Анализ обустройства газового месторождения
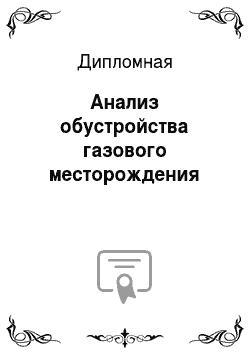
Для глубокой осушки применяют молекулярные сита, так называемые цеолиты. Цеолиты состоят из кислорода, алюминия, кремния и щелочноземельных металлов и представляют собой сложные неорганические полимеры с кристаллической структурой. Форма кристалла цеолита — куб, на каждой из шести сторон его имеются щели, через которые влага проникает во внутреннее пространство. Каждый цеолит имеет свой размер… Читать ещё >
Анализ обустройства газового месторождения (реферат, курсовая, диплом, контрольная)
Введение
На севере Тюменской области разрабатываются такие уникальные по размерам и запасам газовые месторождения как Медвежье, Уренгойское, Ямбургское, которые в течение многих лет обеспечивают потребность в природном газе России и сопредельных государств. Однако, ресурсы этих месторождений постепенно истощаются, что требует ввода в разработку новых перспективных площадей. Буквально за последние годы в промышленную эксплуатацию были введены такие месторождения как Юбилейное, Губкинское, Западно-Таркосалинское, Комсомольское, характеризующиеся существенно меньшими размерами структур и запасами газа. Теперь становится актуальной разработка небольших месторождений, расположенные в выгодных местах, с точки зрения транспортной схемы, природных условий и т. д.
К таким месторождениям относится Вынгаяхинское нефтегазовое месторождение, которое находится на территории Пуровского района Ямало-Ненецкого автономного округа Тюменской области. Поисково-разведочное бурение на площади месторождения было начато в 1968 г. В первой поисковой скважине 3, забуренной в северной части структуры, получен фонтан газа из сеноманских отложений. К настоящему времени залежи углеводородов выявлены практически по всему разрезу от васюганской и баженовской свит до сеномана включительно. Притоки нефти получены из коллекторов ачимовской толщи, пластов Ю0, Ю1, БП11.
На площади месторождения предприятием «Ноябрьскнефтегаз» разрабатываются нефтяные залежи, построены нефтепромысловые сооружения (ЦПС, ДНС, кусты скважин, коммуникации).
Газовая залежь является одним из наиболее привлекательных объектов для первоочередного освоения. Это связано, с одной стороны, с особенностями геологического строения (небольшая глубина залегания, большая продуктивность скважин, высокая степень подтверждаемости запасов газа), с другой, — с выгодным географо-экономическим положением (наличие производственной инфраструктуры, системы магистральных газопроводов, свободных трудовых ресурсов). Экономические показатели освоения и эксплуатации могут быть улучшены за счет комплексной разработки сеноманских газовых залежей Вынгаяхинского и прилегающего к нему Еты-Пуровского месторождений.
Разработка Еты-Пуровского месторождения находится в настоящее время на начальной стадии разработки. Пробурены и обвязаны № 9 и № 10 куст. Происходит завоз основного оборудования и обустройство УППГ.
Основой для выполнения настоящего проекта послужили «Технико-экономические предложения по разработке сеноманской залежи газа Вынгаяхинского Еты-Пуровского месторождения, выполненные ТюменНИИгипрогазом в 1998 г.
1. Общая часть
1.1 Характеристика района работ
Вынгаяхинское нефтегазовое месторождение расположено на территории Пуровского района Ямало-Ненецкого автономного округа в 120 км к югу от п. Тарко-Сале.
В географическом отношении месторождение находится в северной части Западно-Сибирской равнины, в зоне лесотундры. Гидрографически оно расположено в междуречье рек Вынгапур и Тырль-Яха, относящиихся к бассейну р.Пур. Реки на площади мелководны с извилистыми руслами, с большим числом притоков.
Широкое распространение имеют озера. Размеры наиболее значительных озер 2−3 км в поперечнике, их глубина составляет в основном 0,8−1м. Сильная заболоченность района связана с наличием мощного слоя многолетнемерзлых пород, играющего роль водоупора, а также со слабой испаряемостью влаги и затрудненным стоком. Болота, открытые с торфяной подушкой, достигающей толщины 7 м. Абсолютные отметки рельефа колеблются от +62 до +80м.
Климат района резко континентальный, характеризующийся продолжительной холодной зимой и коротким жарким летом. Морозы зимой достигают 50−60 0С, среднегодовая температура — 6,7 0С.
Годовое количество осадков составляет 580 мм. Основная их часть выпадает в период с апреля по октябрь. Реки замерзают в конце сентября, вскрываются ото льда во второй половине мая. Глубина промерзания грунта 1,5−3м, толщина льда на реках и озерах 40−90см.
По берегам рек и ручьев широко распространены хвойные (лиственница, ель, сосна, кедр), реже лиственные (береза) деревья. Среди болот встречаются островки редколесий, а в долинах рек — луга и заросли кустарников.
Экономическое развитие района в последнее время связано с бурным развитием нефтегазодобывающей и перерабатывающей промышленности. Ведется разработка нефтяных залежей Вынгаяхинского месторождения.
Основное занятие местного населения — ненцев, селькупов, хантов — оленеводство, рыболовство, звероводство.
В непосредственной близости к месторождению проходит трасса газопровода Уренгой-Сургут-Челябинск-Новополоцк. Построена трасса нефтепровода подключения от нефтяного промысла.
В Пуровском районе выявлен целый ряд месторождений строительных песков и кирпичных глин. Непосредственно на месторождении разработаны несколько карьеров для отсыпки площадок кустов и дорог.
Вынгаяхинское месторождение расположено в северной, слабоизученной части Западно-Сибирского артезианского бассейна, где гидрогеологические условия верхней части разреза осложнены многолетней мерзлотой.
Водоснабжение работающих буровых установок осуществляется, в основном, из естественных источников: рек, ручьев, озер. Основными водотоками являются реки Вынгапур и Пякупур с многочисленными их притоками. Воды пресные (минерализацией до 100 мг/л), очень мягкие (жесткость 0,95−1,3мг-экв/л). По химическому составу воды сульфатно-гидрокарбонатно-магниево-натриевые, кальциевые.
Для хозяйственно-питьевого водоснабжения пригодны подземные воды верхнего гидрогеологического этажа в отложениях палеоген-четвертичного возраста.
Подземные воды четвертичных отложений могут быть использованы для технологических целей, а после очистки — для водоснабжения населенных пунктов.
Для централизованного хозяйственно-питьевого водоснабжения реко-мендуются подземные воды олигоценового водоносного комплекса, залегающего на глубине 67−107м. Воды напорные, высота напора над кровлей до 90 м. Олигоценовые водоносные пески слабоглинистые, преимущественно среднезернистые, с включениями гравия. Эффективная толщина комплекса 35−50м. Дебиты скважин изменяются от 4,4 до 24,5л/сек при соответственном понижении уровня до 5,1−14,8 м.
По химическому составу подземные воды комплекса пресные и ультрапресные с минерализацией от 0,04 до 0,2г/л, гидрокарбонатно-магниево-кальциевые, с высоким содержанием железа (в среднем до 3,0мг/л) и низким содержанием фтора (0,1−0,2мг/л).
В настоящее время при эксплуатации нефтяных месторождений широко используются подземные воды апт-альб-сеноманского комплекса для поддержания пластового давления путем закачки их в продуктивные пласты.
Еты-Пуровское месторождение.
В административном отношении Еты-Пуровское месторождение расположено на территории Пуровского района Ямало-Ненецкого автономного округа.
Площадь района проектирования приурочена к северной части Западно-Сибирской равнины, в зоне лесотундры. Гидрографически месторождение расположено в междуречье рек Айваседо-Пур, Еты-Пур, Вынга-Пур, относящихся к бассейну реки Пур.
Сильная заболоченность территории связана с наличием мощного слоя многолетнемерзлых пород. Болота чаще открытые, с торфяной подушкой, достигающей толщины 7 м.
Климат района резко-континентальный: продолжительная холодная зима и короткое жаркое лето. Среднегодовая температура +7,5°С, самый холодный месяцянварь (морозы достигают до минус 50°С), самый теплый — июль (до плюс 30°С). Среднегодовое количество осадков, достигает 400−500мм. Снеговой покров устанавливается в конце октября и сходит в конце мая. Толщина снегового покрова до 1,5−2м. Реки замерзают в конце сентября, вскрываются ото льда во второй половине мая. Толщина льда на реках и озерах изменяется от 40 до 90 см. Глубина сезонного промерзания грунта составляет 1,5-Зм.
Лесные массивы на площади месторождения, состоящие из лиственницы, ели, кедра, березы, сосны, приурочены к поймам рек.
Основными видами сообщения являются: водный (в период навигации), воздушный и железнодорожный. В зимнее время возможна транспортировка грузов автомобильным и гусеничным транспортом. Населенные пункты в районе немногочисленны и расположены по берегам рек. Плотность населения низкая: 8−10 человек на 100 км².
Коренное население: русские, ханты, ненцы, селькупы. Основным занятием является охота, рыбная ловля, звероводство. В последние годы проводятся геологоразведочные и строительные работы, развивается нефтегазодобывающая промышленность.
1.2 История освоения района
В районе Вынгаяхинского месторождения региональные геолого-геофи-зические исследования начаты в 1961 г. В результате проведенных работ уточнено тектоническое строение платформенного чехла в данном районе. Был выделен ряд положительных структур 2 и 3 порядков: Пяку-Пуровская, Западнои Восточно-Таркосалинская, Вынгаяхинская, Вынгапякутинская. Кроме того, выделен и оконтурен Айваседо-Пуровский вал, осложненный Айваседопуровским и Еты-Пуровским локальными поднятиями, а также выявлен Вынгаяхинский вал.
Площадными работами МОВ 1967;1968гг. подтвержден Вынгаяхинский вал, с осложняющими локальными поднятиями: Вынгаяхинским и Вынга-Пякутинским.
Поисково-разведочное бурение на Вынгаяхинской площади начато в 1968 г. Первая поисковая скважина 3, пробуренная в северной части поднятия, является первооткрывательницей газовой залежи в сеноманских отложениях.
Несмотря на четкую сейсмическую характеристику структуры, скважина была заложена не в лучших и далеко не в самых благоприятных условиях и вскрыла небольшую по запасам северную газовую залежь.
С 1986 года ОАО «Ноябрьскнефтегаз» осуществляет добычу нефти и растворённого газа. На площади месторождения построены нефтепромысловые сооружения (ЦПС, ДНС, кусты скважин, коммуникации).
Проект обустройства Етыпуровского и Вынгаяхинского месторождения выполняется по варианту — совместная разработка Вынгаяхинского и Етыпуровского месторождений с размещением на Вынгаяхинском месторождении УКПГ, ДКС на полное развитие и УППГ на Етыпуровском месторождении.
На Вынгаяхинском месторождении предусматриваются следующие объекты основного и подсобно-вспомогательного назначения:
— 14 кустов газовых скважин;
— установка комплексной подготовки газа;
— дожимная компрессорная станция;
— опорная база промысла;
— подстанция 35/6 кВт.;
— пожарное депо;
— вахтовый жилой комплекс (ВЖК);
— полигон бытовых отходов;
— водозабор из артскважин;
— поглощающие скважины.
Подготовленный газ с Вынгаяхинского месторождения, а в дальнейшем и с Етыпуровского по газопроводу внешнего транспорта подаётся в газопровод Уренгой-Сургут-Челябинск.
Водоснабжение УКПГ, ДКС, ВЖК, ОБП осуществляется от водозаборных скважин.
Промышленные и бытовые стоки после очистных сооружений закачиваются в поглощающие скважины.
Внешнее электроснабжение потребителей Вынгаяхинского газового промысла предлагается от существующей трансформаторной подстанции ТП- 35/6кВ, расположенной на Вынгаяхинском нефтяном промысле.
Для распределения электроэнергии по потребителям в районе УКПГ предлагается строительство технологического закрытого распределительного устройства 6кВ (ЗРУ- 6кВ).
Отдельно стоящее ЗРУ- 6кВ комплектуется ячейками типа К-104М с вакуумными выключателями Самарского завода «Электрощит» и выполняется в каркаснопанельном индивидуальном исполнении.
По надежности электроснабжения потребители УКПГ и ДКС относятся к первой категории, остальные объекты — ко второй и третьей категории.
скважина сеноманский продуктивный газонасыщенность
2. Геологическая часть
2.1 Геологическая характеристика месторождения
2.1.1 Литолого-стратиграфическая характеристика разреза
Палеозойский фундамент
Породы доюрского фундамента на Вынгаяхинском месторождении не вскрыты. На ближайших площадях (Надымская площадь, — скв.7 и Южно-Русская площадь — скв.21) фундамент вскрыт на глубинах 4462 и 4198 м.
Литологически фундамент представлен алеврито-кремнисто-глинистыми породами. Породы характеризуются массивной текстурой, сильно деформированы, метаморфизованы. Возраст пород фундамента — пермо-триасовый.
Юрская система
Отложения юрской системы представлены тремя отделами: нижним, средним и верхним.
Породы нижнего и среднего отделов юры представлены континентальной толщей тюменской свиты, верхний отдел — преимущественно морского происхождения породами васюганской, георгиевской и баженовской свит.
Тюменская свита представлена частым неравномерным чередованием аргиллитов плотных, крепких, алевролитов слюдистых крепкосцементированных и песчаников мелкозернистых крепкосцементированных глинисто-известковистым цементом, слюдистых. Породы отличаются обилием обугленных растительных остатков, часто наблюдаются сидеритизация, включения пирита. Наибольшая вскрытая толщина свиты 178 м.
Васюганская свита подразделяется на две части: нижнюю — глинистую и верхнюю — песчано-глинистую.
Нижняя подсвита представлена аргиллитами плотными, слабослюдистыми, прослоями алевритистыми.
Верхняя часть свиты, преимущественно, песчаная, к ней приурочен нефтеносный пласт Ю1.
Песчаники тонкозернистые, алевритистые, в отдельных прослоях глинистые, реже известковистые, в продуктивной части нефтенасыщенные с прослоями алевролитов и аргиллитов. Алевролиты от слабо до сильно опесчаненных с глинистым, иногда карбонатным цементом. Аргиллиты тонкоотмученные, слюдистые с мелкорассеянным пиритом, иногда трещиноватые. По всему разрезу свиты наблюдается обугленный растительный детрит. Толщина отложений свиты 64−76м.
Георгиевская свита сложена аргиллитами тонкоотмученными с включениями глауконита, пирита. Толщина свиты 7−27м.
Баженовская свита представлена битуминозными аргиллитами, слюдис-тыми с включениями растительного детрита. Толщина свиты 22−73м. В верхней части свиты находится нефтенасыщенный пласт Ю0.
Меловая система
Отложения меловой системы представлены двумя отделами: нижним и верхним.
Нижний отдел включает в себя породы сортымской, тангаловской и нижней части покурской свиты; верхний — верхнюю часть покурской, кузнецовскую, березовскую и ганькинскую свиты.
Нижний отдел
Сортымская свита сложена терригенными породами, залегающими на битуминозных аргиллитах баженовской свиты.
Нижняя часть свиты представлена аргиллитами однородными, плитчатыми с углистым детритом.
Выше залегает опесчаненная ачимовская толща. В целом толща пред-ставлена неравномерным переслаиванием песчаников, алевролитов с аргиллитами. В нижней и верхней части толщи выявлены пласты БП15 и БП17 с нефтенасыщенными песчаниками.
Выше ачимовской толщи залегают глинистые породы с прослоями песчаников и алевролитов.
Песчаники, преимущественно, мелкозернистые, слюдистые, с глинистым цементом порово-пленочного типа, прослоями с цементом глинисто-карбонатным. Алевролиты прослоями глинистые или карбонатные, местами с включениями песчаного материала и углистого растительного детрита. Аргиллиты неоднородные, слабослюдистые с включениями углистого детрита и макрофауны. Толщина сортымской свиты 368−537м. Песчаники в продуктивной части нефтенасыщенные — платы БП011, БП111, БП211 на глубине 2350 — 2400 м.
Тангаловская свита сложена чередованием песчано-алевритовых и гли-нистых пород.
Глинистые породы имеют преимущественное распространение: слюдистые, тонкослоистые с прослоями песчаников и алевролитов, встречаются прослои углей.
Песчано-алевритовые разности представлены песчаниками и алевролитами, изредка встречаются прослои известняка. Для этой части разреза характерны прибрежно-морские и мелководные осадки. Толщина свиты 514−586м.
Покурская свита разделяется на две части: нижнюю, в которой преобладают глинистые породы и верхнюю, — с преобладанием песков, песчаников и алевролитов.
Нижняя часть разреза свиты на месторождении сложена песчано-алевритовой толщей пород, глинистой, слюдистой, полимиктовой, в верхней части переходящей в глины аргиллитоподобные и алевритистые с прослоями песков и алевролитов.
Верхняя часть покурской свиты представляет частое переслаивание песков, песчаников, алевролитов. Керном охарактеризована только кровля покурской свиты, к которой приурочена сеноманская залежь газа ПК1. Общая толщина свиты 966−1034м.
Верхний отдел
Кузнецовская свита представлена глинами слабослюдистыми, опоковидными с редкими остатками углистого детрита и отпечатками фауны. Толщина свиты изменяется от 13 до 23 м.
Березовская свита сложена глинами и подразделяется на две подcвиты: нижнюю и верхнюю.
Нижнеберезовская подсвита представлена глинами с прослоями глинистых алевролитов. Толщина подcвиты 69−83м.
Верхнеберезовская подсвита сложена переслаиванием алевролитов глинистых и глин алевритистых с прослоями опоковидных глин. Толщина подcвиты 32−61м.
Ганькинская свита представлена толщей глин с прослоями алевролитов, мергелей. В породах встречаются зерна глауконита, конкреции сидерита. Толщина свиты 136−196м.
Палеогеновая система
Отложения системы представлены тремя отделами: палеоценом, эоценом и олигоценом.
В составе системы выделяются: тибейсалинская, люлинворская, тавдинская, атлымская и новомихайловская свиты.
Тибейсалинская свита сложена, преимущественно, глинистымив нижней и более песчаными — в верхней части свиты породами. Толщина свиты составляет 103 м.
Люлинворская свита сложена опоковидными глинами, в верхней части алевритистыми с прослоями диатомовых глин. Толща свиты представлена глинами, алевритистыми. Толщина свиты до 180 м.
Атлымская свита сложена песками с прослоями глин и алевритов. Толщина свиты 30−70м.
Новомихайловская свита представлена неравномерным переслаиванием глин, песков и алевритов. Толщина свиты до 70 м.
Четвертичная система
Литологически отложения четвертичной системы представлены песками, глинами, супесями, суглинками, торфяниками, галечниками.
Толщина четвертичных отложений достигает 125 м.
Еты-Пуровское месторождение.
Геологический разрез месторождения представлен терригенными песчано-глиниетыми отложениями мезозойско-кайнозойского платформенного чехла.
Максимальная вскрытая толщина осадочных пород составляет 3300 м (скв.175). Породы доюрского фундамента на месторождении не вскрыты.
Палеозойский фундамент
Фундамент представлен известняками. Породы фундамента вскрыты на соседних месторождениях: Комсомольском — скв.198 и 199 — на глубинах 3551 и 3650 м; Западно-Таркосалинском — скв.99 — на глубине 4502 м.
Скважина 199 Комсомольского месторождения вскрыла отложения карбона, представленные сланцами пиритизированными с прожилками кварца и кальцита, метаморфизованными.
Юрская система.
Отложения системы несогласно залегают на породах фундамента и представлены тремя отделами: нижним, средним и верхним.
Нижний отдел выделен к котухтинскую свиту, средний — представлен породами тюменской свиты, а отложения верхнего отдела подразделяются на васюганскую и баженовскую свиты.
Котухтинская свита.
Отложения свиты на месторождении не вскрыты. По соседним месторождениям данная свита делится на нижнюю и верхнюю.
Нижняя подсвита подразделяется на песчаную пачку, представленную песчаниками с прослоями алевролитов и уплотненных глин, и верхнюю — глинистую, представленную глинами уплотненными, слабобитуминозными, с прослоями алевролитов и углей. Встречается растительный детрит, остатки листовой флоры. Толщина подвиты около 200 м. …
В основании верхней подсвиты также залегает пачка песчаников прослоями карбонатных, чередующихся с алевролитами и уплотненными глинами. Перекрывается песчаная пачка глинами уплотненными с прослоями песчаников, алевролитов. Толщина свиты около 130 м.
Тюменская свита.
Представлена неравномерным переслаиванием уплотненных глинистых песчаников, алевролитов с прослоями углей, встречается растительный детрит, пирит. К кровле свиты приурочен пласт Юг, при испытании которого на Еты-Пуровском месторождении получен приток нефти. Вскрытая толщина свиты — 96 м.
Васюганская свита.
По литологическому составу делится на две подсвиты. Нижняя подсвита представлена глинами аргиллитоподобными с прослоями алевролитов и песчаников. Встречаются включения пирита. Толщина подсвиты 51−58м
Верхняя подсвита сложена песчаниками средне, мелкозернистыми с прослоями карбонатных разностей глин и алевролитов. К отложениям подсвиты приурочен продуктивный горизонт Ю1). Толщина подвиты 26-Збм.
Общая толщина свиты 77−94м.
Георгиевская свита.
Представлена глинами аргиллитоподобными, реже алевритистыми. Встречаются остатки фауны, включения пирита, галукониты. Толщина свиты 2б-64м.
Баженовская свита.
