Технология получения гранитных блоков без взрывным способом
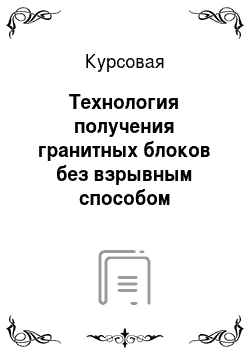
Взрывные работы в карьере производятся силами ООО «Евровзрывпром», обладающим лицензией на право применения и хранения взрывчатых материалов. Проведение взрывных работ осуществляется при наличии паспорта БВР на зарядку блоков, в котором указан тип ВВ, конструкция заряда в шпуре, схема коммутации заряда, направление и место инициирования, размеры блока, общий расход ВВ, СВ и определены основные… Читать ещё >
Технология получения гранитных блоков без взрывным способом (реферат, курсовая, диплом, контрольная)
Технологический процесс по добыче гранита зачастую сравнивают с настоящим искусством. Иногда отделения монолита от горного массива представляет собой сложную задачу.
Основным показателем, характеризующим ценность месторождения блочного камня (мрамор, гранит, известняк и т. п.) и совершенство технологии его разработки, служит выход блоков заданной крупности («извлечение») из добываемого объема полезного ископаемого. На карьере ООО «Возрождение» используется буровзрывной метод добычи полезного ископаемого, который несет в себе ряд проблем. Прежде всего это маленький процентный выход блоков. При отделении монолита от массива с помощью взрыва, камень под действием взрывной волны трескается и теряет свою целостность, а следовательно и ценность. С развитием строительства на северо-западе потребность в добываемом полезном ископаемом растет, но предприятие не успевает вырабатывать нужное количество продукции, в то время как количество заказчиков увеличивается. Данное месторождение имеет ряд особенностей, одно из которых, это наличие горизонтальных трещин, которые располагаются по мере углубления на расстоянии 6−7 м. друг от друга. С течением времени глубина карьера росла, и трещины постепенно стали пропадать.
Разработка месторождений связана с проведением в горных породах выработок, которые нарушают в массиве сложившееся равновесие. Восстановление равновесия массива приводит к деформациям выработок и созданию в массиве полей напряжений, суперпозиция которых с локальными полями напряжений, вызванных воздействием горных работ на породу, изменяет первоначальное поле напряжений и приводит к росту их значений вблизи горных выработок, вызывая в них необратимые деформации.
Так же при работах на нижележащих горизонтах массив испытывает большое давление, что осложняет ведение буровзрывных работ.
В совокупности эти особенности месторождения заставляют задуматься о способах решения представленных проблем.
1. Анализ существующей на карьере технологии, механизации и организации производства.
1.1 Краткая характеристика горно-геологических условий карьера
Месторождение гранитов «Возрождение» находится в центральной части Карельского перешейка в Выборгском районе Ленинградской области в 23 км от города Выборга и в 2 км от жилого поселка «Возрождение» и занимает площадь около 400 га.
В пределах Участка № 8 разведочными выработками и карьером вскрыты следующие разновидности пород Трахитоидные серые граниты (?31 R1v).
Порфировидные розовые граниты (?32 R1v) — «форель».
Крупноовоидные граниты (выборгиты) (?2R1v).
Жилы аплитов и пегматитов (р R2v).
Добыча гранитов для производства блочного камня на месторождении «Возрождение», участок № 8 производится силами ООО «Выборгские граниты».
Размеры участка № 8 в плане по промышленным категориям разведки: длина- 640 м, ширина — 250 м, площадь — около 16 Га.
Абсолютные отметки поверхности участка № 8 на сегодняшний день колеблются в пределах от -12 м до +26 м.
С 2004 г началось постепенное снижение выхода (в среднем 33,26%, в том числе 26,65% блоков I-IIIгрупп в среднем за 2004;2006гг.) за счет вовлечения в отработку центральной, юго-восточной и юго-западной зон карьерного поля и усложнения структурно-тектонических условий месторождения за счет проявлений разгрузок горного давления (разрушение пород и трещинообразование) при углубке карьера.
Структурно-тектоническая обстановка на участке постоянно изменяется в результате периодически возникающих разгрузок массива и связанным с этим процессом образованием трещин по мере проходки карьера, в особенности при его продвижении на более глубокие горизонты.
На месторождении имеются два водоносных горизонта — один приурочен к четвертичным отложениям, другой — к гранитам.
Режим водоносных горизонтов непостоянен и зависит от выпадения осадков и снеготаяния. Грунтовые воды, приуроченные к гранитам, циркулируют по трещинам.
Запасы гранитов на участке 8 месторождения «Возрождение» по следующим категориям:
запасы категории В — 774,0 тыс. м3;
запасы категории С1 — 5456,0 тыс. м3;
всего запасов категории В+С1 — 6230,0 тыс. м3;
запасы категории С2 — 1852,0 тыс. м3;
всего запасов категории В+С1+С2 — 8082,0 тыс. м3.
В соответствии с данными формы 5-гр по состоянию на 01.01.2013 г. на балансе предприятия состояли запасы гранитов по следующим категориям:
запасы категории В — 685,6 тыс. м3;
запасы категории С1 — 4997,9 тыс. м3;
всего запасов категории В+С1 — 5683,5 тыс. м3;
запасы категории С2 — 1852,0 тыс. м3;
всего запасов категории В+С1+С2 — 7535,5 тыс. м3.
Обеспеченность запасами гранита достаточная для промышленной разработки месторождения при планируемом годовом объеме производства блоков I-III категории в количестве 15 200 м?.
Организация производства Планируемый объем разработки скальной горной массы в 2014 г. составит 76 тыс. м3 при планируемом выходе блоков I-III категории 20%.
Качество гранитов как сырья для производства облицовочных материалов и архитектурно-строительных изделий соответствует требованиям следующих государственных стандартов, технологических условий:
ГОСТ 9479–2011 «Блоки из горных пород для производства облицовочных, архитектурно-строительных, мемориальных и других изделий»;
ГОСТ 9480–77 «Плиты облицовочные из природного камня»;
ГОСТ 23 342–91 «Изделия архитектурно-строительные из природного камня».
