΠΏΠΎΠ΄ΡΠ΅ΠΌΠ° ΠΊΠ°Π±Π»ΡΠΊΠ° Π΄ΠΎ ΠΎΡΡΡΠ²Π° Π½ΠΎΡΠΊΠ° Π½Π°Π±Π»ΡΠ΄Π°Π΅ΡΡΡ ΡΡΠ΅Π½ΠΈΠ΅ ΠΊΠ°ΡΠ΅Π½ΠΈΡ. ΠΡΠΈ Ρ ΠΎΠ΄ΡΠ±Π΅ ΠΏΠΎ ΠΏΠΎΠ²Π΅ΡΡ Π½ΠΎΡΡΡΠΌ Ρ Π½ΠΈΠ·ΠΊΠΈΠΌ ΠΊΠΎΡΡΡΠΈΡΠΈΠ΅Π½ΡΠΎΠΌ ΡΡΠ΅Π½ΠΈΡ (Π»Π΅Π΄, ΠΏΠ°ΡΠΊΠ΅Ρ, Π»ΠΈΠ½ΠΎΠ»Π΅ΡΠΌ) ΠΏΡΠ΅ΠΎΠ±Π»Π°Π΄Π°Π΅Ρ ΡΡΠ΅Π½ΠΈΠ΅ ΡΠΊΠΎΠ»ΡΠΆΠ΅Π½ΠΈΡ. Π‘ΠΎΠΎΡΠ½ΠΎΡΠ΅Π½ΠΈΠ΅ ΠΌΠ΅ΠΆΠ΄Ρ ΡΡΠ΅Π½ΠΈΠ΅ΠΌ ΠΊΠ°ΡΠ΅Π½ΠΈΡ ΠΈ ΡΡΠ΅Π½ΠΈΠ΅ΠΌ ΡΠΊΠΎΠ»ΡΠΆΠ΅Π½ΠΈΡ Π·Π°Π²ΠΈΡΠΈΡ ΠΎΡ ΡΡΠ»ΠΎΠ²ΠΈΠΉ Π½ΠΎΡΠΊΠΈ ΠΈ ΠΊΠΎΠ½ΡΡΡΡΠΊΡΠΈΠΈ ΠΎΠ±ΡΠ²ΠΈ.
ΠΠ°ΠΈΠ±ΠΎΠ»ΡΡΠΈΠ΅ ΡΠΈΠ»Ρ ΡΡΠ΅Π½ΠΈΡ Π²ΠΎΠ·Π½ΠΈΠΊΠ°ΡΡ Π½Π° ΡΡΠ°ΡΡΠΊΠ°Ρ ΡΠΎΡΡΠ΅Π΄ΠΎΡΠΎΡΠ΅Π½Π½ΠΎΠ³ΠΎ Π΄Π°Π²Π»Π΅Π½ΠΈΡ: ΠΏΠΎΠ΄ Π±ΠΎΠ»ΡΡΠΈΠΌ ΠΏΠ°Π»ΡΡΠ΅ΠΌ ΠΈ ΠΏΠ»ΡΡΠ½Π΅ΡΠ°Π»Π°Π½Π³ΠΎΠ²ΡΠΌ ΡΠΎΡΠ»Π΅Π½Π΅Π½ΠΈΠ΅ΠΌ ΡΡΠΎΠΏΡ.
ΠΠ° ΠΏΠΎΠ΄ΠΎΡΠ²Ρ ΡΠ°ΠΊΠΆΠ΅ Π΄Π΅ΠΉΡΡΠ²ΡΡΡ ΡΠ΅ΠΌΠΏΠ΅ΡΠ°ΡΡΡΠ° ΠΈ Π²Π»Π°Π³Π° ΠΎΠΊΡΡΠΆΠ°ΡΡΠ΅Π³ΠΎ Π²ΠΎΠ·Π΄ΡΡ Π°, ΠΏΡΠ»Ρ, Π³ΡΡΠ·Ρ ΠΈ Π΄Ρ.
ΠΠΎΡΠΎΠ²ΡΠ΄Π΅Π»Π΅Π½ΠΈΡ ΡΡΠΎΠΏΡ Π² ΠΌΠ°Π»ΠΎΠΉ ΡΡΠ΅ΠΏΠ΅Π½ΠΈ ΠΌΠΎΠ³ΡΡ Π²Π»ΠΈΡΡΡ Π½Π° ΠΈΠ·Π½ΠΎΡ ΠΏΠΎΠ΄ΠΎΡΠ²Ρ, ΡΠ°ΠΊ ΠΊΠ°ΠΊ ΠΎΠ½ΠΈ ΠΏΡΠ°ΠΊΡΠΈΡΠ΅ΡΠΊΠΈ Π½Π΅ Π΄ΠΎΡΡΠΈΠ³Π°ΡΡ Π΅Π΅. Π ΠΏΡΠΎΡΠ΅ΡΡΠ΅ Π½ΠΎΡΠΊΠΈ ΠΊΠΎΠΆΠ°Π½ΡΠ΅ ΠΏΠΎΠ΄ΠΎΡΠ²Ρ ΠΈΠ½ΡΠ΅Π½ΡΠΈΠ²Π½ΠΎ ΠΈΡΡΠΈΡΠ°ΡΡΡΡ Π²ΠΏΠ»ΠΎΡΡ Π΄ΠΎ ΡΠΊΠ²ΠΎΠ·Π½ΠΎΠ³ΠΎ ΠΏΡΠΎΡΠΈΡΠ°Π½ΠΈΡ Π² ΠΏΠΎΠ΄ΠΌΠ΅ΡΠΎΡΠ½ΠΎΠΉ ΡΠ°ΡΡΠΈ, ΠΏΡΠΎΠΌΠΎΠΊΠ°ΡΡ. Π Π΅Π·ΠΈΠ½ΠΎΠ²ΡΠ΅ ΠΏΠΎΠ΄ΠΎΡΠ²Ρ ΠΈΡΡΠΈΡΠ°ΡΡΡΡ Π½Π΅Π·Π½Π°ΡΠΈΡΠ΅Π»ΡΠ½ΠΎ;
ΠΠ° ΠΊΠ°Π±Π»ΡΠΊΠΈ ΠΏΡΠΈ Π½ΠΎΡΠΊΠ΅ ΠΎΠ±ΡΠ²ΠΈ Π²ΠΎΠ·Π΄Π΅ΠΉΡΡΠ²ΡΡΡ ΠΌΠ΅Ρ Π°Π½ΠΈΡΠ΅ΡΠΊΠΈΠ΅ ΡΡΠΈΠ»ΠΈΡ ΡΠΆΠ°ΡΠΈΡ ΠΈ ΠΈΠ·Π³ΠΈΠ±Π°. ΠΡΠΈ ΡΡΠΈΠ»ΠΈΡ Π·Π°Π²ΠΈΡΡΡ ΠΎΡ ΠΊΠΎΠ½ΡΡΡΡΠΊΡΠΈΠΈ ΠΊΠ°Π±Π»ΡΠΊΠ° (Π² ΠΎΡΠ½ΠΎΠ²Π½ΠΎΠΌ Π²ΡΡΠΎΡΡ ΠΈ ΠΏΠΎΠΏΠ΅ΡΠ΅ΡΠ½ΠΎΠ³ΠΎ ΡΠ΅ΡΠ΅Π½ΠΈΡ) ΠΈ ΠΎΡΠΎΠ±Π΅Π½Π½ΠΎΡΡΠ΅ΠΉ ΠΏΠΎΡ ΠΎΠ΄ΠΊΠΈ Π½ΠΎΡΡΠΈΠΊΠ°. ΠΠ»Ρ Π²ΡΡΠΎΠΊΠΈΡ ΠΈ ΠΎΡΠΎΠ±Π΅Π½Π½ΠΎ ΡΠΎΠ½ΠΊΠΈΡ ΠΊΠ°Π±Π»ΡΠΊΠΎΠ² Π½Π°ΠΈΠ±ΠΎΠ»Π΅Π΅ Ρ Π°ΡΠ°ΠΊΡΠ΅ΡΠ½Ρ ΠΈΠ·Π³ΠΈΠ±Π°ΡΡΠΈΠ΅ ΡΡΠΈΠ»ΠΈΡ. ΠΠ°ΠΏΡΡΠΆΠ΅Π½ΠΈΠ΅ ΠΈΠ·Π³ΠΈΠ±Π° Π² Π²ΡΡΠΎΠΊΠΈΡ ΡΠΎΠ½ΠΊΠΈΡ ΠΊΠ°Π±Π»ΡΠΊΠ°Ρ Π΄ΠΎΡΡΠΈΠ³Π°Π΅Ρ 20 ΠΠΠ°, ΡΡΠΎ ΠΌΠΎΠΆΠ΅Ρ Π²ΡΠ·Π²Π°ΡΡ ΠΈΡ ΠΏΠΎΠ»ΠΎΠΌΠΊΡ ΠΎΠΊΠΎΠ»ΠΎ Π½Π°Π±ΠΎΠΉΠΊΠΈ.
ΠΠ»Ρ Π½ΠΈΠ·ΠΊΠΈΡ ΡΠ΅Π·ΠΈΠ½ΠΎΠ²ΡΡ ΠΊΠ°Π±Π»ΡΠΊΠΎΠ², Π½Π΅ ΠΈΠΌΠ΅ΡΡΠΈΡ Π½Π°Π±ΠΎΠΉΠΊΠΈ, Π½Π°ΠΈΠ±ΠΎΠ»Π΅Π΅ Ρ Π°ΡΠ°ΠΊΡΠ΅ΡΠ½ΠΎ ΠΈΡΡΠΈΡΠ°Π½ΠΈΠ΅, ΠΏΡΠΈΡΠ΅ΠΌ Π±ΠΎΠ»Π΅Π΅ ΡΠ΅ΠΌ Π² 90% ΡΠ»ΡΡΠ°Π΅Π² ΠΈΠ·Π½ΠΎΡ ΠΊΠ°Π±Π»ΡΠΊΠΎΠ² Π½Π°Π±Π»ΡΠ΄Π°Π΅ΡΡΡ ΠΏΠΎ Π²Π½Π΅ΡΠ½ΠΈΠΌ ΡΡΠΎΡΠΎΠ½Π°ΠΌ Π·Π°Π΄Π½Π΅Π³ΠΎ ΠΊΡΠ°Ρ.
ΠΠ°Π±ΠΎΠΉΠΊΠΈ ΠΏΠΎΠ΄Π²Π΅ΡΠ³Π°ΡΡΡΡ ΠΈΡΡΠΈΡΠ°Π½ΠΈΡ ΠΈ ΡΠΆΠ°ΡΠΈΡ. ΠΠ° Π½Π°Π±ΠΎΠΉΠΊΠΈ Π²ΡΡΠΎΠΊΠΈΡ ΡΠΎΠ½ΠΊΠΈΡ ΠΊΠ°Π±Π»ΡΠΊΠΎΠ² Π΄Π΅ΠΉΡΡΠ²ΡΡΡ Π½Π°ΠΏΡΡΠΆΠ΅Π½ΠΈΡ ΡΠΆΠ°ΡΠΈΡ Π΄ΠΎ 30 ΠΠΠ°.
ΠΠ°Π±Π»ΡΠΊΠΈ ΠΈ Π½Π°Π±ΠΎΠΉΠΊΠΈ ΡΠ°Π±ΠΎΡΠ°ΡΡ Π² ΡΡΠ»ΠΎΠ²ΠΈΡΡ Π½Π΅ΠΏΠΎΡΡΠ΅Π΄ΡΡΠ²Π΅Π½Π½ΠΎΠ³ΠΎ ΠΊΠΎΠ½ΡΠ°ΠΊΡΠ° Ρ Π³ΡΡΠ½ΡΠΎΠΌ, ΠΏΠΎΡΡΠΎΠΌΡ Π½Π° Π½ΠΈΡ ΠΎΠΊΠ°Π·ΡΠ²Π°ΡΡ Π²Π»ΠΈΡΠ½ΠΈΠ΅ Π°ΡΠΌΠΎΡΡΠ΅ΡΠ½ΡΠ΅ ΠΈ Π΄ΡΡΠ³ΠΈΠ΅ ΡΠ°ΠΊΡΠΎΡΡ.
ΠΡΠ½ΠΎΠ²Π½ΡΠΌΠΈ ΡΡΠ΅Π±ΠΎΠ²Π°Π½ΠΈΡΠΌΠΈ ΠΊ ΠΏΠΎΠ΄ΠΎΡΠ²Π΅Π½Π½ΡΠΌ ΠΌΠ°ΡΠ΅ΡΠΈΠ°Π»Π°ΠΌ ΡΠ²Π»ΡΡΡΡΡ: Π²ΡΡΠΎΠΊΠΈΠ΅ ΡΠΎΠΏΡΠΎΡΠΈΠ²Π»Π΅Π½ΠΈΡ ΠΌΠ½ΠΎΠ³ΠΎΠΊΡΠ°ΡΠ½ΠΎΠΌΡ ΠΈΠ·Π³ΠΈΠ±Ρ ΠΈ ΠΈΡΡΠΈΡΠ°Π½ΠΈΡ, Π²ΠΎΠ΄ΠΎΠ½Π΅ΠΏΡΠΎΠ½ΠΈΡΠ°Π΅ΠΌΠΎΡΡΡ, ΠΎΠ±Π΅ΡΠΏΠ΅ΡΠ΅Π½ΠΈΠ΅ Ρ ΠΎΡΠΎΡΠ΅Π³ΠΎ ΡΡΠ΅ΠΏΠ»Π΅Π½ΠΈΡ Ρ Π³ΡΡΠ½ΡΠΎΠΌ, ΡΠ²Π΅ΡΠ΄ΠΎΡΡΡ ΠΈ Π°ΠΌΠΎΡΡΠΈΠ·Π°ΡΠΈΠΎΠ½Π½Π°Ρ ΡΠΏΠΎΡΠΎΠ±Π½ΠΎΡΡΡ, Π½ΠΈΠ·ΠΊΠ°Ρ ΡΠ΅ΠΏΠ»ΠΎΠΏΡΠΎΠ²ΠΎΠ΄Π½ΠΎΡΡΡ (Π΄Π»Ρ ΠΎΠ±ΡΠ²ΠΈ Π·ΠΈΠΌΠ½Π΅Π³ΠΎ ΡΠ΅Π·ΠΎΠ½Π°), Π½Π΅Π±ΠΎΠ»ΡΡΠ°Ρ ΠΌΠ°ΡΡΠ° ΠΏΡΠΈ Π±ΠΎΠ»ΡΡΠΎΠΉ ΡΠΎΠ»ΡΠΈΠ½Π΅. ΠΠΎΠ΄ΠΎΡΠ²Π΅Π½Π½ΡΠ΅ ΠΌΠ°ΡΠ΅ΡΠΈΠ°Π»Ρ Π΄Π»Ρ ΡΠΏΠ΅ΡΠΈΠ°Π»ΡΠ½ΠΎΠΉ ΠΎΠ±ΡΠ²ΠΈ Π² Π·Π°Π²ΠΈΡΠΈΠΌΠΎΡΡΠΈ ΠΎΡ ΡΡΠ»ΠΎΠ²ΠΈΠΉ ΡΠΊΡΠΏΠ»ΡΠ°ΡΠ°ΡΠΈΠΈ Π΄ΠΎΠ»ΠΆΠ½Ρ Π±ΡΡΡ ΡΠ»Π΅ΠΊΡΡΠΎΠΏΡΠΎΠ²ΠΎΠ΄Π½ΡΠΌΠΈ ΠΈΠ»ΠΈ ΡΠ»Π΅ΠΊΡΡΠΎΠ·Π°ΡΠΈΡΠ½ΡΠΌΠΈ, ΠΌΠ°ΡΠ»ΠΎΠ±Π΅Π½Π·ΠΎΡΡΠΎΠΉΠΊΠΈΠΌΠΈ, Π°Π½ΡΠΈΠΊΠΈΡΠ»ΠΎΡΠ½ΡΠΌΠΈ ΠΈ Ρ. ΠΏ.
ΠΠΎΠ΄ΠΎΡΠ²Π΅Π½Π½ΡΠ΅ ΠΌΠ°ΡΠ΅ΡΠΈΠ°Π»Ρ ΠΌΠΎΠ³ΡΡ ΠΈΠΌΠ΅ΡΡ ΠΈ Π½Π΅Π²ΡΡΠΎΠΊΠΈΠ΅ ΠΏΠΎΠΊΠ°Π·Π°ΡΠ΅Π»ΠΈ Π³ΠΈΠ³ΠΈΠ΅Π½ΠΈΡΠ΅ΡΠΊΠΈΡ ΡΠ²ΠΎΠΉΡΡΠ², ΡΠ°ΠΊ ΠΊΠ°ΠΊ ΠΌΠ΅ΠΆΠ΄Ρ ΡΡΠΎΠΏΠΎΠΉ ΠΈ ΠΏΠΎΠ΄ΠΎΡΠ²ΠΎΠΉ Π½Π°Ρ ΠΎΠ΄ΠΈΡΡΡ Π½Π΅ΡΠΊΠΎΠ»ΡΠΊΠΎ ΡΠ»ΠΎΠ΅Π² ΡΠ°Π·Π»ΠΈΡΠ½ΡΡ ΠΌΠ°ΡΠ΅ΡΠΈΠ°Π»ΠΎΠ², Π² ΡΠΎΠΌ ΡΠΈΡΠ»Π΅ ΠΈ Π½Π΅ΠΏΡΠΎΠ½ΠΈΡΠ°Π΅ΠΌΡΡ Π΄Π»Ρ ΠΏΠ°ΡΠΎΠ² ΠΈ Π²Π»Π°Π³ΠΈ. ΠΠ°ΡΠ΅ΡΠΈΠ°Π»Ρ Ρ Π²ΡΡΠΎΠΊΠΈΠΌΠΈ ΠΏΠΎΠΊΠ°Π·Π°ΡΠ΅Π»ΡΠΌΠΈ ΠΏΠ°ΡΠΎΠΏΡΠΎΠ½ΠΈΡΠ°Π΅ΠΌΠΎΡΡΠΈ, Π²Π»Π°Π³ΠΎΠΏΠΎΠ³Π»ΠΎΡΠ΅Π½ΠΈΡ ΠΈ Π²Π»Π°Π³ΠΎΠΎΡΠ΄Π°ΡΠΈ ΠΌΠΎΠ³ΡΡ ΡΠΎΠ»ΡΠΊΠΎ ΡΡ ΡΠ΄ΡΠΈΡΡ Π²Π»Π°Π³ΠΎΠΈ ΡΠ΅ΠΏΠ»ΠΎΠ·Π°ΡΠΈΡΠ½ΡΠ΅ ΡΠ²ΠΎΠΉΡΡΠ²Π° ΠΎΠ±ΡΠ²ΠΈ.
ΠΠ°ΡΠ΅ΡΠΈΠ°Π»Ρ ΠΊΠ°Π±Π»ΡΠΊΠΎΠ² Π΄ΠΎΠ»ΠΆΠ½Ρ Π±ΡΡΡ ΡΠ²Π΅ΡΠ΄ΡΠΌΠΈ, ΡΠ΄Π΅ΡΠΆΠΈΠ²Π°ΡΡ Π³Π²ΠΎΠ·Π΄ΠΈ ΠΈ Π²ΠΈΠ½ΡΡ, ΠΈΠΌΠ΅ΡΡ Π²ΡΡΠΎΠΊΠΈΠ΅ ΡΠΎΠΏΡΠΎΡΠΈΠ²Π»Π΅Π½ΠΈΡ ΡΠΆΠ°ΡΠΈΡ ΠΈ ΠΈΠ·Π³ΠΈΠ±Ρ, ΡΠΏΠΎΡΠΎΠ±Π½ΠΎΡΡΡ Ρ ΠΎΡΠΎΡΠΎ ΠΏΡΠΈΠΊΠ»Π΅ΠΈΠ²Π°ΡΡΡΡ. ΠΠΎΠ»ΡΡΠΎΠ΅ ΠΊΠΎΠ»ΠΈΡΠ΅ΡΡΠ²ΠΎ ΠΊΠ°Π±Π»ΡΠΊΠΎΠ² ΠΈΠ·Π³ΠΎΡΠ°Π²Π»ΠΈΠ²Π°ΡΡ ΠΌΠ΅ΡΠΎΠ΄Π°ΠΌΠΈ Π»ΠΈΡΡΡ ΠΈΠ· ΡΠ΅ΡΠΌΠΎΠΏΠ»Π°ΡΡΠΈΡΠ½ΡΡ ΠΌΠ°ΡΠ΅ΡΠΈΠ°Π»ΠΎΠ², ΡΠΏΠΎΡΠΎΠ±Π½ΡΡ ΠΏΠ»Π°Π²ΠΈΡΡΡΡ ΠΏΡΠΈ ΠΎΠΏΡΠ΅Π΄Π΅Π»Π΅Π½Π½ΡΡ ΡΠ΅ΠΌΠΏΠ΅ΡΠ°ΡΡΡΠ°Ρ ΠΎΠ±ΡΠ°Π±ΠΎΡΠΊΠΈ.
2. Π Π°Π½ΡΠΎΠ²ΡΠΉ ΠΌΠ΅ΡΠΎΠ΄ ΠΊΡΠ΅ΠΏΠ»Π΅Π½ΠΈΡ ΠΏΠΎΠ΄ΠΎΡΠ² ΠΎΡΠ½ΠΎΡΠΈΡΡΡ ΠΊ Π½ΠΈΡΠΎΡΠ½ΠΎΠΌΡ, ΠΊΠΎΡΠΎΡΡΠΉ ΠΏΡΠΈΠΌΠ΅Π½ΡΡΡ ΠΏΡΠΈ ΠΈΠ·Π³ΠΎΡΠΎΠ²Π»Π΅Π½ΠΈΠΈ ΠΏΠΎΠ²ΡΠ΅Π΄Π½Π΅Π²Π½ΠΎΠΉ, ΠΏΡΠΎΠΈΠ·Π²ΠΎΠ΄ΡΡΠ²Π΅Π½Π½ΠΎΠΉ ΠΈ ΡΠΏΠΎΡΡΠΈΠ²Π½ΠΎΠΉ ΠΎΠ±ΡΠ²ΠΈ Π½Π° ΠΊΠΎΠΆΠ°Π½ΠΎΠΉ ΠΈ ΡΠ΅Π·ΠΈΠ½ΠΎΠ²ΠΎΠΉ ΠΏΠΎΠ΄ΠΎΡΠ²Π°Ρ Π Π°Π½ΡΠΎΠ²ΡΠΉ ΠΌΠ΅ΡΠΎΠ΄ (ΡΠΈΡ. 2) ΡΠΈΡΠΎΠΊΠΎ ΠΏΡΠΈΠΌΠ΅Π½ΡΠ΅ΡΡΡ, Π½Π΅ΡΠΌΠΎΡΡΡ Π½Π° Π·Π½Π°ΡΠΈΡΠ΅Π»ΡΠ½ΡΡ ΡΠ»ΠΎΠΆΠ½ΠΎΡΡΡ, ΡΡΡΠ΄ΠΎΠ΅ΠΌΠΊΠΎΡΡΡ, ΠΏΠΎΠ²ΡΡΠ΅Π½Π½ΡΠΉ ΡΠ°ΡΡ ΠΎΠ΄ ΠΏΠΎΠ΄ΠΎΡΠ²Π΅Π½Π½ΡΡ ΠΈ ΡΡΠ΅Π»Π΅ΡΠ½ΡΡ ΠΌΠ°ΡΠ΅ΡΠΈΠ°Π»ΠΎΠ² ΠΏΠΎ ΡΡΠ°Π²Π½Π΅Π½ΠΈΡ Ρ Π΄ΡΡΠ³ΠΈΠΌΠΈ ΠΌΠ΅ΡΠΎΠ΄Π°ΠΌΠΈ. ΠΡΠΎ ΠΎΠ±ΡΡΡΠ½ΡΠ΅ΡΡΡ ΡΠ΄Π°ΡΠ½ΡΠΌ ΠΊΠΎΠ½ΡΡΡΡΠΊΡΠΈΠ²Π½ΡΠΌ ΡΠ΅ΡΠ΅Π½ΠΈΠ΅ΠΌ, ΡΠΎΡΠ΅ΡΠ°Π½ΠΈΠ΅ΠΌ Π±ΠΎΠ»ΡΡΠΎΠΉ ΠΏΡΠΎΡΠ½ΠΎΡΡΠΈ Ρ Π²ΡΡΠΎΠΊΠΎΠΉ ΡΠ»Π°ΡΡΠΈΡΠ½ΠΎΡΡΡΡ, Ρ ΠΎΡΠΎΡΠΈΠΌΠΈ Π³ΠΈΠ³ΠΈΠ΅Π½ΠΈΡΠ΅ΡΠΊΠΈΠΌΠΈ ΡΠ²ΠΎΠΉΡΡΠ²Π°ΠΌΠΈ, ΠΌΠ°Π»ΠΎΠΉ ΡΠ΅ΠΏΠ»ΠΎΠΏΡΠΎΠ²ΠΎΠ΄Π½ΠΎΡΡΡΡ, ΠΈΠ·ΡΡΠ½ΡΠΌ Π²Π½Π΅ΡΠ½ΠΈΠΌ Π²ΠΈΠ΄ΠΎΠΌ ΠΎΠ±ΡΠ²ΠΈ. Π Π°Π½Ρ ΠΏΡΠΈΠΊΡΠ΅ΠΏΠ»ΡΡΡ ΠΎΠ΄Π½ΠΎΠ½ΠΈΡΠΎΡΠ½ΡΠΌ ΡΠ²ΠΎΠΌ ΠΎΠ΄Π½ΠΎΠ²ΡΠ΅ΠΌΠ΅Π½Π½ΠΎ ΠΊ Π·Π°Π³ΠΎΡΠΎΠ²ΠΊΠ΅ Π²Π΅ΡΡ Π° ΠΈ Π³ΡΠ±Π΅ ΡΠ°Π½ΡΠΎΠ²ΠΎΠΉ ΡΡΠ΅Π»ΡΠΊΠΈ Π½Π° ΡΠ°Π½ΡΠΎΠ²ΡΠΈΠ²Π½ΠΎΠΉ ΠΌΠ°ΡΠΈΠ½Π΅.
