Влияние водорода на процесс газового азотирования стали Х12М
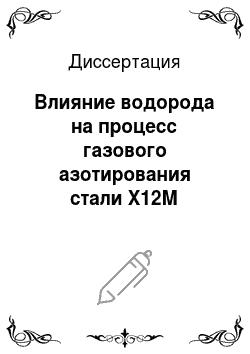
Диссертация
Установлено, что интенсивность формирования азотированного слоя при насыщении стали в продуктах частичной диссоциации аммиака изменяется в зависимости от площади поперечного сечения образца с учетом, соответственно, температурно-временного фактора выдержки при заданном режиме азотирования. Азотированный слой при газовом азотировании в аммиаке наиболее интенсивно формируется при поперечном сечении… Читать ещё >
Список литературы
- Лахтин Ю.М., Коган Я. Д., Шпис Г. Й., Бремер 3. Теория и технология азотирования. М.: Металлургия, 1991. 320 с.
- Лахтин ЮМ. Азотация стали. М.: Машгиз, 1943. 48с.
- Сыропятов В. Я, Зинченко В. М., Перекатов Ю. А. Современная концепция азотного потенциала// МиТОМ, 2004. № 1. с.7
- Лахтин Ю.М., Леонтьева В. П. Материаловедение: Учебник для высших технических учебных заведений. 3-е изд., прераб. и доп. М.: Машиностроение, 1990. 528 с.
- Болховитдинов Н.Ф. Металловедение и термическая обработка. Изд. 6-е перераб и доп. М.: Машиностроение, 1965. 503 с.
- Основы материаловедения. Учебник для ВУЗов под ред. И. И. Сидорина. М.: Машиностроение, 1976. 436 с.
- Гуляев А.П. Металловедение. М.: Металлургия, 1978. 648 с.
- Сулейманов Н.М., Айвазов Б. Ю., Сулейманова С. Н. Двухступенчатая закалка стали Х12М // МиТОМ, 1999. № 11. с. 18−20
- А.с. 797 244 СССР, МКИ С 21 Д1/78. Способ термической обработки инструмента//Бюллетень изобретений. 1980. № 12. с.4
- Алиев Ал.А. Повышение качества пуансонов из стали Х12М // МиТОМ, 2004. № 3. с.38−40
- Зимин А.В. Влияние атомного строения легирующих компонентов на превращения аустенита и разработка режимов термической обработки стали Х12М. Дисс.канд.техн.наук. Москва, 1998. 137 с
- Лахтин Ю.М., Коган Я. Д. Азотирование стали. М.: Машиностроение, 1976.256 с
- Павлова Л.П., Геллер Ю. А. Азотирование штамповых сталей перед закалкой. В кн.: Защитные покрытия на металлах, вып.2, Киев, Наукова думка, 1968, с. 230−236
- Лахтин Ю.М., Коган Я. Д. Азотирование в тлеющем разряде // Технология и механизация термической обработки металлов. М.: НИИинформтяжмаш, 13−74−8, 1076, 36 с
- Heinrich H.J., Lerche W., Zimdars H., Spengler A., Bohmer S // Neue Hutte, 28 (1983) 10, s.626−635
- Бабул Т., Кучариева Т. Г., Наконечный А. Влияние исходной структуры инструментальных сталей на толщину и твердость слоев, полученных в результате карбонитрирования // МиТОМ, 2004. № 7. с.17−20
- Kucharieva N.G., Babul Т., Senatorski J. Struktura I svoistva diffuzyonnych karbidonitridnykh pokryti na bystrorezuschikh I nerzaveuschikh stalyach // Metalloobrabotka Rossia/ St.Petersburg. 2002. № 1 (7). P.21−24
- Анвар Ахмед Ибрагим Хамиль. Азотирование в условиях термоциклических воздействий. Дисс. Канд.техн.наук. Москва, 1999. — 142 с
- Самсонов Г. В., Уманский Я. С. Твердые соединения тугоплавких металлов. М.: Металлургиздат, 1957
- Самсонов Г. В. Тугоплавкие соединения. Справочник. М.: Металлургиздат, 1963
- Кубашевски О. Диаграммы состояния двойных систем на основе железа: пер. с англ./ под ред. JI.A. Петровой. М.: Металлургия, 1985. 184 с
- Банных О.А., Будберг П. Б., Алисова С. П. и др. Диаграммы состояния двойных и многокомпонентных систем на основе железа. М.: Металлургия, 1986.440 с