Граниты месторождения «Возрождение» относятся к IX-X группе пород по СНиП IV-5−82.
1.2 Вскрытие месторождения и применяемая система разработки
Для вскрытия месторождения применялся метод создания фланговой вертикальной траншеи, направленной внутрь карьера, путем производства двух разрезов.
Система разработки месторождения — транспортная. Все принимаемые к отработке горизонты уступов вскрыты посредством устройства на них автодорог, имеющих транспортную связь с промышленной площадкой карьера и отвалом вскрышных пород и окола от производства блоков.
В 2014 г. горные работы будут производиться в контуре границ горного и земельного отвода месторождения.
Система полого залегающих трещин, по которым формируется подошва горизонта, имеет угол наклона в среднем 6. В этой связи, отработка месторождения производится по подстилающим трещинам и условно разделяется на блоки, расположение которых может меняться в пределах принятых рабочих горизонтов, и ограничивается вертикальными природными или искусственными трещинами.
Массив гранитов предусматривается отрабатывать уступами высотой
до 6,0 м с разделением на подступы (2,0 м — 4,0 м) в зависимости от рельефа кровли залежи и конкретных проявлений естественной трещиноватости.
На небольших участках месторождения высота добычного уступа может достигать 7,0 м, что не ухудшает безопасных условий производства работ.
Угол откоса уступа принимается равным 90°
Ширина рабочей площадки 30,0 м.
В 2014 г. отработка месторождения будет производиться 4-мя блоками. На 01.11.2013 г. блоки расположены в пределах следующих горизонтов:
блок 9 — в пределах горизонта на отм. «+4,0 м» в юго-восточном направлении в пределах горизонта на отм. «-9,0 м» в юго-восточном направлении блок 10- в пределах горизонта на отм. «+3,0 м» в юго-западном направлении в пределах горизонта на отм. «-12,0 м» в юго-западном направлении блок 11 — в пределах горизонта на отм. «-9,0 м» в северо-западном направлении блок 12-в пределах горизонта на отм. «-9,0м» в северо-восточном направлении
1.3 Механизация работ
Вскрышные и отвальные работы.
На карьере планируются вскрышные работы в объеме 3,5 тыс. м3
На отвале предусмотрены работы по переработке окола (побочного продукта).
Транспортирование горной массы и вскрыши в отвал предусмотрено автосамосвалом БелАЗ-7540 грузоподъемностью 30 т.
Погрузка горной массы и вскрыши в автотранспорт будет осуществляться погрузчиками «САТ- 988» с ковшом емкостью 5,0 м³.
Планировочные работы на отвале предусмотрено осуществлять имеющимся на предприятии бульдозером Б-10М в соответствии с паспортом отвала.
Добычные работы.
Отрыв монолитного камня от массива производится буровзрывным способом, с применением щадящих взрывчатых средств (черный порох, гранилен).
Бурение массива производится станками «Коммандо» и «Триммер» фирмы «SANDVIK». Шпуры диаметром 32 мм располагаются в один ряд на расстоянии
0,15−0,4 м друг от друга.
Пробуренные шпуры заряжаются порохом или «Граниленом» и взрываются. Взрывные работы производятся специализированной организацией ООО «Евровзрывпром» по договору подряда в соответствии с паспортом на производство взрывных работ по добыче штучного камня на блочном гранитном карьере «Возрождение» ООО «Выборгские граниты».
В результате взрыва происходит отделение монолита от массива. Уступы высотой более 6 м разбиваются на два, при необходимости на три и более подуступа, приуроченных к естественным полого падающим и горизонтальным слоям.
Отделенный от массива монолит, разделывается буро-взрывным или буроклиновым способом на блоки-заготовки.
С помощью фронтальных погрузчиков САТ-980, САТ-988 блоки-заготовки перемещаются на ровную площадку подошвы уступа для их дальнейшей разделки буроклиновым способом на мерные блоки и на заготовки гранитных изделий.
В случае монолитности камня, срастания трещин производится горизонтальное бурение по планируемой подошве подуступа.
Определяющим фактором в этом процессе является использование плоскостей вертикальных постельных (пологопадающих) систем трещин. При отсутствии постельной (пологопадающей) трещины подошва уступа формируется искусственно бурением горизонтальной строчки шпуров по подошве отделяемых монолитов.
С целью создания дополнительных плоскостей обнажения (щелей) применяется буровой станок «Пантера — 800», (скважины O 76 мм, с разбуркой перемычек O 89 мм).
Работы по переработке окола.
На карьере месторождения «Возрождение» все работы по переработке окола (побочного продукта) будут осуществляться в соответствии с требованиями:
— «Единых правил безопасности при разработке месторождений полезных ископаемых открытым способом» ПБ 03−498−02
— «Единые правила безопасности при дроблении, сортировке, обогащении полезных ископаемых и окусковании руд и концентратов» ПБ 03−571−03.
В карьере после основного вида работ (добыча блоков): отделения монолитов от общего массива, их разделки буро-взрывным или буроклиновым способом на блоки-заготовки и дальнейшей пассировки на блоки заданных размеров, остается негабаритная горная масса (окол). Габаритный размер окола достигает до 2000 мм в ребре.
Технологическая схема производства щебня из отходов блочного производства на карьере «Возрождение» включает в себя следующие этапы:
1. Дробление окола в карьере до требуемой крупности кусков горной массы.
2. Загрузка подготовленной горной массы в головную дробилку
3. Первичное дробление подготовленной горной массы
4. Транспортирование дробленной горной массы на вторичное дробление
5. Вторичное дробление (готовая продукция)
6. Вывоз готовой продукции Дробление материала происходит посредством щековой дробилки за счёт сжатия материала между двумя щёковыми плитами, одна из которых является подвижной, а другая неподвижной. Подвижная щёковая плита движется по эллипсоидной траектории и тем самым разрушает материал о неподвижную щёковую плиту. Нижний край подвижной щеки имеет возможность регулировки положения в горизонтальном направлении, которое влияет на ширину минимальной щели, определяющую максимальную крупность материала на выходе из дробилки. Щёки образуют клинообразную форму камеры дробления в которой материал под действием силы тяжести и после разрушения продвигается от верхней части, в которую загружаются крупные куски, до выходной (разгрузочной) щели.