Π ΠΈΡΡΠ½ΠΎΠΊ 2. Π Π°Π½ΡΠΎΠ²ΡΠΉ ΠΌΠ΅ΡΠΎΠ΄ ΠΊΡΠ΅ΠΏΠ»Π΅Π½ΠΈΡ ΠΡΠΈΠΊΡΠ΅ΠΏΠ»Π΅Π½ΠΈΠ΅ ΡΠ°Π½ΡΠ°. ΠΡΠΎΡΠ½ΠΎΡΡΡ ΠΊΡΠ΅ΠΏΠ»Π΅Π½ΠΈΡ Π½ΠΈΠ·Π° ΠΎΠ±ΡΠ²ΠΈ Ρ ΡΠ°Π½ΡΠΎΠΌ Π·Π°Π²ΠΈΡΠΈΡ ΠΎΡ ΠΏΡΠΎΡΠ½ΠΎΡΡΠΈ ΠΊΡΠ΅ΠΏΠ»Π΅Π½ΠΈΡ ΡΠ°Π½ΡΠ° ΠΊ ΡΡΠ΅Π»ΡΠΊΠ΅ ΠΈΠ»ΠΈ Π·Π°Π³ΠΎΡΠΎΠ²ΠΊΠ΅ Π²Π΅ΡΡ Π° ΠΎΠ±ΡΠ²ΠΈ.
Π Π°Π½Ρ ΠΌΠΎΠΆΠ½ΠΎ ΠΏΡΠΈΠΊΡΠ΅ΠΏΠ»ΡΡΡ ΠΊ Π·Π°Π³ΠΎΡΠΎΠ²ΠΊΠ΅ Π²Π΅ΡΡ Π° ΠΎΠ±ΡΠ²ΠΈ ΠΏΠΎΡΠ»Π΅ ΡΠΎΡΠΌΠΎΠ²Π°Π½ΠΈΡ (ΠΎΠ±ΡΠ²Ρ ΠΌΠ΅ΡΠΎΠ΄ΠΎΠ² ΠΊΡΠ΅ΠΏΠ»Π΅Π½ΠΈΡ ΡΠ°Π½ΡΠΎΠ²ΠΎΠ³ΠΎ, ΡΠ°Π½ΡΠΎΠΏΡΠΎΡΠΈΠ²Π½ΠΎΠ³ΠΎ, ΡΠ°Π½ΡΠΎΡΠΊΠΎΠ±ΠΎΡΠ½ΠΎΠ³ΠΎ ΠΈ Π΄Ρ.) ΠΈΠ»ΠΈ ΠΏΠ΅ΡΠ΅Π΄ ΡΠΎΡΠΌΠΎΠ²Π°Π½ΠΈΠ΅ΠΌ (ΠΎΠ±ΡΠ²Ρ ΠΌΠ΅ΡΠΎΠ΄Π° ΠΠ°ΡΠΊΠΎ). ΠΡΠΈ ΠΊΡΠ΅ΠΏΠ»Π΅Π½ΠΈΠΈ ΡΠ°Π½ΡΠ° Π½Π° ΠΏΡΠΎΡΠΈΠ²Π½ΠΎΠΉ ΠΌΠ°ΡΠΈΠ½Π΅ ΡΠΎΠ² ΡΠ°ΡΠΏΠΎΠ»ΠΎΠΆΠ΅Π½ ΠΏΠ΅ΡΠΏΠ΅Π½Π΄ΠΈΠΊΡΠ»ΡΡΠ½ΠΎ ΠΏΠΎΠ²Π΅ΡΡ Π½ΠΎΡΡΠΈ ΡΡΠ΅Π»ΡΠΊΠΈ ΠΈ ΠΈΡΠΏΡΡΡΠ²Π°Π΅Ρ Π±ΠΎΠ»ΡΡΠΈΠ΅ Π½Π°Π³ΡΡΠ·ΠΊΠΈ Π²ΠΎ Π²ΡΠ΅ΠΌΡ Π½ΠΎΡΠΊΠΈ ΠΎΠ±ΡΠ²ΠΈ. ΠΡΠΎΠΌΠ΅ ΡΠΎΠ³ΠΎ, Π½Π° Π½Π΅Π³ΠΎ Π΄Π΅ΠΉΡΡΠ²ΡΠ΅Ρ ΠΏΠΎΡ, Π²ΡΠ΄Π΅Π»ΡΠ΅ΠΌΡΠΉ ΡΡΠΎΠΏΠΎΠΉ, ΠΊΠΎΡΠΎΡΡΠΉ ΡΠ½ΠΈΠΆΠ°Π΅Ρ ΠΏΡΠΎΡΠ½ΠΎΡΡΡ Π»ΡΠ½ΡΠ½ΡΡ Π½ΠΈΡΠΎΠΊ. ΠΡΠΈΠΌΠ΅Π½Π΅Π½ΠΈΠ΅ ΠΊΠ°ΠΏΡΠΎΠ½ΠΎΠ²ΡΡ Π½ΠΈΡΠΎΠΊ Π΄Π°Π»ΠΎ Π²ΠΎΠ·ΠΌΠΎΠΆΠ½ΠΎΡΡΡ ΡΡΡΡΠ°Π½ΠΈΡΡ Π½Π΅ΠΊΠΎΡΠΎΡΡΠ΅ Π½Π΅Π΄ΠΎΡΡΠ°ΡΠΊΠΈ ΡΠ²Π°, ΠΏΠΎΠ»ΡΡΠ°Π΅ΠΌΠΎΠ³ΠΎ ΠΏΡΠΎΡΠΈΠ²Π½ΡΠΌ ΠΌΠ΅ΡΠΎΠ΄ΠΎΠΌ. Π¨ΠΎΠ², ΡΠΊΡΠ΅ΠΏΠ»ΡΡΡΠΈΠΉ ΡΠ°Π½Ρ Ρ Π·Π°Π³ΠΎΡΠΎΠ²ΠΊΠΎΠΉ Π²Π΅ΡΡ Π° ΠΎΠ±ΡΠ²ΠΈ, ΡΠ°ΠΊΠΆΠ΅ ΡΠ°ΡΠΏΠΎΠ»ΠΎΠΆΠ΅Π½ ΠΏΠ΅ΡΠΏΠ΅Π½Π΄ΠΈΠΊΡΠ»ΡΡΠ½ΠΎ ΠΏΠΎΠ²Π΅ΡΡ Π½ΠΎΡΡΠΈ ΡΡΠ΅Π»ΡΠΊΠΈ, Π½ΠΎ ΠΎΠ½ ΠΈΡΠΏΡΡΡΠ²Π°Π΅Ρ ΠΌΠ΅Π½ΡΡΠΈΠ΅ Π½Π°Π³ΡΡΠ·ΠΊΠΈ ΠΈ ΠΈΠ·ΠΎΠ»ΠΈΡΠΎΠ²Π°Π½ ΠΎΡ Π½Π΅ΠΏΠΎΡΡΠ΅Π΄ΡΡΠ²Π΅Π½Π½ΠΎΠ³ΠΎ Π²ΠΎΠ·Π΄Π΅ΠΉΡΡΠ²ΠΈΡ ΠΏΠΎΡΠ°. ΠΠ»Ρ ΠΏΡΠΈΠΊΡΠ΅ΠΏΠ»Π΅Π½ΠΈΡ ΡΠ°Π½ΡΠ° ΠΏΡΠΈΠΌΠ΅Π½ΡΡΡ Ρ Π»ΠΎΠΏΡΠ°ΡΠΎΠ±ΡΠΌΠ°ΠΆΠ½ΡΠ΅ ΠΈ ΠΊΠ°ΠΏΡΠΎΠ½ΠΎΠ²ΡΠ΅ Π½ΠΈΡΠΊΠΈ. ΠΠΎΠΌΠ΅Ρ Π½ΠΈΡΠΊΠΈ Π΄ΠΎΠ»ΠΆΠ΅Π½ ΡΠΎΠΎΡΠ²Π΅ΡΡΡΠ²ΠΎΠ²Π°ΡΡ Π½ΠΎΠΌΠ΅ΡΡ ΠΈΠ³Π»Ρ, Π° ΠΏΡΠΈ ΠΏΡΠΈΠΊΡΠ΅ΠΏΠ»Π΅Π½ΠΈΠΈ ΡΠ°Π½ΡΠ° Π½Π° ΠΌΠ°ΡΠΈΠ½Π΅ ΠΊΠ». 201 ΠΎΠ΄Π½ΠΎΠ½ΠΈΡΠΎΡΠ½ΡΠΌ ΡΠ²ΠΎΠΌ — ΠΈ Π½ΠΎΠΌΠ΅ΡΡ ΡΠΈΠ»Π°. ΠΡΠΏΠΎΠ»ΡΠ·ΡΡΡ Ρ Π»ΠΎΠΏΡΠ°ΡΠΎΠ±ΡΠΌΠ°ΠΆΠ½ΡΠ΅ Π½ΠΈΡΠΊΠΈ № 1, 0 ΠΈ 00, ΠΊΠ°ΠΏΡΠΎΠ½ΠΎΠ²ΡΠ΅ № 3 ΠΈ 5 ΠΏΡΠΈ ΠΏΡΠΈΠΊΡΠ΅ΠΏΠ»Π΅Π½ΠΈΠΈ Π½Π° ΠΌΠ°ΡΠΈΠ½Π°Ρ ΠΊΠ». 23-Π ΠΈ 93, ΠΈΠ³Π»Ρ 0756 № 150, 170, 190 ΠΈ 210 ΠΈ ΠΊΠ°ΠΏΡΠΎΠ½ΠΎΠ²ΡΠ΅ Π½ΠΈΡΠΊΠΈ № 2; 1,8; 1,3 Π½Π° ΠΌΠ°ΡΠΈΠ½Π΅ ΠΊΠ». 201, ΠΈΠ³Π»Ρ 0890 № 175, 200 ΠΈ 224, ΡΠΈΠ»ΡΡ 0897 № 190, 210, 240. Π Π°Π½Ρ ΠΏΡΠΈΠΊΡΠ΅ΠΏΠ»ΡΡΡ Π½Π° ΠΌΠ°ΡΠΈΠ½Π°Ρ ΠΠΠ -1, 3 030/Π 2 ΠΎΠ΄Π½ΠΎΠ½ΠΈΡΠΎΡΠ½ΡΠΌ ΡΠ²ΠΎΠΌ Π½Π°ΡΡΠΆΠ½ΠΎΠ³ΠΎ ΠΏΠ΅ΡΠ΅ΠΏΠ»Π΅ΡΠ΅Π½ΠΈΡ, ΡΠ°ΡΠΏΠΎΠ»ΠΎΠΆΠ΅Π½Π½ΡΠΌ ΠΏΠ°ΡΠ°Π»Π»Π΅Π»ΡΠ½ΠΎ ΠΏΠΎΠ²Π΅ΡΡ Π½ΠΎΡΡΠΈ ΠΏΠΎΠ΄ΠΎΡΠ²Ρ, Π±Π»Π°Π³ΠΎΠ΄Π°ΡΡ ΡΠ΅ΠΌΡ ΠΏΡΠΈ ΠΈΠ·Π³ΠΈΠ±Π΅ ΠΎΠ±ΡΠ²ΠΈ Π½ΠΈΡΠΊΠΈ Π½Π΅ ΠΈΡΠΏΡΡΡΠ²Π°ΡΡ Π±ΠΎΠ»ΡΡΠΎΠ³ΠΎ Π½Π°ΠΏΡΡΠΆΠ΅Π½ΠΈΡ. Π’Π°ΠΊ ΠΊΠ°ΠΊ ΡΡΠ΅ΠΆΠΊΠΈ ΡΠ°ΡΠΏΠΎΠ»ΠΎΠΆΠ΅Π½Ρ ΠΌΠ΅ΠΆΠ΄Ρ ΠΏΠΎΠ΄ΠΎΡΠ²ΠΎΠΉ ΠΈ ΡΡΠ΅Π»ΡΠΊΠΎΠΉ, Π³ΠΈΠ³ΡΠΎΡΠ΅ΡΠΌΠΈΡΠ΅ΡΠΊΠΎΠ΅ Π²ΠΎΠ·Π΄Π΅ΠΉΡΡΠ²ΠΈΠ΅ Π½Π° Π½ΠΈΡΠΊΡ Π½Π΅Π²Π΅Π»ΠΈΠΊΠΎ, Π° ΠΎΡ Π½Π΅ΠΏΠΎΡΡΠ΅Π΄ΡΡΠ²Π΅Π½Π½ΠΎΠ³ΠΎ Π²ΠΎΠ·Π΄Π΅ΠΉΡΡΠ²ΠΈΡ ΠΏΠΎΡΠ° ΠΎΠ½Π° ΠΏΠΎΠ»Π½ΠΎΡΡΡΡ ΠΈΠ·ΠΎΠ»ΠΈΡΠΎΠ²Π°Π½Π°. ΠΠΎ ΡΠΊΠ°Π·Π°Π½Π½ΡΠΌ ΠΏΡΠΈΡΠΈΠ½Π°ΠΌ ΠΎΠ΄Π½ΠΎΠ½ΠΈΡΠΎΡΠ½ΡΠΉ ΡΠΎΠ², ΡΠΊΡΠ΅ΠΏΠ»ΡΡΡΠΈΠΉ ΡΠ°Π½Ρ ΡΠΎ ΡΡΠ΅Π»ΡΠΊΠΎΠΉ, Π½Π°Π΄Π΅ΠΆΠ΅Π½ ΠΈ ΡΠ°Π·ΡΡΡΠ°Π΅ΡΡΡ ΡΠ΅Π΄ΠΊΠΎ. ΠΠ°ΡΠΈΠ½Π° Π΄Π»Ρ ΠΏΡΠΈΠΊΡΠ΅ΠΏΠ»Π΅Π½ΠΈΡ ΡΠ°Π½ΡΠ° ΠΊ Π³ΡΠ±Π΅ ΡΡΠ΅Π»ΡΠΊΠΈ ΡΠ΅Π·ΠΊΠΎ ΠΎΡΠ»ΠΈΡΠ°Π΅ΡΡΡ ΠΎΡ ΠΏΡΠΎΡΠΈΠ²Π½ΠΎΠΉ ΠΌΠ°ΡΠΈΠ½Ρ. ΠΡΠΎ ΠΎΠ±ΡΡΡΠ½ΡΠ΅ΡΡΡ Π½Π΅ΠΎΠ±Ρ ΠΎΠ΄ΠΈΠΌΠΎΡΡΡΡ Π²ΡΠΈΠ²Π°ΡΡ ΡΠ°Π½Ρ ΠΊΡΠΈΠ²ΠΎΠ»ΠΈΠ½Π΅ΠΉΠ½ΠΎΠΉ ΠΈΠ³Π»ΠΎΠΉ. ΠΡΠΎΠΌΠ΅ ΡΠΎΠ³ΠΎ, Π΄Π»Ρ ΠΎΠ±Π΅ΡΠΏΠ΅ΡΠ΅Π½ΠΈΡ ΠΎΠΏΡΠ΅Π΄Π΅Π»Π΅Π½Π½ΠΎΠ³ΠΎ ΠΏΠΎΠ»ΠΎΠΆΠ΅Π½ΠΈΡ ΠΈΠ·Π΄Π΅Π»ΠΈΡ ΠΏΡΠΈΠ²ΡΠΈΠ²Π°Π½ΠΈΠΈ ΡΠ°Π½ΡΠ° (ΡΠΈΠ»Ρ, ΠΏΡΠΈΠ»Π°Π³Π°Π΅ΠΌΡΠ΅ Π΄Π»Ρ ΠΏΡΠΎΠΊΠ°Π»ΡΠ²Π°Π½ΠΈΡ ΠΌΠ°ΡΠ΅ΡΠΈΠ°Π»Π° ΠΈΠ³Π»ΠΎΠΉ ΠΈ ΠΏΡΠΎΡΠ°ΡΠΊΠΈΠ²Π°Π½ΠΈΡ Π½ΠΈΡΠΎΠΊ, ΡΠ°ΡΠΏΠΎΠ»Π°Π³Π°ΡΡΡΡ Π² ΠΏΠ»ΠΎΡΠΊΠΎΡΡΠΈ, ΠΏΡΠΈΠΌΠ΅ΡΠ½ΠΎ ΡΠΎΠ²ΠΏΠ°Π΄Π°ΡΡΠ΅ΠΉ Ρ ΠΏΠ»ΠΎΡΠΊΠΎΡΡΡΡ ΡΠ»Π΅Π΄Π° ΠΎΠ±ΡΠ²ΠΈ) ΠΌΠ°ΡΠΈΠ½Π° ΠΈΠΌΠ΅Π΅Ρ ΡΠ»ΠΎΠΆΠ½ΡΠ΅ ΡΠΏΠΎΡΠ½ΡΠ΅ ΠΌΠ΅Ρ Π°Π½ΠΈΠ·ΠΌΡ.
Π ΠΈΡΡΠ½ΠΎΠΊ 3. ΠΡΠΏΠΎΠ»Π½ΠΈΡΠ΅Π»ΡΠ½ΡΠ΅ ΠΎΡΠ³Π°Π½Ρ ΡΠ°Π½ΡΠΎΠ²ΡΠΈΠ²Π½ΠΎΠΉ ΠΌΠ°ΡΠΈΠ½Ρ Π ΠΈΡΡΠ½ΠΎΠΊ 4. Π‘Ρ Π΅ΠΌΠ° ΠΈΠ³Π»Ρ (Π°) Π΄Π»Ρ ΡΠ°Π½ΡΠΎΠ²ΡΠΈΠ²Π½ΠΎΠΉ ΠΌΠ°ΡΠΈΠ½Ρ ΠΈ ΡΠΎΡΠΌΡ Π·Π°ΡΠΎΡΠΊΠΈ ΠΎΡΡΡΠΈΡ (Π±, Π²) ΠΠ³Π»Π° 1(ΡΠΈΡ. 3) Π΄ΠΎΠ»ΠΆΠ½Π° ΠΏΡΠΎΠΊΠΎΠ»ΠΎΡΡ ΡΠ°Π½Ρ 2 ΠΏΠΎ ΠΆΠ΅Π»ΠΎΠ±ΠΊΡ 3, ΠΏΡΠΎΠΉΡΠΈ Π² ΠΎΡΠ½ΠΎΠ²Π°Π½ΠΈΠ΅ Π³ΡΠ±Ρ ΠΈ, Π²ΡΠΉΠ΄Ρ ΠΈΠ· Π½Π΅Π΅, ΠΎΡΡΠ°Π½ΠΎΠ²ΠΈΡΡΡΡ. Π ΠΌΠΎΠΌΠ΅Π½Ρ ΠΎΡΡΠ°Π½ΠΎΠ²Π° Π½ΠΈΡΠ΅Π½Π°Π±ΡΠ°ΡΡΠ²Π°ΡΠ΅Π»Ρ4 ΠΎΠ±Π²ΠΎΠ΄ΠΈΡ Π½ΠΈΡΠΊΡ Π²ΠΎΠΊΡΡΠ³ ΠΊΠΎΠ½ΡΠ° ΠΈΠ³Π»Ρ. Π ΡΡΠΎ Π²ΡΠ΅ΠΌΡ ΠΊΡΡΡΠΎΠΊ ΠΎΡΡΡΠ³ΠΈΠ²Π°Π΅Ρ Π½ΠΈΡΠΊΡ Π΄Π»Ρ Π·Π°Ρ Π²Π°ΡΠ° Π΅Π΅ ΠΈΠ³Π»ΠΎΠΉ. ΠΡΠΈ ΠΎΠ±ΡΠ°ΡΠ½ΠΎΠΌ Π΄Π²ΠΈΠΆΠ΅Π½ΠΈΠΈ ΠΈΠ³Π»Π° Π²ΡΡΠ°ΡΠΊΠΈΠ²Π°Π΅Ρ ΠΈΠ· ΠΏΡΠΎΠΊΠΎΠ»Π° Π½Π°ΠΊΠΈΠ½ΡΡΡΡ Π½Π° Π½Π΅Π΅ Π½ΠΈΡΠΊΡ. ΠΠ±ΡΠ°Π·ΠΎΠ²Π°Π½Π½Π°Ρ ΡΠ°ΠΊΠΈΠΌ ΠΎΠ±ΡΠ°Π·ΠΎΠΌ ΠΏΠ΅ΡΠ»Ρ ΡΠΊΠ»Π°Π΄ΡΠ²Π°Π΅ΡΡΡ Π² ΠΆΠ΅Π»ΠΎΠ±ΠΎΠΊ ΡΠ°Π½ΡΠ° ΠΏΡΠΈ ΠΏΠΎΠ΄Π°ΡΠ΅ ΠΎΠ±ΡΠ²ΠΈ ΡΡΠ°Π½ΡΠΏΠΎΡΡΠ΅ΡΠΎΠΌ ΠΈ ΠΏΡΠΈ ΠΎΠ±ΡΠ°ΡΠ½ΠΎΠΌ Π΄Π²ΠΈΠΆΠ΅Π½ΠΈΠΈ ΠΈΠ³Π»Ρ, ΠΊΠ°ΠΊ ΡΡΠΎ Π΄Π΅Π»Π°Π΅ΡΡΡ Π½Π° ΠΏΡΠΎΡΠΈΠ²Π½ΠΎΠΉ ΠΌΠ°ΡΠΈΠ½Π΅. ΠΠ°ΡΡΠΆΠ΅Π½ΠΈΠ΅ Π½ΠΈΡΠΊΠΈ ΠΎΡΡΡΠ΅ΡΡΠ²Π»ΡΠ΅ΡΡΡ ΡΠΈΡΡΠ΅ΠΌΠΎΠΉ ΡΠΎΠ»ΠΈΠΊΠΎΠ² (ΡΡΡΠ³ΠΈΠ²Π°ΡΠ΅Π»Π΅ΠΉ), ΠΏΠΎΠ΄Π°ΡΡΠΈΡ Π½ΠΈΡΠΊΡ Π½Π° ΠΈΠ³Π»Ρ ΠΈ Π½Π°ΡΡΠ³ΠΈΠ²Π°ΡΡΠΈΡ Π΅Π΅ Π² ΠΌΠΎΠΌΠ΅Π½Ρ ΠΎΠ±ΡΠ°Π·ΠΎΠ²Π°Π½ΠΈΡ ΡΡΠ΅ΠΆΠΊΠ°. Π£ΡΡΠΆΠΊΠ° ΡΠ΅Π³ΡΠ»ΠΈΡΡΠ΅ΡΡΡ ΡΠΎΡΠΌΠΎΠ·Π½ΡΠΌΠΈ ΡΠΎΠ»ΠΈΠΊΠ°ΠΌΠΈ, ΠΏΠΎ ΠΊΠΎΡΠΎΡΡΠΌ ΠΏΡΠΎΡ ΠΎΠ΄ΠΈΡ Π½ΠΈΡΠΊΠ°, ΠΏΡΠΎΠΏΠΈΡΠ°Π½Π½Π°Ρ Π²Π°ΡΠΎΠΌ.