- Чижевский Н.П. // Изв. Томского технологического института. 1913. т.31. № 3. с. 1−91
- Диаграммы состояния двойных металлических систем: справочник в 3-х т.: т.2 / под общ. Ред. Н. П. Лякишева. М.: Машиностроение, 1997.1024 с
- Андрачников Ш. Л. Термодинамический анализ процесса азотирования // Журнал физической химии, 19 763. т. XLV||. № 10. с.2535−2537
- Смирнов А.В. Таблицы термодинамических функций для реакций, встречающихся при химико термической обработке стали // Труды Ленинградского института авиационного приборостроения, 1957. вып. 22. с.33−77
- Каплина Г. С., Жунковский Г. Л. К вопросу о механизме начальной стадии процесса азотирования. — В кн.: Защитные покрытия на металлах, 1966, вып. 2. с.73−80
- Лахтин Ю.М., Коган Я. Д. Регулируемые процессы азотирования // МиТОМ, 1979. № 8. с.59−64
- Cojoraru М., Florian Е. Comentaria cu azot resultatal schimbului de electroni intre metal si ammoniak // Metallurgia (RSR), 1978 30. № 7. s. 406−409
- Арчаков Ю.И. Водородная коррозия стали. М.: Металлургия, 192 с
- Гельд П.В., Рябов Р. А. Водород в металлах и сплавах. М.: Металлургия, 1974. 274 с
- Бэррер Р. Диффузия в твердом теле. Пер. с англ. М.: ИЛ, 1948. 504 с
- Губанов А.Н. ФТТ, 1964. т.6. № 4 с. 1023−1029- Губанов А. Н., Никулин В. К. ФТТ, 1965. т.7.с. 2701−2707
- Водород в металлах: пер. с англ. / под ред. Алефельда Г. И. и Фелькля Н. М. М.: Мир, 1981. т. 1. 475 с- т.2. 430 с
- Лахтин Ю.М. Физические основы процесса азотирования. М.: Машгиз, 1948. 144 с
- Белоцкий А.В., Мохорт А. В., Пермяков В. Г. Высокотемпературная рентгенография азотирования армко железа // Известия ВУЗов. Черная металлургия, 1966. № 5. с. 147−151
- Юргенсон А.А. Азотирование в энергомашиностроении. М.: Машгиз, 1962. 132 с
- Вороненко Б.И. Водород и флокены в стали // МиТОМ, 1997. № 11. с. 12−18
- Герасимов С.А., Жихарев А. В., Березина Е. В., Зубарев Г. И., Пряничников В. А. Новые идеи о механизме образования структуры азотированных сталей // МиТОМ, 2004. № 1. с. 13−17
- Взаимодествие металлов с газами. В 2-х томах. Т.2. Фаст Дж.Д. пер. с англ. М.: Металлургия, 1975. 352 с
- Катлинский В.М. Изв. АН СССР. Неорганические материалы, 1978. т. 14. № 9. с. 1667−1673
- Добаткин В.И., Габидуллин P.M., Колачев Б. А. и др. Газы и окислы в алюминиевых деформируемых сплавах. М.: Металлургия, 1976. 264 с
- Cochard A.W., Schock G., Wiedersich H. «Acta metallurgia», 1955. v.3. p.533
- Thomas W.R., Leah G.M. -«Proc. Phys. Soc.», 1955. v.b.68. p.1001- v.b.72. p.673
- Petarra D.P., Beshers D.N. «Acta metallurgia», 1967. v.15. p.791
- Ino H., Sugeno T. «Acta metallurgia», 1967. v. 15. p. 1197
- Бунин К.П., Шаповалов В. И., Трофименко B.B. // Доклады АН УССР, 1976. № 3. с.265−267
- Шаповалов В.И. // Изд. ВУЗов. Черная металлургия, 1976. № 12. с.92−96
- Шаповалов В.И. // Журнал физической химии, 1980. т.54. № 11. с.2899−2905
- Шаповалов В.И. Влияние водорода на структуру и свойства железоуглеродистых сплавов. М.: Металлургия, 1982. 232 с
- Шаповалов В.И., Трофименко В. В. // Журнал физической химии, 1978. т.52. № 12. с.3140−3142
- Шаповалов В.И., Трофименко В. В. // Доклады АН УССР, 1977. № 1. с.74−76
- Шаповалов В.И., Карпов В. Ю. // Физика металлов и металловедение, 1983. т.55. № 4.с.805−811
- Шаповалов В.И., Бойко Л. В. // Изв. ВУЗов. Черная металлургия, 1984. № 8. с. 122−125
- Трапнер Б. Хемосорбция. М.: ИЛ, 1958. 327 с.