Представляет собой наиболее глубоководные морские осадки юры. сложена она битуминозными аргиллитами с тонкими прослоями глинистого листового материала и известняков. Породы обогащены растительным детритом, пиритизированными остатками фауны. К кровле баженовской свиты приурочен отражающий сейсмический горизонт «Б». Толщина свиты 122−149м
Меловая система
Отложения свиты представлены тремя отделами: нижним, средним, верхним. Нижний отдел представлен отложениями сортымской и тангаловской свит. Сортымская свита.
Снизу вверх в разделе свиты следится пачка аргиллитоподобных глин, прослоями битуминозных, толщиной около 40 м
Выше залегает ачимовская толща, представленная арглиллитами с подчиненными прослоями песчаников, часто известковистых. Ачимовские отложения на месторождении достигают 180 м. При испытании получены притоки нефти.
Перекрываются эти отложения мощной толщей аргиллитоподобных, тонкоотмученных глин толщиной до 257 м.
Вышележащие породы сортымской свиты представлены песчаниками с прослоями аргиллитов и алевролитов (пласты БП7-БП12). Толщина песчаной толщи -350м.
Завершает разрез свиты чеускинская пачка, представленная глинами аргиллитоподобными с единичными прослоями песчаников.
Общая толщина свиты 728−756м.
Тангаловская свита.
Сложена морскими отложениями в виде неравномерного чередования аргиллитов и песчаников. Подразделяется на три подсвиты: нижнюю, среднюю и верхнюю. Нижняя подсвита представлена песчаниками и алевролитами. Средняя и верхняя подсвиты сложены глинами, чередующимися с песчаниками и алевролитами. Встречается обугленный растительный детрит, отпечатки флоры.
Толщина свиты 381−492м.
Средний отдел представлен отложениями покурской свиты.
Покурская свита.
К отложениям среднею отдела отнесены континентальные и частично прибрежно-морские осадки.
Свита представляет собой хаотичное чередование песчано-алевролитовых и глинистых пород. Характерен растительный детрит, остатки растений, углистые прослои, включения пирита.
В кровельной части свиты залегает газоносный пласт ПК1.
Толщина свиты 8б0−974м.
Верхний отдел сложен отложениями кузнецовской, березовской и ганькинской свит.
Кузнецовская свита.
Начинает цикл морских осадков верхнего мела. Представлена глинами плотными слабослюдистыми, изредка известковистыми. Толщина свиты 14−26м.
Березовая свита.
Подразделяется на две подсвиты: нижнюю и верхнюю.
Нижняя подсвита представлена опоками, переходящими в опоковидные глины с прослоями алевролитов. Толщина подсвиты 39-ЮЗм.
Верхняя подсвита сложена глинами, с прослоями опоковидных глин и опок. Толщина подсвиты 38−114м.
Ганькинская свита.
Завершает разрез меловых отложений и представлена глинами прослоями известковистыми, алевритистыми. Толщина свиты 160−255м.
Палеогеновая система
В состав палеогеновой системы входят отложения талийкой, люлинворской, тавдинской, атлымской и новомихайловской свит.
Талицкая свита.
Сложена, в основном, глинами алевритистыми, с прослоями песчаников в верхней части. Толщина свиты 74−123м
Люлинворская свита.
Представлена глинами алевритистыми с полурастворенной органикой, в нижней части — опоковидными с прослоями диатомовых глин. Толщина свиты 122−196м.
Тавдинская свита.
Сложена алевритистыми глинами с прослоями глауконитового песка. Толщина свиты 106 м.
Атлымская свита
Представлена песчано-алевритовыми породами. Толщина свиты 50 м.
Новомихайловская свита.
Характеризуется неравномерным переслаиванием глин алевритистых, алевритов и песков. Толщина свиты около 45 м.
Четвертичная система
Отложения системы представлены песками, супесями, глинами с включениями гравия и гальки. Толщина около 30 м.
2.1.2 Тектоника
В тектоническом отношении месторождение приурочено к Вынгаяхинскому локальному поднятию.
Согласно структурно-тектонической карте мезозойско-кайнозойского осадочного чехла Западно-Сибирской плиты, Вынгаяхинское поднятие осложняет северную часть Вынгаяхинского вала, входящего в состав Верхне-Пурского мегавала.
Южная часть Вынгаяхинского вала осложнена Вынга-Пякутинским локальным поднятием, которое отделяется от Вынгаяхинского неглубокой седловиной.
К востоку и, частично, к северо-востоку от Вынгаяхинского вала в пределах Верхне-Пурского мегавала выделяется Етыпурский вал и с юга — Вынгапуровское куполовидное поднятие.
Наиболее общую информацию о структуре поднятия по различным гори-зонтам осадочного чехла и, связанных с ним отражающих границ, дают мате-риалы сейсморазведочных работ, которые на рассматриваемой территории проводились с 1967 года.
По материалам МОВ сейсмопартией 30,39/77−78 Вынгаяхинское локальное поднятие закартировано по отражающим горизонтам: «Г» (сеноман), «М» (апт), «В» (верхняя юра), «Т"(подошва платформенных отложений). Наиболее выдержанными в отношении регистрации являются: верхнеюрский сейсмический репер «Б», литологически связанный с кровлей битуминозных аргиллитов баженовской свиты и горизонт «Г», контролирующийся кровлей туронских глин, регионально распространенных в пределах Западной Сибири.
По горизонту «Г» Вынгаяхинское поднятие представляет собой линейно вытянутую в меридиональном направлении брахиантиклинальную складку со сравнительно крутыми западным и восточным крыльями и пологими перикли-налями.
Размеры структуры по замыкающей изогипсе — 775 м составляют 47×12км, амплитуда поднятия 125 м. Свод структуры смещен к южной ее части.
По отражающему горизонту «Б» Вынгаяхинское поднятие представляет собой ту же меридиональную складку, осложненную несколькими кулисообразно расположенными куполами в сводовой части.
Западное крыло круче восточного. К востоку от сводовой части отмечается терраса шириной 6−9км, восточнее которой углы падения увеличиваются и на крыльях достигают 30−3,50, углы наклона к северу уменьшаются до 20 .
По горизонту «Т» строение структуры аналогично горизонту «Б», выделяются те же купола, только несколько другой конфигурации и размеров.
Еты-Пуровское месторождение.
Еты-Пуровское месторождение расположено в южной части Надым-Тазовской синеклизы, в пределах Верхнепурского вала. Вал входит в состав Варьеганско-Пурпейской зоны линейных структур. Верхнепурский вал представляет собой структуру субмеридионального простирания. Вал сформирован с севера на юг Западно-Таркосалинским и Айваседопурским куполовидными поднятиями и Еты-Иурским малым валом. Последний осложнен Еты-Пурским и Южно-Еты-11урским локальными поднятиями.
Но верхнеюрскому опорному отражающему горизонту «Б» (кровля баженовской свиты) Еты-Пуровский вал представляет собой антиклинальную складку северо-западного простирания, оконтуренную изогипсой минус 3080 м. имеющую размеры 82×25км, амплитуду около 300 м.
По опорному отражающему горизонту «Г» (сеноман) Еты-Пуровский вал представляет собой антиклинальную складку северо-западного простирания, оконтуренную изогипсой минус 900 и осложненную по изогипсе — 760 м двумя куполами. Максимальная амплитуда вала около 250 м, размеры 78×17км.
Южно-Еты-Пурскос локальное поднятие по горизонту «Е'' слабо выражено, имеет незначительные размеры 7,5×2км и амплитуду 7 м.
Ссверо-Еты-Пурское локальное поднятие по изогипсе минус 760 м представляет собой антиклинальную складку северо-западного простирания размерами 30,5×1 1 км. и амплитудой до 130 м. Угол падения восточного, более крутого крыла — около 2,5″, западного — 1.5−1,6° Северо-Еты-Пурское локальное поднятие контролирует газовую залежь в пласте. ПК?
По всему разрезу осадочных отложений осевой части Северо-Еты-Пурского локального поднятия выделены зоны тектонических нарушений, имеющих выдержанное северо-западное простирание. Разрывные нарушения подтверждены сейсмикой и данными бурения.
Зоны нарушений имеют вид грабенов с максимальной амплитудой погружения центрального блока на уровне отражающего горизонта «Е» в пределах 30 м.
Разрывные нарушения, делящие залежь пласта ПК) на блоки, не являются газогидродинамическими экранами и не оказывают влияния на положение ЕВК, а дизъюнктивная тектоника отражается лишь на внешней геометрии структуры (граф.прил 2).
С юга на север амплитуда грабена плавно затухает до 10 м.
Кроме того, в юго-восточной части купола складки выделяется сеть оперяющих разломов [I]. Выше по разрезу тектонические нарушения затухают.
2.1.3 Нефтегазоносность
Вынгаяхинское газонефтяное месторождение расположено в пределах Пуровского района НадымПурской нефтегазоносной области.
Залежи углеводородов в пределах этой области выявлены, практически, по всему разрезу вскрытых отложений от васюганской и баженовской свит до сеноманского яруса, включительно.
В изученной части разреза месторождения скопления углеводородов выявлены в отложениях васюганской и баженовской свит, ачимовской толщи, валанжинского и сеноманского ярусов.
Безводные притоки нефти получены из коллекторов ачимовской толщи. Притоки нефти получены в пластах Ю0 и Ю1, БП11.
Основные запасы газа связаны с отложениями сеноманской продуктивной толщи. В отложениях сеномана на месторождении выявлено две самостоятельные залежи, отделенные друг от друга небольшим прогибом. Каждая залежь имеет свой ГВК. Одна газовая залежь выделяется на севере в пределах небольшого локального поднятия в районе скважины 3. Залежь имеет небольшую газонасыщенную толщину — 2,2 м, отметка ГВК — 736,8 м.
Размеры залежи 3×2км. При опробовании скважины в интервале 794−796м был получен фонтан газа дебитом 577,3тыс.м3/сут на диафрагме 25,4 мм. Залежь водоплавающая.
Вторая (основная) залежь газа вскрыта 17 поисково-разведочными скважинами, вытянута в меридиональном направлении. Кровля сеноманских отложений вскрыта на абсолютных отметках 636,5−707,7 м. Представлена переслаиванием песчано-алевритовых и глинистых пород, невыдержанных как по разрезу, так и по площади.
Для разреза характерна слабая сцементированность пород.
Коллекторами газа являются песчаники мелкои среднезернистые прослоями алевритовые или глинистые и алевролиты от мелкодо крупнозернистых, переходящие в песчаники мелкозернистые.
Эффективные газонасыщенные толщины изменяются от 2,4 м до 62,4 м.
Газоводяной контакт имеет наклон с юга на север от а.о.- 704,7 м до а.о.- 713,6 м. Опробование залежи проведено в трех скважинах (33, 34 и 40). Во всех скважинах получены фонтаны газа.
Размер основной залежи 25,3×10,8 км, высота — 72,7 м. По типу залежь массивная, водоплавающая. Запасы газа составляют 100 млрд. м3. Индекс месторождения 1 Г.
Еты-Пуровское месторождение.
Залежи углеводородов выявлены практически по всему разрезу вскрытых отложений от тюменской свиты до сеноманского яруса верхнего мела включительно (пласты Ю2, Ю12, Ю11, Ач1, БП164 БП163, БП12, бП9, БП4−5, БП1, АП10, ПК20, ПК9, ПК1) (всего 14 пластов).
Из коллекторов пласта Ю1 на южном куполе поднятия получен безводный приток нефти в скв.172, дебиты 6.9м3/сут, при депрессии 13.3МПа.
Еоризонт Ю) (пласты Ю11 и Ю12) опробован в четырех скважинах южного купола. Получены притоки нефти от 3,9м3/сут до 169,3мз/сут. Нефтеносность ачимовской толщи (пласт Ач) доказана испытанием скв.87 (северный куполполучена нефть дебитом 0,76м3/сут), скв.171 (южный купол — получена нефть дебитом 5,3м3/сут).
Нефть получена при испытании в скв.179 и 177, 178 пластов БП164 и БП163 Фонтаны нефти составили 20 и 12,2 м3/сут.
Пласт бп12 нефтенасыщен только на южном куполе. Фонтан нефти с пластовой водой получен в скв.179 из пласта БП9. Непереливающий безводный приток нефти получен из коллекторов пласта БГ4−5. Незначительные притоки безводной нефти получены при испытании пластов бп1 и АП10. Продуктивны пласты ПК20 и ПК9.
Газовая залежь ПК1 определена только на северном куполе, где из 11 испытанных скважин получен сухой газ. Залежь пласта ПК1 вскрыта на глубинах 732−854м.
Всего в контуре газоносности пласта ПК1 пробурено 20 скважин (без учета скв. 94, 95) и испытано в разрезе его продуктивной части 11 интервалов. При испытании газонасыщенных объектов рабочие дебиты на шайбах диаметром 16,1−24,1 мм составили 413,2−576,6 тыс.н.м3/сут. при депрессиях 0,08−1,38 МПа. Расчетные значения абсолютно-свободных дебитов определялись в 1752,2−6742,1 тыс.н.м3/сут.
По типу и строению она аналогична одновозрастным залежам газовых месторождений.
Продуктивная толща представлена переслаиванием песчано-алевролитовых и глинистых пород.
Контролируется залежь ПК) Северо-Еты-Пурским поднятием, оконтуривается изогипсой минус 760 м и характеризуется развитием дизъюнктивной тектоники в отложениях сеномана.
Газоводянной контакт (ГВК) отбивается по комплексу ГИС на отметках от 761,0 до 770,7 метров, в среднем составляя 768,8 м.
Залежь пласта ПК1 массивная, водоплавающая. Высота залежи 115 м, размеры ее 11,5×37км.
2.2 Основные параметры сеноманской продуктивной толщи. Пористость, проницаемость, начальная газонасыщенность
В сеноманском разрезе керн отобран в пяти скважинах. Проходка с отбором керна составила 6% от общей газонасыщенной толщины. Всего выполнено 112 определений пористости, из них 53 — в газонасыщенной части разреза.
Коллекторами газа являются среднеи мелкозернистые песчано-алевритовые породы, очень рыхлые, слабосцементированные, с неравномерным распределением глинистого материала. По своему составу породы сходны с сеноманскими коллекторами газовых месторождений севера Тюменской области.
Пористость по керну составляет 30,8%. Возможно, пористость занижена за счет недовыноса керна из наиболее рыхлых песчаных пород. Коэффициент пористости, определенный по зависимостям «керн-геофизика» по скв. 41 и 48 Ямбургского месторождения, составляет 0,318, а по связям, построенным для месторождений южной группы, — равен 0,34. Коэффициент пористости по Ямбургским зависимостям, возможно, занижен, так как разница глубин залегания продуктивной толщи Ямбургского и Вынгаяхинского месторождений составляет 300 м.
Коэффициент начальной газонасыщенности определен по зависимости удельного сопротивления от объемной влажности, полученной по месторождениям с аналогичным типом коллекторов (Вынгапуровское, Комсомольское, Губкинское). Средневзвешенное значение по месторождению равно 0,64.
Проницаемость коллекторов (Кпр) определена по зависимости Кпр=f (Кпэф). Средневзвешенное значение проницаемости составляет 0,7755мкм2. По керну не определены остаточная водонасыщенность и проницаемость.
Для сеноманской толщи характерно достаточно сложное строение: значительная изменчивость литологического состава, сильная расчлененность продуктивной толщи, слоистая неоднородность как по площади, так и по разрезу.
Коэффициент песчанистости (Кпес) по месторождению изменяется от 42,4% (скв. 38) до 100% (скв. 3, 34, 40, 377, 379). Среднее значение Кпес равно 82,8%. Высокие значения промыслово-геологических параметров приурочены к сводовой части структуры (к участкам максимальных толщин). Коэффициент проницаемости по скважинам изменяется от 91мД (скв. 358) до 1969мД (скв. 37). Сводовая часть представлена высокопроницаемыми породами.
Сеноманская толща имеет сложное строение и представляет собой чередование пород коллекторов и неколлекторов.
Коллекторами газа являются песчаники и алевролиты, характеризующиеся слабой степенью цементации. Содержание цемента в коллекторах составляет 5−10% иногда достигая 20%.
Состав цемента глинистый, представлен гидрослюдой, хлоритом, каолинитом. По типу цемент поровый и пленочно-поровый. Коллекторы ПК1 обладают высокими фильтрационно-емкостными свойствами.
Охарактеризована сеноманская продуктивная толща керном в 13 скважинах. Из газонасыщенной части вынесено 90 м керна (22,6% от суммарной эффективной толщины). Суммарный вынос керна составил 153,14 м, что свидетельствует о низкой охарактеризованности пласта ПК1 керном.
Всего из коллекторов сеноманской толщи выполнено 73 определения пористости и 14 — проницаемости .
Пористость по керну изменяется от 29,5 до 47%, средневзвешенное значение составляет 36,6%. Коэффициент пористости, определенный по данным ГИС. равен 35,5%.
Коэффициент начальной газонасыщенности по ГИС составляет 0.76 (см. табл. 2.1.).
Качественных прямых определений проницаемости по керну не получено. По ГИС проницаемость определена по зависимости Кпр = f (Кпэф) и составляет 988 мД .
Физико-химическая характеристика свободного газа.
Сеноманская газовая залежь охарактеризована двумя анализами по скв. 33 и 34. Для газа сеноманской залежи характерно отсутствие или очень низкое содержание тяжелых углеводородов. Содержание метана составляет 98,23%, этана — следы, пропана — 0,01 — 0,03%, бутанов — 0,02 — 0,06%, пентана + высшие — 0,03%. Углекислый газ содержится в количестве 0,04%. Азот, гелий и аргон присутствуют в очень малых количествах, соответственно: 1,62 — 2,18%; 0,02%; 0,01%. Относительная плотность составляет 0,564.
Компонентный состав газа сеноманской залежи определен по шести пробам из 8 скважин. Природный газ имеет метановый состав. Содержание метана изменяется от 98,02% (скв.12) до 98,96 (скв.1).
Высшие гомологи метана представлены этаном — 0,06. Содержание углекислого газа варьирует от 0,04 (скв.12) до 0,43 (скв.10), азота 0,64 -1,95%, сероводород отсутствует, водород обнаружен в трех пробах в количестве 0,02%, содержание гелия составляет 0,02% - 0,017%, аргона — 0,02% .
Среднекритические параметры газа составляют: среднекритическое давление — 4,6МПа, среднекритическая температура 189,93°К.
Температурные условия недр.
Для изучения температурного режима при испытании скважин замерялась пластовая температура одновременно с замерами пластового или забойного давления. Большинство замеров приурочено к продуктивным нефтяным пластам и характеризуют нижнюю часть разреза.
Запись геотермического градиента проведена в скв.30. Скважина находилась в состоянии покоя 56 суток. Средняя температура продуктивных пластов определялась по линии, построенной по точечным замерам, на уровне среднего положения ГВК или ВНК. Температура продуктивной толщи сеномана составляет 320С, пласта БП110- 780С, БП111−800С, БП112−780С.
3. Технологическая часть
3.1 Состояние разработки
Разработка Вынгаяхинского месторождения газа находится в начальной стадии освоения, поэтому технологические показатели разработки газовой залежи выбирались, учитывая ряд факторов геологического, технологического и технико-экономического характера.
К геологическим факторам относятся, в первую очередь, особенности геологического строения, фильтрационно-емкостные характеристики залежей и величины запасов газа. Сеноманская газовая залежь Вынгаяхинского месторождения является водоплавающей массивного или пластово-массивного типа и залегает на небольшой глубине. Запасы газа сравнительно небольшие — 100 млрд. м3. Для залежей подобного строения и с такими запасами, как показывает опыт разработки аналогичных месторождений, оптимальным уровнем годовых отборов газа в основной период разработки является ежегодная добыча 3 — 5% от величины начальных запасов газа.
Из технологических, основным фактором, ограничивающим добычу газа, является продуктивность добывающих скважин. Как показывают результаты газодинамических исследований разведочных скважин, ожидаемая продуктивность залежи при ее разработке достаточно высока. Так, максимальные дебиты разведочных скважин, при небольших депрессиях на пласт, сопоставимы с дебитами эксплуатационных скважин на соседнем Вынгапуровском месторождении. Сеноманская газовая залежь Вынгаяхинского месторождения характеризуется наличием активной подошвенной водой. Согласно расчетам при расстоянии от нижних дыр перфорации до поверхности ГВК порядка 20 м безводный дебит в основной период разработки оценивается в 450−470 тыс. м3/сут. При этом величина депрессии на пласт не превысит 2 кг/см2. Как показывает опыт разработки близлежащих месторождений (Вынгапуровского, Комсомольского, Губкинского) при таких депрессиях не отмечается разрушения призабойной зоны скважины. Такие продуктивности может обеспечить оправдавшая себя на практике центрально-групповая схема размещения кустов эксплуатационных скважин в центральной части структуры.
Фактором, осложняющим обустройство сеноманской газовой залежи, может явиться большое количество нефтяных кустов и линейных коммуникаций на площади месторождения. Но ожидаемая высокая производительность газовых скважин предопределяет их сравнительно небольшое количество, а следовательно и возможность размещения их на площади месторождения.
В условиях рыночной экономики во главу угла ставится получение максимальной прибыли от добычи углеводородного сырья за весь период разработки. Поскольку категорических экономических ограничений на объемы ежегодной добычи газа на месторождении не установлено, то на стадии проектирования разработки встает вопрос о выборе оптимального варианта эксплуатации, обеспечивающего максимальную добычу газа при минимальных капитальных вложениях в обустройство месторождения и эксплуатационных затратах, т. е. уровнями годовой добычи газа в период постоянных отборов газа (4, 5, 6 и 7 млрд. м3).
По выбранному варианту разработки предусматривается уровень годовой добычи газа в период постоянных отборов 5 млрд. м3. Такой уровень добычи может быть достигнут за счет эксплуатации 33 скважин, объединенных в 14 кустов по 2−3 скважины в кусте. Средний рабочий дебит одной скважины ожидается равным 447 тыс. м3/сут при депрессии на пласт 1,0−1,7 кг/см2. Продолжительность периода нарастающей и постоянной добычи составит 13 лет. Пластовое давление в зоне размещения скважин к началу падающей добычи снизится до 45,7 кгс/см2.