ΠΠΈΡΠΊΡ ΠΏΡΠΎΠΏΠΈΡΡΠ²Π°ΡΡ Π²Π°ΡΠΎΠΌ Π΄Π»Ρ ΡΠΎΠ³ΠΎ, ΡΡΠΎΠ±Ρ ΠΏΡΠ΅Π΄ΠΎΡ ΡΠ°Π½ΠΈΡΡ Π΅Π΅ ΠΎΡ ΡΠ°Π·Π»ΠΎΠΆΠ΅Π½ΠΈΡ ΠΏΠΎΠ΄ Π΄Π΅ΠΉΡΡΠ²ΠΈΠ΅ΠΌ ΠΏΠΎΡΠ° ΠΈ Π³ΠΈΠ³ΡΠΎΡΠ΅ΡΠΌΠΈΡΠ΅ΡΠΊΠΈΡ Π²ΠΎΠ·Π΄Π΅ΠΉΡΡΠ²ΠΈΠΉ ΠΎΠΊΡΡΠΆΠ°ΡΡΠ΅ΠΉ ΡΡΠ΅Π΄Ρ, Π° ΡΠ°ΠΊΠΆΠ΅ ΡΠ²Π΅Π»ΠΈΡΠΈΡΡ ΡΡΠ΅ΠΏΠ»Π΅Π½ΠΈΠ΅ (Π°Π΄Π³Π΅Π·ΠΈΡ) Π½ΠΈΡΠΊΠΈ Ρ ΠΏΠΎΠ²Π΅ΡΡ Π½ΠΎΡΡΡΡ ΠΎΡΠ²Π΅ΡΡΡΠΈΡ Π² ΠΌΠ°ΡΠ΅ΡΠΈΠ°Π»Π΅.
ΠΠ° ΠΊΠ°ΡΠ΅ΡΡΠ²ΠΎ ΠΊΡΠ΅ΠΏΠ»Π΅Π½ΠΈΡ ΡΠ°Π½ΡΠ° Π²Π»ΠΈΡΡΡ ΡΠ°Π·ΠΌΠ΅Ρ ΠΈ Π·Π°ΡΠΎΡΠΊΠ° ΠΈΠ³Π»Ρ, ΠΏΡΠΎΡΠ½ΠΎΡΡΡ Π½ΠΈΡΠΊΠΈ ΠΈ ΡΠΎΡΡΠ°Π² ΠΏΡΠΎΠΏΠΈΡΠΊΠΈ, ΡΡΡΠΆΠΊΠ° ΠΈ ΡΠ°Π³ ΡΡΠ΅ΠΆΠΊΠ°, ΡΠ²ΠΎΠΉΡΡΠ²Π° ΡΠΊΡΠ΅ΠΏΠ»ΡΠ΅ΠΌΡΡ ΠΌΠ°ΡΠ΅ΡΠΈΠ°Π»ΠΎΠ². ΠΠΎΠΌΠ΅Ρ ΠΈΠ³Π»Ρ Π·Π°Π²ΠΈΡΠΈΡ ΠΎΡ Π΄ΠΈΠ°ΠΌΠ΅ΡΡΠ° ΠΈ ΡΠ°Π·ΠΌΠ΅ΡΠ° ΠΊΡΡΡΠΊΠ° ΠΎΠΊΠΎΠ»ΠΎ ΠΎΡΡΡΠΈΡ (ΡΠΈΡ. 4).
ΠΠ»Ρ Π²ΡΠΈΠ²Π°Π½ΠΈΡ ΡΠ°Π½ΡΠ° ΠΏΡΠΈΠΌΠ΅Π½ΡΡΡ Π»ΡΠ½ΡΠ½ΡΠ΅ ΠΈ ΠΊΠ°ΠΏΡΠΎΠ½ΠΎΠ²ΡΠ΅ Π½ΠΈΡΠΊΠΈ. ΠΠΎΠΌΠ΅Ρ Π½ΠΈΡΠΊΠΈ Π²ΡΠ±ΠΈΡΠ°ΡΡ Π² ΡΠΎΠΎΡΠ²Π΅ΡΡΡΠ²ΠΈΠΈ Ρ Π½ΠΎΠΌΠ΅ΡΠΎΠΌ ΠΈΠ³Π»Ρ. Π¨Π°Π³ ΡΡΠ΅ΠΆΠΊΠ° ΡΠ°Π²Π΅Π½ 6— 7 ΠΌΠΌ.
ΠΡΠΈΠΊΡΠ΅ΠΏΠ»Π΅Π½ΠΈΠ΅ ΠΏΠΎΠ΄ΠΎΡΠ² ΠΊ ΡΠ°Π½ΡΡ. ΠΠ°ΡΠΈΠ½Π° Π΄Π»Ρ ΠΏΡΠΈΡΠΈΠ²Π°Π½ΠΈΡ ΠΏΠΎΠ΄ΠΎΡΠ²Ρ ΠΊ ΡΠ°Π½ΡΡ ΠΈΠ»ΠΈ Π·Π°ΡΡΠΆΠ½ΠΎΠΉ ΠΊΡΠΎΠΌΠΊΠ΅ Π·Π°Π³ΠΎΡΠΎΠ²ΠΊΠΈ Π²Π΅ΡΡ Π° Π² ΠΎΡΠ»ΠΈΡΠΈΠ΅ ΠΎΡ Π΄ΡΡΠ³ΠΈΡ ΠΌΠ°ΡΠΈΠ½ Π΄Π»Ρ ΠΏΡΠΈΠΊΡΠ΅ΠΏΠ»Π΅Π½ΠΈΡ ΠΏΠΎΠ΄ΠΎΡΠ²Ρ Π½Π΅ ΠΈΠΌΠ΅Π΅Ρ ΡΠΎΠ³Π°-ΡΠΏΠΎΡΠ°. ΠΠ±ΡΠ²Ρ ΡΡΡΠ°Π½Π°Π²Π»ΠΈΠ²Π°ΡΡ ΡΠ°ΠΊ, ΡΡΠΎΠ±Ρ ΡΠ°Π½Ρ ΠΏΠΎΠΌΠ΅ΡΠ°Π»ΡΡ Π½Π° ΡΡΠΎΠ»ΠΈΠΊΠ΅ 6 ΠΌΠ°ΡΠΈΠ½Ρ (ΡΠΈΡ.5), ΠΊΠΎΡΠΎΡΡΠΉ ΡΠ»ΡΠΆΠΈΡ ΡΠ°ΠΊΠΆΠ΅ ΡΠΏΠΎΡΠΎΠΌ. ΠΠΎΠ΄ΠΎΡΠ²Π° ΠΈ ΡΠ°Π½Ρ ΠΏΡΠΈΠΆΠΈΠΌΠ°ΡΡΡΡ ΠΊ ΡΡΠΎΠ»ΠΈΠΊΡ 6 Π»Π°ΠΏΠΊΠΎΠΉ 4, ΠΊΠΎΡΠΎΡΠ°Ρ ΠΏΡΠ΅ΡΡΡΠ΅Ρ ΠΈ Π΄Π°Π΅Ρ Π²ΠΎΠ·ΠΌΠΎΠΆΠ½ΠΎΡΡΡ ΠΏΡΠΎΠΊΠ°Π»ΡΠ²Π°ΡΡ Π΄Π΅ΡΠ°Π»ΠΈ ΡΠΈΠ»ΠΎΠΌ8 ΡΠΎ ΡΡΠΎΡΠΎΠ½Ρ ΡΠ°Π½ΡΠ°. ΠΠ°ΡΠ΅ΡΠΈΠ°Π» ΡΡΠ°Π½ΡΠΏΠΎΡΡΠΈΡΡΠ΅ΡΡΡ ΡΠ΅ΠΌ ΠΆΠ΅ ΡΠΈΠ»ΠΎΠΌ, ΠΊΠΎΡΠΎΡΠΎΠ΅ ΠΌΠΎΠΆΠ΅Ρ ΠΏΠ΅ΡΠ΅ΠΌΠ΅ΡΠ°ΡΡΡΡ Π½Π° ΠΎΠΏΡΠ΅Π΄Π΅Π»Π΅Π½Π½ΡΠΉ ΡΠ°Π³, ΠΈΠ·ΠΌΠ΅Π½ΡΠ΅ΠΌΡΠΉ ΠΏΡΠΈ Π½Π°ΡΡΡΠΎΠΉΠΊΠ΅ ΠΌΠ΅Ρ Π°Π½ΠΈΠ·ΠΌΠ° ΡΠΈΠ»Π°. ΠΠΎ Π²ΡΠ΅ΠΌΡ ΡΡΠ°Π½ΡΠΏΠΎΡΡΠΈΡΠΎΠ²Π°Π½ΠΈΡ Π»Π°ΠΏΠΊΠ° ΠΏΡΠΈΠΏΠΎΠ΄Π½ΠΈΠΌΠ°Π΅ΡΡΡ ΠΈ ΠΎΡΠ²ΠΎΠ±ΠΎΠΆΠ΄Π°Π΅Ρ ΠΌΠ°ΡΠ΅ΡΠΈΠ°Π».
Π ΠΈΡΡΠ½ΠΎΠΊ 5. ΠΡΠΏΠΎΠ»Π½ΠΈΡΠ΅Π»ΡΠ½ΡΠ΅ ΠΎΡΠ³Π°Π½Ρ ΠΌΠ°ΡΠΈΠ½Ρ Π΄Π»Ρ ΠΏΡΠΈΡΡΡΠ°ΡΠΈΠ²Π°Π½ΠΈΡ ΠΏΠΎΠ΄ΠΎΡΠ² ΠΊ ΡΠ°Π½ΡΡ Π¨ΠΈΠ»ΠΎ ΠΏΠΎΠ΄Π°Π΅Ρ ΠΏΡΠΎΠΊΠΎΠ»ΠΎΡΡΡ ΡΠ°ΡΡΡ ΠΏΠΎΠ΄ΠΎΡΠ²Ρ ΠΏΠΎΠ΄ ΠΈΠ³Π»Ρ 5, ΠΊΠΎΡΠΎΡΠ°Ρ ΠΏΠ΅ΡΠ΅ΠΌΠ΅ΡΠ°Π΅ΡΡΡ Π½Π°Π²ΡΡΡΠ΅ΡΡ Π΄Π²ΠΈΠΆΠ΅Π½ΠΈΡ (ΠΊΠ°ΡΠ°Π½ΠΈΡ) ΡΠΈΠ»Π°. ΠΠΎΡΠ»Π΅ Π²ΡΡ ΠΎΠ΄Π° ΡΠΈΠ»Π° ΠΈΠ³Π»Π° Π²Ρ ΠΎΠ΄ΠΈΡ Π² ΠΎΠ±ΡΠ°Π·ΠΎΠ²Π°Π½Π½ΠΎΠ΅ ΠΈΠΌ ΠΎΡΠ²Π΅ΡΡΡΠΈΠ΅. ΠΠ° ΠΈΠ³Π»Ρ 5, ΠΎΡΡΠ°Π½ΠΎΠ²ΠΈΠ²ΡΡΡΡΡ Π² Π½ΠΈΠΆΠ½Π΅ΠΌ ΠΏΠΎΠ»ΠΎΠΆΠ΅Π½ΠΈΠΈ, Π½Π°ΠΊΠΈΠ΄ΡΠ²Π°Π΅ΡΡΡ Π½ΠΈΡΠΊΠ° Π½ΠΈΡΠ΅Π½Π°Π±ΡΠ°ΡΡΠ²Π°ΡΠ΅Π»Π΅ΠΌ9, Π½Π° ΠΊΠΎΡΠΎΡΡΠΉ Π΅Π΅ Π½Π°Π±ΡΠ°ΡΡΠ²Π°Π΅Ρ Π½ΠΈΠΆΠ½ΠΈΠΉ ΠΊΡΡΡΠΎΠΊ 7. ΠΡΠΈ Π΄Π²ΠΈΠΆΠ΅Π½ΠΈΠΈ Π²Π²Π΅ΡΡ ΠΈΠ³Π»Π° ΠΏΡΠΎΡΠ°ΡΠΊΠΈΠ²Π°Π΅Ρ ΡΠ΅ΡΠ΅Π· ΠΎΡΠ²Π΅ΡΡΡΠΈΠ΅ Π½ΠΈΡΠΎΡΠ½ΡΡ ΠΏΠ΅ΡΠ»Ρ, ΠΊΠΎΡΠΎΡΠ°Ρ Π·Π°ΡΠ΅ΠΌ ΡΠ°ΡΡΠΈΡΡΠ΅ΡΡΡ Π²Π΅ΡΡ Π½ΠΈΠΌ ΠΊΡΡΡΠΊΠΎΠΌ 1 ΠΈ Π·Π°Ρ Π²Π°ΡΡΠ²Π°Π΅ΡΡΡ Π½ΠΎΡΠΈΠΊΠΎΠΌ ΡΠ΅Π»Π½ΠΎΠΊΠ° 2. Π§Π΅Π»Π½ΠΎΠΊ, Π²ΡΠ°ΡΠ°ΡΡΡ, ΠΏΠ΅ΡΠ΅ΠΊΠΈΠ΄ΡΠ²Π°Π΅Ρ Π½ΠΈΡΠΊΡ ΡΠ΅ΡΠ΅Π· ΡΠ΅Π±Ρ ΠΈ ΡΠ΅ΡΠ΅Π· ΡΠΏΡΠ»Ρ 3 ΡΠ΅Π»Π½ΠΎΠΊΠ°. ΠΠΎΡΠ»Π΅ ΡΡΠΎΠ³ΠΎ ΠΏΠ΅ΡΠ»Ρ ΠΏΡΠΎΡΡΠ³ΠΈΠ²Π°Π΅ΡΡΡ ΡΠΊΠ²ΠΎΠ·Ρ ΠΎΡΠ²Π΅ΡΡΡΠΈΠ΅ Π² ΠΏΠΎΠ΄ΠΎΡΠ²Π΅ ΠΈ Π²ΡΡΡΠ³ΠΈΠ²Π°Π΅Ρ Π½ΠΈΡΠΊΡ ΠΈΠ· ΡΠΏΡΠ»ΠΈ.
ΠΠ΅ΡΠ΅ΠΏΠ»Π΅ΡΠ΅Π½ΠΈΠ΅ Π΄Π²ΡΡ Π½ΠΈΡΠΎΠΊ Π² ΠΌΠ°ΡΠ΅ΡΠΈΠ°Π»Π΅ Ρ Π°ΡΠ°ΠΊΡΠ΅ΡΠ½ΠΎ Π΄Π»Ρ ΠΎΠΏΠΈΡΡΠ²Π°Π΅ΠΌΠΎΠ³ΠΎ ΠΌΠ΅ΡΠΎΠ΄Π°.
ΠΠ° ΠΌΠ°ΡΠΈΠ½Π°Ρ Π΄Π»Ρ ΠΏΡΠΈΠΊΡΠ΅ΠΏΠ»Π΅Π½ΠΈΡ ΠΏΠΎΠ΄ΠΎΡΠ² ΡΡΠ΅ΠΆΠΊΠΎΠΌ Π²Π½ΡΡΡΠ΅Π½Π½Π΅Π³ΠΎ ΠΏΠ΅ΡΠ΅ΠΏΠ»Π΅ΡΠ΅Π½ΠΈΡ ΠΏΡΠΈΠΌΠ΅Π½ΡΡΡ ΡΠΈΠ»ΡΡ ΡΠΈΠΏΠ° 7 ΠΌΠΎΠ΄Π΅Π»Π΅ΠΉ 0898, 0899, 0900 № 140, 155, 165, 180 (ΡΠ°Π·ΠΌΠ΅Ρ ΡΡΠΎΡΠΎΠ½Ρ, ΡΠΌΠ½ΠΎΠΆΠ΅Π½Π½ΡΠΉ Π½Π° 100). Π Π°Π΄ΠΈΡΡ ΠΊΡΠΈΠ²ΠΈΠ·Π½Ρ ΠΌΠΎΠ΄Π΅Π»Π΅ΠΉ ΡΠΈΠ»ΡΠ΅Π² 0898, 0899 ΡΠ°Π²Π΅Π½ 34 ΠΌΠΌ, Π° ΡΠΈΠ»ΡΠ΅Π² ΠΌΠΎΠ΄Π΅Π»ΠΈ 0900 — 25,4 ΠΌΠΌ. Π‘Π΅ΡΠ΅Π½ΠΈΠ΅ ΡΠΈΠ»Π° ΠΊΠ²Π°Π΄ΡΠ°ΡΠ½ΠΎΠ΅, Π±Π»Π°Π³ΠΎΠ΄Π°ΡΡ ΡΠ΅ΠΌΡ ΠΎΠ±Π»Π΅Π³ΡΠ°Π΅ΡΡΡ ΠΏΡΠΎΠΊΠ°Π»ΡΠ²Π°Π½ΠΈΠ΅ ΠΌΠ°ΡΠ΅ΡΠΈΠ°Π»Π° ΠΈ ΠΎΠ±Π΅ΡΠΏΠ΅ΡΠΈΠ²Π°Π΅ΡΡΡ Π±ΠΎΠ»Π΅Π΅ ΡΠΎΡΠ½ΠΎΠ΅ ΡΠΊΠ»Π°Π΄ΡΠ²Π°Π½ΠΈΠ΅ ΡΡΠ΅ΠΆΠΊΠΎΠ².
ΠΡΠΏΠΎΠ»ΡΠ·ΡΡΡΡΡ ΠΈΠ³Π»Ρ ΡΠΈΠΏΠ° 8 ΠΌΠΎΠ΄Π΅Π»Π΅ΠΉ 0904 ΠΈ 0905. Π Π°Π΄ΠΈΡΡ ΠΊΡΠΈΠ²ΠΈΠ·Π½Ρ ΠΈΠ³Π» ΠΌΠΎΠ΄Π΅Π»ΠΈ 0904 ΡΠ°Π²Π΅Π½ 34 ΠΌΠΌ, ΠΌΠΎΠ΄Π΅Π»ΠΈ 0905 — 25,4 ΠΌΠΌ; № 164, 175, 200, 210, 224.
ΠΡΠΎΡΠ½ΠΎΡΡΡ ΠΊΡΠ΅ΠΏΠ»Π΅Π½ΠΈΡ ΠΏΠΎΠ΄ΠΎΡΠ²Ρ Π·Π°Π²ΠΈΡΠΈΡ ΠΎΡ ΠΏΡΠ°Π²ΠΈΠ»ΡΠ½ΠΎΠ³ΠΎ ΡΠΎΠΎΡΠ½ΠΎΡΠ΅Π½ΠΈΡ Π½ΠΎΠΌΠ΅ΡΠΎΠ² ΡΠΈΠ»Π° ΠΈ ΠΈΠ³Π»Ρ, Π° ΡΠ°ΠΊΠΆΠ΅ ΠΎΡ ΡΠΎΠ»ΡΠΈΠ½Ρ Π½ΠΈΡΠΎΠΊ. Π¨ΠΈΠ»ΡΡ ΠΈ ΠΈΠ³Π»Ρ Π±ΠΎΠ»ΡΡΠΈΡ Π½ΠΎΠΌΠ΅ΡΠΎΠ² ΠΎΡΠ»Π°Π±Π»ΡΡΡ ΡΠΊΡΠ΅ΠΏΠ»ΡΠ΅ΠΌΡΠ΅ Π΄Π΅ΡΠ°Π»ΠΈ, ΡΡΠΎ ΡΠ½ΠΈΠΆΠ°Π΅Ρ ΠΏΡΠΎΡΠ½ΠΎΡΡΡ ΠΊΡΠ΅ΠΏΠ»Π΅Π½ΠΈΡ. ΠΠΈΡΠΊΠ° Π½Π΅ Π·Π°ΠΏΠΎΠ»Π½ΡΠ΅Ρ ΠΏΡΠΎΠΊΠΎΠ»Π°, ΠΏΠΎΡΡΠΎΠΌΡ Π±ΡΡΡΡΠΎ ΠΏΠ΅ΡΠ΅ΡΠΈΡΠ°Π΅ΡΡΡ. ΠΠ΅Π½ΡΡΠΈΠ΅ Π½ΠΎΠΌΠ΅ΡΠ° ΡΠΈΠ»Π° ΠΈ ΠΈΠ³Π»Ρ ΠΎΡΠ»Π°Π±Π»ΡΡΡ ΠΏΡΠΎΡΠ½ΠΎΡΡΡ Π½ΠΈΡΠΎΠΊ Π² ΡΠ΅Π·ΡΠ»ΡΡΠ°ΡΠ΅ ΡΠ²Π΅Π»ΠΈΡΠ΅Π½ΠΈΡ ΡΡΠ΅Π½ΠΈΡ ΠΎ ΡΡΠ΅Π½ΠΊΠΈ ΠΏΡΠΎΠΊΠΎΠ»Π° ΠΈ, ΡΠ»Π΅Π΄ΠΎΠ²Π°ΡΠ΅Π»ΡΠ½ΠΎ, ΠΎΡΠ»Π°Π±Π»Π΅Π½ΠΈΡ ΡΠ°ΠΌΠΎΠ³ΠΎ ΠΊΡΠ΅ΠΏΠ»Π΅Π½ΠΈΡ. Π¨ΠΈΠ»ΠΎ ΠΏΠΎΠ΄Π±ΠΈΡΠ°ΡΡ ΡΠ°ΠΊΠΈΠΌ ΠΎΠ±ΡΠ°Π·ΠΎΠΌ, ΡΡΠΎΠ±Ρ ΠΏΠ»ΠΎΡΠ°Π΄Ρ Π΅Π³ΠΎ ΠΏΠΎΠΏΠ΅ΡΠ΅ΡΠ½ΠΎΠ³ΠΎ ΡΠ΅ΡΠ΅Π½ΠΈΡ Π±ΡΠ»Π° Π½Π΅ΡΠΊΠΎΠ»ΡΠΊΠΎ ΠΌΠ΅Π½ΡΡΠ΅ ΠΏΠ»ΠΎΡΠ°Π΄ΠΈ ΠΏΠΎΠΏΠ΅ΡΠ΅ΡΠ½ΠΎΠ³ΠΎ ΡΠ΅ΡΠ΅Π½ΠΈΡ ΠΈΠ³Π»Ρ.
ΠΠ΅Π½Π°ΡΡΡΠ΅Π½Π½ΡΠΉ (ΠΏΠ΅ΡΠ²Π°Ρ ΡΡΠ°Π΄ΠΈΡ Π½ΠΎΡΠΊΠΈ) Π΄Π²ΡΡ Π½ΠΈΡΠΎΡΠ½ΡΠΉ ΡΠΎΠ² Π²Π½ΡΡΡΠ΅Π½Π½Π΅Π³ΠΎ ΠΏΠ΅ΡΠ΅ΠΏΠ»Π΅ΡΠ΅Π½ΠΈΡ ΠΈΠΌΠ΅Π΅Ρ Π²ΡΡΠΎΠΊΠΎΠ΅ ΡΠΎΠΏΡΠΎΡΠΈΠ²Π»Π΅Π½ΠΈΠ΅ ΠΎΡΡΡΠ²Ρ ΠΏΠΎΠ΄ΠΎΡΠ²Ρ, Π² ΠΎΡΠ½ΠΎΠ²Π½ΠΎΠΌ Π·Π°Π²ΠΈΡΡΡΠ΅Π΅ ΠΎΡ ΡΠΎΠ»ΡΠΈΠ½Ρ ΠΈ Π²ΠΈΠ΄Π° ΠΌΠ°ΡΠ΅ΡΠΈΠ°Π»ΠΎΠ² ΠΏΠΎΠ΄ΠΎΡΠ²Ρ ΠΈ ΡΠ°Π½ΡΠ°, ΠΎΡ ΡΠΎΠΎΡΠ½ΠΎΡΠ΅Π½ΠΈΡ Π½ΠΎΠΌΠ΅ΡΠΎΠ² ΡΠΈΠ»Π°, ΠΈΠ³Π»Ρ ΠΈ Π½ΠΈΡΠΊΠΈ. ΠΠ°ΠΈΠ±ΠΎΠ»ΡΡΠ΅Π΅ Π²Π»ΠΈΡΠ½ΠΈΠ΅ Π½Π° ΡΠΎΠΏΡΠΎΡΠΈΠ²Π»Π΅Π½ΠΈΠ΅ ΠΎΡΡΡΠ²Ρ ΠΏΠΎΠ΄ΠΎΡΠ²Ρ ΠΏΡΠΈ Π½Π΅Π½Π°ΡΡΡΠ΅Π½Π½ΠΎΠΌ ΡΡΠ΅ΠΆΠΊΠ΅ ΠΎΠΊΠ°Π·ΡΠ²Π°ΡΡ ΡΠ²ΠΎΠΉΡΡΠ²Π° ΠΌΠ°ΡΠ΅ΡΠΈΠ°Π»Π° ΠΏΠΎΠ΄ΠΎΡΠ²Ρ.