- Фромм Е., Гебхард Е. Газы и углерод в металлах. М.: Металлургия, 1980.712 с
- Колачев Б.А. Водородная хрупкость металлов. М.: Металлургия, 1985. 216 с
- Астафьев А.А. Водородное охрупчивание конструкционных сталей // МиТОМ, 1984. № 2. с.2−7
- Котрелл А.Х. Дислокации и пластическое течение в металлах. М.: Металлургиздат, 1958
- Лахтин Ю.М., Бутенко О. И., Шашков Д. П., Крымский Ю. Н., Мальцева Т. М. Печное и ионное азотирование маломагнитных сталей в различных газовых средах // Высокопрочные немагнитные сплавы. М.: «Наука», 1973. с. 60−67.
- Астафьев А.А. Рациональные режимы отжига крупных поковок после ковки // МиТОМ, 1962. № 5. с.2
- Панасюк В.В., Ковчик С. Е., Сморода Г. И. Методы оценки водородной хрупкости конструкционных материалов // ФХММ, 1979. № 3. с.5
- Steigerwald Е.А., Shaller F.W., Troiano A.R. Trans. Met. Soc. of ASME, 1959. v.215. № 6. p.16
- Мнушкин O.C., Эстрин Б. М. Взаимодействие стали с водородом при термической обработке в контролируемых атмосферах // МиТОМ, 1983. № 11. с.50−52
- Балтер М.А., Гольднггейн Л. Я., Аксенова С. И. Влияние нагрева в водородсодержащей атмосфере на механические свойства и характер разрушения сталей в высокопрочном состоянии // МиТОМ, 1984. № 2. с. 10−12
- Суранов Г. И. О поведении водорода при разрушении и трении металлов и сплавов // МиТОМ, 1998. № 6. с.18−22
- Суранов Г. И. О механизме наводороживания металлов при деформировании и трении // Долговечность трущихся деталей машин: сб. статей под ред. Д. Н. Гаркунова. М.: Машиностроение, 1987. с.152−162
- Хрусталев Ю.А. Физико — химическая концепция наводороживания металлов / Роль эмиссии электронов с поверхности разрушения конструкционных материалов в процессе образования водорода // Эффект безопасности и триботехнологии, 1997. № 2. с. 19−35
- Шаповалов В.И., Трофименко В. В. Флокены и контроль водорода в стали. М.: Металлургия, 1987. 160 с
- Соловей Н.Ф., Тороп В. В., Матюшенко В .Я. Наводороживание трущихся деталей цилиндро — поршневой группы ДВС // Трение и износ, 1985.T.6. № 4. с.751−754
- Ямопольский Ю.П. Элементарные реакции и механизмы пиролиза водородов. М.: Химия, 1990. 216 с
- Черкис Ю.Ю., Круточина Н. А., Савинков Р. А. Насыщение водородом нержавеющих и конструкционных сталей при азотировании // МиТОМ, 1981. № 3. с.14−19
- Потак Я.М. Хрупкие разрушения стали и стальных деталей. М.: Металлургия, 1955. 284 с
- Щербединский Г. В., Шумаков А. И., Нечаева О. В. Низкотемпературное цианирование быстрорежущих сталей в безводородной плазме // МиТОМ, 2004. № 1. с.40−42
- Юргенсон А.А. Роль водорода при азотировании стали // Физика металлов и металловедение, 1959.Т.7. вып.1. с.110−115
- Лахтин Ю.М. Физические основы процесса азотирования, ВНИИТОМАШ. М.: Машгиз, 1948. с. 119,123
- Юрьев С.Ф. О природе дефектов азотированной поверхности на стали 38ХМЮА. Тр. ЦНИИ, 1946. № 5. с.26
- Носырева С.С., Погребецкая Т. М., Юргенсон А. А. Технология транспортного машиностроения, 1956. 2