Срок разработки 28 лет. Пластовое давление к концу разработки снизится до 12,3 кгс/см2. Обводнение залежи составит 53,6% начального порового объема.
Сеноманская газовая залежь Вынгаяхинского месторождения выгодно отличается от других в плане разработки тем, что залегает на сравнительно небольшой глубине, характеризуется высокими коллекторскими свойствами, а следовательно, ожидаемой большой продуктивностью эксплуатационных скважин. Залежь массивного типа на всей площади подстилается подошвенной водой. Указанные факторы позволяют использовать центрально-групповую схему размещения эксплуатационных скважин, предусматривающую формирование эксплуатационного поля в присводовой части структуры. Аналогичная схема вполне оправдала себя на соседнем Вынгапуровском месторождении, где к настоящему времени, глубина региональной депрессионной воронки не превышает 5−6 кг/см2, несмотря на то, что площадь зоны размещения эксплуатационных скважин не превышает 25% от площади залежи. Такая схема отличается рядом преимуществ по сравнительно с другими (например, равномерным размещением скважин). Сокращается протяженность внутрипромысловых коммуникаций (шлейфов), подъездных автодорог к скважинам, уменьшается площадь земель отведенных на строительство технических сооружений.
Существующий опыт бурения и эксплуатации скважин на аналогичных месторождениях позволяет использовать в качестве основного способа разбуривания, строительство наклонно-направленных скважин, что также значительно снижает затраты на обустройство месторождения и эксплуатацию скважин, уменьшает воздействие на окружающую среду.
Освоение газовой залежи начато с наиболее продуктивной ее части, т. е. первые скважины расположены на участке наибольших газонасыщенных толщин с последующим расширением эксплуатационного поля к периферийным частям залежи. Основные трудности возникают в связи с тем, что площадь размещения эксплуатационных скважин и внутрипромысловые коммуникации накладываются на поле уже пробуренных нефтяных скважин. Здесь же имеется довольно разветвленная схема сбора нефти. Поэтому при выборе точек размещения кустов скважин и схемы сбора газа максимально использованы коридоры нефтесборных коллекторов.
По этой же причине целесообразно расположение УКПГ неподалеку от систем сбора и подготовки нефти (ЦПС, ДНС).
Примерно в 40 км к востоку от Вынгаяхинского месторождения расположено Еты-Пуровское месторождение, которое также является перспективным объектом для первоочередного освоения. С целью предотвращения дублирования транспортных потоков газа с этих двух месторождений при обустройстве Вынгаяхинского промысла предусмотренно строительство газопровода подключения с учетом последующей врезки газопровода с Еты-Пура.
Как показывают теоретические расчеты и опыт разработки аналогичных месторождений количество эксплуатационных скважин в кусте контролируется эффективной газонасыщенной толщиной, с которой коррелятивно связана величина газопроницаемости. Но, поскольку, объем геологической информации на этапе первичного проектирования не позволяет построить достаточно достоверную модель изменения проницаемости по площади залежи, в основу схемы размещения эксплуатационных скважин положена карта изопахит.
Для обоснования зоны размещения скважин на площади Вынгаяхинского месторождения, в проекте разработки на сеточной модели проведены многовариантные расчеты, позволяющие провести анализ эффективности дренирования залежи в зависимости от площади эксплуатационного поля. В результате расчетов установлено, что оптимальная степень дренирования достигается при размещении скважин в пределах изопахиты 30−40 м. При этом подавляющее большинство скважин должно быть расположено в пределах 40-вой изопахиты. Но в перспективе наибольшая глубина депрессионной воронки ожидается в северной и северно-восточной частях залежи, в связи с чем на этих участках также необходимо разместить эксплуатационные скважины.
Фактором, контролирующим количество скважин в кусте, является величина удельных запасов газа, приходящихся на один куст. Поэтому в зоне наибольших удельных запасов газа, ограниченной изопахитой 60 м размещены кусты из трех эксплуатационных скважин с диаметром эксплуатационной колонны 168 мм, а на участке ограниченном изопахитати 30−60 м — кусты из двух скважин.
С целью выбора продуктивных пластов для перфорации первая скважина куста пробурена вертикальной со вскрытием ГВК и спуском эксплуатационной колонны на глубину 810 м (по вертикали). Данная скважина выполняет функции эксплуатационно-наблюдательной. Исключением являются кусты №№ 3, 7, 12, в которых пробурены наблюдательные скважин. Вторая (третья) скважины пробурены наклонно-направленным способом в зависимости от фактически установленного разреза по результатам ГИС, проведенного в первой пробуренной скважине куста, и остановкой забоев на 10−20 м от начального ГВК. Такая схема разбуривания по имеющемуся опыту разработки обеспечивает длительную безводную эксплуатацию скважин в течении 15−18 лет.
Кроме указанных факторов, при выборе схемы размещения скважин, оказывает влияние наличие на площади нефтяных коммуникаций и природоохранные ограничения.
По выбранному варианту пробурено 39 скважин, в том числе 33 эксплуатационных (14 кустов), 3 наблюдательных в кустах и 3 одиночных наблюдательных скважин.
Разработка северной залежи (район разведочной скважины 3) предполагается на поздней стадии эксплуатации месторождения. Учитывая, что она изолирована от основной залежи, в технологических расчетах она принимается как самостоятельный объект.
4 Техническая часть
4.1 Конструкция скважин
В качестве основного способа разбуривания залежи приняты как наклонно-направленный способ, так и строительство вертикальных скважин. На кустовых площадках размещены от двух до четырех скважин (с учетом наблюдательных).
Все наклонные скважины бурятся по трехинтервальному профилю, с участком набора угла наклона в интервале спуска кондуктора со стабилизацией угла до кровли продуктивного горизонта. В интервале залегания продуктивного пласта предполагается естественное падение угла наклона, характерное для прямых компоновок без центрирующих элементов.
Исходя из проектных добывных возможностей продуктивного пласта предусмотрена соответствующая конструкция скважин. Эксплуатационная колонна диаметром 168 мм спускается на глубину 780 м по вертикали. Центраторы устанавливаются в интервале набора кривизны через каждые 20 м, над кровлей продуктивного пласта через каждые 20 м и устанавливаются два комплекта технологической оснастки, включающие центраторы, турбулизаторы и скребки.
В устьевой части колонна оборудована жесткими центраторами в количестве 10 шт., устанавливаемых на первых 10 трубах.
Глубина спуска кондуктора определяется согласно РД 39−093−91 «Инструкция по испытанию обсадных колонн на герметичность», Самара, 1991 г. по формуле
Нк 1,105Рвн/гр (4.1)
где Рвн — ожидаемое внутреннее давление на глубине Нк (Рвн=Рпл/еs), мПа;
гр — градиент давления гидроразрыва на глубине Нк, мПа/м.
Согласно расчетам глубина спуска кондуктора диаметром 245 мм принимается равной 500 м. Кондуктор спускается для перекрытия зон обвалообразований и установки на него противовыбросового оборудования. Комплектуется из труб марки «Д» .
Для перекрытия неустойчивых четвертичных отложений спускается направление диаметром 324 мм на глубину 150 м.
Значения глубин спуска эксплуатационных колонн, конкретно по каждой скважине, уточняются геологической службой добывающего предприятия, исходя из расположения скважины на структуре.
Таблица 4.1 Конструкция скважин
Наименование | Диаметр, | Глубина | Цель спуска | |
Колонн | Мм | спуска, м | колонн | |
1. Направление | Перекрытие неустойчивых четвертичных отложений | |||
2. Кондуктор | Предупреждение обвалообра-зований в верхней части разреза | |||
3. Эксплуатационная колонна | Перекрытие промыслового газосодержащего объекта | |||
Конструкция наблюдательных и эксплуатационно-наблюдательных скважин аналогична конструкции эксплуатационных наклонных скважин и предусматривает глубину спуска эксплуатационной колонны 810 м по вертикали.
4.2 Конструкция фонтанных подъемников и оборудование скважин
Эксплуатационные скважины сеноманских отложений Вынгаяхинского месторождения для обеспечения оптимальных режимов работы должны оснащаться лифтовой колонной диаметром 114 мм. Для обеспечения безаварийной эксплуатации скважин в условиях многолетней мерзлоты более безопасна пакерная схема. Следует отметить, что в условиях Вынгаяхинского месторождения допускается беспакерная схема эксплуатации, использование которой возможно при наличии технологического регламента, согласованного с органами госгортехнадзора, госпожнадзора и противофонтанной службы.
Исходя из геолого-технических условий предлагается следующая компоновка лифтовой колонны:
от устья до глубины на 50 м выше кровли продуктивного пласта — колонна высокогерметичных насосно-компрессорных труб типа НКМ диаметром 114 мм;
ниже, над кровлей продуктивного горизонта, — комплекс подземного скважинного оборудования типоразмера 168/114−21 отечественного или зарубежного производства:
ниже комплекса, до нижних перфорационных отверстий эксплуатационной колонны, — подпакерный хвостовик из насосно-компрессорных труб диаметром 114 мм.
Комплекс подземного скважинного оборудования должен состоять как минимум из пакера, циркуляционного клапана, посадочного ниппеля, с устанавливаемым в нем забойным клапаном-отсекателем, срезного клапана. При необходимости возможна дополнительная установка в составе лифтовой колонны выше циркуляционного клапана — телескопического соединения и скважинной камеры с устанавливаемым в ней ингибиторным клапаном.
Пакер предназначен для герметизации затрубного пространства между эксплуатационной и лифтовой колоннами. Исполнение пакера — стационарно-съемное, гидравлического действия.
Срезной клапан предназначен для запакеровки пакера и с целью уменьшения гидроудара при запакеровке должен устанавливаться на конце подпакерного хвостовика.
Посадочный ниппель предназначен для установки в нем забойного клапана-отсекателя в процессе эксплуатации или глухой пробки при ремонте с целью обеспечения противофонтанной безопасности.
Забойный клапан-отсекатель предназначен для перекрытия лифтовой колонны в аварийных ситуациях. Исполнение — съемное, автономного действия. Устанавливается в посадочном ниппеле после вызова притока из пласта.
Циркуляционный клапан предназначен для временного сообщения затрубного пространства скважины с трубным в процессе ее ремонта.
Ингибиторный клапан предназначен для подачи ингибитора c целью предупреждения гидратообразования или парафиноотложений. Исполнение — съемное. Устанавливается в скважинной камере.
Скважинная камера предназначена для установки в ней ингибиторного клапана в процессе эксплуатации.
Телескопическое соединение предназначено для компенсации температурных изменений длины лифтовой колонны.
Подпакерный хвостовик предназначен для регулирования местоположения башмака лифтовой колонны относительно интервала вскрытия пласта и транспортировки добываемого флюида из пласта в интервале от срезного клапана до пакера.
Лифтовая колонна предназначена для транспортировки добываемого флюида в интервале от пакера на дневную поверхность.
Для сеноманских скважин рекомендуются комплексы КОС 89/168−35 ТУ 51−338−87 (ВНПО «Союзтурбогаз», Украина), КПГ 114−35−140 ТУ 26−16−29−77 (ОКБ «Нефтемаш», Азербайджан), SABL (фирма «Baker Oil Tool, Inc», США).
Лифтовая колонна подвешивается в фонтанной арматуре, устанавливаемой на колонной головке.
Колонная головка предназначена для обвязки устья и подвески эксплуатационной и технических колонн. Исходя из количества обсадных колонн в конструкции скважины следует производить обвязку устья односекционной клиньевой колонной головкой типа ОКК по схеме 1 ТУ 26−02−201−579−76−74 с условным проходом верхнего фланца 280 мм с ручным управлением.
Фонтанная арматура предназначена для обвязки устья и подвески лифтовой колонны, а также транспортировки по ней добываемого флюида. Исходя из производительности скважин следует монтировать на устье фонтанную арматуру типа АФК, оборудованной манометрами и термометром, по схеме 6 ГОСТ 13 846–89 с условным проходом ствола и рабочих струн 100 мм с ручным приводом.
5 Специальная часть
5.1 Обустройство куста газовых скважин
Эксплуатационные скважины группируются в кусты из 2−3 скважин с расстоянием между устьями не менее 40 м. Кустовая площадка сеноманских газовых скважин должна располагаться на расстоянии не менее 70 м от кустовой площадки нефтяных скважин.
Устье скважины обвязывается манифольдом, в состав которого должны входить, как минимум, устьевой клапан-отсекатель, быстросъемное сужающее устройство, прямоточные задвижки. Устье скважины должно быть оборудовано двумя задавочными линиями с обратными клапанами и быстросъемными соединениями, а также при необходимости метанолопроводом.
Куст скважин должен быть оборудован факельной линией с вертикальным или горизонтальным факельным устройством (ГФУ), а также измерительной установкой (коллектором) типа Надым-2 или сепаратором.
Газосборный коллектор от скважин куста выполнен в подземном исполнении.
Кустовая площадка оборудована фундаментами под подъемные агрегаты для капитального ремонта скважин, якорями под оттяжки подъемных агрегатов, емкостями под технологические растворы, необходимые для ремонта скважин. В целях предотвращения затопления талыми водами кустовая площадка должна быть отсыпана выше максимального подъема воды, иметь уклон в сторону амбара ГФУ, а в целях исключения снегозаносимости территории и образования «повышенных» объемов талых вод, образующихся при весеннем таянии снега, — не обвалована и иметь подъездные пути.
Существуют принципиальные схемы обвязки устья скважин с различным расположением рабочих струн фонтанной арматуры относительно оси скважин и с использованием амбара ГФУ, построенного при бурении скважин:
традиционная схема обвязки с расположением арматуры параллельно оси скважин;
схема обвязки с расположением арматуры перпендикулярно оси скважин, обеспечивающая снижение потерь давления и некоторое уменьшение металлоемкости за счет устранения ряда поворотов обвязки;
схема обвязки двух эксплуатационных скважин с расположением одной из арматур под углом к оси скважин, что обеспечивает снижение металлоемкости при некотором увеличении размеров самой кустовой площадки;
Оптимальной схемой следует считать схему с расположением арматуры параллельно оси скважин с использованием уже имеющегося амбара ГФУ.
В проекте предусматривается обустройство 33 эксплуатационных скважин на 14 кустах. Наблюдательные скважины (6 шт.) размещаются в контуре газоносности для контроля за разработкой залежи, три из них размещаются на кустовых площадках.
Распределение скважин по кустовым площадкам приведено в таблицу 5.1.
Таблица 5.1 Распределение скважин по кустовым площадкам
Номер куста | Количество скважин в кусте, шт. | |||
эксплуатационные | наблюдательные | всего | ||
6…11, 14, 15 | ; | |||
2, 4, 5, 13 | ; | |||
Одиночные (1Н, 2Н, 3Н, 4Н) | ; | |||
Устья скважин размещаются на расстоянии 40 м друг от друга.
Режим работы скважин — безгидратный.
Выкидные трубопроводы эксплуатационных скважин подключаются к шлейфу.
Обвязка кустов запроектирована на статическое давление газа.
В обвязке устьев скважин предусмотрены клапаны — отсекатели для отключения скважин в случае порыва шлейфа и устройства регулирующие с дистанционным управлением УР 1610АЭ с электрическим приводом для выравнивания давления газа в выкидных трубопроводах скважин. Для обеспечения замера дебита скважин выкидные трубопроводы оборудуются сужающими быстросменными устройствами.
На трубопроводе выхода газа с куста устанавливается дистанционно управляемый шаровый кран наземной установки производства ООО «Самараволгомаш» класса давления 600 с электроприводом для отключения шлейфа.
Газ при выводе скважин на режим отводится для сжигания на горизонтальный факел. На факельном трубопроводе предусмотрен регулирующий штуцер для снижения давления газа. Для проведения работ по исследованию скважин на каждом кусте предусматривается установка коллектора «Надым-2М».
Газ при проведении работ по исследованию скважин возвращается в шлейф или сжигается на факеле.
При глушении скважин подача раствора хлористого кальция предусматривается от передвижного задавочного агрегата и емкостей через задавочные трубопроводы, выведенные к проезду куста. Каждый трубопровод заканчивается арматурой и гнездом конуса для подключения задавочного агрегата.
Проектом предусмотрены: местный замер давления и температуры газа по каждой скважине на выкидном трубопроводе и в шлейфах на выходе с куста, давления газа на факельном трубопроводе после редуцирующего устройства; дистанционный замер расхода, давления и температуры газа по каждой скважине на выкидном трубопроводе, давления и температуры газа в шлейфах на выходе с куста.
Технологические трубопроводы в пределах площадки куста прокладываются надземно на опорах в теплоизоляции, трубопроводы на факел и для подключения задавочного агрегата — без теплоизоляции.
Для обвязки кустов скважин применяются узлы трубопроводов заводского изготовления.
Защита надземных трубопроводов от коррозии предусмотрена лакокрасочными покрытиями, теплоизоляция трубопроводов предусмотрена плитами теплоизоляционными из минеральной ваты на синтетическом связующем.
Выбор труб произведён в соответствии с требованиями «Инструкции по применению труб в газовой и нефтяной промышленности», трубопроводы запроектированы из труб группы В, сталь 09Г2С, сортамент по ГОСТ 8732–78, технические условия на изготовление по ГОСТ 8731–74.
Выбор трубопроводной арматуры осуществлен с учетом статического давления, максимальных и минимальных температур, которые принимает арматура в процессе эксплуатации. Арматура принята исполнения «ХЛ».
5.2 Анализ вариантов схем сбора газа
На газовых месторождениях Тюменской области широкое распространение получили две основные схемы промыслового сбора газа — лучевая и коллекторная.
В проекте разработки были предложены четыре варианта промыслового сбора газа:
I вариант — коллекторная схема сбора, при которой газ от кустов по семи коллекторам подается на УКПГ. К одному коллектору подключается 2 куста. Расчетную схему см. рис. 5.1.
II вариант — коллекторная схема сбора, при которой газ от кустов по трем коллекторам подается на УКПГ. К одному коллектору подключается 4 — 6 кустов. Кусты № 4 и № 9 подключаются к коллектору в 1,3 км. от УКПГ. Расчетную схему см. рисунок 5.2.
III вариант — лучевая схема сбора газа, при которой газ от кустов по шлейфам подается на УКПГ. Расчетную схему см. рисунок 5.3.
IV вариант — коллекторная схема сбора, при которой газ от кустов по двум коллекторам подается на УКПГ. К одному коллектору подключается 7 кустов. Расчетную схему см. рисунок 5.4.
Каждая из рассмотренных схем имеет преимущества и недостатки. Если I и III варианты обеспечивают высокую надежность, II вариант обеспечивает экономию материальных и трудовых ресурсов, то IV вариант обеспечивает значительную экономию материальных и трудовых ресурсов при достаточной надежности.
На основании долговременного опыта эксплуатации систем сбора газа на северных месторождениях Тюменской области (Комсомольское, Губкинское месторождения) и, исходя из технико-экономического расчета и анализа вероятности возможных аварий, для Вынгаяхинского месторождения принята коллекторная схема сбора газа с подключением кустов к телескопическим коллекторам по IV варианту. Такая схема обеспечивает меньшую металлоемкость, безгидратный, более благоприятный гидравлический и температурный режим транспорта газа и достаточную надежность. Вероятность возможных аварий для коллектора от куста 7 составит 5,66×10−3 случаев в год, для коллектора от куста 10 — 8,19×10−3 случаев в год.
Потребное количество труб и металлоемкость по вариантам см. таблицу 5.2.
Рис. 5.1 1 вариант расчетной схемы сбора газа (по 7 коллекторам)
Рис. 5.2 2 вариант расчетной схемы сбора газа (по 3 коллекторам)
Рис. 5.3 3 вариант сбора газа (по лучевой схеме)
Рис. 5.4 4 вариант расчетной схемы сбора газа (по 2 коллекторам)
Таблица 5.2 Потребное количество труб и металлоемкость по вариантам
Наружный диаметр и | Количество, км. | ||||
толщина стенки, мм. | I вариант | II вариант | III вариант | IV вариант | |
159×4,5 | 1,651 | 0,639 | ; | 0,859 | |
219х6 | 24,742 | 8,728 | 9,526 | 6,443 | |
273х7 | 16,717 | 6,791 | 81,096 | 7,661 | |
325х8 | 18,945 | 4,650 | 7,680 | 5,578 | |
426х9 | ; | 17,517 | ; | 3,477 | |
530х9 | ; | ; | ; | 6,245 | |
Общая протяженность, км. | 62,055 | 38,325 | 98,302 | 30,263 | |
Металлоемкость, т. | |||||
На газовые месторождениях Тюменской области широкое распространение получили две основные схемы внутрипромыслового сбора газа — лучевая и коллекторная.
Каждая из применяемых схем имеет преимущества и недостатки. Если при лучевой схеме обеспечивается высокая надежность системы и эффективный контроль за работой кустов и скважин, то при коллекторной достигается значительная экономия материальных и трудовых ресурсов при достаточной надежности.
Рассмотрены три варианта внутрипромыслового сбора газа:
— коллекторная схема сбора газа. при которой газ от кустов по семи коллекторам подается на УКПГ. К одному коллектору подключается два-три куста;
— коллекторная схема сбора газа. при которой газ от кустов по пяти коллекторам подается на УКПГ. К одному коллектору подключаются три-пять кустов;
— лучевая схема сбора газа. при которой газ от кустов по 17−20 шлейфам подается на УКПГ'.
Режим работы шлейфов и коллекторов по всем вариантам безгидратный. подача ингибитора гидрообразования от УКПГ к кустам скважин не требуется.