Π£Π·Π΅Π» ΠΏΠ΅ΡΠ΅ΠΏΠ»Π΅ΡΠ΅Π½ΠΈΡ Π½ΠΈΡΠΎΠΊ Π΄ΠΎΠ»ΠΆΠ΅Π½ Π»Π΅ΠΆΠ°ΡΡ Π½Π° ΡΠ°ΡΡΡΠΎΡΠ½ΠΈΠΈ ΡΠΎΠ»ΡΠΈΠ½Ρ ΠΎΡ Ρ ΠΎΠ΄ΠΎΠ²ΠΎΠΉ ΡΡΠΎΡΠΎΠ½Ρ ΠΏΠΎΠ΄ΠΎΡΠ²Ρ. ΠΡΠ΅Π½Ρ Π²Π°ΠΆΠ½ΠΎ, ΡΡΠΎΠ±Ρ ΠΏΠΎΠ΄ΠΎΡΠ²Π° ΠΈ ΡΠ°Π½Ρ Π±ΡΠ»ΠΈ ΠΏΠ»ΠΎΡΠ½ΠΎ ΠΏΡΠΈΡΡΠ½ΡΡΡ Π΄ΡΡΠ³ ΠΊ Π΄ΡΡΠ³Ρ ΠΈ Π²ΠΎ Π²ΡΠ΅ΠΌΡ Π½ΠΎΡΠΊΠΈ ΠΎΠ±ΡΠ²ΠΈ ΠΌΠ΅ΠΆΠ΄Ρ Π½ΠΈΠΌΠΈ Π½Π΅ Π²ΠΎΠ·Π½ΠΈΠΊΠ°Π» ΡΠ΄Π²ΠΈΠ³, ΡΡΠΎ Π΄ΠΎΡΡΠΈΠ³Π°Π΅ΡΡΡ Π½Π°ΡΡΠΆΠ΅Π½ΠΈΠ΅ΠΌ Π½ΠΈΡΠΊΠΈ ΠΏΡΠΈ ΠΎΠ±ΡΠ°Π·ΠΎΠ²Π°Π½ΠΈΠΈ ΡΡΠ΅ΠΆΠΊΠ° ΡΠΎΠ»ΠΈΠΊΠ°ΠΌΠΈ. ΠΠΈΡΠΊΠ°, ΠΊΠΎΡΠΎΡΠ°Ρ ΡΠ°ΡΠΏΠΎΠ»Π°Π³Π°Π΅ΡΡΡ Π½Π° ΡΠ°Π½ΡΠ΅ (Π²Π΅ΡΡ Π½ΡΡ), ΠΏΡΠΎΠΏΠΈΡΡΠ²Π°Π΅ΡΡΡ Π±Π΅ΡΡΠ²Π΅ΡΠ½ΡΠΌ ΠΊΠ»Π΅ΡΡΠΈΠΌ Π²Π΅ΡΠ΅ΡΡΠ²ΠΎΠΌ, Π° Π½ΠΈΡΠΊΠ°, ΡΠ°ΡΠΏΠΎΠ»ΠΎΠΆΠ΅Π½Π½Π°Ρ Π½Π° ΠΏΠΎΠ΄ΠΎΡΠ²Π΅ (Π½ΠΈΠΆΠ½ΡΡ), — ΡΠ°ΡΠΏΠ»Π°Π²Π»Π΅Π½Π½ΡΠΌ Π²Π°ΡΠΎΠΌ. ΠΡΠΎ Π΄Π΅Π»Π°Π΅ΡΡΡ ΠΏΠΎΡΠΎΠΌΡ, ΡΡΠΎ ΡΡΡΠΎΡΠΊΠ° ΡΠΎ ΡΡΠΎΡΠΎΠ½Ρ ΡΠ°Π½ΡΠ° ΡΠ»ΡΠΆΠΈΡ ΡΠΊΡΠ°ΡΠ΅Π½ΠΈΠ΅ΠΌ, Π° ΠΏΡΠΎΠΏΠΈΡΠ°Π½Π½ΡΡ Π²Π°ΡΠΎΠΌ Π½ΠΈΡΠΊΡ Π½Π΅Π»ΡΠ·Ρ ΠΎΠΊΡΠ°ΡΠΈΡΡ Π² ΡΠ²Π΅ΡΠ»ΡΠ΅ ΡΠΎΠ½Π°. ΠΡΠΎΠΌΠ΅ ΡΠΎΠ³ΠΎ, ΡΡΠ΅ΠΊΠ°ΡΡΠΈΠΉ Ρ Π½ΠΈΡΠΊΠΈ ΡΠ°ΡΠΏΠ»Π°Π²Π»Π΅Π½Π½ΡΠΉ Π²Π°Ρ Π·Π°Π³ΡΡΠ·Π½ΡΠ΅Ρ ΠΌΠ°ΡΠΈΠ½Ρ. ΠΠ»Ρ ΠΏΠΎΠ΄Π΄Π΅ΡΠΆΠ°Π½ΠΈΡ Π²Π°ΡΠ° Π² ΡΠ°ΡΠΏΠ»Π°Π²Π»Π΅Π½Π½ΠΎΠΌ ΡΠΎΡΡΠΎΡΠ½ΠΈΠΈ Π½Π΅ΠΎΠ±Ρ ΠΎΠ΄ΠΈΠΌΠΎ ΠΎΠ±ΠΎΡΡΠ΄ΠΎΠ²Π°ΡΡ ΠΌΠ°ΡΠΈΠ½Ρ ΡΠ»Π΅ΠΊΡΡΠΎΠΎΠ±ΠΎΠ³ΡΠ΅Π²ΠΎΠΌ. ΠΠ΅ΡΡ Π½ΡΡ Π½ΠΈΡΠΊΡ ΠΏΡΠΎΠΏΠΈΡΡΠ²Π°ΡΡ 10%-ΠΌΠ²ΠΎΠ΄Π½ΡΠΌ ΡΠ°ΡΡΠ²ΠΎΡΠΎΠΌ ΡΡΠ°Π³Π°Π½ΡΠ°. Π’ΡΠ°Π³Π°Π½Ρ ΠΌΠΎΠΆΠ½ΠΎ Π·Π°ΠΌΠ΅Π½ΡΡΡ 5%-ΠΌ ΡΠ°ΡΡΠ²ΠΎΡΠΎΠΌ ΠΊΡΠ°Ρ ΠΌΠ°Π»Π° Π² ΠΈΠ·Π²Π΅ΡΡΠΊΠΎΠ²ΠΎΠΉ Π²ΠΎΠ΄Π΅ (ΡΠ ΠΎΠΊΠΎΠ»ΠΎ 12). Π‘ΠΈΠ»ΡΠ½ΠΎ Π²Π»ΠΈΡΠ΅Ρ Π½Π° ΠΊΠ°ΡΠ΅ΡΡΠ²ΠΎ ΡΠ²Π° ΠΏΡΠΎΠΏΠΈΡΠΊΠ° Π½ΠΈΠΆΠ½Π΅ΠΉ Π½ΠΈΡΠΊΠΈ, Π·Π°ΠΏΡΠ°Π²Π»Π΅Π½Π½ΠΎΠΉ Π² ΡΠ΅Π»Π½ΠΎΠΊ, ΠΊΠ»Π΅ΡΡΠΈΠΌΠΈ ΠΈ ΡΠΌΠ°Π·ΡΠ²Π°ΡΡΠΈΠΌΠΈ ΠΌΠ°ΡΠ΅ΡΠΈΠ°Π»Π°ΠΌΠΈ. Π’Π°ΠΊΠ°Ρ ΠΏΡΠΎΠΏΠΈΡΠΊΠ° ΠΎΠ±Π»Π΅Π³ΡΠ°Π΅Ρ ΠΏΡΠΎΡΡΠ³ΠΈΠ²Π°Π½ΠΈΠ΅ Π½ΠΈΡΠΎΠΊ ΡΠ΅ΡΠ΅Π· ΠΌΠ΅Ρ Π°Π½ΠΈΠ·ΠΌ ΠΌΠ°ΡΠΈΠ½Ρ ΠΈ ΠΎΡΠΎΠ±Π΅Π½Π½ΠΎ ΡΠ΅ΡΠ΅Π· ΠΊΡΡΡΠΎΠΊ ΠΈΠ³Π»Ρ, ΠΏΡΠ΅Π΄ΠΎΡΠ²ΡΠ°ΡΠ°Π΅Ρ ΠΈΡ ΠΈΡΡΠΈΡΠ°Π½ΠΈΠ΅ ΠΈ ΡΠ°Π·Π»ΠΎΡ ΠΌΠ°ΡΠΈΠ²Π°Π½ΠΈΠ΅, ΠΎΠ±Π»Π΅Π³ΡΠ°Π΅Ρ ΡΠΊΠΎΠ»ΡΠΆΠ΅Π½ΠΈΠ΅ Π½ΠΈΡΠΎΠΊ ΠΏΡΠΈ ΠΎΠ±ΡΠ°Π·ΠΎΠ²Π°Π½ΠΈΠΈ ΠΈ ΡΡΡΠΆΠΊΠ΅ ΡΡΠ΅ΠΆΠΊΠ°. ΠΡΠΈ Π²ΡΠ±ΠΎΡΠ΅ ΠΏΡΠΎΠΏΠΈΡΡΠ²Π°ΡΡΠ΅Π³ΠΎ ΠΌΠ°ΡΠ΅ΡΠΈΠ°Π»Π° Π½Π΅ΠΎΠ±Ρ ΠΎΠ΄ΠΈΠΌΠΎ ΡΡΠΈΡΡΠ²Π°ΡΡ Π²ΠΎΠ·ΠΌΠΎΠΆΠ½ΠΎΡΡΡ ΠΈΡΠΏΠΎΠ»ΡΠ·ΠΎΠ²Π°Π½ΠΈΡ Π΅Π³ΠΎ Π½Π° ΠΌΠ°ΡΠΈΠ½Π΅. ΠΠ»Ρ ΠΏΡΠΈΡΠΈΠ²Π°Π½ΠΈΡ ΠΊΠΎΠΆΠ°Π½ΠΎΠΉ ΠΏΠΎΠ΄ΠΎΡΠ²Ρ Π½Π°ΠΈΠ±ΠΎΠ»Π΅Π΅ ΠΏΠΎΠ΄Ρ ΠΎΠ΄ΡΡΠΈΠΌ ΠΏΡΠΎΠΏΠΈΡΡΠ²Π°ΡΡΠΈΠΌ ΠΌΠ°ΡΠ΅ΡΠΈΠ°Π»ΠΎΠΌ ΡΠ²Π»ΡΠ΅ΡΡΡ Π²Π°Ρ, ΠΈΠΌΠ΅ΡΡΠΈΠΉ ΡΠ΅ΠΌΠΏΠ΅ΡΠ°ΡΡΡΡ ΠΏΠ»Π°Π²Π»Π΅Π½ΠΈΡ 65—75Β°Π‘. ΠΠΎΠΏΡΡΠΊΠ° Π·Π°ΠΌΠ΅Π½ΠΈΡΡ ΡΠ°ΡΠΏΠ»Π°Π²Π»Π΅Π½Π½ΡΠΉ Π²Π°Ρ Π²Π°ΡΠΎΠΌ, ΡΠ°ΡΡΠ²ΠΎΡΠ΅Π½Π½ΡΠΌ Π² Π°ΡΠ΅ΡΠΎΠ½Π΅ ΠΈ Π΄ΡΡΠ³ΠΈΡ ΡΠ°ΡΡΠ²ΠΎΡΠΈΡΠ΅Π»ΡΡ , Π½Π΅ ΠΏΡΠΈΠ²Π΅Π»Π° ΠΊ ΡΡΠΏΠ΅Ρ Ρ. ΠΡΠΎΡΠ½ΠΎΡΡΡ Π½ΠΈΡΠΊΠΈ, ΠΏΡΠΎΠΏΠΈΡΠ°Π½Π½ΠΎΠΉ Ρ ΠΎΠ»ΠΎΠ΄Π½ΡΠΌ Π²Π°ΡΠΎΠΌ, ΠΏΠΎΠ²ΡΡΠ°Π΅ΡΡΡ ΠΏΠΎ ΡΡΠ°Π²Π½Π΅Π½ΠΈΡ Ρ ΠΏΡΠΎΡΠ½ΠΎΡΡΡΡ Π½ΠΈΡΠΊΠΈ, ΠΏΡΠΎΠΏΠΈΡΠ°Π½Π½ΠΎΠΉ Π³ΠΎΡΡΡΠΈΠΌ Π²Π°ΡΠΎΠΌ, Π½ΠΎ Π½Π΅Π»ΡΠ·Ρ Π΄ΠΎΠΏΡΡΠΊΠ°ΡΡ ΠΈΡΠΏΠ°ΡΠ΅Π½ΠΈΡ ΡΠ°ΡΡΠ²ΠΎΡΠΈΡΠ΅Π»Ρ, ΠΏΠΎΠΊΠ° Π½ΠΈΡΠΊΠ° Π½Π΅ ΠΎΠ±ΡΠ°Π·ΡΠ΅Ρ ΡΡΡΠΎΡΠΊΡ. ΠΡΠΈ Π±ΠΎΠ»Π΅Π΅ ΠΈΠ»ΠΈ ΠΌΠ΅Π½Π΅Π΅ ΠΏΡΠΎΠ΄ΠΎΠ»ΠΆΠΈΡΠ΅Π»ΡΠ½ΠΎΠΌ ΠΎΡΡΠ°Π½ΠΎΠ²Π΅ ΠΌΠ°ΡΠΈΠ½Ρ Π½ΠΈΡΠΊΠ°, ΠΏΡΠΎΠΏΠΈΡΠ°Π½Π½Π°Ρ Ρ ΠΎΠ»ΠΎΠ΄Π½ΡΠΌ Π²Π°ΡΠΎΠΌ, ΡΡΠ°Π½ΠΎΠ²ΠΈΡΡΡ ΠΆΠ΅ΡΡΠΊΠΎΠΉ ΠΈ Π½Π΅ΠΏΡΠΈΠ³ΠΎΠ΄Π½ΠΎΠΉ Π΄Π»Ρ ΡΠ°Π±ΠΎΡΡ. ΠΠ»Ρ ΠΎΡΠΈΡΡΠΊΠΈ ΠΌΠ°ΡΠΈΠ½Ρ ΠΎΡ Π·Π°Π³ΡΡΠ·Π½Π΅Π½ΠΈΡ Π½Π΅ΠΎΠ±Ρ ΠΎΠ΄ΠΈΠΌ ΡΠ°ΡΡΠ²ΠΎΡΠΈΡΠ΅Π»Ρ ΠΈΠ»ΠΈ Π½Π°Π³ΡΠ΅Π²Π°ΡΠ΅Π»ΠΈ, ΡΡΠΎ Π»ΠΈΠΊΠ²ΠΈΠ΄ΠΈΡΡΠ΅Ρ Π²ΡΠ΅ ΠΏΡΠ΅ΠΈΠΌΡΡΠ΅ΡΡΠ²Π° Ρ ΠΎΠ»ΠΎΠ΄Π½ΠΎΠΉ ΠΏΡΠΎΠΏΠΈΡΠΊΠΈ.
ΠΠ° ΠΏΡΠΎΡΠ½ΠΎΡΡΡ ΠΊΡΠ΅ΠΏΠ»Π΅Π½ΠΈΡ ΠΊΠΎΠΆΠ°Π½ΡΡ ΠΏΠΎΠ΄ΠΎΡΠ² Π²Π»ΠΈΡΠ΅Ρ ΠΈΡ Π²Π»Π°ΠΆΠ½ΠΎΡΡΡ. Π£Π²Π΅Π»ΠΈΡΠ΅Π½ΠΈΠ΅ Π²Π»Π°ΠΆΠ½ΠΎΡΡΠΈ ΠΏΠΎΠ΄ΠΎΡΠ²Ρ Π΄ΠΎ 35—40% ΠΏΠΎΠ²ΡΡΠ°Π΅Ρ ΡΠΎΠΏΡΠΎΡΠΈΠ²Π»Π΅Π½ΠΈΠ΅ Π²ΡΡΡΠ²Π°Π½ΠΈΡ Π½Π°ΡΡΡΠ΅Π½Π½ΠΎΠ³ΠΎ ΡΡΠ΅ΠΆΠΊΠ° Π½Π° 30%. Π‘ΠΎΠΏΡΠΎΡΠΈΠ²Π»Π΅Π½ΠΈΠ΅ ΠΏΡΠΎΠΊΠ°Π»ΡΠ²Π°Π½ΠΈΡ ΡΠ²Π»Π°ΠΆΠ½Π΅Π½Π½ΠΎΠΉ ΠΏΠΎΠ΄ΠΎΡΠ²Ρ ΡΠ½ΠΈΠΆΠ°Π΅ΡΡΡ Π±Π»Π°Π³ΠΎΠ΄Π°ΡΡ ΠΏΠΎΠ²ΡΡΠ΅Π½ΠΈΡ Π³ΠΈΠ±ΠΊΠΎΡΡΠΈ Π΅Π΅ Π²ΠΎΠ»ΠΎΠΊΠΎΠ½; ΠΏΡΠΎΠΊΠ°Π»ΡΠ²Π°Π½ΠΈΠ΅ ΡΠΎΠΏΡΠΎΠ²ΠΎΠΆΠ΄Π°Π΅ΡΡΡ ΠΌΠ΅Π½ΡΡΠΈΠΌ ΠΈΡ ΡΠ°Π·ΡΡΠ²ΠΎΠΌ. ΠΡΠΎ ΠΏΡΠΈΠ²ΠΎΠ΄ΠΈΡ ΠΊ ΡΠΎΠΌΡ, ΡΡΠΎ ΠΏΡΠΈ ΠΏΠΎΡΠ»Π΅Π΄ΡΡΡΠ΅ΠΌ ΡΠ½ΠΈΠΆΠ΅Π½ΠΈΠΈ Π²Π»Π°ΠΆΠ½ΠΎΡΡΠΈ ΠΏΠΎΠ΄ΠΎΡΠ²Ρ ΡΡΠ΅Π½ΠΊΠΈ ΠΎΡΠ²Π΅ΡΡΡΠΈΠΉ ΠΏΠ»ΠΎΡΠ½Π΅Π΅ ΠΎΡ Π²Π°ΡΡΠ²Π°ΡΡ Π½ΠΈΡΠΊΡ. ΠΠΎΡΠ»Π΅ ΡΡΡΠΊΠΈ ΠΏΠ»ΠΎΡΠ°Π΄Ρ ΡΠ²Π»Π°ΠΆΠ½Π΅Π½Π½ΠΎΠΉ ΠΏΠΎΠ΄ΠΎΡΠ²Ρ ΡΠΎΠΊΡΠ°ΡΠ°Π΅ΡΡΡ, ΡΡΠΎ ΡΠΎΠ·Π΄Π°Π΅Ρ Π±ΠΎΠ»ΡΡΠΈΠ΅ Π½Π°ΠΏΡΡΠΆΠ΅Π½ΠΈΡ Π½ΠΈΡΠΊΠΈ Π² ΡΠ²Π΅. Π’Π°ΠΊΠΈΠΌ ΠΎΠ±ΡΠ°Π·ΠΎΠΌ, ΡΠ²Π»Π°ΠΆΠ½ΡΡΡ ΡΠ»Π΅Π΄ΡΠ΅Ρ ΡΠΎΠ»ΡΠΊΠΎ Π½Π°ΡΡΠΆΠ½ΡΠΉ ΠΊΡΠ°ΠΉ ΠΏΠΎΠ΄ΠΎΡΠ²Ρ. ΠΠΎΠ²ΡΠΎΡΠ½ΡΠ΅ ΡΠ²Π»Π°ΠΆΠ½Π΅Π½ΠΈΠ΅ ΠΈ ΡΡΡΠΊΠ° Π² Π½ΠΎΡΠΊΠ΅ ΡΠ½ΠΈΠΆΠ°ΡΡ ΠΏΡΠΎΡΠ½ΠΎΡΡΡ ΡΠ²Π° Π½Π° 20—40% (ΠΏΠΎ Π΄Π°Π½Π½ΡΠΌ ΡΠ°Π·Π½ΡΡ ΠΈΡΡΠ»Π΅Π΄ΠΎΠ²Π°ΡΠ΅Π»Π΅ΠΉ). ΠΠ° ΠΏΡΠΎΡΠ½ΠΎΡΡΡ ΡΠ²Π° Π²Π»ΠΈΡΠ΅Ρ ΡΠ°Π³ ΡΡΠ΅ΠΆΠΊΠ°. ΠΠ»Ρ ΠΊΠΎΠΆΠ°Π½ΠΎΠΉ ΠΏΠΎΠ΄ΠΎΡΠ²Ρ ΠΎΠΏΡΠΈΠΌΠ°Π»Π΅Π½ ΡΠ°Π³ ΡΡΠ΅ΠΆΠΊΠ° 3—3,5 ΠΌΠΌ (ΡΡΠΈ ΡΡΠ΅ΠΆΠΊΠ° Π½Π° 1 ΡΠΌ ΡΡΡΠΎΡΠΊΠΈ). ΠΠ»Ρ ΡΠ΅Π·ΠΈΠ½ΠΎΠ²ΡΡ ΠΏΠΎΠ΄ΠΎΡΠ² ΡΠ°Π³ ΡΡΠ΅ΠΆΠΊΠ° Π·Π°Π²ΠΈΡΠΈΡ ΠΎΡ ΠΏΠ»ΠΎΡΠ½ΠΎΡΡΠΈ ΠΌΠ°ΡΠ΅ΡΠΈΠ°Π»Π°. ΠΡΠΈ ΠΏΠ»ΠΎΡΠ½ΠΎΡΡΠΈ Π±ΠΎΠ»Π΅Π΅ 1,2 Π³/ΡΠΌ3, 1,1—1,2 ΠΈ 0,9—1 Π³/ΡΠΌ3 ΡΠ°Π³ ΡΡΠ΅ΠΆΠΊΠ° ΡΠ°Π²Π΅Π½ ΡΠΎΠΎΡΠ²Π΅ΡΡΡΠ²Π΅Π½Π½ΠΎ 4 ΠΌΠΌ, 4,5 ΠΈ 5,5 ΠΌΠΌ.