Приемочное отверстие щековой дробилки позволяет дробить материал крупностью до 600 мм, размер фракции на выходе 0−150 мм, далее материал поступает в конусную дробилку.
Дробление камня 0−150 мм в конусной дробилке происходит в пространстве, образованном поверхностями двух усеченных конусов: наружный остается неподвижный, внутренний вращается. Размер выходной щели меняется в зависимости от высоты, на которую перемещается подвижный конус, вследствие чего получаем дробленый материал крупностью 0−40мм. Далее материал поступает на грохот, где и происходит сортировка на фр. 0−5мм, 5−20мм и 20−40мм.
ДСУ фирмы «Sandvik» или аналогичное оборудование, размещается на открытой площадке в карьере или на складе окола в пределах земельного отвода.
Готовая продукция складируется на открытых конусных складах и отгружается погрузчиками САТ — 988 в автомобильный транспорт потребителей.
Взрывные работы.
В качестве ВВ применяются дымный порох и патроны гранилена ЗЭТ. Способ инициирования зарядов электрический.
Взрывные работы в карьере производятся силами ООО «Евровзрывпром», обладающим лицензией на право применения и хранения взрывчатых материалов. Проведение взрывных работ осуществляется при наличии паспорта БВР на зарядку блоков, в котором указан тип ВВ, конструкция заряда в шпуре, схема коммутации заряда, направление и место инициирования, размеры блока, общий расход ВВ, СВ и определены основные мероприятия по технике безопасности.
Параметры безопасных расстояний при взрывных работах определены в соответствии с требованиями главы VIII «Порядок определения безопасных расстояний при взрывных работах и хранении ВМ», ПБ13−407−01.
На время производства взрывных работ в карьере:
все люди выводятся за пределы границы опасной зоны;
подъездная автодорога на границе опасной зоны перекрывается шлагбаумом;
за пределами опасной зоны по разлету кусков от границ карьера устанавливаются щиты с предупредительными надписями;
на границах опасной зоны перед началом заряжания выставляются посты, обеспечивающие охрану опасной зоны;
порядок и график перекрытия автодорог при взрывных работах согласовывается в соответствии с действующими правилами.
Технологический транспорт.
Карьерный транспорт осуществляет перевозки горной массы (окола) и вскрышных пород в отвал (склад). Транспортирование планируемых объемов горной массы и вскрышных пород предусмотрено осуществлять автосамосвалами БелАЗ-7540 грузоподъемностью 30 т.
Потребный рабочий парк автосамосвалов БелАЗ-7540 (при проектной производительности 1760 т/смену или 1250м3/смену) составляет 1 машину в смену.
1.4 Работа вспомогательных участков служб
Вспомогательный участок — склад товарных блоков Контроль за приемкой товарных блоков осуществляет контролер Отдела Контроля Качеством (ОКК) в соответствии с требованиями ГОСТ 9479–2011 «Блоки из горных пород для производства облицовочных, архитектурно-строительных, мемориальных и других изделий».
Испытание блоков проводятся в соответствии с ГОСТ 30 629–99 «Материалы и изделия облицовочные из горных пород.
Ремонт оборудования.
Ремонтная служба на карьере предназначена для поддержания оборудования в рабочем состоянии.
Ремонт оборудования предусмотрено производить по системе планово-предупредительных ремонтов сменно-узловым методом.
Мелкий текущий ремонт оборудования предусмотрено производить непосредственно в карьере.
Техническое обслуживание, средний и капитальный ремонт оборудования предусмотрено производить в специализированном боксе на промышленной площадке силами ремонтной службы предприятия и специализированных организаций.
Снабжение горного оборудования запасными частями предусмотрено производить с материального склада «УК «ГУ ПО «Возрождение».
Хранение горюче-смазочных материалов на промышленной площадке карьера не предусматривается.
Снабжение оборудования дизельным топливом предусмотрено производить специальным автомобилем-заправщиком по договору поставки со специализированной организацией.
Заправку самоходного карьерного оборудования, передвижных дизельных компрессоров и буровых станков предусмотрено производить непосредственно в карьере.
На товарные блоки имеются санитарно-эпидемиологическое заключение и сертификаты качества
1.5 Организация труда и производства
Режим работы карьера круглогодовой вахтовым методом с непрерывной рабочей неделей (пять через пять дней) продолжительность смены 12 часов.
Средняя заработная плата на карьере 25 000 рублей в месяц.
1.6 Экономические показатели работы карьера
Планируемый объем разработки скальной горной массы в 2014 г. составит 95,9 тыс. м3 при планируемом выходе блоков I-III категории 19,8%.
На карьере задействован персонал в количестве, 21 человек.
Таблица 1.6.1 Расчетные величины годовой, суточной и сменной производительности карьера по добыче гранитов по кварталам 2014 г
Вид работ | Показатели. | Ед. изм. | Объемы производства | |||||
всего | в том числе по кварталам | |||||||
I | II | III | IV | |||||
Добыча гранитов | Годовой объем работ | тыс. м3 | ||||||
Количество рабочих дней | дней | |||||||
Суточный объем работ | м3 | |||||||
Сменный объем работ | м3 | |||||||
Таблица 1.6.2 Планируемых объемов производства добычных работ по блокам и по кварталам в 2014 г.