На основании долговременного опыта эксплуатации систем сбора газа на северных месторождениях Западной Сибири и исходя из технико-экономического расчета для Еты-Пуровского месторождения принята коллекторная схема сбора газа с подключением кустов к пяти коллекторам. Такая схема обладает меньшей металлоемкостью, достаточной надежностью и обеспечивает благоприятный гидравлический и температурный режимы транспорта газа.
Гидравлический расчет газосборных сетей выполнен в соответствии с требованиями ОНТП 51−1-85 с использованием ЭВМ по программе «ОЮКА 2». Расчет произволен на весь период эксплуатации (32 года).
Расчет схемы и подбор диаметров шлейфов и коллекторов выполнен из условия минимальной разницы давлений по более удаленным коллекторам на входе в УКПГ. минимальной разницы транзитного потока и потока от кустов в месте подключения, а также исходя из существующего сортамента труб. В расчетах принят допустимый перепад давления до 6% от устьевого давления газа.
Расчетные схемы газосборных сетей приведены на рис. 5.5.-5.8. потребное количество труб и общая металлоемкость по вариантам в табл. 5.3.
Сопоставление вариантов разработки при указанной цене на газ позволяет рекомендовать третий вариант разработки к практической реализации, предусматривающий уровень годовой добычи газа в объеме 13 млрд. м3 для реализации которого потребуется 3639.91 млн.р. капитальных вложений, в т. ч. 1281,1 млн.р. в бурении и 2312.56 млн.р. в обустройстве.
Таким образом. III вариант обустройства промысла и эксплуатации месторождения характеризуется следующими технико-экономическими показателями:
— срок эксплуатации месторождения — 30 лет;
— накопленная добыча газа — 279,95 млрд. м3;
— число эксплуатационных скважин — 75 шт;
— количество кустов — 18 шт;
— средний дебит скважин — 509 м3/сут;
— объем кап. вложений в обустройство месторождения -2312.56 млн руб.
— эксплуатациднные затраты за весь период разработки — 15 513 млн руб.
— средняя себестоимость добычи 1000 м3газа- 56,2 руб.
— дисконтированная накопленная денежная наличность — 361.44 млн руб.
— внутренняя норма доходности — 11.44%
срок окупаемости кап. вложений (с начала строительства) — 10 лет.
Газ от кустов скважин поступает на входные краны пункта переключающей арматуры (ППА), а затем через сборный коллектор условным диаметром 1000 мм подается на установку сепарации газа. Сборный коллектор служит одновременно для предварительной сепарации газа от жидкости, особенно при ее пробковом поступлении из системы сбора, и защиты первичных сепараторов. Продувка сборного коллектора осуществляется в общую дренажную емкость.
Отсепарированный газ поступает на ДКС, где проходит вторую ступень очистки в фильтрах-сепараторах и компримнруется до давления, обеспечивающего его подачу в магистральный газопровод. Согласно технологическим показателям разработки ввод ДКС необходим для 1 варианта — с третьего года эксплуатации, для 2, 3 и 4 вариантов — с первого года эксплуатации. Первые два года в первом варианте отсепарированный газ поступает сразу на установку осушки.
Рис. 5.5 1 вариант расчетной схемы сбора газа (по 5 коллекторам) Рис. 5.6 2 вариант расчетной схемы сбора газа (по 5 коллекторам) Рис. 5.7 3 вариант расчетной схемы сбора газа (по 5 коллекторам) Рис. 5.8 4 вариант расчетной схемы сбора газа (по 5 коллекторам)
Таблица 5.3 Потребное количество труб и металлоемкость по вариантам
Наружный диаметр и | Количество, км. | ||||
толщина стенки, мм. | I вариант | II вариант | III вариант | IV вариант | |
720×10 | ; | ; | 9,4 | 10,5 | |
219х6 | 1,7 | 0,7 | 0,9 | 0,8 | |
273х6 | 5,3 | 2,0 | 1,6 | 2,6 | |
325х7 | 18,1 | 9,9 | 15,2 | 18,7 | |
426х9 | 10,0 | 21,3 | 7,3 | 10,3 | |
530х8 | 16,7 | 17,9 | 18,2 | 10,5 | |
Общая протяженность, км. | 51,8 | 51,8 | 52,6 | 58,8 | |
Металлоемкость, т. | |||||
Температурный режим систем сбора определяет технологический режим газа на УКПГ, условия гидратообразования и меры по их предотвращению. Согласно термодинамическим расчетам устьевая температура потока газа в основной период оценивается в 17 0С. Температура смешанного потока в точках врезки кустов определялась на основе теплового баланса. Расчет температурного режима проведен для характерных участков в точках смешения потоков и смены диаметров шлейфов. Результаты расчета температурного режима для II варианта приведены в табл. 5.3.
Таблица 5.3 Температуры гидратообразования
Давление, кг/см2 | |||||||
Температура гидратообразования, 0 С | 7,6 | 6,9 | 6,1 | 5,3 | 4,4 | 3,4 | |
При пуске кустов в зимний период необходима подачи ингибитора (метанола) на время прогрева шлейфов.
5.3 Анализ эффективности системы подготовки газа
Подготовка газа к транспорту осуществляется в несколько этапов:
1) очистка от механических примесей;
2) осушка газа.
Очистка от механических примесей
К механическим примесям относятся частицы породы, выносимые газовым потоком из скважины, строительный шлак, оставшийся после окончания строительства промысловых газосборных сетей и магистральных трубопроводов, продукты коррозии и эрозии внутренних поверхностей и жидкие включения конденсата и воды.
Согласно техническим требованиям на природные и нефтяные газы содержание жидкой взвеси в транспортируемом газе не должно превышать 25—50 г. на 1000 м³ газа. Еще более жесткие требования необходимо предъявлять к содержанию твердой взвеси (не более 0,05мг/м3), которая способствует эрозионному износу технологического оборудования газопроводов. Так, при содержании 5—7 мг/м3 твердой взвеси к.п.д. трубопроводов уменьшается на 3—5% в течение двух месяцев эксплуатации, а при запыленности более чем ЗОмг/м3 трубопровод выходит из строя через несколько часов из-за полного эрозионно-ударного износа.
По принципу работы аппараты для очистки газа от механических примесей подразделяются на:
работающие по принципу «сухого» отделения пыли. В таких аппаратах отделение пыли происходит в основном с использованием сил гравитации и инерции. К ним относятся циклонные пылеуловители, гравитационные сепараторы, различные фильтры;
работающие по принципу «мокрого» улавливания пыли. В этом случае удаляемая из газа взвесь смачивается промывочной жидкостью, которая отделяется от газового потока, выводится из аппарата для регенерации и очистки и затем возвращается в аппарат. К ним относятся масляные пылеуловители, шаровые скрубберы и т. д.;
использующие принцип электроосаждения. Данные аппараты почти не применяются для очистки природного газа.
Наиболее широко используются аппараты «мокрого» и «сухого» пылеулавливания.
Для ограничения выноса из месторождения породы призабойную зону оборудуют фильтром.
На промысле газ проходит очистку в наземных сепараторах, в которых сепарируется жидкость (вода и конденсат) и газ очищается от частиц породы и пыли. Промысловые очистные аппараты работают, используя свойства выпадения взвеси под действием силы тяжести при уменьшении скорости потока газа или используя действие центробежных сил при специальной закрутке потока. Поэтому промысловые аппараты очистки делятся на гравитационные и циклонные. Гравитационные аппараты бывают вертикальные и горизонтальные. Вертикальные гравитационные аппараты рекомендуются для сепарации газов, содержащих твердые частицы и тяжелые смолистые фракции, так как они имеют лучшие условия очистки и дренажа.
Вертикальные сепараторы изготовляют диаметром 400—1650мм, горизонтальные — диаметром 400—1500мм при максимальном давлении 16 МПа. При оптимальной скорости эффективность сепарации составляет до 80%.
Осушка газа.
При больших объемах транспортируемого газа его осушка является наиболее эффективным и экономичным способом предупреждения образования кристаллогидратов в магистральном газопроводе. Существующие способы осушки при промысловой подготовке газа к транспорту подразделяются на две основные группы: абсорбция и адсорбция и охлаждение газового потока.
В результате осушки газа точка росы паров воды должна быть снижена ниже минимальной температуры при транспортировании газа.
Сорбционные способы осушки газа
Жидкие сорбенты, применяемые для осушки природных и нефтяных газов, должны иметь высокую растворимость в воде, низкую стоимость, хорошую антикоррозионность, стабильность по отношению к газовым компонентам и при регенерации; простоту регенерации, малую вязкость и т. д.
Большинству этих требований наилучшим образом отвечают ДЭГ и ТЭГ и в меньшей степени ЭГ.
Этиленгликоль (СН2ОН—СН2ОН) — простейший двухатомный спирт, используется в основном как ингибитор, не применяется для осушки
Диэтиленгликоль (СН2ОН-СН2-О-СН2-СН2ОН) в химически чистом виде — бесцветная жидкость. Как показали эксперименты в лабораторных и промышленных условиях, максимальное понижение точки росы газа при осушке ДЭГ обычно не превышает 30—35° С, что довольно часто оказывается недостаточным. В связи с разработкой более глубоких газовых месторождений, температура газа которых значительная и в летнее время почти не понижается в коммуникациях до газоосушительных установок, потребовался более сильный влагопоглотитель.
Триэтиленгликоль (СН2ОН-СН2-О-СН2- О-СН2-СН2ОН) получают соединением трех молекул ЭГ с образованием воды.
Гликоли хорошо озирают влагу из газов в большом интервале температур.
При сравнении ДЭГ и ТЭГ необходимо иметь в виду, что ДЭГ более дешевый. Однако при использовании ТЭГ можно получить большее снижение точки росы газа (на 45—50°). Потери ТЭГ при регенерации значительно меньше, чем потери ДЭГ вследствие более низкой упругости паров.
Экономичность работы абсорбционных установок в значительной степени зависит от потерь сорбента. Для их снижения в первую очередь необходимо строго поддерживать расчетный температурный режим десорбера, тщательно сепарировать газ и водяной пар и по возможности исключить пенообразование при контакте газа с абсорбентом за счет специальных добавок.
Осушка газа твердыми поглотителями
В качестве твердых поглотителей влаги в газовой промышленности широко применяются активированная окись алюминия и боксит, который на 50—60% состоит из Al2O3. Поглотительная способность боксита 4,0—6,5% от собственной массы.
Преимущества метода: низкая точка росы осушенного газа (до —65° С), простота регенерации поглотителя, компактность, несложность и низкая стоимость установки.
Осушка газа молекулярными ситами
Для глубокой осушки применяют молекулярные сита, так называемые цеолиты. Цеолиты состоят из кислорода, алюминия, кремния и щелочноземельных металлов и представляют собой сложные неорганические полимеры с кристаллической структурой. Форма кристалла цеолита — куб, на каждой из шести сторон его имеются щели, через которые влага проникает во внутреннее пространство. Каждый цеолит имеет свой размер щелей, образованных атомами кислорода. Благодаря этому цеолиты способны резко избирательно сорбировать в основном мелкие молекулы, т. е. при адсорбции происходит как бы отсеивание более мелких от более крупных молекул. Мелкие молекулы проникают во внутреннее пространство кристалла и застревают в нем, а крупные молекулы не проходят и, следовательно, не будут адсорбироваться.
Цеолиты, применяемые в виде порошка или гранул размером до 3 мм, обладают высокой пористостью (до 50%) и огромной поверхностью пор. Их активность достигает 14—16 г. на 100 г. цеолитов при парциальном давлении 0,4 мм рт.ст.
Для регенерации молекулярных сит используют сухой газ, нагретый до 200−300° С, который пропускают через слой цеолита в направлении, обратном движению газа при осушке.
Цеолиты выдерживают до 5000 циклов, теряя при этом около 30% своей поглотительной способности.
Осушка газа охлаждением.
Охлаждение широко применяется для осушки и выделения конденсата и газа газоконденсатных месторождений на установках низкотемпературной сепарации, а также при получении индивидуальных компонентов газа сжижении газов и т. д.
Газ можно охлаждать путем расширения, когда необходимо снижать его давление, а также пропуская через холодильные установки. В условиях Крайнего Севера для охлаждения газа можно использовать низкую температуру окружающего воздуха (в зимнее время).
Процесс расширения с целью понижения температуры осуществляется двумя способами — дросселированием без совершения внешней работы (изоэнтальпийный процесс) или адиабатическим расширением с отдачей внешней работы (изоэнтропийный процесс).
В тех случаях, когда давления газа на входе в установки низкотемпературной сепарации недостаточно для его охлаждения расширением, устанавливают холодильные установки, заменяющие или дополняющие узел расширения. Необходимая температура сепарации может обеспечиваться за счет установки дополнительных теплообменников-рекуператоров и холодильников. Для предупреждения гидратообразования перед теплообменником в поток сырого газа впрыскивается гликоль. Предусмотрен также ввод ингибитора.
Рассматривая рациональную область применения указанных способов осушки и извлечения конденсата из природных и попутных газов, необходимо отметить, что осушку весьма тощих газов (чисто газовых месторождений) целесообразно вести с применением диэтиленгликоля и триэтиленгликоля, активированного боксита и цеолитов. Применять другие методы нерентабельно. Если же требуется только частичное удаление влаги из газа (получение точек росы не ниже —10° С), лучше применять гликоли. Для более глубокой осушки, а также при необходимости получения отдельных фракций желательно осушку вести активированным бокситом или цеолитом. Осушку и извлечение конденсата из газа газоконденсатных месторождений, в газах которых находится достаточно много конденсата, как правило, наиболее выгодно производить на установках низкотемпературной сепарации. При этом эффективность использования низкотемпературной сепарации газа зависит от начального давления и темпов его падения.
Для подготовки газа целесообразно применение метода абсорбционной осушки газа с использованием в качестве абсорбента триэтиленгликоля (ТЭГа) концентрации 98,5 массовых.
Метод абсорбционной осушки газа имеет ряд преимуществ: непрерывность, гибкость работы в условиях зимы и лета за счет изменения концентрации и количества ТЭГа; полная автоматизация технологического процесса; меньшие потери давления в абсорберах; отсутствие низконапорного газа, подлежащего утилизации с применением компрессорных агрегатов; меньшая металлоемкость основного оборудования; возможность работы в широком диапазоне давлений и нагрузок.
Применение для осушки газа ТЭГа, а не диэтиленгликоля (ДЭГа) основано на анализе сравнительных показателей абсорбентов (технические преимущества, физико-химические свойства, осушающая способность).
На основе анализа выявлены преимущества ТЭГа: более глубокая осушка газа, меньшие потери от уноса с газом и от термического разложения, лучшая регенерируемость, сокращение расхода топливного газа на регенерацию.
ТЭГ имеет более высокую температуру начала термического разложения (206С), ДЭГ-(164С). Применение ТЭГа позволяет использовать установку атмосферной регенерации, для регенерации ДЭГа необходима более дорогостоящая установка вакуумной регенерации. Возможность нагрева ТЭГа до более высоких температур позволяет уменьшить остаточное количество конденсата в регенерированном растворе.
Применение более вязкого ТЭГа позволяет сократить его унос с осушенным газом с 15 до 7г/1000м3. ТЭГ имеет по сравнению с ДЭГом более высокую температуру вспышки паров (158С и 135С соответственно) и воспламенения (170С и 143С), что снижает пожарную опасность объекта.
Гликоли относятся к веществам с относительно низкой токсичностью. При этом ТЭГ считается менее токсичным, что объясняется меньшим значением давления насыщенных паров. Таким образом, применение ТЭГа обеспечивает повышение безопасности эксплуатации и экологичности технологических установок.
Проектом предусматривается подготовка газа месторождения к транспорту совместно с газом Етыпуровского месторождения на УКПГ, расположенной на Вынгаяхинском месторождении.
Рассматриваемый вариант совместной подготовки газа Вынгаяхинского и Етыпуровского месторождений на УКПГ Вынгаяхинского месторождения по сравнению с раздельной подготовкой газа на месторождениях имеет свои преимущества и недостатки.
К недостаткам относятся:
— строительство дополнительной установки сепарации для газа Етыпуровского месторождения на УКПГ;
— увеличение диаметра межпромыслового газопровода от Етыпуровского месторождения с Ду 1000 до Ду 1200 мм.;
— увеличение мощности ДКС в связи с большими потерями давления в межпромысловом газопроводе при подаче газа с Етыпуровского месторождения под собственным давлением по сравнению с подачей под давлением ДКС;
— дополнительный расход метанола на ингибирование межпромыслового газопровода;
— увеличение ёмкости склада метанола на Етыпуровском месторождении.
К преимуществам относятся:
— концентрация мощностей по подготовке и компримированию газа на одной площадке с размещением объектов инфраструктуры и инженерного обеспечения;
— использование для осушки газа оборудования большой производительности;
— уменьшение количества резервного оборудования установки осушки газа, регенерации ТЭГа и ДКС;
— использование одного типа газоперекачивающих агрегатов;
— сокращение сроков строительства УКПГ и ДКС при размещении их на одной площадке;
— сокращение площадей застройки УКПГ, ДКС, ОБП при размещении их на одной площадке;
— возможность использования единой установки регенерации ТЭГа;
— отсутствие необходимости завоза ТЭГа для осушки газа на Етыпуровское месторождение;
— сокращение площадей строительства на Етыпуровском месторождении приводит к уменьшению экологического ущерба.
В проекте обустройства Вынгаяхинского месторождения предусматриваются следующие объекты основного технологического назначения:
кусты газовых скважин;
УКПГ;
дожимная компрессорная станция (ДКС).
Газ от кустов скважин по шлейфам и двум сборным коллекторам под собственным давлением подаётся на УКПГ. Прокладка газосборных сетей принята подземная, режим работы — безгидратный, запас температур газа от равновесной температуры гидратообразования составляет 2−40С.
Газ Етыпуровского месторождения из межпромыслового газопровода поступает на установку сепарации газа.
Газ обоих месторождений не содержит вредных примесей, содержание углеводородного конденсата незначительно, поэтому для его подготовки к транспорту в соответствии с ОСТ 51.40−93 необходима очистка от мехпримесей и воды до точки росы по воде в зимний период — минус 20С, в летний период — минус 10С.
Очистка газа от капельной влаги и мехпримесей на УКПГ производится в сепараторах производительностью 10 млн. м3/сут. каждый, рекомендуемое число аппаратов выбирается с учётом разницы давлений отдельно для каждого месторождения: для Вынгаяхинского — две штуки, для Етыпуровского — четыре штуки и один общий резервный сепаратор.
Для осушки газа предусмотрено семь абсорберов (один резервный) производительностью 10 млн. м3/сут. каждый.
В связи с тем, что в составе газа после ДКС с пятого года эксплуатации появляется капельная жидкость (до 0,45 м.3/час) в абсорберах необходимо увеличить высоту массообменной части по сравнению с аналогом (ГП1467.02.00.000), для снижения уноса с газом ТЭГа — применить регулярную насадку.
Насыщенный триэтиленгликоль с концентрацией 95,4% подается на установку атмосферной регенерации.
После регенерации ТЭГ возвращается в технологический процесс.
Для восполнения потерь ТЭГа предусмотрена его подача со склада. Величина потерь ТЭГа — 10 г на 1000 м³ газа — принята согласно данных ООО «Ноябрьскгаздобыча», полученных при эксплуатации Губкинского УКПГ. Максимальный годовой расход ТЭГа составляет 200 т/год. Для осушки газа в технологическом процессе циркулирует от 23,5 т/сут. ТЭГа в первые годы до 456 т/сут. ТЭГа в конце периода постоянной добычи газа.
При работе без ДКС газ после установки сепарации поступает на установку осушки.
В связи с низким пластовым давлением газа Вынгаяхинского месторождения для обеспечения необходимого давления газа в точке врезки в магистральный газопровод требуется ввод ДКС с третьего года эксплуатации.
Подключение ДКС предусмотрено между установкой сепарации газа и установкой осушки газа. При работе с ДКС газ с расчетной температурой 25С (летом) и 15С (зимой) поступает в абсорберы для осушки.
Для комплексной подготовки газа применяется оборудование, разработанное ЦКБН и поставленное на промышленное производство.
Предусматривается коллекторная схема подключения сепараторов и абсорберов, позволяющая выполнять ремонтные работы одного аппарата без остановки других. Для предупреждения гидратообразования в обвязке оборудования установки сепарации газа предусмотрена подача метанола во входные потоки газа перед арматурой, отключающей газосборные коллектора, и на вход каждого сепаратора. Подготовленный к транспорту газ подаётся через пункт измерения расхода в трубопровод внешнего транспорта Ду 1000 мм. Структурная схема УКПГ приведена на рисунке 5.5. Технологические показатели разработки и параметры газа Вынгаяхинского месторождения приведены в таблице 5.4.
Таблица 5.4 Технологические показатели разработки и параметры газа
Год разработки | Добыча, млрд. м3 | Дебит скважин, тыс. м3/ сут. | Фонд скважин, шт. | Давление, МПа | Температура, 0 С | ||||
устьевое | на входе в сепаратор | устьевая | на входе в сепаратор | Гидратообразования в шлейфах | |||||
6,75 | 6,65 | 13,2 | 10,6 | 8,6 | |||||
3,5 | 6,44 | 6,14 | 13,3 | 10,8 | 8,0 | ||||
5,0 | 6,16 | 5,85 | 13,3 | 10,6 | 7,5 | ||||
5,0 | 5,89 | 5,58 | 13,3 | 10,6 | 7,1 | ||||
5,0 | 5,63 | 5,31 | 13,3 | 10,6 | 6,6 | ||||
5,0 | 5,39 | 5,05 | 13,3 | 10,6 | 6,1 | ||||
5,0 | 3,66 | 3,07 | 13,3 | 10,6 | 1,6 | ||||
2,342 | 1,89 | 1,60 | 6,7 | 4,4 | — 4,2 | ||||
0,662 | 1,00 | 0,92 | 2,6 | 0,8 | — 8,9 | ||||
Пластовая вода из сепараторов направляется в дегазаторы и после разгазирования — на очистные сооружения, максимальная концентрация метанола составляет до 1,75% объёмных.