3. ΠΠΈΡΡΠ΅ Ρ ΠΎΠ±ΡΠ°Π·ΠΎΠ²Π°Π½ΠΈΠ΅ΠΌ ΠΏΠΎΠ»ΠΈΠΌΠ΅ΡΠ½ΠΎΠ³ΠΎ ΠΌΠ°ΡΠ΅ΡΠΈΠ°Π»Π° Π² ΡΠΎΡΠΌΠ΅, Π½Π°Π·ΡΠ²Π°Π΅ΠΌΠΎΠ΅ Π΅ΡΠ΅ ΠΆΠΈΠ΄ΠΊΠΈΠΌ ΡΠΎΡΠΌΠΈΡΠΎΠ²Π°Π½ΠΈΠ΅ΠΌ, ΠΏΡΠΈΠΌΠ΅Π½ΡΠ΅ΡΡΡ Π΄Π»Ρ ΠΏΠΎΠ»ΡΡΠ΅Π½ΠΈΡ ΠΈΠ·Π΄Π΅Π»ΠΈΠΉ ΠΈΠ· ΠΏΠΎΠ»ΠΈΡΡΠ΅ΡΠ°Π½Π°, ΠΏΠΎΡΡΠΎΠΌΡ ΠΈ ΠΌΠ΅ΡΠΎΠ΄ ΠΈΠ½ΠΎΠ³Π΄Π° Π½Π°Π·ΡΠ²Π°ΡΡ ΠΏΡΠΎΡΡΠΎ Π»ΠΈΡΡΠ΅ΠΌ ΠΏΠΎΠ»ΠΈΡΡΠΈΡΠ°Π½ΠΎΠ² ΠΡΠ½ΠΎΠ²Ρ ΠΌΠ΅ΡΠΎΠ΄Π°. ΠΠΈΠ΄ΠΊΠΈΠΌ ΡΠΎΡΠΌΠΎΠ²Π°Π½ΠΈΠ΅ΠΌ ΠΎΡΠ»ΠΈΠ²Π°Π΅ΡΡΡ Π½ΠΈΠ· Π½Π° ΠΎΠ±ΡΠ²ΠΈ, ΡΠ΅Π»ΡΠ½ΠΎΡΠΎΡΠΌΠΎΠ²Π°Π½Π½Π°Ρ ΠΎΠ±ΡΠ²Ρ, ΠΎΡΠ΄Π΅Π»ΡΠ½ΠΎ ΠΏΠΎΠ΄ΠΎΡΠ²Ρ, ΠΏΡΠΎΡΠΈΠ»ΠΈΡΠΎΠ²Π°Π½Π½ΡΠ΅ ΡΡΠ΅Π»ΡΠΊΠΈ (Π΄Π»Ρ ΠΌΠ΅Π΄ΠΈΡΠΈΠ½ΡΠΊΠΎΠΉ, ΡΠΏΠΎΡΡΠΈΠ²Π½ΠΎΠΉ ΠΎΠ±ΡΠ²ΠΈ), ΠΊΠ°Π±Π»ΡΠΊΠΈ, ΡΠ»Π°ΡΡΠΈΡΠ½ΡΠ΅ Π²ΠΊΠ»Π°Π΄ΡΡΠΈ Π² ΠΎΠ±ΡΠ²Ρ, Π° ΡΠ°ΠΊΠΆΠ΅ ΠΊΠΎΠΆΠ³Π°Π»Π°Π½ΡΠ΅ΡΠ΅ΠΉΠ½ΡΠ΅ ΠΈΠ·Π΄Π΅Π»ΠΈΡ ΠΈ Π΄Π΅ΡΠ°Π»ΠΈ (ΡΡΡΠ»ΡΡΡ Π΄Π»Ρ ΡΠΎΡΠΎΠ°ΠΏΠΏΠ°ΡΠ°ΡΠΎΠ², Π΄ΡΡΠ³ΠΈΡ ΠΏΡΠ΅Π΄ΠΌΠ΅ΡΠΎΠ² ΠΈ Ρ. ΠΏ.). ΠΡΠΈ ΡΡΠΎΠΌ ΠΈΡΡ ΠΎΠ΄Π½ΡΠ΅ ΠΊΠΎΠΌΠΏΠΎΠ½Π΅Π½ΡΡ Ρ ΠΏΠΎΠΌΠΎΡΡΡ ΡΠΏΠ΅ΡΠΈΠ°Π»ΡΠ½ΠΎΠ³ΠΎ ΠΎΠ±ΠΎΡΡΠ΄ΠΎΠ²Π°Π½ΠΈΡ ΡΠΌΠ΅ΡΠΈΠ²Π°ΡΡΡΡ, Π΄ΠΎΠ·ΠΈΡΠΎΠ²Π°Π½Π½ΠΎ ΠΏΠΎΠ΄Π°ΡΡΡΡ Π² Π»ΠΈΡΡΠ΅Π²ΡΡ ΡΠΎΡΠΌΡ, Π³Π΄Π΅ Π² ΡΠ΅Π·ΡΠ»ΡΡΠ°ΡΠ΅ Ρ ΠΈΠΌΠΈΡΠ΅ΡΠΊΠΈΡ ΡΠ΅Π°ΠΊΡΠΈΠΉ ΠΎΠ±ΡΠ°Π·ΡΠ΅ΡΡΡ ΠΏΠΎΠ»ΠΈΠΌΠ΅ΡΠ½ΡΠΉ ΠΌΠ°ΡΠ΅ΡΠΈΠ°Π» — ΠΏΠΎΠ»ΠΈΡΡΠ΅ΡΠ°Π½, ΠΊΠΎΡΠΎΡΡΠΉ, ΠΏΠΎΠ΄ Π²ΠΎΠ·Π΄Π΅ΠΉΡΡΠ²ΠΈΠ΅ΠΌ Π΄Π°Π²Π»Π΅Π½ΠΈΡ, ΡΠΎΠ·Π΄Π°Π²ΡΠ΅Π³ΠΎΡΡ Π² Π·Π°ΠΊΡΡΡΠΎΠΌ ΠΏΡΠΎΡΡΡΠ°Π½ΡΡΠ²Π΅ ΡΠΎΡΠΌΡ, ΡΠΎΡΠΌΡΠ΅ΡΡΡ ΠΏΠΎ Π΅Π΅ Π²Π½ΡΡΡΠ΅Π½Π½Π΅ΠΌΡ ΠΎΠ±ΡΠ΅ΠΌΡ. Π‘ΡΡΠ΅ΡΡΠ²ΡΠ΅Ρ ΠΌΠ½ΠΎΠΆΠ΅ΡΡΠ²ΠΎ Π²ΠΈΠ΄ΠΎΠ² ΠΏΠΎΠ»ΠΈΡΡΠ΅ΡΠ°Π½ΠΎΠ². ΠΠΈΠ°ΠΏΠ°Π·ΠΎΠ½ ΠΈΡ ΡΠΈΠ·ΠΈΡΠ΅ΡΠΊΠΈΡ ΡΠ²ΠΎΠΉΡΡΠ² Π²Π΅ΡΡΠΌΠ° ΡΠΈΡΠΎΠΊ — ΠΎΡ ΠΆΠ΅ΡΡΠΊΠΈΡ ΠΏΠ»ΠΎΡΠ½ΡΡ Π΄ΠΎ ΠΌΡΠ³ΠΊΠΈΡ ΠΏΠΎΡΠΈΡΡΡΡ ΡΠ»Π°ΡΡΠΎΠΌΠ΅ΡΠΎΠ² ΠΈ ΠΏΠ΅Π½ΠΈΡΡΡΡ ΠΌΠ°ΡΠ΅ΡΠΈΠ°Π»ΠΎΠ² Π²Π΅ΡΡΠΌΠ° ΠΌΠ°Π»ΠΎΠΉ ΠΏΠ»ΠΎΡΠ½ΠΎΡΡΠΈ (ΠΌΠ΅Π½Π΅Π΅ 0,1 Π³/ΡΠΌ3). ΠΡΠΎ Π΄ΠΎΡΡΠΈΠ³Π°Π΅ΡΡΡ ΡΠΎΠΎΡΠ²Π΅ΡΡΡΠ²ΡΡΡΠΈΠΌ ΠΏΠΎΠ΄Π±ΠΎΡΠΎΠΌ ΠΈΡΡ ΠΎΠ΄Π½ΡΡ ΠΊΠΎΠΌΠΏΠΎΠ½Π΅Π½ΡΠΎΠ², ΡΡΠ°ΡΡΠ²ΡΡΡΠΈΡ Π² ΡΠ΅Π°ΠΊΡΠΈΡΡ ΠΏΠΎΠ»ΡΡΠ΅Π½ΠΈΡ ΠΏΠΎΠ»ΠΈΠΌΠ΅ΡΠ°, ΠΈ ΡΡΠ»ΠΎΠ²ΠΈΡΠΌΠΈ ΠΏΡΠΎΠ²Π΅Π΄Π΅Π½ΠΈΡ ΡΠ°ΠΌΠΈΡ ΡΠ΅Π°ΠΊΡΠΈΠΉ. ΠΠΎΠ·ΠΌΠΎΠΆΠ½Ρ Π΄Π²Π° ΠΌΠ΅ΡΠΎΠ΄Π° ΠΏΠΎΠ»ΡΡΠ΅Π½ΠΈΡ ΠΏΠΎΠ»ΠΈΡΡΠ΅ΡΠ°Π½Π° ΠΏΠΎ ΡΠ΅Ρ Π½ΠΎΠ»ΠΎΠ³ΠΈΠΈ ΠΆΠΈΠ΄ΠΊΠΎΠ³ΠΎ ΡΠΎΡΠΌΠΎΠ²Π°Π½ΠΈΡ — ΠΎΠ΄Π½ΠΎΠΈ Π΄Π²ΡΡ ΡΡΠ°Π΄ΠΈΠΉΠ½ΡΠΉ. ΠΡΠΈ ΠΎΠ΄Π½ΠΎΡΡΠ°Π΄ΠΈΠΉΠ½ΠΎΠΌ ΠΌΠ΅ΡΠΎΠ΄Π΅ ΠΎΠ±Π° ΡΡΠ°ΠΏΠ° ΡΠ΅Π°ΠΊΡΠΈΠΉ ΡΠΈΠ½ΡΠ΅Π·Π° ΠΏΠΎΠ»ΠΈΡΡΠ΅ΡΠ°Π½Π°— ΠΎΠ±ΡΠ°Π·ΠΎΠ²Π°Π½ΠΈΠ΅ ΡΡΠ΅ΡΠ°Π½ΠΎΠ²ΠΎΠ³ΠΎ ΠΎΠ»ΠΈΠ³ΠΎΠΌΠ΅ΡΠ° (ΡΠΎΡΠΏΠΎΠ»ΠΈΠΌΠ΅ΡΠ°) ΠΈ Π·Π°ΡΠ΅ΠΌ ΠΎΠ±ΡΠ°Π·ΠΎΠ²Π°Π½ΠΈΠ΅ ΠΏΠΎΠ»ΠΈΠΌΠ΅ΡΠ° ΠΏΠΎ ΠΌΠ΅Ρ Π°Π½ΠΈΠ·ΠΌΡ ΠΏΡΠΈΡΠΎΠ΅Π΄ΠΈΠ½Π΅Π½ΠΈΡ ΠΈ ΡΠΎΡΡΠ° ΡΠ΅ΠΏΠΈ — ΡΠΎΠ²ΠΌΠ΅ΡΠ΅Π½Ρ ΠΈ ΡΠ΅Ρ Π½ΠΎΠ»ΠΎΠ³ΠΈΡΠ΅ΡΠΊΠΈ ΠΏΡΠΎΠ²ΠΎΠ΄ΡΡΡΡ Π² ΠΎΠ΄Π½Ρ ΡΡΠ°Π΄ΠΈΡ, Π² ΠΎΠ΄ΠΈΠ½ ΠΏΡΠΈΠ΅ΠΌ. Π Π·Π°ΡΡΠ±Π΅ΠΆΠ½ΠΎΠΉ ΡΠΏΠ΅ΡΠΈΠ°Π»ΡΠ½ΠΎΠΉ Π»ΠΈΡΠ΅ΡΠ°ΡΡΡΠ΅ ΡΠ°ΠΊΠΎΠΉ ΠΌΠ΅ΡΠΎΠ΄ ΠΈΠ½ΠΎΠ³Π΄Π° Π½Π°Π·ΡΠ²Π°Π΅ΡΡΡ Πne-Shot-System (ΡΠ°Π½-ΡΠΎΡ-ΡΠΈΡΡΠ΅ΠΌ). ΠΡΠΈ Π΄Π²ΡΡ ΡΡΠ°Π΄ΠΈΠΉΠ½ΠΎΠΌ ΠΌΠ΅ΡΠΎΠ΄Π΅ ΠΏΡΠΎΡΠ΅ΡΡ ΠΎΠ±ΡΠ°Π·ΠΎΠ²Π°Π½ΠΈΡ ΠΏΠΎΠ»ΠΈΡΡΠ΅ΡΠ°Π½Π° ΡΠ΅Ρ Π½ΠΎΠ»ΠΎΠ³ΠΈΡΠ΅ΡΠΊΠΈ ΡΠ°Π·Π΄Π΅Π»Π΅Π½ Π½Π° Π΄Π²Π΅ ΡΡΠ°Π΄ΠΈΠΈ: Π½Π° ΠΏΠ΅ΡΠ²ΠΎΠΉ Ρ ΠΈΡΠΏΠΎΠ»ΡΠ·ΠΎΠ²Π°Π½ΠΈΠ΅ΠΌ ΠΎΡΠ΄Π΅Π»ΡΠ½ΠΎΠ³ΠΎ ΠΎΠ±ΠΎΡΡΠ΄ΠΎΠ²Π°Π½ΠΈΡ ΠΏΡΠΎΠ²ΠΎΠ΄ΠΈΡΡΡ ΠΎΠ±ΡΠ°Π·ΠΎΠ²Π°Π½ΠΈΠ΅ ΡΠΎΡΠΏΠΎΠ»ΠΈΠΌΠ΅ΡΠ°, Π° Π·Π°ΡΠ΅ΠΌ, Π½Π° Π²ΡΠΎΡΠΎΠΉ ΡΡΠ°Π΄ΠΈΠΈ, ΡΠΎΡΠΏΠΎΠ»ΠΈΠΌΠ΅Ρ ΠΊΠ°ΠΊ ΡΠ°ΠΌΠΎΡΡΠΎΡΡΠ΅Π»ΡΠ½ΡΠΉ ΠΊΠΎΠΌΠΏΠΎΠ½Π΅Π½Ρ Π²Π·Π°ΠΈΠΌΠΎΠ΄Π΅ΠΉΡΡΠ²ΡΠ΅Ρ Ρ ΡΠ΄Π»ΠΈΠ½ΠΈΡΠ΅Π»Π΅ΠΌ ΡΠ΅ΠΏΠΈ, ΡΠ°ΡΡΠΈΡΠ½ΠΎ ΡΠ°ΠΊΠΆΠ΅ ΡΠ³ΠΈΠ΄ΡΠΎΠΊΡΠΈΠ»ΡΠΎΠ΄Π΅ΡΠΆΠ°ΡΠΈΠΌΠΈ ΠΎΠ»ΠΈΠ³ΠΎΡΠΎΠ΅Π΄ΠΈΠ½Π΅Π½ΠΈΡΠΌΠΈ ΠΈ ΠΏΠΎΠ»ΡΡΠ°Π΅ΡΡΡ ΠΊΠΎΠ½Π΅ΡΠ½ΡΠΉ ΠΏΡΠΎΠ΄ΡΠΊΡ — Π²ΡΡΠΎΠΊΠΎΠΌΠΎΠ»Π΅ΠΊΡΠ»ΡΡΠ½ΡΠΉ ΠΏΠΎΠ»ΠΈΡΡΠ΅ΡΠ°Π½. ΠΠ΅ΡΠ²Π°Ρ ΠΈ Π²ΡΠΎΡΠ°Ρ ΡΡΠ°Π΄ΠΈΠΈ — ΠΏΠΎΠ»ΡΡΠ΅Π½ΠΈΠ΅ ΡΠΎΡΠΏΠΎΠ»ΠΈΠΌΠ΅ΡΠ° ΠΈ ΠΈΠ·Π΄Π΅Π»ΠΈΡ ΠΈΠ· ΠΏΠΎΠ»ΠΈΠΌΠ΅ΡΠ½ΠΎΠ³ΠΎ ΠΌΠ°ΡΠ΅ΡΠΈΠ°Π»Π° — ΠΌΠΎΠ³ΡΡ ΠΏΡΠΎΠ²ΠΎΠ΄ΠΈΡΡΡΡ Π½Π΅ Π½Π΅ΠΏΠΎΡΡΠ΅Π΄ΡΡΠ²Π΅Π½Π½ΠΎ ΠΎΠ΄Π½Π° Π·Π° Π΄ΡΡΠ³ΠΎΠΉ, Π° ΠΏΡΠ΅Π΄ΠΏΡΠΈΡΡΠΈΡ-ΠΈΠ·Π³ΠΎΡΠΎΠ²ΠΈΡΠ΅Π»Ρ ΠΈΠ·Π΄Π΅Π»ΠΈΠΉ ΠΈΠ· ΠΏΠΎΠ»ΠΈΡΡΠ΅ΡΠ°Π½Π° ΡΠΎΡΠΏΠΎΠ»ΠΈΠΌΠ΅Ρ ΠΌΠΎΠΆΠ΅Ρ ΠΏΠΎΡΡΠ°Π²Π»ΡΡΡΡΡ ΠΊΠ°ΠΊ ΡΡΡΡΠ΅ Π½Π°ΡΡΠ΄Ρ Ρ Π΄ΡΡΠ³ΠΈΠΌΠΈ ΠΊΠΎΠΌΠΏΠΎΠ½Π΅Π½ΡΠ°ΠΌΠΈ. Π ΠΏΡΠΎΠΈΠ·Π²ΠΎΠ΄ΡΡΠ²Π΅ ΠΈΠ·Π΄Π΅Π»ΠΈΠΉ ΠΈΠ· ΠΊΠΎΠΆΠΈ ΠΏΡΠΈΠΌΠ΅Π½ΡΠ΅ΡΡΡ Π³Π»Π°Π²Π½ΡΠΌ ΠΎΠ±ΡΠ°Π·ΠΎΠΌ Π΄Π²ΡΡ ΡΡΠ°Π΄ΠΈΠΉΠ½ΡΠΉ ΠΌΠ΅ΡΠΎΠ΄, Ρ ΠΎΡΡ ΠΎΠ΄Π½ΠΎΡΡΠ°Π΄ΠΈΠΉΠ½ΡΠΉ, ΠΊΠ°Π·Π°Π»ΠΎΡΡ Π±Ρ, ΠΏΡΠΎΡΠ΅. Π’Π΅Ρ Π½ΠΎΠ»ΠΎΠ³ΠΈΡ ΠΆΠΈΠ΄ΠΊΠΎΠ³ΠΎ ΡΠΎΡΠΌΠΈΡΠΎΠ²Π°Π½ΠΈΡ. ΠΠ±ΠΎΡΡΠ΄ΠΎΠ²Π°Π½ΠΈΠ΅. Π’Π΅Ρ Π½ΠΎΠ»ΠΎΠ³ΠΈΡΠ΅ΡΠΊΠΈΠΉ ΠΏΡΠΎΡΠ΅ΡΡ ΠΆΠΈΠ΄ΠΊΠΎΠ³ΠΎ ΡΠΎΡΠΌΠΎΠ²Π°Π½ΠΈΡ ΠΈΠ·Π΄Π΅Π»ΠΈΠΉ ΠΈΠ· ΠΏΠΎΠ»ΠΈΡΡΠ΅ΡΠ°Π½ΠΎΠ² ΠΏΡΠΎΠ²ΠΎΠ΄ΠΈΡΡΡ Π½Π° ΡΠΏΠ΅ΡΠΈΠ°Π»ΡΠ½ΠΎΠΌ ΠΎΠ±ΠΎΡΡΠ΄ΠΎΠ²Π°Π½ΠΈΠΈ (ΡΠΈΡ. 6). ΠΠ½ΠΎ ΠΈΠΌΠ΅Π΅Ρ Π΄Π²Π° ΡΠ΅Π·Π΅ΡΠ²ΡΠ°ΡΠ°-ΡΠ΅Π°ΠΊΡΠΎΡΠ°, Π ΠΈ Π, Π² ΠΊΠΎΡΠΎΡΡΡ Π½Π°Ρ ΠΎΠ΄ΡΡΡΡ ΠΈΡΡ ΠΎΠ΄Π½ΡΠ΅ ΠΊΠΎΠΌΠΏΠΎΠ½Π΅Π½ΡΡ: Π² ΡΠ΅Π·Π΅ΡΠ²ΡΠ°ΡΠ΅, Π — Π³ΠΈΠ΄-ΡΠΎΠΊΡΠΈΠ»ΡΠΎΠ΄Π΅ΡΠΆΠ°ΡΠΈΠ΅ ΡΠΎΠ΅Π΄ΠΈΠ½Π΅Π½ΠΈΡ ΠΈ Π²ΡΠ΅ ΡΠ΅Ρ Π½ΠΎΠ»ΠΎΠ³ΠΈΡΠ΅ΡΠΊΠΈΠ΅ Π΄ΠΎΠ±Π°Π²ΠΊΠΈ (ΠΊΠ°ΡΠ°Π»ΠΈΠ·Π°ΡΠΎΡΡ, ΠΏΠΎΡΠΎΠΎΠ±ΡΠ°Π·ΠΎΠ²Π°ΡΠ΅Π»ΠΈ ΠΈ Π΄Ρ.), Π² ΡΠ΅Π·Π΅ΡΠ²ΡΠ°ΡΠ΅ Π — ΠΈΠ·ΠΎΡΠΈΠ°Π½Π°ΡΡΠΎΠ΄Π΅ΡΠΆΠ°ΡΠΈΠ΅ ΠΊΠΎΠΌΠΏΠΎΠ½Π΅Π½ΡΡ. ΠΠ· ΡΡΠΈΡ ΡΠ΅Π·Π΅ΡΠ²ΡΠ°ΡΠΎΠ² ΡΠΎΡΠΌΠΈΡΡΡΡΡΡ Π΄Π²Π° ΠΏΠΎΡΠΎΠΊΠ° (Π ΠΈ Π), ΠΊΠΎΡΠΎΡΡΠ΅ Π·Π°ΡΠ΅ΠΌ ΡΠΌΠ΅ΡΠΈΠ²Π°ΡΡΡΡ ΠΈ Ρ ΠΈΠΌΠΈΡΠ΅ΡΠΊΠΈ ΡΠ΅Π°Π³ΠΈΡΡΡΡ. Π Π΅Π·Π΅ΡΠ²ΡΠ°ΡΡ Ρ ΠΏΠΎΠΌΠΎΡΡΡ Π³ΠΈΠ±ΠΊΠΈΡ ΡΡΡΠ±ΠΎΠΏΡΠΎΠ²ΠΎΠ΄ΠΎΠ² ΡΠΎΠ΅Π΄ΠΈΠ½Π΅Π½Ρ Ρ Π΄ΠΎΠ·ΠΈΡΡΡΡΠΈΠΌΠΈ ΡΡΡΡΠΎΠΉΡΡΠ²Π°ΠΌΠΈ, Π° ΡΠ΅ Π² ΡΠ²ΠΎΡ ΠΎΡΠ΅ΡΠ΅Π΄Ρ ΡΠ΅ΡΠ΅Π· ΡΠΈΡΡΠ΅ΠΌΡ ΡΡΡΠ±ΠΎΠΏΡΠΎΠ²ΠΎΠ΄ΠΎΠ² Ρ Π²Π΅Π½ΡΠΈΠ»ΡΠΌΠΈ, ΡΠΎ ΡΠΌΠ΅ΡΠΈΡΠ΅Π»ΡΠ½ΠΎΠΉ ΠΊΠ°ΠΌΠ΅ΡΠΎΠΉ, Π² ΠΊΠΎΡΠΎΡΠΎΠΉ ΠΏΡΠΎΠΈΡΡ ΠΎΠ΄ΠΈΡ ΡΠΌΠ΅ΡΠ΅Π½ΠΈΠ΅ ΠΊΠΎΠΌΠΏΠΎΠ½Π΅Π½ΡΠΎΠ² ΠΈ Π·Π°ΡΠ΅ΠΌ ΡΠ΅ΡΠ΅Π· ΡΠΎΠΏΠ»ΠΎ ΠΏΠΎΠ΄Π°ΡΠ° Π² ΡΠΎΡΠΌΡ, Π½Π°Ρ ΠΎΠ΄ΡΡΡΡΡΡ Π½Π° ΡΠΎΡΠΌΠΎΠ΄Π΅ΡΠΆΠ°ΡΠ΅Π»Π΅.
ΠΠΎΠ·ΠΈΡΡΡΡΠ΅Π΅ ΡΡΡΡΠΎΠΉΡΡΠ²ΠΎ ΡΠ°ΡΠ΅ Π²ΡΠ΅Π³ΠΎ ΠΏΡΠ΅Π΄ΡΡΠ°Π²Π»ΡΠ΅Ρ ΡΠΎΠ±ΠΎΠΉ ΡΠ΅ΡΡΠ΅ΡΠ΅Π½ΡΠ°ΡΡΠΉ Π½Π°ΡΠΎΡ, ΠΎΠ±Π΅ΡΠΏΠ΅ΡΠΈΠ²Π°ΡΡΠΈΠΉ ΡΠΎΡΠ½ΠΎ ΡΠ΅Π³ΡΠ»ΠΈΡΡΠ΅ΠΌΠΎΠ΅ Π΄ΠΎΠ·ΠΈΡΠΎΠ²Π°Π½ΠΈΠ΅. ΠΠ»Ρ ΡΠΌΠ΅ΡΠ΅Π½ΠΈΡ ΠΌΠ°Π»ΠΎΠ²ΡΠ·ΠΊΠΈΡ ΠΊΠΎΠΌΠΏΠΎΠ½Π΅Π½ΡΠΎΠ² (ΠΏΡΠΈ ΠΎΠ΄Π½ΠΎΡΡΠ°Π΄ΠΈΠΉΠ½ΠΎΠΌ ΠΌΠ΅ΡΠΎΠ΄Π΅) ΡΡΡΠ΅ΠΊΡΠΈΠ²Π½ΡΠΌΠΈ ΠΌΠΎΠ³ΡΡ Π±ΡΡΡ ΠΏΠΎΡΡΠ½Π΅Π²ΡΠ΅ Π½Π°ΡΠΎΡΡ Π²ΡΡΠΎΠΊΠΎΠ³ΠΎ Π΄Π°Π²Π»Π΅Π½ΠΈΡ.