блоки | Наименование | Ед. изм. | Объемы производства | |||||
Всего | в том числе по кварталам | |||||||
Ide | II | III | IV | |||||
Горизонт «-12 « | ||||||||
Блок 10 | Горная масса | м3 | ||||||
Объем блоков | м3 | |||||||
Выход блоков | % | 15,0 | 8,0 | 16,0 | 18,0 | 18,0 | ||
Горизонт «-9 « | ||||||||
Блок 9 | Горная масса | м3 | ||||||
Объем блоков | м3 | |||||||
Выход блоков | % | 19,7 | 21,0 | 12,6 | 17,6 | 27,9 | ||
Блок 11 | Горная масса | м3 | ; | |||||
Объем блоков | м3 | ; | ||||||
Выход блоков | % | 25,7 | 30,8 | 35,0 | ; | 10,0 | ||
Блок 12 | Горная масса | м3 | ; | |||||
Объем блоков | м3 | ; | ||||||
Выход блоков | % | 36,7 | 35,0 | 37,8 | 36,4 | ; | ||
Горизонт «+3 « | ||||||||
Блок 10 | Горная масса | м3 | ||||||
Объем блоков | м3 | |||||||
Выход блоков | % | 12,4 | 3,5 | 21,6 | 23,2 | |||
Горизонт «+4 « | ||||||||
Блок 9 | Горная масса | м3 | ; | |||||
Объем блоков | м3 | ; | ||||||
Выход блоков | % | 16,0 | ; | 16,0 | 16,0 | 16,0 | ||
Итого | Горная масса | м3 | ||||||
Объем блоков | м3 | |||||||
Выход блоков | % | 19,1 | 16,1 | 22,3 | 22,3 | |||
2. Анализ выполнения плана производства и производственные возможности карьера
2.1 Выполнение плана по товарной продукции и ее реализации
10 лет назад выход товарных блоков составлял 33,6%, что считается высоким показателем для блочных карьеров. С 2004 г началось постепенное снижение выхода (в среднем 33,26%, в том числе 26,65% блоков I-IIIгрупп в среднем за 2004;2006гг.) за счет вовлечения в отработку центральной, юго-восточной и юго-западной зон карьерного поля и усложнения структурно-тектонических условий месторождения за счет проявлений разгрузок горного давления (разрушение пород и трещинообразование) при углубке карьера. В 2013 году было добыто 16 900 м³ блоков I-IV категории Важно заметить, что при явном снижении процентного выхода товарных блоков количество заказов не уменьшалось. Следовательно предприятие столкнулось с проблемой недостатка продукции для продажи.
По положению горных работ на август 2014 года количество реализованных блоков составляет 10 970. На данный момент предприятие отстает от плана по реализации товарных блоков на 5%, что в дальнейшем может привести к существенным экономическим потерям. На конец года планируется добыть 19 010 м³ блоков, что соответсвует плану горных работ.
2.2 Выполнение плана добычных работ за анализируемый период
За 9 месяцев 2014 года на карьере при годовом плане 95 900 м³ по горной массе было добыто 84 392 м³ скальной горной массы (88%). Ожидаемая добыча на конец 2014 года 107 408 м³, что составит 112% от запланированных объемов на 2014 год.
Из статистических данных можно сделать вывод, что план по добычным работам перевыполняется на 12%. Но даже этот факт не сказывается положительно на реализации блоков.
2.3 Выполнение плана вскрышных работ за анализируемый период
В2014 году на карьере планируются вскрышные работы в объеме 3,5 тыс. м3
За 9 месяцев 2014 года план по вскрыше выполняется на 100%.
2.4 Выполнение плана буровых работ за анализируемый период
Объемы буровых работ:
Проходка отрезной щели:
Объем бурения равен 17 589 п. м. Диаметр шпура 76 мм.
Разделка монолита на блоки-заготовки:
Объем бурения равен 81 180 п. м. Диаметр шпура 32 мм.
Разделка блоков-заготовок на товарные блоки:
Объем бурения равен 49 950 п. м. Диаметр шпура 32 мм.
Бурение шпуров для разделки блоков-заготовок на товарные блоки осуществляется буровым станком Commando — 110.
Объем бурения шпуров диаметром 32 мм — 131 130 п.м.
Объем бурения шпуров диаметром 76 мм — 17 589 п.м.
Буровые работы ведутся в полном обьеме согласно плану буровых работ на 2014 год.
2.5 Расчет профиля производственной мощности
Машины и оборудование | Сменная эксплуатационная производительность машин | Кол-во смен в год, смен | Годовая производительность, | |
Буровые работы | ||||
1. Commando-120 | 1.714 | |||
Добычные работы | ||||
1. САТ- 988 2. САТ- 980 | ||||
2.6 Результаты анализа
Из графика видно, что карьер имеет большой запас производственной мощности и при росте объемов добычи, техника будет выполнять план. Но при использовании данной технологии имеется недостаточный процентный выход блоков.
Чтобы его увеличить, необходимо внедрить технологию с использованием Алмазно-канатного пиления и карьерно-дисковых установок.
Положительные стороны в работе карьера:
— Все работы в карьере ведутся в полном обьеме согласно плану горных работ в карьере. А добычные работы и вовсе превышают план.
— Предприятие имеет высокую организацию и исполнительную выучку персонала, что позволяет ежегодно обеспечивать необходимый обьем строительного камня.
Отрицательные стороны:
— С углубкой карьера растет горное давление. Структурно-тектоническая обстановка на участке постоянно изменяется в результате периодически возникающих разгрузок массива и связанным с этим процессом образованием трещин по мере проходки карьера, в особенности при его продвижении на более глубокие горизонты.
— На данном месторождении по мере углубления стали пропадать горизонтальные трещины, что осложняет добычу гранита привычным способ. Приходится создавать искусственные горизонтальные плоскости, что на нижележащих горизонтах осуществить без нарушения целостности монолита довольно сложно, так возникает горное давление.
— С каждым годом снижется процентный выход блоков. При растущем уровне строительства на северо-западе это существенная проблема не только для предприятия, но и для покупателей. Количество объемов под заказ не соответствует уровню и возможности реализации.
Чтобы решить представленную проблему, нужно внедрить в производство технологию с использованием алмазно-канатного пиления и карьерно-дисковых установок, которые успешно используются на карьерах по добыче блочного камня.