В составе УКПГ для сброса газа перед ремонтами и при авариях предусмотрена свеча рассеивания, т.к. газ месторождения легкий (относительная плотность 0,564), постоянные сбросы газа отсутствуют, в сбросах отсутствуют вещества 1 и 2 класса опасности, кроме того, плата за выбросы загрязняющих веществ в атмосферу при сжигании газа превышает плату за выбросы без сжигания в 5 раз.
Для слива жидких продуктов из оборудования на период ремонтов предусмотрены дренажные ёмкости.
5.4 Установка комплексной подготовки газа
Технология комплексной подготовки газа к транспорту включает следующие процессы:
— сепарацию газа для очистки от капельной жидкости, выносимой из пласта;
— абсорбционную осушку газа раствором ТЭГа;
— регенерацию ТЭГа и возвращение его в технологический процесс осушки газа;
— дистанционное отключение коллекторов от УКПГ и переключение их на свечу;
— защиту технологического оборудования от превышения давления;
— подогрев и редуцирование газа на собственные нужды;
— замер количества осушенного газа и подачу в магистральный газопровод;
— аварийное опорожнение установок и рассеивание газа на свече;
— хранение ТЭГа, метанола и использование их в технологическом процессе.
Для осуществления названных процессов в составе УКПГ предусмотрены следующие технологические объекты:
— установка переключающей арматуры и сепарации газа;
— установка осушки и регенерации ТЭГа;
— пункт измерения расхода газа;
— дренажные ёмкости;
— свеча рассеивания;
— внутриплощадочные технологические трубопроводы.
Установка переключающей арматуры; оборудование для сепарации и осушки газа, регенерации ТЭГа, подготовки газа на собственные нужды; пункт измерения расхода газа размещаются в отдельных цехах (зданиях); дренажные ёмкости — на открытой площадке.
5.4.1 Цех входа и сепарации газа
Газ от кустов скважин Вынгаяхинского месторождения по коллекторам и газ Етыпуровского месторождения по трубопроводу Ду 1200 мм. поступает на установку входа и сепарации газа, включающую узлы переключающей арматуры, семь сепараторов производительностью 10 млн. м3/сут. каждый, два дегазатора для сбора пластовой воды.
Узлы переключающей арматуры предназначены для:
— подключения газосборных коллекторов от кустов скважин к общему сборному коллектору и трубопровода Ду 1200 мм. и распределения подачи газа по сепараторам;
— дистанционного отключения газосборных коллекторов от УКПГ и переключения их для продувки на свечу;
— распределения и регулирования подачи метанола.
Каждый коллектор входа газа в цех оборудуется пневмогидрокраном, который служит для отключений коллектора и цеха, в том числе и аварийных; ручным краном для продувки газосборного коллектора на свечу; электроприводной арматурой для ввода метанола. Газосборные коллектора Вынгаяхинского месторождения дополнительно оборудуются ручными кранами — регуляторами для выравнивания давления на входе и подключаются к общему сборному коллектору Ду 700 мм.
На каждом коллекторе входа газа производится замер температуры и давления газа с передачей данных в операторную.
При падении давления газа в газосборных коллекторах до отсекающих кранов производится автоматическое отключение коллекторов, при превышении давления выше допустимого — 7,5 МПа — выдаётся аварийный сигнал.
Общий сборный коллектор служит одновременно для предварительной сепарации газа от жидкости, особенно при ее пробковом поступлении из системы сбора, и распределения газа по сепараторам. Слив жидкости из общего сборного коллектора осуществляется в дренажную емкость.
Из общего сборного коллектора газ поступает в сепараторы.
В сепараторах производится отделение механических примесей, солей, улавливание капельной жидкости, выносимой из пласта, и частично метанола путём промывки рефлюксной водой. Сепараторы применены по типу ГП 1467.02.00.000 с промывочной секцией для снижения засоления ТЭГа.
Равномерная загрузка сепараторов по сырому газу производится с помощью электроприводных кранов-регуляторов КлР 2.8…КлР 2.14, установленных на трубопроводах выхода газа из сепараторов, по расходу газа, за счёт отбора газа из общего сборного коллектора.
На входе и выходе газа из каждого сепаратора установлены пневмогидрокраны с дистанционным управлением, позволяющие осуществить аварийную остановку сепаратора.
Газ после сепарации поступает на установку осушки газа или на ДКС.
Уловленная в сепараторах жидкость поступает в дегазатор Д 1 и после разгазирования — на очистные сооружения.
Газ из дегазаторов используется на собственные нужды.
Предусмотрена подача метанола для предотвращения гидратообразования в общем сборном коллекторе и сепараторах.
Распределение подачи метанола осуществляется по системе трубопроводов с помощью электрозадвижек, регулирование — насосов с регулируемой подачей.
При ремонтах освобождение технологического оборудования и трубопроводов от газа осуществляется на свечу рассеивания, жидкость сливается в дренажную ёмкость. Предусмотрены узлы учёта всех сбрасываемых продуктов.
В качестве регулирующей арматуры применены: краны-регуляторы расхода газа — шаровые краны с электроприводом и краны-регуляторы давления Вынгаяхинского газа — ручные шаровые краны наземной установки производства ООО «Самараволгомаш» класса давления 600; регуляторы уровня жидкости в сепараторах и дегазаторах и давления газа в дегазаторах — арматура с электроприводом, входящая в состав блоков оборудования разработки ЦКБН.
Компоновка оборудования в помещении одноярусная. Для механизации грузоподъемных работ при ремонтах установлен ручной подвесной кран.
5.4.2 Цех осушки газа и регенерации ТЭГа
В цехе выделены:
— помещение осушки газа;
— помещение огневых регенераторов;
— помещение насосно — емкостного оборудования.
Газ после сепарации или от ДКС поступает на общую установку осушки газа, состоящую из семи абсорберов (один резервный) с арматурными блоками.
Равномерная загрузка абсорберов производится с помощью электроприводных кранов-регуляторов КлР 3.15…КлР 3.21, установленных на трубопроводах выхода газа из абсорберов, по расходу газа; производится регулирование уровня насыщенного ТЭГа, замер и регулирование подачи регенерированного ТЭГа.
В абсорберах газ осушается РТЭГом концентрацией 98,5%.
РТЭГ подается в абсорберы насосами, установленными для удобства обслуживания в помещении осушки газа. Регулирование подачи РТЭГа осуществляется с помощью замерных устройств и регулирующих клапанов, входящих в состав арматурных блоков.
НТЭГ из помещения осушки газа по коллектору подается на регенерацию.
Осушенный газ после абсорберов поступает на пункт измерения расхода газа.
На входе и выходе газа из каждого абсорбера установлены пневмогидрокраны с дистанционным управлением, позволяющие осуществить аварийную остановку абсорбера и цеха. Предусмотрено освобождение каждого абсорбера на свечу рассеивания, жидкость сливается в дренажную емкость.
В помещении осушки газа размещён узел подготовки газа на собственные нужды, включающий теплообменник, узлы редуцирования и замера количества газа.
В качестве дистанционной регулирующей арматуры применены: краны-регуляторы расхода газа — шаровые краны с электроприводом наземной установки производства ООО «Самараволгомаш» класса давления 600; регуляторы подачи РТЭГа и уровня НТЭГа в абсорберах — арматура с электроприводом, входящая в состав блоков оборудования разработки ЦКБН.
Компоновка оборудования в помещении осушки газа одноярусная. Для механизации грузоподъемных работ при ремонтах установлен ручной подвесной кран.
Для слива ТЭГа при аварии и перед ремонтом оборудования рядом с помещением осушки газа размещается дренажная емкость.
В помещениях насосно-емкостного оборудования и огневых регенераторов размещены: дегазаторы, блоки фильтров и аппарата магнитной обработки, теплообменники, блоки регенерации, арматурные блоки, сборник солей, конденсаторы воздушные, емкость разделителя рефлюкса, насосы орошения, горячие насосы.
Для регенерации ТЭГа используются блоки с огневыми испарителями БОР 1 по типу ГП 1467.08.00.000−01 производительностью 20 м3/час каждый.
Предусматривается коллекторное подключение оборудования.
Компоновка оборудования в помещении насосно-емкостного оборудования одноярусная, в помещении огневых регенераторов — двухъярусная. На первом ярусе размещены блоки регенерации ТЭГа и блоки горячих насосов, на втором — установлены арматурные блоки и сборник солей.
Для механизации грузоподъемных работ при ремонтах установлены ручные подвесные краны.
Оборудование, трубопроводы и арматура с температурой более 45С теплоизолируются.
Для слива ТЭГа при аварии и перед ремонтами оборудования рядом с помещением огневых регенераторов размещается дренажная емкость.
5.4.3 Пункт измерения расхода газа
После осушки газ поступает на пункт измерения расхода газа, предназначенный для коммерческого замера расхода.
Пункт измерения расхода газа выполнен в соответствии с нормами для коммерческого замера расхода — РД 50−213−80, ГОСТ 8.563.1−97…ГОСТ 8.563.3−97 и состоит из четырёх рабочих замерных линий (одна резервная), оборудованных устройствами быстросменными сужающими типа УСБ Ду 700 мм.; Ру8 МПа, предназначенными для измерения перепада давления на диафрагме, а в комплекте с дифманометром — для измерения расхода газа.
Замерные устройства расположены в отапливаемом здании, отключающая арматура — на открытой площадке.
Для проведения ремонтных работ предусматривается сброс давления с каждой линии на свечу.
5.4.4 Дренажные ёмкости
Для слива жидких продуктов (пластовой воды, ТЭГа) из оборудования и трубопроводов при аварии и перед ремонтом рядом с цехами предусмотрены подземные дренажные ёмкости объёмом 12,5 и 40 м³ с электронасосными агрегатами во взрывозащищенном исполнении и свечами рассеивания с огнепреградителем. По мере накопления продукт из емкостей откачивается: пластовая вода — на утилизацию через узел учёта, расположенный в цехе входа и сепарации газа, ТЭГ возвращается в технологический процесс.
5.4.5 Свеча рассеивания
Для освобождения от газа технологического оборудования при подготовке к ремонту, для продувки коллекторов и сброса газа в аварийных ситуациях предусматривается свеча рассеивания Ду 500 мм.
Диаметр свечи рассеивания определён по максимально допустимой скорости истечения газа в атмосферу в соответствии с требованиями ВНТП 01−81. Высота свечи, равная 40 м, обеспечивает эффективное рассеивание сбрасываемого газа, исключает образование взрывоопасных концентраций в зоне размещения технологического оборудования, зданий и сооружений. Максимальная приземная концентрация метана (равная 0,98 ПДК), достигается на расстоянии 1700 м от свечи рассеивания.
5.4.6 Внутриплощадочные трубопроводы
На площадке УКПГ основные газовые коллекторы прокладываются подземно, трубопроводы замерных линий на пункте измерения расхода газа — надземно, технологические трубопроводы — надземно на отметке не менее 2,2 м от уровня земли и 5 м над дорогами.
Предусмотрена возможность временной подачи газа в газопровод, минуя цех осушки газа.
На газовом коллекторе предусмотрена установка крановых узлов в укрытии для подключения ДКС.
Все трубопроводы прокладываются с учетом их тепловых удлинений, которые компенсируются принятой конфигурацией или П-образными компенсаторами.
На трубопроводах входа метанола и ТЭГа в цеха устанавливаются электроприводные задвижки, автоматически закрывающиеся при пожаре.
Трубопроводы и арматура с температурой более 45С теплоизолируются.
Подземные трубопроводы покрываются антикоррозионной изоляцией усиленного типа согласно СНиП 2.05−06−85* и ГОСТ Р 51 164−98, надземные трубопроводы — лакокрасочными покрытиями, теплоизоляция трубопроводов предусмотрена плитами теплоизоляционными из минеральной ваты на синтетическом связующем.
Выбор труб выполняется в соответствии с требованиями «Инструкции по применению труб в газовой и нефтяной промышленности», трубопроводы запроектированы из труб группы В сталь 09Г2С, сортамент по ГОСТ 8732–78, технические условия на изготовление по ГОСТ 8731–74.
5.5 Дожимная компрессорная станция
Дожимная компрессорная станция (ДКС) предназначена:
для обеспечения необходимого давления газа в точке подключения к магистральному газопроводу.
для поддержания давления газа и расчетной производительности абсорберов установки осушки газа.
Подключение ДКС выполнено до УКПГ. ДКС размещается на площадке, смежной с УКПГ.
Преимущества использования газоперекачивающих агрегатов ГПА-Ц-16С следующие:
агрегаты позволяют в одном и том же корпусе компрессора устанавливать сменные проточные части, что требуется для изменения степеней сжатия ДКС и полной загрузки рабочих ГПА на весь период эксплуатации месторождения;
ГПА-Ц-16С является одним из наиболее экономичных агрегатов, выпускаемых в России и на Украине. В «Концепции энергосбережения в ОАО „Газпром“ на 2001;2002годы» представлены технические показатели ГПА нового поколения производства российских и украинских фирм. КПД ГПА-Ц-16С с двигателем ДГ-90 составляет 34%.
Газодобывающие объекты Вынгаяхинского и Етыпуровского месторождения входят в состав ООО" Ноябрьскгаздобыча", где имеются аналогичные газоперекачивающие агрегаты на ДКС Комсомольского и Губкинского газовых месторождений. Унификация типов ГПА облегчает и делает более экономичным обслуживание и ремонт агрегатов.
В составе ДКС предусматриваются следующие здания и сооружения:
· установка очистки газа;
· установка компримирования газа;
· установка охлаждения газа;
· установка подготовки топливного и импульсного газа;
· емкость дренажная, V=8м?;
· площадка свечей;
· маслохозяйство;
· вспомогательные объекты.
По предлагаемому варианту строительство ДКС осуществляется в три очереди.
Первая очередь строительства предусматривает ввод:
· семи ГПА на конечное давление 7,45МПа,
· установки очистки газа,
· установки охлаждения газа из тридцати семи АВО,
· установки подготовки топливного и импульсного газа на полное развитие ДКС,
· вспомогательных объектов, рассчитанных на полное развитие ДКС.
Вторая очередь строительства предусматривает ввод четырех ГПА на конечное давление 5,49МПа.
Прокладка основных технологических газопроводов по площадке ДКС предусматривается подземная, трубопроводы топливного и импульсного газа прокладываются надземно.
Узел подключения ДКС предусмотрен в составе УКПГ и состоит из входного крана № 7, выходного крана № 8, крана № 38 на байпасной линии и обводных кранов № 7', № 8' и № 38', предназначенных для заполнения контура ДКС и выравнивания давления перед открытием основных кранов.
Газ по газопроводу диаметром 1220 мм. после первой ступени очистки на УКПГ поступает на установку второй ступени очистки (УОГ), затем по трубам диаметром 1020 мм. поступает к ГПА.
Схема подключения ГПА — параллельная, коллекторная, с секционированием по ступеням сжатия, каждый агрегат имеет отключающую арматуру.
Для нормальной работы ГПА к ним подводятся:
— топливный и импульсный газ от установки подготовки топливного и импульсного газа;
— масла чистые со склада ГСМ.
Схемой предусматривается работа ГПА в режиме «кольцо» (краны № 6р, № 6'р и № 6''р) и защита от превышения давления газа на выходе.
Запуск ГПА производится через пусковой контур и систему противопомпажной защиты.
Для продувки технологических газопроводов на общую свечу при остановке ДКС предусматриваются краны № 17, № 18, для продувки ГПА на индивидуальные свечи — краны № 5, для продувки контуров ГПА на индивидуальные свечи — краны № 9.
После сжатия до расчетного давления газ по трубопроводам диаметром 1020 мм. подается на установку охлаждения газа.
Обвязка аппаратов воздушного охлаждения газа (АВО) — предусмотрена коллекторной, с секционированием по ступеням сжатия, каждый аппарат имеет ручную отключающую арматуру. К установке охлаждения газа подводится импульсный газ для управления кранами.
5.5.1 Установка очистки газа
В состав установки очистки газа входят блоки фильтров — сепараторов по типу ГП 835.00.00.000−07 разработки ЦКБН. Основные технические характеристики указаны в таблице 5.5.
Фильтры-сепараторы предназначены для очистки природного газа от жидкости и механических примесей с целью защиты нагнетателей ГПА.
Фильтры-сепараторы устанавливаются в здании. Размеры здания 54,4×18,0 (м.) Для производства ремонтных работ в здании предусмотрена таль грузоподъемностью 1 т.
Согласно графика зависимости производительности фильтра-сепаратора от рабочего давления на полное развитие ДКС (с 2014 года) требуется пять фильтров-сепараторов (4 рабочих, 1 резервный), на первую очередь строительства — 4 шт. (3 рабочих, 1 резервный).
Таблица 5.5 Основные технические характеристики фильтра-сепаратора
Наименование | Величина | |
Производительность по газу, млн.нм.?/сут. | 25,0 | |
Давление, МПа рабочее расчетное | 7,5 7,5 | |
Расчетная температура стенки аппарата, находящегося под давлением, °С | ||
Минимальная допустимая температура стенки элементов блока, находящегося под давлением, °С | Минус 55 | |
Масса, т. | 36,5 | |
5.5.2 Установка компримирования газа
В состав установки компримирования газа входит газоперекачивающий агрегат ГПА-16, который представляет собой блочно-контейнерный автоматизированный агрегат с газотурбинным приводом мощностью 16 МВт.
Агрегаты ГПА-16 позволяют в одном и том же корпусе компрессора устанавливать сменные проточные части (СПЧ) с отношением давлений входа и выхода газа 1,25; 1,44; 1,7 и 2,2.
Изменение степеней сжатия ДКС достигается своевременной заменой СПЧ нагнетателей.
В расчетах количества ГПА и подбора СПЧ учитывалось приращение температуры газа на выходе из нагнетателя.
В то же время при использовании ГПА со степенью сжатия 2,2 значительно увеличивается температура газа на выходе из нагнетателя. Если приращение температуры газа для ГПА со степенью сжатия 1,7 составляет 50? С, то для ГПА со степенью сжатия 2,2 — 80? С. При работе ДКС в две и более ступеней со степенью сжатия 2,2 и использованием АВО газа в жаркие дни летнего периода температура газа на входе второй и последующих ступеней может подняться до 40? С, а на выходе 120? С.
Выпускаемая предприятиями России трубопроводная арматура рассчитана на температуру газа не более 80? С, монтаж трубопроводов необходимо будет заканчивать при положительных температурах воздуха, увеличатся размеры звеньев обвязки ГПА, компенсирующих температурные деформации.
Снизить температуру газа на входе второй и последующих ступеней ДКС до 0? С, возможно используя в летний период станцию охлаждения газа, что значительно усложнит ДКС и увеличит капитальные затраты.
Для упрощения обвязки ДКС и сокращения количества ступеней сжатия до трех на первой ступени можно использовать агрегаты ГПА со степенью сжатия 2,08, на второй и третьей со степенью сжатия 1,7. При этом температура газа на выходе ГПА всех ступеней не превысит 80? С. Запуск первого агрегата будет производиться по «большому» кольцу через установку охлаждения во избежание перегрева центробежного нагнетателя.
Исходя из вышеуказанного применение СПЧ со степенью сжатия 2,2 возможно только на первой ступени сжатия, в связи с тем, что температура газа на входе УКПГ не превышает 11 °C и имеется тенденция к понижению температуры входного газа по годам.
5.5.3 Установка охлаждения газа
После компримирования охлаждение газа производится для обеспечения теплового режима работы оборудования цеха осушки газа и газопровода внешнего транспорта газа.
Температура газа на входе цеха осушки газа допускается в пределах от 15 до 25С.
Максимальная температура газа, допустимая для нормальной работы газопровода внешнего транспорта, не должна превышать 40С.
Температура газа на входе в ГПА, согласно данным предприятия-изготовителя, допускается от минус 30С до плюс 45С, а при кратковременной работе на «кольцо"-до +60С.
Расчетная температура газа на входе в ДКС в летний период +11С.
Охлаждение газа предусматривается аппаратами воздушного охлаждения (АВО) сырого газа с рециркуляцией нагретого воздуха. Аппараты с рециркуляцией нагретого воздуха предназначены для предотвращения переохлаждения газа в нижних рядах труб секций при помощи системы автоматического управления положением створок входных, выходных и переточных жалюзи.
В проекте рассмотрены варианты применения двух типов АВО:
АВГБС-83Р, разработки и поставки АО" Кедр" ;
ГП 1911, разработки ЦКБН.
Основные технические характеристики указанных АВО представлены в таблице 4.4.7.
Таблица 5.6 Основные технические характеристики
Наименование | Величина | ||
АВГБС-83Р | ГП 1911 | ||
Расчетная поверхность охлаждения, м2 | |||
Коэффициент оребрения труб | 4-х верхних рядов-20 2-х нижних рядов-14,6 | ||
Количество вентиляторов, шт. | |||
Мощность одного вентилятора, кВт. | |||
Расчетное давление, МПа | 8,30 | 7,7 | |
Масса, т. | 41,00 | 76,24 | |
Размеры в плане, м. | 12,15×9,35 | 11,61×10,40 | |
При анализе технических характеристик указанных АВО выявлены преимущества аппарата АВГБС-83Р как по техническим показателям, так и по компактности размещения аппаратов на площадке ДКС.
Расчет количества АВО выполнен при расчетной средней температуре воздуха теплого периода года обеспеченностью 0,95- 18,8С. Согласно ОНТП 51−1-85 «Общесоюзные нормы технологического проектирования. Магистральные трубопроводы» поправка на изменчивость климатических условий принята равной +2С. Расчетная температура газа после АВО принята равной +25С.