ΠΠ°ΠΈΠ±ΠΎΠ»ΡΡΠ΅Π΅ ΡΠ°ΡΠΏΡΠΎΡΡΡΠ°Π½Π΅Π½ΠΈΠ΅ ΡΡΠ΅Π΄ΠΈ ΠΊΠΎΠ½ΡΡΡΡΠΊΡΠΈΠΉ ΡΠΌΠ΅ΡΠΈΡΠ΅Π»Π΅ΠΉ ΠΈΠΌΠ΅Π΅Ρ ΡΠΌΠ΅ΡΠΈΡΠ΅Π»Ρ ΡΠΈΠΏΠ° ΡΠΊΠΎΡΠΎΡΡΠ½ΠΎΠ³ΠΎ ΡΠΊΡΡΡΡΠ΄Π΅ΡΠ° Ρ ΠΊΠΎΠ½ΡΡΠΎΠΎΠ±ΡΠ°Π·Π½ΡΠΌ ΡΠ½Π΅ΠΊΠΎΠΌ Π΄ΠΈΠ°ΠΌΠ΅ΡΡΠΎΠΌ 25—30 ΠΌΠΌ, ΠΈΠΌΠ΅ΡΡΠΈΠΌ ΠΎΡΠ΅Π²ΠΎΠ΅ ΠΏΠ΅ΡΠ΅ΠΌΠ΅ΡΠ΅Π½ΠΈΠ΅ Π΄ΠΎ 20 ΠΌΠΌ ΠΈ ΡΠ°ΡΡΠΎΡΡ Π²ΡΠ°ΡΠ΅Π½ΠΈΡ 150—300 Ρ -1. Π ΠΎΠ±ΠΎΡΡΠ΄ΠΎΠ²Π°Π½ΠΈΠΈ ΠΎΠ±Π΅ΡΠΏΠ΅ΡΠΈΠ²Π°Π΅ΡΡΡ ΡΠΎΡΠ½ΠΎΠ΅ ΡΠ΅Π³ΡΠ»ΠΈΡΠΎΠ²Π°Π½ΠΈΠ΅ ΡΠ΅ΠΌΠΏΠ΅ΡΠ°ΡΡΡΡ: Π² ΡΠ΅Π·Π΅ΡΠ²ΡΠ°ΡΠ°Ρ , Π° ΡΠ°ΠΊΠΆΠ΅ Π² ΡΡΡΠ±ΠΎΠΏΡΠΎΠ²ΠΎΠ΄Π°Ρ ΠΏΡΠ΅Π΄ΡΡΠΌΠΎΡΡΠ΅Π½Π° Π²ΠΎΠ·ΠΌΠΎΠΆΠ½ΠΎΡΡΡ ΠΏΠΎΠ΄ΠΎΠ³ΡΠ΅Π²Π° — ΡΠ΅ΡΠΌΠΎΡΡΠ°ΡΠΈΡΠΎΠ²Π°Π½ΠΈΡ, Π² ΡΠΌΠ΅ΡΠΈΡΠ΅Π»ΡΠ½ΠΎΠΌ ΡΡΡΡΠΎΠΉΡΡΠ²Π΅ ΠΈ ΡΠΎΡΠΌΠ°Ρ — ΠΏΠΎΠ΄ΠΎΠ³ΡΠ΅Π²Π° ΠΈ ΠΎΡ Π»Π°ΠΆΠ΄Π΅Π½ΠΈΡ. Π ΠΏΡΠΎΡΠ΅ΡΡΠ΅ Π»ΠΈΡΡΡ ΡΠ΅Π°ΠΊΡΠΈΠΎΠ½Π½ΡΡ ΡΠΌΠ΅ΡΡ ΠΌΠΎΠΆΠ½ΠΎ ΠΏΠΎΠ΄Π°Π²Π°ΡΡ Π² ΠΎΡΠΊΡΡΡΡΡ ΠΈΠ»ΠΈ Π·Π°ΠΊΡΡΡΡΡ ΡΠΎΡΠΌΡ. ΠΠ΅ΡΠ²ΡΠΉ ΡΠΏΠΎΡΠΎΠ± ΡΠ°ΡΠ΅ ΠΏΡΠΈΠΌΠ΅Π½ΡΠ΅ΡΡΡ ΠΏΡΠΈ Π»ΠΈΡΡΠ΅ ΠΎΡΠ΄Π΅Π»ΡΠ½ΡΡ Π΄Π΅ΡΠ°Π»Π΅ΠΉ, Π½Π°ΠΏΡΠΈΠΌΠ΅Ρ ΠΏΠΎΠ΄ΠΎΡΠ². ΠΠΎΡΠ»Π΅ ΠΏΠΎΠ΄Π°ΡΠΈ Π΄ΠΎΠ·ΠΈΡΠΎΠ²Π°Π½Π½ΠΎΠ³ΠΎ ΠΊΠΎΠ»ΠΈΡΠ΅ΡΡΠ²Π° ΡΠΌΠ΅ΡΠΈ ΡΠΎΡΠΌΠ° ΡΠΎΡΡΠ°Ρ ΠΆΠ΅ Π·Π°ΠΊΡΡΠ²Π°Π΅ΡΡΡ. ΠΡΠΈ Π»ΠΈΡΡΠ΅ Π½ΠΈΠ·Π° Π½Π° ΠΎΠ±ΡΠ²ΠΈ ΡΠ°ΡΠ΅ ΠΏΡΠΈΠΌΠ΅Π½ΡΠ΅ΡΡΡ ΠΌΠ΅ΡΠΎΠ΄ ΠΏΠΎΠ΄Π°ΡΠΈ ΡΠ΅Π°ΠΊΡΠΈΠΎΠ½Π½ΠΎΠΉ ΡΠΌΠ΅ΡΠΈ Π² Π·Π°ΠΊΡΡΡΡΡ ΡΠΎΡΠΌΡ. ΠΡΠΏΠΎΠ»ΡΠ·ΡΡΡΡΡ Π°Π»ΡΠΌΠΈΠ½ΠΈΠ΅Π²ΡΠ΅ ΡΠΎΡΠΌΡ ΠΈΠ»ΠΈ ΠΈΠ·Π³ΠΎΡΠΎΠ²Π»Π΅Π½Π½ΡΠ΅ Π³Π°Π»ΡΠ²Π°Π½ΠΈΡΠ΅ΡΠΊΠΈΠΌ ΡΠΏΠΎΡΠΎΠ±ΠΎΠΌ ΠΈΠ· Π»Π΅Π³ΠΊΠΈΡ ΡΠΏΠ»Π°Π²ΠΎΠ².
Π ΠΈΡΡΠ½ΠΎΠΊ 6. Π‘Ρ Π΅ΠΌΠ° ΡΠ΅Ρ Π½ΠΎΠ»ΠΎΠ³ΠΈΡΠ΅ΡΠΊΠΎΠ³ΠΎ ΠΏΡΠΎΡΠ΅ΡΡΠ° ΠΆΠΈΠ΄ΠΊΠΎΠ³ΠΎ ΡΠΎΡΠΌΠΎΠ²Π°Π½ΠΈΡ ΠΈΠ·Π΄Π΅Π»ΠΈΠΉ ΠΈΠ· ΠΏΠΎΠ»ΠΈΡΡΠ΅ΡΠ°Π½ΠΎΠ²: 1 — ΡΠΌΠ΅ΡΠΈΡΠ΅Π»ΡΠ½Π°Ρ ΠΊΠ°ΠΌΠ΅ΡΠ°; 2 — ΠΏΡΠΈΠ²ΠΎΠ΄ ΠΊΠ°ΠΌΠ΅ΡΡ; 3 — ΠΊΠ»Π°ΠΏΠ°Π½Ρ; 4 — Π΄ΠΎΠ·Π°ΡΠΎΡ; 5 — ΠΏΡΠΈΠ²ΠΎΠ΄ Π΄ΠΎΠ·Π°ΡΠΎΡΠ°; 6 — ΠΊΡΠ°Π½Ρ; 7 — ΠΌΠ΅ΡΠ°Π»ΠΊΠΈ; 8 — ΡΠ΅Π·Π΅ΡΠ²ΡΠ°ΡΡ-ΡΠ΅Π°ΠΊΡΠΎΡΡ Π΄Π»Ρ ΠΊΠΎΠΌΠΏΠΎΠ½Π΅Π½ΡΠΎΠ²; 9 — ΠΏΡΠΈΠ²ΠΎΠ΄ ΠΌΠ΅ΡΠ°Π»ΠΊΠΈ; 10 — ΡΠ΅Π΄ΡΠΊΡΠΎΡ; 11 — Π±Π°Π»Π»ΠΎΠ½ ΡΠΎ ΡΠΆΠ°ΡΡΠΌ Π°Π·ΠΎΡΠΎΠΌ Π΄Π»Ρ ΠΎΡ Π»Π°ΠΆΠ΄Π΅Π½ΠΈΡ ΠΠΎΠ½ΡΡΡΡΠΊΡΠΈΡ ΡΠΎΡΠΌ Π΄Π»Ρ ΠΆΠΈΠ΄ΠΊΠΎΠ³ΠΎ ΡΠΎΡΠΌΠΎΠ²Π°Π½ΠΈΡ ΠΌΠΎΠΆΠ΅Ρ Π±ΡΡΡ ΡΠ°Π·Π»ΠΈΡΠ½ΠΎΠΉ. ΠΠ»Ρ Π»ΠΈΡΡΡ Π½ΠΈΠ·Π° Π½Π° ΠΎΠ±ΡΠ²ΠΈ ΠΎΠ±ΡΡΠ½ΠΎ ΠΏΡΠΈΠΌΠ΅Π½ΡΡΡΡΡ ΡΠΎΡΠΌΡ ΠΈΠ· ΡΠ΅Ρ ΠΆΠ΅ ΡΠ°ΡΡΠ΅ΠΉ, ΡΡΠΎ ΠΈ Π΄Π»Ρ Π»ΠΈΡΡΡ ΠΏΠΎΠ΄ Π΄Π°Π²Π»Π΅Π½ΠΈΠ΅ΠΌ: ΠΈΠ· Π΄Π²ΡΡ ΠΏΠΎΠ»ΡΠΌΠ°ΡΡΠΈΡ, ΠΏΡΠ°Π½ΡΠΎΠ½Π°, ΠΎΡΠΎΡΠΌΠ»ΡΡΡΠ΅Π³ΠΎ Ρ ΠΎΠ΄ΠΎΠ²ΡΡ ΠΏΠΎΠ²Π΅ΡΡ Π½ΠΎΡΡΡ ΠΏΠΎΠ΄ΠΎΡΠ²Ρ, ΠΈ ΠΊΡΡΡΠΊΠΈ (ΡΠΈΡ. 7). Π ΠΎΠ»Ρ ΠΊΡΡΡΠΊΠΈ ΠΏΡΠΈ Π»ΠΈΡΡΠ΅ ΠΎΠ΄Π½ΠΎΡΠ²Π΅ΡΠ½ΠΎΠ³ΠΎ Π½ΠΈΠ·Π° ΠΈΠ³ΡΠ°Π΅Ρ ΡΠ»Π΅Π΄ Π·Π°ΡΡΠ½ΡΡΠΎΠΉ Π½Π° ΠΊΠΎΠ»ΠΎΠ΄ΠΊΡ ΠΎΠ±ΡΠ²ΠΈ, Π° ΠΏΡΠΈ Π»ΠΈΡΡΠ΅ Π΄Π²ΡΡ ΡΠ²Π΅ΡΠ½ΠΎΠ³ΠΎ Π½ΠΈΠ·Π° — ΠΏΠΎΠΎΡΠ΅ΡΠ΅Π΄Π½ΠΎ ΠΎΠ³ΡΠ°Π½ΠΈΡΠΈΠ²Π°ΡΡΠ°Ρ ΠΊΡΡΡΠΊΠ° (Π΄Π»Ρ Π»ΠΈΡΡΡ ΠΏΠ΅ΡΠ²ΠΎΠ³ΠΎ ΠΌΠ°ΡΠ΅ΡΠΈΠ°Π»Π°) ΠΈ ΡΠ»Π΅Π΄ ΠΎΠ±ΡΠ²ΠΈ (Π΄Π»Ρ Π»ΠΈΡΡΡ Π²ΡΠΎΡΠΎΠ³ΠΎ ΠΌΠ°ΡΠ΅ΡΠΈΠ°Π»Π°), Π°Π½Π°Π»ΠΎΠ³ΠΈΡΠ½ΠΎ ΡΡ Π΅ΠΌΠ΅, ΠΏΠΎΠΊΠ°Π·Π°Π½Π½ΠΎΠΉ Π½Π° ΡΠΈΡ. 8. Π’Π°ΠΊΠΈΠ΅ ΡΠΎΡΠΌΡ Π·Π°ΠΏΠΎΠ»Π½ΡΡΡΡΡ Π² Π·Π°ΠΊΡΡΡΠΎΠΌ Π²ΠΈΠ΄Π΅. ΠΠΎΠ½ΡΡΡΡΠΊΡΠΈΡ ΡΠΎΡΠΌ, Π·Π°ΠΏΠΎΠ»Π½ΡΠ΅ΠΌΡΡ Π² ΠΎΡΠΊΡΡΡΠΎΠΌ Π²ΠΈΠ΄Π΅, ΠΏΡΠΎΡΠ΅. ΠΠ½ΠΈ ΠΌΠΎΠ³ΡΡ ΡΠΎΡΡΠΎΡΡΡ Π»ΠΈΡΡ ΠΈΠ· ΠΊΠΎΡΠΏΡΡΠ° Ρ Π²ΡΠ΅ΠΌΠΊΠΎΠΉ, ΠΏΠΎΠ²Π΅ΡΡ Π½ΠΎΡΡΡ ΠΊΠΎΡΠΎΡΠΎΠΉ ΡΠ²Π»ΡΠ΅ΡΡΡ Π½Π΅Π³Π°ΡΠΈΠ²Π½ΡΠΌ ΠΎΡΠΎΠ±ΡΠ°ΠΆΠ΅Π½ΠΈΠ΅ΠΌ ΡΠΎΡΠΌΡΠ΅ΠΌΠΎΠ³ΠΎ ΠΏΡΠ΅Π΄ΠΌΠ΅ΡΠ°, ΠΈ ΠΊΡΡΡΠΊΠΈ Ρ Π½Π΅ΡΠ»ΠΎΠΆΠ½ΡΠΌ, Π½Π°ΠΏΡΠΈΠΌΠ΅Ρ ΡΡΡΠ°ΠΆΠ½ΡΠΌ, ΠΌΠ΅Ρ Π°Π½ΠΈΠ·ΠΌΠΎΠΌ Π·Π°ΠΏΠΈΡΠ°Π½ΠΈΡ.
Π ΠΈΡΡΠ½ΠΎΠΊ 7. ΠΡΠ΅ΡΡ-ΡΠΎΡΠΌΠ° Π΄Π»Ρ Π»ΠΈΡΡΡ ΠΏΠΎΠ»ΠΈΡΡΠΈΡΠ°Π½ΠΎΠ²: 1 — ΠΏΠΎΠ»ΡΠΌΠ°ΡΡΠΈΡΡ;, 2 — ΠΏΡΠ°Π½ΡΠΎΠ½; 3 — ΡΠΎΡΠΌΠ° Π΄Π»Ρ Π½ΠΎΡΠΊΠ°; 4 — Π»ΠΈΡΠ½ΠΈΠΊΠΎΠ²ΡΠΉ ΠΊΠ°Π½Π°Π»; 5 — ΠΊΠΎΠ»ΠΎΠ΄ΠΊΠ° Π ΠΈΡΡΠ½ΠΎΠΊ 8. Π‘Ρ Π΅ΠΌΠ° ΠΏΡΠΎΡΠ΅ΡΡΠ° Π»ΠΈΡΡΡ Π΄Π²ΡΡ ΡΠ²Π΅ΡΠ½ΠΎΠ³ΠΎ Π½ΠΈΠ·Π° Π½Π° ΠΎΠ±ΡΠ²ΠΈ Π€ΠΎΡΠΌΠ° Π·Π°ΠΏΠΎΠ»Π½ΡΠ΅ΡΡΡ Π² ΡΠΎΠΎΡΠ²Π΅ΡΡΡΠ²ΠΈΠΈ Ρ ΠΆΠ΅Π»Π°Π΅ΠΌΠΎΠΉ ΠΊΠ°ΠΆΡΡΠ΅ΠΉΡΡ ΠΏΠ»ΠΎΡΠ½ΠΎΡΡΡΡ ΠΈΠ·Π³ΠΎΡΠΎΠ²Π»ΡΠ΅ΠΌΠΎΠ³ΠΎ ΠΈΠ·Π΄Π΅Π»ΠΈΡ. ΠΠ°ΠΏΡΠΈΠΌΠ΅Ρ, Π΄Π»Ρ ΠΏΠΎΠ»ΡΡΠ΅Π½ΠΈΡ ΠΏΠ»ΠΎΡΠ½ΠΎΡΡΠΈ 0,4—0,7 Π³/ΡΠΌ3 ΡΠΎΡΠΌΠ° Π·Π°ΠΏΠΎΠ»Π½ΡΠ΅ΡΡΡ Π½Π° 35—60% ΠΎΠ±ΡΠ΅ΠΌΠ°. Π ΠΏΡΠΎΡΠ΅ΡΡΠ΅ ΠΏΡΠΎΡ ΠΎΠΆΠ΄Π΅Π½ΠΈΡ ΡΠ΅Π°ΠΊΡΠΈΠΈ ΠΎΠ±ΡΠ°Π·ΠΎΠ²Π°Π½ΠΈΡ ΠΏΠΎΠ»ΠΈΠΌΠ΅ΡΠ° Π²ΡΠ΄Π΅Π»ΡΡΡΡΡ Π³Π°Π·Ρ (Π‘Π2), ΡΠ²Π΅Π»ΠΈΡΠΈΠ²Π°Π΅ΡΡΡ ΠΎΠ±ΡΠ΅ΠΌ ΡΠΌΠ΅ΡΠΈ, Π·Π°Π½ΠΈΠΌΠ°Ρ Π²Π΅ΡΡ ΠΎΠ±ΡΠ΅ΠΌ ΡΠΎΡΠΌΡ (ΡΠΏΠΎΡΠΎΠ± ΡΠΎΡΡΠ° ΠΌΠ°ΡΡΡ).
Π Π·Π°ΠΊΡΡΡΡΡ ΡΠΎΡΠΌΠ°Ρ Π΄Π»Ρ ΠΆΠΈΠ΄ΠΊΠΎΠ³ΠΎ ΡΠΎΡΠΌΠΎΠ²Π°Π½ΠΈΡ ΠΏΡΠ΅Π΄ΡΡΠΌΠΎΡΡΠ΅Π½Ρ ΠΌΠΈΠΊΡΠΎΠΊΠ°Π½Π°Π»Ρ Π΄Π»Ρ ΠΎΡΠ²ΠΎΠ΄Π° Π²ΠΎΠ·Π΄ΡΡ Π° ΠΏΡΠΈ Π΅Π΅ Π·Π°ΠΏΠΎΠ»Π½Π΅Π½ΠΈΠΈ. ΠΡΠΎΠΌΠ΅ ΡΠΎΠ³ΠΎ, ΠΊΠΎΠ½ΡΡΡΡΠΊΡΠΈΡ Π·Π°ΠΊΡΡΡΡΡ ΡΠΎΡΠΌ ΠΌΠΎΠΆΠ΅Ρ Π±ΡΡΡ ΡΡΡΡΠΎΠ΅Π½Π° ΡΠ°ΠΊ, ΡΡΠΎ ΠΏΠΎΡΠ»Π΅ Π·Π°ΠΏΠΎΠ»Π½Π΅Π½ΠΈΡ ΠΏΡΠ°Π½ΡΠΎΠ½ Π½Π΅ΡΠΊΠΎΠ»ΡΠΊΠΎ ΠΏΠΎΠ΄Π½ΠΈΠΌΠ°Π΅ΡΡΡ ΠΈ Π·Π°ΠΊΡΡΠ²Π°Π΅Ρ Π»ΠΈΡΠ½ΠΈΠΊΠΎΠ²ΡΠΉ ΠΊΠ°Π½Π°Π» Π΄Π»Ρ ΠΏΡΠ΅Π΄ΠΎΡΠ²ΡΠ°ΡΠ΅Π½ΠΈΡ Π²ΡΡΠ΅ΠΊΠ°Π½ΠΈΡ ΡΠ΅Π°ΠΊΡΠΈΠΎΠ½Π½ΠΎΠΉ ΡΠΌΠ΅ΡΠΈ.
ΠΠ°ΠΆΠ½ΠΎΠΉ ΠΎΠΏΠ΅ΡΠ°ΡΠΈΠ΅ΠΉ ΠΏΡΠΈ ΠΆΠΈΠ΄ΠΊΠΎΠΌ ΡΠΎΡΠΌΠΎΠ²Π°Π½ΠΈΠΈ ΠΏΠΎΠ»ΠΈΡΡΠ΅ΡΠ°Π½ΠΎΠ² ΡΠ²Π»ΡΠ΅ΡΡΡ Π°Π½ΡΠΈΠ°Π΄Π³Π΅Π·ΠΈΠΎΠ½Π½Π°Ρ ΠΎΠ±ΡΠ°Π±ΠΎΡΠΊΠ° Π²Π½ΡΡΡΠ΅Π½Π½ΠΈΡ ΠΏΠΎΠ²Π΅ΡΡ Π½ΠΎΡΡΠ΅ΠΉ ΡΠΎΡΠΌΡ Π΄Π»Ρ ΠΏΡΠ΅Π΄ΠΎΡΠ²ΡΠ°ΡΠ΅Π½ΠΈΡ ΠΏΡΠΈΠ»ΠΈΠΏΠ°Π½ΠΈΡ ΠΏΠΎΠ»ΠΈΡΡΠ΅ΡΠ°Π½Π°, ΠΊΠΎΡΠΎΡΡΠΉ ΡΠ²Π»ΡΠ΅ΡΡΡ Π²Π΅ΡΡΠΌΠ° Π°Π΄Π³Π΅Π·ΠΈΠΎΠ½Π½ΠΎΡΠΏΠΎΡΠΎΠ±Π½ΡΠΌ ΠΏΠΎ ΠΎΡΠ½ΠΎΡΠ΅Π½ΠΈΡ ΠΊ ΠΌΠ΅ΡΠ°Π»Π»Π°ΠΌ (ΠΈΠ·ΠΎΡΠΈΠ°Π½ΠΎΠ²ΡΠ΅ Π³ΡΡΠΏΠΏΡ).