карьер гранит дисковый канатный
3. Организационно-техническое мероприятие по улучшению технико-экономических показателей работы карьера с обоснованием экономической эффективности
Для повышения технико-экономических показателей работы карьера мною предлагается внедрить без взрывной метод добычи гранита с использованием Карьерно-дисковой установки (КДУ) HKYS-3500-B и Алмазно-канатной установки (АКУ) Telediam Elektronik TDI- 65. Данный метод предлагается использовать в совокупности с взрывными работами. Полный отказ от взрывных работ на данном месторождении невозможен. Алмазно-канатное пиление совместно с карьерно-дисковой установкой планируется применять на 20% от всего обьема горных пород. Данное решение основанно на некоторых особенностях представленного месторождения. Технология с приминением АКУ и КДУ используется на карьерах с повышенной блочностью и пониженной трещиноватостью горных пород, чем не может похвастаться карьер «Возрождение». Но все же карьер помимо зон крутопадающих трещин имеет зоны, в которых средняя плотность трещин не проевышает 0,2м/м, что позволяет использовать данную технологию. Система трещен, возможность применения данной техники только в температурный режим максимум до -3, нестабильный выход блоков, относительная медленная работа техники и не высокая производительность по сравнению с взрывными работами позволяет использование представленного метода только на 20%. Но даже при частичном использовании повысится процентный выход блоков, общая производительность по блокам и следовательно экономическая прибыль для предприятия.
3.1 Описание метода
Технология добычи блоков пилением с помощью карьерно-дисковых установок (КДУ) и алмазно-канатных установок (АКУ)
Добычные работы предусматривается вести по двухстадийной схеме. Первоначально от массива отпиливаются крупные монолиты. Затем производится раскалывание монолита на блоки-заготовки и блоки.
— Вертикальное карьерно-дисковое пиление КДУ Добычные уступы отрабатываются последовательно сверху вниз. Высота уступа 1,5 м.
На подготовленную площадку устанавливаются, а затем соединяются между собой элементы рельсового пути, который располагается непосредственно на распиливаемом монолите. После проверки правильности сборки рельсового пути на них, при помощи подъемного устройства устанавливается карьерно-дисковая установка, затем на КДУ устанавливаются дисковые пилы O 2,6 м. и O 3,5 м., которые производят вертикальное пиление монолита.
После окончания пиления первого технологического монолита устанавливают АКУ для горизонтального пиления монолита на заготовки.
Пиление массива организуется таким образом, чтобы проводить одновременно пиление монолита на технологические панели (КДУ) и горизонтальное пиление монолита на заготовки (АКУ).
После окончательной работы с дисковой установки демонтируются дисковые пилы, а сам станок, на время хранения, снимается с рельсового пути. Рельсы разбираются и так же убираются в место хранения.
— Горизонтальное алмазно-канатное пиление АКУ На подготовленную площадку устанавливаются, а за тем и соединяются между собой элементы рельсового пути, на которые устанавливается АКУ.
Алмазный канат заводится в вертикальные пропилы, концы каната соединяются между собой. После проведения ручного «запила» персонал выводится из опасной зоны работы станка, после чего установка переводится в автоматический режим с заданными параметрами пиления.
АКУ выполняют вертикальные, горизонтальные и наклонные (при подготовке и разделке монолитов) пропилы.
Толщина пропила при применении технологии АКП соответствует толщине алмазного каната и составляет 9−12 мм.
Для охлаждения дисков КДУ и алмазного каната АКУ, а так же выноса шлама из распила используется вода. Расход воды — до 30 литров в минуту, в зависимости от конкретных условий.
Разделение монолитов и технологических панелей на товарные блоки производится буроклиновым способом. Разделение технологических панелей на блоки-заготовки возможно при помощи АКУ и КДУ.
Все добытые кондиционные блоки маркируются службой ОТК и вывозятся на склад готовой продукции. Со склада блоки отгружаются фронтальным погрузчиком САТ-980, САТ-988
Снабжение сжатым воздухом потребителей карьера предусмотрено от передвижного компрессора XAS-146 и собственных компрессоров буровых установок.
В борьбе с возникающим горным давлением предложено при подготовке горизонтов к отработке предварительно по контуру нерабочего борта проходить разгрузочные щели канатной пилой или буровой установкой.
4. График организации работ на уступе
Первая стадия работ включает в себя проходку вертикальных пропилов с помощью карьерно-дисковой установки, затем создается горизонтальный пропил с помощью алмазно-канатного пиления, после чего та же установка разделывает монолит на первичные блоки заготовки.
5. Расчет эффективности мероприятия, предложенного на карьере
5.1 Существующий вариант
Амортизация оборудования Норма амортизации на Компрессор XAS 146DD
Срок эксплуатации на все горное оборудование составляет 8−12 лет. Принимаем срок амортизации на компрессор XAS 146DD — 10 лет, тогда:
;
Sстоимость рассчитываемого оборудования;
S=800 000 руб.
Норма амортизации на погрузчик «Caterpillar-980»:
NA=100% /(срок эксплуатации).
;
S = 20 510 000 тыс. руб;
.
Норма амортизации на погрузчик «Caterpillar-988»:
NA=100% /(срок эксплуатации).
S = 24 400 000 тыс. руб;
Норма амортизации на буровую установку «Trimmer-240»:
NA=100% /(срок эксплуатации).
;
S = 12 000 000 руб;
.
Норма амортизации на буровой станок «Commando-120»:
NA=100% /(срок эксплуатации).
;
S = 7 000 000 руб;
.
Норма амортизации на буровой станок «Panthera-800»:
NA=100% /(срок эксплуатации).
;
S = 20 000 000руб;
.
Норма амортизации на гидрроклиновую установку Splitstone
NA=100% /(срок эксплуатации).
;
S=12 000 000 руб.
Таким образом, суммарные расходы на существующее оборудование по статье затрат «Амортизация» составят:
Затраты на ремонт оборудования (запасные части) составляют 10% от суммы на амортизационные отчисления составляют, 1 221 100 руб./год.
Топливо на технологические цели Затраты топлива на 1 час работы гидрроклиновой установки Splitstone составляют,
10л., — расход за смену 120 л, Тсм/год — кол-во смен в году 714, цена топлива за 1 литр 25 рублей.
Расход на смазочные материалы составляет 10% от суммы затрат на топливо и, таким образом, составит 214 200 тыс. руб./год.
Затраты топлива на 1 час работы Компрессора XAS 146DD 15 л, расход за смену 75 л, кол-во смен в году 714
;
Расход на смазочные материалы составляет 10% от суммы затрат на топливо и, таким образом, составит 1 338 750 тыс. руб./год.