Повышение температуры газа после компримирования принималось в зависимости от степени повышения давления.
5.5.4 Установка подготовки топливного и импульсного газа
Основные технические характеристики технологического оборудования установки подготовки топливного и импульсного газа приведены в таблице 5.7.
Количество оборудования рассчитано на восемь рабочих ГПА.
Таблица 5.7 Основные технические характеристики технологического оборудования УПТИГ
Обозначение | Наименование | Количество | Характеристика оборудования | Обозначение чертежа | |
БОГ | Блок очистки газа | Q=48 930н.м?/час Pрасч.=7,8 МПа | По типу ГПР1225.01 ЦКБН | ||
БЗГ | Блок замера газа | Q=48 930н.м?/час Pрасч.=7,8 МПа | По типу ГПР1225.03−05 ЦКБН | ||
БОИХГ | Блок осушки и хранения импульсного газа | Q=5000н.м?/час Pрасч.=7,8 МПа | По типу ГПР1225.07 ЦКБН | ||
БРТГ | Блок редуцирования топливного газа | Q=48 930н.м?/час Pрасч.=10,0 МПа | По типу ГПР1225.03−04 ЦКБН | ||
БПТГ1, БПТГ3 | Блок подогревателя газа | Q=22 834нм?/час P расч.= 7,8МПа | По типу ГПР1225.06 ЦКБН | ||
Е1 | Емкость дренажная | V=3м? Ррасч.= 0,07МПа | АО" Курганхиммаш" | ||
Е2 | Емкость | V=8 м? Ррасч.= 0,07МПа | |||
5.5.5 Маслохозяйство
Масляное хозяйство предназначено для приема, хранения и подачи масла к газоперекачивающим агрегатам ГПА-Ц-16С с маслеными уплотнениями. Проектом предусматривается использование двух сортов масла: Мс-8П для смазки узлов двигателя и Тп-22с для смазки узлов компрессора. Потребность в смазочных материалах на эксплуатацию газоперекачивающих агрегатов определена по паспортным данным и приведена в таблице 4.4.12
Таблица 5.8 Годовой расход масла
Сорт масла | Количество рабочих агрегатов, шт. | Годовой расход масла на замену, м3 (т.) | Годовой расход масла на безвозвратные потери | Годовой расход масла, м3 (т.) | |
Мс-8П | 70,722 (61,952) | 42,00(36,792) | 112,722 (98,744) | ||
Тп-22с | 161,067(141,095) | 21,00 (18,396) | 182,067(159,491) | ||
В состав масляного хозяйства входят следующие сооружения:
— насосная масел со складом масел в таре;
— склад масел;
— дренажная емкость.
Для каждого сорта масла проектом предусмотрено по 3 резервуара объемом 25 м³ каждый предназначенные для хранения резервного запаса. Для слива отработанного каждого сорта масла для последующей очистки и хранения чистого предусмотрено по две емкости по 25 м³. Общее количество резервуаров на складе масла — 10 единиц. Все резервуары надземного расположения обогреваются и теплоизолированы.
6 Организационно — экономическая часть
В организационно — экономической части рассмотрим сравнение четырех схем сбора газа с кустов:
1) по семи коллекторам;
2) по трем коллекторам;
3) по шлейфам;
4) по двум коллекторам.
Эти варианты отличаются металлоемкостью и протяженностью, что приводит к изменению не только капитальных, но и текущих затрат.
Обоснование выбора экономически целесообразного варианта сбора газа предполагает определение критериев оптимальности. Согласно методике Мирового банка реконструкции и развития в качестве таких критериев используются:
— максимум накопленного потока денежной наличности и чистой текущей стоимости;
— минимальный срок окупаемости проекта;
— максимальный коэффициент отдачи капитала;
— максимальная внутренняя норма рентабельности проекта.
Расчет по системе выше перечисленных показателей производится по каждому варианту разработки месторождения по ниже приведенной методике:
ПДНt = Bt — Иt — Kt — Ht, (6.1)
где ПДНt — поток денежной наличности полученный в t-ом году, млн. р,
Bt — выручка от реализации продукции в t-ом году, млн. р,
Иt — текущие затраты в t-ом году, млн. р,
Kt — капитальные затраты в t-ом году, млн. р,
Ht — налоги, выплачиваемые в t-ом году, млн.р.
При расчете выручки по формуле (6.1) целесообразно использовать цены предприятия на газ без учета акцизного налога и налога на добавленную стоимость
N
Bt = ?Qit · Цit ,
i=1 (6.2)
где n — количество производимых углеводородных продуктов,
Qit — объём реализации i-го углеводородного продукта в t —ом году, млн. м3,
Цit — цена предприятия на i-ый продукт в t-ом году, р/тыс. м3.
Текущие затраты (Иt) представляют собой затраты на добычу газа без амортизационных отчислений. Текущие затраты рассчитываются на основе разработки предыдущих месторождений. В текущие затраты включены издержки производства, плата за недра, различные отчисления.
Капитальные затраты (Kt) представляют собой единовременные затраты на создание скважин, объектов промыслового строительства и оборудования, не входящего в сметы строек. Расчет капитальных затрат производится на основе соответствующих нормативов капитальных затрат.
Таблица 6.1 Затраты по вариантам за весь период разработки
Виды затрат | 1 вариант | 2 вариант | 3 вариант | 4 вариант | |
Капитальные затраты, млн.р. | 1101,77 | 1243,74 | 1162,31 | 1482,53 | |
Текущие затраты, млн.р. | 3324,2 | 3477,92 | 3387,26 | ||
Расчёт налогов (Ht) в формуле (6.1) предполагает определение размера налогов, относимых на финансовый результат, и налога на прибыль.
Нt=Нимt+Нпрt (6.3)
где Ним — налог на имущество;
Нпр — налог на прибыль.
Нимt = (? Kt —? Aмt) • 0,02, (6.4)
где Амt — амортизационные отчисления в t-ом году.
Нпрt = (Bt — Иt — АмtНимt) • 0,24, (6.5)
После расчета годовых потоков денежной наличности (ПДНt) рассчитывается накопленный поток (НПДНt):
T
НПДНt =? ПДНk,
k=1 (6.6)
где k — количество лет разработки месторождения до t — го года включительно;
t Т, Т — период разработки месторождения.
Накопленный поток денежной наличности за весь период разработки (НПДНt) показывает сколько наличных средств накопится на расчетном счёте предприятия от реализации выбранного варианта.
Поскольку результаты и затраты осуществляются в различные периоды времени, то возникает необходимость в их приведении к одному году (tp), например, предшествующему началу разработки месторождения. Эту процедуру можно осуществить при помощи коэффициента дисконтирования по формуле:
?t = (1 + Енп) tp-t (6.7)
где ?t — коэффициент дисконтирования для t — го года,
Eнп — нормативный коэффициент приведения.
Дисконтированный годовой поток денежной наличности (ДПДНt) можно определить по формуле:
ДПДНt = ПДНt • t (6.8)
Накопленный дисконтированный поток денежной наличности представляет собой чистую текущую стоимость:
t
ЧТСt=? ДПДНk,
k=1 (6.9)
где k — годы разработки до t-го года включительно,
t Т, t — текущий год разработки, Т — период разработки месторождения.
Чистая текущая стоимость проекта за весь период разработки месторождения (ЧТСт) является важнейшим критерием выбора оптимального варианта разработки месторождения.
Варианты рассчитывались в Excel. Результаты расчета НПДНt и ЧТСt для первого варианта представлены в таблице 6.2. и на рисунке 6.1.
Рис. 6.1 Профили НПДН и ЧТС По графику динамики НПДН и ЧТС можно определить срок окупаемости капитальных вложений (Ток). Это точка пересечения НПДН и ЧТС с осью абсцисс. Срок окупаемости может быть также определён расчётным путём:
/НПДН0/
Ток = Т0 + —————;
НПДН1 + /НПДН0/ (6.10)
где Т0 — количество полных лет, в течение которых наблюдается отрицательный НПДН, НПДН0 — последнее отрицательное значение накопленного потока, тыс. р.
НПДН1 — первое положительное значение потока, тыс.р.
Для оценки эффективности капитальных вложений необходимо кроме срока окупаемости рассчитать коэффициент отдачи капитала (КОК):
ЧТСt
КОК = ——— + 1 ,
ЧТСинв (6.11)
где ЧТС инв — дисконтированные инвестиции, млн.руб.
Т ЧТСинв =? (Kt · ?t)
t=1 (6.12)
где Kt — капитальные вложения в t-ом году, млн. руб.
Коэффициент отдачи капитала показывает, сколько рублей дохода даёт один рубль инвестиций, вложенных в данный проект за весь период разработки с учётом дисконтирования результатов и затрат.
Внутренняя норма рентабельности проекта (е) определяется из условия равенства чистой текущей стоимости нулю:
T
? [ПДНt · (1+е)tp-t] = 0,
t=1 (6.13)
Варианты расчетов ранжируются по внутренней норме рентабельности.
После расчёта выше приведённых показателей по всем вариантам разработки выбирается лучший вариант на основе критериев оптимальности:
НПДНt => max;
ЧТСt => max ;
Ток => min ;
??? => max;
? => max.
Сравнение вариантов представлено в таблице 6.3
Таблица 6.3. Сравнение схем сбора газа
Показатель | 1 вариант | 2 вариант | 3 вариант | 4 вариант | |
НПДН | 3070,089 | 2833,683 | 2976,884 | 2399,091 | |
ЧТС | 398,9731 | 262,6583 | 342,6609 | 19,4052 | |
Срок окупаемости, Ток | 8,614 181 | 9,45 | 8,96 | 11,2 | |
Коэффициент отдачи капитала, КОК | 0,4566 | 0,267 894 | 0,372 751 | 0,16 731 | |
Внутренняя норма рентабельности, e | 15,5 | 13,35 | 14,58 | 10,2 | |
Поскольку проекты в нефтегазодобывающем производстве имеют определённую степень риска, связанную с природными факторами и рыночными (риск изменения цен), то необходимо провести анализ чувствительности каждого варианта проекта. Для этого выбирается интервал наиболее вероятного диапазона изменения каждого фактора:
— годовая добыча [-30%;+10%];
— цены на газ [-20%;+20%];
— текущие затраты [-10%; +10%];
— капитальные затраты [-5%; +15%];
— налоги [-20%; +20%]
Для каждого фактора определяется зависимость: ЧТС (Q); ЧТС (Ц); ЧТС (И); ЧТС (К); ЧТС (Н).
Полученные зависимости чистой текущей стоимости от факторов показаны на рисунке 6.2.
Рис. 6.2 Диаграмма «паук»
Из расчетов видно, что проект имеет риск при значительном объема добычи газа. Вариант прокладки газосборных сетей с двумя коллекторами является самым выгодным с экономической точки зрения. Немногим уступает вариант с тремя коллекторами.
7. Безопасность и экологичность
7.1 Обеспечение безопасности работающих
Основные опасности и вредности при эксплуатации нефтяных и газовых месторождений.
МЕТАН — газ, являющийся составной частью добываемого природного газа. Метан не имеет ощутимого запаха, но при содержании его воздухе около 10% человек испытывает недостаток кислорода, при большем содержании может наступить удушье, предельно допустимая концентрация составляет 300 мг/м3.
ПАРЫ углеводородов поступают в организм человека главным образом через дыхательные пути. При легких отравлениях в начале наблюдается период возбуждения, характеризующийся сонливостью, беспричинной веселостью, затем появляется головная боль, головокружение, усиленное сердцебиение, тошнота.
При тяжелых отравлениях парами углеводородов наступает потеря сознания, судороги, ослабление дыхания.
ПДК — 300 мг/м3. Некоторые пары углеводородов и нефтяные газы, так же как и сероводород, тяжелее воздуха, вследствие чего они смолятся и скапливаются в плохо вентилируемых углублениях, внутри аппаратов и помещений. При отравлении парами углеводородов пострадавшего нужно немедленно вывести на свежий воздух, освободить тело от стесняющей одежды, согреть тело. При отсутствии дыхания немедленно сделать искусственное дыхание.
МЕТАНОЛ (МЕТИЛОВЫЙ СПИРТ) — сильный яд, действующий на нервную и сосудистую систему, слизистую оболочку дыхательных путей.
Из-за его схожих свойств с этиловым спиртом часто происходят тяжелые отравления. Небольшое количество метанола (до 10−15 г) приводят к тяжелым отравлениям, ведущим к слепоте и даже к смерти. Отравление происходит не только при попадании жидкости внутрь, но и при вдыхании паров и проникновения их через кожу тела.
ПДК метанола в воздухе рабочих помещений — не более 5 мг/м3. Метанол медленно накапливается в организме и еще медленнее выводится. Хроническое отравление наступает медленно при выдыхании паров и сопровождается раздражением слизистых оболочек, головными болями, шумом в ушах, общим стрессом, расстройством зрения, вплоть до слепоты.
При острых отравлениях метанолом следует произвести промывание желудка в течение двух часов 5%-м раствором питьевой соды. В качестве противоядия можно применять этиловый спирт введением его внутривенно или приемом внутрь.
Технические требования к оборудованию и рабочему инструменту, гарантирующему безопасность.
Предусмотрена герметизация технологического оборудования и трубопроводов.
Применённая арматура, материалы труб и деталей трубопроводов соответствуют климатическим условиям и условиям эксплуатации.
Запорная арматура для газа, метанола, конденсата газа принята по классу герметичности затвора А, В по ГОСТ 9544–93. Основная запорная арматура имеет местное и дистанционное управление, обеспечивающее быстрое отключение оборудования и трубопроводов.
Соединения труб предусмотрено выполнить сваркой.
Предусмотрен 100% контроль качества физическими методами сварных соединений трубопроводов категории I и трубопроводов с рабочим давлением выше 10 МПа.
Сжигание газа при подготовке технологического оборудования к ремонтам, продувке коллекторов и сбросов в аварийных ситуациях предусмотрено в существующую факельную систему УКПГ сеноманского промысла.
Вытеснение воздуха из оборудования и трубопроводов после ремонта и снижение давления до атмосферного перед ремонтом предусмотрено через свечи рассеивания, выступающие на 3 м выше крыш зданий.
Аварийный слив жидких продуктов из оборудования и трубопроводов при аварии и перед ремонтом предусмотрен в установленную около площадки буферных ёмкостей подземную дренажную ёмкость с электронасосным агрегатом во взрывозащищенном исполнении. Ёмкость оборудована свечой рассеивания с огнепреградителем.
Для защиты от превышения рабочего давления на трубопроводах входа газа установлены предохранительные клапаны.
Предусмотрено заземление электрооборудования, молниезащита, защита от статического электричества и заноса высокого потенциала.
Все электрооборудование взрывоопасных цехов и сооружений принято во взрывозащищенном исполнении.
Проектом предусматривается обеспечение работающего персонала средствами индивидуальной защиты. Все средства индивидуальной защиты разделяются на виды в зависимости от того, какие органы они предохраняют, — средства защиты человека, органов дыхания, зрения, органов слуха, кожный покров.
Защита тела человека осуществляется спецодеждой, спецобувью, рукавицами, касками, подшлемниками, перчатками, изолирующими подставками, резиновыми ковриками и дорожками, щитками, диэлектрическими перчатками, галошами и ботами, предохранительными поясами, указателями напряжения тока, шлемами, масками и др. Спецобувь — кирзовые ботинки с медными гвоздями, спецодежда — костюм хлопчатобумажный.
Защита органов зрения осуществляется при помощи различных предохранительных очков. Обычно применяются очки одного из следующих типов:
а) для защиты глаз от механического повреждения отлетающими осколками, стружками и другими отходами, которые могут попасть в глаз прямо или сбоку;
б) для защиты глаз от пыли, брызг и капель кислоты, щелочи, вредных паров и газов;
в) для защиты глаз от пыли и ветра;
г) для защиты глаз от вредного воздействия лучистой энергии ультрафиолетовых, инфракрасных лучей или яркого света.
Защита органов дыхания обеспечивается применением различного рода респираторов и противогазов.
Санитарные требования.
Газотурбинная электростанция, газоперекачивающие агрегаты, АВО газа создающие повышенный уровень шума достигающий 85−92дб. располагаются на удалении от зданий с постоянным пребыванием людей. Кроме того, предусматриваются дополнительные мероприятия по снижению шума и вибраций путём устройства шумопоглощающих перегородок, вентиляторы венткамер устанавливаются на виброопоры.
Конструкции индивидуальных зданий рассчитаны с учётом коэффициентов соответствующих классу ответственности здания.
В случае взрыва газовоздушной смеси во взрывоопасных помещениях для снижения воздействия ударной волны на несущие конструкции, участки наружных стен предусмотрены легкосбрасываемыми за счёт малой собственной массы (не более 25 кг/м2) и специальных крепёжных элементов.
Для исключения растекания опасных жидкостей в помещениях с ЛГЖ предусматриваются бортики вдоль стен и отверстий, а также пандусы у входов.
Площадки ёмкостей с опасными жидкостями обетонированы и имеют бортики.
Межцеховые коммуникации для удобства наблюдения и ремонта располагаются на надземных эстакадах.
Наиболее благоприятные условия труда на ремонтных участках опорной базы промысла создаются на основе правильного использования технологических средств, мероприятий по предупреждению вредных выделений, соблюдения норм планировки и разрывов между оборудованием и строительными конструкциями, обеспечения взрыво — и пожаробезопасности.
Для создания нормальных санитарно-гигиенических условий проектом предусмотрены следующие мероприятия:
— поддержание нормальной температуры, влажности и чистоты;
— устройство местных отсосов от оборудования с вредными выделениями, обеспечение помещений приточно-вытяжной вентиляцией.
Безопасность при выполнении работ обеспечивается:
— устройством ограждений всех выступающих подвижных частей станков и механизмов;
— проведением профилактического осмотра технического состояния оборудования;
— надежной изоляцией токоведущих частей, защитным заземлением и занулением;
— освещением рабочих мест в соответствии с нормами;
— применением специальных щитков и масок при электросварке и очков при газорезке.
Противопожарные требования и средства пожаротушения.
При проектировании зданий и сооружений учитываются требования СНиП 2.01.02−85* «Противопожарные нормы», СНиП 21−01−97 разд. 6,7,8 «Пожарная безопасность зданий и сооружений», СНиП 2.09.02−85* «Производственные здания», СНиП 2.09.04−87* «Административные и бытовые здания». Количество эвакуационных выходов, огнестойкость конструкций на путях эвакуации приняты согласно разд. 4 СНиП 2.01.02−85* и разд. 6 СНиП 21−01−97.Противопожарные преграды (стены, перегородки, перекрытия) и их огнестойкость приняты согласно разд. 3 СНиП 2.01.02−85*, пункта 2.10 СНиП 2.09.02−85*, пункта 1.25 СНиП 2.09.04−87*.
Все взрывоопасные помещения отделяются от других помещений противопожарными, газонепроницаемыми стенами и перегородками. В местах проёмов этих преград устраиваются несгораемые тамбур-шлюзы. В качестве легкосбрасываемых конструкций используется остекление окон. При недостаточной площади остекления в качестве легкосбрасываемых конструкций используются участки стен из лёгких металлических панелей, с соответствующим закреплением их к ветровым ригелям на расчётную нагрузку до 70кг/м2.
Металлические колонны и балки перекрытий встроек, лестничные косоуры и балки из металла, а также элементы каркаса СЭБ оштукатуриваются цементно-песчаным раствором по сетке.
Кабельные проводки с открытым расположением кабелей предусмотрены на высоте 2.5м. от земли. Спуски и вводы в здания ниже этой отметки закрываются защитными кожухами.
Лестницы для выхода на кровли при высоте здания более 10 м. и в местах перепада высот, а также ограждение у свеса кровли предусматриваются в соответствии с требованиями п.п.2.9−2.12 СНиП 2.01.02−85* и п. 2.60 СНиП 2.09.02−85*.
Пожаротушение объектов УКПГК предусматривается двумя системами: автоматической пенной и водяной от противопожарного водопровода.
Защита от пожара и загазованности воздушной среды выполнена на приборах и оборудовании, перечисленных ниже.
1. Ультрафиолетовые инфракрасные пожарные извещатели FL3112.
2. Стационарные сигнализаторы горючих газов СТМ-30.
3. Контроллеры ЭК 2000.
При обнаружении пламени любыми двумя детекторами или нажатии кнопки станции ручного оповещения, контроллер пожаротушения выдает команду на включение звуковой и световой сигнализации по месту и в операторной и на открытие электрозадвижки подачи пены в защищаемую зону пожаротушения, см. таблицу 15. Через 10 минут после начала пенной атаки электрозадвижка закрывается.
Мероприятия по безопасности при выполнении газоопасных работ.
Все ремонтные работы во взрывопожароопасных помещениях должны производиться инструментами, изготовленными из металлов, не дающих при ударах искр. Запрещается применение стальных и неисправных инструментов. Без инструментов, отвечающих требованиям безопасного производства работ, приступать к работе запрещается.
Ремонт оборудования должен проводиться только после его отключения, сброса давления, остановки движущихся частей и принятия мер, предотвращающих случайное приведение их в движение под действием силы тяжести или других факторов. На пусковом устройстве необходимо вывесить плакат с надписью: «Не включать. Работают люди» .
На всех подводящих и отводящих трубопроводах к ремонтируемому оборудованию необходимо установить заглушки с хвостовиками, выступающими за пределы фланцев. Заглушки, устанавливаемые на трубопроводах, должны быть рассчитаны на максимально возможное давление газа в трубопроводах. Не допускается применять заглушки из стали более низкого качества, чем трубопроводы. Места установки заглушек фиксируются в специальном журнале.