Π‘ΡΡΠ΅ΡΡΠ²ΡΡΡ ΡΠ°Π·Π»ΠΈΡΠ½ΡΠ΅ ΡΠΈΠΏΡ ΠΎΠ±ΠΎΡΡΠ΄ΠΎΠ²Π°Π½ΠΈΡ Π΄Π»Ρ ΠΆΠΈΠ΄ΠΊΠΎΠ³ΠΎ ΡΠΎΡΠΌΠΎΠ²Π°Π½ΠΈΡ. Π‘ ΡΠΎΡΠΊΠΈ Π·ΡΠ΅Π½ΠΈΡ ΠΎΡΠ³Π°Π½ΠΈΠ·Π°ΡΠΈΠΈ ΡΠ΅Ρ Π½ΠΎΠ»ΠΎΠ³ΠΈΡΠ΅ΡΠΊΠΎΠ³ΠΎ ΠΏΡΠΎΡΠ΅ΡΡΠ° ΠΎΠ½ΠΈ ΡΠ°Π·Π»ΠΈΡΠ°ΡΡΡΡ Π³Π»Π°Π²Π½ΡΠΌ ΠΎΠ±ΡΠ°Π·ΠΎΠΌ ΠΏΠΎ Π΄Π²ΡΠΌ ΠΏΡΠΈΠ·Π½Π°ΠΊΠ°ΠΌ: ΠΏΠΎ ΠΊΠΎΠ½ΡΡΡΡΠΊΡΠΈΠΈ ΡΠΎΡΠΌΠΎΠ½ΠΎΡΠΈΡΠ΅Π»Ρ ΠΈ ΠΊΠΎΠ½ΡΡΡΡΠΊΡΠΈΠΈ ΠΌΠ΅Ρ Π°Π½ΠΈΠ·ΠΌΠ° Π·Π°ΠΏΠΎΠ»Π½Π΅Π½ΠΈΡ ΡΠΎΡΠΌ. ΠΠΎ ΠΏΠ΅ΡΠ²ΠΎΠΌΡ ΠΏΡΠΈΠ·Π½Π°ΠΊΡ ΡΠ»Π΅Π΄ΡΠ΅Ρ ΡΠ°Π·Π»ΠΈΡΠ°ΡΡ:
* ΡΠΎΡΠΎΡΠ½ΡΠ΅ Π»ΠΈΡΡΠ΅Π²ΡΠ΅ ΠΌΠ°ΡΠΈΠ½Ρ, Π² ΠΊΠΎΡΠΎΡΡΡ ΡΠΎΡΠΌΡ ΡΡΡΠ°Π½ΠΎΠ²Π»Π΅Π½Ρ Π½Π° ΠΊΠ°ΡΡΡΠ΅Π»ΡΠ½ΠΎΠΌ ΡΡΠΎΠ»Π΅ (Π½Π°ΠΏΡΠΈΠΌΠ΅Ρ, «Desma» ΡΠ΅ΡΠΈΠΈ 1511—1516 ΠΈΠ»ΠΈ Π±ΠΎΠ»Π΅Π΅ Π½ΠΎΠ²ΡΠ΅ — ΡΠ΅ΡΠΈΠΈ 521S—526S, ΡΡΡΠ°Π½ΠΎΠ²ΠΊΠΈ Π°Π²ΡΡΡΠΈΠΉΡΠΊΠΎΠΉ ΡΠΈΡΠΌΡ «Π ΠΎlΡΠ΅Π³» ;
* Π»ΠΈΡΡΠ΅Π²ΡΠ΅ ΡΡΡΠ°Π½ΠΎΠ²ΠΊΠΈ, Π² ΠΊΠΎΡΠΎΡΡΡ ΡΠΎΡΠΌΡ ΡΠ°ΡΠΏΠΎΠ»ΠΎΠΆΠ΅Π½Ρ Π½Π° ΡΡΠ°Π½ΡΠΏΠΎΡΡΠ½ΠΎΠΌ ΡΡΡΡΠΎΠΉΡΡΠ²Π΅ Π³ΠΎΡΠΈΠ·ΠΎΠ½ΡΠ°Π»ΡΠ½ΠΎΠ³ΠΎ Π·Π°ΠΌΠΊΠ½ΡΡΠΎΠ³ΠΎ ΠΊΠΎΠ½Π²Π΅ΠΉΠ΅ΡΠ° (ΡΠ°Π·ΡΠ°Π±ΠΎΡΠΊΠΈ ΡΠΈΡΠΌ «Desma» ΠΈ «Πastogran» Π€Π Π); Π·Π°ΠΏΠΎΠ»Π½Π΅Π½ΠΈΠ΅ ΠΏΡΠΈ ΡΡΠΎΠΌ, ΠΊΠ°ΠΊ ΠΏΡΠ°Π²ΠΈΠ»ΠΎ, ΠΏΡΠΎΠΈΠ·Π²ΠΎΠ΄ΠΈΡΡΡ Π² ΠΎΡΠΊΡΡΡΡΠ΅ ΡΠΎΡΠΌΡ;
* Π»ΠΈΡΡΠ΅Π²ΡΠ΅ ΡΡΡΠ°Π½ΠΎΠ²ΠΊΠΈ Ρ ΡΠΎΡΠΌΠ°ΠΌΠΈ Π½Π΅ ΠΏΠ΅ΡΠ΅ΠΌΠ΅ΡΠ°ΡΡΠΈΠΌΠΈΡΡ, Π° Π½Π°Ρ ΠΎΠ΄ΡΡΠΈΠΌΠΈΡΡ Π² ΡΡΠ°ΡΠΈΠΎΠ½Π°ΡΠ½ΠΎΠΌ ΠΏΠΎΠ»ΠΎΠΆΠ΅Π½ΠΈΠΈ, Π½Π°ΠΏΡΠΈΠΌΠ΅Ρ ΡΠ°ΡΠΏΠΎΠ»ΠΎΠΆΠ΅Π½Π½ΡΠΌΠΈ Π½Π° Π½Π΅ΠΏΠΎΠ΄Π²ΠΈΠΆΠ½ΠΎΠΌ ΠΊΡΡΠ³Π»ΠΎΠΌ ΡΡΠΎΠ»Π΅ (ΡΠ°Π·ΡΠ°Π±ΠΎΡΠΊΠ° ΡΠΈΡΠΌΡ «Πlastogran»).
ΠΠ΅Ρ Π°Π½ΠΈΠ·ΠΌΡ Π·Π°ΠΏΠΎΠ»Π½Π΅Π½ΠΈΡ ΡΠΎΡΠΌ ΠΌΠΎΠ³ΡΡ Π±ΡΡΡ ΡΡΠ°ΡΠΈΠΎΠ½Π°ΡΠ½ΡΠΌΠΈ, ΠΏΡΠ΅Π΄ΡΡΠ°Π²Π»ΡΡΡΠΈΠΌΠΈ ΡΠΎΠ±ΠΎΠΉ Π³ΠΎΠ»ΠΎΠ²ΠΊΡ ΡΠΌΠ΅ΡΠΈΡΠ΅Π»Ρ Ρ ΡΠΎΠΏΠ»ΠΎΠΌ, ΠΈ ΠΏΠΎΠ΄Π²ΠΈΠΆΠ½ΡΠΌΠΈ, Π² ΠΊΠΎΡΠΎΡΡΡ ΡΠ°Π·Π»ΠΈΠ²ΠΎΡΠ½Π°Ρ Π³ΠΎΠ»ΠΎΠ²ΠΊΠ° ΡΠΎΠ΅Π΄ΠΈΠ½Π΅Π½Π° ΡΠΎ ΡΠΌΠ΅ΡΠΈΡΠ΅Π»Π΅ΠΌ Π³ΠΈΠ±ΠΊΠΈΠΌ ΡΡΡΠ±ΠΎΠΏΡΠΎΠ²ΠΎΠ΄ΠΎΠΌ ΠΈ Ρ ΠΏΠΎΠΌΠΎΡΡΡ ΠΌΠ°Π½ΠΈΠΏΡΠ»ΡΡΠΎΡΠ° ΠΌΠΎΠΆΠ΅Ρ ΠΏΠ΅ΡΠ΅ΠΌΠ΅ΡΠ°ΡΡΡΡ ΠΎΡ ΡΠΎΡΠΌΡ ΠΊ ΡΠΎΡΠΌΠ΅, ΡΡΠΎ ΡΠ΄ΠΎΠ±Π½ΠΎ ΠΏΡΠΈ Π·Π°ΠΏΠΎΠ»Π½Π΅Π½ΠΈΠΈ ΠΎΡΠΊΡΡΡΡΡ ΡΡΠ°ΡΠΈΠΎΠ½Π°ΡΠ½ΡΡ ΡΠΎΡΠΌ. ΠΡΠΎΠΌΠ΅ ΡΠΎΠ³ΠΎ, Π΄Π»Ρ Π·Π°ΠΏΠΎΠ»Π½Π΅Π½ΠΈΡ ΠΎΡΠΊΡΡΡΡΡ ΡΡΠ°Π½ΡΠΏΠΎΡΡΠΈΡΡΠ΅ΠΌΡΡ ΡΠΎΡΠΌ ΠΏΡΠΈΠΌΠ΅Π½ΡΡΡΡΡ ΡΡΠ°ΡΠΈΠΎΠ½Π°ΡΠ½ΡΠ΅ ΡΠ°Π·Π»ΠΈΠ²ΠΎΡΠ½ΡΠ΅ Π³ΠΎΠ»ΠΎΠ²ΠΊΠΈ, ΡΠΎΠ΅Π΄ΠΈΠ½Π΅Π½Π½ΡΠ΅ ΡΠΎ ΡΠΌΠ΅ΡΠΈΡΠ΅Π»Π΅ΠΌ Π³ΠΈΠ±ΠΊΠΈΠΌ ΡΡΡΠ±ΠΎΠΏΡΠΎΠ²ΠΎΠ΄ΠΎΠΌ.
ΠΡΠΈ Π΄Π²ΡΡ ΡΠ²Π΅ΡΠ½ΠΎΠΌ Π»ΠΈΡΡΠ΅ Π² Π»ΠΈΡΡΠ΅Π²ΠΎΠΌ ΠΎΠ±ΠΎΡΡΠ΄ΠΎΠ²Π°Π½ΠΈΠΈ ΠΏΡΠ΅Π΄ΡΡΠΌΠ°ΡΡΠΈΠ²Π°Π΅ΡΡΡ Π΄Π²Π° ΡΠ·Π»Π° ΡΠΌΠ΅ΡΠ΅Π½ΠΈΡ ΠΈ Π²ΠΏΡΡΡΠΊΠ° ΡΠ΅Π°ΠΊΡΠΈΠΎΠ½Π½ΠΎΠΉ ΡΠΌΠ΅ΡΠΈΠ² ΡΠΎΡΠΌΡ. Π£ΡΡΠ°Π½ΠΎΠ²ΠΊΠΈ ΡΠΎΡΠΎΡΠ½ΠΎΠ³ΠΎ ΡΠΈΠΏΠ° ΡΠΈΡΠΌΡ «Desma», ΠΌΠΎΠ΄Π΅Π»Π΅ΠΉ 5235—5265, ΠΏΡΠ΅Π΄Π½Π°Π·Π½Π°ΡΠ΅Π½Π½ΡΠ΅ Π΄Π»Ρ Π΄Π²ΡΡ ΡΠ²Π΅ΡΠ½ΠΎΠ³ΠΎ Π»ΠΈΡΡΡ, ΠΌΠΎΠ³ΡΡ ΠΈΠΌΠ΅ΡΡ ΠΌΠ΅ΡΠ°Π»Π»ΠΈΡΠ΅ΡΠΊΠΈΠ΅ ΠΎΠ΄ΠΈΠ½Π°ΡΠ½ΡΠ΅ ΠΈΠ»ΠΈ ΡΠ΄Π²ΠΎΠ΅Π½Π½ΡΠ΅ ΠΊΠΎΠ»ΠΎΠ΄ΠΊΠΈ ΠΈΠ»ΠΈ ΠΆΠ΅ Π·Π°ΡΡΠΆΠ½ΡΠ΅ ΡΡΠ΅ΠΌΠ½ΡΠ΅ ΠΊΠΎΠ»ΠΎΠ΄ΠΊΠΈ. Π Π½ΠΈΡ ΠΏΡΠ΅Π΄ΡΡΠΌΠΎΡΡΠ΅Π½Π° Π°Π²ΡΠΎΠΌΠ°ΡΠΈΡΠ΅ΡΠΊΠ°Ρ ΠΎΡΠΈΡΡΠΊΠ° Π³ΠΎΠ»ΠΎΠ²ΠΊΠΈ Π²ΠΏΡΡΡΠΊΠ° ΡΠΌΠ΅ΡΠΈΡΠ΅Π»Ρ Π±Π΅Π· ΠΏΡΠΈΠΌΠ΅Π½Π΅Π½ΠΈΡ ΠΌΠΎΡΡΠΈΡ ΡΡΠ΅Π΄ΡΡΠ². ΠΠΌΠ΅Π΅ΡΡΡ ΡΠΈΡΡΠ΅ΠΌΠ° ΠΏΡΠΎΠ³ΡΠ°ΠΌΠΌΠΈΡΠΎΠ²Π°Π½Π½ΠΎΠ³ΠΎ ΡΠΏΡΠ°Π²Π»Π΅Π½ΠΈΡ ΠΎΡ Π·Π°ΠΏΠΎΠΌΠΈΠ½Π°ΡΡΠ΅Π³ΠΎ ΡΡΡΡΠΎΠΉΡΡΠ²Π° Ρ ΡΠΈΡΡΠΎΠ²ΡΠΌ Π²Π²ΠΎΠ΄ΠΎΠΌ Π²ΡΠ΅Ρ ΠΏΠ°ΡΠ°ΠΌΠ΅ΡΡΠΎΠ² ΠΏΡΠΎΡΠ΅ΡΡΠ°. Π‘Ρ Π΅ΠΌΠ° Π΄Π²ΡΡ ΡΠ²Π΅ΡΠ½ΠΎΠ³ΠΎ Π»ΠΈΡΡΡ Π² Π΄Π°Π½Π½ΠΎΠΌ ΡΠ»ΡΡΠ°Π΅ Π°Π½Π°Π»ΠΎΠ³ΠΈΡΠ½Π° ΠΏΠΎΠΊΠ°Π·Π°Π½Π½ΠΎΠΉ Π½Π° ΡΠΈΡ. 3.15. Π Π·Π°Π²ΠΈΡΠΈΠΌΠΎΡΡΠΈ ΠΎΡ ΠΊΠΎΠ½ΡΡΡΡΠΊΡΠΈΠΈ ΡΠΎΡΠΌΡ Π²ΠΎΠ·ΠΌΠΎΠΆΠ½ΠΎ Π»ΠΈΡΡΠ΅ ΠΏΠΎΠ΄ΠΎΡΠ²Ρ ΠΎΠ΄Π½ΠΎΠ²ΡΠ΅ΠΌΠ΅Π½Π½ΠΎ Ρ Π½ΠΎΡΠΊΠΎΠΌ ΠΈΠ»ΠΈ Π½Π°ΡΡΠΆΠ½ΡΠΌ Π·Π°Π΄Π½ΠΈΠΊΠΎΠΌ. ΠΠ±ΡΠ°Π·ΠΎΠ²Π°Π½ΠΈΠ΅ ΠΏΠΎΠ»ΠΈΡΡΠ΅ΡΠ°Π½Π° ΠΏΡΠΈ ΠΏΠΎΠ»ΡΡΠ΅Π½ΠΈΠΈ Π΅Π³ΠΎ ΠΌΠ΅ΡΠΎΠ΄ΠΎΠΌ ΠΆΠΈΠ΄ΠΊΠΎΠ³ΠΎ ΡΠΎΡΠΌΠΎΠ²Π°Π½ΠΈΡ ΠΏΡΠΎΠΈΡΡ ΠΎΠ΄ΠΈΡ Π² Π½Π΅ΡΠΊΠΎΠ»ΡΠΊΠΎ ΡΡΠ°ΠΏΠΎΠ² ΠΈ Π½Π΅ Π·Π°ΠΊΠ°Π½ΡΠΈΠ²Π°Π΅ΡΡΡ ΠΎΡΠΊΡΡΡΠΈΠ΅ΠΌ ΡΠΎΡΠΌΡ ΠΈ ΠΈΠ·Π²Π»Π΅ΡΠ΅Π½ΠΈΠ΅ΠΌ ΠΎΡΠ»ΠΈΠ²ΠΊΠΈ ΠΈΠ· Π½Π΅Π΅. ΠΠΎΡΠ»Π΅ ΡΡΠΎΠ³ΠΎ Ρ ΠΈΠΌΠΈΡΠ΅ΡΠΊΠΈΠ΅ ΡΠ΅Π°ΠΊΡΠΈΠΈ Π² ΠΌΠ°ΡΡΠ΅ ΠΈΠ·Π΄Π΅Π»ΠΈΡ Π΅ΡΠ΅ ΠΏΡΠΎΠ΄ΠΎΠ»ΠΆΠ°ΡΡΡΡ ΠΈ ΠΏΠΎΠΊΠ°Π·Π°ΡΠ΅Π»ΠΈ ΠΌΠ΅Ρ Π°Π½ΠΈΡΠ΅ΡΠΊΠΈΡ ΡΠ²ΠΎΠΉΡΡΠ² ΠΌΠ°ΡΠ΅ΡΠΈΠ°Π»Π° ΠΏΠΎΠ²ΡΡΠ°ΡΡΡΡ Π΅ΡΠ΅ ΠΎΠΊΠΎΠ»ΠΎ ΡΡΡΠΎΠΊ.
ΠΠΈΡΡΠ΅ Π½ΠΈΠ·Π° Π½Π° ΠΎΠ±ΡΠ²ΠΈ. ΠΠ° ΡΠΈΡ. 9 Π΄Π°Π½Π° ΡΡ Π΅ΠΌΠ° ΠΏΡΠΎΡΠ΅ΡΡΠ° Π»ΠΈΡΡΡ Π½Π° ΡΠΎΡΠΎΡΠ½ΠΎΠΉ 24-ΡΠ΅ΠΊΡΠΈΠΎΠ½Π½ΠΎΠΉ Π»ΠΈΡΡΠ΅Π²ΠΎΠΉ ΠΌΠ°ΡΠΈΠ½Π΅ ΡΠΎ ΡΠΏΠ°ΡΠ΅Π½Π½ΡΠΌΠΈ ΠΌΠ΅ΡΠ°Π»Π»ΠΈΡΠ΅ΡΠΊΠΈΠΌΠΈ ΠΊΠΎΠ»ΠΎΠ΄ΠΊΠ°ΠΌΠΈ (ΡΠΈΡ. 10).ΠΠ°Π³ΠΎΡΠΎΠ²ΠΊΠΈ Π²Π΅ΡΡ Π° ΠΎΠ±ΡΠ²ΠΈ Π½Π°Π΄Π΅Π²Π°ΡΡΡΡ Π½Π° ΠΌΠ΅ΡΠ°Π»Π»ΠΈΡΠ΅ΡΠΊΠΈΠ΅ (ΠΏΠΎΠ΄ΠΎΠ³ΡΠ΅ΡΡΠ΅ Π΄ΠΎ ΡΠ΅ΠΌΠΏΠ΅ΡΠ°ΡΡΡΡ 30— 40 Β°Π‘) ΠΊΠΎΠ»ΠΎΠ΄ΠΊΠΈ ΠΎΠ±ΡΡΠ½ΠΎ Π² ΠΈΠ½ΡΠ΅ΡΠ²Π°Π»Π΅ ΠΌΠ΅ΠΆΠ΄Ρ ΠΏΠΎΠ·ΠΈΡΠΈΡΠΌΠΈ 14—21. Π‘ΠΌΡΠΊΠ°Π½ΠΈΠ΅ ΡΠ°ΡΡΠ΅ΠΉ ΡΠΎΡΠΌΡ ΠΈ ΠΎΠΏΡΡΠΊΠ°Π½ΠΈΠ΅ Π½Π° Π½Π΅Π΅ ΠΊΠΎΠ»ΠΎΠ΄ΠΊΠΈ Ρ ΠΎΠ±ΡΠ²ΡΡ ΠΏΡΠΎΠΈΡΡ ΠΎΠ΄ΠΈΡ Π½Π΅ΠΏΠΎΡΡΠ΅Π΄ΡΡΠ²Π΅Π½Π½ΠΎ ΠΏΠ΅ΡΠ΅Π΄ Π·Π°ΠΏΠΎΠ»Π½Π΅Π½ΠΈΠ΅ΠΌ (//). ΠΠ°ΡΠ΅ΠΌ ΡΠ»Π΅Π΄ΡΠ΅Ρ Π·Π°ΠΏΠΎΠ»Π½Π΅Π½ΠΈΠ΅ ΡΠΎΡΠΌΡ (///). ΠΡΠΈ ΡΡΠΎΠΌ ΡΠΌΠ΅ΡΠΈΡΠ΅Π»Ρ ΡΠΎΠ²Π΅ΡΡΠ°Π΅Ρ ΠΏΠΎΡΡΡΠΏΠ°ΡΠ΅Π»ΡΠ½ΠΎΠ΅ Π΄Π²ΠΈΠΆΠ΅Π½ΠΈΠ΅ (Π΄ΠΎ 200 ΠΌΠΌ) Π²ΠΏΠ΅ΡΠ΅Π΄ ΠΈ ΡΠΎΠΏΠ»ΠΎ ΡΠΎΠ΅Π΄ΠΈΠ½ΡΠ΅ΡΡΡ Ρ ΠΎΡΠ²Π΅ΡΡΡΠΈΠ΅ΠΌ Π»ΠΈΡΠ½ΠΈΠΊΠΎΠ²ΠΎΠ³ΠΎ ΠΊΠ°Π½Π°Π»Π° ΡΠΎΡΠΌΡ. ΠΠ°Π»Π΅Π΅ ΡΠ»Π΅Π΄ΡΠ΅Ρ ΠΎΠ±ΡΠ°Π·ΠΎΠ²Π°Π½ΠΈΠ΅ ΠΏΠΎΠ»ΠΈΡΡΠ΅ΡΠ°Π½Π° ΠΈ ΡΠΎΡΠΌΠΈΡΠΎΠ²Π°Π½ΠΈΠ΅ Π½ΠΈΠ·Π° ΠΎΠ±ΡΠ²ΠΈ (IV—VI), ΠΎΡΠΊΡΡΡΠΈΠ΅ ΡΠΎΡΠΌΡ (V//), ΠΏΠΎΡΠ»Π΅ ΡΠ΅Π³ΠΎ ΠΎΠ±ΡΠ²Ρ Ρ ΠΊΠΎΠ»ΠΎΠ΄ΠΊΠΎΠΉ ΠΏΠΎΠ²ΠΎΡΠ°ΡΠΈΠ²Π°Π΅ΡΡΡ Π² Π²Π΅ΡΡ Π½Π΅Π΅ ΠΏΠΎΠ»ΠΎΠΆΠ΅Π½ΠΈΠ΅ ΠΈ ΠΏΡΠΎΠΈΡΡ ΠΎΠ΄ΠΈΡ Π΄Π°Π»ΡΠ½Π΅ΠΉΡΠ΅Π΅ ΡΠΎΡΠΌΠΈΡΠΎΠ²Π°Π½ΠΈΠ΅ ΠΈ ΡΠΏΡΠΎΡΠ½Π΅Π½ΠΈΠ΅ ΠΌΠ°ΡΠ΅ΡΠΈΠ°Π»Π° Π½ΠΈΠ·Π° (VIII). ΠΠ°ΡΠ΅ΠΌ ΠΎΠ±ΡΠ²Ρ ΡΠ½ΠΈΠΌΠ°Π΅ΡΡΡ Ρ ΠΊΠΎΠ»ΠΎΠ΄ΠΎΠΊ (IX) ΠΈ ΠΏΠΎΡΠ»Π΅Π΄ΡΡΡΠ΅Π΅ ΠΏΡΠΎΠ΄ΠΎΠ»ΠΆΠ΅Π½ΠΈΠ΅ ΡΠ΅Ρ Π½ΠΎΠ»ΠΎΠ³ΠΈΡΠ΅ΡΠΊΠΎΠ³ΠΎ ΠΏΡΠΎΡΠ΅ΡΡΠ° ΠΏΡΠΎΠΈΡΡ ΠΎΠ΄ΠΈΡ ΡΠΆΠ΅ Π²Π½Π΅ Π»ΠΈΡΡΠ΅Π²ΠΎΠΉ ΠΌΠ°ΡΠΈΠ½Ρ.