- Минкевич А.Н. Химико-термическая обработка металлов и сплавов. М.: Машиностроение, 1965.490 с
- Минкевич А.Н. Химико-термическая обработка стали. М.: Машгиз, 1950
- Френкель Я.И. Введение в теорию металлов. М.: Физматгиз, 1958. 368 с
- Геллер Ю.А. Инструментальные стали. 4-е изд. М.: Металлургия, 1975. 584 с
- Гуляев А.П., Акименцева A.JI. -ЖТФ, 1955. т.16. вып.2. с.299−300
- Акишин А.И. Ионная бомбардировка в вакууме. М.- JL: Госэнергоиздат, 1963. 114 с
- Халдеев Г. В. Образование и развитие микротрещин в трансформаторной стали при наводороживании. Деп. ВНИИТИ № 3177−75, 1976
- Beachem С. Metal. Trans., 1972. v.3. № 2. р.437
- Савченков Э.А., Светличкин А. Ф. Разрушение стали на различных стадиях водородного охрупчивания // МиТОМ, 1980. № 12. с.19−21
- Крылов В.П. Об аномалиях деформационной способности деазотированных металлов при температурах обратимого водородного охрупчивания // МиТОМ, 1995. № 12. с. 15−18
- Карпенко Г. В. Влияние активных жидких сред на выносливость стали. Изд. АН УССР, 1955
- Карпенко Г. В., Крипяткевич Р. И. Влияние водорода на свойства стали. М.: Металлургиздат, 1962.197 с
- Мороз Л.С., Мингин Т. Э., Сб. Металловедение, вып.2, Судпромгиз, 1958. с.3−24
- Мороз Л.С., Мингин Т. Э., Сб. Металловедение, вып. З, Судпромгиз, 1959. с.51−57
- Bastien P., Azou P., Compt. Rend, 1949. 228 р.1337
- Bastien P., Azou P., Proceedings of the First World Metallurgical Congress, ASME, 1651. p.535−552
- Frohmberg R.D., Barnett W.J., Troiano A.R. Trans., ASME, 1955, 47. p. 892−925
- Bastien P., Azou P., Compt. Rend, 1955. № 24. p.241
- Hobson J.D., Hewitt J.J., Iron and Steel Inst., 1953. 173. № 2. p. 131−140
- Просвирин В.И. К вопросу об ионной диффузии в металлах. Вестник металлопромышленности. 1937. № 12
- Францевич Н.Н., Калинович Д. Ф. Явление электропереноса в твердых металлических растворах. Вопросы порошковой металлургии и прочности металлов. 1956. Вып. З
- Pierre, Chevenard. Journal Academie Siens. 1953. № 13
- Kopietz K. Harterei Techn. und Warmebehandlung. 1958. № 6
- Латышев А. А., Суранов Г. И. Влияние электролитического наводороживания на содержание легирующих элементов в стали // МиТОМ, 2003. № 3. с.32−36
- Strauss В. Mikroskopische Stahluntersuchung // Stahl und Eisen. 1914. № 34. s.1814−1820
- Bohnenkamp K. Uber das Nitrieren von Reineisen und legierten Stahlen // Arch. Eisenhuttenwes. 1967. № 38. s.229−232. s.433−437
- Echstein H.-J., Lerche W. Untersuchungen zur Beschleunigung der Nitrierung in der Gasphase //Neue Hutte. 1968. № 13. s.210−215
- Spies H.-J., Vogt F. Gasoxinitrieren hochlegierten Stahle // HTM. 1997. № 52. s.342−349
- Gemma K., Kawakami H., Hagiwara M. Effect of NH3−02 gas mixtures on the protective oxide film on high chromium alloi steel // Mat.- Wiss. U. Werkstofftech. 1993. № 24. p.378−385
- Шпис Х.-И. Вторая лекция Лахтинских мемориальных чтений // МиТОМ. 2000. № 5. с.4−17
- Лахтин Ю.М., Лебедева Г. В. Азотирование титаносодержащих сталей //МиТОМ. 1971. № 12. с.16−19