На закрытой запорной арматуре необходимо вывесить плакаты с надписью: «Не открывать, оборудование в ремонте» .
Перед вскрытием оборудование должно быть освобождено от продуктов, продуто инертным газом или пропарено. Пропарку оборудования следует вести при одном открытом люке или воздушнике.
Оборудование после пропарки должно быть промыто водой. После охлаждения (температура поверхностей должна быть не выше 30 °С) из него выпускается вода, после чего осторожно открывается верхний люк.
После пропарки и промывки оборудование должно быть оставлено с открытыми люками для естественной вентиляции.
Содержание опасных веществ после продувки воздухом не должно превышать ПДК, а объёмное содержание кислорода должно быть не менее 20%.
Насосы, подлежащие разборке, должны быть отсоединены от электродвигателей, опорожнены и продуты на свечу. Электродвигатели насосов должны быть обесточены в распредустройстве в двух местах отключением рубильника и снятием плавкой вставки предохранителя.
Все детали, предназначенные для замены неисправных, перед ремонтными работами должны быть осмотрены. Поверхности труб, деталей трубопроводов, фланцев, прокладок, корпусов и крышек арматуры не должны иметь трещин, раковин, плен. заусенцев и других дефектов.
После выполнения подготовительных мероприятий составляется акт о подготовке оборудования к ремонту. В акте указывается дата его составления, вид ремонта, ставится подпись составителя акта.
При проведении ремонтных работ рабочие должны носить каски, а на рабочих местах должны быть вывешены плакаты с предупредительными знаками и плакаты по безопасному ведению работ. Работа на высоте при отсутствии ограждений должна выполняться с применением предохранительных поясов.
При выполнении ремонтных работ не допускается загромождение проходов и проездов, а также окружающей территории различным оборудованием, материалами и строительными отходами.
Ремонты, связанные с огневыми работами, следует проводить с соблюдением требований «Правил пожарной безопасности для предприятий и организаций газовой промышленности» ВППБ 01−04−98 и «Типовой инструкцией по организации безопасного проведения огневых работ на взрывоопасных и взрывопожароопасных объектах» .
При нарушении технологического режима, возникновении загазованности, пожара, аварии, появления опасности для работающих, ответственное лицо обязано немедленно прекратить работу и удалить людей из опасной зоны.
Работы могут быть возобновлены только в случае ликвидации аварийной ситуации, если при анализе пробы воздуха концентрация газа не превысит допустимых санитарных норм.
Во время проведения ремонтов оборудования, установленного во взрывопожароопасных помещениях, системы приточно-вытяжной вентиляции в этих помещениях должны работать.
Ремонтные работы в ночное время производятся только с письменного разрешения технического руководителя предприятия при условии обеспечения дополнительных мер безопасности (усиление освещения, дополнительный надзор, непрерывный контроль загазованности).
По окончании ремонтных работ должен быть проведён контроль сварных соединений, проведено испытание оборудования и трубопроводов на прочность и плотность в соответствии с проектной документацией и с требованиями СНиП 3.05.05−84 «Технологическое оборудование и технологические трубопроводы». «Правил устройства и безопасной эксплуатации сосудов, работающих под давлением» и «Правил устройства и безопасной эксплуатации технологических трубопроводов» .
Арматура после ремонта подлежит испытанию на прочность и плотность на стенде, причём испытание на прочность следует производить при открытом запорном устройстве.
Результаты ремонта и испытания арматуры оформляют актами. Акты должны храниться вместе с паспортами на арматуру.
7.2 Экологичность проекта
Влияние проектируемых работ на окружающую среду.
Практически все проектируемые на месторождении объекты (УКПГ, ДКС, кусты газовых скважин, газосборные сети, газопровод внешнего транспорта, ВЛ-6 кВ, ЗРУ-6кВ, автодороги) будут оказывать в той или иной степени воздействие на окружающую среду.
Воздействие на атмосферный воздух при строительстве и эксплуатации объектов на Вынгаяхинском месторождении будет происходить в результате выбросов:
газоообразных, аэрозольных и взвешенных веществ от технологического оборудования, а также от ГФУ при освоении скважин;
продуктов сгорания топлива от дымовых труб котельных;
выхлопных газов автомобильного транспорта.
Основными источниками выбросов будут УКПГ, ДКС и газовые скважины.
Источниками организованных выбросов являются дымовые трубы, вентиляционные шахты, дыхательные клапаны и т. п. К неорганизованным выбросам относятся выделения вредных веществ через неплотности в арматуре и во фланцевых соединениях. Источниками залповых выбросов служат продувочные свечи от технологических аппаратов, кустов скважин и газосборных сетей, дыхательные клапаны емкостей («большое дыхание»).
Анализ данных по разрабатываемым газовых месторождениям показывает, что основной объем (99%) выбросов от стационарных источников составляют оксиды углерода и азота, метан и другие углеводороды. Наиболее неблагоприятными являются указанные диоксиды и метан, относящиеся ко 2−4 классам опасности. Остальные загрязняющие вещества не оказывают существенного влияния на атмосферный воздух.
УКПГ будет введена в действие в 2003 г. Проектная производительность ее (5 млрд. м3 газа в год) будет обеспечена в третий год эксплуатации. Первая, вторая, третья и четвертая ступени ДКС с агрегатами ГТН-6 (или ГПА-6,3) вводятся соответственно в 2005, 2011 и 2016 и 2021 гг.
Количества выбросов УКПГ Вынгаяхинского месторождения определены по аналогии с УКПГ Губкинского месторождения с учетом соотношения их производительностей (соответственно 5 и 13 млрд. м3 газа в год) и того, что на Вынгаяхинском месторождении в качестве теплоносителя будет использован антифриз, а не вода. Эти количества составляют (т/год): оксидов азота 4,2, окиси углерода 8,7 и метана 83,8 (в том числе залповые выбросы — 24,9).
Оценка валовых выбросов ДКС произведена согласно регламенту. Эти выбросы приведены, в таблице 7.1.
Таблица 7.1 Количество выбросов вредных веществ от ДКС
Годы | Число рабочих агрегатов | Количество выбросов, т/год | ||||
двуокиси азота | окиси азота | окиси углерода | Метана | |||
2003;2008 | 4,3 | 82,5 | 168,7 | 83,3 | ||
2009;2013 | 8,7 | 165,1 | 337,4 | |||
2014;2018 | 247,6 | 506,1 | 132,6 | |||
2019;2028 | 17,4 | 330,1 | 674,8 | 157,3 | ||
Расчет выбросов вредных веществ, образующихся при сжигании газа на ГФУ в процессе освоения эксплуатационных скважин (после бурения и капитальных ремонтов) и разведочных скважин (после реконструкции в наблюдательные за давлением в залежи), выполнен по формуле
Мi = УВi? G, (7.1)
где Мi — мощность выброса i — го вещества, г/с;
УВi — удельный выброс i — го вещества, г/г; он принимается равным 0,003 для оксидов азота в пересчете на NO2, 0,02 для окиси углерода и 0,0005 для метана и других углеводородов в пересчете на СН4;
В — расход газа, г/с.
При расчетах время технологического отжига скважины при ее освоении принято равным 48 ч. Результаты расчетов приведены в таблице 7.2.
Таблица 7.2 Расчет количества выбросов вредных веществ при освоении скважин
Указанные выше расчетные величины выбросов вредных веществ в атмосферу являются ориентировочными и должны быть уточнены в проекте обустройства месторождения.
Результаты расчетов и замеров по разрабатываемым месторождениям севера Тюменской области свидетельствуют, что максимальные содержания вредных веществ в воздухе на границах СЗЗ (расстояние от промыслов до этих границ принималось, согласно СН, равным 1000 м) меньше ПДК. Согласно СанПиН для предприятий по добыче газа расстояние до границы СЗЗ должно быть не менее 2000 м. Кроме того, производительность УКПГ, проектируемой на Вынгаяхинском месторождении, намного меньше. Следовательно, содержание вредных веществ на границе СЗЗ этой УКПГ будет еще меньше.
Основными источниками шума на промысле являются газоперекачивающие агрегаты и аппараты воздушного охлаждения газа, а также насосное оборудование, технологические трубопроводы и запорная арматура. Предельный уровень шума будет достигаться на расстояниях: 9 м — для рабочей зоны и 281 м — для жилых застроек, что намного меньше, чем нормативное расстояние до границы СЗЗ.
На газовых месторождениях севера Тюменской области источниками воздействия на поверхностные водоемы, водотоки и подземные водоносные горизонты являются площадные и линейные объекты основного и вспомогательного технологических процессов, а также объекты сопутствующей инфраструктуры: УКПГ, ДКС, кусты скважин, трубопроводы, автодороги, мосты, водозаборы и др.
Источники воздействия и их количество существенно меняются в зависимости от стадии обустройства месторождения. На этапе строительства основными источниками воздействия являются трассы автодорог, трубопроводов и других коммуникаций. На этапе ввода месторождения в эксплуатацию к ним добавляются УКПГ, ДКС, кусты скважин и другие объекты.
К основным источникам и видам воздействия на водные объекты относятся:
неочищенные или недоочищенные хоз-бытовые и промышленные стоки и отходы;
попадание в водотоки целлюлозы из захороненных на трассах древесных остатков;
засорение и заиление русел рек и ручьев при строительстве;
нарушение нерестилищ при подводных и дноуглубительных работах, при строительстве подводных переходов трубопроводов;
нарушение гидрологии малых рек, водоемов из-за устройства временных проездов, непроектной прокладки трубопроводов;
нарушение водного и теплового режима болот;
изъятие водных ресурсов
При бурении скважин может произойти загрязнение природных вод:
буровыми и тампонажными растворами;
материалами для приготовления буровых и тампонажных растворов;
буровыми сточными водами и выбуренным шламом;
горюче-смазочными материалами (ГСМ);
хозяйственно-бытовыми сточными водами и твердыми бытовыми отходами;
загрязненными талыми и ливневыми сточными водами.
Возможные причины загрязнения:
отсутствие надежной гидроизоляции дна стенок шламовых амбаров, технологических площадок буровой, котельной и склада ГСМ;
неорганизованный сбор сточных вод и сброс их в водоемы или на рельеф местности;
разгерметизация систем циркуляции промывочных и других жидкостей, емкостей с ГСМ, порывы трубопроводов;
нарушение технологических требований в процессе погрузки, транспортировки, разгрузки и хранения материалов, используемых для приготовления буровых и цементных растворов;
аварийные ситуации в процессе бурения, связанные с выбросом флюидов;
проникновение буровых растворов в водоносные пласты вследствие несоблюдения технологических требований к проходке этих пластов;
перетоки пластовых флюидов в случае некачественного цементирования и негерметичности обсадных колонн.
Загрязнение природных вод может происходить также при проведении ремонтных работ на скважинах.
Растворенные вещества из поверхностных и грунтовых вод попадают в верхние надмерзлотные и межмерзлотные, водоносные горизонты.
Мероприятия по защите окружающей среды.
Для уменьшения выбросов загрязняющих веществ в атмосферу предусмотрены следующие мероприятия:
полная герметизация всего оборудования, арматуры и трубопроводов, исключающая постоянные выбросы;
выбор оборудования с учетом взрывоопасности, пожароопасности и токсичности продуктов;
выполнение сваркой всех соединений, за исключением фланцевых;
направление всех сбросов с предохранительных клапанов оборудования в факельную систему;
применение «дыхательных клапанов», позволяющих ограничить испарение в атмосферу токсичных и легковоспламеняющихся жидкостей, хранящихся в резервуарах при атмосферном давлении;
покрытие таких резервуаров светлой краской с целью уменьшения испарения жидкостей;
применение для исследования скважин устройства «Надым-2М»; исключающего выбросы в атмосферу.
Основными источниками шума в бескомпрессорный период являются открытые участки трубопроводов и запорная арматура. С целью снижения воздействия шума предусматривается:
звукоизоляция труб на указанных участках,
установка акустических кожухов на регулирующую аппаратуру,
использование акустических перегородок для защиты ремонтного персонала,
использование наушников и противошумовых касок.
Главными источниками шума на ДКС являются всасывающее выхлопное устройство газовой турбины, компрессорный агрегат и его обвязка.
Основным мероприятием по снижению шума выхлопа газоперекачивающего агрегата является установка шумоглушителя — утилизатора тепла выхлопа агрегатов.
Для снижения шума, распространяющегося через стенки дымовой шахты на окружающую территорию, ее наружная поверхность облицовывается звукои теплоизолирующим покрытием.
На краны технологической обвязки трубопроводов устанавливаются металлические кожухи со съемной крышкой.
Технологические трубопроводы покрываются слоем теплоизоляции толщиной от 30 до 80 мм.
Для повышения звукоизоляции стены контейнера турбоагрегата рекомендуется применение вибропоглощающей мастики, а для повышения декремента затухания — звукоизолирующих конструкций контейнера.
Сооружение объектов следует начинать лишь после создания локальных или временных устройств водоподготовки и обезвреживания бытовых и строительных отходов.
Для предотвращения нарушения поверхностного стока при производстве земляных работ, строительстве трубопроводов и дорог должны сооружаться водопропускные устройства, проводиться противоэрозионные мероприятия.
При пересечении трубопроводами водных преград следует предусматривать трубы с утолщенной стенкой и усиленной изоляцией, берегоукрепительные и противоэрозионные работы. После монтажа трубы опрессовывают воздухом.
Сточные воды так же, как и другие отходы буровых, должны захороняться в соответствии с регламентом /13/.
Для защиты поверхностных и пресных подземных вод от загрязнения сточными водами, промышленными и бытовыми отходами предусматривается:
твердое покрытие, обваловка и ограждение, а также система канализации для сбора и обезвреживания дождевых и талых вод или проливов ГСМ и химреагентов на промплощадках;
контроль за количеством и составом сточных вод;
сбор, утилизация или обезвреживание промышленных и бытовых отходов;
твердое покрытие площадок и гидроизоляция емкостей для хранения и ликвидации отходов;
использование разработанной СеверНИПИгазом и АКХ технологии утилизации твердых отходов вместе с осадками КОС, заключающейся в сжигании их с дожигом отходящих газов и очисткой дыма; образующаяся при этом зола используется при рекультивации нарушенных земель и для подсыпки дорог.
Для сокращения площади нарушаемых земель предусмотрены:
кустовая схема разбуривания месторождения;
бурение наклонно-направленных газоконденсатных скважин и нефтяных скважин с горизонтальным окончанием ствола;
опережающая прокладка только методом «от себя» подъездных автодорог ко всем строительным площадкам, с максимальным сохранением мохово-растительного слоя;
утилизация твердых бытовых отходов и древесины.
ограничение срезки грунта участком будущей траншеи при планировке трасс линейных сооружений;
движение транспортной и строительной техники в теплое время года только по постоянным дорогам;
противоэрозионные мероприятия, включающие устройство водопонижающих террас, водозадерживающих валов и водопереливных валиков.
Защите от загрязнения почв и растительности служат указанные выше воздухои водоохранных мероприятия.
При строительных работах необходимо производить снятие и складирование верхнего (гумусового) слоя почвы для последующего его использования при рекультивации.
Для сохранения земельного массива от развивающихся геологических процессов (ветровая эрозия, термоэрозия) должно быть предусмотрено проведение внепланового «залечивания» повреждений окружающей среды и предупреждение дальнейшей деградации земель.
Чрезвычайные ситуации.
Природный газ и метанол по целому ряду критериев (взрывопожароопасность, токсичность, воздействие на людей и окружающую среду) относятся к опасным веществам.
Наиболее высокая вероятность аварий для скважин существует в период бурения. В долевом соотношении вероятность аварий скважин для бурения, эксплуатации и капитального ремонта составляет соответственно 0,58: 0,18: 0,24.
На внутрипромысловых трубопроводах наиболее опасными участками, с точки зрения последствий аварий, являются переходы через автомобильные дороги и действующие газопроводы. Частота видов разрушений для внутрипромысловых и магистральных газопроводов распределяется следующим образом:
20% - разрушение на полное сечение;
80% - выбросы в течение часа через отверстие диаметром 25,4 мм.
Вероятность возможного пожара при выбросе составляет 50%.
Наиболее опасная ситуация может возникнуть на УКПГ в результате аварии в цехе осушки газа (разрыв адсорбера и газопроводов его обвязки), при этом в окружающее пространство выбросится большое количество природного газа, находящегося в рабочих условиях под высоким давлением. Однако вероятность такой аварии, с учетом принимаемых по ее предотвращению мер, очень мала.
При авариях происходит загрязнение воздуха природным газом и продуктами его сгорания, оказывается также термическое воздействие. Однако последствия аварий носят, как правило, локальный характер.
Избыточное давление в зоне детонационной волны ?? ф1= 900 (кПа). Радиус зоны детонационной волны ®, м определяется по уравнению:
R1=18,53vQ, (7.2)
где Q — количество газа, пара в тоннах.
Так при взрыве газа массой 90 кг в абсорбере в цехе осушки газа, радиус зоны детонационной волны составит 8,29 м.
Давление во фронте ударной волны?? ф2 на расстоянии? до объекта, находящегося в зоне ударной волны определяют по таблице 7.3.
Таблица 7.3 Давление во фронте ударной волны
??ф1 | Значение ??ф1 на расстояниях от центра взрыва в долях от (? /R1) | ||||||||||||||
кПа | 1,05 | 1,1 | 1,2 | 1,4 | 1,6 | ||||||||||
1.8 | 4,5 | 2,7 | 1,8 | ||||||||||||
От места возможного взрыва до ближайших зданий расстояние 60 м.
Следовательно, давление во фронте ударной волны составит 13 кПа, что может привести к слабым разрушениям зданий.
Зона безопасного удаления при?? ф2=5кПа составляет Rбу=14*R1=116,2 м.
Радиус зоны смертельного поражения людей (Rспл) определяется по формуле:
Rспл=303vQ=13,44 м, (7.3)
Следовательно, в результате взрыва абсорбера:
— Ущерб третьим лица маловероятен.
— Зона полных, сильных и средних разрушений локализуется в пределах в корпусах подготовки газа. При крупных авариях возможно сильное повреждение оборудования — сепараторов, абсорберов. Возможно травмирование персонала, находящегося в момент аварии непосредственно в технологическом цехе.
— Соседние технологические объекты в зону умеренных повреждений не попадают.
— Таким образом аварии в цехе осушки газа не представляют непосредственной угрозы гибели для остального персонала на УКПГ, в местах постоянного его нахождения.
Вывод
В проекте разработки и обустройства Вынгаяхинского месторождения подробно рассмотрены все вопросы по структуре, организации и ведению экологического мониторинга на территории месторождения. Рассмотрены вопросы охраны труда работающих, пожарная безопасность, промышленная санитария. Предполагаемые работы при разработке месторождения должны отвечать всем стандартам безопасности и экологичности.
При рассмотрении аварийных ситуаций, сделаны выводы о том, что расположение технологических объектов, пожарная сигнализация и средства пожаротушения, позволяют максимально исключить гибель людей и сильное разрушение объектов промысла.
Заключение
Еты-Пуровское газоконденсатонефтяное месторождение расположено на территории Пуровского района Ямало-Ненецкого автономного округа Тюменской области, в 100 км южнее поселка Тарко-Сале и в 142 км северо-восточное г. Ноябрьска. В 50 м к западу от месторождения проходит трасса магистрального газопровода «Уренгой — Сургут — Челябинск» и железная дорога «Тюмень — Сургут — Новый Уренгой».
Гидрографически месторождение расположено в междуречье рек Айваседо-Пур. Еты-Пур. Вынга-Пур. относящихся к бассейну реки Пур. Для площади месторождения характерна сильная заболоченность территории, связанная с наличием мощного слоя вечномерзлых пород. Болота открытые, с торфяной подушкой, достигающей толщины 7 м.
Климат района резко-континентальный и характеризуется продолжительной холодной зимой и коротким жарким летом. Среднегодовая температура воздуха составляет + 7,5°С, самый холодный месяц — январь (морозы достигают до минус 50°С), самый теплый — июль (до плюс 30°С). Годовое количество осадков составляет 400−500мм. Снеговой покров устанавливается в конце октября и сходит в конце мая. Толщина снегового покрова — до 1,5−2м. Реки замерзают в конце сентября, вскрываются ото льда во второй половине мая. Толщина льда на реках и озерах изменяется от 40 до 90 см.
Для хозяйственно-питьевого водоснабжения пригодны пресные подземные воды палеоген-четвертичного возраста. В качестве возможного источника водоснабжения могут быть использованы надмерзлотные, межмерзлотные, подмерзлотные воды сквозных таликов.
В районе Еты-Пуровского месторождения первые сейсмические исследования были начаты в 1961 году. В период 1961;1964г, были проведены региональные сейсмические исследования. По результатам этих работ уточнено тектоническое строение платформенного чехла в данном районе. В 1964;1967гг. выявлены структуры: Пяку-Пуровская.
Северо-Пурпейская, Западно-Таркосалинская и Вынгапякутинская. оконтурен Айваседо-Пуровский вал и осложняющие его Айваседо-Пуровское и Еты-Пуровское локальные поднятия.
Поисковое бурение на нефть и газ на Еты-Пуровской площади началось в 1971 году.
Первой поисковой скважиной, пробуренной в 1971 году была открыта сеноианская газовая залежь. С 1973 года на месторождении начато поисковое бурение на нижнемеловые и юрские отложения, а в 1974 -1975гг. проведены региональные работы КМПВ в масштабе 1:200 000. В результате этих работ определена мощность осадочного чехла (4100м).
В 1978;1981гг. выполнены сейсморазведочные работы МОВ ОГТ масштаба 1:100 000. В 1990 г. проводились работы масштаба 1:50 000.
Непосредственно на Еты-Пуровском месторождении выявлено месторождение песка с запасами 4,3млн.м3. средней эффективной толщиной 5,15 м. Пески пригодны для отсыпки автодорог и кустовых площадок.