Π ΠΈΡΡΠ½ΠΎΠΊ 9. Π‘Ρ Π΅ΠΌΠ° ΡΠ΅Ρ Π½ΠΎΠ»ΠΎΠ³ΠΈΡΠ΅ΡΠΊΠΎΠ³ΠΎ ΠΏΡΠΎΡΠ΅ΡΡΠ° Π»ΠΈΡΡΡ ΠΏΠΎΠ»ΠΈΡΡΠ΅ΡΠ°Π½ΠΎΠ²ΠΎΠ³ΠΎ Π½ΠΈΠ·Π° ΠΎΠ±ΡΠ²ΠΈ Π½Π° ΡΠΎΡΠΎΡΠ½ΠΎΠΉ 24-ΡΠ΅ΠΊΡΠΈΠΎΠ½Π½ΠΎΠΉ Π»ΠΈΡΡΠ΅Π²ΠΎΠΉ ΠΌΠ°ΡΠΈΠ½Π΅ ΡΠΎ ΡΠΏΠ°ΡΠ΅Π½Π½ΡΠΌΠΈ ΠΌΠ΅ΡΠ°Π»Π»ΠΈΡΠ΅ΡΠΊΠΈΠΌΠΈ ΠΊΠΎΠ»ΠΎΠ΄ΠΊΠ°ΠΌΠΈ Π ΡΠ΅Ρ Π½ΠΎΠ»ΠΎΠ³ΠΈΠΈ ΠΏΡΠΎΠΈΠ·Π²ΠΎΠ΄ΡΡΠ²Π° ΠΎΠ±ΡΠ²ΠΈ Ρ ΠΏΡΠΈΠΌΠ΅Π½Π΅Π½ΠΈΠ΅ΠΌ ΠΌΠ΅ΡΠΎΠ΄Π° ΠΆΠΈΠ΄ΠΊΠΎΠ³ΠΎ ΡΠΎΡΠΌΠΎΠ²Π°Π½ΠΈΡ Π΄Π»Ρ ΠΎΠ±ΡΠ°Π·ΠΎΠ²Π°Π½ΠΈΡ Π½ΠΈΠ·Π° ΠΈΠ· ΠΏΠΎΠ»ΠΈΡΡΠ΅ΡΠ°Π½ΠΎΠ² ΠΈΠ·Π³ΠΎΡΠΎΠ²Π»Π΅Π½ΠΈΠ΅ Π·Π°Π³ΠΎΡΠΎΠ²ΠΎΠΊ Π²Π΅ΡΡ Π°, ΡΠΎΡΠΌΠΎΠ²Π°Π½ΠΈΠ΅ Π½Π° ΠΊΠΎΠ»ΠΎΠ΄ΠΊΠ΅, ΠΏΠΎΠ΄Π³ΠΎΡΠΎΠ²ΠΊΠ° ΡΠ»Π΅Π΄Π° Π΄Π»Ρ ΠΊΡΠ΅ΠΏΠ»Π΅Π½ΠΈΡ Π½ΠΈΠ·Π°, Π° ΡΠ°ΠΊΠΆΠ΅ Π½Π°Π΄Π΅Π²Π°Π½ΠΈΠ΅ Π·Π°Π³ΠΎΡΠΎΠ²ΠΎΠΊ Π½Π° Π»ΠΈΡΡΠ΅Π²ΡΠ΅ ΠΊΠΎΠ»ΠΎΠ΄ΠΊΠΈ — ΡΠ°ΠΊΠΈΠ΅ ΠΆΠ΅, ΠΊΠ°ΠΊ ΠΏΡΠΈ Π΄ΡΡΠ³ΠΈΡ Π»ΠΈΡΡΠ΅Π²ΡΡ ΠΌΠ΅ΡΠΎΠ΄Π°Ρ . ΠΠ»Ρ Π²Π΅ΡΡ Π° ΠΎΠ±ΡΠ²ΠΈ ΠΈΠ· Π²Π΅Π»ΡΡΠ°, ΡΠ΅ΠΊΡΡΠΈΠ»ΡΠ½ΡΡ ΠΌΠ°ΡΠ΅ΡΠΈΠ°Π»ΠΎΠ², Π½Π΅ΠΊΠΎΡΠΎΡΡΡ ΡΠΈΠ½ΡΠ΅ΡΠΈΡΠ΅ΡΠΊΠΈΡ ΠΊΠΎΠΆ Π½Π΅ ΡΡΠ΅Π±ΡΠ΅ΡΡΡ Π²Π·ΡΠ΅ΡΠΎΡΠΈΠ²Π°Π½ΠΈΡ Π·Π°ΡΡΠΆΠ½ΠΎΠΉ ΠΊΡΠΎΠΌΠΊΠΈ ΠΈ ΠΌΠΎΠΆΠ½ΠΎ Π½Π΅ ΠΏΡΠΈΠΌΠ΅Π½ΡΡΡ ΠΊΠ»Π΅Π΅Π². ΠΠ»Ρ ΠΎΠ±ΡΠ²ΠΈ ΠΈΠ· Π½Π°ΡΡΡΠ°Π»ΡΠ½ΡΡ ΠΊΠΎΠΆ Ρ Π΅ΡΡΠ΅ΡΡΠ²Π΅Π½Π½ΠΎΠΉ Π»ΠΈΠ±ΠΎ Ρ ΠΈΡΠΊΡΡΡΡΠ²Π΅Π½Π½ΠΎΠΉ Π»ΠΈΡΠ΅Π²ΠΎΠΉ ΠΏΠΎΠ²Π΅ΡΡ Π½ΠΎΡΡΡΡ ΡΡΠ΅Π±ΡΠ΅ΡΡΡ Π²Π·ΡΠ΅ΡΠΎΡΠΈΠ²Π°Π½ΠΈΠ΅ Π·Π°ΡΡΠΆΠ½ΠΎΠΉ ΠΊΡΠΎΠΌΠΊΠΈ ΠΈ ΠΏΡΠΈΠΌΠ΅Π½Π΅Π½ΠΈΠ΅ ΠΏΠΎΠ»ΠΈΡΡΠ΅ΡΠ°Π½ΠΎΠ²ΡΡ ΠΊΠ»Π΅Π΅Π². Π£Π΄Π°Π»Π΅Π½ΠΈΠ΅ Π²ΡΠΏΡΠ΅ΡΡΠΎΠ²ΠΎΠΊ ΠΏΡΠΈ ΠΆΠΈΠ΄ΠΊΠΎΠΌ ΡΠΎΡΠΌΠΎΠ²Π°Π½ΠΈΠΈ Π² ΠΎΡΠ»ΠΈΡΠΈΠ΅ ΠΎΡ Π΄ΡΡΠ³ΠΈΡ ΠΌΠ΅ΡΠΎΠ΄ΠΎΠ² Π»ΠΈΡΡΡ Π΄ΠΎΠ»ΠΆΠ½ΠΎ Π²ΡΠΏΠΎΠ»Π½ΡΡΡΡΡ Π²ΡΠΊΠΎΡΠ΅ ΠΏΠΎΡΠ»Π΅ Π·Π°ΠΏΠΎΠ»Π½Π΅Π½ΠΈΡ ΡΠΎΡΠΌΡ (ΡΠ΅ΡΠ΅Π· 15—30 Ρ) Π½Π° ΡΡΠ°Π΄ΠΈΠΈ ΡΠΎΡΠΌΠΈΡΠΎΠ²Π°Π½ΠΈΡ ΠΏΠΎΠ»ΠΈΡΡΠ΅ΡΠ°Π½Π°, ΠΏΠΎΠΊΠ° ΠΌΠ°ΡΠ΅ΡΠΈΠ°Π» Π΅ΡΠ΅ Π½Π΅ ΠΏΡΠΈΠΎΠ±ΡΠ΅Π» Π΄ΠΎΡΡΠ°ΡΠΎΡΠ½ΠΎ Π²ΡΡΠΎΠΊΠΎΠΉ ΠΊΠΎΠ³Π΅Π·ΠΈΠΎΠ½Π½ΠΎΠΉ ΠΏΡΠΎΡΠ½ΠΎΡΡΠΈ ΠΈ Π²ΡΠΏΡΠ΅ΡΡΠΎΠ²ΠΊΠΈ Π»Π΅Π³ΠΊΠΎ ΠΎΡΠ΄Π΅Π»ΠΈΠΌΡ ΠΎΡ ΠΈΠ·Π΄Π΅Π»ΠΈΡ.
Π ΠΈΡΡΠ½ΠΎΠΊ 10. ΠΡΠ΅ΡΡΠΎΠ²ΡΠ΅ ΡΠ·Π»Ρ Π΄Π»Ρ Π»ΠΈΡΡΡ Π½ΠΈΠ·Π° Π½Π° ΠΎΠ±ΡΠ²ΠΈ ΠΊ ΠΌΠ°ΡΠΈΠ½Π΅ D731S (ΡΠΈΡΠΌΠ° «Desma»)
ΠΡΠ΅Π½Ρ Π²Π°ΠΆΠ½ΠΎ, ΡΡΠΎΠ±Ρ ΠΏΠΎΡΠ»Π΅ ΠΎΡΠΊΡΡΡΠΈΡ ΡΠΎΡΠΌΡ ΠΈ ΡΠ½ΡΡΠΈΡ Ρ ΠΊΠΎΠ»ΠΎΠ΄ΠΎΠΊ ΠΏΠΎΠ»ΠΈΡΡΠ΅ΡΠ°Π½ΠΎΠ²ΡΠΉ Π½ΠΈΠ· ΠΈΠΌΠ΅Π» Π²ΠΎΠ·ΠΌΠΎΠΆΠ½ΠΎΡΡΡ Π²ΡΡΡΠΎΡ Π² ΠΏΠΎΠΊΠΎΠ΅ Π΄ΠΎ ΠΏΠΎΡΠ»Π΅Π΄ΡΡΡΠΈΡ ΠΎΠΏΠ΅ΡΠ°ΡΠΈΠΉ Π² ΡΠ΅ΡΠ΅Π½ΠΈΠ΅ ΠΎΠΊΠΎΠ»ΠΎ 8 Ρ, ΡΠ΅Π³ΠΎ Π½Π΅ ΡΡΠ΅Π±ΡΠ΅ΡΡΡ ΠΏΡΠΈ Π΄ΡΡΠ³ΠΈΡ ΠΌΠ΅ΡΠΎΠ΄Π°Ρ Π»ΠΈΡΡΡ. ΠΡΠΈ ΠΏΡΠΎΠ΅ΠΊΡΠΈΡΠΎΠ²Π°Π½ΠΈΠΈ ΡΠ΅Ρ Π½ΠΎΠ»ΠΎΠ³ΠΈΡΠ΅ΡΠΊΠΎΠ³ΠΎ ΠΏΡΠΎΡΠ΅ΡΡΠ° ΡΡΠΎ ΡΠ»Π΅Π΄ΡΠ΅Ρ ΡΡΠ΅ΡΡΡ.
ΠΠ°ΡΠ°Π»Π»Π΅Π»ΡΠ½ΠΎ Ρ ΠΏΠΎΠ΄Π³ΠΎΡΠΎΠ²ΠΊΠΎΠΉ ΠΎΠ±ΡΠ²ΠΈ ΠΊ Π»ΠΈΡΡΡ Π½ΠΈΠ·Π° Π³ΠΎΡΠΎΠ²ΡΡΡΡ ΠΊΠΎΠΌΠΏΠΎΠ½Π΅Π½ΡΡ ΡΠ΅Π°ΠΊΡΠΈΠΎΠ½Π½ΠΎΠΉ ΡΠΌΠ΅ΡΠΈ, Π ΠΈ Π. ΠΠΎΠΌΠΏΠΎΠ½Π΅Π½ΡΡ, Π ΠΈ Π ΠΏΠ΅ΡΠ΅Π΄ ΡΠΌΠ΅ΡΠ΅Π½ΠΈΠ΅ΠΌ ΡΠ΅ΡΠΌΠΎΡΡΠ°ΡΠΈΡΡΡΡΡΡ (ΠΏΠΎΠ΄ΠΎΠ³ΡΠ΅Π²Π°ΡΡΡΡ) ΠΈ Π·Π°ΡΠ΅ΠΌ Π²ΠΏΠ»ΠΎΡΡ Π΄ΠΎ Π·Π°ΠΏΠΎΠ»Π½Π΅Π½ΠΈΡ ΡΠΎΡΠΌΡ ΡΠ΅ΠΌΠΏΠ΅ΡΠ°ΡΡΡΠ½ΡΠΉ ΡΠ΅ΠΆΠΈΠΌ ΡΠΌΠ΅ΡΠΈ Π°Π²ΡΠΎΠΌΠ°ΡΠΈΡΠ΅ΡΠΊΠΈ ΡΠ΅Π³ΡΠ»ΠΈΡΡΠ΅ΡΡΡ.
Π£ΡΡΠ°Π½ΠΎΠ²ΠΈΡΡ ΠΎΡΠΈΠ΅Π½ΡΠΈΡΠΎΠ²ΠΎΡΠ½ΡΠ΅ Π²ΡΠ΅ΠΌΠ΅Π½Π½ΡΠ΅ ΡΠ΅ΠΆΠΈΠΌΡ Π΄Π»Ρ ΠΊΠΎΠ½ΠΊΡΠ΅ΡΠ½ΠΎΠ³ΠΎ ΡΠΎΡΡΠ°Π²Π° ΡΠ΅Π°ΠΊΡΠΈΠΎΠ½Π½ΠΎΠΉ ΡΠΌΠ΅ΡΠΈ ΠΌΠΎΠΆΠ½ΠΎ Π½Π΅ΡΠ»ΠΎΠΆΠ½ΡΠΌ Π»Π°Π±ΠΎΡΠ°ΡΠΎΡΠ½ΡΠΌ ΠΌΠ΅ΡΠΎΠ΄ΠΎΠΌ. ΠΠ»Ρ ΡΡΠΎΠ³ΠΎ Π² ΠΎΠ±ΡΡΠ½ΠΎΠΌ Π»Π°Π±ΠΎΡΠ°ΡΠΎΡΠ½ΠΎΠΌ ΡΡΠ°ΠΊΠ°Π½Π΅ ΡΠΌΠ΅ΡΠΈΠ²Π°ΡΡΡΡ ΠΊΠΎΠΌΠΏΠΎΠ½Π΅Π½ΡΡ, Π ΠΈ Π ΠΈ ΡΠΈΠΊΡΠΈΡΡΠ΅ΡΡΡ Π²ΡΠ΅ΠΌΡ Π½Π°ΡΠ°Π»Π° Ρ ΠΈΠΌΠΈΡΠ΅ΡΠΊΠΎΠΉ ΡΠ΅Π°ΠΊΡΠΈΠΈ, ΡΠΎΡΡΠ° ΠΌΠ°ΡΡΡ (ΠΏΠΎΡΠΎΠΎΠ±ΡΠ°Π·ΠΎΠ²Π°Π½ΠΈΠ΅) ΠΈ ΡΠΎΡΠΌΠΈΡΠΎΠ²Π°Π½ΠΈΡ ΠΌΠ°ΡΠ΅ΡΠΈΠ°Π»Π°. ΠΡΠΈ Π²ΡΠ΅ΠΌΠ΅Π½Π½ΡΠ΅ ΠΏΠ°ΡΠ°ΠΌΠ΅ΡΡΡ ΠΌΠΎΠ³ΡΡ Π±ΡΡΡ Π±Π»ΠΈΠ·ΠΊΠΈΠΌΠΈ ΠΊ ΡΠ°ΠΊΠΎΠ²ΡΠΌ Π² ΡΠΎΡΠΌΠ΅, Π΅ΡΠ»ΠΈ Π² Π»Π°Π±ΠΎΡΠ°ΡΠΎΡΠ½ΠΎΠΌ ΡΡΠ°ΠΊΠ°Π½Π΅ ΡΠΎΠ·Π΄Π°ΡΡ ΡΠ΅ΠΆΠΈΠΌ ΡΠ΅ΡΠΌΠΎΡΠ΅Π³ΡΠ»ΠΈΡΠΎΠ²Π°Π½ΠΈΡ (ΠΎΡ Π»Π°ΠΆΠ΄Π΅Π½ΠΈΠ΅) ΠΊΠ°ΠΊ ΠΈ Π΄Π»Ρ ΡΠΎΡΠΌΡ Π² ΠΏΡΠΎΠΌΡΡΠ»Π΅Π½Π½ΠΎΠΉ ΡΡΡΠ°Π½ΠΎΠ²ΠΊΠ΅.
ΠΠ°ΠΊΠ»ΡΡΠ΅Π½ΠΈΠ΅
ΠΠ΄Π½ΠΈΠΌ ΠΈΠ· ΠΎΡΠ½ΠΎΠ²Π½ΡΡ Π½Π°ΠΏΡΠ°Π²Π»Π΅Π½ΠΈΠΉ ΡΠΎΠ²Π΅ΡΡΠ΅Π½ΡΡΠ²ΠΎΠ²Π°Π½ΠΈΡ ΠΈ ΡΠ°Π·Π²ΠΈΡΠΈΡ ΠΎΠ±ΡΠ²Π½ΠΎΠΉ ΠΈ ΠΊΠΎΠΆΠ³Π°Π»Π°Π½ΡΠ΅ΡΠ΅ΠΉΠ½ΠΎΠΉ ΠΏΡΠΎΠΌΡΡΠ»Π΅Π½Π½ΠΎΡΡΠΈ ΡΠ²Π»ΡΠ΅ΡΡΡ Ρ ΠΈΠΌΠΈΠ·Π°ΡΠΈΡ, Π·Π°ΠΊΠ»ΡΡΠ°ΡΡΠ°ΡΡΡ Π² ΠΏΡΠΈΠΌΠ΅Π½Π΅Π½ΠΈΠΈ ΡΠΈΠ½ΡΠ΅ΡΠΈΡΠ΅ΡΠΊΠΈΡ ΠΈ ΠΈΡΠΊΡΡΡΡΠ²Π΅Π½Π½ΡΡ ΠΌΠ°ΡΠ΅ΡΠΈΠ°Π»ΠΎΠ² ΠΈ Π½ΠΎΠ²ΡΡ ΡΠΏΠΎΡΠΎΠ±ΠΎΠ² ΠΎΠ±ΡΠ°Π±ΠΎΡΠΊΠΈ ΠΌΠ°ΡΠ΅ΡΠΈΠ°Π»ΠΎΠ² ΠΈ Π΄Π΅ΡΠ°Π»Π΅ΠΉ ΠΎΠ±ΡΠ²ΠΈ ΠΈΠ· Π½ΠΈΡ .
ΠΡΠΏΠΎΠ»ΡΠ·ΠΎΠ²Π°Π½ΠΈΠ΅ ΡΠΈΠ½ΡΠ΅ΡΠΈΡΠ΅ΡΠΊΠΈΡ ΠΈ ΠΈΡΠΊΡΡΡΡΠ²Π΅Π½Π½ΡΡ ΠΌΠ°ΡΠ΅ΡΠΈΠ°Π»ΠΎΠ², ΠΎΡΠ»ΠΈΡΠ°ΡΡΠΈΡ ΡΡ ΠΎΡ Π½Π°ΡΡΡΠ°Π»ΡΠ½ΡΡ ΡΠ°Π²Π½ΠΎΠΌΠ΅ΡΠ½ΠΎΡΡΡΡ ΡΠ²ΠΎΠΉΡΡΠ² ΠΏΠΎ Π²ΡΠ΅ΠΉ ΠΏΠ»ΠΎΡΠ°Π΄ΠΈ ΠΈ ΠΎΡΡΡΡΡΡΠ²ΠΈΠ΅ΠΌ Π΄Π΅ΡΠ΅ΠΊΡΠΎΠ² Π»ΠΈΡΠ΅Π²ΠΎΠΉ ΠΏΠΎΠ²Π΅ΡΡ Π½ΠΎΡΡΠΈ, ΠΏΠΎΠ·Π²ΠΎΠ»ΡΠ΅Ρ ΡΠ°ΠΊΠΆΠ΅ Π΄ΠΎΠ±ΠΈΡΡΡΡ Π±ΠΎΠ»ΡΡΠΎΠ³ΠΎ ΡΠΊΠΎΠ½ΠΎΠΌΠΈΡΠ΅ΡΠΊΠΎΠ³ΠΎ ΡΡΡΠ΅ΠΊΡΠ° Π² ΡΠ΅Π·ΡΠ»ΡΡΠ°ΡΠ΅ Π»ΡΡΡΠ΅Π³ΠΎ ΠΈΡΠΏΠΎΠ»ΡΠ·ΠΎΠ²Π°Π½ΠΈΡ ΠΌΠ°ΡΠ΅ΡΠΈΠ°Π»ΠΎΠ² ΠΏΡΠΈ ΡΠ°ΡΠΊΡΠΎΠ΅, ΡΠΌΠ΅Π½ΡΡΠ΅Π½ΠΈΡ ΠΏΡΠΈΠΏΡΡΠΊΠΎΠ² Π½Π° ΠΎΠ±ΡΠ°Π±ΠΎΡΠΊΡ, ΠΏΠΎΠ²ΡΡΠ΅Π½ΠΈΡ ΠΏΡΠΎΠΈΠ·Π²ΠΎΠ΄ΠΈΡΠ΅Π»ΡΠ½ΠΎΡΡΠΈ ΡΡΡΠ΄Π° ΠΏΡΠΈ ΠΏΡΠΈΠΌΠ΅Π½Π΅Π½ΠΈΠΈ ΠΌΠ΅ΡΠΎΠ΄ΠΎΠ² Π»ΠΈΡΡΡ, ΡΠ²Π°ΡΠΊΠΈ ΠΈ Π²ΡΠ»ΠΊΠ°Π½ΠΈΠ·Π°ΡΠΈΠΈ. ΠΡΠ΅ ΡΡΠΎ Π² ΡΠ²ΠΎΡ ΠΎΡΠ΅ΡΠ΅Π΄Ρ ΠΏΡΠΈΠ²ΠΎΠ΄ΠΈΡ ΠΊ ΡΠ½ΠΈΠΆΠ΅Π½ΠΈΡ ΡΠ΅Π±Π΅ΡΡΠΎΠΈΠΌΠΎΡΡΠΈ ΠΈΠ·Π΄Π΅Π»ΠΈΠΉ ΠΈΠ· ΠΊΠΎΠΆΠΈ, Π² ΠΊΠΎΡΠΎΡΠΎΠΉ Π·Π°ΡΡΠ°ΡΡ Π½Π° ΠΌΠ°ΡΠ΅ΡΠΈΠ°Π»Ρ ΡΠΎΡΡΠ°Π²Π»ΡΡΡ 80—85%.
1. ΠΡΠ°ΡΠ½ΠΎΠ² Π. Π―. ΠΠ°ΡΠ΅ΡΠΈΠ°Π»Ρ Π΄Π»Ρ ΠΈΠ·Π΄Π΅Π»ΠΈΠΉ ΠΈΠ· ΠΊΠΎΠΆΠΈ / Π. Π―. ΠΡΠ°ΡΠ½ΠΎΠ². — Π.: ΠΠ΅Π³ΠΊΠ°Ρ ΠΈ ΠΏΠΈΡΠ΅Π²Π°Ρ ΠΏΡΠΎΠΌΡΡΠ»Π΅Π½Π½ΠΎΡΡΡ, 1981. — 344 Ρ.
2.Π Π°ΡΡΠΊΠ°Ρ Π. Π. Π’Π΅Ρ Π½ΠΎΠ»ΠΎΠ³ΠΈΡ ΠΈΠ·Π΄Π΅Π»ΠΈΠΉ ΠΈΠ· ΠΊΠΎΠΆΠΈ.: Π£ΡΠ΅Π±Π½ΠΈΠΊ Π΄Π»Ρ Π²ΡΠ·ΠΎΠ². Π 2-Ρ Ρ. Π§.2. / Π Π°ΡΡΠΊΠ°Ρ Π. Π., ΠΠ΅ΡΡΠ΅ΡΠΎΠ² Π. Π.; ΠΠΎΠ΄ ΡΠ΅Π΄. Π. Π. Π€ΡΠΊΠΈΠ½Π°.— Π.: ΠΠ΅Π³ΠΏΡΠΎΠΌΠ±ΡΡΠΈΠ·Π΄Π°Ρ, 1988.— 320 Ρ.
3. Π€ΡΠΊΠΈΠ½ Π. Π. Π’Π΅Ρ Π½ΠΎΠ»ΠΎΠ³ΠΈΡ ΠΈΠ·Π΄Π΅Π»ΠΈΠΉ ΠΈΠ· ΠΊΠΎΠΆΠΈ.: Π£ΡΠ΅Π±Π½ΠΈΠΊ Π΄Π»Ρ Π²ΡΠ·ΠΎΠ². Π 2-Ρ Ρ. Π§.1 / Π. Π. Π€ΡΠΊΠΈΠ½, Π. Π. ΠΠ΅ΡΡΠ΅ΡΠΎΠ²; ΠΠΎΠ΄ ΡΠ΅Π΄. Π. Π. Π€ΡΠΊΠΈΠ½Π°. — Π.: ΠΠ΅Π³ΠΏΡΠΎΠΌΠ±ΡΡΠΈΠ·Π΄Π°Ρ, 1988.— 272 Ρ.