Затраты топлива на 1 час работы Погрузчик «Caterpillar-980» составляют 12 л Расход топлива за смену 144 л, количество смен в год 357
Расход на смазочные материалы составляет 10% от суммы затрат на топливо и, таким образом, составит 128 520 руб./год.
Затраты топлива на 1 час работы Погрузчик «Caterpillar-988» составляют 10 л Расход топлива за смену 120 л, количество смен в год 357
Расход на смазочные материалы составляет 10% от суммы затрат на топливо и, таким образом, составит 214 200 тыс. руб./год.
Затраты топлива на 1 час работы буровая установка «Trimmer-200"составляют 11 л Расход топлива за смену 132 л, количество смен в год 714
Расход на смазочные материалы составляет 10% от суммы затрат на топливо и, таким образом, составит 235 620 руб./год.
Затраты топлива на 1 час работы бурового станка «Commando-110» составляют 9 л Расход топлива за смену 108 л, количество смен в год 714
Расход на смазочные материалы составляет 10% от суммы затрат на топливо и, таким образом, составит 192 780 тыс. руб./год.
Затраты топлива на 1 час работы бурового станка «Panthera-800» составляют 8 л Расход топлива за смену 96 л, количество смен в год 357
Расход на смазочные материалы составляет 10% от суммы затрат на топливо и, таким образом, составит 85 680 руб./год.
Таким образом, общая сумма по статье «Топливо на технологические цели» составит Заработная плата Рассчитаем фонд заработной платы основных рабочих, занятых на производстве при добычи буровзрывным способом.
Численность основных рабочих:
Начальник карьера — 1 чел.
Горный инженер — 1 чел.
Горный мастер — 2 чел.
Машинист буровой установки — 3 чел.
Машинист бурового станка — 2 чел.
Машинист бурового станка — 2 чел.
Машинист погрузчика — 3 чел.
Кольщик — 2 чел.
Электрики — 2 чел.
Механики — 3 чел.
Всего рабочих — 17 человека. Инженерно-технических работников — 4 чел. Общее количество работников -21 чел. Средняя заработная плата составляет 25 000 руб.
Сумма отчислений по данной статье составляет 6 300 000. 0,3 = 1 890 000 тыс. руб.
Общая сумма затрат Общая сумма затрат на ведение работ при существующей технологии составит:
Себестоимость 1 м? блочного камня при существующей технологии работ составляет. Калькуляция себестоимости полезного ископаемого представлена в таблице
— Оббьем блоков, добываемых буровзрывным способом.
Таблица 5.1.1 Калькуляция себестоимости добычи блочного камня
Статьи затрат | По существующей технологии | ||
На весь обьем, руб. | на 1 м³,.руб. | ||
Запасные части | 64,2 | ||
ФОТ | 331,4 | ||
Начисления на ФОТ 26% | 99,4 | ||
Топливо | 633,8 | ||
ГСМ | 63,3 | ||
Амортизация | 642,3 | ||
ИТОГО: | |||
5.2 Предложенный вариант
По проектируемому варианту 20% добычи будет вестись технологией, включающее в себя использование алмазно-канатного пиления и камнерезных машин. Список техники задействованной на карьере представлен в таблице 4.2.1
Таблица 5.2.1 Оборудование, применяемое на карьере
Количество используемой техники. | ||||
№ | Наименование оборудования | С БВР (80%) | Без БВР (20%) | |
Буровая установка «Триммер 240» | ||||
Буровая установка «Коммандо-120» | ||||
Буровая установка «Пантера — 800» | ||||
Погрузчик САТ 988 НВ с комплектом навесного оборудования | ; | |||
Погрузчик САТ 980 Н с комплектом навесного оборудования | ||||
Компрессор XAS 146DD | ||||
Камнерезная машина HKYS-3500-B | ||||
Telediam Elektronik TDI- 65 | ||||
Telediam Elektronik TDI-100 | ||||
Гидроклин SlipStone | ||||
Общие затраты по статьям Амортизация, топливо на технологические цели, заработная плата, представлены в таблицах 5.2.2 и 5.2.3
Таблица 5.2.2
Затраты по статьям: Амортизация и топливо на технологические цели
Амортизация | Топливо | электроэнергия | |||||
20% | 80% | 20% | 80% | 20% | 80% | ||
Компрессор XAS 146DD | |||||||
Commando-120 | |||||||
гидрроклин | |||||||
Caterpillar-980 | |||||||
Caterpillar-988 | |||||||
Trimmer-240 | |||||||
Panthera-800 | |||||||
АКУ | |||||||
КДУ | |||||||
Сумма | |||||||
зап.части ГСМ | 100 406,2 | 1 104 468,8 | 113 332,5 | ||||
Общ.Затраты | 1 104 468,2 | 12 149 156,8 | |||||
Таблица 5.2.3 Затраты по статье Заработная плата
Способ добычи | ||||
кол-во человек | ||||
Начальник карьера | ||||
Горный инженер | ||||
Горный мастер | ||||
Машинист Т | ||||
МашинистP | ||||
МашинистC | ||||
Машинист погр | ||||
Кольщик | ||||
Электрики | ||||
Механики | ||||
КДУ | ||||
АКУ | ||||
отчисления | ||||
сумма | ||||
Амортизация выбранного оборудования Некоторое оборудование будет использоваться в обоих методах добычи полезного ископаемого, следовательно затраты по статье Амортизация на одну единицу техники будут распределены на два метода в отношении 80% на буровзрывной метод и 20% на метод с использованием КДУ и АКУ. Норма амортизации на Компрессор XAS 146DD
А = S. NA, рублей/год;
S=800 000 руб.
Проектируемый вариант | ||
С использованием АКУ и КДУ 20%, руб. | БВР 80%, руб. | |
Норма амортизации на буровой станок «Commando-120»:
NA=100% /(срок эксплуатации).
А = S. NA, рублей/год;
S = 7 000 000 руб;
Проектируемый вариант | ||
С использованием АКУ и КДУ 20%, руб. | БВР 80%, руб. | |
Норма амортизации на буровую установку «Trimmer-240»:
NA=100% /(срок эксплуатации).
