Система автоматизации проектирования технологических параметров литья на основе моделирования обратной задачи охлаждения отливки
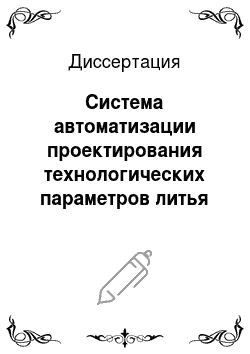
Диссертация
При изготовлении отливок применяют различные сплавы на основе железа, меди, алюминия, магния, титана, цинка и других металлов. Некоторые сплавы, например чугун, используют только в литейных цехах, так как вследствие хрупкости их нельзя подвергать ковке, штамповке и другим видам обработки давлением. Анализ методик и средств моделирования и проектирования технологий производства отливок, принципов… Читать ещё >
Список литературы
- Алифанов О.М. Идентификация процессов теплообмена летательных аппаратов. — М.: Машиностроение, 1979. 216 с.
- Алифанов О.М. О состоянии и перспективах развития обратных задач теплообмена в исследовании тепловых процессов и проектирования технических систем. Минск, 1977. — 14 с.
- Алифанов О.М. Обратные задачи теплообмена. — М.: Машиностроение, 1988. -280 с.
- Алифанов О.М. Экспериментальные методы решения некорректных задач / О. М. Алифанов, Е. А. Артюхин, C.B. Румянцев. М.: Наука, 1988. — 288 с.
- Анисович Г. А. Охлаждение отливки в комбинированной форме. -Машиностроение, 1969. 136 с.
- Антушев Г. С. Методы параметрического синтеза сложных технических систем. -М.: Наука, 1989. 88 с.
- Баландин Г. Ф. Основы формирования отливки. 4.1. Тепловые основы теории. Затвердевание и охлаждение отливки. М.: Машиностроение, 1976. — 328 с.
- Барановский Э.Ф. Идентификация теплообмена при литье металлов и сплавов / Э. Ф. Барановский, П. В. Севастьянов. Мн.: Наука и техника, 1989. — 189 с.
- Бахвалов Н.С., Жидков Н. П., Кобельков Г. М. Численные методы. М.: Наука, 1987.-600 с.
- Бек Дж. Некорректные обратные задачи теплопроводности. М: Мир, 1989. -312 с.
- Берзинь В.А. Оптимизация режимов затвердевания непрерывного слитка. Рига: Зинатне, 1977. — 148 с.
- Биргер И.А. Остаточные напряжения. М: Машгиз. — 1963. — 232 с.
- Бойченко М.С. Непрерывная разливка стали / М. С. Бойченко, B.C. Рутес, В. В. Фульмахт. М.: Металлургия, 1964. — 517 с.
- Боли Б.А., Уэйнер Д. Х. Теория температурных напряжений. М.: Мир, 1964. -517 с.
- Борисов В.Т., Голиков И. Н., Манюхин А. И., Уразаев P.A. Непрерывная разливка стали. МЧМ СССР. — 1974. — № 2. — С. 5 — 29.
- Бялик О.М., Ментковский Ю. Л. Вопросы динамической теории затвердевания металлических отливок. К.: Вища школа, Головное изд-во, 1983. — 111 с.
- Вейник А.И. Теория затвердевания отливки. М.: Машгиз, 1963. — 435 с.
- Воеводин В.В., Кузнецов Ю. А. Матрицы и вычисления. М.: Наука, 1984. — 320 с.
- Галанин М.П., Щеглов И. А. Разработка и реализация алгоритмов трехмерной триангуляции сложных пространственных областей: итерационные методы. М.: ИПМ им. М. В. Келдыша РАН, 2006. — 32 с.
- Галанин М.П., Щеглов И. А. Разработка и реализация алгоритмов трехмерной триангуляции сложных пространственных областей: прямые методы. М.: ИПМ им. М. В. Келдыша РАН, 2006. — 32 с.
- Гиршович Н.Г. Чугунное литье. М.: Металлургиздат, 1949. — 708с.
- Голод В.М. Интеграция средств анализа и синтеза в САПР литейной технологии «POLYCAST» литейного завода КАМАЗ. Литейное производство. — 1994. — № 10-П. С. 44−47.
- Голод В.М. Металлургические технологии в машиностроении: динамика последних десятилетий и резервы роста. , — Металлургия машиностроения. — 2001, № 1.
- Голод В.М. Проблемы оптимизации питания отливок / Сб. «Теплофизика процессов затвердевания стали» Киев: Институт проблем литья, 1979.
- Голод В.М. Системы автоматизированного моделирования: информационное обеспечение и адаптация математических моделей. Литейное производство. -1992.-№ 6.-С. 23−25.