К настоящему времени на месторождении пробурено 28 поисковых и разведочных скважин.
Геологический разрез месторождения представлен терригенными песчано-глинистыми отложениями мезозойско-кайнозойского платформенного чехла. Максимальная вскрытая толщина осадочных пород составляет 3300 м (скв.175).
В тектоническом отношении Еты-Пуровское месторождение расположено в южной части Надым-Тазовской синеклизы, в пределах Верхнепурского вала. Вал входит в состав Варьеганско-Пурпейской зоны линейных структур. Верхнепурский вал представляет собой структуру субмеридионального простирания. Вал сформирован с севера на юг Западно-Таркосалннским и Аиваседопурским куполовидными поднятиями и Еты-Пурским малым валом. Последний осложнен Еты-Пурским и Южно-Еты-Пурским локальными поднятиями.
По верхнеюрскому опорному отражающему горизонту «Б» (кровля баженовской свиты) Еты-Пуровский вал представляет собой антиклинальную складку северо-западного простирания, оконтуренную изогипсой — 3080 м, имеющую размеры 82×25км, амплитуду около 300 м. По опорному отражающему горизонту «Г» (сеноман) это антиклинальная складка северо-западного простирания, оконтуренная изогипсой — 900 и осложненная по изогипсе — 760 м двумя куполами. Максимальная амплитуда вала около 250 м, размеры 78×17км.
Залежи углеводородов выявлены на обоих куполах и практически по всему разрезу вскрытых отложений от тюменской свиты до сеноманского яруса верхнего мела включительно (пласты Ю2, Ю1|2, Ю11, Ач1, БП164, БП163, БП12, БП9, БП4−5, БП1, АП10, ПК20, ПК9, ПК1) (всего 14 пластов).
Газовая залежь ПК1 выявлена только на северном куполе, где из первых же разведочных скважин получены притоки пластового газа. Залежь пласта ПК] вскрыта на глубинах 732−854м.
Всего в контуре газоносности пласта ПК1 пробурено 22 скважины и испытано 11 интервалов. При испытании газонасыщенных объектов рабочие дебиты на шайбах диаметром 16.1−24,1 мм составили 413.2−576,6 т.н.м3/сут. при депрессиях 0,08−1,38 МПа. Расчетные значения абсолютно-свободных дебитов оцениваются в 1752,2−6742,1 тыс. м3/сут.
Сеноманская залежь контролируется Северо-Еты-Пурским поднятием, оконтуривается изогипсой -760м и характеризуется развитием дизъюнктивной тектоники в отложениях сеномана.
Газоводянной контакт (ГВК) отбивается по комплексу ГИС на отметках от 761,0 до 770,7 метров в среднем составляя 768,8 м.
Залежь пласта ПК1 массивная, водоплавающая. Высота залежи 115 м. размеры ее 11,537 км.
Еты-Пуровское месторождение входит в подгруппу высокопродуктивных залежей Южной группы месторождений, высокая эффективность разработки которых подтверждена освоением Вынгапуровского, Комсомольского, Западно-Таркосали некого и Губкинского месторождений.
Сеноманская толща имеет сложное строение и представляет собой чередование пород коллекторов и неколлекторов.
Продуктивная толща охарактеризована керном в 13 скважинах. Из газонасыщенной части вынесено 90 м керна (22.6% от суммарной проходки), что свидетельствует о низкой изученности пласта ПК1 керном. Всего из коллекторов сеноманской толщи выполнено 73 определения пористости и 14 проницаемости.
Пористость по керну изменяется от 29,5 до 47%. средневзвешенное значение составляет 36,6%. Коэффициент пористости, определенный по данным ГИС, равен 35,5%.
Коэффициент начальной газонасыщенности по ГИС составляет 0,76.
Качественных прямых определений проницаемости по керну не получено. По ГИС проницаемость определена по зависимости Кпр = f (Кпэф) и составляет 988 мД.
В сводовой части разреза вскрыты наиболее высокие значения эффективных толщин, величины которых достигают 89,6 м (скв.88). На периферии разрез заглинизирован, эффективные толщины колеблются от 7,6 м (скв. 176) до 28,4 м (скв.5).
Компонентный состав газа сеноманской залежи определен по шести пробам. Природный газ имеет преимущественно метановый состав. Содержание метана изменяется от 98,02 до 98,96%. Высшие гомологи метана представлены этаном -0,06%. Содержание углекислого газа варьирует от 0,04 до 0,43%, азота 0,64 -1,95%, сероводород отсутствует, водород обнаружен в трех пробах в количестве 0,02%, содержание гелия составляет 0,02% - 0,017%, аргона — 0,02%.
Среднекритические параметры газа составляют: среднекритическое давление -4,6МПа. среднекритическая температура 189.93°К.
Значение температуры продуктивной части пласта ПК1 по геотермограмме составляет 25 °C на отметке 770 м, соответствующей 1/3 залежи от среднего положения ГВК.
Запасы газа утверждены ГКЗ РФ в 1997 г. в объеме 299 488 млн. м3 по категории С, и 10 000 млн. м3 по категории Сз (Протокол ГКЗ РФ № 499 от 31.10.1997 г.).
Работы по исследованию разведочных скважин на Еты-Пуровском месторождении проводились силами Тарко-Салинской нефтегазоразведочной экспедиции производственного объединения «Пурнефтегазгеология'' в основном с 1971 по 1975 гг. за исключением скв.82, которая была пробурена и испытана в 1987 г. Исследовательские работы проводились как в открытом стволе в процессе бурения, так и в обсаженных скважинах после их перфорации.
Максимальные дебиты на режимах были достигнуты по скв.1 и 4 — 736 761 тыс. м3/сут при депрессиях на пласт 0.16 — 0,20 МПа, минимальный дебит при испытании нижнего интервала (а.о.755,6 — 760,6 м) скв. 10. что на 6 м выше поверхности ГВК — 263 тыс. м3/сут при депрессии 1,46 МПа.
Статическое давление на устьях-разведочных скважин колебалось-от 7,56'до 7.80 МПа в среднем составляя 7,64 МПа. Среднее пластовое давление, рассчитанное по барометрической формуле, составляет 8,17 МПа, замеренное глубинными манометрами — 8,11 МПа.
Как показывают результаты исследований интервалов разведочных скважин сеноманская газовая залежь Еты-Пуровского месторождения характеризуется высокой потенциальной продуктивностью. В основном объеме исследований коэффициента фильтрационного сопротивления «а» составляют 0,12 — 0.51×10−2 МПа2 сут/тыс.м3, а «b» меняются от 0.3 — 0.0018×10−2 (МПа сут/тыс.м3)2 при величине вскрытой толщины 5−10 м. Такой порядок коэффициентов отмечался по разведочным скважинам Комсомольского. Губкинского. Западно-Таркосалинского. Вынгапуровского месторождений. Эксплуатационные скважины этих месторождений в основной период разработки давали дебиты 450−800 тыс. м3/сут.
Статистическая обработка результатов исследований по ряду разрабатываемых месторождений, расположенных вблизи Еты-Пуровского и характеризующихся аналогичным геологическим строением, позволила установить статистические зависимости между продуктивностью скважин и величиной перфорированной толщины.
В соответствии с установленными зависимостями проектные величины коэффициентов фильтрационного сопротивления для сеноманской залежи оцениваются:
а = 0,22×10−2 МПа2 сут/тыс.м3
b= 0,26×10−2 (МПасут/тыс.м3)2.
Следует отметить, что полученные оценки проектной продуктивности эксплуатационных скважин нуждаются в уточнении, поскольку объем информации на этапе поисково-разведочных работ крайне ограничен. В то же время полученные оценки достаточно хорошо согласуются с фактическими данными по продуктивности скважин на Комсомольском и Западно-Таркосалинском месторождениях, имеющих аналогичное геологическое строение. На этапе разбуривания залежи по результатам первичных исследований эксплуатационных скважин их продуктивные характеристики должны быть уточнены.
Сеноманская газовая залежь является водоплавающей, т. е. по всей площади подстилается пластовой водой. Это обстоятельство обуславливает опасность прорыва пластовой воды к забоям скважин и их преждевременного обводнения. В реальных условиях на разрабатываемых месторождениях (Комсомольское, Западно-Таркосалинское. Вынгапуровское и др.) для предотвращения прорыва воды нижние отверстия перфорации устанавливаются на 15−20 м выше поверхности ГВК. Очевидно данная схема перфорации вполне приемлема для Еты-Пуровского месторождения.
Согласно расчетам максимальная депрессия на пласт оценивается в 0,15−0,2 МПа. При этом средний безводный дебит газовой скважины в первые годы разработки может достигать 600−650 тыс. м3/сут. По мере снижения запаса пластовой энергии в основной период разработки безводный дебит оценивается в 500−550. тыс. м3/сут, а на поздней стадии эксплуатации он уменьшится до 100−150 тыс. м3/сут.
При дебите порядка 500 тыс. м3/сут. оптимальным-диаметром-лифтовой колонны, при котором обеспечиваются рациональные потери давления от забоя до устья, является 114 мм. Эксплуатация скважин с таким лифтом обеспечит потери давления в стволе на протяжении всего периода нарастающей и постоянной добычи от 0,7 до 0,85 МПа.
Температура потока газа на устьях скважин в основной период разработки составит 15−17°С.
При выборе расчетных вариантов разработки учитывался ряд факторов геологического, технологического и технико-экономического характера.
В проекте рассмотрены четыре варианта добычи газа:
I — годовая добыча газа 10 млрд. м3 ;
II — годовая добыча газа 12 млрд. м3;
III — годовая добыча газа 13 млрд. м3;
IV — годовая добыча газа 15 млрд. м3.
При оценке показателей разработки сеноманской газовой залежи Еты-Пуровского месторождения, с учетом ранее обоснованных параметров и опыта разработки других месторождений, приняты следующие ограничения:
— предельная депрессия на пласт — 2 кг/см2;
— минимальное устьевое давление в конце разработки — 10 кг/см2;
— давление нагнетания (ДКС) — 75 кг/см2;
— минимальный дебит скважины в конце эксплуатации-50 тыс. м3/сут:
— максимальное обводнение скважины, при котором происходит ее выбытие из эксплуатационного фонда — 50% величины интервала перфорации;
— диаметр лифтовой колонны — 114 мм.
Варианты технологических показателей разработки сеноманской газовой залежи Еты-Пуровского месторождения рассчитаны на основе сеточной геологогазогидродинамической модели, включающей в себя построение геолого-промысловой модели и алгоритм численного решения системы дифференциальных уравнений совместной фильтрации жидкостей и газов в пористой среде.
К практической реализации рекомендуется разработка месторождения по варианту III.
Согласно технологическим расчетам по данному варианту предусматривается уровень годовой добычи газа в период достоянных отборов 13 млрд. м3 или 4.3% от начальных запасов. Такая добыча достигается за счет эксплуатации 75 скважин, объединенных в 18 кустов по 3−5 скважины в кусте. Средний рабочий дебит одной скважины на протяжении периода постоянных отборов составит 509 тыс. м3/сут при депрессии на пласт 1,2−2,0 кг/см2.
Продолжительность периода нарастающей и постоянной добычи — 14 лет, за которые из залежи будет отобрано 164 млрд. м3 или 55% от начальных запасов газа. Пластовое давление в зоне размещения скважин к началу падающей добычи снизится до 45.5 кгс/см2 или на 55% от начального, в залежь внедриться 800 млн. м3 пластовой воды, что обусловит обводнение 23,6% перового объема. Средний подъем ГВК в зоне размещения эксплуатационных скважин к этому времени составит 14,7 м. Срок эксплуатации залежи составит 30 лет при накопленном отборе 275,95 млрд. м3, соответствующем конечной газоотдаче 92,3%. Отработка залежи по площади будет достаточно равномерна. Пластовое давление в зоне размещения эксплуатационных скважин снизится до 13,5 кгс/см2. Обводнение залежи составит 65,6% начального перового объема, в результате которого внедрится 2,21 млрд. м3 пластовой воды. Средний подьем ГВК в зоне размещения эксплуатационных скважин составит 45 м. Начиная с 17 года разработки предполагается выбытие скважин из эксплуатации по причине их обводнения и низкодебитности. в результате чего к концу разработки 22% фонда скважин выйдут из эксплуатации.
Сеноманская газовая залежь Еты-Пуровского месторождения выгодно отличается от других в плане разработки тем, что залегает на сравнительно небольшой глубине, характеризуется высокой продуктивностью эксплуатационных скважин. Залежь массивного типа на всей площади подстилается подошвенной водой. Указанные факторы позволяют рекомендовать центрально-групповую схему размещения эксплуатационных скважин, предусматривающую формирование эксплуатационного поля в присводовой части структуры.
Существующий опыт бурения и эксплуатации скважин на аналогичных месторождениях позволяет использовать в качестве основного способа разбуривания, строительство наклонно-направленных скважин, что также значительно снижает затраты на обустройство месторождения и эксплуатацию скважин, уменьшает воздействие на окружающую среду.
Освоение газовой залежи следует начать с наиболее продуктивной ее части, т. е. первые скважины следует заложить на участке наибольших газонасыщенных толщин с последующим расширением эксплуатационного поля к периферийным частям залежи. Оптимальная степень дренирования достигается при размещении скважин в пределах изопахиты 50 м. Фактором, контролирующим количество скважин в кусте является величина удельных запасов газа. приходящихся на один куст. Поэтому в зоне наибольших удельных запасов газа, ограниченной изопахитами 70−80 м предлагается разместить кусты из пяти эксплуатационных скважин, а на участке ограниченном изопахитам 50−70м — кусты из четырех и трех скважин.
Диаметр эксплуатационной колонны принимается равным 168 мм, лифтовой -114 мм.
С целью уточнения геологического строения и выбора продуктивных пластов для перфорации первая скважина куста бурится вертикальной со вскрытием ГВК и спуском эксплуатационной колонны на глубину до 900 м (по вертикали), которая в дальнейшем будет выполнять функции эксплуатационно-наблюдательной.
Исключением являются кусты №№ 1, 7, 16, в которых предусмотрено бурение специальных вертикальных наблюдательных скважин. Остальные скважины бурятся наклонно-направленным способом и перфорируются в зависимости от фактически установленного разреза по результатам ГИС, проведенного в первой пробуренной скважине куста. Нижние отверстия перфорации устанавливаются не менее чем на 15−20 м выше начальной поверхности ГВК. Такая схема разбуривания обеспечивает длительную безводную эксплуатацию скважин в течение 15−18 лет.
При выборе схемы размещения скважин учтены также природоохранные ограничения.
По рекомендуемому варианту III потребуется пробурить 87 скважины, в том числе 75 эксплуатационных (18 кустов), 3 наблюдательных в кустах и 9 одиночных наблюдательных скважин.
В качестве пьезометрических рекомендовано использовать приконтурные и законтурные разведочные скважины, а также наблюдательные геофизические скважины, в случае их полного обводнения.
Проектные скважины бурятся наклонно-направленным способом с отходом от устья 350 м на кровлю сеномана.
Эксплуатационные скважины группируются в кусты из 3−5 скважин с расстоянием между устьями 40 м.
Выкидные линии эксплуатационных скважин подключаются к шлейфу и оборудуются сужающими быстросменными устройствами для замера дебита клапанами-отсекателями для отключения их в случае разрыва шлейфа, прямоточными задвижками.
В целях предотвращения затопления талыми водами кустовая площадка отсыпается выше максимального уровня вод. имеет уклон в сторону амбара горизонтального факела, а в целях исключения снегозаносимости территории и накопления талых весенних вод не обвалована, имеет подъездные пути.
Для внутрипромыслового сбора газа на месторождения принята коллекторная схема сбора с подключением кустов к пяти коллекторам (по 3−4 куста к каждому коллектору).
Режим работы шлейфов и коллекторов безгидратный, подача ингибитора гидрообразования от УКПГ к кустам скважин не требуется.
Расчет схемы и подбор диаметров шлейфов и коллекторов выполнен из условия минимальной разницы давлений по более удаленным коллекторам на входе в УКПГ. минимальной разницы транзитного потока и потока от кустов в месте подключения, а также исходя из существующего сортамента труб. В расчетах принят допустимый перепад давления до 6% от устьевого давления газа. Диаметры шлейфов изменяются от 219 до 720 мм.
Общая протяженность газосборных коллекторов составит 52,6 км, металлоемкость — 5122 тонны.
Предусмотрена подземная прокладка газосборных сетей.
Газ месторождения не содержит конденсата газа. в соответствии с требованиями ОСТ 51.40−93 необходима его осушка по влаге до точки росы минус 20 °C в холодный период и минус 10 °C — в теплый период года.
Для подготовки газа целесообразно принять метод абсорбционной осушки газа с использованием в качестве абсорбента триэтиленгликоля (ТЭГа) концентрации 98,5% массовых.
Подготовка газа к транспорту производится на установке комплексной подготовки газа (УКПГ).
Газ от кустов скважин поступает на входные краны пункта переключающей арматуры (ППА), а затем через сборный коллектор условным диаметром 1000 мм подается на установку сепарации газа. Сборный коллектор служит одновременно для предварительной сепарации газа от жидкости, особенно при ее пробковом поступлении из системы сбора, и защиты первичных сепараторов. Продувка сборного коллектора осуществляется в общую дренажную емкость.
Отсепарированный газ поступает на ДКС, где проходит вторую ступень очистки в фильтрах-сепараторах и компримируется до давления, обеспечивающего его подачу в магистральный газопровод.
Согласно технологическим расчетам ввод ДКС для рекомендуемого варианта разработки необходим с первого года эксплуатации. ДКС должна быть оснащена газоперекачиваюшими агрегатами типа ГПА-10 в количестве 9 штук. Максимальная установленная мощность составит 90 МВт.
После компримирования газ охлаждается для обеспечения теплового режима работы установки осушки газа (до плюс 25°С) и газопровода внешнего транспорта газа (не более плюс 40°С), затем поступает на установку осушки.
Осушка газа проводится в абсорберах, где газ последовательно проходит две секции: массообменную с контактно-сепарационнымн центробежными элементами и сепарационную, состоящую из двух сепарационных тарелок с прямоточно-центробежными элементами. Осушенный газ через пункт измерения расхода (ПИР) поступает в газопровод внешнего транспорта.
Газопровод внешнего транспорта предназначен для подачи газа от УКПГ Еты-Пуровского месторождения до точки врезки в межпромысловый газопровод с УКПГ Вынгаяхинского месторождения.
Протяженность трассы газопровода 40 км. Максимальное давление в газопроводе равно 7,5МПа. Предусмотрена подземная прокладка газопровода.
Гидравлический расчет выполнялся в соответствии с требованиями ОНТП 51−1-85 с использованием ЭВМ по программе «GIDRA 2», из условия обеспечения давления газа в точке врезки в межпромысловый газопровод 6,2МПа.
Проведенные технико-экономические расчеты показали, что при существующей отпускной цене газа на промысле (55 руб. за 1000м3), разработка месторождения по всем вариантам убыточна. Приемлемый уровень рентабельности, может быть, достигнут при повышении цены на газ на промысле до 100 руб. за 1000 м³.
Сопоставление вариантов разработки при указанной цене на газ позволяет рекомендовать третий вариант разработки к практической реализации, предусматривающий уровень годовой добычи газа в объеме 13 млрд. м3, для реализации которого потребуется 3639,91 млн.р. капитальных вложений, в т. ч. 1281,1 млн.р. в бурении и 2312,56 млн.р. в обустройстве.
Таким образом, III вариант обустройства промысла и эксплуатации месторождения характеризуется следующими технико-экономическими показателями:
— срок эксплуатации месторождения — 30 лет;
— накопленная добыча газа — 279,95 млрд. м3;
— число эксплуатационных скважин — 75 шт;
— количество кустов — 18 шт;
— средний дебит скважин — 509 м3/сут;
— объем кап. вложений в обустройство месторождения -2312,56. млн.руб.
— эксплуатационные затраты за весь период разработки — 15 513 млн. руб;
— средняя себестоимость добычи 1000 м3/газа- 56,2 руб.
— дисконтированная накопленная денежная наличность — 361,44 млн руб.
— внутренняя норма доходности — 11.44%
— срок окупаемости кап. вложений (с начала строительства) — 10 лет.
Технико-экономические предложения по разработке сеноманской залежи газа Вынгаяхинского месторождения, ТюменНИИгипрогаз, 1998г
Гришин Ф. А. Оценка разведанных запасов нефти и газа. — М.: Недра, 1969.
Закиров С. Н., Лапук Б. Б. Проектирование и разработка газовых месторождений. — М.: Недра, 1974.
Закиров С. Н. Теория и проектирование разработки газовых и газоконденсатных месторождений. — М.: Недра, 1989.
Бекиров Т. М., Шаталов А. Т. Сбор и подготовка к транспорту природных газов. — М.: Недра, 1986.
Коротаев Ю. П., Ширковский А. И. Добыча, транспорт и подземное хренение газа. — М.: Недра, 1984.
Оптимизация темпов разработки газовых месторождений./ Гацолаев А. С., Тышляр И. С. — М.: Недра, 1994.
Методы повышения эффективности процессов добычи и транспорта газа./ Мирсаджанзаде А. Х., Зайцев Ю. В. и др. — М.: Недра, 1979.
Влияние обводнения многопластовых газовых и газоконденсатных месторождений на их разработку./ Рассохин Г. В., Леонтьев И. А. и др. — М.: Недра, 1973.
Инструкция по комплексному исследованию газовых газоконденсатных пластов и скважин. — М.: Недра, 1980.
Shell, 1998 Services Guide, Интерактивный журнал.
Старикова Г. В., Милевский В. П., Шантарин В. Д. Методические указания к выполнению раздела «Безопасность и экологичность проекта». ТГНГУ, 1997.
.ur