;
S = 12 000 000 руб;
.
Вся сумма полностью относится к способу с использованием БВР.
Норма амортизации на буровой станок «Panthera-800»:
NA=100% /(срок эксплуатации).
;
S = 20 000 000руб;
.
Вся сумма полностью относится к способу с использованием БВР.
Норма амортизации на гидрроклиновую установку Splitstone
NA=100% /(срок эксплуатации).
А = S. NA, рублей/год;
S=12 000 000 руб.
Проектируемый вариант | ||
С использованием АКУ и КДУ 20%, руб. | БВР 80%, руб. | |
Норма амортизации на погрузчик «Caterpillar-980»:
NA=100% /(срок эксплуатации).
А = S. NA, рублей/год;
S = 20 510 000 тыс. руб;
Вся сумма полностью относится к способу с использованием АКУ и КДУ.
Норма амортизации на погрузчик «Caterpillar-988»:
NA=100% /(срок эксплуатации).
А = S. NA, рублей/год;
S = 24 400 000 руб;
Вся сумма полностью относится к способу с использованием БВР.
Норма амортизации на КДУ
NA=100% /(срок эксплуатации).
А = S. NA, рублей/год;
S = 2 000 000 руб;
Вся сумма полностью относится к способу с использованием АКУ и КДУ.
Норма амортизации на АКУ (2 установки):
NA=100% /(срок эксплуатации).
А = S. NA, рублей/год;
S = 5 000 000 руб;
Вся сумма полностью относится к способу с использованием АКУ и КДУ.
Таким образом, суммарные расходы на существующее оборудование по статье затрат «Амортизация» составят:
Проектируемый вариант | ||
С использованием АКУ и КДУ 20%, руб. | БВР 80%, руб. | |
Затраты на ремонт оборудования (10% от суммы на амортизационные отчисления) составляют 364 700.руб./год и 966 400.руб./год
Топливо на технологические цели При расчете данной статьи необходимо учесть, что проектируемый способ с внедрением алмазно-канатного пиления использованием камнерезных машин, будет применятся только 9 месяцев в году в связи с метеоусловиями в данном регионе.
Из этого следует, что техника, которая была задействована при этом методе, перейдет на работу по добыче полезного ископаемого буровзрывным способом на три месяца. Затраты топлива на 1 час commando-120 9 л, расход за смену 108 л, кол-во смен в году 714
Проектируемый вариант | ||
С использованием АКУ и КДУ 20%, руб. | БВР 80%, руб. | |
Расход на смазочные материалы составляет 10% от суммы затрат на топливо и, таким образом, составит 28 917 руб./год. И 163 863. руб./год Затраты топлива на 1 час работы Компрессора XAS 146DD 15 л, расход за смену 75 л, кол-во смен в году 714
Проектируемый вариант | ||
С использованием АКУ и КДУ 20%, руб. | БВР 80%, руб. | |
Расход на смазочные материалы составляет 10% от суммы затрат на топливо и, таким образом, составит 20 081,2. руб./год. 1 137 993,8. руб./год Затраты топлива на 1 час работы гидрроклиновой установки Splitstone составляют 10 л, расход за смену 120 л, кол-во смен в году 714
Проектируемый вариант | ||
С использованием АКУ и КДУ 20%, руб. | БВР 80%, руб. | |
Расход на смазочные материалы составляет 10% от суммы затрат на топливо и, таким образом, составит 32 130 руб./год. и 182 070 руб./год соответсвенно. Затраты топлива на 1 час работы Погрузчик «Caterpillar-980» составляют 12 л Расход топлива за смену 144 л, количество смен в год 357
Проектируемый вариант | ||
С использованием АКУ и КДУ 20%, руб. | БВР 80%, руб. | |
Расход на смазочные материалы составляет 10% от суммы затрат на топливо и, таким образом, составит 19 278 руб./год. и 109 242 руб./год соответственно.
Затраты топлива на 1 час работы Погрузчик «Caterpillar-988» составляют 10 л Расход топлива за смену 120 л, количество смен в год 357
Вся сумма полностью относится к способу с использованием БВР.
Расход на смазочные материалы составляет 10% от суммы затрат на топливо и, таким образом, составит 214 200 тыс. руб./год.
Затраты топлива на 1 час работы буровая установка «Trimmer-200"составляют 11 л Расход топлива за смену 132 л, количество смен в год 714
Вся сумма полностью относится к способу с использованием БВР Расход на смазочные материалы составляет 10% от суммы затрат на топливо и, таким образом, составит 235 620 руб./год.
Затраты топлива на 1 час работы бурового станка «Panthera-800» составляют 8 л Расход топлива за смену 96 л, количество смен в год 357
Вся сумма полностью относится к способу с использованием БВР Расход на смазочные материалы составляет 10% от суммы затрат на топливо и, таким образом, составит 85 680 руб./год.
Таким образом, суммарные расходы на существующее оборудование по статье затрат «Топливо на технологические цели» составят:
Проектируемый вариант | ||
С использованием АКУ и КДУ 20%, руб. | БВР 80%, руб. | |
Затраты на электроэнергию Затраты электроэнергии на 1 час работы у КДУ составляют 45 кВт Расход электроэнергии за смену 540 кВт, количество смен в год 365
При стоимости электроэнергии 3 руб за 1 кВт сумма отчислений на электроэнергию составит Вся сумма полностью относится к способу с использованием АКУ и КДУ.
Расход на смазочные материалы составляет 10% от суммы затрат на электроэнергию и, таким образом, составит 44 347,5 тыс. руб./год.
Затраты электроэнергии на 1 час работы у АКУ составляют 35 кВт Расход электроэнергии за смену 420 кВт, количество смен в год 365
При стоимости электроэнергии 3 руб за 1 кВт сумма отчислений на электроэнергию составит Расход на смазочные материалы составляет 10% от суммы затрат на электроэнергию и, таким образом, составит 68 985 тыс. руб./год.