- Голод В.М. Теория формирования отливки: очевидные достижения и неочевидные проблемы. Литейное производство. — 2001. — № 6. — С. 21 — 23.
- Голод В.М. Теория, компьютерный анализ и технология стального литья / В. М. Голод, В. А. Денисов. СПб.: ИПЦСПГУТД, 2007. — 610 с.
- Голод В.M., Дьяченко С. А. Численный расчет затвердевания чугунных отливок / Сб. «Кристаллизация. Теория и эксперимент» Ижевск: УлГУ, 1987. — С. 26 — 33.
- Голод В.М., Нехендзи Ю. А. Определение некоторых теплофизических свойств по кривым охлаждения / Сб. «Теплообмен между отливкой и формой» Минск: Высшая школа, 1967. — С. 179 — 183.
- Голод В.М., Тихомиров М. Д., Сабиров Д. Х. Системный анализ процесса формирования отливки (прикладные аспекты). Литейное производство. — 1995, № 4−5, С. 68.
- Громадка И.Т. Комплексный метод граничных элементов в инженерных задачах / И. Т. Громадка, Ч. Лей. М.: Мир, 1990. — 303 с.
- Гуляев Б.Б. Теория литейных процессов Л.: Машиностроение, 1976. — 216 с.
- Евтеев Д.П., Колыбалов И. Н. Непрерывное литье стали. М.: Металлургия, 1984. — 200 с.
- Евтеев Д.П., Соколов Л. А., Лебедев В. И. Сталь. — 1975. — № 1, С. 32 — 34.
- Журавлев В.А., Китаев Е. М. Теплофизика формирования непрерывного слитка. -М.: Металлургия, 1974. 216 с.
- Иванцов Г. П., Поляк Б. Т. Кристаллизация металлов. М.: АН СССР, 1960. — С. 139- 149.
- Карслоу Г., Егер Д. Теплопроводность твердых тел. М.: Наука, 1964. — 488 с.
- Клочнев Н.И., Стрижов Г. С. Исследование остаточных (литейных) напряжений в высокопрочном чугуне. Металловедение и обработка металлов. — 1957. — № 1.
- Коздоба JI.А. Методы решения обратных задач теплопереноса / JI.A. Коздоба, Н. Г. Круковский П.Г. Киев: Наук. Думка, 1982. — 360 с.
- Константинов JI.C. Механизм возникновения температурных напряжений и деформаций в отливках. Литейное производство. — 1963. — № 11. — С. 25 — 32.
- Константинов Л.С. Расчет термических напряжений и деформаций отливок постоянного сечения (метод подвижной нейтрали). Литейное производство. -1959.-№ И.
- Коцюбинский О.Ю. Коробление чугунных отливок от остаточных напряжений -М.: Машиностроение, 1965. 174 с.
- Кропоткин В.В., Васькин В.В, Компьютерные модели кристаллизации металлических сплавов. Литейное производство. — 1996. — № 10.
- Куманин И.Б. Вопросы теории литейных процессов. М.: Машиностроение, 1976.-216 с.
- Курдюмов A.B., Пику нов М.В., Чурсин В. М. Литейное производство цветных и редких металлов. М.: Металлургия, 1983. — 352 с.
- Кучин П.С. Математическое моделирование процессов литья металлов и сплавов. Литейное производство. — 2008. — № 10. — С. 37 — 39.
- Лахтин Ю.М., Леонтьева В. П. Материаловедение. М.: Машиностроение, 1980. -493 с.
- Ли К. Основы САПР (CAD/CAM/CAE). СПб.: Питер, 2004. — 560 с.
- Мальгавко Д.С. Использование моделирующей системы при разработке технологического процесса литья / материалы 10-й Международной научно-технической конференции «Информационно-вычислительные технологии и их приложения» Пенза, 2009. — 292 с.
- Мальгавко Д.С. Компьютерная программа синтеза параметров технологии литья на основе обратного моделирования / материалы 5-й Международной научно-технической конференции «Прогрессивные технологии в машиностроении» Пенза, 2009.- 176 с.
- Мальгавко Д.С. Моделирование условий равномерного охлаждения отливки / материалы 7-й Международной научно-технической конференции «Динамика систем, механизмов и машин» Омск, 2009. — 452 с.
- Мальгавко Д.С. Обратное моделирование технологии литья. — Омский научный вестник. 2009. — № 1. — С. 26 — 27.
- Мальгавко Д.С. Расчет средств воздействия на основе обратного моделирования затвердевания отливки / сборник трудов Всероссийской конференции молодых ученых и специалистов «Будущее машиностроения России» М.: МГТУ им. Н. Э. Баумана, 2009. — 220 с.