Таким образом, общая сумма по статье «Топливо на технологические цели» составит
Проектируемый вариант | ||
С использованием АКУ и КДУ 20%, руб. | БВР 80%, руб. | |
Заработная плата При расчете данной статьи необходимо учесть, что проектируемый способ с внедрением алмазно-канатного пиления использованием камнерезных машин, будет применятся только 9 месяцев в году в связи с метеоусловиями в данном регионе.
Из этого следует, что техника, которая была задействована при этом методе, перейдет на работу по добыче полезного ископаемого буровзрывным способом на три месяца.
Рассчитаем фонд заработной платы основных рабочих.
Всего рабочих — 21 человека. Инженерно-технических работников — 4 чел. Общее количество работников -25 чел. Средняя заработная плата составляет 25 000 руб.
Таблица 5.2.4
кол-во человек | ||||
Начальник карьера | ||||
Горный инженер | ||||
Горный мастер | ||||
Машинист Тrimmer | ||||
Машинист Pantera-800 | ||||
Машинист Cammando-120 | ||||
Машинист погр | ||||
Кольщик | ||||
Электрики | ||||
Механики | ||||
Машинист КДУ | ||||
Машинист АКУ | ||||
Сумма отчислениий | ||||
Суммарные затраты | ||||
Пример расчетов: Средняя зар. плата кольщика 25 000 рублей в месяц. В год он зарабатывает300 000 рублей. При этом 9 месяце он работает с блоками, которые добывают двумя разными способами, а три месяца работает с блоками, добытыми буровзрывным способом.
Следовательно его зарплата составит:
Проектируемый вариант | ||
С использованием АКУ и КДУ 20%, руб. | БВР 80%, руб. | |
Общая сумма затрат на ведение работ при существующей технологии составит
Проектируемый вариант | ||
С использованием АКУ и КДУ 20%, руб. | БВР 80%, руб. | |
Себестоимость переработки 1 м? полезного ископаемого при предложенной технологии работ составляет
Проектируемый вариант | ||
С использованием АКУ и КДУ 20%, руб. | БВР 80%, руб. | |
Таблица 5.2.5 Калькуляция себестоимости получения гранитных блоков безвзрывным способом
Статьи затрат | По проектируемому варианту | ||
на весь объем, тыс.руб. | на 1 м³,.руб. | ||
Запасные части | 47,5 | ||
ФОТ | 230,7 | ||
Начисления на ФОТ 30% | 69,2 | ||
Топливо | 130,8 | ||
ГСМ | 100 406,2 | 13,0 | |
Электроэнергия | 147,7 | ||
СМ (новые Машины) | 113 332,5 | 14,7 | |
Амортизация | 475,3 | ||
ИТОГО: | |||
Таблица 5.2.6 Калькуляция себестоимости получения гранитных блоков буровзрывным способом
Статьи затрат | По проектируемому варианту | ||
на весь объем, тыс.руб. | на 1 м³,.руб. | ||
Запасные части | 62,9 | ||
ФОТ | 363,6 | ||
Начисления на ФОТ 30% | 109,0 | ||
Топливо | 719,8 | ||
ГСМ | 1 104 468,8 | 71,9 | |
Амортизация | 629,8 | ||
ИТОГО: | 1957,3 | ||
Технико-экономические показатели Таблица 5.2.7
№ | Наименование показателя | Ед.изм. | показатели | |||
существующая технология | предложенная технология | |||||
АКУ и КДУ 20% | БВР 80% | |||||
Производительность по монолитам | шт/мес | |||||
Используемое оборудование: | ||||||
1.Погрузчик «Caterpillar-980» | шт. | ; | ||||
2.Погрузчик «Caterpillar-988» | шт. | |||||
3.Буровая установка «Trimmer-200» | шт. | ; | ||||
4.Буровой станок «Commando-120» | шт. | |||||
5.Буровой станок «Panthera-800» | шт. | ; | ||||
6. Компрессор XAS 146DD | шт. | |||||
7. Камнерезная машина HKYS-3500-B | шт. | ; | ||||
9. Telediam Elektronik TDI- 65 | шт. | ; | ||||
10.Telediam Elektronik TDI-100 | шт. | ; | ||||
11.гидрроклиноваяустановка Splitstone | шт. | |||||
Численность работников на карьере | чел. | |||||
Процент выхода блоков | % | |||||
Себестоимость 1 м³ гранита | руб/м3 | |||||
Средняя цена без НДС | руб/м3 | |||||
Объем реализации блоков | тыс.м3 | 19,01 | 23,1 | |||
Итого реализации в рублях | руб. | |||||
Дополнительная прибыль | руб./год | ; | ||||
Данные по существующей технологии взяты на предприятии.
Расчет предложенной технологии:
По плану горных работ на карьере обьем горных работ должен составить 95 900 .
При выходе блоков в 20% обьем реализуемых блоков составит 19 010 по цене 6350 рублей за, следовательно общая прибыль составит:
После внедрения новой технологии 20% от объема всей горной массы будет добываться с применением КДУ и АКУ и как показывает практика, с использованием данной технологии выход блоков увеличится до 40% и составит 7672. Предприятие планирует реализовывать блоки добытые с помощью везвзрывного способа по цене 7950 руб/, следовательно общая прибыль составит:
С использованием представленной технологии выход блоков повысится на 3%, что принесет прибыль в размере 33 887 744 рубля.
Заключение
В данном проекте была затронута проблема недостаточно большого процентного выхода блоков при добычи блочного камня на месторождении Возрождение (20%). Была предложена и обоснована технология добычи ископаемого с помощью КДУ (Карьерно-Дисковая Установка) и АКУ (Алмазно-канатная установка). Использование данной технологии повысило общую производительность карьера и выход блоков до 24%
Внедрение данной технологии принесет дополнительную прибыль предприятию в размере 33 887 744рублей.
Список используемой литературы
1. «Организация, планирование и управление производством» под редакцией Н. Я. Лобанова /Москва, «Недра», 1994.
2. «Технология горного производства «А. П. Килячков, 1992.
3. Справочник. Открытые горные работы. М: Горное бюро, 1994.
4. Единые правила безопасности при разработке месторождений полезных ископаемых открытым способом. М., Госгортехнадзор России, 1992.
.ur