- Мальгавко Д.С. Синтез параметров технологии литья на основе обратного моделирования процесса охлаждения отливки в форме. Автоматизация в промышленности. — 2009. -№ 8. — С. 41- 43.
- Мацевитый Ю.М. Идентификация в задачах теплопроводности / Ю. М. Мацевитый, А. В Мултановский. Киев: Наук. Думка, 1982. — 240 с.
- Монастырский A.B. ProCAST 2009.0. Что нового?. Литейное производство. -2009.-№ 4.-С. 19−20.
- Монастырский A.B. Моделирование литейных процессов. Работаем в ProCAST. Литейное производство. — 2009. — № 2. — С. 29 — 34.
- Монастырский В.П. Моделирование напряженно-деформированного состояния отливки при кристаллизации. Литейное производство. — 2007. — № 8. — С. 45 — 47.
- Мяченков В.И., Мальцев В. П., Майборода В. П. и др. Расчеты машиностроительных конструкций методом конечных элементов. М.: Машиностроение, 1989. — 520 с.
- Неуструев A.A. Разработка САПР технологических процессов литья / A.A. Неуструев, A.B. Моисеев, А. Ф. Смыков. М.: ЭКОМЕТ, 2005. — 216 с.
- Неуструев A.A. Теория формирования отливки и САПР ЛТ литья, 1997, № 11
- Нехендзи Ю.А. Стальное литье М.: Металлургиздат, 1948. — 766 с.
- Норенков И.П. Основы автоматизированного проектирования. М.: МГТУ им. Н. Э. Баумана, 2002. 333 с.
- Норри Д., де Фриз Ж. Введение в метод конечных элементов. М.: Мир, 1981. -304 с.
- Огородникова О.М. Компьютерное моделирование горячих трещин в литых деталях. Литейное производство. — 2007. — № 2. — С. 27 — 30.
- Огородникова О.М. Прогнозирование кристаллизационных трещин в стальных отливках. Литейное производство. — 2008. — № 10. — С. 29 — 34.
- Огородникова О.М., Черменский В. И. Литейные CAE-системы AFSolid и WinCast. САПР и Графика. — 2001. — № 8.
- Озеров В.А. Основы литейного производства. М.: Высшая школа, 1987. — 304 с.
- Омельченко К.Т., Пчелкин В. Г. ИФЖ. — 1975. — Т. 29. — № 1.
- Оно А. Затвердевание металлов. М. Металлургия, 1980. — 147 с.
- Рутес B.C., Аскольдов В. И., Евтеев Д. П. и др. Теория непрерывной разливки. -М.: Металлургия, 1976. 335 с.
- Рыжиков A.A. Теоретические основы литейного производства. М.: Свердловск Машгиз, 1961. — 447 с.
- Рысев М.А. Системы компьютерного моделирования литейных процессов. -Литейное производство. 2001. -№ 1.-С.28−29.
- Сабонадьер Ж.К. Метод конечных элементов и САПР / Ж. К. Сабонадьер, Ж. Л. Кулон. М.: Мир, 1989. — 190 с.
- Самарский A.A. Теория разностных схем. М.: Наука, 1989.
- Сегерлинд Л. Применение метода конечных элементов. М.: Мир, 1979. — 392 с.
- Сладкоштеев В.Т., Ахтырский В. И., Потанин Р. В. Качество стали при непрерывной разливке. М.: Металлургия, 1964. — 174 с.
- Соболев В.В., Трефилов П. М. Оптимизация тепловых режимов затвердевания расплавов. Красноярск, 1986. — 154 с.
- Соболев В.В., Трефилов П. М. Процессы тепломассопереноса при затвердевании непрерывных слитков. Красноярск, 1984.
- Соболев В.В., Трефилов П. М. Теплофизика затвердевания металла при непрерывном литье. М.: Металлуглия, 1988. — 160 с.
- Справочник по чугунному литью / под ред. Н. Г. Гиршовича. — JI.: Машиностроение, 1978. 758 с.
- Тихомиров М.Д. Модели литейных процессов в САМ ЛП «Полигон» / Сб. науч. тр. ЦНИИМ «Литейные материалы, технология, оборудование» СПб, 1995. — С. 21 -26.
- Тихомиров М.Д. Модели литейных процессов в СКМ ЛП «Полигон» / Сборник трудов ЦНИИМ «Литейные материалы, технология, оборудование» СПб., 1995. -85 с.
- Тихомиров М.Д. Основы моделирования литейных процессов. Тепловая задача.- Литейное производство. 1998. — № 4. — С. 30 — 34.
- Тихомиров М.Д. Основы моделирования литейных процессов. Усадочная задача.